Supply Chain Management in IKEA
VerifiedAdded on 2022/12/27
|12
|3027
|36
AI Summary
This report discusses the supply chain management in IKEA, focusing on customer service, transportation, warehousing, and competitive advantage. It also addresses a critical issue in the organization and provides suggestions for improvement.
Contribute Materials
Your contribution can guide someone’s learning journey. Share your
documents today.
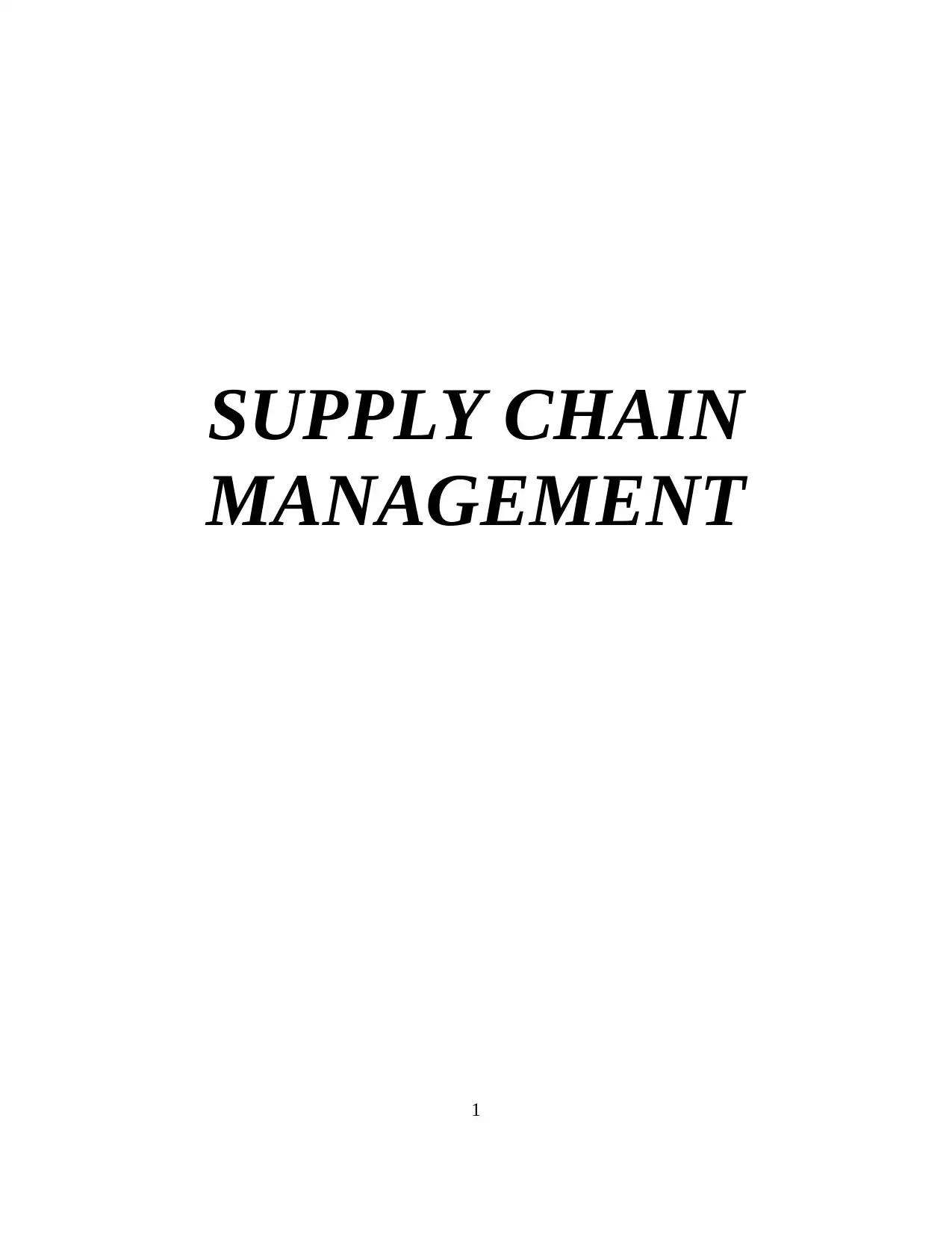
SUPPLY CHAIN
MANAGEMENT
1
MANAGEMENT
1
Secure Best Marks with AI Grader
Need help grading? Try our AI Grader for instant feedback on your assignments.
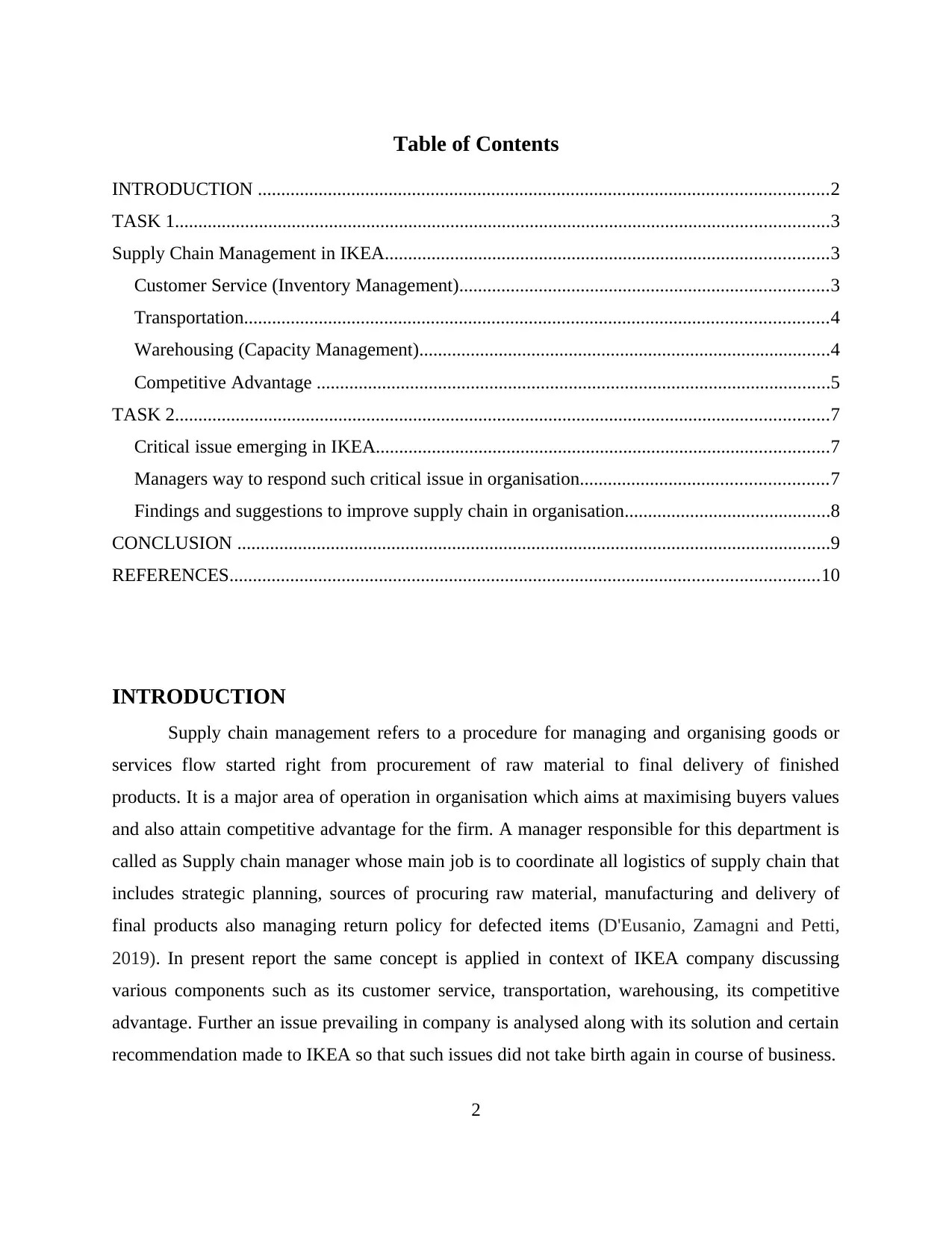
Table of Contents
INTRODUCTION ..........................................................................................................................2
TASK 1............................................................................................................................................3
Supply Chain Management in IKEA...............................................................................................3
Customer Service (Inventory Management)...............................................................................3
Transportation.............................................................................................................................4
Warehousing (Capacity Management)........................................................................................4
Competitive Advantage ..............................................................................................................5
TASK 2............................................................................................................................................7
Critical issue emerging in IKEA.................................................................................................7
Managers way to respond such critical issue in organisation.....................................................7
Findings and suggestions to improve supply chain in organisation............................................8
CONCLUSION ...............................................................................................................................9
REFERENCES..............................................................................................................................10
INTRODUCTION
Supply chain management refers to a procedure for managing and organising goods or
services flow started right from procurement of raw material to final delivery of finished
products. It is a major area of operation in organisation which aims at maximising buyers values
and also attain competitive advantage for the firm. A manager responsible for this department is
called as Supply chain manager whose main job is to coordinate all logistics of supply chain that
includes strategic planning, sources of procuring raw material, manufacturing and delivery of
final products also managing return policy for defected items (D'Eusanio, Zamagni and Petti,
2019). In present report the same concept is applied in context of IKEA company discussing
various components such as its customer service, transportation, warehousing, its competitive
advantage. Further an issue prevailing in company is analysed along with its solution and certain
recommendation made to IKEA so that such issues did not take birth again in course of business.
2
INTRODUCTION ..........................................................................................................................2
TASK 1............................................................................................................................................3
Supply Chain Management in IKEA...............................................................................................3
Customer Service (Inventory Management)...............................................................................3
Transportation.............................................................................................................................4
Warehousing (Capacity Management)........................................................................................4
Competitive Advantage ..............................................................................................................5
TASK 2............................................................................................................................................7
Critical issue emerging in IKEA.................................................................................................7
Managers way to respond such critical issue in organisation.....................................................7
Findings and suggestions to improve supply chain in organisation............................................8
CONCLUSION ...............................................................................................................................9
REFERENCES..............................................................................................................................10
INTRODUCTION
Supply chain management refers to a procedure for managing and organising goods or
services flow started right from procurement of raw material to final delivery of finished
products. It is a major area of operation in organisation which aims at maximising buyers values
and also attain competitive advantage for the firm. A manager responsible for this department is
called as Supply chain manager whose main job is to coordinate all logistics of supply chain that
includes strategic planning, sources of procuring raw material, manufacturing and delivery of
final products also managing return policy for defected items (D'Eusanio, Zamagni and Petti,
2019). In present report the same concept is applied in context of IKEA company discussing
various components such as its customer service, transportation, warehousing, its competitive
advantage. Further an issue prevailing in company is analysed along with its solution and certain
recommendation made to IKEA so that such issues did not take birth again in course of business.
2

TASK 1
Supply Chain Management in IKEA
Customer Service (Inventory Management)
The term customer service refers to a face to face or telephonic conversation directly with
company's customers by their representative on behalf of an organisation. Customer service is a
key to satisfy company's potential buyers as this the on;y way through which their queries can be
solved or feedback can be collected in order to improve product. This involves providing
assistance to those customers who buys company's product or services and fulfils their demand
(Deng and et. al., 2019). In order to have better customer experience and good brand image it is
very necessary for every company to strengthen its customer service department and satisfy their
customers needs to the fullest. Some companies maintains a separate department or customer
relationship management in their organisation which is sole responsible in handling customers
queries and satisfying their demands by providing best service of their business.
Inventory management refers to a process of managing and arranging inventories such as
raw material or equipments which are necessary for day to day operations of company (Garrido-
Hidalgo and et. al., 2019). This comprises procurement, arrangement and selling of both kinds of
goods that is raw material or final goods into market.
IKEA is a retailer company based in United Kingdom dealing in home furnishing items.
Company is having more than 400 stores expanded in more than 50 countries across world. The
inventory management by IKEA is in a way that can store approx 9500 products in its store at
one time. IKEA's authorised employees orders inventory when needed in organisation for further
production after identification of items and logistics requirement. After the production of final
product company then delivers its items to its outlets for sale. Company keeps few concepts of
inventory management in mind such as Cost-per-touch, Maximum/Minimum Replenishment or
High-Flow/Low-Flow technique.
The company manages its customers satisfaction by accepting back all those items in
warranty period by consumption of which the buyers did not gets satisfied.
3
Supply Chain Management in IKEA
Customer Service (Inventory Management)
The term customer service refers to a face to face or telephonic conversation directly with
company's customers by their representative on behalf of an organisation. Customer service is a
key to satisfy company's potential buyers as this the on;y way through which their queries can be
solved or feedback can be collected in order to improve product. This involves providing
assistance to those customers who buys company's product or services and fulfils their demand
(Deng and et. al., 2019). In order to have better customer experience and good brand image it is
very necessary for every company to strengthen its customer service department and satisfy their
customers needs to the fullest. Some companies maintains a separate department or customer
relationship management in their organisation which is sole responsible in handling customers
queries and satisfying their demands by providing best service of their business.
Inventory management refers to a process of managing and arranging inventories such as
raw material or equipments which are necessary for day to day operations of company (Garrido-
Hidalgo and et. al., 2019). This comprises procurement, arrangement and selling of both kinds of
goods that is raw material or final goods into market.
IKEA is a retailer company based in United Kingdom dealing in home furnishing items.
Company is having more than 400 stores expanded in more than 50 countries across world. The
inventory management by IKEA is in a way that can store approx 9500 products in its store at
one time. IKEA's authorised employees orders inventory when needed in organisation for further
production after identification of items and logistics requirement. After the production of final
product company then delivers its items to its outlets for sale. Company keeps few concepts of
inventory management in mind such as Cost-per-touch, Maximum/Minimum Replenishment or
High-Flow/Low-Flow technique.
The company manages its customers satisfaction by accepting back all those items in
warranty period by consumption of which the buyers did not gets satisfied.
3
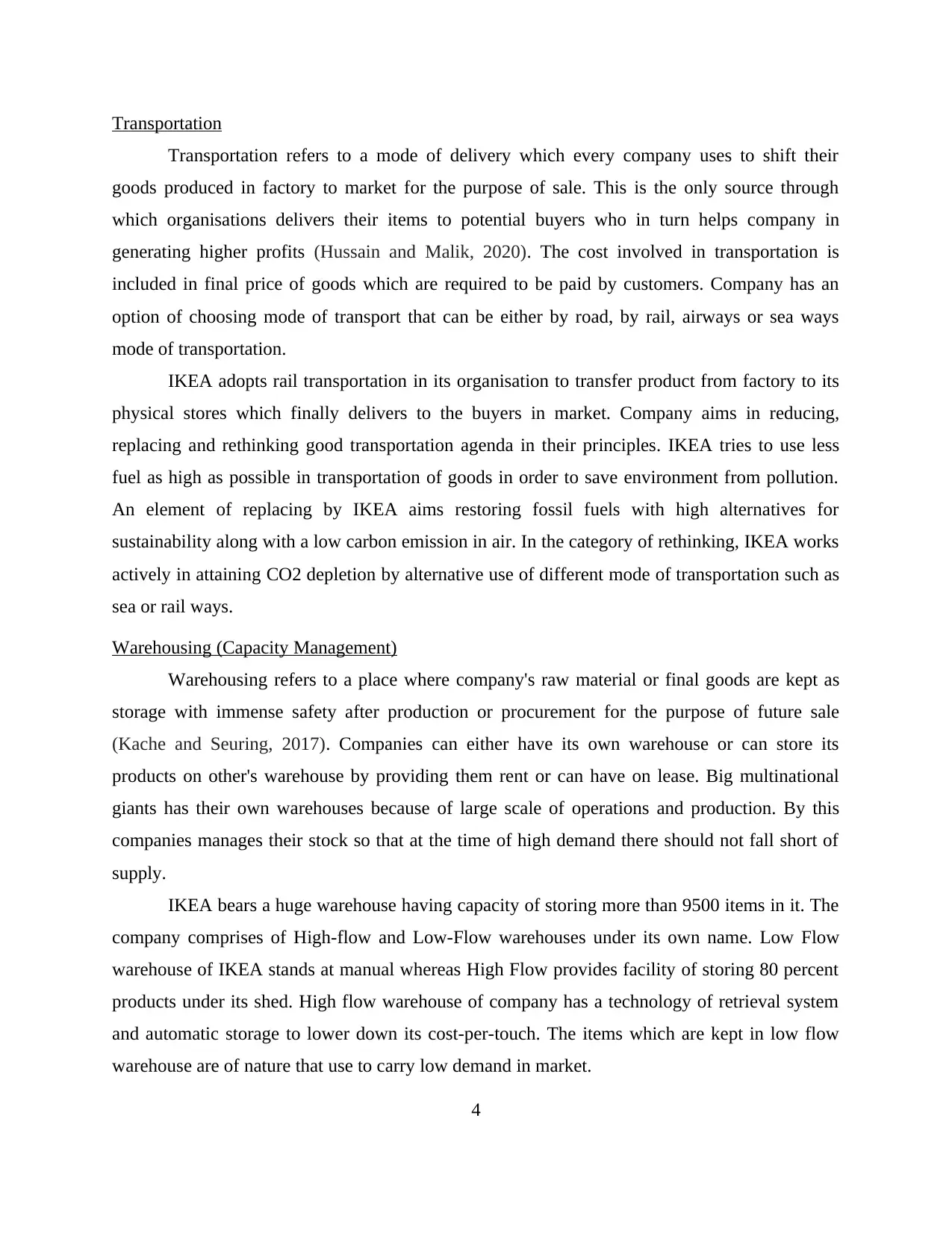
Transportation
Transportation refers to a mode of delivery which every company uses to shift their
goods produced in factory to market for the purpose of sale. This is the only source through
which organisations delivers their items to potential buyers who in turn helps company in
generating higher profits (Hussain and Malik, 2020). The cost involved in transportation is
included in final price of goods which are required to be paid by customers. Company has an
option of choosing mode of transport that can be either by road, by rail, airways or sea ways
mode of transportation.
IKEA adopts rail transportation in its organisation to transfer product from factory to its
physical stores which finally delivers to the buyers in market. Company aims in reducing,
replacing and rethinking good transportation agenda in their principles. IKEA tries to use less
fuel as high as possible in transportation of goods in order to save environment from pollution.
An element of replacing by IKEA aims restoring fossil fuels with high alternatives for
sustainability along with a low carbon emission in air. In the category of rethinking, IKEA works
actively in attaining CO2 depletion by alternative use of different mode of transportation such as
sea or rail ways.
Warehousing (Capacity Management)
Warehousing refers to a place where company's raw material or final goods are kept as
storage with immense safety after production or procurement for the purpose of future sale
(Kache and Seuring, 2017). Companies can either have its own warehouse or can store its
products on other's warehouse by providing them rent or can have on lease. Big multinational
giants has their own warehouses because of large scale of operations and production. By this
companies manages their stock so that at the time of high demand there should not fall short of
supply.
IKEA bears a huge warehouse having capacity of storing more than 9500 items in it. The
company comprises of High-flow and Low-Flow warehouses under its own name. Low Flow
warehouse of IKEA stands at manual whereas High Flow provides facility of storing 80 percent
products under its shed. High flow warehouse of company has a technology of retrieval system
and automatic storage to lower down its cost-per-touch. The items which are kept in low flow
warehouse are of nature that use to carry low demand in market.
4
Transportation refers to a mode of delivery which every company uses to shift their
goods produced in factory to market for the purpose of sale. This is the only source through
which organisations delivers their items to potential buyers who in turn helps company in
generating higher profits (Hussain and Malik, 2020). The cost involved in transportation is
included in final price of goods which are required to be paid by customers. Company has an
option of choosing mode of transport that can be either by road, by rail, airways or sea ways
mode of transportation.
IKEA adopts rail transportation in its organisation to transfer product from factory to its
physical stores which finally delivers to the buyers in market. Company aims in reducing,
replacing and rethinking good transportation agenda in their principles. IKEA tries to use less
fuel as high as possible in transportation of goods in order to save environment from pollution.
An element of replacing by IKEA aims restoring fossil fuels with high alternatives for
sustainability along with a low carbon emission in air. In the category of rethinking, IKEA works
actively in attaining CO2 depletion by alternative use of different mode of transportation such as
sea or rail ways.
Warehousing (Capacity Management)
Warehousing refers to a place where company's raw material or final goods are kept as
storage with immense safety after production or procurement for the purpose of future sale
(Kache and Seuring, 2017). Companies can either have its own warehouse or can store its
products on other's warehouse by providing them rent or can have on lease. Big multinational
giants has their own warehouses because of large scale of operations and production. By this
companies manages their stock so that at the time of high demand there should not fall short of
supply.
IKEA bears a huge warehouse having capacity of storing more than 9500 items in it. The
company comprises of High-flow and Low-Flow warehouses under its own name. Low Flow
warehouse of IKEA stands at manual whereas High Flow provides facility of storing 80 percent
products under its shed. High flow warehouse of company has a technology of retrieval system
and automatic storage to lower down its cost-per-touch. The items which are kept in low flow
warehouse are of nature that use to carry low demand in market.
4
Secure Best Marks with AI Grader
Need help grading? Try our AI Grader for instant feedback on your assignments.
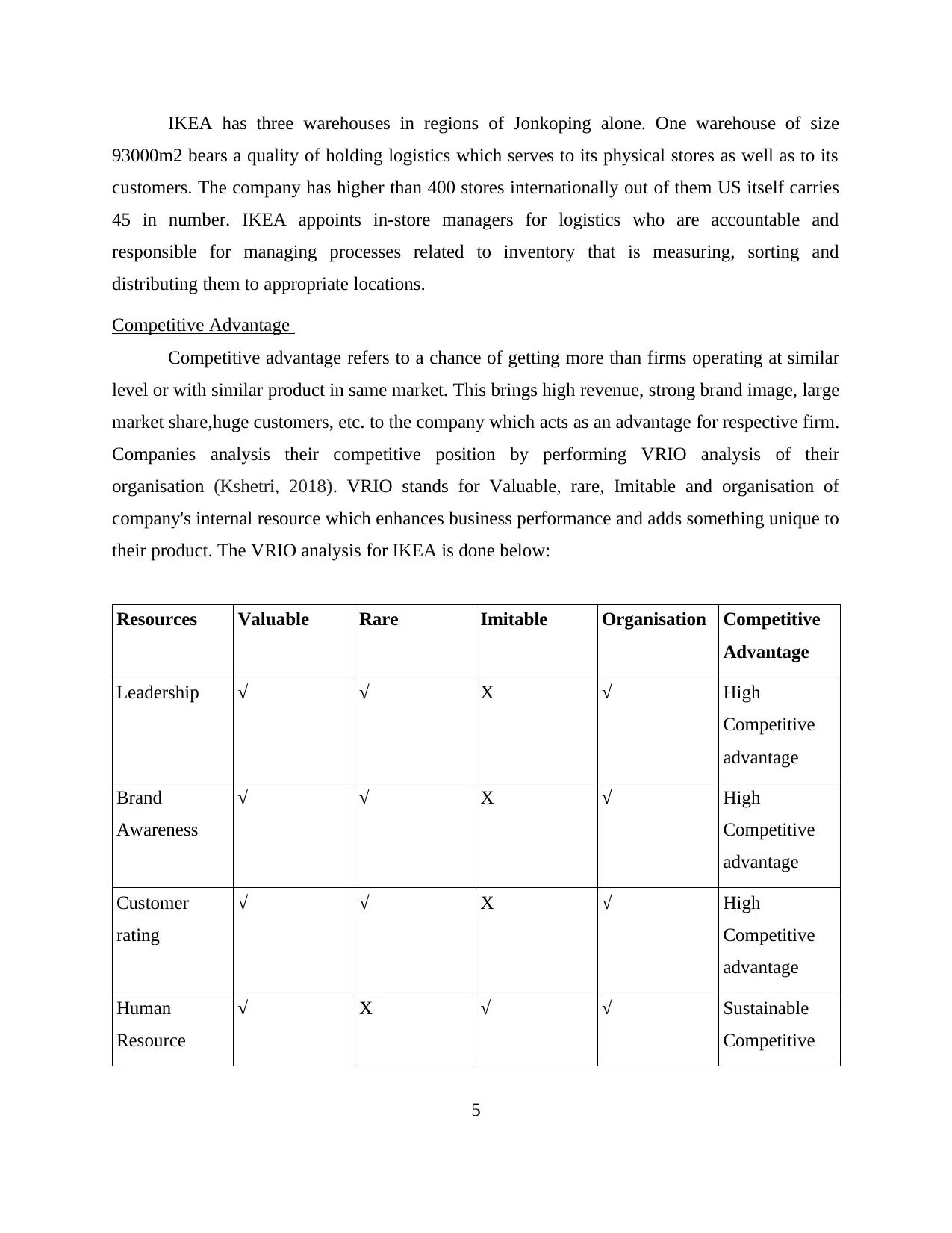
IKEA has three warehouses in regions of Jonkoping alone. One warehouse of size
93000m2 bears a quality of holding logistics which serves to its physical stores as well as to its
customers. The company has higher than 400 stores internationally out of them US itself carries
45 in number. IKEA appoints in-store managers for logistics who are accountable and
responsible for managing processes related to inventory that is measuring, sorting and
distributing them to appropriate locations.
Competitive Advantage
Competitive advantage refers to a chance of getting more than firms operating at similar
level or with similar product in same market. This brings high revenue, strong brand image, large
market share,huge customers, etc. to the company which acts as an advantage for respective firm.
Companies analysis their competitive position by performing VRIO analysis of their
organisation (Kshetri, 2018). VRIO stands for Valuable, rare, Imitable and organisation of
company's internal resource which enhances business performance and adds something unique to
their product. The VRIO analysis for IKEA is done below:
Resources Valuable Rare Imitable Organisation Competitive
Advantage
Leadership √ √ X √ High
Competitive
advantage
Brand
Awareness
√ √ X √ High
Competitive
advantage
Customer
rating
√ √ X √ High
Competitive
advantage
Human
Resource
√ X √ √ Sustainable
Competitive
5
93000m2 bears a quality of holding logistics which serves to its physical stores as well as to its
customers. The company has higher than 400 stores internationally out of them US itself carries
45 in number. IKEA appoints in-store managers for logistics who are accountable and
responsible for managing processes related to inventory that is measuring, sorting and
distributing them to appropriate locations.
Competitive Advantage
Competitive advantage refers to a chance of getting more than firms operating at similar
level or with similar product in same market. This brings high revenue, strong brand image, large
market share,huge customers, etc. to the company which acts as an advantage for respective firm.
Companies analysis their competitive position by performing VRIO analysis of their
organisation (Kshetri, 2018). VRIO stands for Valuable, rare, Imitable and organisation of
company's internal resource which enhances business performance and adds something unique to
their product. The VRIO analysis for IKEA is done below:
Resources Valuable Rare Imitable Organisation Competitive
Advantage
Leadership √ √ X √ High
Competitive
advantage
Brand
Awareness
√ √ X √ High
Competitive
advantage
Customer
rating
√ √ X √ High
Competitive
advantage
Human
Resource
√ X √ √ Sustainable
Competitive
5
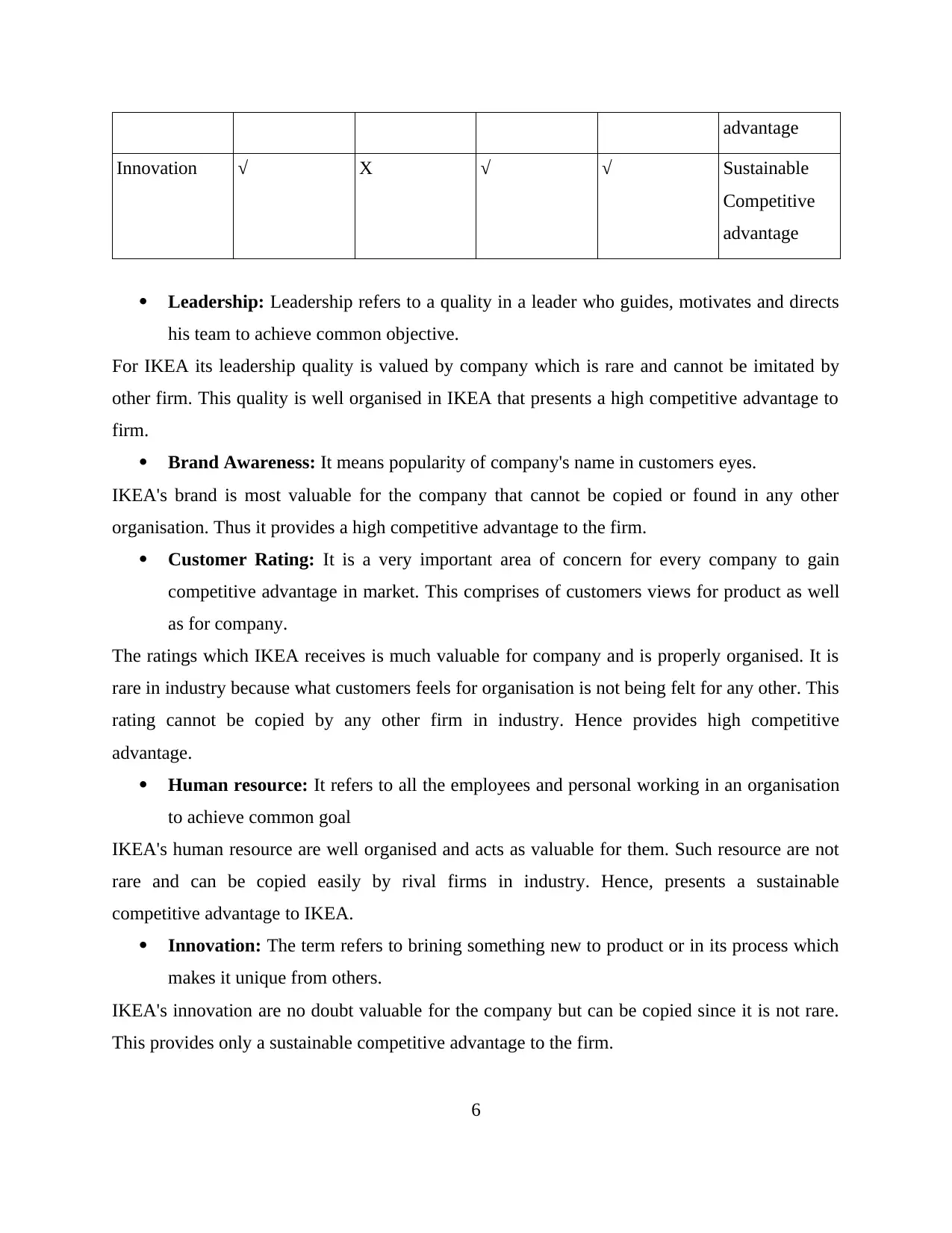
advantage
Innovation √ X √ √ Sustainable
Competitive
advantage
Leadership: Leadership refers to a quality in a leader who guides, motivates and directs
his team to achieve common objective.
For IKEA its leadership quality is valued by company which is rare and cannot be imitated by
other firm. This quality is well organised in IKEA that presents a high competitive advantage to
firm.
Brand Awareness: It means popularity of company's name in customers eyes.
IKEA's brand is most valuable for the company that cannot be copied or found in any other
organisation. Thus it provides a high competitive advantage to the firm.
Customer Rating: It is a very important area of concern for every company to gain
competitive advantage in market. This comprises of customers views for product as well
as for company.
The ratings which IKEA receives is much valuable for company and is properly organised. It is
rare in industry because what customers feels for organisation is not being felt for any other. This
rating cannot be copied by any other firm in industry. Hence provides high competitive
advantage.
Human resource: It refers to all the employees and personal working in an organisation
to achieve common goal
IKEA's human resource are well organised and acts as valuable for them. Such resource are not
rare and can be copied easily by rival firms in industry. Hence, presents a sustainable
competitive advantage to IKEA.
Innovation: The term refers to brining something new to product or in its process which
makes it unique from others.
IKEA's innovation are no doubt valuable for the company but can be copied since it is not rare.
This provides only a sustainable competitive advantage to the firm.
6
Innovation √ X √ √ Sustainable
Competitive
advantage
Leadership: Leadership refers to a quality in a leader who guides, motivates and directs
his team to achieve common objective.
For IKEA its leadership quality is valued by company which is rare and cannot be imitated by
other firm. This quality is well organised in IKEA that presents a high competitive advantage to
firm.
Brand Awareness: It means popularity of company's name in customers eyes.
IKEA's brand is most valuable for the company that cannot be copied or found in any other
organisation. Thus it provides a high competitive advantage to the firm.
Customer Rating: It is a very important area of concern for every company to gain
competitive advantage in market. This comprises of customers views for product as well
as for company.
The ratings which IKEA receives is much valuable for company and is properly organised. It is
rare in industry because what customers feels for organisation is not being felt for any other. This
rating cannot be copied by any other firm in industry. Hence provides high competitive
advantage.
Human resource: It refers to all the employees and personal working in an organisation
to achieve common goal
IKEA's human resource are well organised and acts as valuable for them. Such resource are not
rare and can be copied easily by rival firms in industry. Hence, presents a sustainable
competitive advantage to IKEA.
Innovation: The term refers to brining something new to product or in its process which
makes it unique from others.
IKEA's innovation are no doubt valuable for the company but can be copied since it is not rare.
This provides only a sustainable competitive advantage to the firm.
6
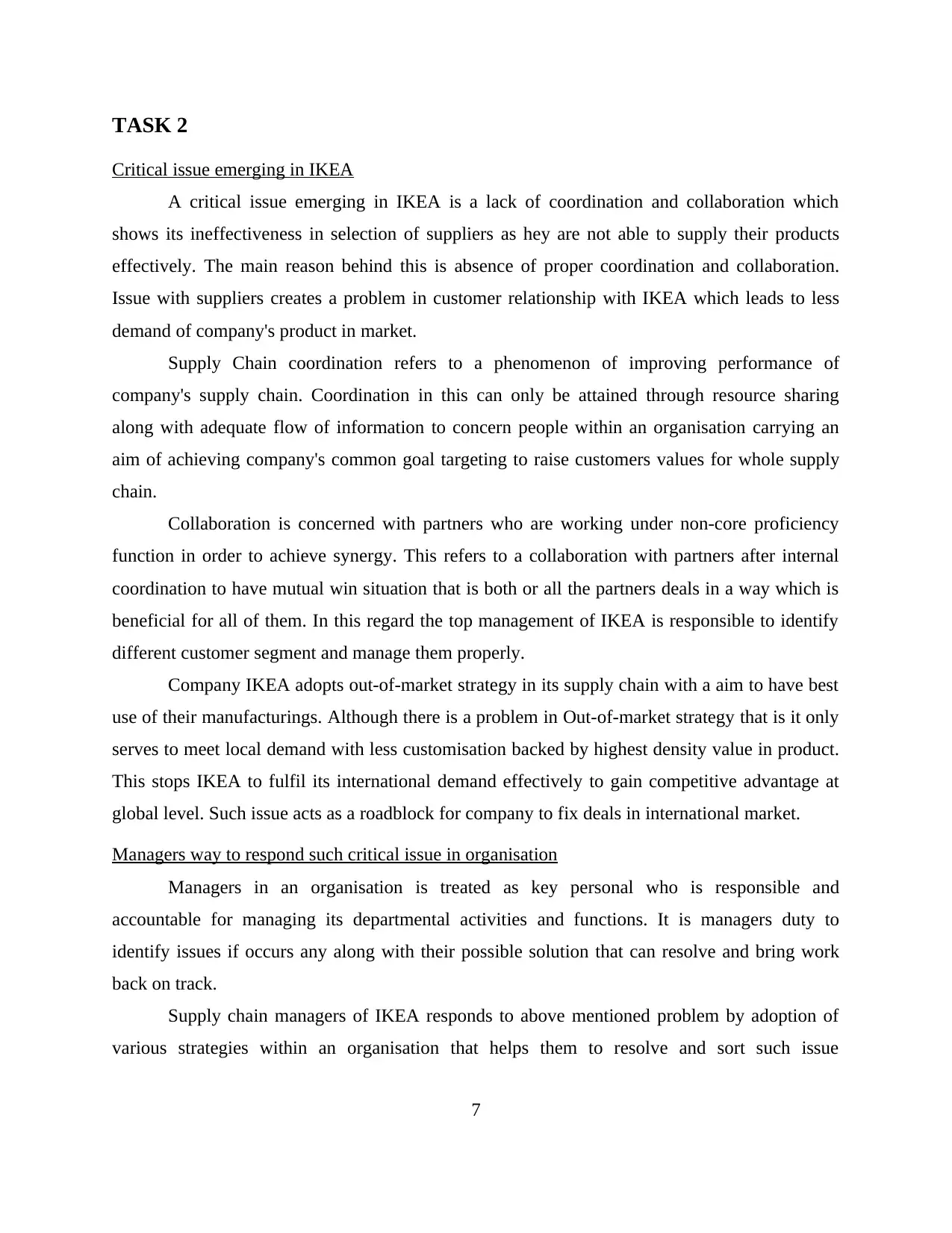
TASK 2
Critical issue emerging in IKEA
A critical issue emerging in IKEA is a lack of coordination and collaboration which
shows its ineffectiveness in selection of suppliers as hey are not able to supply their products
effectively. The main reason behind this is absence of proper coordination and collaboration.
Issue with suppliers creates a problem in customer relationship with IKEA which leads to less
demand of company's product in market.
Supply Chain coordination refers to a phenomenon of improving performance of
company's supply chain. Coordination in this can only be attained through resource sharing
along with adequate flow of information to concern people within an organisation carrying an
aim of achieving company's common goal targeting to raise customers values for whole supply
chain.
Collaboration is concerned with partners who are working under non-core proficiency
function in order to achieve synergy. This refers to a collaboration with partners after internal
coordination to have mutual win situation that is both or all the partners deals in a way which is
beneficial for all of them. In this regard the top management of IKEA is responsible to identify
different customer segment and manage them properly.
Company IKEA adopts out-of-market strategy in its supply chain with a aim to have best
use of their manufacturings. Although there is a problem in Out-of-market strategy that is it only
serves to meet local demand with less customisation backed by highest density value in product.
This stops IKEA to fulfil its international demand effectively to gain competitive advantage at
global level. Such issue acts as a roadblock for company to fix deals in international market.
Managers way to respond such critical issue in organisation
Managers in an organisation is treated as key personal who is responsible and
accountable for managing its departmental activities and functions. It is managers duty to
identify issues if occurs any along with their possible solution that can resolve and bring work
back on track.
Supply chain managers of IKEA responds to above mentioned problem by adoption of
various strategies within an organisation that helps them to resolve and sort such issue
7
Critical issue emerging in IKEA
A critical issue emerging in IKEA is a lack of coordination and collaboration which
shows its ineffectiveness in selection of suppliers as hey are not able to supply their products
effectively. The main reason behind this is absence of proper coordination and collaboration.
Issue with suppliers creates a problem in customer relationship with IKEA which leads to less
demand of company's product in market.
Supply Chain coordination refers to a phenomenon of improving performance of
company's supply chain. Coordination in this can only be attained through resource sharing
along with adequate flow of information to concern people within an organisation carrying an
aim of achieving company's common goal targeting to raise customers values for whole supply
chain.
Collaboration is concerned with partners who are working under non-core proficiency
function in order to achieve synergy. This refers to a collaboration with partners after internal
coordination to have mutual win situation that is both or all the partners deals in a way which is
beneficial for all of them. In this regard the top management of IKEA is responsible to identify
different customer segment and manage them properly.
Company IKEA adopts out-of-market strategy in its supply chain with a aim to have best
use of their manufacturings. Although there is a problem in Out-of-market strategy that is it only
serves to meet local demand with less customisation backed by highest density value in product.
This stops IKEA to fulfil its international demand effectively to gain competitive advantage at
global level. Such issue acts as a roadblock for company to fix deals in international market.
Managers way to respond such critical issue in organisation
Managers in an organisation is treated as key personal who is responsible and
accountable for managing its departmental activities and functions. It is managers duty to
identify issues if occurs any along with their possible solution that can resolve and bring work
back on track.
Supply chain managers of IKEA responds to above mentioned problem by adoption of
various strategies within an organisation that helps them to resolve and sort such issue
7
Paraphrase This Document
Need a fresh take? Get an instant paraphrase of this document with our AI Paraphraser
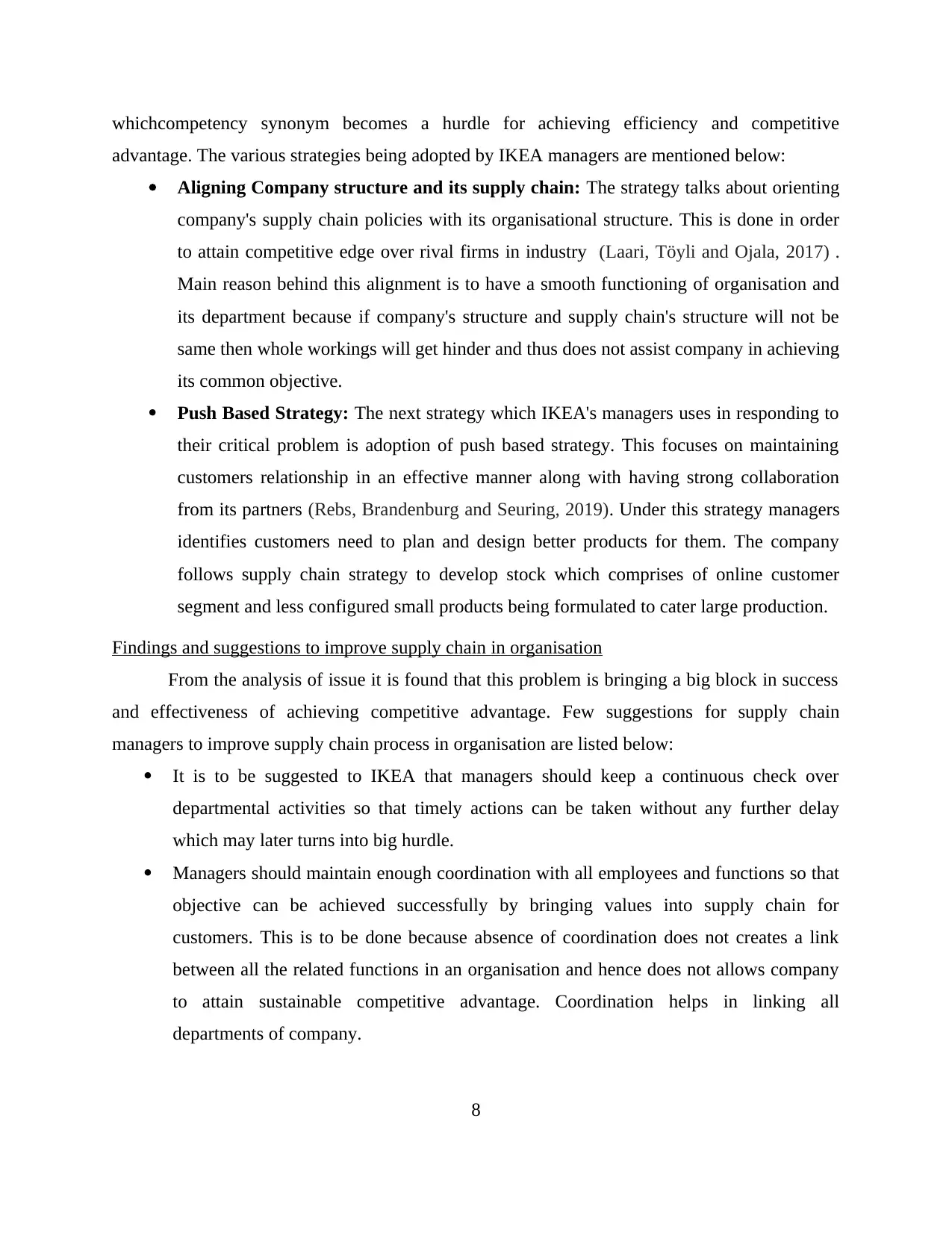
whichcompetency synonym becomes a hurdle for achieving efficiency and competitive
advantage. The various strategies being adopted by IKEA managers are mentioned below:
Aligning Company structure and its supply chain: The strategy talks about orienting
company's supply chain policies with its organisational structure. This is done in order
to attain competitive edge over rival firms in industry (Laari, Töyli and Ojala, 2017) .
Main reason behind this alignment is to have a smooth functioning of organisation and
its department because if company's structure and supply chain's structure will not be
same then whole workings will get hinder and thus does not assist company in achieving
its common objective.
Push Based Strategy: The next strategy which IKEA's managers uses in responding to
their critical problem is adoption of push based strategy. This focuses on maintaining
customers relationship in an effective manner along with having strong collaboration
from its partners (Rebs, Brandenburg and Seuring, 2019). Under this strategy managers
identifies customers need to plan and design better products for them. The company
follows supply chain strategy to develop stock which comprises of online customer
segment and less configured small products being formulated to cater large production.
Findings and suggestions to improve supply chain in organisation
From the analysis of issue it is found that this problem is bringing a big block in success
and effectiveness of achieving competitive advantage. Few suggestions for supply chain
managers to improve supply chain process in organisation are listed below:
It is to be suggested to IKEA that managers should keep a continuous check over
departmental activities so that timely actions can be taken without any further delay
which may later turns into big hurdle.
Managers should maintain enough coordination with all employees and functions so that
objective can be achieved successfully by bringing values into supply chain for
customers. This is to be done because absence of coordination does not creates a link
between all the related functions in an organisation and hence does not allows company
to attain sustainable competitive advantage. Coordination helps in linking all
departments of company.
8
advantage. The various strategies being adopted by IKEA managers are mentioned below:
Aligning Company structure and its supply chain: The strategy talks about orienting
company's supply chain policies with its organisational structure. This is done in order
to attain competitive edge over rival firms in industry (Laari, Töyli and Ojala, 2017) .
Main reason behind this alignment is to have a smooth functioning of organisation and
its department because if company's structure and supply chain's structure will not be
same then whole workings will get hinder and thus does not assist company in achieving
its common objective.
Push Based Strategy: The next strategy which IKEA's managers uses in responding to
their critical problem is adoption of push based strategy. This focuses on maintaining
customers relationship in an effective manner along with having strong collaboration
from its partners (Rebs, Brandenburg and Seuring, 2019). Under this strategy managers
identifies customers need to plan and design better products for them. The company
follows supply chain strategy to develop stock which comprises of online customer
segment and less configured small products being formulated to cater large production.
Findings and suggestions to improve supply chain in organisation
From the analysis of issue it is found that this problem is bringing a big block in success
and effectiveness of achieving competitive advantage. Few suggestions for supply chain
managers to improve supply chain process in organisation are listed below:
It is to be suggested to IKEA that managers should keep a continuous check over
departmental activities so that timely actions can be taken without any further delay
which may later turns into big hurdle.
Managers should maintain enough coordination with all employees and functions so that
objective can be achieved successfully by bringing values into supply chain for
customers. This is to be done because absence of coordination does not creates a link
between all the related functions in an organisation and hence does not allows company
to attain sustainable competitive advantage. Coordination helps in linking all
departments of company.
8
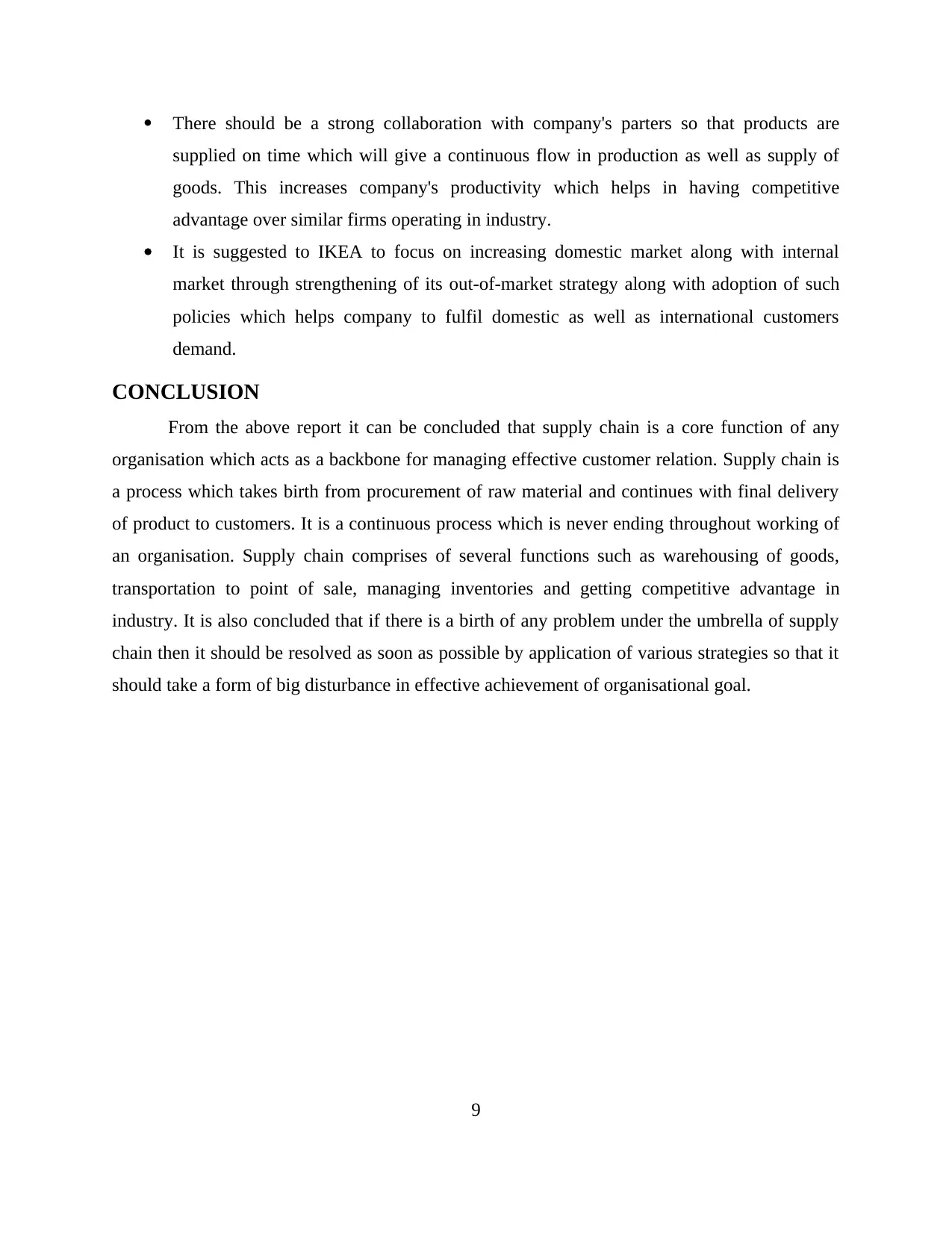
There should be a strong collaboration with company's parters so that products are
supplied on time which will give a continuous flow in production as well as supply of
goods. This increases company's productivity which helps in having competitive
advantage over similar firms operating in industry.
It is suggested to IKEA to focus on increasing domestic market along with internal
market through strengthening of its out-of-market strategy along with adoption of such
policies which helps company to fulfil domestic as well as international customers
demand.
CONCLUSION
From the above report it can be concluded that supply chain is a core function of any
organisation which acts as a backbone for managing effective customer relation. Supply chain is
a process which takes birth from procurement of raw material and continues with final delivery
of product to customers. It is a continuous process which is never ending throughout working of
an organisation. Supply chain comprises of several functions such as warehousing of goods,
transportation to point of sale, managing inventories and getting competitive advantage in
industry. It is also concluded that if there is a birth of any problem under the umbrella of supply
chain then it should be resolved as soon as possible by application of various strategies so that it
should take a form of big disturbance in effective achievement of organisational goal.
9
supplied on time which will give a continuous flow in production as well as supply of
goods. This increases company's productivity which helps in having competitive
advantage over similar firms operating in industry.
It is suggested to IKEA to focus on increasing domestic market along with internal
market through strengthening of its out-of-market strategy along with adoption of such
policies which helps company to fulfil domestic as well as international customers
demand.
CONCLUSION
From the above report it can be concluded that supply chain is a core function of any
organisation which acts as a backbone for managing effective customer relation. Supply chain is
a process which takes birth from procurement of raw material and continues with final delivery
of product to customers. It is a continuous process which is never ending throughout working of
an organisation. Supply chain comprises of several functions such as warehousing of goods,
transportation to point of sale, managing inventories and getting competitive advantage in
industry. It is also concluded that if there is a birth of any problem under the umbrella of supply
chain then it should be resolved as soon as possible by application of various strategies so that it
should take a form of big disturbance in effective achievement of organisational goal.
9
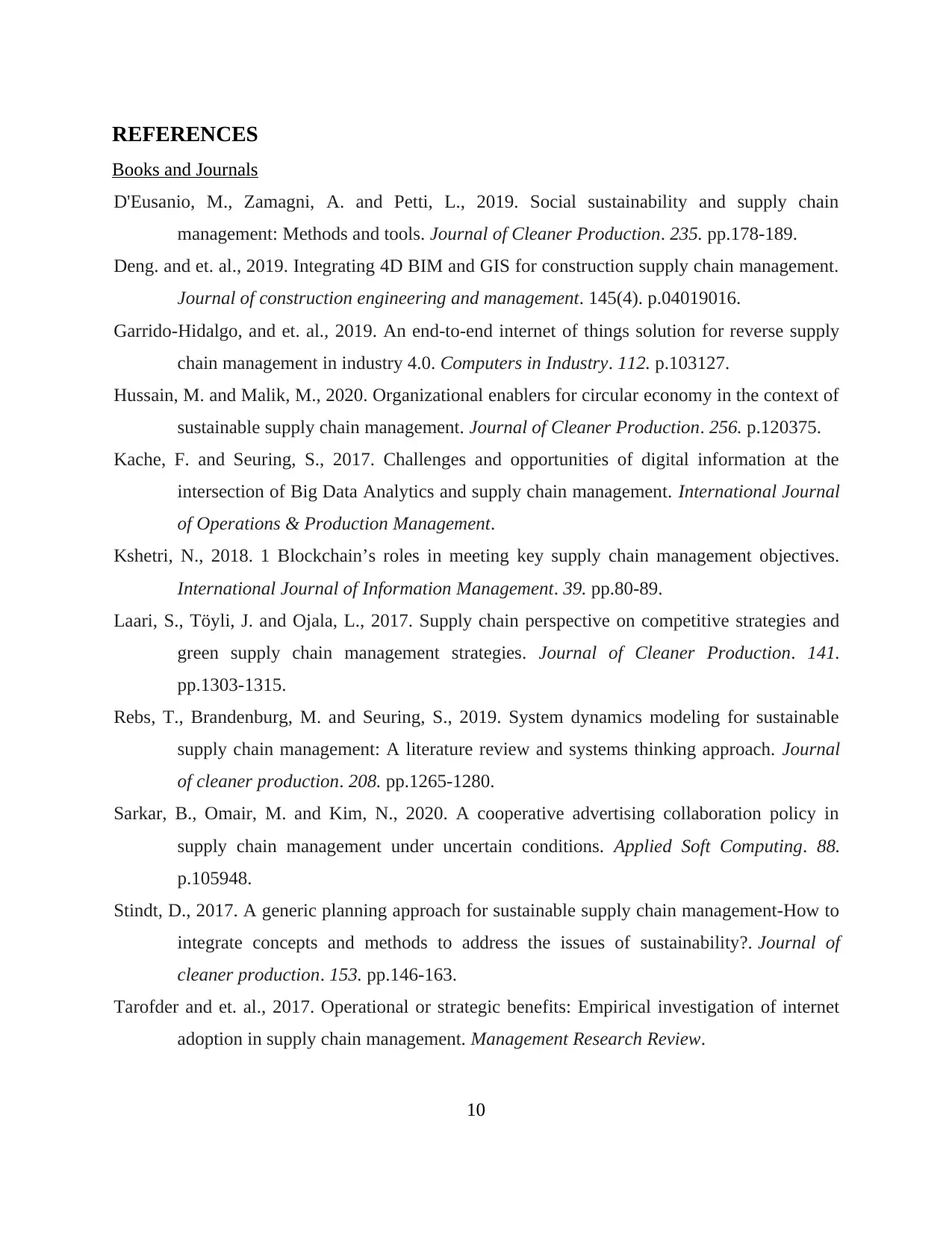
REFERENCES
Books and Journals
D'Eusanio, M., Zamagni, A. and Petti, L., 2019. Social sustainability and supply chain
management: Methods and tools. Journal of Cleaner Production. 235. pp.178-189.
Deng. and et. al., 2019. Integrating 4D BIM and GIS for construction supply chain management.
Journal of construction engineering and management. 145(4). p.04019016.
Garrido-Hidalgo, and et. al., 2019. An end-to-end internet of things solution for reverse supply
chain management in industry 4.0. Computers in Industry. 112. p.103127.
Hussain, M. and Malik, M., 2020. Organizational enablers for circular economy in the context of
sustainable supply chain management. Journal of Cleaner Production. 256. p.120375.
Kache, F. and Seuring, S., 2017. Challenges and opportunities of digital information at the
intersection of Big Data Analytics and supply chain management. International Journal
of Operations & Production Management.
Kshetri, N., 2018. 1 Blockchain’s roles in meeting key supply chain management objectives.
International Journal of Information Management. 39. pp.80-89.
Laari, S., Töyli, J. and Ojala, L., 2017. Supply chain perspective on competitive strategies and
green supply chain management strategies. Journal of Cleaner Production. 141.
pp.1303-1315.
Rebs, T., Brandenburg, M. and Seuring, S., 2019. System dynamics modeling for sustainable
supply chain management: A literature review and systems thinking approach. Journal
of cleaner production. 208. pp.1265-1280.
Sarkar, B., Omair, M. and Kim, N., 2020. A cooperative advertising collaboration policy in
supply chain management under uncertain conditions. Applied Soft Computing. 88.
p.105948.
Stindt, D., 2017. A generic planning approach for sustainable supply chain management-How to
integrate concepts and methods to address the issues of sustainability?. Journal of
cleaner production. 153. pp.146-163.
Tarofder and et. al., 2017. Operational or strategic benefits: Empirical investigation of internet
adoption in supply chain management. Management Research Review.
10
Books and Journals
D'Eusanio, M., Zamagni, A. and Petti, L., 2019. Social sustainability and supply chain
management: Methods and tools. Journal of Cleaner Production. 235. pp.178-189.
Deng. and et. al., 2019. Integrating 4D BIM and GIS for construction supply chain management.
Journal of construction engineering and management. 145(4). p.04019016.
Garrido-Hidalgo, and et. al., 2019. An end-to-end internet of things solution for reverse supply
chain management in industry 4.0. Computers in Industry. 112. p.103127.
Hussain, M. and Malik, M., 2020. Organizational enablers for circular economy in the context of
sustainable supply chain management. Journal of Cleaner Production. 256. p.120375.
Kache, F. and Seuring, S., 2017. Challenges and opportunities of digital information at the
intersection of Big Data Analytics and supply chain management. International Journal
of Operations & Production Management.
Kshetri, N., 2018. 1 Blockchain’s roles in meeting key supply chain management objectives.
International Journal of Information Management. 39. pp.80-89.
Laari, S., Töyli, J. and Ojala, L., 2017. Supply chain perspective on competitive strategies and
green supply chain management strategies. Journal of Cleaner Production. 141.
pp.1303-1315.
Rebs, T., Brandenburg, M. and Seuring, S., 2019. System dynamics modeling for sustainable
supply chain management: A literature review and systems thinking approach. Journal
of cleaner production. 208. pp.1265-1280.
Sarkar, B., Omair, M. and Kim, N., 2020. A cooperative advertising collaboration policy in
supply chain management under uncertain conditions. Applied Soft Computing. 88.
p.105948.
Stindt, D., 2017. A generic planning approach for sustainable supply chain management-How to
integrate concepts and methods to address the issues of sustainability?. Journal of
cleaner production. 153. pp.146-163.
Tarofder and et. al., 2017. Operational or strategic benefits: Empirical investigation of internet
adoption in supply chain management. Management Research Review.
10
Secure Best Marks with AI Grader
Need help grading? Try our AI Grader for instant feedback on your assignments.
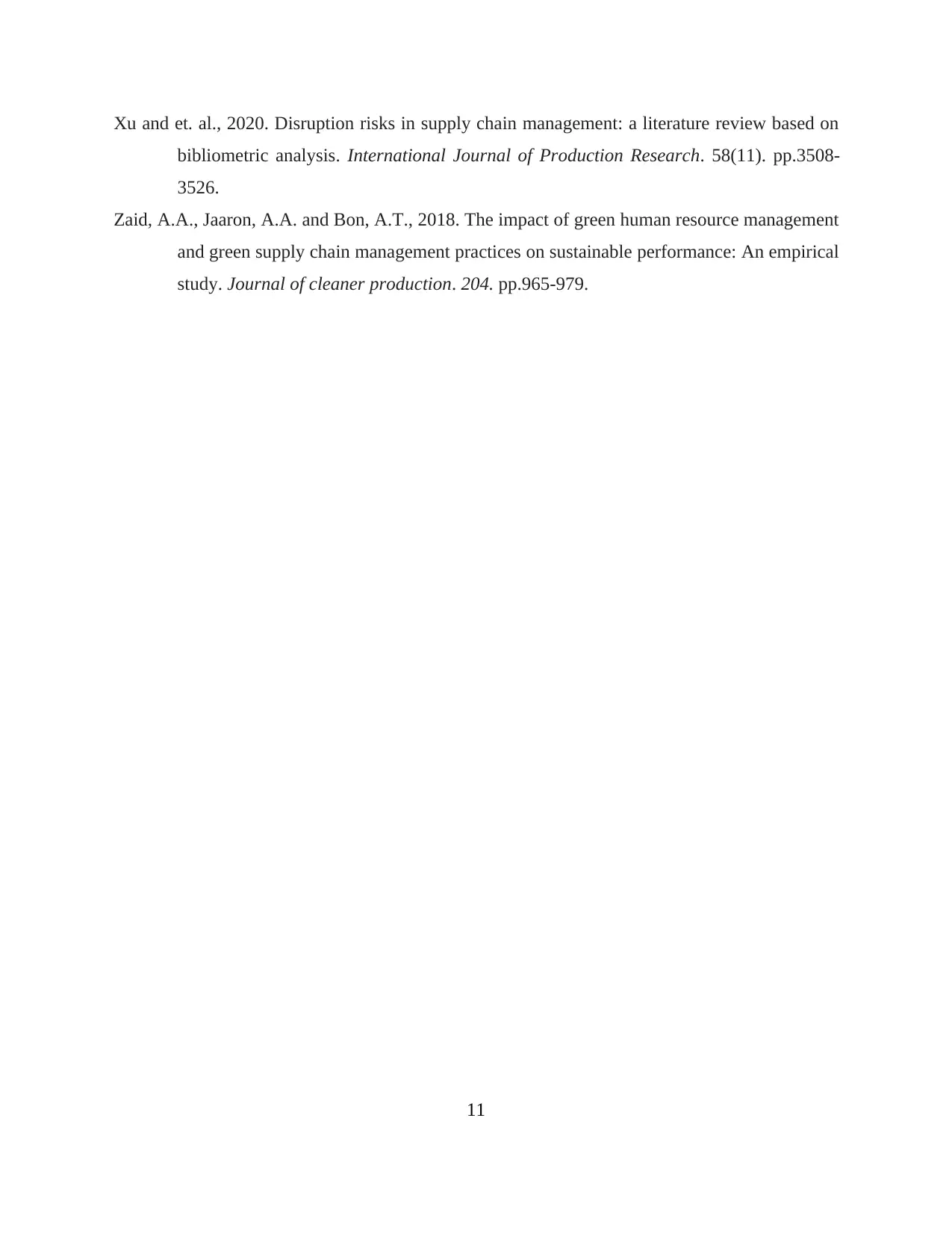
Xu and et. al., 2020. Disruption risks in supply chain management: a literature review based on
bibliometric analysis. International Journal of Production Research. 58(11). pp.3508-
3526.
Zaid, A.A., Jaaron, A.A. and Bon, A.T., 2018. The impact of green human resource management
and green supply chain management practices on sustainable performance: An empirical
study. Journal of cleaner production. 204. pp.965-979.
11
bibliometric analysis. International Journal of Production Research. 58(11). pp.3508-
3526.
Zaid, A.A., Jaaron, A.A. and Bon, A.T., 2018. The impact of green human resource management
and green supply chain management practices on sustainable performance: An empirical
study. Journal of cleaner production. 204. pp.965-979.
11
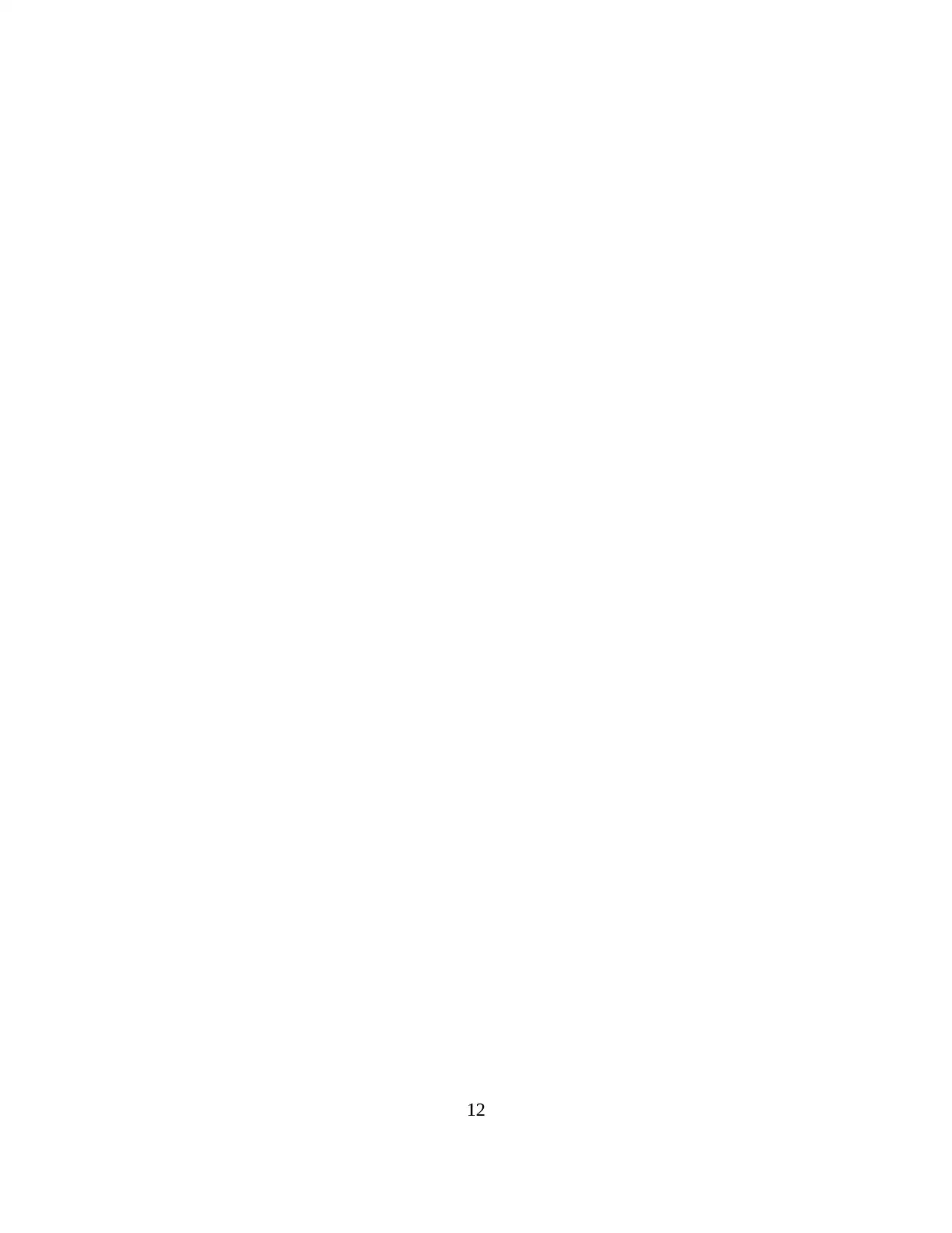
12
1 out of 12
Related Documents
![[object Object]](/_next/image/?url=%2F_next%2Fstatic%2Fmedia%2Flogo.6d15ce61.png&w=640&q=75)
Your All-in-One AI-Powered Toolkit for Academic Success.
+13062052269
info@desklib.com
Available 24*7 on WhatsApp / Email
Unlock your academic potential
© 2024 | Zucol Services PVT LTD | All rights reserved.