Quality Assurance and Management Assignment
Added on 2020-03-15
19 Pages6411 Words35 Views
Running head: PLANNING AND ANALYSIS OF QUALITY
Planning and Analysis of Quality
Name of the Student:
Name of the University:
Author’s Note:
Planning and Analysis of Quality
Name of the Student:
Name of the University:
Author’s Note:
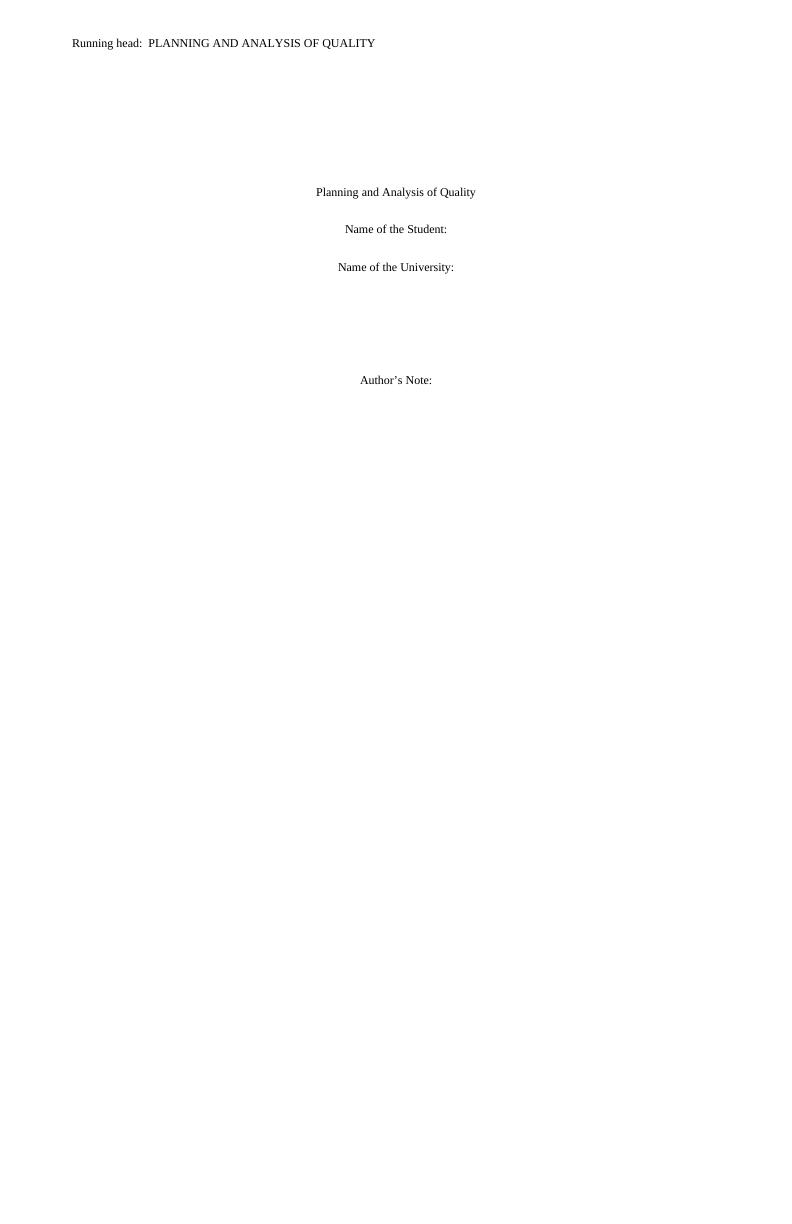
PLANNING AND ANALYSIS OF QUALITY 1
Executive Summary:
The report discusses about the quality planning, activity and analysis for future. Here we are elaborately providing an overview of
quality assurance and management. The scope and measures of selling a product is also discussed in the report. A SWOT analysis is
incorporated for proper planning. Finally, we have provided a broad conclusion about analyzed data, graphs and calculations.
Necessary Kano analysis, stakeholder analysis and SPC charts are provided in the following report. The following report extends the
helping hands towards business analysis and engineering. For customer evaluation and satisfaction, designing the risk analysis and
Supplier Selection System are the provided in the report. This report is the reflection of problem solving strategies that reflects the true
scenario of quality planning and analysis apprehended by statistical packages and marketing criteria. Our objective is to provide the
pathway of marketing and management strategies inferred by statistical conclusions.
Executive Summary:
The report discusses about the quality planning, activity and analysis for future. Here we are elaborately providing an overview of
quality assurance and management. The scope and measures of selling a product is also discussed in the report. A SWOT analysis is
incorporated for proper planning. Finally, we have provided a broad conclusion about analyzed data, graphs and calculations.
Necessary Kano analysis, stakeholder analysis and SPC charts are provided in the following report. The following report extends the
helping hands towards business analysis and engineering. For customer evaluation and satisfaction, designing the risk analysis and
Supplier Selection System are the provided in the report. This report is the reflection of problem solving strategies that reflects the true
scenario of quality planning and analysis apprehended by statistical packages and marketing criteria. Our objective is to provide the
pathway of marketing and management strategies inferred by statistical conclusions.
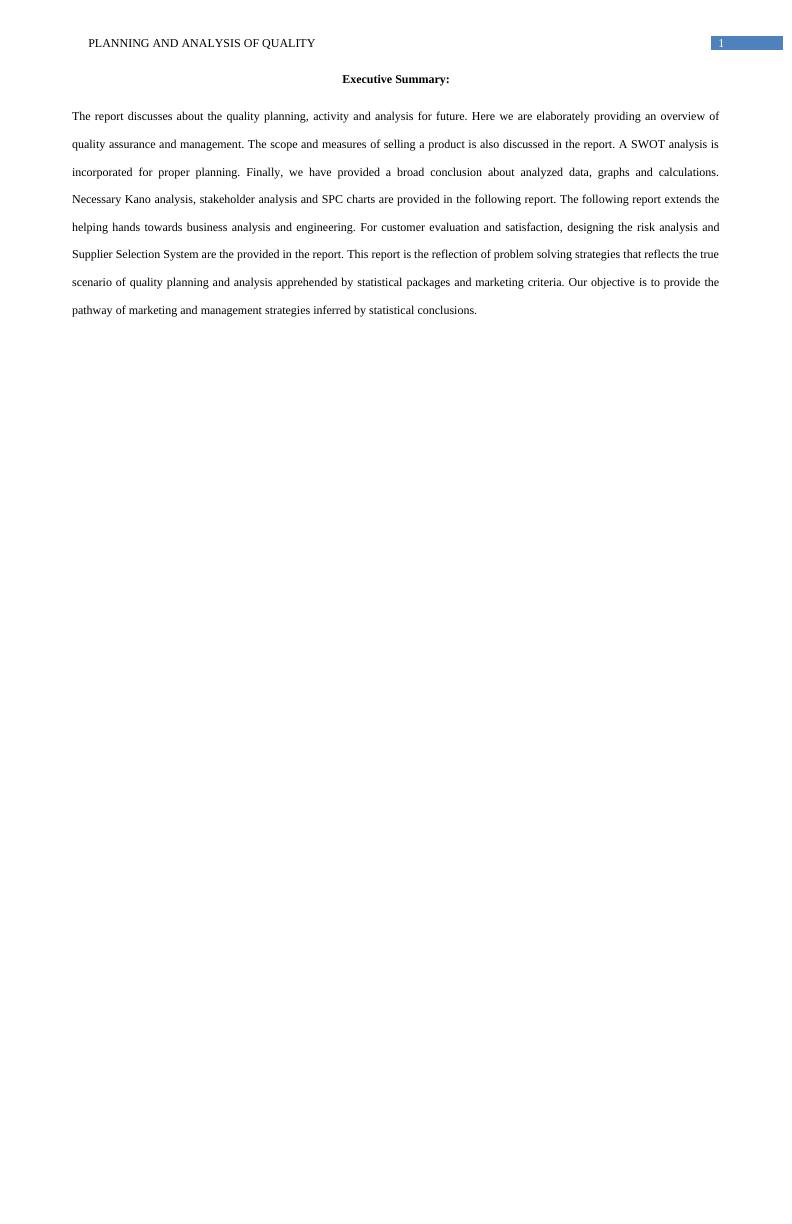
PLANNING AND ANALYSIS OF QUALITY 2
Table of Contents
1. Introduction:-.......................................................................................................................................................................................3
Overview of Quality Management characteristics:-................................................................................................................................3
2. CUSTOMER SATISFACTION:.........................................................................................................................................................3
2.1. Stakeholder Analysis:.......................................................................................................................................................................3
2.2. Process of capturing the Customer needs:........................................................................................................................................5
2.3. Analysis of Customer Needs (Kano Analysis):................................................................................................................................5
3. REQUIREMENTS OF DESIGNING:....................................................................................................................................................7
3.1. Translation of Customer Needs to Design Requirements (QFD):....................................................................................................7
3.2. Design Risk Analysis:.......................................................................................................................................................................9
4.SUPPLIER SELECTION AND EVALUATION:.................................................................................................................................10
4.1. Identification of Component elements:..........................................................................................................................................10
4.2. Method of developing the Supplier Selection System:...................................................................................................................10
4.3. Construction and Use of a Supplier Selection System:..................................................................................................................11
4.4. Conclusion:-....................................................................................................................................................................................11
5. METHOD OF STATISTICAL PROCESS CONTROL:......................................................................................................................12
5.1. Identification of the processes:.......................................................................................................................................................12
5.2. Construction and Use of a SPC chart:.........................................................................................................................................13
6. STRATEGY TO SOLVE THE PROBLEM:........................................................................................................................................14
6.1. Identification of Problems and Use of Problem-Solving Tools:....................................................................................................14
6.2. Construction and Use of Problem-Solving Tools:..........................................................................................................................15
Check sheet:-.....................................................................................................................................................................................15
Problem solving form........................................................................................................................................................................15
7. Conclusion:............................................................................................................................................................................................16
Reference:-.................................................................................................................................................................................................17
Table of Contents
1. Introduction:-.......................................................................................................................................................................................3
Overview of Quality Management characteristics:-................................................................................................................................3
2. CUSTOMER SATISFACTION:.........................................................................................................................................................3
2.1. Stakeholder Analysis:.......................................................................................................................................................................3
2.2. Process of capturing the Customer needs:........................................................................................................................................5
2.3. Analysis of Customer Needs (Kano Analysis):................................................................................................................................5
3. REQUIREMENTS OF DESIGNING:....................................................................................................................................................7
3.1. Translation of Customer Needs to Design Requirements (QFD):....................................................................................................7
3.2. Design Risk Analysis:.......................................................................................................................................................................9
4.SUPPLIER SELECTION AND EVALUATION:.................................................................................................................................10
4.1. Identification of Component elements:..........................................................................................................................................10
4.2. Method of developing the Supplier Selection System:...................................................................................................................10
4.3. Construction and Use of a Supplier Selection System:..................................................................................................................11
4.4. Conclusion:-....................................................................................................................................................................................11
5. METHOD OF STATISTICAL PROCESS CONTROL:......................................................................................................................12
5.1. Identification of the processes:.......................................................................................................................................................12
5.2. Construction and Use of a SPC chart:.........................................................................................................................................13
6. STRATEGY TO SOLVE THE PROBLEM:........................................................................................................................................14
6.1. Identification of Problems and Use of Problem-Solving Tools:....................................................................................................14
6.2. Construction and Use of Problem-Solving Tools:..........................................................................................................................15
Check sheet:-.....................................................................................................................................................................................15
Problem solving form........................................................................................................................................................................15
7. Conclusion:............................................................................................................................................................................................16
Reference:-.................................................................................................................................................................................................17
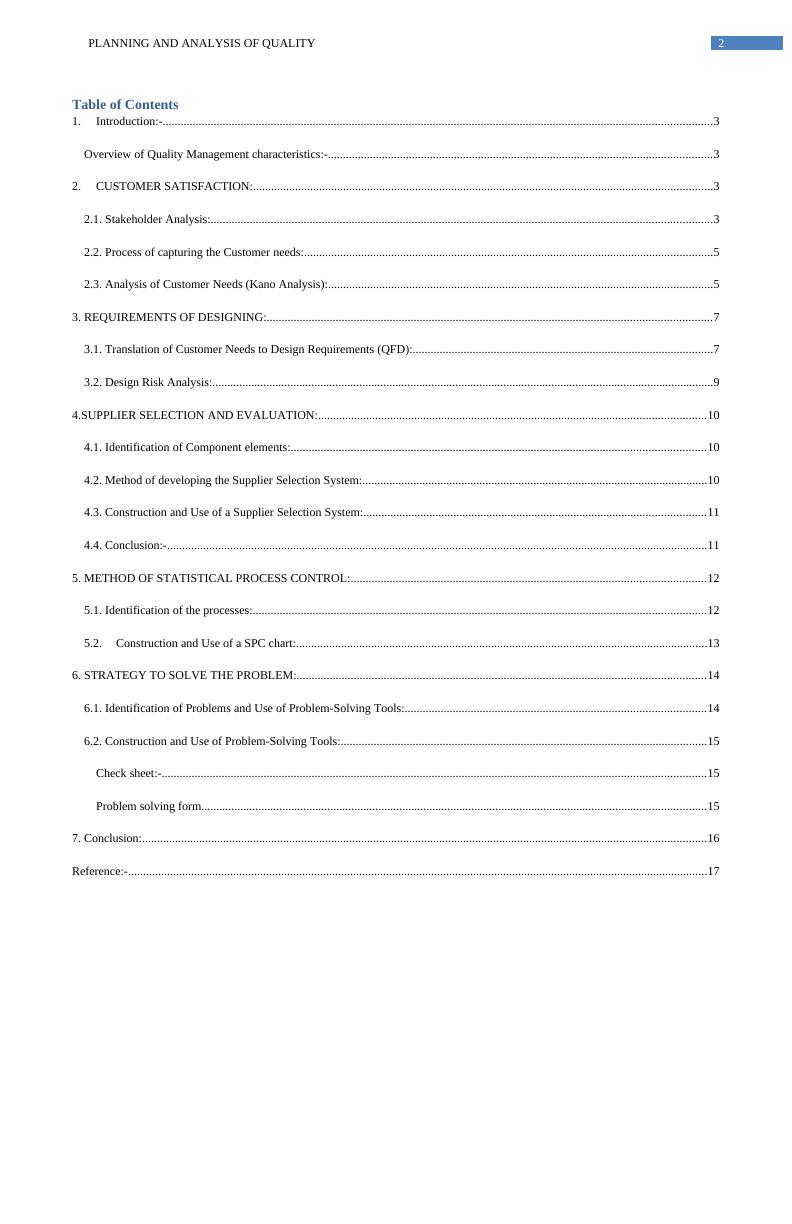
PLANNING AND ANALYSIS OF QUALITY 3
1. Introduction:-
The definition of ‘quality management’ involves the processes, relationships, organizational management and structures.
Quality is mobile condition associated with product and services that fulfils customer needs and expectations. It helps to produce
superior value. Quality is a state that changes frequently and provides three elements such as quality, superior cost and superior
service. The characteristics of total quality management have various outlooks. Quality organizations have strategic plan of vision,
mission, objectives and activities (Armstrong et al. 2015). Building awareness in both the need for improvement and opportunities
could increase quality characteristics.
The report incorporates the ideas of ‘quality management’ and explores the hypothesis that there is a vital link between quality
management and services. The report defines the existing quality development and control. It also suggests the statistical process
control measures, expected quality and continual improved process.
The rationale for quality management could be found to compete the global marketplace. Consumer satisfaction and expected
quality measure focus on the improvement of quality (Blut et al. 2017). According to this discussion, the three aspects and designs are
elaborated. The data and information given in the assignment is relevant to the topic and proficiently analyzed.
Overview of Quality Management characteristics:-
The market competition, total commitment and fundamental improvement are the major dimensions of quality management
(Simatupang and Sridharan 2014). It has mainly four objectives such as customer satisfaction, effectiveness, cost leadership and
integration with the supplier base. We have to make sure that the management is committed to quality for long-term basis. Our aim is
to encourage employees and solve the obstacles they face in attempting to meet quality goals. The determination, education and
implementation could define the zero defect management.
2. CUSTOMER SATISFACTION:
Rational costs have the strongest association with repurchase cost. Satisfaction-repurchase link could be mitigated by the
relational and procedural costs. Customer dis-satisfaction may directly or indirectly spoil marketing strategy. A meta-analysis of 233
effects from over 133,000 customers shows that the relational costs have the strongest association with repurchase behavior (Hanski et
al 2014). It also indicates the procedural and relational costs that associate between satisfaction and repurchase intentions. The product
and service development issues have to get sustainable solutions. Product developers, designers, consultancies, policy-makers would
focus on customer satisfaction.
The customer knowledge and customer satisfaction are correlated to each other. Now-a-days social media have transformed
the buyers and sellers interaction (Agnihotri et al. 2017). Findings and analyses reveal that social media has a vital role in
communicating information to customers. Therefore, to increase customer satisfaction, managers carefully assess targets related to the
social media due to demand of sales.
2.1. Stakeholder Analysis:
Internal Stakeholders Expectations
1. Introduction:-
The definition of ‘quality management’ involves the processes, relationships, organizational management and structures.
Quality is mobile condition associated with product and services that fulfils customer needs and expectations. It helps to produce
superior value. Quality is a state that changes frequently and provides three elements such as quality, superior cost and superior
service. The characteristics of total quality management have various outlooks. Quality organizations have strategic plan of vision,
mission, objectives and activities (Armstrong et al. 2015). Building awareness in both the need for improvement and opportunities
could increase quality characteristics.
The report incorporates the ideas of ‘quality management’ and explores the hypothesis that there is a vital link between quality
management and services. The report defines the existing quality development and control. It also suggests the statistical process
control measures, expected quality and continual improved process.
The rationale for quality management could be found to compete the global marketplace. Consumer satisfaction and expected
quality measure focus on the improvement of quality (Blut et al. 2017). According to this discussion, the three aspects and designs are
elaborated. The data and information given in the assignment is relevant to the topic and proficiently analyzed.
Overview of Quality Management characteristics:-
The market competition, total commitment and fundamental improvement are the major dimensions of quality management
(Simatupang and Sridharan 2014). It has mainly four objectives such as customer satisfaction, effectiveness, cost leadership and
integration with the supplier base. We have to make sure that the management is committed to quality for long-term basis. Our aim is
to encourage employees and solve the obstacles they face in attempting to meet quality goals. The determination, education and
implementation could define the zero defect management.
2. CUSTOMER SATISFACTION:
Rational costs have the strongest association with repurchase cost. Satisfaction-repurchase link could be mitigated by the
relational and procedural costs. Customer dis-satisfaction may directly or indirectly spoil marketing strategy. A meta-analysis of 233
effects from over 133,000 customers shows that the relational costs have the strongest association with repurchase behavior (Hanski et
al 2014). It also indicates the procedural and relational costs that associate between satisfaction and repurchase intentions. The product
and service development issues have to get sustainable solutions. Product developers, designers, consultancies, policy-makers would
focus on customer satisfaction.
The customer knowledge and customer satisfaction are correlated to each other. Now-a-days social media have transformed
the buyers and sellers interaction (Agnihotri et al. 2017). Findings and analyses reveal that social media has a vital role in
communicating information to customers. Therefore, to increase customer satisfaction, managers carefully assess targets related to the
social media due to demand of sales.
2.1. Stakeholder Analysis:
Internal Stakeholders Expectations
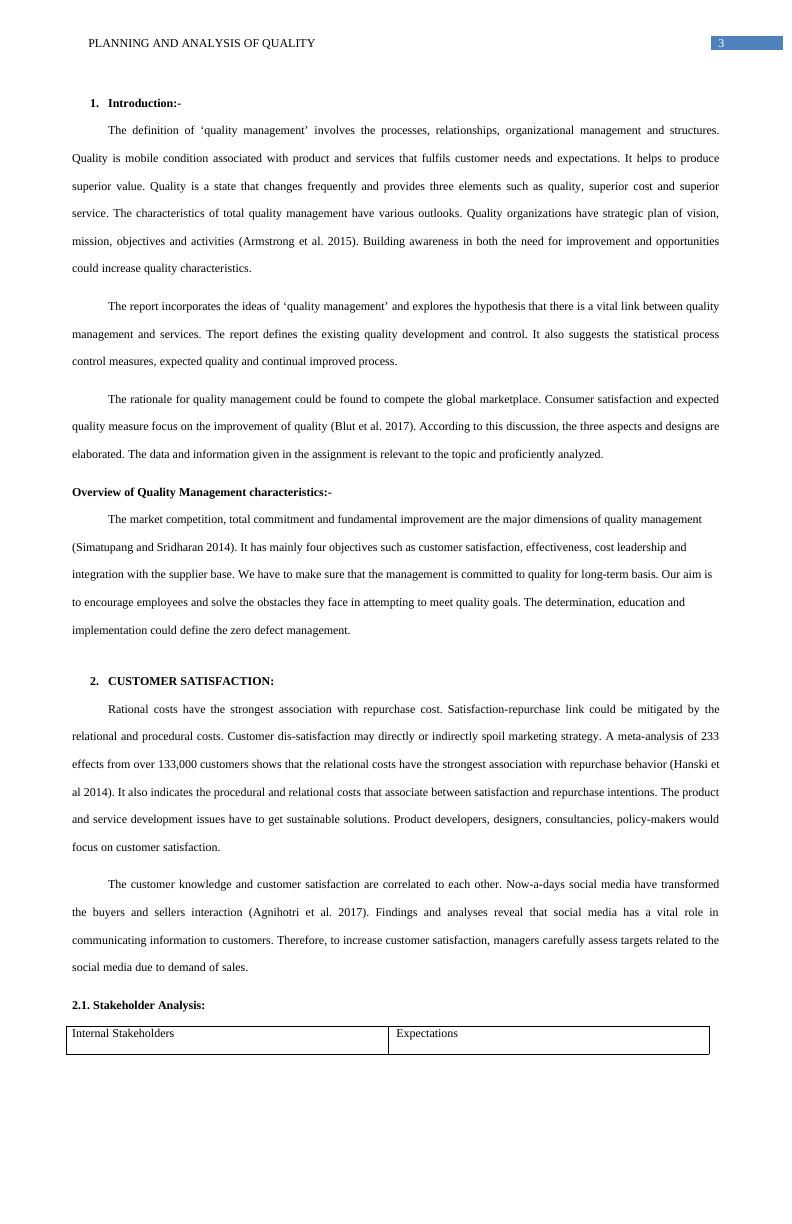
End of preview
Want to access all the pages? Upload your documents or become a member.
Related Documents
Quality Planning and Analysis: Porcelain Tileslg...
|48
|10314
|183
Quality Planning and Analysislg...
|36
|8010
|92
Quality Planning & Analysis Assignmentlg...
|38
|8828
|64
Quality Analysis Report (doc)lg...
|40
|9654
|342
Quality Planning Analysis for English Training at British Councillg...
|31
|5230
|425
Customer Satisfaction and Design Requirements for Porcelain Tileslg...
|39
|7799
|464