Case Study on Operational Management by Eljet Printing
VerifiedAdded on 2022/07/21
|28
|7832
|25
AI Summary
This case study is an analysis of the current situation of operations of Eljet Printing and Services, a t-shirt printing service provider at Guimbal, Iloilo, through identifying the business’ transformation process, competitiveness, and design as well as its production/operations process. We will also be looking into the supply chain and location strategy of Eljet Printing and Services to see how effective it is. With the help of operation management theories and techniques, we intend to identify points of improvement within the business.
Contribute Materials
Your contribution can guide someone’s learning journey. Share your
documents today.
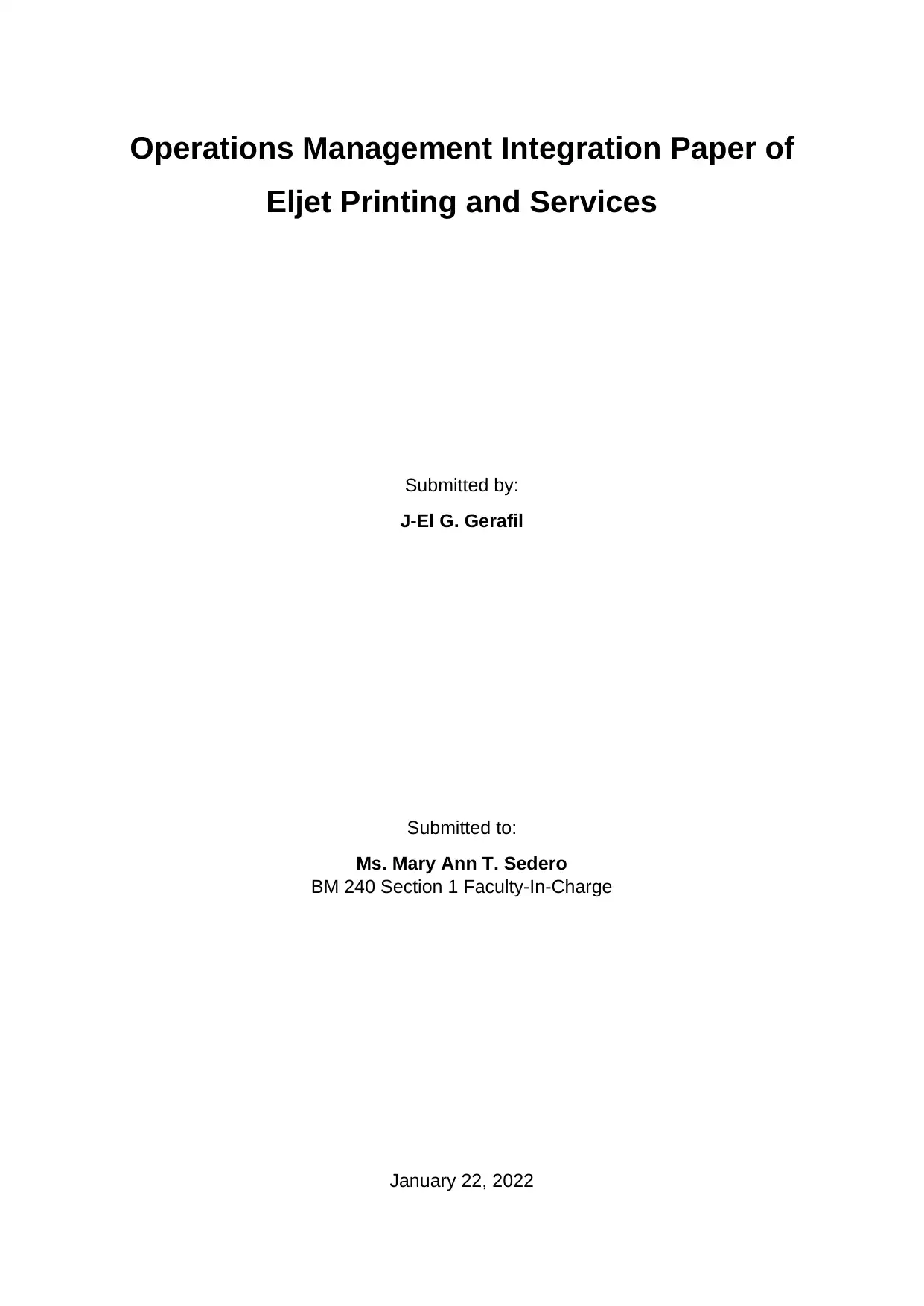
Operations Management Integration Paper of
Eljet Printing and Services
Submitted by:
J-El G. Gerafil
Submitted to:
Ms. Mary Ann T. Sedero
BM 240 Section 1 Faculty-In-Charge
January 22, 2022
Eljet Printing and Services
Submitted by:
J-El G. Gerafil
Submitted to:
Ms. Mary Ann T. Sedero
BM 240 Section 1 Faculty-In-Charge
January 22, 2022
Secure Best Marks with AI Grader
Need help grading? Try our AI Grader for instant feedback on your assignments.
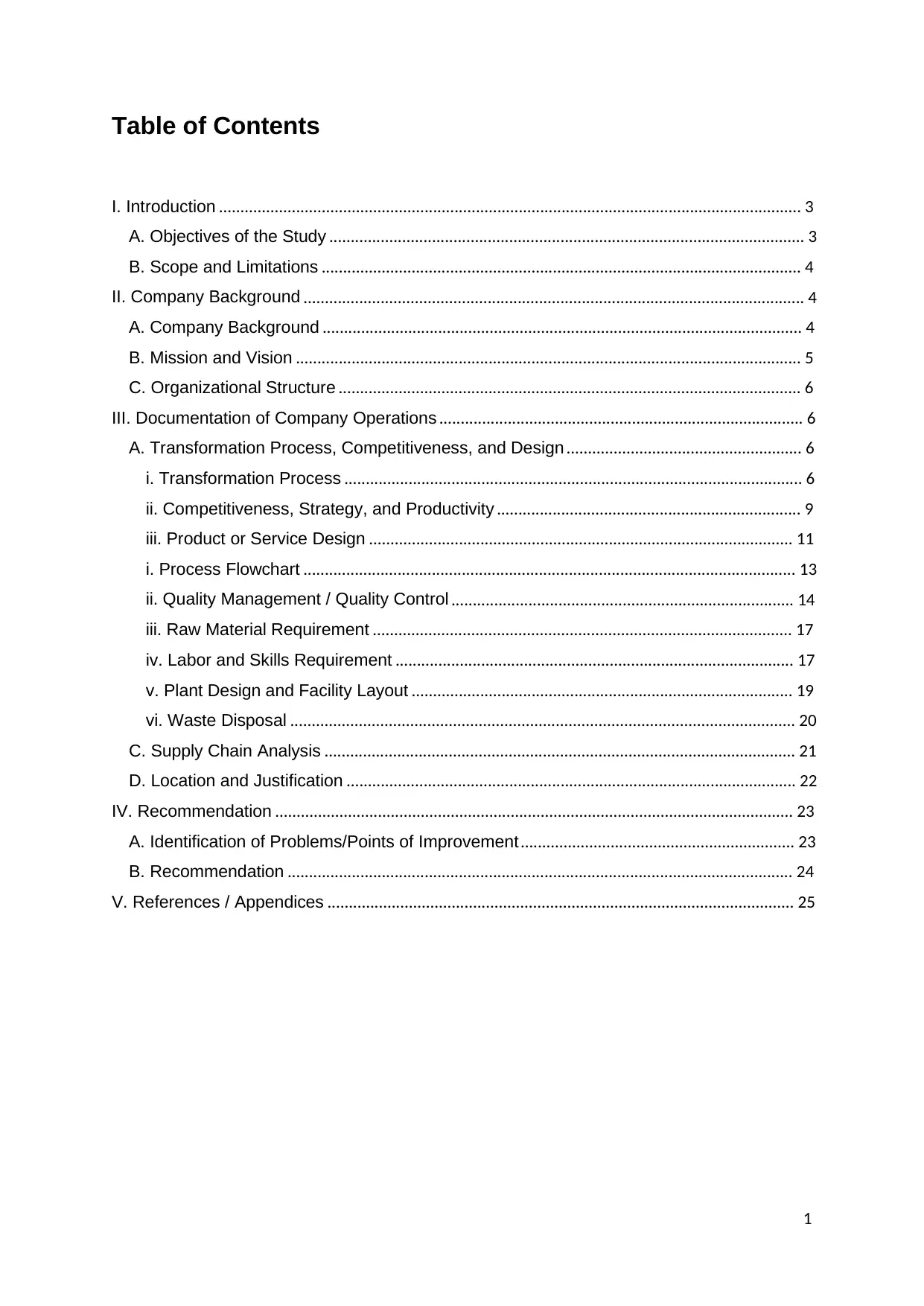
1
Table of Contents
I. Introduction ........................................................................................................................................ 3
A. Objectives of the Study ............................................................................................................... 3
B. Scope and Limitations ................................................................................................................ 4
II. Company Background ..................................................................................................................... 4
A. Company Background ................................................................................................................ 4
B. Mission and Vision ...................................................................................................................... 5
C. Organizational Structure ............................................................................................................ 6
III. Documentation of Company Operations ..................................................................................... 6
A. Transformation Process, Competitiveness, and Design ....................................................... 6
i. Transformation Process ........................................................................................................... 6
ii. Competitiveness, Strategy, and Productivity ....................................................................... 9
iii. Product or Service Design ................................................................................................... 11
i. Process Flowchart ................................................................................................................... 13
ii. Quality Management / Quality Control ................................................................................ 14
iii. Raw Material Requirement .................................................................................................. 17
iv. Labor and Skills Requirement ............................................................................................. 17
v. Plant Design and Facility Layout ......................................................................................... 19
vi. Waste Disposal ...................................................................................................................... 20
C. Supply Chain Analysis .............................................................................................................. 21
D. Location and Justification ......................................................................................................... 22
IV. Recommendation ......................................................................................................................... 23
A. Identification of Problems/Points of Improvement ................................................................ 23
B. Recommendation ...................................................................................................................... 24
V. References / Appendices ............................................................................................................. 25
Table of Contents
I. Introduction ........................................................................................................................................ 3
A. Objectives of the Study ............................................................................................................... 3
B. Scope and Limitations ................................................................................................................ 4
II. Company Background ..................................................................................................................... 4
A. Company Background ................................................................................................................ 4
B. Mission and Vision ...................................................................................................................... 5
C. Organizational Structure ............................................................................................................ 6
III. Documentation of Company Operations ..................................................................................... 6
A. Transformation Process, Competitiveness, and Design ....................................................... 6
i. Transformation Process ........................................................................................................... 6
ii. Competitiveness, Strategy, and Productivity ....................................................................... 9
iii. Product or Service Design ................................................................................................... 11
i. Process Flowchart ................................................................................................................... 13
ii. Quality Management / Quality Control ................................................................................ 14
iii. Raw Material Requirement .................................................................................................. 17
iv. Labor and Skills Requirement ............................................................................................. 17
v. Plant Design and Facility Layout ......................................................................................... 19
vi. Waste Disposal ...................................................................................................................... 20
C. Supply Chain Analysis .............................................................................................................. 21
D. Location and Justification ......................................................................................................... 22
IV. Recommendation ......................................................................................................................... 23
A. Identification of Problems/Points of Improvement ................................................................ 23
B. Recommendation ...................................................................................................................... 24
V. References / Appendices ............................................................................................................. 25
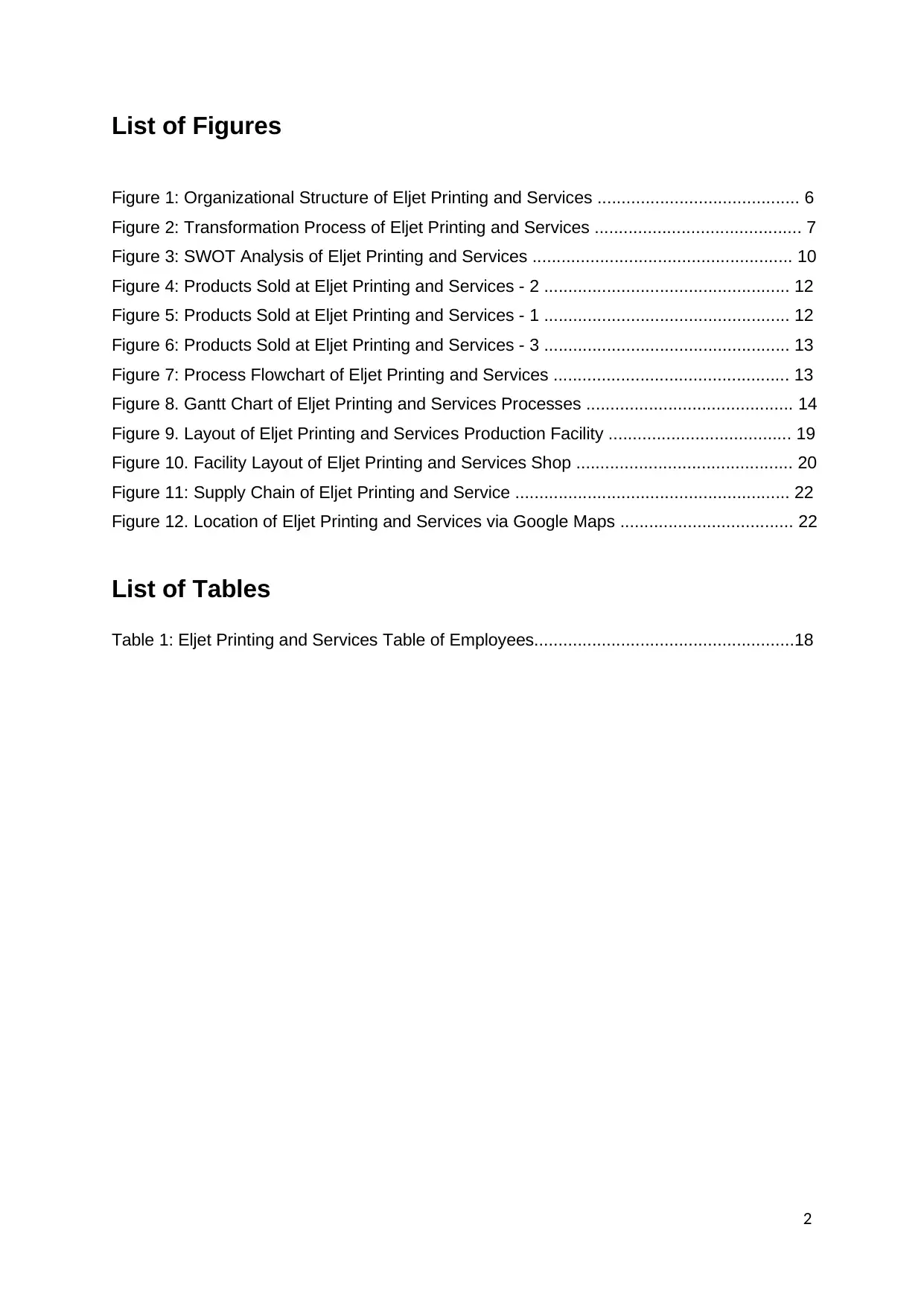
2
List of Figures
Figure 1: Organizational Structure of Eljet Printing and Services .......................................... 6
Figure 2: Transformation Process of Eljet Printing and Services ........................................... 7
Figure 3: SWOT Analysis of Eljet Printing and Services ...................................................... 10
Figure 4: Products Sold at Eljet Printing and Services - 2 ................................................... 12
Figure 5: Products Sold at Eljet Printing and Services - 1 ................................................... 12
Figure 6: Products Sold at Eljet Printing and Services - 3 ................................................... 13
Figure 7: Process Flowchart of Eljet Printing and Services ................................................. 13
Figure 8. Gantt Chart of Eljet Printing and Services Processes ........................................... 14
Figure 9. Layout of Eljet Printing and Services Production Facility ...................................... 19
Figure 10. Facility Layout of Eljet Printing and Services Shop ............................................. 20
Figure 11: Supply Chain of Eljet Printing and Service ......................................................... 22
Figure 12. Location of Eljet Printing and Services via Google Maps .................................... 22
List of Tables
Table 1: Eljet Printing and Services Table of Employees......................................................18
List of Figures
Figure 1: Organizational Structure of Eljet Printing and Services .......................................... 6
Figure 2: Transformation Process of Eljet Printing and Services ........................................... 7
Figure 3: SWOT Analysis of Eljet Printing and Services ...................................................... 10
Figure 4: Products Sold at Eljet Printing and Services - 2 ................................................... 12
Figure 5: Products Sold at Eljet Printing and Services - 1 ................................................... 12
Figure 6: Products Sold at Eljet Printing and Services - 3 ................................................... 13
Figure 7: Process Flowchart of Eljet Printing and Services ................................................. 13
Figure 8. Gantt Chart of Eljet Printing and Services Processes ........................................... 14
Figure 9. Layout of Eljet Printing and Services Production Facility ...................................... 19
Figure 10. Facility Layout of Eljet Printing and Services Shop ............................................. 20
Figure 11: Supply Chain of Eljet Printing and Service ......................................................... 22
Figure 12. Location of Eljet Printing and Services via Google Maps .................................... 22
List of Tables
Table 1: Eljet Printing and Services Table of Employees......................................................18
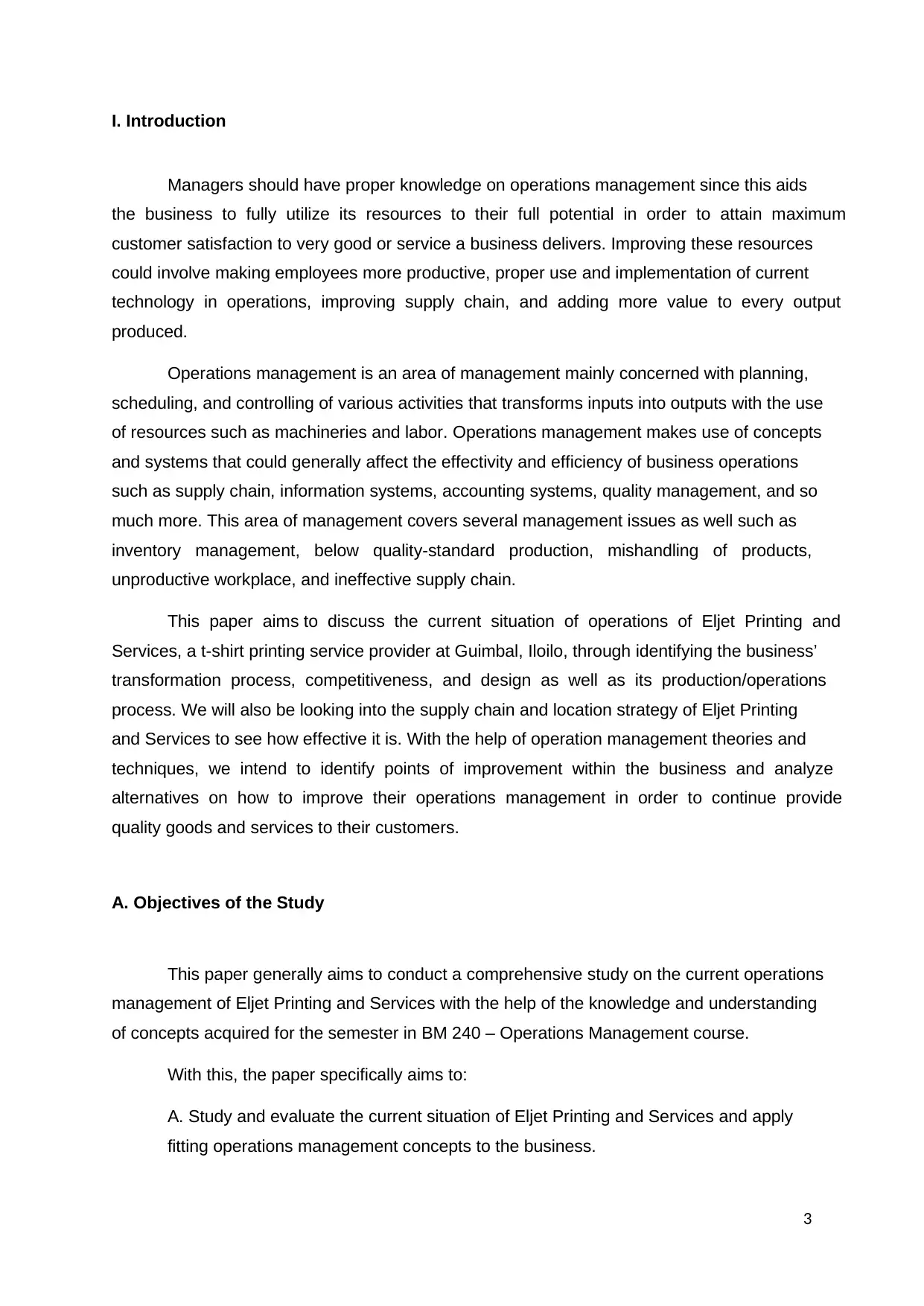
3
I. Introduction
Managers should have proper knowledge on operations management since this aids
the business to fully utilize its resources to their full potential in order to attain maximum
customer satisfaction to very good or service a business delivers. Improving these resources
could involve making employees more productive, proper use and implementation of current
technology in operations, improving supply chain, and adding more value to every output
produced.
Operations management is an area of management mainly concerned with planning,
scheduling, and controlling of various activities that transforms inputs into outputs with the use
of resources such as machineries and labor. Operations management makes use of concepts
and systems that could generally affect the effectivity and efficiency of business operations
such as supply chain, information systems, accounting systems, quality management, and so
much more. This area of management covers several management issues as well such as
inventory management, below quality-standard production, mishandling of products,
unproductive workplace, and ineffective supply chain.
This paper aims to discuss the current situation of operations of Eljet Printing and
Services, a t-shirt printing service provider at Guimbal, Iloilo, through identifying the business’
transformation process, competitiveness, and design as well as its production/operations
process. We will also be looking into the supply chain and location strategy of Eljet Printing
and Services to see how effective it is. With the help of operation management theories and
techniques, we intend to identify points of improvement within the business and analyze
alternatives on how to improve their operations management in order to continue provide
quality goods and services to their customers.
A. Objectives of the Study
This paper generally aims to conduct a comprehensive study on the current operations
management of Eljet Printing and Services with the help of the knowledge and understanding
of concepts acquired for the semester in BM 240 – Operations Management course.
With this, the paper specifically aims to:
A. Study and evaluate the current situation of Eljet Printing and Services and apply
fitting operations management concepts to the business.
I. Introduction
Managers should have proper knowledge on operations management since this aids
the business to fully utilize its resources to their full potential in order to attain maximum
customer satisfaction to very good or service a business delivers. Improving these resources
could involve making employees more productive, proper use and implementation of current
technology in operations, improving supply chain, and adding more value to every output
produced.
Operations management is an area of management mainly concerned with planning,
scheduling, and controlling of various activities that transforms inputs into outputs with the use
of resources such as machineries and labor. Operations management makes use of concepts
and systems that could generally affect the effectivity and efficiency of business operations
such as supply chain, information systems, accounting systems, quality management, and so
much more. This area of management covers several management issues as well such as
inventory management, below quality-standard production, mishandling of products,
unproductive workplace, and ineffective supply chain.
This paper aims to discuss the current situation of operations of Eljet Printing and
Services, a t-shirt printing service provider at Guimbal, Iloilo, through identifying the business’
transformation process, competitiveness, and design as well as its production/operations
process. We will also be looking into the supply chain and location strategy of Eljet Printing
and Services to see how effective it is. With the help of operation management theories and
techniques, we intend to identify points of improvement within the business and analyze
alternatives on how to improve their operations management in order to continue provide
quality goods and services to their customers.
A. Objectives of the Study
This paper generally aims to conduct a comprehensive study on the current operations
management of Eljet Printing and Services with the help of the knowledge and understanding
of concepts acquired for the semester in BM 240 – Operations Management course.
With this, the paper specifically aims to:
A. Study and evaluate the current situation of Eljet Printing and Services and apply
fitting operations management concepts to the business.
Secure Best Marks with AI Grader
Need help grading? Try our AI Grader for instant feedback on your assignments.
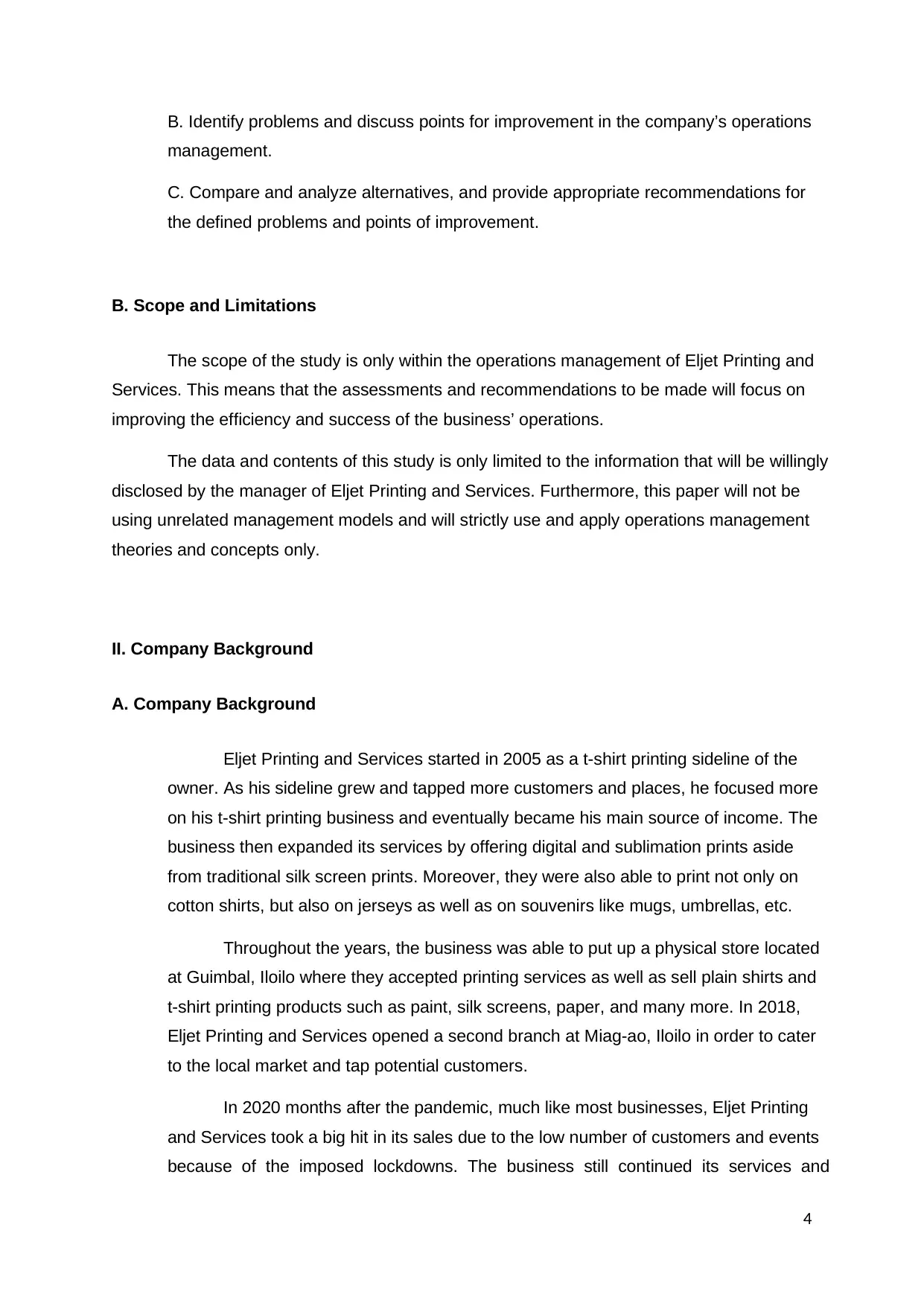
4
B. Identify problems and discuss points for improvement in the company’s operations
management.
C. Compare and analyze alternatives, and provide appropriate recommendations for
the defined problems and points of improvement.
B. Scope and Limitations
The scope of the study is only within the operations management of Eljet Printing and
Services. This means that the assessments and recommendations to be made will focus on
improving the efficiency and success of the business’ operations.
The data and contents of this study is only limited to the information that will be willingly
disclosed by the manager of Eljet Printing and Services. Furthermore, this paper will not be
using unrelated management models and will strictly use and apply operations management
theories and concepts only.
II. Company Background
A. Company Background
Eljet Printing and Services started in 2005 as a t-shirt printing sideline of the
owner. As his sideline grew and tapped more customers and places, he focused more
on his t-shirt printing business and eventually became his main source of income. The
business then expanded its services by offering digital and sublimation prints aside
from traditional silk screen prints. Moreover, they were also able to print not only on
cotton shirts, but also on jerseys as well as on souvenirs like mugs, umbrellas, etc.
Throughout the years, the business was able to put up a physical store located
at Guimbal, Iloilo where they accepted printing services as well as sell plain shirts and
t-shirt printing products such as paint, silk screens, paper, and many more. In 2018,
Eljet Printing and Services opened a second branch at Miag-ao, Iloilo in order to cater
to the local market and tap potential customers.
In 2020 months after the pandemic, much like most businesses, Eljet Printing
and Services took a big hit in its sales due to the low number of customers and events
because of the imposed lockdowns. The business still continued its services and
B. Identify problems and discuss points for improvement in the company’s operations
management.
C. Compare and analyze alternatives, and provide appropriate recommendations for
the defined problems and points of improvement.
B. Scope and Limitations
The scope of the study is only within the operations management of Eljet Printing and
Services. This means that the assessments and recommendations to be made will focus on
improving the efficiency and success of the business’ operations.
The data and contents of this study is only limited to the information that will be willingly
disclosed by the manager of Eljet Printing and Services. Furthermore, this paper will not be
using unrelated management models and will strictly use and apply operations management
theories and concepts only.
II. Company Background
A. Company Background
Eljet Printing and Services started in 2005 as a t-shirt printing sideline of the
owner. As his sideline grew and tapped more customers and places, he focused more
on his t-shirt printing business and eventually became his main source of income. The
business then expanded its services by offering digital and sublimation prints aside
from traditional silk screen prints. Moreover, they were also able to print not only on
cotton shirts, but also on jerseys as well as on souvenirs like mugs, umbrellas, etc.
Throughout the years, the business was able to put up a physical store located
at Guimbal, Iloilo where they accepted printing services as well as sell plain shirts and
t-shirt printing products such as paint, silk screens, paper, and many more. In 2018,
Eljet Printing and Services opened a second branch at Miag-ao, Iloilo in order to cater
to the local market and tap potential customers.
In 2020 months after the pandemic, much like most businesses, Eljet Printing
and Services took a big hit in its sales due to the low number of customers and events
because of the imposed lockdowns. The business still continued its services and
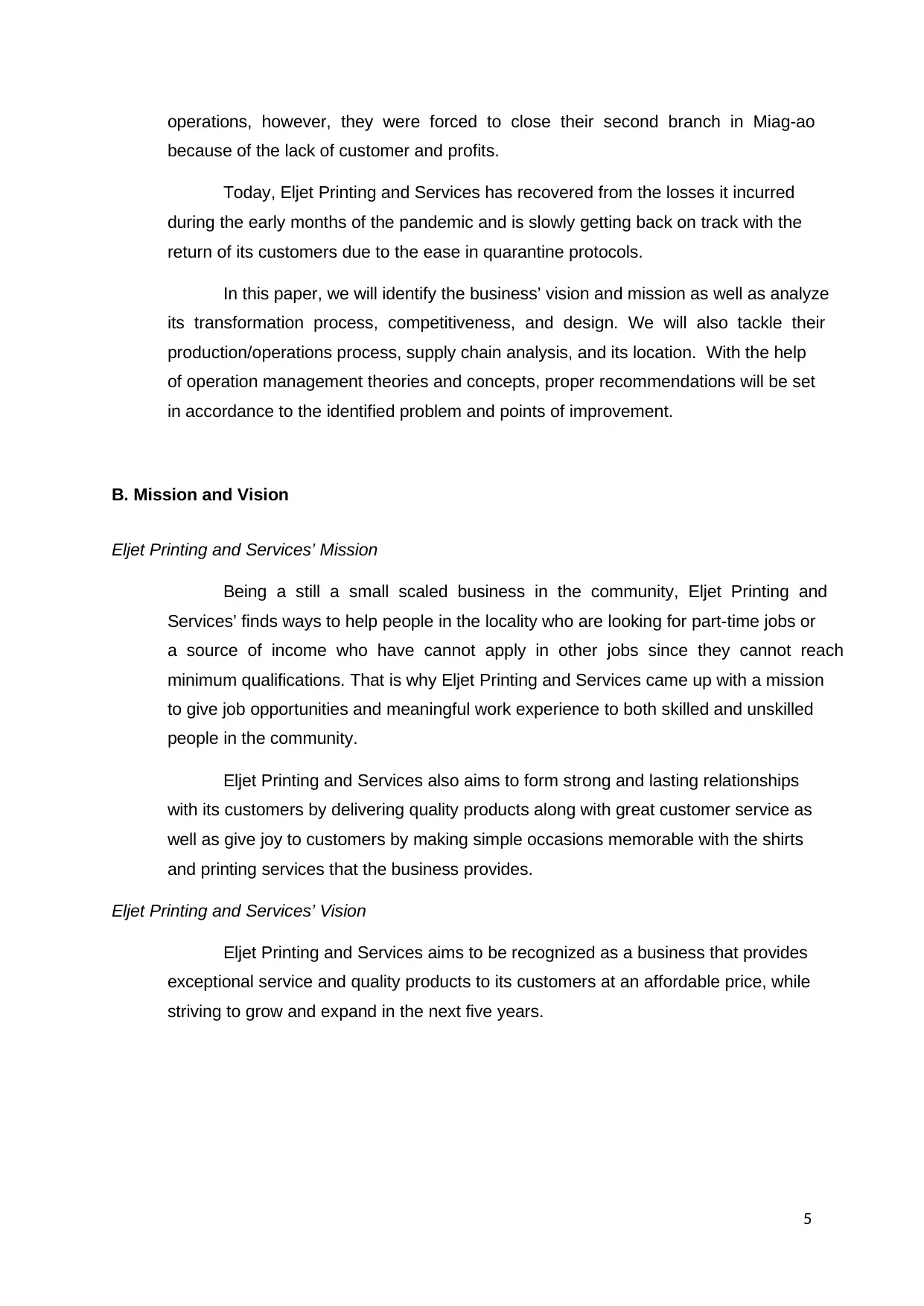
5
operations, however, they were forced to close their second branch in Miag-ao
because of the lack of customer and profits.
Today, Eljet Printing and Services has recovered from the losses it incurred
during the early months of the pandemic and is slowly getting back on track with the
return of its customers due to the ease in quarantine protocols.
In this paper, we will identify the business’ vision and mission as well as analyze
its transformation process, competitiveness, and design. We will also tackle their
production/operations process, supply chain analysis, and its location. With the help
of operation management theories and concepts, proper recommendations will be set
in accordance to the identified problem and points of improvement.
B. Mission and Vision
Eljet Printing and Services’ Mission
Being a still a small scaled business in the community, Eljet Printing and
Services’ finds ways to help people in the locality who are looking for part-time jobs or
a source of income who have cannot apply in other jobs since they cannot reach
minimum qualifications. That is why Eljet Printing and Services came up with a mission
to give job opportunities and meaningful work experience to both skilled and unskilled
people in the community.
Eljet Printing and Services also aims to form strong and lasting relationships
with its customers by delivering quality products along with great customer service as
well as give joy to customers by making simple occasions memorable with the shirts
and printing services that the business provides.
Eljet Printing and Services’ Vision
Eljet Printing and Services aims to be recognized as a business that provides
exceptional service and quality products to its customers at an affordable price, while
striving to grow and expand in the next five years.
operations, however, they were forced to close their second branch in Miag-ao
because of the lack of customer and profits.
Today, Eljet Printing and Services has recovered from the losses it incurred
during the early months of the pandemic and is slowly getting back on track with the
return of its customers due to the ease in quarantine protocols.
In this paper, we will identify the business’ vision and mission as well as analyze
its transformation process, competitiveness, and design. We will also tackle their
production/operations process, supply chain analysis, and its location. With the help
of operation management theories and concepts, proper recommendations will be set
in accordance to the identified problem and points of improvement.
B. Mission and Vision
Eljet Printing and Services’ Mission
Being a still a small scaled business in the community, Eljet Printing and
Services’ finds ways to help people in the locality who are looking for part-time jobs or
a source of income who have cannot apply in other jobs since they cannot reach
minimum qualifications. That is why Eljet Printing and Services came up with a mission
to give job opportunities and meaningful work experience to both skilled and unskilled
people in the community.
Eljet Printing and Services also aims to form strong and lasting relationships
with its customers by delivering quality products along with great customer service as
well as give joy to customers by making simple occasions memorable with the shirts
and printing services that the business provides.
Eljet Printing and Services’ Vision
Eljet Printing and Services aims to be recognized as a business that provides
exceptional service and quality products to its customers at an affordable price, while
striving to grow and expand in the next five years.
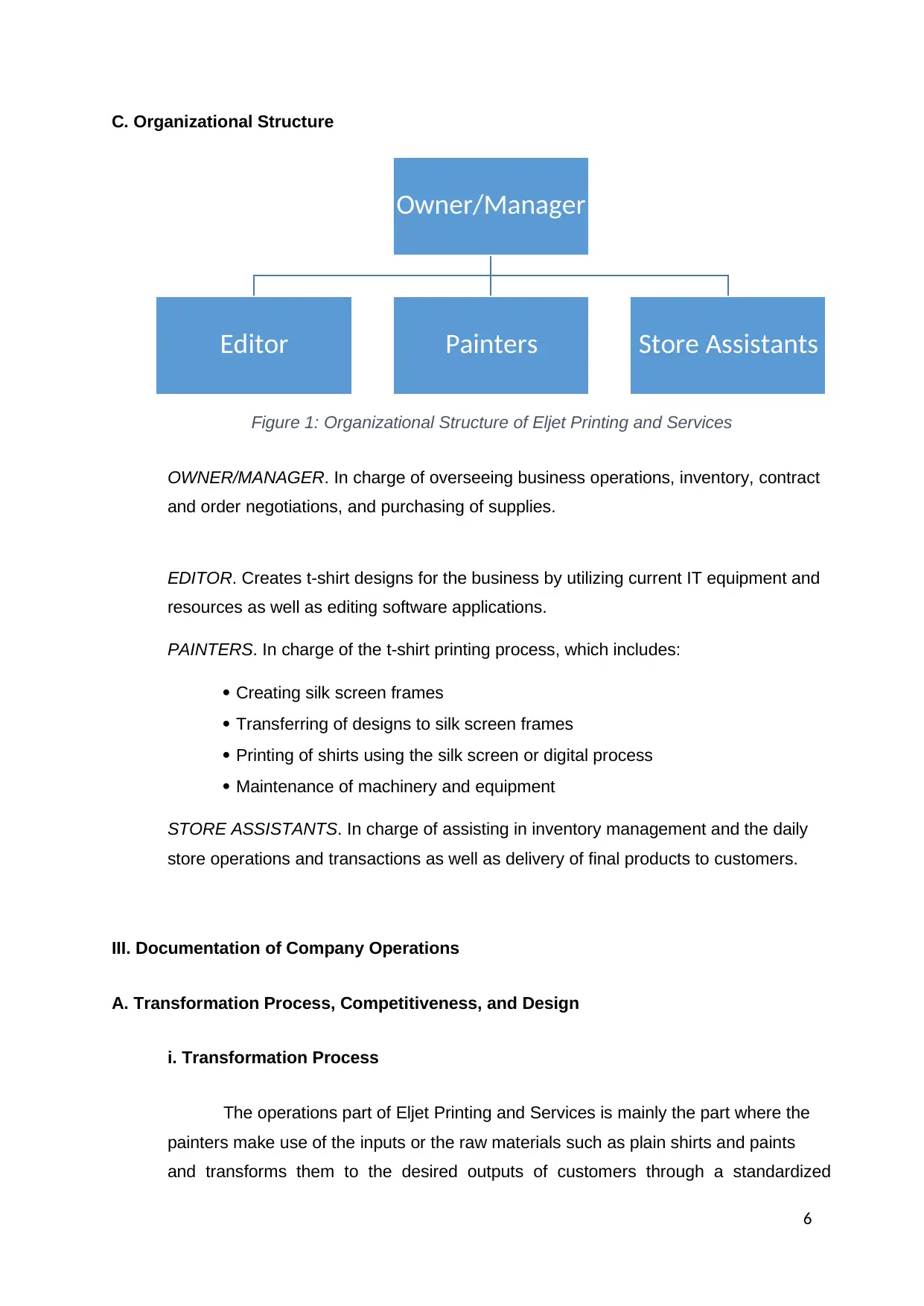
6
C. Organizational Structure
OWNER/MANAGER. In charge of overseeing business operations, inventory, contract
and order negotiations, and purchasing of supplies.
EDITOR. Creates t-shirt designs for the business by utilizing current IT equipment and
resources as well as editing software applications.
PAINTERS. In charge of the t-shirt printing process, which includes:
Creating silk screen frames
Transferring of designs to silk screen frames
Printing of shirts using the silk screen or digital process
Maintenance of machinery and equipment
STORE ASSISTANTS. In charge of assisting in inventory management and the daily
store operations and transactions as well as delivery of final products to customers.
III. Documentation of Company Operations
A. Transformation Process, Competitiveness, and Design
i. Transformation Process
The operations part of Eljet Printing and Services is mainly the part where the
painters make use of the inputs or the raw materials such as plain shirts and paints
and transforms them to the desired outputs of customers through a standardized
Owner/Manager
Editor Painters Store Assistants
Figure 1: Organizational Structure of Eljet Printing and Services
C. Organizational Structure
OWNER/MANAGER. In charge of overseeing business operations, inventory, contract
and order negotiations, and purchasing of supplies.
EDITOR. Creates t-shirt designs for the business by utilizing current IT equipment and
resources as well as editing software applications.
PAINTERS. In charge of the t-shirt printing process, which includes:
Creating silk screen frames
Transferring of designs to silk screen frames
Printing of shirts using the silk screen or digital process
Maintenance of machinery and equipment
STORE ASSISTANTS. In charge of assisting in inventory management and the daily
store operations and transactions as well as delivery of final products to customers.
III. Documentation of Company Operations
A. Transformation Process, Competitiveness, and Design
i. Transformation Process
The operations part of Eljet Printing and Services is mainly the part where the
painters make use of the inputs or the raw materials such as plain shirts and paints
and transforms them to the desired outputs of customers through a standardized
Owner/Manager
Editor Painters Store Assistants
Figure 1: Organizational Structure of Eljet Printing and Services
Paraphrase This Document
Need a fresh take? Get an instant paraphrase of this document with our AI Paraphraser
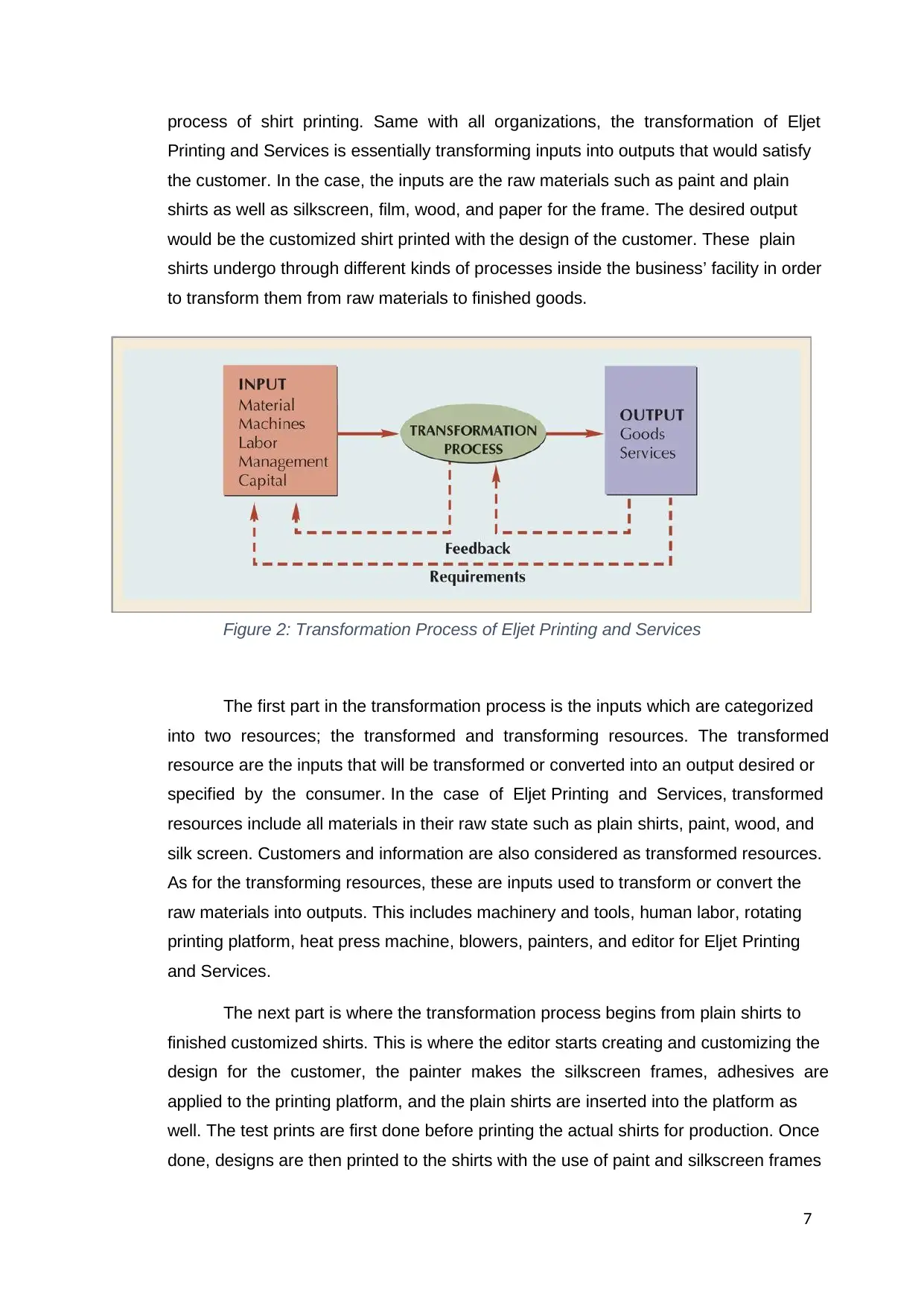
7
process of shirt printing. Same with all organizations, the transformation of Eljet
Printing and Services is essentially transforming inputs into outputs that would satisfy
the customer. In the case, the inputs are the raw materials such as paint and plain
shirts as well as silkscreen, film, wood, and paper for the frame. The desired output
would be the customized shirt printed with the design of the customer. These plain
shirts undergo through different kinds of processes inside the business’ facility in order
to transform them from raw materials to finished goods.
The first part in the transformation process is the inputs which are categorized
into two resources; the transformed and transforming resources. The transformed
resource are the inputs that will be transformed or converted into an output desired or
specified by the consumer. In the case of Eljet Printing and Services, transformed
resources include all materials in their raw state such as plain shirts, paint, wood, and
silk screen. Customers and information are also considered as transformed resources.
As for the transforming resources, these are inputs used to transform or convert the
raw materials into outputs. This includes machinery and tools, human labor, rotating
printing platform, heat press machine, blowers, painters, and editor for Eljet Printing
and Services.
The next part is where the transformation process begins from plain shirts to
finished customized shirts. This is where the editor starts creating and customizing the
design for the customer, the painter makes the silkscreen frames, adhesives are
applied to the printing platform, and the plain shirts are inserted into the platform as
well. The test prints are first done before printing the actual shirts for production. Once
done, designs are then printed to the shirts with the use of paint and silkscreen frames
Figure 2: Transformation Process of Eljet Printing and Services
process of shirt printing. Same with all organizations, the transformation of Eljet
Printing and Services is essentially transforming inputs into outputs that would satisfy
the customer. In the case, the inputs are the raw materials such as paint and plain
shirts as well as silkscreen, film, wood, and paper for the frame. The desired output
would be the customized shirt printed with the design of the customer. These plain
shirts undergo through different kinds of processes inside the business’ facility in order
to transform them from raw materials to finished goods.
The first part in the transformation process is the inputs which are categorized
into two resources; the transformed and transforming resources. The transformed
resource are the inputs that will be transformed or converted into an output desired or
specified by the consumer. In the case of Eljet Printing and Services, transformed
resources include all materials in their raw state such as plain shirts, paint, wood, and
silk screen. Customers and information are also considered as transformed resources.
As for the transforming resources, these are inputs used to transform or convert the
raw materials into outputs. This includes machinery and tools, human labor, rotating
printing platform, heat press machine, blowers, painters, and editor for Eljet Printing
and Services.
The next part is where the transformation process begins from plain shirts to
finished customized shirts. This is where the editor starts creating and customizing the
design for the customer, the painter makes the silkscreen frames, adhesives are
applied to the printing platform, and the plain shirts are inserted into the platform as
well. The test prints are first done before printing the actual shirts for production. Once
done, designs are then printed to the shirts with the use of paint and silkscreen frames
Figure 2: Transformation Process of Eljet Printing and Services
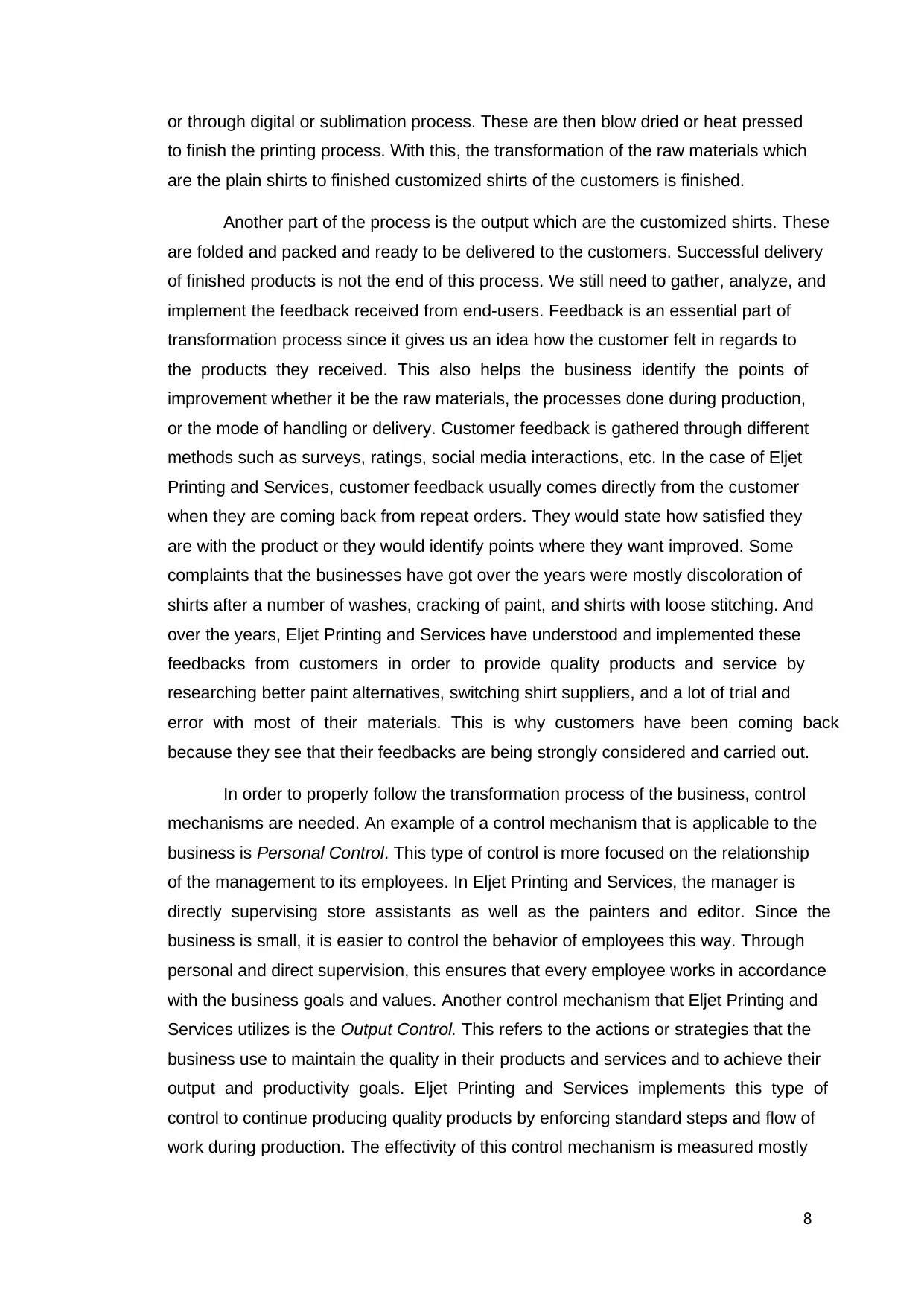
8
or through digital or sublimation process. These are then blow dried or heat pressed
to finish the printing process. With this, the transformation of the raw materials which
are the plain shirts to finished customized shirts of the customers is finished.
Another part of the process is the output which are the customized shirts. These
are folded and packed and ready to be delivered to the customers. Successful delivery
of finished products is not the end of this process. We still need to gather, analyze, and
implement the feedback received from end-users. Feedback is an essential part of
transformation process since it gives us an idea how the customer felt in regards to
the products they received. This also helps the business identify the points of
improvement whether it be the raw materials, the processes done during production,
or the mode of handling or delivery. Customer feedback is gathered through different
methods such as surveys, ratings, social media interactions, etc. In the case of Eljet
Printing and Services, customer feedback usually comes directly from the customer
when they are coming back from repeat orders. They would state how satisfied they
are with the product or they would identify points where they want improved. Some
complaints that the businesses have got over the years were mostly discoloration of
shirts after a number of washes, cracking of paint, and shirts with loose stitching. And
over the years, Eljet Printing and Services have understood and implemented these
feedbacks from customers in order to provide quality products and service by
researching better paint alternatives, switching shirt suppliers, and a lot of trial and
error with most of their materials. This is why customers have been coming back
because they see that their feedbacks are being strongly considered and carried out.
In order to properly follow the transformation process of the business, control
mechanisms are needed. An example of a control mechanism that is applicable to the
business is Personal Control. This type of control is more focused on the relationship
of the management to its employees. In Eljet Printing and Services, the manager is
directly supervising store assistants as well as the painters and editor. Since the
business is small, it is easier to control the behavior of employees this way. Through
personal and direct supervision, this ensures that every employee works in accordance
with the business goals and values. Another control mechanism that Eljet Printing and
Services utilizes is the Output Control. This refers to the actions or strategies that the
business use to maintain the quality in their products and services and to achieve their
output and productivity goals. Eljet Printing and Services implements this type of
control to continue producing quality products by enforcing standard steps and flow of
work during production. The effectivity of this control mechanism is measured mostly
or through digital or sublimation process. These are then blow dried or heat pressed
to finish the printing process. With this, the transformation of the raw materials which
are the plain shirts to finished customized shirts of the customers is finished.
Another part of the process is the output which are the customized shirts. These
are folded and packed and ready to be delivered to the customers. Successful delivery
of finished products is not the end of this process. We still need to gather, analyze, and
implement the feedback received from end-users. Feedback is an essential part of
transformation process since it gives us an idea how the customer felt in regards to
the products they received. This also helps the business identify the points of
improvement whether it be the raw materials, the processes done during production,
or the mode of handling or delivery. Customer feedback is gathered through different
methods such as surveys, ratings, social media interactions, etc. In the case of Eljet
Printing and Services, customer feedback usually comes directly from the customer
when they are coming back from repeat orders. They would state how satisfied they
are with the product or they would identify points where they want improved. Some
complaints that the businesses have got over the years were mostly discoloration of
shirts after a number of washes, cracking of paint, and shirts with loose stitching. And
over the years, Eljet Printing and Services have understood and implemented these
feedbacks from customers in order to provide quality products and service by
researching better paint alternatives, switching shirt suppliers, and a lot of trial and
error with most of their materials. This is why customers have been coming back
because they see that their feedbacks are being strongly considered and carried out.
In order to properly follow the transformation process of the business, control
mechanisms are needed. An example of a control mechanism that is applicable to the
business is Personal Control. This type of control is more focused on the relationship
of the management to its employees. In Eljet Printing and Services, the manager is
directly supervising store assistants as well as the painters and editor. Since the
business is small, it is easier to control the behavior of employees this way. Through
personal and direct supervision, this ensures that every employee works in accordance
with the business goals and values. Another control mechanism that Eljet Printing and
Services utilizes is the Output Control. This refers to the actions or strategies that the
business use to maintain the quality in their products and services and to achieve their
output and productivity goals. Eljet Printing and Services implements this type of
control to continue producing quality products by enforcing standard steps and flow of
work during production. The effectivity of this control mechanism is measured mostly
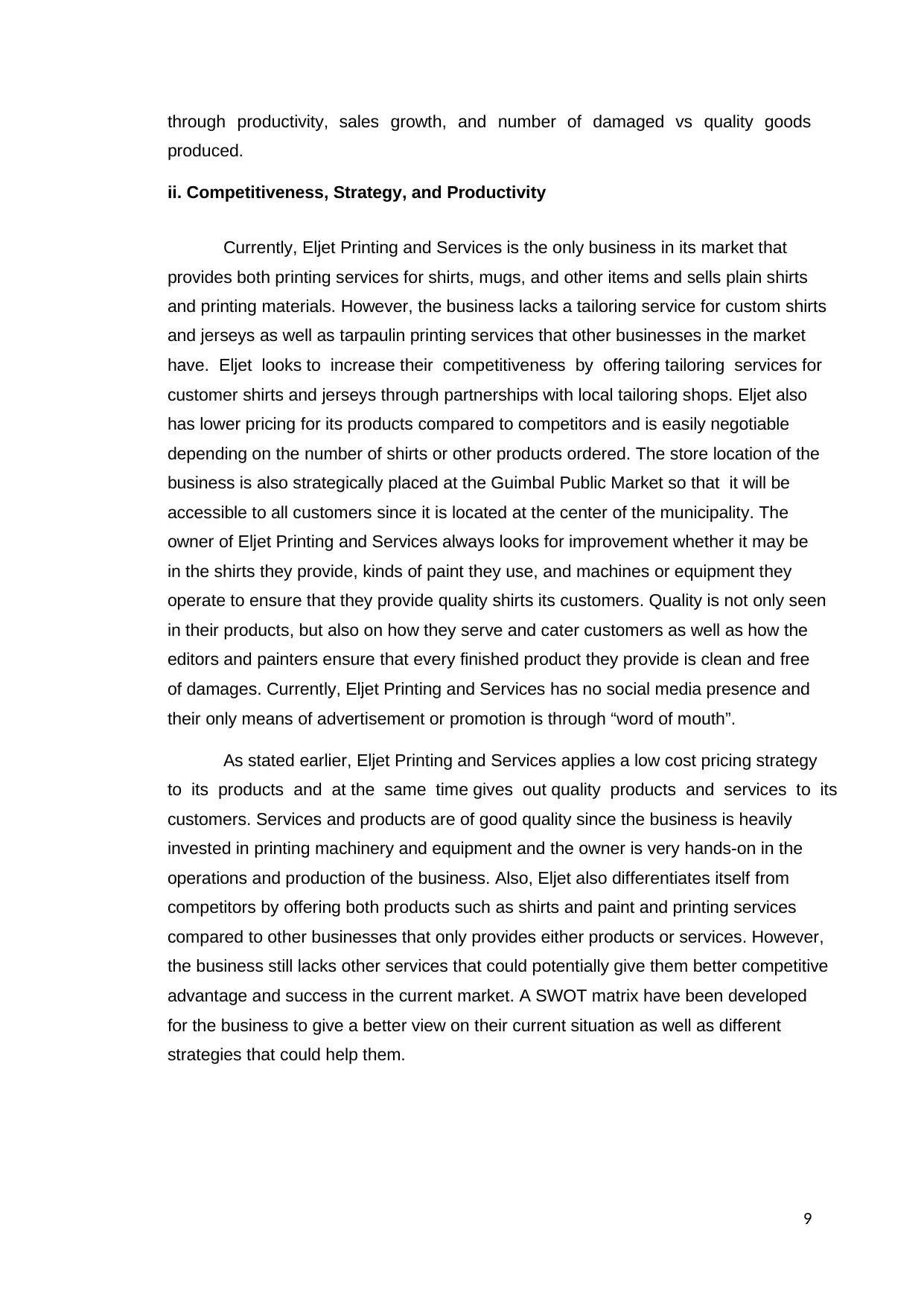
9
through productivity, sales growth, and number of damaged vs quality goods
produced.
ii. Competitiveness, Strategy, and Productivity
Currently, Eljet Printing and Services is the only business in its market that
provides both printing services for shirts, mugs, and other items and sells plain shirts
and printing materials. However, the business lacks a tailoring service for custom shirts
and jerseys as well as tarpaulin printing services that other businesses in the market
have. Eljet looks to increase their competitiveness by offering tailoring services for
customer shirts and jerseys through partnerships with local tailoring shops. Eljet also
has lower pricing for its products compared to competitors and is easily negotiable
depending on the number of shirts or other products ordered. The store location of the
business is also strategically placed at the Guimbal Public Market so that it will be
accessible to all customers since it is located at the center of the municipality. The
owner of Eljet Printing and Services always looks for improvement whether it may be
in the shirts they provide, kinds of paint they use, and machines or equipment they
operate to ensure that they provide quality shirts its customers. Quality is not only seen
in their products, but also on how they serve and cater customers as well as how the
editors and painters ensure that every finished product they provide is clean and free
of damages. Currently, Eljet Printing and Services has no social media presence and
their only means of advertisement or promotion is through “word of mouth”.
As stated earlier, Eljet Printing and Services applies a low cost pricing strategy
to its products and at the same time gives out quality products and services to its
customers. Services and products are of good quality since the business is heavily
invested in printing machinery and equipment and the owner is very hands-on in the
operations and production of the business. Also, Eljet also differentiates itself from
competitors by offering both products such as shirts and paint and printing services
compared to other businesses that only provides either products or services. However,
the business still lacks other services that could potentially give them better competitive
advantage and success in the current market. A SWOT matrix have been developed
for the business to give a better view on their current situation as well as different
strategies that could help them.
through productivity, sales growth, and number of damaged vs quality goods
produced.
ii. Competitiveness, Strategy, and Productivity
Currently, Eljet Printing and Services is the only business in its market that
provides both printing services for shirts, mugs, and other items and sells plain shirts
and printing materials. However, the business lacks a tailoring service for custom shirts
and jerseys as well as tarpaulin printing services that other businesses in the market
have. Eljet looks to increase their competitiveness by offering tailoring services for
customer shirts and jerseys through partnerships with local tailoring shops. Eljet also
has lower pricing for its products compared to competitors and is easily negotiable
depending on the number of shirts or other products ordered. The store location of the
business is also strategically placed at the Guimbal Public Market so that it will be
accessible to all customers since it is located at the center of the municipality. The
owner of Eljet Printing and Services always looks for improvement whether it may be
in the shirts they provide, kinds of paint they use, and machines or equipment they
operate to ensure that they provide quality shirts its customers. Quality is not only seen
in their products, but also on how they serve and cater customers as well as how the
editors and painters ensure that every finished product they provide is clean and free
of damages. Currently, Eljet Printing and Services has no social media presence and
their only means of advertisement or promotion is through “word of mouth”.
As stated earlier, Eljet Printing and Services applies a low cost pricing strategy
to its products and at the same time gives out quality products and services to its
customers. Services and products are of good quality since the business is heavily
invested in printing machinery and equipment and the owner is very hands-on in the
operations and production of the business. Also, Eljet also differentiates itself from
competitors by offering both products such as shirts and paint and printing services
compared to other businesses that only provides either products or services. However,
the business still lacks other services that could potentially give them better competitive
advantage and success in the current market. A SWOT matrix have been developed
for the business to give a better view on their current situation as well as different
strategies that could help them.
Secure Best Marks with AI Grader
Need help grading? Try our AI Grader for instant feedback on your assignments.
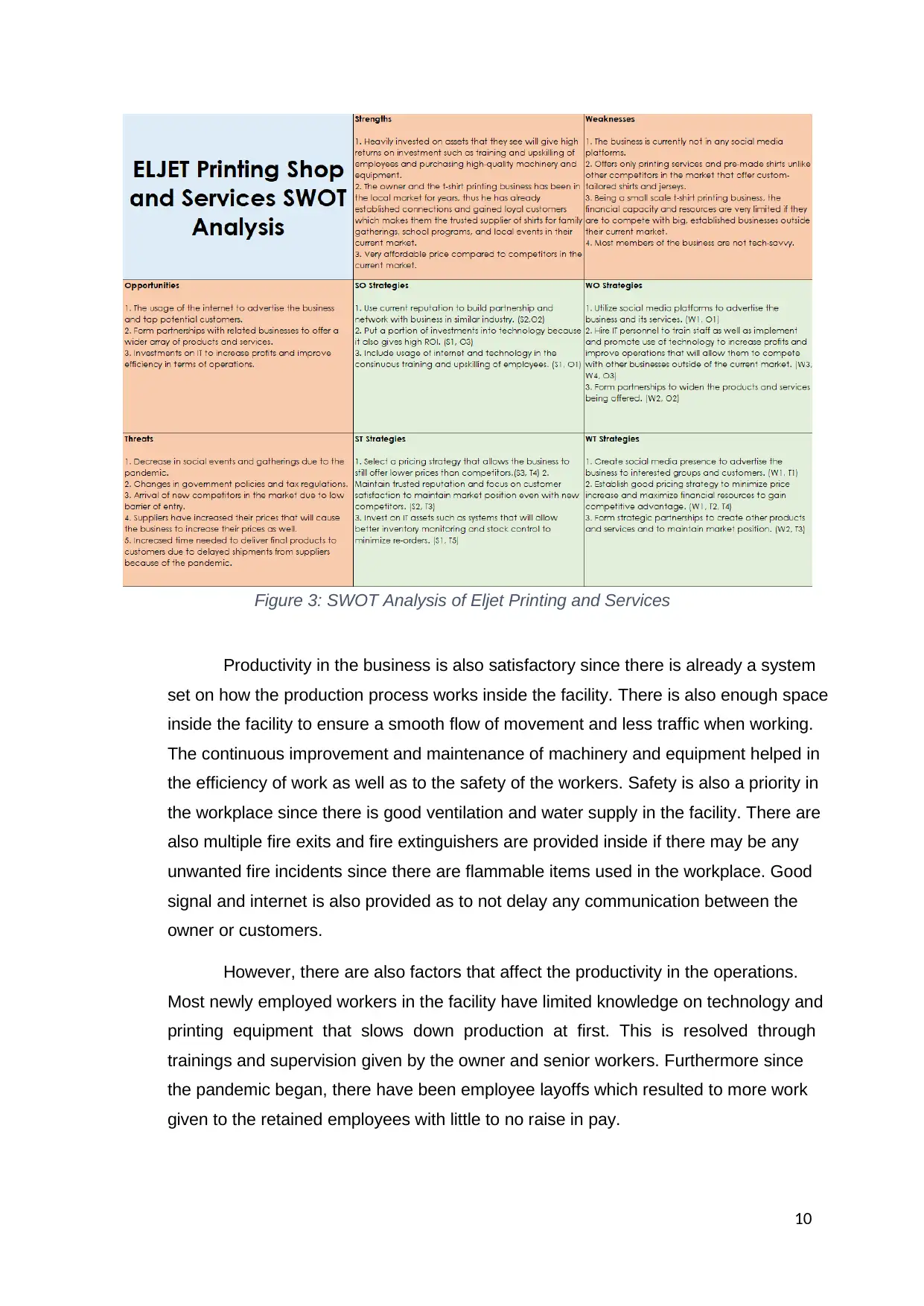
10
Productivity in the business is also satisfactory since there is already a system
set on how the production process works inside the facility. There is also enough space
inside the facility to ensure a smooth flow of movement and less traffic when working.
The continuous improvement and maintenance of machinery and equipment helped in
the efficiency of work as well as to the safety of the workers. Safety is also a priority in
the workplace since there is good ventilation and water supply in the facility. There are
also multiple fire exits and fire extinguishers are provided inside if there may be any
unwanted fire incidents since there are flammable items used in the workplace. Good
signal and internet is also provided as to not delay any communication between the
owner or customers.
However, there are also factors that affect the productivity in the operations.
Most newly employed workers in the facility have limited knowledge on technology and
printing equipment that slows down production at first. This is resolved through
trainings and supervision given by the owner and senior workers. Furthermore since
the pandemic began, there have been employee layoffs which resulted to more work
given to the retained employees with little to no raise in pay.
Figure 3: SWOT Analysis of Eljet Printing and Services
Productivity in the business is also satisfactory since there is already a system
set on how the production process works inside the facility. There is also enough space
inside the facility to ensure a smooth flow of movement and less traffic when working.
The continuous improvement and maintenance of machinery and equipment helped in
the efficiency of work as well as to the safety of the workers. Safety is also a priority in
the workplace since there is good ventilation and water supply in the facility. There are
also multiple fire exits and fire extinguishers are provided inside if there may be any
unwanted fire incidents since there are flammable items used in the workplace. Good
signal and internet is also provided as to not delay any communication between the
owner or customers.
However, there are also factors that affect the productivity in the operations.
Most newly employed workers in the facility have limited knowledge on technology and
printing equipment that slows down production at first. This is resolved through
trainings and supervision given by the owner and senior workers. Furthermore since
the pandemic began, there have been employee layoffs which resulted to more work
given to the retained employees with little to no raise in pay.
Figure 3: SWOT Analysis of Eljet Printing and Services
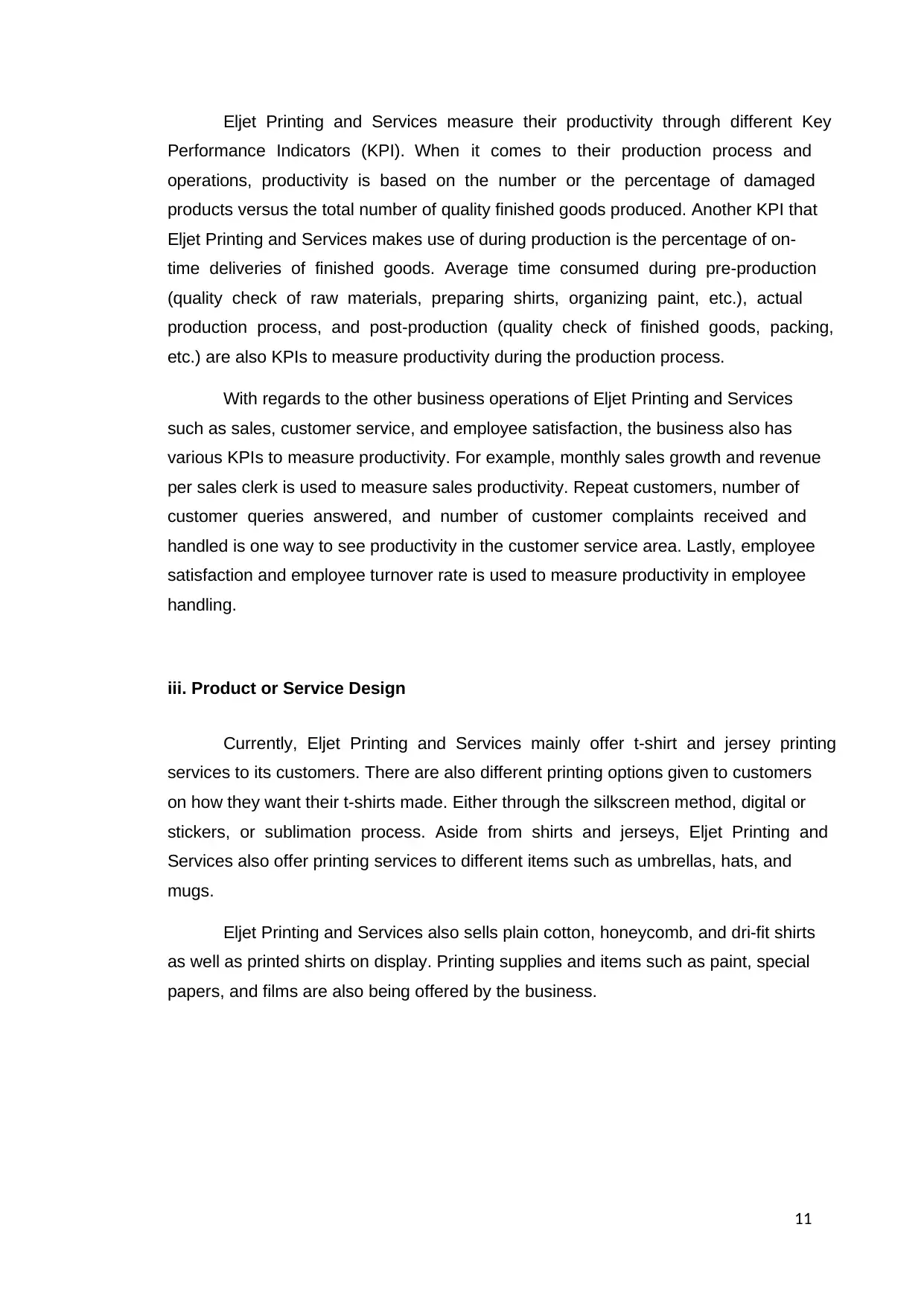
11
Eljet Printing and Services measure their productivity through different Key
Performance Indicators (KPI). When it comes to their production process and
operations, productivity is based on the number or the percentage of damaged
products versus the total number of quality finished goods produced. Another KPI that
Eljet Printing and Services makes use of during production is the percentage of on-
time deliveries of finished goods. Average time consumed during pre-production
(quality check of raw materials, preparing shirts, organizing paint, etc.), actual
production process, and post-production (quality check of finished goods, packing,
etc.) are also KPIs to measure productivity during the production process.
With regards to the other business operations of Eljet Printing and Services
such as sales, customer service, and employee satisfaction, the business also has
various KPIs to measure productivity. For example, monthly sales growth and revenue
per sales clerk is used to measure sales productivity. Repeat customers, number of
customer queries answered, and number of customer complaints received and
handled is one way to see productivity in the customer service area. Lastly, employee
satisfaction and employee turnover rate is used to measure productivity in employee
handling.
iii. Product or Service Design
Currently, Eljet Printing and Services mainly offer t-shirt and jersey printing
services to its customers. There are also different printing options given to customers
on how they want their t-shirts made. Either through the silkscreen method, digital or
stickers, or sublimation process. Aside from shirts and jerseys, Eljet Printing and
Services also offer printing services to different items such as umbrellas, hats, and
mugs.
Eljet Printing and Services also sells plain cotton, honeycomb, and dri-fit shirts
as well as printed shirts on display. Printing supplies and items such as paint, special
papers, and films are also being offered by the business.
Eljet Printing and Services measure their productivity through different Key
Performance Indicators (KPI). When it comes to their production process and
operations, productivity is based on the number or the percentage of damaged
products versus the total number of quality finished goods produced. Another KPI that
Eljet Printing and Services makes use of during production is the percentage of on-
time deliveries of finished goods. Average time consumed during pre-production
(quality check of raw materials, preparing shirts, organizing paint, etc.), actual
production process, and post-production (quality check of finished goods, packing,
etc.) are also KPIs to measure productivity during the production process.
With regards to the other business operations of Eljet Printing and Services
such as sales, customer service, and employee satisfaction, the business also has
various KPIs to measure productivity. For example, monthly sales growth and revenue
per sales clerk is used to measure sales productivity. Repeat customers, number of
customer queries answered, and number of customer complaints received and
handled is one way to see productivity in the customer service area. Lastly, employee
satisfaction and employee turnover rate is used to measure productivity in employee
handling.
iii. Product or Service Design
Currently, Eljet Printing and Services mainly offer t-shirt and jersey printing
services to its customers. There are also different printing options given to customers
on how they want their t-shirts made. Either through the silkscreen method, digital or
stickers, or sublimation process. Aside from shirts and jerseys, Eljet Printing and
Services also offer printing services to different items such as umbrellas, hats, and
mugs.
Eljet Printing and Services also sells plain cotton, honeycomb, and dri-fit shirts
as well as printed shirts on display. Printing supplies and items such as paint, special
papers, and films are also being offered by the business.
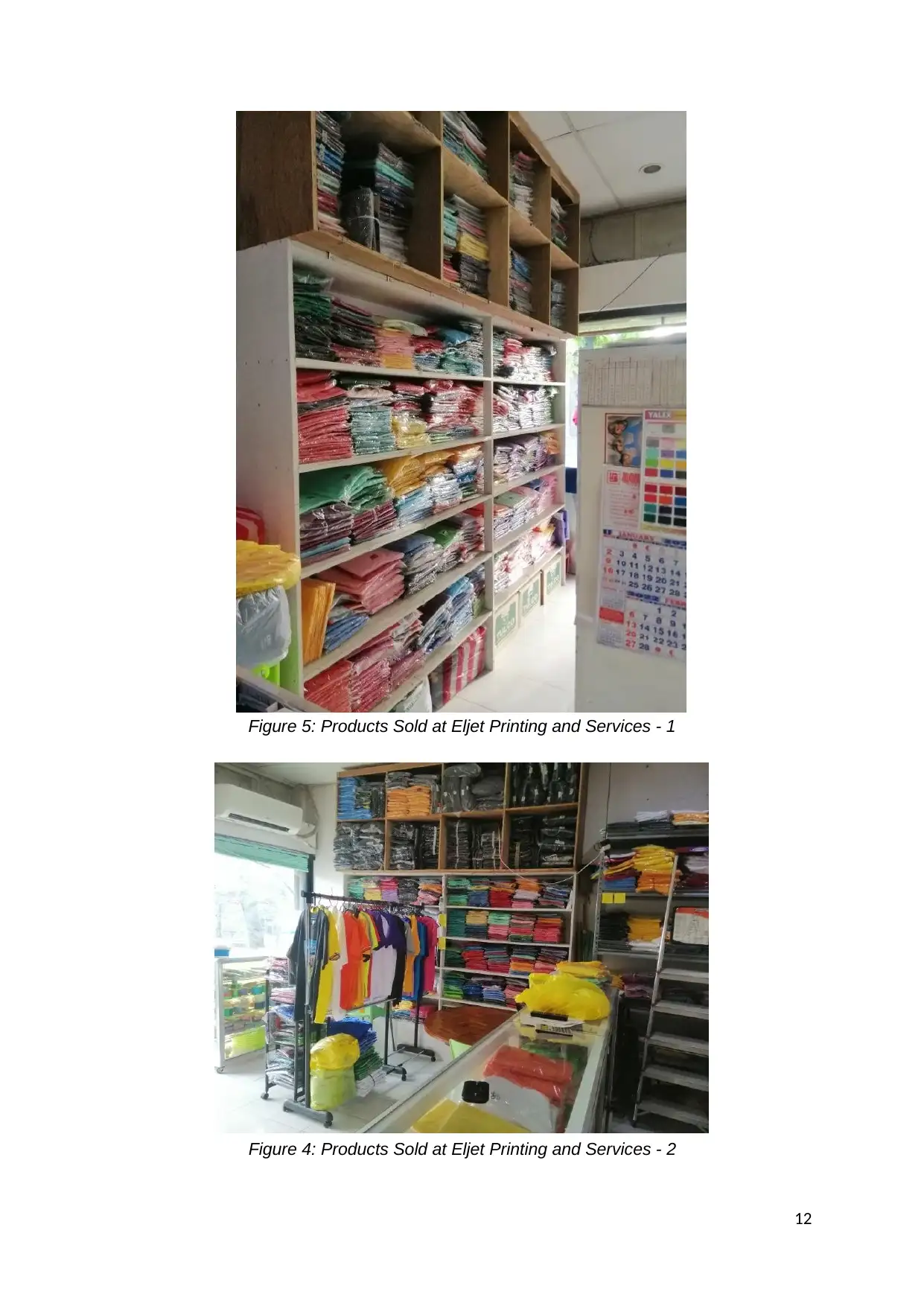
12
Figure 4: Products Sold at Eljet Printing and Services - 2
Figure 5: Products Sold at Eljet Printing and Services - 1
Figure 4: Products Sold at Eljet Printing and Services - 2
Figure 5: Products Sold at Eljet Printing and Services - 1
Paraphrase This Document
Need a fresh take? Get an instant paraphrase of this document with our AI Paraphraser
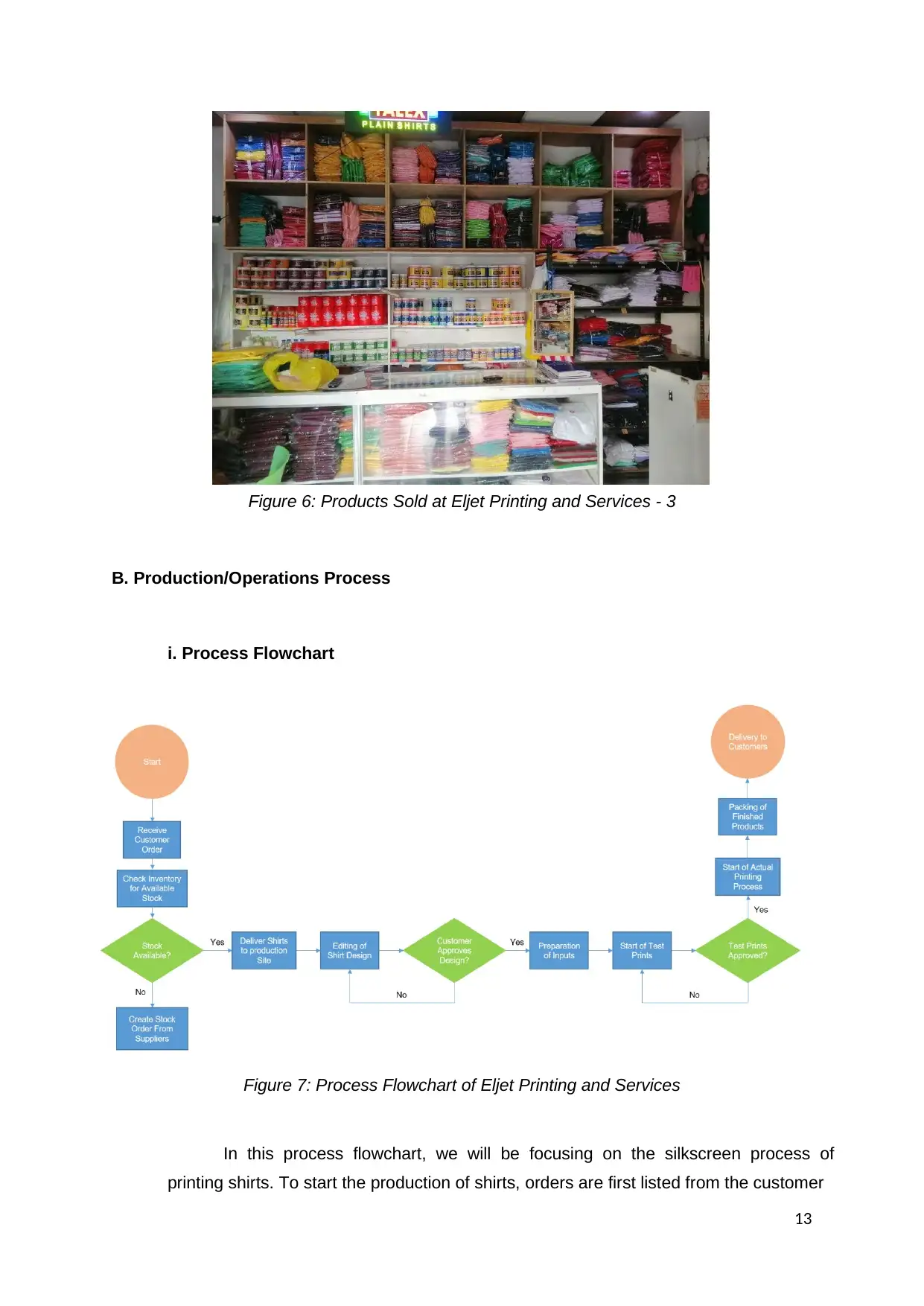
13
B. Production/Operations Process
i. Process Flowchart
In this process flowchart, we will be focusing on the silkscreen process of
printing shirts. To start the production of shirts, orders are first listed from the customer
Figure 6: Products Sold at Eljet Printing and Services - 3
Figure 7: Process Flowchart of Eljet Printing and Services
B. Production/Operations Process
i. Process Flowchart
In this process flowchart, we will be focusing on the silkscreen process of
printing shirts. To start the production of shirts, orders are first listed from the customer
Figure 6: Products Sold at Eljet Printing and Services - 3
Figure 7: Process Flowchart of Eljet Printing and Services
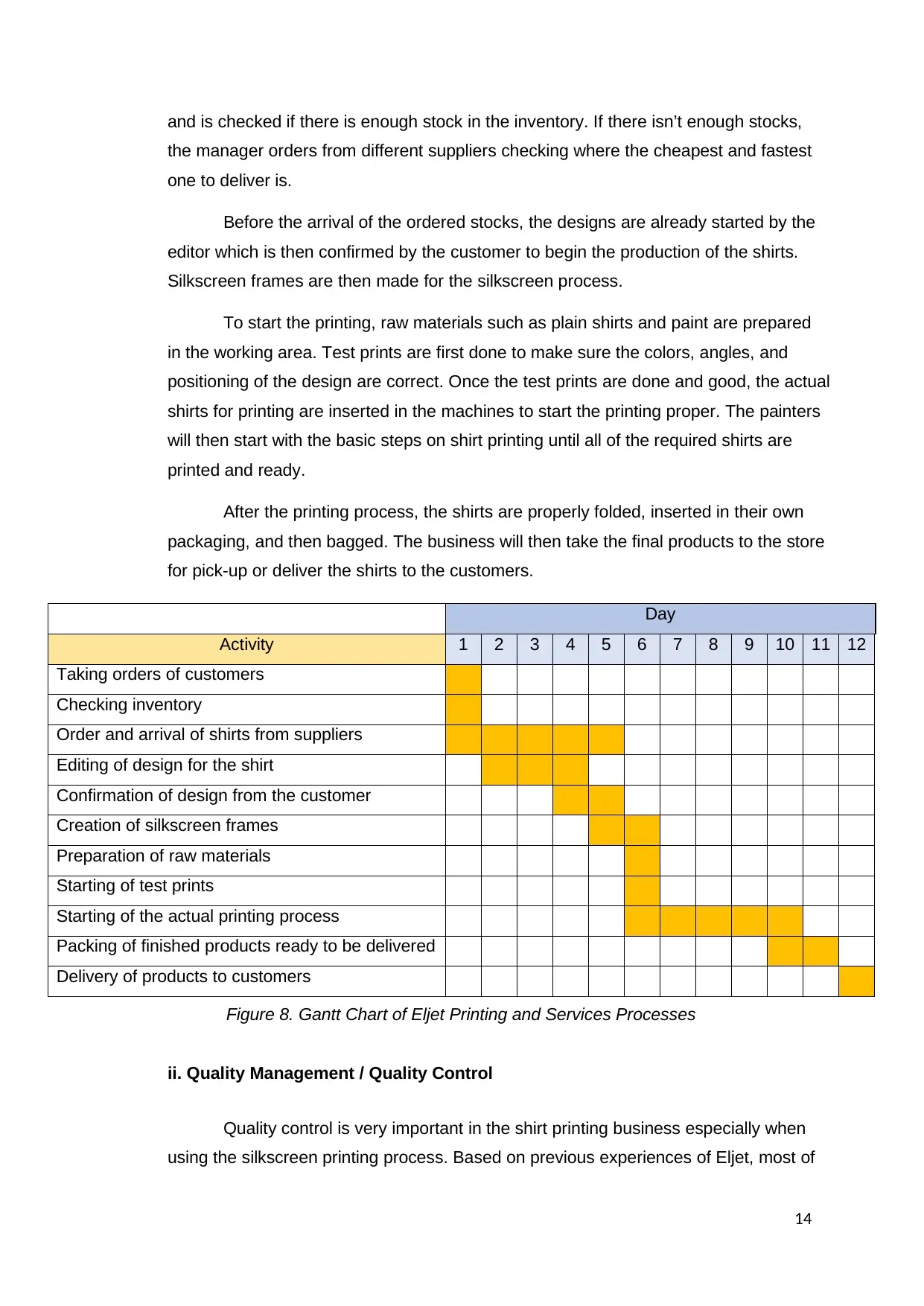
14
and is checked if there is enough stock in the inventory. If there isn’t enough stocks,
the manager orders from different suppliers checking where the cheapest and fastest
one to deliver is.
Before the arrival of the ordered stocks, the designs are already started by the
editor which is then confirmed by the customer to begin the production of the shirts.
Silkscreen frames are then made for the silkscreen process.
To start the printing, raw materials such as plain shirts and paint are prepared
in the working area. Test prints are first done to make sure the colors, angles, and
positioning of the design are correct. Once the test prints are done and good, the actual
shirts for printing are inserted in the machines to start the printing proper. The painters
will then start with the basic steps on shirt printing until all of the required shirts are
printed and ready.
After the printing process, the shirts are properly folded, inserted in their own
packaging, and then bagged. The business will then take the final products to the store
for pick-up or deliver the shirts to the customers.
ii. Quality Management / Quality Control
Quality control is very important in the shirt printing business especially when
using the silkscreen printing process. Based on previous experiences of Eljet, most of
Day
Activity 1 2 3 4 5 6 7 8 9 10 11 12
Taking orders of customers
Checking inventory
Order and arrival of shirts from suppliers
Editing of design for the shirt
Confirmation of design from the customer
Creation of silkscreen frames
Preparation of raw materials
Starting of test prints
Starting of the actual printing process
Packing of finished products ready to be delivered
Delivery of products to customers
Figure 8. Gantt Chart of Eljet Printing and Services Processes
and is checked if there is enough stock in the inventory. If there isn’t enough stocks,
the manager orders from different suppliers checking where the cheapest and fastest
one to deliver is.
Before the arrival of the ordered stocks, the designs are already started by the
editor which is then confirmed by the customer to begin the production of the shirts.
Silkscreen frames are then made for the silkscreen process.
To start the printing, raw materials such as plain shirts and paint are prepared
in the working area. Test prints are first done to make sure the colors, angles, and
positioning of the design are correct. Once the test prints are done and good, the actual
shirts for printing are inserted in the machines to start the printing proper. The painters
will then start with the basic steps on shirt printing until all of the required shirts are
printed and ready.
After the printing process, the shirts are properly folded, inserted in their own
packaging, and then bagged. The business will then take the final products to the store
for pick-up or deliver the shirts to the customers.
ii. Quality Management / Quality Control
Quality control is very important in the shirt printing business especially when
using the silkscreen printing process. Based on previous experiences of Eljet, most of
Day
Activity 1 2 3 4 5 6 7 8 9 10 11 12
Taking orders of customers
Checking inventory
Order and arrival of shirts from suppliers
Editing of design for the shirt
Confirmation of design from the customer
Creation of silkscreen frames
Preparation of raw materials
Starting of test prints
Starting of the actual printing process
Packing of finished products ready to be delivered
Delivery of products to customers
Figure 8. Gantt Chart of Eljet Printing and Services Processes
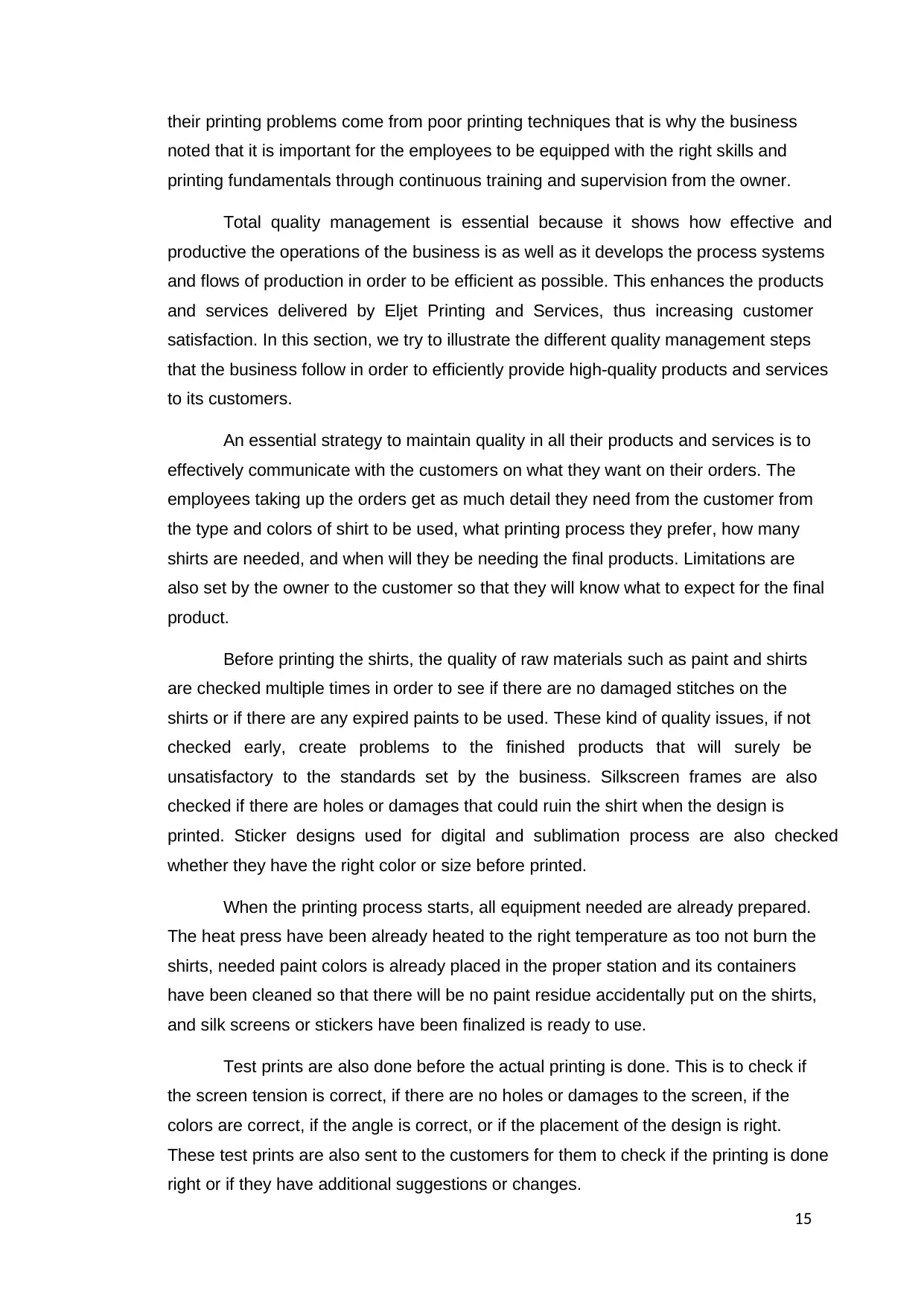
15
their printing problems come from poor printing techniques that is why the business
noted that it is important for the employees to be equipped with the right skills and
printing fundamentals through continuous training and supervision from the owner.
Total quality management is essential because it shows how effective and
productive the operations of the business is as well as it develops the process systems
and flows of production in order to be efficient as possible. This enhances the products
and services delivered by Eljet Printing and Services, thus increasing customer
satisfaction. In this section, we try to illustrate the different quality management steps
that the business follow in order to efficiently provide high-quality products and services
to its customers.
An essential strategy to maintain quality in all their products and services is to
effectively communicate with the customers on what they want on their orders. The
employees taking up the orders get as much detail they need from the customer from
the type and colors of shirt to be used, what printing process they prefer, how many
shirts are needed, and when will they be needing the final products. Limitations are
also set by the owner to the customer so that they will know what to expect for the final
product.
Before printing the shirts, the quality of raw materials such as paint and shirts
are checked multiple times in order to see if there are no damaged stitches on the
shirts or if there are any expired paints to be used. These kind of quality issues, if not
checked early, create problems to the finished products that will surely be
unsatisfactory to the standards set by the business. Silkscreen frames are also
checked if there are holes or damages that could ruin the shirt when the design is
printed. Sticker designs used for digital and sublimation process are also checked
whether they have the right color or size before printed.
When the printing process starts, all equipment needed are already prepared.
The heat press have been already heated to the right temperature as too not burn the
shirts, needed paint colors is already placed in the proper station and its containers
have been cleaned so that there will be no paint residue accidentally put on the shirts,
and silk screens or stickers have been finalized is ready to use.
Test prints are also done before the actual printing is done. This is to check if
the screen tension is correct, if there are no holes or damages to the screen, if the
colors are correct, if the angle is correct, or if the placement of the design is right.
These test prints are also sent to the customers for them to check if the printing is done
right or if they have additional suggestions or changes.
their printing problems come from poor printing techniques that is why the business
noted that it is important for the employees to be equipped with the right skills and
printing fundamentals through continuous training and supervision from the owner.
Total quality management is essential because it shows how effective and
productive the operations of the business is as well as it develops the process systems
and flows of production in order to be efficient as possible. This enhances the products
and services delivered by Eljet Printing and Services, thus increasing customer
satisfaction. In this section, we try to illustrate the different quality management steps
that the business follow in order to efficiently provide high-quality products and services
to its customers.
An essential strategy to maintain quality in all their products and services is to
effectively communicate with the customers on what they want on their orders. The
employees taking up the orders get as much detail they need from the customer from
the type and colors of shirt to be used, what printing process they prefer, how many
shirts are needed, and when will they be needing the final products. Limitations are
also set by the owner to the customer so that they will know what to expect for the final
product.
Before printing the shirts, the quality of raw materials such as paint and shirts
are checked multiple times in order to see if there are no damaged stitches on the
shirts or if there are any expired paints to be used. These kind of quality issues, if not
checked early, create problems to the finished products that will surely be
unsatisfactory to the standards set by the business. Silkscreen frames are also
checked if there are holes or damages that could ruin the shirt when the design is
printed. Sticker designs used for digital and sublimation process are also checked
whether they have the right color or size before printed.
When the printing process starts, all equipment needed are already prepared.
The heat press have been already heated to the right temperature as too not burn the
shirts, needed paint colors is already placed in the proper station and its containers
have been cleaned so that there will be no paint residue accidentally put on the shirts,
and silk screens or stickers have been finalized is ready to use.
Test prints are also done before the actual printing is done. This is to check if
the screen tension is correct, if there are no holes or damages to the screen, if the
colors are correct, if the angle is correct, or if the placement of the design is right.
These test prints are also sent to the customers for them to check if the printing is done
right or if they have additional suggestions or changes.
Secure Best Marks with AI Grader
Need help grading? Try our AI Grader for instant feedback on your assignments.
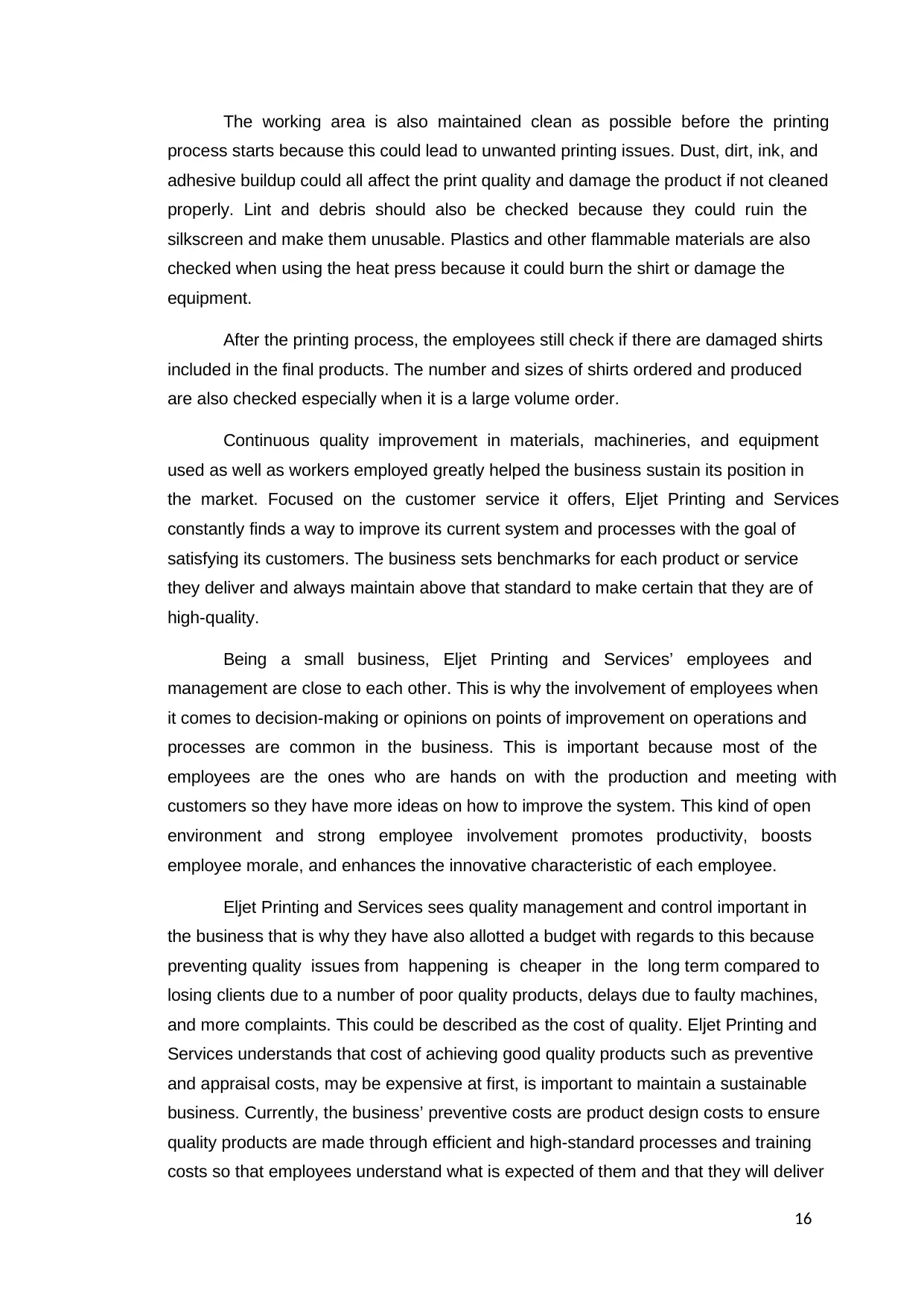
16
The working area is also maintained clean as possible before the printing
process starts because this could lead to unwanted printing issues. Dust, dirt, ink, and
adhesive buildup could all affect the print quality and damage the product if not cleaned
properly. Lint and debris should also be checked because they could ruin the
silkscreen and make them unusable. Plastics and other flammable materials are also
checked when using the heat press because it could burn the shirt or damage the
equipment.
After the printing process, the employees still check if there are damaged shirts
included in the final products. The number and sizes of shirts ordered and produced
are also checked especially when it is a large volume order.
Continuous quality improvement in materials, machineries, and equipment
used as well as workers employed greatly helped the business sustain its position in
the market. Focused on the customer service it offers, Eljet Printing and Services
constantly finds a way to improve its current system and processes with the goal of
satisfying its customers. The business sets benchmarks for each product or service
they deliver and always maintain above that standard to make certain that they are of
high-quality.
Being a small business, Eljet Printing and Services’ employees and
management are close to each other. This is why the involvement of employees when
it comes to decision-making or opinions on points of improvement on operations and
processes are common in the business. This is important because most of the
employees are the ones who are hands on with the production and meeting with
customers so they have more ideas on how to improve the system. This kind of open
environment and strong employee involvement promotes productivity, boosts
employee morale, and enhances the innovative characteristic of each employee.
Eljet Printing and Services sees quality management and control important in
the business that is why they have also allotted a budget with regards to this because
preventing quality issues from happening is cheaper in the long term compared to
losing clients due to a number of poor quality products, delays due to faulty machines,
and more complaints. This could be described as the cost of quality. Eljet Printing and
Services understands that cost of achieving good quality products such as preventive
and appraisal costs, may be expensive at first, is important to maintain a sustainable
business. Currently, the business’ preventive costs are product design costs to ensure
quality products are made through efficient and high-standard processes and training
costs so that employees understand what is expected of them and that they will deliver
The working area is also maintained clean as possible before the printing
process starts because this could lead to unwanted printing issues. Dust, dirt, ink, and
adhesive buildup could all affect the print quality and damage the product if not cleaned
properly. Lint and debris should also be checked because they could ruin the
silkscreen and make them unusable. Plastics and other flammable materials are also
checked when using the heat press because it could burn the shirt or damage the
equipment.
After the printing process, the employees still check if there are damaged shirts
included in the final products. The number and sizes of shirts ordered and produced
are also checked especially when it is a large volume order.
Continuous quality improvement in materials, machineries, and equipment
used as well as workers employed greatly helped the business sustain its position in
the market. Focused on the customer service it offers, Eljet Printing and Services
constantly finds a way to improve its current system and processes with the goal of
satisfying its customers. The business sets benchmarks for each product or service
they deliver and always maintain above that standard to make certain that they are of
high-quality.
Being a small business, Eljet Printing and Services’ employees and
management are close to each other. This is why the involvement of employees when
it comes to decision-making or opinions on points of improvement on operations and
processes are common in the business. This is important because most of the
employees are the ones who are hands on with the production and meeting with
customers so they have more ideas on how to improve the system. This kind of open
environment and strong employee involvement promotes productivity, boosts
employee morale, and enhances the innovative characteristic of each employee.
Eljet Printing and Services sees quality management and control important in
the business that is why they have also allotted a budget with regards to this because
preventing quality issues from happening is cheaper in the long term compared to
losing clients due to a number of poor quality products, delays due to faulty machines,
and more complaints. This could be described as the cost of quality. Eljet Printing and
Services understands that cost of achieving good quality products such as preventive
and appraisal costs, may be expensive at first, is important to maintain a sustainable
business. Currently, the business’ preventive costs are product design costs to ensure
quality products are made through efficient and high-standard processes and training
costs so that employees understand what is expected of them and that they will deliver
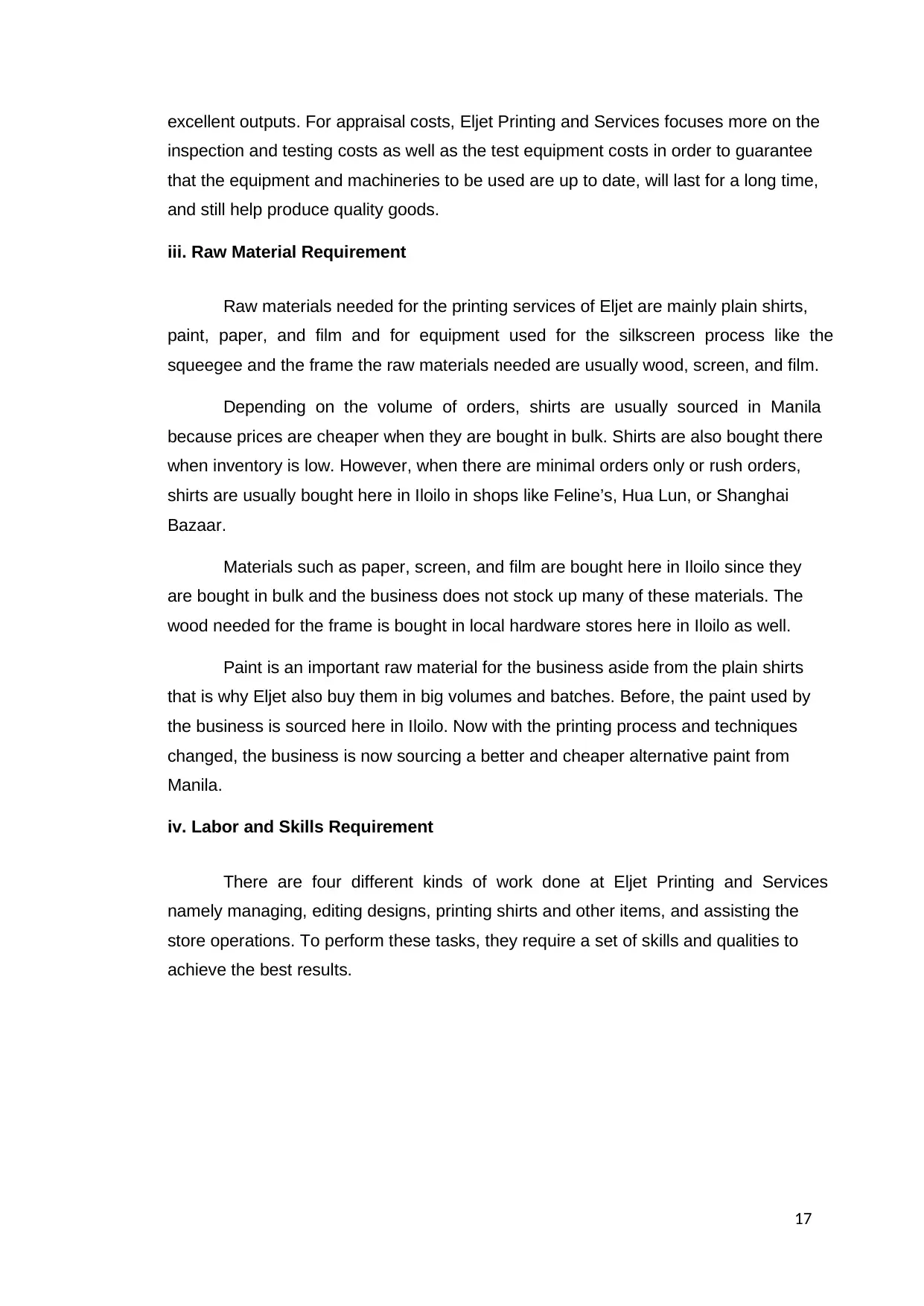
17
excellent outputs. For appraisal costs, Eljet Printing and Services focuses more on the
inspection and testing costs as well as the test equipment costs in order to guarantee
that the equipment and machineries to be used are up to date, will last for a long time,
and still help produce quality goods.
iii. Raw Material Requirement
Raw materials needed for the printing services of Eljet are mainly plain shirts,
paint, paper, and film and for equipment used for the silkscreen process like the
squeegee and the frame the raw materials needed are usually wood, screen, and film.
Depending on the volume of orders, shirts are usually sourced in Manila
because prices are cheaper when they are bought in bulk. Shirts are also bought there
when inventory is low. However, when there are minimal orders only or rush orders,
shirts are usually bought here in Iloilo in shops like Feline’s, Hua Lun, or Shanghai
Bazaar.
Materials such as paper, screen, and film are bought here in Iloilo since they
are bought in bulk and the business does not stock up many of these materials. The
wood needed for the frame is bought in local hardware stores here in Iloilo as well.
Paint is an important raw material for the business aside from the plain shirts
that is why Eljet also buy them in big volumes and batches. Before, the paint used by
the business is sourced here in Iloilo. Now with the printing process and techniques
changed, the business is now sourcing a better and cheaper alternative paint from
Manila.
iv. Labor and Skills Requirement
There are four different kinds of work done at Eljet Printing and Services
namely managing, editing designs, printing shirts and other items, and assisting the
store operations. To perform these tasks, they require a set of skills and qualities to
achieve the best results.
excellent outputs. For appraisal costs, Eljet Printing and Services focuses more on the
inspection and testing costs as well as the test equipment costs in order to guarantee
that the equipment and machineries to be used are up to date, will last for a long time,
and still help produce quality goods.
iii. Raw Material Requirement
Raw materials needed for the printing services of Eljet are mainly plain shirts,
paint, paper, and film and for equipment used for the silkscreen process like the
squeegee and the frame the raw materials needed are usually wood, screen, and film.
Depending on the volume of orders, shirts are usually sourced in Manila
because prices are cheaper when they are bought in bulk. Shirts are also bought there
when inventory is low. However, when there are minimal orders only or rush orders,
shirts are usually bought here in Iloilo in shops like Feline’s, Hua Lun, or Shanghai
Bazaar.
Materials such as paper, screen, and film are bought here in Iloilo since they
are bought in bulk and the business does not stock up many of these materials. The
wood needed for the frame is bought in local hardware stores here in Iloilo as well.
Paint is an important raw material for the business aside from the plain shirts
that is why Eljet also buy them in big volumes and batches. Before, the paint used by
the business is sourced here in Iloilo. Now with the printing process and techniques
changed, the business is now sourcing a better and cheaper alternative paint from
Manila.
iv. Labor and Skills Requirement
There are four different kinds of work done at Eljet Printing and Services
namely managing, editing designs, printing shirts and other items, and assisting the
store operations. To perform these tasks, they require a set of skills and qualities to
achieve the best results.
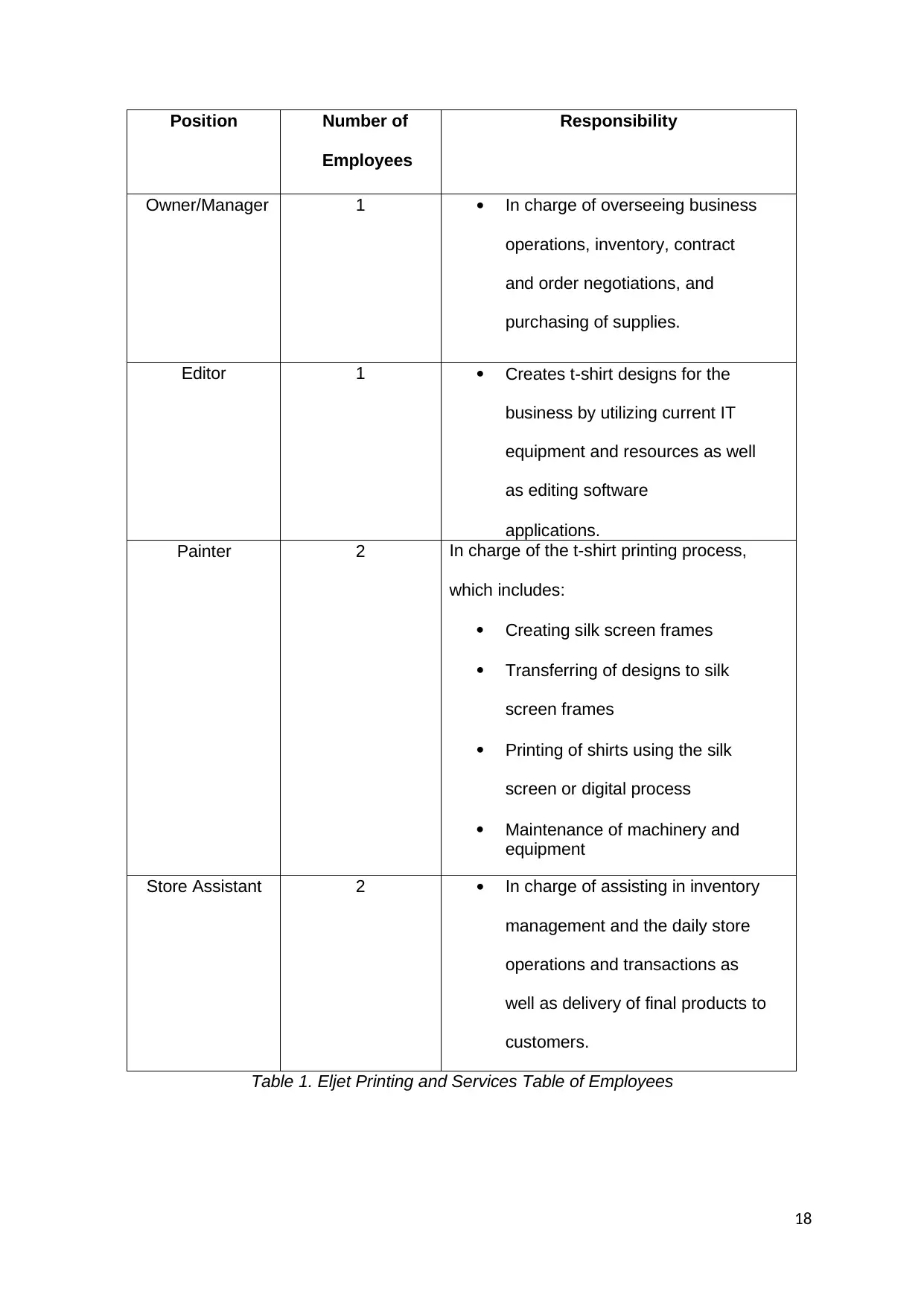
18
Table 1. Eljet Printing and Services Table of Employees
Position Number of
Employees
Responsibility
Owner/Manager 1 In charge of overseeing business
operations, inventory, contract
and order negotiations, and
purchasing of supplies.
Editor 1 Creates t-shirt designs for the
business by utilizing current IT
equipment and resources as well
as editing software
applications.
Painter 2 In charge of the t-shirt printing process,
which includes:
Creating silk screen frames
Transferring of designs to silk
screen frames
Printing of shirts using the silk
screen or digital process
Maintenance of machinery and
equipment
Store Assistant 2 In charge of assisting in inventory
management and the daily store
operations and transactions as
well as delivery of final products to
customers.
Table 1. Eljet Printing and Services Table of Employees
Position Number of
Employees
Responsibility
Owner/Manager 1 In charge of overseeing business
operations, inventory, contract
and order negotiations, and
purchasing of supplies.
Editor 1 Creates t-shirt designs for the
business by utilizing current IT
equipment and resources as well
as editing software
applications.
Painter 2 In charge of the t-shirt printing process,
which includes:
Creating silk screen frames
Transferring of designs to silk
screen frames
Printing of shirts using the silk
screen or digital process
Maintenance of machinery and
equipment
Store Assistant 2 In charge of assisting in inventory
management and the daily store
operations and transactions as
well as delivery of final products to
customers.
Paraphrase This Document
Need a fresh take? Get an instant paraphrase of this document with our AI Paraphraser
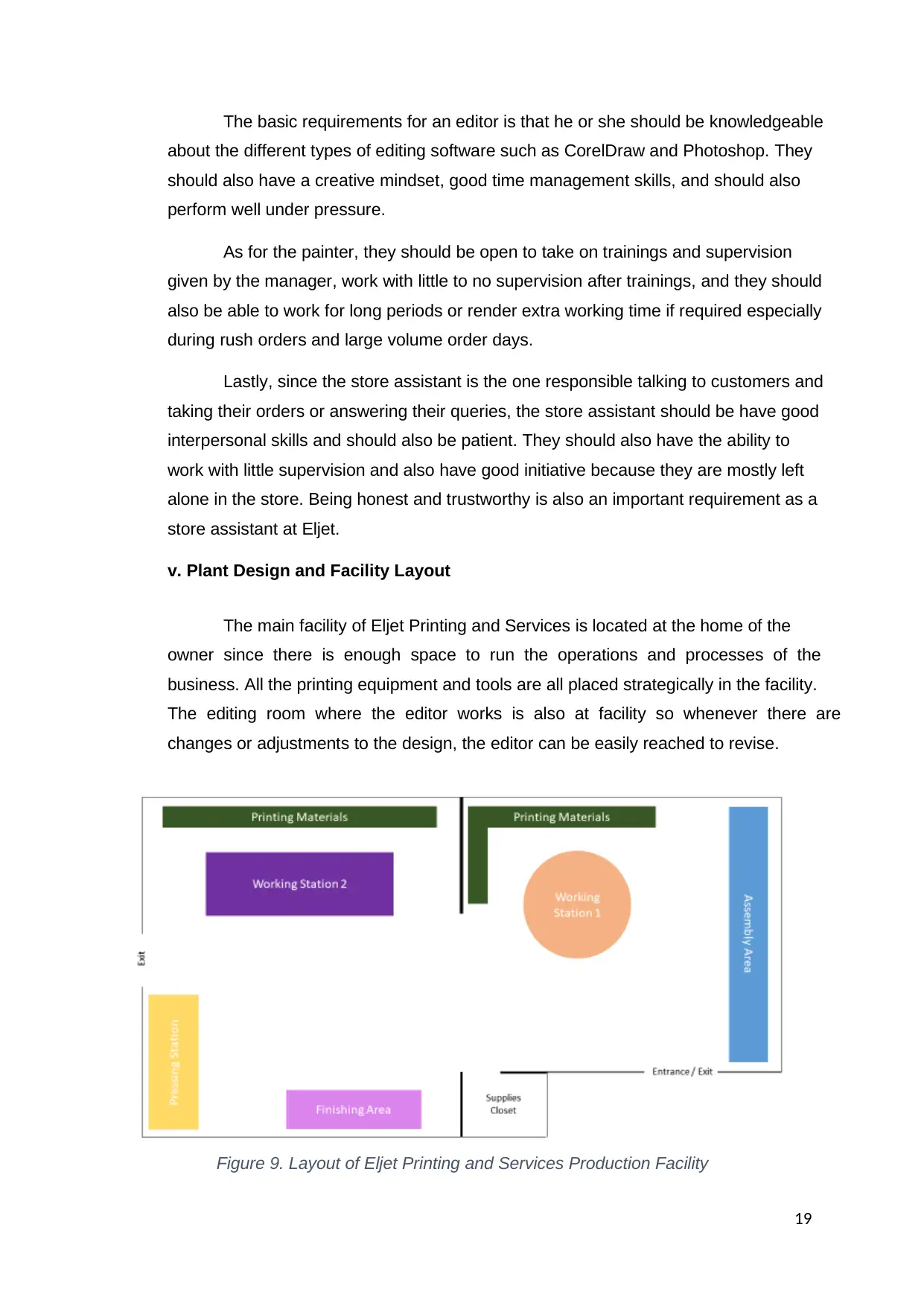
19
Figure 9. Layout of Eljet Printing and Services Production Facility
The basic requirements for an editor is that he or she should be knowledgeable
about the different types of editing software such as CorelDraw and Photoshop. They
should also have a creative mindset, good time management skills, and should also
perform well under pressure.
As for the painter, they should be open to take on trainings and supervision
given by the manager, work with little to no supervision after trainings, and they should
also be able to work for long periods or render extra working time if required especially
during rush orders and large volume order days.
Lastly, since the store assistant is the one responsible talking to customers and
taking their orders or answering their queries, the store assistant should be have good
interpersonal skills and should also be patient. They should also have the ability to
work with little supervision and also have good initiative because they are mostly left
alone in the store. Being honest and trustworthy is also an important requirement as a
store assistant at Eljet.
v. Plant Design and Facility Layout
The main facility of Eljet Printing and Services is located at the home of the
owner since there is enough space to run the operations and processes of the
business. All the printing equipment and tools are all placed strategically in the facility.
The editing room where the editor works is also at facility so whenever there are
changes or adjustments to the design, the editor can be easily reached to revise.
Figure 9. Layout of Eljet Printing and Services Production Facility
The basic requirements for an editor is that he or she should be knowledgeable
about the different types of editing software such as CorelDraw and Photoshop. They
should also have a creative mindset, good time management skills, and should also
perform well under pressure.
As for the painter, they should be open to take on trainings and supervision
given by the manager, work with little to no supervision after trainings, and they should
also be able to work for long periods or render extra working time if required especially
during rush orders and large volume order days.
Lastly, since the store assistant is the one responsible talking to customers and
taking their orders or answering their queries, the store assistant should be have good
interpersonal skills and should also be patient. They should also have the ability to
work with little supervision and also have good initiative because they are mostly left
alone in the store. Being honest and trustworthy is also an important requirement as a
store assistant at Eljet.
v. Plant Design and Facility Layout
The main facility of Eljet Printing and Services is located at the home of the
owner since there is enough space to run the operations and processes of the
business. All the printing equipment and tools are all placed strategically in the facility.
The editing room where the editor works is also at facility so whenever there are
changes or adjustments to the design, the editor can be easily reached to revise.
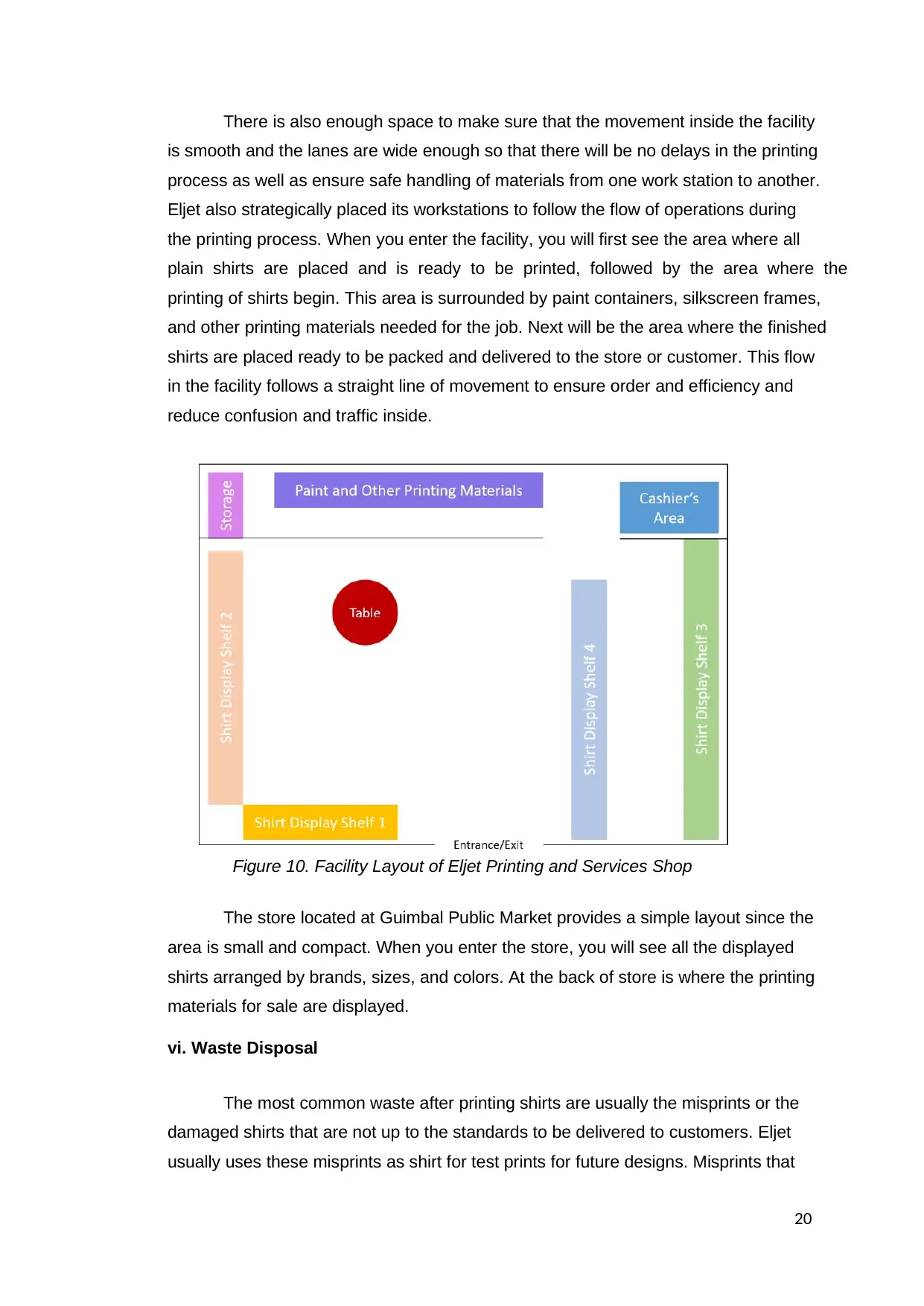
20
Figure 10. Facility Layout of Eljet Printing and Services Shop
There is also enough space to make sure that the movement inside the facility
is smooth and the lanes are wide enough so that there will be no delays in the printing
process as well as ensure safe handling of materials from one work station to another.
Eljet also strategically placed its workstations to follow the flow of operations during
the printing process. When you enter the facility, you will first see the area where all
plain shirts are placed and is ready to be printed, followed by the area where the
printing of shirts begin. This area is surrounded by paint containers, silkscreen frames,
and other printing materials needed for the job. Next will be the area where the finished
shirts are placed ready to be packed and delivered to the store or customer. This flow
in the facility follows a straight line of movement to ensure order and efficiency and
reduce confusion and traffic inside.
The store located at Guimbal Public Market provides a simple layout since the
area is small and compact. When you enter the store, you will see all the displayed
shirts arranged by brands, sizes, and colors. At the back of store is where the printing
materials for sale are displayed.
vi. Waste Disposal
The most common waste after printing shirts are usually the misprints or the
damaged shirts that are not up to the standards to be delivered to customers. Eljet
usually uses these misprints as shirt for test prints for future designs. Misprints that
Figure 10. Facility Layout of Eljet Printing and Services Shop
There is also enough space to make sure that the movement inside the facility
is smooth and the lanes are wide enough so that there will be no delays in the printing
process as well as ensure safe handling of materials from one work station to another.
Eljet also strategically placed its workstations to follow the flow of operations during
the printing process. When you enter the facility, you will first see the area where all
plain shirts are placed and is ready to be printed, followed by the area where the
printing of shirts begin. This area is surrounded by paint containers, silkscreen frames,
and other printing materials needed for the job. Next will be the area where the finished
shirts are placed ready to be packed and delivered to the store or customer. This flow
in the facility follows a straight line of movement to ensure order and efficiency and
reduce confusion and traffic inside.
The store located at Guimbal Public Market provides a simple layout since the
area is small and compact. When you enter the store, you will see all the displayed
shirts arranged by brands, sizes, and colors. At the back of store is where the printing
materials for sale are displayed.
vi. Waste Disposal
The most common waste after printing shirts are usually the misprints or the
damaged shirts that are not up to the standards to be delivered to customers. Eljet
usually uses these misprints as shirt for test prints for future designs. Misprints that
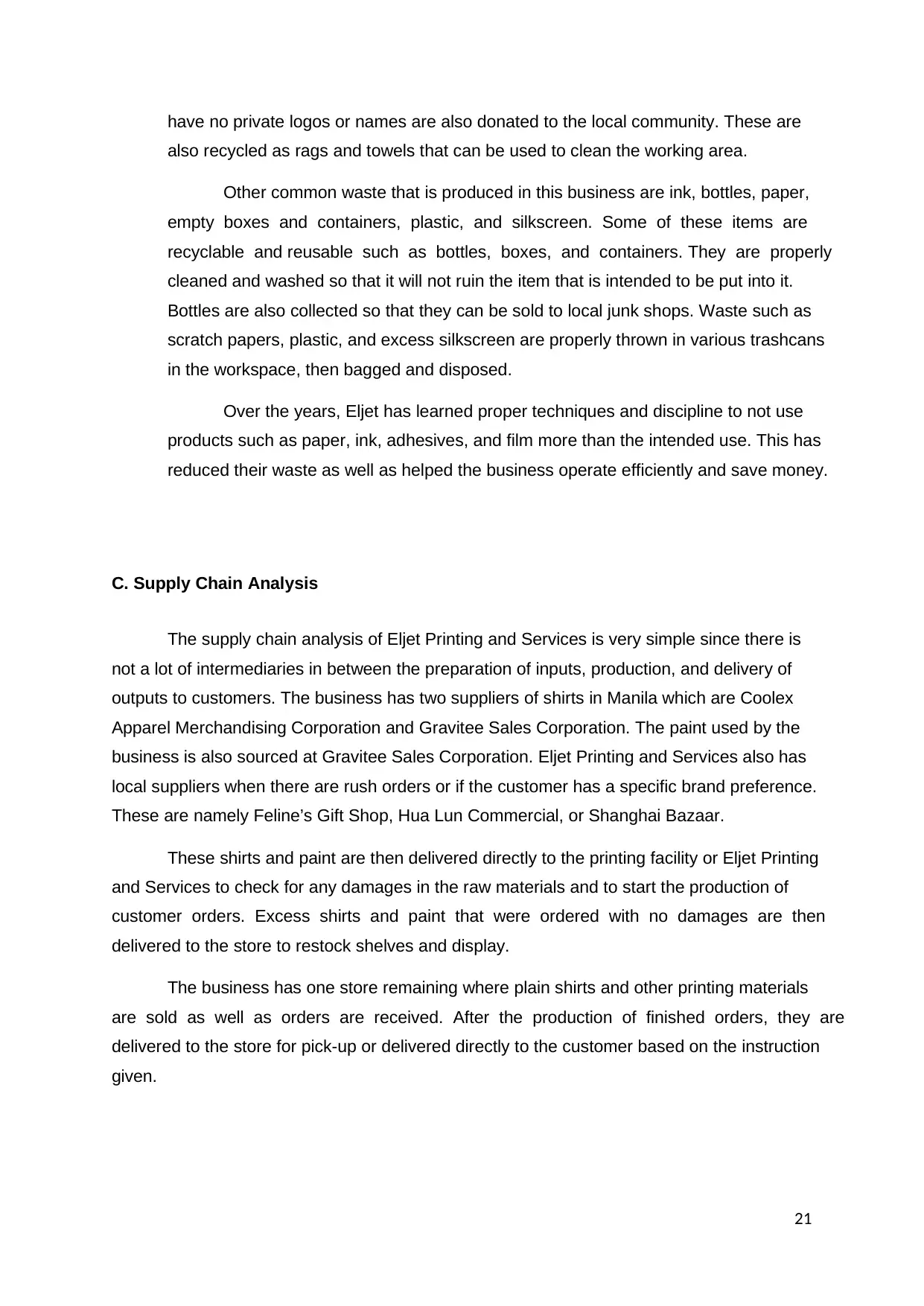
21
have no private logos or names are also donated to the local community. These are
also recycled as rags and towels that can be used to clean the working area.
Other common waste that is produced in this business are ink, bottles, paper,
empty boxes and containers, plastic, and silkscreen. Some of these items are
recyclable and reusable such as bottles, boxes, and containers. They are properly
cleaned and washed so that it will not ruin the item that is intended to be put into it.
Bottles are also collected so that they can be sold to local junk shops. Waste such as
scratch papers, plastic, and excess silkscreen are properly thrown in various trashcans
in the workspace, then bagged and disposed.
Over the years, Eljet has learned proper techniques and discipline to not use
products such as paper, ink, adhesives, and film more than the intended use. This has
reduced their waste as well as helped the business operate efficiently and save money.
C. Supply Chain Analysis
The supply chain analysis of Eljet Printing and Services is very simple since there is
not a lot of intermediaries in between the preparation of inputs, production, and delivery of
outputs to customers. The business has two suppliers of shirts in Manila which are Coolex
Apparel Merchandising Corporation and Gravitee Sales Corporation. The paint used by the
business is also sourced at Gravitee Sales Corporation. Eljet Printing and Services also has
local suppliers when there are rush orders or if the customer has a specific brand preference.
These are namely Feline’s Gift Shop, Hua Lun Commercial, or Shanghai Bazaar.
These shirts and paint are then delivered directly to the printing facility or Eljet Printing
and Services to check for any damages in the raw materials and to start the production of
customer orders. Excess shirts and paint that were ordered with no damages are then
delivered to the store to restock shelves and display.
The business has one store remaining where plain shirts and other printing materials
are sold as well as orders are received. After the production of finished orders, they are
delivered to the store for pick-up or delivered directly to the customer based on the instruction
given.
have no private logos or names are also donated to the local community. These are
also recycled as rags and towels that can be used to clean the working area.
Other common waste that is produced in this business are ink, bottles, paper,
empty boxes and containers, plastic, and silkscreen. Some of these items are
recyclable and reusable such as bottles, boxes, and containers. They are properly
cleaned and washed so that it will not ruin the item that is intended to be put into it.
Bottles are also collected so that they can be sold to local junk shops. Waste such as
scratch papers, plastic, and excess silkscreen are properly thrown in various trashcans
in the workspace, then bagged and disposed.
Over the years, Eljet has learned proper techniques and discipline to not use
products such as paper, ink, adhesives, and film more than the intended use. This has
reduced their waste as well as helped the business operate efficiently and save money.
C. Supply Chain Analysis
The supply chain analysis of Eljet Printing and Services is very simple since there is
not a lot of intermediaries in between the preparation of inputs, production, and delivery of
outputs to customers. The business has two suppliers of shirts in Manila which are Coolex
Apparel Merchandising Corporation and Gravitee Sales Corporation. The paint used by the
business is also sourced at Gravitee Sales Corporation. Eljet Printing and Services also has
local suppliers when there are rush orders or if the customer has a specific brand preference.
These are namely Feline’s Gift Shop, Hua Lun Commercial, or Shanghai Bazaar.
These shirts and paint are then delivered directly to the printing facility or Eljet Printing
and Services to check for any damages in the raw materials and to start the production of
customer orders. Excess shirts and paint that were ordered with no damages are then
delivered to the store to restock shelves and display.
The business has one store remaining where plain shirts and other printing materials
are sold as well as orders are received. After the production of finished orders, they are
delivered to the store for pick-up or delivered directly to the customer based on the instruction
given.
Secure Best Marks with AI Grader
Need help grading? Try our AI Grader for instant feedback on your assignments.
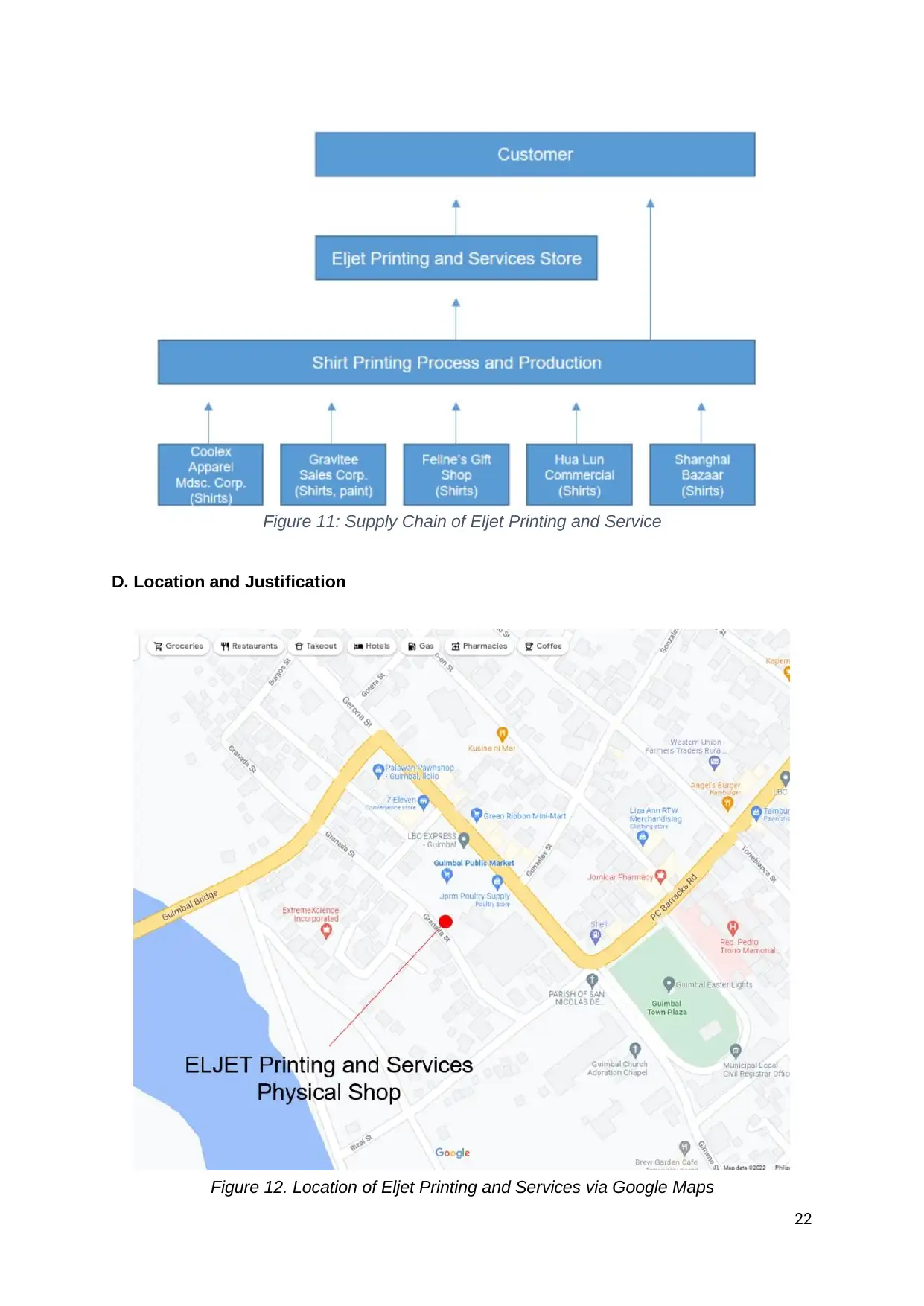
22
Figure 12. Location of Eljet Printing and Services via Google Maps
D. Location and Justification
Figure 11: Supply Chain of Eljet Printing and Service
Figure 12. Location of Eljet Printing and Services via Google Maps
D. Location and Justification
Figure 11: Supply Chain of Eljet Printing and Service

23
The remaining store of Eljet Printing and Services is located at the Guimbal Public
Market. This location was chosen due to the number of people passing by in the area. Because
the market is at the center of the municipality, a lot of businesses are situated in the area as
well. This makes the store of Eljet Printing and Services accessible to its customers. The
business is also renting a space at the market since it is a lot cheaper than buying a lot and
building a store from scratch.
IV. Recommendation
A. Identification of Problems/Points of Improvement
One of the areas where we see Eljet Printing and Services could improve is through
its employees. Most employees of the business are not knowledgeable when it comes to
information systems and technological resources such as the accounting system and
inventory control system that is currently implemented at the business. These employees goes
back to manual encoding of sales and checking of inventory, thus slowing down store
operations and reconciliation of data during reporting time.
Currently, Eljet Printing and Services is also experiencing high employee turnover
since the pandemic because the salary of workers especially its painters and editor are based
on the number of working days. Employees who stayed are also burdened by additional work
when one employee resigns. The salary of employees are competitive, however the work is
not regular. This causes delays in orders and production as well as low productivity to the
remaining employees.
In regards to their sales, Eljet Printing and Services do not properly forecast sales and
order of shirts and paints that is why they have a surplus of these items in their inventory. It is
mentioned by the owner that this surplus in inventory is because of the monthly order of stocks
to replenish the ones they used for production. However, when they have rush orders, they
buy needed stock again at suppliers in Iloilo City because their ordered shirts have not yet
been delivered. Therefore, shirts continue to pile up in their inventory and sold at a much later
period.
Furthermore, Eljet Printing and Services is currently not on any social media platform.
This does not only affect the marketing and advertising side of the business but it also limits
the means to get feedback from customers and to expand, as well. Currently, the business
depends on customers with repeat orders to get their feedback. Even if it is effective, it is still
The remaining store of Eljet Printing and Services is located at the Guimbal Public
Market. This location was chosen due to the number of people passing by in the area. Because
the market is at the center of the municipality, a lot of businesses are situated in the area as
well. This makes the store of Eljet Printing and Services accessible to its customers. The
business is also renting a space at the market since it is a lot cheaper than buying a lot and
building a store from scratch.
IV. Recommendation
A. Identification of Problems/Points of Improvement
One of the areas where we see Eljet Printing and Services could improve is through
its employees. Most employees of the business are not knowledgeable when it comes to
information systems and technological resources such as the accounting system and
inventory control system that is currently implemented at the business. These employees goes
back to manual encoding of sales and checking of inventory, thus slowing down store
operations and reconciliation of data during reporting time.
Currently, Eljet Printing and Services is also experiencing high employee turnover
since the pandemic because the salary of workers especially its painters and editor are based
on the number of working days. Employees who stayed are also burdened by additional work
when one employee resigns. The salary of employees are competitive, however the work is
not regular. This causes delays in orders and production as well as low productivity to the
remaining employees.
In regards to their sales, Eljet Printing and Services do not properly forecast sales and
order of shirts and paints that is why they have a surplus of these items in their inventory. It is
mentioned by the owner that this surplus in inventory is because of the monthly order of stocks
to replenish the ones they used for production. However, when they have rush orders, they
buy needed stock again at suppliers in Iloilo City because their ordered shirts have not yet
been delivered. Therefore, shirts continue to pile up in their inventory and sold at a much later
period.
Furthermore, Eljet Printing and Services is currently not on any social media platform.
This does not only affect the marketing and advertising side of the business but it also limits
the means to get feedback from customers and to expand, as well. Currently, the business
depends on customers with repeat orders to get their feedback. Even if it is effective, it is still
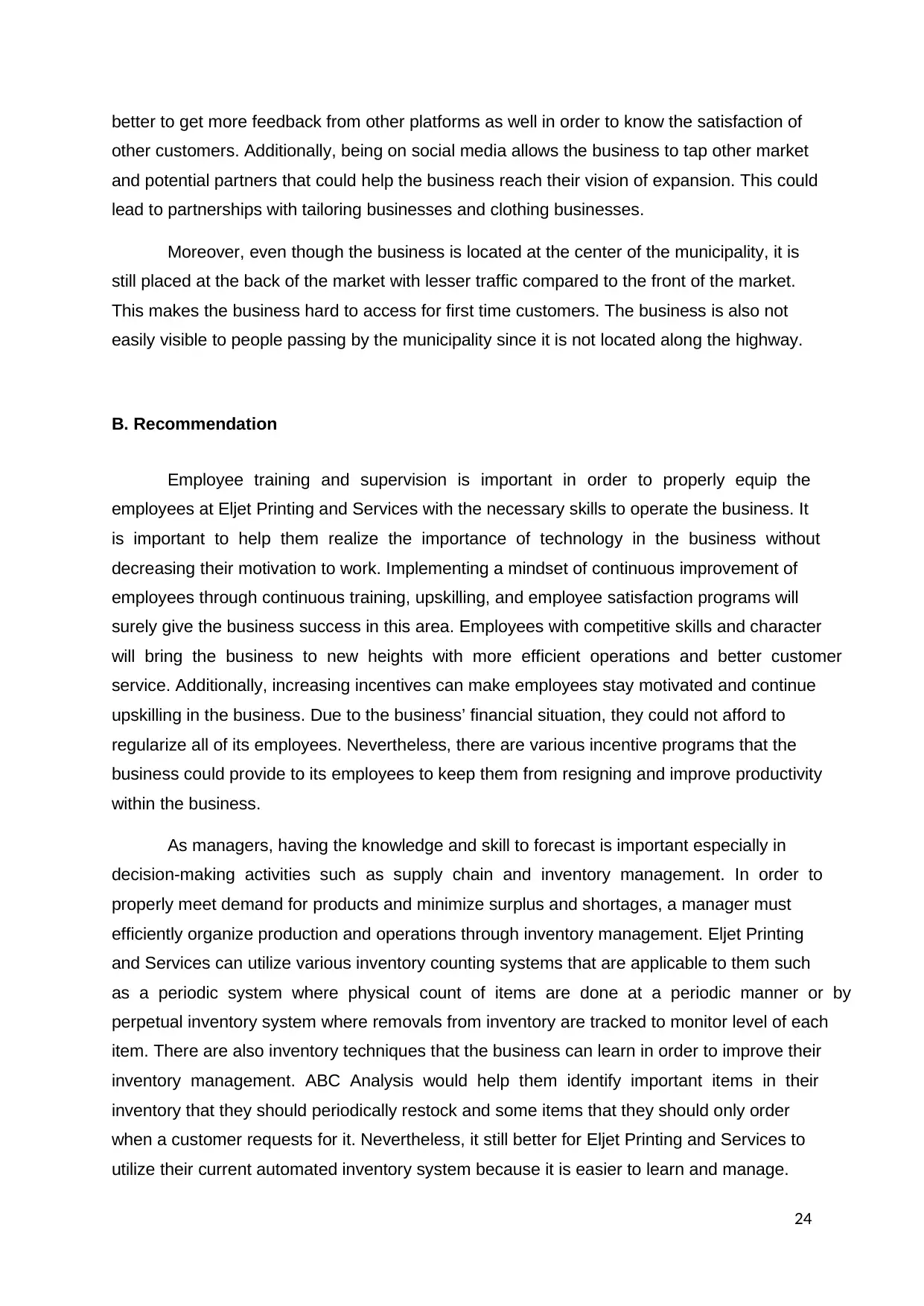
24
better to get more feedback from other platforms as well in order to know the satisfaction of
other customers. Additionally, being on social media allows the business to tap other market
and potential partners that could help the business reach their vision of expansion. This could
lead to partnerships with tailoring businesses and clothing businesses.
Moreover, even though the business is located at the center of the municipality, it is
still placed at the back of the market with lesser traffic compared to the front of the market.
This makes the business hard to access for first time customers. The business is also not
easily visible to people passing by the municipality since it is not located along the highway.
B. Recommendation
Employee training and supervision is important in order to properly equip the
employees at Eljet Printing and Services with the necessary skills to operate the business. It
is important to help them realize the importance of technology in the business without
decreasing their motivation to work. Implementing a mindset of continuous improvement of
employees through continuous training, upskilling, and employee satisfaction programs will
surely give the business success in this area. Employees with competitive skills and character
will bring the business to new heights with more efficient operations and better customer
service. Additionally, increasing incentives can make employees stay motivated and continue
upskilling in the business. Due to the business’ financial situation, they could not afford to
regularize all of its employees. Nevertheless, there are various incentive programs that the
business could provide to its employees to keep them from resigning and improve productivity
within the business.
As managers, having the knowledge and skill to forecast is important especially in
decision-making activities such as supply chain and inventory management. In order to
properly meet demand for products and minimize surplus and shortages, a manager must
efficiently organize production and operations through inventory management. Eljet Printing
and Services can utilize various inventory counting systems that are applicable to them such
as a periodic system where physical count of items are done at a periodic manner or by
perpetual inventory system where removals from inventory are tracked to monitor level of each
item. There are also inventory techniques that the business can learn in order to improve their
inventory management. ABC Analysis would help them identify important items in their
inventory that they should periodically restock and some items that they should only order
when a customer requests for it. Nevertheless, it still better for Eljet Printing and Services to
utilize their current automated inventory system because it is easier to learn and manage.
better to get more feedback from other platforms as well in order to know the satisfaction of
other customers. Additionally, being on social media allows the business to tap other market
and potential partners that could help the business reach their vision of expansion. This could
lead to partnerships with tailoring businesses and clothing businesses.
Moreover, even though the business is located at the center of the municipality, it is
still placed at the back of the market with lesser traffic compared to the front of the market.
This makes the business hard to access for first time customers. The business is also not
easily visible to people passing by the municipality since it is not located along the highway.
B. Recommendation
Employee training and supervision is important in order to properly equip the
employees at Eljet Printing and Services with the necessary skills to operate the business. It
is important to help them realize the importance of technology in the business without
decreasing their motivation to work. Implementing a mindset of continuous improvement of
employees through continuous training, upskilling, and employee satisfaction programs will
surely give the business success in this area. Employees with competitive skills and character
will bring the business to new heights with more efficient operations and better customer
service. Additionally, increasing incentives can make employees stay motivated and continue
upskilling in the business. Due to the business’ financial situation, they could not afford to
regularize all of its employees. Nevertheless, there are various incentive programs that the
business could provide to its employees to keep them from resigning and improve productivity
within the business.
As managers, having the knowledge and skill to forecast is important especially in
decision-making activities such as supply chain and inventory management. In order to
properly meet demand for products and minimize surplus and shortages, a manager must
efficiently organize production and operations through inventory management. Eljet Printing
and Services can utilize various inventory counting systems that are applicable to them such
as a periodic system where physical count of items are done at a periodic manner or by
perpetual inventory system where removals from inventory are tracked to monitor level of each
item. There are also inventory techniques that the business can learn in order to improve their
inventory management. ABC Analysis would help them identify important items in their
inventory that they should periodically restock and some items that they should only order
when a customer requests for it. Nevertheless, it still better for Eljet Printing and Services to
utilize their current automated inventory system because it is easier to learn and manage.
Paraphrase This Document
Need a fresh take? Get an instant paraphrase of this document with our AI Paraphraser
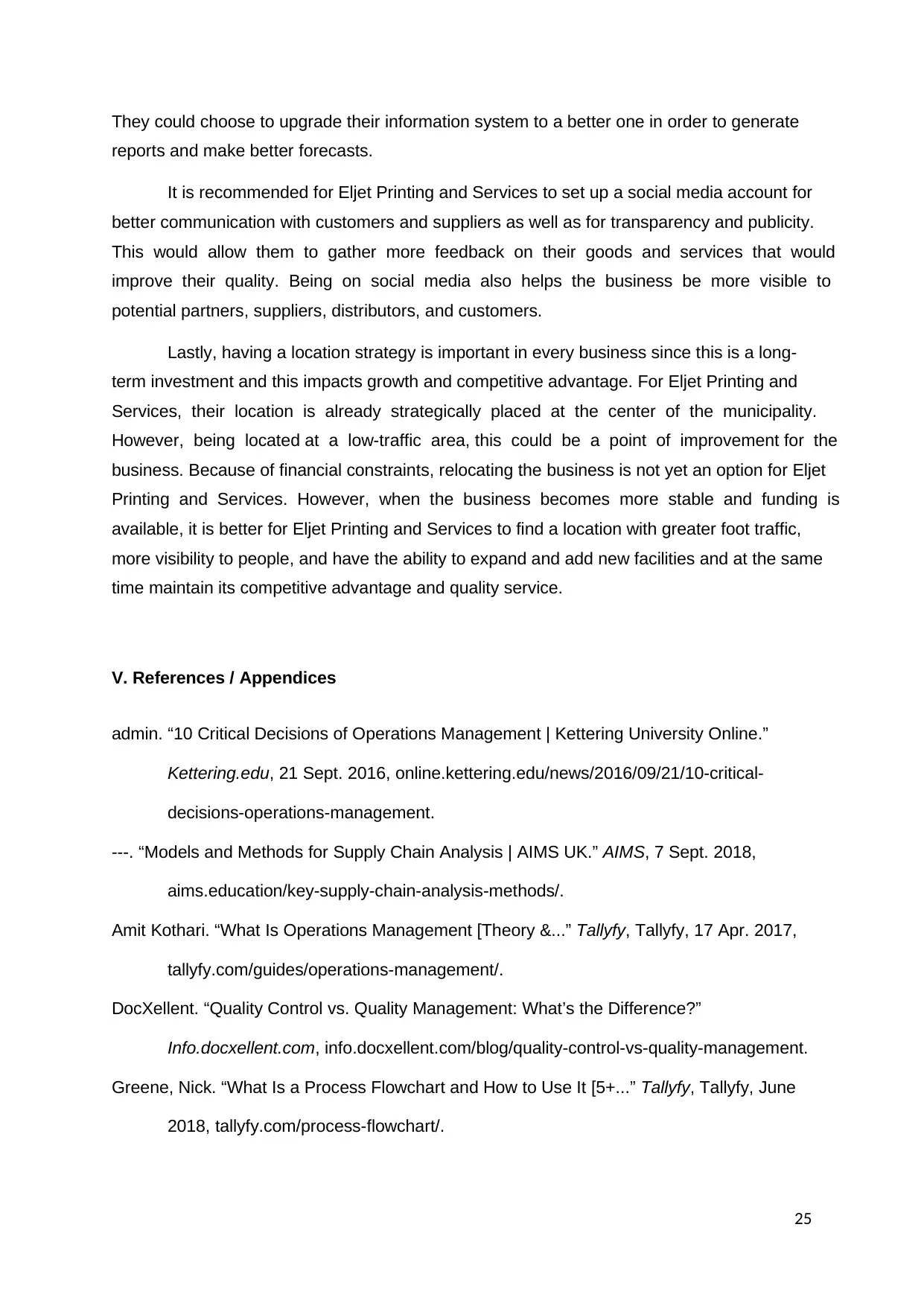
25
They could choose to upgrade their information system to a better one in order to generate
reports and make better forecasts.
It is recommended for Eljet Printing and Services to set up a social media account for
better communication with customers and suppliers as well as for transparency and publicity.
This would allow them to gather more feedback on their goods and services that would
improve their quality. Being on social media also helps the business be more visible to
potential partners, suppliers, distributors, and customers.
Lastly, having a location strategy is important in every business since this is a long-
term investment and this impacts growth and competitive advantage. For Eljet Printing and
Services, their location is already strategically placed at the center of the municipality.
However, being located at a low-traffic area, this could be a point of improvement for the
business. Because of financial constraints, relocating the business is not yet an option for Eljet
Printing and Services. However, when the business becomes more stable and funding is
available, it is better for Eljet Printing and Services to find a location with greater foot traffic,
more visibility to people, and have the ability to expand and add new facilities and at the same
time maintain its competitive advantage and quality service.
V. References / Appendices
admin. “10 Critical Decisions of Operations Management | Kettering University Online.”
Kettering.edu, 21 Sept. 2016, online.kettering.edu/news/2016/09/21/10-critical-
decisions-operations-management.
---. “Models and Methods for Supply Chain Analysis | AIMS UK.” AIMS, 7 Sept. 2018,
aims.education/key-supply-chain-analysis-methods/.
Amit Kothari. “What Is Operations Management [Theory &...” Tallyfy, Tallyfy, 17 Apr. 2017,
tallyfy.com/guides/operations-management/.
DocXellent. “Quality Control vs. Quality Management: What’s the Difference?”
Info.docxellent.com, info.docxellent.com/blog/quality-control-vs-quality-management.
Greene, Nick. “What Is a Process Flowchart and How to Use It [5+...” Tallyfy, Tallyfy, June
2018, tallyfy.com/process-flowchart/.
They could choose to upgrade their information system to a better one in order to generate
reports and make better forecasts.
It is recommended for Eljet Printing and Services to set up a social media account for
better communication with customers and suppliers as well as for transparency and publicity.
This would allow them to gather more feedback on their goods and services that would
improve their quality. Being on social media also helps the business be more visible to
potential partners, suppliers, distributors, and customers.
Lastly, having a location strategy is important in every business since this is a long-
term investment and this impacts growth and competitive advantage. For Eljet Printing and
Services, their location is already strategically placed at the center of the municipality.
However, being located at a low-traffic area, this could be a point of improvement for the
business. Because of financial constraints, relocating the business is not yet an option for Eljet
Printing and Services. However, when the business becomes more stable and funding is
available, it is better for Eljet Printing and Services to find a location with greater foot traffic,
more visibility to people, and have the ability to expand and add new facilities and at the same
time maintain its competitive advantage and quality service.
V. References / Appendices
admin. “10 Critical Decisions of Operations Management | Kettering University Online.”
Kettering.edu, 21 Sept. 2016, online.kettering.edu/news/2016/09/21/10-critical-
decisions-operations-management.
---. “Models and Methods for Supply Chain Analysis | AIMS UK.” AIMS, 7 Sept. 2018,
aims.education/key-supply-chain-analysis-methods/.
Amit Kothari. “What Is Operations Management [Theory &...” Tallyfy, Tallyfy, 17 Apr. 2017,
tallyfy.com/guides/operations-management/.
DocXellent. “Quality Control vs. Quality Management: What’s the Difference?”
Info.docxellent.com, info.docxellent.com/blog/quality-control-vs-quality-management.
Greene, Nick. “What Is a Process Flowchart and How to Use It [5+...” Tallyfy, Tallyfy, June
2018, tallyfy.com/process-flowchart/.
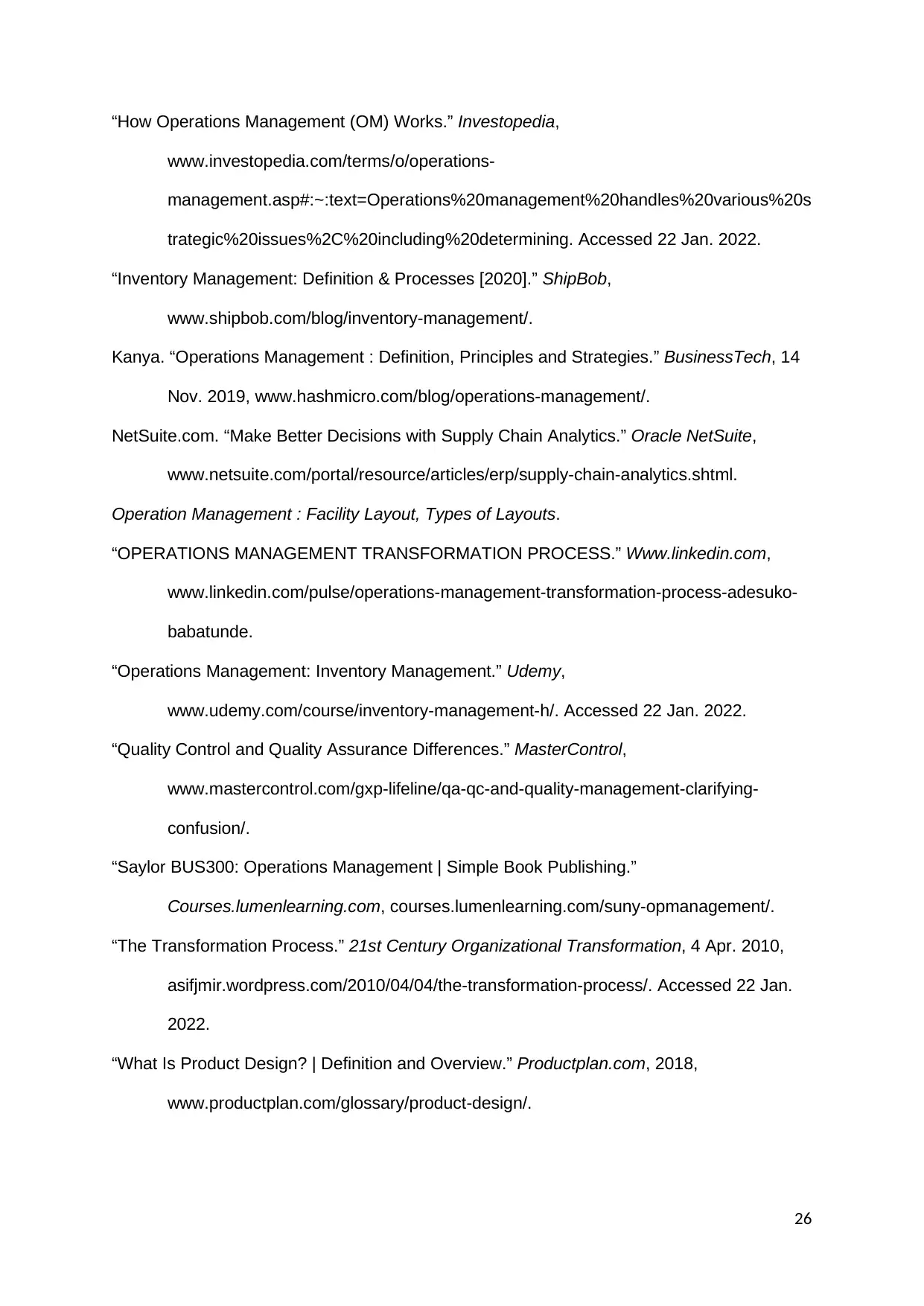
26
“How Operations Management (OM) Works.” Investopedia,
www.investopedia.com/terms/o/operations-
management.asp#:~:text=Operations%20management%20handles%20various%20s
trategic%20issues%2C%20including%20determining. Accessed 22 Jan. 2022.
“Inventory Management: Definition & Processes [2020].” ShipBob,
www.shipbob.com/blog/inventory-management/.
Kanya. “Operations Management : Definition, Principles and Strategies.” BusinessTech, 14
Nov. 2019, www.hashmicro.com/blog/operations-management/.
NetSuite.com. “Make Better Decisions with Supply Chain Analytics.” Oracle NetSuite,
www.netsuite.com/portal/resource/articles/erp/supply-chain-analytics.shtml.
Operation Management : Facility Layout, Types of Layouts.
“OPERATIONS MANAGEMENT TRANSFORMATION PROCESS.” Www.linkedin.com,
www.linkedin.com/pulse/operations-management-transformation-process-adesuko-
babatunde.
“Operations Management: Inventory Management.” Udemy,
www.udemy.com/course/inventory-management-h/. Accessed 22 Jan. 2022.
“Quality Control and Quality Assurance Differences.” MasterControl,
www.mastercontrol.com/gxp-lifeline/qa-qc-and-quality-management-clarifying-
confusion/.
“Saylor BUS300: Operations Management | Simple Book Publishing.”
Courses.lumenlearning.com, courses.lumenlearning.com/suny-opmanagement/.
“The Transformation Process.” 21st Century Organizational Transformation, 4 Apr. 2010,
asifjmir.wordpress.com/2010/04/04/the-transformation-process/. Accessed 22 Jan.
2022.
“What Is Product Design? | Definition and Overview.” Productplan.com, 2018,
www.productplan.com/glossary/product-design/.
“How Operations Management (OM) Works.” Investopedia,
www.investopedia.com/terms/o/operations-
management.asp#:~:text=Operations%20management%20handles%20various%20s
trategic%20issues%2C%20including%20determining. Accessed 22 Jan. 2022.
“Inventory Management: Definition & Processes [2020].” ShipBob,
www.shipbob.com/blog/inventory-management/.
Kanya. “Operations Management : Definition, Principles and Strategies.” BusinessTech, 14
Nov. 2019, www.hashmicro.com/blog/operations-management/.
NetSuite.com. “Make Better Decisions with Supply Chain Analytics.” Oracle NetSuite,
www.netsuite.com/portal/resource/articles/erp/supply-chain-analytics.shtml.
Operation Management : Facility Layout, Types of Layouts.
“OPERATIONS MANAGEMENT TRANSFORMATION PROCESS.” Www.linkedin.com,
www.linkedin.com/pulse/operations-management-transformation-process-adesuko-
babatunde.
“Operations Management: Inventory Management.” Udemy,
www.udemy.com/course/inventory-management-h/. Accessed 22 Jan. 2022.
“Quality Control and Quality Assurance Differences.” MasterControl,
www.mastercontrol.com/gxp-lifeline/qa-qc-and-quality-management-clarifying-
confusion/.
“Saylor BUS300: Operations Management | Simple Book Publishing.”
Courses.lumenlearning.com, courses.lumenlearning.com/suny-opmanagement/.
“The Transformation Process.” 21st Century Organizational Transformation, 4 Apr. 2010,
asifjmir.wordpress.com/2010/04/04/the-transformation-process/. Accessed 22 Jan.
2022.
“What Is Product Design? | Definition and Overview.” Productplan.com, 2018,
www.productplan.com/glossary/product-design/.
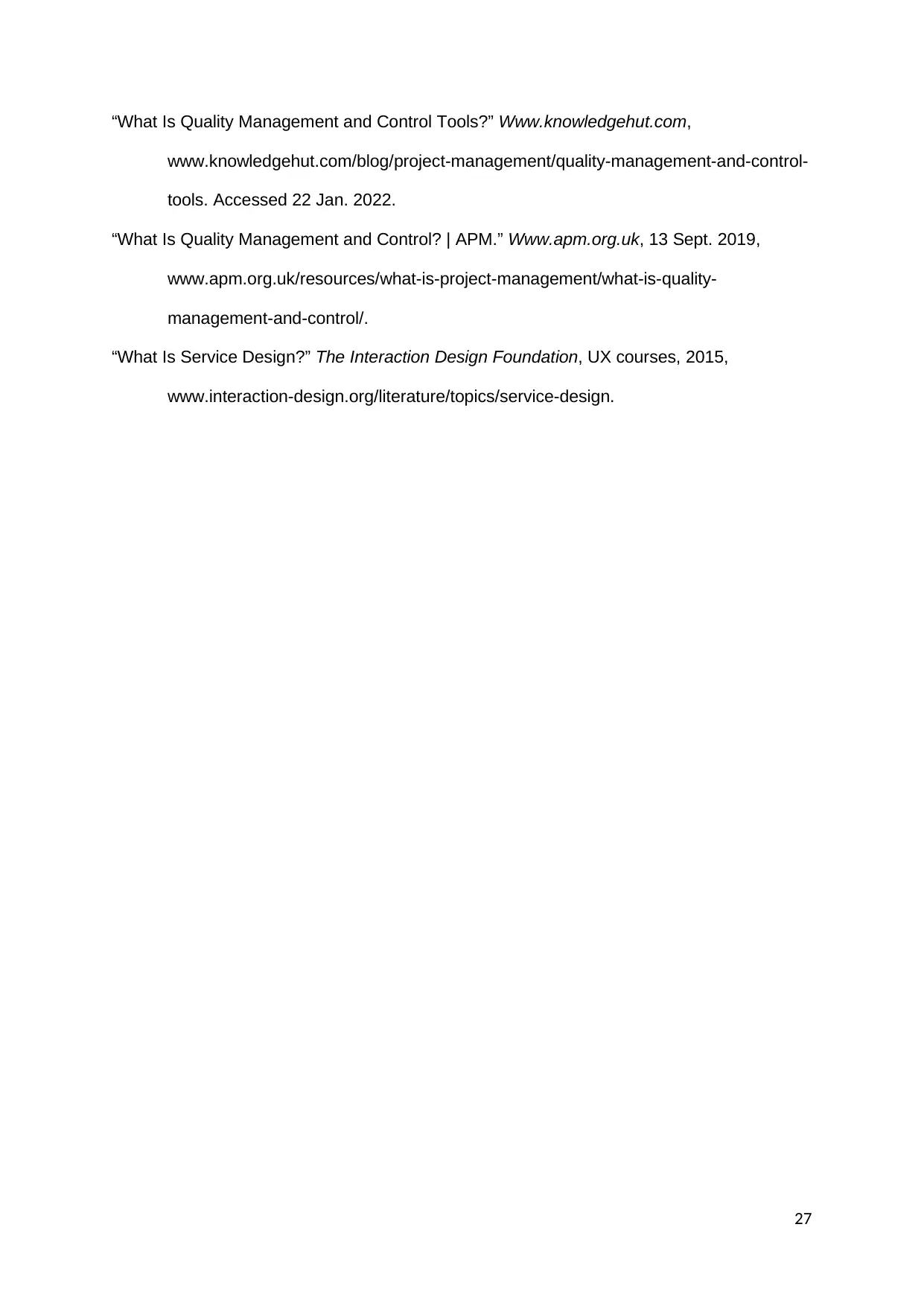
27
“What Is Quality Management and Control Tools?” Www.knowledgehut.com,
www.knowledgehut.com/blog/project-management/quality-management-and-control-
tools. Accessed 22 Jan. 2022.
“What Is Quality Management and Control? | APM.” Www.apm.org.uk, 13 Sept. 2019,
www.apm.org.uk/resources/what-is-project-management/what-is-quality-
management-and-control/.
“What Is Service Design?” The Interaction Design Foundation, UX courses, 2015,
www.interaction-design.org/literature/topics/service-design.
“What Is Quality Management and Control Tools?” Www.knowledgehut.com,
www.knowledgehut.com/blog/project-management/quality-management-and-control-
tools. Accessed 22 Jan. 2022.
“What Is Quality Management and Control? | APM.” Www.apm.org.uk, 13 Sept. 2019,
www.apm.org.uk/resources/what-is-project-management/what-is-quality-
management-and-control/.
“What Is Service Design?” The Interaction Design Foundation, UX courses, 2015,
www.interaction-design.org/literature/topics/service-design.
1 out of 28
Related Documents
![[object Object]](/_next/image/?url=%2F_next%2Fstatic%2Fmedia%2Flogo.6d15ce61.png&w=640&q=75)
Your All-in-One AI-Powered Toolkit for Academic Success.
+13062052269
info@desklib.com
Available 24*7 on WhatsApp / Email
Unlock your academic potential
© 2024 | Zucol Services PVT LTD | All rights reserved.