Supply Chain Management in IKEA
Added on 2022-12-27
12 Pages3027 Words36 Views
SUPPLY CHAIN
MANAGEMENT
1
MANAGEMENT
1
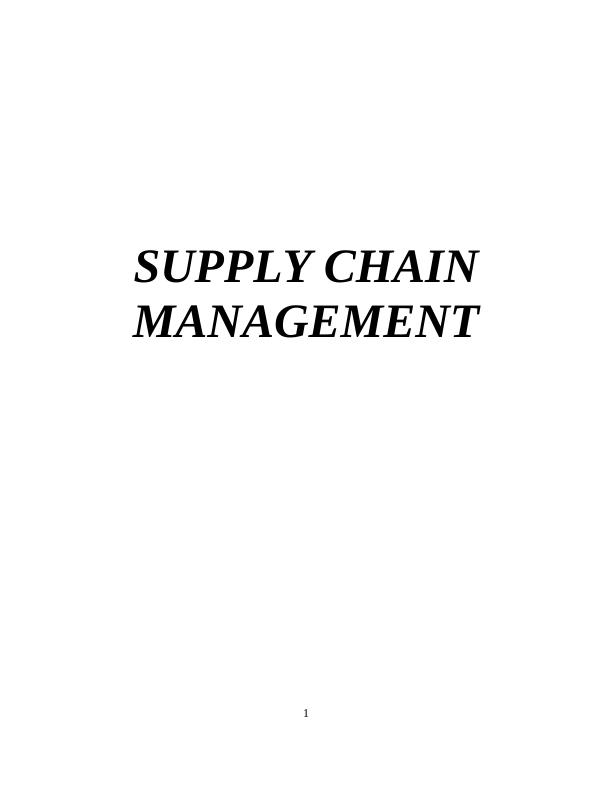
Table of Contents
INTRODUCTION ..........................................................................................................................2
TASK 1............................................................................................................................................3
Supply Chain Management in IKEA...............................................................................................3
Customer Service (Inventory Management)...............................................................................3
Transportation.............................................................................................................................4
Warehousing (Capacity Management)........................................................................................4
Competitive Advantage ..............................................................................................................5
TASK 2............................................................................................................................................7
Critical issue emerging in IKEA.................................................................................................7
Managers way to respond such critical issue in organisation.....................................................7
Findings and suggestions to improve supply chain in organisation............................................8
CONCLUSION ...............................................................................................................................9
REFERENCES..............................................................................................................................10
INTRODUCTION
Supply chain management refers to a procedure for managing and organising goods or
services flow started right from procurement of raw material to final delivery of finished
products. It is a major area of operation in organisation which aims at maximising buyers values
and also attain competitive advantage for the firm. A manager responsible for this department is
called as Supply chain manager whose main job is to coordinate all logistics of supply chain that
includes strategic planning, sources of procuring raw material, manufacturing and delivery of
final products also managing return policy for defected items (D'Eusanio, Zamagni and Petti,
2019). In present report the same concept is applied in context of IKEA company discussing
various components such as its customer service, transportation, warehousing, its competitive
advantage. Further an issue prevailing in company is analysed along with its solution and certain
recommendation made to IKEA so that such issues did not take birth again in course of business.
2
INTRODUCTION ..........................................................................................................................2
TASK 1............................................................................................................................................3
Supply Chain Management in IKEA...............................................................................................3
Customer Service (Inventory Management)...............................................................................3
Transportation.............................................................................................................................4
Warehousing (Capacity Management)........................................................................................4
Competitive Advantage ..............................................................................................................5
TASK 2............................................................................................................................................7
Critical issue emerging in IKEA.................................................................................................7
Managers way to respond such critical issue in organisation.....................................................7
Findings and suggestions to improve supply chain in organisation............................................8
CONCLUSION ...............................................................................................................................9
REFERENCES..............................................................................................................................10
INTRODUCTION
Supply chain management refers to a procedure for managing and organising goods or
services flow started right from procurement of raw material to final delivery of finished
products. It is a major area of operation in organisation which aims at maximising buyers values
and also attain competitive advantage for the firm. A manager responsible for this department is
called as Supply chain manager whose main job is to coordinate all logistics of supply chain that
includes strategic planning, sources of procuring raw material, manufacturing and delivery of
final products also managing return policy for defected items (D'Eusanio, Zamagni and Petti,
2019). In present report the same concept is applied in context of IKEA company discussing
various components such as its customer service, transportation, warehousing, its competitive
advantage. Further an issue prevailing in company is analysed along with its solution and certain
recommendation made to IKEA so that such issues did not take birth again in course of business.
2
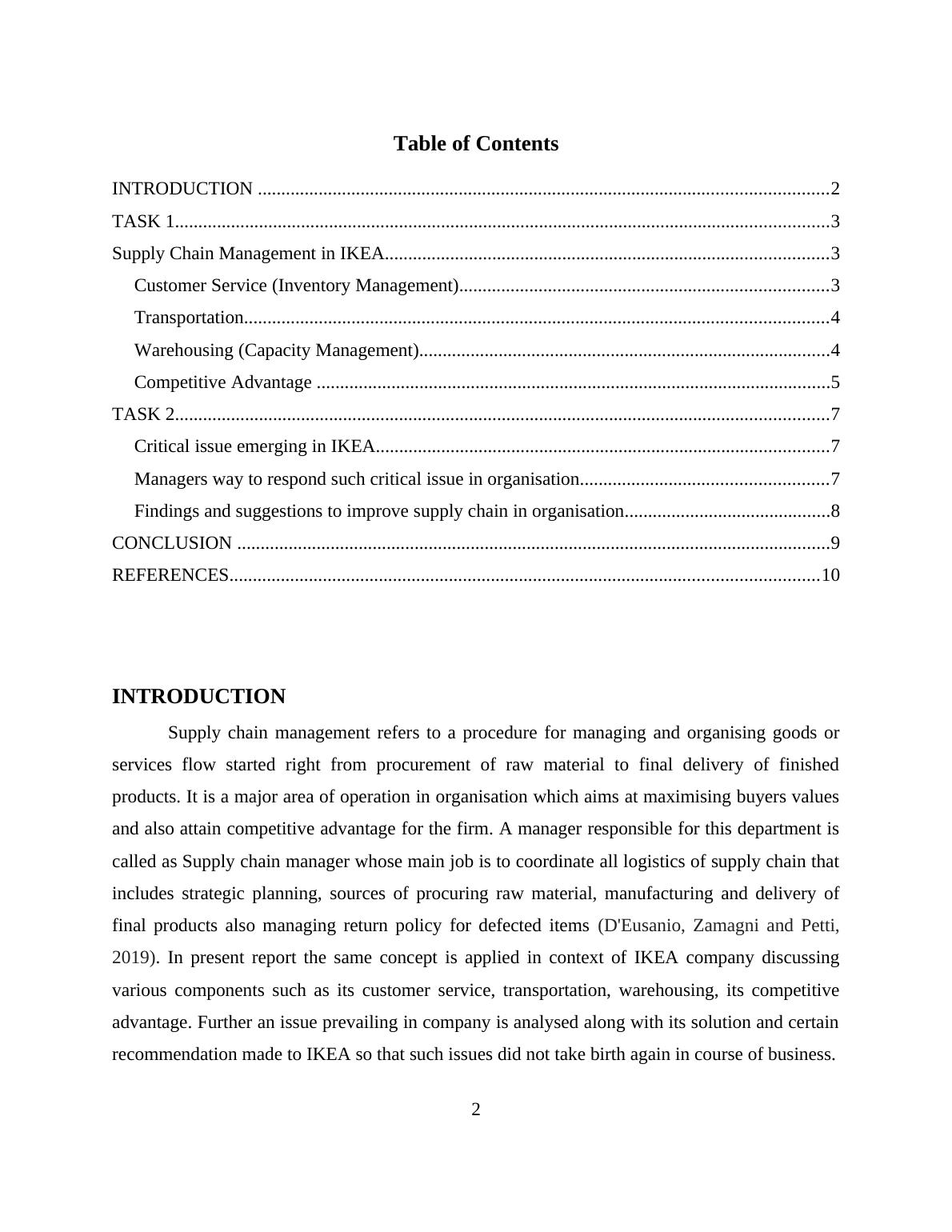
TASK 1
Supply Chain Management in IKEA
Customer Service (Inventory Management)
The term customer service refers to a face to face or telephonic conversation directly with
company's customers by their representative on behalf of an organisation. Customer service is a
key to satisfy company's potential buyers as this the on;y way through which their queries can be
solved or feedback can be collected in order to improve product. This involves providing
assistance to those customers who buys company's product or services and fulfils their demand
(Deng and et. al., 2019). In order to have better customer experience and good brand image it is
very necessary for every company to strengthen its customer service department and satisfy their
customers needs to the fullest. Some companies maintains a separate department or customer
relationship management in their organisation which is sole responsible in handling customers
queries and satisfying their demands by providing best service of their business.
Inventory management refers to a process of managing and arranging inventories such as
raw material or equipments which are necessary for day to day operations of company (Garrido-
Hidalgo and et. al., 2019). This comprises procurement, arrangement and selling of both kinds of
goods that is raw material or final goods into market.
IKEA is a retailer company based in United Kingdom dealing in home furnishing items.
Company is having more than 400 stores expanded in more than 50 countries across world. The
inventory management by IKEA is in a way that can store approx 9500 products in its store at
one time. IKEA's authorised employees orders inventory when needed in organisation for further
production after identification of items and logistics requirement. After the production of final
product company then delivers its items to its outlets for sale. Company keeps few concepts of
inventory management in mind such as Cost-per-touch, Maximum/Minimum Replenishment or
High-Flow/Low-Flow technique.
The company manages its customers satisfaction by accepting back all those items in
warranty period by consumption of which the buyers did not gets satisfied.
3
Supply Chain Management in IKEA
Customer Service (Inventory Management)
The term customer service refers to a face to face or telephonic conversation directly with
company's customers by their representative on behalf of an organisation. Customer service is a
key to satisfy company's potential buyers as this the on;y way through which their queries can be
solved or feedback can be collected in order to improve product. This involves providing
assistance to those customers who buys company's product or services and fulfils their demand
(Deng and et. al., 2019). In order to have better customer experience and good brand image it is
very necessary for every company to strengthen its customer service department and satisfy their
customers needs to the fullest. Some companies maintains a separate department or customer
relationship management in their organisation which is sole responsible in handling customers
queries and satisfying their demands by providing best service of their business.
Inventory management refers to a process of managing and arranging inventories such as
raw material or equipments which are necessary for day to day operations of company (Garrido-
Hidalgo and et. al., 2019). This comprises procurement, arrangement and selling of both kinds of
goods that is raw material or final goods into market.
IKEA is a retailer company based in United Kingdom dealing in home furnishing items.
Company is having more than 400 stores expanded in more than 50 countries across world. The
inventory management by IKEA is in a way that can store approx 9500 products in its store at
one time. IKEA's authorised employees orders inventory when needed in organisation for further
production after identification of items and logistics requirement. After the production of final
product company then delivers its items to its outlets for sale. Company keeps few concepts of
inventory management in mind such as Cost-per-touch, Maximum/Minimum Replenishment or
High-Flow/Low-Flow technique.
The company manages its customers satisfaction by accepting back all those items in
warranty period by consumption of which the buyers did not gets satisfied.
3
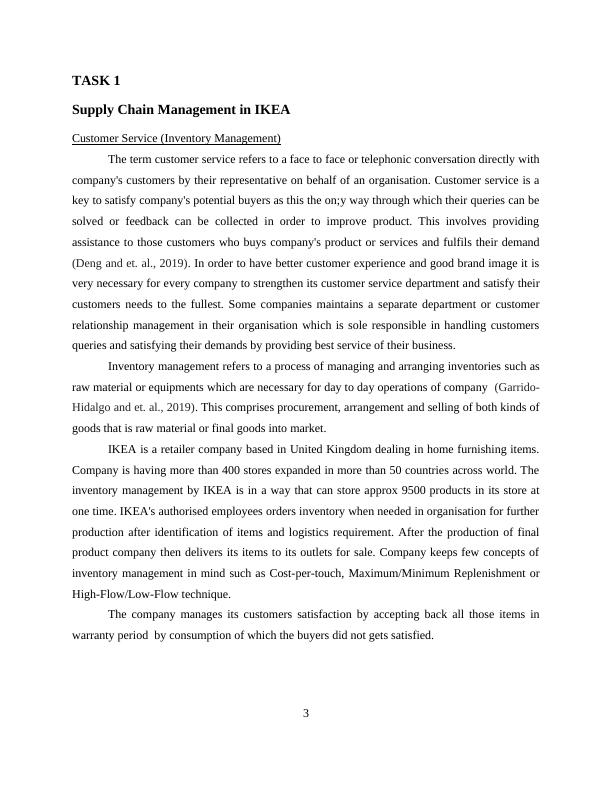
Transportation
Transportation refers to a mode of delivery which every company uses to shift their
goods produced in factory to market for the purpose of sale. This is the only source through
which organisations delivers their items to potential buyers who in turn helps company in
generating higher profits (Hussain and Malik, 2020). The cost involved in transportation is
included in final price of goods which are required to be paid by customers. Company has an
option of choosing mode of transport that can be either by road, by rail, airways or sea ways
mode of transportation.
IKEA adopts rail transportation in its organisation to transfer product from factory to its
physical stores which finally delivers to the buyers in market. Company aims in reducing,
replacing and rethinking good transportation agenda in their principles. IKEA tries to use less
fuel as high as possible in transportation of goods in order to save environment from pollution.
An element of replacing by IKEA aims restoring fossil fuels with high alternatives for
sustainability along with a low carbon emission in air. In the category of rethinking, IKEA works
actively in attaining CO2 depletion by alternative use of different mode of transportation such as
sea or rail ways.
Warehousing (Capacity Management)
Warehousing refers to a place where company's raw material or final goods are kept as
storage with immense safety after production or procurement for the purpose of future sale
(Kache and Seuring, 2017). Companies can either have its own warehouse or can store its
products on other's warehouse by providing them rent or can have on lease. Big multinational
giants has their own warehouses because of large scale of operations and production. By this
companies manages their stock so that at the time of high demand there should not fall short of
supply.
IKEA bears a huge warehouse having capacity of storing more than 9500 items in it. The
company comprises of High-flow and Low-Flow warehouses under its own name. Low Flow
warehouse of IKEA stands at manual whereas High Flow provides facility of storing 80 percent
products under its shed. High flow warehouse of company has a technology of retrieval system
and automatic storage to lower down its cost-per-touch. The items which are kept in low flow
warehouse are of nature that use to carry low demand in market.
4
Transportation refers to a mode of delivery which every company uses to shift their
goods produced in factory to market for the purpose of sale. This is the only source through
which organisations delivers their items to potential buyers who in turn helps company in
generating higher profits (Hussain and Malik, 2020). The cost involved in transportation is
included in final price of goods which are required to be paid by customers. Company has an
option of choosing mode of transport that can be either by road, by rail, airways or sea ways
mode of transportation.
IKEA adopts rail transportation in its organisation to transfer product from factory to its
physical stores which finally delivers to the buyers in market. Company aims in reducing,
replacing and rethinking good transportation agenda in their principles. IKEA tries to use less
fuel as high as possible in transportation of goods in order to save environment from pollution.
An element of replacing by IKEA aims restoring fossil fuels with high alternatives for
sustainability along with a low carbon emission in air. In the category of rethinking, IKEA works
actively in attaining CO2 depletion by alternative use of different mode of transportation such as
sea or rail ways.
Warehousing (Capacity Management)
Warehousing refers to a place where company's raw material or final goods are kept as
storage with immense safety after production or procurement for the purpose of future sale
(Kache and Seuring, 2017). Companies can either have its own warehouse or can store its
products on other's warehouse by providing them rent or can have on lease. Big multinational
giants has their own warehouses because of large scale of operations and production. By this
companies manages their stock so that at the time of high demand there should not fall short of
supply.
IKEA bears a huge warehouse having capacity of storing more than 9500 items in it. The
company comprises of High-flow and Low-Flow warehouses under its own name. Low Flow
warehouse of IKEA stands at manual whereas High Flow provides facility of storing 80 percent
products under its shed. High flow warehouse of company has a technology of retrieval system
and automatic storage to lower down its cost-per-touch. The items which are kept in low flow
warehouse are of nature that use to carry low demand in market.
4
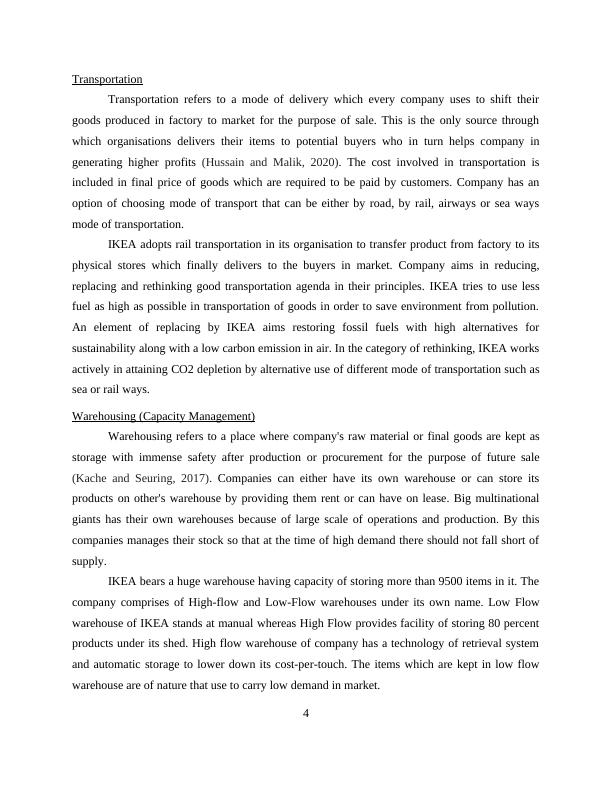
End of preview
Want to access all the pages? Upload your documents or become a member.
Related Documents
Supply Chain Management in IKEAlg...
|12
|3120
|430
Enhancing Supply Chain Management in Sainsburylg...
|11
|3391
|1
Logistics and Supply Chain Management in Tescolg...
|13
|3414
|73
Supply Chain Management in Debenhamslg...
|13
|3353
|74
Supply Chain and Inventory Controllg...
|5
|804
|19
Event Supply and Logistics Introductionlg...
|11
|2841
|157