Quality Management in Engineering Organizations Research 2022
VerifiedAdded on 2022/09/28
|13
|2997
|21
AI Summary
Contribute Materials
Your contribution can guide someone’s learning journey. Share your
documents today.
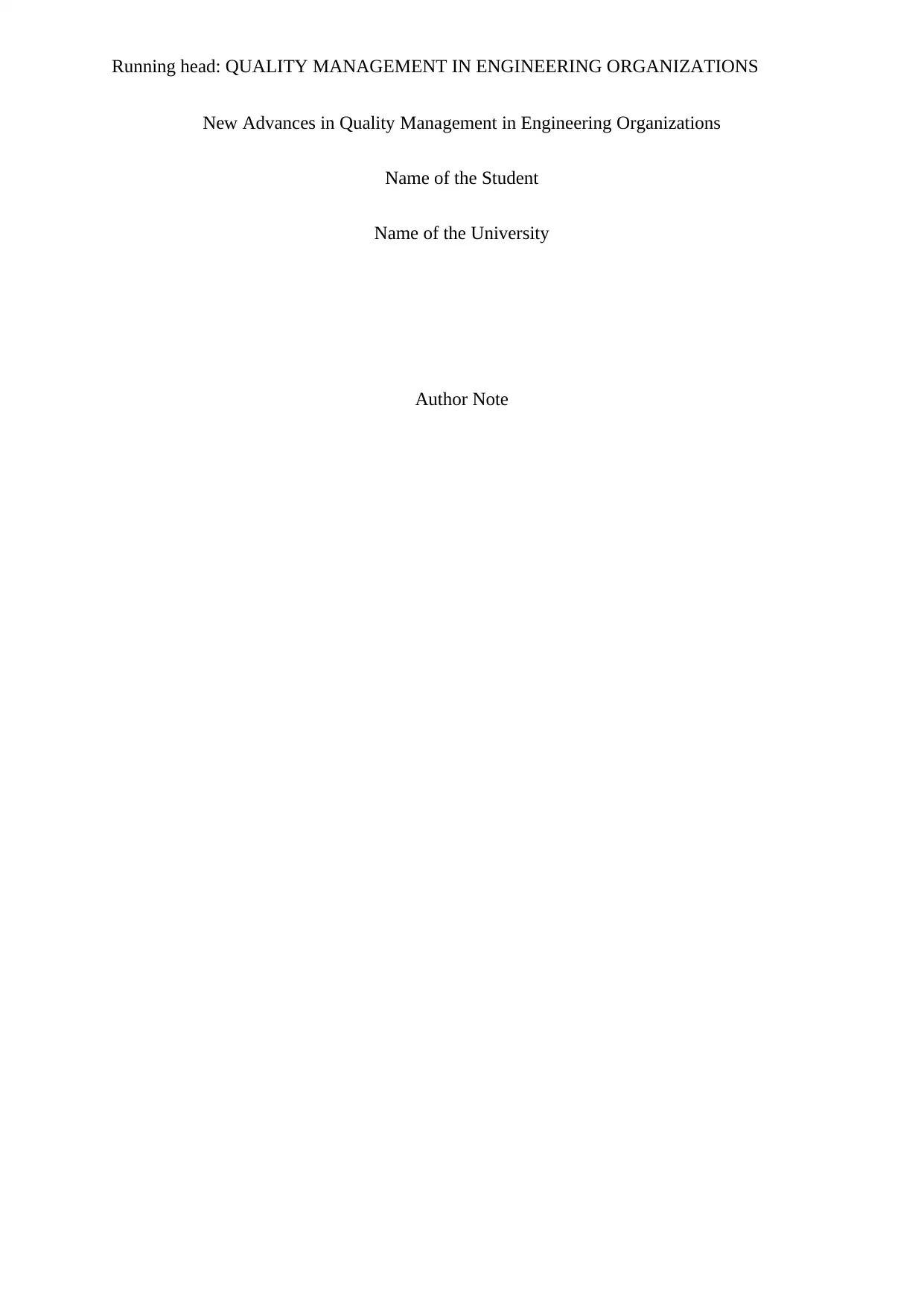
Running head: QUALITY MANAGEMENT IN ENGINEERING ORGANIZATIONS
New Advances in Quality Management in Engineering Organizations
Name of the Student
Name of the University
Author Note
New Advances in Quality Management in Engineering Organizations
Name of the Student
Name of the University
Author Note
Secure Best Marks with AI Grader
Need help grading? Try our AI Grader for instant feedback on your assignments.
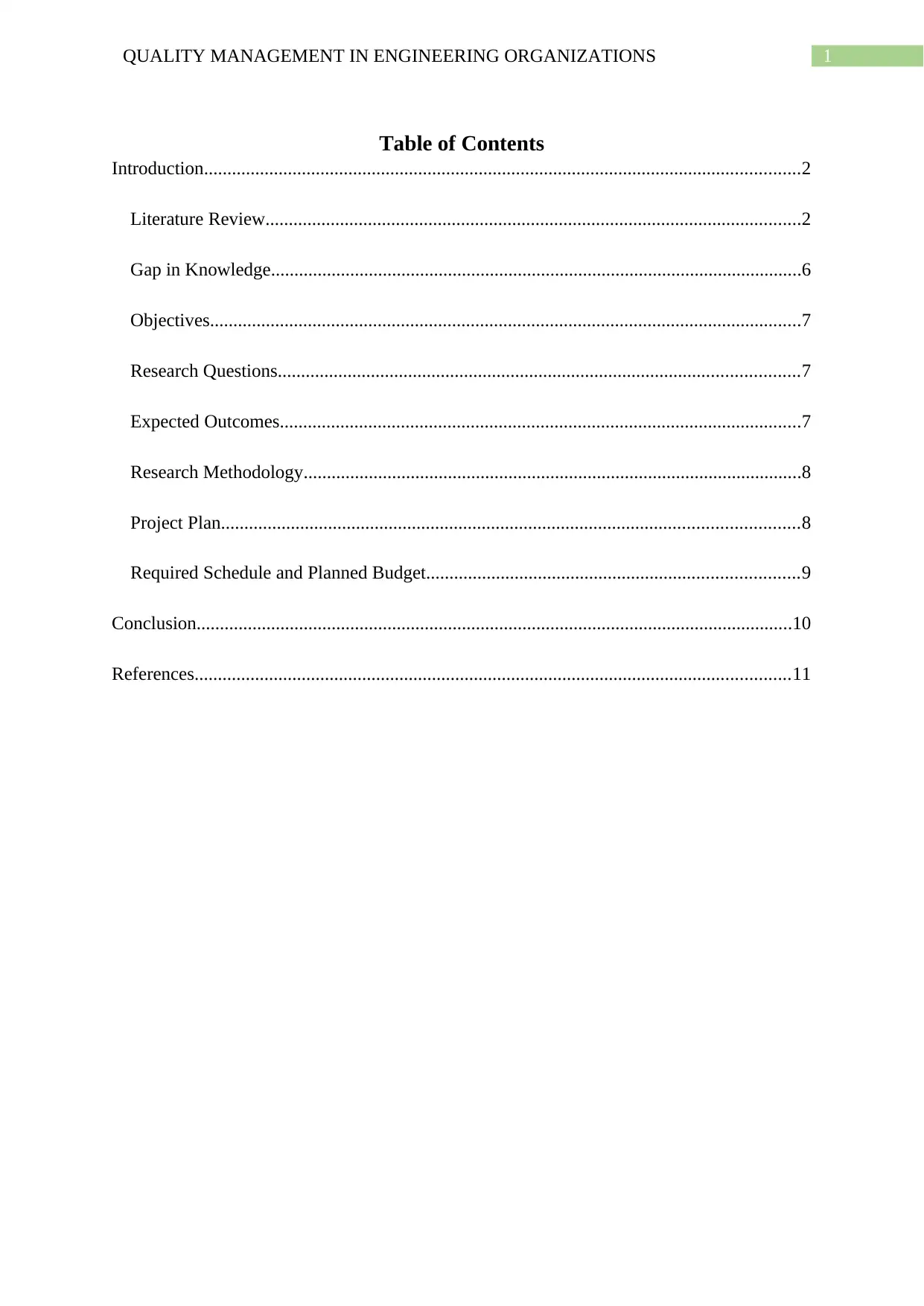
1QUALITY MANAGEMENT IN ENGINEERING ORGANIZATIONS
Table of Contents
Introduction................................................................................................................................2
Literature Review...................................................................................................................2
Gap in Knowledge..................................................................................................................6
Objectives...............................................................................................................................7
Research Questions................................................................................................................7
Expected Outcomes................................................................................................................7
Research Methodology...........................................................................................................8
Project Plan............................................................................................................................8
Required Schedule and Planned Budget................................................................................9
Conclusion................................................................................................................................10
References................................................................................................................................11
Table of Contents
Introduction................................................................................................................................2
Literature Review...................................................................................................................2
Gap in Knowledge..................................................................................................................6
Objectives...............................................................................................................................7
Research Questions................................................................................................................7
Expected Outcomes................................................................................................................7
Research Methodology...........................................................................................................8
Project Plan............................................................................................................................8
Required Schedule and Planned Budget................................................................................9
Conclusion................................................................................................................................10
References................................................................................................................................11
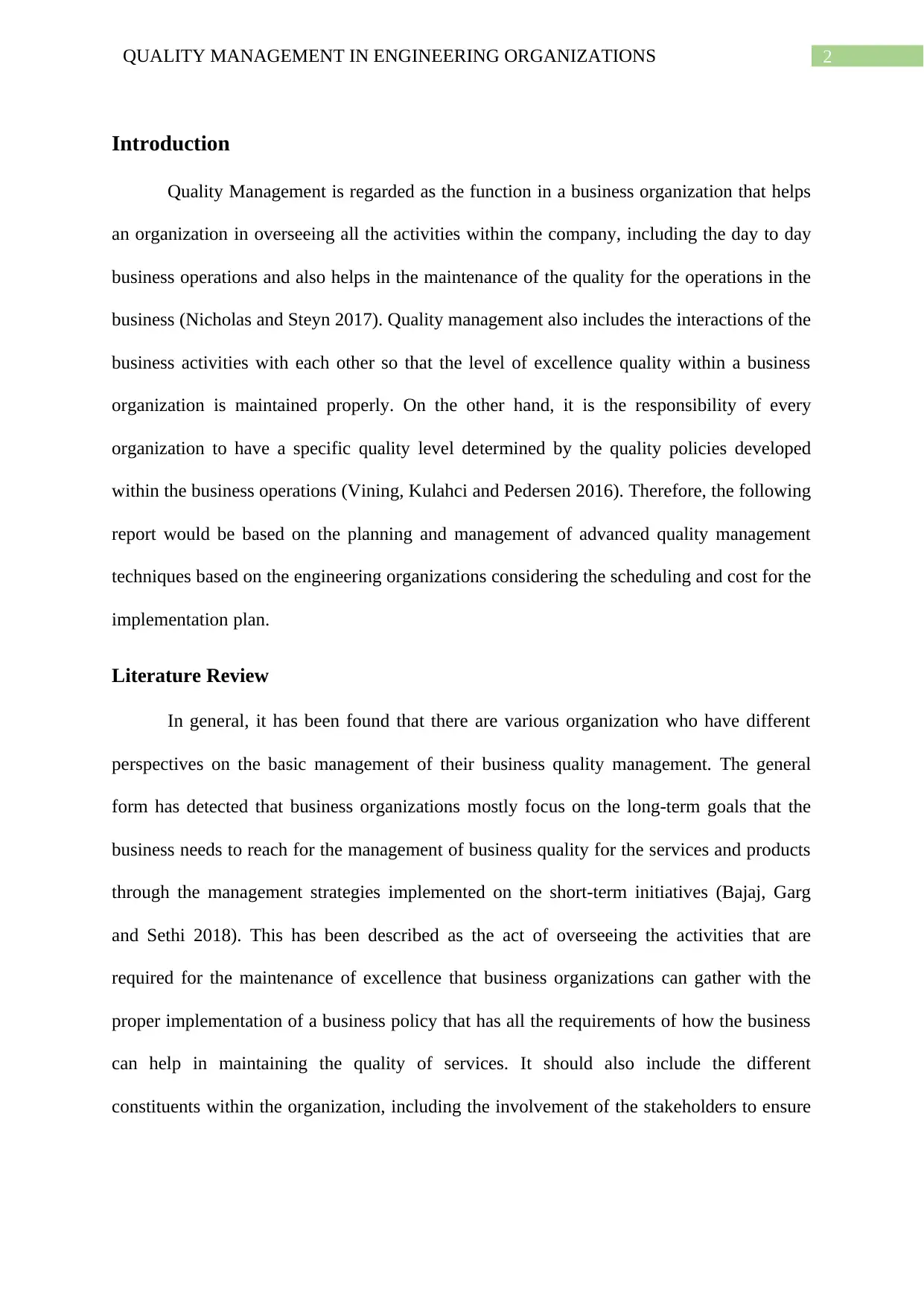
2QUALITY MANAGEMENT IN ENGINEERING ORGANIZATIONS
Introduction
Quality Management is regarded as the function in a business organization that helps
an organization in overseeing all the activities within the company, including the day to day
business operations and also helps in the maintenance of the quality for the operations in the
business (Nicholas and Steyn 2017). Quality management also includes the interactions of the
business activities with each other so that the level of excellence quality within a business
organization is maintained properly. On the other hand, it is the responsibility of every
organization to have a specific quality level determined by the quality policies developed
within the business operations (Vining, Kulahci and Pedersen 2016). Therefore, the following
report would be based on the planning and management of advanced quality management
techniques based on the engineering organizations considering the scheduling and cost for the
implementation plan.
Literature Review
In general, it has been found that there are various organization who have different
perspectives on the basic management of their business quality management. The general
form has detected that business organizations mostly focus on the long-term goals that the
business needs to reach for the management of business quality for the services and products
through the management strategies implemented on the short-term initiatives (Bajaj, Garg
and Sethi 2018). This has been described as the act of overseeing the activities that are
required for the maintenance of excellence that business organizations can gather with the
proper implementation of a business policy that has all the requirements of how the business
can help in maintaining the quality of services. It should also include the different
constituents within the organization, including the involvement of the stakeholders to ensure
Introduction
Quality Management is regarded as the function in a business organization that helps
an organization in overseeing all the activities within the company, including the day to day
business operations and also helps in the maintenance of the quality for the operations in the
business (Nicholas and Steyn 2017). Quality management also includes the interactions of the
business activities with each other so that the level of excellence quality within a business
organization is maintained properly. On the other hand, it is the responsibility of every
organization to have a specific quality level determined by the quality policies developed
within the business operations (Vining, Kulahci and Pedersen 2016). Therefore, the following
report would be based on the planning and management of advanced quality management
techniques based on the engineering organizations considering the scheduling and cost for the
implementation plan.
Literature Review
In general, it has been found that there are various organization who have different
perspectives on the basic management of their business quality management. The general
form has detected that business organizations mostly focus on the long-term goals that the
business needs to reach for the management of business quality for the services and products
through the management strategies implemented on the short-term initiatives (Bajaj, Garg
and Sethi 2018). This has been described as the act of overseeing the activities that are
required for the maintenance of excellence that business organizations can gather with the
proper implementation of a business policy that has all the requirements of how the business
can help in maintaining the quality of services. It should also include the different
constituents within the organization, including the involvement of the stakeholders to ensure
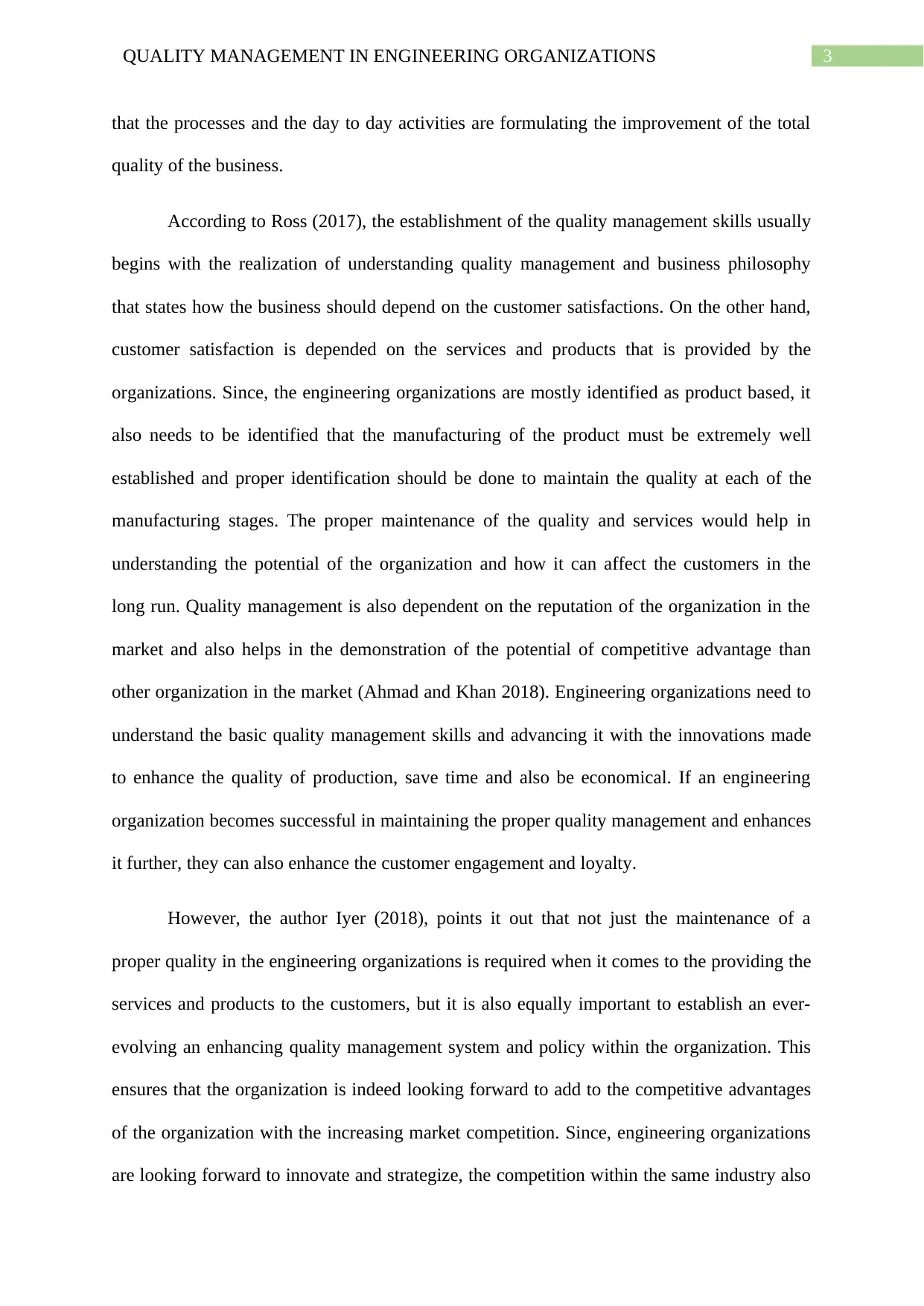
3QUALITY MANAGEMENT IN ENGINEERING ORGANIZATIONS
that the processes and the day to day activities are formulating the improvement of the total
quality of the business.
According to Ross (2017), the establishment of the quality management skills usually
begins with the realization of understanding quality management and business philosophy
that states how the business should depend on the customer satisfactions. On the other hand,
customer satisfaction is depended on the services and products that is provided by the
organizations. Since, the engineering organizations are mostly identified as product based, it
also needs to be identified that the manufacturing of the product must be extremely well
established and proper identification should be done to maintain the quality at each of the
manufacturing stages. The proper maintenance of the quality and services would help in
understanding the potential of the organization and how it can affect the customers in the
long run. Quality management is also dependent on the reputation of the organization in the
market and also helps in the demonstration of the potential of competitive advantage than
other organization in the market (Ahmad and Khan 2018). Engineering organizations need to
understand the basic quality management skills and advancing it with the innovations made
to enhance the quality of production, save time and also be economical. If an engineering
organization becomes successful in maintaining the proper quality management and enhances
it further, they can also enhance the customer engagement and loyalty.
However, the author Iyer (2018), points it out that not just the maintenance of a
proper quality in the engineering organizations is required when it comes to the providing the
services and products to the customers, but it is also equally important to establish an ever-
evolving an enhancing quality management system and policy within the organization. This
ensures that the organization is indeed looking forward to add to the competitive advantages
of the organization with the increasing market competition. Since, engineering organizations
are looking forward to innovate and strategize, the competition within the same industry also
that the processes and the day to day activities are formulating the improvement of the total
quality of the business.
According to Ross (2017), the establishment of the quality management skills usually
begins with the realization of understanding quality management and business philosophy
that states how the business should depend on the customer satisfactions. On the other hand,
customer satisfaction is depended on the services and products that is provided by the
organizations. Since, the engineering organizations are mostly identified as product based, it
also needs to be identified that the manufacturing of the product must be extremely well
established and proper identification should be done to maintain the quality at each of the
manufacturing stages. The proper maintenance of the quality and services would help in
understanding the potential of the organization and how it can affect the customers in the
long run. Quality management is also dependent on the reputation of the organization in the
market and also helps in the demonstration of the potential of competitive advantage than
other organization in the market (Ahmad and Khan 2018). Engineering organizations need to
understand the basic quality management skills and advancing it with the innovations made
to enhance the quality of production, save time and also be economical. If an engineering
organization becomes successful in maintaining the proper quality management and enhances
it further, they can also enhance the customer engagement and loyalty.
However, the author Iyer (2018), points it out that not just the maintenance of a
proper quality in the engineering organizations is required when it comes to the providing the
services and products to the customers, but it is also equally important to establish an ever-
evolving an enhancing quality management system and policy within the organization. This
ensures that the organization is indeed looking forward to add to the competitive advantages
of the organization with the increasing market competition. Since, engineering organizations
are looking forward to innovate and strategize, the competition within the same industry also
Secure Best Marks with AI Grader
Need help grading? Try our AI Grader for instant feedback on your assignments.
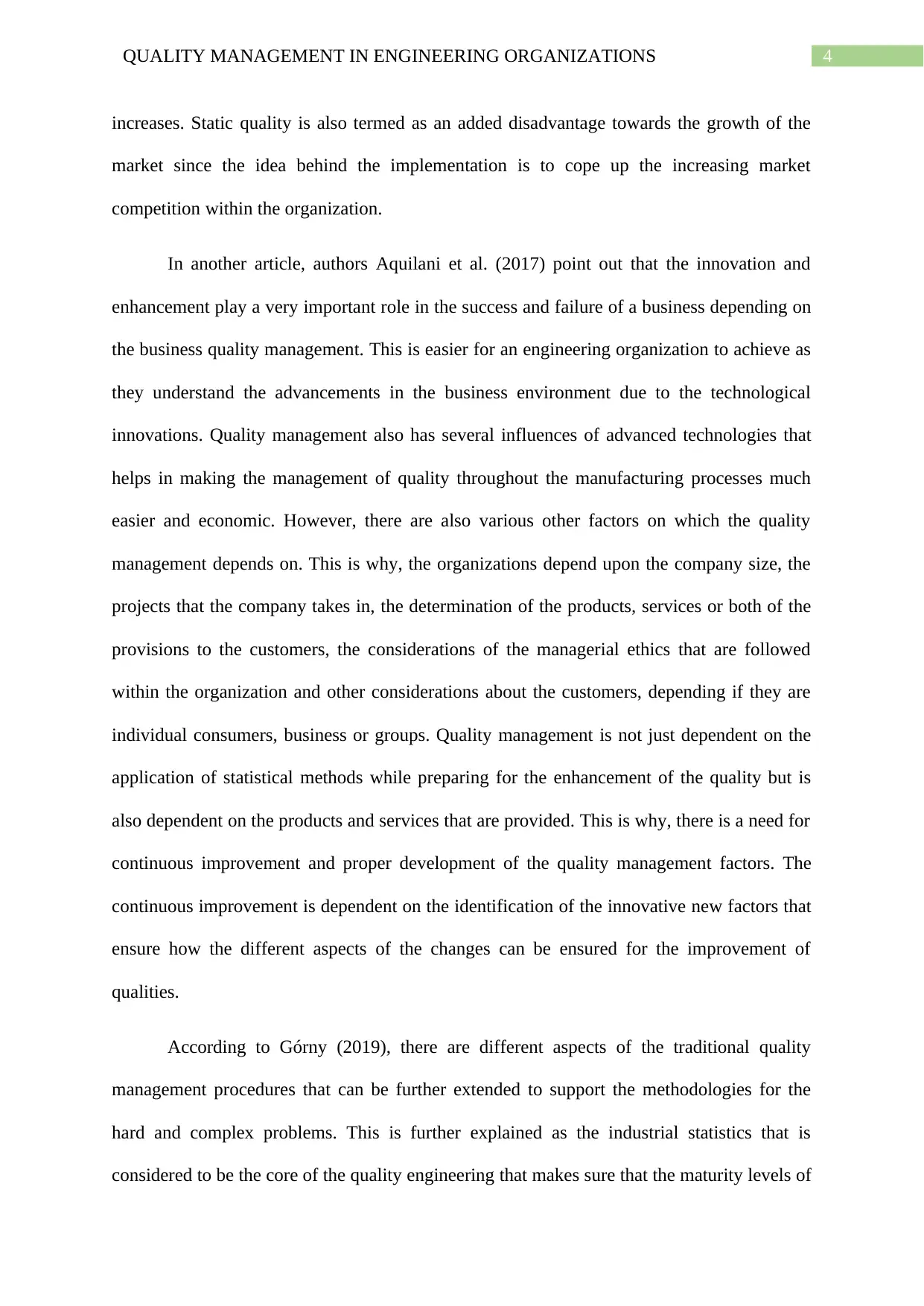
4QUALITY MANAGEMENT IN ENGINEERING ORGANIZATIONS
increases. Static quality is also termed as an added disadvantage towards the growth of the
market since the idea behind the implementation is to cope up the increasing market
competition within the organization.
In another article, authors Aquilani et al. (2017) point out that the innovation and
enhancement play a very important role in the success and failure of a business depending on
the business quality management. This is easier for an engineering organization to achieve as
they understand the advancements in the business environment due to the technological
innovations. Quality management also has several influences of advanced technologies that
helps in making the management of quality throughout the manufacturing processes much
easier and economic. However, there are also various other factors on which the quality
management depends on. This is why, the organizations depend upon the company size, the
projects that the company takes in, the determination of the products, services or both of the
provisions to the customers, the considerations of the managerial ethics that are followed
within the organization and other considerations about the customers, depending if they are
individual consumers, business or groups. Quality management is not just dependent on the
application of statistical methods while preparing for the enhancement of the quality but is
also dependent on the products and services that are provided. This is why, there is a need for
continuous improvement and proper development of the quality management factors. The
continuous improvement is dependent on the identification of the innovative new factors that
ensure how the different aspects of the changes can be ensured for the improvement of
qualities.
According to Górny (2019), there are different aspects of the traditional quality
management procedures that can be further extended to support the methodologies for the
hard and complex problems. This is further explained as the industrial statistics that is
considered to be the core of the quality engineering that makes sure that the maturity levels of
increases. Static quality is also termed as an added disadvantage towards the growth of the
market since the idea behind the implementation is to cope up the increasing market
competition within the organization.
In another article, authors Aquilani et al. (2017) point out that the innovation and
enhancement play a very important role in the success and failure of a business depending on
the business quality management. This is easier for an engineering organization to achieve as
they understand the advancements in the business environment due to the technological
innovations. Quality management also has several influences of advanced technologies that
helps in making the management of quality throughout the manufacturing processes much
easier and economic. However, there are also various other factors on which the quality
management depends on. This is why, the organizations depend upon the company size, the
projects that the company takes in, the determination of the products, services or both of the
provisions to the customers, the considerations of the managerial ethics that are followed
within the organization and other considerations about the customers, depending if they are
individual consumers, business or groups. Quality management is not just dependent on the
application of statistical methods while preparing for the enhancement of the quality but is
also dependent on the products and services that are provided. This is why, there is a need for
continuous improvement and proper development of the quality management factors. The
continuous improvement is dependent on the identification of the innovative new factors that
ensure how the different aspects of the changes can be ensured for the improvement of
qualities.
According to Górny (2019), there are different aspects of the traditional quality
management procedures that can be further extended to support the methodologies for the
hard and complex problems. This is further explained as the industrial statistics that is
considered to be the core of the quality engineering that makes sure that the maturity levels of
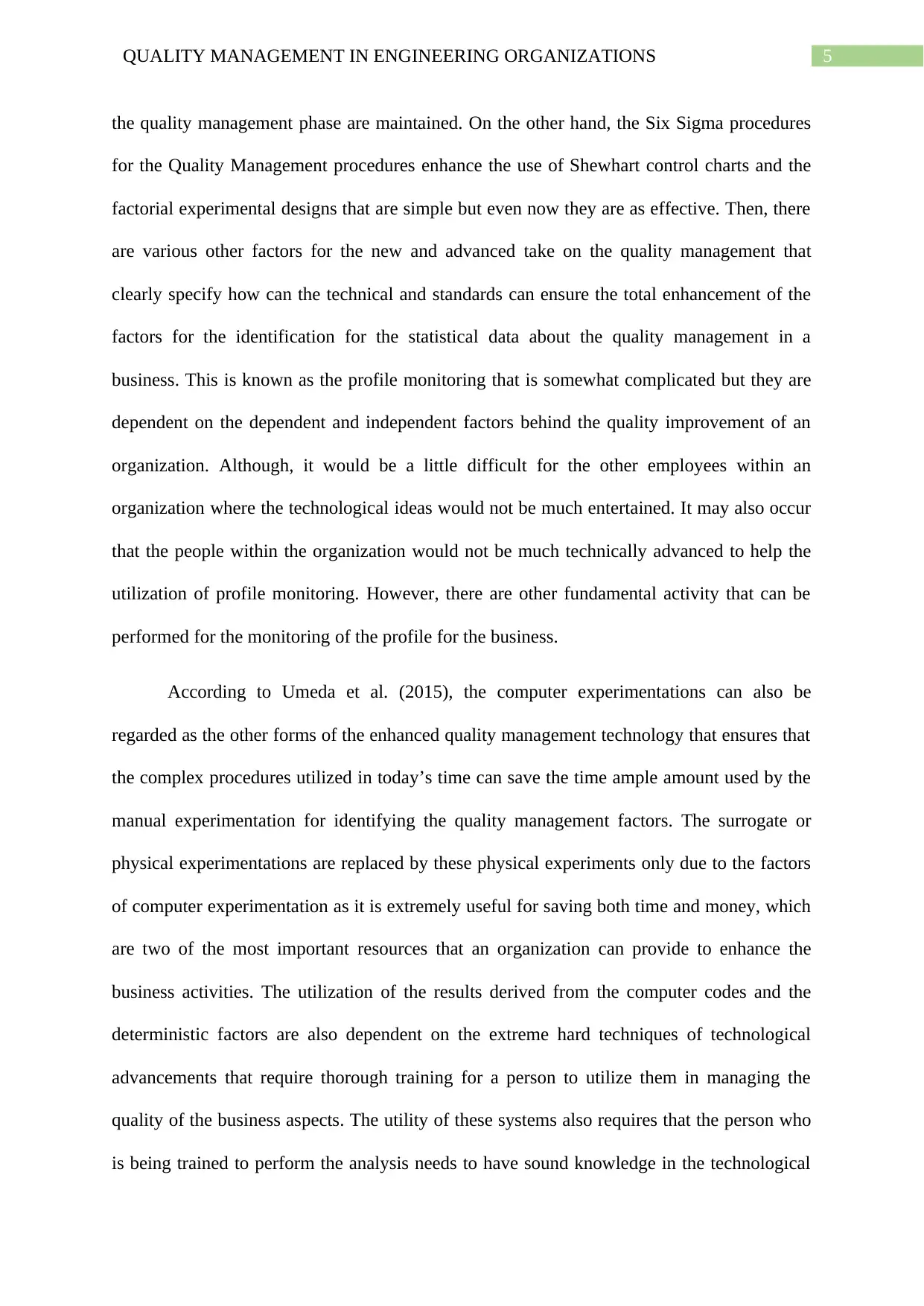
5QUALITY MANAGEMENT IN ENGINEERING ORGANIZATIONS
the quality management phase are maintained. On the other hand, the Six Sigma procedures
for the Quality Management procedures enhance the use of Shewhart control charts and the
factorial experimental designs that are simple but even now they are as effective. Then, there
are various other factors for the new and advanced take on the quality management that
clearly specify how can the technical and standards can ensure the total enhancement of the
factors for the identification for the statistical data about the quality management in a
business. This is known as the profile monitoring that is somewhat complicated but they are
dependent on the dependent and independent factors behind the quality improvement of an
organization. Although, it would be a little difficult for the other employees within an
organization where the technological ideas would not be much entertained. It may also occur
that the people within the organization would not be much technically advanced to help the
utilization of profile monitoring. However, there are other fundamental activity that can be
performed for the monitoring of the profile for the business.
According to Umeda et al. (2015), the computer experimentations can also be
regarded as the other forms of the enhanced quality management technology that ensures that
the complex procedures utilized in today’s time can save the time ample amount used by the
manual experimentation for identifying the quality management factors. The surrogate or
physical experimentations are replaced by these physical experiments only due to the factors
of computer experimentation as it is extremely useful for saving both time and money, which
are two of the most important resources that an organization can provide to enhance the
business activities. The utilization of the results derived from the computer codes and the
deterministic factors are also dependent on the extreme hard techniques of technological
advancements that require thorough training for a person to utilize them in managing the
quality of the business aspects. The utility of these systems also requires that the person who
is being trained to perform the analysis needs to have sound knowledge in the technological
the quality management phase are maintained. On the other hand, the Six Sigma procedures
for the Quality Management procedures enhance the use of Shewhart control charts and the
factorial experimental designs that are simple but even now they are as effective. Then, there
are various other factors for the new and advanced take on the quality management that
clearly specify how can the technical and standards can ensure the total enhancement of the
factors for the identification for the statistical data about the quality management in a
business. This is known as the profile monitoring that is somewhat complicated but they are
dependent on the dependent and independent factors behind the quality improvement of an
organization. Although, it would be a little difficult for the other employees within an
organization where the technological ideas would not be much entertained. It may also occur
that the people within the organization would not be much technically advanced to help the
utilization of profile monitoring. However, there are other fundamental activity that can be
performed for the monitoring of the profile for the business.
According to Umeda et al. (2015), the computer experimentations can also be
regarded as the other forms of the enhanced quality management technology that ensures that
the complex procedures utilized in today’s time can save the time ample amount used by the
manual experimentation for identifying the quality management factors. The surrogate or
physical experimentations are replaced by these physical experiments only due to the factors
of computer experimentation as it is extremely useful for saving both time and money, which
are two of the most important resources that an organization can provide to enhance the
business activities. The utilization of the results derived from the computer codes and the
deterministic factors are also dependent on the extreme hard techniques of technological
advancements that require thorough training for a person to utilize them in managing the
quality of the business aspects. The utility of these systems also requires that the person who
is being trained to perform the analysis needs to have sound knowledge in the technological
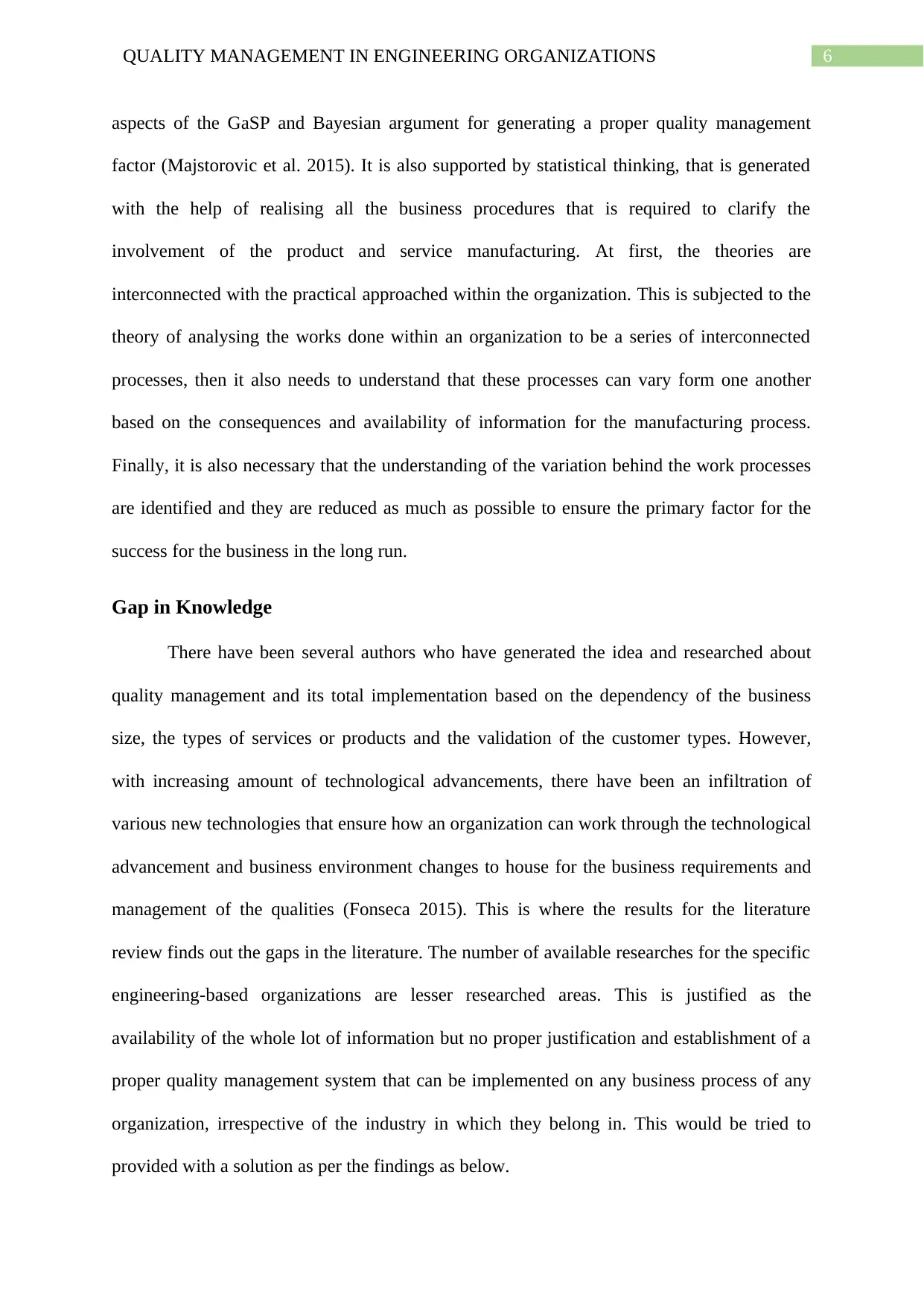
6QUALITY MANAGEMENT IN ENGINEERING ORGANIZATIONS
aspects of the GaSP and Bayesian argument for generating a proper quality management
factor (Majstorovic et al. 2015). It is also supported by statistical thinking, that is generated
with the help of realising all the business procedures that is required to clarify the
involvement of the product and service manufacturing. At first, the theories are
interconnected with the practical approached within the organization. This is subjected to the
theory of analysing the works done within an organization to be a series of interconnected
processes, then it also needs to understand that these processes can vary form one another
based on the consequences and availability of information for the manufacturing process.
Finally, it is also necessary that the understanding of the variation behind the work processes
are identified and they are reduced as much as possible to ensure the primary factor for the
success for the business in the long run.
Gap in Knowledge
There have been several authors who have generated the idea and researched about
quality management and its total implementation based on the dependency of the business
size, the types of services or products and the validation of the customer types. However,
with increasing amount of technological advancements, there have been an infiltration of
various new technologies that ensure how an organization can work through the technological
advancement and business environment changes to house for the business requirements and
management of the qualities (Fonseca 2015). This is where the results for the literature
review finds out the gaps in the literature. The number of available researches for the specific
engineering-based organizations are lesser researched areas. This is justified as the
availability of the whole lot of information but no proper justification and establishment of a
proper quality management system that can be implemented on any business process of any
organization, irrespective of the industry in which they belong in. This would be tried to
provided with a solution as per the findings as below.
aspects of the GaSP and Bayesian argument for generating a proper quality management
factor (Majstorovic et al. 2015). It is also supported by statistical thinking, that is generated
with the help of realising all the business procedures that is required to clarify the
involvement of the product and service manufacturing. At first, the theories are
interconnected with the practical approached within the organization. This is subjected to the
theory of analysing the works done within an organization to be a series of interconnected
processes, then it also needs to understand that these processes can vary form one another
based on the consequences and availability of information for the manufacturing process.
Finally, it is also necessary that the understanding of the variation behind the work processes
are identified and they are reduced as much as possible to ensure the primary factor for the
success for the business in the long run.
Gap in Knowledge
There have been several authors who have generated the idea and researched about
quality management and its total implementation based on the dependency of the business
size, the types of services or products and the validation of the customer types. However,
with increasing amount of technological advancements, there have been an infiltration of
various new technologies that ensure how an organization can work through the technological
advancement and business environment changes to house for the business requirements and
management of the qualities (Fonseca 2015). This is where the results for the literature
review finds out the gaps in the literature. The number of available researches for the specific
engineering-based organizations are lesser researched areas. This is justified as the
availability of the whole lot of information but no proper justification and establishment of a
proper quality management system that can be implemented on any business process of any
organization, irrespective of the industry in which they belong in. This would be tried to
provided with a solution as per the findings as below.
Paraphrase This Document
Need a fresh take? Get an instant paraphrase of this document with our AI Paraphraser
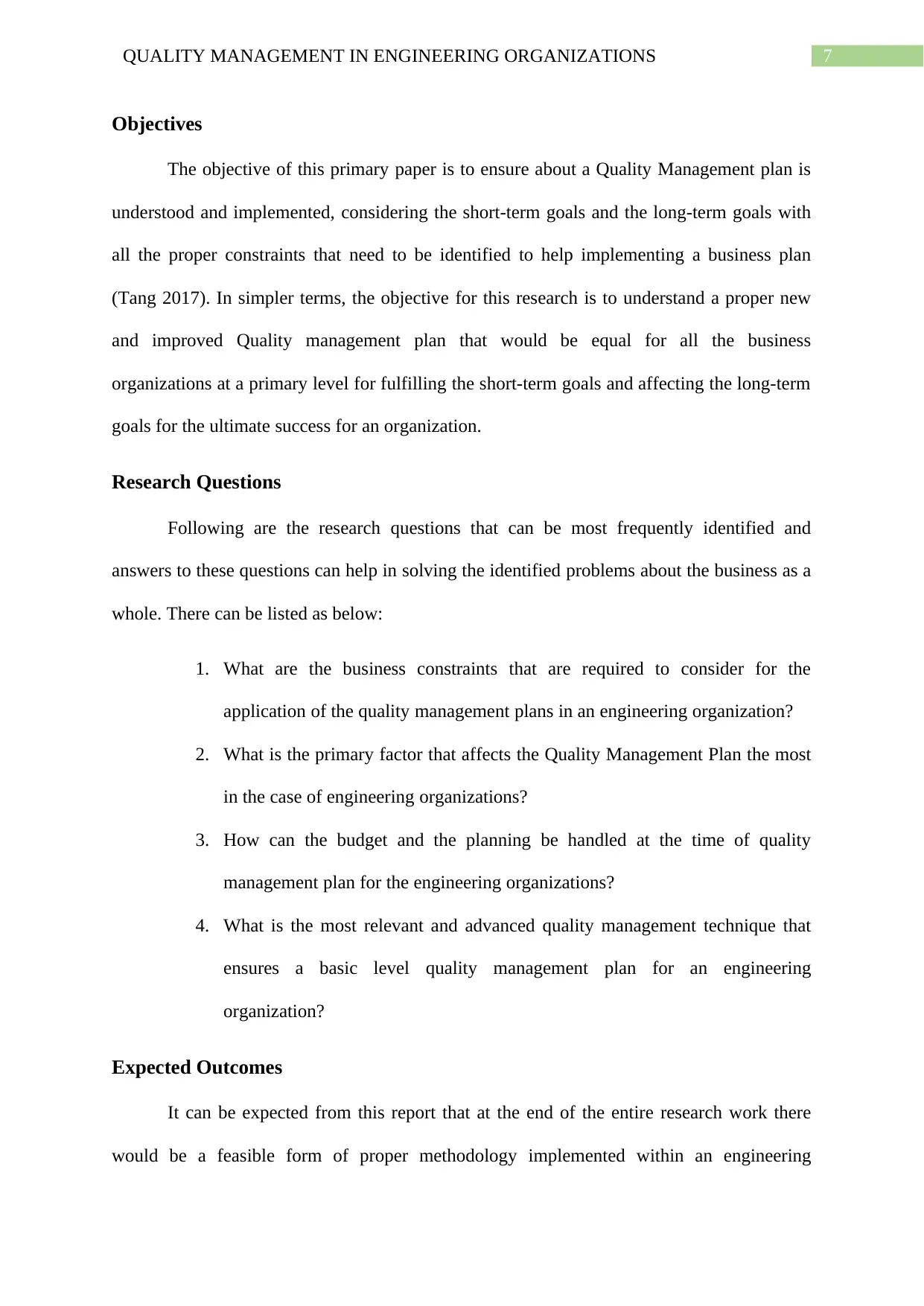
7QUALITY MANAGEMENT IN ENGINEERING ORGANIZATIONS
Objectives
The objective of this primary paper is to ensure about a Quality Management plan is
understood and implemented, considering the short-term goals and the long-term goals with
all the proper constraints that need to be identified to help implementing a business plan
(Tang 2017). In simpler terms, the objective for this research is to understand a proper new
and improved Quality management plan that would be equal for all the business
organizations at a primary level for fulfilling the short-term goals and affecting the long-term
goals for the ultimate success for an organization.
Research Questions
Following are the research questions that can be most frequently identified and
answers to these questions can help in solving the identified problems about the business as a
whole. There can be listed as below:
1. What are the business constraints that are required to consider for the
application of the quality management plans in an engineering organization?
2. What is the primary factor that affects the Quality Management Plan the most
in the case of engineering organizations?
3. How can the budget and the planning be handled at the time of quality
management plan for the engineering organizations?
4. What is the most relevant and advanced quality management technique that
ensures a basic level quality management plan for an engineering
organization?
Expected Outcomes
It can be expected from this report that at the end of the entire research work there
would be a feasible form of proper methodology implemented within an engineering
Objectives
The objective of this primary paper is to ensure about a Quality Management plan is
understood and implemented, considering the short-term goals and the long-term goals with
all the proper constraints that need to be identified to help implementing a business plan
(Tang 2017). In simpler terms, the objective for this research is to understand a proper new
and improved Quality management plan that would be equal for all the business
organizations at a primary level for fulfilling the short-term goals and affecting the long-term
goals for the ultimate success for an organization.
Research Questions
Following are the research questions that can be most frequently identified and
answers to these questions can help in solving the identified problems about the business as a
whole. There can be listed as below:
1. What are the business constraints that are required to consider for the
application of the quality management plans in an engineering organization?
2. What is the primary factor that affects the Quality Management Plan the most
in the case of engineering organizations?
3. How can the budget and the planning be handled at the time of quality
management plan for the engineering organizations?
4. What is the most relevant and advanced quality management technique that
ensures a basic level quality management plan for an engineering
organization?
Expected Outcomes
It can be expected from this report that at the end of the entire research work there
would be a feasible form of proper methodology implemented within an engineering
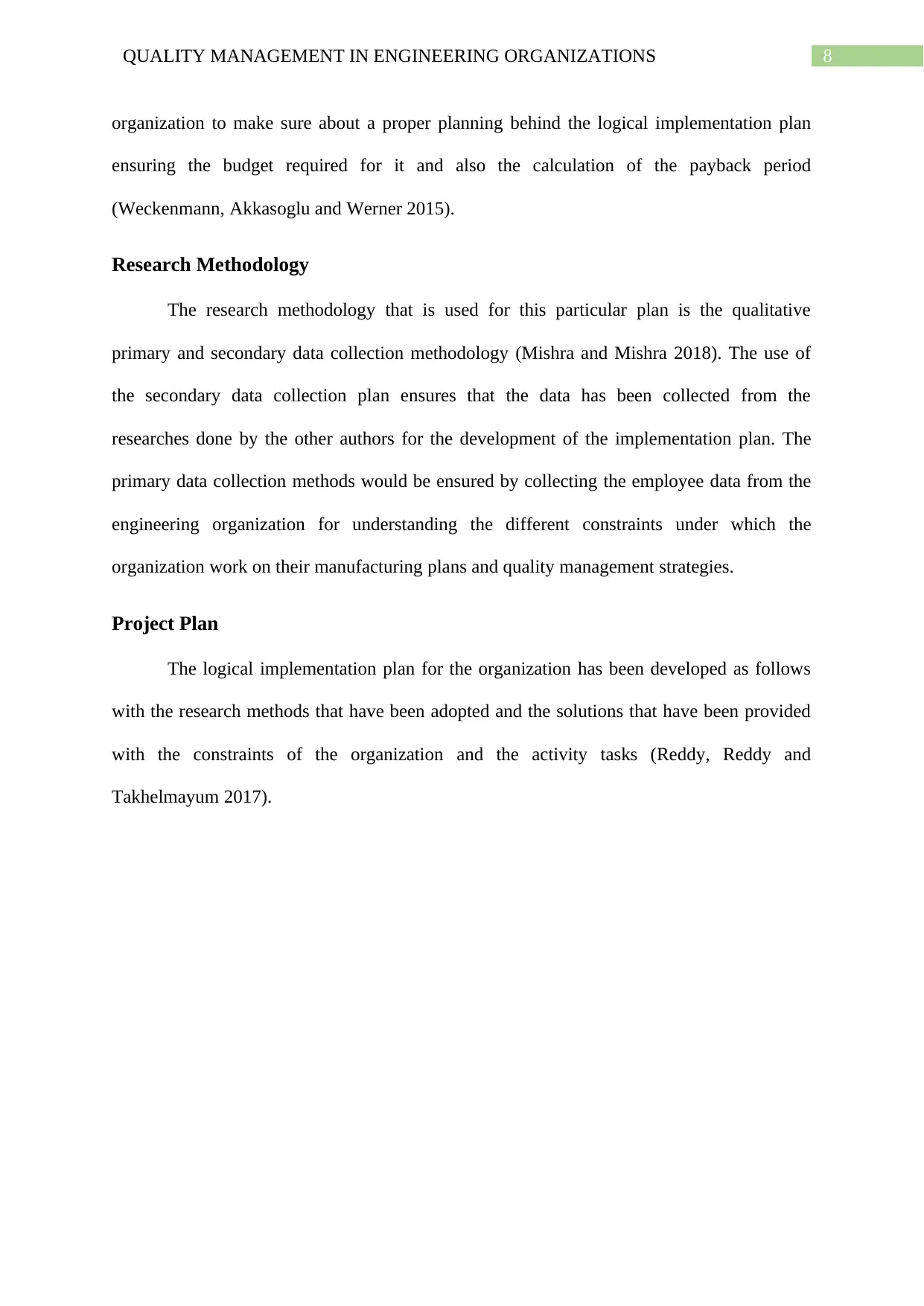
8QUALITY MANAGEMENT IN ENGINEERING ORGANIZATIONS
organization to make sure about a proper planning behind the logical implementation plan
ensuring the budget required for it and also the calculation of the payback period
(Weckenmann, Akkasoglu and Werner 2015).
Research Methodology
The research methodology that is used for this particular plan is the qualitative
primary and secondary data collection methodology (Mishra and Mishra 2018). The use of
the secondary data collection plan ensures that the data has been collected from the
researches done by the other authors for the development of the implementation plan. The
primary data collection methods would be ensured by collecting the employee data from the
engineering organization for understanding the different constraints under which the
organization work on their manufacturing plans and quality management strategies.
Project Plan
The logical implementation plan for the organization has been developed as follows
with the research methods that have been adopted and the solutions that have been provided
with the constraints of the organization and the activity tasks (Reddy, Reddy and
Takhelmayum 2017).
organization to make sure about a proper planning behind the logical implementation plan
ensuring the budget required for it and also the calculation of the payback period
(Weckenmann, Akkasoglu and Werner 2015).
Research Methodology
The research methodology that is used for this particular plan is the qualitative
primary and secondary data collection methodology (Mishra and Mishra 2018). The use of
the secondary data collection plan ensures that the data has been collected from the
researches done by the other authors for the development of the implementation plan. The
primary data collection methods would be ensured by collecting the employee data from the
engineering organization for understanding the different constraints under which the
organization work on their manufacturing plans and quality management strategies.
Project Plan
The logical implementation plan for the organization has been developed as follows
with the research methods that have been adopted and the solutions that have been provided
with the constraints of the organization and the activity tasks (Reddy, Reddy and
Takhelmayum 2017).
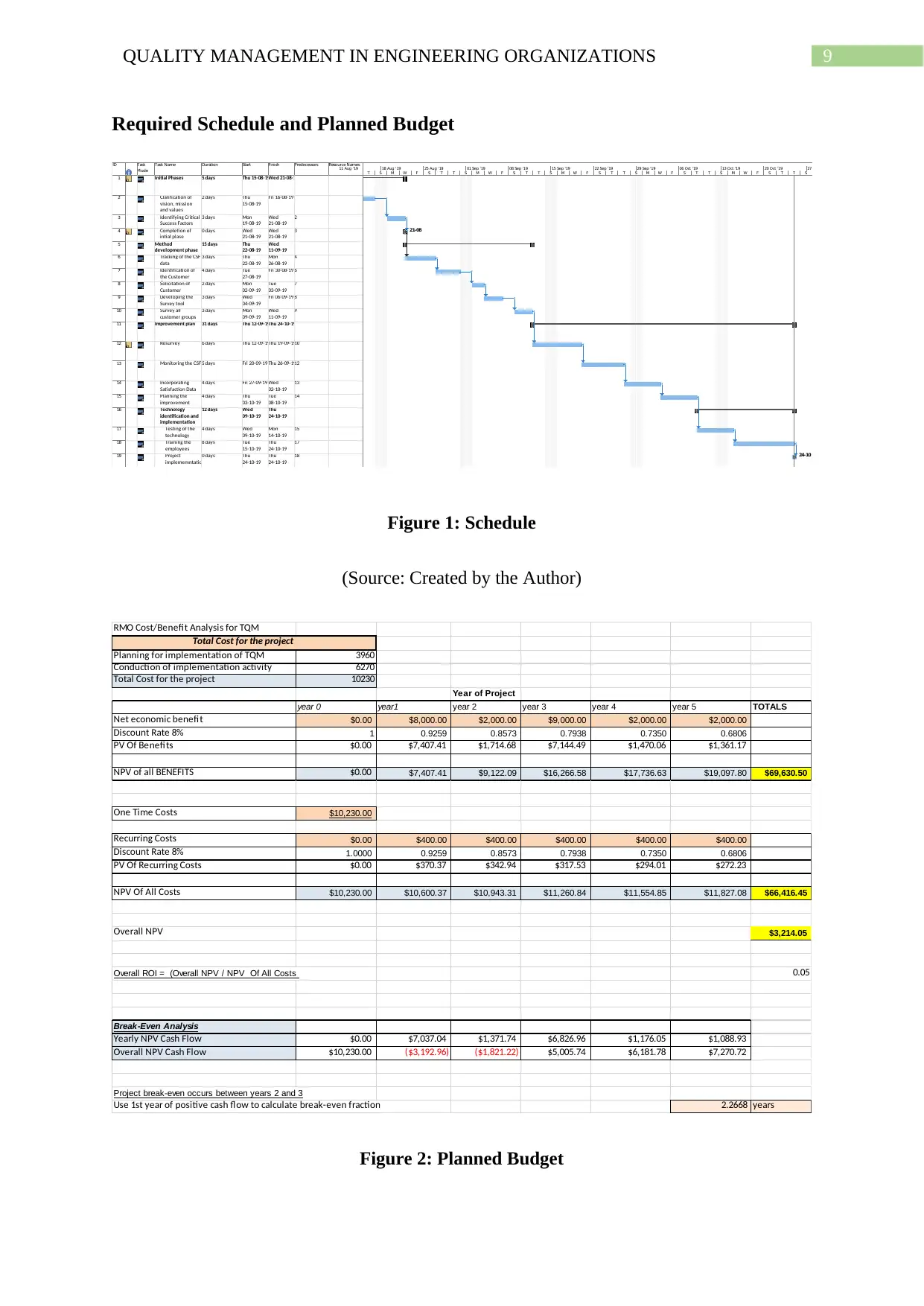
9QUALITY MANAGEMENT IN ENGINEERING ORGANIZATIONS
Required Schedule and Planned Budget
Figure 1: Schedule
(Source: Created by the Author)
RMO Cost/Benefit Analysis for TQM
Planning for implementation of TQM 3960
Conduction of implementation activity 6270
Total Cost for the project 10230
Year of Project
year 0 year1 year 2 year 3 year 4 year 5 TOTALS
Net economic benefit $0.00 $8,000.00 $2,000.00 $9,000.00 $2,000.00 $2,000.00
Discount Rate 8% 1 0.9259 0.8573 0.7938 0.7350 0.6806
PV Of Benefits $0.00 $7,407.41 $1,714.68 $7,144.49 $1,470.06 $1,361.17
NPV of all BENEFITS $0.00 $7,407.41 $9,122.09 $16,266.58 $17,736.63 $19,097.80 $69,630.50
One Time Costs $10,230.00
Recurring Costs $0.00 $400.00 $400.00 $400.00 $400.00 $400.00
Discount Rate 8% 1.0000 0.9259 0.8573 0.7938 0.7350 0.6806
PV Of Recurring Costs $0.00 $370.37 $342.94 $317.53 $294.01 $272.23
NPV Of All Costs $10,230.00 $10,600.37 $10,943.31 $11,260.84 $11,554.85 $11,827.08 $66,416.45
Overall NPV $3,214.05
Overall ROI = (Overall NPV / NPV Of All Costs 0.05
Break-Even Analysis
Yearly NPV Cash Flow $0.00 $7,037.04 $1,371.74 $6,826.96 $1,176.05 $1,088.93
Overall NPV Cash Flow $10,230.00 ($3,192.96) ($1,821.22) $5,005.74 $6,181.78 $7,270.72
Project break-even occurs between years 2 and 3
Use 1st year of positive cash flow to calculate break-even fraction 2.2668 years
Total Cost for the project
Figure 2: Planned Budget
ID Task
Mode
Task Name Duration Start Finish Predecessors Resource Names
1 Initial Phases 5 days Thu 15-08-19Wed 21-08-19
2 Clarification of
vision, mission
and values
2 days Thu
15-08-19
Fri 16-08-19
3 Identifying Critical
Success Factors
3 days Mon
19-08-19
Wed
21-08-19
2
4 Completion of
intial plase
0 days Wed
21-08-19
Wed
21-08-19
3
5 Method
development phase
15 days Thu
22-08-19
Wed
11-09-19
6 Tracking of the CSF
data
3 days Thu
22-08-19
Mon
26-08-19
4
7 Identification of
the Customer
Group
4 days Tue
27-08-19
Fri 30-08-19 6
8 Solicitation of
Customer
Feedback
2 days Mon
02-09-19
Tue
03-09-19
7
9 Developing the
Survey tool
3 days Wed
04-09-19
Fri 06-09-19 8
10 Survey all
customer groups
3 days Mon
09-09-19
Wed
11-09-19
9
11 Improvement plan 31 days Thu 12-09-19Thu 24-10-19
12 Resurvey 6 days Thu 12-09-19Thu 19-09-1910
13 Monitoring the CSF 5 days Fri 20-09-19 Thu 26-09-1912
14 Incorporating
Satisfaction Data
4 days Fri 27-09-19 Wed
02-10-19
13
15 Planning the
improvement
4 days Thu
03-10-19
Tue
08-10-19
14
16 Technology
identification and
implementation
12 days Wed
09-10-19
Thu
24-10-19
17 Testing of the
technology
4 days Wed
09-10-19
Mon
14-10-19
15
18 Training the
employees
8 days Tue
15-10-19
Thu
24-10-19
17
19 Project
implememntation
0 days Thu
24-10-19
Thu
24-10-19
18
21-08
24-10
T S M W F S T T S M W F S T T S M W F S T T S M W F S T T S M W F S T T S
11 Aug '19 18 Aug '19 25 Aug '19 01 Sep '19 08 Sep '19 15 Sep '19 22 Sep '19 29 Sep '19 06 Oct '19 13 Oct '19 20 Oct '19 27 Oct '19
Required Schedule and Planned Budget
Figure 1: Schedule
(Source: Created by the Author)
RMO Cost/Benefit Analysis for TQM
Planning for implementation of TQM 3960
Conduction of implementation activity 6270
Total Cost for the project 10230
Year of Project
year 0 year1 year 2 year 3 year 4 year 5 TOTALS
Net economic benefit $0.00 $8,000.00 $2,000.00 $9,000.00 $2,000.00 $2,000.00
Discount Rate 8% 1 0.9259 0.8573 0.7938 0.7350 0.6806
PV Of Benefits $0.00 $7,407.41 $1,714.68 $7,144.49 $1,470.06 $1,361.17
NPV of all BENEFITS $0.00 $7,407.41 $9,122.09 $16,266.58 $17,736.63 $19,097.80 $69,630.50
One Time Costs $10,230.00
Recurring Costs $0.00 $400.00 $400.00 $400.00 $400.00 $400.00
Discount Rate 8% 1.0000 0.9259 0.8573 0.7938 0.7350 0.6806
PV Of Recurring Costs $0.00 $370.37 $342.94 $317.53 $294.01 $272.23
NPV Of All Costs $10,230.00 $10,600.37 $10,943.31 $11,260.84 $11,554.85 $11,827.08 $66,416.45
Overall NPV $3,214.05
Overall ROI = (Overall NPV / NPV Of All Costs 0.05
Break-Even Analysis
Yearly NPV Cash Flow $0.00 $7,037.04 $1,371.74 $6,826.96 $1,176.05 $1,088.93
Overall NPV Cash Flow $10,230.00 ($3,192.96) ($1,821.22) $5,005.74 $6,181.78 $7,270.72
Project break-even occurs between years 2 and 3
Use 1st year of positive cash flow to calculate break-even fraction 2.2668 years
Total Cost for the project
Figure 2: Planned Budget
ID Task
Mode
Task Name Duration Start Finish Predecessors Resource Names
1 Initial Phases 5 days Thu 15-08-19Wed 21-08-19
2 Clarification of
vision, mission
and values
2 days Thu
15-08-19
Fri 16-08-19
3 Identifying Critical
Success Factors
3 days Mon
19-08-19
Wed
21-08-19
2
4 Completion of
intial plase
0 days Wed
21-08-19
Wed
21-08-19
3
5 Method
development phase
15 days Thu
22-08-19
Wed
11-09-19
6 Tracking of the CSF
data
3 days Thu
22-08-19
Mon
26-08-19
4
7 Identification of
the Customer
Group
4 days Tue
27-08-19
Fri 30-08-19 6
8 Solicitation of
Customer
Feedback
2 days Mon
02-09-19
Tue
03-09-19
7
9 Developing the
Survey tool
3 days Wed
04-09-19
Fri 06-09-19 8
10 Survey all
customer groups
3 days Mon
09-09-19
Wed
11-09-19
9
11 Improvement plan 31 days Thu 12-09-19Thu 24-10-19
12 Resurvey 6 days Thu 12-09-19Thu 19-09-1910
13 Monitoring the CSF 5 days Fri 20-09-19 Thu 26-09-1912
14 Incorporating
Satisfaction Data
4 days Fri 27-09-19 Wed
02-10-19
13
15 Planning the
improvement
4 days Thu
03-10-19
Tue
08-10-19
14
16 Technology
identification and
implementation
12 days Wed
09-10-19
Thu
24-10-19
17 Testing of the
technology
4 days Wed
09-10-19
Mon
14-10-19
15
18 Training the
employees
8 days Tue
15-10-19
Thu
24-10-19
17
19 Project
implememntation
0 days Thu
24-10-19
Thu
24-10-19
18
21-08
24-10
T S M W F S T T S M W F S T T S M W F S T T S M W F S T T S M W F S T T S
11 Aug '19 18 Aug '19 25 Aug '19 01 Sep '19 08 Sep '19 15 Sep '19 22 Sep '19 29 Sep '19 06 Oct '19 13 Oct '19 20 Oct '19 27 Oct '19
Secure Best Marks with AI Grader
Need help grading? Try our AI Grader for instant feedback on your assignments.
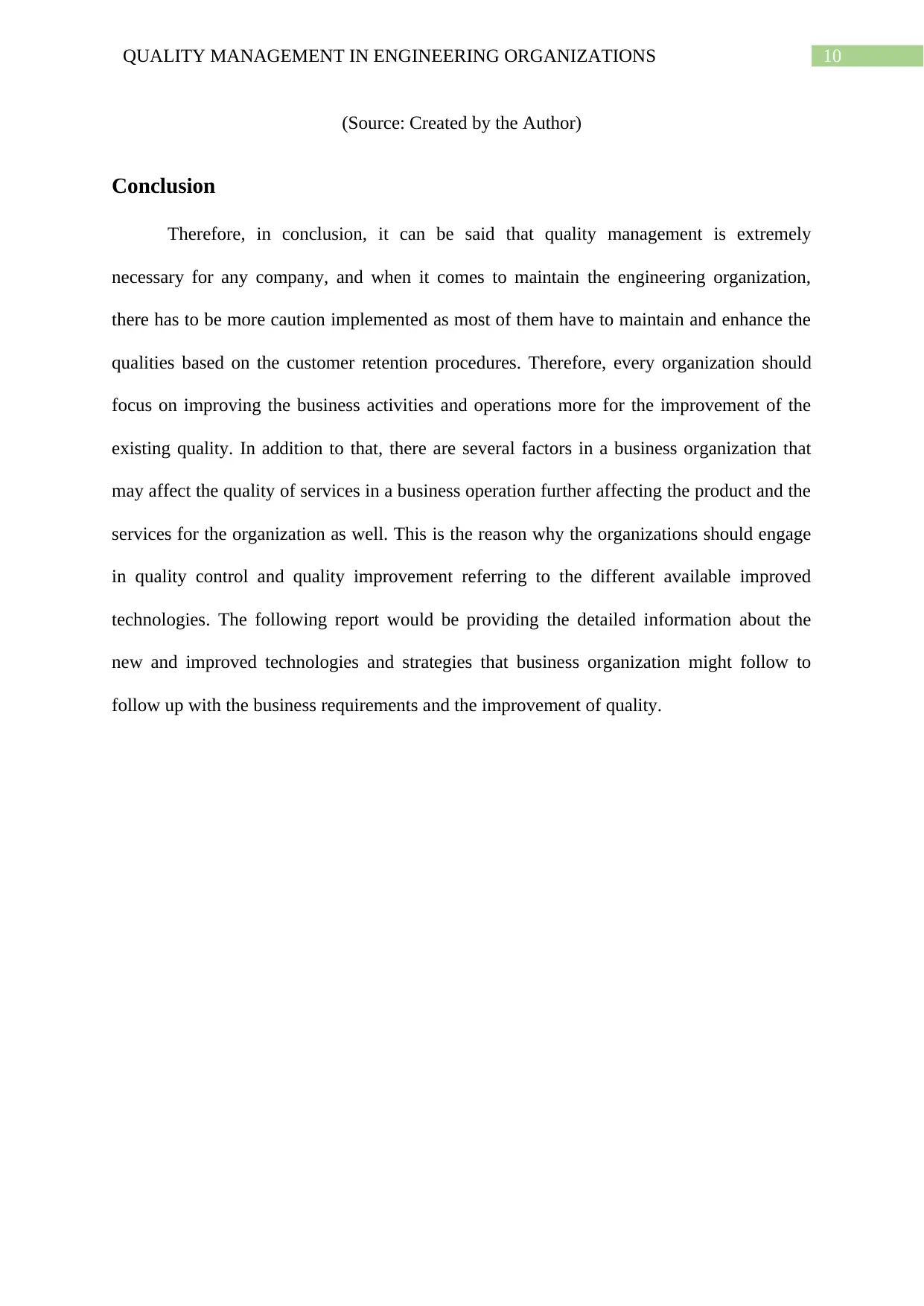
10QUALITY MANAGEMENT IN ENGINEERING ORGANIZATIONS
(Source: Created by the Author)
Conclusion
Therefore, in conclusion, it can be said that quality management is extremely
necessary for any company, and when it comes to maintain the engineering organization,
there has to be more caution implemented as most of them have to maintain and enhance the
qualities based on the customer retention procedures. Therefore, every organization should
focus on improving the business activities and operations more for the improvement of the
existing quality. In addition to that, there are several factors in a business organization that
may affect the quality of services in a business operation further affecting the product and the
services for the organization as well. This is the reason why the organizations should engage
in quality control and quality improvement referring to the different available improved
technologies. The following report would be providing the detailed information about the
new and improved technologies and strategies that business organization might follow to
follow up with the business requirements and the improvement of quality.
(Source: Created by the Author)
Conclusion
Therefore, in conclusion, it can be said that quality management is extremely
necessary for any company, and when it comes to maintain the engineering organization,
there has to be more caution implemented as most of them have to maintain and enhance the
qualities based on the customer retention procedures. Therefore, every organization should
focus on improving the business activities and operations more for the improvement of the
existing quality. In addition to that, there are several factors in a business organization that
may affect the quality of services in a business operation further affecting the product and the
services for the organization as well. This is the reason why the organizations should engage
in quality control and quality improvement referring to the different available improved
technologies. The following report would be providing the detailed information about the
new and improved technologies and strategies that business organization might follow to
follow up with the business requirements and the improvement of quality.
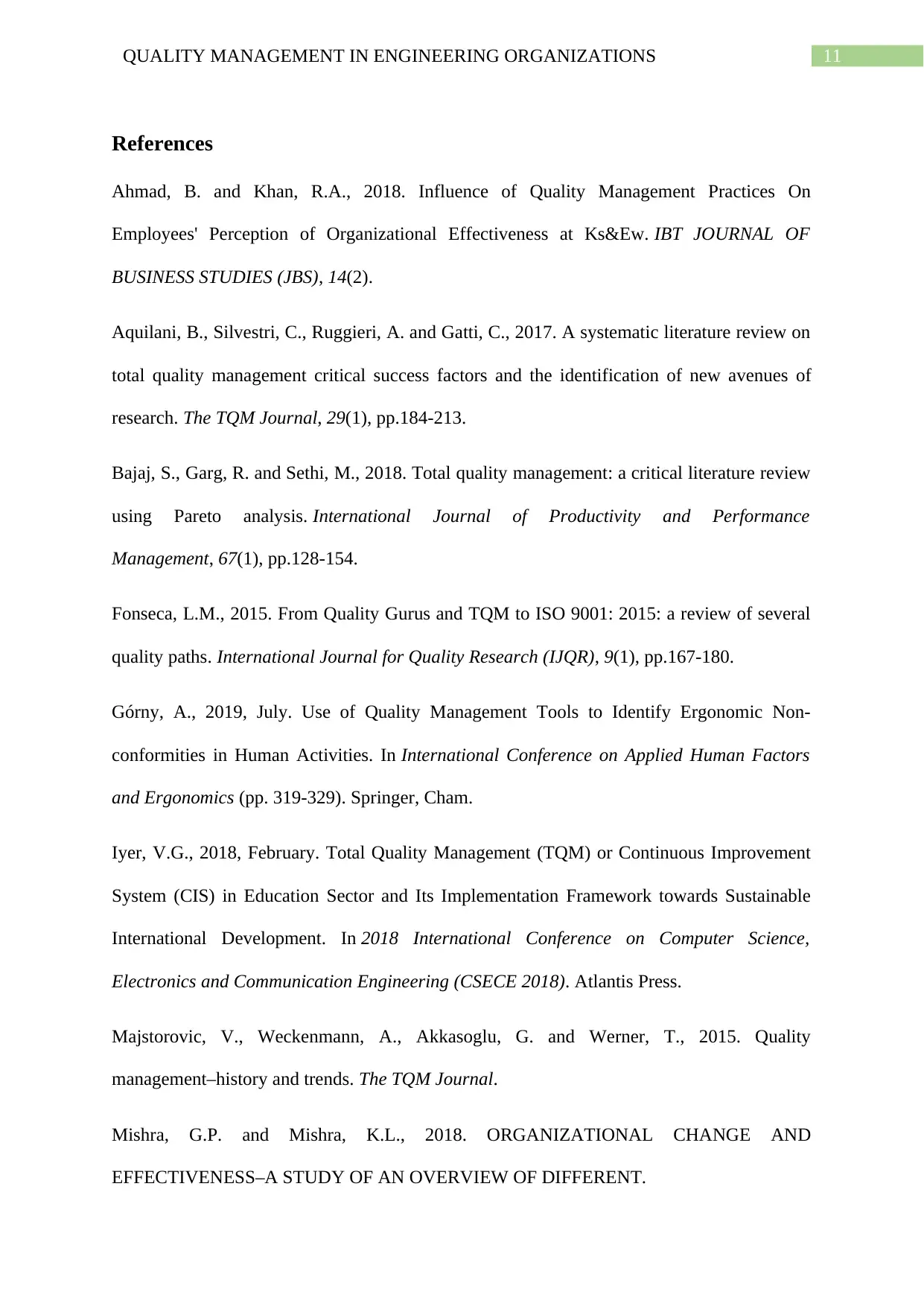
11QUALITY MANAGEMENT IN ENGINEERING ORGANIZATIONS
References
Ahmad, B. and Khan, R.A., 2018. Influence of Quality Management Practices On
Employees' Perception of Organizational Effectiveness at Ks&Ew. IBT JOURNAL OF
BUSINESS STUDIES (JBS), 14(2).
Aquilani, B., Silvestri, C., Ruggieri, A. and Gatti, C., 2017. A systematic literature review on
total quality management critical success factors and the identification of new avenues of
research. The TQM Journal, 29(1), pp.184-213.
Bajaj, S., Garg, R. and Sethi, M., 2018. Total quality management: a critical literature review
using Pareto analysis. International Journal of Productivity and Performance
Management, 67(1), pp.128-154.
Fonseca, L.M., 2015. From Quality Gurus and TQM to ISO 9001: 2015: a review of several
quality paths. International Journal for Quality Research (IJQR), 9(1), pp.167-180.
Górny, A., 2019, July. Use of Quality Management Tools to Identify Ergonomic Non-
conformities in Human Activities. In International Conference on Applied Human Factors
and Ergonomics (pp. 319-329). Springer, Cham.
Iyer, V.G., 2018, February. Total Quality Management (TQM) or Continuous Improvement
System (CIS) in Education Sector and Its Implementation Framework towards Sustainable
International Development. In 2018 International Conference on Computer Science,
Electronics and Communication Engineering (CSECE 2018). Atlantis Press.
Majstorovic, V., Weckenmann, A., Akkasoglu, G. and Werner, T., 2015. Quality
management–history and trends. The TQM Journal.
Mishra, G.P. and Mishra, K.L., 2018. ORGANIZATIONAL CHANGE AND
EFFECTIVENESS–A STUDY OF AN OVERVIEW OF DIFFERENT.
References
Ahmad, B. and Khan, R.A., 2018. Influence of Quality Management Practices On
Employees' Perception of Organizational Effectiveness at Ks&Ew. IBT JOURNAL OF
BUSINESS STUDIES (JBS), 14(2).
Aquilani, B., Silvestri, C., Ruggieri, A. and Gatti, C., 2017. A systematic literature review on
total quality management critical success factors and the identification of new avenues of
research. The TQM Journal, 29(1), pp.184-213.
Bajaj, S., Garg, R. and Sethi, M., 2018. Total quality management: a critical literature review
using Pareto analysis. International Journal of Productivity and Performance
Management, 67(1), pp.128-154.
Fonseca, L.M., 2015. From Quality Gurus and TQM to ISO 9001: 2015: a review of several
quality paths. International Journal for Quality Research (IJQR), 9(1), pp.167-180.
Górny, A., 2019, July. Use of Quality Management Tools to Identify Ergonomic Non-
conformities in Human Activities. In International Conference on Applied Human Factors
and Ergonomics (pp. 319-329). Springer, Cham.
Iyer, V.G., 2018, February. Total Quality Management (TQM) or Continuous Improvement
System (CIS) in Education Sector and Its Implementation Framework towards Sustainable
International Development. In 2018 International Conference on Computer Science,
Electronics and Communication Engineering (CSECE 2018). Atlantis Press.
Majstorovic, V., Weckenmann, A., Akkasoglu, G. and Werner, T., 2015. Quality
management–history and trends. The TQM Journal.
Mishra, G.P. and Mishra, K.L., 2018. ORGANIZATIONAL CHANGE AND
EFFECTIVENESS–A STUDY OF AN OVERVIEW OF DIFFERENT.
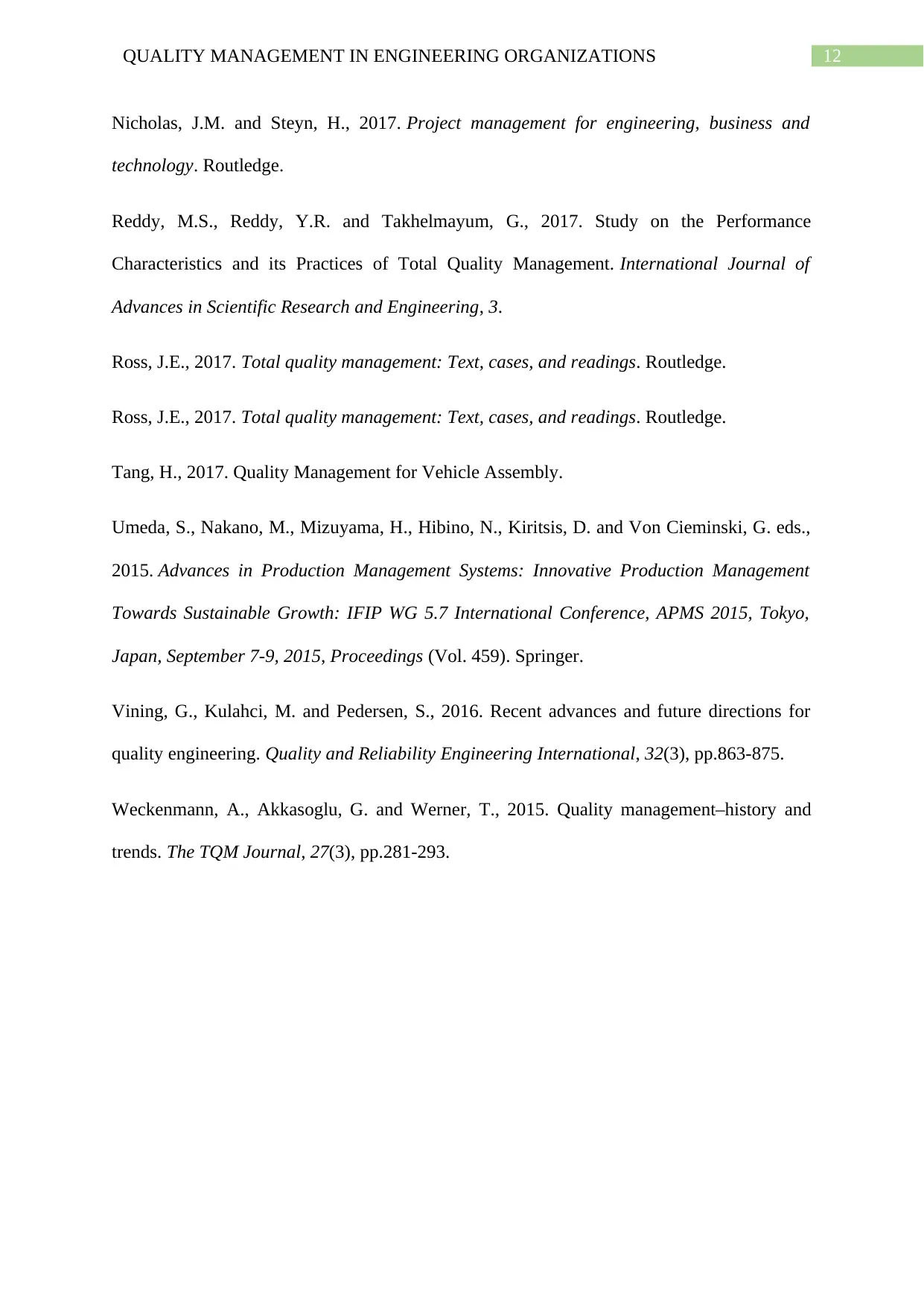
12QUALITY MANAGEMENT IN ENGINEERING ORGANIZATIONS
Nicholas, J.M. and Steyn, H., 2017. Project management for engineering, business and
technology. Routledge.
Reddy, M.S., Reddy, Y.R. and Takhelmayum, G., 2017. Study on the Performance
Characteristics and its Practices of Total Quality Management. International Journal of
Advances in Scientific Research and Engineering, 3.
Ross, J.E., 2017. Total quality management: Text, cases, and readings. Routledge.
Ross, J.E., 2017. Total quality management: Text, cases, and readings. Routledge.
Tang, H., 2017. Quality Management for Vehicle Assembly.
Umeda, S., Nakano, M., Mizuyama, H., Hibino, N., Kiritsis, D. and Von Cieminski, G. eds.,
2015. Advances in Production Management Systems: Innovative Production Management
Towards Sustainable Growth: IFIP WG 5.7 International Conference, APMS 2015, Tokyo,
Japan, September 7-9, 2015, Proceedings (Vol. 459). Springer.
Vining, G., Kulahci, M. and Pedersen, S., 2016. Recent advances and future directions for
quality engineering. Quality and Reliability Engineering International, 32(3), pp.863-875.
Weckenmann, A., Akkasoglu, G. and Werner, T., 2015. Quality management–history and
trends. The TQM Journal, 27(3), pp.281-293.
Nicholas, J.M. and Steyn, H., 2017. Project management for engineering, business and
technology. Routledge.
Reddy, M.S., Reddy, Y.R. and Takhelmayum, G., 2017. Study on the Performance
Characteristics and its Practices of Total Quality Management. International Journal of
Advances in Scientific Research and Engineering, 3.
Ross, J.E., 2017. Total quality management: Text, cases, and readings. Routledge.
Ross, J.E., 2017. Total quality management: Text, cases, and readings. Routledge.
Tang, H., 2017. Quality Management for Vehicle Assembly.
Umeda, S., Nakano, M., Mizuyama, H., Hibino, N., Kiritsis, D. and Von Cieminski, G. eds.,
2015. Advances in Production Management Systems: Innovative Production Management
Towards Sustainable Growth: IFIP WG 5.7 International Conference, APMS 2015, Tokyo,
Japan, September 7-9, 2015, Proceedings (Vol. 459). Springer.
Vining, G., Kulahci, M. and Pedersen, S., 2016. Recent advances and future directions for
quality engineering. Quality and Reliability Engineering International, 32(3), pp.863-875.
Weckenmann, A., Akkasoglu, G. and Werner, T., 2015. Quality management–history and
trends. The TQM Journal, 27(3), pp.281-293.
1 out of 13
Related Documents
![[object Object]](/_next/image/?url=%2F_next%2Fstatic%2Fmedia%2Flogo.6d15ce61.png&w=640&q=75)
Your All-in-One AI-Powered Toolkit for Academic Success.
+13062052269
info@desklib.com
Available 24*7 on WhatsApp / Email
Unlock your academic potential
© 2024 | Zucol Services PVT LTD | All rights reserved.