Effectiveness of Kanban System in Toyota Motor Co.
VerifiedAdded on 2023/01/13
|6
|1395
|65
AI Summary
This report evaluates the effectiveness of the Kanban system in Toyota Motor Co. and its impact on production and waste reduction. It discusses key elements of the system and provides evidence of its success. The report also highlights the importance of Just-in-Time and Total Quality Management principles in achieving uninterrupted and effective manufacturing. Overall, the report concludes that the Kanban system is highly effective in producing quality products and reducing costs.
Contribute Materials
Your contribution can guide someone’s learning journey. Share your
documents today.
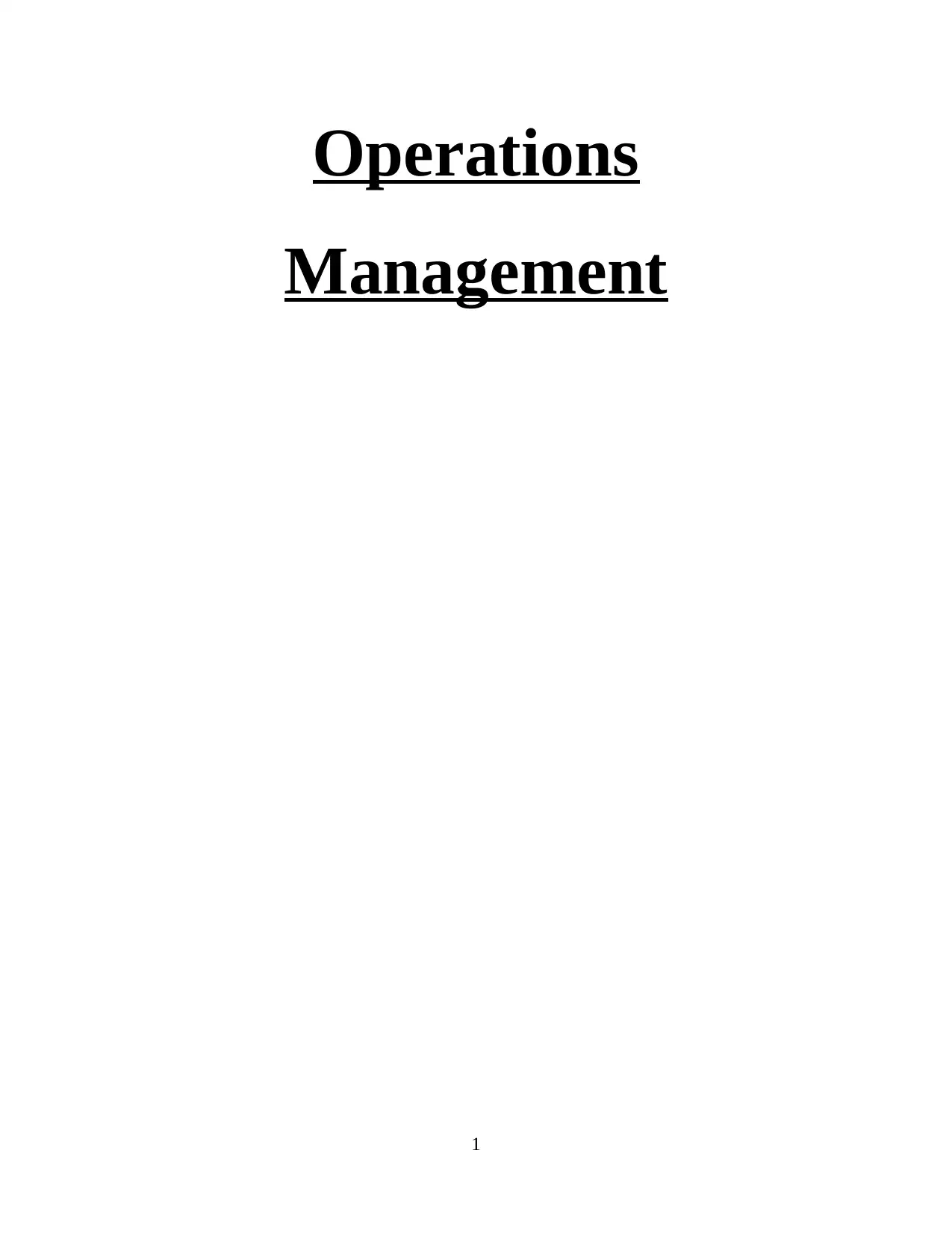
Operations
Management
1
Management
1
Secure Best Marks with AI Grader
Need help grading? Try our AI Grader for instant feedback on your assignments.
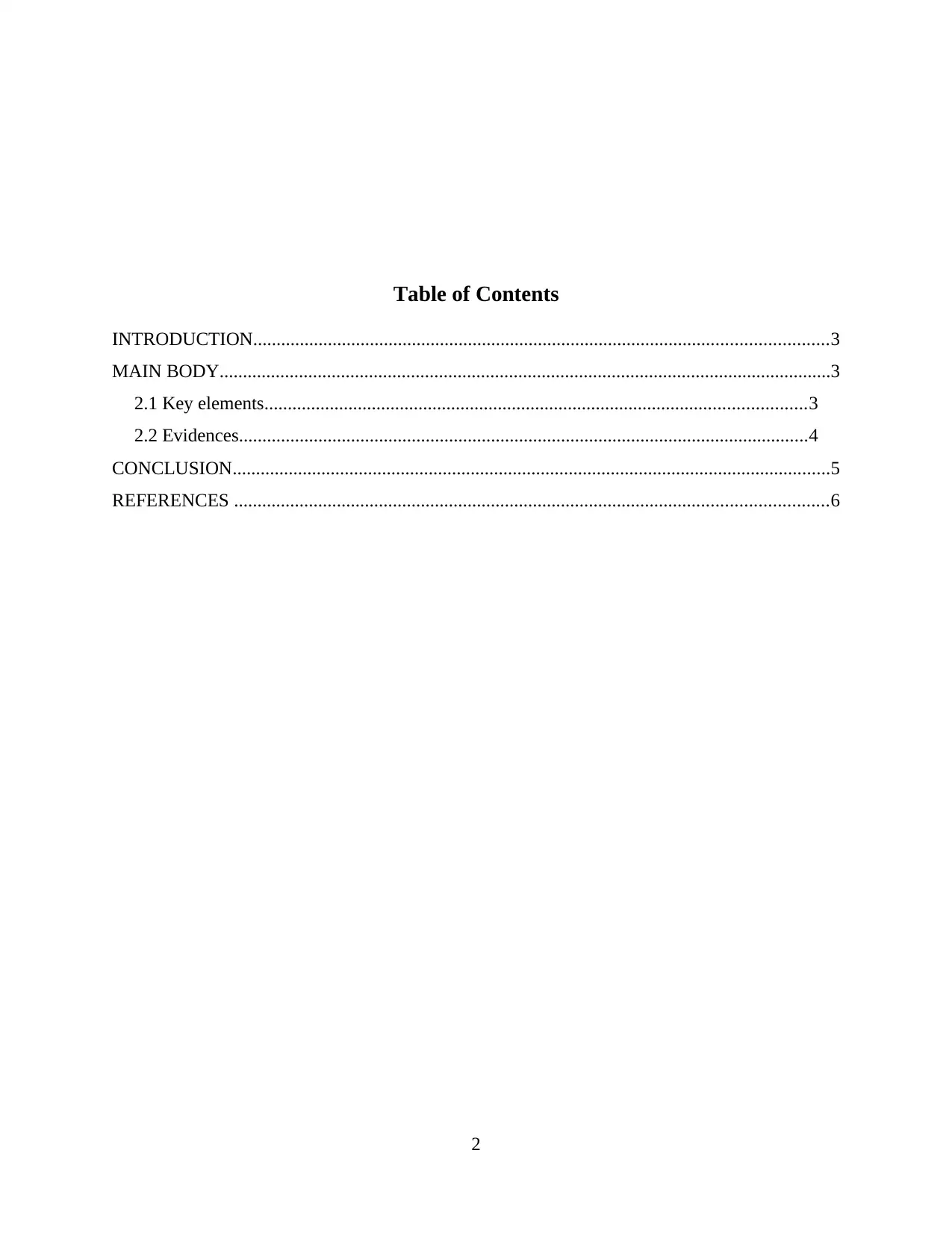
Table of Contents
INTRODUCTION...........................................................................................................................3
MAIN BODY...................................................................................................................................3
2.1 Key elements....................................................................................................................3
2.2 Evidences..........................................................................................................................4
CONCLUSION................................................................................................................................5
REFERENCES ...............................................................................................................................6
2
INTRODUCTION...........................................................................................................................3
MAIN BODY...................................................................................................................................3
2.1 Key elements....................................................................................................................3
2.2 Evidences..........................................................................................................................4
CONCLUSION................................................................................................................................5
REFERENCES ...............................................................................................................................6
2
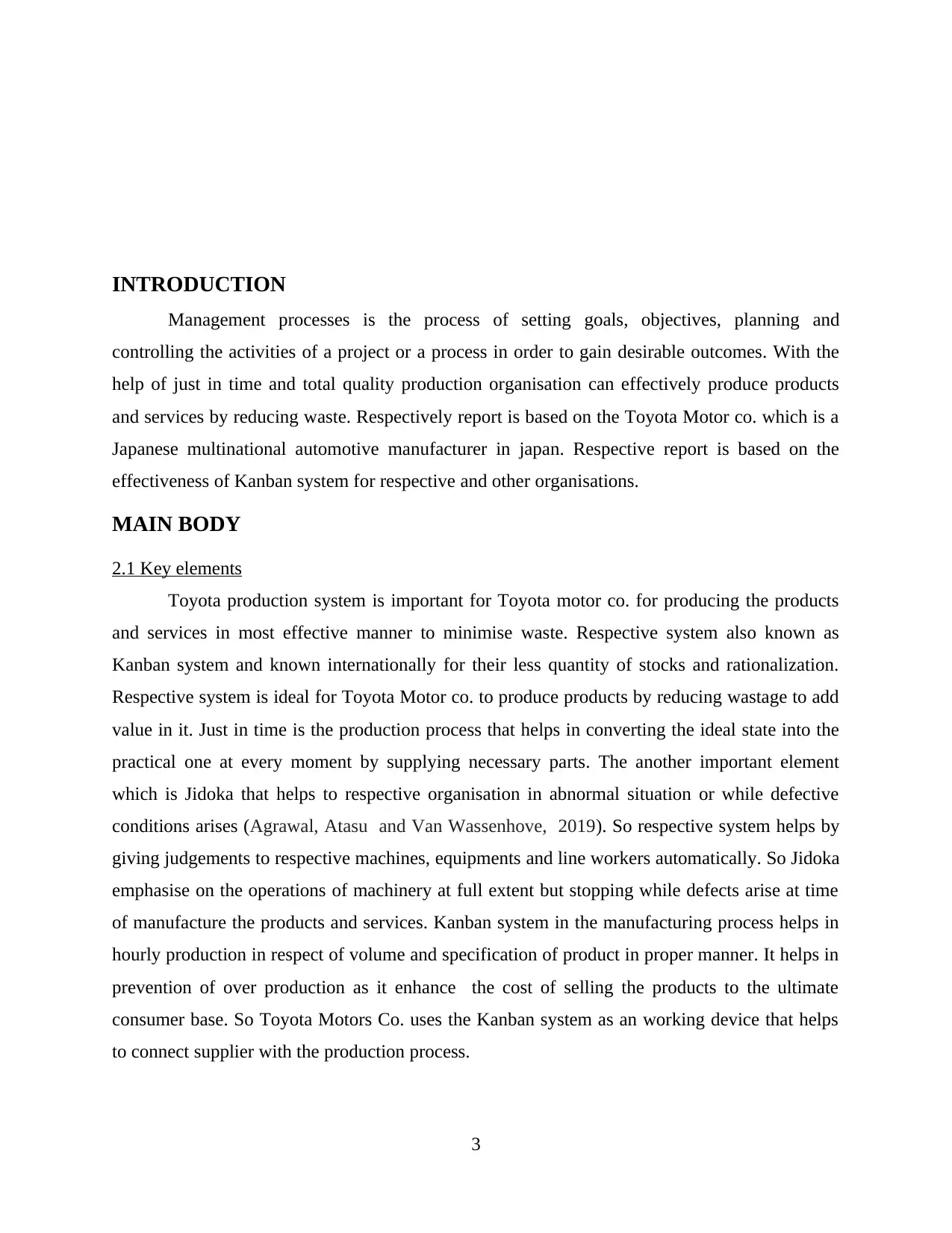
INTRODUCTION
Management processes is the process of setting goals, objectives, planning and
controlling the activities of a project or a process in order to gain desirable outcomes. With the
help of just in time and total quality production organisation can effectively produce products
and services by reducing waste. Respectively report is based on the Toyota Motor co. which is a
Japanese multinational automotive manufacturer in japan. Respective report is based on the
effectiveness of Kanban system for respective and other organisations.
MAIN BODY
2.1 Key elements
Toyota production system is important for Toyota motor co. for producing the products
and services in most effective manner to minimise waste. Respective system also known as
Kanban system and known internationally for their less quantity of stocks and rationalization.
Respective system is ideal for Toyota Motor co. to produce products by reducing wastage to add
value in it. Just in time is the production process that helps in converting the ideal state into the
practical one at every moment by supplying necessary parts. The another important element
which is Jidoka that helps to respective organisation in abnormal situation or while defective
conditions arises (Agrawal, Atasu and Van Wassenhove, 2019). So respective system helps by
giving judgements to respective machines, equipments and line workers automatically. So Jidoka
emphasise on the operations of machinery at full extent but stopping while defects arise at time
of manufacture the products and services. Kanban system in the manufacturing process helps in
hourly production in respect of volume and specification of product in proper manner. It helps in
prevention of over production as it enhance the cost of selling the products to the ultimate
consumer base. So Toyota Motors Co. uses the Kanban system as an working device that helps
to connect supplier with the production process.
3
Management processes is the process of setting goals, objectives, planning and
controlling the activities of a project or a process in order to gain desirable outcomes. With the
help of just in time and total quality production organisation can effectively produce products
and services by reducing waste. Respectively report is based on the Toyota Motor co. which is a
Japanese multinational automotive manufacturer in japan. Respective report is based on the
effectiveness of Kanban system for respective and other organisations.
MAIN BODY
2.1 Key elements
Toyota production system is important for Toyota motor co. for producing the products
and services in most effective manner to minimise waste. Respective system also known as
Kanban system and known internationally for their less quantity of stocks and rationalization.
Respective system is ideal for Toyota Motor co. to produce products by reducing wastage to add
value in it. Just in time is the production process that helps in converting the ideal state into the
practical one at every moment by supplying necessary parts. The another important element
which is Jidoka that helps to respective organisation in abnormal situation or while defective
conditions arises (Agrawal, Atasu and Van Wassenhove, 2019). So respective system helps by
giving judgements to respective machines, equipments and line workers automatically. So Jidoka
emphasise on the operations of machinery at full extent but stopping while defects arise at time
of manufacture the products and services. Kanban system in the manufacturing process helps in
hourly production in respect of volume and specification of product in proper manner. It helps in
prevention of over production as it enhance the cost of selling the products to the ultimate
consumer base. So Toyota Motors Co. uses the Kanban system as an working device that helps
to connect supplier with the production process.
3
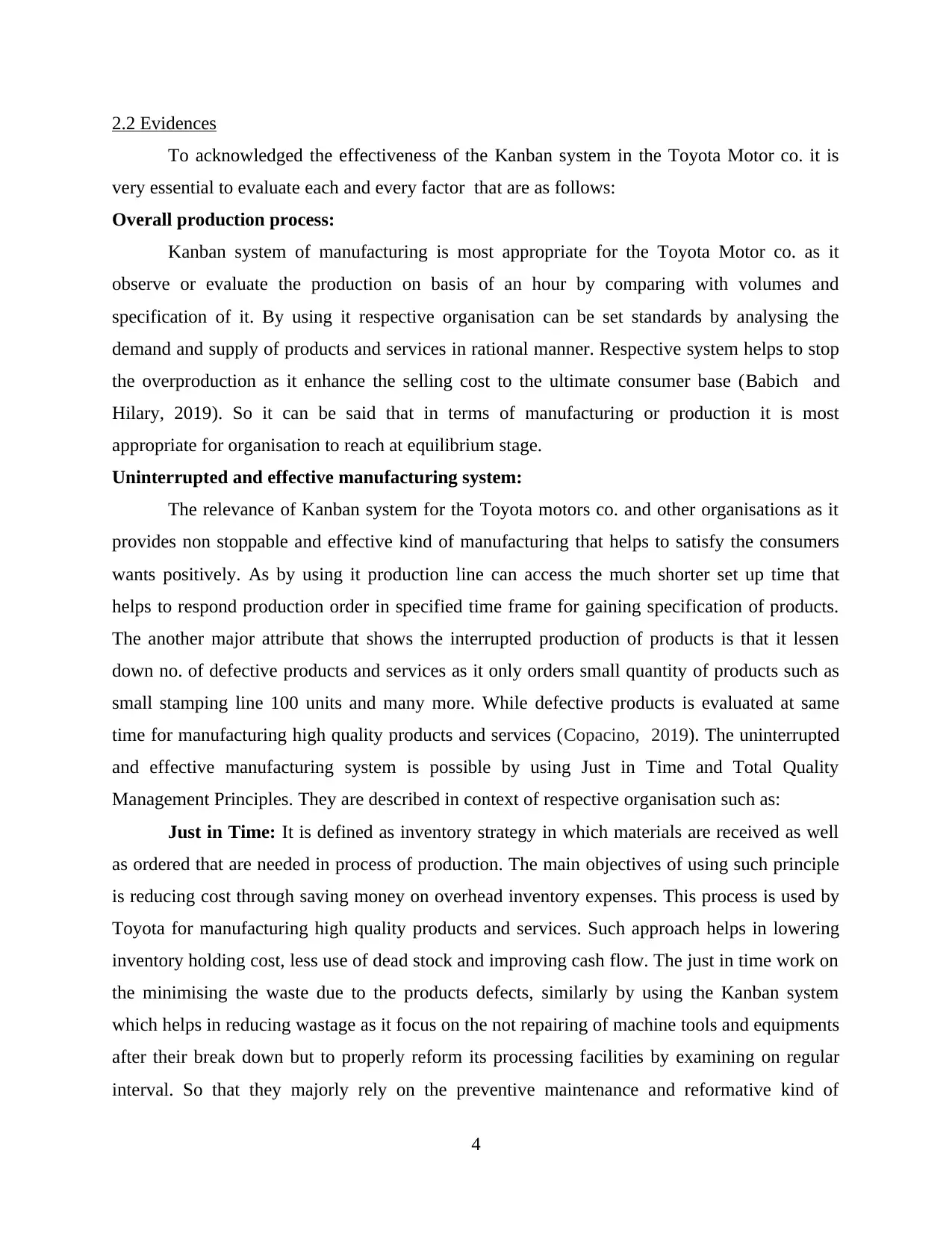
2.2 Evidences
To acknowledged the effectiveness of the Kanban system in the Toyota Motor co. it is
very essential to evaluate each and every factor that are as follows:
Overall production process:
Kanban system of manufacturing is most appropriate for the Toyota Motor co. as it
observe or evaluate the production on basis of an hour by comparing with volumes and
specification of it. By using it respective organisation can be set standards by analysing the
demand and supply of products and services in rational manner. Respective system helps to stop
the overproduction as it enhance the selling cost to the ultimate consumer base (Babich and
Hilary, 2019). So it can be said that in terms of manufacturing or production it is most
appropriate for organisation to reach at equilibrium stage.
Uninterrupted and effective manufacturing system:
The relevance of Kanban system for the Toyota motors co. and other organisations as it
provides non stoppable and effective kind of manufacturing that helps to satisfy the consumers
wants positively. As by using it production line can access the much shorter set up time that
helps to respond production order in specified time frame for gaining specification of products.
The another major attribute that shows the interrupted production of products is that it lessen
down no. of defective products and services as it only orders small quantity of products such as
small stamping line 100 units and many more. While defective products is evaluated at same
time for manufacturing high quality products and services (Copacino, 2019). The uninterrupted
and effective manufacturing system is possible by using Just in Time and Total Quality
Management Principles. They are described in context of respective organisation such as:
Just in Time: It is defined as inventory strategy in which materials are received as well
as ordered that are needed in process of production. The main objectives of using such principle
is reducing cost through saving money on overhead inventory expenses. This process is used by
Toyota for manufacturing high quality products and services. Such approach helps in lowering
inventory holding cost, less use of dead stock and improving cash flow. The just in time work on
the minimising the waste due to the products defects, similarly by using the Kanban system
which helps in reducing wastage as it focus on the not repairing of machine tools and equipments
after their break down but to properly reform its processing facilities by examining on regular
interval. So that they majorly rely on the preventive maintenance and reformative kind of
4
To acknowledged the effectiveness of the Kanban system in the Toyota Motor co. it is
very essential to evaluate each and every factor that are as follows:
Overall production process:
Kanban system of manufacturing is most appropriate for the Toyota Motor co. as it
observe or evaluate the production on basis of an hour by comparing with volumes and
specification of it. By using it respective organisation can be set standards by analysing the
demand and supply of products and services in rational manner. Respective system helps to stop
the overproduction as it enhance the selling cost to the ultimate consumer base (Babich and
Hilary, 2019). So it can be said that in terms of manufacturing or production it is most
appropriate for organisation to reach at equilibrium stage.
Uninterrupted and effective manufacturing system:
The relevance of Kanban system for the Toyota motors co. and other organisations as it
provides non stoppable and effective kind of manufacturing that helps to satisfy the consumers
wants positively. As by using it production line can access the much shorter set up time that
helps to respond production order in specified time frame for gaining specification of products.
The another major attribute that shows the interrupted production of products is that it lessen
down no. of defective products and services as it only orders small quantity of products such as
small stamping line 100 units and many more. While defective products is evaluated at same
time for manufacturing high quality products and services (Copacino, 2019). The uninterrupted
and effective manufacturing system is possible by using Just in Time and Total Quality
Management Principles. They are described in context of respective organisation such as:
Just in Time: It is defined as inventory strategy in which materials are received as well
as ordered that are needed in process of production. The main objectives of using such principle
is reducing cost through saving money on overhead inventory expenses. This process is used by
Toyota for manufacturing high quality products and services. Such approach helps in lowering
inventory holding cost, less use of dead stock and improving cash flow. The just in time work on
the minimising the waste due to the products defects, similarly by using the Kanban system
which helps in reducing wastage as it focus on the not repairing of machine tools and equipments
after their break down but to properly reform its processing facilities by examining on regular
interval. So that they majorly rely on the preventive maintenance and reformative kind of
4
Secure Best Marks with AI Grader
Need help grading? Try our AI Grader for instant feedback on your assignments.
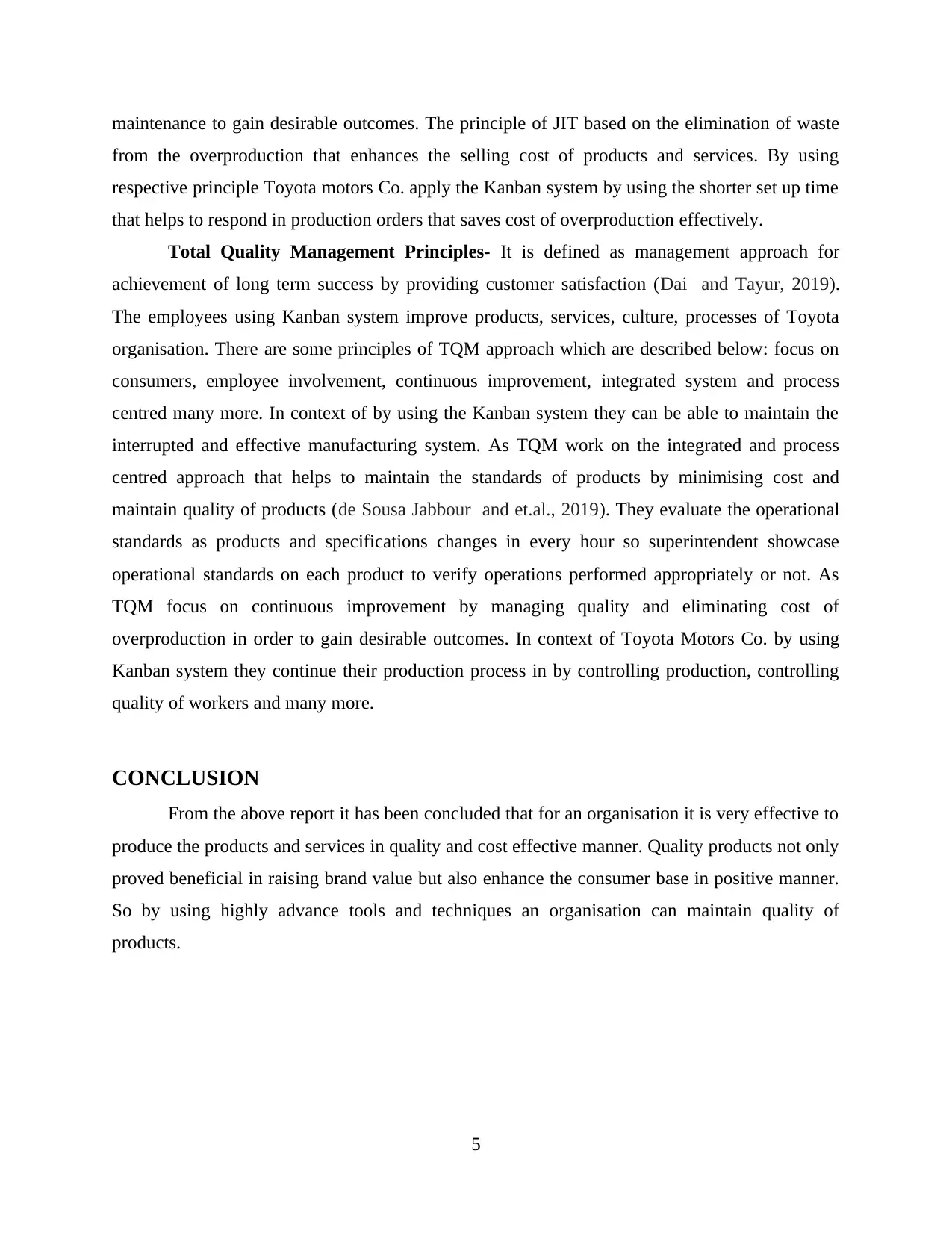
maintenance to gain desirable outcomes. The principle of JIT based on the elimination of waste
from the overproduction that enhances the selling cost of products and services. By using
respective principle Toyota motors Co. apply the Kanban system by using the shorter set up time
that helps to respond in production orders that saves cost of overproduction effectively.
Total Quality Management Principles- It is defined as management approach for
achievement of long term success by providing customer satisfaction (Dai and Tayur, 2019).
The employees using Kanban system improve products, services, culture, processes of Toyota
organisation. There are some principles of TQM approach which are described below: focus on
consumers, employee involvement, continuous improvement, integrated system and process
centred many more. In context of by using the Kanban system they can be able to maintain the
interrupted and effective manufacturing system. As TQM work on the integrated and process
centred approach that helps to maintain the standards of products by minimising cost and
maintain quality of products (de Sousa Jabbour and et.al., 2019). They evaluate the operational
standards as products and specifications changes in every hour so superintendent showcase
operational standards on each product to verify operations performed appropriately or not. As
TQM focus on continuous improvement by managing quality and eliminating cost of
overproduction in order to gain desirable outcomes. In context of Toyota Motors Co. by using
Kanban system they continue their production process in by controlling production, controlling
quality of workers and many more.
CONCLUSION
From the above report it has been concluded that for an organisation it is very effective to
produce the products and services in quality and cost effective manner. Quality products not only
proved beneficial in raising brand value but also enhance the consumer base in positive manner.
So by using highly advance tools and techniques an organisation can maintain quality of
products.
5
from the overproduction that enhances the selling cost of products and services. By using
respective principle Toyota motors Co. apply the Kanban system by using the shorter set up time
that helps to respond in production orders that saves cost of overproduction effectively.
Total Quality Management Principles- It is defined as management approach for
achievement of long term success by providing customer satisfaction (Dai and Tayur, 2019).
The employees using Kanban system improve products, services, culture, processes of Toyota
organisation. There are some principles of TQM approach which are described below: focus on
consumers, employee involvement, continuous improvement, integrated system and process
centred many more. In context of by using the Kanban system they can be able to maintain the
interrupted and effective manufacturing system. As TQM work on the integrated and process
centred approach that helps to maintain the standards of products by minimising cost and
maintain quality of products (de Sousa Jabbour and et.al., 2019). They evaluate the operational
standards as products and specifications changes in every hour so superintendent showcase
operational standards on each product to verify operations performed appropriately or not. As
TQM focus on continuous improvement by managing quality and eliminating cost of
overproduction in order to gain desirable outcomes. In context of Toyota Motors Co. by using
Kanban system they continue their production process in by controlling production, controlling
quality of workers and many more.
CONCLUSION
From the above report it has been concluded that for an organisation it is very effective to
produce the products and services in quality and cost effective manner. Quality products not only
proved beneficial in raising brand value but also enhance the consumer base in positive manner.
So by using highly advance tools and techniques an organisation can maintain quality of
products.
5
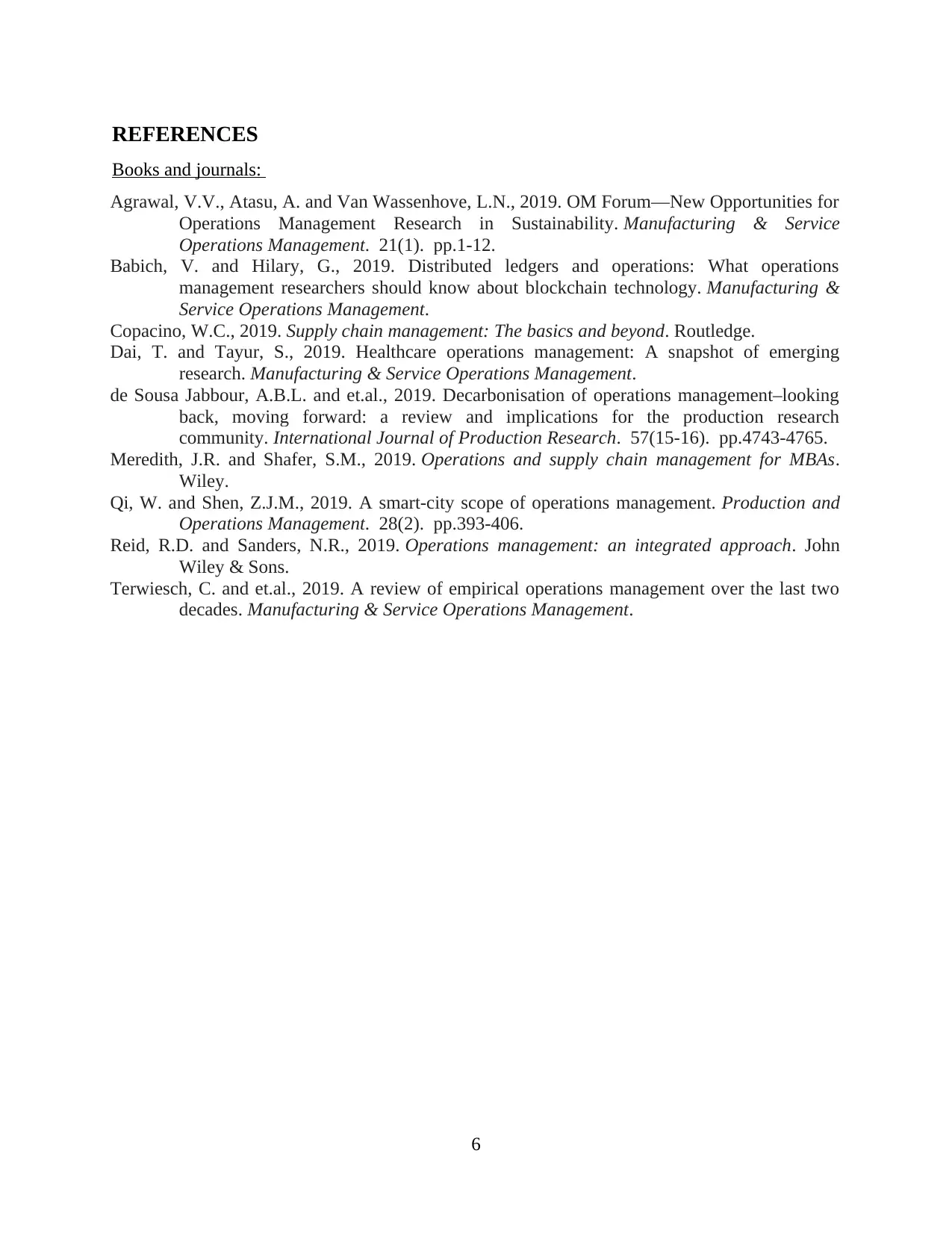
REFERENCES
Books and journals:
Agrawal, V.V., Atasu, A. and Van Wassenhove, L.N., 2019. OM Forum—New Opportunities for
Operations Management Research in Sustainability. Manufacturing & Service
Operations Management. 21(1). pp.1-12.
Babich, V. and Hilary, G., 2019. Distributed ledgers and operations: What operations
management researchers should know about blockchain technology. Manufacturing &
Service Operations Management.
Copacino, W.C., 2019. Supply chain management: The basics and beyond. Routledge.
Dai, T. and Tayur, S., 2019. Healthcare operations management: A snapshot of emerging
research. Manufacturing & Service Operations Management.
de Sousa Jabbour, A.B.L. and et.al., 2019. Decarbonisation of operations management–looking
back, moving forward: a review and implications for the production research
community. International Journal of Production Research. 57(15-16). pp.4743-4765.
Meredith, J.R. and Shafer, S.M., 2019. Operations and supply chain management for MBAs.
Wiley.
Qi, W. and Shen, Z.J.M., 2019. A smart‐city scope of operations management. Production and
Operations Management. 28(2). pp.393-406.
Reid, R.D. and Sanders, N.R., 2019. Operations management: an integrated approach. John
Wiley & Sons.
Terwiesch, C. and et.al., 2019. A review of empirical operations management over the last two
decades. Manufacturing & Service Operations Management.
6
Books and journals:
Agrawal, V.V., Atasu, A. and Van Wassenhove, L.N., 2019. OM Forum—New Opportunities for
Operations Management Research in Sustainability. Manufacturing & Service
Operations Management. 21(1). pp.1-12.
Babich, V. and Hilary, G., 2019. Distributed ledgers and operations: What operations
management researchers should know about blockchain technology. Manufacturing &
Service Operations Management.
Copacino, W.C., 2019. Supply chain management: The basics and beyond. Routledge.
Dai, T. and Tayur, S., 2019. Healthcare operations management: A snapshot of emerging
research. Manufacturing & Service Operations Management.
de Sousa Jabbour, A.B.L. and et.al., 2019. Decarbonisation of operations management–looking
back, moving forward: a review and implications for the production research
community. International Journal of Production Research. 57(15-16). pp.4743-4765.
Meredith, J.R. and Shafer, S.M., 2019. Operations and supply chain management for MBAs.
Wiley.
Qi, W. and Shen, Z.J.M., 2019. A smart‐city scope of operations management. Production and
Operations Management. 28(2). pp.393-406.
Reid, R.D. and Sanders, N.R., 2019. Operations management: an integrated approach. John
Wiley & Sons.
Terwiesch, C. and et.al., 2019. A review of empirical operations management over the last two
decades. Manufacturing & Service Operations Management.
6
1 out of 6
Related Documents
![[object Object]](/_next/image/?url=%2F_next%2Fstatic%2Fmedia%2Flogo.6d15ce61.png&w=640&q=75)
Your All-in-One AI-Powered Toolkit for Academic Success.
+13062052269
info@desklib.com
Available 24*7 on WhatsApp / Email
Unlock your academic potential
© 2024 | Zucol Services PVT LTD | All rights reserved.