Operations Management Systems: Pre-lecture Questions
VerifiedAdded on 2022/11/18
|19
|4994
|233
AI Summary
This document covers pre-lecture questions related to Operations Management Systems including operations as a transformation process, major decision-making processes, competitiveness of business organization, productivity, influence of non-economic factors on make-or-buy decisions, types of processes, line balancing, job design and methods analysis, stopwatch time study, determinants of quality, costs of quality, quality-productivity ratio, control chart: c-chart, aggregate planning, strategies of aggregate planning, available-to-promise inventory, rough-cut capacity planning, material requirement planning MRP I, MRP: Outputs, lot sizing in MRP processing, capacity requirement planning, MRP II and ERP, ultimate goal of lean operation, waste in lean systems, design and operation of lean system, SMED (Single-minute exchange of die) relation with lean operation, difference between push systems and pull systems, Kanban Calculation, and significance of Operation Management.
Contribute Materials
Your contribution can guide someone’s learning journey. Share your
documents today.
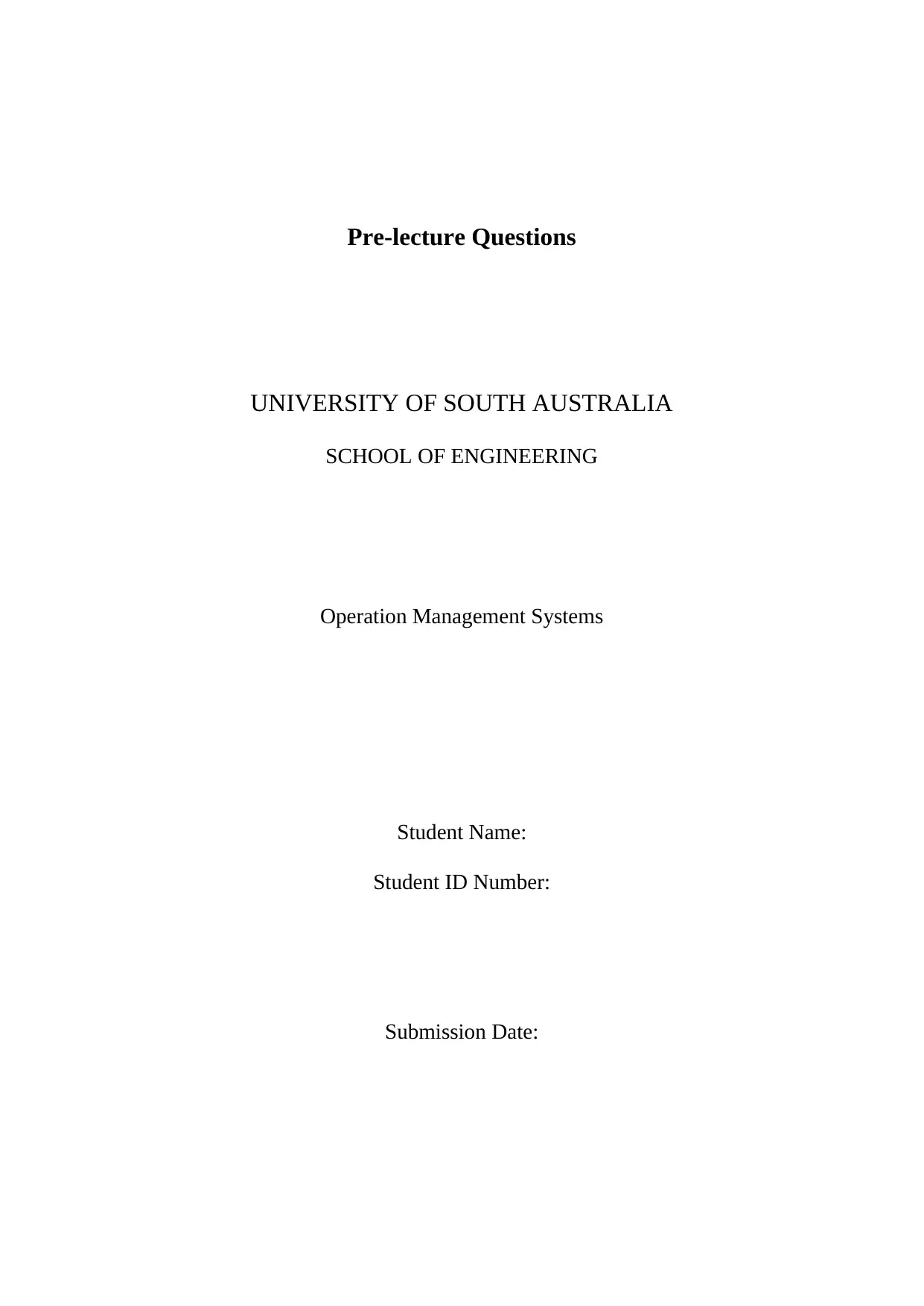
Pre-lecture Questions
UNIVERSITY OF SOUTH AUSTRALIA
SCHOOL OF ENGINEERING
Operation Management Systems
Student Name:
Student ID Number:
Submission Date:
UNIVERSITY OF SOUTH AUSTRALIA
SCHOOL OF ENGINEERING
Operation Management Systems
Student Name:
Student ID Number:
Submission Date:
Secure Best Marks with AI Grader
Need help grading? Try our AI Grader for instant feedback on your assignments.
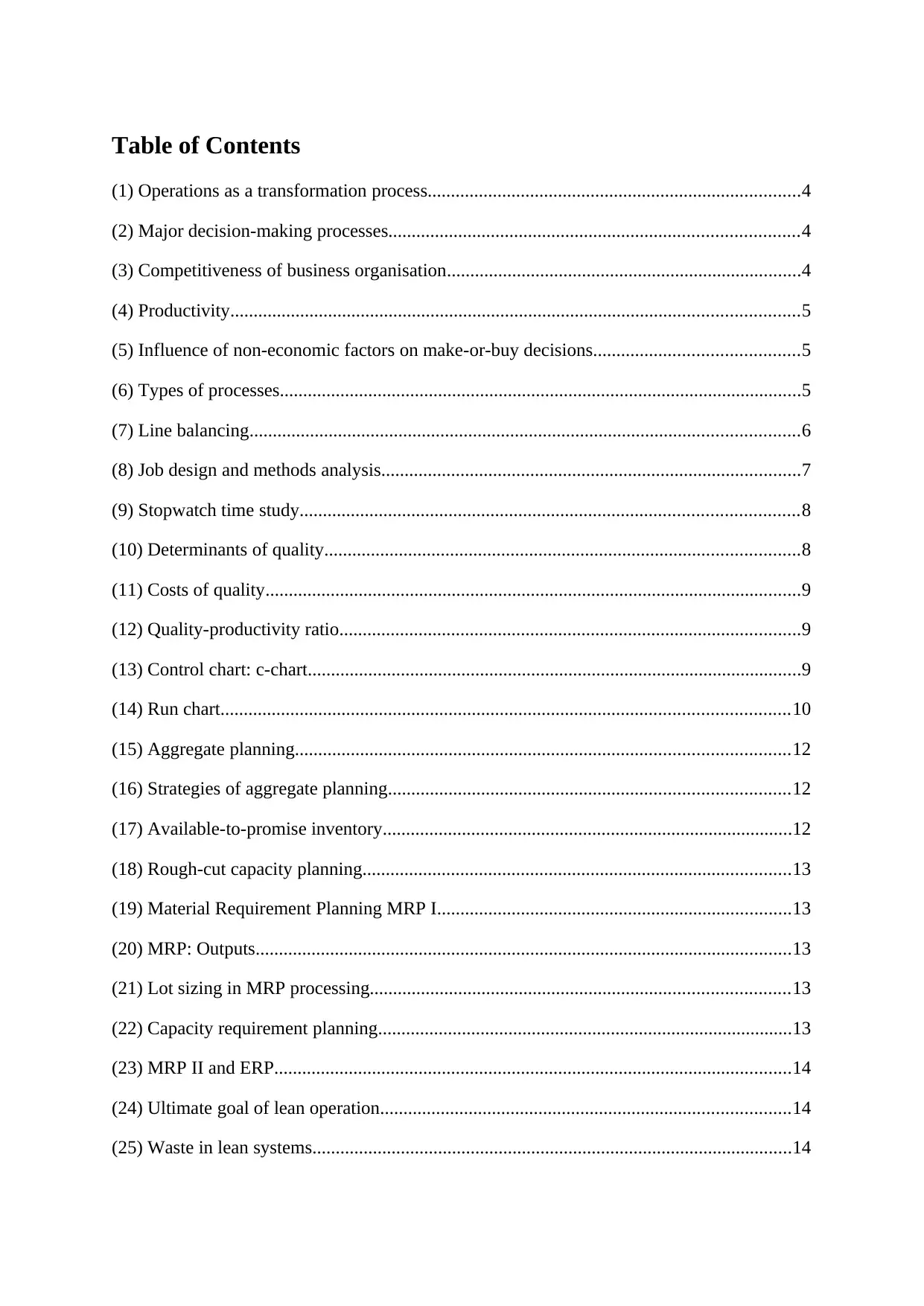
Table of Contents
(1) Operations as a transformation process................................................................................4
(2) Major decision-making processes........................................................................................4
(3) Competitiveness of business organisation............................................................................4
(4) Productivity..........................................................................................................................5
(5) Influence of non-economic factors on make-or-buy decisions............................................5
(6) Types of processes................................................................................................................5
(7) Line balancing......................................................................................................................6
(8) Job design and methods analysis..........................................................................................7
(9) Stopwatch time study...........................................................................................................8
(10) Determinants of quality......................................................................................................8
(11) Costs of quality...................................................................................................................9
(12) Quality-productivity ratio...................................................................................................9
(13) Control chart: c-chart..........................................................................................................9
(14) Run chart..........................................................................................................................10
(15) Aggregate planning..........................................................................................................12
(16) Strategies of aggregate planning......................................................................................12
(17) Available-to-promise inventory........................................................................................12
(18) Rough-cut capacity planning............................................................................................13
(19) Material Requirement Planning MRP I............................................................................13
(20) MRP: Outputs...................................................................................................................13
(21) Lot sizing in MRP processing..........................................................................................13
(22) Capacity requirement planning.........................................................................................13
(23) MRP II and ERP...............................................................................................................14
(24) Ultimate goal of lean operation........................................................................................14
(25) Waste in lean systems.......................................................................................................14
(1) Operations as a transformation process................................................................................4
(2) Major decision-making processes........................................................................................4
(3) Competitiveness of business organisation............................................................................4
(4) Productivity..........................................................................................................................5
(5) Influence of non-economic factors on make-or-buy decisions............................................5
(6) Types of processes................................................................................................................5
(7) Line balancing......................................................................................................................6
(8) Job design and methods analysis..........................................................................................7
(9) Stopwatch time study...........................................................................................................8
(10) Determinants of quality......................................................................................................8
(11) Costs of quality...................................................................................................................9
(12) Quality-productivity ratio...................................................................................................9
(13) Control chart: c-chart..........................................................................................................9
(14) Run chart..........................................................................................................................10
(15) Aggregate planning..........................................................................................................12
(16) Strategies of aggregate planning......................................................................................12
(17) Available-to-promise inventory........................................................................................12
(18) Rough-cut capacity planning............................................................................................13
(19) Material Requirement Planning MRP I............................................................................13
(20) MRP: Outputs...................................................................................................................13
(21) Lot sizing in MRP processing..........................................................................................13
(22) Capacity requirement planning.........................................................................................13
(23) MRP II and ERP...............................................................................................................14
(24) Ultimate goal of lean operation........................................................................................14
(25) Waste in lean systems.......................................................................................................14
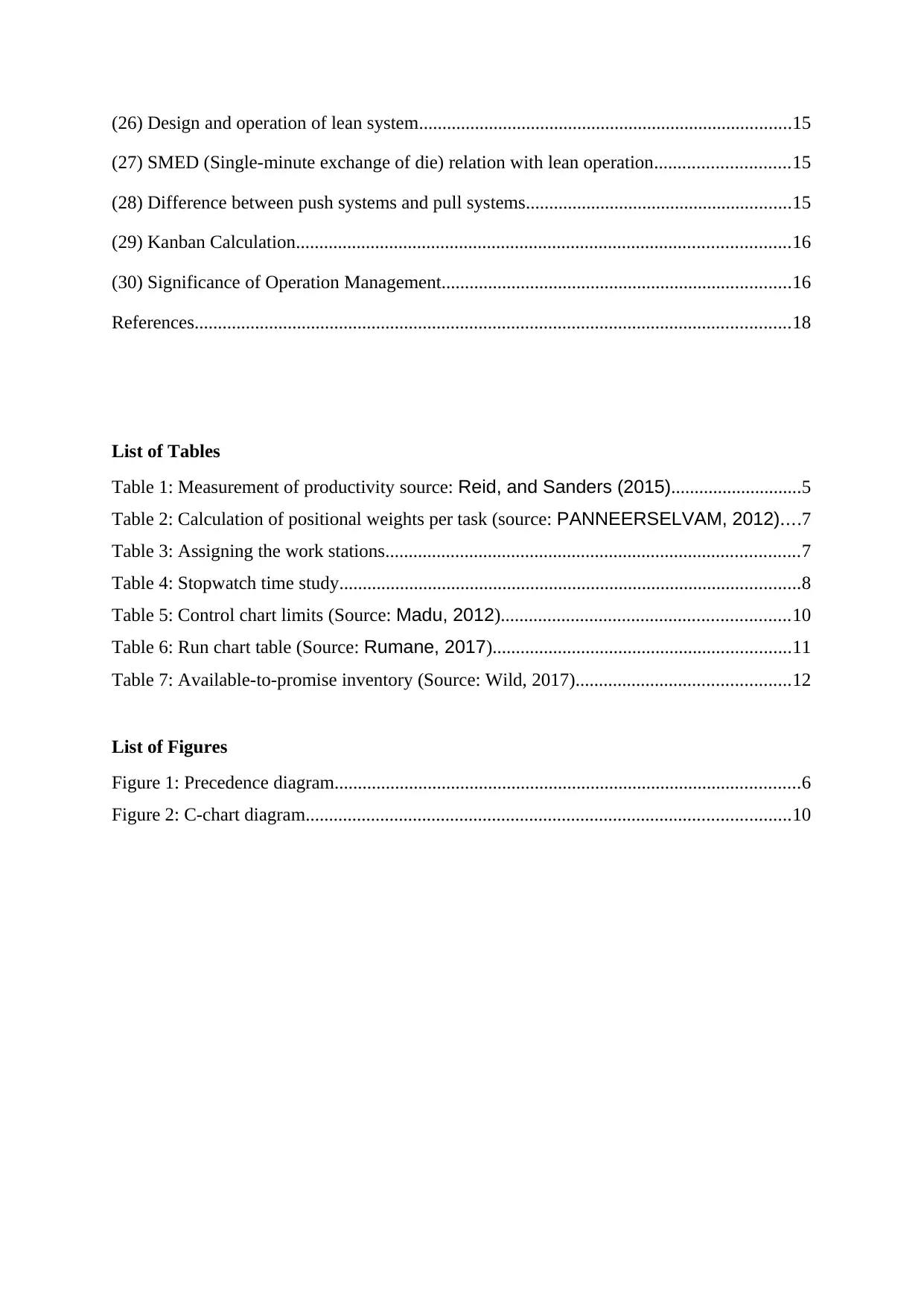
(26) Design and operation of lean system................................................................................15
(27) SMED (Single-minute exchange of die) relation with lean operation.............................15
(28) Difference between push systems and pull systems.........................................................15
(29) Kanban Calculation..........................................................................................................16
(30) Significance of Operation Management...........................................................................16
References................................................................................................................................18
List of Tables
Table 1: Measurement of productivity source: Reid, and Sanders (2015)............................5
Table 2: Calculation of positional weights per task (source: PANNEERSELVAM, 2012)....7
Table 3: Assigning the work stations.........................................................................................7
Table 4: Stopwatch time study...................................................................................................8
Table 5: Control chart limits (Source: Madu, 2012)..............................................................10
Table 6: Run chart table (Source: Rumane, 2017)................................................................11
Table 7: Available-to-promise inventory (Source: Wild, 2017)..............................................12
List of Figures
Figure 1: Precedence diagram....................................................................................................6
Figure 2: C-chart diagram........................................................................................................10
(27) SMED (Single-minute exchange of die) relation with lean operation.............................15
(28) Difference between push systems and pull systems.........................................................15
(29) Kanban Calculation..........................................................................................................16
(30) Significance of Operation Management...........................................................................16
References................................................................................................................................18
List of Tables
Table 1: Measurement of productivity source: Reid, and Sanders (2015)............................5
Table 2: Calculation of positional weights per task (source: PANNEERSELVAM, 2012)....7
Table 3: Assigning the work stations.........................................................................................7
Table 4: Stopwatch time study...................................................................................................8
Table 5: Control chart limits (Source: Madu, 2012)..............................................................10
Table 6: Run chart table (Source: Rumane, 2017)................................................................11
Table 7: Available-to-promise inventory (Source: Wild, 2017)..............................................12
List of Figures
Figure 1: Precedence diagram....................................................................................................6
Figure 2: C-chart diagram........................................................................................................10
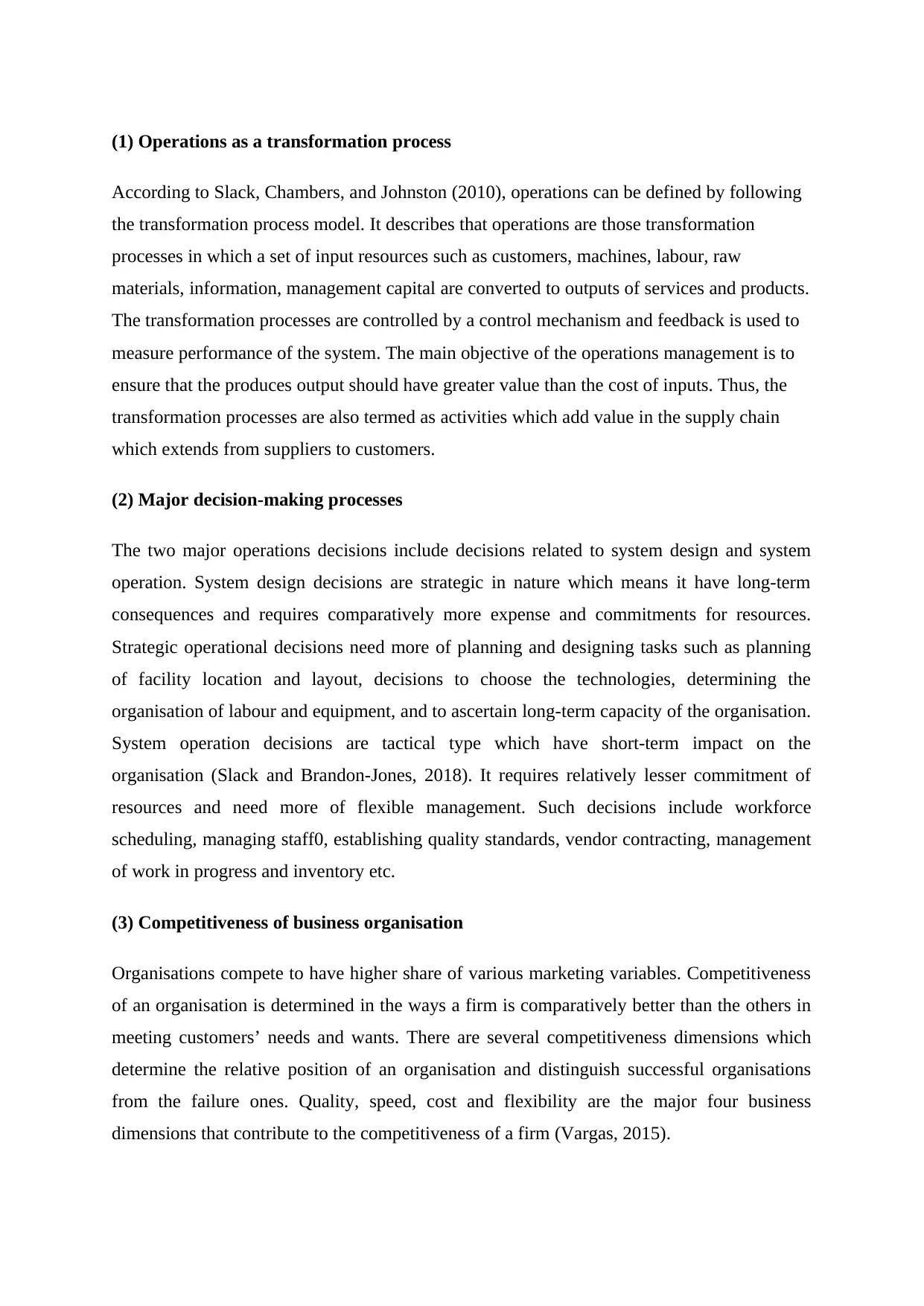
(1) Operations as a transformation process
According to Slack, Chambers, and Johnston (2010), operations can be defined by following
the transformation process model. It describes that operations are those transformation
processes in which a set of input resources such as customers, machines, labour, raw
materials, information, management capital are converted to outputs of services and products.
The transformation processes are controlled by a control mechanism and feedback is used to
measure performance of the system. The main objective of the operations management is to
ensure that the produces output should have greater value than the cost of inputs. Thus, the
transformation processes are also termed as activities which add value in the supply chain
which extends from suppliers to customers.
(2) Major decision-making processes
The two major operations decisions include decisions related to system design and system
operation. System design decisions are strategic in nature which means it have long-term
consequences and requires comparatively more expense and commitments for resources.
Strategic operational decisions need more of planning and designing tasks such as planning
of facility location and layout, decisions to choose the technologies, determining the
organisation of labour and equipment, and to ascertain long-term capacity of the organisation.
System operation decisions are tactical type which have short-term impact on the
organisation (Slack and Brandon-Jones, 2018). It requires relatively lesser commitment of
resources and need more of flexible management. Such decisions include workforce
scheduling, managing staff0, establishing quality standards, vendor contracting, management
of work in progress and inventory etc.
(3) Competitiveness of business organisation
Organisations compete to have higher share of various marketing variables. Competitiveness
of an organisation is determined in the ways a firm is comparatively better than the others in
meeting customers’ needs and wants. There are several competitiveness dimensions which
determine the relative position of an organisation and distinguish successful organisations
from the failure ones. Quality, speed, cost and flexibility are the major four business
dimensions that contribute to the competitiveness of a firm (Vargas, 2015).
According to Slack, Chambers, and Johnston (2010), operations can be defined by following
the transformation process model. It describes that operations are those transformation
processes in which a set of input resources such as customers, machines, labour, raw
materials, information, management capital are converted to outputs of services and products.
The transformation processes are controlled by a control mechanism and feedback is used to
measure performance of the system. The main objective of the operations management is to
ensure that the produces output should have greater value than the cost of inputs. Thus, the
transformation processes are also termed as activities which add value in the supply chain
which extends from suppliers to customers.
(2) Major decision-making processes
The two major operations decisions include decisions related to system design and system
operation. System design decisions are strategic in nature which means it have long-term
consequences and requires comparatively more expense and commitments for resources.
Strategic operational decisions need more of planning and designing tasks such as planning
of facility location and layout, decisions to choose the technologies, determining the
organisation of labour and equipment, and to ascertain long-term capacity of the organisation.
System operation decisions are tactical type which have short-term impact on the
organisation (Slack and Brandon-Jones, 2018). It requires relatively lesser commitment of
resources and need more of flexible management. Such decisions include workforce
scheduling, managing staff0, establishing quality standards, vendor contracting, management
of work in progress and inventory etc.
(3) Competitiveness of business organisation
Organisations compete to have higher share of various marketing variables. Competitiveness
of an organisation is determined in the ways a firm is comparatively better than the others in
meeting customers’ needs and wants. There are several competitiveness dimensions which
determine the relative position of an organisation and distinguish successful organisations
from the failure ones. Quality, speed, cost and flexibility are the major four business
dimensions that contribute to the competitiveness of a firm (Vargas, 2015).
Secure Best Marks with AI Grader
Need help grading? Try our AI Grader for instant feedback on your assignments.
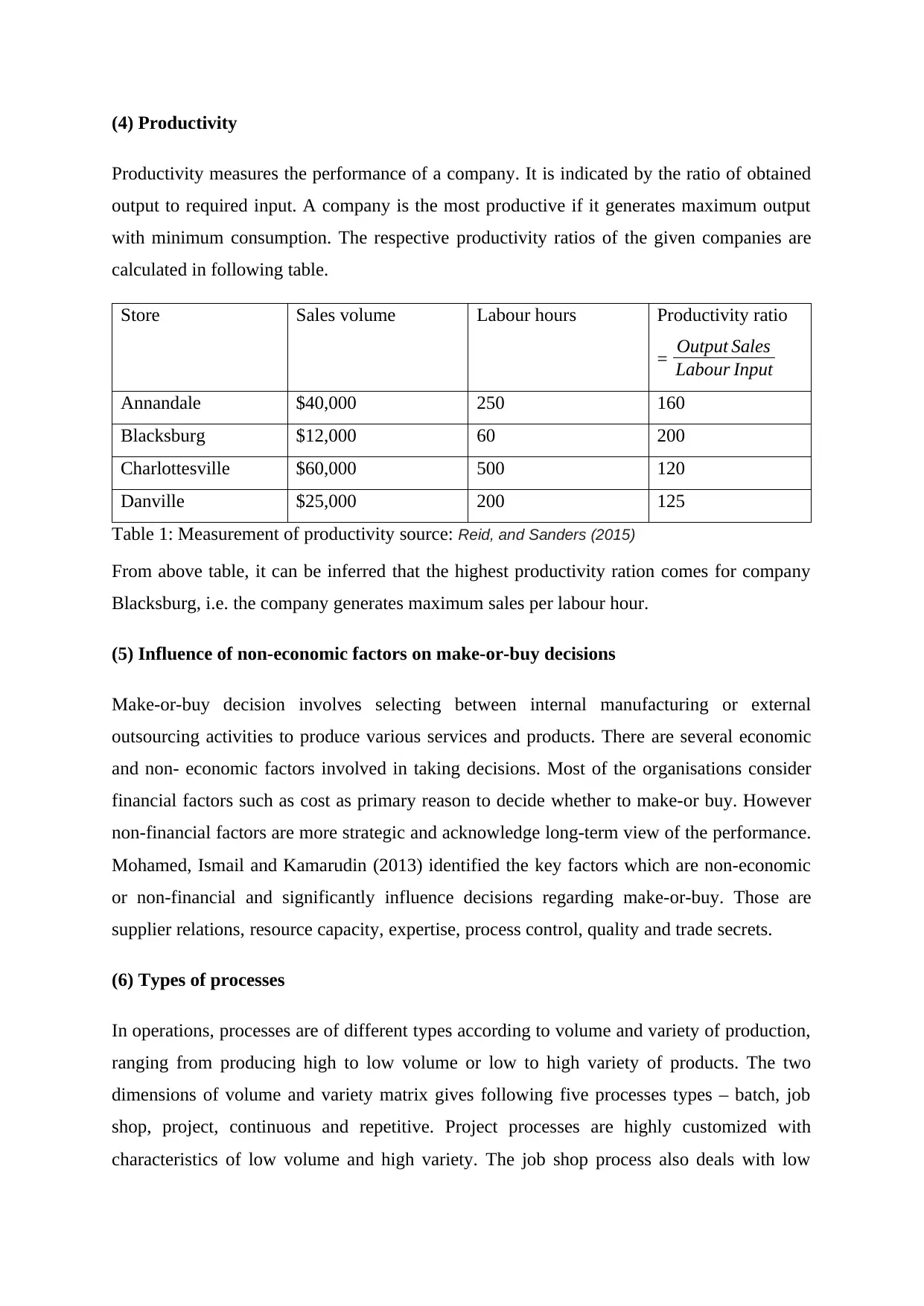
(4) Productivity
Productivity measures the performance of a company. It is indicated by the ratio of obtained
output to required input. A company is the most productive if it generates maximum output
with minimum consumption. The respective productivity ratios of the given companies are
calculated in following table.
Store Sales volume Labour hours Productivity ratio
= Output Sales
Labour Input
Annandale $40,000 250 160
Blacksburg $12,000 60 200
Charlottesville $60,000 500 120
Danville $25,000 200 125
Table 1: Measurement of productivity source: Reid, and Sanders (2015)
From above table, it can be inferred that the highest productivity ration comes for company
Blacksburg, i.e. the company generates maximum sales per labour hour.
(5) Influence of non-economic factors on make-or-buy decisions
Make-or-buy decision involves selecting between internal manufacturing or external
outsourcing activities to produce various services and products. There are several economic
and non- economic factors involved in taking decisions. Most of the organisations consider
financial factors such as cost as primary reason to decide whether to make-or buy. However
non-financial factors are more strategic and acknowledge long-term view of the performance.
Mohamed, Ismail and Kamarudin (2013) identified the key factors which are non-economic
or non-financial and significantly influence decisions regarding make-or-buy. Those are
supplier relations, resource capacity, expertise, process control, quality and trade secrets.
(6) Types of processes
In operations, processes are of different types according to volume and variety of production,
ranging from producing high to low volume or low to high variety of products. The two
dimensions of volume and variety matrix gives following five processes types – batch, job
shop, project, continuous and repetitive. Project processes are highly customized with
characteristics of low volume and high variety. The job shop process also deals with low
Productivity measures the performance of a company. It is indicated by the ratio of obtained
output to required input. A company is the most productive if it generates maximum output
with minimum consumption. The respective productivity ratios of the given companies are
calculated in following table.
Store Sales volume Labour hours Productivity ratio
= Output Sales
Labour Input
Annandale $40,000 250 160
Blacksburg $12,000 60 200
Charlottesville $60,000 500 120
Danville $25,000 200 125
Table 1: Measurement of productivity source: Reid, and Sanders (2015)
From above table, it can be inferred that the highest productivity ration comes for company
Blacksburg, i.e. the company generates maximum sales per labour hour.
(5) Influence of non-economic factors on make-or-buy decisions
Make-or-buy decision involves selecting between internal manufacturing or external
outsourcing activities to produce various services and products. There are several economic
and non- economic factors involved in taking decisions. Most of the organisations consider
financial factors such as cost as primary reason to decide whether to make-or buy. However
non-financial factors are more strategic and acknowledge long-term view of the performance.
Mohamed, Ismail and Kamarudin (2013) identified the key factors which are non-economic
or non-financial and significantly influence decisions regarding make-or-buy. Those are
supplier relations, resource capacity, expertise, process control, quality and trade secrets.
(6) Types of processes
In operations, processes are of different types according to volume and variety of production,
ranging from producing high to low volume or low to high variety of products. The two
dimensions of volume and variety matrix gives following five processes types – batch, job
shop, project, continuous and repetitive. Project processes are highly customized with
characteristics of low volume and high variety. The job shop process also deals with low
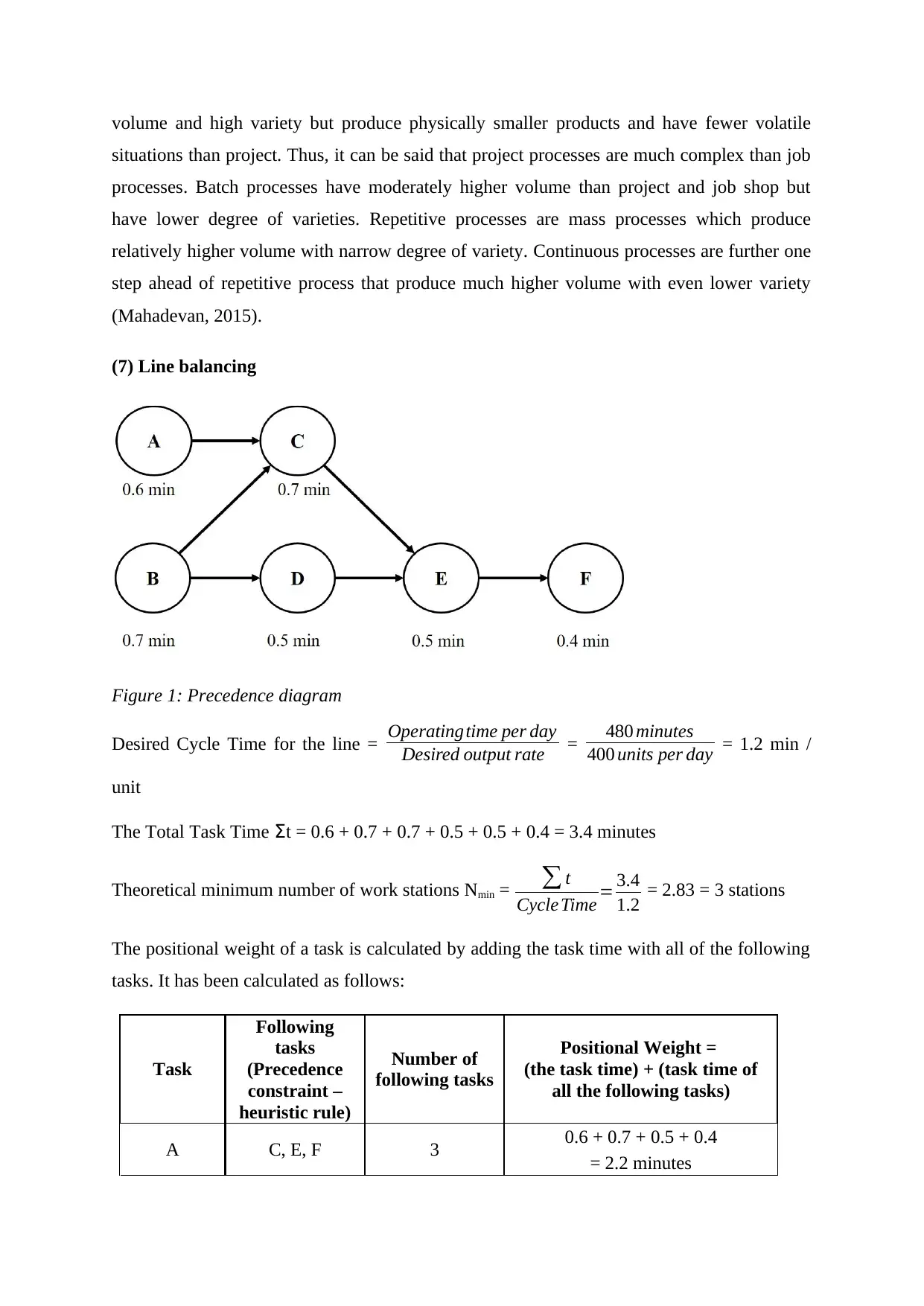
volume and high variety but produce physically smaller products and have fewer volatile
situations than project. Thus, it can be said that project processes are much complex than job
processes. Batch processes have moderately higher volume than project and job shop but
have lower degree of varieties. Repetitive processes are mass processes which produce
relatively higher volume with narrow degree of variety. Continuous processes are further one
step ahead of repetitive process that produce much higher volume with even lower variety
(Mahadevan, 2015).
(7) Line balancing
Figure 1: Precedence diagram
Desired Cycle Time for the line = Operatingtime per day
Desired output rate = 480 minutes
400 units per day = 1.2 min /
unit
The Total Task Time Σt = 0.6 + 0.7 + 0.7 + 0.5 + 0.5 + 0.4 = 3.4 minutes
Theoretical minimum number of work stations Nmin = ∑ t
Cycle Time = 3.4
1.2 = 2.83 = 3 stations
The positional weight of a task is calculated by adding the task time with all of the following
tasks. It has been calculated as follows:
Task
Following
tasks
(Precedence
constraint –
heuristic rule)
Number of
following tasks
Positional Weight =
(the task time) + (task time of
all the following tasks)
A C, E, F 3 0.6 + 0.7 + 0.5 + 0.4
= 2.2 minutes
situations than project. Thus, it can be said that project processes are much complex than job
processes. Batch processes have moderately higher volume than project and job shop but
have lower degree of varieties. Repetitive processes are mass processes which produce
relatively higher volume with narrow degree of variety. Continuous processes are further one
step ahead of repetitive process that produce much higher volume with even lower variety
(Mahadevan, 2015).
(7) Line balancing
Figure 1: Precedence diagram
Desired Cycle Time for the line = Operatingtime per day
Desired output rate = 480 minutes
400 units per day = 1.2 min /
unit
The Total Task Time Σt = 0.6 + 0.7 + 0.7 + 0.5 + 0.5 + 0.4 = 3.4 minutes
Theoretical minimum number of work stations Nmin = ∑ t
Cycle Time = 3.4
1.2 = 2.83 = 3 stations
The positional weight of a task is calculated by adding the task time with all of the following
tasks. It has been calculated as follows:
Task
Following
tasks
(Precedence
constraint –
heuristic rule)
Number of
following tasks
Positional Weight =
(the task time) + (task time of
all the following tasks)
A C, E, F 3 0.6 + 0.7 + 0.5 + 0.4
= 2.2 minutes

B C, E, F 3 0.7 + 0.7 + 0.5 + 0.4
= 2.3 minutes
C E, F 2 0.7 + 0.5 + 0.4
= 1.6 minutes
D E, F 2 0.5 + 0.5 + 0.4
= 1.4 minutes
E F 1 0.5 + 0.4
= 0.9 minutes
F - 0 0.4 minutes
Table 2: Calculation of positional weights per task (source: PANNEERSELVAM, 2012)
“Highest positional weight” as the primary rule and “longest operating time” as the secondary
rule has been used to assign tasks to workstations and following chart is calculated.
Work
Statio
n
Cycle
time
remaining
Eligible task
with operating
time
Eligible task
with Positional
weight
Assigned
task
Station idle
time
I
1.2 A (0.6), B (0.7) A (2.2), B (2.3) B
0.5 A (0.6), C (0.7),
D (0.5)
A (2.2), C (1.6),
D (1.4) D 0
II 1.2 A (0.6), C (0.7),
E (0.5)
A (2.2), C (1.6),
E (0.9) A
0.6 C (0.7), E (0.5) C (1.6), E (0.9) E 0.1
III 1.2 C (0.7), F (0.4) C (1.6), F (0.4) C
0.5 F (0.4) F (0.4) F 0.1
Total idle time 0.2 minutes
Table 3: Assigning the work stations
The efficiency of the line is calculated as follows:
The efficiency of line solution= ( Number of work station ) X ( Cycletime )−(total idle time)
( Cycle time ) X ( Number of workstations) X 100
¿ 3 X 1.2−0.2
1.2 X 3
¿ 3.4
3.6 X 100=94.44 %
= 2.3 minutes
C E, F 2 0.7 + 0.5 + 0.4
= 1.6 minutes
D E, F 2 0.5 + 0.5 + 0.4
= 1.4 minutes
E F 1 0.5 + 0.4
= 0.9 minutes
F - 0 0.4 minutes
Table 2: Calculation of positional weights per task (source: PANNEERSELVAM, 2012)
“Highest positional weight” as the primary rule and “longest operating time” as the secondary
rule has been used to assign tasks to workstations and following chart is calculated.
Work
Statio
n
Cycle
time
remaining
Eligible task
with operating
time
Eligible task
with Positional
weight
Assigned
task
Station idle
time
I
1.2 A (0.6), B (0.7) A (2.2), B (2.3) B
0.5 A (0.6), C (0.7),
D (0.5)
A (2.2), C (1.6),
D (1.4) D 0
II 1.2 A (0.6), C (0.7),
E (0.5)
A (2.2), C (1.6),
E (0.9) A
0.6 C (0.7), E (0.5) C (1.6), E (0.9) E 0.1
III 1.2 C (0.7), F (0.4) C (1.6), F (0.4) C
0.5 F (0.4) F (0.4) F 0.1
Total idle time 0.2 minutes
Table 3: Assigning the work stations
The efficiency of the line is calculated as follows:
The efficiency of line solution= ( Number of work station ) X ( Cycletime )−(total idle time)
( Cycle time ) X ( Number of workstations) X 100
¿ 3 X 1.2−0.2
1.2 X 3
¿ 3.4
3.6 X 100=94.44 %
Paraphrase This Document
Need a fresh take? Get an instant paraphrase of this document with our AI Paraphraser
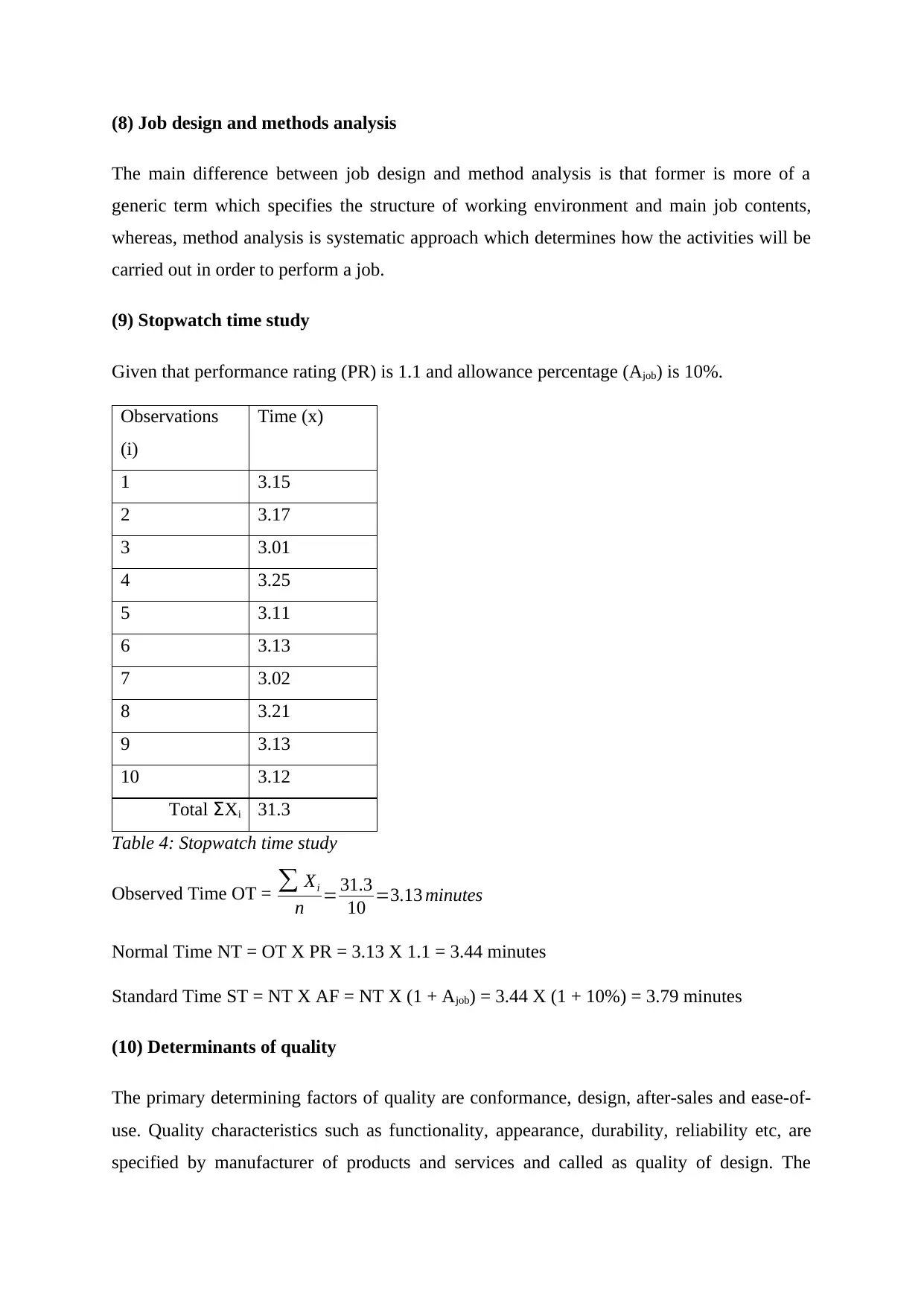
(8) Job design and methods analysis
The main difference between job design and method analysis is that former is more of a
generic term which specifies the structure of working environment and main job contents,
whereas, method analysis is systematic approach which determines how the activities will be
carried out in order to perform a job.
(9) Stopwatch time study
Given that performance rating (PR) is 1.1 and allowance percentage (Ajob) is 10%.
Observations
(i)
Time (x)
1 3.15
2 3.17
3 3.01
4 3.25
5 3.11
6 3.13
7 3.02
8 3.21
9 3.13
10 3.12
Total ΣXi 31.3
Table 4: Stopwatch time study
Observed Time OT = ∑ Xi
n = 31.3
10 =3.13 minutes
Normal Time NT = OT X PR = 3.13 X 1.1 = 3.44 minutes
Standard Time ST = NT X AF = NT X (1 + Ajob) = 3.44 X (1 + 10%) = 3.79 minutes
(10) Determinants of quality
The primary determining factors of quality are conformance, design, after-sales and ease-of-
use. Quality characteristics such as functionality, appearance, durability, reliability etc, are
specified by manufacturer of products and services and called as quality of design. The
The main difference between job design and method analysis is that former is more of a
generic term which specifies the structure of working environment and main job contents,
whereas, method analysis is systematic approach which determines how the activities will be
carried out in order to perform a job.
(9) Stopwatch time study
Given that performance rating (PR) is 1.1 and allowance percentage (Ajob) is 10%.
Observations
(i)
Time (x)
1 3.15
2 3.17
3 3.01
4 3.25
5 3.11
6 3.13
7 3.02
8 3.21
9 3.13
10 3.12
Total ΣXi 31.3
Table 4: Stopwatch time study
Observed Time OT = ∑ Xi
n = 31.3
10 =3.13 minutes
Normal Time NT = OT X PR = 3.13 X 1.1 = 3.44 minutes
Standard Time ST = NT X AF = NT X (1 + Ajob) = 3.44 X (1 + 10%) = 3.79 minutes
(10) Determinants of quality
The primary determining factors of quality are conformance, design, after-sales and ease-of-
use. Quality characteristics such as functionality, appearance, durability, reliability etc, are
specified by manufacturer of products and services and called as quality of design. The
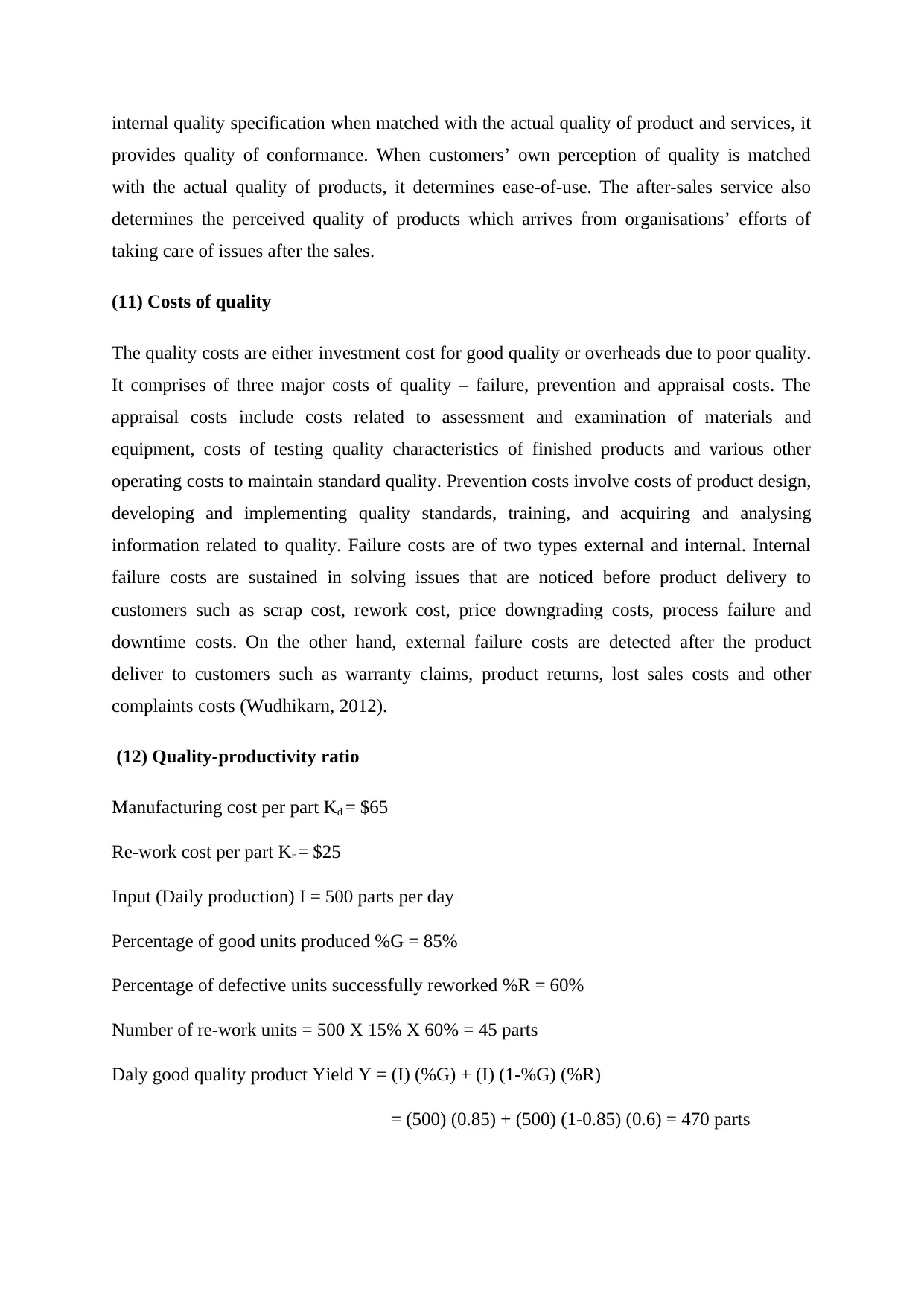
internal quality specification when matched with the actual quality of product and services, it
provides quality of conformance. When customers’ own perception of quality is matched
with the actual quality of products, it determines ease-of-use. The after-sales service also
determines the perceived quality of products which arrives from organisations’ efforts of
taking care of issues after the sales.
(11) Costs of quality
The quality costs are either investment cost for good quality or overheads due to poor quality.
It comprises of three major costs of quality – failure, prevention and appraisal costs. The
appraisal costs include costs related to assessment and examination of materials and
equipment, costs of testing quality characteristics of finished products and various other
operating costs to maintain standard quality. Prevention costs involve costs of product design,
developing and implementing quality standards, training, and acquiring and analysing
information related to quality. Failure costs are of two types external and internal. Internal
failure costs are sustained in solving issues that are noticed before product delivery to
customers such as scrap cost, rework cost, price downgrading costs, process failure and
downtime costs. On the other hand, external failure costs are detected after the product
deliver to customers such as warranty claims, product returns, lost sales costs and other
complaints costs (Wudhikarn, 2012).
(12) Quality-productivity ratio
Manufacturing cost per part Kd = $65
Re-work cost per part Kr = $25
Input (Daily production) I = 500 parts per day
Percentage of good units produced %G = 85%
Percentage of defective units successfully reworked %R = 60%
Number of re-work units = 500 X 15% X 60% = 45 parts
Daly good quality product Yield Y = (I) (%G) + (I) (1-%G) (%R)
= (500) (0.85) + (500) (1-0.85) (0.6) = 470 parts
provides quality of conformance. When customers’ own perception of quality is matched
with the actual quality of products, it determines ease-of-use. The after-sales service also
determines the perceived quality of products which arrives from organisations’ efforts of
taking care of issues after the sales.
(11) Costs of quality
The quality costs are either investment cost for good quality or overheads due to poor quality.
It comprises of three major costs of quality – failure, prevention and appraisal costs. The
appraisal costs include costs related to assessment and examination of materials and
equipment, costs of testing quality characteristics of finished products and various other
operating costs to maintain standard quality. Prevention costs involve costs of product design,
developing and implementing quality standards, training, and acquiring and analysing
information related to quality. Failure costs are of two types external and internal. Internal
failure costs are sustained in solving issues that are noticed before product delivery to
customers such as scrap cost, rework cost, price downgrading costs, process failure and
downtime costs. On the other hand, external failure costs are detected after the product
deliver to customers such as warranty claims, product returns, lost sales costs and other
complaints costs (Wudhikarn, 2012).
(12) Quality-productivity ratio
Manufacturing cost per part Kd = $65
Re-work cost per part Kr = $25
Input (Daily production) I = 500 parts per day
Percentage of good units produced %G = 85%
Percentage of defective units successfully reworked %R = 60%
Number of re-work units = 500 X 15% X 60% = 45 parts
Daly good quality product Yield Y = (I) (%G) + (I) (1-%G) (%R)
= (500) (0.85) + (500) (1-0.85) (0.6) = 470 parts
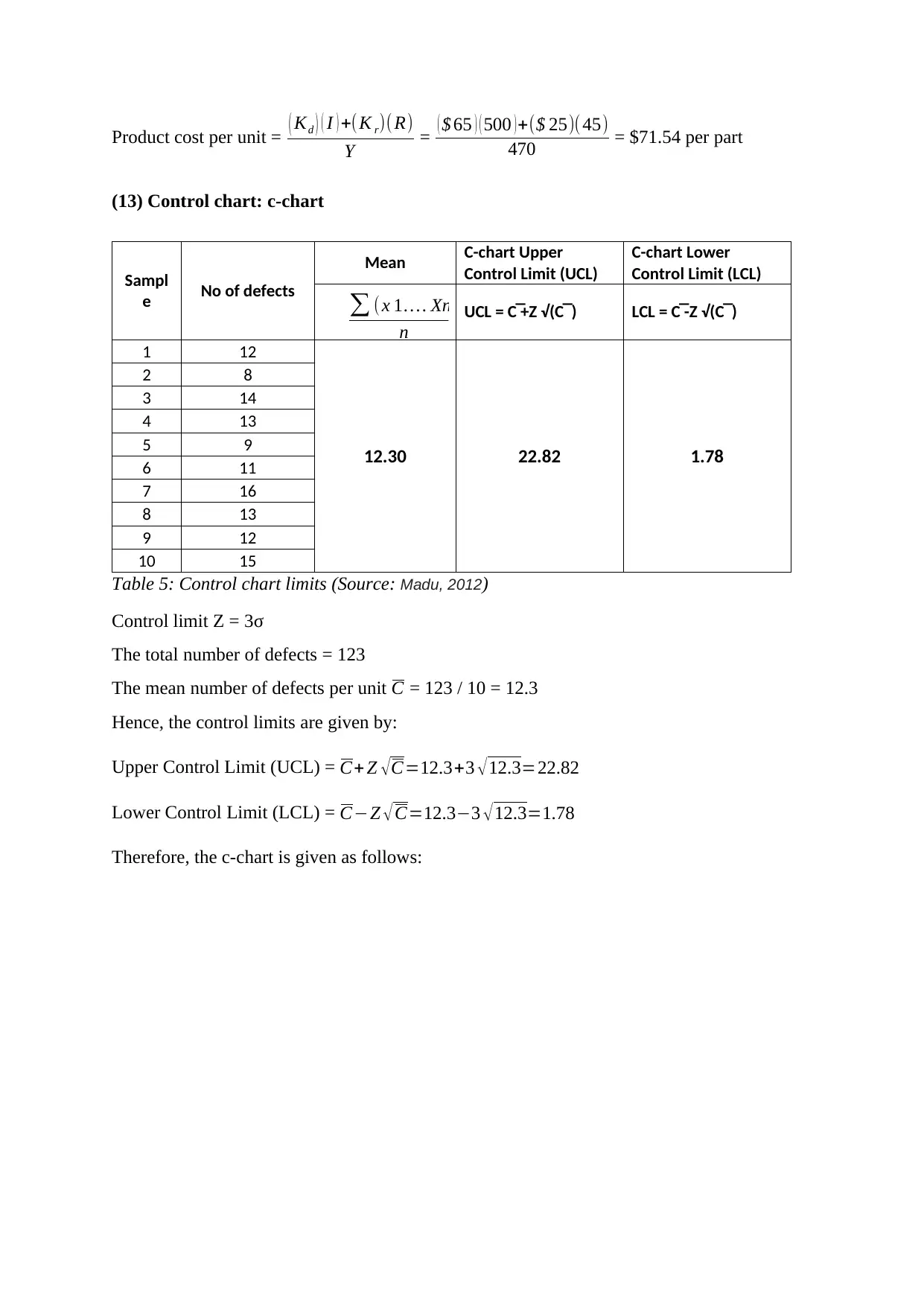
Product cost per unit = ( Kd ) ( I ) +(K r)( R)
Y = ( $ 65 ) ( 500 )+($ 25)(45)
470 = $71.54 per part
(13) Control chart: c-chart
Sampl
e No of defects
Mean C-chart Upper
Control Limit (UCL)
C-chart Lower
Control Limit (LCL)
UCL = C ̅ +Z √(C ̅ ) LCL = C ̅ -Z √(C ̅ )
1 12
12.30 22.82 1.78
2 8
3 14
4 13
5 9
6 11
7 16
8 13
9 12
10 15
Table 5: Control chart limits (Source: Madu, 2012)
Control limit Z = 3σ
The total number of defects = 123
The mean number of defects per unit C = 123 / 10 = 12.3
Hence, the control limits are given by:
Upper Control Limit (UCL) = C+ Z √C=12.3+3 √12.3=22.82
Lower Control Limit (LCL) = C−Z √ C=12.3−3 √12.3=1.78
Therefore, the c-chart is given as follows:
∑ ( x 1… . Xn)
n
Y = ( $ 65 ) ( 500 )+($ 25)(45)
470 = $71.54 per part
(13) Control chart: c-chart
Sampl
e No of defects
Mean C-chart Upper
Control Limit (UCL)
C-chart Lower
Control Limit (LCL)
UCL = C ̅ +Z √(C ̅ ) LCL = C ̅ -Z √(C ̅ )
1 12
12.30 22.82 1.78
2 8
3 14
4 13
5 9
6 11
7 16
8 13
9 12
10 15
Table 5: Control chart limits (Source: Madu, 2012)
Control limit Z = 3σ
The total number of defects = 123
The mean number of defects per unit C = 123 / 10 = 12.3
Hence, the control limits are given by:
Upper Control Limit (UCL) = C+ Z √C=12.3+3 √12.3=22.82
Lower Control Limit (LCL) = C−Z √ C=12.3−3 √12.3=1.78
Therefore, the c-chart is given as follows:
∑ ( x 1… . Xn)
n
Secure Best Marks with AI Grader
Need help grading? Try our AI Grader for instant feedback on your assignments.
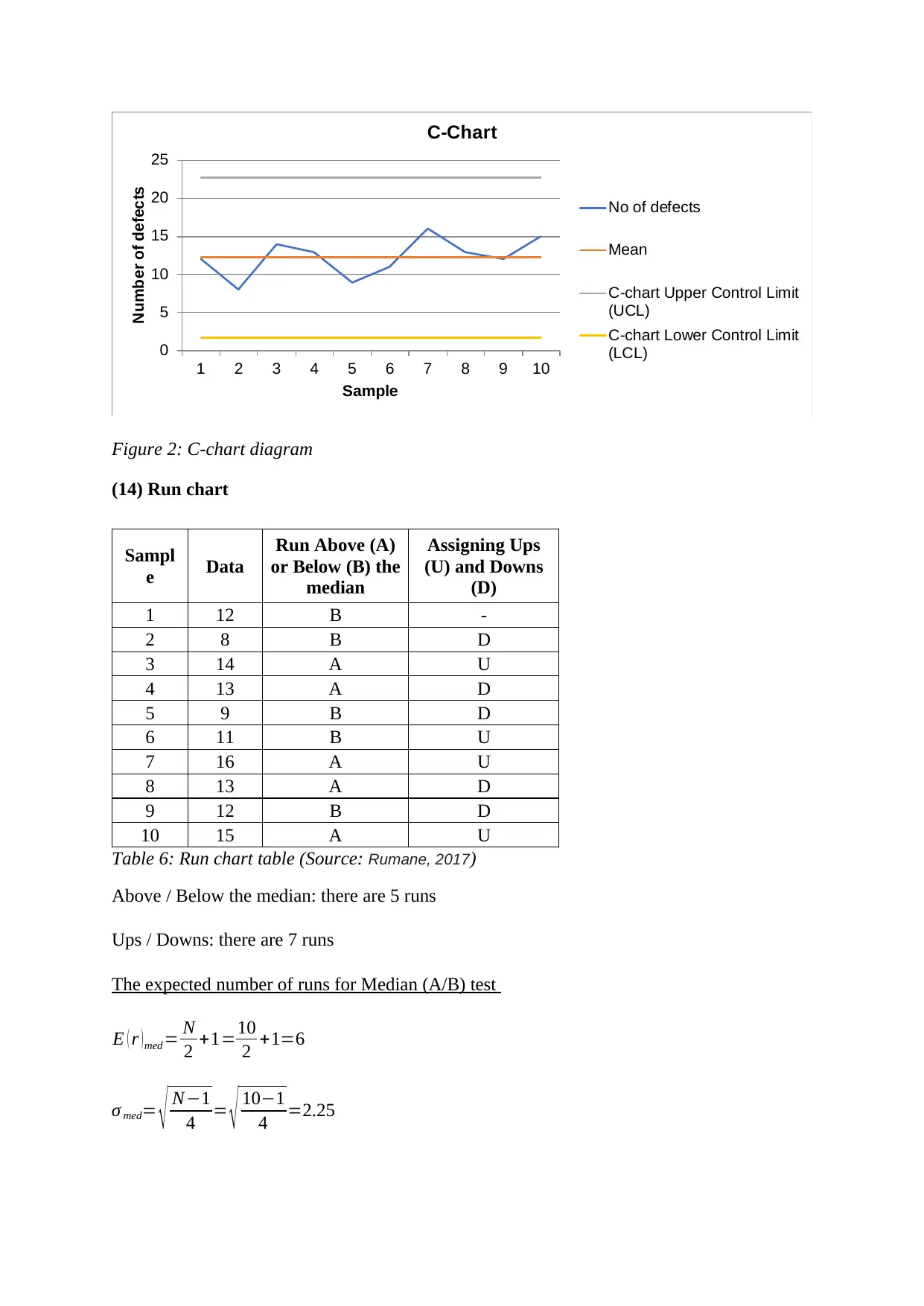
0
5
10
15
20
25
1 2 3 4 5 6 7 8 9 10
Number of defects
Sample
C-Chart
No of defects
Mean
C-chart Upper Control Limit
(UCL)
C-chart Lower Control Limit
(LCL)
Figure 2: C-chart diagram
(14) Run chart
Sampl
e Data
Run Above (A)
or Below (B) the
median
Assigning Ups
(U) and Downs
(D)
1 12 B -
2 8 B D
3 14 A U
4 13 A D
5 9 B D
6 11 B U
7 16 A U
8 13 A D
9 12 B D
10 15 A U
Table 6: Run chart table (Source: Rumane, 2017)
Above / Below the median: there are 5 runs
Ups / Downs: there are 7 runs
The expected number of runs for Median (A/B) test
E ( r )med = N
2 +1=10
2 +1=6
σ med= √ N−1
4 = √ 10−1
4 =2.25
5
10
15
20
25
1 2 3 4 5 6 7 8 9 10
Number of defects
Sample
C-Chart
No of defects
Mean
C-chart Upper Control Limit
(UCL)
C-chart Lower Control Limit
(LCL)
Figure 2: C-chart diagram
(14) Run chart
Sampl
e Data
Run Above (A)
or Below (B) the
median
Assigning Ups
(U) and Downs
(D)
1 12 B -
2 8 B D
3 14 A U
4 13 A D
5 9 B D
6 11 B U
7 16 A U
8 13 A D
9 12 B D
10 15 A U
Table 6: Run chart table (Source: Rumane, 2017)
Above / Below the median: there are 5 runs
Ups / Downs: there are 7 runs
The expected number of runs for Median (A/B) test
E ( r )med = N
2 +1=10
2 +1=6
σ med= √ N−1
4 = √ 10−1
4 =2.25

Zmed= observed no of runs−expected no of runs
standard deviation of no of runs = 5−6
2.25 =−0.44
Zmedvalue is within the limit, which is Z = 2, therefore, there are no non-random variation
present in data.
The expected number of runs for Median (for U/D) test
E ( r )u /d = 2 N −1
3 =2 ( 10 ) −1
3 =6.33→ 6
σ u/ d= √ 16 N−29
90 = √ 16(10)−29
90 =1.46
Zu / d= observed no of runs−expected no of runs
standard deviation of no of runs = 7−6
1.46 =0.69
Zu / dvalue is within the limit, which is Z = 2, therefore, there are no non-random variation
present in data.
Since, both Up/Down and Above/Below median are within the limit, the process is said to be
in control.
(15) Aggregate planning
It is a process to adjust production according to the changing demands. Aggregate planning
techniques are used by organisations to make decisions both long term and short-term for
improving the performance. The key aim of aggregate planning is to establish a production
planning schedule which ensures optimum utilisation of available resources to meet the
expected demand (Meindl, 2016).
(16) Strategies of aggregate planning
Aggregate planning strategy may involve demand options or supply options or a mixed
approach involving the both options. When demand is adjusted in correspond to the available
supply, it is known as demand options. It can be done by altering prices, promotional
techniques, short selling backorders. Conversely, when supply is amended in parallel with the
demand, the supply options are used. There are various supply strategic options such as hiring
and dismissing of workers, training workers, part time jobs, storing inventories,
subcontracting and overtime workers (Meindl, 2016).
standard deviation of no of runs = 5−6
2.25 =−0.44
Zmedvalue is within the limit, which is Z = 2, therefore, there are no non-random variation
present in data.
The expected number of runs for Median (for U/D) test
E ( r )u /d = 2 N −1
3 =2 ( 10 ) −1
3 =6.33→ 6
σ u/ d= √ 16 N−29
90 = √ 16(10)−29
90 =1.46
Zu / d= observed no of runs−expected no of runs
standard deviation of no of runs = 7−6
1.46 =0.69
Zu / dvalue is within the limit, which is Z = 2, therefore, there are no non-random variation
present in data.
Since, both Up/Down and Above/Below median are within the limit, the process is said to be
in control.
(15) Aggregate planning
It is a process to adjust production according to the changing demands. Aggregate planning
techniques are used by organisations to make decisions both long term and short-term for
improving the performance. The key aim of aggregate planning is to establish a production
planning schedule which ensures optimum utilisation of available resources to meet the
expected demand (Meindl, 2016).
(16) Strategies of aggregate planning
Aggregate planning strategy may involve demand options or supply options or a mixed
approach involving the both options. When demand is adjusted in correspond to the available
supply, it is known as demand options. It can be done by altering prices, promotional
techniques, short selling backorders. Conversely, when supply is amended in parallel with the
demand, the supply options are used. There are various supply strategic options such as hiring
and dismissing of workers, training workers, part time jobs, storing inventories,
subcontracting and overtime workers (Meindl, 2016).
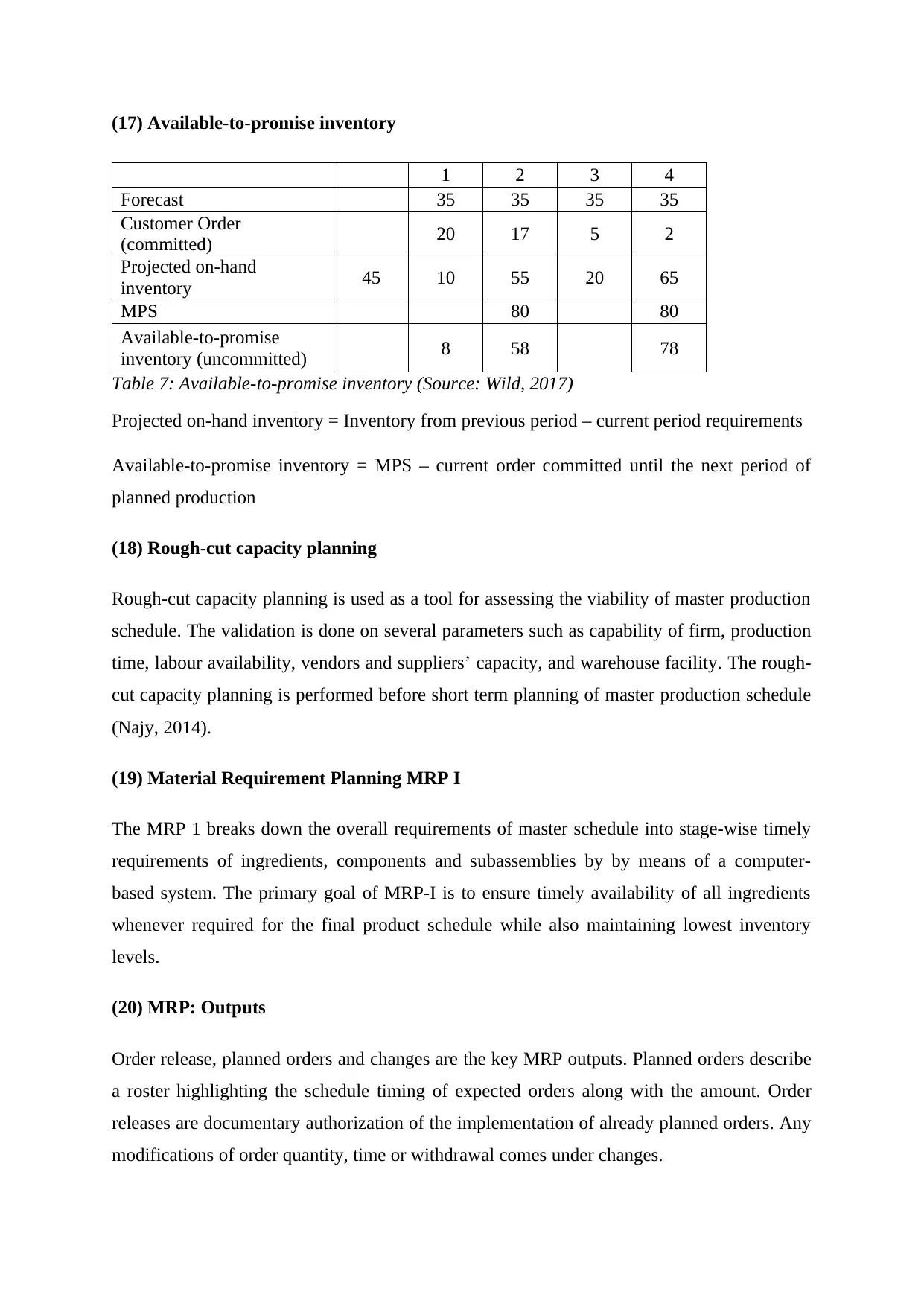
(17) Available-to-promise inventory
1 2 3 4
Forecast 35 35 35 35
Customer Order
(committed) 20 17 5 2
Projected on-hand
inventory 45 10 55 20 65
MPS 80 80
Available-to-promise
inventory (uncommitted) 8 58 78
Table 7: Available-to-promise inventory (Source: Wild, 2017)
Projected on-hand inventory = Inventory from previous period – current period requirements
Available-to-promise inventory = MPS – current order committed until the next period of
planned production
(18) Rough-cut capacity planning
Rough-cut capacity planning is used as a tool for assessing the viability of master production
schedule. The validation is done on several parameters such as capability of firm, production
time, labour availability, vendors and suppliers’ capacity, and warehouse facility. The rough-
cut capacity planning is performed before short term planning of master production schedule
(Najy, 2014).
(19) Material Requirement Planning MRP I
The MRP 1 breaks down the overall requirements of master schedule into stage-wise timely
requirements of ingredients, components and subassemblies by by means of a computer-
based system. The primary goal of MRP-I is to ensure timely availability of all ingredients
whenever required for the final product schedule while also maintaining lowest inventory
levels.
(20) MRP: Outputs
Order release, planned orders and changes are the key MRP outputs. Planned orders describe
a roster highlighting the schedule timing of expected orders along with the amount. Order
releases are documentary authorization of the implementation of already planned orders. Any
modifications of order quantity, time or withdrawal comes under changes.
1 2 3 4
Forecast 35 35 35 35
Customer Order
(committed) 20 17 5 2
Projected on-hand
inventory 45 10 55 20 65
MPS 80 80
Available-to-promise
inventory (uncommitted) 8 58 78
Table 7: Available-to-promise inventory (Source: Wild, 2017)
Projected on-hand inventory = Inventory from previous period – current period requirements
Available-to-promise inventory = MPS – current order committed until the next period of
planned production
(18) Rough-cut capacity planning
Rough-cut capacity planning is used as a tool for assessing the viability of master production
schedule. The validation is done on several parameters such as capability of firm, production
time, labour availability, vendors and suppliers’ capacity, and warehouse facility. The rough-
cut capacity planning is performed before short term planning of master production schedule
(Najy, 2014).
(19) Material Requirement Planning MRP I
The MRP 1 breaks down the overall requirements of master schedule into stage-wise timely
requirements of ingredients, components and subassemblies by by means of a computer-
based system. The primary goal of MRP-I is to ensure timely availability of all ingredients
whenever required for the final product schedule while also maintaining lowest inventory
levels.
(20) MRP: Outputs
Order release, planned orders and changes are the key MRP outputs. Planned orders describe
a roster highlighting the schedule timing of expected orders along with the amount. Order
releases are documentary authorization of the implementation of already planned orders. Any
modifications of order quantity, time or withdrawal comes under changes.
Paraphrase This Document
Need a fresh take? Get an instant paraphrase of this document with our AI Paraphraser
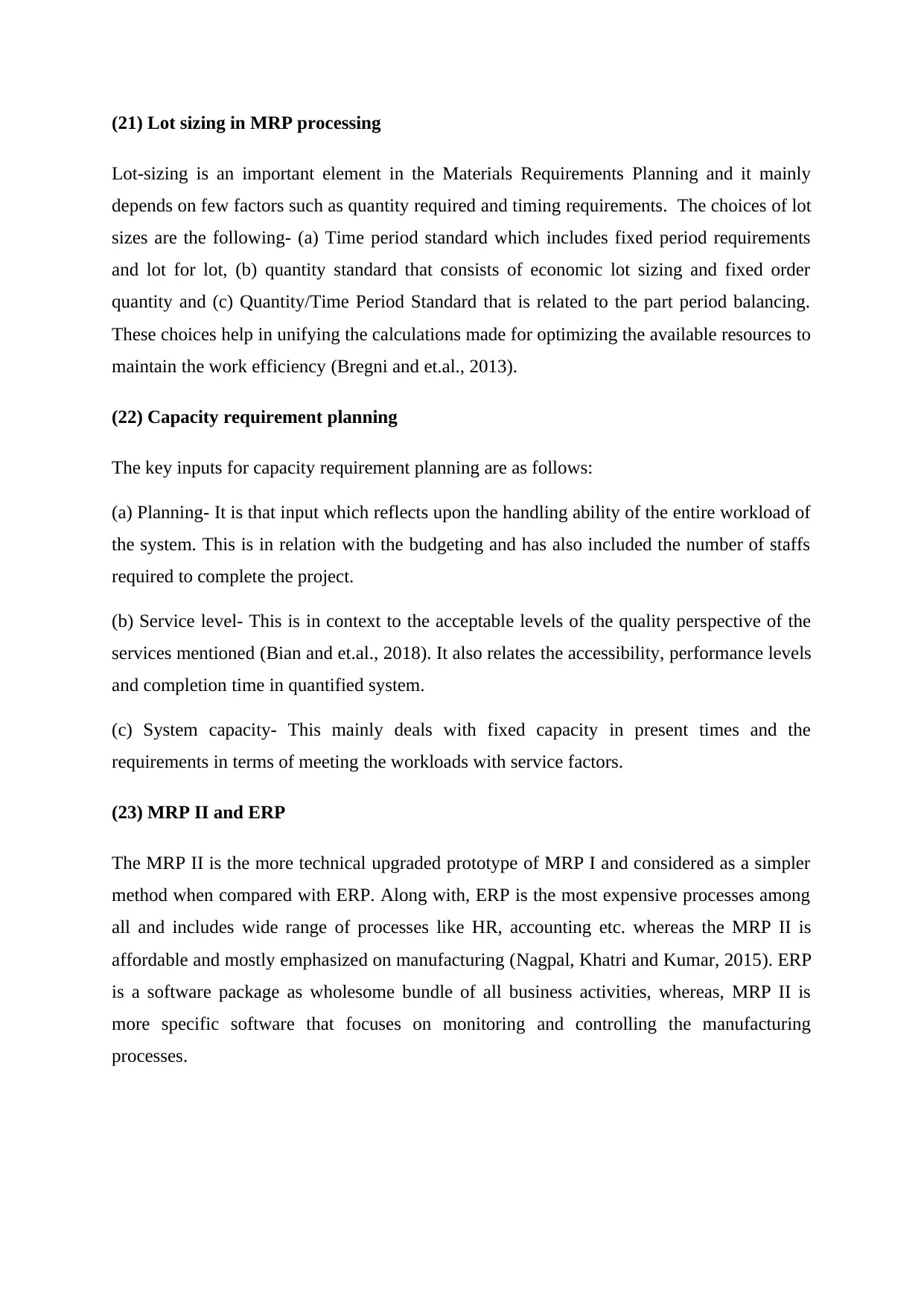
(21) Lot sizing in MRP processing
Lot-sizing is an important element in the Materials Requirements Planning and it mainly
depends on few factors such as quantity required and timing requirements. The choices of lot
sizes are the following- (a) Time period standard which includes fixed period requirements
and lot for lot, (b) quantity standard that consists of economic lot sizing and fixed order
quantity and (c) Quantity/Time Period Standard that is related to the part period balancing.
These choices help in unifying the calculations made for optimizing the available resources to
maintain the work efficiency (Bregni and et.al., 2013).
(22) Capacity requirement planning
The key inputs for capacity requirement planning are as follows:
(a) Planning- It is that input which reflects upon the handling ability of the entire workload of
the system. This is in relation with the budgeting and has also included the number of staffs
required to complete the project.
(b) Service level- This is in context to the acceptable levels of the quality perspective of the
services mentioned (Bian and et.al., 2018). It also relates the accessibility, performance levels
and completion time in quantified system.
(c) System capacity- This mainly deals with fixed capacity in present times and the
requirements in terms of meeting the workloads with service factors.
(23) MRP II and ERP
The MRP II is the more technical upgraded prototype of MRP I and considered as a simpler
method when compared with ERP. Along with, ERP is the most expensive processes among
all and includes wide range of processes like HR, accounting etc. whereas the MRP II is
affordable and mostly emphasized on manufacturing (Nagpal, Khatri and Kumar, 2015). ERP
is a software package as wholesome bundle of all business activities, whereas, MRP II is
more specific software that focuses on monitoring and controlling the manufacturing
processes.
Lot-sizing is an important element in the Materials Requirements Planning and it mainly
depends on few factors such as quantity required and timing requirements. The choices of lot
sizes are the following- (a) Time period standard which includes fixed period requirements
and lot for lot, (b) quantity standard that consists of economic lot sizing and fixed order
quantity and (c) Quantity/Time Period Standard that is related to the part period balancing.
These choices help in unifying the calculations made for optimizing the available resources to
maintain the work efficiency (Bregni and et.al., 2013).
(22) Capacity requirement planning
The key inputs for capacity requirement planning are as follows:
(a) Planning- It is that input which reflects upon the handling ability of the entire workload of
the system. This is in relation with the budgeting and has also included the number of staffs
required to complete the project.
(b) Service level- This is in context to the acceptable levels of the quality perspective of the
services mentioned (Bian and et.al., 2018). It also relates the accessibility, performance levels
and completion time in quantified system.
(c) System capacity- This mainly deals with fixed capacity in present times and the
requirements in terms of meeting the workloads with service factors.
(23) MRP II and ERP
The MRP II is the more technical upgraded prototype of MRP I and considered as a simpler
method when compared with ERP. Along with, ERP is the most expensive processes among
all and includes wide range of processes like HR, accounting etc. whereas the MRP II is
affordable and mostly emphasized on manufacturing (Nagpal, Khatri and Kumar, 2015). ERP
is a software package as wholesome bundle of all business activities, whereas, MRP II is
more specific software that focuses on monitoring and controlling the manufacturing
processes.
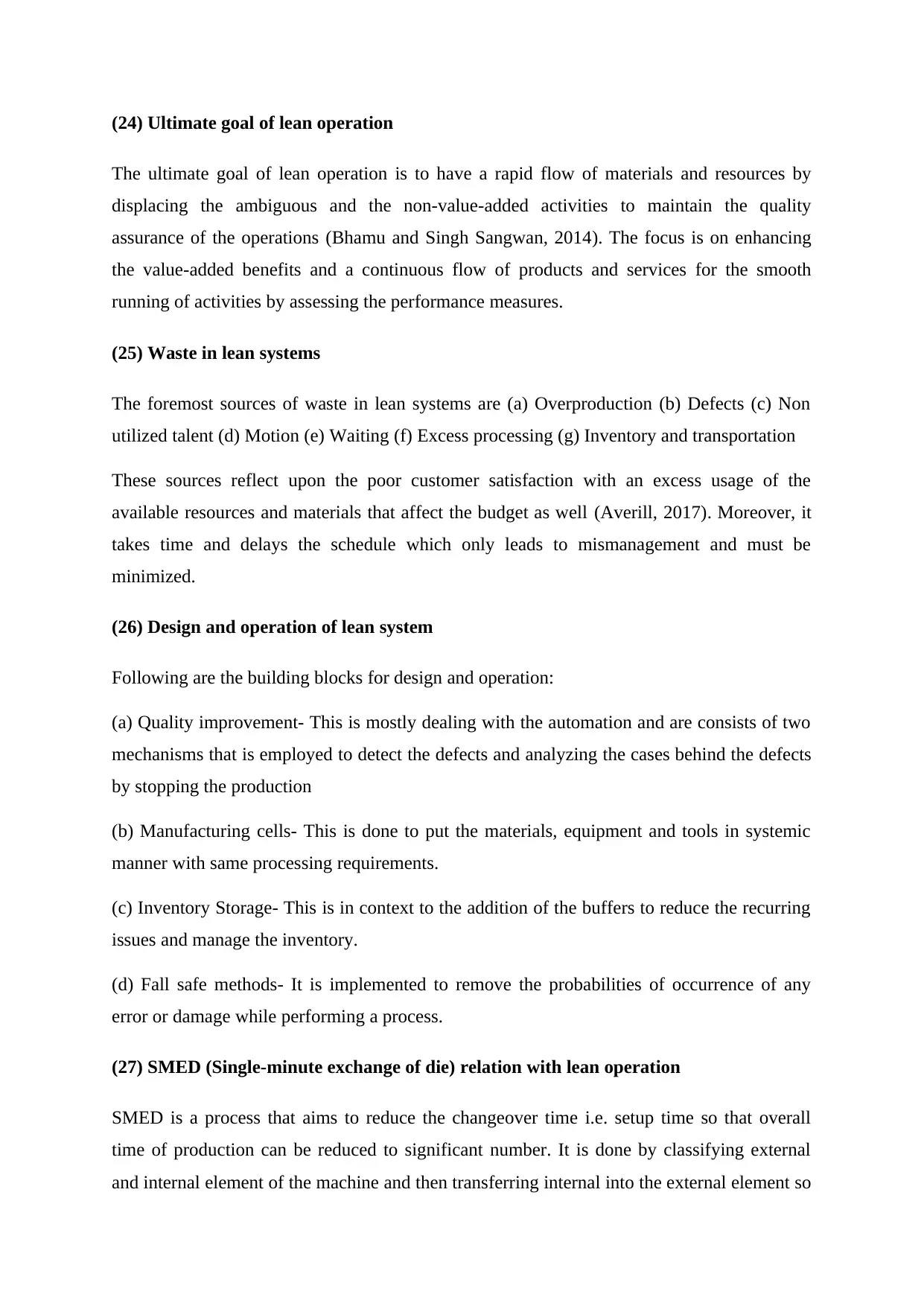
(24) Ultimate goal of lean operation
The ultimate goal of lean operation is to have a rapid flow of materials and resources by
displacing the ambiguous and the non-value-added activities to maintain the quality
assurance of the operations (Bhamu and Singh Sangwan, 2014). The focus is on enhancing
the value-added benefits and a continuous flow of products and services for the smooth
running of activities by assessing the performance measures.
(25) Waste in lean systems
The foremost sources of waste in lean systems are (a) Overproduction (b) Defects (c) Non
utilized talent (d) Motion (e) Waiting (f) Excess processing (g) Inventory and transportation
These sources reflect upon the poor customer satisfaction with an excess usage of the
available resources and materials that affect the budget as well (Averill, 2017). Moreover, it
takes time and delays the schedule which only leads to mismanagement and must be
minimized.
(26) Design and operation of lean system
Following are the building blocks for design and operation:
(a) Quality improvement- This is mostly dealing with the automation and are consists of two
mechanisms that is employed to detect the defects and analyzing the cases behind the defects
by stopping the production
(b) Manufacturing cells- This is done to put the materials, equipment and tools in systemic
manner with same processing requirements.
(c) Inventory Storage- This is in context to the addition of the buffers to reduce the recurring
issues and manage the inventory.
(d) Fall safe methods- It is implemented to remove the probabilities of occurrence of any
error or damage while performing a process.
(27) SMED (Single-minute exchange of die) relation with lean operation
SMED is a process that aims to reduce the changeover time i.e. setup time so that overall
time of production can be reduced to significant number. It is done by classifying external
and internal element of the machine and then transferring internal into the external element so
The ultimate goal of lean operation is to have a rapid flow of materials and resources by
displacing the ambiguous and the non-value-added activities to maintain the quality
assurance of the operations (Bhamu and Singh Sangwan, 2014). The focus is on enhancing
the value-added benefits and a continuous flow of products and services for the smooth
running of activities by assessing the performance measures.
(25) Waste in lean systems
The foremost sources of waste in lean systems are (a) Overproduction (b) Defects (c) Non
utilized talent (d) Motion (e) Waiting (f) Excess processing (g) Inventory and transportation
These sources reflect upon the poor customer satisfaction with an excess usage of the
available resources and materials that affect the budget as well (Averill, 2017). Moreover, it
takes time and delays the schedule which only leads to mismanagement and must be
minimized.
(26) Design and operation of lean system
Following are the building blocks for design and operation:
(a) Quality improvement- This is mostly dealing with the automation and are consists of two
mechanisms that is employed to detect the defects and analyzing the cases behind the defects
by stopping the production
(b) Manufacturing cells- This is done to put the materials, equipment and tools in systemic
manner with same processing requirements.
(c) Inventory Storage- This is in context to the addition of the buffers to reduce the recurring
issues and manage the inventory.
(d) Fall safe methods- It is implemented to remove the probabilities of occurrence of any
error or damage while performing a process.
(27) SMED (Single-minute exchange of die) relation with lean operation
SMED is a process that aims to reduce the changeover time i.e. setup time so that overall
time of production can be reduced to significant number. It is done by classifying external
and internal element of the machine and then transferring internal into the external element so
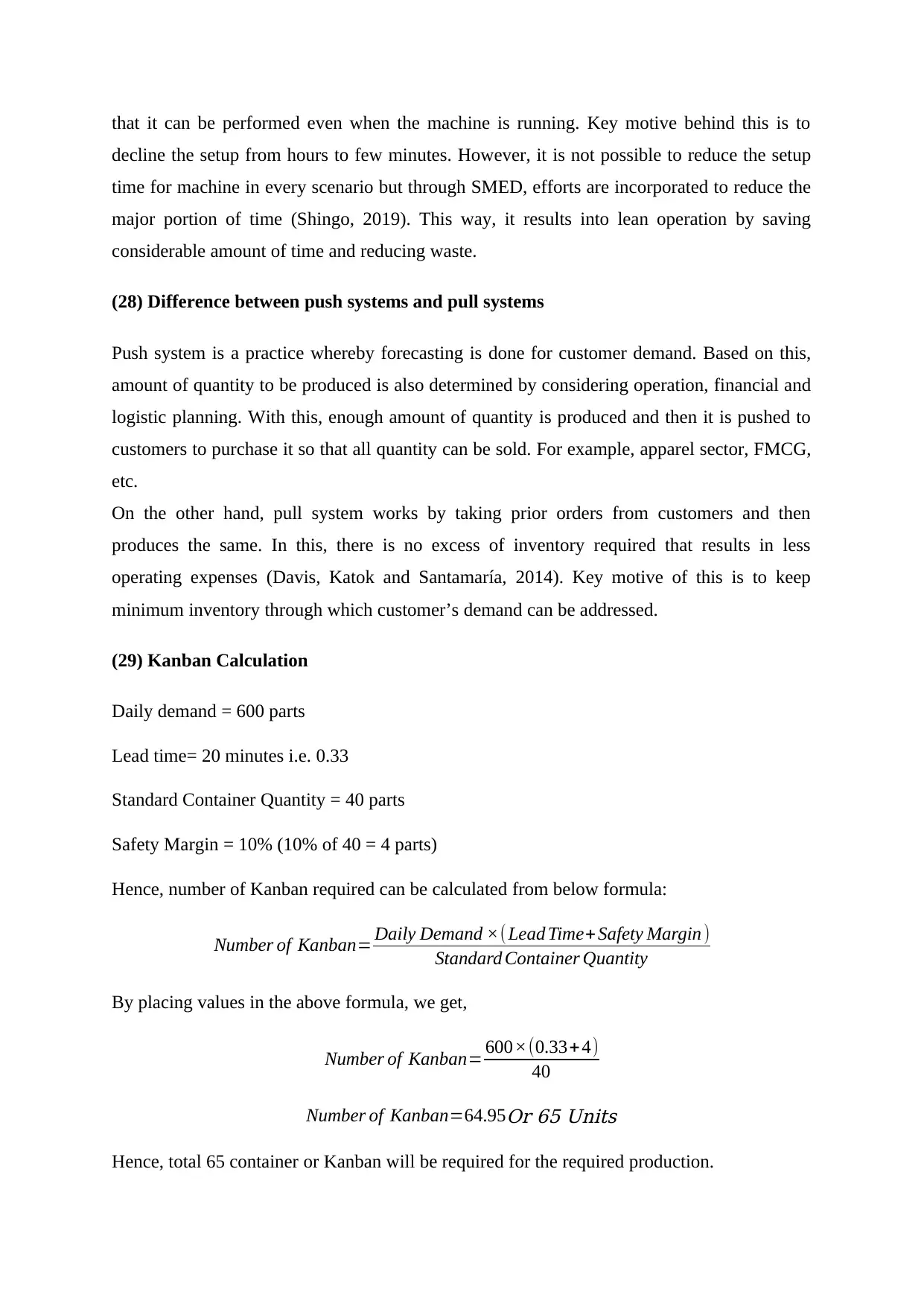
that it can be performed even when the machine is running. Key motive behind this is to
decline the setup from hours to few minutes. However, it is not possible to reduce the setup
time for machine in every scenario but through SMED, efforts are incorporated to reduce the
major portion of time (Shingo, 2019). This way, it results into lean operation by saving
considerable amount of time and reducing waste.
(28) Difference between push systems and pull systems
Push system is a practice whereby forecasting is done for customer demand. Based on this,
amount of quantity to be produced is also determined by considering operation, financial and
logistic planning. With this, enough amount of quantity is produced and then it is pushed to
customers to purchase it so that all quantity can be sold. For example, apparel sector, FMCG,
etc.
On the other hand, pull system works by taking prior orders from customers and then
produces the same. In this, there is no excess of inventory required that results in less
operating expenses (Davis, Katok and Santamaría, 2014). Key motive of this is to keep
minimum inventory through which customer’s demand can be addressed.
(29) Kanban Calculation
Daily demand = 600 parts
Lead time= 20 minutes i.e. 0.33
Standard Container Quantity = 40 parts
Safety Margin = 10% (10% of 40 = 4 parts)
Hence, number of Kanban required can be calculated from below formula:
Number of Kanban= Daily Demand ×( Lead Time+ Safety Margin )
Standard Container Quantity
By placing values in the above formula, we get,
Number of Kanban= 600×(0.33+ 4)
40
Number of Kanban=64.95
Or 65 Units
Hence, total 65 container or Kanban will be required for the required production.
decline the setup from hours to few minutes. However, it is not possible to reduce the setup
time for machine in every scenario but through SMED, efforts are incorporated to reduce the
major portion of time (Shingo, 2019). This way, it results into lean operation by saving
considerable amount of time and reducing waste.
(28) Difference between push systems and pull systems
Push system is a practice whereby forecasting is done for customer demand. Based on this,
amount of quantity to be produced is also determined by considering operation, financial and
logistic planning. With this, enough amount of quantity is produced and then it is pushed to
customers to purchase it so that all quantity can be sold. For example, apparel sector, FMCG,
etc.
On the other hand, pull system works by taking prior orders from customers and then
produces the same. In this, there is no excess of inventory required that results in less
operating expenses (Davis, Katok and Santamaría, 2014). Key motive of this is to keep
minimum inventory through which customer’s demand can be addressed.
(29) Kanban Calculation
Daily demand = 600 parts
Lead time= 20 minutes i.e. 0.33
Standard Container Quantity = 40 parts
Safety Margin = 10% (10% of 40 = 4 parts)
Hence, number of Kanban required can be calculated from below formula:
Number of Kanban= Daily Demand ×( Lead Time+ Safety Margin )
Standard Container Quantity
By placing values in the above formula, we get,
Number of Kanban= 600×(0.33+ 4)
40
Number of Kanban=64.95
Or 65 Units
Hence, total 65 container or Kanban will be required for the required production.
Secure Best Marks with AI Grader
Need help grading? Try our AI Grader for instant feedback on your assignments.
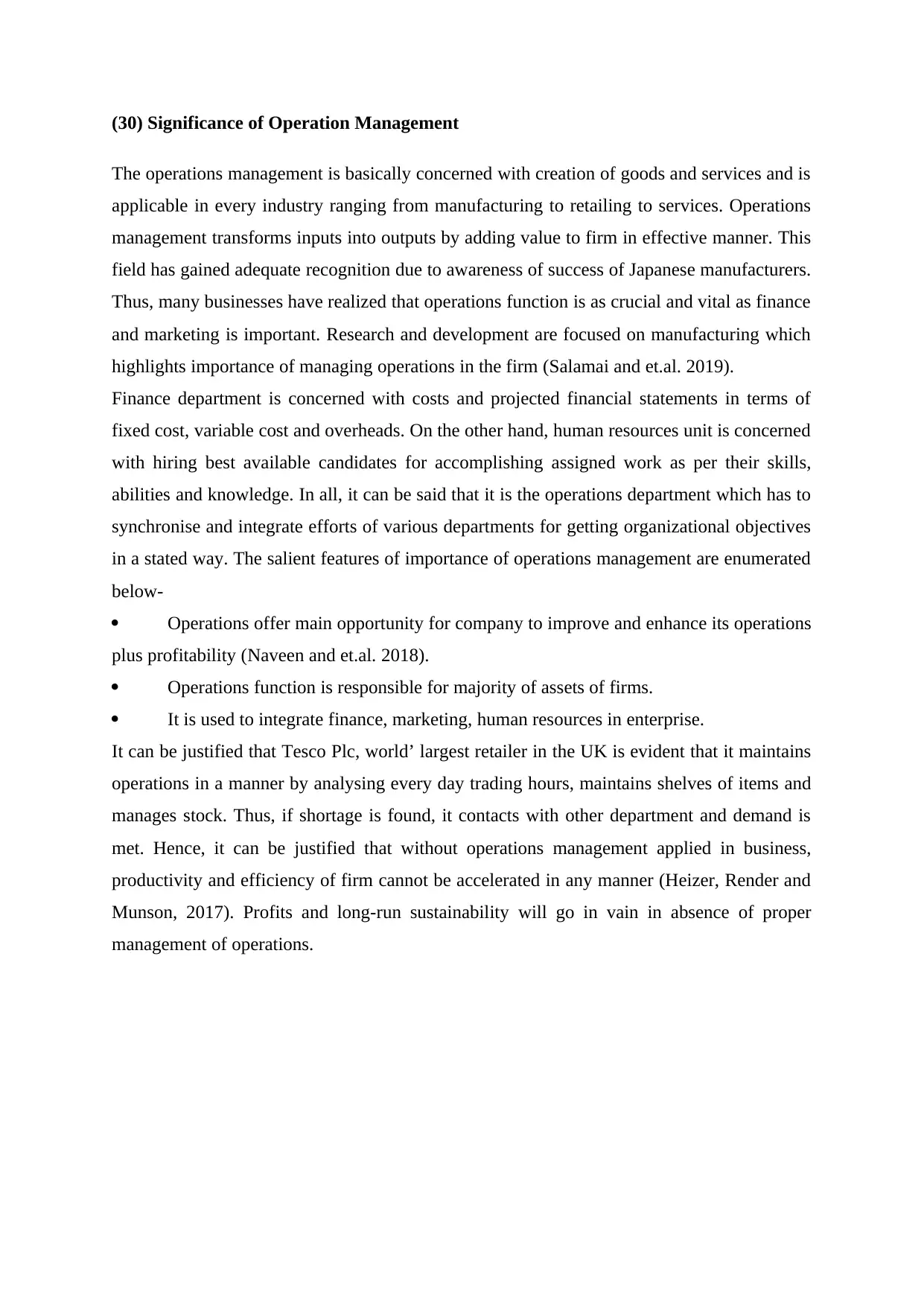
(30) Significance of Operation Management
The operations management is basically concerned with creation of goods and services and is
applicable in every industry ranging from manufacturing to retailing to services. Operations
management transforms inputs into outputs by adding value to firm in effective manner. This
field has gained adequate recognition due to awareness of success of Japanese manufacturers.
Thus, many businesses have realized that operations function is as crucial and vital as finance
and marketing is important. Research and development are focused on manufacturing which
highlights importance of managing operations in the firm (Salamai and et.al. 2019).
Finance department is concerned with costs and projected financial statements in terms of
fixed cost, variable cost and overheads. On the other hand, human resources unit is concerned
with hiring best available candidates for accomplishing assigned work as per their skills,
abilities and knowledge. In all, it can be said that it is the operations department which has to
synchronise and integrate efforts of various departments for getting organizational objectives
in a stated way. The salient features of importance of operations management are enumerated
below-
Operations offer main opportunity for company to improve and enhance its operations
plus profitability (Naveen and et.al. 2018).
Operations function is responsible for majority of assets of firms.
It is used to integrate finance, marketing, human resources in enterprise.
It can be justified that Tesco Plc, world’ largest retailer in the UK is evident that it maintains
operations in a manner by analysing every day trading hours, maintains shelves of items and
manages stock. Thus, if shortage is found, it contacts with other department and demand is
met. Hence, it can be justified that without operations management applied in business,
productivity and efficiency of firm cannot be accelerated in any manner (Heizer, Render and
Munson, 2017). Profits and long-run sustainability will go in vain in absence of proper
management of operations.
The operations management is basically concerned with creation of goods and services and is
applicable in every industry ranging from manufacturing to retailing to services. Operations
management transforms inputs into outputs by adding value to firm in effective manner. This
field has gained adequate recognition due to awareness of success of Japanese manufacturers.
Thus, many businesses have realized that operations function is as crucial and vital as finance
and marketing is important. Research and development are focused on manufacturing which
highlights importance of managing operations in the firm (Salamai and et.al. 2019).
Finance department is concerned with costs and projected financial statements in terms of
fixed cost, variable cost and overheads. On the other hand, human resources unit is concerned
with hiring best available candidates for accomplishing assigned work as per their skills,
abilities and knowledge. In all, it can be said that it is the operations department which has to
synchronise and integrate efforts of various departments for getting organizational objectives
in a stated way. The salient features of importance of operations management are enumerated
below-
Operations offer main opportunity for company to improve and enhance its operations
plus profitability (Naveen and et.al. 2018).
Operations function is responsible for majority of assets of firms.
It is used to integrate finance, marketing, human resources in enterprise.
It can be justified that Tesco Plc, world’ largest retailer in the UK is evident that it maintains
operations in a manner by analysing every day trading hours, maintains shelves of items and
manages stock. Thus, if shortage is found, it contacts with other department and demand is
met. Hence, it can be justified that without operations management applied in business,
productivity and efficiency of firm cannot be accelerated in any manner (Heizer, Render and
Munson, 2017). Profits and long-run sustainability will go in vain in absence of proper
management of operations.
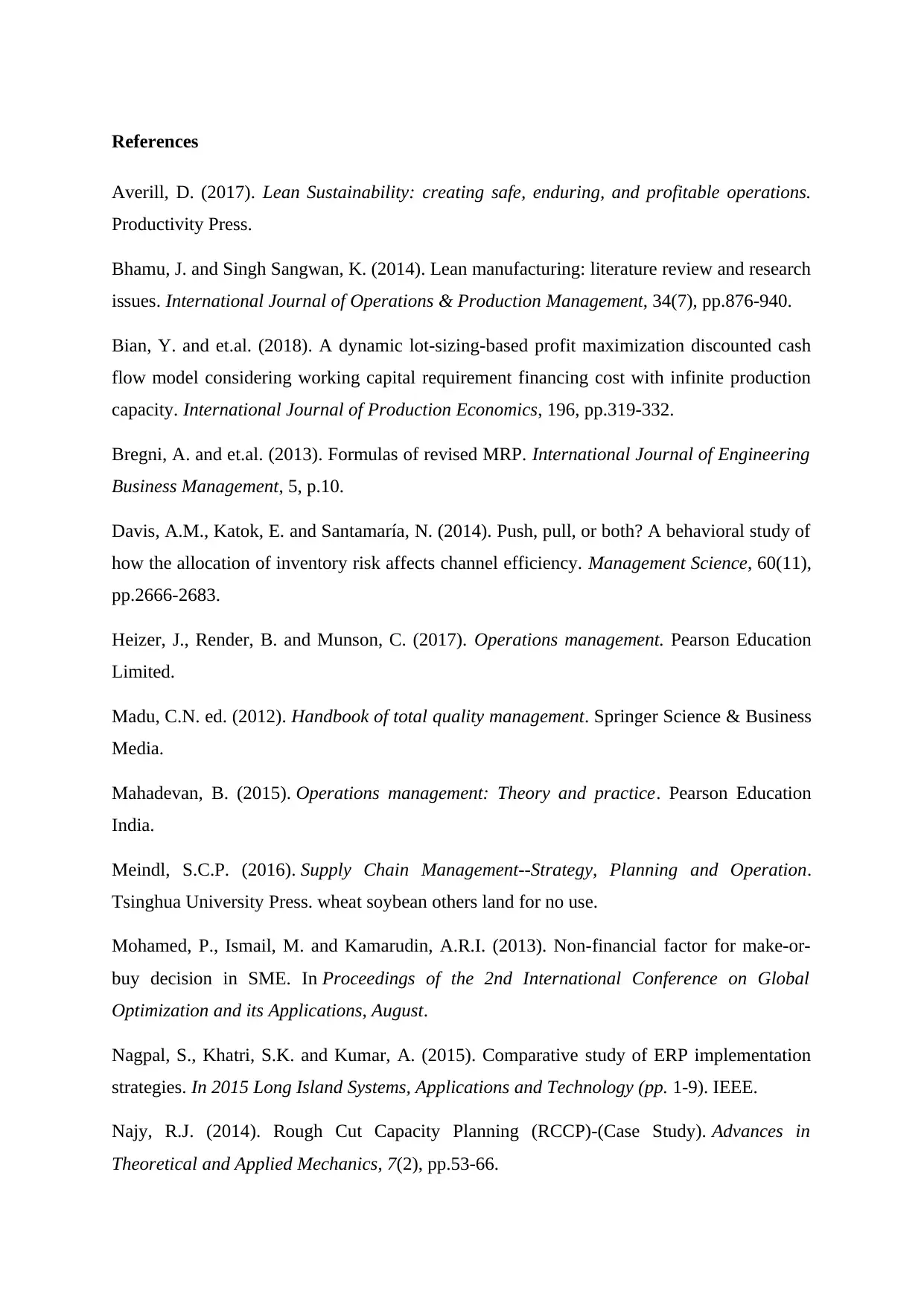
References
Averill, D. (2017). Lean Sustainability: creating safe, enduring, and profitable operations.
Productivity Press.
Bhamu, J. and Singh Sangwan, K. (2014). Lean manufacturing: literature review and research
issues. International Journal of Operations & Production Management, 34(7), pp.876-940.
Bian, Y. and et.al. (2018). A dynamic lot-sizing-based profit maximization discounted cash
flow model considering working capital requirement financing cost with infinite production
capacity. International Journal of Production Economics, 196, pp.319-332.
Bregni, A. and et.al. (2013). Formulas of revised MRP. International Journal of Engineering
Business Management, 5, p.10.
Davis, A.M., Katok, E. and Santamaría, N. (2014). Push, pull, or both? A behavioral study of
how the allocation of inventory risk affects channel efficiency. Management Science, 60(11),
pp.2666-2683.
Heizer, J., Render, B. and Munson, C. (2017). Operations management. Pearson Education
Limited.
Madu, C.N. ed. (2012). Handbook of total quality management. Springer Science & Business
Media.
Mahadevan, B. (2015). Operations management: Theory and practice. Pearson Education
India.
Meindl, S.C.P. (2016). Supply Chain Management--Strategy, Planning and Operation.
Tsinghua University Press. wheat soybean others land for no use.
Mohamed, P., Ismail, M. and Kamarudin, A.R.I. (2013). Non-financial factor for make-or-
buy decision in SME. In Proceedings of the 2nd International Conference on Global
Optimization and its Applications, August.
Nagpal, S., Khatri, S.K. and Kumar, A. (2015). Comparative study of ERP implementation
strategies. In 2015 Long Island Systems, Applications and Technology (pp. 1-9). IEEE.
Najy, R.J. (2014). Rough Cut Capacity Planning (RCCP)-(Case Study). Advances in
Theoretical and Applied Mechanics, 7(2), pp.53-66.
Averill, D. (2017). Lean Sustainability: creating safe, enduring, and profitable operations.
Productivity Press.
Bhamu, J. and Singh Sangwan, K. (2014). Lean manufacturing: literature review and research
issues. International Journal of Operations & Production Management, 34(7), pp.876-940.
Bian, Y. and et.al. (2018). A dynamic lot-sizing-based profit maximization discounted cash
flow model considering working capital requirement financing cost with infinite production
capacity. International Journal of Production Economics, 196, pp.319-332.
Bregni, A. and et.al. (2013). Formulas of revised MRP. International Journal of Engineering
Business Management, 5, p.10.
Davis, A.M., Katok, E. and Santamaría, N. (2014). Push, pull, or both? A behavioral study of
how the allocation of inventory risk affects channel efficiency. Management Science, 60(11),
pp.2666-2683.
Heizer, J., Render, B. and Munson, C. (2017). Operations management. Pearson Education
Limited.
Madu, C.N. ed. (2012). Handbook of total quality management. Springer Science & Business
Media.
Mahadevan, B. (2015). Operations management: Theory and practice. Pearson Education
India.
Meindl, S.C.P. (2016). Supply Chain Management--Strategy, Planning and Operation.
Tsinghua University Press. wheat soybean others land for no use.
Mohamed, P., Ismail, M. and Kamarudin, A.R.I. (2013). Non-financial factor for make-or-
buy decision in SME. In Proceedings of the 2nd International Conference on Global
Optimization and its Applications, August.
Nagpal, S., Khatri, S.K. and Kumar, A. (2015). Comparative study of ERP implementation
strategies. In 2015 Long Island Systems, Applications and Technology (pp. 1-9). IEEE.
Najy, R.J. (2014). Rough Cut Capacity Planning (RCCP)-(Case Study). Advances in
Theoretical and Applied Mechanics, 7(2), pp.53-66.
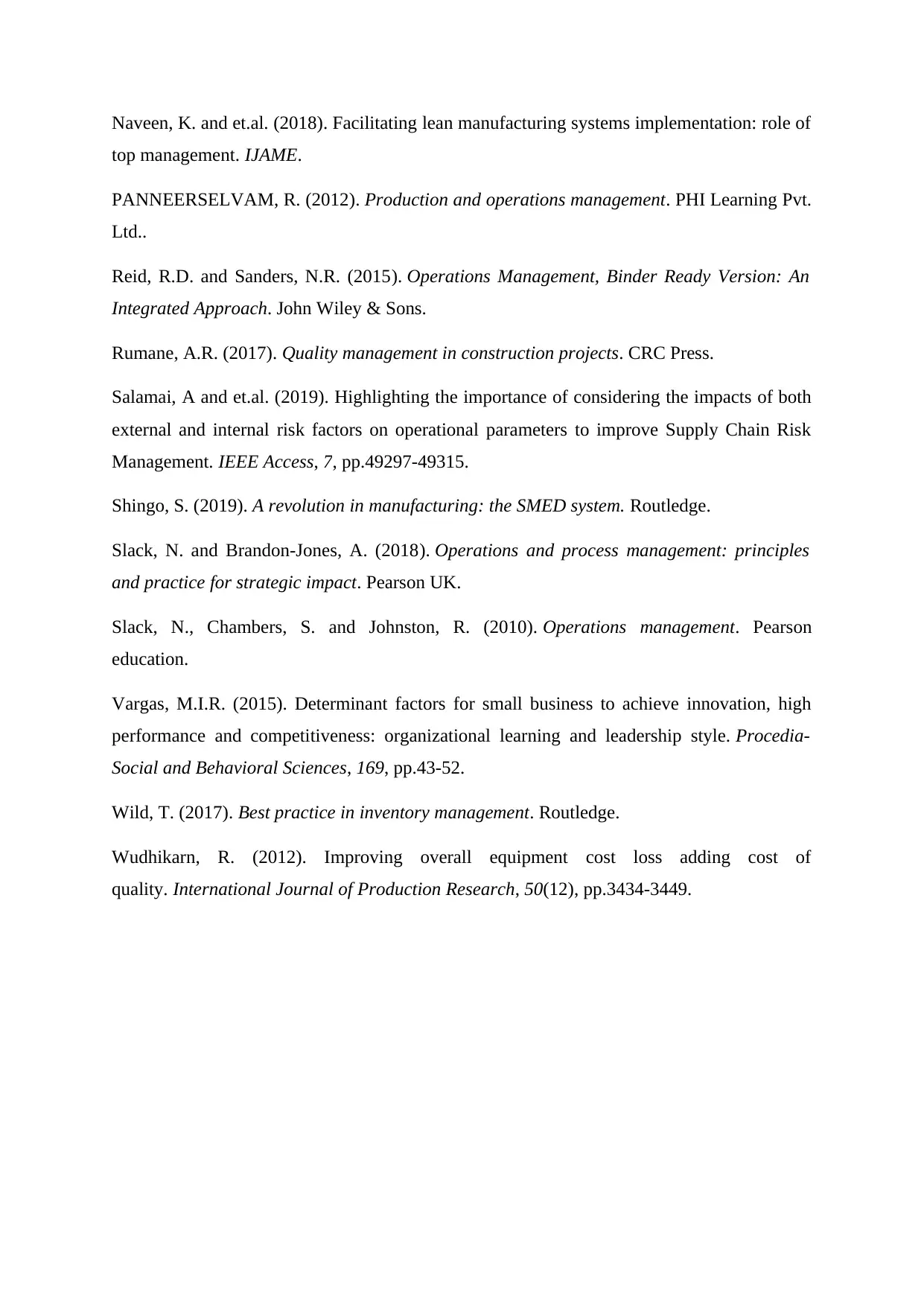
Naveen, K. and et.al. (2018). Facilitating lean manufacturing systems implementation: role of
top management. IJAME.
PANNEERSELVAM, R. (2012). Production and operations management. PHI Learning Pvt.
Ltd..
Reid, R.D. and Sanders, N.R. (2015). Operations Management, Binder Ready Version: An
Integrated Approach. John Wiley & Sons.
Rumane, A.R. (2017). Quality management in construction projects. CRC Press.
Salamai, A and et.al. (2019). Highlighting the importance of considering the impacts of both
external and internal risk factors on operational parameters to improve Supply Chain Risk
Management. IEEE Access, 7, pp.49297-49315.
Shingo, S. (2019). A revolution in manufacturing: the SMED system. Routledge.
Slack, N. and Brandon-Jones, A. (2018). Operations and process management: principles
and practice for strategic impact. Pearson UK.
Slack, N., Chambers, S. and Johnston, R. (2010). Operations management. Pearson
education.
Vargas, M.I.R. (2015). Determinant factors for small business to achieve innovation, high
performance and competitiveness: organizational learning and leadership style. Procedia-
Social and Behavioral Sciences, 169, pp.43-52.
Wild, T. (2017). Best practice in inventory management. Routledge.
Wudhikarn, R. (2012). Improving overall equipment cost loss adding cost of
quality. International Journal of Production Research, 50(12), pp.3434-3449.
top management. IJAME.
PANNEERSELVAM, R. (2012). Production and operations management. PHI Learning Pvt.
Ltd..
Reid, R.D. and Sanders, N.R. (2015). Operations Management, Binder Ready Version: An
Integrated Approach. John Wiley & Sons.
Rumane, A.R. (2017). Quality management in construction projects. CRC Press.
Salamai, A and et.al. (2019). Highlighting the importance of considering the impacts of both
external and internal risk factors on operational parameters to improve Supply Chain Risk
Management. IEEE Access, 7, pp.49297-49315.
Shingo, S. (2019). A revolution in manufacturing: the SMED system. Routledge.
Slack, N. and Brandon-Jones, A. (2018). Operations and process management: principles
and practice for strategic impact. Pearson UK.
Slack, N., Chambers, S. and Johnston, R. (2010). Operations management. Pearson
education.
Vargas, M.I.R. (2015). Determinant factors for small business to achieve innovation, high
performance and competitiveness: organizational learning and leadership style. Procedia-
Social and Behavioral Sciences, 169, pp.43-52.
Wild, T. (2017). Best practice in inventory management. Routledge.
Wudhikarn, R. (2012). Improving overall equipment cost loss adding cost of
quality. International Journal of Production Research, 50(12), pp.3434-3449.
1 out of 19
Related Documents
![[object Object]](/_next/image/?url=%2F_next%2Fstatic%2Fmedia%2Flogo.6d15ce61.png&w=640&q=75)
Your All-in-One AI-Powered Toolkit for Academic Success.
+13062052269
info@desklib.com
Available 24*7 on WhatsApp / Email
Unlock your academic potential
© 2024 | Zucol Services PVT LTD | All rights reserved.