Operations Management: Layers, Capacity Planning, Inventory Planning, SCM and Deming Cycle
VerifiedAdded on 2022/11/18
|9
|2705
|131
AI Summary
This document covers the foundational pillars of operation management layers, steps required for capacity planning, techniques used for inventory planning, efficient and responsive supply chain management, and how Emirates Airlines uses Deming Cycle to attain excellence. It also includes references for further reading.
Contribute Materials
Your contribution can guide someone’s learning journey. Share your
documents today.
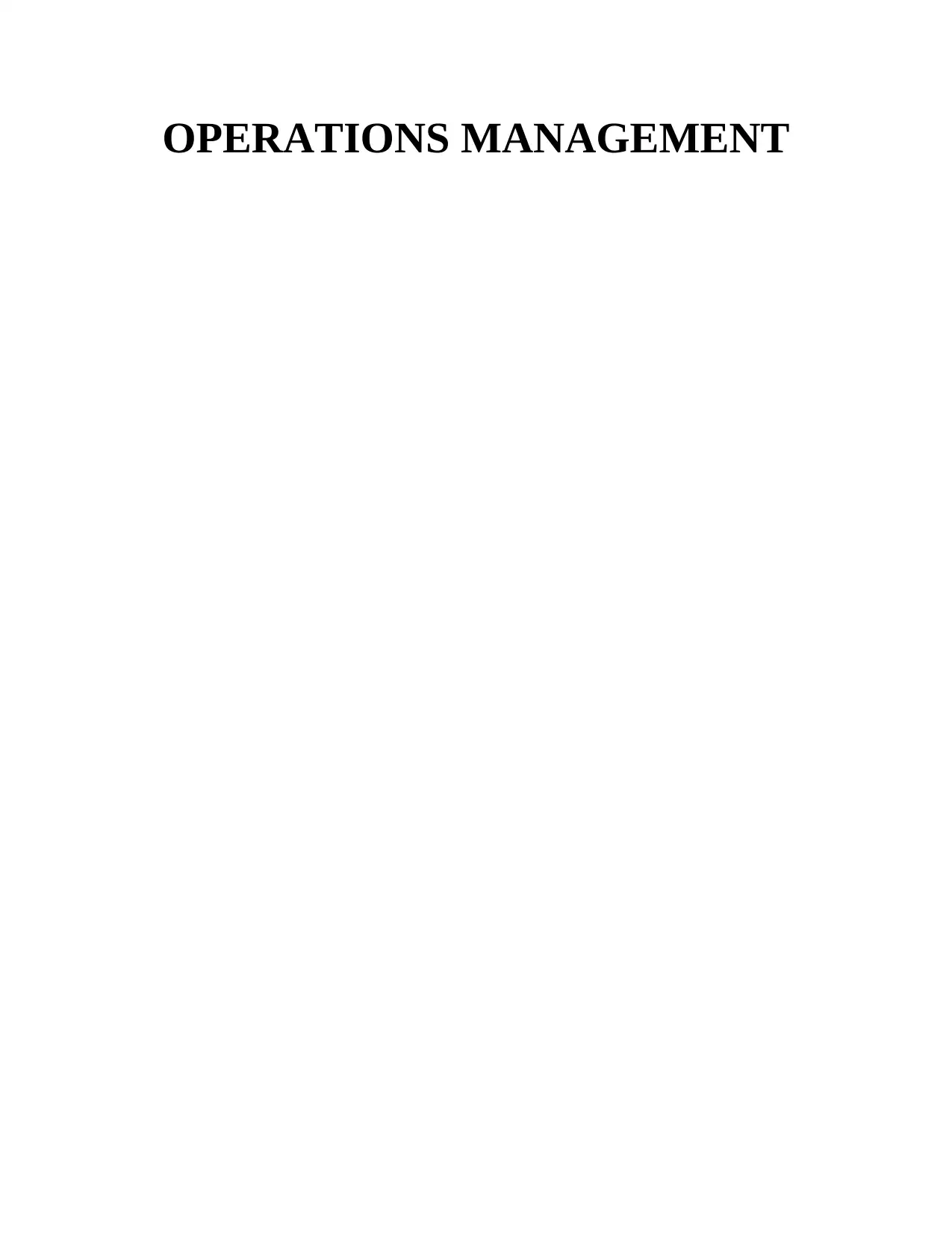
OPERATIONS MANAGEMENT
Secure Best Marks with AI Grader
Need help grading? Try our AI Grader for instant feedback on your assignments.
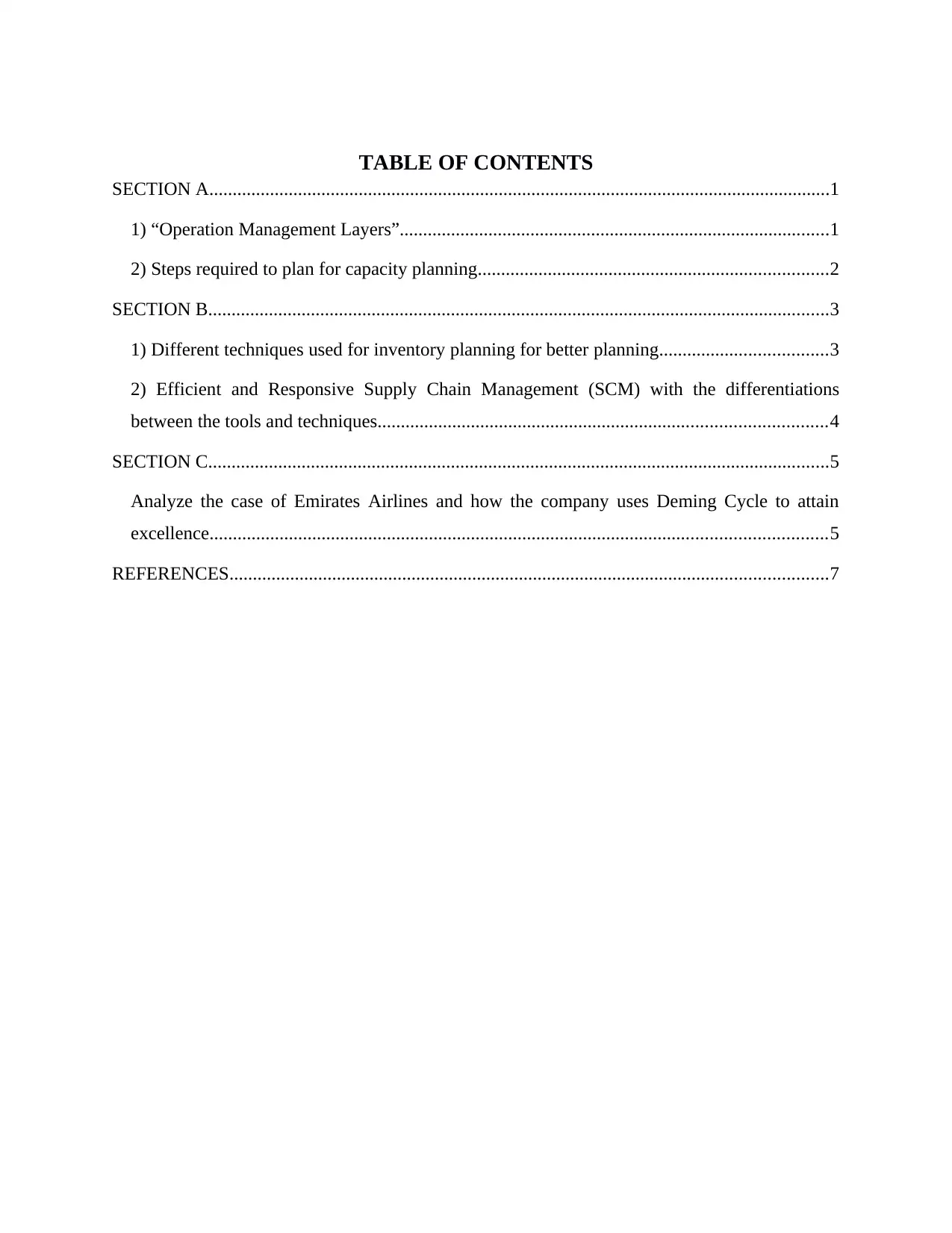
TABLE OF CONTENTS
SECTION A.....................................................................................................................................1
1) “Operation Management Layers”............................................................................................1
2) Steps required to plan for capacity planning...........................................................................2
SECTION B.....................................................................................................................................3
1) Different techniques used for inventory planning for better planning....................................3
2) Efficient and Responsive Supply Chain Management (SCM) with the differentiations
between the tools and techniques................................................................................................4
SECTION C.....................................................................................................................................5
Analyze the case of Emirates Airlines and how the company uses Deming Cycle to attain
excellence....................................................................................................................................5
REFERENCES................................................................................................................................7
SECTION A.....................................................................................................................................1
1) “Operation Management Layers”............................................................................................1
2) Steps required to plan for capacity planning...........................................................................2
SECTION B.....................................................................................................................................3
1) Different techniques used for inventory planning for better planning....................................3
2) Efficient and Responsive Supply Chain Management (SCM) with the differentiations
between the tools and techniques................................................................................................4
SECTION C.....................................................................................................................................5
Analyze the case of Emirates Airlines and how the company uses Deming Cycle to attain
excellence....................................................................................................................................5
REFERENCES................................................................................................................................7
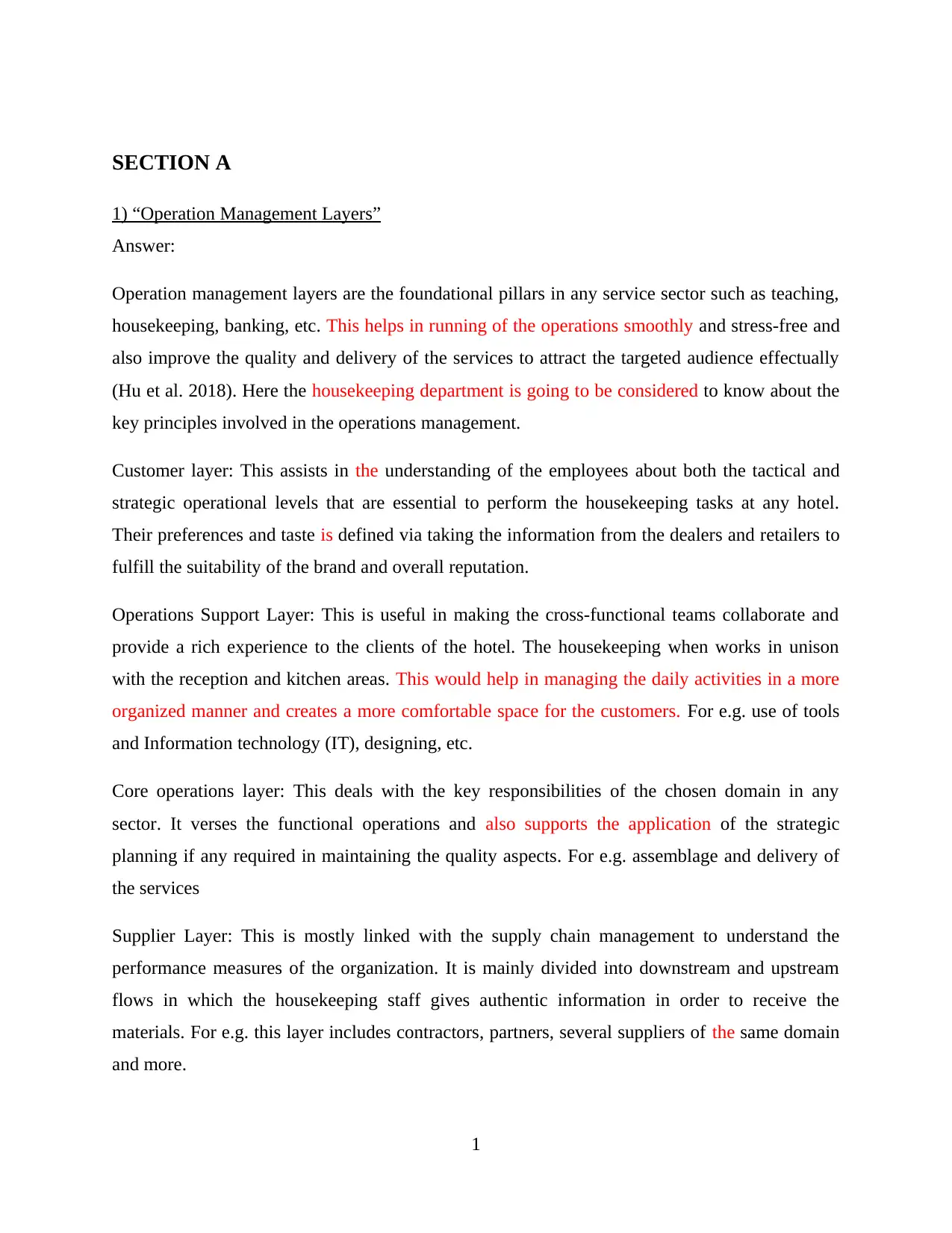
SECTION A
1) “Operation Management Layers”
Answer:
Operation management layers are the foundational pillars in any service sector such as teaching,
housekeeping, banking, etc. This helps in running of the operations smoothly and stress-free and
also improve the quality and delivery of the services to attract the targeted audience effectually
(Hu et al. 2018). Here the housekeeping department is going to be considered to know about the
key principles involved in the operations management.
Customer layer: This assists in the understanding of the employees about both the tactical and
strategic operational levels that are essential to perform the housekeeping tasks at any hotel.
Their preferences and taste is defined via taking the information from the dealers and retailers to
fulfill the suitability of the brand and overall reputation.
Operations Support Layer: This is useful in making the cross-functional teams collaborate and
provide a rich experience to the clients of the hotel. The housekeeping when works in unison
with the reception and kitchen areas. This would help in managing the daily activities in a more
organized manner and creates a more comfortable space for the customers. For e.g. use of tools
and Information technology (IT), designing, etc.
Core operations layer: This deals with the key responsibilities of the chosen domain in any
sector. It verses the functional operations and also supports the application of the strategic
planning if any required in maintaining the quality aspects. For e.g. assemblage and delivery of
the services
Supplier Layer: This is mostly linked with the supply chain management to understand the
performance measures of the organization. It is mainly divided into downstream and upstream
flows in which the housekeeping staff gives authentic information in order to receive the
materials. For e.g. this layer includes contractors, partners, several suppliers of the same domain
and more.
1
1) “Operation Management Layers”
Answer:
Operation management layers are the foundational pillars in any service sector such as teaching,
housekeeping, banking, etc. This helps in running of the operations smoothly and stress-free and
also improve the quality and delivery of the services to attract the targeted audience effectually
(Hu et al. 2018). Here the housekeeping department is going to be considered to know about the
key principles involved in the operations management.
Customer layer: This assists in the understanding of the employees about both the tactical and
strategic operational levels that are essential to perform the housekeeping tasks at any hotel.
Their preferences and taste is defined via taking the information from the dealers and retailers to
fulfill the suitability of the brand and overall reputation.
Operations Support Layer: This is useful in making the cross-functional teams collaborate and
provide a rich experience to the clients of the hotel. The housekeeping when works in unison
with the reception and kitchen areas. This would help in managing the daily activities in a more
organized manner and creates a more comfortable space for the customers. For e.g. use of tools
and Information technology (IT), designing, etc.
Core operations layer: This deals with the key responsibilities of the chosen domain in any
sector. It verses the functional operations and also supports the application of the strategic
planning if any required in maintaining the quality aspects. For e.g. assemblage and delivery of
the services
Supplier Layer: This is mostly linked with the supply chain management to understand the
performance measures of the organization. It is mainly divided into downstream and upstream
flows in which the housekeeping staff gives authentic information in order to receive the
materials. For e.g. this layer includes contractors, partners, several suppliers of the same domain
and more.
1
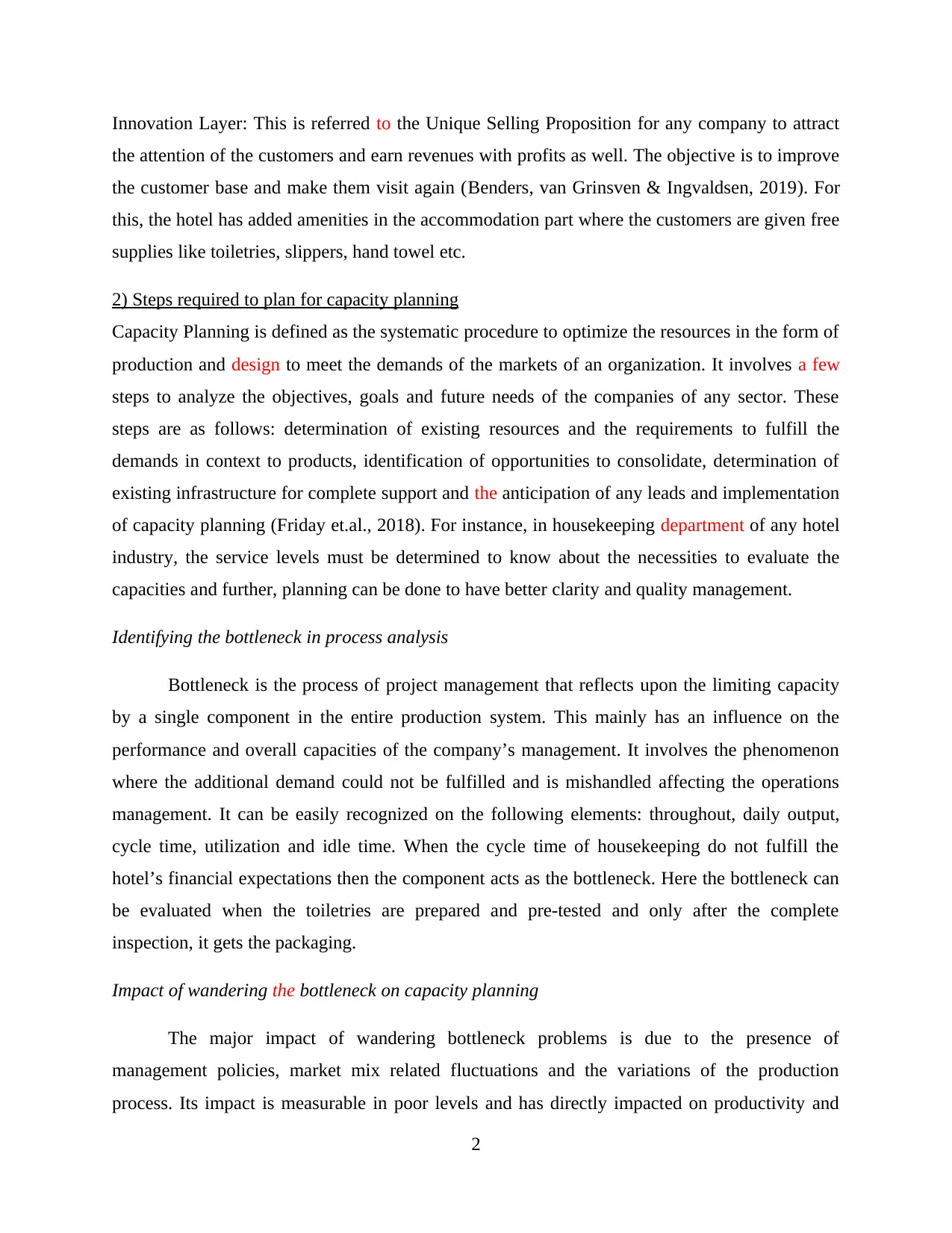
Innovation Layer: This is referred to the Unique Selling Proposition for any company to attract
the attention of the customers and earn revenues with profits as well. The objective is to improve
the customer base and make them visit again (Benders, van Grinsven & Ingvaldsen, 2019). For
this, the hotel has added amenities in the accommodation part where the customers are given free
supplies like toiletries, slippers, hand towel etc.
2) Steps required to plan for capacity planning
Capacity Planning is defined as the systematic procedure to optimize the resources in the form of
production and design to meet the demands of the markets of an organization. It involves a few
steps to analyze the objectives, goals and future needs of the companies of any sector. These
steps are as follows: determination of existing resources and the requirements to fulfill the
demands in context to products, identification of opportunities to consolidate, determination of
existing infrastructure for complete support and the anticipation of any leads and implementation
of capacity planning (Friday et.al., 2018). For instance, in housekeeping department of any hotel
industry, the service levels must be determined to know about the necessities to evaluate the
capacities and further, planning can be done to have better clarity and quality management.
Identifying the bottleneck in process analysis
Bottleneck is the process of project management that reflects upon the limiting capacity
by a single component in the entire production system. This mainly has an influence on the
performance and overall capacities of the company’s management. It involves the phenomenon
where the additional demand could not be fulfilled and is mishandled affecting the operations
management. It can be easily recognized on the following elements: throughout, daily output,
cycle time, utilization and idle time. When the cycle time of housekeeping do not fulfill the
hotel’s financial expectations then the component acts as the bottleneck. Here the bottleneck can
be evaluated when the toiletries are prepared and pre-tested and only after the complete
inspection, it gets the packaging.
Impact of wandering the bottleneck on capacity planning
The major impact of wandering bottleneck problems is due to the presence of
management policies, market mix related fluctuations and the variations of the production
process. Its impact is measurable in poor levels and has directly impacted on productivity and
2
the attention of the customers and earn revenues with profits as well. The objective is to improve
the customer base and make them visit again (Benders, van Grinsven & Ingvaldsen, 2019). For
this, the hotel has added amenities in the accommodation part where the customers are given free
supplies like toiletries, slippers, hand towel etc.
2) Steps required to plan for capacity planning
Capacity Planning is defined as the systematic procedure to optimize the resources in the form of
production and design to meet the demands of the markets of an organization. It involves a few
steps to analyze the objectives, goals and future needs of the companies of any sector. These
steps are as follows: determination of existing resources and the requirements to fulfill the
demands in context to products, identification of opportunities to consolidate, determination of
existing infrastructure for complete support and the anticipation of any leads and implementation
of capacity planning (Friday et.al., 2018). For instance, in housekeeping department of any hotel
industry, the service levels must be determined to know about the necessities to evaluate the
capacities and further, planning can be done to have better clarity and quality management.
Identifying the bottleneck in process analysis
Bottleneck is the process of project management that reflects upon the limiting capacity
by a single component in the entire production system. This mainly has an influence on the
performance and overall capacities of the company’s management. It involves the phenomenon
where the additional demand could not be fulfilled and is mishandled affecting the operations
management. It can be easily recognized on the following elements: throughout, daily output,
cycle time, utilization and idle time. When the cycle time of housekeeping do not fulfill the
hotel’s financial expectations then the component acts as the bottleneck. Here the bottleneck can
be evaluated when the toiletries are prepared and pre-tested and only after the complete
inspection, it gets the packaging.
Impact of wandering the bottleneck on capacity planning
The major impact of wandering bottleneck problems is due to the presence of
management policies, market mix related fluctuations and the variations of the production
process. Its impact is measurable in poor levels and has directly impacted on productivity and
2
Secure Best Marks with AI Grader
Need help grading? Try our AI Grader for instant feedback on your assignments.
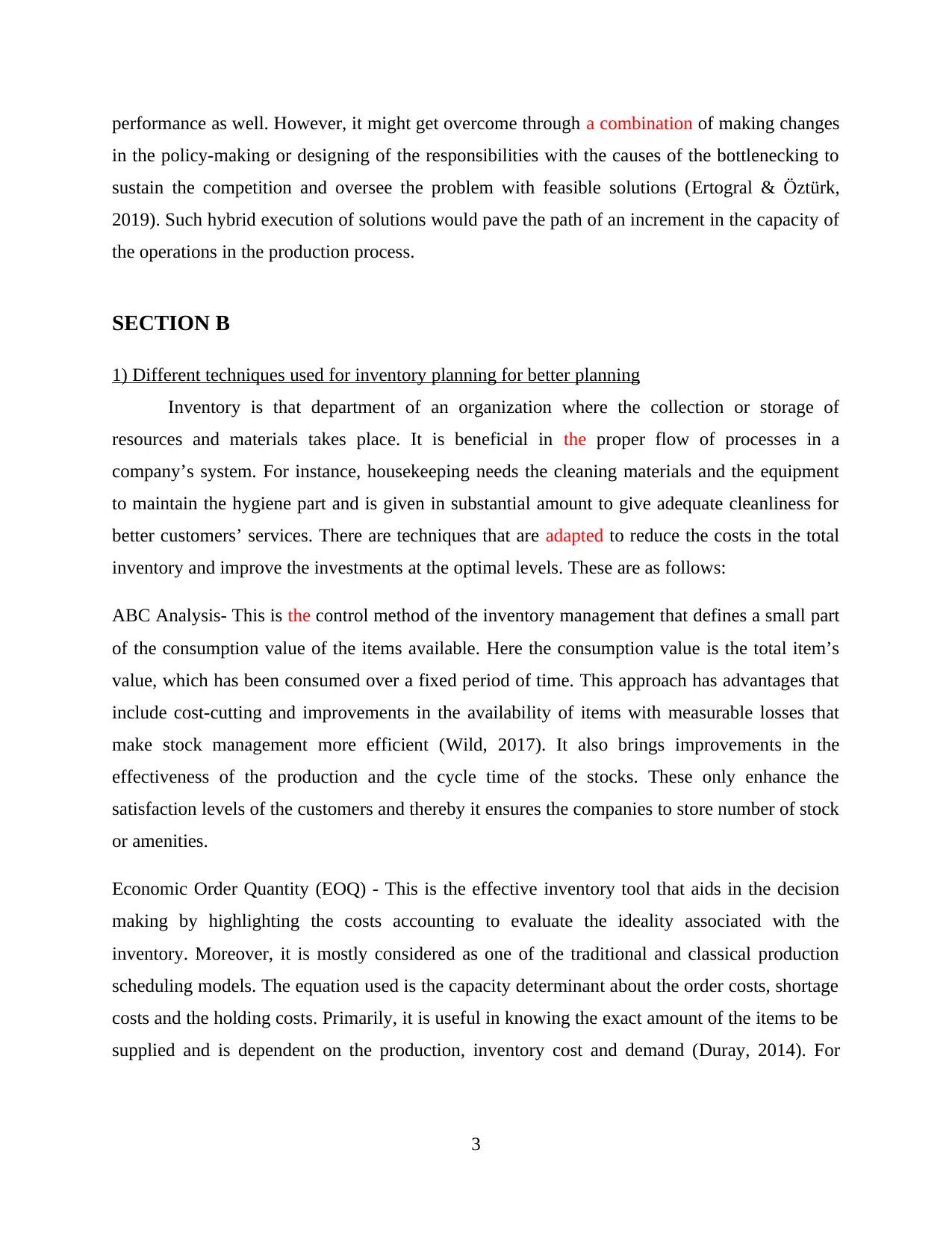
performance as well. However, it might get overcome through a combination of making changes
in the policy-making or designing of the responsibilities with the causes of the bottlenecking to
sustain the competition and oversee the problem with feasible solutions (Ertogral & Öztürk,
2019). Such hybrid execution of solutions would pave the path of an increment in the capacity of
the operations in the production process.
SECTION B
1) Different techniques used for inventory planning for better planning
Inventory is that department of an organization where the collection or storage of
resources and materials takes place. It is beneficial in the proper flow of processes in a
company’s system. For instance, housekeeping needs the cleaning materials and the equipment
to maintain the hygiene part and is given in substantial amount to give adequate cleanliness for
better customers’ services. There are techniques that are adapted to reduce the costs in the total
inventory and improve the investments at the optimal levels. These are as follows:
ABC Analysis- This is the control method of the inventory management that defines a small part
of the consumption value of the items available. Here the consumption value is the total item’s
value, which has been consumed over a fixed period of time. This approach has advantages that
include cost-cutting and improvements in the availability of items with measurable losses that
make stock management more efficient (Wild, 2017). It also brings improvements in the
effectiveness of the production and the cycle time of the stocks. These only enhance the
satisfaction levels of the customers and thereby it ensures the companies to store number of stock
or amenities.
Economic Order Quantity (EOQ) - This is the effective inventory tool that aids in the decision
making by highlighting the costs accounting to evaluate the ideality associated with the
inventory. Moreover, it is mostly considered as one of the traditional and classical production
scheduling models. The equation used is the capacity determinant about the order costs, shortage
costs and the holding costs. Primarily, it is useful in knowing the exact amount of the items to be
supplied and is dependent on the production, inventory cost and demand (Duray, 2014). For
3
in the policy-making or designing of the responsibilities with the causes of the bottlenecking to
sustain the competition and oversee the problem with feasible solutions (Ertogral & Öztürk,
2019). Such hybrid execution of solutions would pave the path of an increment in the capacity of
the operations in the production process.
SECTION B
1) Different techniques used for inventory planning for better planning
Inventory is that department of an organization where the collection or storage of
resources and materials takes place. It is beneficial in the proper flow of processes in a
company’s system. For instance, housekeeping needs the cleaning materials and the equipment
to maintain the hygiene part and is given in substantial amount to give adequate cleanliness for
better customers’ services. There are techniques that are adapted to reduce the costs in the total
inventory and improve the investments at the optimal levels. These are as follows:
ABC Analysis- This is the control method of the inventory management that defines a small part
of the consumption value of the items available. Here the consumption value is the total item’s
value, which has been consumed over a fixed period of time. This approach has advantages that
include cost-cutting and improvements in the availability of items with measurable losses that
make stock management more efficient (Wild, 2017). It also brings improvements in the
effectiveness of the production and the cycle time of the stocks. These only enhance the
satisfaction levels of the customers and thereby it ensures the companies to store number of stock
or amenities.
Economic Order Quantity (EOQ) - This is the effective inventory tool that aids in the decision
making by highlighting the costs accounting to evaluate the ideality associated with the
inventory. Moreover, it is mostly considered as one of the traditional and classical production
scheduling models. The equation used is the capacity determinant about the order costs, shortage
costs and the holding costs. Primarily, it is useful in knowing the exact amount of the items to be
supplied and is dependent on the production, inventory cost and demand (Duray, 2014). For
3
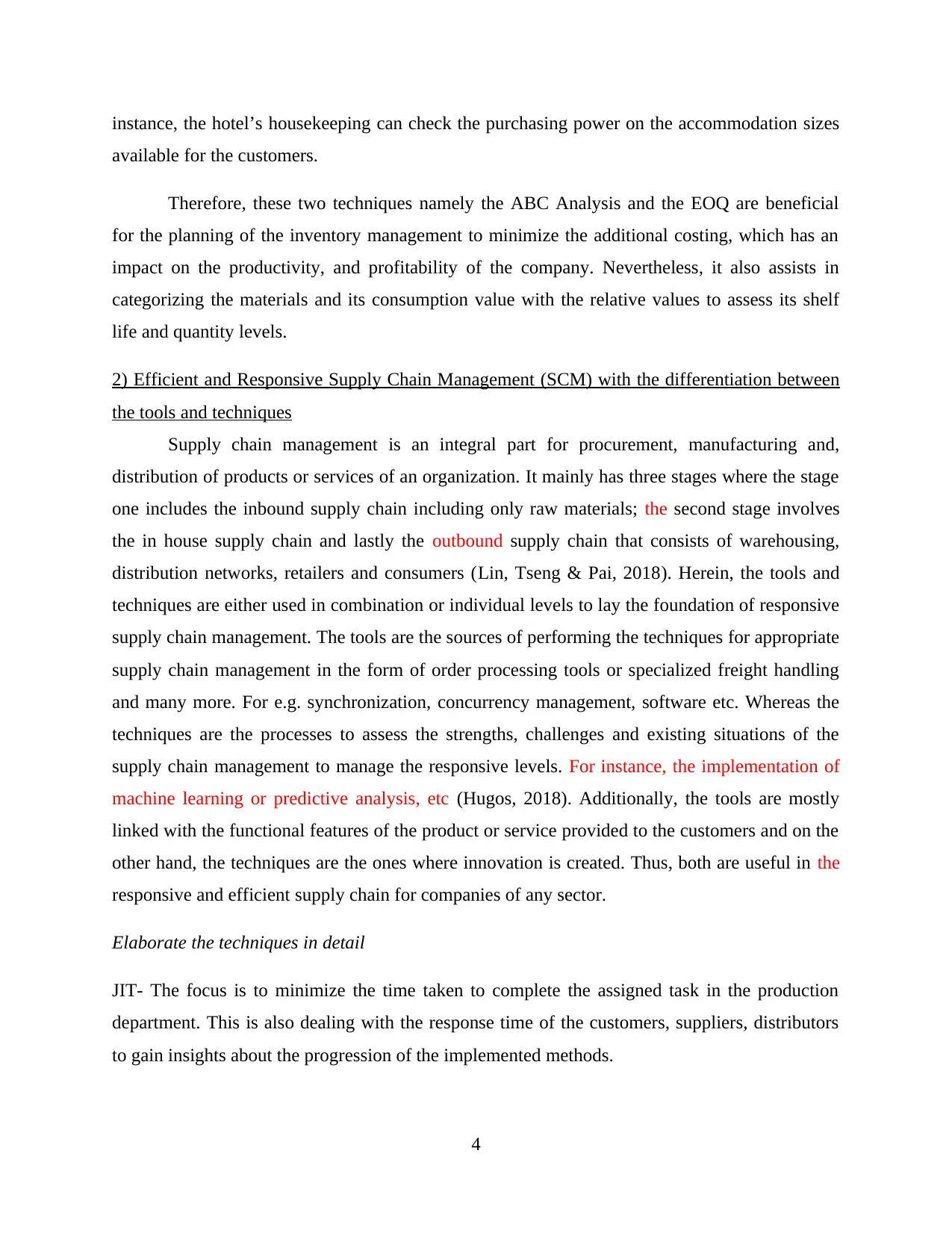
instance, the hotel’s housekeeping can check the purchasing power on the accommodation sizes
available for the customers.
Therefore, these two techniques namely the ABC Analysis and the EOQ are beneficial
for the planning of the inventory management to minimize the additional costing, which has an
impact on the productivity, and profitability of the company. Nevertheless, it also assists in
categorizing the materials and its consumption value with the relative values to assess its shelf
life and quantity levels.
2) Efficient and Responsive Supply Chain Management (SCM) with the differentiation between
the tools and techniques
Supply chain management is an integral part for procurement, manufacturing and,
distribution of products or services of an organization. It mainly has three stages where the stage
one includes the inbound supply chain including only raw materials; the second stage involves
the in house supply chain and lastly the outbound supply chain that consists of warehousing,
distribution networks, retailers and consumers (Lin, Tseng & Pai, 2018). Herein, the tools and
techniques are either used in combination or individual levels to lay the foundation of responsive
supply chain management. The tools are the sources of performing the techniques for appropriate
supply chain management in the form of order processing tools or specialized freight handling
and many more. For e.g. synchronization, concurrency management, software etc. Whereas the
techniques are the processes to assess the strengths, challenges and existing situations of the
supply chain management to manage the responsive levels. For instance, the implementation of
machine learning or predictive analysis, etc (Hugos, 2018). Additionally, the tools are mostly
linked with the functional features of the product or service provided to the customers and on the
other hand, the techniques are the ones where innovation is created. Thus, both are useful in the
responsive and efficient supply chain for companies of any sector.
Elaborate the techniques in detail
JIT- The focus is to minimize the time taken to complete the assigned task in the production
department. This is also dealing with the response time of the customers, suppliers, distributors
to gain insights about the progression of the implemented methods.
4
available for the customers.
Therefore, these two techniques namely the ABC Analysis and the EOQ are beneficial
for the planning of the inventory management to minimize the additional costing, which has an
impact on the productivity, and profitability of the company. Nevertheless, it also assists in
categorizing the materials and its consumption value with the relative values to assess its shelf
life and quantity levels.
2) Efficient and Responsive Supply Chain Management (SCM) with the differentiation between
the tools and techniques
Supply chain management is an integral part for procurement, manufacturing and,
distribution of products or services of an organization. It mainly has three stages where the stage
one includes the inbound supply chain including only raw materials; the second stage involves
the in house supply chain and lastly the outbound supply chain that consists of warehousing,
distribution networks, retailers and consumers (Lin, Tseng & Pai, 2018). Herein, the tools and
techniques are either used in combination or individual levels to lay the foundation of responsive
supply chain management. The tools are the sources of performing the techniques for appropriate
supply chain management in the form of order processing tools or specialized freight handling
and many more. For e.g. synchronization, concurrency management, software etc. Whereas the
techniques are the processes to assess the strengths, challenges and existing situations of the
supply chain management to manage the responsive levels. For instance, the implementation of
machine learning or predictive analysis, etc (Hugos, 2018). Additionally, the tools are mostly
linked with the functional features of the product or service provided to the customers and on the
other hand, the techniques are the ones where innovation is created. Thus, both are useful in the
responsive and efficient supply chain for companies of any sector.
Elaborate the techniques in detail
JIT- The focus is to minimize the time taken to complete the assigned task in the production
department. This is also dealing with the response time of the customers, suppliers, distributors
to gain insights about the progression of the implemented methods.
4
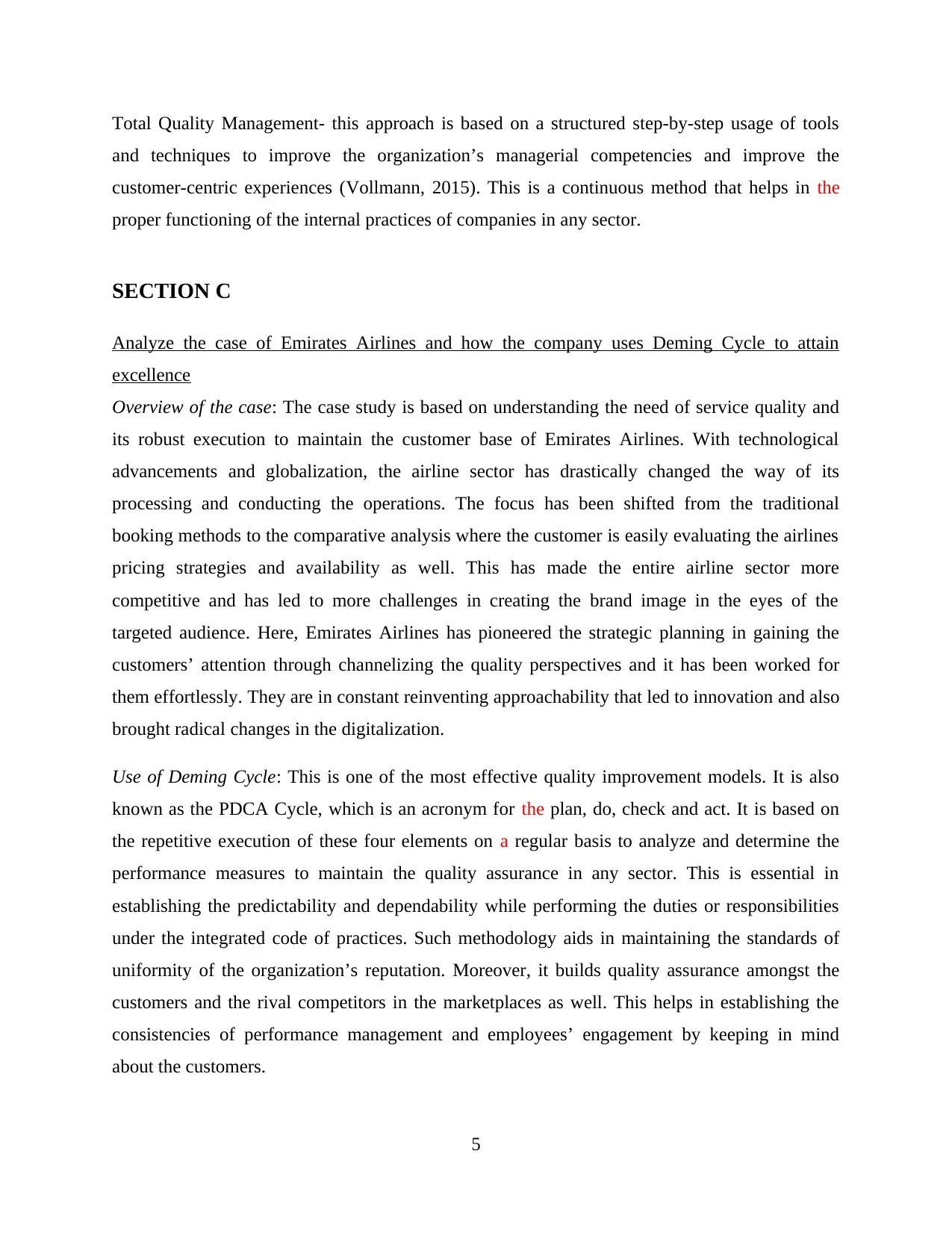
Total Quality Management- this approach is based on a structured step-by-step usage of tools
and techniques to improve the organization’s managerial competencies and improve the
customer-centric experiences (Vollmann, 2015). This is a continuous method that helps in the
proper functioning of the internal practices of companies in any sector.
SECTION C
Analyze the case of Emirates Airlines and how the company uses Deming Cycle to attain
excellence
Overview of the case: The case study is based on understanding the need of service quality and
its robust execution to maintain the customer base of Emirates Airlines. With technological
advancements and globalization, the airline sector has drastically changed the way of its
processing and conducting the operations. The focus has been shifted from the traditional
booking methods to the comparative analysis where the customer is easily evaluating the airlines
pricing strategies and availability as well. This has made the entire airline sector more
competitive and has led to more challenges in creating the brand image in the eyes of the
targeted audience. Here, Emirates Airlines has pioneered the strategic planning in gaining the
customers’ attention through channelizing the quality perspectives and it has been worked for
them effortlessly. They are in constant reinventing approachability that led to innovation and also
brought radical changes in the digitalization.
Use of Deming Cycle: This is one of the most effective quality improvement models. It is also
known as the PDCA Cycle, which is an acronym for the plan, do, check and act. It is based on
the repetitive execution of these four elements on a regular basis to analyze and determine the
performance measures to maintain the quality assurance in any sector. This is essential in
establishing the predictability and dependability while performing the duties or responsibilities
under the integrated code of practices. Such methodology aids in maintaining the standards of
uniformity of the organization’s reputation. Moreover, it builds quality assurance amongst the
customers and the rival competitors in the marketplaces as well. This helps in establishing the
consistencies of performance management and employees’ engagement by keeping in mind
about the customers.
5
and techniques to improve the organization’s managerial competencies and improve the
customer-centric experiences (Vollmann, 2015). This is a continuous method that helps in the
proper functioning of the internal practices of companies in any sector.
SECTION C
Analyze the case of Emirates Airlines and how the company uses Deming Cycle to attain
excellence
Overview of the case: The case study is based on understanding the need of service quality and
its robust execution to maintain the customer base of Emirates Airlines. With technological
advancements and globalization, the airline sector has drastically changed the way of its
processing and conducting the operations. The focus has been shifted from the traditional
booking methods to the comparative analysis where the customer is easily evaluating the airlines
pricing strategies and availability as well. This has made the entire airline sector more
competitive and has led to more challenges in creating the brand image in the eyes of the
targeted audience. Here, Emirates Airlines has pioneered the strategic planning in gaining the
customers’ attention through channelizing the quality perspectives and it has been worked for
them effortlessly. They are in constant reinventing approachability that led to innovation and also
brought radical changes in the digitalization.
Use of Deming Cycle: This is one of the most effective quality improvement models. It is also
known as the PDCA Cycle, which is an acronym for the plan, do, check and act. It is based on
the repetitive execution of these four elements on a regular basis to analyze and determine the
performance measures to maintain the quality assurance in any sector. This is essential in
establishing the predictability and dependability while performing the duties or responsibilities
under the integrated code of practices. Such methodology aids in maintaining the standards of
uniformity of the organization’s reputation. Moreover, it builds quality assurance amongst the
customers and the rival competitors in the marketplaces as well. This helps in establishing the
consistencies of performance management and employees’ engagement by keeping in mind
about the customers.
5
Paraphrase This Document
Need a fresh take? Get an instant paraphrase of this document with our AI Paraphraser
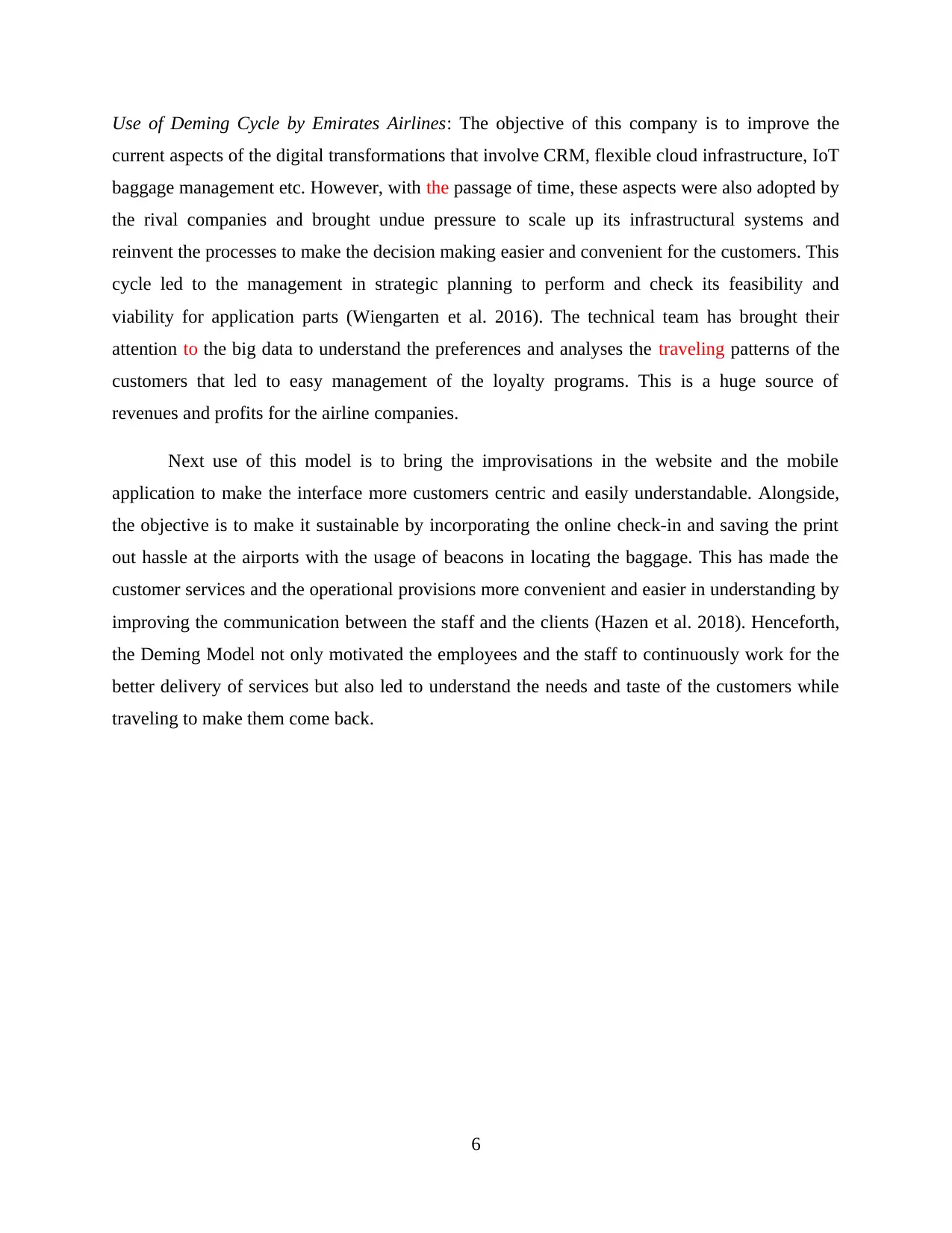
Use of Deming Cycle by Emirates Airlines: The objective of this company is to improve the
current aspects of the digital transformations that involve CRM, flexible cloud infrastructure, IoT
baggage management etc. However, with the passage of time, these aspects were also adopted by
the rival companies and brought undue pressure to scale up its infrastructural systems and
reinvent the processes to make the decision making easier and convenient for the customers. This
cycle led to the management in strategic planning to perform and check its feasibility and
viability for application parts (Wiengarten et al. 2016). The technical team has brought their
attention to the big data to understand the preferences and analyses the traveling patterns of the
customers that led to easy management of the loyalty programs. This is a huge source of
revenues and profits for the airline companies.
Next use of this model is to bring the improvisations in the website and the mobile
application to make the interface more customers centric and easily understandable. Alongside,
the objective is to make it sustainable by incorporating the online check-in and saving the print
out hassle at the airports with the usage of beacons in locating the baggage. This has made the
customer services and the operational provisions more convenient and easier in understanding by
improving the communication between the staff and the clients (Hazen et al. 2018). Henceforth,
the Deming Model not only motivated the employees and the staff to continuously work for the
better delivery of services but also led to understand the needs and taste of the customers while
traveling to make them come back.
6
current aspects of the digital transformations that involve CRM, flexible cloud infrastructure, IoT
baggage management etc. However, with the passage of time, these aspects were also adopted by
the rival companies and brought undue pressure to scale up its infrastructural systems and
reinvent the processes to make the decision making easier and convenient for the customers. This
cycle led to the management in strategic planning to perform and check its feasibility and
viability for application parts (Wiengarten et al. 2016). The technical team has brought their
attention to the big data to understand the preferences and analyses the traveling patterns of the
customers that led to easy management of the loyalty programs. This is a huge source of
revenues and profits for the airline companies.
Next use of this model is to bring the improvisations in the website and the mobile
application to make the interface more customers centric and easily understandable. Alongside,
the objective is to make it sustainable by incorporating the online check-in and saving the print
out hassle at the airports with the usage of beacons in locating the baggage. This has made the
customer services and the operational provisions more convenient and easier in understanding by
improving the communication between the staff and the clients (Hazen et al. 2018). Henceforth,
the Deming Model not only motivated the employees and the staff to continuously work for the
better delivery of services but also led to understand the needs and taste of the customers while
traveling to make them come back.
6
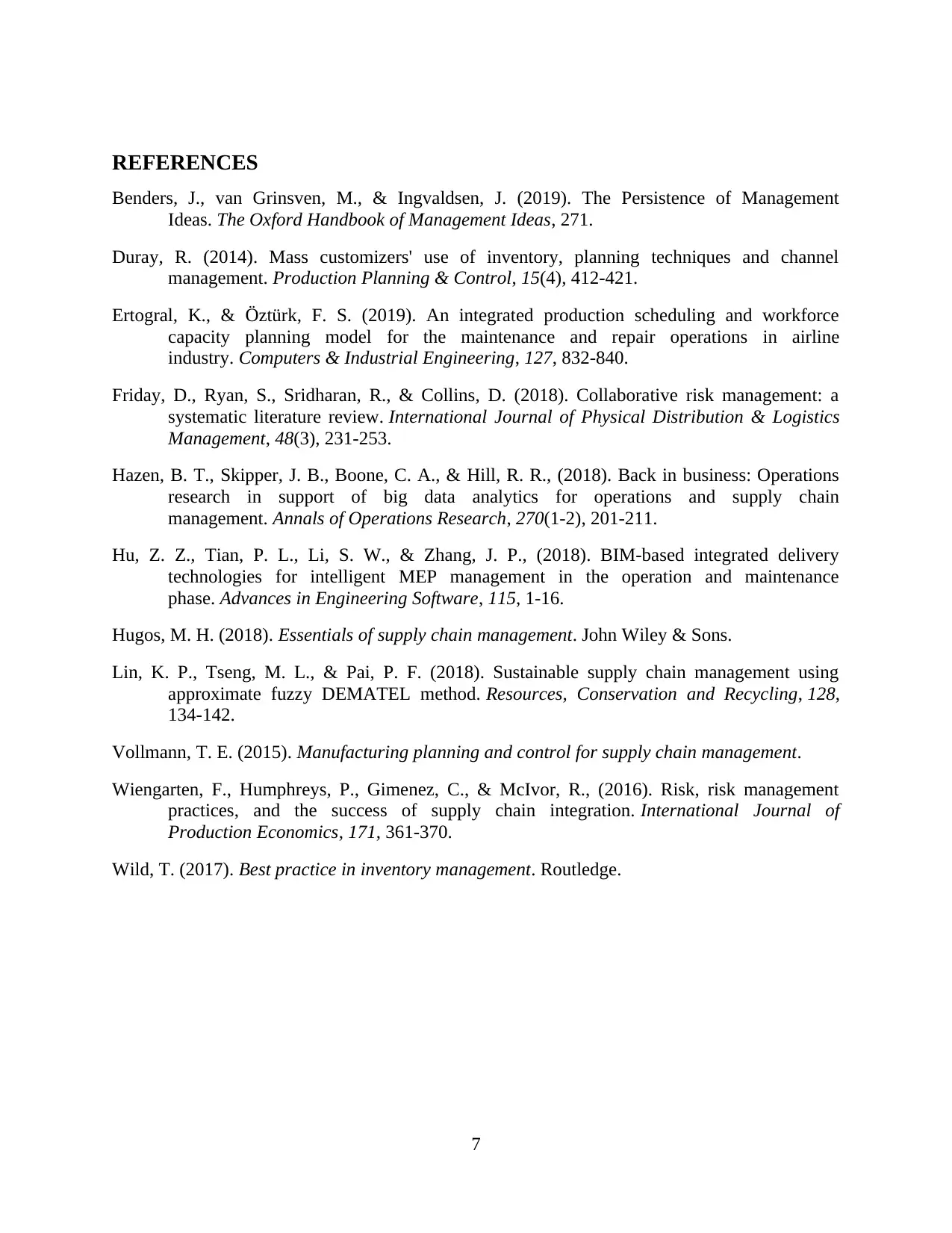
REFERENCES
Benders, J., van Grinsven, M., & Ingvaldsen, J. (2019). The Persistence of Management
Ideas. The Oxford Handbook of Management Ideas, 271.
Duray, R. (2014). Mass customizers' use of inventory, planning techniques and channel
management. Production Planning & Control, 15(4), 412-421.
Ertogral, K., & Öztürk, F. S. (2019). An integrated production scheduling and workforce
capacity planning model for the maintenance and repair operations in airline
industry. Computers & Industrial Engineering, 127, 832-840.
Friday, D., Ryan, S., Sridharan, R., & Collins, D. (2018). Collaborative risk management: a
systematic literature review. International Journal of Physical Distribution & Logistics
Management, 48(3), 231-253.
Hazen, B. T., Skipper, J. B., Boone, C. A., & Hill, R. R., (2018). Back in business: Operations
research in support of big data analytics for operations and supply chain
management. Annals of Operations Research, 270(1-2), 201-211.
Hu, Z. Z., Tian, P. L., Li, S. W., & Zhang, J. P., (2018). BIM-based integrated delivery
technologies for intelligent MEP management in the operation and maintenance
phase. Advances in Engineering Software, 115, 1-16.
Hugos, M. H. (2018). Essentials of supply chain management. John Wiley & Sons.
Lin, K. P., Tseng, M. L., & Pai, P. F. (2018). Sustainable supply chain management using
approximate fuzzy DEMATEL method. Resources, Conservation and Recycling, 128,
134-142.
Vollmann, T. E. (2015). Manufacturing planning and control for supply chain management.
Wiengarten, F., Humphreys, P., Gimenez, C., & McIvor, R., (2016). Risk, risk management
practices, and the success of supply chain integration. International Journal of
Production Economics, 171, 361-370.
Wild, T. (2017). Best practice in inventory management. Routledge.
7
Benders, J., van Grinsven, M., & Ingvaldsen, J. (2019). The Persistence of Management
Ideas. The Oxford Handbook of Management Ideas, 271.
Duray, R. (2014). Mass customizers' use of inventory, planning techniques and channel
management. Production Planning & Control, 15(4), 412-421.
Ertogral, K., & Öztürk, F. S. (2019). An integrated production scheduling and workforce
capacity planning model for the maintenance and repair operations in airline
industry. Computers & Industrial Engineering, 127, 832-840.
Friday, D., Ryan, S., Sridharan, R., & Collins, D. (2018). Collaborative risk management: a
systematic literature review. International Journal of Physical Distribution & Logistics
Management, 48(3), 231-253.
Hazen, B. T., Skipper, J. B., Boone, C. A., & Hill, R. R., (2018). Back in business: Operations
research in support of big data analytics for operations and supply chain
management. Annals of Operations Research, 270(1-2), 201-211.
Hu, Z. Z., Tian, P. L., Li, S. W., & Zhang, J. P., (2018). BIM-based integrated delivery
technologies for intelligent MEP management in the operation and maintenance
phase. Advances in Engineering Software, 115, 1-16.
Hugos, M. H. (2018). Essentials of supply chain management. John Wiley & Sons.
Lin, K. P., Tseng, M. L., & Pai, P. F. (2018). Sustainable supply chain management using
approximate fuzzy DEMATEL method. Resources, Conservation and Recycling, 128,
134-142.
Vollmann, T. E. (2015). Manufacturing planning and control for supply chain management.
Wiengarten, F., Humphreys, P., Gimenez, C., & McIvor, R., (2016). Risk, risk management
practices, and the success of supply chain integration. International Journal of
Production Economics, 171, 361-370.
Wild, T. (2017). Best practice in inventory management. Routledge.
7
1 out of 9
Related Documents
![[object Object]](/_next/image/?url=%2F_next%2Fstatic%2Fmedia%2Flogo.6d15ce61.png&w=640&q=75)
Your All-in-One AI-Powered Toolkit for Academic Success.
+13062052269
info@desklib.com
Available 24*7 on WhatsApp / Email
Unlock your academic potential
© 2024 | Zucol Services PVT LTD | All rights reserved.