Introduction to Business Operations and Services 2019
12 Pages3623 Words20 Views
Added on 2023-01-17
About This Document
This document provides an introduction to business operations and services, covering topics such as operational improvement strategies, tools and techniques, and gaining market share from Toyota. It discusses the importance of optimizing supply chains and focusing on quality, customer-oriented products, inventory management, and implementing Six Sigma.
Introduction to Business Operations and Services 2019
Added on 2023-01-17
ShareRelated Documents
INTRODUCTION TO
BUSINESS OPERATIONS
AND SERVICES 2019
BUSINESS OPERATIONS
AND SERVICES 2019
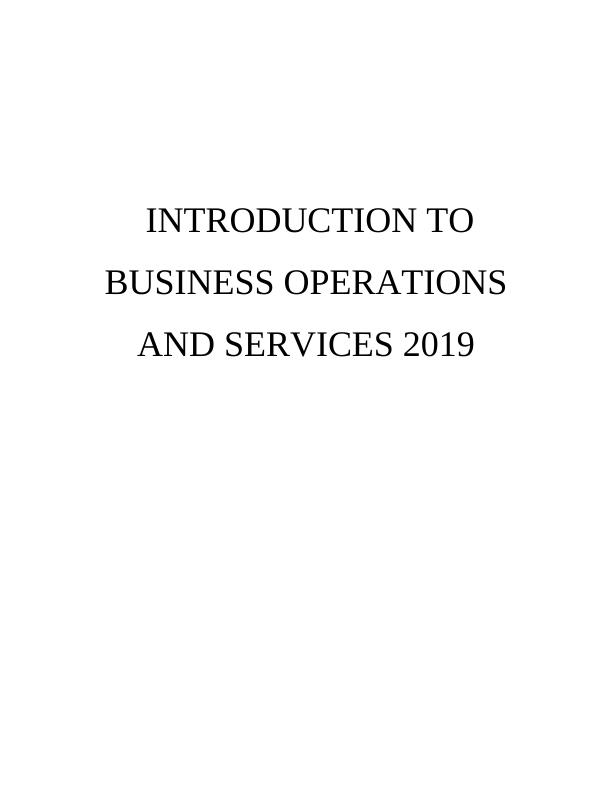
TABLE OF CONTENTS
INTRODUCTION...........................................................................................................................1
MAIN BODY...................................................................................................................................1
I) Introducing new operational improvement strategy and the tools and techniques that will be
used by company..........................................................................................................................1
II) Operational strategies that Ford and GM can implement to gain market share from Toyota 6
CONCLUSION................................................................................................................................7
REFERENCES................................................................................................................................9
INTRODUCTION...........................................................................................................................1
MAIN BODY...................................................................................................................................1
I) Introducing new operational improvement strategy and the tools and techniques that will be
used by company..........................................................................................................................1
II) Operational strategies that Ford and GM can implement to gain market share from Toyota 6
CONCLUSION................................................................................................................................7
REFERENCES................................................................................................................................9
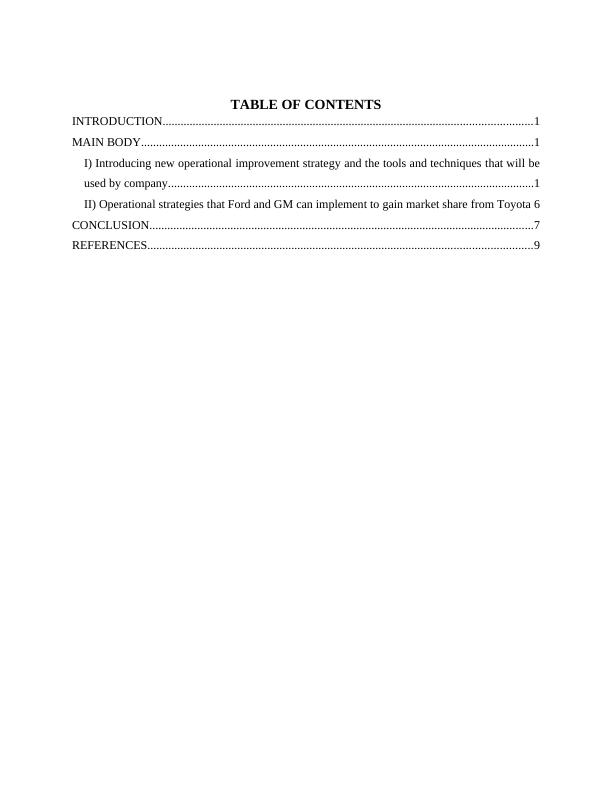
INTRODUCTION
Business operation refer to the activities in which the businesses are engaged on daily
basis for increasing value of enterprises and earning profits. Activities could be optimized for
generating sufficient revenues for covering the expenses and for earning the profits for the
business owners. Employees of company helps in accomplishing the goals of business through
performance of certain functions like accounting, marketing, manufacturing and many more.
Operations of business evolves with the growth of business and management of the company are
required to have proper planning for dealing with these changes effectively so that they do not
create discrepancies in future (Giannakis and Papadopoulos, 2016). There are different business
operations depending on the the of industry. The report will provide the details about the
practices and processes that are involved in business operations and services. It will also cover
the factors that are involved in managing the business operations. In the present case downfall of
Toyota could lead to profits for its competitors GM and Ford. The improvement strategies the
company will adopt to enhance its process. It will also suggest the strategies that GM and Ford
could adopt for gaining the market share from Toyota.
MAIN BODY
I) Introducing new operational improvement strategy and the tools and techniques that will be
used by company.
Toyota is recognised as 7th largest company in world and 2nd largest automobile
manufacturer tht that is having production units in around 28 nations of world. It has also been
3rd largest automobile manufacturer in the world in net sales and unit sales. Toyota is known for
maintaining the customer relationships and providing the best quality products to its customers.
Above manufacturing company also have its own research and development facilities that helps
it in achieving the best designs and innovation in its products. Company never encountered a
problem that helped the company in building such a strong brand image in the automobile
industry.
A defect in the manufacturing of the cars strongly hit the market image and trust on the
company. The fall of the company started after collision of Lexus ES350 on highway of San
Diego, California that killed four occupants. The case was an serious issue for the car
manufacturing company.
1
Business operation refer to the activities in which the businesses are engaged on daily
basis for increasing value of enterprises and earning profits. Activities could be optimized for
generating sufficient revenues for covering the expenses and for earning the profits for the
business owners. Employees of company helps in accomplishing the goals of business through
performance of certain functions like accounting, marketing, manufacturing and many more.
Operations of business evolves with the growth of business and management of the company are
required to have proper planning for dealing with these changes effectively so that they do not
create discrepancies in future (Giannakis and Papadopoulos, 2016). There are different business
operations depending on the the of industry. The report will provide the details about the
practices and processes that are involved in business operations and services. It will also cover
the factors that are involved in managing the business operations. In the present case downfall of
Toyota could lead to profits for its competitors GM and Ford. The improvement strategies the
company will adopt to enhance its process. It will also suggest the strategies that GM and Ford
could adopt for gaining the market share from Toyota.
MAIN BODY
I) Introducing new operational improvement strategy and the tools and techniques that will be
used by company.
Toyota is recognised as 7th largest company in world and 2nd largest automobile
manufacturer tht that is having production units in around 28 nations of world. It has also been
3rd largest automobile manufacturer in the world in net sales and unit sales. Toyota is known for
maintaining the customer relationships and providing the best quality products to its customers.
Above manufacturing company also have its own research and development facilities that helps
it in achieving the best designs and innovation in its products. Company never encountered a
problem that helped the company in building such a strong brand image in the automobile
industry.
A defect in the manufacturing of the cars strongly hit the market image and trust on the
company. The fall of the company started after collision of Lexus ES350 on highway of San
Diego, California that killed four occupants. The case was an serious issue for the car
manufacturing company.
1
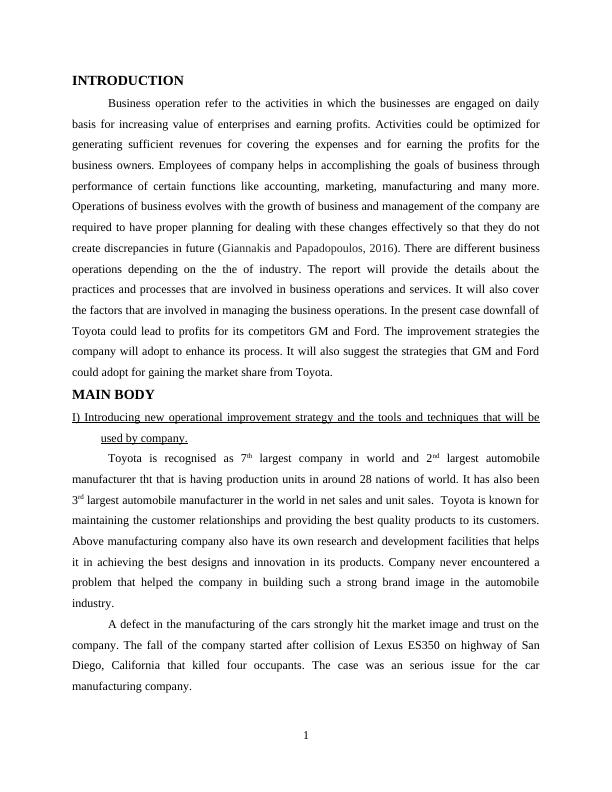
Company recalled around 8.5 million of its tucks and cars due to unintended acceleration leading
to the death of innocent people. Cars were having brake problems, floor mats issues and sticky
gas pedals.
Problems were in gas pedal mechanism causing accelerator in becoming sticky regardless
of presence of floor mats in cars. The pedal mechanism was also becoming hard to press and
slow to return. The length of accelerator was more that left no space between the floor mats and
it. For fixing the problems it introduced a massive recall worldwide for fixing the problems
attributing to sticky gas pedals, faulty accelerators and the brake problems. Company
overwhelmed by the massive products recall and faced reputation damages after the question
over safety of cars. Allegations were laid on company that it did not responded to the
problems quickly (Toyota Case Study, 2019). After this National Highway Traffic Safety
Administration played prosecutor's role against Toyota and problem was connected to various
factors like gas pedals, mechanism and ignition system of the car. The Japanese company as
solution shorten the pedal length so that it carpet is not stuck with pedal. Company did not
identified the root causes behind the problems and introduced the system software that
overrides electronic gas pedals when brake pedal was pressed.
The unfortunate technical issues in cars, compelled the company to implement new
standards and procedures for ensuring final quality of the vehicles and company was required to
regain image and prestige in public. The credibility loss reflected in sales volume and resulted in
20% decrease in the sales and stopped production of few of its models. The case does not only
reflect the technical failure but the quality check procedures being followed in company.
Company is trusted by people because of it high quality and safety features but the defects in
large number of vehicles established a question mark on the company (Toyota Case Study,
2019). The management defaults have result in the defects in the cars, if company had proper
quality control procedures than it may not have to suffer the damages(Laudon and Laudon,
2016).
Machine Monitoring Systems
Machine monitoring systems collects data automatically from the machines which
provides data for real time notifications and virtualisations and historical analysis that helps
operators and the management in making faster and informed decisions. This management
systems helps in detecting the problems at their initial stages. They provide glance performance
2
to the death of innocent people. Cars were having brake problems, floor mats issues and sticky
gas pedals.
Problems were in gas pedal mechanism causing accelerator in becoming sticky regardless
of presence of floor mats in cars. The pedal mechanism was also becoming hard to press and
slow to return. The length of accelerator was more that left no space between the floor mats and
it. For fixing the problems it introduced a massive recall worldwide for fixing the problems
attributing to sticky gas pedals, faulty accelerators and the brake problems. Company
overwhelmed by the massive products recall and faced reputation damages after the question
over safety of cars. Allegations were laid on company that it did not responded to the
problems quickly (Toyota Case Study, 2019). After this National Highway Traffic Safety
Administration played prosecutor's role against Toyota and problem was connected to various
factors like gas pedals, mechanism and ignition system of the car. The Japanese company as
solution shorten the pedal length so that it carpet is not stuck with pedal. Company did not
identified the root causes behind the problems and introduced the system software that
overrides electronic gas pedals when brake pedal was pressed.
The unfortunate technical issues in cars, compelled the company to implement new
standards and procedures for ensuring final quality of the vehicles and company was required to
regain image and prestige in public. The credibility loss reflected in sales volume and resulted in
20% decrease in the sales and stopped production of few of its models. The case does not only
reflect the technical failure but the quality check procedures being followed in company.
Company is trusted by people because of it high quality and safety features but the defects in
large number of vehicles established a question mark on the company (Toyota Case Study,
2019). The management defaults have result in the defects in the cars, if company had proper
quality control procedures than it may not have to suffer the damages(Laudon and Laudon,
2016).
Machine Monitoring Systems
Machine monitoring systems collects data automatically from the machines which
provides data for real time notifications and virtualisations and historical analysis that helps
operators and the management in making faster and informed decisions. This management
systems helps in detecting the problems at their initial stages. They provide glance performance
2
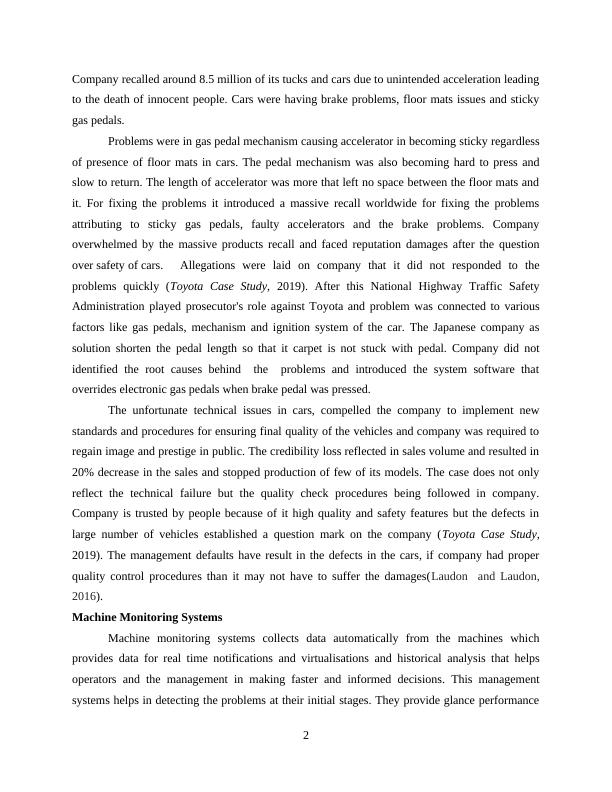
End of preview
Want to access all the pages? Upload your documents or become a member.
Related Documents
case of Toyota Assignment Samplelg...
|11
|2569
|295
Report on Business Ethics 2022lg...
|10
|2978
|25
Toyota Quality Managementlg...
|4
|771
|472
Toyota motor corporation (PDF)lg...
|10
|3680
|35
Toyota's Operational Problem: Accelerator and Brake Issueslg...
|6
|1323
|324
Toyota Recall Crisis: Strategic Intelligence and Possible Solutionslg...
|12
|3738
|367