Operations and Project Management Report on Sainsbury's: Review, Critique, and Improvement Plan
VerifiedAdded on 2023/06/07
|14
|4263
|358
AI Summary
This report focuses on the review, critique, and improvement plan of operations management principles in Sainsbury's. It includes the use of Six Sigma and Kaizen models, the Project Life Cycle (PLC), and recommendations for Lean production principles. The subject is Operations and Project Management, and the course code is OPMG2001. The college/university is not mentioned.
Contribute Materials
Your contribution can guide someone’s learning journey. Share your
documents today.
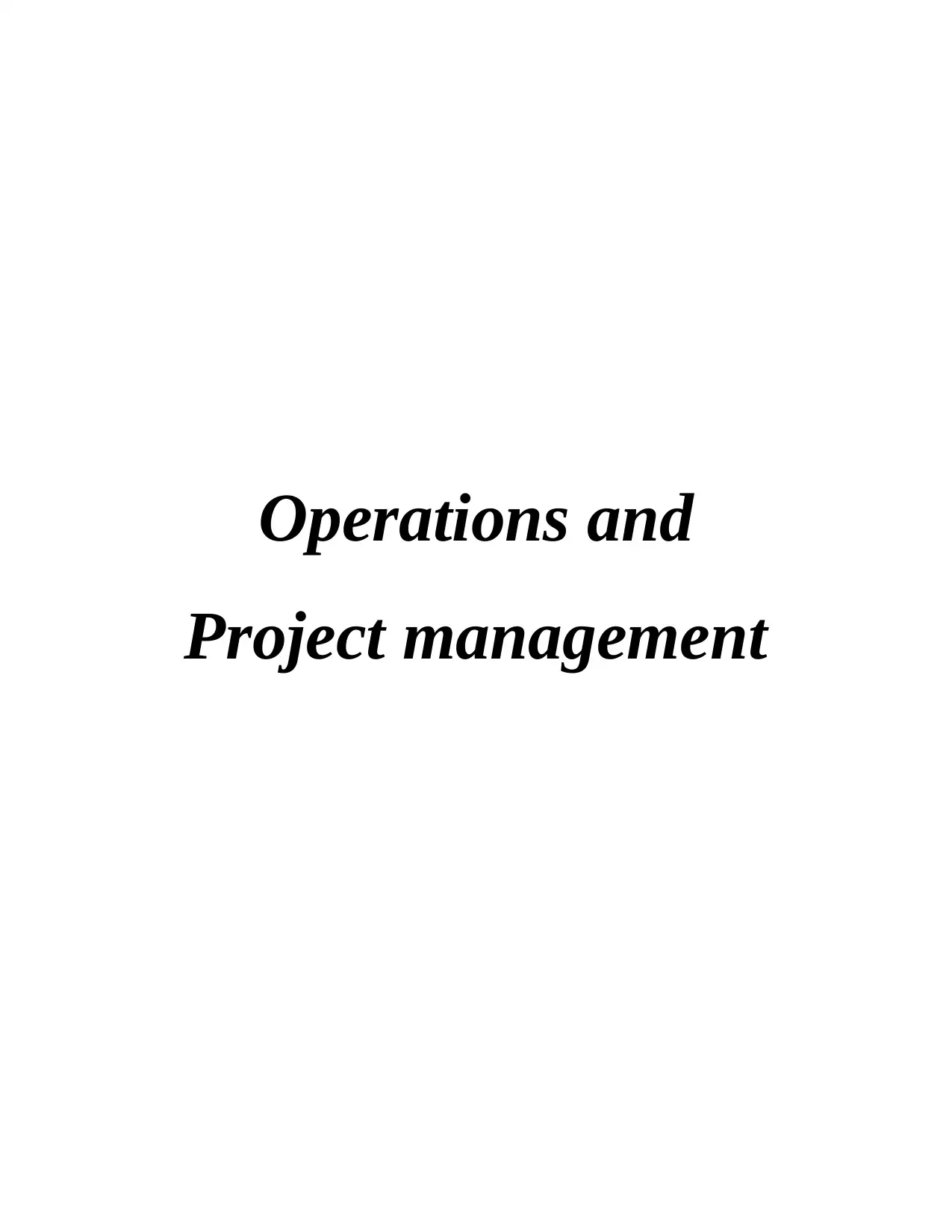
Operations and
Project management
Project management
Secure Best Marks with AI Grader
Need help grading? Try our AI Grader for instant feedback on your assignments.
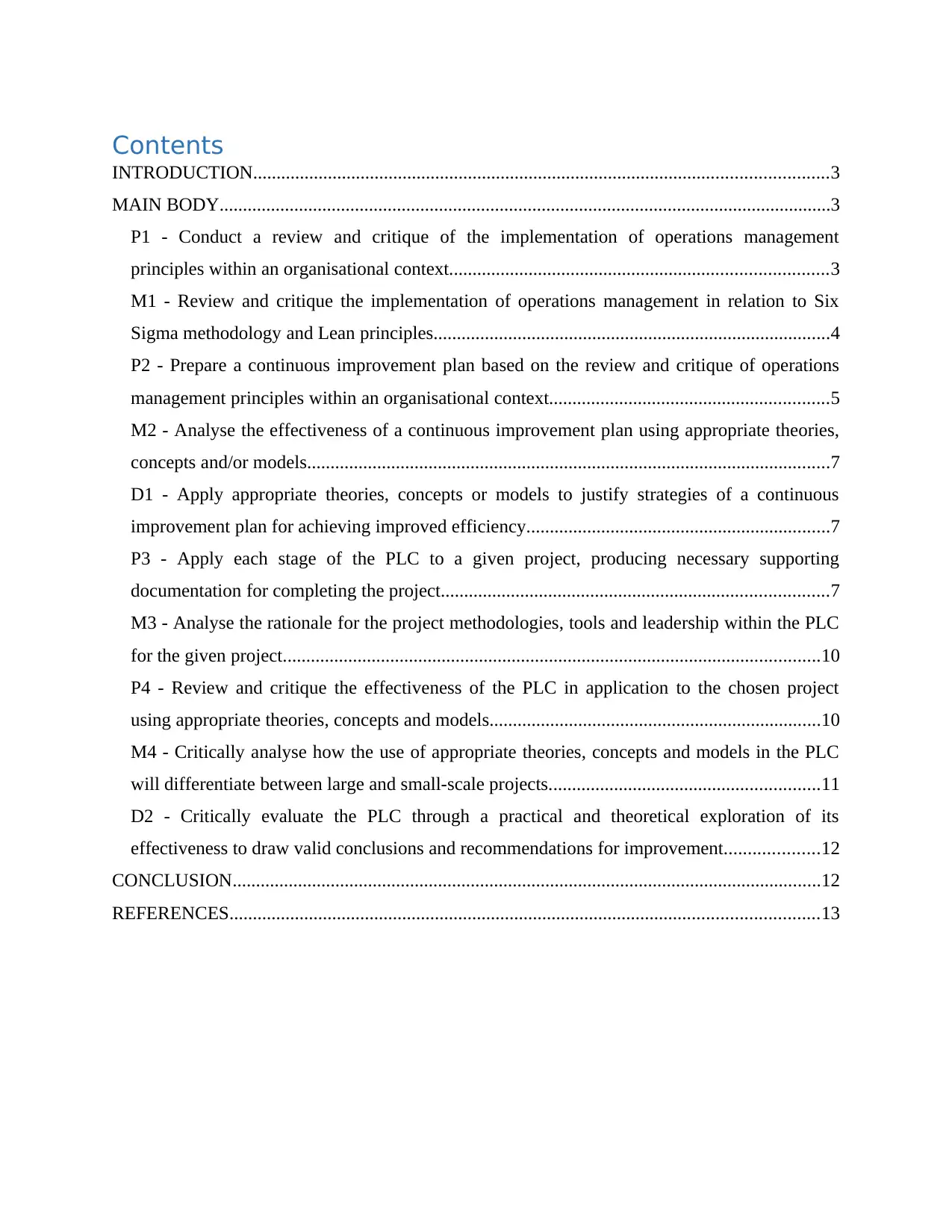
Contents
INTRODUCTION...........................................................................................................................3
MAIN BODY...................................................................................................................................3
P1 - Conduct a review and critique of the implementation of operations management
principles within an organisational context.................................................................................3
M1 - Review and critique the implementation of operations management in relation to Six
Sigma methodology and Lean principles.....................................................................................4
P2 - Prepare a continuous improvement plan based on the review and critique of operations
management principles within an organisational context............................................................5
M2 - Analyse the effectiveness of a continuous improvement plan using appropriate theories,
concepts and/or models................................................................................................................7
D1 - Apply appropriate theories, concepts or models to justify strategies of a continuous
improvement plan for achieving improved efficiency.................................................................7
P3 - Apply each stage of the PLC to a given project, producing necessary supporting
documentation for completing the project...................................................................................7
M3 - Analyse the rationale for the project methodologies, tools and leadership within the PLC
for the given project...................................................................................................................10
P4 - Review and critique the effectiveness of the PLC in application to the chosen project
using appropriate theories, concepts and models.......................................................................10
M4 - Critically analyse how the use of appropriate theories, concepts and models in the PLC
will differentiate between large and small-scale projects..........................................................11
D2 - Critically evaluate the PLC through a practical and theoretical exploration of its
effectiveness to draw valid conclusions and recommendations for improvement....................12
CONCLUSION..............................................................................................................................12
REFERENCES..............................................................................................................................13
INTRODUCTION...........................................................................................................................3
MAIN BODY...................................................................................................................................3
P1 - Conduct a review and critique of the implementation of operations management
principles within an organisational context.................................................................................3
M1 - Review and critique the implementation of operations management in relation to Six
Sigma methodology and Lean principles.....................................................................................4
P2 - Prepare a continuous improvement plan based on the review and critique of operations
management principles within an organisational context............................................................5
M2 - Analyse the effectiveness of a continuous improvement plan using appropriate theories,
concepts and/or models................................................................................................................7
D1 - Apply appropriate theories, concepts or models to justify strategies of a continuous
improvement plan for achieving improved efficiency.................................................................7
P3 - Apply each stage of the PLC to a given project, producing necessary supporting
documentation for completing the project...................................................................................7
M3 - Analyse the rationale for the project methodologies, tools and leadership within the PLC
for the given project...................................................................................................................10
P4 - Review and critique the effectiveness of the PLC in application to the chosen project
using appropriate theories, concepts and models.......................................................................10
M4 - Critically analyse how the use of appropriate theories, concepts and models in the PLC
will differentiate between large and small-scale projects..........................................................11
D2 - Critically evaluate the PLC through a practical and theoretical exploration of its
effectiveness to draw valid conclusions and recommendations for improvement....................12
CONCLUSION..............................................................................................................................12
REFERENCES..............................................................................................................................13
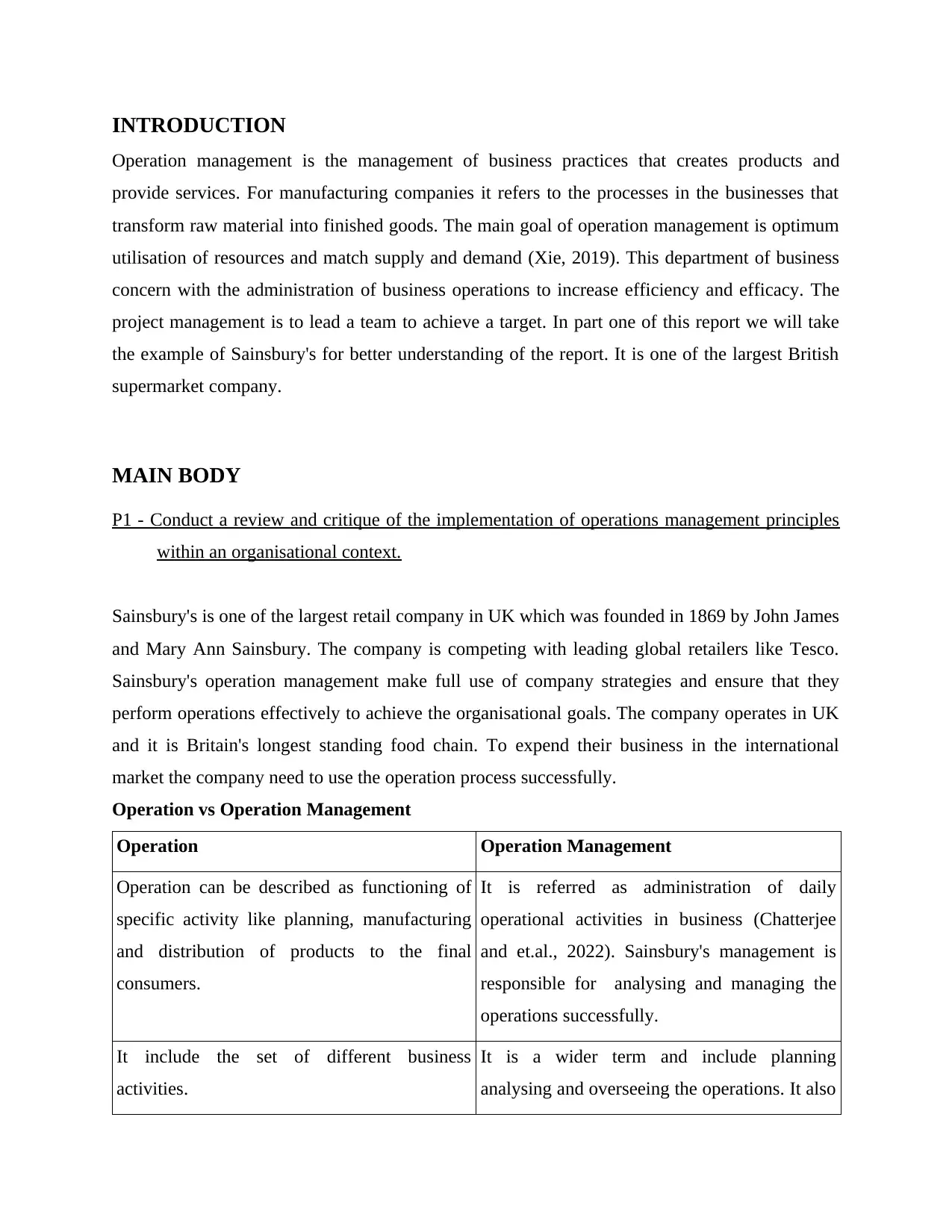
INTRODUCTION
Operation management is the management of business practices that creates products and
provide services. For manufacturing companies it refers to the processes in the businesses that
transform raw material into finished goods. The main goal of operation management is optimum
utilisation of resources and match supply and demand (Xie, 2019). This department of business
concern with the administration of business operations to increase efficiency and efficacy. The
project management is to lead a team to achieve a target. In part one of this report we will take
the example of Sainsbury's for better understanding of the report. It is one of the largest British
supermarket company.
MAIN BODY
P1 - Conduct a review and critique of the implementation of operations management principles
within an organisational context.
Sainsbury's is one of the largest retail company in UK which was founded in 1869 by John James
and Mary Ann Sainsbury. The company is competing with leading global retailers like Tesco.
Sainsbury's operation management make full use of company strategies and ensure that they
perform operations effectively to achieve the organisational goals. The company operates in UK
and it is Britain's longest standing food chain. To expend their business in the international
market the company need to use the operation process successfully.
Operation vs Operation Management
Operation Operation Management
Operation can be described as functioning of
specific activity like planning, manufacturing
and distribution of products to the final
consumers.
It is referred as administration of daily
operational activities in business (Chatterjee
and et.al., 2022). Sainsbury's management is
responsible for analysing and managing the
operations successfully.
It include the set of different business
activities.
It is a wider term and include planning
analysing and overseeing the operations. It also
Operation management is the management of business practices that creates products and
provide services. For manufacturing companies it refers to the processes in the businesses that
transform raw material into finished goods. The main goal of operation management is optimum
utilisation of resources and match supply and demand (Xie, 2019). This department of business
concern with the administration of business operations to increase efficiency and efficacy. The
project management is to lead a team to achieve a target. In part one of this report we will take
the example of Sainsbury's for better understanding of the report. It is one of the largest British
supermarket company.
MAIN BODY
P1 - Conduct a review and critique of the implementation of operations management principles
within an organisational context.
Sainsbury's is one of the largest retail company in UK which was founded in 1869 by John James
and Mary Ann Sainsbury. The company is competing with leading global retailers like Tesco.
Sainsbury's operation management make full use of company strategies and ensure that they
perform operations effectively to achieve the organisational goals. The company operates in UK
and it is Britain's longest standing food chain. To expend their business in the international
market the company need to use the operation process successfully.
Operation vs Operation Management
Operation Operation Management
Operation can be described as functioning of
specific activity like planning, manufacturing
and distribution of products to the final
consumers.
It is referred as administration of daily
operational activities in business (Chatterjee
and et.al., 2022). Sainsbury's management is
responsible for analysing and managing the
operations successfully.
It include the set of different business
activities.
It is a wider term and include planning
analysing and overseeing the operations. It also

include controlling process.
Employees are hired to perform operations. Managers are hired to carry out operational
management activities.
The organisations use different principles of operation management to create a effective and
efficient operation process in the organisation. The managers and workforce of the Sainsbury's
has to follow some important management principles mentioned below -
The first principle of management according to F.W. Taylor is that the management
should use the scientific analysis to take any decisions regarding business operations.
Taylor believed that even the smallest business activity can be planned scientifically
(Eichhorn and Towers, 2018). This principle also insist that managers must not make
decisions by their personal judgement.
Taylor believed that their should be harmony between employees and management in
organisation. If management and workers will understand each others perspective than
the organisation can create an efficient operational process.
For successful operation management it is important for Sainsbury's management team
to monitor the day to day operations carefully provide feedbacks and suggestions to
employees. This ensures that the company is using their resources effectively and
efficiently.
The company should assign tasks and responsibilities to the employees according to their
skills and knowledge. This increases employees motivation and employees are tend to
take challenges related to work.
M1 - Review and critique the implementation of operations management in relation to Six Sigma
methodology and Lean principles.
Operation management refers to the efficient use of the organisational resources like, workforce,
raw material and equipments increase efficiency and effectiveness in the operation. Operation
management helps business to guide and manage the main business activities. Sainsbury's
management team always tries to make optimum utilisation of resources to increase companies
Employees are hired to perform operations. Managers are hired to carry out operational
management activities.
The organisations use different principles of operation management to create a effective and
efficient operation process in the organisation. The managers and workforce of the Sainsbury's
has to follow some important management principles mentioned below -
The first principle of management according to F.W. Taylor is that the management
should use the scientific analysis to take any decisions regarding business operations.
Taylor believed that even the smallest business activity can be planned scientifically
(Eichhorn and Towers, 2018). This principle also insist that managers must not make
decisions by their personal judgement.
Taylor believed that their should be harmony between employees and management in
organisation. If management and workers will understand each others perspective than
the organisation can create an efficient operational process.
For successful operation management it is important for Sainsbury's management team
to monitor the day to day operations carefully provide feedbacks and suggestions to
employees. This ensures that the company is using their resources effectively and
efficiently.
The company should assign tasks and responsibilities to the employees according to their
skills and knowledge. This increases employees motivation and employees are tend to
take challenges related to work.
M1 - Review and critique the implementation of operations management in relation to Six Sigma
methodology and Lean principles.
Operation management refers to the efficient use of the organisational resources like, workforce,
raw material and equipments increase efficiency and effectiveness in the operation. Operation
management helps business to guide and manage the main business activities. Sainsbury's
management team always tries to make optimum utilisation of resources to increase companies
Secure Best Marks with AI Grader
Need help grading? Try our AI Grader for instant feedback on your assignments.
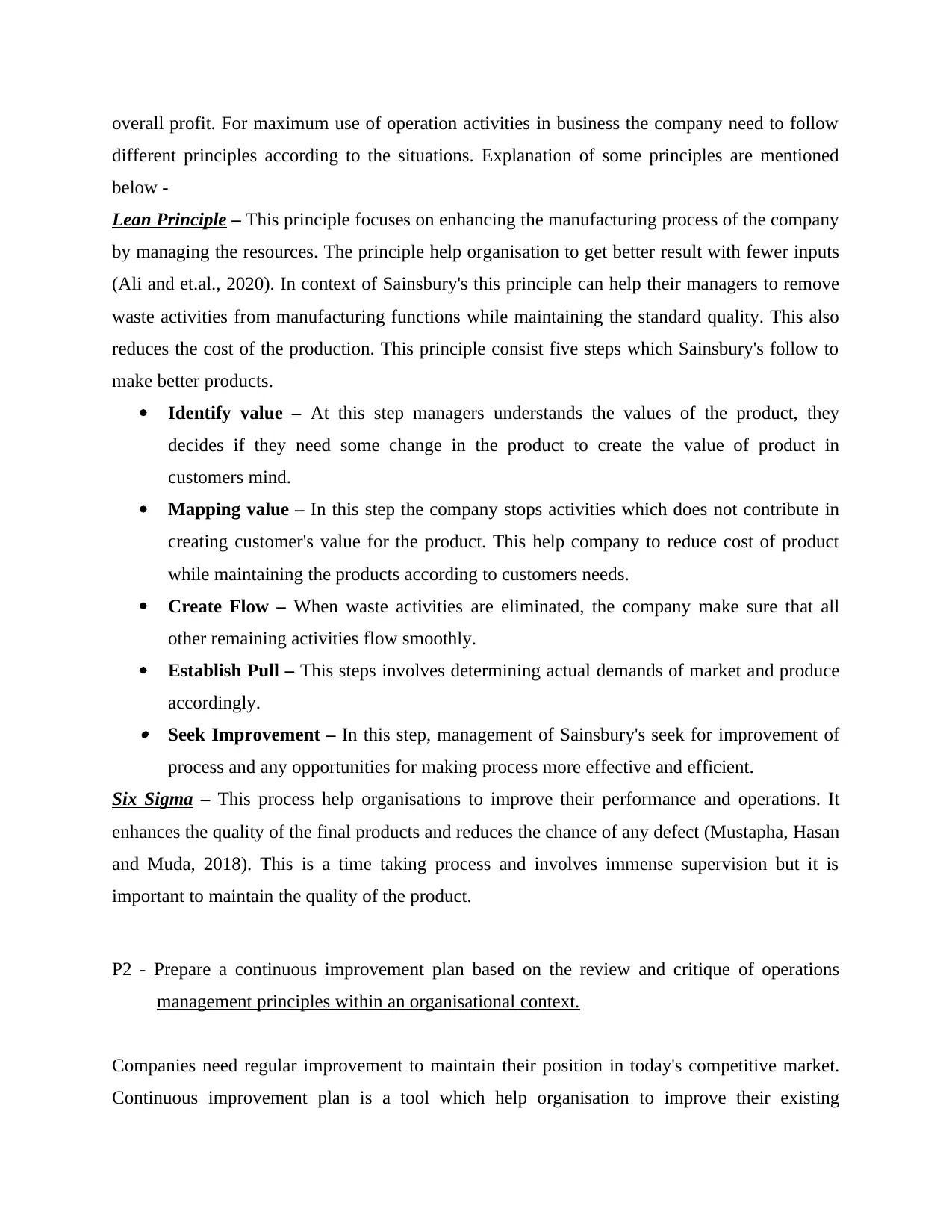
overall profit. For maximum use of operation activities in business the company need to follow
different principles according to the situations. Explanation of some principles are mentioned
below -
Lean Principle – This principle focuses on enhancing the manufacturing process of the company
by managing the resources. The principle help organisation to get better result with fewer inputs
(Ali and et.al., 2020). In context of Sainsbury's this principle can help their managers to remove
waste activities from manufacturing functions while maintaining the standard quality. This also
reduces the cost of the production. This principle consist five steps which Sainsbury's follow to
make better products.
Identify value – At this step managers understands the values of the product, they
decides if they need some change in the product to create the value of product in
customers mind.
Mapping value – In this step the company stops activities which does not contribute in
creating customer's value for the product. This help company to reduce cost of product
while maintaining the products according to customers needs.
Create Flow – When waste activities are eliminated, the company make sure that all
other remaining activities flow smoothly.
Establish Pull – This steps involves determining actual demands of market and produce
accordingly. Seek Improvement – In this step, management of Sainsbury's seek for improvement of
process and any opportunities for making process more effective and efficient.
Six Sigma – This process help organisations to improve their performance and operations. It
enhances the quality of the final products and reduces the chance of any defect (Mustapha, Hasan
and Muda, 2018). This is a time taking process and involves immense supervision but it is
important to maintain the quality of the product.
P2 - Prepare a continuous improvement plan based on the review and critique of operations
management principles within an organisational context.
Companies need regular improvement to maintain their position in today's competitive market.
Continuous improvement plan is a tool which help organisation to improve their existing
different principles according to the situations. Explanation of some principles are mentioned
below -
Lean Principle – This principle focuses on enhancing the manufacturing process of the company
by managing the resources. The principle help organisation to get better result with fewer inputs
(Ali and et.al., 2020). In context of Sainsbury's this principle can help their managers to remove
waste activities from manufacturing functions while maintaining the standard quality. This also
reduces the cost of the production. This principle consist five steps which Sainsbury's follow to
make better products.
Identify value – At this step managers understands the values of the product, they
decides if they need some change in the product to create the value of product in
customers mind.
Mapping value – In this step the company stops activities which does not contribute in
creating customer's value for the product. This help company to reduce cost of product
while maintaining the products according to customers needs.
Create Flow – When waste activities are eliminated, the company make sure that all
other remaining activities flow smoothly.
Establish Pull – This steps involves determining actual demands of market and produce
accordingly. Seek Improvement – In this step, management of Sainsbury's seek for improvement of
process and any opportunities for making process more effective and efficient.
Six Sigma – This process help organisations to improve their performance and operations. It
enhances the quality of the final products and reduces the chance of any defect (Mustapha, Hasan
and Muda, 2018). This is a time taking process and involves immense supervision but it is
important to maintain the quality of the product.
P2 - Prepare a continuous improvement plan based on the review and critique of operations
management principles within an organisational context.
Companies need regular improvement to maintain their position in today's competitive market.
Continuous improvement plan is a tool which help organisation to improve their existing
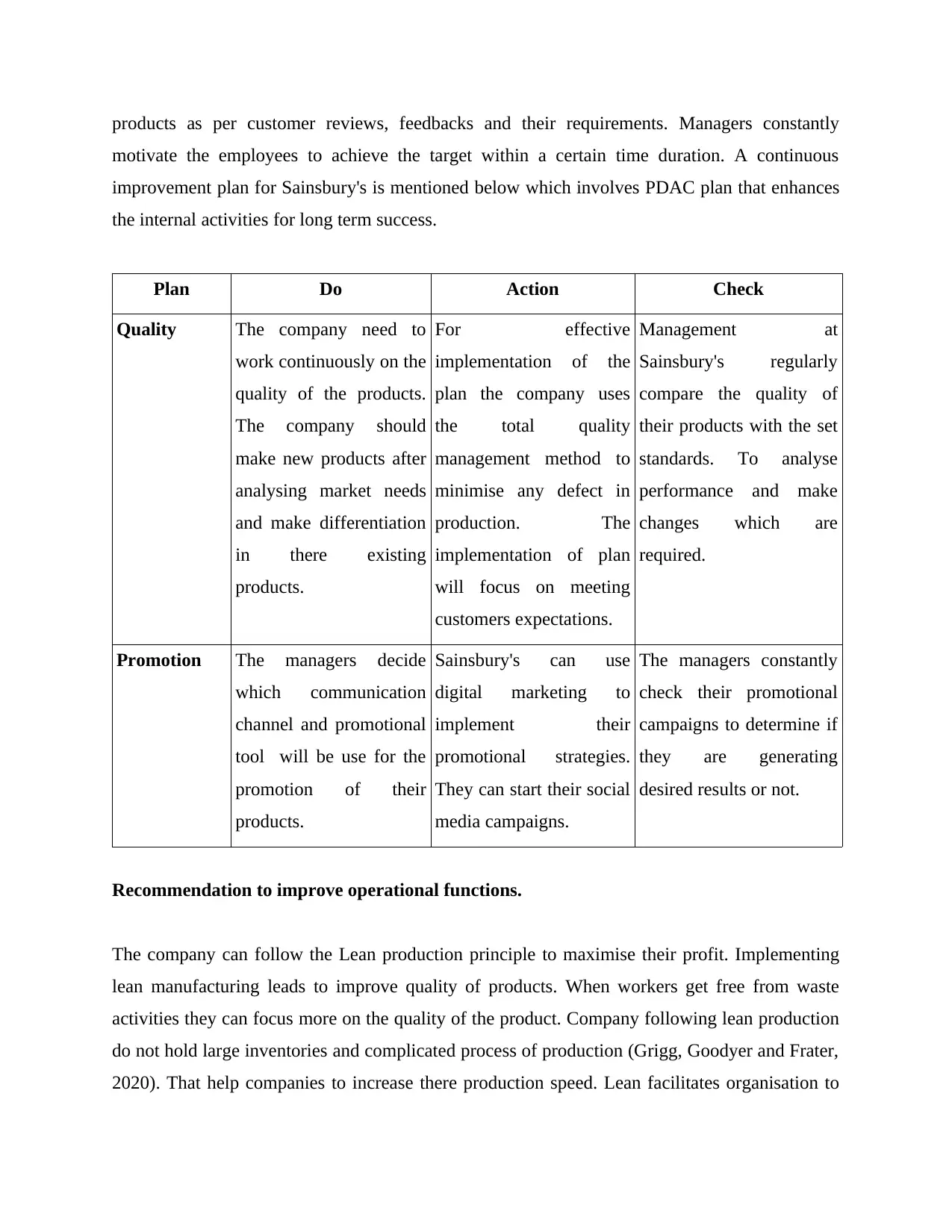
products as per customer reviews, feedbacks and their requirements. Managers constantly
motivate the employees to achieve the target within a certain time duration. A continuous
improvement plan for Sainsbury's is mentioned below which involves PDAC plan that enhances
the internal activities for long term success.
Plan Do Action Check
Quality The company need to
work continuously on the
quality of the products.
The company should
make new products after
analysing market needs
and make differentiation
in there existing
products.
For effective
implementation of the
plan the company uses
the total quality
management method to
minimise any defect in
production. The
implementation of plan
will focus on meeting
customers expectations.
Management at
Sainsbury's regularly
compare the quality of
their products with the set
standards. To analyse
performance and make
changes which are
required.
Promotion The managers decide
which communication
channel and promotional
tool will be use for the
promotion of their
products.
Sainsbury's can use
digital marketing to
implement their
promotional strategies.
They can start their social
media campaigns.
The managers constantly
check their promotional
campaigns to determine if
they are generating
desired results or not.
Recommendation to improve operational functions.
The company can follow the Lean production principle to maximise their profit. Implementing
lean manufacturing leads to improve quality of products. When workers get free from waste
activities they can focus more on the quality of the product. Company following lean production
do not hold large inventories and complicated process of production (Grigg, Goodyer and Frater,
2020). That help companies to increase there production speed. Lean facilitates organisation to
motivate the employees to achieve the target within a certain time duration. A continuous
improvement plan for Sainsbury's is mentioned below which involves PDAC plan that enhances
the internal activities for long term success.
Plan Do Action Check
Quality The company need to
work continuously on the
quality of the products.
The company should
make new products after
analysing market needs
and make differentiation
in there existing
products.
For effective
implementation of the
plan the company uses
the total quality
management method to
minimise any defect in
production. The
implementation of plan
will focus on meeting
customers expectations.
Management at
Sainsbury's regularly
compare the quality of
their products with the set
standards. To analyse
performance and make
changes which are
required.
Promotion The managers decide
which communication
channel and promotional
tool will be use for the
promotion of their
products.
Sainsbury's can use
digital marketing to
implement their
promotional strategies.
They can start their social
media campaigns.
The managers constantly
check their promotional
campaigns to determine if
they are generating
desired results or not.
Recommendation to improve operational functions.
The company can follow the Lean production principle to maximise their profit. Implementing
lean manufacturing leads to improve quality of products. When workers get free from waste
activities they can focus more on the quality of the product. Company following lean production
do not hold large inventories and complicated process of production (Grigg, Goodyer and Frater,
2020). That help companies to increase there production speed. Lean facilitates organisation to
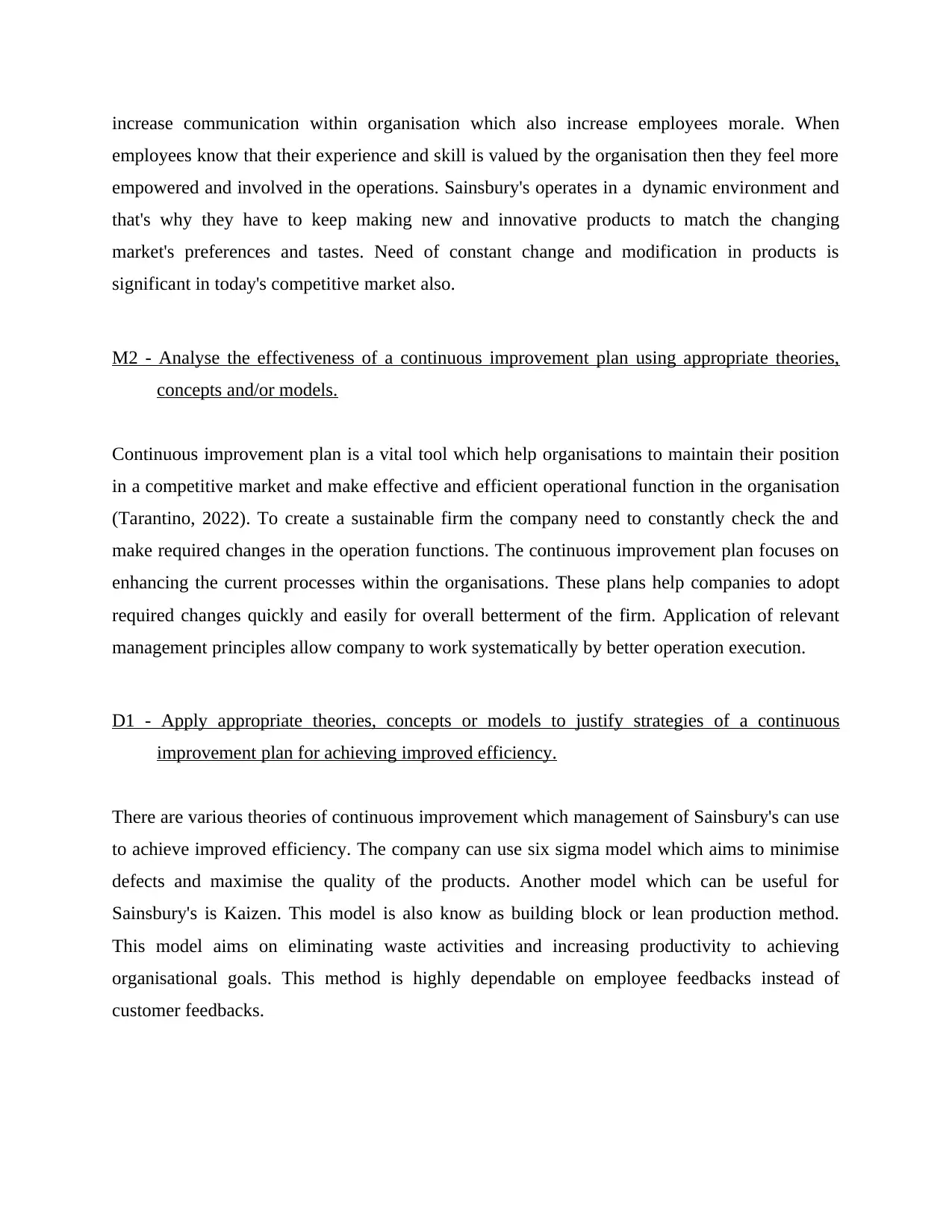
increase communication within organisation which also increase employees morale. When
employees know that their experience and skill is valued by the organisation then they feel more
empowered and involved in the operations. Sainsbury's operates in a dynamic environment and
that's why they have to keep making new and innovative products to match the changing
market's preferences and tastes. Need of constant change and modification in products is
significant in today's competitive market also.
M2 - Analyse the effectiveness of a continuous improvement plan using appropriate theories,
concepts and/or models.
Continuous improvement plan is a vital tool which help organisations to maintain their position
in a competitive market and make effective and efficient operational function in the organisation
(Tarantino, 2022). To create a sustainable firm the company need to constantly check the and
make required changes in the operation functions. The continuous improvement plan focuses on
enhancing the current processes within the organisations. These plans help companies to adopt
required changes quickly and easily for overall betterment of the firm. Application of relevant
management principles allow company to work systematically by better operation execution.
D1 - Apply appropriate theories, concepts or models to justify strategies of a continuous
improvement plan for achieving improved efficiency.
There are various theories of continuous improvement which management of Sainsbury's can use
to achieve improved efficiency. The company can use six sigma model which aims to minimise
defects and maximise the quality of the products. Another model which can be useful for
Sainsbury's is Kaizen. This model is also know as building block or lean production method.
This model aims on eliminating waste activities and increasing productivity to achieving
organisational goals. This method is highly dependable on employee feedbacks instead of
customer feedbacks.
employees know that their experience and skill is valued by the organisation then they feel more
empowered and involved in the operations. Sainsbury's operates in a dynamic environment and
that's why they have to keep making new and innovative products to match the changing
market's preferences and tastes. Need of constant change and modification in products is
significant in today's competitive market also.
M2 - Analyse the effectiveness of a continuous improvement plan using appropriate theories,
concepts and/or models.
Continuous improvement plan is a vital tool which help organisations to maintain their position
in a competitive market and make effective and efficient operational function in the organisation
(Tarantino, 2022). To create a sustainable firm the company need to constantly check the and
make required changes in the operation functions. The continuous improvement plan focuses on
enhancing the current processes within the organisations. These plans help companies to adopt
required changes quickly and easily for overall betterment of the firm. Application of relevant
management principles allow company to work systematically by better operation execution.
D1 - Apply appropriate theories, concepts or models to justify strategies of a continuous
improvement plan for achieving improved efficiency.
There are various theories of continuous improvement which management of Sainsbury's can use
to achieve improved efficiency. The company can use six sigma model which aims to minimise
defects and maximise the quality of the products. Another model which can be useful for
Sainsbury's is Kaizen. This model is also know as building block or lean production method.
This model aims on eliminating waste activities and increasing productivity to achieving
organisational goals. This method is highly dependable on employee feedbacks instead of
customer feedbacks.
Paraphrase This Document
Need a fresh take? Get an instant paraphrase of this document with our AI Paraphraser
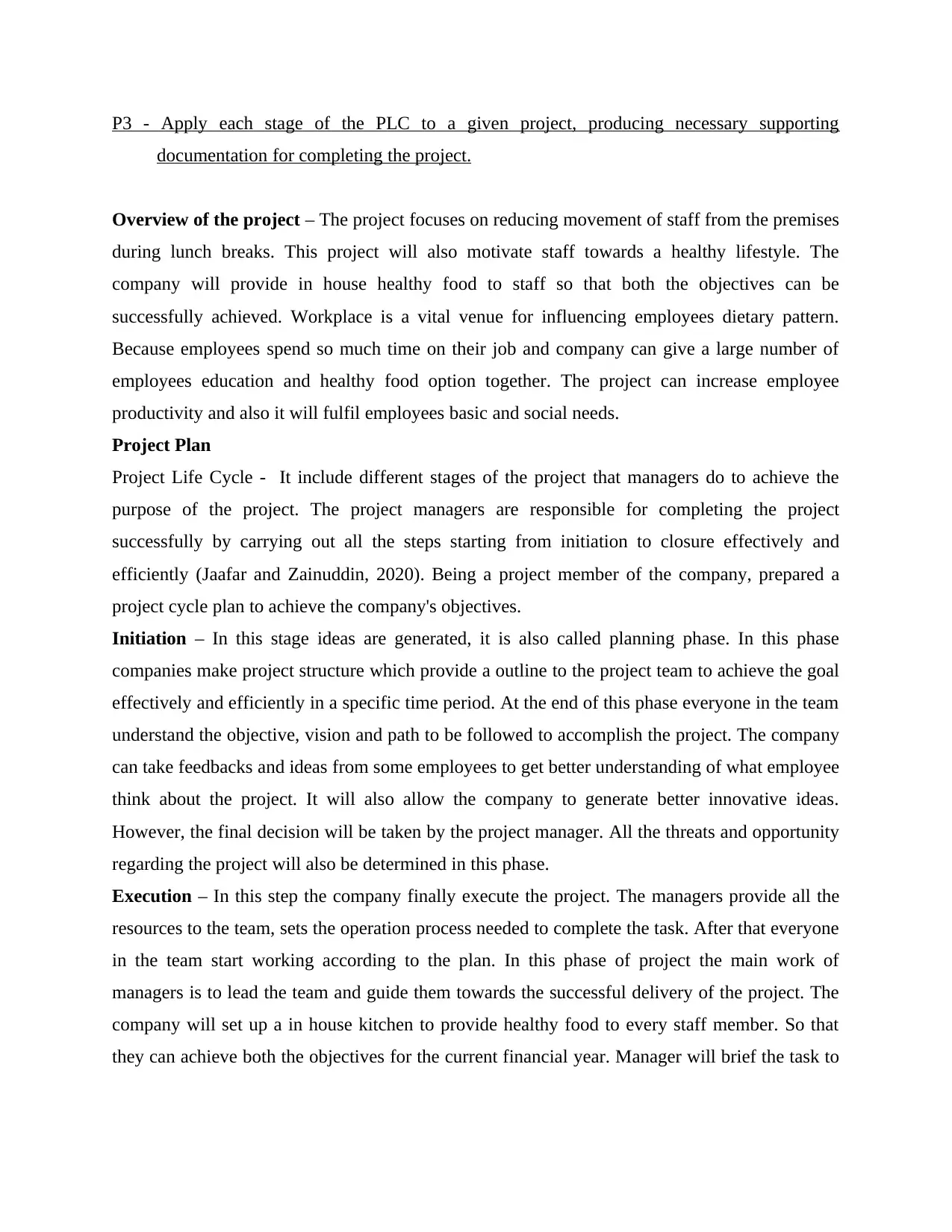
P3 - Apply each stage of the PLC to a given project, producing necessary supporting
documentation for completing the project.
Overview of the project – The project focuses on reducing movement of staff from the premises
during lunch breaks. This project will also motivate staff towards a healthy lifestyle. The
company will provide in house healthy food to staff so that both the objectives can be
successfully achieved. Workplace is a vital venue for influencing employees dietary pattern.
Because employees spend so much time on their job and company can give a large number of
employees education and healthy food option together. The project can increase employee
productivity and also it will fulfil employees basic and social needs.
Project Plan
Project Life Cycle - It include different stages of the project that managers do to achieve the
purpose of the project. The project managers are responsible for completing the project
successfully by carrying out all the steps starting from initiation to closure effectively and
efficiently (Jaafar and Zainuddin, 2020). Being a project member of the company, prepared a
project cycle plan to achieve the company's objectives.
Initiation – In this stage ideas are generated, it is also called planning phase. In this phase
companies make project structure which provide a outline to the project team to achieve the goal
effectively and efficiently in a specific time period. At the end of this phase everyone in the team
understand the objective, vision and path to be followed to accomplish the project. The company
can take feedbacks and ideas from some employees to get better understanding of what employee
think about the project. It will also allow the company to generate better innovative ideas.
However, the final decision will be taken by the project manager. All the threats and opportunity
regarding the project will also be determined in this phase.
Execution – In this step the company finally execute the project. The managers provide all the
resources to the team, sets the operation process needed to complete the task. After that everyone
in the team start working according to the plan. In this phase of project the main work of
managers is to lead the team and guide them towards the successful delivery of the project. The
company will set up a in house kitchen to provide healthy food to every staff member. So that
they can achieve both the objectives for the current financial year. Manager will brief the task to
documentation for completing the project.
Overview of the project – The project focuses on reducing movement of staff from the premises
during lunch breaks. This project will also motivate staff towards a healthy lifestyle. The
company will provide in house healthy food to staff so that both the objectives can be
successfully achieved. Workplace is a vital venue for influencing employees dietary pattern.
Because employees spend so much time on their job and company can give a large number of
employees education and healthy food option together. The project can increase employee
productivity and also it will fulfil employees basic and social needs.
Project Plan
Project Life Cycle - It include different stages of the project that managers do to achieve the
purpose of the project. The project managers are responsible for completing the project
successfully by carrying out all the steps starting from initiation to closure effectively and
efficiently (Jaafar and Zainuddin, 2020). Being a project member of the company, prepared a
project cycle plan to achieve the company's objectives.
Initiation – In this stage ideas are generated, it is also called planning phase. In this phase
companies make project structure which provide a outline to the project team to achieve the goal
effectively and efficiently in a specific time period. At the end of this phase everyone in the team
understand the objective, vision and path to be followed to accomplish the project. The company
can take feedbacks and ideas from some employees to get better understanding of what employee
think about the project. It will also allow the company to generate better innovative ideas.
However, the final decision will be taken by the project manager. All the threats and opportunity
regarding the project will also be determined in this phase.
Execution – In this step the company finally execute the project. The managers provide all the
resources to the team, sets the operation process needed to complete the task. After that everyone
in the team start working according to the plan. In this phase of project the main work of
managers is to lead the team and guide them towards the successful delivery of the project. The
company will set up a in house kitchen to provide healthy food to every staff member. So that
they can achieve both the objectives for the current financial year. Manager will brief the task to
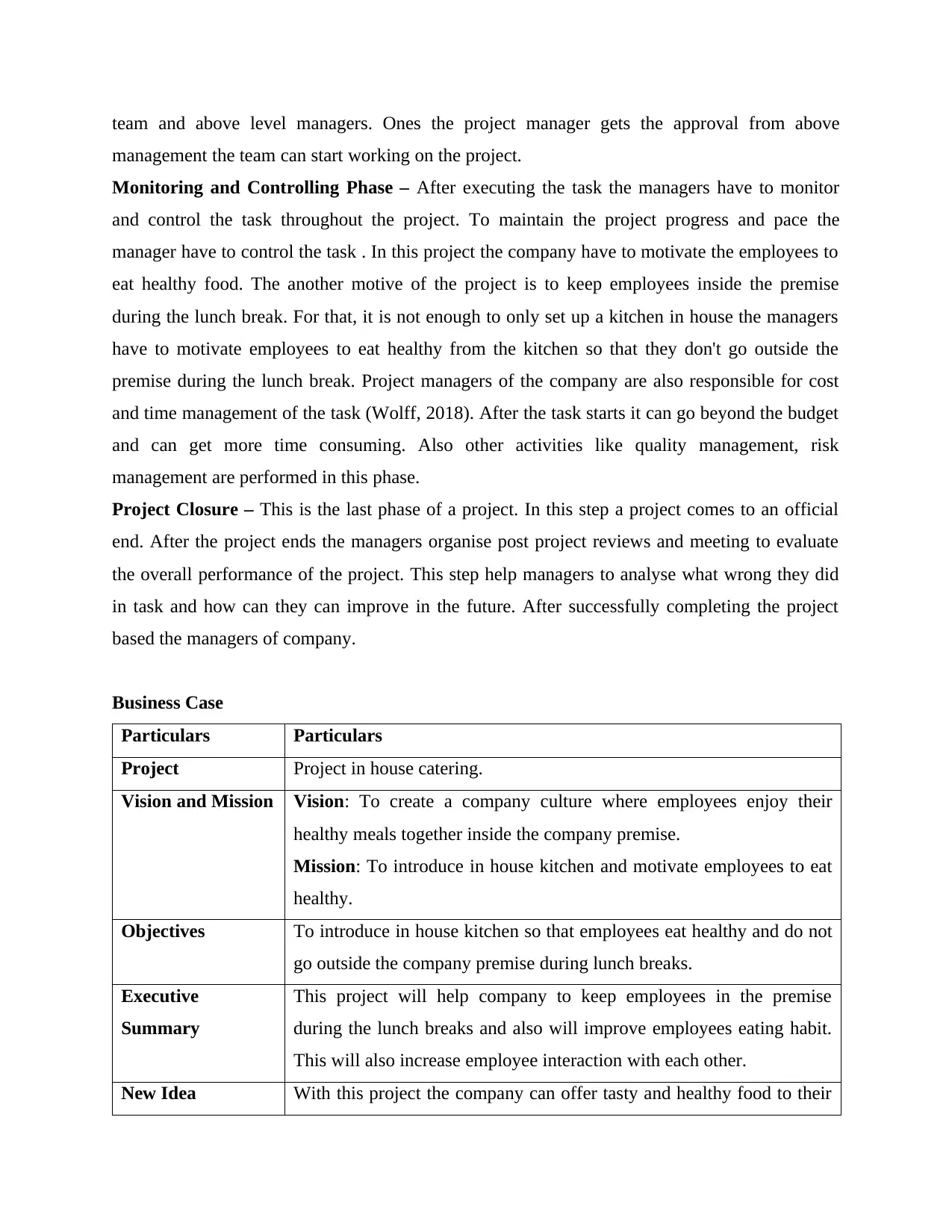
team and above level managers. Ones the project manager gets the approval from above
management the team can start working on the project.
Monitoring and Controlling Phase – After executing the task the managers have to monitor
and control the task throughout the project. To maintain the project progress and pace the
manager have to control the task . In this project the company have to motivate the employees to
eat healthy food. The another motive of the project is to keep employees inside the premise
during the lunch break. For that, it is not enough to only set up a kitchen in house the managers
have to motivate employees to eat healthy from the kitchen so that they don't go outside the
premise during the lunch break. Project managers of the company are also responsible for cost
and time management of the task (Wolff, 2018). After the task starts it can go beyond the budget
and can get more time consuming. Also other activities like quality management, risk
management are performed in this phase.
Project Closure – This is the last phase of a project. In this step a project comes to an official
end. After the project ends the managers organise post project reviews and meeting to evaluate
the overall performance of the project. This step help managers to analyse what wrong they did
in task and how can they can improve in the future. After successfully completing the project
based the managers of company.
Business Case
Particulars Particulars
Project Project in house catering.
Vision and Mission Vision: To create a company culture where employees enjoy their
healthy meals together inside the company premise.
Mission: To introduce in house kitchen and motivate employees to eat
healthy.
Objectives To introduce in house kitchen so that employees eat healthy and do not
go outside the company premise during lunch breaks.
Executive
Summary
This project will help company to keep employees in the premise
during the lunch breaks and also will improve employees eating habit.
This will also increase employee interaction with each other.
New Idea With this project the company can offer tasty and healthy food to their
management the team can start working on the project.
Monitoring and Controlling Phase – After executing the task the managers have to monitor
and control the task throughout the project. To maintain the project progress and pace the
manager have to control the task . In this project the company have to motivate the employees to
eat healthy food. The another motive of the project is to keep employees inside the premise
during the lunch break. For that, it is not enough to only set up a kitchen in house the managers
have to motivate employees to eat healthy from the kitchen so that they don't go outside the
premise during the lunch break. Project managers of the company are also responsible for cost
and time management of the task (Wolff, 2018). After the task starts it can go beyond the budget
and can get more time consuming. Also other activities like quality management, risk
management are performed in this phase.
Project Closure – This is the last phase of a project. In this step a project comes to an official
end. After the project ends the managers organise post project reviews and meeting to evaluate
the overall performance of the project. This step help managers to analyse what wrong they did
in task and how can they can improve in the future. After successfully completing the project
based the managers of company.
Business Case
Particulars Particulars
Project Project in house catering.
Vision and Mission Vision: To create a company culture where employees enjoy their
healthy meals together inside the company premise.
Mission: To introduce in house kitchen and motivate employees to eat
healthy.
Objectives To introduce in house kitchen so that employees eat healthy and do not
go outside the company premise during lunch breaks.
Executive
Summary
This project will help company to keep employees in the premise
during the lunch breaks and also will improve employees eating habit.
This will also increase employee interaction with each other.
New Idea With this project the company can offer tasty and healthy food to their
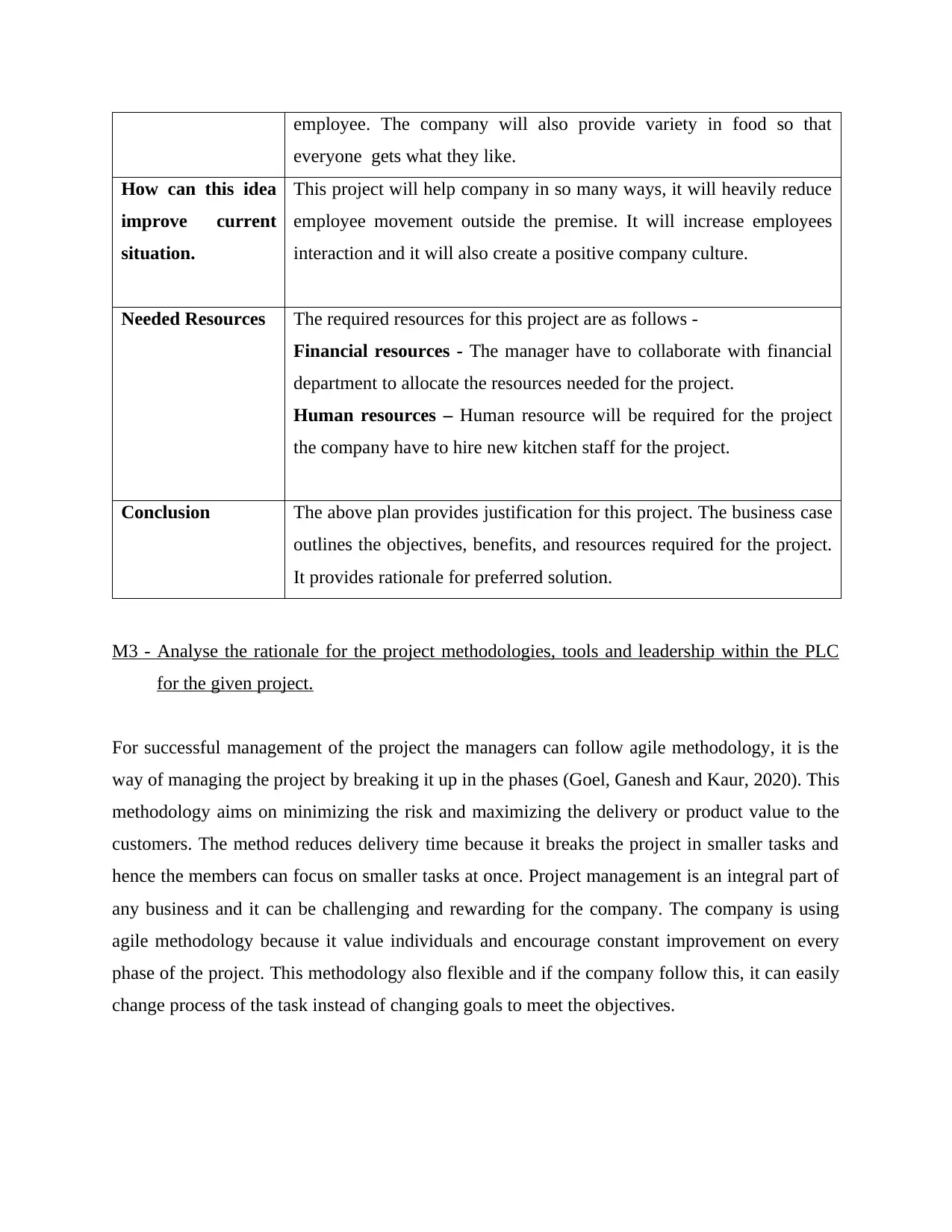
employee. The company will also provide variety in food so that
everyone gets what they like.
How can this idea
improve current
situation.
This project will help company in so many ways, it will heavily reduce
employee movement outside the premise. It will increase employees
interaction and it will also create a positive company culture.
Needed Resources The required resources for this project are as follows -
Financial resources - The manager have to collaborate with financial
department to allocate the resources needed for the project.
Human resources – Human resource will be required for the project
the company have to hire new kitchen staff for the project.
Conclusion The above plan provides justification for this project. The business case
outlines the objectives, benefits, and resources required for the project.
It provides rationale for preferred solution.
M3 - Analyse the rationale for the project methodologies, tools and leadership within the PLC
for the given project.
For successful management of the project the managers can follow agile methodology, it is the
way of managing the project by breaking it up in the phases (Goel, Ganesh and Kaur, 2020). This
methodology aims on minimizing the risk and maximizing the delivery or product value to the
customers. The method reduces delivery time because it breaks the project in smaller tasks and
hence the members can focus on smaller tasks at once. Project management is an integral part of
any business and it can be challenging and rewarding for the company. The company is using
agile methodology because it value individuals and encourage constant improvement on every
phase of the project. This methodology also flexible and if the company follow this, it can easily
change process of the task instead of changing goals to meet the objectives.
everyone gets what they like.
How can this idea
improve current
situation.
This project will help company in so many ways, it will heavily reduce
employee movement outside the premise. It will increase employees
interaction and it will also create a positive company culture.
Needed Resources The required resources for this project are as follows -
Financial resources - The manager have to collaborate with financial
department to allocate the resources needed for the project.
Human resources – Human resource will be required for the project
the company have to hire new kitchen staff for the project.
Conclusion The above plan provides justification for this project. The business case
outlines the objectives, benefits, and resources required for the project.
It provides rationale for preferred solution.
M3 - Analyse the rationale for the project methodologies, tools and leadership within the PLC
for the given project.
For successful management of the project the managers can follow agile methodology, it is the
way of managing the project by breaking it up in the phases (Goel, Ganesh and Kaur, 2020). This
methodology aims on minimizing the risk and maximizing the delivery or product value to the
customers. The method reduces delivery time because it breaks the project in smaller tasks and
hence the members can focus on smaller tasks at once. Project management is an integral part of
any business and it can be challenging and rewarding for the company. The company is using
agile methodology because it value individuals and encourage constant improvement on every
phase of the project. This methodology also flexible and if the company follow this, it can easily
change process of the task instead of changing goals to meet the objectives.
Secure Best Marks with AI Grader
Need help grading? Try our AI Grader for instant feedback on your assignments.
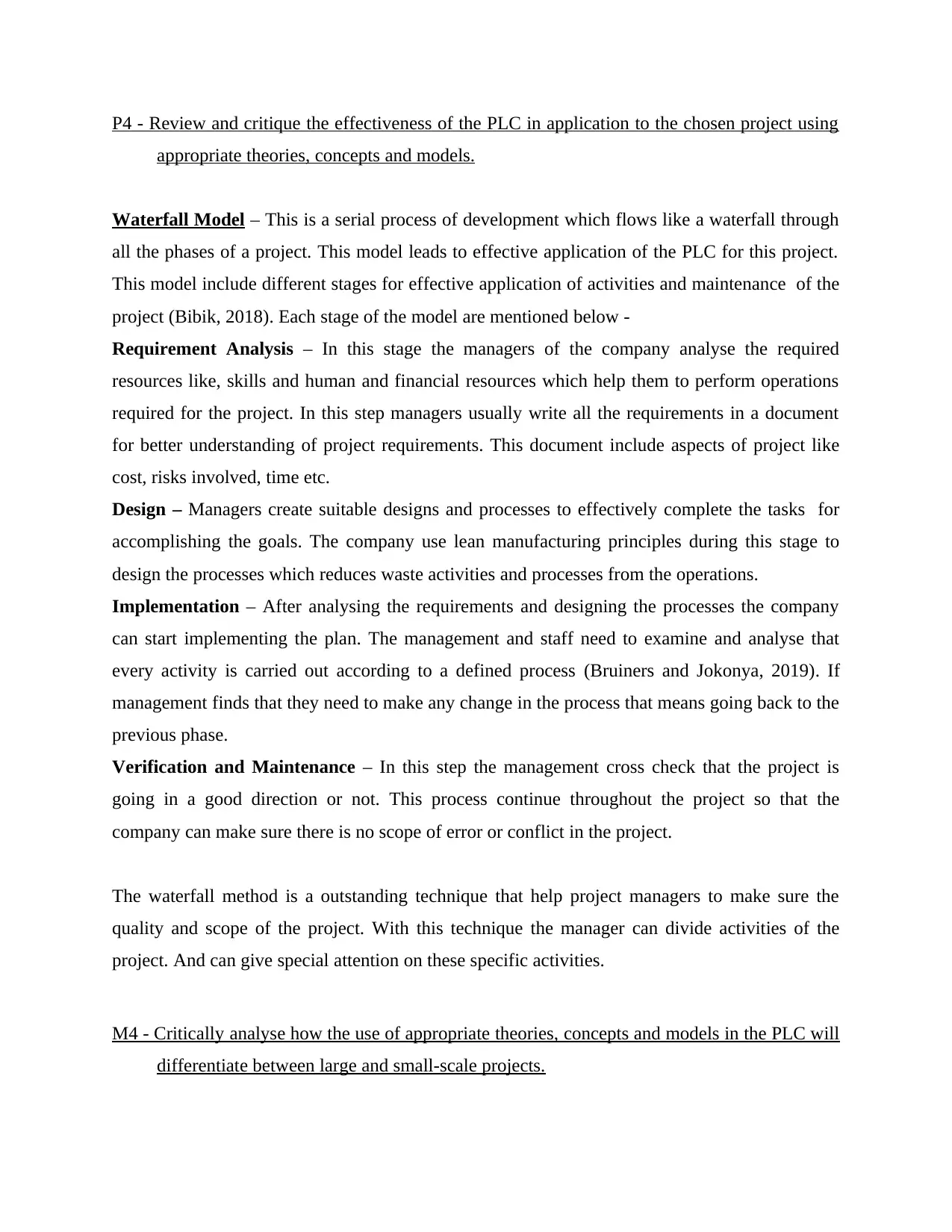
P4 - Review and critique the effectiveness of the PLC in application to the chosen project using
appropriate theories, concepts and models.
Waterfall Model – This is a serial process of development which flows like a waterfall through
all the phases of a project. This model leads to effective application of the PLC for this project.
This model include different stages for effective application of activities and maintenance of the
project (Bibik, 2018). Each stage of the model are mentioned below -
Requirement Analysis – In this stage the managers of the company analyse the required
resources like, skills and human and financial resources which help them to perform operations
required for the project. In this step managers usually write all the requirements in a document
for better understanding of project requirements. This document include aspects of project like
cost, risks involved, time etc.
Design – Managers create suitable designs and processes to effectively complete the tasks for
accomplishing the goals. The company use lean manufacturing principles during this stage to
design the processes which reduces waste activities and processes from the operations.
Implementation – After analysing the requirements and designing the processes the company
can start implementing the plan. The management and staff need to examine and analyse that
every activity is carried out according to a defined process (Bruiners and Jokonya, 2019). If
management finds that they need to make any change in the process that means going back to the
previous phase.
Verification and Maintenance – In this step the management cross check that the project is
going in a good direction or not. This process continue throughout the project so that the
company can make sure there is no scope of error or conflict in the project.
The waterfall method is a outstanding technique that help project managers to make sure the
quality and scope of the project. With this technique the manager can divide activities of the
project. And can give special attention on these specific activities.
M4 - Critically analyse how the use of appropriate theories, concepts and models in the PLC will
differentiate between large and small-scale projects.
appropriate theories, concepts and models.
Waterfall Model – This is a serial process of development which flows like a waterfall through
all the phases of a project. This model leads to effective application of the PLC for this project.
This model include different stages for effective application of activities and maintenance of the
project (Bibik, 2018). Each stage of the model are mentioned below -
Requirement Analysis – In this stage the managers of the company analyse the required
resources like, skills and human and financial resources which help them to perform operations
required for the project. In this step managers usually write all the requirements in a document
for better understanding of project requirements. This document include aspects of project like
cost, risks involved, time etc.
Design – Managers create suitable designs and processes to effectively complete the tasks for
accomplishing the goals. The company use lean manufacturing principles during this stage to
design the processes which reduces waste activities and processes from the operations.
Implementation – After analysing the requirements and designing the processes the company
can start implementing the plan. The management and staff need to examine and analyse that
every activity is carried out according to a defined process (Bruiners and Jokonya, 2019). If
management finds that they need to make any change in the process that means going back to the
previous phase.
Verification and Maintenance – In this step the management cross check that the project is
going in a good direction or not. This process continue throughout the project so that the
company can make sure there is no scope of error or conflict in the project.
The waterfall method is a outstanding technique that help project managers to make sure the
quality and scope of the project. With this technique the manager can divide activities of the
project. And can give special attention on these specific activities.
M4 - Critically analyse how the use of appropriate theories, concepts and models in the PLC will
differentiate between large and small-scale projects.
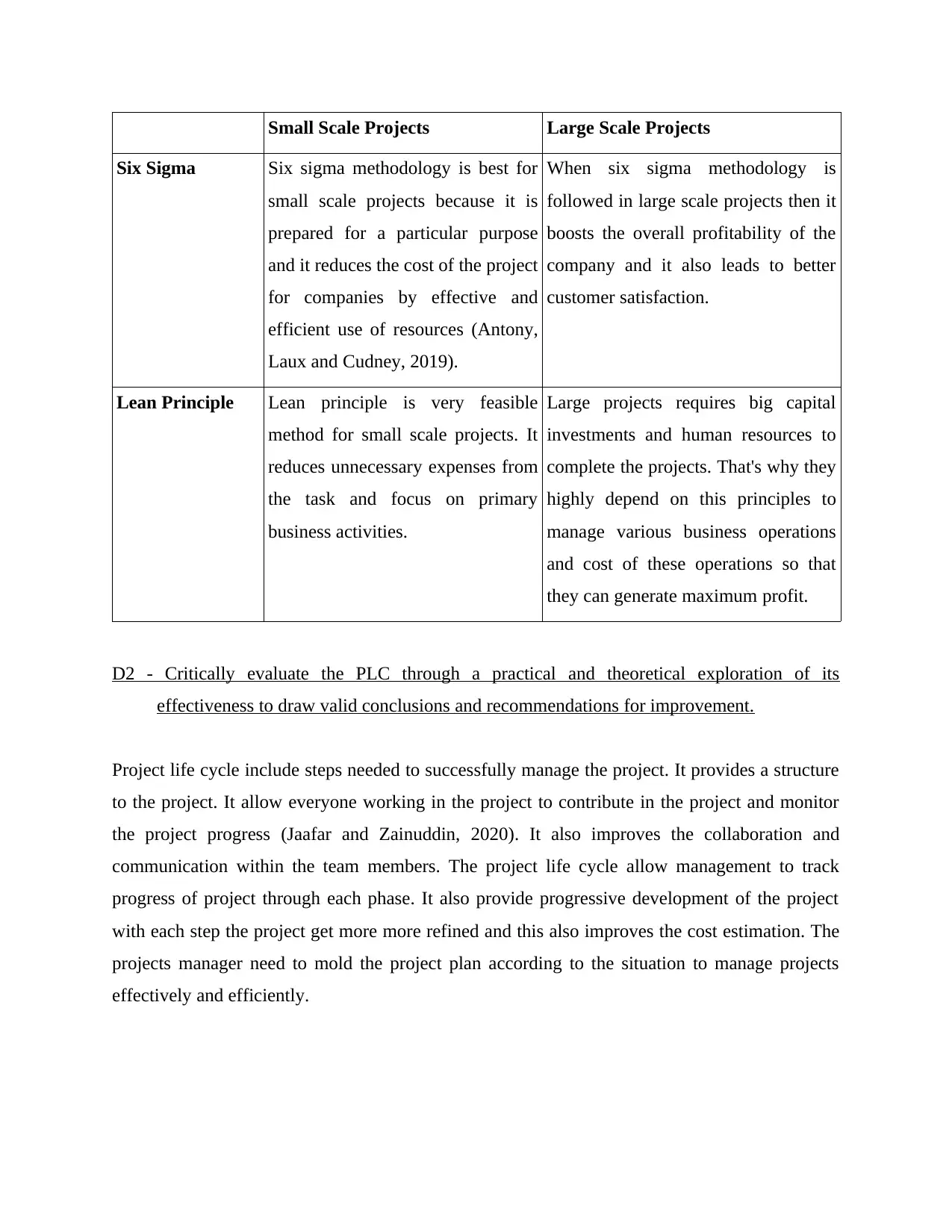
Small Scale Projects Large Scale Projects
Six Sigma Six sigma methodology is best for
small scale projects because it is
prepared for a particular purpose
and it reduces the cost of the project
for companies by effective and
efficient use of resources (Antony,
Laux and Cudney, 2019).
When six sigma methodology is
followed in large scale projects then it
boosts the overall profitability of the
company and it also leads to better
customer satisfaction.
Lean Principle Lean principle is very feasible
method for small scale projects. It
reduces unnecessary expenses from
the task and focus on primary
business activities.
Large projects requires big capital
investments and human resources to
complete the projects. That's why they
highly depend on this principles to
manage various business operations
and cost of these operations so that
they can generate maximum profit.
D2 - Critically evaluate the PLC through a practical and theoretical exploration of its
effectiveness to draw valid conclusions and recommendations for improvement.
Project life cycle include steps needed to successfully manage the project. It provides a structure
to the project. It allow everyone working in the project to contribute in the project and monitor
the project progress (Jaafar and Zainuddin, 2020). It also improves the collaboration and
communication within the team members. The project life cycle allow management to track
progress of project through each phase. It also provide progressive development of the project
with each step the project get more more refined and this also improves the cost estimation. The
projects manager need to mold the project plan according to the situation to manage projects
effectively and efficiently.
Six Sigma Six sigma methodology is best for
small scale projects because it is
prepared for a particular purpose
and it reduces the cost of the project
for companies by effective and
efficient use of resources (Antony,
Laux and Cudney, 2019).
When six sigma methodology is
followed in large scale projects then it
boosts the overall profitability of the
company and it also leads to better
customer satisfaction.
Lean Principle Lean principle is very feasible
method for small scale projects. It
reduces unnecessary expenses from
the task and focus on primary
business activities.
Large projects requires big capital
investments and human resources to
complete the projects. That's why they
highly depend on this principles to
manage various business operations
and cost of these operations so that
they can generate maximum profit.
D2 - Critically evaluate the PLC through a practical and theoretical exploration of its
effectiveness to draw valid conclusions and recommendations for improvement.
Project life cycle include steps needed to successfully manage the project. It provides a structure
to the project. It allow everyone working in the project to contribute in the project and monitor
the project progress (Jaafar and Zainuddin, 2020). It also improves the collaboration and
communication within the team members. The project life cycle allow management to track
progress of project through each phase. It also provide progressive development of the project
with each step the project get more more refined and this also improves the cost estimation. The
projects manager need to mold the project plan according to the situation to manage projects
effectively and efficiently.
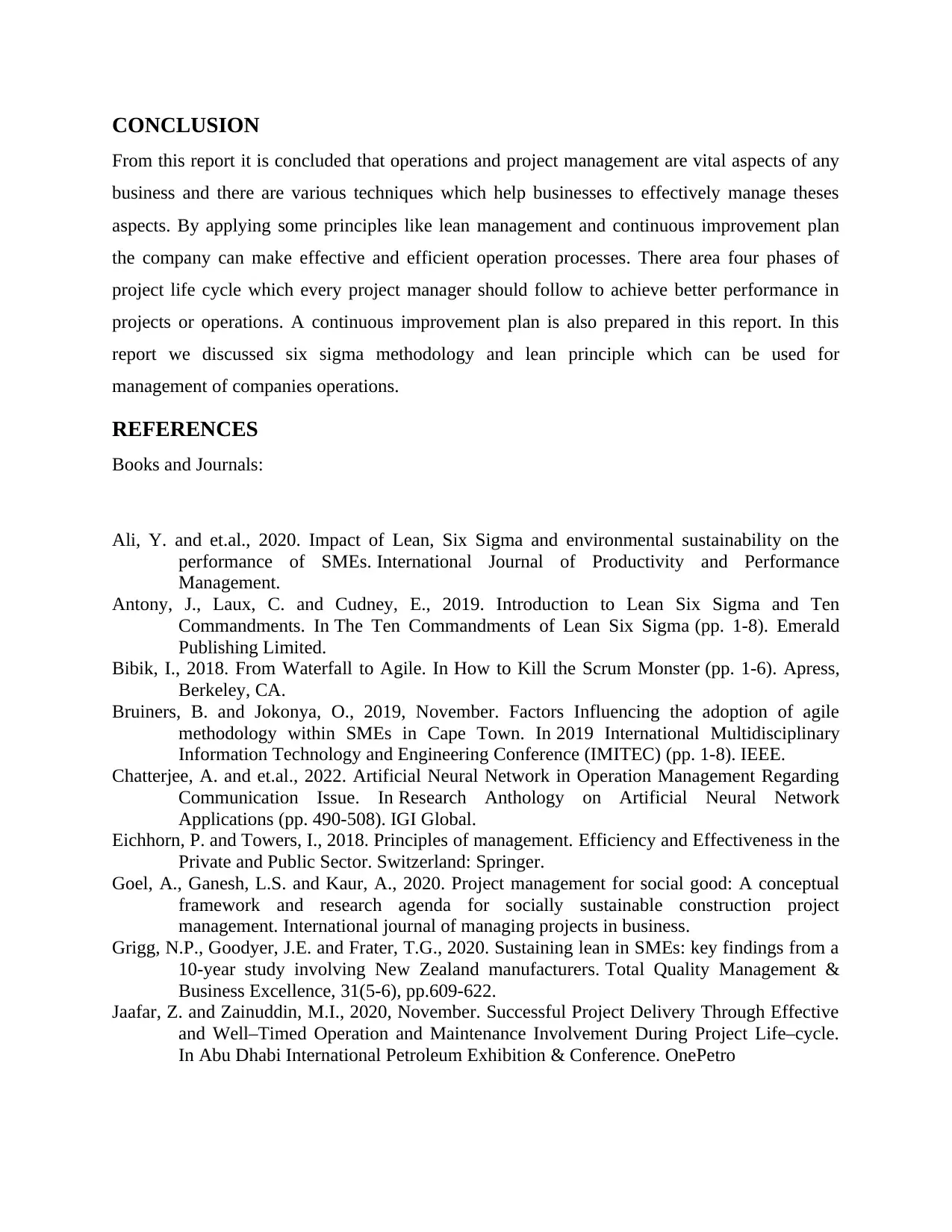
CONCLUSION
From this report it is concluded that operations and project management are vital aspects of any
business and there are various techniques which help businesses to effectively manage theses
aspects. By applying some principles like lean management and continuous improvement plan
the company can make effective and efficient operation processes. There area four phases of
project life cycle which every project manager should follow to achieve better performance in
projects or operations. A continuous improvement plan is also prepared in this report. In this
report we discussed six sigma methodology and lean principle which can be used for
management of companies operations.
REFERENCES
Books and Journals:
Ali, Y. and et.al., 2020. Impact of Lean, Six Sigma and environmental sustainability on the
performance of SMEs. International Journal of Productivity and Performance
Management.
Antony, J., Laux, C. and Cudney, E., 2019. Introduction to Lean Six Sigma and Ten
Commandments. In The Ten Commandments of Lean Six Sigma (pp. 1-8). Emerald
Publishing Limited.
Bibik, I., 2018. From Waterfall to Agile. In How to Kill the Scrum Monster (pp. 1-6). Apress,
Berkeley, CA.
Bruiners, B. and Jokonya, O., 2019, November. Factors Influencing the adoption of agile
methodology within SMEs in Cape Town. In 2019 International Multidisciplinary
Information Technology and Engineering Conference (IMITEC) (pp. 1-8). IEEE.
Chatterjee, A. and et.al., 2022. Artificial Neural Network in Operation Management Regarding
Communication Issue. In Research Anthology on Artificial Neural Network
Applications (pp. 490-508). IGI Global.
Eichhorn, P. and Towers, I., 2018. Principles of management. Efficiency and Effectiveness in the
Private and Public Sector. Switzerland: Springer.
Goel, A., Ganesh, L.S. and Kaur, A., 2020. Project management for social good: A conceptual
framework and research agenda for socially sustainable construction project
management. International journal of managing projects in business.
Grigg, N.P., Goodyer, J.E. and Frater, T.G., 2020. Sustaining lean in SMEs: key findings from a
10-year study involving New Zealand manufacturers. Total Quality Management &
Business Excellence, 31(5-6), pp.609-622.
Jaafar, Z. and Zainuddin, M.I., 2020, November. Successful Project Delivery Through Effective
and Well–Timed Operation and Maintenance Involvement During Project Life–cycle.
In Abu Dhabi International Petroleum Exhibition & Conference. OnePetro
From this report it is concluded that operations and project management are vital aspects of any
business and there are various techniques which help businesses to effectively manage theses
aspects. By applying some principles like lean management and continuous improvement plan
the company can make effective and efficient operation processes. There area four phases of
project life cycle which every project manager should follow to achieve better performance in
projects or operations. A continuous improvement plan is also prepared in this report. In this
report we discussed six sigma methodology and lean principle which can be used for
management of companies operations.
REFERENCES
Books and Journals:
Ali, Y. and et.al., 2020. Impact of Lean, Six Sigma and environmental sustainability on the
performance of SMEs. International Journal of Productivity and Performance
Management.
Antony, J., Laux, C. and Cudney, E., 2019. Introduction to Lean Six Sigma and Ten
Commandments. In The Ten Commandments of Lean Six Sigma (pp. 1-8). Emerald
Publishing Limited.
Bibik, I., 2018. From Waterfall to Agile. In How to Kill the Scrum Monster (pp. 1-6). Apress,
Berkeley, CA.
Bruiners, B. and Jokonya, O., 2019, November. Factors Influencing the adoption of agile
methodology within SMEs in Cape Town. In 2019 International Multidisciplinary
Information Technology and Engineering Conference (IMITEC) (pp. 1-8). IEEE.
Chatterjee, A. and et.al., 2022. Artificial Neural Network in Operation Management Regarding
Communication Issue. In Research Anthology on Artificial Neural Network
Applications (pp. 490-508). IGI Global.
Eichhorn, P. and Towers, I., 2018. Principles of management. Efficiency and Effectiveness in the
Private and Public Sector. Switzerland: Springer.
Goel, A., Ganesh, L.S. and Kaur, A., 2020. Project management for social good: A conceptual
framework and research agenda for socially sustainable construction project
management. International journal of managing projects in business.
Grigg, N.P., Goodyer, J.E. and Frater, T.G., 2020. Sustaining lean in SMEs: key findings from a
10-year study involving New Zealand manufacturers. Total Quality Management &
Business Excellence, 31(5-6), pp.609-622.
Jaafar, Z. and Zainuddin, M.I., 2020, November. Successful Project Delivery Through Effective
and Well–Timed Operation and Maintenance Involvement During Project Life–cycle.
In Abu Dhabi International Petroleum Exhibition & Conference. OnePetro
Paraphrase This Document
Need a fresh take? Get an instant paraphrase of this document with our AI Paraphraser
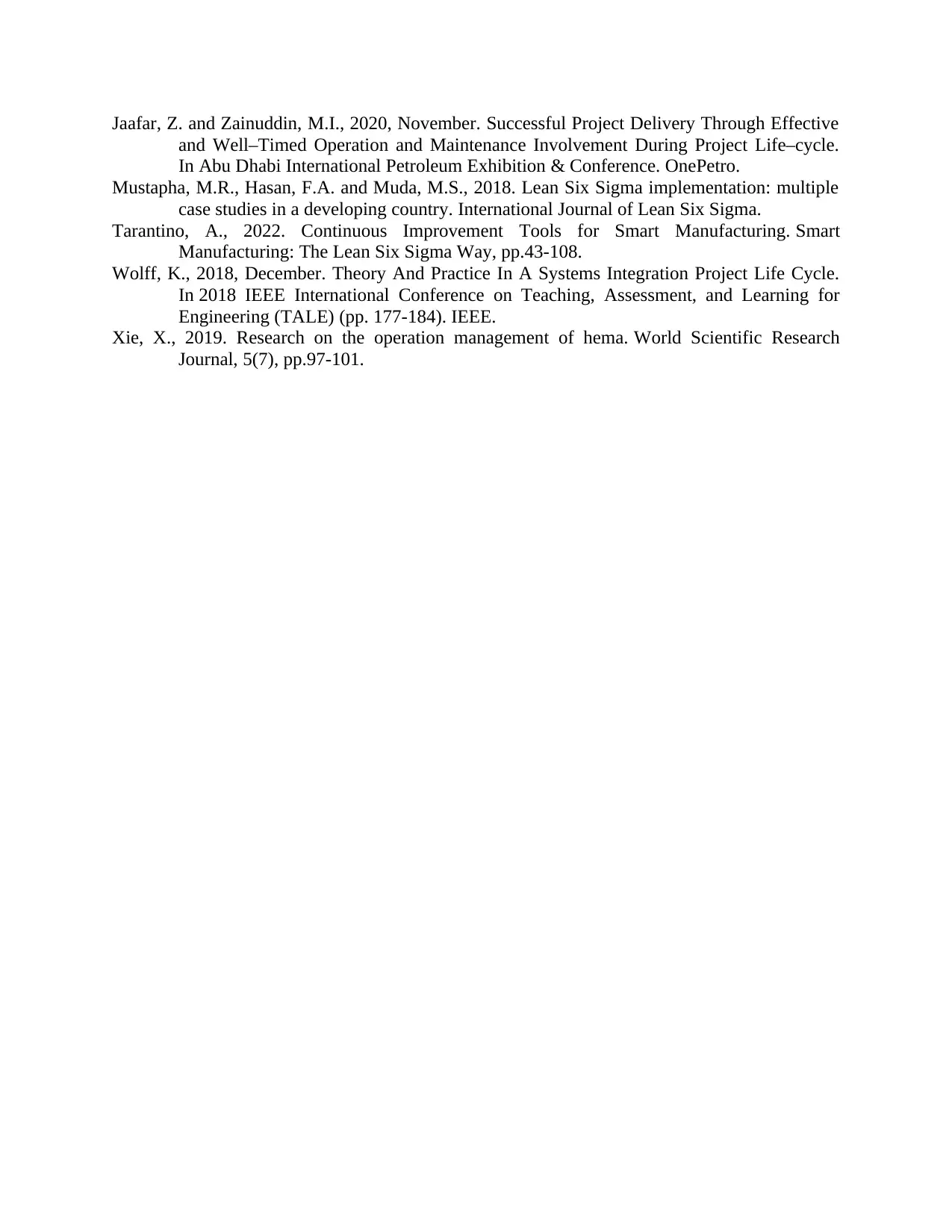
Jaafar, Z. and Zainuddin, M.I., 2020, November. Successful Project Delivery Through Effective
and Well–Timed Operation and Maintenance Involvement During Project Life–cycle.
In Abu Dhabi International Petroleum Exhibition & Conference. OnePetro.
Mustapha, M.R., Hasan, F.A. and Muda, M.S., 2018. Lean Six Sigma implementation: multiple
case studies in a developing country. International Journal of Lean Six Sigma.
Tarantino, A., 2022. Continuous Improvement Tools for Smart Manufacturing. Smart
Manufacturing: The Lean Six Sigma Way, pp.43-108.
Wolff, K., 2018, December. Theory And Practice In A Systems Integration Project Life Cycle.
In 2018 IEEE International Conference on Teaching, Assessment, and Learning for
Engineering (TALE) (pp. 177-184). IEEE.
Xie, X., 2019. Research on the operation management of hema. World Scientific Research
Journal, 5(7), pp.97-101.
and Well–Timed Operation and Maintenance Involvement During Project Life–cycle.
In Abu Dhabi International Petroleum Exhibition & Conference. OnePetro.
Mustapha, M.R., Hasan, F.A. and Muda, M.S., 2018. Lean Six Sigma implementation: multiple
case studies in a developing country. International Journal of Lean Six Sigma.
Tarantino, A., 2022. Continuous Improvement Tools for Smart Manufacturing. Smart
Manufacturing: The Lean Six Sigma Way, pp.43-108.
Wolff, K., 2018, December. Theory And Practice In A Systems Integration Project Life Cycle.
In 2018 IEEE International Conference on Teaching, Assessment, and Learning for
Engineering (TALE) (pp. 177-184). IEEE.
Xie, X., 2019. Research on the operation management of hema. World Scientific Research
Journal, 5(7), pp.97-101.
1 out of 14
Related Documents
![[object Object]](/_next/image/?url=%2F_next%2Fstatic%2Fmedia%2Flogo.6d15ce61.png&w=640&q=75)
Your All-in-One AI-Powered Toolkit for Academic Success.
+13062052269
info@desklib.com
Available 24*7 on WhatsApp / Email
Unlock your academic potential
© 2024 | Zucol Services PVT LTD | All rights reserved.