Literature Review on Supply Chain Management
VerifiedAdded on 2020/10/22
|14
|3914
|244
AI Summary
This assignment requires a thorough review of 11 literature pieces related to supply chain management, covering topics such as cost management models, revenue-oriented green supply chain network design, and mechanism design in a supply chain with ambiguity in private information. The sources include articles from peer-reviewed journals, books, and conference proceedings from reputable authors and institutions.
Contribute Materials
Your contribution can guide someone’s learning journey. Share your
documents today.
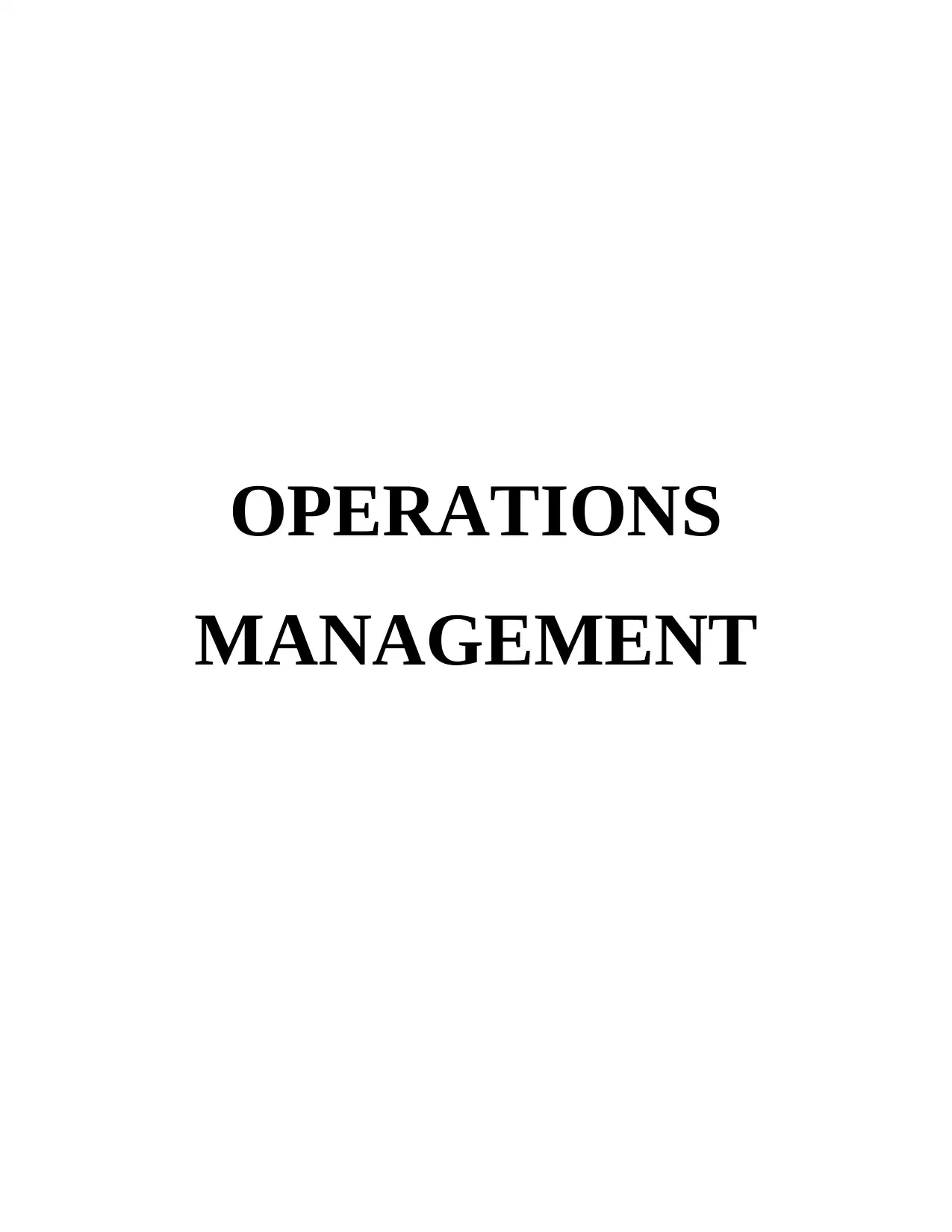
OPERATIONS
MANAGEMENT
MANAGEMENT
Secure Best Marks with AI Grader
Need help grading? Try our AI Grader for instant feedback on your assignments.
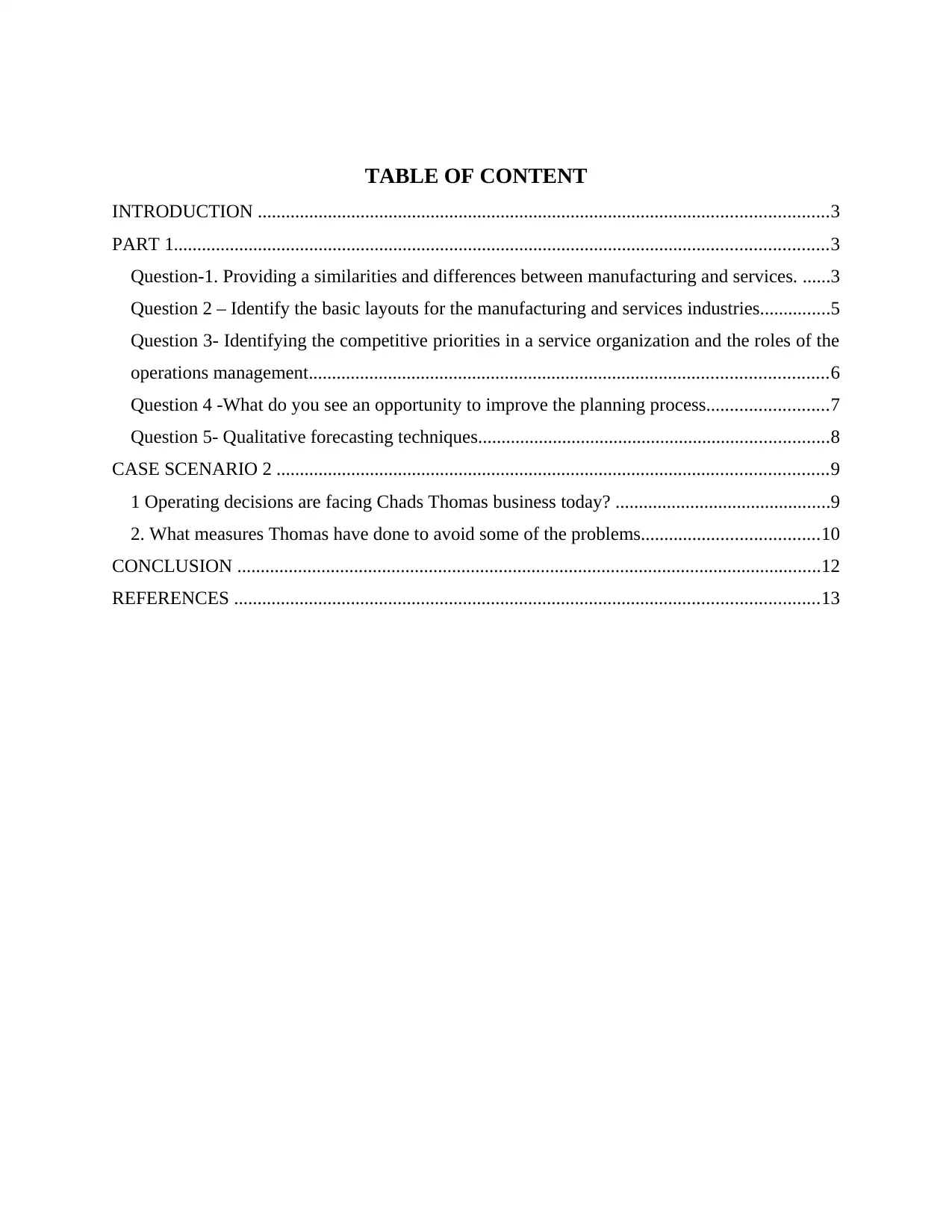
TABLE OF CONTENT
INTRODUCTION ..........................................................................................................................3
PART 1............................................................................................................................................3
Question-1. Providing a similarities and differences between manufacturing and services. ......3
Question 2 – Identify the basic layouts for the manufacturing and services industries...............5
Question 3- Identifying the competitive priorities in a service organization and the roles of the
operations management...............................................................................................................6
Question 4 -What do you see an opportunity to improve the planning process..........................7
Question 5- Qualitative forecasting techniques...........................................................................8
CASE SCENARIO 2 ......................................................................................................................9
1 Operating decisions are facing Chads Thomas business today? ..............................................9
2. What measures Thomas have done to avoid some of the problems......................................10
CONCLUSION .............................................................................................................................12
REFERENCES .............................................................................................................................13
INTRODUCTION ..........................................................................................................................3
PART 1............................................................................................................................................3
Question-1. Providing a similarities and differences between manufacturing and services. ......3
Question 2 – Identify the basic layouts for the manufacturing and services industries...............5
Question 3- Identifying the competitive priorities in a service organization and the roles of the
operations management...............................................................................................................6
Question 4 -What do you see an opportunity to improve the planning process..........................7
Question 5- Qualitative forecasting techniques...........................................................................8
CASE SCENARIO 2 ......................................................................................................................9
1 Operating decisions are facing Chads Thomas business today? ..............................................9
2. What measures Thomas have done to avoid some of the problems......................................10
CONCLUSION .............................................................................................................................12
REFERENCES .............................................................................................................................13
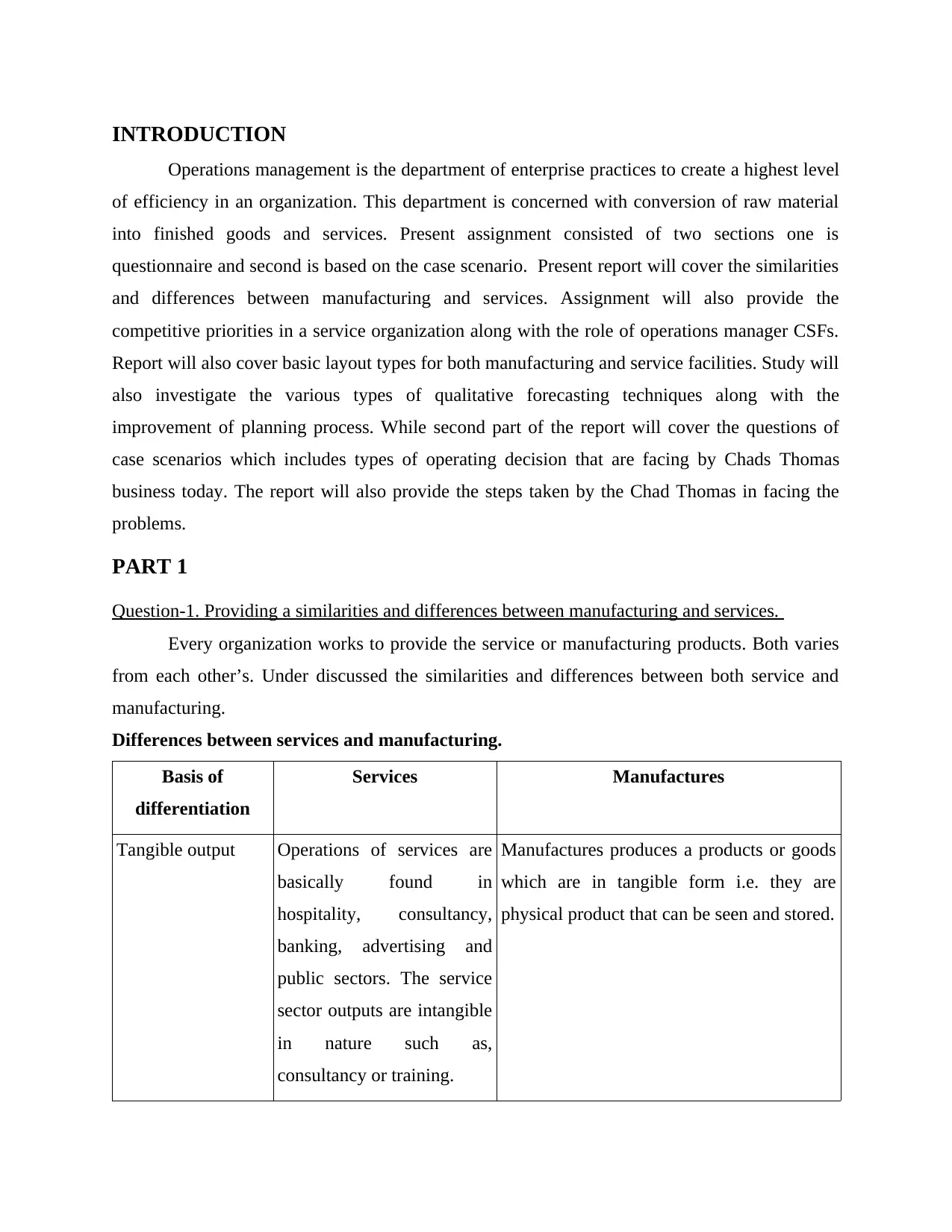
INTRODUCTION
Operations management is the department of enterprise practices to create a highest level
of efficiency in an organization. This department is concerned with conversion of raw material
into finished goods and services. Present assignment consisted of two sections one is
questionnaire and second is based on the case scenario. Present report will cover the similarities
and differences between manufacturing and services. Assignment will also provide the
competitive priorities in a service organization along with the role of operations manager CSFs.
Report will also cover basic layout types for both manufacturing and service facilities. Study will
also investigate the various types of qualitative forecasting techniques along with the
improvement of planning process. While second part of the report will cover the questions of
case scenarios which includes types of operating decision that are facing by Chads Thomas
business today. The report will also provide the steps taken by the Chad Thomas in facing the
problems.
PART 1
Question-1. Providing a similarities and differences between manufacturing and services.
Every organization works to provide the service or manufacturing products. Both varies
from each other’s. Under discussed the similarities and differences between both service and
manufacturing.
Differences between services and manufacturing.
Basis of
differentiation
Services Manufactures
Tangible output Operations of services are
basically found in
hospitality, consultancy,
banking, advertising and
public sectors. The service
sector outputs are intangible
in nature such as,
consultancy or training.
Manufactures produces a products or goods
which are in tangible form i.e. they are
physical product that can be seen and stored.
Operations management is the department of enterprise practices to create a highest level
of efficiency in an organization. This department is concerned with conversion of raw material
into finished goods and services. Present assignment consisted of two sections one is
questionnaire and second is based on the case scenario. Present report will cover the similarities
and differences between manufacturing and services. Assignment will also provide the
competitive priorities in a service organization along with the role of operations manager CSFs.
Report will also cover basic layout types for both manufacturing and service facilities. Study will
also investigate the various types of qualitative forecasting techniques along with the
improvement of planning process. While second part of the report will cover the questions of
case scenarios which includes types of operating decision that are facing by Chads Thomas
business today. The report will also provide the steps taken by the Chad Thomas in facing the
problems.
PART 1
Question-1. Providing a similarities and differences between manufacturing and services.
Every organization works to provide the service or manufacturing products. Both varies
from each other’s. Under discussed the similarities and differences between both service and
manufacturing.
Differences between services and manufacturing.
Basis of
differentiation
Services Manufactures
Tangible output Operations of services are
basically found in
hospitality, consultancy,
banking, advertising and
public sectors. The service
sector outputs are intangible
in nature such as,
consultancy or training.
Manufactures produces a products or goods
which are in tangible form i.e. they are
physical product that can be seen and stored.
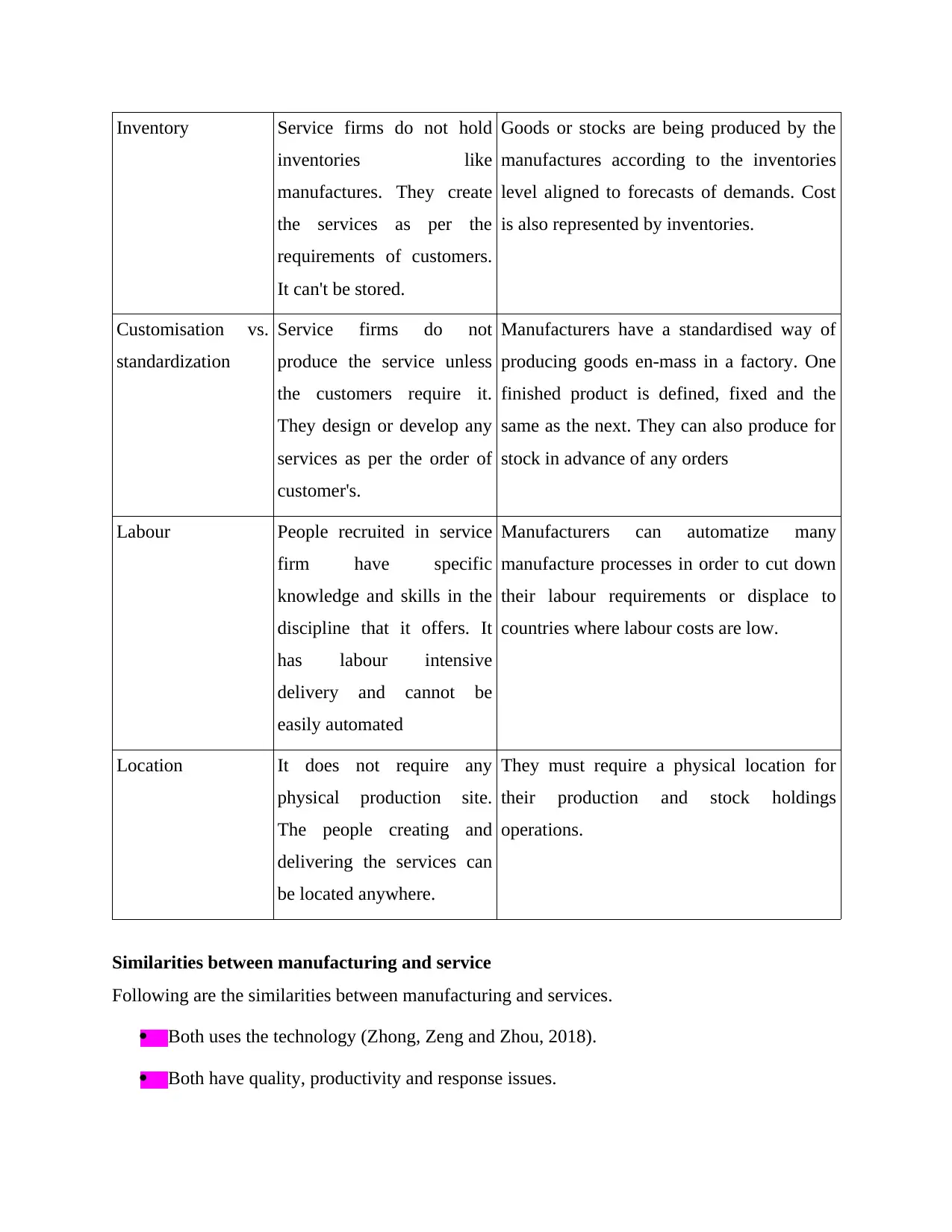
Inventory Service firms do not hold
inventories like
manufactures. They create
the services as per the
requirements of customers.
It can't be stored.
Goods or stocks are being produced by the
manufactures according to the inventories
level aligned to forecasts of demands. Cost
is also represented by inventories.
Customisation vs.
standardization
Service firms do not
produce the service unless
the customers require it.
They design or develop any
services as per the order of
customer's.
Manufacturers have a standardised way of
producing goods en-mass in a factory. One
finished product is defined, fixed and the
same as the next. They can also produce for
stock in advance of any orders
Labour People recruited in service
firm have specific
knowledge and skills in the
discipline that it offers. It
has labour intensive
delivery and cannot be
easily automated
Manufacturers can automatize many
manufacture processes in order to cut down
their labour requirements or displace to
countries where labour costs are low.
Location It does not require any
physical production site.
The people creating and
delivering the services can
be located anywhere.
They must require a physical location for
their production and stock holdings
operations.
Similarities between manufacturing and service
Following are the similarities between manufacturing and services.
Both uses the technology (Zhong, Zeng and Zhou, 2018).
Both have quality, productivity and response issues.
inventories like
manufactures. They create
the services as per the
requirements of customers.
It can't be stored.
Goods or stocks are being produced by the
manufactures according to the inventories
level aligned to forecasts of demands. Cost
is also represented by inventories.
Customisation vs.
standardization
Service firms do not
produce the service unless
the customers require it.
They design or develop any
services as per the order of
customer's.
Manufacturers have a standardised way of
producing goods en-mass in a factory. One
finished product is defined, fixed and the
same as the next. They can also produce for
stock in advance of any orders
Labour People recruited in service
firm have specific
knowledge and skills in the
discipline that it offers. It
has labour intensive
delivery and cannot be
easily automated
Manufacturers can automatize many
manufacture processes in order to cut down
their labour requirements or displace to
countries where labour costs are low.
Location It does not require any
physical production site.
The people creating and
delivering the services can
be located anywhere.
They must require a physical location for
their production and stock holdings
operations.
Similarities between manufacturing and service
Following are the similarities between manufacturing and services.
Both uses the technology (Zhong, Zeng and Zhou, 2018).
Both have quality, productivity and response issues.
Secure Best Marks with AI Grader
Need help grading? Try our AI Grader for instant feedback on your assignments.
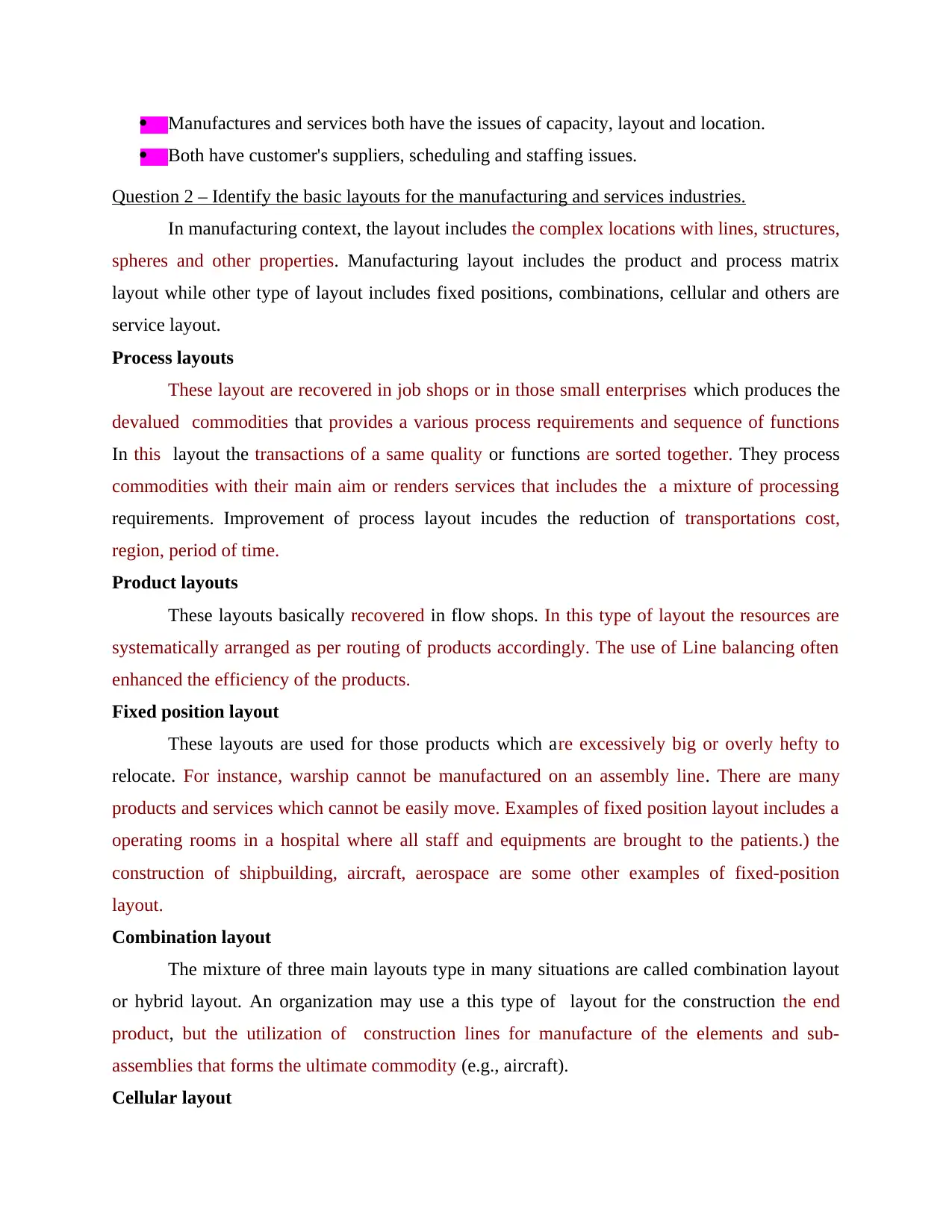
Manufactures and services both have the issues of capacity, layout and location.
Both have customer's suppliers, scheduling and staffing issues.
Question 2 – Identify the basic layouts for the manufacturing and services industries.
In manufacturing context, the layout includes the complex locations with lines, structures,
spheres and other properties. Manufacturing layout includes the product and process matrix
layout while other type of layout includes fixed positions, combinations, cellular and others are
service layout.
Process layouts
These layout are recovered in job shops or in those small enterprises which produces the
devalued commodities that provides a various process requirements and sequence of functions
In this layout the transactions of a same quality or functions are sorted together. They process
commodities with their main aim or renders services that includes the a mixture of processing
requirements. Improvement of process layout incudes the reduction of transportations cost,
region, period of time.
Product layouts
These layouts basically recovered in flow shops. In this type of layout the resources are
systematically arranged as per routing of products accordingly. The use of Line balancing often
enhanced the efficiency of the products.
Fixed position layout
These layouts are used for those products which are excessively big or overly hefty to
relocate. For instance, warship cannot be manufactured on an assembly line. There are many
products and services which cannot be easily move. Examples of fixed position layout includes a
operating rooms in a hospital where all staff and equipments are brought to the patients.) the
construction of shipbuilding, aircraft, aerospace are some other examples of fixed-position
layout.
Combination layout
The mixture of three main layouts type in many situations are called combination layout
or hybrid layout. An organization may use a this type of layout for the construction the end
product, but the utilization of construction lines for manufacture of the elements and sub-
assemblies that forms the ultimate commodity (e.g., aircraft).
Cellular layout
Both have customer's suppliers, scheduling and staffing issues.
Question 2 – Identify the basic layouts for the manufacturing and services industries.
In manufacturing context, the layout includes the complex locations with lines, structures,
spheres and other properties. Manufacturing layout includes the product and process matrix
layout while other type of layout includes fixed positions, combinations, cellular and others are
service layout.
Process layouts
These layout are recovered in job shops or in those small enterprises which produces the
devalued commodities that provides a various process requirements and sequence of functions
In this layout the transactions of a same quality or functions are sorted together. They process
commodities with their main aim or renders services that includes the a mixture of processing
requirements. Improvement of process layout incudes the reduction of transportations cost,
region, period of time.
Product layouts
These layouts basically recovered in flow shops. In this type of layout the resources are
systematically arranged as per routing of products accordingly. The use of Line balancing often
enhanced the efficiency of the products.
Fixed position layout
These layouts are used for those products which are excessively big or overly hefty to
relocate. For instance, warship cannot be manufactured on an assembly line. There are many
products and services which cannot be easily move. Examples of fixed position layout includes a
operating rooms in a hospital where all staff and equipments are brought to the patients.) the
construction of shipbuilding, aircraft, aerospace are some other examples of fixed-position
layout.
Combination layout
The mixture of three main layouts type in many situations are called combination layout
or hybrid layout. An organization may use a this type of layout for the construction the end
product, but the utilization of construction lines for manufacture of the elements and sub-
assemblies that forms the ultimate commodity (e.g., aircraft).
Cellular layout
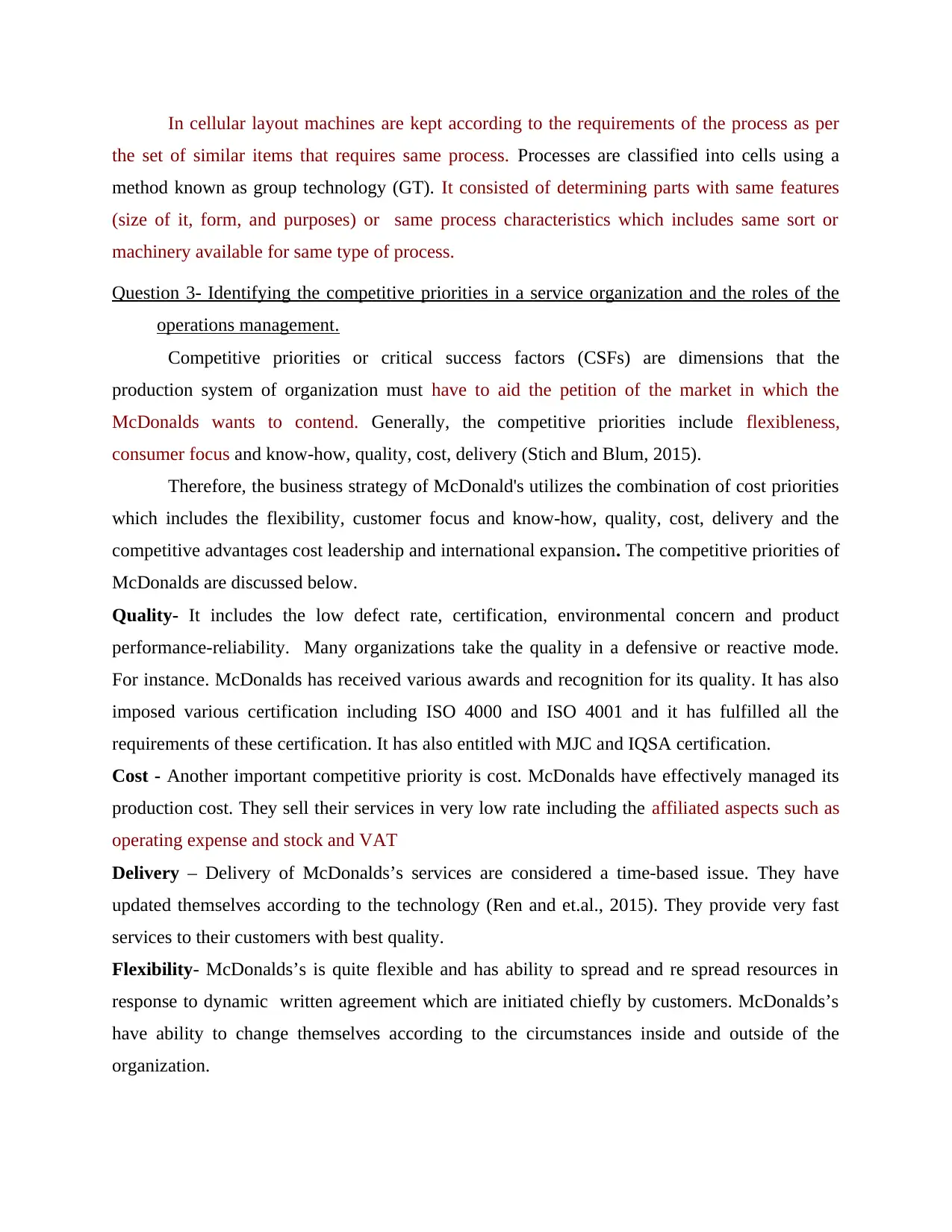
In cellular layout machines are kept according to the requirements of the process as per
the set of similar items that requires same process. Processes are classified into cells using a
method known as group technology (GT). It consisted of determining parts with same features
(size of it, form, and purposes) or same process characteristics which includes same sort or
machinery available for same type of process.
Question 3- Identifying the competitive priorities in a service organization and the roles of the
operations management.
Competitive priorities or critical success factors (CSFs) are dimensions that the
production system of organization must have to aid the petition of the market in which the
McDonalds wants to contend. Generally, the competitive priorities include flexibleness,
consumer focus and know-how, quality, cost, delivery (Stich and Blum, 2015).
Therefore, the business strategy of McDonald's utilizes the combination of cost priorities
which includes the flexibility, customer focus and know-how, quality, cost, delivery and the
competitive advantages cost leadership and international expansion. The competitive priorities of
McDonalds are discussed below.
Quality- It includes the low defect rate, certification, environmental concern and product
performance-reliability. Many organizations take the quality in a defensive or reactive mode.
For instance. McDonalds has received various awards and recognition for its quality. It has also
imposed various certification including ISO 4000 and ISO 4001 and it has fulfilled all the
requirements of these certification. It has also entitled with MJC and IQSA certification.
Cost - Another important competitive priority is cost. McDonalds have effectively managed its
production cost. They sell their services in very low rate including the affiliated aspects such as
operating expense and stock and VAT
Delivery – Delivery of McDonalds’s services are considered a time-based issue. They have
updated themselves according to the technology (Ren and et.al., 2015). They provide very fast
services to their customers with best quality.
Flexibility- McDonalds’s is quite flexible and has ability to spread and re spread resources in
response to dynamic written agreement which are initiated chiefly by customers. McDonalds’s
have ability to change themselves according to the circumstances inside and outside of the
organization.
the set of similar items that requires same process. Processes are classified into cells using a
method known as group technology (GT). It consisted of determining parts with same features
(size of it, form, and purposes) or same process characteristics which includes same sort or
machinery available for same type of process.
Question 3- Identifying the competitive priorities in a service organization and the roles of the
operations management.
Competitive priorities or critical success factors (CSFs) are dimensions that the
production system of organization must have to aid the petition of the market in which the
McDonalds wants to contend. Generally, the competitive priorities include flexibleness,
consumer focus and know-how, quality, cost, delivery (Stich and Blum, 2015).
Therefore, the business strategy of McDonald's utilizes the combination of cost priorities
which includes the flexibility, customer focus and know-how, quality, cost, delivery and the
competitive advantages cost leadership and international expansion. The competitive priorities of
McDonalds are discussed below.
Quality- It includes the low defect rate, certification, environmental concern and product
performance-reliability. Many organizations take the quality in a defensive or reactive mode.
For instance. McDonalds has received various awards and recognition for its quality. It has also
imposed various certification including ISO 4000 and ISO 4001 and it has fulfilled all the
requirements of these certification. It has also entitled with MJC and IQSA certification.
Cost - Another important competitive priority is cost. McDonalds have effectively managed its
production cost. They sell their services in very low rate including the affiliated aspects such as
operating expense and stock and VAT
Delivery – Delivery of McDonalds’s services are considered a time-based issue. They have
updated themselves according to the technology (Ren and et.al., 2015). They provide very fast
services to their customers with best quality.
Flexibility- McDonalds’s is quite flexible and has ability to spread and re spread resources in
response to dynamic written agreement which are initiated chiefly by customers. McDonalds’s
have ability to change themselves according to the circumstances inside and outside of the
organization.
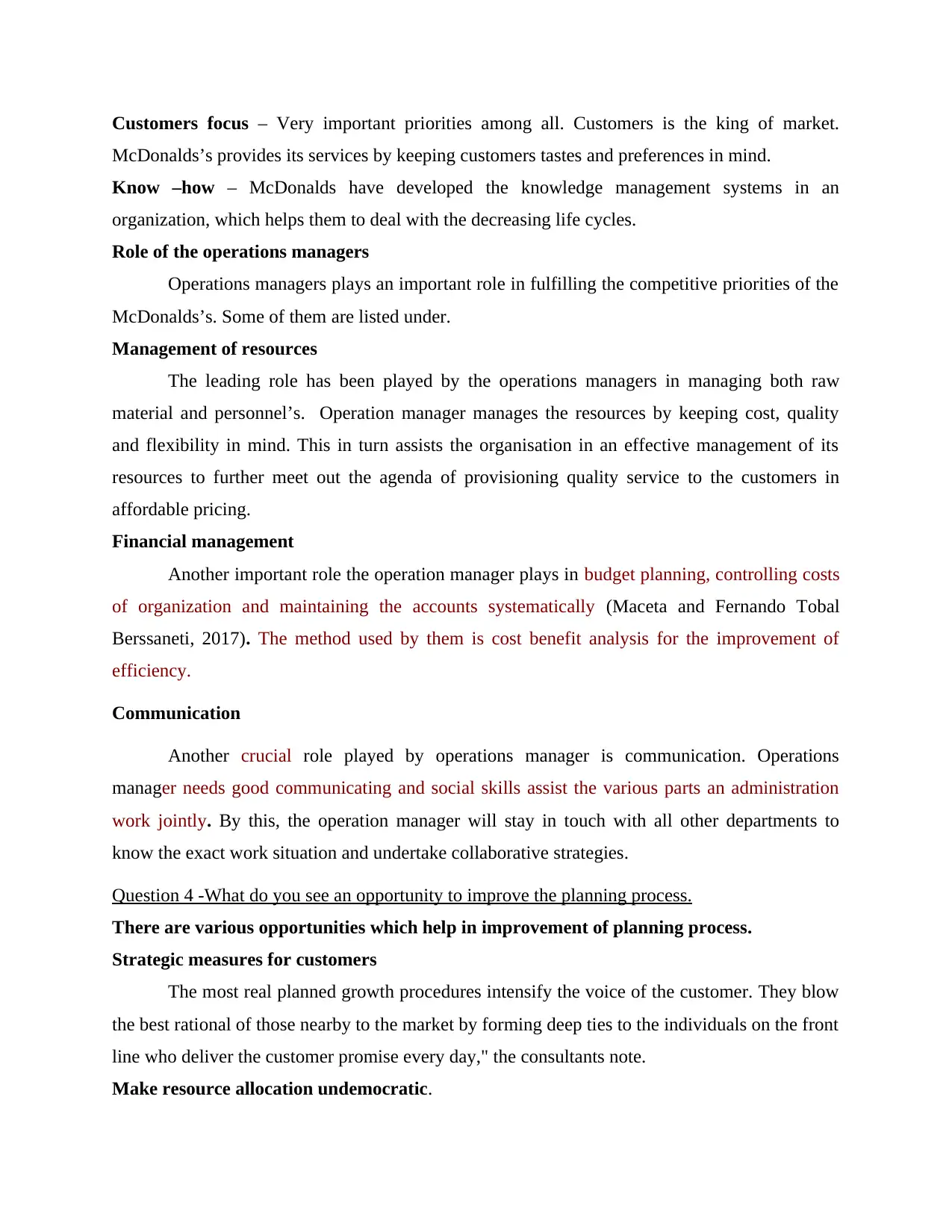
Customers focus – Very important priorities among all. Customers is the king of market.
McDonalds’s provides its services by keeping customers tastes and preferences in mind.
Know –how – McDonalds have developed the knowledge management systems in an
organization, which helps them to deal with the decreasing life cycles.
Role of the operations managers
Operations managers plays an important role in fulfilling the competitive priorities of the
McDonalds’s. Some of them are listed under.
Management of resources
The leading role has been played by the operations managers in managing both raw
material and personnel’s. Operation manager manages the resources by keeping cost, quality
and flexibility in mind. This in turn assists the organisation in an effective management of its
resources to further meet out the agenda of provisioning quality service to the customers in
affordable pricing.
Financial management
Another important role the operation manager plays in budget planning, controlling costs
of organization and maintaining the accounts systematically (Maceta and Fernando Tobal
Berssaneti, 2017). The method used by them is cost benefit analysis for the improvement of
efficiency.
Communication
Another crucial role played by operations manager is communication. Operations
manager needs good communicating and social skills assist the various parts an administration
work jointly. By this, the operation manager will stay in touch with all other departments to
know the exact work situation and undertake collaborative strategies.
Question 4 -What do you see an opportunity to improve the planning process.
There are various opportunities which help in improvement of planning process.
Strategic measures for customers
The most real planned growth procedures intensify the voice of the customer. They blow
the best rational of those nearby to the market by forming deep ties to the individuals on the front
line who deliver the customer promise every day," the consultants note.
Make resource allocation undemocratic.
McDonalds’s provides its services by keeping customers tastes and preferences in mind.
Know –how – McDonalds have developed the knowledge management systems in an
organization, which helps them to deal with the decreasing life cycles.
Role of the operations managers
Operations managers plays an important role in fulfilling the competitive priorities of the
McDonalds’s. Some of them are listed under.
Management of resources
The leading role has been played by the operations managers in managing both raw
material and personnel’s. Operation manager manages the resources by keeping cost, quality
and flexibility in mind. This in turn assists the organisation in an effective management of its
resources to further meet out the agenda of provisioning quality service to the customers in
affordable pricing.
Financial management
Another important role the operation manager plays in budget planning, controlling costs
of organization and maintaining the accounts systematically (Maceta and Fernando Tobal
Berssaneti, 2017). The method used by them is cost benefit analysis for the improvement of
efficiency.
Communication
Another crucial role played by operations manager is communication. Operations
manager needs good communicating and social skills assist the various parts an administration
work jointly. By this, the operation manager will stay in touch with all other departments to
know the exact work situation and undertake collaborative strategies.
Question 4 -What do you see an opportunity to improve the planning process.
There are various opportunities which help in improvement of planning process.
Strategic measures for customers
The most real planned growth procedures intensify the voice of the customer. They blow
the best rational of those nearby to the market by forming deep ties to the individuals on the front
line who deliver the customer promise every day," the consultants note.
Make resource allocation undemocratic.
Paraphrase This Document
Need a fresh take? Get an instant paraphrase of this document with our AI Paraphraser
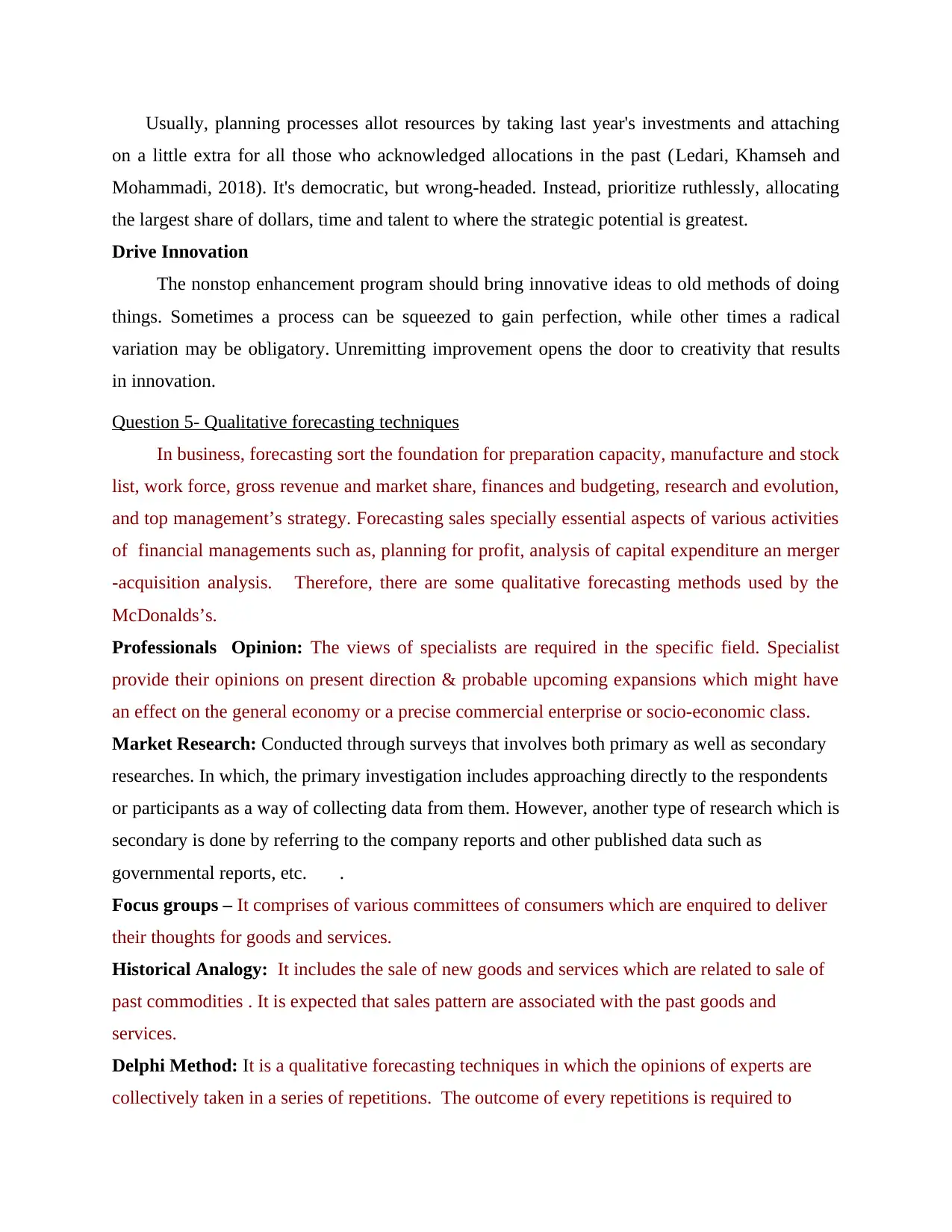
Usually, planning processes allot resources by taking last year's investments and attaching
on a little extra for all those who acknowledged allocations in the past (Ledari, Khamseh and
Mohammadi, 2018). It's democratic, but wrong-headed. Instead, prioritize ruthlessly, allocating
the largest share of dollars, time and talent to where the strategic potential is greatest.
Drive Innovation
The nonstop enhancement program should bring innovative ideas to old methods of doing
things. Sometimes a process can be squeezed to gain perfection, while other times a radical
variation may be obligatory. Unremitting improvement opens the door to creativity that results
in innovation.
Question 5- Qualitative forecasting techniques
In business, forecasting sort the foundation for preparation capacity, manufacture and stock
list, work force, gross revenue and market share, finances and budgeting, research and evolution,
and top management’s strategy. Forecasting sales specially essential aspects of various activities
of financial managements such as, planning for profit, analysis of capital expenditure an merger
-acquisition analysis. Therefore, there are some qualitative forecasting methods used by the
McDonalds’s.
Professionals Opinion: The views of specialists are required in the specific field. Specialist
provide their opinions on present direction & probable upcoming expansions which might have
an effect on the general economy or a precise commercial enterprise or socio-economic class.
Market Research: Conducted through surveys that involves both primary as well as secondary
researches. In which, the primary investigation includes approaching directly to the respondents
or participants as a way of collecting data from them. However, another type of research which is
secondary is done by referring to the company reports and other published data such as
governmental reports, etc. .
Focus groups – It comprises of various committees of consumers which are enquired to deliver
their thoughts for goods and services.
Historical Analogy: It includes the sale of new goods and services which are related to sale of
past commodities . It is expected that sales pattern are associated with the past goods and
services.
Delphi Method: It is a qualitative forecasting techniques in which the opinions of experts are
collectively taken in a series of repetitions. The outcome of every repetitions is required to
on a little extra for all those who acknowledged allocations in the past (Ledari, Khamseh and
Mohammadi, 2018). It's democratic, but wrong-headed. Instead, prioritize ruthlessly, allocating
the largest share of dollars, time and talent to where the strategic potential is greatest.
Drive Innovation
The nonstop enhancement program should bring innovative ideas to old methods of doing
things. Sometimes a process can be squeezed to gain perfection, while other times a radical
variation may be obligatory. Unremitting improvement opens the door to creativity that results
in innovation.
Question 5- Qualitative forecasting techniques
In business, forecasting sort the foundation for preparation capacity, manufacture and stock
list, work force, gross revenue and market share, finances and budgeting, research and evolution,
and top management’s strategy. Forecasting sales specially essential aspects of various activities
of financial managements such as, planning for profit, analysis of capital expenditure an merger
-acquisition analysis. Therefore, there are some qualitative forecasting methods used by the
McDonalds’s.
Professionals Opinion: The views of specialists are required in the specific field. Specialist
provide their opinions on present direction & probable upcoming expansions which might have
an effect on the general economy or a precise commercial enterprise or socio-economic class.
Market Research: Conducted through surveys that involves both primary as well as secondary
researches. In which, the primary investigation includes approaching directly to the respondents
or participants as a way of collecting data from them. However, another type of research which is
secondary is done by referring to the company reports and other published data such as
governmental reports, etc. .
Focus groups – It comprises of various committees of consumers which are enquired to deliver
their thoughts for goods and services.
Historical Analogy: It includes the sale of new goods and services which are related to sale of
past commodities . It is expected that sales pattern are associated with the past goods and
services.
Delphi Method: It is a qualitative forecasting techniques in which the opinions of experts are
collectively taken in a series of repetitions. The outcome of every repetitions is required to
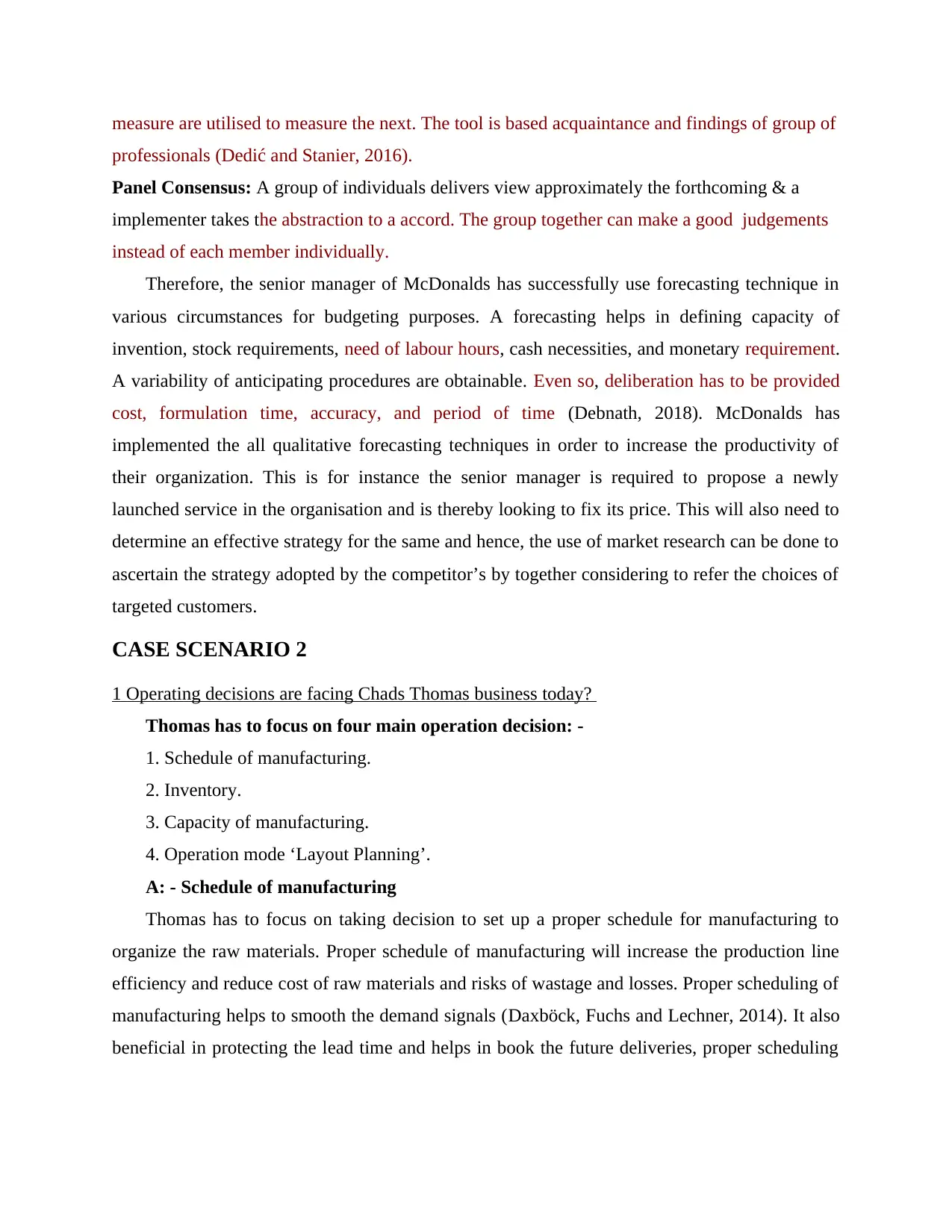
measure are utilised to measure the next. The tool is based acquaintance and findings of group of
professionals (Dedić and Stanier, 2016).
Panel Consensus: A group of individuals delivers view approximately the forthcoming & a
implementer takes the abstraction to a accord. The group together can make a good judgements
instead of each member individually.
Therefore, the senior manager of McDonalds has successfully use forecasting technique in
various circumstances for budgeting purposes. A forecasting helps in defining capacity of
invention, stock requirements, need of labour hours, cash necessities, and monetary requirement.
A variability of anticipating procedures are obtainable. Even so, deliberation has to be provided
cost, formulation time, accuracy, and period of time (Debnath, 2018). McDonalds has
implemented the all qualitative forecasting techniques in order to increase the productivity of
their organization. This is for instance the senior manager is required to propose a newly
launched service in the organisation and is thereby looking to fix its price. This will also need to
determine an effective strategy for the same and hence, the use of market research can be done to
ascertain the strategy adopted by the competitor’s by together considering to refer the choices of
targeted customers.
CASE SCENARIO 2
1 Operating decisions are facing Chads Thomas business today?
Thomas has to focus on four main operation decision: -
1. Schedule of manufacturing.
2. Inventory.
3. Capacity of manufacturing.
4. Operation mode ‘Layout Planning’.
A: - Schedule of manufacturing
Thomas has to focus on taking decision to set up a proper schedule for manufacturing to
organize the raw materials. Proper schedule of manufacturing will increase the production line
efficiency and reduce cost of raw materials and risks of wastage and losses. Proper scheduling of
manufacturing helps to smooth the demand signals (Daxböck, Fuchs and Lechner, 2014). It also
beneficial in protecting the lead time and helps in book the future deliveries, proper scheduling
professionals (Dedić and Stanier, 2016).
Panel Consensus: A group of individuals delivers view approximately the forthcoming & a
implementer takes the abstraction to a accord. The group together can make a good judgements
instead of each member individually.
Therefore, the senior manager of McDonalds has successfully use forecasting technique in
various circumstances for budgeting purposes. A forecasting helps in defining capacity of
invention, stock requirements, need of labour hours, cash necessities, and monetary requirement.
A variability of anticipating procedures are obtainable. Even so, deliberation has to be provided
cost, formulation time, accuracy, and period of time (Debnath, 2018). McDonalds has
implemented the all qualitative forecasting techniques in order to increase the productivity of
their organization. This is for instance the senior manager is required to propose a newly
launched service in the organisation and is thereby looking to fix its price. This will also need to
determine an effective strategy for the same and hence, the use of market research can be done to
ascertain the strategy adopted by the competitor’s by together considering to refer the choices of
targeted customers.
CASE SCENARIO 2
1 Operating decisions are facing Chads Thomas business today?
Thomas has to focus on four main operation decision: -
1. Schedule of manufacturing.
2. Inventory.
3. Capacity of manufacturing.
4. Operation mode ‘Layout Planning’.
A: - Schedule of manufacturing
Thomas has to focus on taking decision to set up a proper schedule for manufacturing to
organize the raw materials. Proper schedule of manufacturing will increase the production line
efficiency and reduce cost of raw materials and risks of wastage and losses. Proper scheduling of
manufacturing helps to smooth the demand signals (Daxböck, Fuchs and Lechner, 2014). It also
beneficial in protecting the lead time and helps in book the future deliveries, proper scheduling
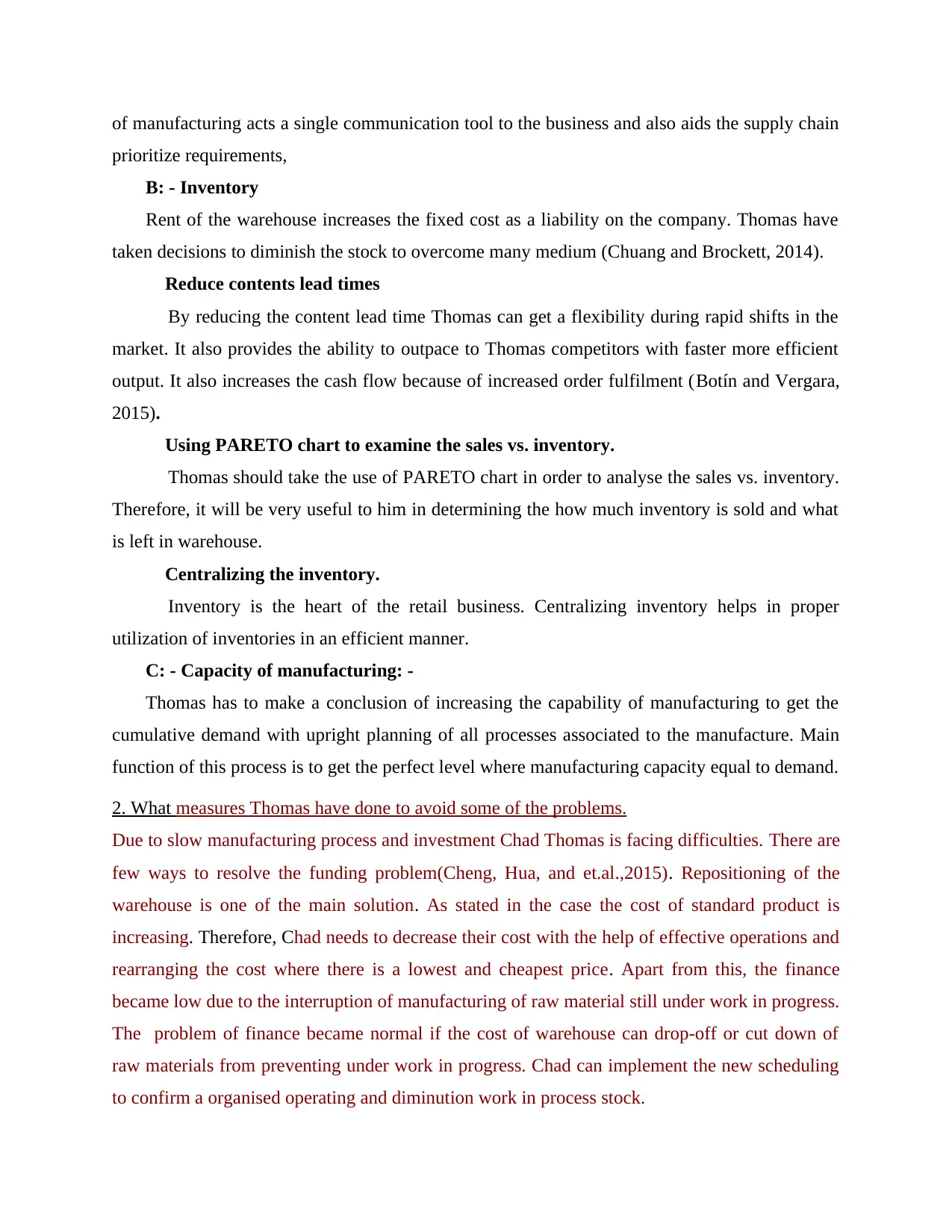
of manufacturing acts a single communication tool to the business and also aids the supply chain
prioritize requirements,
B: - Inventory
Rent of the warehouse increases the fixed cost as a liability on the company. Thomas have
taken decisions to diminish the stock to overcome many medium (Chuang and Brockett, 2014).
Reduce contents lead times
By reducing the content lead time Thomas can get a flexibility during rapid shifts in the
market. It also provides the ability to outpace to Thomas competitors with faster more efficient
output. It also increases the cash flow because of increased order fulfilment (Botín and Vergara,
2015).
Using PARETO chart to examine the sales vs. inventory.
Thomas should take the use of PARETO chart in order to analyse the sales vs. inventory.
Therefore, it will be very useful to him in determining the how much inventory is sold and what
is left in warehouse.
Centralizing the inventory.
Inventory is the heart of the retail business. Centralizing inventory helps in proper
utilization of inventories in an efficient manner.
C: - Capacity of manufacturing: -
Thomas has to make a conclusion of increasing the capability of manufacturing to get the
cumulative demand with upright planning of all processes associated to the manufacture. Main
function of this process is to get the perfect level where manufacturing capacity equal to demand.
2. What measures Thomas have done to avoid some of the problems.
Due to slow manufacturing process and investment Chad Thomas is facing difficulties. There are
few ways to resolve the funding problem(Cheng, Hua, and et.al.,2015). Repositioning of the
warehouse is one of the main solution. As stated in the case the cost of standard product is
increasing. Therefore, Chad needs to decrease their cost with the help of effective operations and
rearranging the cost where there is a lowest and cheapest price. Apart from this, the finance
became low due to the interruption of manufacturing of raw material still under work in progress.
The problem of finance became normal if the cost of warehouse can drop-off or cut down of
raw materials from preventing under work in progress. Chad can implement the new scheduling
to confirm a organised operating and diminution work in process stock.
prioritize requirements,
B: - Inventory
Rent of the warehouse increases the fixed cost as a liability on the company. Thomas have
taken decisions to diminish the stock to overcome many medium (Chuang and Brockett, 2014).
Reduce contents lead times
By reducing the content lead time Thomas can get a flexibility during rapid shifts in the
market. It also provides the ability to outpace to Thomas competitors with faster more efficient
output. It also increases the cash flow because of increased order fulfilment (Botín and Vergara,
2015).
Using PARETO chart to examine the sales vs. inventory.
Thomas should take the use of PARETO chart in order to analyse the sales vs. inventory.
Therefore, it will be very useful to him in determining the how much inventory is sold and what
is left in warehouse.
Centralizing the inventory.
Inventory is the heart of the retail business. Centralizing inventory helps in proper
utilization of inventories in an efficient manner.
C: - Capacity of manufacturing: -
Thomas has to make a conclusion of increasing the capability of manufacturing to get the
cumulative demand with upright planning of all processes associated to the manufacture. Main
function of this process is to get the perfect level where manufacturing capacity equal to demand.
2. What measures Thomas have done to avoid some of the problems.
Due to slow manufacturing process and investment Chad Thomas is facing difficulties. There are
few ways to resolve the funding problem(Cheng, Hua, and et.al.,2015). Repositioning of the
warehouse is one of the main solution. As stated in the case the cost of standard product is
increasing. Therefore, Chad needs to decrease their cost with the help of effective operations and
rearranging the cost where there is a lowest and cheapest price. Apart from this, the finance
became low due to the interruption of manufacturing of raw material still under work in progress.
The problem of finance became normal if the cost of warehouse can drop-off or cut down of
raw materials from preventing under work in progress. Chad can implement the new scheduling
to confirm a organised operating and diminution work in process stock.
Secure Best Marks with AI Grader
Need help grading? Try our AI Grader for instant feedback on your assignments.
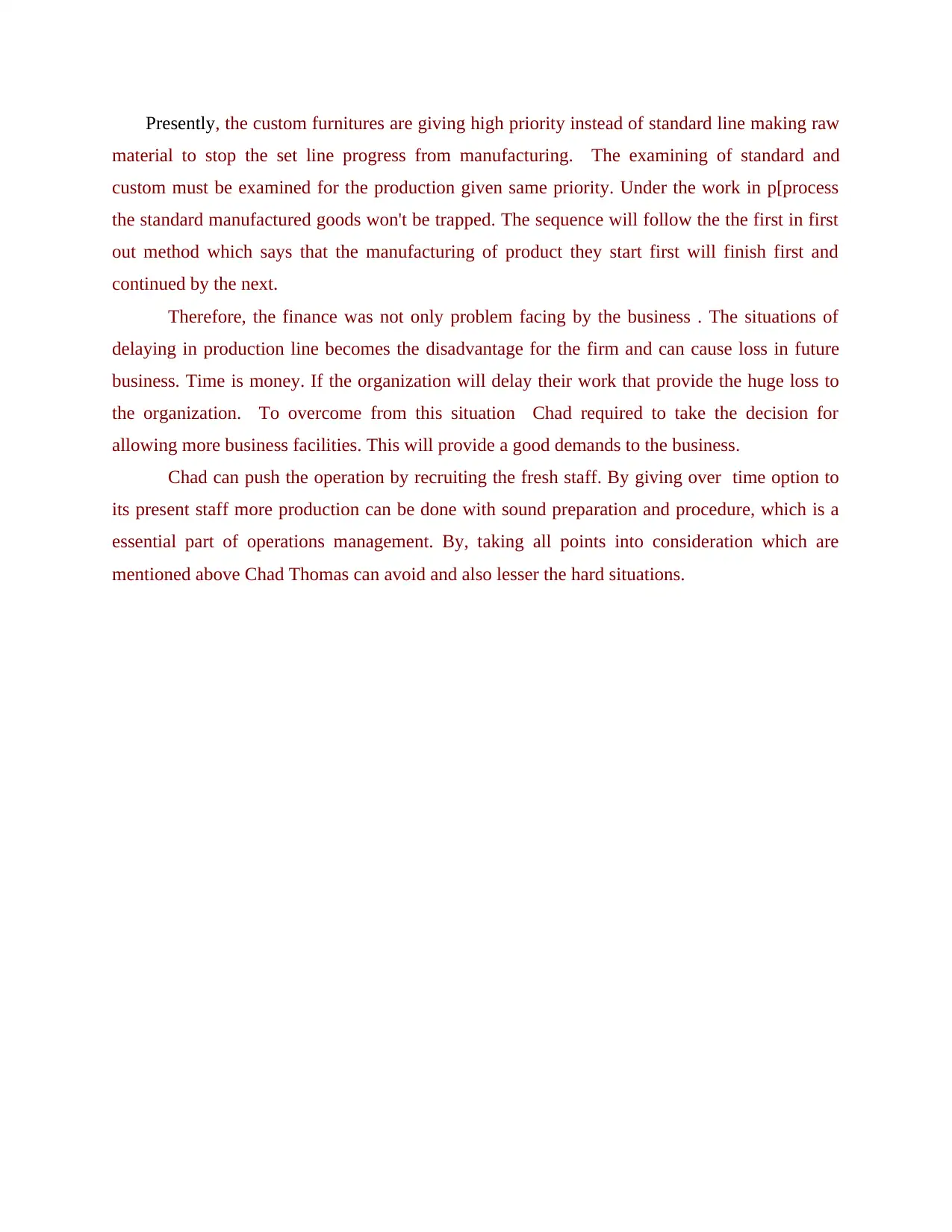
Presently, the custom furnitures are giving high priority instead of standard line making raw
material to stop the set line progress from manufacturing. The examining of standard and
custom must be examined for the production given same priority. Under the work in p[process
the standard manufactured goods won't be trapped. The sequence will follow the the first in first
out method which says that the manufacturing of product they start first will finish first and
continued by the next.
Therefore, the finance was not only problem facing by the business . The situations of
delaying in production line becomes the disadvantage for the firm and can cause loss in future
business. Time is money. If the organization will delay their work that provide the huge loss to
the organization. To overcome from this situation Chad required to take the decision for
allowing more business facilities. This will provide a good demands to the business.
Chad can push the operation by recruiting the fresh staff. By giving over time option to
its present staff more production can be done with sound preparation and procedure, which is a
essential part of operations management. By, taking all points into consideration which are
mentioned above Chad Thomas can avoid and also lesser the hard situations.
material to stop the set line progress from manufacturing. The examining of standard and
custom must be examined for the production given same priority. Under the work in p[process
the standard manufactured goods won't be trapped. The sequence will follow the the first in first
out method which says that the manufacturing of product they start first will finish first and
continued by the next.
Therefore, the finance was not only problem facing by the business . The situations of
delaying in production line becomes the disadvantage for the firm and can cause loss in future
business. Time is money. If the organization will delay their work that provide the huge loss to
the organization. To overcome from this situation Chad required to take the decision for
allowing more business facilities. This will provide a good demands to the business.
Chad can push the operation by recruiting the fresh staff. By giving over time option to
its present staff more production can be done with sound preparation and procedure, which is a
essential part of operations management. By, taking all points into consideration which are
mentioned above Chad Thomas can avoid and also lesser the hard situations.

CONCLUSION
From the above report it can be concluded that operations management plays an important
role in every organization the report has covered every aspects of operations management.
Present report has covered the similarities and differences between manufacturing and services.
Assignment has also provided the competitive priorities in a service organization along with the
role of operations manager CSFs. Report has also provided a deeper insight of basic layout types
for both manufacturing and service facilities. Study has also investigated the various types of
qualitative forecasting techniques. The second part of the report is consisted of questions of case
scenarios which includes types of operating decision that are facing by Chads Thomas business
today. The report has also provided the steps taken by the Chad Thomas in facing the problems.
From the above report it can be concluded that operations management plays an important
role in every organization the report has covered every aspects of operations management.
Present report has covered the similarities and differences between manufacturing and services.
Assignment has also provided the competitive priorities in a service organization along with the
role of operations manager CSFs. Report has also provided a deeper insight of basic layout types
for both manufacturing and service facilities. Study has also investigated the various types of
qualitative forecasting techniques. The second part of the report is consisted of questions of case
scenarios which includes types of operating decision that are facing by Chads Thomas business
today. The report has also provided the steps taken by the Chad Thomas in facing the problems.
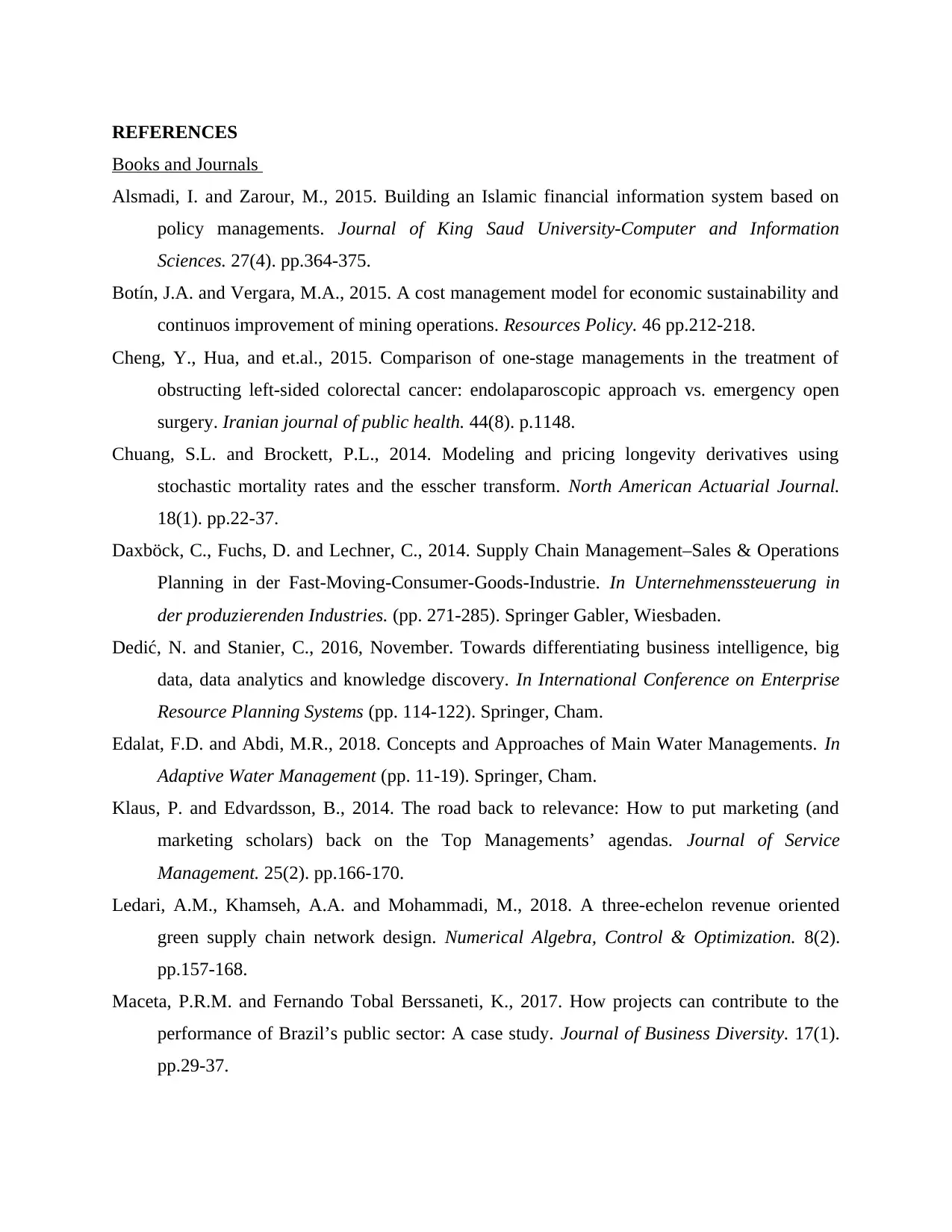
REFERENCES
Books and Journals
Alsmadi, I. and Zarour, M., 2015. Building an Islamic financial information system based on
policy managements. Journal of King Saud University-Computer and Information
Sciences. 27(4). pp.364-375.
Botín, J.A. and Vergara, M.A., 2015. A cost management model for economic sustainability and
continuos improvement of mining operations. Resources Policy. 46 pp.212-218.
Cheng, Y., Hua, and et.al., 2015. Comparison of one-stage managements in the treatment of
obstructing left-sided colorectal cancer: endolaparoscopic approach vs. emergency open
surgery. Iranian journal of public health. 44(8). p.1148.
Chuang, S.L. and Brockett, P.L., 2014. Modeling and pricing longevity derivatives using
stochastic mortality rates and the esscher transform. North American Actuarial Journal.
18(1). pp.22-37.
Daxböck, C., Fuchs, D. and Lechner, C., 2014. Supply Chain Management–Sales & Operations
Planning in der Fast-Moving-Consumer-Goods-Industrie. In Unternehmenssteuerung in
der produzierenden Industries. (pp. 271-285). Springer Gabler, Wiesbaden.
Dedić, N. and Stanier, C., 2016, November. Towards differentiating business intelligence, big
data, data analytics and knowledge discovery. In International Conference on Enterprise
Resource Planning Systems (pp. 114-122). Springer, Cham.
Edalat, F.D. and Abdi, M.R., 2018. Concepts and Approaches of Main Water Managements. In
Adaptive Water Management (pp. 11-19). Springer, Cham.
Klaus, P. and Edvardsson, B., 2014. The road back to relevance: How to put marketing (and
marketing scholars) back on the Top Managements’ agendas. Journal of Service
Management. 25(2). pp.166-170.
Ledari, A.M., Khamseh, A.A. and Mohammadi, M., 2018. A three-echelon revenue oriented
green supply chain network design. Numerical Algebra, Control & Optimization. 8(2).
pp.157-168.
Maceta, P.R.M. and Fernando Tobal Berssaneti, K., 2017. How projects can contribute to the
performance of Brazil’s public sector: A case study. Journal of Business Diversity. 17(1).
pp.29-37.
Books and Journals
Alsmadi, I. and Zarour, M., 2015. Building an Islamic financial information system based on
policy managements. Journal of King Saud University-Computer and Information
Sciences. 27(4). pp.364-375.
Botín, J.A. and Vergara, M.A., 2015. A cost management model for economic sustainability and
continuos improvement of mining operations. Resources Policy. 46 pp.212-218.
Cheng, Y., Hua, and et.al., 2015. Comparison of one-stage managements in the treatment of
obstructing left-sided colorectal cancer: endolaparoscopic approach vs. emergency open
surgery. Iranian journal of public health. 44(8). p.1148.
Chuang, S.L. and Brockett, P.L., 2014. Modeling and pricing longevity derivatives using
stochastic mortality rates and the esscher transform. North American Actuarial Journal.
18(1). pp.22-37.
Daxböck, C., Fuchs, D. and Lechner, C., 2014. Supply Chain Management–Sales & Operations
Planning in der Fast-Moving-Consumer-Goods-Industrie. In Unternehmenssteuerung in
der produzierenden Industries. (pp. 271-285). Springer Gabler, Wiesbaden.
Dedić, N. and Stanier, C., 2016, November. Towards differentiating business intelligence, big
data, data analytics and knowledge discovery. In International Conference on Enterprise
Resource Planning Systems (pp. 114-122). Springer, Cham.
Edalat, F.D. and Abdi, M.R., 2018. Concepts and Approaches of Main Water Managements. In
Adaptive Water Management (pp. 11-19). Springer, Cham.
Klaus, P. and Edvardsson, B., 2014. The road back to relevance: How to put marketing (and
marketing scholars) back on the Top Managements’ agendas. Journal of Service
Management. 25(2). pp.166-170.
Ledari, A.M., Khamseh, A.A. and Mohammadi, M., 2018. A three-echelon revenue oriented
green supply chain network design. Numerical Algebra, Control & Optimization. 8(2).
pp.157-168.
Maceta, P.R.M. and Fernando Tobal Berssaneti, K., 2017. How projects can contribute to the
performance of Brazil’s public sector: A case study. Journal of Business Diversity. 17(1).
pp.29-37.
Paraphrase This Document
Need a fresh take? Get an instant paraphrase of this document with our AI Paraphraser
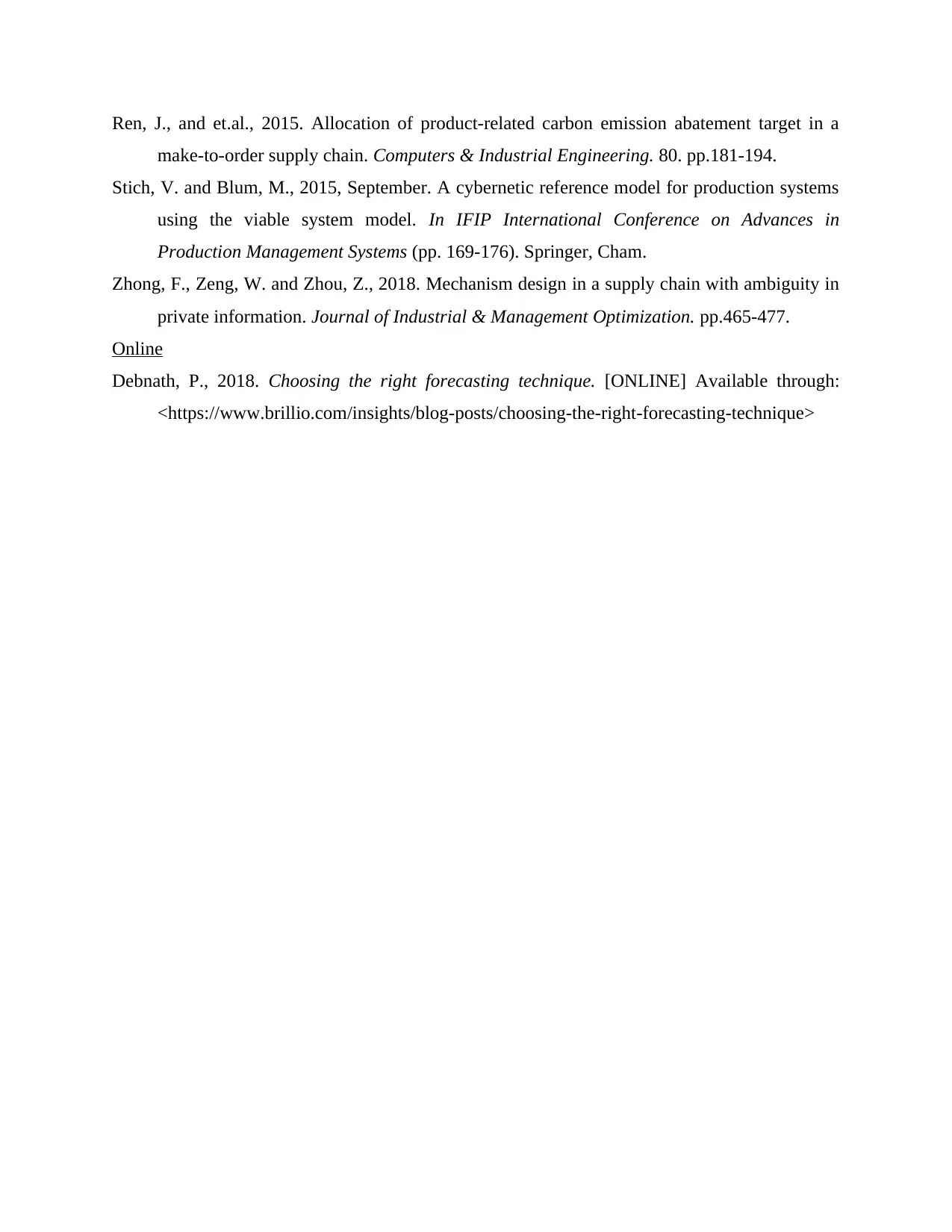
Ren, J., and et.al., 2015. Allocation of product-related carbon emission abatement target in a
make-to-order supply chain. Computers & Industrial Engineering. 80. pp.181-194.
Stich, V. and Blum, M., 2015, September. A cybernetic reference model for production systems
using the viable system model. In IFIP International Conference on Advances in
Production Management Systems (pp. 169-176). Springer, Cham.
Zhong, F., Zeng, W. and Zhou, Z., 2018. Mechanism design in a supply chain with ambiguity in
private information. Journal of Industrial & Management Optimization. pp.465-477.
Online
Debnath, P., 2018. Choosing the right forecasting technique. [ONLINE] Available through:
<https://www.brillio.com/insights/blog-posts/choosing-the-right-forecasting-technique>
make-to-order supply chain. Computers & Industrial Engineering. 80. pp.181-194.
Stich, V. and Blum, M., 2015, September. A cybernetic reference model for production systems
using the viable system model. In IFIP International Conference on Advances in
Production Management Systems (pp. 169-176). Springer, Cham.
Zhong, F., Zeng, W. and Zhou, Z., 2018. Mechanism design in a supply chain with ambiguity in
private information. Journal of Industrial & Management Optimization. pp.465-477.
Online
Debnath, P., 2018. Choosing the right forecasting technique. [ONLINE] Available through:
<https://www.brillio.com/insights/blog-posts/choosing-the-right-forecasting-technique>
1 out of 14
Related Documents
![[object Object]](/_next/image/?url=%2F_next%2Fstatic%2Fmedia%2Flogo.6d15ce61.png&w=640&q=75)
Your All-in-One AI-Powered Toolkit for Academic Success.
+13062052269
info@desklib.com
Available 24*7 on WhatsApp / Email
Unlock your academic potential
© 2024 | Zucol Services PVT LTD | All rights reserved.