Analysis of Sustainable Supply Chain Management
VerifiedAdded on 2020/07/22
|14
|4198
|84
AI Summary
This assignment is designed to analyze the concept of sustainable supply chain management (SCM) in depth. It requires students to understand the significance of SCM, its key components, and the strategies for implementing it effectively. The assignment also discusses various models and frameworks used in SCM, including Just-In-Time Approach and Lean Manufacturing. It further examines the role of logistics capabilities in achieving supply chain agility and the relationship between supply chain integration and operational performance.
Contribute Materials
Your contribution can guide someone’s learning journey. Share your
documents today.
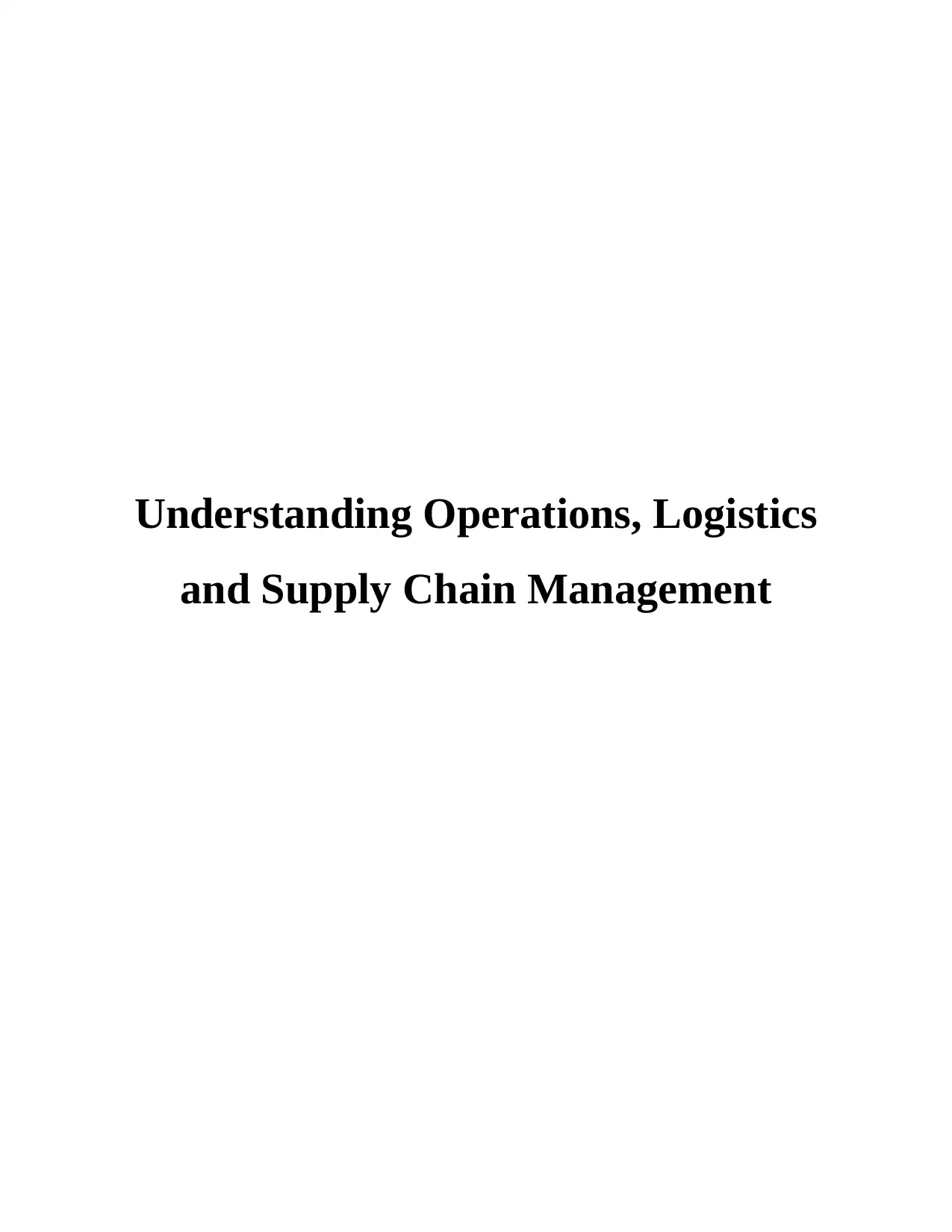
Understanding Operations, Logistics
and Supply Chain Management
and Supply Chain Management
Secure Best Marks with AI Grader
Need help grading? Try our AI Grader for instant feedback on your assignments.
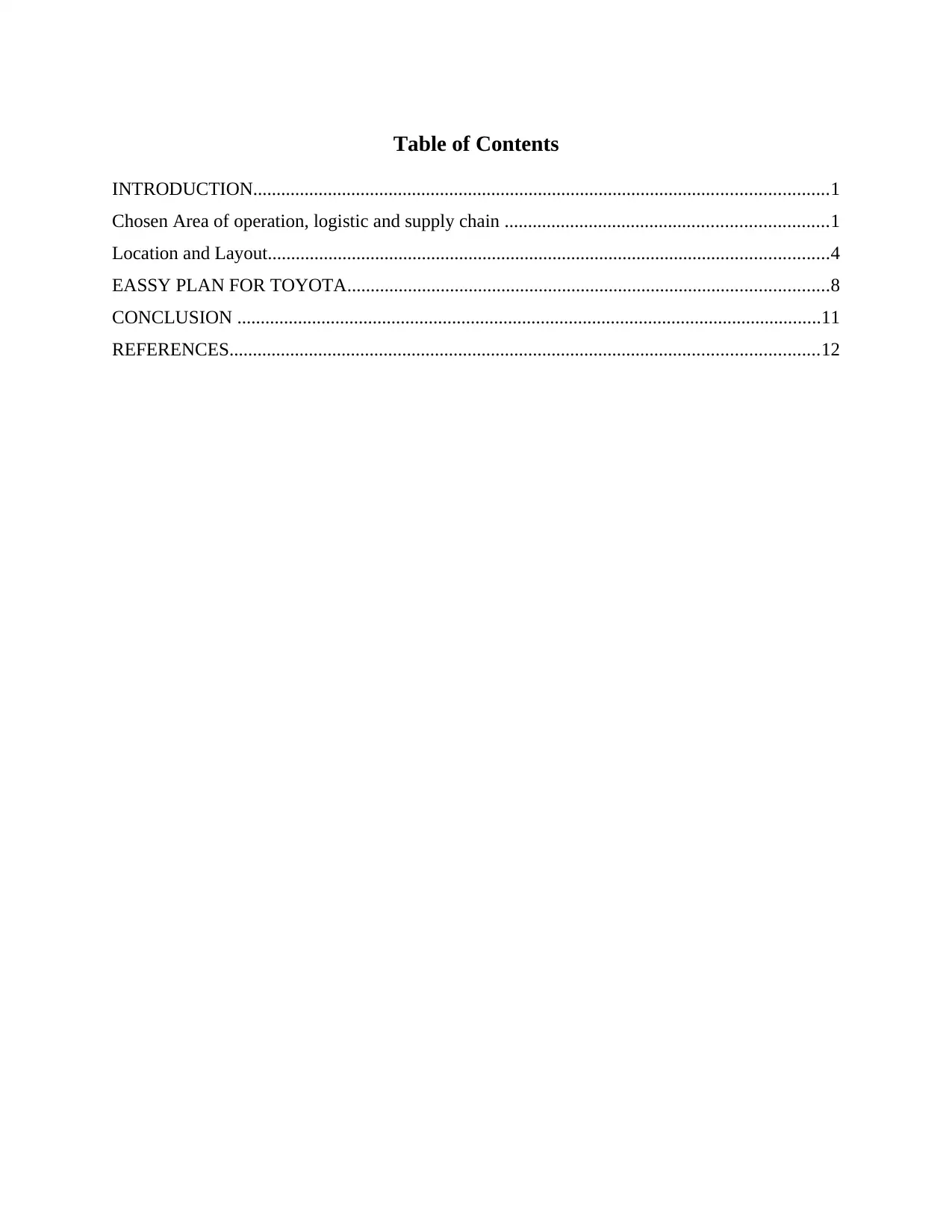
Table of Contents
INTRODUCTION...........................................................................................................................1
Chosen Area of operation, logistic and supply chain .....................................................................1
Location and Layout........................................................................................................................4
EASSY PLAN FOR TOYOTA.......................................................................................................8
CONCLUSION .............................................................................................................................11
REFERENCES..............................................................................................................................12
INTRODUCTION...........................................................................................................................1
Chosen Area of operation, logistic and supply chain .....................................................................1
Location and Layout........................................................................................................................4
EASSY PLAN FOR TOYOTA.......................................................................................................8
CONCLUSION .............................................................................................................................11
REFERENCES..............................................................................................................................12
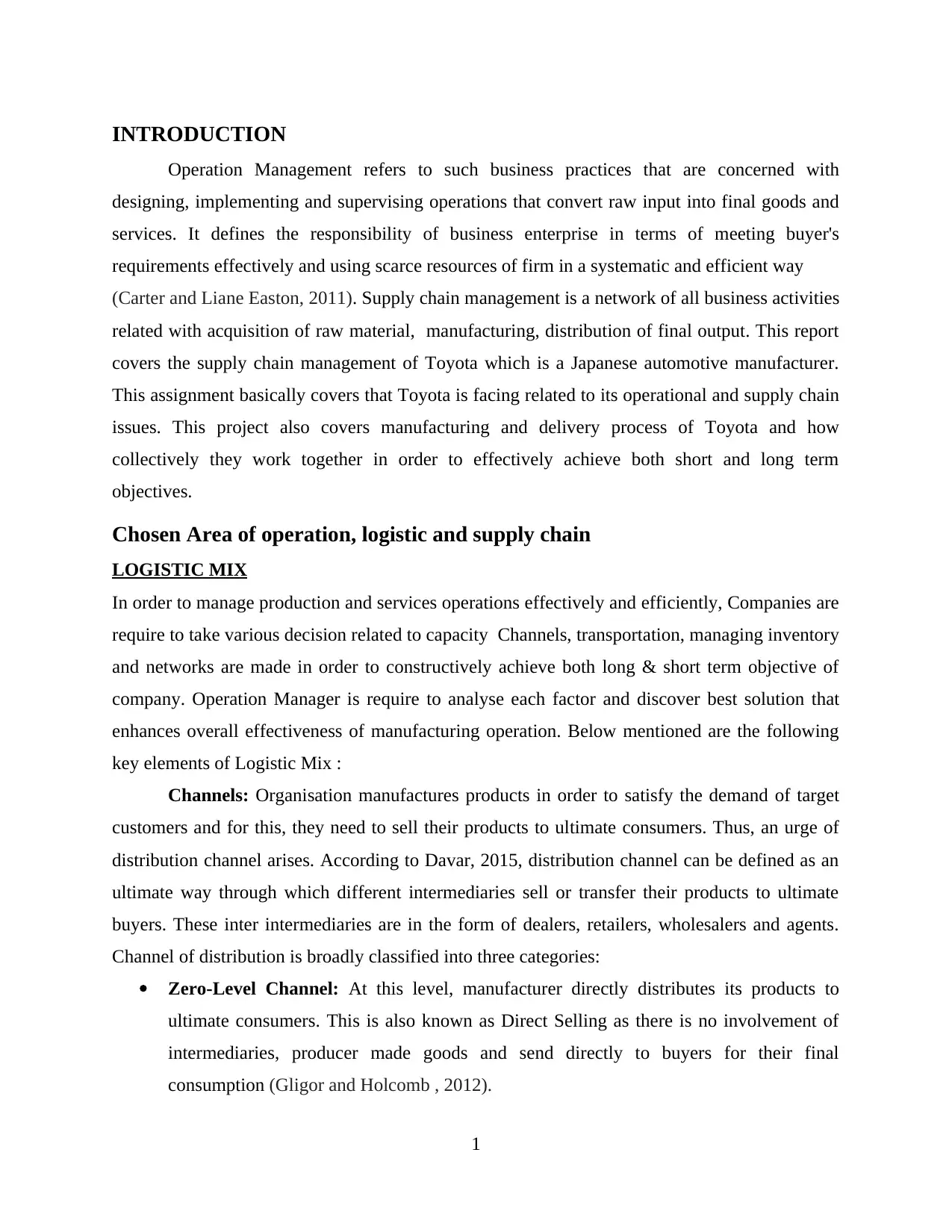
INTRODUCTION
Operation Management refers to such business practices that are concerned with
designing, implementing and supervising operations that convert raw input into final goods and
services. It defines the responsibility of business enterprise in terms of meeting buyer's
requirements effectively and using scarce resources of firm in a systematic and efficient way
(Carter and Liane Easton, 2011). Supply chain management is a network of all business activities
related with acquisition of raw material, manufacturing, distribution of final output. This report
covers the supply chain management of Toyota which is a Japanese automotive manufacturer.
This assignment basically covers that Toyota is facing related to its operational and supply chain
issues. This project also covers manufacturing and delivery process of Toyota and how
collectively they work together in order to effectively achieve both short and long term
objectives.
Chosen Area of operation, logistic and supply chain
LOGISTIC MIX
In order to manage production and services operations effectively and efficiently, Companies are
require to take various decision related to capacity Channels, transportation, managing inventory
and networks are made in order to constructively achieve both long & short term objective of
company. Operation Manager is require to analyse each factor and discover best solution that
enhances overall effectiveness of manufacturing operation. Below mentioned are the following
key elements of Logistic Mix :
Channels: Organisation manufactures products in order to satisfy the demand of target
customers and for this, they need to sell their products to ultimate consumers. Thus, an urge of
distribution channel arises. According to Davar, 2015, distribution channel can be defined as an
ultimate way through which different intermediaries sell or transfer their products to ultimate
buyers. These inter intermediaries are in the form of dealers, retailers, wholesalers and agents.
Channel of distribution is broadly classified into three categories:
Zero-Level Channel: At this level, manufacturer directly distributes its products to
ultimate consumers. This is also known as Direct Selling as there is no involvement of
intermediaries, producer made goods and send directly to buyers for their final
consumption (Gligor and Holcomb , 2012).
1
Operation Management refers to such business practices that are concerned with
designing, implementing and supervising operations that convert raw input into final goods and
services. It defines the responsibility of business enterprise in terms of meeting buyer's
requirements effectively and using scarce resources of firm in a systematic and efficient way
(Carter and Liane Easton, 2011). Supply chain management is a network of all business activities
related with acquisition of raw material, manufacturing, distribution of final output. This report
covers the supply chain management of Toyota which is a Japanese automotive manufacturer.
This assignment basically covers that Toyota is facing related to its operational and supply chain
issues. This project also covers manufacturing and delivery process of Toyota and how
collectively they work together in order to effectively achieve both short and long term
objectives.
Chosen Area of operation, logistic and supply chain
LOGISTIC MIX
In order to manage production and services operations effectively and efficiently, Companies are
require to take various decision related to capacity Channels, transportation, managing inventory
and networks are made in order to constructively achieve both long & short term objective of
company. Operation Manager is require to analyse each factor and discover best solution that
enhances overall effectiveness of manufacturing operation. Below mentioned are the following
key elements of Logistic Mix :
Channels: Organisation manufactures products in order to satisfy the demand of target
customers and for this, they need to sell their products to ultimate consumers. Thus, an urge of
distribution channel arises. According to Davar, 2015, distribution channel can be defined as an
ultimate way through which different intermediaries sell or transfer their products to ultimate
buyers. These inter intermediaries are in the form of dealers, retailers, wholesalers and agents.
Channel of distribution is broadly classified into three categories:
Zero-Level Channel: At this level, manufacturer directly distributes its products to
ultimate consumers. This is also known as Direct Selling as there is no involvement of
intermediaries, producer made goods and send directly to buyers for their final
consumption (Gligor and Holcomb , 2012).
1
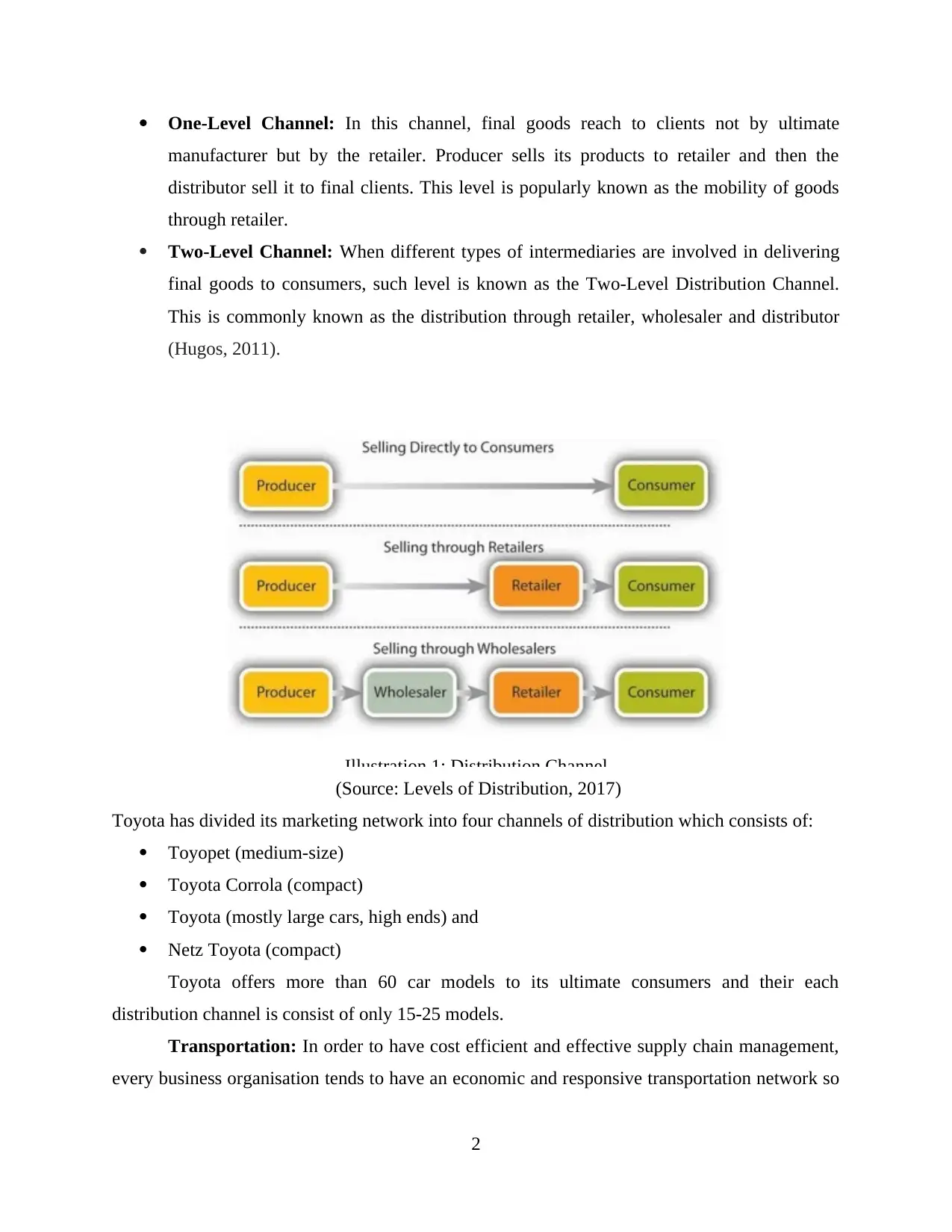
One-Level Channel: In this channel, final goods reach to clients not by ultimate
manufacturer but by the retailer. Producer sells its products to retailer and then the
distributor sell it to final clients. This level is popularly known as the mobility of goods
through retailer.
Two-Level Channel: When different types of intermediaries are involved in delivering
final goods to consumers, such level is known as the Two-Level Distribution Channel.
This is commonly known as the distribution through retailer, wholesaler and distributor
(Hugos, 2011).
(Source: Levels of Distribution, 2017)
Toyota has divided its marketing network into four channels of distribution which consists of:
Toyopet (medium-size)
Toyota Corrola (compact)
Toyota (mostly large cars, high ends) and
Netz Toyota (compact)
Toyota offers more than 60 car models to its ultimate consumers and their each
distribution channel is consist of only 15-25 models.
Transportation: In order to have cost efficient and effective supply chain management,
every business organisation tends to have an economic and responsive transportation network so
2
Illustration 1: Distribution Channel
manufacturer but by the retailer. Producer sells its products to retailer and then the
distributor sell it to final clients. This level is popularly known as the mobility of goods
through retailer.
Two-Level Channel: When different types of intermediaries are involved in delivering
final goods to consumers, such level is known as the Two-Level Distribution Channel.
This is commonly known as the distribution through retailer, wholesaler and distributor
(Hugos, 2011).
(Source: Levels of Distribution, 2017)
Toyota has divided its marketing network into four channels of distribution which consists of:
Toyopet (medium-size)
Toyota Corrola (compact)
Toyota (mostly large cars, high ends) and
Netz Toyota (compact)
Toyota offers more than 60 car models to its ultimate consumers and their each
distribution channel is consist of only 15-25 models.
Transportation: In order to have cost efficient and effective supply chain management,
every business organisation tends to have an economic and responsive transportation network so
2
Illustration 1: Distribution Channel
Secure Best Marks with AI Grader
Need help grading? Try our AI Grader for instant feedback on your assignments.
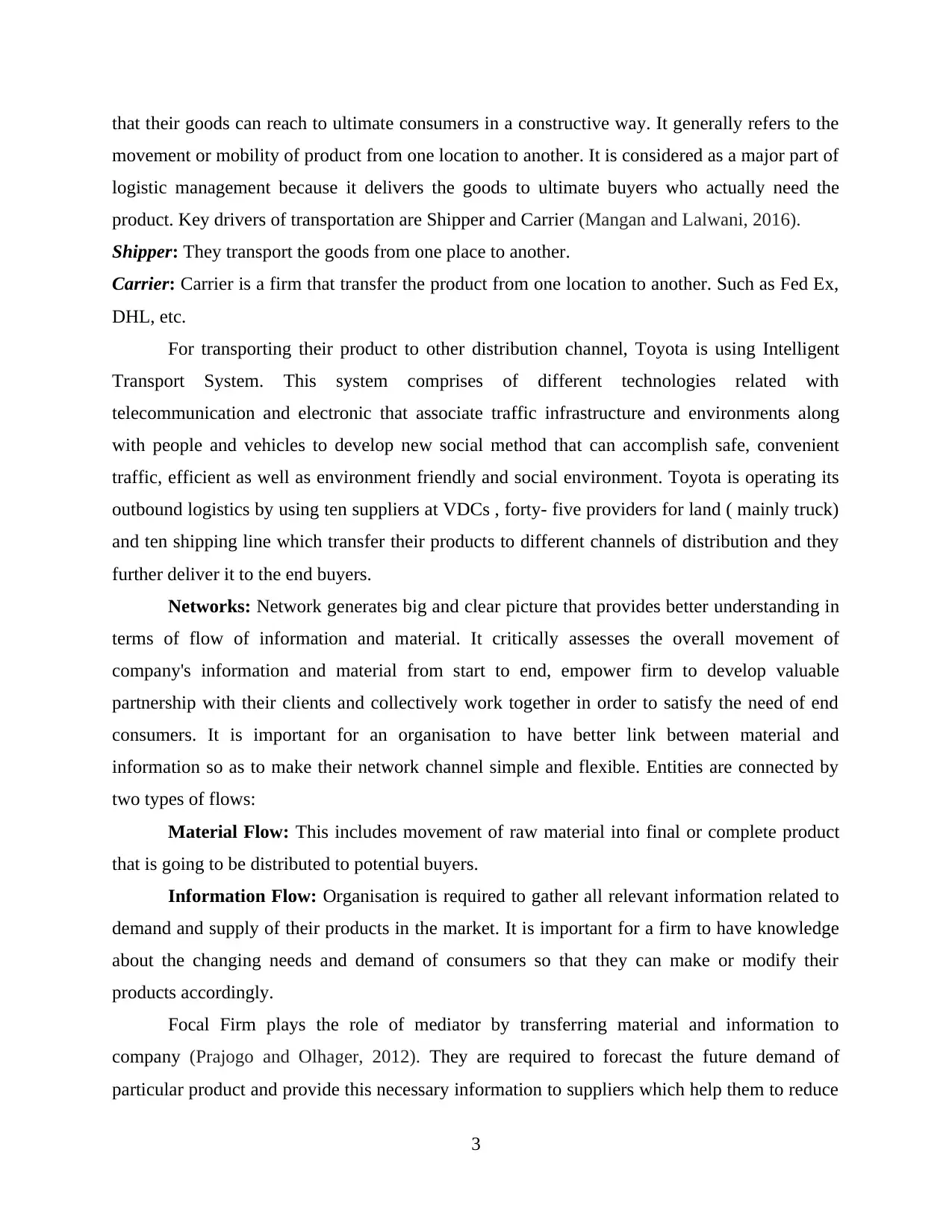
that their goods can reach to ultimate consumers in a constructive way. It generally refers to the
movement or mobility of product from one location to another. It is considered as a major part of
logistic management because it delivers the goods to ultimate buyers who actually need the
product. Key drivers of transportation are Shipper and Carrier (Mangan and Lalwani, 2016).
Shipper: They transport the goods from one place to another.
Carrier: Carrier is a firm that transfer the product from one location to another. Such as Fed Ex,
DHL, etc.
For transporting their product to other distribution channel, Toyota is using Intelligent
Transport System. This system comprises of different technologies related with
telecommunication and electronic that associate traffic infrastructure and environments along
with people and vehicles to develop new social method that can accomplish safe, convenient
traffic, efficient as well as environment friendly and social environment. Toyota is operating its
outbound logistics by using ten suppliers at VDCs , forty- five providers for land ( mainly truck)
and ten shipping line which transfer their products to different channels of distribution and they
further deliver it to the end buyers.
Networks: Network generates big and clear picture that provides better understanding in
terms of flow of information and material. It critically assesses the overall movement of
company's information and material from start to end, empower firm to develop valuable
partnership with their clients and collectively work together in order to satisfy the need of end
consumers. It is important for an organisation to have better link between material and
information so as to make their network channel simple and flexible. Entities are connected by
two types of flows:
Material Flow: This includes movement of raw material into final or complete product
that is going to be distributed to potential buyers.
Information Flow: Organisation is required to gather all relevant information related to
demand and supply of their products in the market. It is important for a firm to have knowledge
about the changing needs and demand of consumers so that they can make or modify their
products accordingly.
Focal Firm plays the role of mediator by transferring material and information to
company (Prajogo and Olhager, 2012). They are required to forecast the future demand of
particular product and provide this necessary information to suppliers which help them to reduce
3
movement or mobility of product from one location to another. It is considered as a major part of
logistic management because it delivers the goods to ultimate buyers who actually need the
product. Key drivers of transportation are Shipper and Carrier (Mangan and Lalwani, 2016).
Shipper: They transport the goods from one place to another.
Carrier: Carrier is a firm that transfer the product from one location to another. Such as Fed Ex,
DHL, etc.
For transporting their product to other distribution channel, Toyota is using Intelligent
Transport System. This system comprises of different technologies related with
telecommunication and electronic that associate traffic infrastructure and environments along
with people and vehicles to develop new social method that can accomplish safe, convenient
traffic, efficient as well as environment friendly and social environment. Toyota is operating its
outbound logistics by using ten suppliers at VDCs , forty- five providers for land ( mainly truck)
and ten shipping line which transfer their products to different channels of distribution and they
further deliver it to the end buyers.
Networks: Network generates big and clear picture that provides better understanding in
terms of flow of information and material. It critically assesses the overall movement of
company's information and material from start to end, empower firm to develop valuable
partnership with their clients and collectively work together in order to satisfy the need of end
consumers. It is important for an organisation to have better link between material and
information so as to make their network channel simple and flexible. Entities are connected by
two types of flows:
Material Flow: This includes movement of raw material into final or complete product
that is going to be distributed to potential buyers.
Information Flow: Organisation is required to gather all relevant information related to
demand and supply of their products in the market. It is important for a firm to have knowledge
about the changing needs and demand of consumers so that they can make or modify their
products accordingly.
Focal Firm plays the role of mediator by transferring material and information to
company (Prajogo and Olhager, 2012). They are required to forecast the future demand of
particular product and provide this necessary information to suppliers which help them to reduce
3
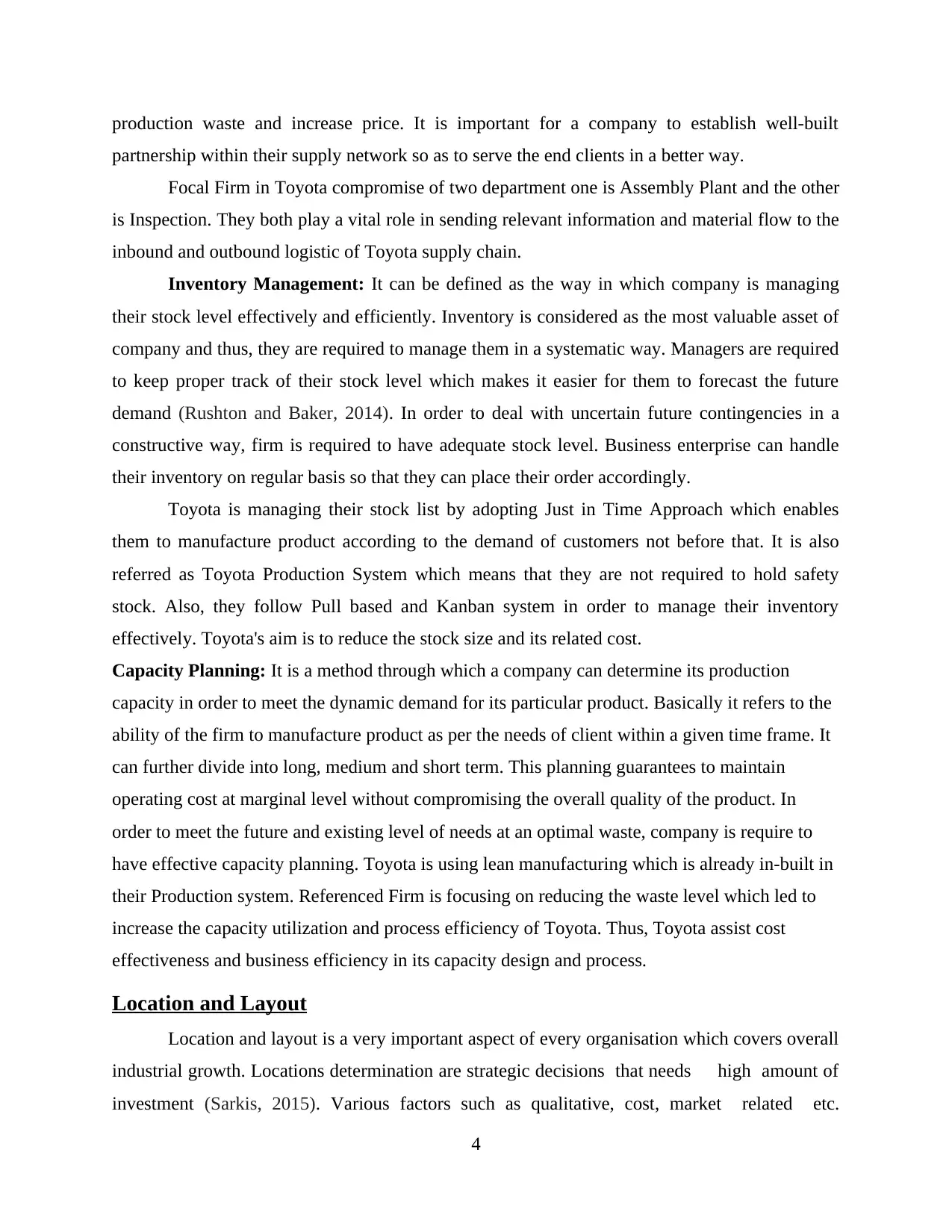
production waste and increase price. It is important for a company to establish well-built
partnership within their supply network so as to serve the end clients in a better way.
Focal Firm in Toyota compromise of two department one is Assembly Plant and the other
is Inspection. They both play a vital role in sending relevant information and material flow to the
inbound and outbound logistic of Toyota supply chain.
Inventory Management: It can be defined as the way in which company is managing
their stock level effectively and efficiently. Inventory is considered as the most valuable asset of
company and thus, they are required to manage them in a systematic way. Managers are required
to keep proper track of their stock level which makes it easier for them to forecast the future
demand (Rushton and Baker, 2014). In order to deal with uncertain future contingencies in a
constructive way, firm is required to have adequate stock level. Business enterprise can handle
their inventory on regular basis so that they can place their order accordingly.
Toyota is managing their stock list by adopting Just in Time Approach which enables
them to manufacture product according to the demand of customers not before that. It is also
referred as Toyota Production System which means that they are not required to hold safety
stock. Also, they follow Pull based and Kanban system in order to manage their inventory
effectively. Toyota's aim is to reduce the stock size and its related cost.
Capacity Planning: It is a method through which a company can determine its production
capacity in order to meet the dynamic demand for its particular product. Basically it refers to the
ability of the firm to manufacture product as per the needs of client within a given time frame. It
can further divide into long, medium and short term. This planning guarantees to maintain
operating cost at marginal level without compromising the overall quality of the product. In
order to meet the future and existing level of needs at an optimal waste, company is require to
have effective capacity planning. Toyota is using lean manufacturing which is already in-built in
their Production system. Referenced Firm is focusing on reducing the waste level which led to
increase the capacity utilization and process efficiency of Toyota. Thus, Toyota assist cost
effectiveness and business efficiency in its capacity design and process.
Location and Layout
Location and layout is a very important aspect of every organisation which covers overall
industrial growth. Locations determination are strategic decisions that needs high amount of
investment (Sarkis, 2015). Various factors such as qualitative, cost, market related etc.
4
partnership within their supply network so as to serve the end clients in a better way.
Focal Firm in Toyota compromise of two department one is Assembly Plant and the other
is Inspection. They both play a vital role in sending relevant information and material flow to the
inbound and outbound logistic of Toyota supply chain.
Inventory Management: It can be defined as the way in which company is managing
their stock level effectively and efficiently. Inventory is considered as the most valuable asset of
company and thus, they are required to manage them in a systematic way. Managers are required
to keep proper track of their stock level which makes it easier for them to forecast the future
demand (Rushton and Baker, 2014). In order to deal with uncertain future contingencies in a
constructive way, firm is required to have adequate stock level. Business enterprise can handle
their inventory on regular basis so that they can place their order accordingly.
Toyota is managing their stock list by adopting Just in Time Approach which enables
them to manufacture product according to the demand of customers not before that. It is also
referred as Toyota Production System which means that they are not required to hold safety
stock. Also, they follow Pull based and Kanban system in order to manage their inventory
effectively. Toyota's aim is to reduce the stock size and its related cost.
Capacity Planning: It is a method through which a company can determine its production
capacity in order to meet the dynamic demand for its particular product. Basically it refers to the
ability of the firm to manufacture product as per the needs of client within a given time frame. It
can further divide into long, medium and short term. This planning guarantees to maintain
operating cost at marginal level without compromising the overall quality of the product. In
order to meet the future and existing level of needs at an optimal waste, company is require to
have effective capacity planning. Toyota is using lean manufacturing which is already in-built in
their Production system. Referenced Firm is focusing on reducing the waste level which led to
increase the capacity utilization and process efficiency of Toyota. Thus, Toyota assist cost
effectiveness and business efficiency in its capacity design and process.
Location and Layout
Location and layout is a very important aspect of every organisation which covers overall
industrial growth. Locations determination are strategic decisions that needs high amount of
investment (Sarkis, 2015). Various factors such as qualitative, cost, market related etc.
4
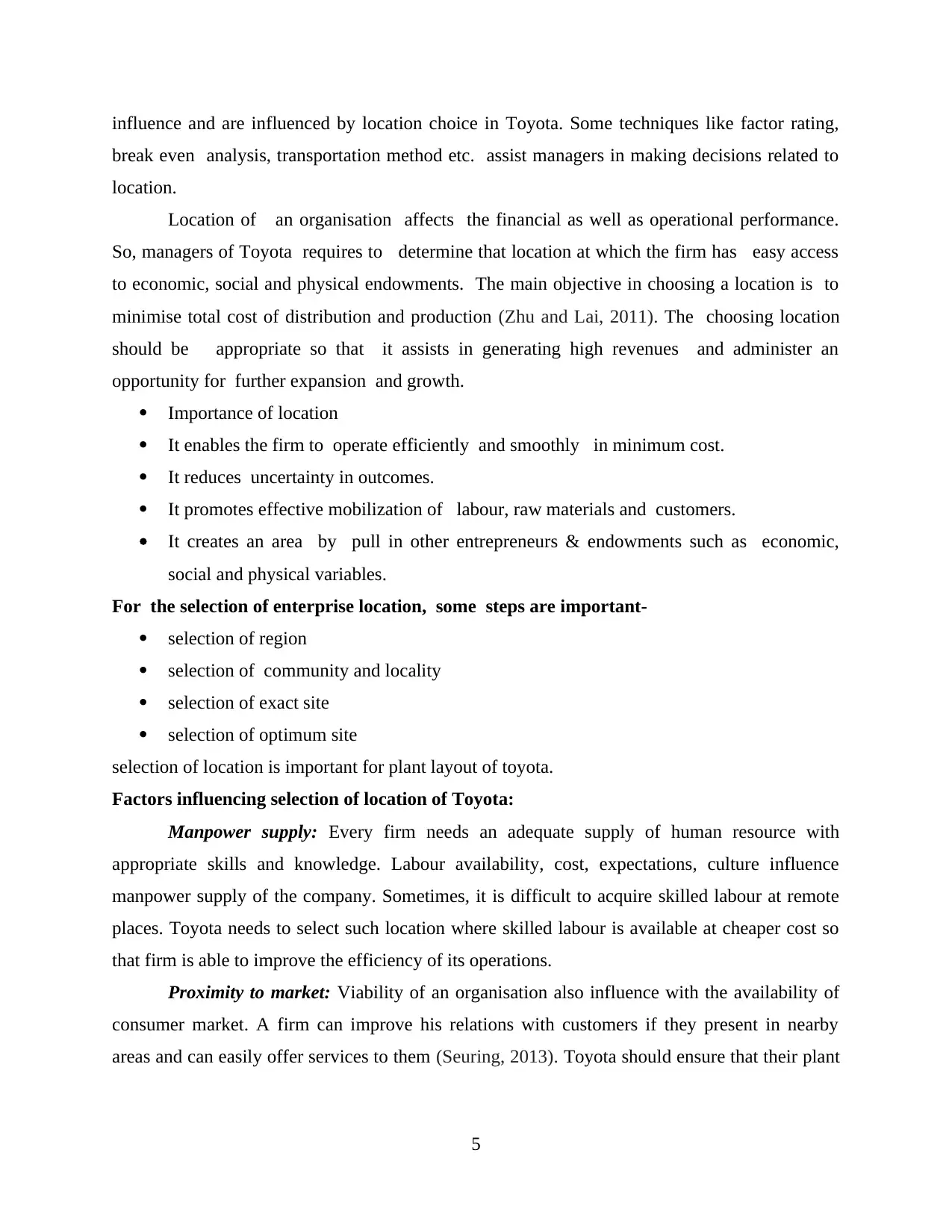
influence and are influenced by location choice in Toyota. Some techniques like factor rating,
break even analysis, transportation method etc. assist managers in making decisions related to
location.
Location of an organisation affects the financial as well as operational performance.
So, managers of Toyota requires to determine that location at which the firm has easy access
to economic, social and physical endowments. The main objective in choosing a location is to
minimise total cost of distribution and production (Zhu and Lai, 2011). The choosing location
should be appropriate so that it assists in generating high revenues and administer an
opportunity for further expansion and growth.
Importance of location
It enables the firm to operate efficiently and smoothly in minimum cost.
It reduces uncertainty in outcomes.
It promotes effective mobilization of labour, raw materials and customers.
It creates an area by pull in other entrepreneurs & endowments such as economic,
social and physical variables.
For the selection of enterprise location, some steps are important-
selection of region
selection of community and locality
selection of exact site
selection of optimum site
selection of location is important for plant layout of toyota.
Factors influencing selection of location of Toyota:
Manpower supply: Every firm needs an adequate supply of human resource with
appropriate skills and knowledge. Labour availability, cost, expectations, culture influence
manpower supply of the company. Sometimes, it is difficult to acquire skilled labour at remote
places. Toyota needs to select such location where skilled labour is available at cheaper cost so
that firm is able to improve the efficiency of its operations.
Proximity to market: Viability of an organisation also influence with the availability of
consumer market. A firm can improve his relations with customers if they present in nearby
areas and can easily offer services to them (Seuring, 2013). Toyota should ensure that their plant
5
break even analysis, transportation method etc. assist managers in making decisions related to
location.
Location of an organisation affects the financial as well as operational performance.
So, managers of Toyota requires to determine that location at which the firm has easy access
to economic, social and physical endowments. The main objective in choosing a location is to
minimise total cost of distribution and production (Zhu and Lai, 2011). The choosing location
should be appropriate so that it assists in generating high revenues and administer an
opportunity for further expansion and growth.
Importance of location
It enables the firm to operate efficiently and smoothly in minimum cost.
It reduces uncertainty in outcomes.
It promotes effective mobilization of labour, raw materials and customers.
It creates an area by pull in other entrepreneurs & endowments such as economic,
social and physical variables.
For the selection of enterprise location, some steps are important-
selection of region
selection of community and locality
selection of exact site
selection of optimum site
selection of location is important for plant layout of toyota.
Factors influencing selection of location of Toyota:
Manpower supply: Every firm needs an adequate supply of human resource with
appropriate skills and knowledge. Labour availability, cost, expectations, culture influence
manpower supply of the company. Sometimes, it is difficult to acquire skilled labour at remote
places. Toyota needs to select such location where skilled labour is available at cheaper cost so
that firm is able to improve the efficiency of its operations.
Proximity to market: Viability of an organisation also influence with the availability of
consumer market. A firm can improve his relations with customers if they present in nearby
areas and can easily offer services to them (Seuring, 2013). Toyota should ensure that their plant
5
Paraphrase This Document
Need a fresh take? Get an instant paraphrase of this document with our AI Paraphraser
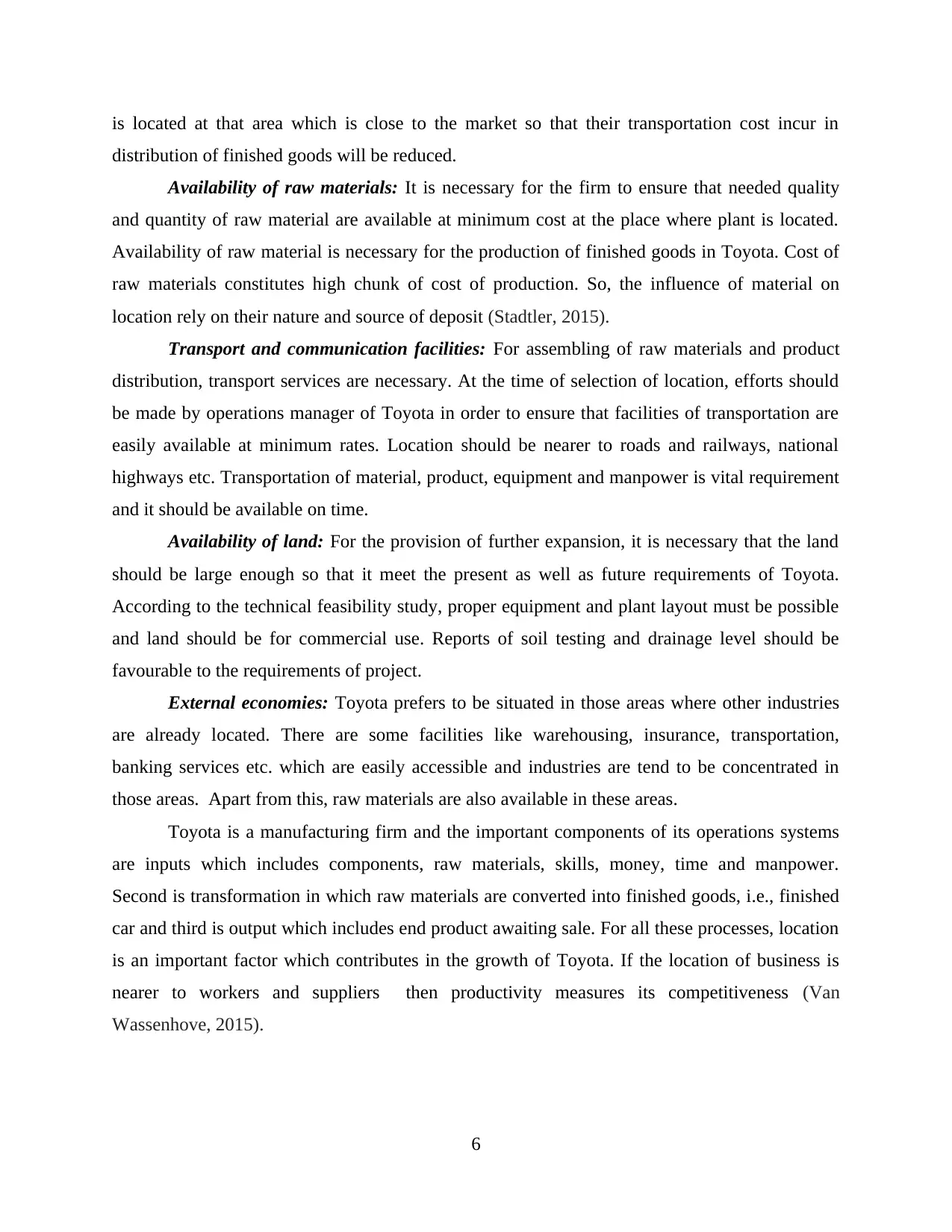
is located at that area which is close to the market so that their transportation cost incur in
distribution of finished goods will be reduced.
Availability of raw materials: It is necessary for the firm to ensure that needed quality
and quantity of raw material are available at minimum cost at the place where plant is located.
Availability of raw material is necessary for the production of finished goods in Toyota. Cost of
raw materials constitutes high chunk of cost of production. So, the influence of material on
location rely on their nature and source of deposit (Stadtler, 2015).
Transport and communication facilities: For assembling of raw materials and product
distribution, transport services are necessary. At the time of selection of location, efforts should
be made by operations manager of Toyota in order to ensure that facilities of transportation are
easily available at minimum rates. Location should be nearer to roads and railways, national
highways etc. Transportation of material, product, equipment and manpower is vital requirement
and it should be available on time.
Availability of land: For the provision of further expansion, it is necessary that the land
should be large enough so that it meet the present as well as future requirements of Toyota.
According to the technical feasibility study, proper equipment and plant layout must be possible
and land should be for commercial use. Reports of soil testing and drainage level should be
favourable to the requirements of project.
External economies: Toyota prefers to be situated in those areas where other industries
are already located. There are some facilities like warehousing, insurance, transportation,
banking services etc. which are easily accessible and industries are tend to be concentrated in
those areas. Apart from this, raw materials are also available in these areas.
Toyota is a manufacturing firm and the important components of its operations systems
are inputs which includes components, raw materials, skills, money, time and manpower.
Second is transformation in which raw materials are converted into finished goods, i.e., finished
car and third is output which includes end product awaiting sale. For all these processes, location
is an important factor which contributes in the growth of Toyota. If the location of business is
nearer to workers and suppliers then productivity measures its competitiveness (Van
Wassenhove, 2015).
6
distribution of finished goods will be reduced.
Availability of raw materials: It is necessary for the firm to ensure that needed quality
and quantity of raw material are available at minimum cost at the place where plant is located.
Availability of raw material is necessary for the production of finished goods in Toyota. Cost of
raw materials constitutes high chunk of cost of production. So, the influence of material on
location rely on their nature and source of deposit (Stadtler, 2015).
Transport and communication facilities: For assembling of raw materials and product
distribution, transport services are necessary. At the time of selection of location, efforts should
be made by operations manager of Toyota in order to ensure that facilities of transportation are
easily available at minimum rates. Location should be nearer to roads and railways, national
highways etc. Transportation of material, product, equipment and manpower is vital requirement
and it should be available on time.
Availability of land: For the provision of further expansion, it is necessary that the land
should be large enough so that it meet the present as well as future requirements of Toyota.
According to the technical feasibility study, proper equipment and plant layout must be possible
and land should be for commercial use. Reports of soil testing and drainage level should be
favourable to the requirements of project.
External economies: Toyota prefers to be situated in those areas where other industries
are already located. There are some facilities like warehousing, insurance, transportation,
banking services etc. which are easily accessible and industries are tend to be concentrated in
those areas. Apart from this, raw materials are also available in these areas.
Toyota is a manufacturing firm and the important components of its operations systems
are inputs which includes components, raw materials, skills, money, time and manpower.
Second is transformation in which raw materials are converted into finished goods, i.e., finished
car and third is output which includes end product awaiting sale. For all these processes, location
is an important factor which contributes in the growth of Toyota. If the location of business is
nearer to workers and suppliers then productivity measures its competitiveness (Van
Wassenhove, 2015).
6
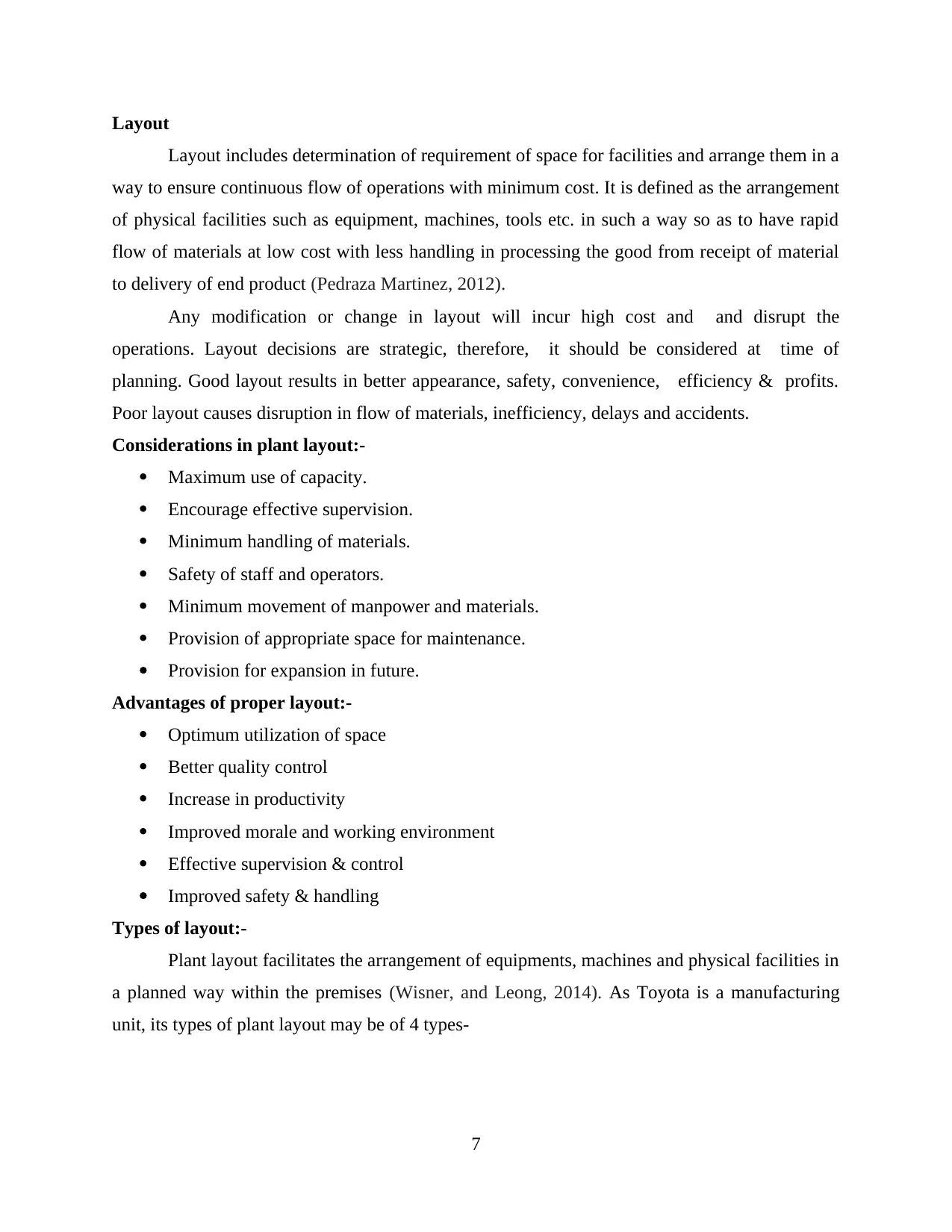
Layout
Layout includes determination of requirement of space for facilities and arrange them in a
way to ensure continuous flow of operations with minimum cost. It is defined as the arrangement
of physical facilities such as equipment, machines, tools etc. in such a way so as to have rapid
flow of materials at low cost with less handling in processing the good from receipt of material
to delivery of end product (Pedraza Martinez, 2012).
Any modification or change in layout will incur high cost and and disrupt the
operations. Layout decisions are strategic, therefore, it should be considered at time of
planning. Good layout results in better appearance, safety, convenience, efficiency & profits.
Poor layout causes disruption in flow of materials, inefficiency, delays and accidents.
Considerations in plant layout:-
Maximum use of capacity.
Encourage effective supervision.
Minimum handling of materials.
Safety of staff and operators.
Minimum movement of manpower and materials.
Provision of appropriate space for maintenance.
Provision for expansion in future.
Advantages of proper layout:-
Optimum utilization of space
Better quality control
Increase in productivity
Improved morale and working environment
Effective supervision & control
Improved safety & handling
Types of layout:-
Plant layout facilitates the arrangement of equipments, machines and physical facilities in
a planned way within the premises (Wisner, and Leong, 2014). As Toyota is a manufacturing
unit, its types of plant layout may be of 4 types-
7
Layout includes determination of requirement of space for facilities and arrange them in a
way to ensure continuous flow of operations with minimum cost. It is defined as the arrangement
of physical facilities such as equipment, machines, tools etc. in such a way so as to have rapid
flow of materials at low cost with less handling in processing the good from receipt of material
to delivery of end product (Pedraza Martinez, 2012).
Any modification or change in layout will incur high cost and and disrupt the
operations. Layout decisions are strategic, therefore, it should be considered at time of
planning. Good layout results in better appearance, safety, convenience, efficiency & profits.
Poor layout causes disruption in flow of materials, inefficiency, delays and accidents.
Considerations in plant layout:-
Maximum use of capacity.
Encourage effective supervision.
Minimum handling of materials.
Safety of staff and operators.
Minimum movement of manpower and materials.
Provision of appropriate space for maintenance.
Provision for expansion in future.
Advantages of proper layout:-
Optimum utilization of space
Better quality control
Increase in productivity
Improved morale and working environment
Effective supervision & control
Improved safety & handling
Types of layout:-
Plant layout facilitates the arrangement of equipments, machines and physical facilities in
a planned way within the premises (Wisner, and Leong, 2014). As Toyota is a manufacturing
unit, its types of plant layout may be of 4 types-
7
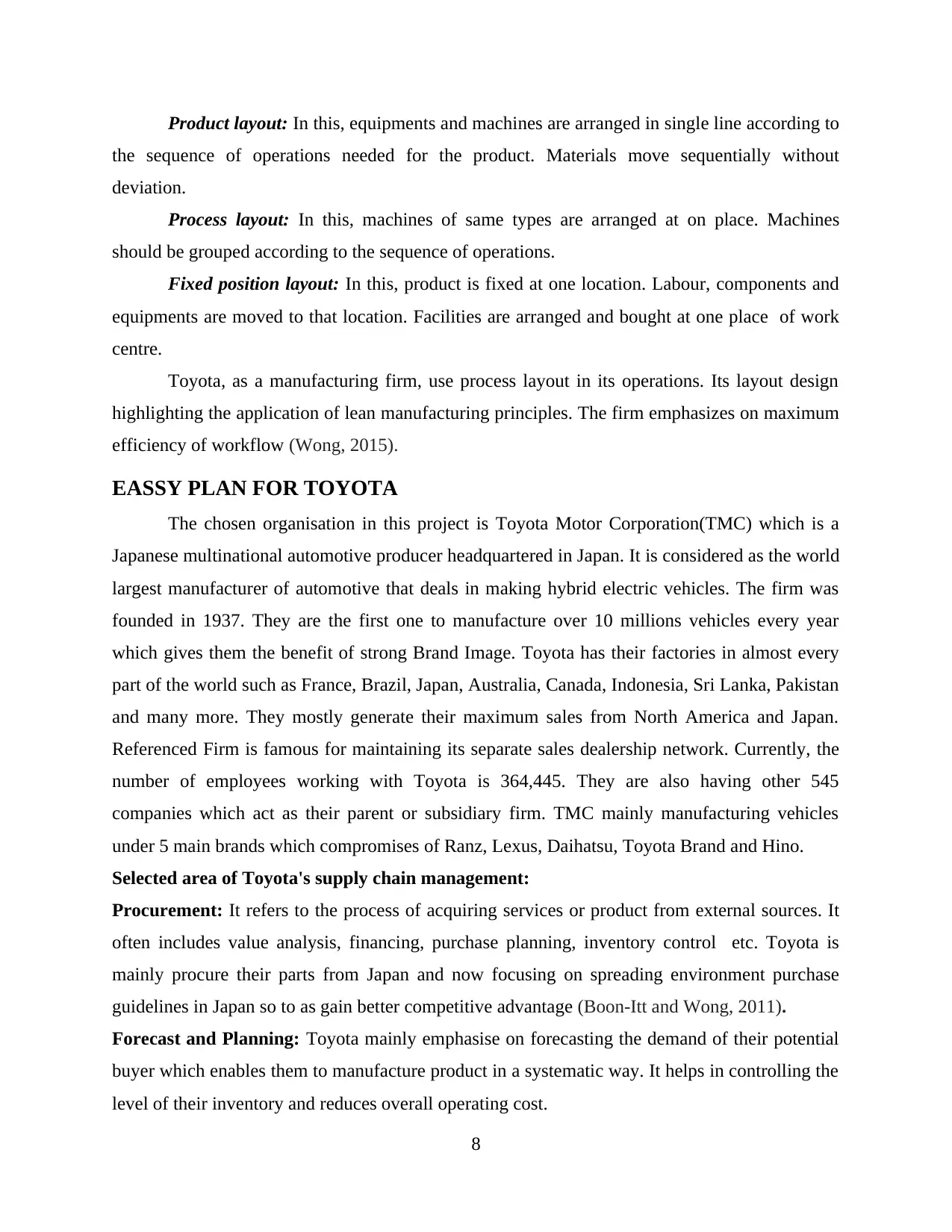
Product layout: In this, equipments and machines are arranged in single line according to
the sequence of operations needed for the product. Materials move sequentially without
deviation.
Process layout: In this, machines of same types are arranged at on place. Machines
should be grouped according to the sequence of operations.
Fixed position layout: In this, product is fixed at one location. Labour, components and
equipments are moved to that location. Facilities are arranged and bought at one place of work
centre.
Toyota, as a manufacturing firm, use process layout in its operations. Its layout design
highlighting the application of lean manufacturing principles. The firm emphasizes on maximum
efficiency of workflow (Wong, 2015).
EASSY PLAN FOR TOYOTA
The chosen organisation in this project is Toyota Motor Corporation(TMC) which is a
Japanese multinational automotive producer headquartered in Japan. It is considered as the world
largest manufacturer of automotive that deals in making hybrid electric vehicles. The firm was
founded in 1937. They are the first one to manufacture over 10 millions vehicles every year
which gives them the benefit of strong Brand Image. Toyota has their factories in almost every
part of the world such as France, Brazil, Japan, Australia, Canada, Indonesia, Sri Lanka, Pakistan
and many more. They mostly generate their maximum sales from North America and Japan.
Referenced Firm is famous for maintaining its separate sales dealership network. Currently, the
number of employees working with Toyota is 364,445. They are also having other 545
companies which act as their parent or subsidiary firm. TMC mainly manufacturing vehicles
under 5 main brands which compromises of Ranz, Lexus, Daihatsu, Toyota Brand and Hino.
Selected area of Toyota's supply chain management:
Procurement: It refers to the process of acquiring services or product from external sources. It
often includes value analysis, financing, purchase planning, inventory control etc. Toyota is
mainly procure their parts from Japan and now focusing on spreading environment purchase
guidelines in Japan so to as gain better competitive advantage (Boon-Itt and Wong, 2011).
Forecast and Planning: Toyota mainly emphasise on forecasting the demand of their potential
buyer which enables them to manufacture product in a systematic way. It helps in controlling the
level of their inventory and reduces overall operating cost.
8
the sequence of operations needed for the product. Materials move sequentially without
deviation.
Process layout: In this, machines of same types are arranged at on place. Machines
should be grouped according to the sequence of operations.
Fixed position layout: In this, product is fixed at one location. Labour, components and
equipments are moved to that location. Facilities are arranged and bought at one place of work
centre.
Toyota, as a manufacturing firm, use process layout in its operations. Its layout design
highlighting the application of lean manufacturing principles. The firm emphasizes on maximum
efficiency of workflow (Wong, 2015).
EASSY PLAN FOR TOYOTA
The chosen organisation in this project is Toyota Motor Corporation(TMC) which is a
Japanese multinational automotive producer headquartered in Japan. It is considered as the world
largest manufacturer of automotive that deals in making hybrid electric vehicles. The firm was
founded in 1937. They are the first one to manufacture over 10 millions vehicles every year
which gives them the benefit of strong Brand Image. Toyota has their factories in almost every
part of the world such as France, Brazil, Japan, Australia, Canada, Indonesia, Sri Lanka, Pakistan
and many more. They mostly generate their maximum sales from North America and Japan.
Referenced Firm is famous for maintaining its separate sales dealership network. Currently, the
number of employees working with Toyota is 364,445. They are also having other 545
companies which act as their parent or subsidiary firm. TMC mainly manufacturing vehicles
under 5 main brands which compromises of Ranz, Lexus, Daihatsu, Toyota Brand and Hino.
Selected area of Toyota's supply chain management:
Procurement: It refers to the process of acquiring services or product from external sources. It
often includes value analysis, financing, purchase planning, inventory control etc. Toyota is
mainly procure their parts from Japan and now focusing on spreading environment purchase
guidelines in Japan so to as gain better competitive advantage (Boon-Itt and Wong, 2011).
Forecast and Planning: Toyota mainly emphasise on forecasting the demand of their potential
buyer which enables them to manufacture product in a systematic way. It helps in controlling the
level of their inventory and reduces overall operating cost.
8
Secure Best Marks with AI Grader
Need help grading? Try our AI Grader for instant feedback on your assignments.
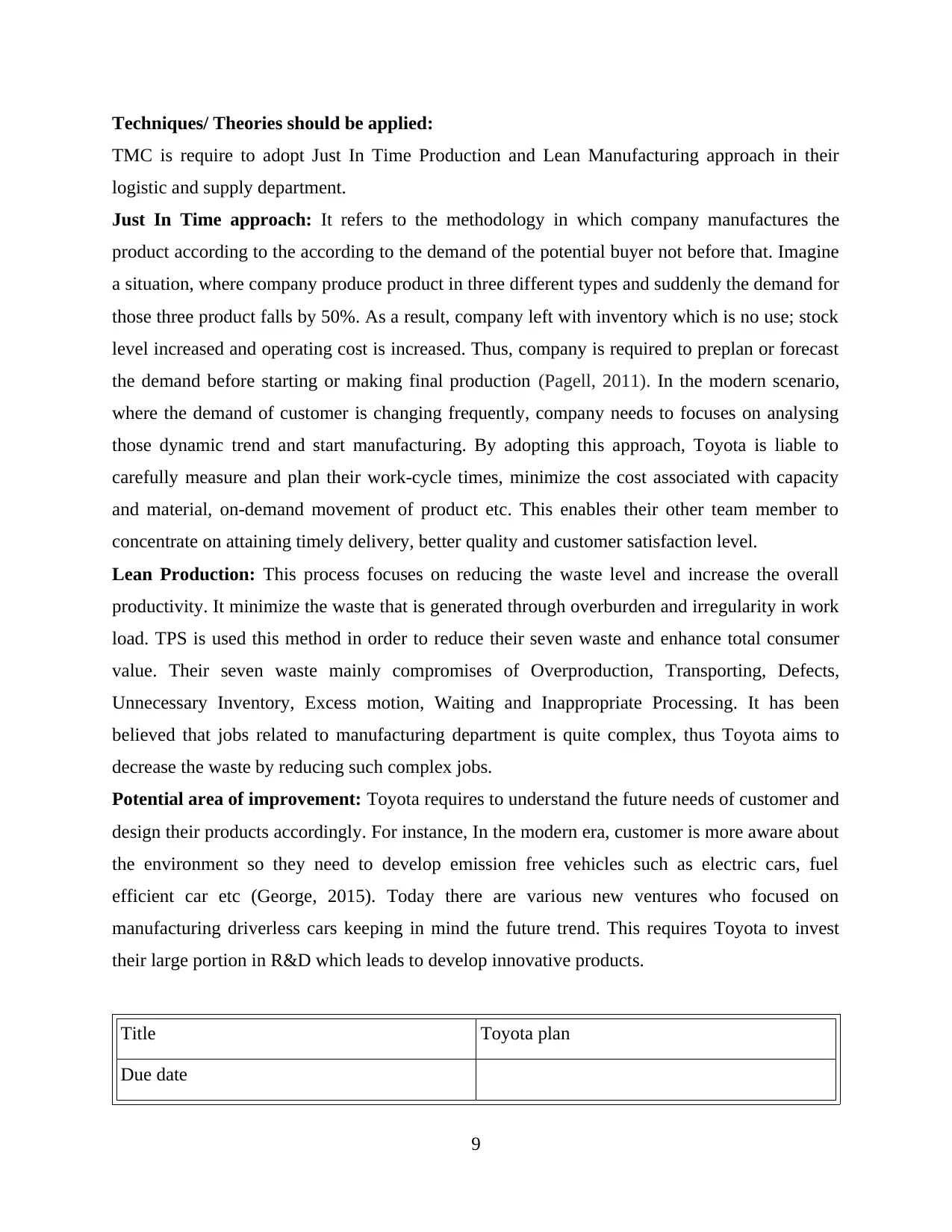
Techniques/ Theories should be applied:
TMC is require to adopt Just In Time Production and Lean Manufacturing approach in their
logistic and supply department.
Just In Time approach: It refers to the methodology in which company manufactures the
product according to the according to the demand of the potential buyer not before that. Imagine
a situation, where company produce product in three different types and suddenly the demand for
those three product falls by 50%. As a result, company left with inventory which is no use; stock
level increased and operating cost is increased. Thus, company is required to preplan or forecast
the demand before starting or making final production (Pagell, 2011). In the modern scenario,
where the demand of customer is changing frequently, company needs to focuses on analysing
those dynamic trend and start manufacturing. By adopting this approach, Toyota is liable to
carefully measure and plan their work-cycle times, minimize the cost associated with capacity
and material, on-demand movement of product etc. This enables their other team member to
concentrate on attaining timely delivery, better quality and customer satisfaction level.
Lean Production: This process focuses on reducing the waste level and increase the overall
productivity. It minimize the waste that is generated through overburden and irregularity in work
load. TPS is used this method in order to reduce their seven waste and enhance total consumer
value. Their seven waste mainly compromises of Overproduction, Transporting, Defects,
Unnecessary Inventory, Excess motion, Waiting and Inappropriate Processing. It has been
believed that jobs related to manufacturing department is quite complex, thus Toyota aims to
decrease the waste by reducing such complex jobs.
Potential area of improvement: Toyota requires to understand the future needs of customer and
design their products accordingly. For instance, In the modern era, customer is more aware about
the environment so they need to develop emission free vehicles such as electric cars, fuel
efficient car etc (George, 2015). Today there are various new ventures who focused on
manufacturing driverless cars keeping in mind the future trend. This requires Toyota to invest
their large portion in R&D which leads to develop innovative products.
Title Toyota plan
Due date
9
TMC is require to adopt Just In Time Production and Lean Manufacturing approach in their
logistic and supply department.
Just In Time approach: It refers to the methodology in which company manufactures the
product according to the according to the demand of the potential buyer not before that. Imagine
a situation, where company produce product in three different types and suddenly the demand for
those three product falls by 50%. As a result, company left with inventory which is no use; stock
level increased and operating cost is increased. Thus, company is required to preplan or forecast
the demand before starting or making final production (Pagell, 2011). In the modern scenario,
where the demand of customer is changing frequently, company needs to focuses on analysing
those dynamic trend and start manufacturing. By adopting this approach, Toyota is liable to
carefully measure and plan their work-cycle times, minimize the cost associated with capacity
and material, on-demand movement of product etc. This enables their other team member to
concentrate on attaining timely delivery, better quality and customer satisfaction level.
Lean Production: This process focuses on reducing the waste level and increase the overall
productivity. It minimize the waste that is generated through overburden and irregularity in work
load. TPS is used this method in order to reduce their seven waste and enhance total consumer
value. Their seven waste mainly compromises of Overproduction, Transporting, Defects,
Unnecessary Inventory, Excess motion, Waiting and Inappropriate Processing. It has been
believed that jobs related to manufacturing department is quite complex, thus Toyota aims to
decrease the waste by reducing such complex jobs.
Potential area of improvement: Toyota requires to understand the future needs of customer and
design their products accordingly. For instance, In the modern era, customer is more aware about
the environment so they need to develop emission free vehicles such as electric cars, fuel
efficient car etc (George, 2015). Today there are various new ventures who focused on
manufacturing driverless cars keeping in mind the future trend. This requires Toyota to invest
their large portion in R&D which leads to develop innovative products.
Title Toyota plan
Due date
9
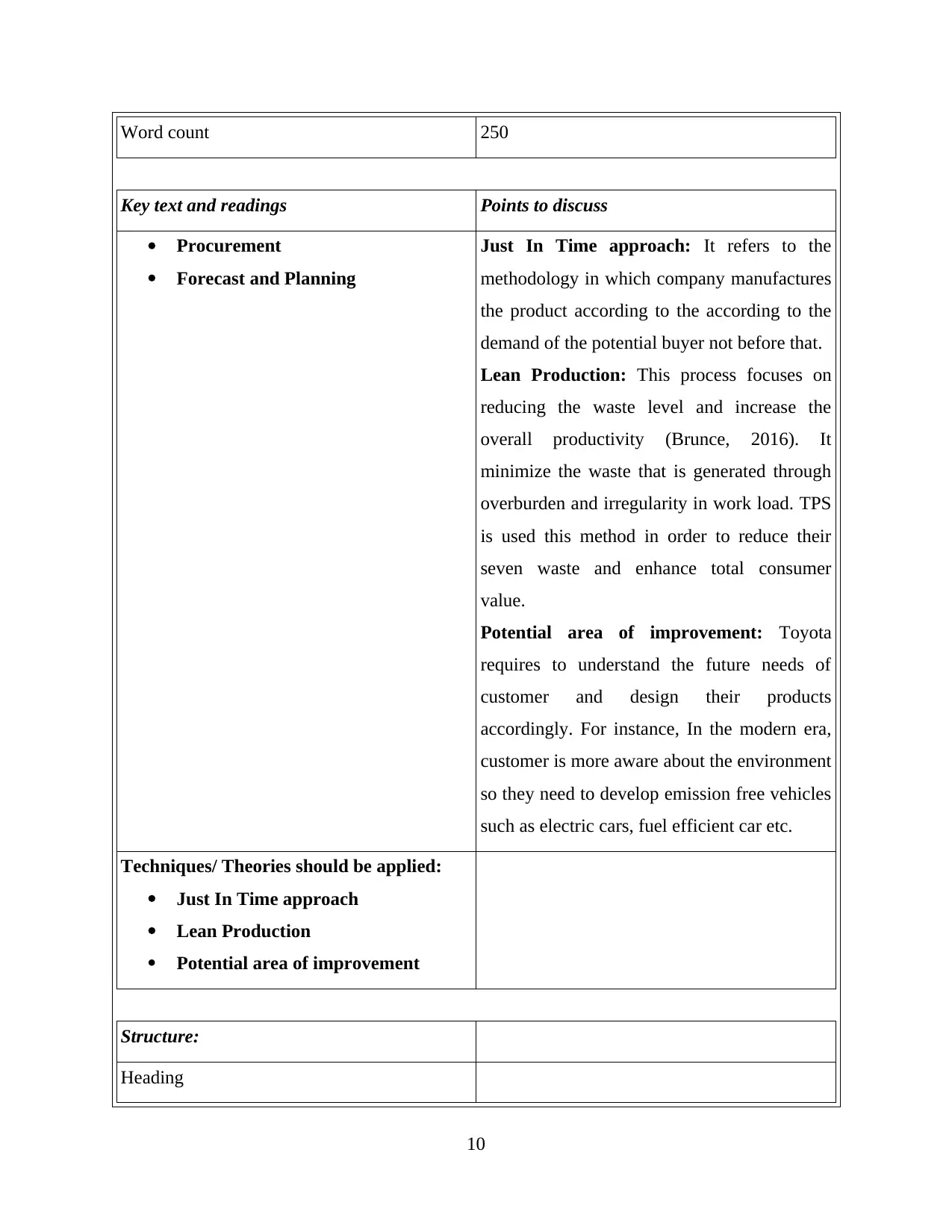
Word count 250
Key text and readings Points to discuss
Procurement
Forecast and Planning
Just In Time approach: It refers to the
methodology in which company manufactures
the product according to the according to the
demand of the potential buyer not before that.
Lean Production: This process focuses on
reducing the waste level and increase the
overall productivity (Brunce, 2016). It
minimize the waste that is generated through
overburden and irregularity in work load. TPS
is used this method in order to reduce their
seven waste and enhance total consumer
value.
Potential area of improvement: Toyota
requires to understand the future needs of
customer and design their products
accordingly. For instance, In the modern era,
customer is more aware about the environment
so they need to develop emission free vehicles
such as electric cars, fuel efficient car etc.
Techniques/ Theories should be applied:
Just In Time approach
Lean Production
Potential area of improvement
Structure:
Heading
10
Key text and readings Points to discuss
Procurement
Forecast and Planning
Just In Time approach: It refers to the
methodology in which company manufactures
the product according to the according to the
demand of the potential buyer not before that.
Lean Production: This process focuses on
reducing the waste level and increase the
overall productivity (Brunce, 2016). It
minimize the waste that is generated through
overburden and irregularity in work load. TPS
is used this method in order to reduce their
seven waste and enhance total consumer
value.
Potential area of improvement: Toyota
requires to understand the future needs of
customer and design their products
accordingly. For instance, In the modern era,
customer is more aware about the environment
so they need to develop emission free vehicles
such as electric cars, fuel efficient car etc.
Techniques/ Theories should be applied:
Just In Time approach
Lean Production
Potential area of improvement
Structure:
Heading
10
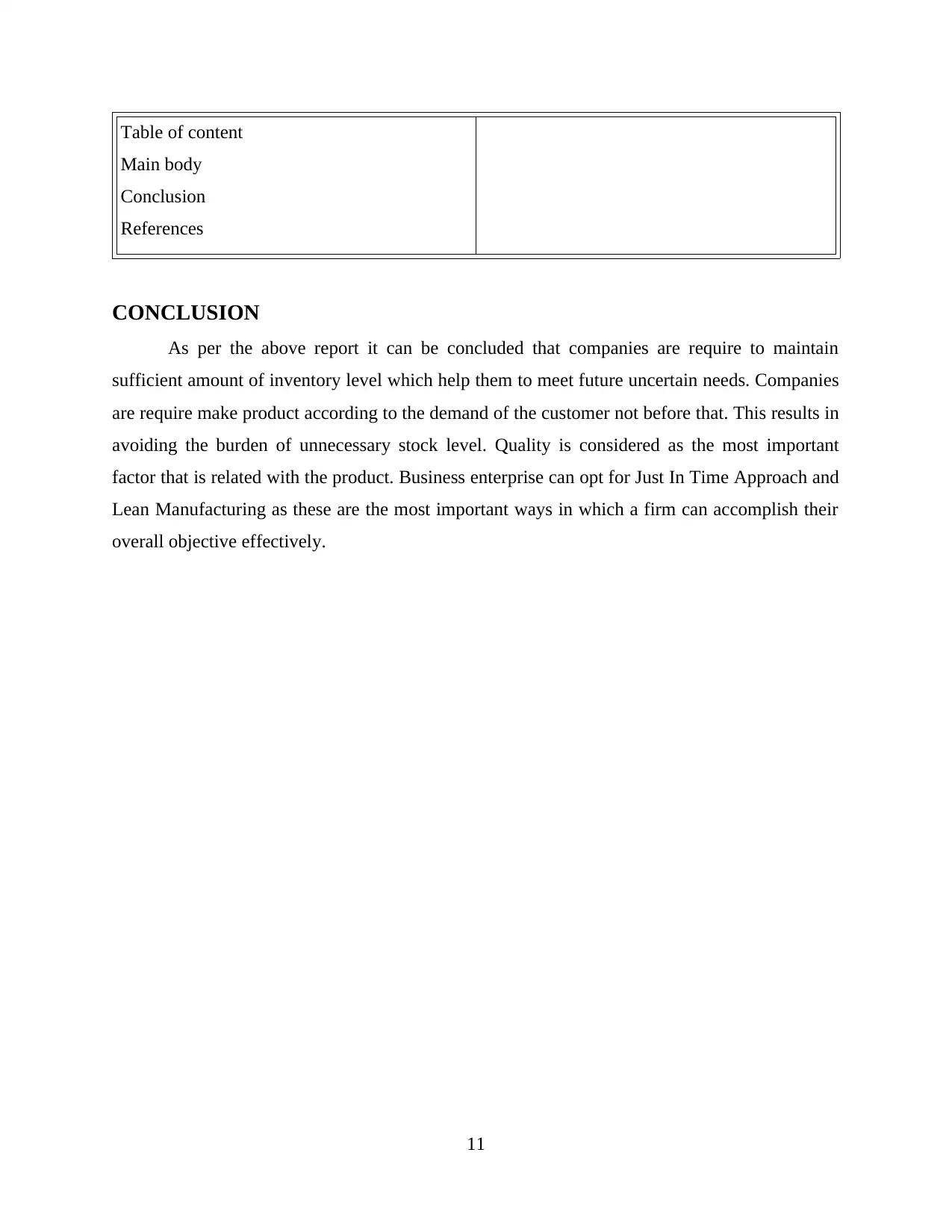
Table of content
Main body
Conclusion
References
CONCLUSION
As per the above report it can be concluded that companies are require to maintain
sufficient amount of inventory level which help them to meet future uncertain needs. Companies
are require make product according to the demand of the customer not before that. This results in
avoiding the burden of unnecessary stock level. Quality is considered as the most important
factor that is related with the product. Business enterprise can opt for Just In Time Approach and
Lean Manufacturing as these are the most important ways in which a firm can accomplish their
overall objective effectively.
11
Main body
Conclusion
References
CONCLUSION
As per the above report it can be concluded that companies are require to maintain
sufficient amount of inventory level which help them to meet future uncertain needs. Companies
are require make product according to the demand of the customer not before that. This results in
avoiding the burden of unnecessary stock level. Quality is considered as the most important
factor that is related with the product. Business enterprise can opt for Just In Time Approach and
Lean Manufacturing as these are the most important ways in which a firm can accomplish their
overall objective effectively.
11
Paraphrase This Document
Need a fresh take? Get an instant paraphrase of this document with our AI Paraphraser
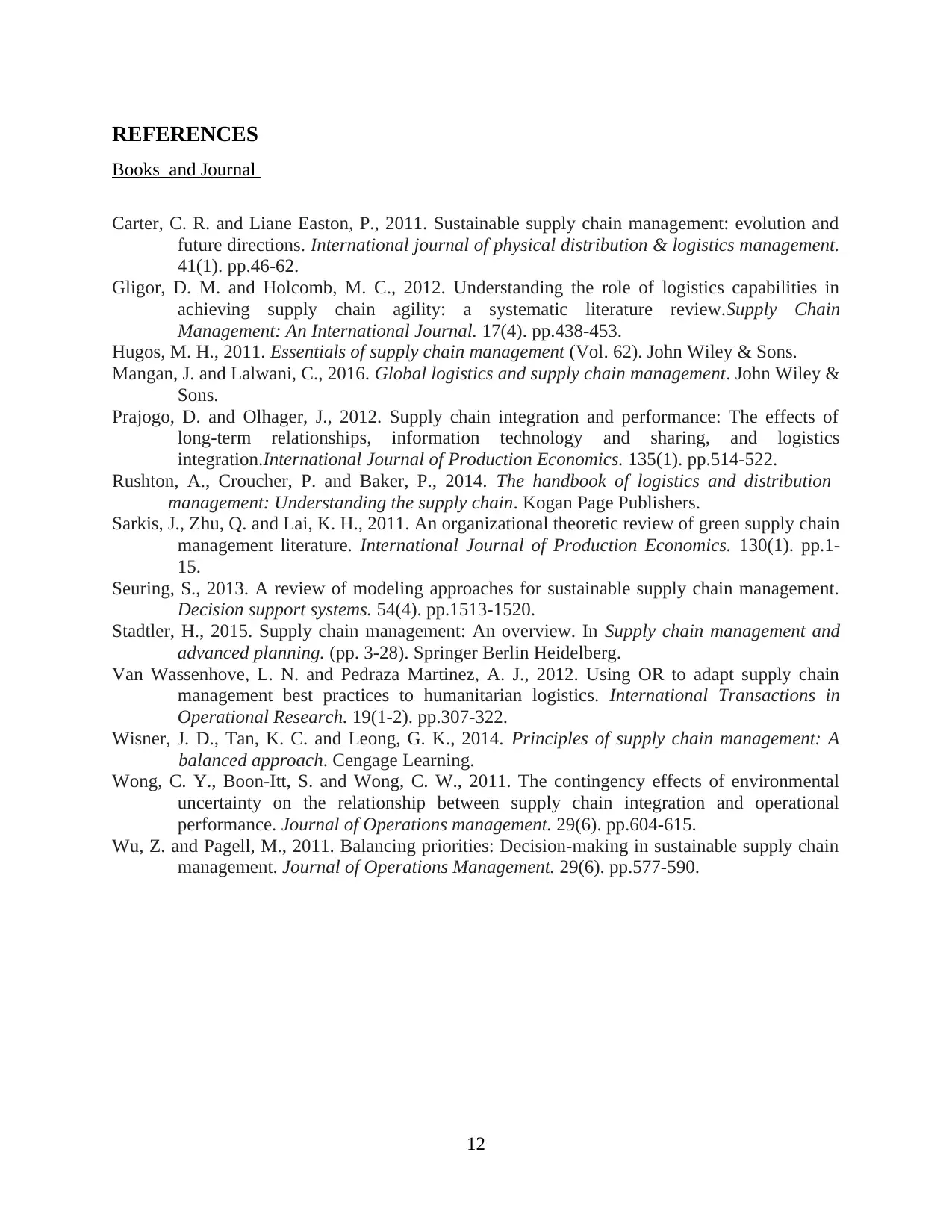
REFERENCES
Books and Journal
Carter, C. R. and Liane Easton, P., 2011. Sustainable supply chain management: evolution and
future directions. International journal of physical distribution & logistics management.
41(1). pp.46-62.
Gligor, D. M. and Holcomb, M. C., 2012. Understanding the role of logistics capabilities in
achieving supply chain agility: a systematic literature review.Supply Chain
Management: An International Journal. 17(4). pp.438-453.
Hugos, M. H., 2011. Essentials of supply chain management (Vol. 62). John Wiley & Sons.
Mangan, J. and Lalwani, C., 2016. Global logistics and supply chain management. John Wiley &
Sons.
Prajogo, D. and Olhager, J., 2012. Supply chain integration and performance: The effects of
long-term relationships, information technology and sharing, and logistics
integration.International Journal of Production Economics. 135(1). pp.514-522.
Rushton, A., Croucher, P. and Baker, P., 2014. The handbook of logistics and distribution
management: Understanding the supply chain. Kogan Page Publishers.
Sarkis, J., Zhu, Q. and Lai, K. H., 2011. An organizational theoretic review of green supply chain
management literature. International Journal of Production Economics. 130(1). pp.1-
15.
Seuring, S., 2013. A review of modeling approaches for sustainable supply chain management.
Decision support systems. 54(4). pp.1513-1520.
Stadtler, H., 2015. Supply chain management: An overview. In Supply chain management and
advanced planning. (pp. 3-28). Springer Berlin Heidelberg.
Van Wassenhove, L. N. and Pedraza Martinez, A. J., 2012. Using OR to adapt supply chain
management best practices to humanitarian logistics. International Transactions in
Operational Research. 19(1-2). pp.307-322.
Wisner, J. D., Tan, K. C. and Leong, G. K., 2014. Principles of supply chain management: A
balanced approach. Cengage Learning.
Wong, C. Y., Boon-Itt, S. and Wong, C. W., 2011. The contingency effects of environmental
uncertainty on the relationship between supply chain integration and operational
performance. Journal of Operations management. 29(6). pp.604-615.
Wu, Z. and Pagell, M., 2011. Balancing priorities: Decision-making in sustainable supply chain
management. Journal of Operations Management. 29(6). pp.577-590.
12
Books and Journal
Carter, C. R. and Liane Easton, P., 2011. Sustainable supply chain management: evolution and
future directions. International journal of physical distribution & logistics management.
41(1). pp.46-62.
Gligor, D. M. and Holcomb, M. C., 2012. Understanding the role of logistics capabilities in
achieving supply chain agility: a systematic literature review.Supply Chain
Management: An International Journal. 17(4). pp.438-453.
Hugos, M. H., 2011. Essentials of supply chain management (Vol. 62). John Wiley & Sons.
Mangan, J. and Lalwani, C., 2016. Global logistics and supply chain management. John Wiley &
Sons.
Prajogo, D. and Olhager, J., 2012. Supply chain integration and performance: The effects of
long-term relationships, information technology and sharing, and logistics
integration.International Journal of Production Economics. 135(1). pp.514-522.
Rushton, A., Croucher, P. and Baker, P., 2014. The handbook of logistics and distribution
management: Understanding the supply chain. Kogan Page Publishers.
Sarkis, J., Zhu, Q. and Lai, K. H., 2011. An organizational theoretic review of green supply chain
management literature. International Journal of Production Economics. 130(1). pp.1-
15.
Seuring, S., 2013. A review of modeling approaches for sustainable supply chain management.
Decision support systems. 54(4). pp.1513-1520.
Stadtler, H., 2015. Supply chain management: An overview. In Supply chain management and
advanced planning. (pp. 3-28). Springer Berlin Heidelberg.
Van Wassenhove, L. N. and Pedraza Martinez, A. J., 2012. Using OR to adapt supply chain
management best practices to humanitarian logistics. International Transactions in
Operational Research. 19(1-2). pp.307-322.
Wisner, J. D., Tan, K. C. and Leong, G. K., 2014. Principles of supply chain management: A
balanced approach. Cengage Learning.
Wong, C. Y., Boon-Itt, S. and Wong, C. W., 2011. The contingency effects of environmental
uncertainty on the relationship between supply chain integration and operational
performance. Journal of Operations management. 29(6). pp.604-615.
Wu, Z. and Pagell, M., 2011. Balancing priorities: Decision-making in sustainable supply chain
management. Journal of Operations Management. 29(6). pp.577-590.
12
1 out of 14
Related Documents
![[object Object]](/_next/image/?url=%2F_next%2Fstatic%2Fmedia%2Flogo.6d15ce61.png&w=640&q=75)
Your All-in-One AI-Powered Toolkit for Academic Success.
+13062052269
info@desklib.com
Available 24*7 on WhatsApp / Email
Unlock your academic potential
© 2024 | Zucol Services PVT LTD | All rights reserved.