Essay on Operation Management.
VerifiedAdded on 2022/08/22
|5
|1405
|14
AI Summary
Contribute Materials
Your contribution can guide someone’s learning journey. Share your
documents today.
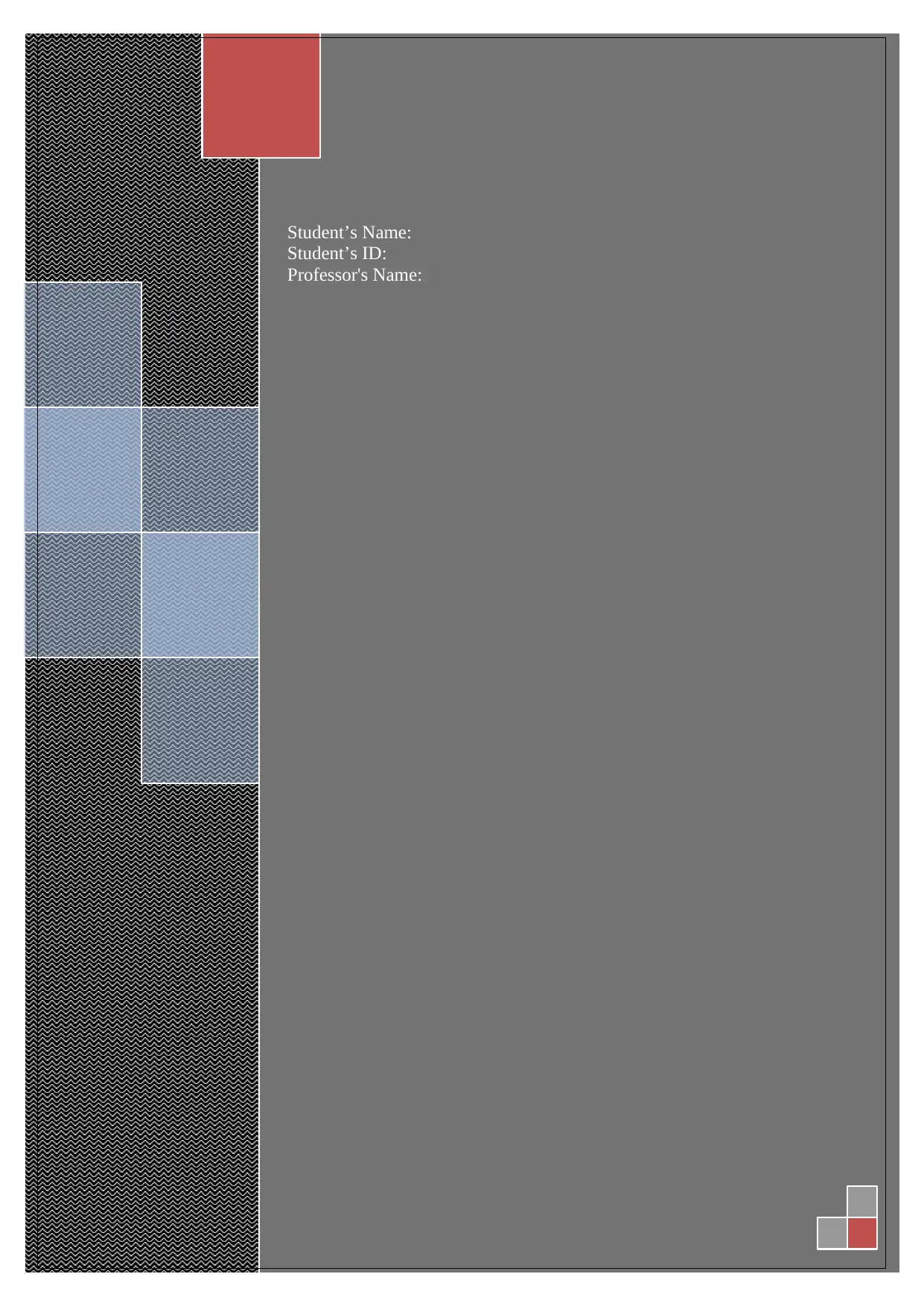
Student’s Name:
Student’s ID:
Professor's Name:
Student’s ID:
Professor's Name:
Secure Best Marks with AI Grader
Need help grading? Try our AI Grader for instant feedback on your assignments.
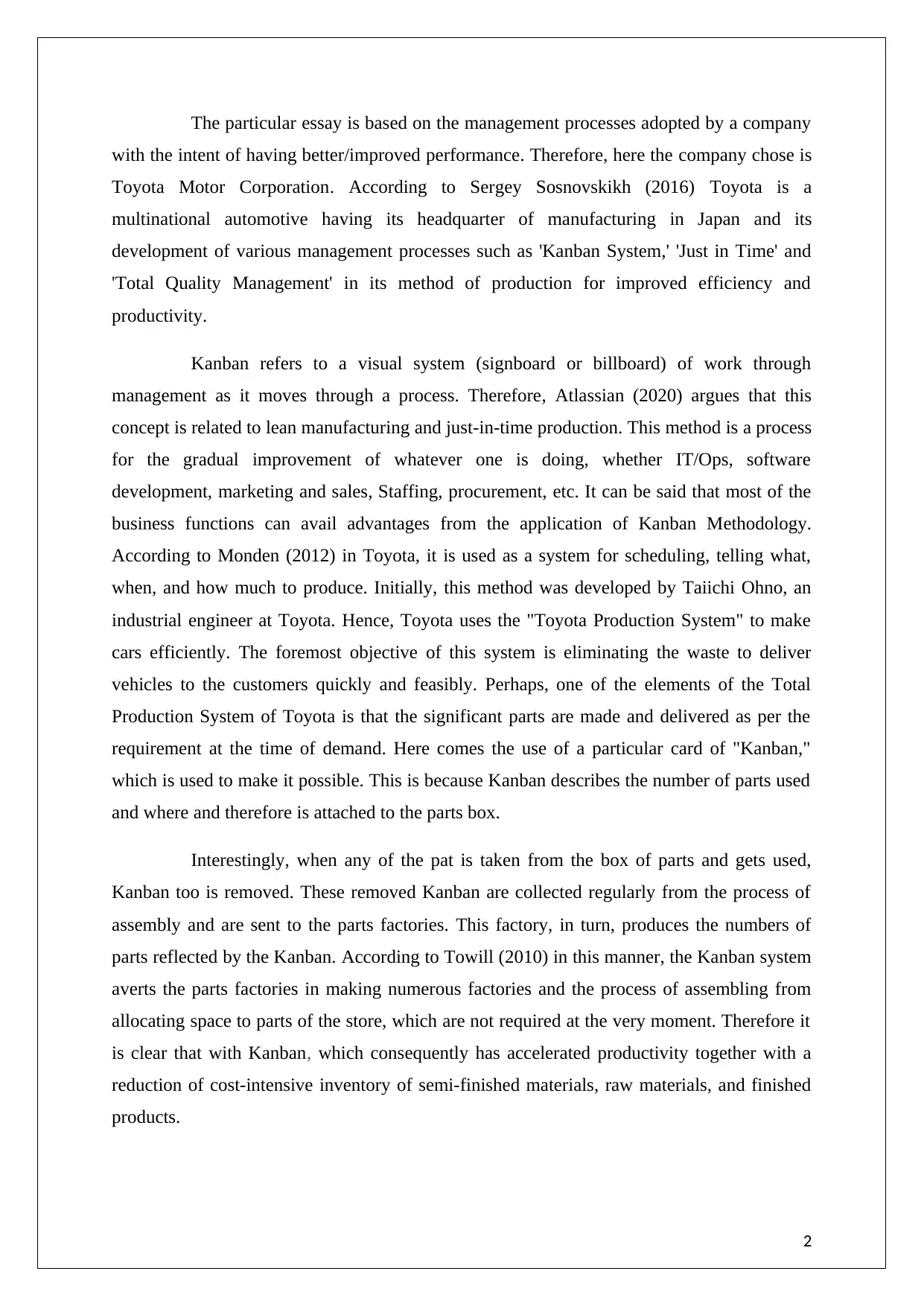
The particular essay is based on the management processes adopted by a company
with the intent of having better/improved performance. Therefore, here the company chose is
Toyota Motor Corporation. According to Sergey Sosnovskikh (2016) Toyota is a
multinational automotive having its headquarter of manufacturing in Japan and its
development of various management processes such as 'Kanban System,' 'Just in Time' and
'Total Quality Management' in its method of production for improved efficiency and
productivity.
Kanban refers to a visual system (signboard or billboard) of work through
management as it moves through a process. Therefore, Atlassian (2020) argues that this
concept is related to lean manufacturing and just-in-time production. This method is a process
for the gradual improvement of whatever one is doing, whether IT/Ops, software
development, marketing and sales, Staffing, procurement, etc. It can be said that most of the
business functions can avail advantages from the application of Kanban Methodology.
According to Monden (2012) in Toyota, it is used as a system for scheduling, telling what,
when, and how much to produce. Initially, this method was developed by Taiichi Ohno, an
industrial engineer at Toyota. Hence, Toyota uses the "Toyota Production System" to make
cars efficiently. The foremost objective of this system is eliminating the waste to deliver
vehicles to the customers quickly and feasibly. Perhaps, one of the elements of the Total
Production System of Toyota is that the significant parts are made and delivered as per the
requirement at the time of demand. Here comes the use of a particular card of "Kanban,"
which is used to make it possible. This is because Kanban describes the number of parts used
and where and therefore is attached to the parts box.
Interestingly, when any of the pat is taken from the box of parts and gets used,
Kanban too is removed. These removed Kanban are collected regularly from the process of
assembly and are sent to the parts factories. This factory, in turn, produces the numbers of
parts reflected by the Kanban. According to Towill (2010) in this manner, the Kanban system
averts the parts factories in making numerous factories and the process of assembling from
allocating space to parts of the store, which are not required at the very moment. Therefore it
is clear that with Kanban, which consequently has accelerated productivity together with a
reduction of cost-intensive inventory of semi-finished materials, raw materials, and finished
products.
2
with the intent of having better/improved performance. Therefore, here the company chose is
Toyota Motor Corporation. According to Sergey Sosnovskikh (2016) Toyota is a
multinational automotive having its headquarter of manufacturing in Japan and its
development of various management processes such as 'Kanban System,' 'Just in Time' and
'Total Quality Management' in its method of production for improved efficiency and
productivity.
Kanban refers to a visual system (signboard or billboard) of work through
management as it moves through a process. Therefore, Atlassian (2020) argues that this
concept is related to lean manufacturing and just-in-time production. This method is a process
for the gradual improvement of whatever one is doing, whether IT/Ops, software
development, marketing and sales, Staffing, procurement, etc. It can be said that most of the
business functions can avail advantages from the application of Kanban Methodology.
According to Monden (2012) in Toyota, it is used as a system for scheduling, telling what,
when, and how much to produce. Initially, this method was developed by Taiichi Ohno, an
industrial engineer at Toyota. Hence, Toyota uses the "Toyota Production System" to make
cars efficiently. The foremost objective of this system is eliminating the waste to deliver
vehicles to the customers quickly and feasibly. Perhaps, one of the elements of the Total
Production System of Toyota is that the significant parts are made and delivered as per the
requirement at the time of demand. Here comes the use of a particular card of "Kanban,"
which is used to make it possible. This is because Kanban describes the number of parts used
and where and therefore is attached to the parts box.
Interestingly, when any of the pat is taken from the box of parts and gets used,
Kanban too is removed. These removed Kanban are collected regularly from the process of
assembly and are sent to the parts factories. This factory, in turn, produces the numbers of
parts reflected by the Kanban. According to Towill (2010) in this manner, the Kanban system
averts the parts factories in making numerous factories and the process of assembling from
allocating space to parts of the store, which are not required at the very moment. Therefore it
is clear that with Kanban, which consequently has accelerated productivity together with a
reduction of cost-intensive inventory of semi-finished materials, raw materials, and finished
products.
2
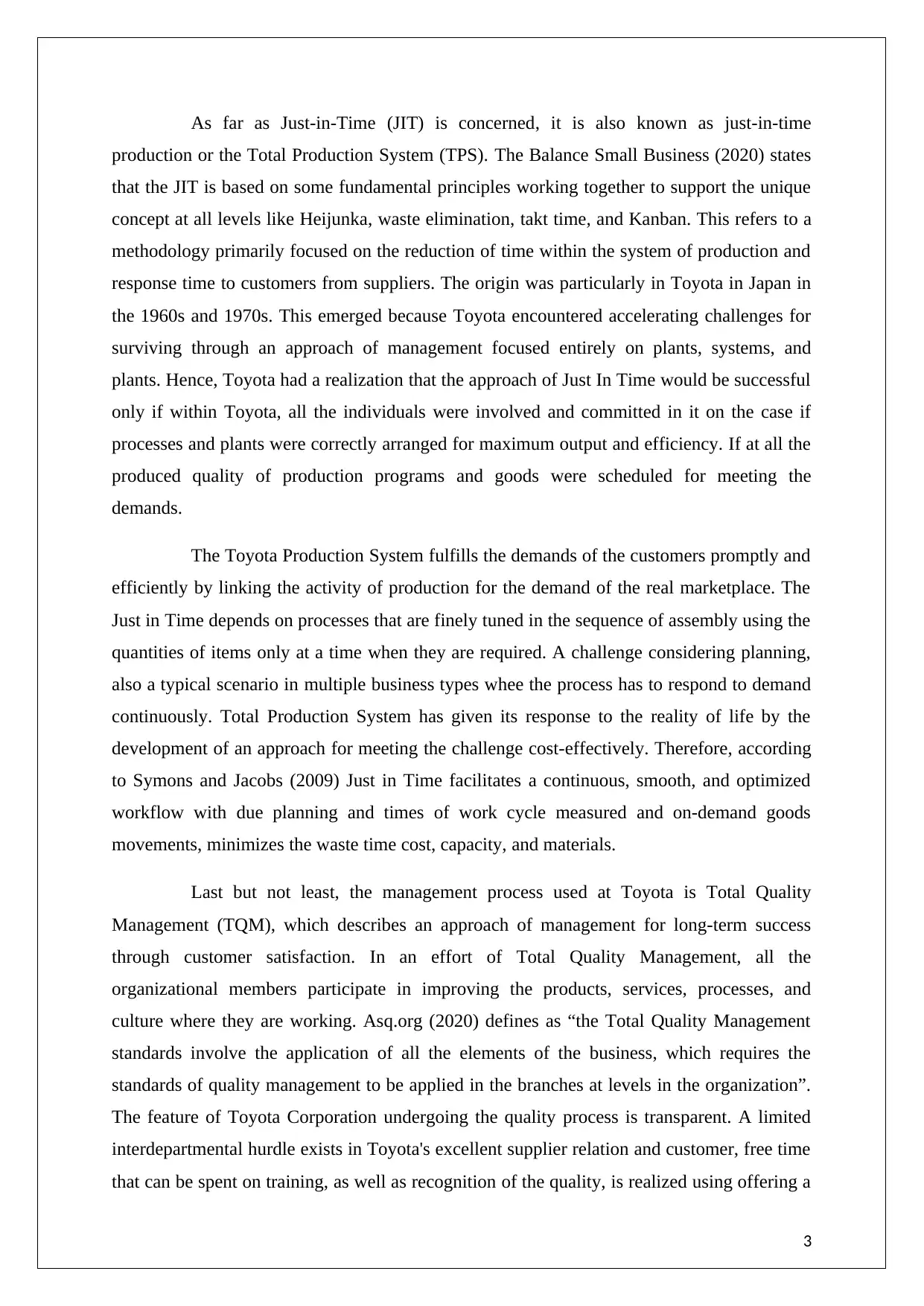
As far as Just-in-Time (JIT) is concerned, it is also known as just-in-time
production or the Total Production System (TPS). The Balance Small Business (2020) states
that the JIT is based on some fundamental principles working together to support the unique
concept at all levels like Heijunka, waste elimination, takt time, and Kanban. This refers to a
methodology primarily focused on the reduction of time within the system of production and
response time to customers from suppliers. The origin was particularly in Toyota in Japan in
the 1960s and 1970s. This emerged because Toyota encountered accelerating challenges for
surviving through an approach of management focused entirely on plants, systems, and
plants. Hence, Toyota had a realization that the approach of Just In Time would be successful
only if within Toyota, all the individuals were involved and committed in it on the case if
processes and plants were correctly arranged for maximum output and efficiency. If at all the
produced quality of production programs and goods were scheduled for meeting the
demands.
The Toyota Production System fulfills the demands of the customers promptly and
efficiently by linking the activity of production for the demand of the real marketplace. The
Just in Time depends on processes that are finely tuned in the sequence of assembly using the
quantities of items only at a time when they are required. A challenge considering planning,
also a typical scenario in multiple business types whee the process has to respond to demand
continuously. Total Production System has given its response to the reality of life by the
development of an approach for meeting the challenge cost-effectively. Therefore, according
to Symons and Jacobs (2009) Just in Time facilitates a continuous, smooth, and optimized
workflow with due planning and times of work cycle measured and on-demand goods
movements, minimizes the waste time cost, capacity, and materials.
Last but not least, the management process used at Toyota is Total Quality
Management (TQM), which describes an approach of management for long-term success
through customer satisfaction. In an effort of Total Quality Management, all the
organizational members participate in improving the products, services, processes, and
culture where they are working. Asq.org (2020) defines as “the Total Quality Management
standards involve the application of all the elements of the business, which requires the
standards of quality management to be applied in the branches at levels in the organization”.
The feature of Toyota Corporation undergoing the quality process is transparent. A limited
interdepartmental hurdle exists in Toyota's excellent supplier relation and customer, free time
that can be spent on training, as well as recognition of the quality, is realized using offering a
3
production or the Total Production System (TPS). The Balance Small Business (2020) states
that the JIT is based on some fundamental principles working together to support the unique
concept at all levels like Heijunka, waste elimination, takt time, and Kanban. This refers to a
methodology primarily focused on the reduction of time within the system of production and
response time to customers from suppliers. The origin was particularly in Toyota in Japan in
the 1960s and 1970s. This emerged because Toyota encountered accelerating challenges for
surviving through an approach of management focused entirely on plants, systems, and
plants. Hence, Toyota had a realization that the approach of Just In Time would be successful
only if within Toyota, all the individuals were involved and committed in it on the case if
processes and plants were correctly arranged for maximum output and efficiency. If at all the
produced quality of production programs and goods were scheduled for meeting the
demands.
The Toyota Production System fulfills the demands of the customers promptly and
efficiently by linking the activity of production for the demand of the real marketplace. The
Just in Time depends on processes that are finely tuned in the sequence of assembly using the
quantities of items only at a time when they are required. A challenge considering planning,
also a typical scenario in multiple business types whee the process has to respond to demand
continuously. Total Production System has given its response to the reality of life by the
development of an approach for meeting the challenge cost-effectively. Therefore, according
to Symons and Jacobs (2009) Just in Time facilitates a continuous, smooth, and optimized
workflow with due planning and times of work cycle measured and on-demand goods
movements, minimizes the waste time cost, capacity, and materials.
Last but not least, the management process used at Toyota is Total Quality
Management (TQM), which describes an approach of management for long-term success
through customer satisfaction. In an effort of Total Quality Management, all the
organizational members participate in improving the products, services, processes, and
culture where they are working. Asq.org (2020) defines as “the Total Quality Management
standards involve the application of all the elements of the business, which requires the
standards of quality management to be applied in the branches at levels in the organization”.
The feature of Toyota Corporation undergoing the quality process is transparent. A limited
interdepartmental hurdle exists in Toyota's excellent supplier relation and customer, free time
that can be spent on training, as well as recognition of the quality, is realized using offering a
3
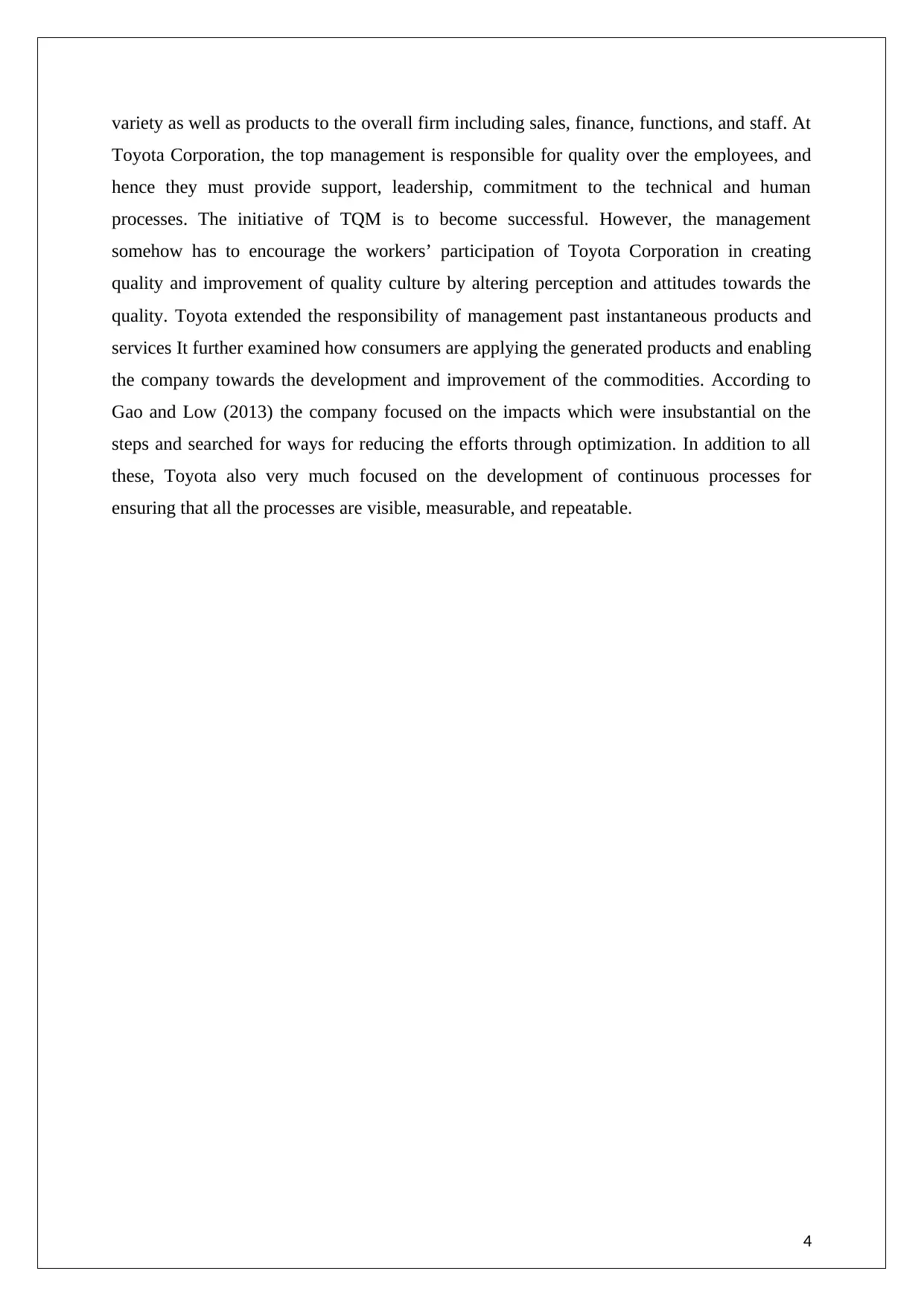
variety as well as products to the overall firm including sales, finance, functions, and staff. At
Toyota Corporation, the top management is responsible for quality over the employees, and
hence they must provide support, leadership, commitment to the technical and human
processes. The initiative of TQM is to become successful. However, the management
somehow has to encourage the workers’ participation of Toyota Corporation in creating
quality and improvement of quality culture by altering perception and attitudes towards the
quality. Toyota extended the responsibility of management past instantaneous products and
services It further examined how consumers are applying the generated products and enabling
the company towards the development and improvement of the commodities. According to
Gao and Low (2013) the company focused on the impacts which were insubstantial on the
steps and searched for ways for reducing the efforts through optimization. In addition to all
these, Toyota also very much focused on the development of continuous processes for
ensuring that all the processes are visible, measurable, and repeatable.
4
Toyota Corporation, the top management is responsible for quality over the employees, and
hence they must provide support, leadership, commitment to the technical and human
processes. The initiative of TQM is to become successful. However, the management
somehow has to encourage the workers’ participation of Toyota Corporation in creating
quality and improvement of quality culture by altering perception and attitudes towards the
quality. Toyota extended the responsibility of management past instantaneous products and
services It further examined how consumers are applying the generated products and enabling
the company towards the development and improvement of the commodities. According to
Gao and Low (2013) the company focused on the impacts which were insubstantial on the
steps and searched for ways for reducing the efforts through optimization. In addition to all
these, Toyota also very much focused on the development of continuous processes for
ensuring that all the processes are visible, measurable, and repeatable.
4
Secure Best Marks with AI Grader
Need help grading? Try our AI Grader for instant feedback on your assignments.
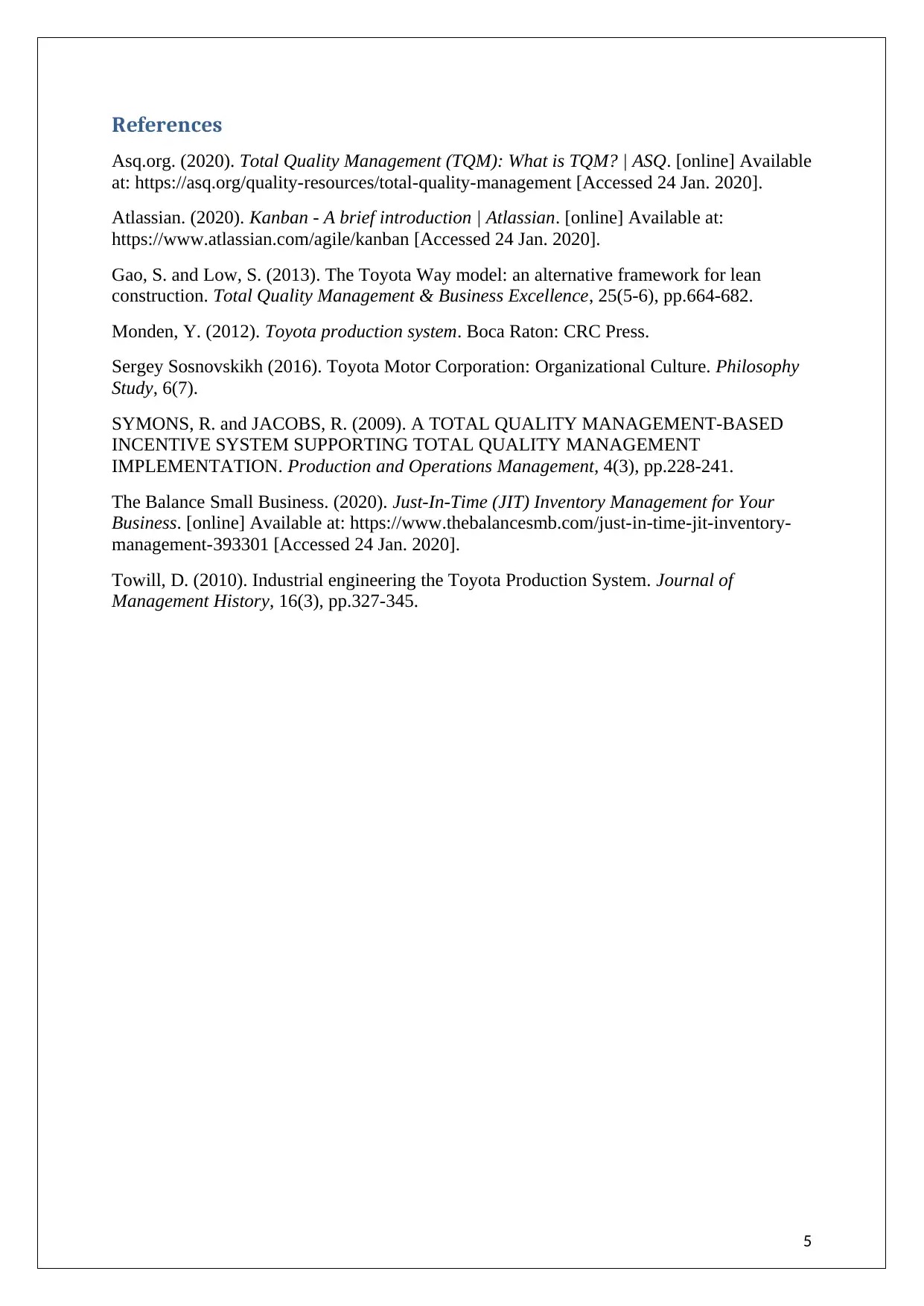
References
Asq.org. (2020). Total Quality Management (TQM): What is TQM? | ASQ. [online] Available
at: https://asq.org/quality-resources/total-quality-management [Accessed 24 Jan. 2020].
Atlassian. (2020). Kanban - A brief introduction | Atlassian. [online] Available at:
https://www.atlassian.com/agile/kanban [Accessed 24 Jan. 2020].
Gao, S. and Low, S. (2013). The Toyota Way model: an alternative framework for lean
construction. Total Quality Management & Business Excellence, 25(5-6), pp.664-682.
Monden, Y. (2012). Toyota production system. Boca Raton: CRC Press.
Sergey Sosnovskikh (2016). Toyota Motor Corporation: Organizational Culture. Philosophy
Study, 6(7).
SYMONS, R. and JACOBS, R. (2009). A TOTAL QUALITY MANAGEMENT-BASED
INCENTIVE SYSTEM SUPPORTING TOTAL QUALITY MANAGEMENT
IMPLEMENTATION. Production and Operations Management, 4(3), pp.228-241.
The Balance Small Business. (2020). Just-In-Time (JIT) Inventory Management for Your
Business. [online] Available at: https://www.thebalancesmb.com/just-in-time-jit-inventory-
management-393301 [Accessed 24 Jan. 2020].
Towill, D. (2010). Industrial engineering the Toyota Production System. Journal of
Management History, 16(3), pp.327-345.
5
Asq.org. (2020). Total Quality Management (TQM): What is TQM? | ASQ. [online] Available
at: https://asq.org/quality-resources/total-quality-management [Accessed 24 Jan. 2020].
Atlassian. (2020). Kanban - A brief introduction | Atlassian. [online] Available at:
https://www.atlassian.com/agile/kanban [Accessed 24 Jan. 2020].
Gao, S. and Low, S. (2013). The Toyota Way model: an alternative framework for lean
construction. Total Quality Management & Business Excellence, 25(5-6), pp.664-682.
Monden, Y. (2012). Toyota production system. Boca Raton: CRC Press.
Sergey Sosnovskikh (2016). Toyota Motor Corporation: Organizational Culture. Philosophy
Study, 6(7).
SYMONS, R. and JACOBS, R. (2009). A TOTAL QUALITY MANAGEMENT-BASED
INCENTIVE SYSTEM SUPPORTING TOTAL QUALITY MANAGEMENT
IMPLEMENTATION. Production and Operations Management, 4(3), pp.228-241.
The Balance Small Business. (2020). Just-In-Time (JIT) Inventory Management for Your
Business. [online] Available at: https://www.thebalancesmb.com/just-in-time-jit-inventory-
management-393301 [Accessed 24 Jan. 2020].
Towill, D. (2010). Industrial engineering the Toyota Production System. Journal of
Management History, 16(3), pp.327-345.
5
1 out of 5
Related Documents
![[object Object]](/_next/image/?url=%2F_next%2Fstatic%2Fmedia%2Flogo.6d15ce61.png&w=640&q=75)
Your All-in-One AI-Powered Toolkit for Academic Success.
+13062052269
info@desklib.com
Available 24*7 on WhatsApp / Email
Unlock your academic potential
© 2024 | Zucol Services PVT LTD | All rights reserved.