Unit 9 Manufacturing Planning and Scheduling
11 Pages2213 Words55 Views
Added on 2021-04-17
Unit 9 Manufacturing Planning and Scheduling
Added on 2021-04-17
ShareRelated Documents
UNIT 9 MANUFACTURING PLANNING AND SCHEDULING A/601/1480NameDate
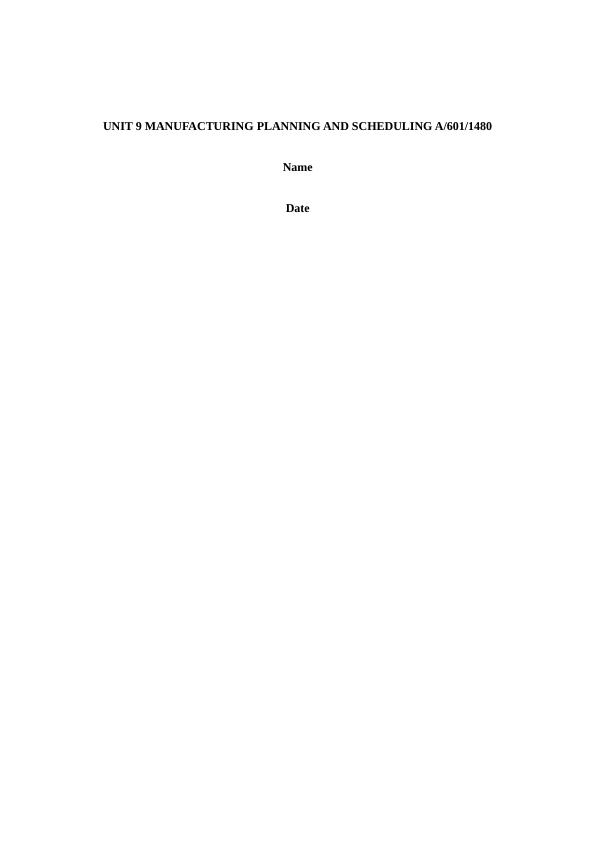
Task OneLO1: 1.11i.Critical Path Method (CPM): CPM was first put to action in 1957 and has since grown to become an important tool for overseeing large undertakings, such as major construction projects. It enhances efficiency through dividing efforts that are complicated into a series of smaller tasks with the resources and costs associated with each task. This enables managers to see areas that can experience potential breakdowns (Jack, 2013). Strengths of CPM: It makes it easy for project managers to build teams and create human networks for efficient handling projects with multiple tasks. It also binds the entire team together, helps projects be completed efficiently, and accurate project duration estimation and costing (Constantinou, 2013)Weaknesses of CPM: It can become very complicated in big projects, it cannot create and control schedules of people working in a project. For big projects, the critical path is not always clear, and CPM can be time consuming (Constantinou, 2013)ii.Materials Requirement Planning (MRP): MRP is a system for managing manufacturing processes. Initially, MRP was created in 1964 to support the Polaris program as a response to the Toyota Manufacturing Program. Black & Decker was its first user and had been implemented in 700 firms by 1975. It was developed in MRP II in 1983 by Oliver Wight to bring together rough cut capacity planning, master scheduling, and planning for capacity requirements. The MRP II software formed a third of all software sold in the US software sector by 1989 (Ptak, 2013). Strengths of MRP: Ensure materials needed for production are availed on time, results in little or no excess inventory, leads to timely deliveries of finished products, and uses manufacturing resources optimally. (Ptak, 2013). Weaknesses of MRP: Requires precise data to be entered and clean records to be kept, it also just provides a framework that has be used effectively, and if data is not accurate, a lot of problems can be experienced( Ptak, 2013). iii.Project Evaluation and Review Technique (PERT): It is a scheduling tool used commonly in project management, Was first used in the late 1950s in the US Navy in the Polaris missile project and uses a system of numbering events in sequences of tens or hundreds (Koontz and Weihrich, 2010)Strengths of PERT: Allows for analyses of activities, improves coordination n departments by improving planning and decision making, and enables analysis of what-if situations
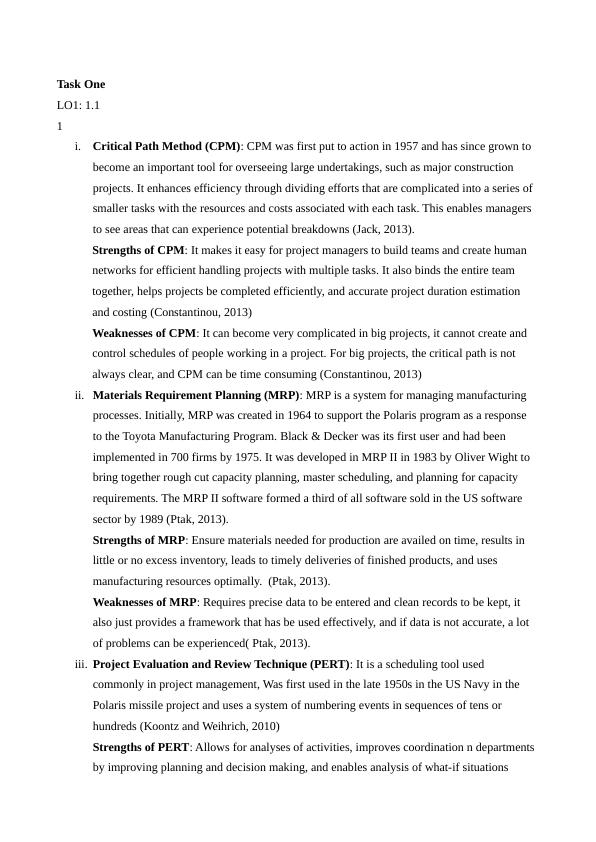
Weaknesses of PERT: It is a subjective analysis tool that requires new project activities to be identified and then arranged in sequence. Its basically a method focused on time and is resource intensive (Koontz and Weihrich, 2010)Task TwoLo1: 1.31i.Critical path Analysis: First, it requires activities to be identified, the activities sequence determined, and a network of the activities created. The completion time for all identified activities are then entered and the longest possible path (the critical path) to complete all the activities is then identified. The progress of the CPM should be updated regularly (Rodriguez, 2017)ii.Optimized Production Technology Philosophy: This is a proprietary computer software system of scheduling. OPT starts with performance measurement, planning projects, and identifying the software and hardware requirements. This is followed by plant analysis where manufacturing processes and their management are analyzed. Bottlenecks are then analyzed and computer modeling of the system done, followed by definition of data (data to be fed into system). Th outputs are then defined to create the MPS (master production schedule): this is achieved by planning for constraint capacity. The OPT is then operated through the OPT software to control complex manufacturing processes (Burcher, 2015). Task ThreeLO1: 1.2 1)Lead capacity strategy: in this strategy, capacity is added in expectation of demand. This isusually done by medium to large companies and is associated with large investments. This isa high capital intensive strategy Lag capacity strategy: This a capacity strategy where capacity is only added after the materialization of demand. This entails adding capacity only when existing capacity is exhausted or exceeded and is a more conservative strategy used by small to medium organizations. The investment in this case is small to medium Match capacity strategy: A strategy for capacity in which a balance between lag and lead capacity strategies is struck by avoiding periods of high over- or under- utilization. This is a moderate strategy with very low to low-medium investment implications and is used, or is suitable for very small organizations to medium firms, or even startups (Ross, 2015)2)Process list
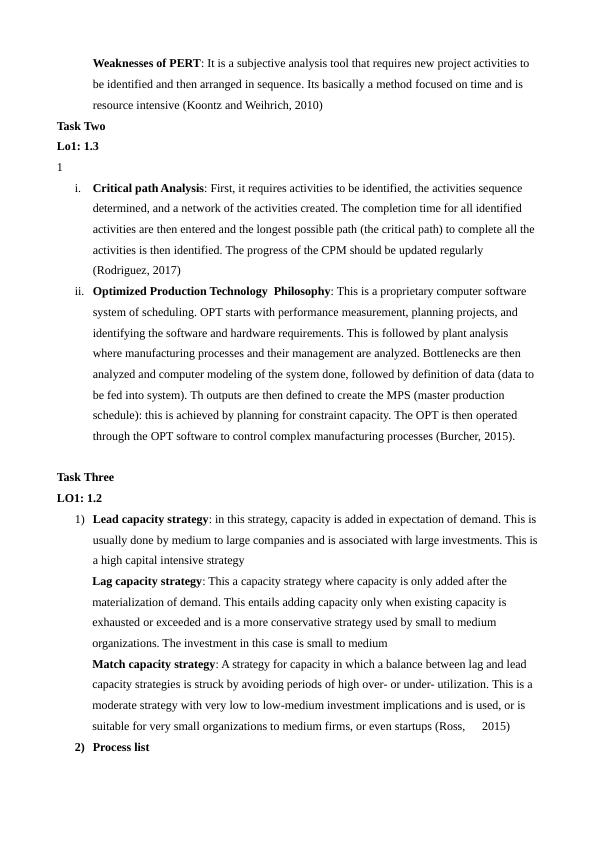
A thermoset wood plastic composite is assumed: The process entails air drying the wood particles until all moisture is removed. Plastic, usually polypropylene in fine powder form is then mixed afterweighing ) with plastic and then mixed together. Forming is then done in a stainless steel mold and Pre-heated, then heated in a hot press. They are then placed in the cold press (DeGarmo, Black and Kohser, 2008)This is a secondary manufacturing process that involves getting edges of the cooled panel trimmed to the desired shape. Drills are then used to make holes where screws will be drilled to make drawers (Rauner, 2012). 3)Capacity Assessmenti.Laminate composite material The laminated composite (wood plastic) is produced as follows:Laminate composite production takes 2160 seconds, forming. ii.Drilling takes 420 seconds. Assembly and inspection take 1020 seconds. Total time (CPM) is 3600 seconds (60 minutes) for a drawer set with five drawers. At 14 hours per day for 6 days, the capacity using a single line is 84 drawers as shown in the image belowActivityTime in SecondsLaminate productionPouring wood particles30Particles drying360Plastic particles pouring30High speed mixing300Forming300Pre heating300Hot pressing480Cold pressing360trimming and cuttingTrimming / cutting300Drilling120Assembling drawer900Inspection120Total Time 3600
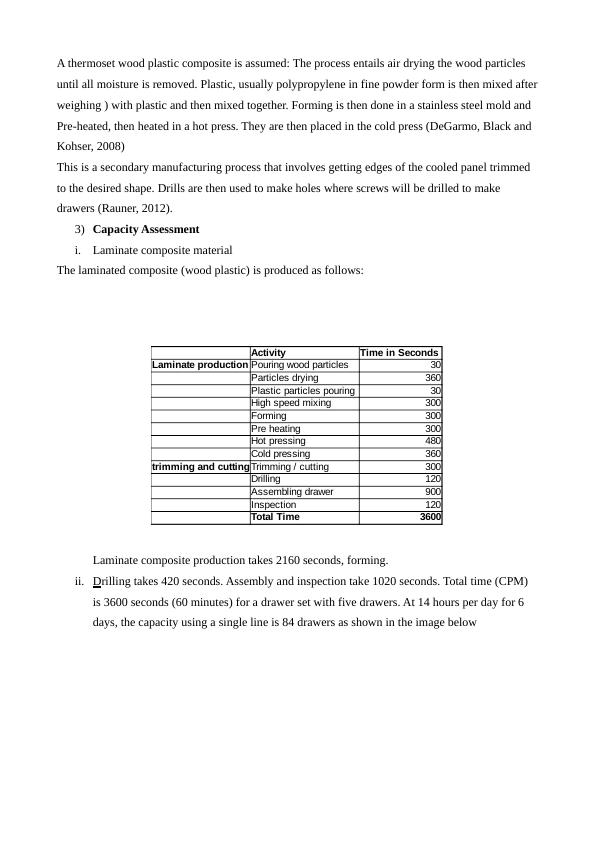
End of preview
Want to access all the pages? Upload your documents or become a member.
Related Documents
Project Time Cost Management Analysis 2022lg...
|5
|735
|27
Project Management: PERT, Critical Path Method, Crashinglg...
|6
|1153
|285
Report on PERT and CPM in Project Managementlg...
|16
|4190
|572
Project Management Techniques for Website Development for Target Australialg...
|23
|2955
|206
Development of website for Target Australialg...
|23
|3045
|12
Project Quality Management RUNNING HEADlg...
|5
|534
|154