Introduction to Business Operations and Services 2019
VerifiedAdded on 2023/01/17
|12
|3623
|20
AI Summary
This document provides an introduction to business operations and services, covering topics such as operational improvement strategies, tools and techniques, and gaining market share from Toyota. It discusses the importance of optimizing supply chains and focusing on quality, customer-oriented products, inventory management, and implementing Six Sigma.
Contribute Materials
Your contribution can guide someone’s learning journey. Share your
documents today.
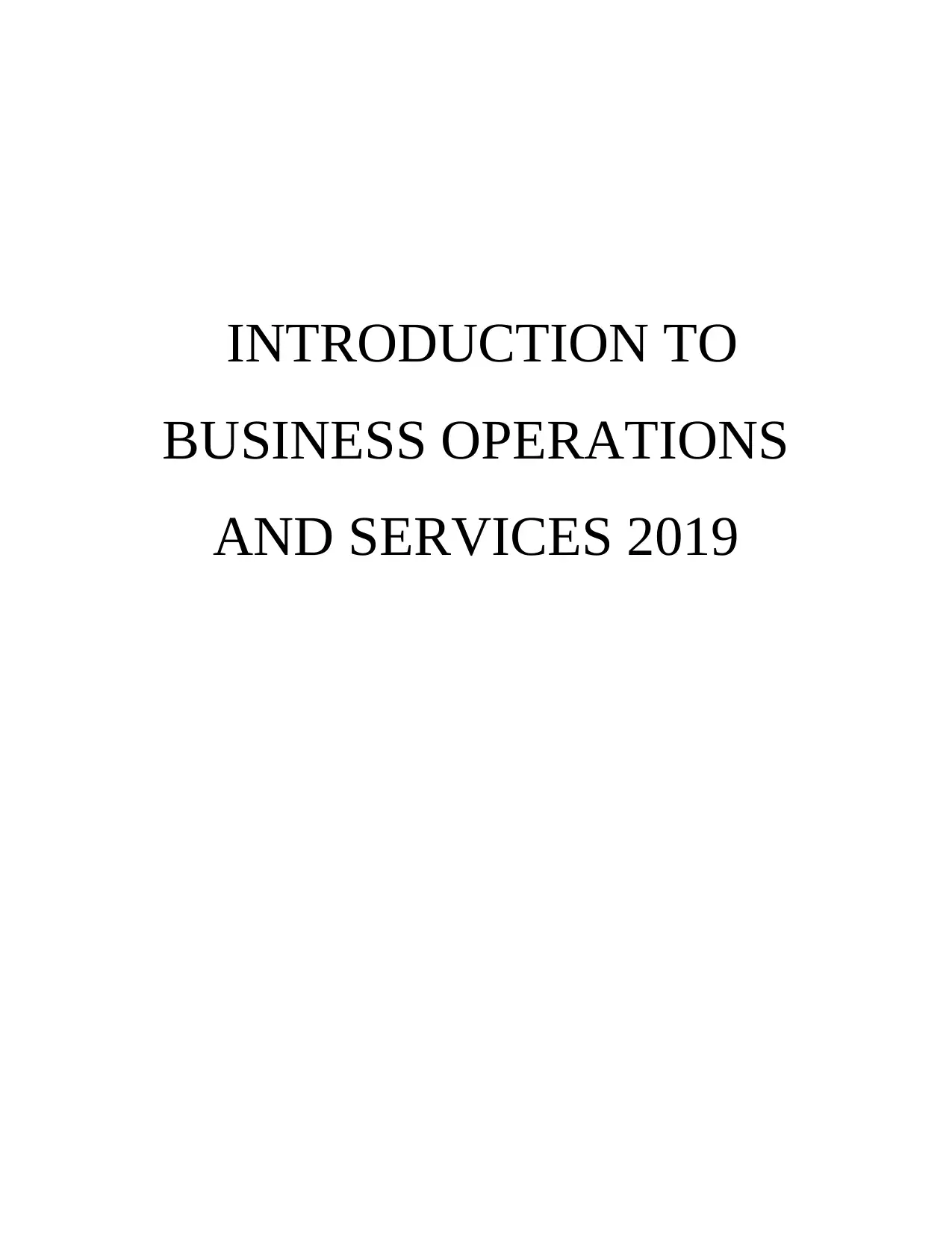
INTRODUCTION TO
BUSINESS OPERATIONS
AND SERVICES 2019
BUSINESS OPERATIONS
AND SERVICES 2019
Secure Best Marks with AI Grader
Need help grading? Try our AI Grader for instant feedback on your assignments.
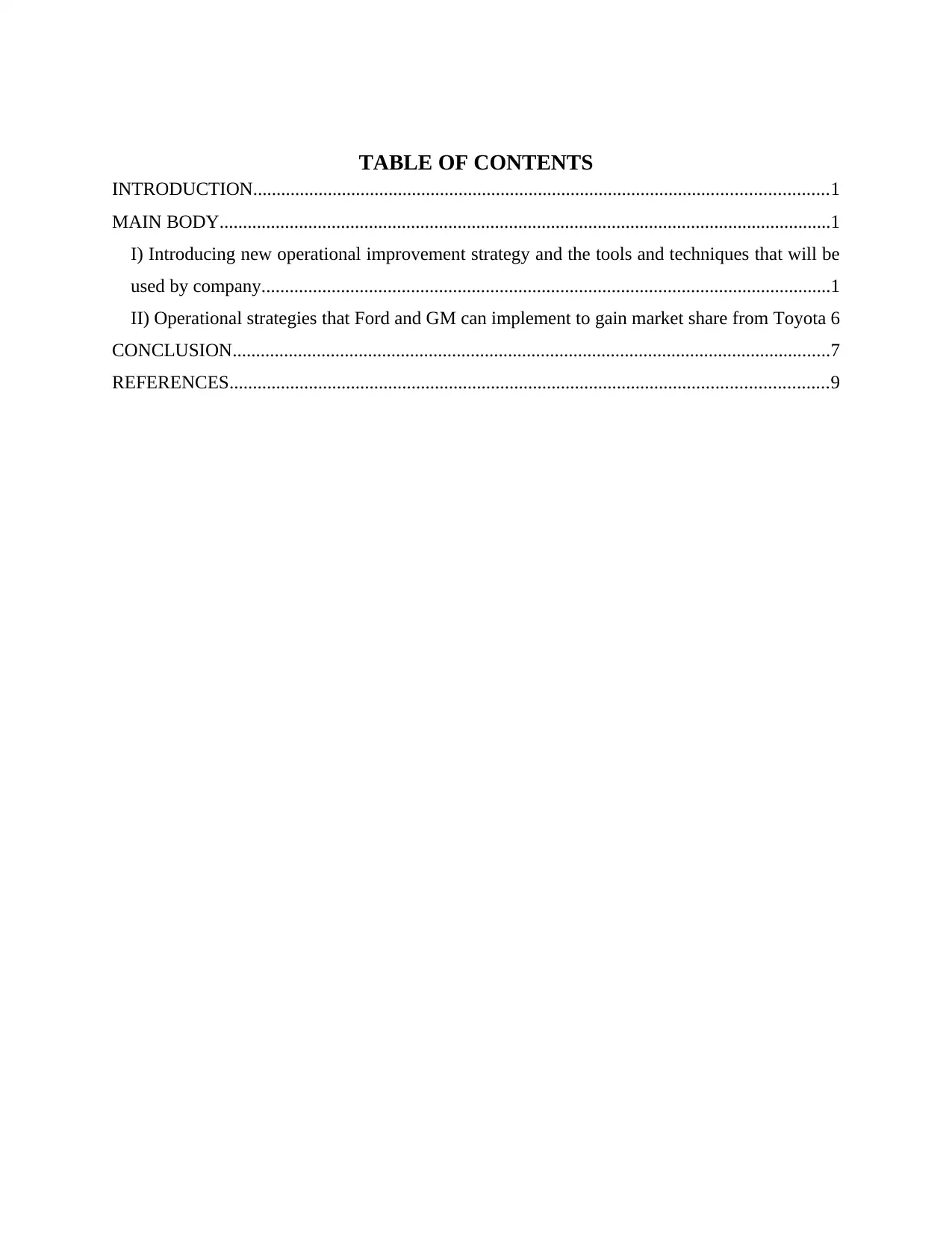
TABLE OF CONTENTS
INTRODUCTION...........................................................................................................................1
MAIN BODY...................................................................................................................................1
I) Introducing new operational improvement strategy and the tools and techniques that will be
used by company..........................................................................................................................1
II) Operational strategies that Ford and GM can implement to gain market share from Toyota 6
CONCLUSION................................................................................................................................7
REFERENCES................................................................................................................................9
INTRODUCTION...........................................................................................................................1
MAIN BODY...................................................................................................................................1
I) Introducing new operational improvement strategy and the tools and techniques that will be
used by company..........................................................................................................................1
II) Operational strategies that Ford and GM can implement to gain market share from Toyota 6
CONCLUSION................................................................................................................................7
REFERENCES................................................................................................................................9
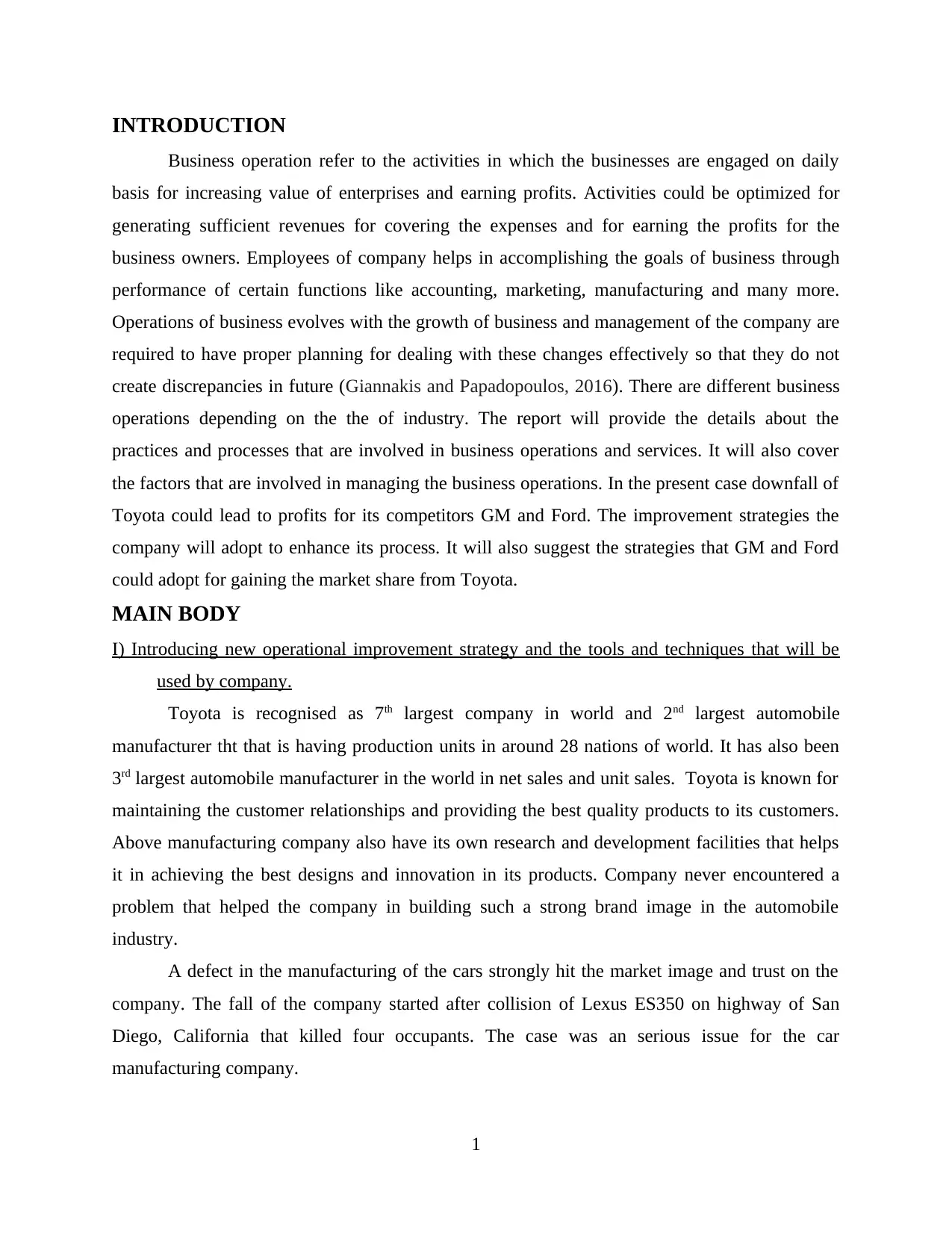
INTRODUCTION
Business operation refer to the activities in which the businesses are engaged on daily
basis for increasing value of enterprises and earning profits. Activities could be optimized for
generating sufficient revenues for covering the expenses and for earning the profits for the
business owners. Employees of company helps in accomplishing the goals of business through
performance of certain functions like accounting, marketing, manufacturing and many more.
Operations of business evolves with the growth of business and management of the company are
required to have proper planning for dealing with these changes effectively so that they do not
create discrepancies in future (Giannakis and Papadopoulos, 2016). There are different business
operations depending on the the of industry. The report will provide the details about the
practices and processes that are involved in business operations and services. It will also cover
the factors that are involved in managing the business operations. In the present case downfall of
Toyota could lead to profits for its competitors GM and Ford. The improvement strategies the
company will adopt to enhance its process. It will also suggest the strategies that GM and Ford
could adopt for gaining the market share from Toyota.
MAIN BODY
I) Introducing new operational improvement strategy and the tools and techniques that will be
used by company.
Toyota is recognised as 7th largest company in world and 2nd largest automobile
manufacturer tht that is having production units in around 28 nations of world. It has also been
3rd largest automobile manufacturer in the world in net sales and unit sales. Toyota is known for
maintaining the customer relationships and providing the best quality products to its customers.
Above manufacturing company also have its own research and development facilities that helps
it in achieving the best designs and innovation in its products. Company never encountered a
problem that helped the company in building such a strong brand image in the automobile
industry.
A defect in the manufacturing of the cars strongly hit the market image and trust on the
company. The fall of the company started after collision of Lexus ES350 on highway of San
Diego, California that killed four occupants. The case was an serious issue for the car
manufacturing company.
1
Business operation refer to the activities in which the businesses are engaged on daily
basis for increasing value of enterprises and earning profits. Activities could be optimized for
generating sufficient revenues for covering the expenses and for earning the profits for the
business owners. Employees of company helps in accomplishing the goals of business through
performance of certain functions like accounting, marketing, manufacturing and many more.
Operations of business evolves with the growth of business and management of the company are
required to have proper planning for dealing with these changes effectively so that they do not
create discrepancies in future (Giannakis and Papadopoulos, 2016). There are different business
operations depending on the the of industry. The report will provide the details about the
practices and processes that are involved in business operations and services. It will also cover
the factors that are involved in managing the business operations. In the present case downfall of
Toyota could lead to profits for its competitors GM and Ford. The improvement strategies the
company will adopt to enhance its process. It will also suggest the strategies that GM and Ford
could adopt for gaining the market share from Toyota.
MAIN BODY
I) Introducing new operational improvement strategy and the tools and techniques that will be
used by company.
Toyota is recognised as 7th largest company in world and 2nd largest automobile
manufacturer tht that is having production units in around 28 nations of world. It has also been
3rd largest automobile manufacturer in the world in net sales and unit sales. Toyota is known for
maintaining the customer relationships and providing the best quality products to its customers.
Above manufacturing company also have its own research and development facilities that helps
it in achieving the best designs and innovation in its products. Company never encountered a
problem that helped the company in building such a strong brand image in the automobile
industry.
A defect in the manufacturing of the cars strongly hit the market image and trust on the
company. The fall of the company started after collision of Lexus ES350 on highway of San
Diego, California that killed four occupants. The case was an serious issue for the car
manufacturing company.
1
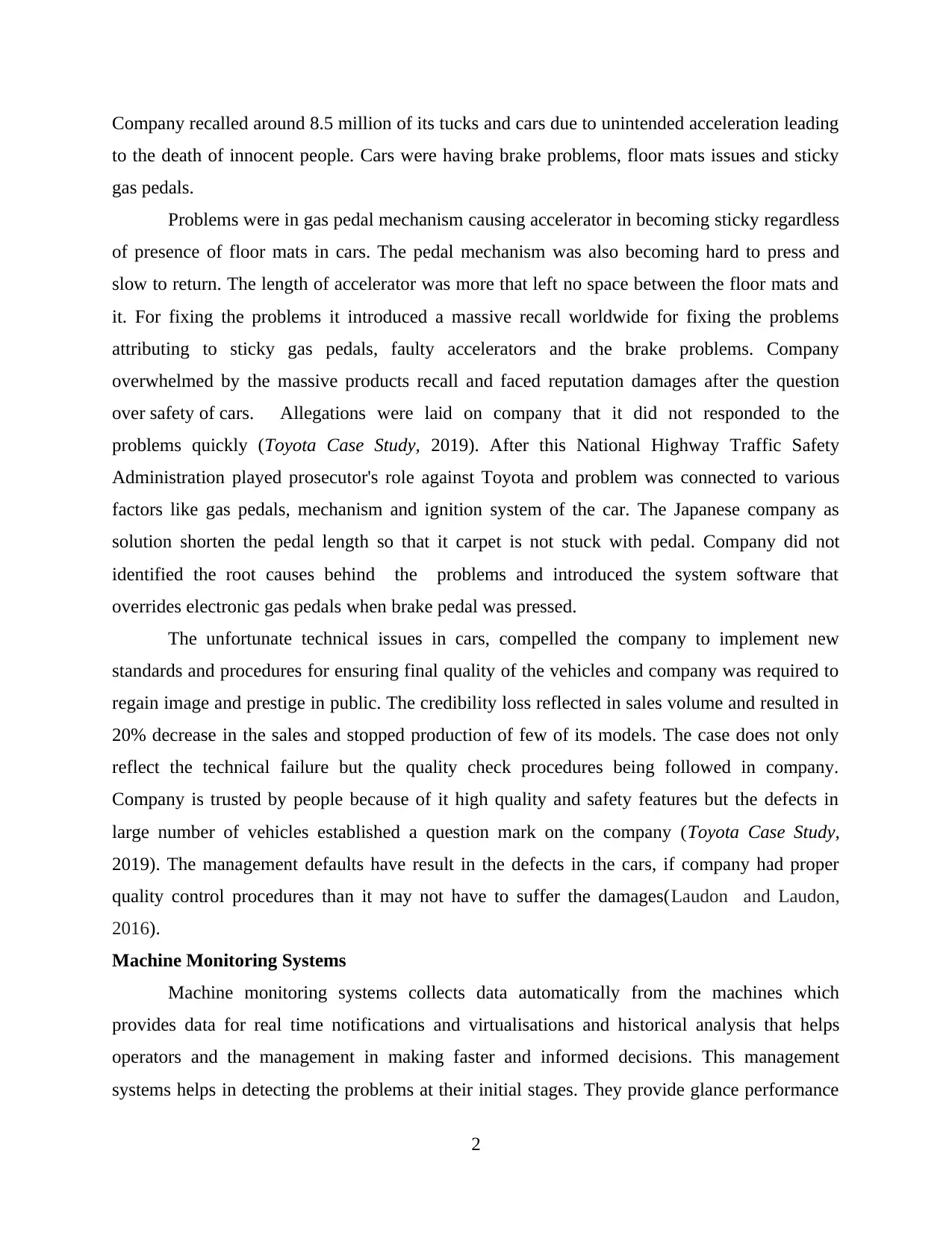
Company recalled around 8.5 million of its tucks and cars due to unintended acceleration leading
to the death of innocent people. Cars were having brake problems, floor mats issues and sticky
gas pedals.
Problems were in gas pedal mechanism causing accelerator in becoming sticky regardless
of presence of floor mats in cars. The pedal mechanism was also becoming hard to press and
slow to return. The length of accelerator was more that left no space between the floor mats and
it. For fixing the problems it introduced a massive recall worldwide for fixing the problems
attributing to sticky gas pedals, faulty accelerators and the brake problems. Company
overwhelmed by the massive products recall and faced reputation damages after the question
over safety of cars. Allegations were laid on company that it did not responded to the
problems quickly (Toyota Case Study, 2019). After this National Highway Traffic Safety
Administration played prosecutor's role against Toyota and problem was connected to various
factors like gas pedals, mechanism and ignition system of the car. The Japanese company as
solution shorten the pedal length so that it carpet is not stuck with pedal. Company did not
identified the root causes behind the problems and introduced the system software that
overrides electronic gas pedals when brake pedal was pressed.
The unfortunate technical issues in cars, compelled the company to implement new
standards and procedures for ensuring final quality of the vehicles and company was required to
regain image and prestige in public. The credibility loss reflected in sales volume and resulted in
20% decrease in the sales and stopped production of few of its models. The case does not only
reflect the technical failure but the quality check procedures being followed in company.
Company is trusted by people because of it high quality and safety features but the defects in
large number of vehicles established a question mark on the company (Toyota Case Study,
2019). The management defaults have result in the defects in the cars, if company had proper
quality control procedures than it may not have to suffer the damages(Laudon and Laudon,
2016).
Machine Monitoring Systems
Machine monitoring systems collects data automatically from the machines which
provides data for real time notifications and virtualisations and historical analysis that helps
operators and the management in making faster and informed decisions. This management
systems helps in detecting the problems at their initial stages. They provide glance performance
2
to the death of innocent people. Cars were having brake problems, floor mats issues and sticky
gas pedals.
Problems were in gas pedal mechanism causing accelerator in becoming sticky regardless
of presence of floor mats in cars. The pedal mechanism was also becoming hard to press and
slow to return. The length of accelerator was more that left no space between the floor mats and
it. For fixing the problems it introduced a massive recall worldwide for fixing the problems
attributing to sticky gas pedals, faulty accelerators and the brake problems. Company
overwhelmed by the massive products recall and faced reputation damages after the question
over safety of cars. Allegations were laid on company that it did not responded to the
problems quickly (Toyota Case Study, 2019). After this National Highway Traffic Safety
Administration played prosecutor's role against Toyota and problem was connected to various
factors like gas pedals, mechanism and ignition system of the car. The Japanese company as
solution shorten the pedal length so that it carpet is not stuck with pedal. Company did not
identified the root causes behind the problems and introduced the system software that
overrides electronic gas pedals when brake pedal was pressed.
The unfortunate technical issues in cars, compelled the company to implement new
standards and procedures for ensuring final quality of the vehicles and company was required to
regain image and prestige in public. The credibility loss reflected in sales volume and resulted in
20% decrease in the sales and stopped production of few of its models. The case does not only
reflect the technical failure but the quality check procedures being followed in company.
Company is trusted by people because of it high quality and safety features but the defects in
large number of vehicles established a question mark on the company (Toyota Case Study,
2019). The management defaults have result in the defects in the cars, if company had proper
quality control procedures than it may not have to suffer the damages(Laudon and Laudon,
2016).
Machine Monitoring Systems
Machine monitoring systems collects data automatically from the machines which
provides data for real time notifications and virtualisations and historical analysis that helps
operators and the management in making faster and informed decisions. This management
systems helps in detecting the problems at their initial stages. They provide glance performance
2
Secure Best Marks with AI Grader
Need help grading? Try our AI Grader for instant feedback on your assignments.
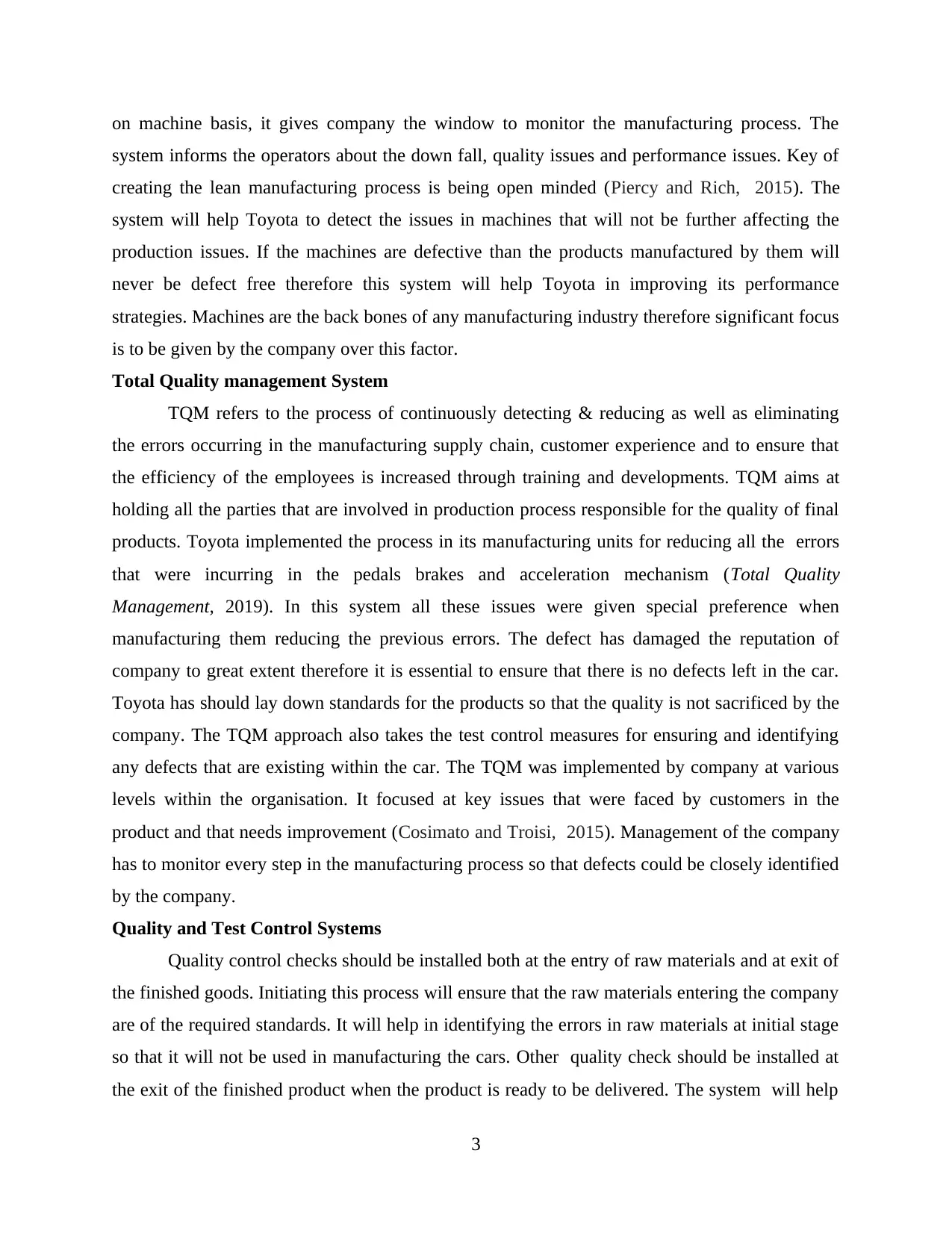
on machine basis, it gives company the window to monitor the manufacturing process. The
system informs the operators about the down fall, quality issues and performance issues. Key of
creating the lean manufacturing process is being open minded (Piercy and Rich, 2015). The
system will help Toyota to detect the issues in machines that will not be further affecting the
production issues. If the machines are defective than the products manufactured by them will
never be defect free therefore this system will help Toyota in improving its performance
strategies. Machines are the back bones of any manufacturing industry therefore significant focus
is to be given by the company over this factor.
Total Quality management System
TQM refers to the process of continuously detecting & reducing as well as eliminating
the errors occurring in the manufacturing supply chain, customer experience and to ensure that
the efficiency of the employees is increased through training and developments. TQM aims at
holding all the parties that are involved in production process responsible for the quality of final
products. Toyota implemented the process in its manufacturing units for reducing all the errors
that were incurring in the pedals brakes and acceleration mechanism (Total Quality
Management, 2019). In this system all these issues were given special preference when
manufacturing them reducing the previous errors. The defect has damaged the reputation of
company to great extent therefore it is essential to ensure that there is no defects left in the car.
Toyota has should lay down standards for the products so that the quality is not sacrificed by the
company. The TQM approach also takes the test control measures for ensuring and identifying
any defects that are existing within the car. The TQM was implemented by company at various
levels within the organisation. It focused at key issues that were faced by customers in the
product and that needs improvement (Cosimato and Troisi, 2015). Management of the company
has to monitor every step in the manufacturing process so that defects could be closely identified
by the company.
Quality and Test Control Systems
Quality control checks should be installed both at the entry of raw materials and at exit of
the finished goods. Initiating this process will ensure that the raw materials entering the company
are of the required standards. It will help in identifying the errors in raw materials at initial stage
so that it will not be used in manufacturing the cars. Other quality check should be installed at
the exit of the finished product when the product is ready to be delivered. The system will help
3
system informs the operators about the down fall, quality issues and performance issues. Key of
creating the lean manufacturing process is being open minded (Piercy and Rich, 2015). The
system will help Toyota to detect the issues in machines that will not be further affecting the
production issues. If the machines are defective than the products manufactured by them will
never be defect free therefore this system will help Toyota in improving its performance
strategies. Machines are the back bones of any manufacturing industry therefore significant focus
is to be given by the company over this factor.
Total Quality management System
TQM refers to the process of continuously detecting & reducing as well as eliminating
the errors occurring in the manufacturing supply chain, customer experience and to ensure that
the efficiency of the employees is increased through training and developments. TQM aims at
holding all the parties that are involved in production process responsible for the quality of final
products. Toyota implemented the process in its manufacturing units for reducing all the errors
that were incurring in the pedals brakes and acceleration mechanism (Total Quality
Management, 2019). In this system all these issues were given special preference when
manufacturing them reducing the previous errors. The defect has damaged the reputation of
company to great extent therefore it is essential to ensure that there is no defects left in the car.
Toyota has should lay down standards for the products so that the quality is not sacrificed by the
company. The TQM approach also takes the test control measures for ensuring and identifying
any defects that are existing within the car. The TQM was implemented by company at various
levels within the organisation. It focused at key issues that were faced by customers in the
product and that needs improvement (Cosimato and Troisi, 2015). Management of the company
has to monitor every step in the manufacturing process so that defects could be closely identified
by the company.
Quality and Test Control Systems
Quality control checks should be installed both at the entry of raw materials and at exit of
the finished goods. Initiating this process will ensure that the raw materials entering the company
are of the required standards. It will help in identifying the errors in raw materials at initial stage
so that it will not be used in manufacturing the cars. Other quality check should be installed at
the exit of the finished product when the product is ready to be delivered. The system will help
3
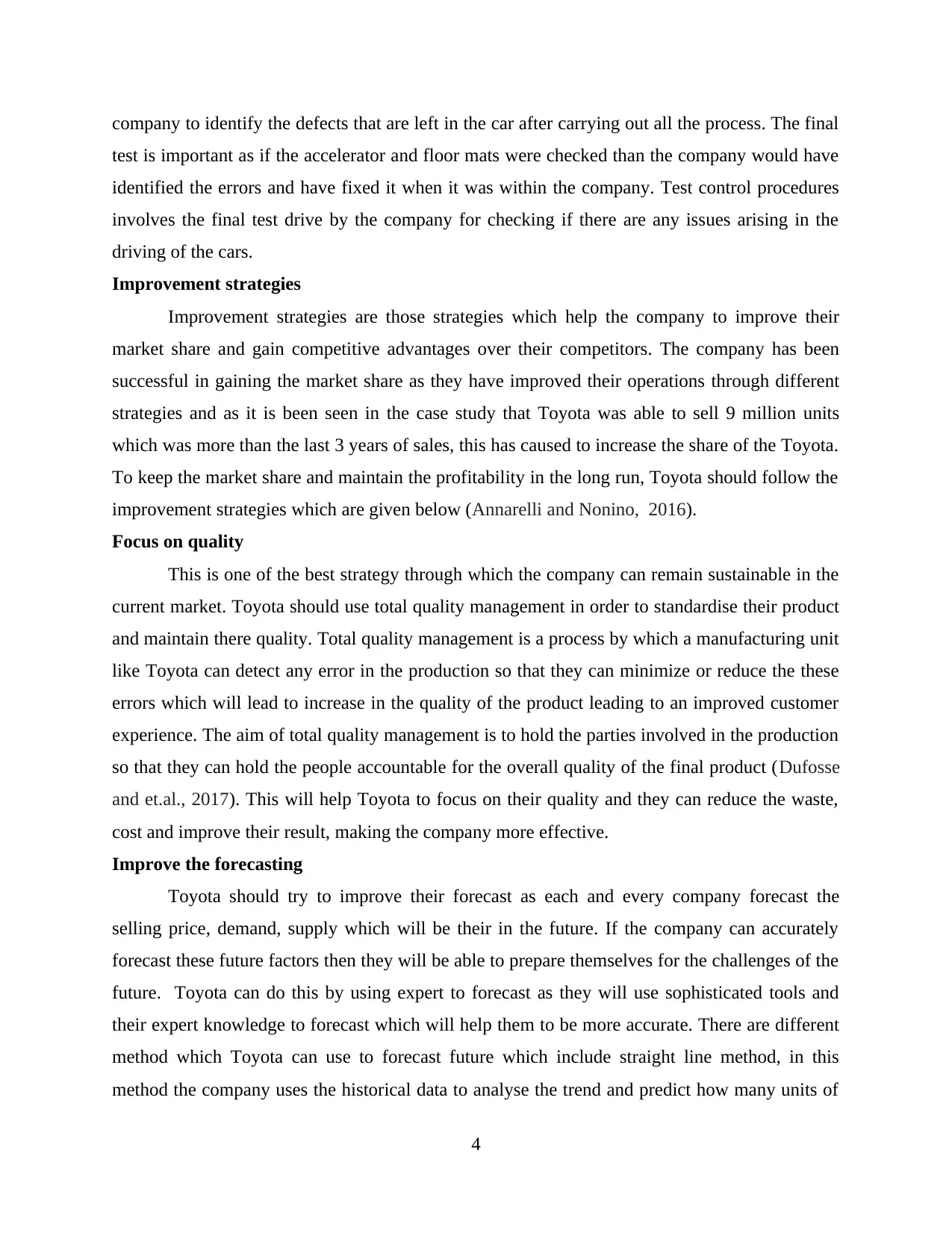
company to identify the defects that are left in the car after carrying out all the process. The final
test is important as if the accelerator and floor mats were checked than the company would have
identified the errors and have fixed it when it was within the company. Test control procedures
involves the final test drive by the company for checking if there are any issues arising in the
driving of the cars.
Improvement strategies
Improvement strategies are those strategies which help the company to improve their
market share and gain competitive advantages over their competitors. The company has been
successful in gaining the market share as they have improved their operations through different
strategies and as it is been seen in the case study that Toyota was able to sell 9 million units
which was more than the last 3 years of sales, this has caused to increase the share of the Toyota.
To keep the market share and maintain the profitability in the long run, Toyota should follow the
improvement strategies which are given below (Annarelli and Nonino, 2016).
Focus on quality
This is one of the best strategy through which the company can remain sustainable in the
current market. Toyota should use total quality management in order to standardise their product
and maintain there quality. Total quality management is a process by which a manufacturing unit
like Toyota can detect any error in the production so that they can minimize or reduce the these
errors which will lead to increase in the quality of the product leading to an improved customer
experience. The aim of total quality management is to hold the parties involved in the production
so that they can hold the people accountable for the overall quality of the final product (Dufosse
and et.al., 2017). This will help Toyota to focus on their quality and they can reduce the waste,
cost and improve their result, making the company more effective.
Improve the forecasting
Toyota should try to improve their forecast as each and every company forecast the
selling price, demand, supply which will be their in the future. If the company can accurately
forecast these future factors then they will be able to prepare themselves for the challenges of the
future. Toyota can do this by using expert to forecast as they will use sophisticated tools and
their expert knowledge to forecast which will help them to be more accurate. There are different
method which Toyota can use to forecast future which include straight line method, in this
method the company uses the historical data to analyse the trend and predict how many units of
4
test is important as if the accelerator and floor mats were checked than the company would have
identified the errors and have fixed it when it was within the company. Test control procedures
involves the final test drive by the company for checking if there are any issues arising in the
driving of the cars.
Improvement strategies
Improvement strategies are those strategies which help the company to improve their
market share and gain competitive advantages over their competitors. The company has been
successful in gaining the market share as they have improved their operations through different
strategies and as it is been seen in the case study that Toyota was able to sell 9 million units
which was more than the last 3 years of sales, this has caused to increase the share of the Toyota.
To keep the market share and maintain the profitability in the long run, Toyota should follow the
improvement strategies which are given below (Annarelli and Nonino, 2016).
Focus on quality
This is one of the best strategy through which the company can remain sustainable in the
current market. Toyota should use total quality management in order to standardise their product
and maintain there quality. Total quality management is a process by which a manufacturing unit
like Toyota can detect any error in the production so that they can minimize or reduce the these
errors which will lead to increase in the quality of the product leading to an improved customer
experience. The aim of total quality management is to hold the parties involved in the production
so that they can hold the people accountable for the overall quality of the final product (Dufosse
and et.al., 2017). This will help Toyota to focus on their quality and they can reduce the waste,
cost and improve their result, making the company more effective.
Improve the forecasting
Toyota should try to improve their forecast as each and every company forecast the
selling price, demand, supply which will be their in the future. If the company can accurately
forecast these future factors then they will be able to prepare themselves for the challenges of the
future. Toyota can do this by using expert to forecast as they will use sophisticated tools and
their expert knowledge to forecast which will help them to be more accurate. There are different
method which Toyota can use to forecast future which include straight line method, in this
method the company uses the historical data to analyse the trend and predict how many units of
4
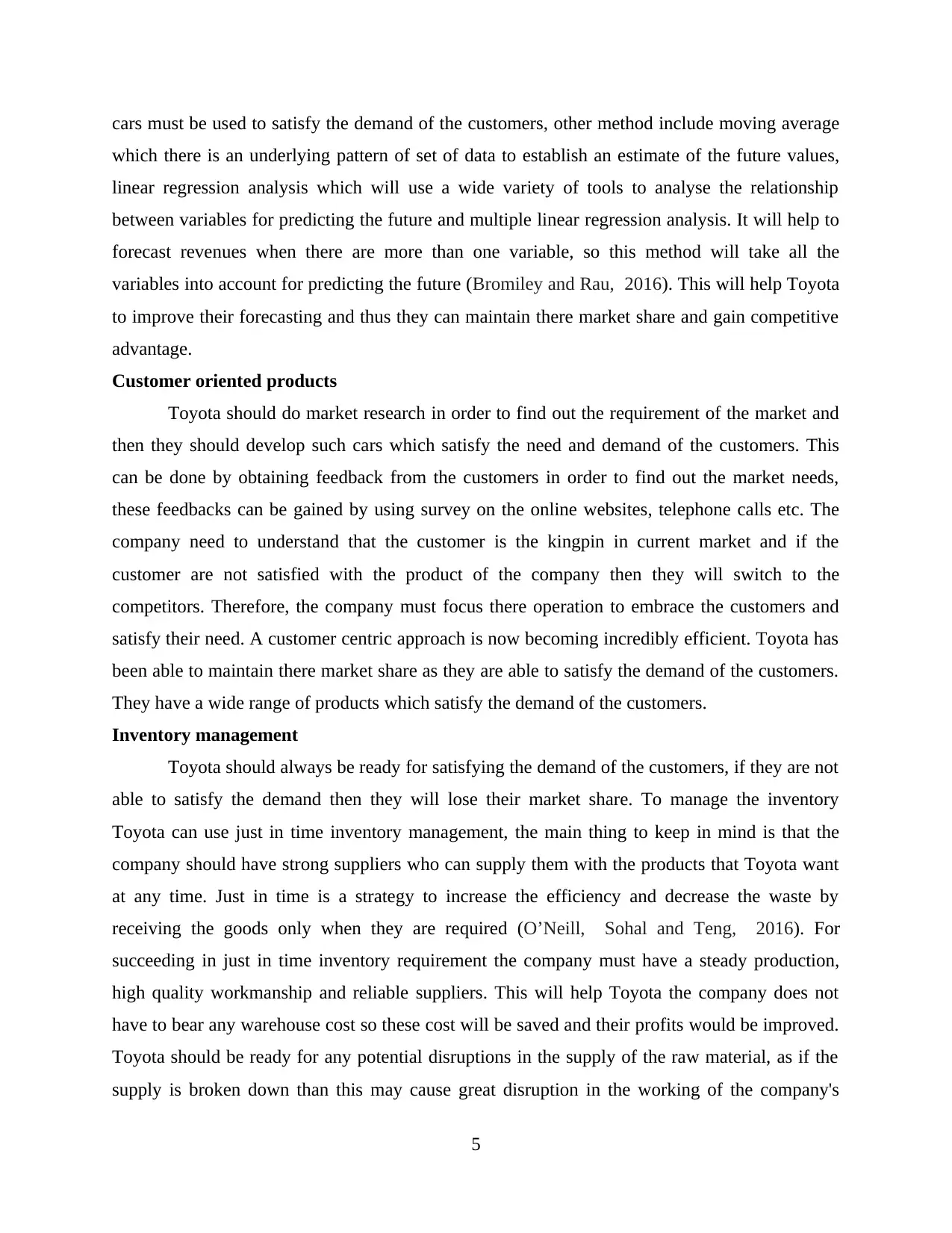
cars must be used to satisfy the demand of the customers, other method include moving average
which there is an underlying pattern of set of data to establish an estimate of the future values,
linear regression analysis which will use a wide variety of tools to analyse the relationship
between variables for predicting the future and multiple linear regression analysis. It will help to
forecast revenues when there are more than one variable, so this method will take all the
variables into account for predicting the future (Bromiley and Rau, 2016). This will help Toyota
to improve their forecasting and thus they can maintain there market share and gain competitive
advantage.
Customer oriented products
Toyota should do market research in order to find out the requirement of the market and
then they should develop such cars which satisfy the need and demand of the customers. This
can be done by obtaining feedback from the customers in order to find out the market needs,
these feedbacks can be gained by using survey on the online websites, telephone calls etc. The
company need to understand that the customer is the kingpin in current market and if the
customer are not satisfied with the product of the company then they will switch to the
competitors. Therefore, the company must focus there operation to embrace the customers and
satisfy their need. A customer centric approach is now becoming incredibly efficient. Toyota has
been able to maintain there market share as they are able to satisfy the demand of the customers.
They have a wide range of products which satisfy the demand of the customers.
Inventory management
Toyota should always be ready for satisfying the demand of the customers, if they are not
able to satisfy the demand then they will lose their market share. To manage the inventory
Toyota can use just in time inventory management, the main thing to keep in mind is that the
company should have strong suppliers who can supply them with the products that Toyota want
at any time. Just in time is a strategy to increase the efficiency and decrease the waste by
receiving the goods only when they are required (O’Neill, Sohal and Teng, 2016). For
succeeding in just in time inventory requirement the company must have a steady production,
high quality workmanship and reliable suppliers. This will help Toyota the company does not
have to bear any warehouse cost so these cost will be saved and their profits would be improved.
Toyota should be ready for any potential disruptions in the supply of the raw material, as if the
supply is broken down than this may cause great disruption in the working of the company's
5
which there is an underlying pattern of set of data to establish an estimate of the future values,
linear regression analysis which will use a wide variety of tools to analyse the relationship
between variables for predicting the future and multiple linear regression analysis. It will help to
forecast revenues when there are more than one variable, so this method will take all the
variables into account for predicting the future (Bromiley and Rau, 2016). This will help Toyota
to improve their forecasting and thus they can maintain there market share and gain competitive
advantage.
Customer oriented products
Toyota should do market research in order to find out the requirement of the market and
then they should develop such cars which satisfy the need and demand of the customers. This
can be done by obtaining feedback from the customers in order to find out the market needs,
these feedbacks can be gained by using survey on the online websites, telephone calls etc. The
company need to understand that the customer is the kingpin in current market and if the
customer are not satisfied with the product of the company then they will switch to the
competitors. Therefore, the company must focus there operation to embrace the customers and
satisfy their need. A customer centric approach is now becoming incredibly efficient. Toyota has
been able to maintain there market share as they are able to satisfy the demand of the customers.
They have a wide range of products which satisfy the demand of the customers.
Inventory management
Toyota should always be ready for satisfying the demand of the customers, if they are not
able to satisfy the demand then they will lose their market share. To manage the inventory
Toyota can use just in time inventory management, the main thing to keep in mind is that the
company should have strong suppliers who can supply them with the products that Toyota want
at any time. Just in time is a strategy to increase the efficiency and decrease the waste by
receiving the goods only when they are required (O’Neill, Sohal and Teng, 2016). For
succeeding in just in time inventory requirement the company must have a steady production,
high quality workmanship and reliable suppliers. This will help Toyota the company does not
have to bear any warehouse cost so these cost will be saved and their profits would be improved.
Toyota should be ready for any potential disruptions in the supply of the raw material, as if the
supply is broken down than this may cause great disruption in the working of the company's
5
Paraphrase This Document
Need a fresh take? Get an instant paraphrase of this document with our AI Paraphraser
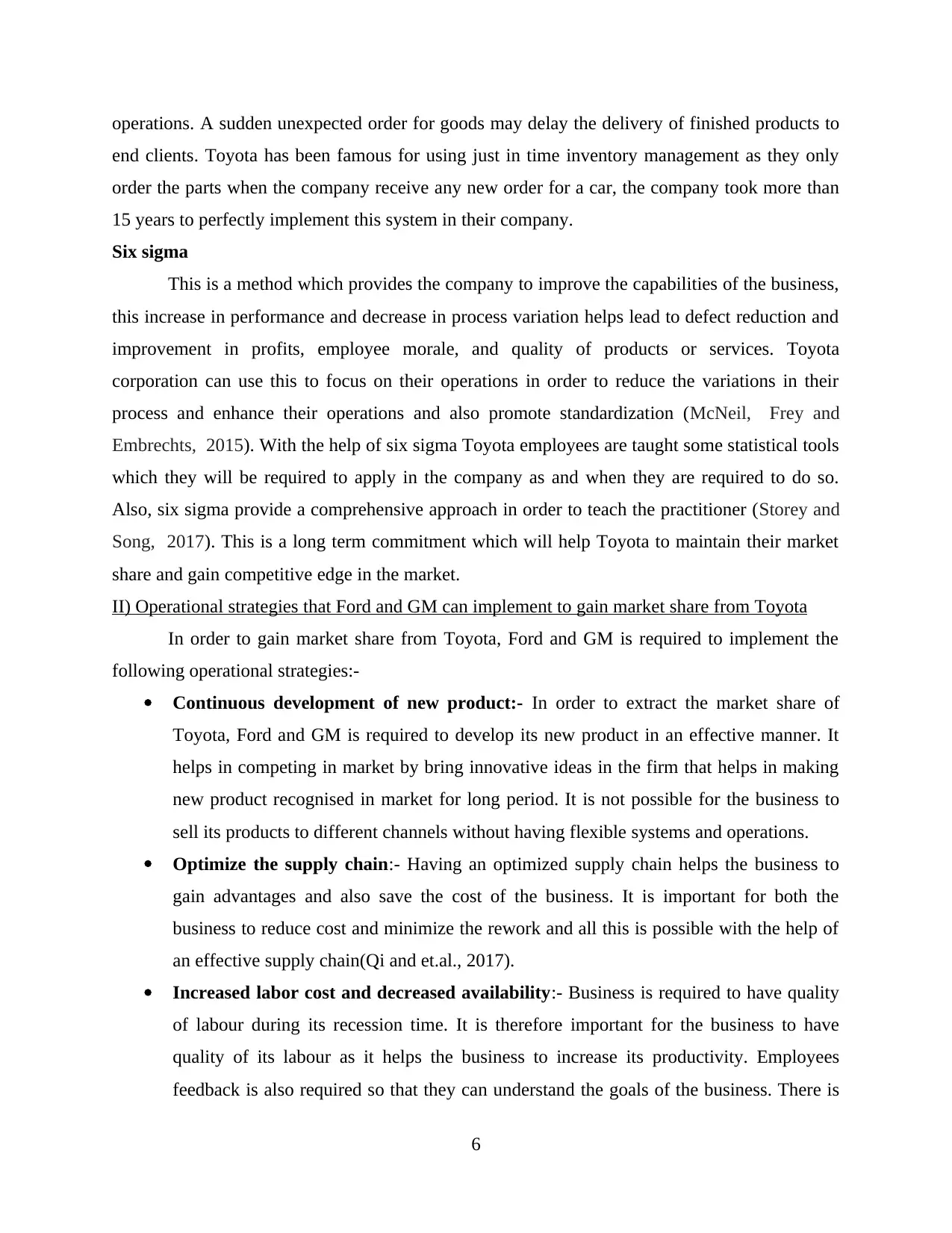
operations. A sudden unexpected order for goods may delay the delivery of finished products to
end clients. Toyota has been famous for using just in time inventory management as they only
order the parts when the company receive any new order for a car, the company took more than
15 years to perfectly implement this system in their company.
Six sigma
This is a method which provides the company to improve the capabilities of the business,
this increase in performance and decrease in process variation helps lead to defect reduction and
improvement in profits, employee morale, and quality of products or services. Toyota
corporation can use this to focus on their operations in order to reduce the variations in their
process and enhance their operations and also promote standardization (McNeil, Frey and
Embrechts, 2015). With the help of six sigma Toyota employees are taught some statistical tools
which they will be required to apply in the company as and when they are required to do so.
Also, six sigma provide a comprehensive approach in order to teach the practitioner (Storey and
Song, 2017). This is a long term commitment which will help Toyota to maintain their market
share and gain competitive edge in the market.
II) Operational strategies that Ford and GM can implement to gain market share from Toyota
In order to gain market share from Toyota, Ford and GM is required to implement the
following operational strategies:-
Continuous development of new product:- In order to extract the market share of
Toyota, Ford and GM is required to develop its new product in an effective manner. It
helps in competing in market by bring innovative ideas in the firm that helps in making
new product recognised in market for long period. It is not possible for the business to
sell its products to different channels without having flexible systems and operations.
Optimize the supply chain:- Having an optimized supply chain helps the business to
gain advantages and also save the cost of the business. It is important for both the
business to reduce cost and minimize the rework and all this is possible with the help of
an effective supply chain(Qi and et.al., 2017).
Increased labor cost and decreased availability:- Business is required to have quality
of labour during its recession time. It is therefore important for the business to have
quality of its labour as it helps the business to increase its productivity. Employees
feedback is also required so that they can understand the goals of the business. There is
6
end clients. Toyota has been famous for using just in time inventory management as they only
order the parts when the company receive any new order for a car, the company took more than
15 years to perfectly implement this system in their company.
Six sigma
This is a method which provides the company to improve the capabilities of the business,
this increase in performance and decrease in process variation helps lead to defect reduction and
improvement in profits, employee morale, and quality of products or services. Toyota
corporation can use this to focus on their operations in order to reduce the variations in their
process and enhance their operations and also promote standardization (McNeil, Frey and
Embrechts, 2015). With the help of six sigma Toyota employees are taught some statistical tools
which they will be required to apply in the company as and when they are required to do so.
Also, six sigma provide a comprehensive approach in order to teach the practitioner (Storey and
Song, 2017). This is a long term commitment which will help Toyota to maintain their market
share and gain competitive edge in the market.
II) Operational strategies that Ford and GM can implement to gain market share from Toyota
In order to gain market share from Toyota, Ford and GM is required to implement the
following operational strategies:-
Continuous development of new product:- In order to extract the market share of
Toyota, Ford and GM is required to develop its new product in an effective manner. It
helps in competing in market by bring innovative ideas in the firm that helps in making
new product recognised in market for long period. It is not possible for the business to
sell its products to different channels without having flexible systems and operations.
Optimize the supply chain:- Having an optimized supply chain helps the business to
gain advantages and also save the cost of the business. It is important for both the
business to reduce cost and minimize the rework and all this is possible with the help of
an effective supply chain(Qi and et.al., 2017).
Increased labor cost and decreased availability:- Business is required to have quality
of labour during its recession time. It is therefore important for the business to have
quality of its labour as it helps the business to increase its productivity. Employees
feedback is also required so that they can understand the goals of the business. There is
6
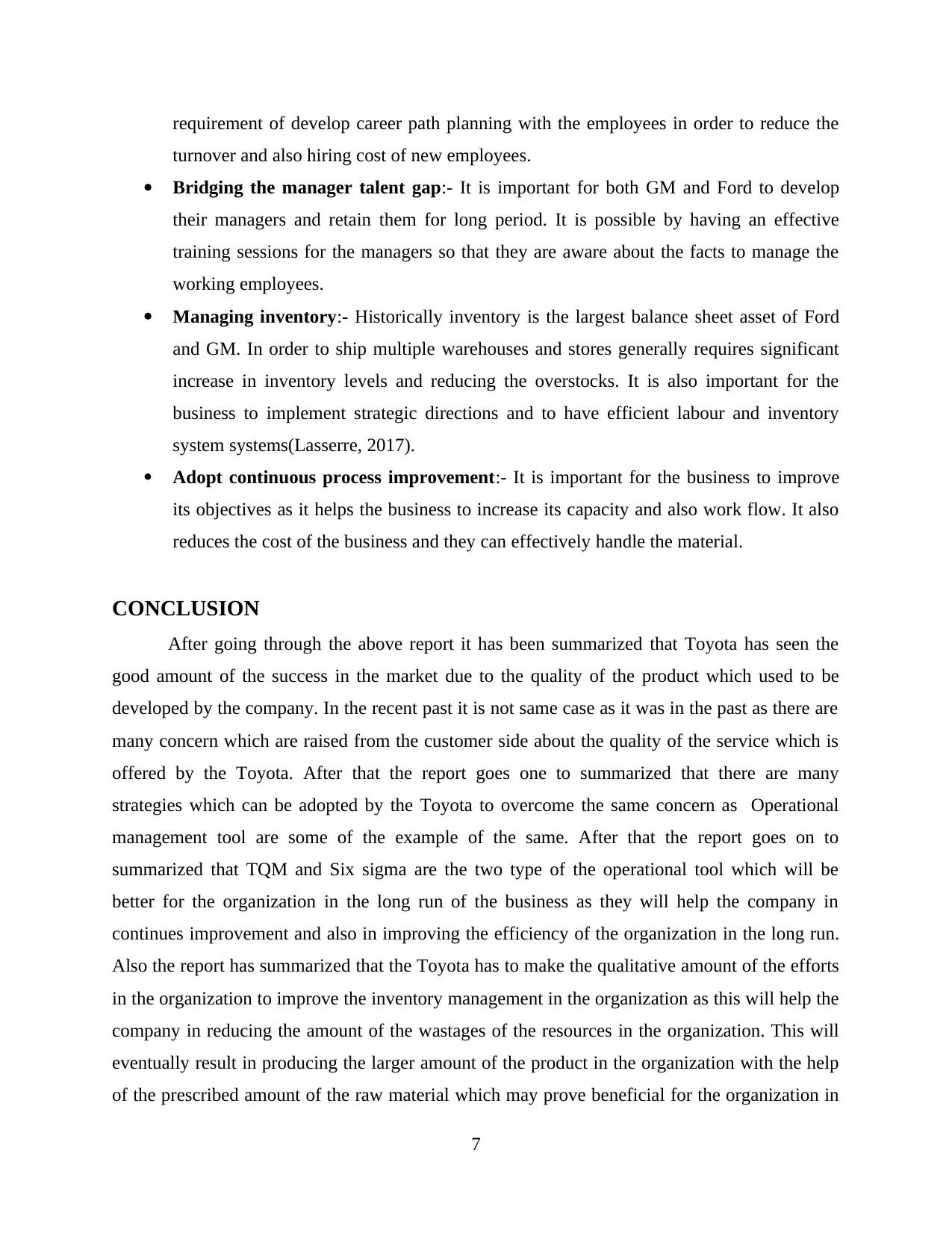
requirement of develop career path planning with the employees in order to reduce the
turnover and also hiring cost of new employees.
Bridging the manager talent gap:- It is important for both GM and Ford to develop
their managers and retain them for long period. It is possible by having an effective
training sessions for the managers so that they are aware about the facts to manage the
working employees.
Managing inventory:- Historically inventory is the largest balance sheet asset of Ford
and GM. In order to ship multiple warehouses and stores generally requires significant
increase in inventory levels and reducing the overstocks. It is also important for the
business to implement strategic directions and to have efficient labour and inventory
system systems(Lasserre, 2017).
Adopt continuous process improvement:- It is important for the business to improve
its objectives as it helps the business to increase its capacity and also work flow. It also
reduces the cost of the business and they can effectively handle the material.
CONCLUSION
After going through the above report it has been summarized that Toyota has seen the
good amount of the success in the market due to the quality of the product which used to be
developed by the company. In the recent past it is not same case as it was in the past as there are
many concern which are raised from the customer side about the quality of the service which is
offered by the Toyota. After that the report goes one to summarized that there are many
strategies which can be adopted by the Toyota to overcome the same concern as Operational
management tool are some of the example of the same. After that the report goes on to
summarized that TQM and Six sigma are the two type of the operational tool which will be
better for the organization in the long run of the business as they will help the company in
continues improvement and also in improving the efficiency of the organization in the long run.
Also the report has summarized that the Toyota has to make the qualitative amount of the efforts
in the organization to improve the inventory management in the organization as this will help the
company in reducing the amount of the wastages of the resources in the organization. This will
eventually result in producing the larger amount of the product in the organization with the help
of the prescribed amount of the raw material which may prove beneficial for the organization in
7
turnover and also hiring cost of new employees.
Bridging the manager talent gap:- It is important for both GM and Ford to develop
their managers and retain them for long period. It is possible by having an effective
training sessions for the managers so that they are aware about the facts to manage the
working employees.
Managing inventory:- Historically inventory is the largest balance sheet asset of Ford
and GM. In order to ship multiple warehouses and stores generally requires significant
increase in inventory levels and reducing the overstocks. It is also important for the
business to implement strategic directions and to have efficient labour and inventory
system systems(Lasserre, 2017).
Adopt continuous process improvement:- It is important for the business to improve
its objectives as it helps the business to increase its capacity and also work flow. It also
reduces the cost of the business and they can effectively handle the material.
CONCLUSION
After going through the above report it has been summarized that Toyota has seen the
good amount of the success in the market due to the quality of the product which used to be
developed by the company. In the recent past it is not same case as it was in the past as there are
many concern which are raised from the customer side about the quality of the service which is
offered by the Toyota. After that the report goes one to summarized that there are many
strategies which can be adopted by the Toyota to overcome the same concern as Operational
management tool are some of the example of the same. After that the report goes on to
summarized that TQM and Six sigma are the two type of the operational tool which will be
better for the organization in the long run of the business as they will help the company in
continues improvement and also in improving the efficiency of the organization in the long run.
Also the report has summarized that the Toyota has to make the qualitative amount of the efforts
in the organization to improve the inventory management in the organization as this will help the
company in reducing the amount of the wastages of the resources in the organization. This will
eventually result in producing the larger amount of the product in the organization with the help
of the prescribed amount of the raw material which may prove beneficial for the organization in
7
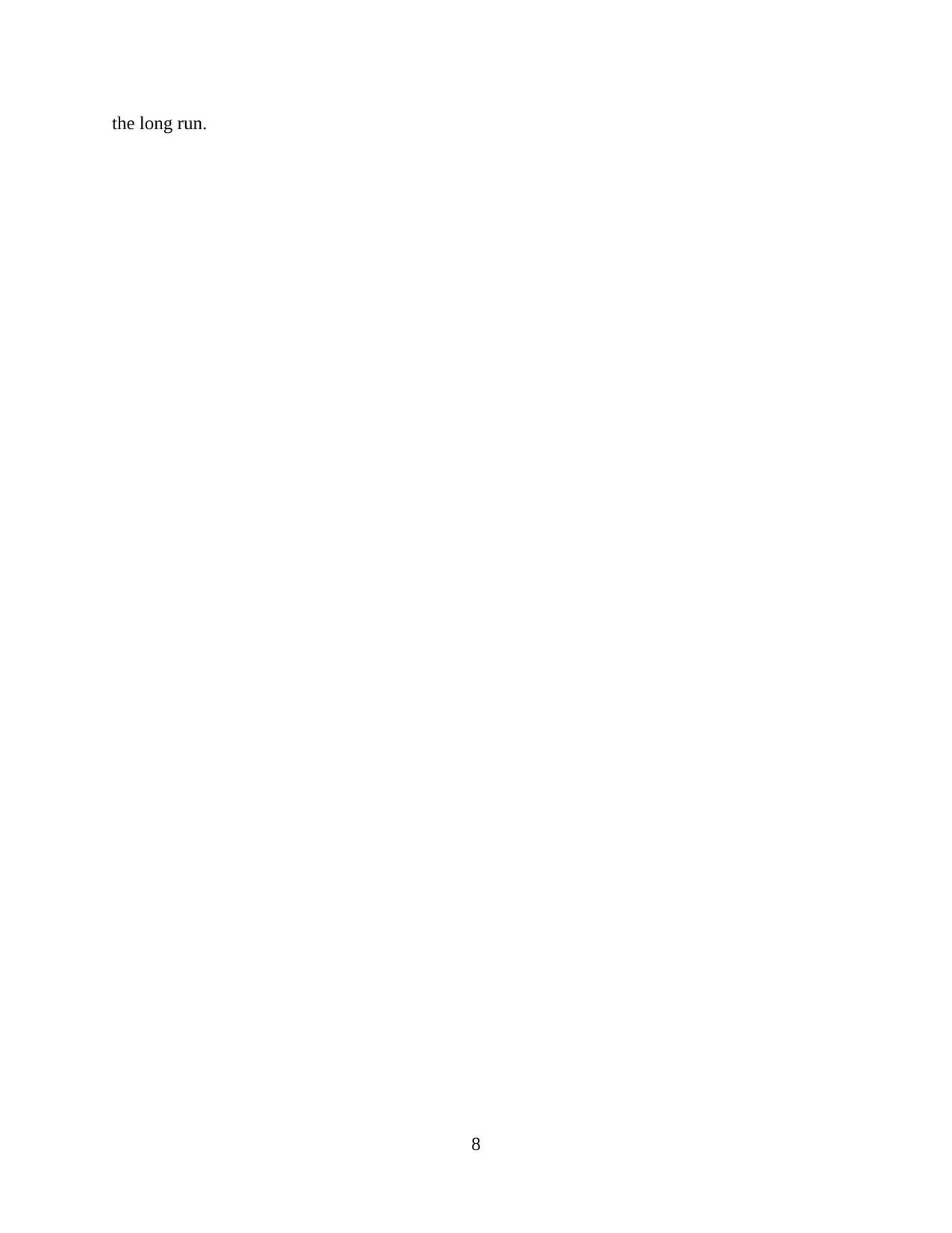
the long run.
8
8
Secure Best Marks with AI Grader
Need help grading? Try our AI Grader for instant feedback on your assignments.
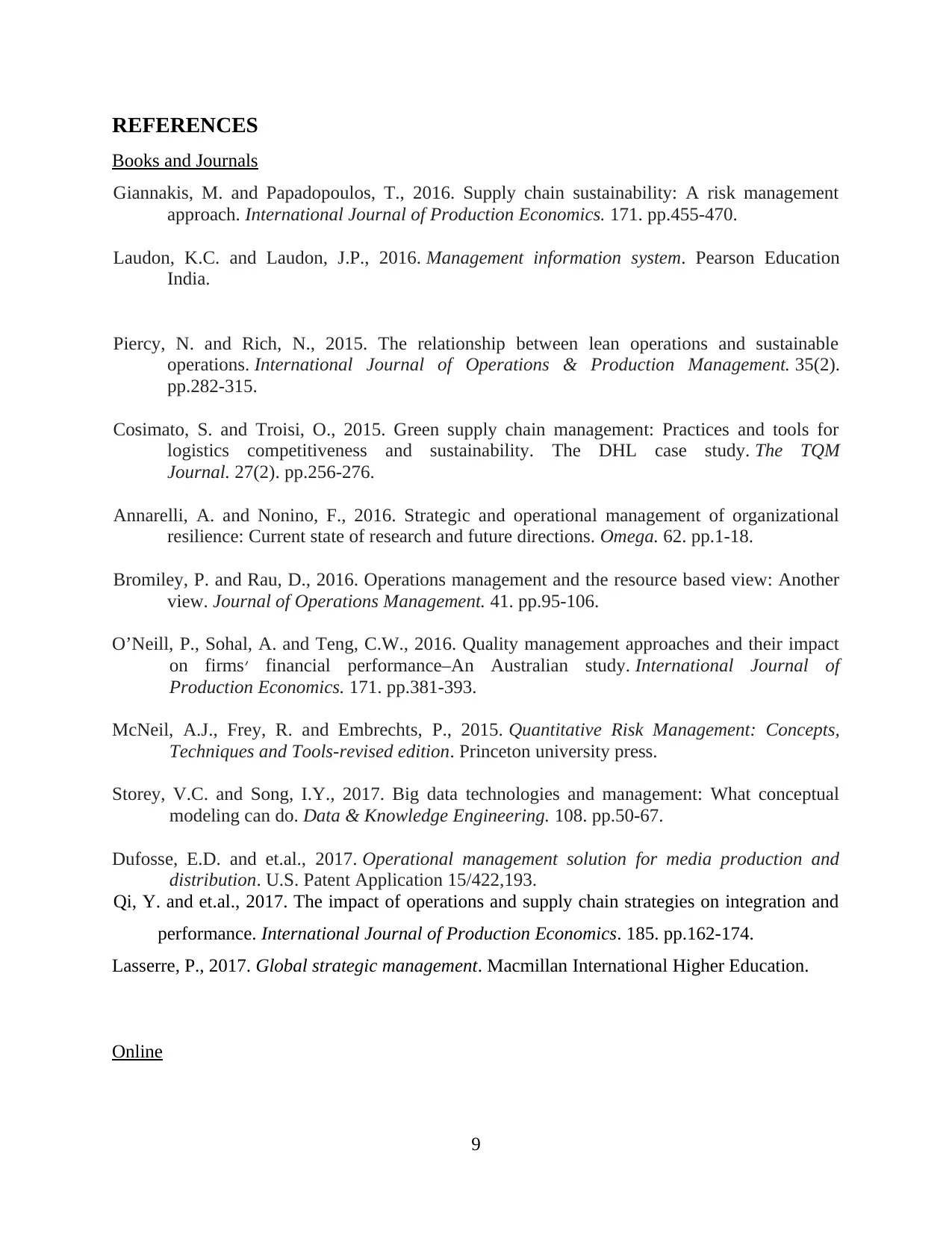
REFERENCES
Books and Journals
Giannakis, M. and Papadopoulos, T., 2016. Supply chain sustainability: A risk management
approach. International Journal of Production Economics. 171. pp.455-470.
Laudon, K.C. and Laudon, J.P., 2016. Management information system. Pearson Education
India.
Piercy, N. and Rich, N., 2015. The relationship between lean operations and sustainable
operations. International Journal of Operations & Production Management. 35(2).
pp.282-315.
Cosimato, S. and Troisi, O., 2015. Green supply chain management: Practices and tools for
logistics competitiveness and sustainability. The DHL case study. The TQM
Journal. 27(2). pp.256-276.
Annarelli, A. and Nonino, F., 2016. Strategic and operational management of organizational
resilience: Current state of research and future directions. Omega. 62. pp.1-18.
Bromiley, P. and Rau, D., 2016. Operations management and the resource based view: Another
view. Journal of Operations Management. 41. pp.95-106.
O’Neill, P., Sohal, A. and Teng, C.W., 2016. Quality management approaches and their impact
on firms׳ financial performance–An Australian study. International Journal of
Production Economics. 171. pp.381-393.
McNeil, A.J., Frey, R. and Embrechts, P., 2015. Quantitative Risk Management: Concepts,
Techniques and Tools-revised edition. Princeton university press.
Storey, V.C. and Song, I.Y., 2017. Big data technologies and management: What conceptual
modeling can do. Data & Knowledge Engineering. 108. pp.50-67.
Dufosse, E.D. and et.al., 2017. Operational management solution for media production and
distribution. U.S. Patent Application 15/422,193.
Qi, Y. and et.al., 2017. The impact of operations and supply chain strategies on integration and
performance. International Journal of Production Economics. 185. pp.162-174.
Lasserre, P., 2017. Global strategic management. Macmillan International Higher Education.
Online
9
Books and Journals
Giannakis, M. and Papadopoulos, T., 2016. Supply chain sustainability: A risk management
approach. International Journal of Production Economics. 171. pp.455-470.
Laudon, K.C. and Laudon, J.P., 2016. Management information system. Pearson Education
India.
Piercy, N. and Rich, N., 2015. The relationship between lean operations and sustainable
operations. International Journal of Operations & Production Management. 35(2).
pp.282-315.
Cosimato, S. and Troisi, O., 2015. Green supply chain management: Practices and tools for
logistics competitiveness and sustainability. The DHL case study. The TQM
Journal. 27(2). pp.256-276.
Annarelli, A. and Nonino, F., 2016. Strategic and operational management of organizational
resilience: Current state of research and future directions. Omega. 62. pp.1-18.
Bromiley, P. and Rau, D., 2016. Operations management and the resource based view: Another
view. Journal of Operations Management. 41. pp.95-106.
O’Neill, P., Sohal, A. and Teng, C.W., 2016. Quality management approaches and their impact
on firms׳ financial performance–An Australian study. International Journal of
Production Economics. 171. pp.381-393.
McNeil, A.J., Frey, R. and Embrechts, P., 2015. Quantitative Risk Management: Concepts,
Techniques and Tools-revised edition. Princeton university press.
Storey, V.C. and Song, I.Y., 2017. Big data technologies and management: What conceptual
modeling can do. Data & Knowledge Engineering. 108. pp.50-67.
Dufosse, E.D. and et.al., 2017. Operational management solution for media production and
distribution. U.S. Patent Application 15/422,193.
Qi, Y. and et.al., 2017. The impact of operations and supply chain strategies on integration and
performance. International Journal of Production Economics. 185. pp.162-174.
Lasserre, P., 2017. Global strategic management. Macmillan International Higher Education.
Online
9
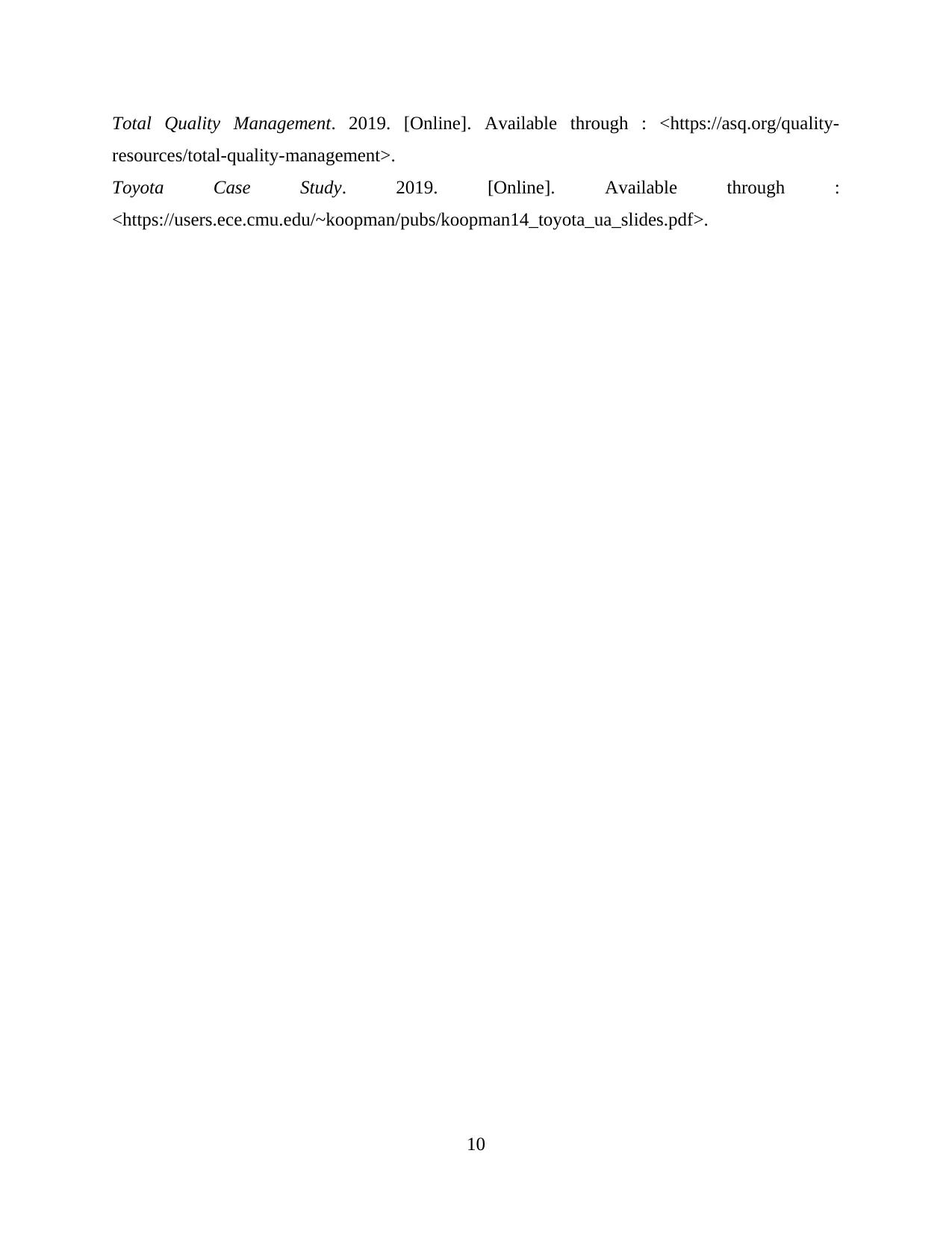
Total Quality Management. 2019. [Online]. Available through : <https://asq.org/quality-
resources/total-quality-management>.
Toyota Case Study. 2019. [Online]. Available through :
<https://users.ece.cmu.edu/~koopman/pubs/koopman14_toyota_ua_slides.pdf>.
10
resources/total-quality-management>.
Toyota Case Study. 2019. [Online]. Available through :
<https://users.ece.cmu.edu/~koopman/pubs/koopman14_toyota_ua_slides.pdf>.
10
1 out of 12
Related Documents
![[object Object]](/_next/image/?url=%2F_next%2Fstatic%2Fmedia%2Flogo.6d15ce61.png&w=640&q=75)
Your All-in-One AI-Powered Toolkit for Academic Success.
+13062052269
info@desklib.com
Available 24*7 on WhatsApp / Email
Unlock your academic potential
© 2024 | Zucol Services PVT LTD | All rights reserved.