L2 NVQ in Wood Occupations (Construction) QCF - Knowledge Question Paper
VerifiedAdded on 2023/01/10
|26
|11599
|53
AI Summary
This document is a knowledge question paper for the L2 NVQ in Wood Occupations (Construction) QCF. It covers topics such as health and safety control equipment, hazards in the work environment, and organizational policies and procedures for health, safety, and welfare.
Contribute Materials
Your contribution can guide someone’s learning journey. Share your
documents today.
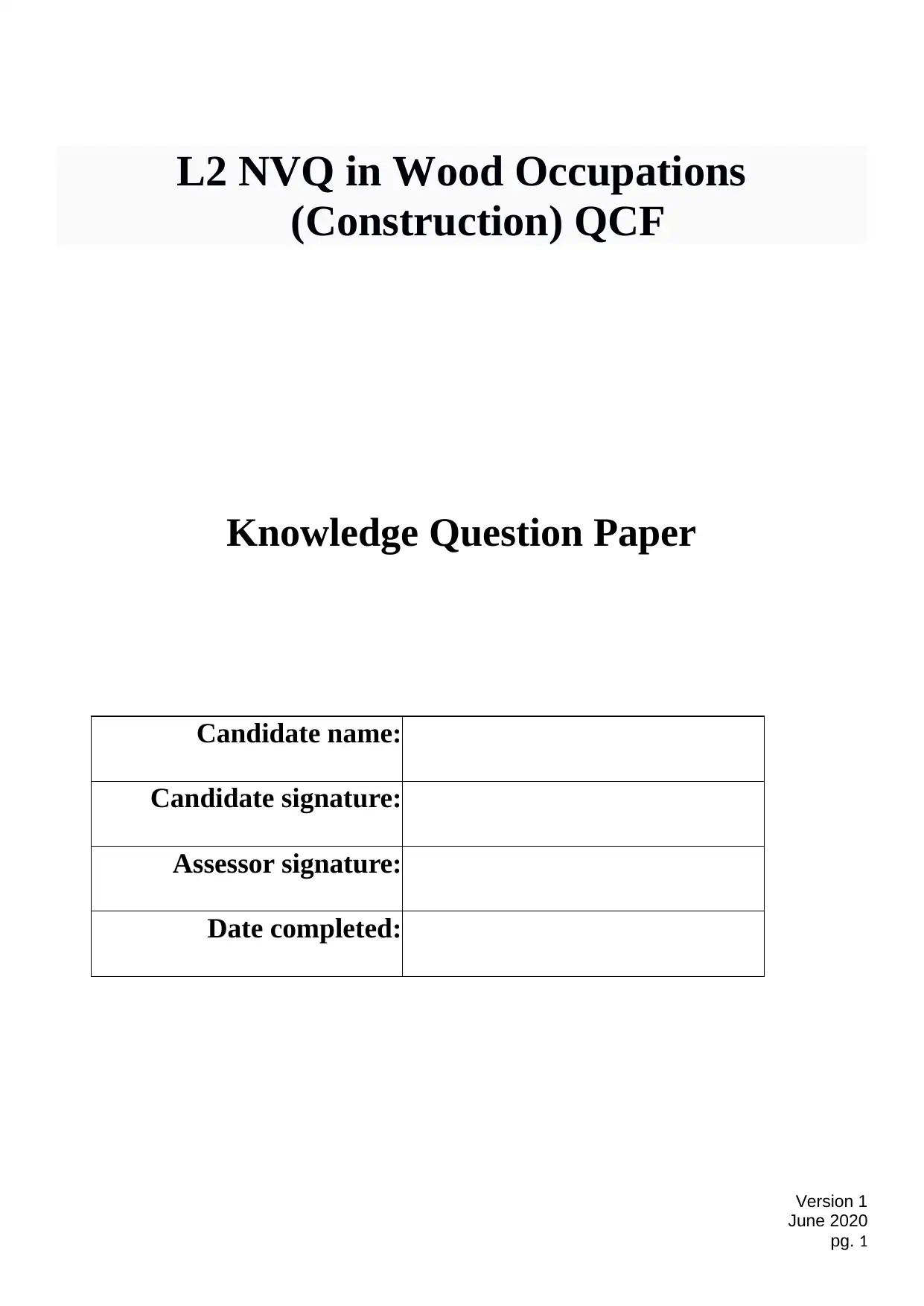
L2 NVQ in Wood Occupations
(Construction) QCF
Knowledge Question Paper
Candidate name:
Candidate signature:
Assessor signature:
Date completed:
Version 1
June 2020
pg. 1
(Construction) QCF
Knowledge Question Paper
Candidate name:
Candidate signature:
Assessor signature:
Date completed:
Version 1
June 2020
pg. 1
Secure Best Marks with AI Grader
Need help grading? Try our AI Grader for instant feedback on your assignments.
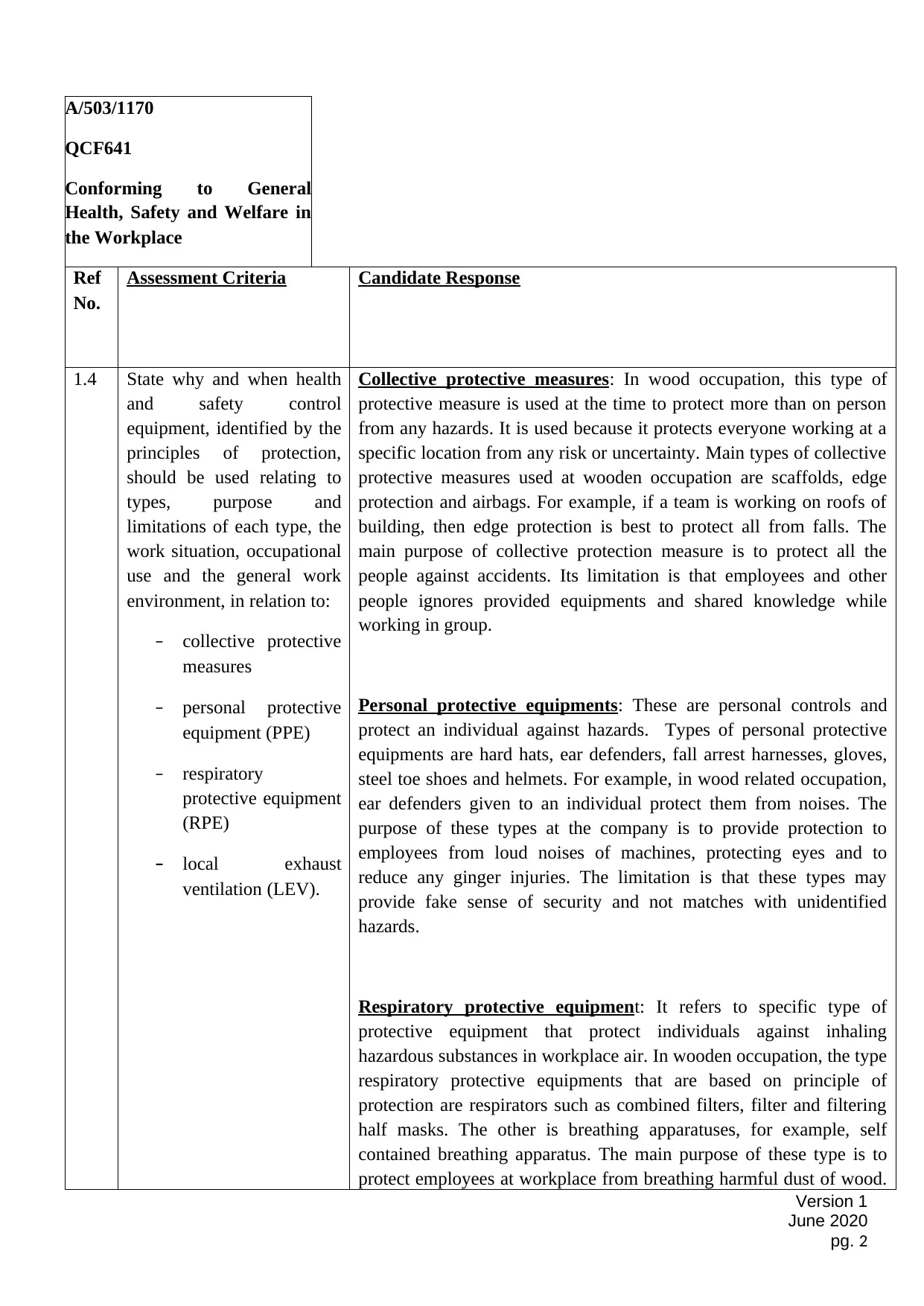
A/503/1170
QCF641
Conforming to General
Health, Safety and Welfare in
the Workplace
Ref
No.
Assessment Criteria Candidate Response
1.4 State why and when health
and safety control
equipment, identified by the
principles of protection,
should be used relating to
types, purpose and
limitations of each type, the
work situation, occupational
use and the general work
environment, in relation to:
– collective protective
measures
– personal protective
equipment (PPE)
– respiratory
protective equipment
(RPE)
– local exhaust
ventilation (LEV).
Collective protective measures: In wood occupation, this type of
protective measure is used at the time to protect more than on person
from any hazards. It is used because it protects everyone working at a
specific location from any risk or uncertainty. Main types of collective
protective measures used at wooden occupation are scaffolds, edge
protection and airbags. For example, if a team is working on roofs of
building, then edge protection is best to protect all from falls. The
main purpose of collective protection measure is to protect all the
people against accidents. Its limitation is that employees and other
people ignores provided equipments and shared knowledge while
working in group.
Personal protective equipments: These are personal controls and
protect an individual against hazards. Types of personal protective
equipments are hard hats, ear defenders, fall arrest harnesses, gloves,
steel toe shoes and helmets. For example, in wood related occupation,
ear defenders given to an individual protect them from noises. The
purpose of these types at the company is to provide protection to
employees from loud noises of machines, protecting eyes and to
reduce any ginger injuries. The limitation is that these types may
provide fake sense of security and not matches with unidentified
hazards.
Respiratory protective equipment: It refers to specific type of
protective equipment that protect individuals against inhaling
hazardous substances in workplace air. In wooden occupation, the type
respiratory protective equipments that are based on principle of
protection are respirators such as combined filters, filter and filtering
half masks. The other is breathing apparatuses, for example, self
contained breathing apparatus. The main purpose of these type is to
protect employees at workplace from breathing harmful dust of wood.
Version 1
June 2020
pg. 2
QCF641
Conforming to General
Health, Safety and Welfare in
the Workplace
Ref
No.
Assessment Criteria Candidate Response
1.4 State why and when health
and safety control
equipment, identified by the
principles of protection,
should be used relating to
types, purpose and
limitations of each type, the
work situation, occupational
use and the general work
environment, in relation to:
– collective protective
measures
– personal protective
equipment (PPE)
– respiratory
protective equipment
(RPE)
– local exhaust
ventilation (LEV).
Collective protective measures: In wood occupation, this type of
protective measure is used at the time to protect more than on person
from any hazards. It is used because it protects everyone working at a
specific location from any risk or uncertainty. Main types of collective
protective measures used at wooden occupation are scaffolds, edge
protection and airbags. For example, if a team is working on roofs of
building, then edge protection is best to protect all from falls. The
main purpose of collective protection measure is to protect all the
people against accidents. Its limitation is that employees and other
people ignores provided equipments and shared knowledge while
working in group.
Personal protective equipments: These are personal controls and
protect an individual against hazards. Types of personal protective
equipments are hard hats, ear defenders, fall arrest harnesses, gloves,
steel toe shoes and helmets. For example, in wood related occupation,
ear defenders given to an individual protect them from noises. The
purpose of these types at the company is to provide protection to
employees from loud noises of machines, protecting eyes and to
reduce any ginger injuries. The limitation is that these types may
provide fake sense of security and not matches with unidentified
hazards.
Respiratory protective equipment: It refers to specific type of
protective equipment that protect individuals against inhaling
hazardous substances in workplace air. In wooden occupation, the type
respiratory protective equipments that are based on principle of
protection are respirators such as combined filters, filter and filtering
half masks. The other is breathing apparatuses, for example, self
contained breathing apparatus. The main purpose of these type is to
protect employees at workplace from breathing harmful dust of wood.
Version 1
June 2020
pg. 2
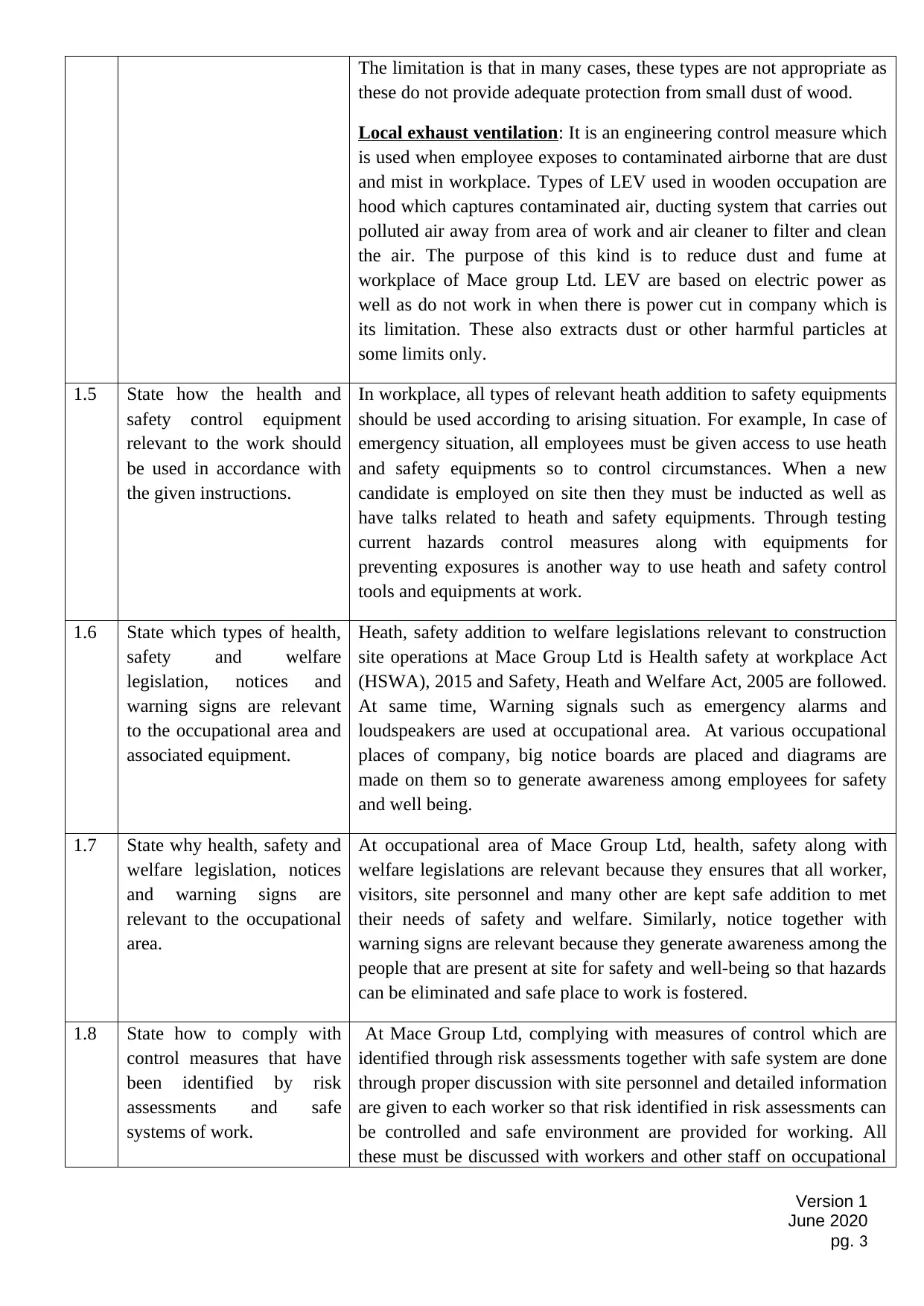
The limitation is that in many cases, these types are not appropriate as
these do not provide adequate protection from small dust of wood.
Local exhaust ventilation: It is an engineering control measure which
is used when employee exposes to contaminated airborne that are dust
and mist in workplace. Types of LEV used in wooden occupation are
hood which captures contaminated air, ducting system that carries out
polluted air away from area of work and air cleaner to filter and clean
the air. The purpose of this kind is to reduce dust and fume at
workplace of Mace group Ltd. LEV are based on electric power as
well as do not work in when there is power cut in company which is
its limitation. These also extracts dust or other harmful particles at
some limits only.
1.5 State how the health and
safety control equipment
relevant to the work should
be used in accordance with
the given instructions.
In workplace, all types of relevant heath addition to safety equipments
should be used according to arising situation. For example, In case of
emergency situation, all employees must be given access to use heath
and safety equipments so to control circumstances. When a new
candidate is employed on site then they must be inducted as well as
have talks related to heath and safety equipments. Through testing
current hazards control measures along with equipments for
preventing exposures is another way to use heath and safety control
tools and equipments at work.
1.6 State which types of health,
safety and welfare
legislation, notices and
warning signs are relevant
to the occupational area and
associated equipment.
Heath, safety addition to welfare legislations relevant to construction
site operations at Mace Group Ltd is Health safety at workplace Act
(HSWA), 2015 and Safety, Heath and Welfare Act, 2005 are followed.
At same time, Warning signals such as emergency alarms and
loudspeakers are used at occupational area. At various occupational
places of company, big notice boards are placed and diagrams are
made on them so to generate awareness among employees for safety
and well being.
1.7 State why health, safety and
welfare legislation, notices
and warning signs are
relevant to the occupational
area.
At occupational area of Mace Group Ltd, health, safety along with
welfare legislations are relevant because they ensures that all worker,
visitors, site personnel and many other are kept safe addition to met
their needs of safety and welfare. Similarly, notice together with
warning signs are relevant because they generate awareness among the
people that are present at site for safety and well-being so that hazards
can be eliminated and safe place to work is fostered.
1.8 State how to comply with
control measures that have
been identified by risk
assessments and safe
systems of work.
At Mace Group Ltd, complying with measures of control which are
identified through risk assessments together with safe system are done
through proper discussion with site personnel and detailed information
are given to each worker so that risk identified in risk assessments can
be controlled and safe environment are provided for working. All
these must be discussed with workers and other staff on occupational
Version 1
June 2020
pg. 3
these do not provide adequate protection from small dust of wood.
Local exhaust ventilation: It is an engineering control measure which
is used when employee exposes to contaminated airborne that are dust
and mist in workplace. Types of LEV used in wooden occupation are
hood which captures contaminated air, ducting system that carries out
polluted air away from area of work and air cleaner to filter and clean
the air. The purpose of this kind is to reduce dust and fume at
workplace of Mace group Ltd. LEV are based on electric power as
well as do not work in when there is power cut in company which is
its limitation. These also extracts dust or other harmful particles at
some limits only.
1.5 State how the health and
safety control equipment
relevant to the work should
be used in accordance with
the given instructions.
In workplace, all types of relevant heath addition to safety equipments
should be used according to arising situation. For example, In case of
emergency situation, all employees must be given access to use heath
and safety equipments so to control circumstances. When a new
candidate is employed on site then they must be inducted as well as
have talks related to heath and safety equipments. Through testing
current hazards control measures along with equipments for
preventing exposures is another way to use heath and safety control
tools and equipments at work.
1.6 State which types of health,
safety and welfare
legislation, notices and
warning signs are relevant
to the occupational area and
associated equipment.
Heath, safety addition to welfare legislations relevant to construction
site operations at Mace Group Ltd is Health safety at workplace Act
(HSWA), 2015 and Safety, Heath and Welfare Act, 2005 are followed.
At same time, Warning signals such as emergency alarms and
loudspeakers are used at occupational area. At various occupational
places of company, big notice boards are placed and diagrams are
made on them so to generate awareness among employees for safety
and well being.
1.7 State why health, safety and
welfare legislation, notices
and warning signs are
relevant to the occupational
area.
At occupational area of Mace Group Ltd, health, safety along with
welfare legislations are relevant because they ensures that all worker,
visitors, site personnel and many other are kept safe addition to met
their needs of safety and welfare. Similarly, notice together with
warning signs are relevant because they generate awareness among the
people that are present at site for safety and well-being so that hazards
can be eliminated and safe place to work is fostered.
1.8 State how to comply with
control measures that have
been identified by risk
assessments and safe
systems of work.
At Mace Group Ltd, complying with measures of control which are
identified through risk assessments together with safe system are done
through proper discussion with site personnel and detailed information
are given to each worker so that risk identified in risk assessments can
be controlled and safe environment are provided for working. All
these must be discussed with workers and other staff on occupational
Version 1
June 2020
pg. 3
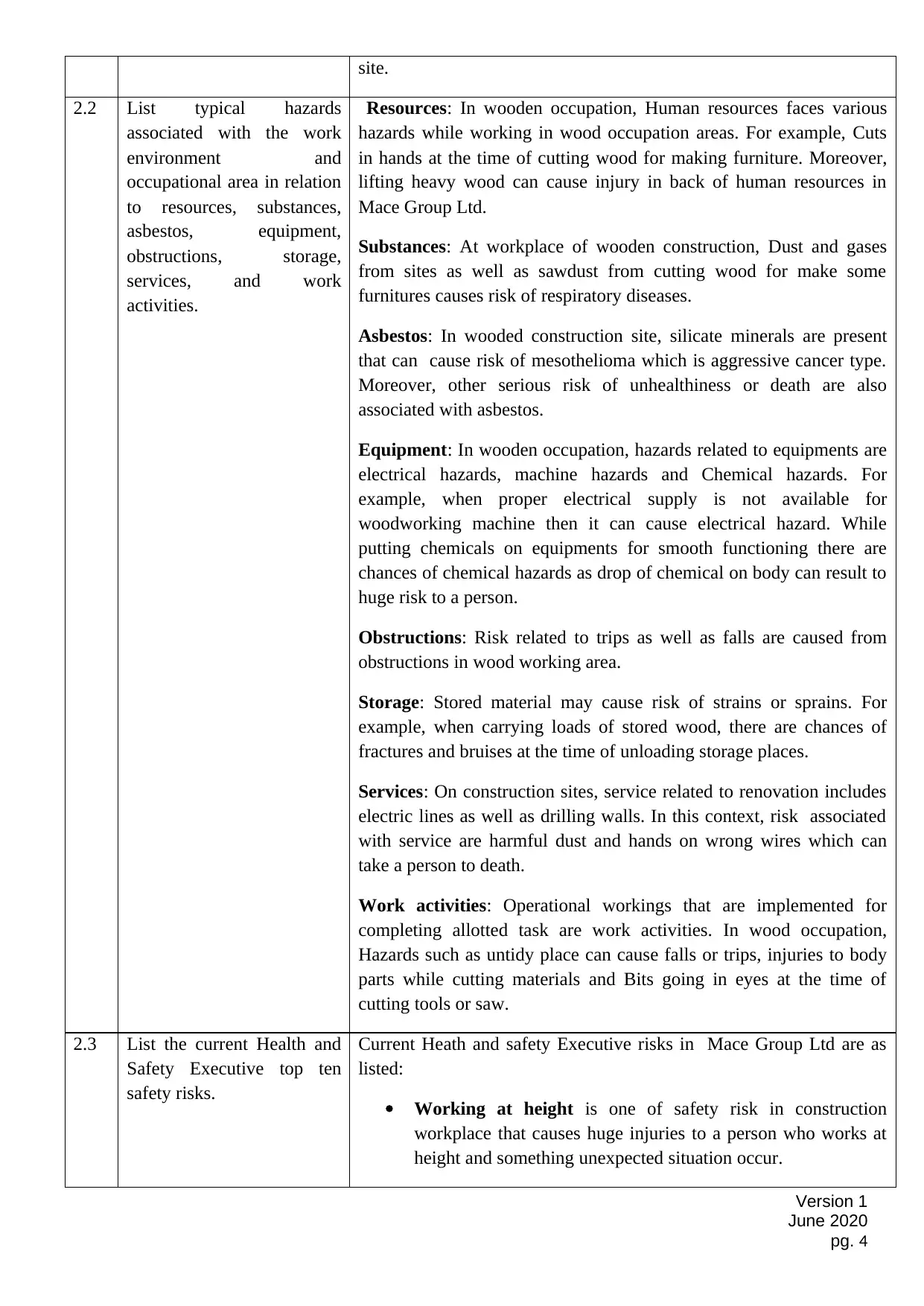
site.
2.2 List typical hazards
associated with the work
environment and
occupational area in relation
to resources, substances,
asbestos, equipment,
obstructions, storage,
services, and work
activities.
Resources: In wooden occupation, Human resources faces various
hazards while working in wood occupation areas. For example, Cuts
in hands at the time of cutting wood for making furniture. Moreover,
lifting heavy wood can cause injury in back of human resources in
Mace Group Ltd.
Substances: At workplace of wooden construction, Dust and gases
from sites as well as sawdust from cutting wood for make some
furnitures causes risk of respiratory diseases.
Asbestos: In wooded construction site, silicate minerals are present
that can cause risk of mesothelioma which is aggressive cancer type.
Moreover, other serious risk of unhealthiness or death are also
associated with asbestos.
Equipment: In wooden occupation, hazards related to equipments are
electrical hazards, machine hazards and Chemical hazards. For
example, when proper electrical supply is not available for
woodworking machine then it can cause electrical hazard. While
putting chemicals on equipments for smooth functioning there are
chances of chemical hazards as drop of chemical on body can result to
huge risk to a person.
Obstructions: Risk related to trips as well as falls are caused from
obstructions in wood working area.
Storage: Stored material may cause risk of strains or sprains. For
example, when carrying loads of stored wood, there are chances of
fractures and bruises at the time of unloading storage places.
Services: On construction sites, service related to renovation includes
electric lines as well as drilling walls. In this context, risk associated
with service are harmful dust and hands on wrong wires which can
take a person to death.
Work activities: Operational workings that are implemented for
completing allotted task are work activities. In wood occupation,
Hazards such as untidy place can cause falls or trips, injuries to body
parts while cutting materials and Bits going in eyes at the time of
cutting tools or saw.
2.3 List the current Health and
Safety Executive top ten
safety risks.
Current Heath and safety Executive risks in Mace Group Ltd are as
listed:
Working at height is one of safety risk in construction
workplace that causes huge injuries to a person who works at
height and something unexpected situation occur.
Version 1
June 2020
pg. 4
2.2 List typical hazards
associated with the work
environment and
occupational area in relation
to resources, substances,
asbestos, equipment,
obstructions, storage,
services, and work
activities.
Resources: In wooden occupation, Human resources faces various
hazards while working in wood occupation areas. For example, Cuts
in hands at the time of cutting wood for making furniture. Moreover,
lifting heavy wood can cause injury in back of human resources in
Mace Group Ltd.
Substances: At workplace of wooden construction, Dust and gases
from sites as well as sawdust from cutting wood for make some
furnitures causes risk of respiratory diseases.
Asbestos: In wooded construction site, silicate minerals are present
that can cause risk of mesothelioma which is aggressive cancer type.
Moreover, other serious risk of unhealthiness or death are also
associated with asbestos.
Equipment: In wooden occupation, hazards related to equipments are
electrical hazards, machine hazards and Chemical hazards. For
example, when proper electrical supply is not available for
woodworking machine then it can cause electrical hazard. While
putting chemicals on equipments for smooth functioning there are
chances of chemical hazards as drop of chemical on body can result to
huge risk to a person.
Obstructions: Risk related to trips as well as falls are caused from
obstructions in wood working area.
Storage: Stored material may cause risk of strains or sprains. For
example, when carrying loads of stored wood, there are chances of
fractures and bruises at the time of unloading storage places.
Services: On construction sites, service related to renovation includes
electric lines as well as drilling walls. In this context, risk associated
with service are harmful dust and hands on wrong wires which can
take a person to death.
Work activities: Operational workings that are implemented for
completing allotted task are work activities. In wood occupation,
Hazards such as untidy place can cause falls or trips, injuries to body
parts while cutting materials and Bits going in eyes at the time of
cutting tools or saw.
2.3 List the current Health and
Safety Executive top ten
safety risks.
Current Heath and safety Executive risks in Mace Group Ltd are as
listed:
Working at height is one of safety risk in construction
workplace that causes huge injuries to a person who works at
height and something unexpected situation occur.
Version 1
June 2020
pg. 4
Secure Best Marks with AI Grader
Need help grading? Try our AI Grader for instant feedback on your assignments.
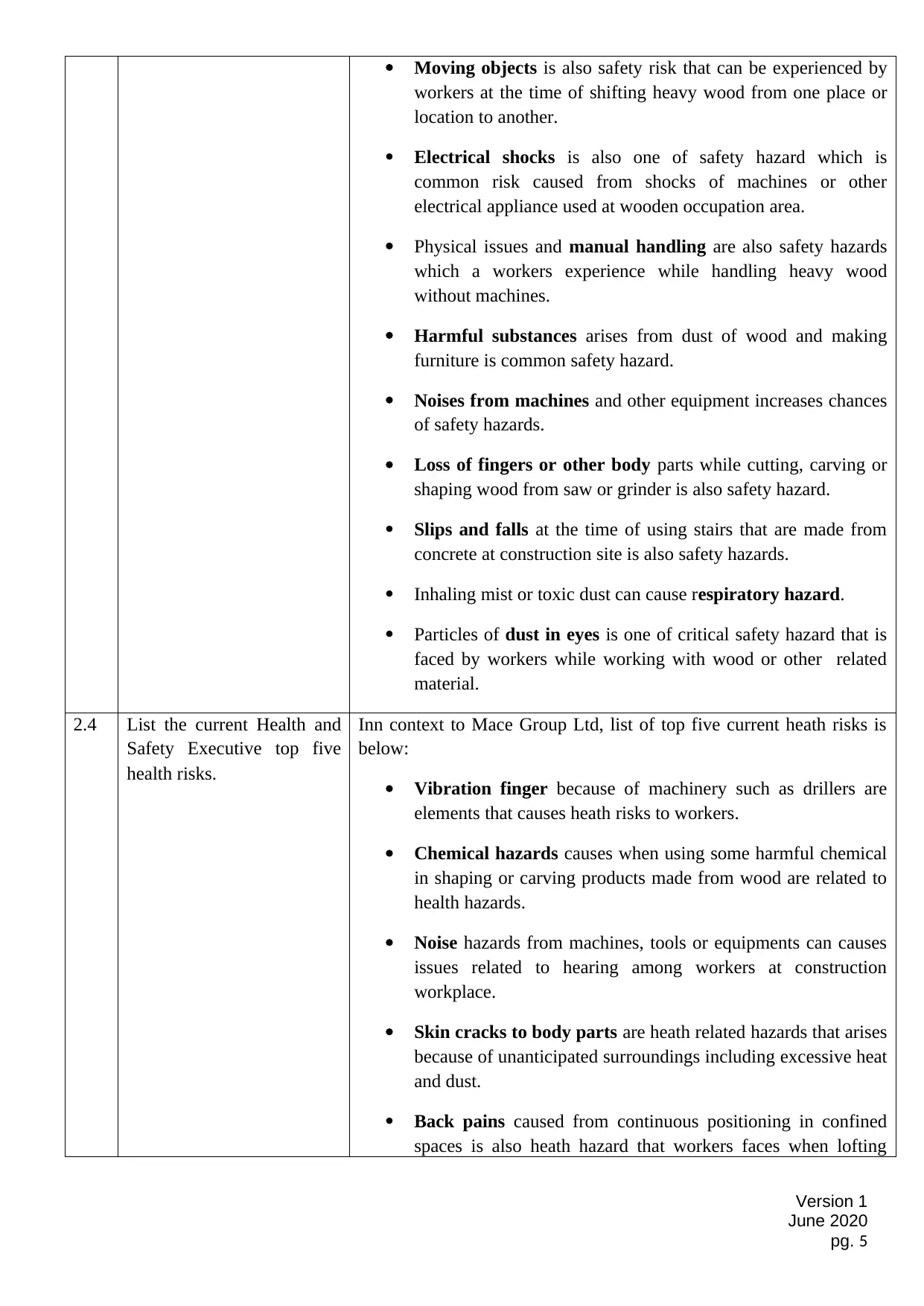
Moving objects is also safety risk that can be experienced by
workers at the time of shifting heavy wood from one place or
location to another.
Electrical shocks is also one of safety hazard which is
common risk caused from shocks of machines or other
electrical appliance used at wooden occupation area.
Physical issues and manual handling are also safety hazards
which a workers experience while handling heavy wood
without machines.
Harmful substances arises from dust of wood and making
furniture is common safety hazard.
Noises from machines and other equipment increases chances
of safety hazards.
Loss of fingers or other body parts while cutting, carving or
shaping wood from saw or grinder is also safety hazard.
Slips and falls at the time of using stairs that are made from
concrete at construction site is also safety hazards.
Inhaling mist or toxic dust can cause respiratory hazard.
Particles of dust in eyes is one of critical safety hazard that is
faced by workers while working with wood or other related
material.
2.4 List the current Health and
Safety Executive top five
health risks.
Inn context to Mace Group Ltd, list of top five current heath risks is
below:
Vibration finger because of machinery such as drillers are
elements that causes heath risks to workers.
Chemical hazards causes when using some harmful chemical
in shaping or carving products made from wood are related to
health hazards.
Noise hazards from machines, tools or equipments can causes
issues related to hearing among workers at construction
workplace.
Skin cracks to body parts are heath related hazards that arises
because of unanticipated surroundings including excessive heat
and dust.
Back pains caused from continuous positioning in confined
spaces is also heath hazard that workers faces when lofting
Version 1
June 2020
pg. 5
workers at the time of shifting heavy wood from one place or
location to another.
Electrical shocks is also one of safety hazard which is
common risk caused from shocks of machines or other
electrical appliance used at wooden occupation area.
Physical issues and manual handling are also safety hazards
which a workers experience while handling heavy wood
without machines.
Harmful substances arises from dust of wood and making
furniture is common safety hazard.
Noises from machines and other equipment increases chances
of safety hazards.
Loss of fingers or other body parts while cutting, carving or
shaping wood from saw or grinder is also safety hazard.
Slips and falls at the time of using stairs that are made from
concrete at construction site is also safety hazards.
Inhaling mist or toxic dust can cause respiratory hazard.
Particles of dust in eyes is one of critical safety hazard that is
faced by workers while working with wood or other related
material.
2.4 List the current Health and
Safety Executive top five
health risks.
Inn context to Mace Group Ltd, list of top five current heath risks is
below:
Vibration finger because of machinery such as drillers are
elements that causes heath risks to workers.
Chemical hazards causes when using some harmful chemical
in shaping or carving products made from wood are related to
health hazards.
Noise hazards from machines, tools or equipments can causes
issues related to hearing among workers at construction
workplace.
Skin cracks to body parts are heath related hazards that arises
because of unanticipated surroundings including excessive heat
and dust.
Back pains caused from continuous positioning in confined
spaces is also heath hazard that workers faces when lofting
Version 1
June 2020
pg. 5
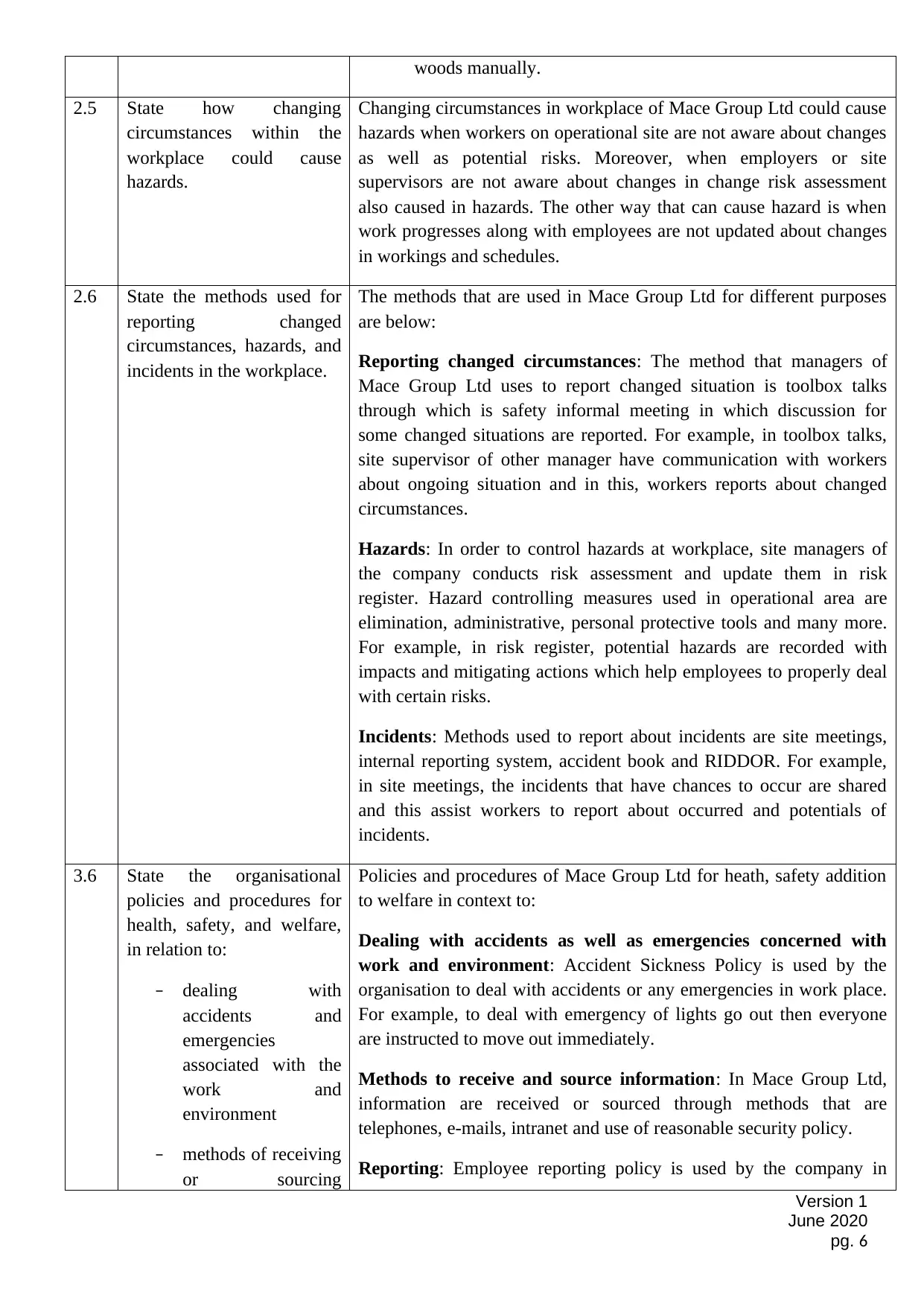
woods manually.
2.5 State how changing
circumstances within the
workplace could cause
hazards.
Changing circumstances in workplace of Mace Group Ltd could cause
hazards when workers on operational site are not aware about changes
as well as potential risks. Moreover, when employers or site
supervisors are not aware about changes in change risk assessment
also caused in hazards. The other way that can cause hazard is when
work progresses along with employees are not updated about changes
in workings and schedules.
2.6 State the methods used for
reporting changed
circumstances, hazards, and
incidents in the workplace.
The methods that are used in Mace Group Ltd for different purposes
are below:
Reporting changed circumstances: The method that managers of
Mace Group Ltd uses to report changed situation is toolbox talks
through which is safety informal meeting in which discussion for
some changed situations are reported. For example, in toolbox talks,
site supervisor of other manager have communication with workers
about ongoing situation and in this, workers reports about changed
circumstances.
Hazards: In order to control hazards at workplace, site managers of
the company conducts risk assessment and update them in risk
register. Hazard controlling measures used in operational area are
elimination, administrative, personal protective tools and many more.
For example, in risk register, potential hazards are recorded with
impacts and mitigating actions which help employees to properly deal
with certain risks.
Incidents: Methods used to report about incidents are site meetings,
internal reporting system, accident book and RIDDOR. For example,
in site meetings, the incidents that have chances to occur are shared
and this assist workers to report about occurred and potentials of
incidents.
3.6 State the organisational
policies and procedures for
health, safety, and welfare,
in relation to:
– dealing with
accidents and
emergencies
associated with the
work and
environment
– methods of receiving
or sourcing
Policies and procedures of Mace Group Ltd for heath, safety addition
to welfare in context to:
Dealing with accidents as well as emergencies concerned with
work and environment: Accident Sickness Policy is used by the
organisation to deal with accidents or any emergencies in work place.
For example, to deal with emergency of lights go out then everyone
are instructed to move out immediately.
Methods to receive and source information: In Mace Group Ltd,
information are received or sourced through methods that are
telephones, e-mails, intranet and use of reasonable security policy.
Reporting: Employee reporting policy is used by the company in
Version 1
June 2020
pg. 6
2.5 State how changing
circumstances within the
workplace could cause
hazards.
Changing circumstances in workplace of Mace Group Ltd could cause
hazards when workers on operational site are not aware about changes
as well as potential risks. Moreover, when employers or site
supervisors are not aware about changes in change risk assessment
also caused in hazards. The other way that can cause hazard is when
work progresses along with employees are not updated about changes
in workings and schedules.
2.6 State the methods used for
reporting changed
circumstances, hazards, and
incidents in the workplace.
The methods that are used in Mace Group Ltd for different purposes
are below:
Reporting changed circumstances: The method that managers of
Mace Group Ltd uses to report changed situation is toolbox talks
through which is safety informal meeting in which discussion for
some changed situations are reported. For example, in toolbox talks,
site supervisor of other manager have communication with workers
about ongoing situation and in this, workers reports about changed
circumstances.
Hazards: In order to control hazards at workplace, site managers of
the company conducts risk assessment and update them in risk
register. Hazard controlling measures used in operational area are
elimination, administrative, personal protective tools and many more.
For example, in risk register, potential hazards are recorded with
impacts and mitigating actions which help employees to properly deal
with certain risks.
Incidents: Methods used to report about incidents are site meetings,
internal reporting system, accident book and RIDDOR. For example,
in site meetings, the incidents that have chances to occur are shared
and this assist workers to report about occurred and potentials of
incidents.
3.6 State the organisational
policies and procedures for
health, safety, and welfare,
in relation to:
– dealing with
accidents and
emergencies
associated with the
work and
environment
– methods of receiving
or sourcing
Policies and procedures of Mace Group Ltd for heath, safety addition
to welfare in context to:
Dealing with accidents as well as emergencies concerned with
work and environment: Accident Sickness Policy is used by the
organisation to deal with accidents or any emergencies in work place.
For example, to deal with emergency of lights go out then everyone
are instructed to move out immediately.
Methods to receive and source information: In Mace Group Ltd,
information are received or sourced through methods that are
telephones, e-mails, intranet and use of reasonable security policy.
Reporting: Employee reporting policy is used by the company in
Version 1
June 2020
pg. 6
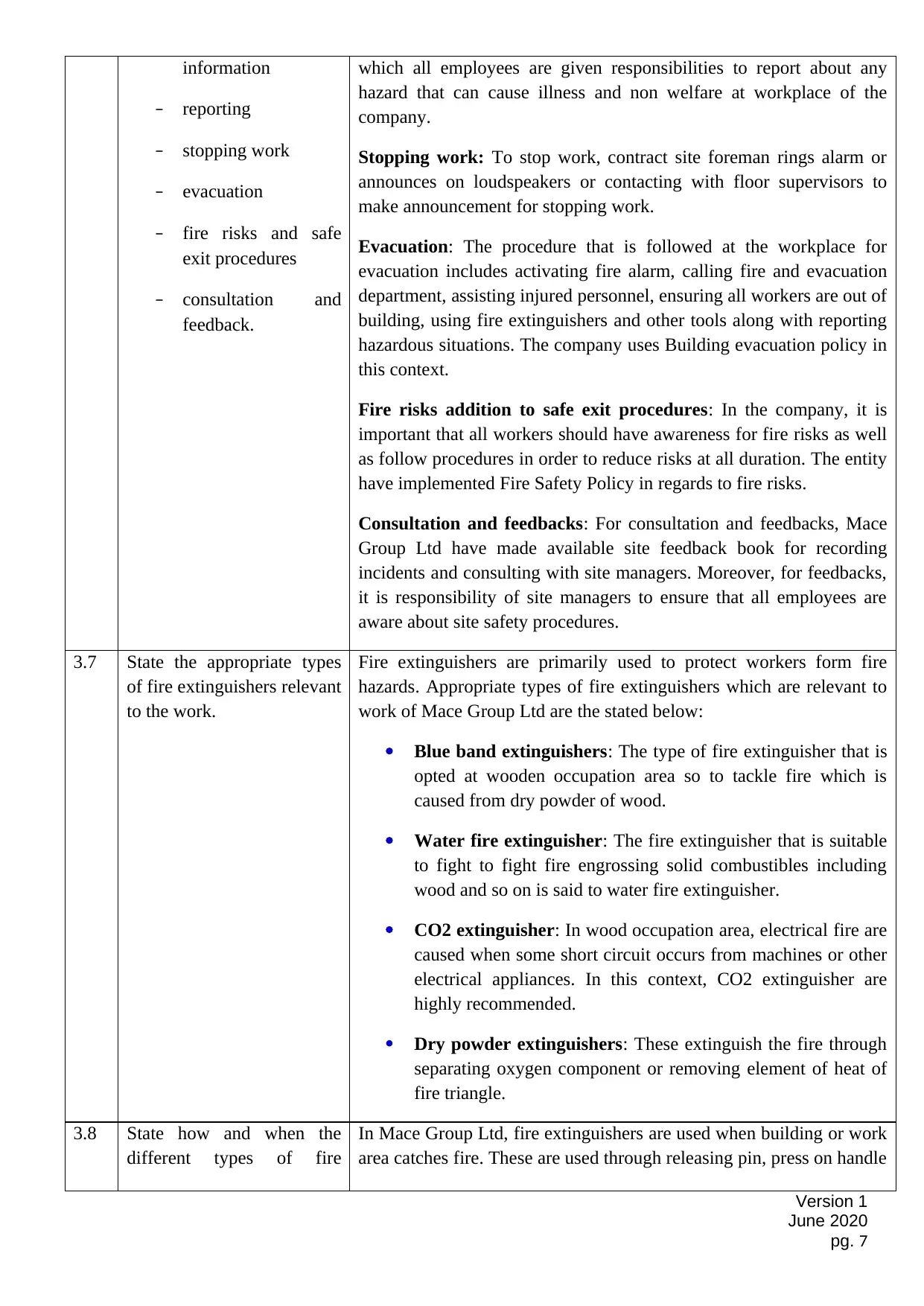
information
– reporting
– stopping work
– evacuation
– fire risks and safe
exit procedures
– consultation and
feedback.
which all employees are given responsibilities to report about any
hazard that can cause illness and non welfare at workplace of the
company.
Stopping work: To stop work, contract site foreman rings alarm or
announces on loudspeakers or contacting with floor supervisors to
make announcement for stopping work.
Evacuation: The procedure that is followed at the workplace for
evacuation includes activating fire alarm, calling fire and evacuation
department, assisting injured personnel, ensuring all workers are out of
building, using fire extinguishers and other tools along with reporting
hazardous situations. The company uses Building evacuation policy in
this context.
Fire risks addition to safe exit procedures: In the company, it is
important that all workers should have awareness for fire risks as well
as follow procedures in order to reduce risks at all duration. The entity
have implemented Fire Safety Policy in regards to fire risks.
Consultation and feedbacks: For consultation and feedbacks, Mace
Group Ltd have made available site feedback book for recording
incidents and consulting with site managers. Moreover, for feedbacks,
it is responsibility of site managers to ensure that all employees are
aware about site safety procedures.
3.7 State the appropriate types
of fire extinguishers relevant
to the work.
Fire extinguishers are primarily used to protect workers form fire
hazards. Appropriate types of fire extinguishers which are relevant to
work of Mace Group Ltd are the stated below:
Blue band extinguishers: The type of fire extinguisher that is
opted at wooden occupation area so to tackle fire which is
caused from dry powder of wood.
Water fire extinguisher: The fire extinguisher that is suitable
to fight to fight fire engrossing solid combustibles including
wood and so on is said to water fire extinguisher.
CO2 extinguisher: In wood occupation area, electrical fire are
caused when some short circuit occurs from machines or other
electrical appliances. In this context, CO2 extinguisher are
highly recommended.
Dry powder extinguishers: These extinguish the fire through
separating oxygen component or removing element of heat of
fire triangle.
3.8 State how and when the
different types of fire
In Mace Group Ltd, fire extinguishers are used when building or work
area catches fire. These are used through releasing pin, press on handle
Version 1
June 2020
pg. 7
– reporting
– stopping work
– evacuation
– fire risks and safe
exit procedures
– consultation and
feedback.
which all employees are given responsibilities to report about any
hazard that can cause illness and non welfare at workplace of the
company.
Stopping work: To stop work, contract site foreman rings alarm or
announces on loudspeakers or contacting with floor supervisors to
make announcement for stopping work.
Evacuation: The procedure that is followed at the workplace for
evacuation includes activating fire alarm, calling fire and evacuation
department, assisting injured personnel, ensuring all workers are out of
building, using fire extinguishers and other tools along with reporting
hazardous situations. The company uses Building evacuation policy in
this context.
Fire risks addition to safe exit procedures: In the company, it is
important that all workers should have awareness for fire risks as well
as follow procedures in order to reduce risks at all duration. The entity
have implemented Fire Safety Policy in regards to fire risks.
Consultation and feedbacks: For consultation and feedbacks, Mace
Group Ltd have made available site feedback book for recording
incidents and consulting with site managers. Moreover, for feedbacks,
it is responsibility of site managers to ensure that all employees are
aware about site safety procedures.
3.7 State the appropriate types
of fire extinguishers relevant
to the work.
Fire extinguishers are primarily used to protect workers form fire
hazards. Appropriate types of fire extinguishers which are relevant to
work of Mace Group Ltd are the stated below:
Blue band extinguishers: The type of fire extinguisher that is
opted at wooden occupation area so to tackle fire which is
caused from dry powder of wood.
Water fire extinguisher: The fire extinguisher that is suitable
to fight to fight fire engrossing solid combustibles including
wood and so on is said to water fire extinguisher.
CO2 extinguisher: In wood occupation area, electrical fire are
caused when some short circuit occurs from machines or other
electrical appliances. In this context, CO2 extinguisher are
highly recommended.
Dry powder extinguishers: These extinguish the fire through
separating oxygen component or removing element of heat of
fire triangle.
3.8 State how and when the
different types of fire
In Mace Group Ltd, fire extinguishers are used when building or work
area catches fire. These are used through releasing pin, press on handle
Version 1
June 2020
pg. 7
Paraphrase This Document
Need a fresh take? Get an instant paraphrase of this document with our AI Paraphraser
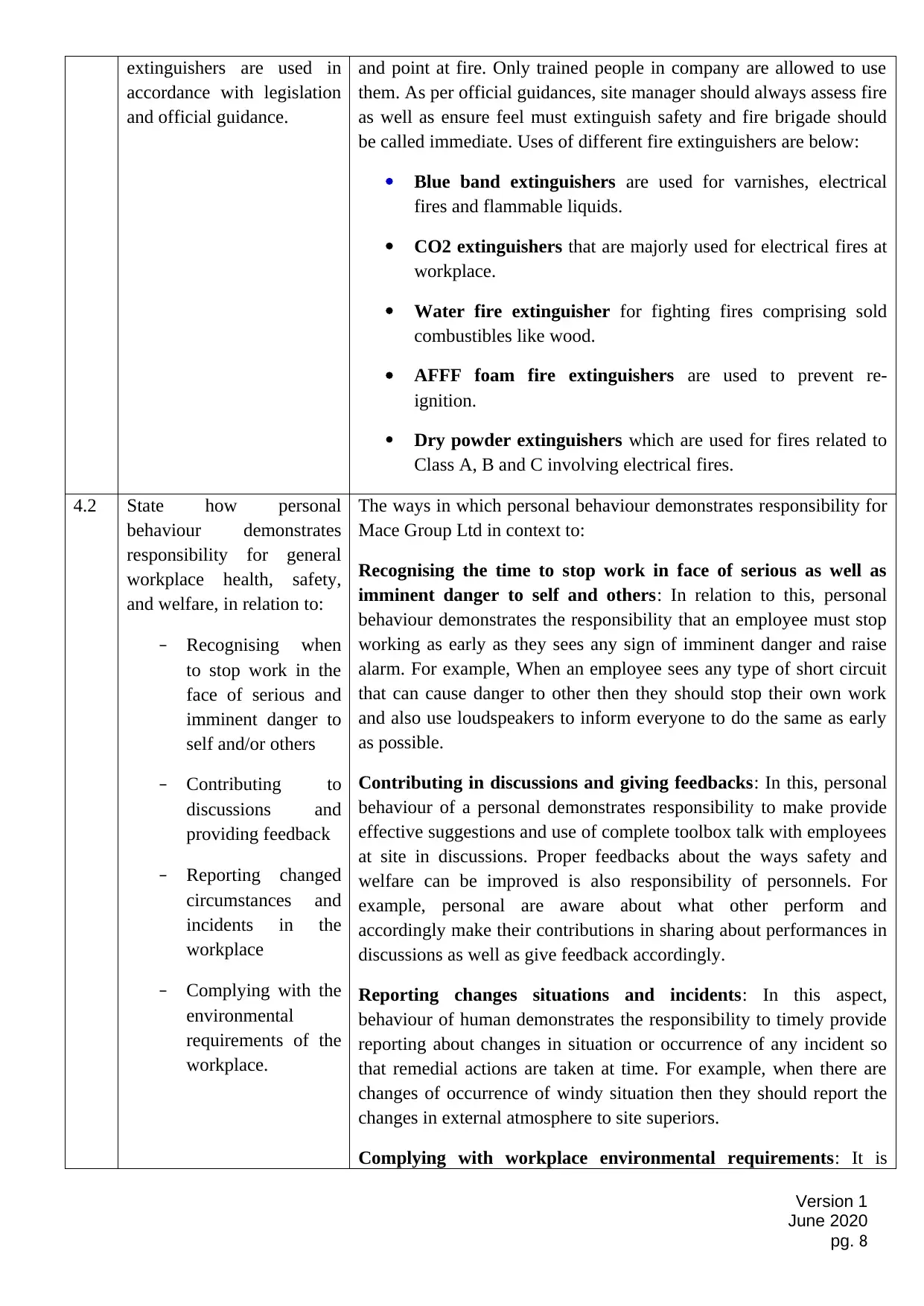
extinguishers are used in
accordance with legislation
and official guidance.
and point at fire. Only trained people in company are allowed to use
them. As per official guidances, site manager should always assess fire
as well as ensure feel must extinguish safety and fire brigade should
be called immediate. Uses of different fire extinguishers are below:
Blue band extinguishers are used for varnishes, electrical
fires and flammable liquids.
CO2 extinguishers that are majorly used for electrical fires at
workplace.
Water fire extinguisher for fighting fires comprising sold
combustibles like wood.
AFFF foam fire extinguishers are used to prevent re-
ignition.
Dry powder extinguishers which are used for fires related to
Class A, B and C involving electrical fires.
4.2 State how personal
behaviour demonstrates
responsibility for general
workplace health, safety,
and welfare, in relation to:
– Recognising when
to stop work in the
face of serious and
imminent danger to
self and/or others
– Contributing to
discussions and
providing feedback
– Reporting changed
circumstances and
incidents in the
workplace
– Complying with the
environmental
requirements of the
workplace.
The ways in which personal behaviour demonstrates responsibility for
Mace Group Ltd in context to:
Recognising the time to stop work in face of serious as well as
imminent danger to self and others: In relation to this, personal
behaviour demonstrates the responsibility that an employee must stop
working as early as they sees any sign of imminent danger and raise
alarm. For example, When an employee sees any type of short circuit
that can cause danger to other then they should stop their own work
and also use loudspeakers to inform everyone to do the same as early
as possible.
Contributing in discussions and giving feedbacks: In this, personal
behaviour of a personal demonstrates responsibility to make provide
effective suggestions and use of complete toolbox talk with employees
at site in discussions. Proper feedbacks about the ways safety and
welfare can be improved is also responsibility of personnels. For
example, personal are aware about what other perform and
accordingly make their contributions in sharing about performances in
discussions as well as give feedback accordingly.
Reporting changes situations and incidents: In this aspect,
behaviour of human demonstrates the responsibility to timely provide
reporting about changes in situation or occurrence of any incident so
that remedial actions are taken at time. For example, when there are
changes of occurrence of windy situation then they should report the
changes in external atmosphere to site superiors.
Complying with workplace environmental requirements: It is
Version 1
June 2020
pg. 8
accordance with legislation
and official guidance.
and point at fire. Only trained people in company are allowed to use
them. As per official guidances, site manager should always assess fire
as well as ensure feel must extinguish safety and fire brigade should
be called immediate. Uses of different fire extinguishers are below:
Blue band extinguishers are used for varnishes, electrical
fires and flammable liquids.
CO2 extinguishers that are majorly used for electrical fires at
workplace.
Water fire extinguisher for fighting fires comprising sold
combustibles like wood.
AFFF foam fire extinguishers are used to prevent re-
ignition.
Dry powder extinguishers which are used for fires related to
Class A, B and C involving electrical fires.
4.2 State how personal
behaviour demonstrates
responsibility for general
workplace health, safety,
and welfare, in relation to:
– Recognising when
to stop work in the
face of serious and
imminent danger to
self and/or others
– Contributing to
discussions and
providing feedback
– Reporting changed
circumstances and
incidents in the
workplace
– Complying with the
environmental
requirements of the
workplace.
The ways in which personal behaviour demonstrates responsibility for
Mace Group Ltd in context to:
Recognising the time to stop work in face of serious as well as
imminent danger to self and others: In relation to this, personal
behaviour demonstrates the responsibility that an employee must stop
working as early as they sees any sign of imminent danger and raise
alarm. For example, When an employee sees any type of short circuit
that can cause danger to other then they should stop their own work
and also use loudspeakers to inform everyone to do the same as early
as possible.
Contributing in discussions and giving feedbacks: In this, personal
behaviour of a personal demonstrates responsibility to make provide
effective suggestions and use of complete toolbox talk with employees
at site in discussions. Proper feedbacks about the ways safety and
welfare can be improved is also responsibility of personnels. For
example, personal are aware about what other perform and
accordingly make their contributions in sharing about performances in
discussions as well as give feedback accordingly.
Reporting changes situations and incidents: In this aspect,
behaviour of human demonstrates the responsibility to timely provide
reporting about changes in situation or occurrence of any incident so
that remedial actions are taken at time. For example, when there are
changes of occurrence of windy situation then they should report the
changes in external atmosphere to site superiors.
Complying with workplace environmental requirements: It is
Version 1
June 2020
pg. 8
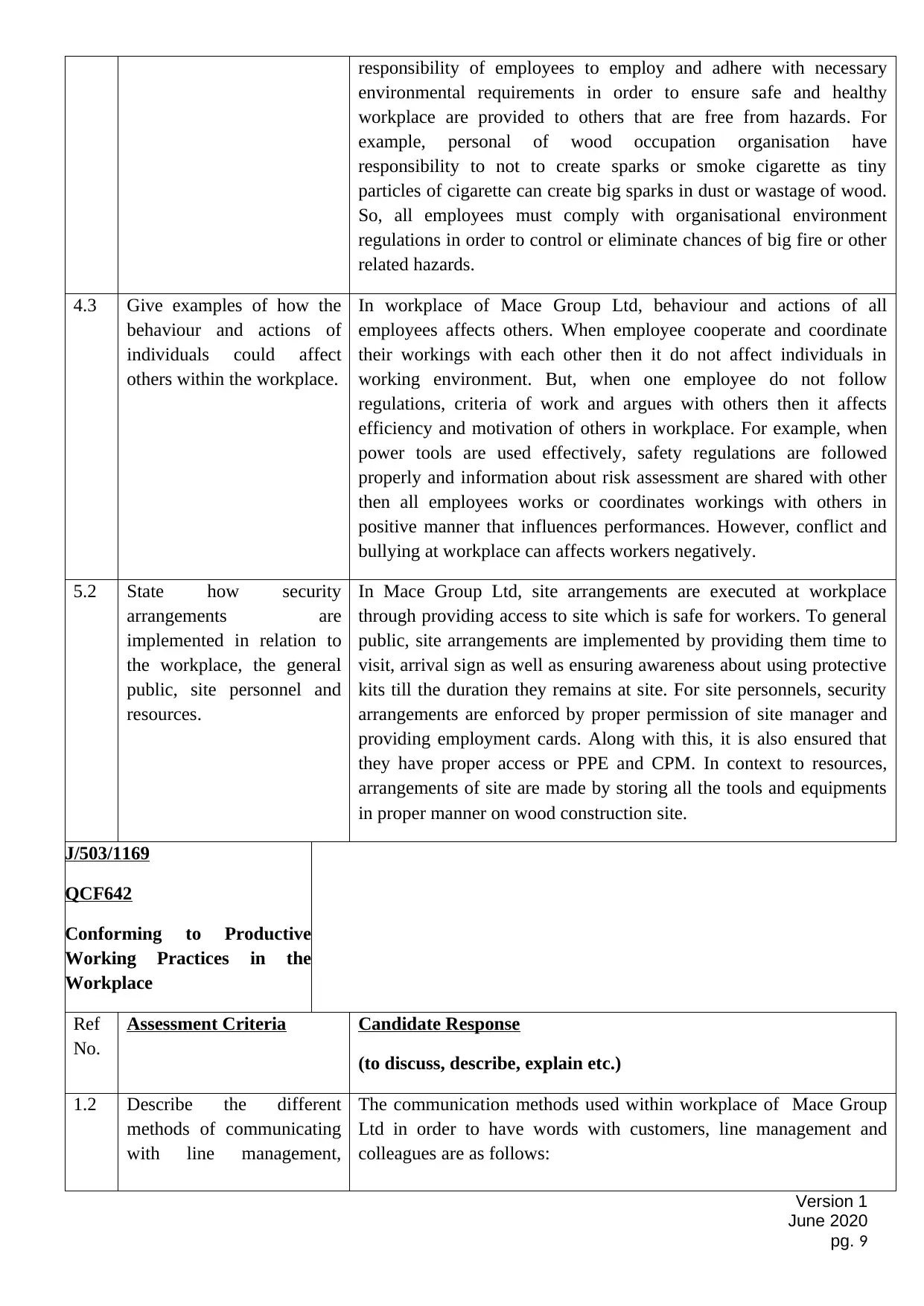
responsibility of employees to employ and adhere with necessary
environmental requirements in order to ensure safe and healthy
workplace are provided to others that are free from hazards. For
example, personal of wood occupation organisation have
responsibility to not to create sparks or smoke cigarette as tiny
particles of cigarette can create big sparks in dust or wastage of wood.
So, all employees must comply with organisational environment
regulations in order to control or eliminate chances of big fire or other
related hazards.
4.3 Give examples of how the
behaviour and actions of
individuals could affect
others within the workplace.
In workplace of Mace Group Ltd, behaviour and actions of all
employees affects others. When employee cooperate and coordinate
their workings with each other then it do not affect individuals in
working environment. But, when one employee do not follow
regulations, criteria of work and argues with others then it affects
efficiency and motivation of others in workplace. For example, when
power tools are used effectively, safety regulations are followed
properly and information about risk assessment are shared with other
then all employees works or coordinates workings with others in
positive manner that influences performances. However, conflict and
bullying at workplace can affects workers negatively.
5.2 State how security
arrangements are
implemented in relation to
the workplace, the general
public, site personnel and
resources.
In Mace Group Ltd, site arrangements are executed at workplace
through providing access to site which is safe for workers. To general
public, site arrangements are implemented by providing them time to
visit, arrival sign as well as ensuring awareness about using protective
kits till the duration they remains at site. For site personnels, security
arrangements are enforced by proper permission of site manager and
providing employment cards. Along with this, it is also ensured that
they have proper access or PPE and CPM. In context to resources,
arrangements of site are made by storing all the tools and equipments
in proper manner on wood construction site.
J/503/1169
QCF642
Conforming to Productive
Working Practices in the
Workplace
Ref
No.
Assessment Criteria Candidate Response
(to discuss, describe, explain etc.)
1.2 Describe the different
methods of communicating
with line management,
The communication methods used within workplace of Mace Group
Ltd in order to have words with customers, line management and
colleagues are as follows:
Version 1
June 2020
pg. 9
environmental requirements in order to ensure safe and healthy
workplace are provided to others that are free from hazards. For
example, personal of wood occupation organisation have
responsibility to not to create sparks or smoke cigarette as tiny
particles of cigarette can create big sparks in dust or wastage of wood.
So, all employees must comply with organisational environment
regulations in order to control or eliminate chances of big fire or other
related hazards.
4.3 Give examples of how the
behaviour and actions of
individuals could affect
others within the workplace.
In workplace of Mace Group Ltd, behaviour and actions of all
employees affects others. When employee cooperate and coordinate
their workings with each other then it do not affect individuals in
working environment. But, when one employee do not follow
regulations, criteria of work and argues with others then it affects
efficiency and motivation of others in workplace. For example, when
power tools are used effectively, safety regulations are followed
properly and information about risk assessment are shared with other
then all employees works or coordinates workings with others in
positive manner that influences performances. However, conflict and
bullying at workplace can affects workers negatively.
5.2 State how security
arrangements are
implemented in relation to
the workplace, the general
public, site personnel and
resources.
In Mace Group Ltd, site arrangements are executed at workplace
through providing access to site which is safe for workers. To general
public, site arrangements are implemented by providing them time to
visit, arrival sign as well as ensuring awareness about using protective
kits till the duration they remains at site. For site personnels, security
arrangements are enforced by proper permission of site manager and
providing employment cards. Along with this, it is also ensured that
they have proper access or PPE and CPM. In context to resources,
arrangements of site are made by storing all the tools and equipments
in proper manner on wood construction site.
J/503/1169
QCF642
Conforming to Productive
Working Practices in the
Workplace
Ref
No.
Assessment Criteria Candidate Response
(to discuss, describe, explain etc.)
1.2 Describe the different
methods of communicating
with line management,
The communication methods used within workplace of Mace Group
Ltd in order to have words with customers, line management and
colleagues are as follows:
Version 1
June 2020
pg. 9
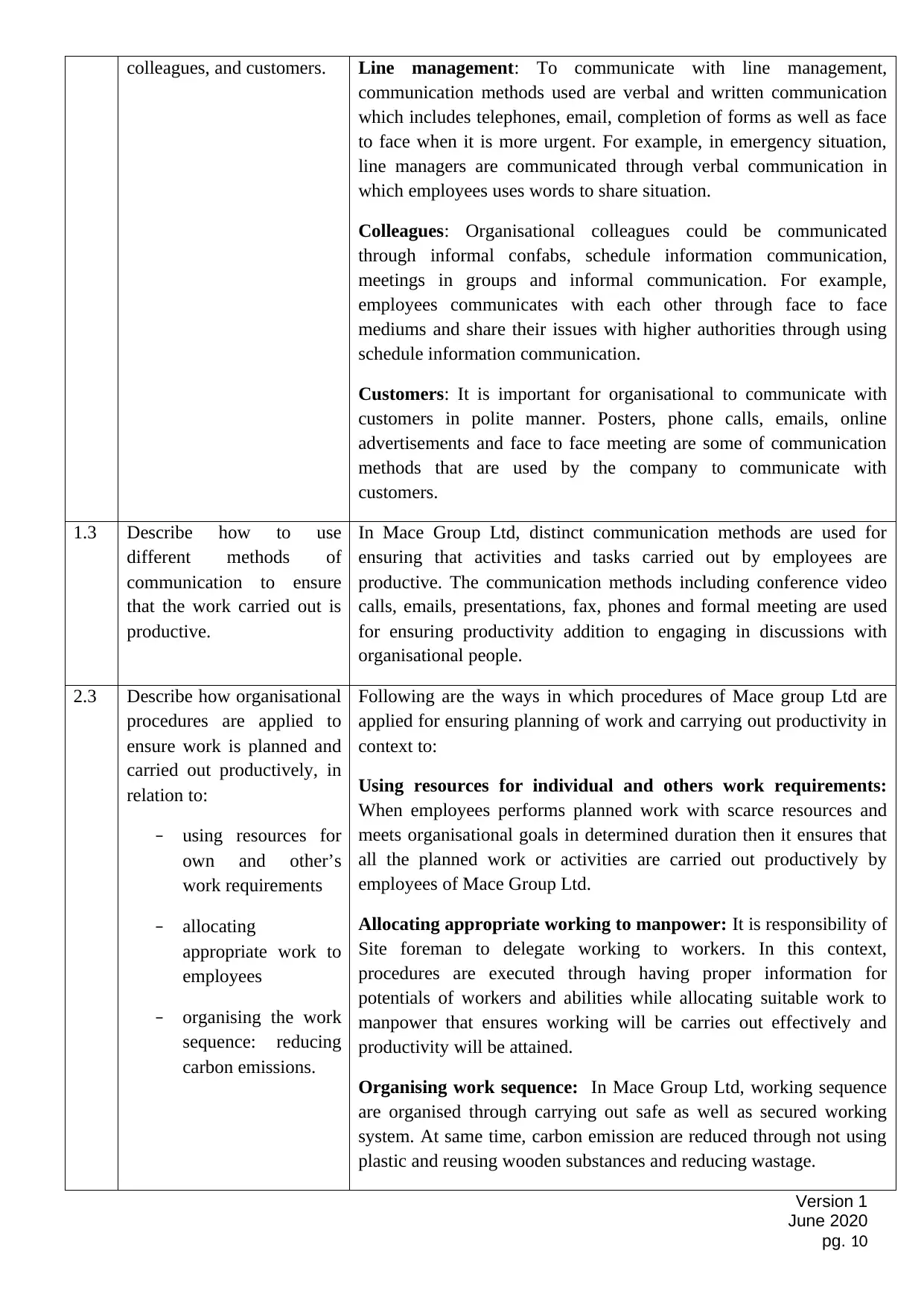
colleagues, and customers. Line management: To communicate with line management,
communication methods used are verbal and written communication
which includes telephones, email, completion of forms as well as face
to face when it is more urgent. For example, in emergency situation,
line managers are communicated through verbal communication in
which employees uses words to share situation.
Colleagues: Organisational colleagues could be communicated
through informal confabs, schedule information communication,
meetings in groups and informal communication. For example,
employees communicates with each other through face to face
mediums and share their issues with higher authorities through using
schedule information communication.
Customers: It is important for organisational to communicate with
customers in polite manner. Posters, phone calls, emails, online
advertisements and face to face meeting are some of communication
methods that are used by the company to communicate with
customers.
1.3 Describe how to use
different methods of
communication to ensure
that the work carried out is
productive.
In Mace Group Ltd, distinct communication methods are used for
ensuring that activities and tasks carried out by employees are
productive. The communication methods including conference video
calls, emails, presentations, fax, phones and formal meeting are used
for ensuring productivity addition to engaging in discussions with
organisational people.
2.3 Describe how organisational
procedures are applied to
ensure work is planned and
carried out productively, in
relation to:
– using resources for
own and other’s
work requirements
– allocating
appropriate work to
employees
– organising the work
sequence: reducing
carbon emissions.
Following are the ways in which procedures of Mace group Ltd are
applied for ensuring planning of work and carrying out productivity in
context to:
Using resources for individual and others work requirements:
When employees performs planned work with scarce resources and
meets organisational goals in determined duration then it ensures that
all the planned work or activities are carried out productively by
employees of Mace Group Ltd.
Allocating appropriate working to manpower: It is responsibility of
Site foreman to delegate working to workers. In this context,
procedures are executed through having proper information for
potentials of workers and abilities while allocating suitable work to
manpower that ensures working will be carries out effectively and
productivity will be attained.
Organising work sequence: In Mace Group Ltd, working sequence
are organised through carrying out safe as well as secured working
system. At same time, carbon emission are reduced through not using
plastic and reusing wooden substances and reducing wastage.
Version 1
June 2020
pg. 10
communication methods used are verbal and written communication
which includes telephones, email, completion of forms as well as face
to face when it is more urgent. For example, in emergency situation,
line managers are communicated through verbal communication in
which employees uses words to share situation.
Colleagues: Organisational colleagues could be communicated
through informal confabs, schedule information communication,
meetings in groups and informal communication. For example,
employees communicates with each other through face to face
mediums and share their issues with higher authorities through using
schedule information communication.
Customers: It is important for organisational to communicate with
customers in polite manner. Posters, phone calls, emails, online
advertisements and face to face meeting are some of communication
methods that are used by the company to communicate with
customers.
1.3 Describe how to use
different methods of
communication to ensure
that the work carried out is
productive.
In Mace Group Ltd, distinct communication methods are used for
ensuring that activities and tasks carried out by employees are
productive. The communication methods including conference video
calls, emails, presentations, fax, phones and formal meeting are used
for ensuring productivity addition to engaging in discussions with
organisational people.
2.3 Describe how organisational
procedures are applied to
ensure work is planned and
carried out productively, in
relation to:
– using resources for
own and other’s
work requirements
– allocating
appropriate work to
employees
– organising the work
sequence: reducing
carbon emissions.
Following are the ways in which procedures of Mace group Ltd are
applied for ensuring planning of work and carrying out productivity in
context to:
Using resources for individual and others work requirements:
When employees performs planned work with scarce resources and
meets organisational goals in determined duration then it ensures that
all the planned work or activities are carried out productively by
employees of Mace Group Ltd.
Allocating appropriate working to manpower: It is responsibility of
Site foreman to delegate working to workers. In this context,
procedures are executed through having proper information for
potentials of workers and abilities while allocating suitable work to
manpower that ensures working will be carries out effectively and
productivity will be attained.
Organising work sequence: In Mace Group Ltd, working sequence
are organised through carrying out safe as well as secured working
system. At same time, carbon emission are reduced through not using
plastic and reusing wooden substances and reducing wastage.
Version 1
June 2020
pg. 10
Secure Best Marks with AI Grader
Need help grading? Try our AI Grader for instant feedback on your assignments.
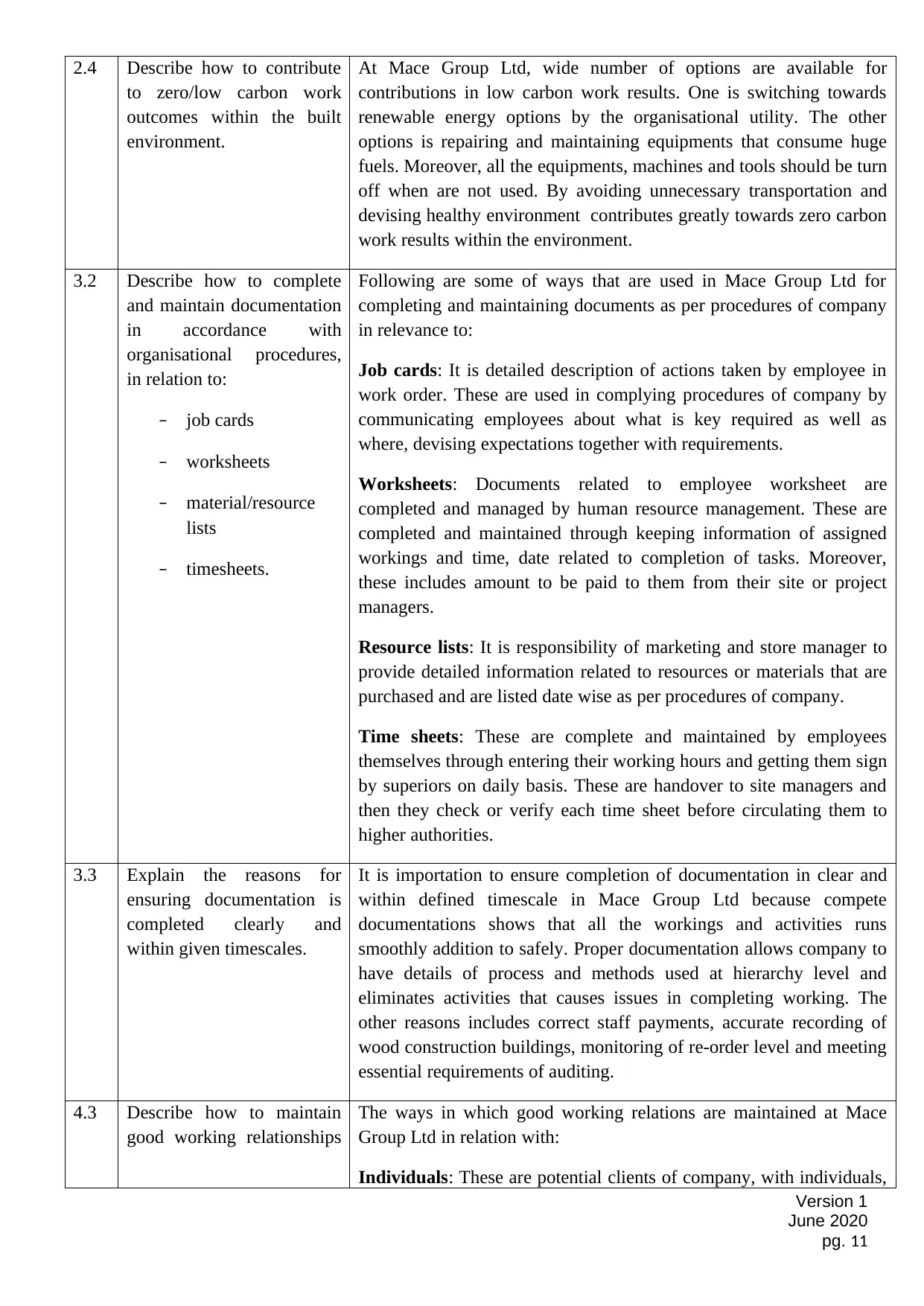
2.4 Describe how to contribute
to zero/low carbon work
outcomes within the built
environment.
At Mace Group Ltd, wide number of options are available for
contributions in low carbon work results. One is switching towards
renewable energy options by the organisational utility. The other
options is repairing and maintaining equipments that consume huge
fuels. Moreover, all the equipments, machines and tools should be turn
off when are not used. By avoiding unnecessary transportation and
devising healthy environment contributes greatly towards zero carbon
work results within the environment.
3.2 Describe how to complete
and maintain documentation
in accordance with
organisational procedures,
in relation to:
– job cards
– worksheets
– material/resource
lists
– timesheets.
Following are some of ways that are used in Mace Group Ltd for
completing and maintaining documents as per procedures of company
in relevance to:
Job cards: It is detailed description of actions taken by employee in
work order. These are used in complying procedures of company by
communicating employees about what is key required as well as
where, devising expectations together with requirements.
Worksheets: Documents related to employee worksheet are
completed and managed by human resource management. These are
completed and maintained through keeping information of assigned
workings and time, date related to completion of tasks. Moreover,
these includes amount to be paid to them from their site or project
managers.
Resource lists: It is responsibility of marketing and store manager to
provide detailed information related to resources or materials that are
purchased and are listed date wise as per procedures of company.
Time sheets: These are complete and maintained by employees
themselves through entering their working hours and getting them sign
by superiors on daily basis. These are handover to site managers and
then they check or verify each time sheet before circulating them to
higher authorities.
3.3 Explain the reasons for
ensuring documentation is
completed clearly and
within given timescales.
It is importation to ensure completion of documentation in clear and
within defined timescale in Mace Group Ltd because compete
documentations shows that all the workings and activities runs
smoothly addition to safely. Proper documentation allows company to
have details of process and methods used at hierarchy level and
eliminates activities that causes issues in completing working. The
other reasons includes correct staff payments, accurate recording of
wood construction buildings, monitoring of re-order level and meeting
essential requirements of auditing.
4.3 Describe how to maintain
good working relationships
The ways in which good working relations are maintained at Mace
Group Ltd in relation with:
Individuals: These are potential clients of company, with individuals,
Version 1
June 2020
pg. 11
to zero/low carbon work
outcomes within the built
environment.
At Mace Group Ltd, wide number of options are available for
contributions in low carbon work results. One is switching towards
renewable energy options by the organisational utility. The other
options is repairing and maintaining equipments that consume huge
fuels. Moreover, all the equipments, machines and tools should be turn
off when are not used. By avoiding unnecessary transportation and
devising healthy environment contributes greatly towards zero carbon
work results within the environment.
3.2 Describe how to complete
and maintain documentation
in accordance with
organisational procedures,
in relation to:
– job cards
– worksheets
– material/resource
lists
– timesheets.
Following are some of ways that are used in Mace Group Ltd for
completing and maintaining documents as per procedures of company
in relevance to:
Job cards: It is detailed description of actions taken by employee in
work order. These are used in complying procedures of company by
communicating employees about what is key required as well as
where, devising expectations together with requirements.
Worksheets: Documents related to employee worksheet are
completed and managed by human resource management. These are
completed and maintained through keeping information of assigned
workings and time, date related to completion of tasks. Moreover,
these includes amount to be paid to them from their site or project
managers.
Resource lists: It is responsibility of marketing and store manager to
provide detailed information related to resources or materials that are
purchased and are listed date wise as per procedures of company.
Time sheets: These are complete and maintained by employees
themselves through entering their working hours and getting them sign
by superiors on daily basis. These are handover to site managers and
then they check or verify each time sheet before circulating them to
higher authorities.
3.3 Explain the reasons for
ensuring documentation is
completed clearly and
within given timescales.
It is importation to ensure completion of documentation in clear and
within defined timescale in Mace Group Ltd because compete
documentations shows that all the workings and activities runs
smoothly addition to safely. Proper documentation allows company to
have details of process and methods used at hierarchy level and
eliminates activities that causes issues in completing working. The
other reasons includes correct staff payments, accurate recording of
wood construction buildings, monitoring of re-order level and meeting
essential requirements of auditing.
4.3 Describe how to maintain
good working relationships
The ways in which good working relations are maintained at Mace
Group Ltd in relation with:
Individuals: These are potential clients of company, with individuals,
Version 1
June 2020
pg. 11
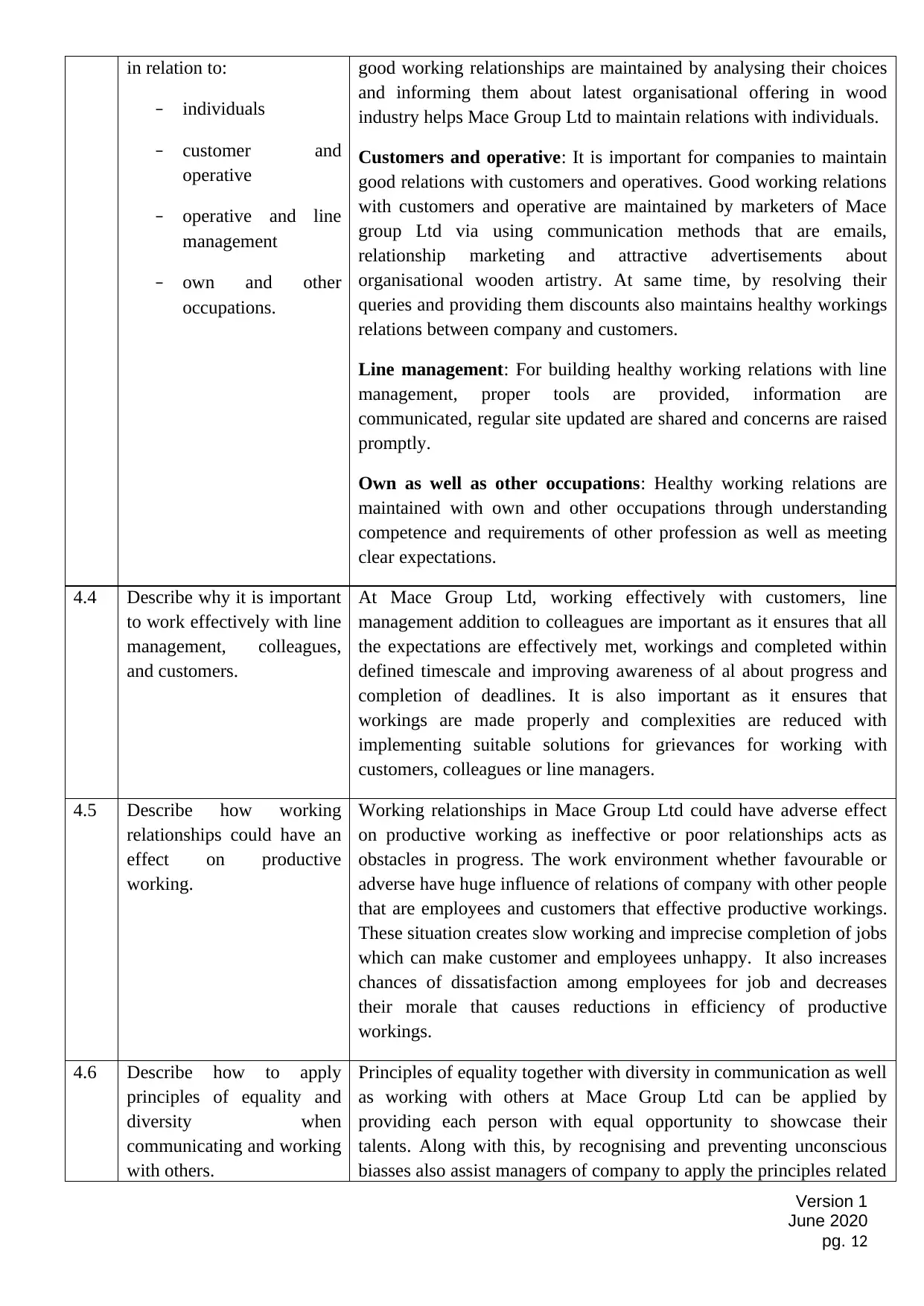
in relation to:
– individuals
– customer and
operative
– operative and line
management
– own and other
occupations.
good working relationships are maintained by analysing their choices
and informing them about latest organisational offering in wood
industry helps Mace Group Ltd to maintain relations with individuals.
Customers and operative: It is important for companies to maintain
good relations with customers and operatives. Good working relations
with customers and operative are maintained by marketers of Mace
group Ltd via using communication methods that are emails,
relationship marketing and attractive advertisements about
organisational wooden artistry. At same time, by resolving their
queries and providing them discounts also maintains healthy workings
relations between company and customers.
Line management: For building healthy working relations with line
management, proper tools are provided, information are
communicated, regular site updated are shared and concerns are raised
promptly.
Own as well as other occupations: Healthy working relations are
maintained with own and other occupations through understanding
competence and requirements of other profession as well as meeting
clear expectations.
4.4 Describe why it is important
to work effectively with line
management, colleagues,
and customers.
At Mace Group Ltd, working effectively with customers, line
management addition to colleagues are important as it ensures that all
the expectations are effectively met, workings and completed within
defined timescale and improving awareness of al about progress and
completion of deadlines. It is also important as it ensures that
workings are made properly and complexities are reduced with
implementing suitable solutions for grievances for working with
customers, colleagues or line managers.
4.5 Describe how working
relationships could have an
effect on productive
working.
Working relationships in Mace Group Ltd could have adverse effect
on productive working as ineffective or poor relationships acts as
obstacles in progress. The work environment whether favourable or
adverse have huge influence of relations of company with other people
that are employees and customers that effective productive workings.
These situation creates slow working and imprecise completion of jobs
which can make customer and employees unhappy. It also increases
chances of dissatisfaction among employees for job and decreases
their morale that causes reductions in efficiency of productive
workings.
4.6 Describe how to apply
principles of equality and
diversity when
communicating and working
with others.
Principles of equality together with diversity in communication as well
as working with others at Mace Group Ltd can be applied by
providing each person with equal opportunity to showcase their
talents. Along with this, by recognising and preventing unconscious
biasses also assist managers of company to apply the principles related
Version 1
June 2020
pg. 12
– individuals
– customer and
operative
– operative and line
management
– own and other
occupations.
good working relationships are maintained by analysing their choices
and informing them about latest organisational offering in wood
industry helps Mace Group Ltd to maintain relations with individuals.
Customers and operative: It is important for companies to maintain
good relations with customers and operatives. Good working relations
with customers and operative are maintained by marketers of Mace
group Ltd via using communication methods that are emails,
relationship marketing and attractive advertisements about
organisational wooden artistry. At same time, by resolving their
queries and providing them discounts also maintains healthy workings
relations between company and customers.
Line management: For building healthy working relations with line
management, proper tools are provided, information are
communicated, regular site updated are shared and concerns are raised
promptly.
Own as well as other occupations: Healthy working relations are
maintained with own and other occupations through understanding
competence and requirements of other profession as well as meeting
clear expectations.
4.4 Describe why it is important
to work effectively with line
management, colleagues,
and customers.
At Mace Group Ltd, working effectively with customers, line
management addition to colleagues are important as it ensures that all
the expectations are effectively met, workings and completed within
defined timescale and improving awareness of al about progress and
completion of deadlines. It is also important as it ensures that
workings are made properly and complexities are reduced with
implementing suitable solutions for grievances for working with
customers, colleagues or line managers.
4.5 Describe how working
relationships could have an
effect on productive
working.
Working relationships in Mace Group Ltd could have adverse effect
on productive working as ineffective or poor relationships acts as
obstacles in progress. The work environment whether favourable or
adverse have huge influence of relations of company with other people
that are employees and customers that effective productive workings.
These situation creates slow working and imprecise completion of jobs
which can make customer and employees unhappy. It also increases
chances of dissatisfaction among employees for job and decreases
their morale that causes reductions in efficiency of productive
workings.
4.6 Describe how to apply
principles of equality and
diversity when
communicating and working
with others.
Principles of equality together with diversity in communication as well
as working with others at Mace Group Ltd can be applied by
providing each person with equal opportunity to showcase their
talents. Along with this, by recognising and preventing unconscious
biasses also assist managers of company to apply the principles related
Version 1
June 2020
pg. 12
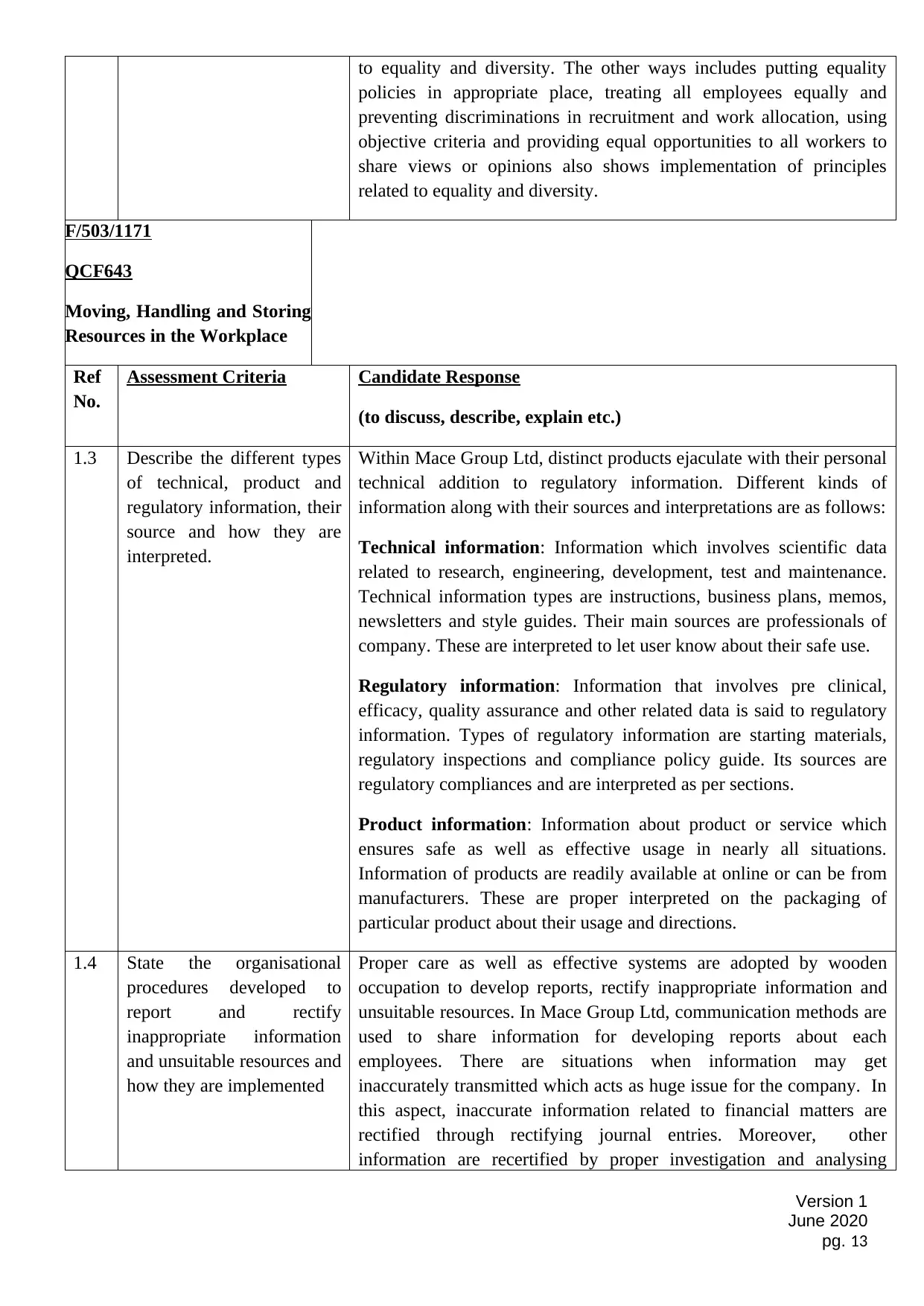
to equality and diversity. The other ways includes putting equality
policies in appropriate place, treating all employees equally and
preventing discriminations in recruitment and work allocation, using
objective criteria and providing equal opportunities to all workers to
share views or opinions also shows implementation of principles
related to equality and diversity.
F/503/1171
QCF643
Moving, Handling and Storing
Resources in the Workplace
Ref
No.
Assessment Criteria Candidate Response
(to discuss, describe, explain etc.)
1.3 Describe the different types
of technical, product and
regulatory information, their
source and how they are
interpreted.
Within Mace Group Ltd, distinct products ejaculate with their personal
technical addition to regulatory information. Different kinds of
information along with their sources and interpretations are as follows:
Technical information: Information which involves scientific data
related to research, engineering, development, test and maintenance.
Technical information types are instructions, business plans, memos,
newsletters and style guides. Their main sources are professionals of
company. These are interpreted to let user know about their safe use.
Regulatory information: Information that involves pre clinical,
efficacy, quality assurance and other related data is said to regulatory
information. Types of regulatory information are starting materials,
regulatory inspections and compliance policy guide. Its sources are
regulatory compliances and are interpreted as per sections.
Product information: Information about product or service which
ensures safe as well as effective usage in nearly all situations.
Information of products are readily available at online or can be from
manufacturers. These are proper interpreted on the packaging of
particular product about their usage and directions.
1.4 State the organisational
procedures developed to
report and rectify
inappropriate information
and unsuitable resources and
how they are implemented
Proper care as well as effective systems are adopted by wooden
occupation to develop reports, rectify inappropriate information and
unsuitable resources. In Mace Group Ltd, communication methods are
used to share information for developing reports about each
employees. There are situations when information may get
inaccurately transmitted which acts as huge issue for the company. In
this aspect, inaccurate information related to financial matters are
rectified through rectifying journal entries. Moreover, other
information are recertified by proper investigation and analysing
Version 1
June 2020
pg. 13
policies in appropriate place, treating all employees equally and
preventing discriminations in recruitment and work allocation, using
objective criteria and providing equal opportunities to all workers to
share views or opinions also shows implementation of principles
related to equality and diversity.
F/503/1171
QCF643
Moving, Handling and Storing
Resources in the Workplace
Ref
No.
Assessment Criteria Candidate Response
(to discuss, describe, explain etc.)
1.3 Describe the different types
of technical, product and
regulatory information, their
source and how they are
interpreted.
Within Mace Group Ltd, distinct products ejaculate with their personal
technical addition to regulatory information. Different kinds of
information along with their sources and interpretations are as follows:
Technical information: Information which involves scientific data
related to research, engineering, development, test and maintenance.
Technical information types are instructions, business plans, memos,
newsletters and style guides. Their main sources are professionals of
company. These are interpreted to let user know about their safe use.
Regulatory information: Information that involves pre clinical,
efficacy, quality assurance and other related data is said to regulatory
information. Types of regulatory information are starting materials,
regulatory inspections and compliance policy guide. Its sources are
regulatory compliances and are interpreted as per sections.
Product information: Information about product or service which
ensures safe as well as effective usage in nearly all situations.
Information of products are readily available at online or can be from
manufacturers. These are proper interpreted on the packaging of
particular product about their usage and directions.
1.4 State the organisational
procedures developed to
report and rectify
inappropriate information
and unsuitable resources and
how they are implemented
Proper care as well as effective systems are adopted by wooden
occupation to develop reports, rectify inappropriate information and
unsuitable resources. In Mace Group Ltd, communication methods are
used to share information for developing reports about each
employees. There are situations when information may get
inaccurately transmitted which acts as huge issue for the company. In
this aspect, inaccurate information related to financial matters are
rectified through rectifying journal entries. Moreover, other
information are recertified by proper investigation and analysing
Version 1
June 2020
pg. 13
Paraphrase This Document
Need a fresh take? Get an instant paraphrase of this document with our AI Paraphraser
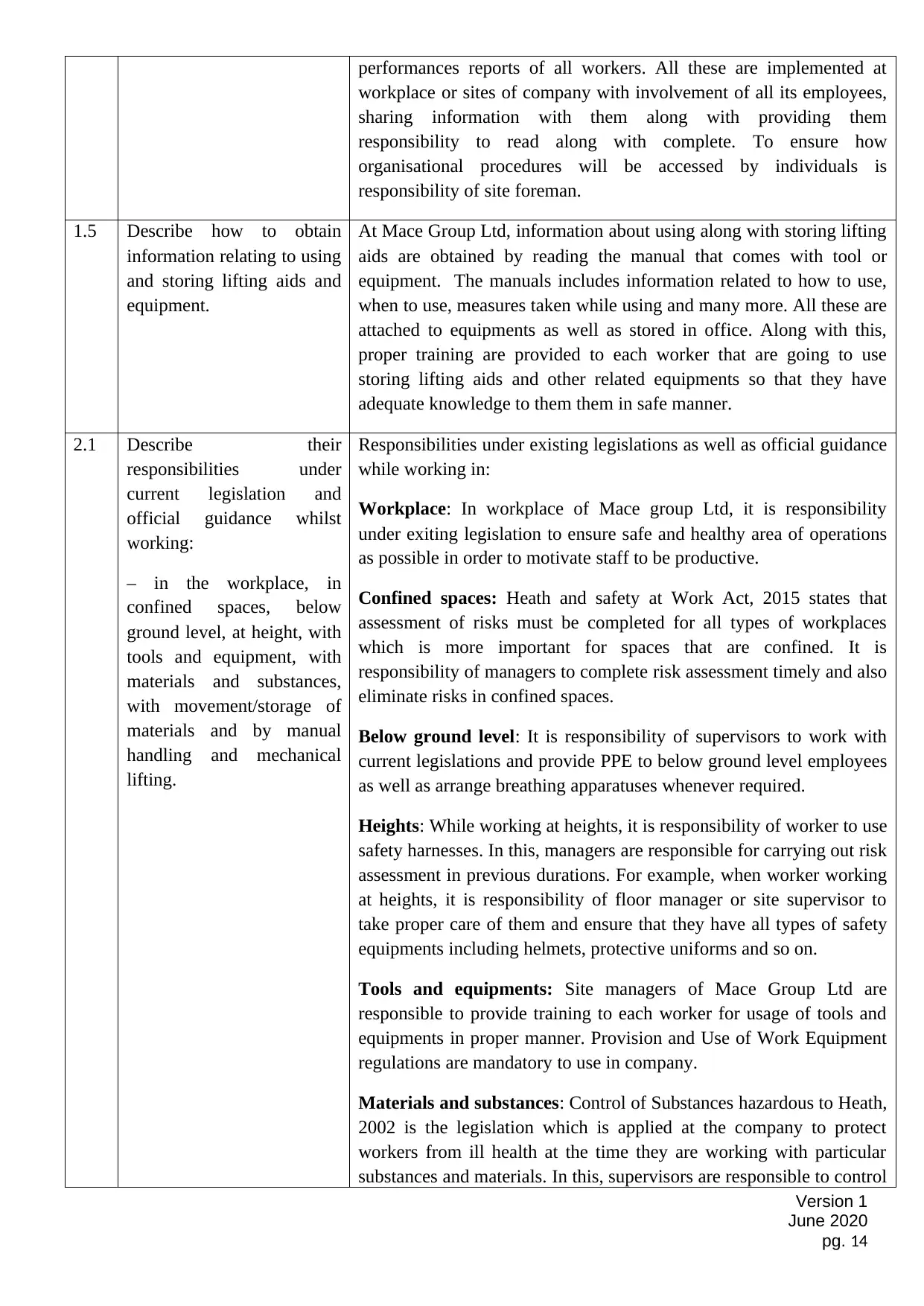
performances reports of all workers. All these are implemented at
workplace or sites of company with involvement of all its employees,
sharing information with them along with providing them
responsibility to read along with complete. To ensure how
organisational procedures will be accessed by individuals is
responsibility of site foreman.
1.5 Describe how to obtain
information relating to using
and storing lifting aids and
equipment.
At Mace Group Ltd, information about using along with storing lifting
aids are obtained by reading the manual that comes with tool or
equipment. The manuals includes information related to how to use,
when to use, measures taken while using and many more. All these are
attached to equipments as well as stored in office. Along with this,
proper training are provided to each worker that are going to use
storing lifting aids and other related equipments so that they have
adequate knowledge to them them in safe manner.
2.1 Describe their
responsibilities under
current legislation and
official guidance whilst
working:
– in the workplace, in
confined spaces, below
ground level, at height, with
tools and equipment, with
materials and substances,
with movement/storage of
materials and by manual
handling and mechanical
lifting.
Responsibilities under existing legislations as well as official guidance
while working in:
Workplace: In workplace of Mace group Ltd, it is responsibility
under exiting legislation to ensure safe and healthy area of operations
as possible in order to motivate staff to be productive.
Confined spaces: Heath and safety at Work Act, 2015 states that
assessment of risks must be completed for all types of workplaces
which is more important for spaces that are confined. It is
responsibility of managers to complete risk assessment timely and also
eliminate risks in confined spaces.
Below ground level: It is responsibility of supervisors to work with
current legislations and provide PPE to below ground level employees
as well as arrange breathing apparatuses whenever required.
Heights: While working at heights, it is responsibility of worker to use
safety harnesses. In this, managers are responsible for carrying out risk
assessment in previous durations. For example, when worker working
at heights, it is responsibility of floor manager or site supervisor to
take proper care of them and ensure that they have all types of safety
equipments including helmets, protective uniforms and so on.
Tools and equipments: Site managers of Mace Group Ltd are
responsible to provide training to each worker for usage of tools and
equipments in proper manner. Provision and Use of Work Equipment
regulations are mandatory to use in company.
Materials and substances: Control of Substances hazardous to Heath,
2002 is the legislation which is applied at the company to protect
workers from ill health at the time they are working with particular
substances and materials. In this, supervisors are responsible to control
Version 1
June 2020
pg. 14
workplace or sites of company with involvement of all its employees,
sharing information with them along with providing them
responsibility to read along with complete. To ensure how
organisational procedures will be accessed by individuals is
responsibility of site foreman.
1.5 Describe how to obtain
information relating to using
and storing lifting aids and
equipment.
At Mace Group Ltd, information about using along with storing lifting
aids are obtained by reading the manual that comes with tool or
equipment. The manuals includes information related to how to use,
when to use, measures taken while using and many more. All these are
attached to equipments as well as stored in office. Along with this,
proper training are provided to each worker that are going to use
storing lifting aids and other related equipments so that they have
adequate knowledge to them them in safe manner.
2.1 Describe their
responsibilities under
current legislation and
official guidance whilst
working:
– in the workplace, in
confined spaces, below
ground level, at height, with
tools and equipment, with
materials and substances,
with movement/storage of
materials and by manual
handling and mechanical
lifting.
Responsibilities under existing legislations as well as official guidance
while working in:
Workplace: In workplace of Mace group Ltd, it is responsibility
under exiting legislation to ensure safe and healthy area of operations
as possible in order to motivate staff to be productive.
Confined spaces: Heath and safety at Work Act, 2015 states that
assessment of risks must be completed for all types of workplaces
which is more important for spaces that are confined. It is
responsibility of managers to complete risk assessment timely and also
eliminate risks in confined spaces.
Below ground level: It is responsibility of supervisors to work with
current legislations and provide PPE to below ground level employees
as well as arrange breathing apparatuses whenever required.
Heights: While working at heights, it is responsibility of worker to use
safety harnesses. In this, managers are responsible for carrying out risk
assessment in previous durations. For example, when worker working
at heights, it is responsibility of floor manager or site supervisor to
take proper care of them and ensure that they have all types of safety
equipments including helmets, protective uniforms and so on.
Tools and equipments: Site managers of Mace Group Ltd are
responsible to provide training to each worker for usage of tools and
equipments in proper manner. Provision and Use of Work Equipment
regulations are mandatory to use in company.
Materials and substances: Control of Substances hazardous to Heath,
2002 is the legislation which is applied at the company to protect
workers from ill health at the time they are working with particular
substances and materials. In this, supervisors are responsible to control
Version 1
June 2020
pg. 14
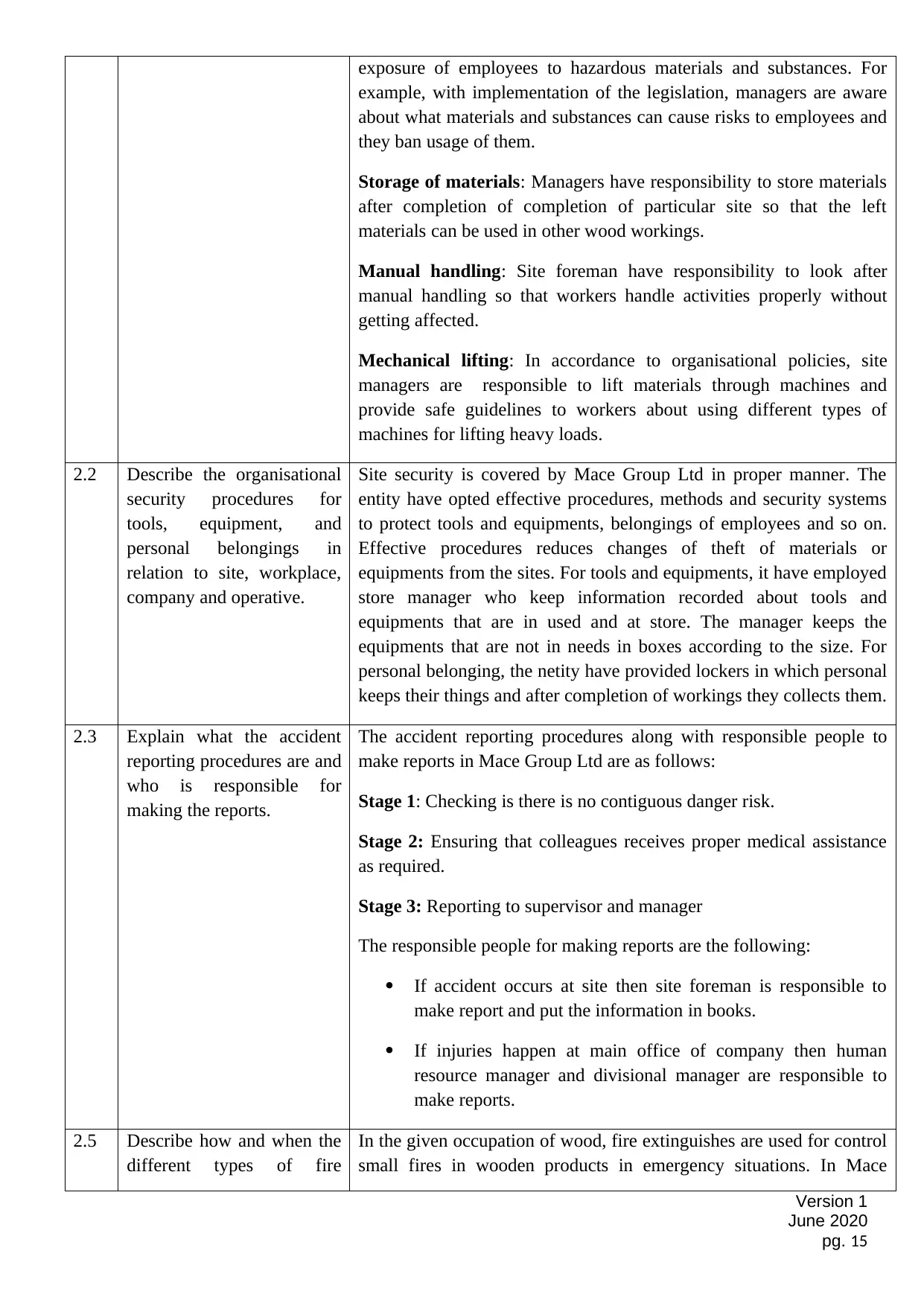
exposure of employees to hazardous materials and substances. For
example, with implementation of the legislation, managers are aware
about what materials and substances can cause risks to employees and
they ban usage of them.
Storage of materials: Managers have responsibility to store materials
after completion of completion of particular site so that the left
materials can be used in other wood workings.
Manual handling: Site foreman have responsibility to look after
manual handling so that workers handle activities properly without
getting affected.
Mechanical lifting: In accordance to organisational policies, site
managers are responsible to lift materials through machines and
provide safe guidelines to workers about using different types of
machines for lifting heavy loads.
2.2 Describe the organisational
security procedures for
tools, equipment, and
personal belongings in
relation to site, workplace,
company and operative.
Site security is covered by Mace Group Ltd in proper manner. The
entity have opted effective procedures, methods and security systems
to protect tools and equipments, belongings of employees and so on.
Effective procedures reduces changes of theft of materials or
equipments from the sites. For tools and equipments, it have employed
store manager who keep information recorded about tools and
equipments that are in used and at store. The manager keeps the
equipments that are not in needs in boxes according to the size. For
personal belonging, the netity have provided lockers in which personal
keeps their things and after completion of workings they collects them.
2.3 Explain what the accident
reporting procedures are and
who is responsible for
making the reports.
The accident reporting procedures along with responsible people to
make reports in Mace Group Ltd are as follows:
Stage 1: Checking is there is no contiguous danger risk.
Stage 2: Ensuring that colleagues receives proper medical assistance
as required.
Stage 3: Reporting to supervisor and manager
The responsible people for making reports are the following:
If accident occurs at site then site foreman is responsible to
make report and put the information in books.
If injuries happen at main office of company then human
resource manager and divisional manager are responsible to
make reports.
2.5 Describe how and when the
different types of fire
In the given occupation of wood, fire extinguishes are used for control
small fires in wooden products in emergency situations. In Mace
Version 1
June 2020
pg. 15
example, with implementation of the legislation, managers are aware
about what materials and substances can cause risks to employees and
they ban usage of them.
Storage of materials: Managers have responsibility to store materials
after completion of completion of particular site so that the left
materials can be used in other wood workings.
Manual handling: Site foreman have responsibility to look after
manual handling so that workers handle activities properly without
getting affected.
Mechanical lifting: In accordance to organisational policies, site
managers are responsible to lift materials through machines and
provide safe guidelines to workers about using different types of
machines for lifting heavy loads.
2.2 Describe the organisational
security procedures for
tools, equipment, and
personal belongings in
relation to site, workplace,
company and operative.
Site security is covered by Mace Group Ltd in proper manner. The
entity have opted effective procedures, methods and security systems
to protect tools and equipments, belongings of employees and so on.
Effective procedures reduces changes of theft of materials or
equipments from the sites. For tools and equipments, it have employed
store manager who keep information recorded about tools and
equipments that are in used and at store. The manager keeps the
equipments that are not in needs in boxes according to the size. For
personal belonging, the netity have provided lockers in which personal
keeps their things and after completion of workings they collects them.
2.3 Explain what the accident
reporting procedures are and
who is responsible for
making the reports.
The accident reporting procedures along with responsible people to
make reports in Mace Group Ltd are as follows:
Stage 1: Checking is there is no contiguous danger risk.
Stage 2: Ensuring that colleagues receives proper medical assistance
as required.
Stage 3: Reporting to supervisor and manager
The responsible people for making reports are the following:
If accident occurs at site then site foreman is responsible to
make report and put the information in books.
If injuries happen at main office of company then human
resource manager and divisional manager are responsible to
make reports.
2.5 Describe how and when the
different types of fire
In the given occupation of wood, fire extinguishes are used for control
small fires in wooden products in emergency situations. In Mace
Version 1
June 2020
pg. 15
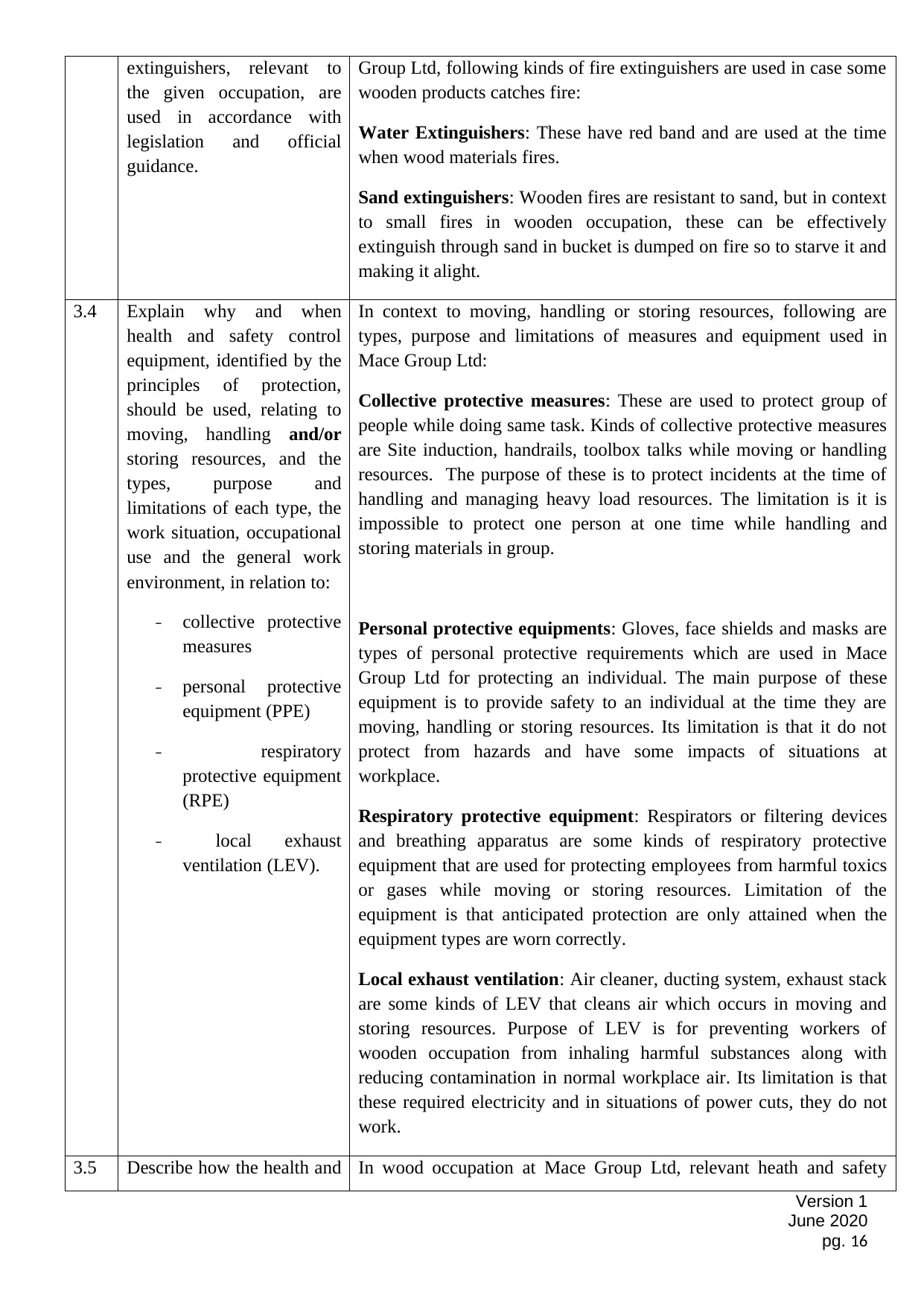
extinguishers, relevant to
the given occupation, are
used in accordance with
legislation and official
guidance.
Group Ltd, following kinds of fire extinguishers are used in case some
wooden products catches fire:
Water Extinguishers: These have red band and are used at the time
when wood materials fires.
Sand extinguishers: Wooden fires are resistant to sand, but in context
to small fires in wooden occupation, these can be effectively
extinguish through sand in bucket is dumped on fire so to starve it and
making it alight.
3.4 Explain why and when
health and safety control
equipment, identified by the
principles of protection,
should be used, relating to
moving, handling and/or
storing resources, and the
types, purpose and
limitations of each type, the
work situation, occupational
use and the general work
environment, in relation to:
– collective protective
measures
– personal protective
equipment (PPE)
– respiratory
protective equipment
(RPE)
– local exhaust
ventilation (LEV).
In context to moving, handling or storing resources, following are
types, purpose and limitations of measures and equipment used in
Mace Group Ltd:
Collective protective measures: These are used to protect group of
people while doing same task. Kinds of collective protective measures
are Site induction, handrails, toolbox talks while moving or handling
resources. The purpose of these is to protect incidents at the time of
handling and managing heavy load resources. The limitation is it is
impossible to protect one person at one time while handling and
storing materials in group.
Personal protective equipments: Gloves, face shields and masks are
types of personal protective requirements which are used in Mace
Group Ltd for protecting an individual. The main purpose of these
equipment is to provide safety to an individual at the time they are
moving, handling or storing resources. Its limitation is that it do not
protect from hazards and have some impacts of situations at
workplace.
Respiratory protective equipment: Respirators or filtering devices
and breathing apparatus are some kinds of respiratory protective
equipment that are used for protecting employees from harmful toxics
or gases while moving or storing resources. Limitation of the
equipment is that anticipated protection are only attained when the
equipment types are worn correctly.
Local exhaust ventilation: Air cleaner, ducting system, exhaust stack
are some kinds of LEV that cleans air which occurs in moving and
storing resources. Purpose of LEV is for preventing workers of
wooden occupation from inhaling harmful substances along with
reducing contamination in normal workplace air. Its limitation is that
these required electricity and in situations of power cuts, they do not
work.
3.5 Describe how the health and In wood occupation at Mace Group Ltd, relevant heath and safety
Version 1
June 2020
pg. 16
the given occupation, are
used in accordance with
legislation and official
guidance.
Group Ltd, following kinds of fire extinguishers are used in case some
wooden products catches fire:
Water Extinguishers: These have red band and are used at the time
when wood materials fires.
Sand extinguishers: Wooden fires are resistant to sand, but in context
to small fires in wooden occupation, these can be effectively
extinguish through sand in bucket is dumped on fire so to starve it and
making it alight.
3.4 Explain why and when
health and safety control
equipment, identified by the
principles of protection,
should be used, relating to
moving, handling and/or
storing resources, and the
types, purpose and
limitations of each type, the
work situation, occupational
use and the general work
environment, in relation to:
– collective protective
measures
– personal protective
equipment (PPE)
– respiratory
protective equipment
(RPE)
– local exhaust
ventilation (LEV).
In context to moving, handling or storing resources, following are
types, purpose and limitations of measures and equipment used in
Mace Group Ltd:
Collective protective measures: These are used to protect group of
people while doing same task. Kinds of collective protective measures
are Site induction, handrails, toolbox talks while moving or handling
resources. The purpose of these is to protect incidents at the time of
handling and managing heavy load resources. The limitation is it is
impossible to protect one person at one time while handling and
storing materials in group.
Personal protective equipments: Gloves, face shields and masks are
types of personal protective requirements which are used in Mace
Group Ltd for protecting an individual. The main purpose of these
equipment is to provide safety to an individual at the time they are
moving, handling or storing resources. Its limitation is that it do not
protect from hazards and have some impacts of situations at
workplace.
Respiratory protective equipment: Respirators or filtering devices
and breathing apparatus are some kinds of respiratory protective
equipment that are used for protecting employees from harmful toxics
or gases while moving or storing resources. Limitation of the
equipment is that anticipated protection are only attained when the
equipment types are worn correctly.
Local exhaust ventilation: Air cleaner, ducting system, exhaust stack
are some kinds of LEV that cleans air which occurs in moving and
storing resources. Purpose of LEV is for preventing workers of
wooden occupation from inhaling harmful substances along with
reducing contamination in normal workplace air. Its limitation is that
these required electricity and in situations of power cuts, they do not
work.
3.5 Describe how the health and In wood occupation at Mace Group Ltd, relevant heath and safety
Version 1
June 2020
pg. 16
Secure Best Marks with AI Grader
Need help grading? Try our AI Grader for instant feedback on your assignments.
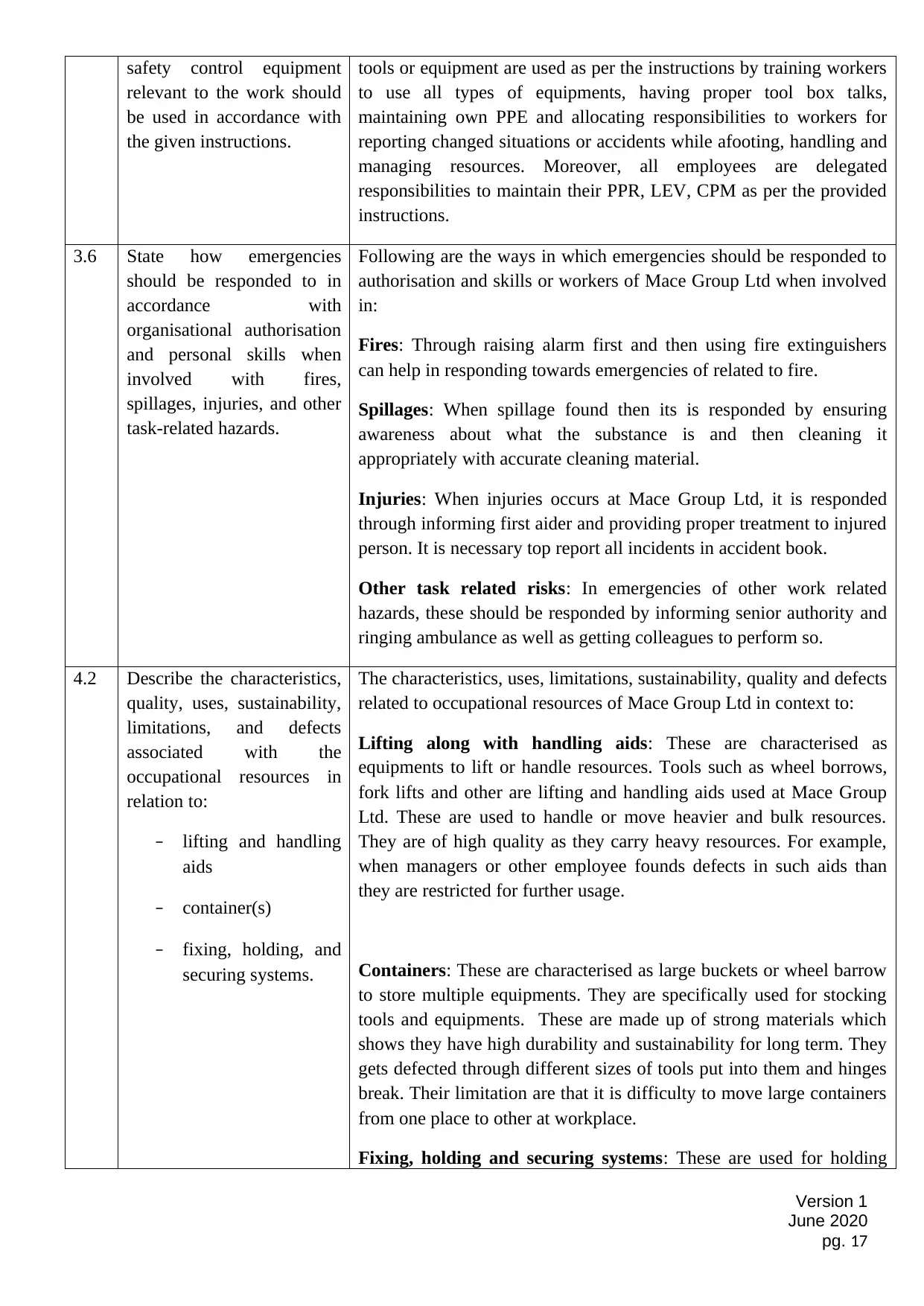
safety control equipment
relevant to the work should
be used in accordance with
the given instructions.
tools or equipment are used as per the instructions by training workers
to use all types of equipments, having proper tool box talks,
maintaining own PPE and allocating responsibilities to workers for
reporting changed situations or accidents while afooting, handling and
managing resources. Moreover, all employees are delegated
responsibilities to maintain their PPR, LEV, CPM as per the provided
instructions.
3.6 State how emergencies
should be responded to in
accordance with
organisational authorisation
and personal skills when
involved with fires,
spillages, injuries, and other
task-related hazards.
Following are the ways in which emergencies should be responded to
authorisation and skills or workers of Mace Group Ltd when involved
in:
Fires: Through raising alarm first and then using fire extinguishers
can help in responding towards emergencies of related to fire.
Spillages: When spillage found then its is responded by ensuring
awareness about what the substance is and then cleaning it
appropriately with accurate cleaning material.
Injuries: When injuries occurs at Mace Group Ltd, it is responded
through informing first aider and providing proper treatment to injured
person. It is necessary top report all incidents in accident book.
Other task related risks: In emergencies of other work related
hazards, these should be responded by informing senior authority and
ringing ambulance as well as getting colleagues to perform so.
4.2 Describe the characteristics,
quality, uses, sustainability,
limitations, and defects
associated with the
occupational resources in
relation to:
– lifting and handling
aids
– container(s)
– fixing, holding, and
securing systems.
The characteristics, uses, limitations, sustainability, quality and defects
related to occupational resources of Mace Group Ltd in context to:
Lifting along with handling aids: These are characterised as
equipments to lift or handle resources. Tools such as wheel borrows,
fork lifts and other are lifting and handling aids used at Mace Group
Ltd. These are used to handle or move heavier and bulk resources.
They are of high quality as they carry heavy resources. For example,
when managers or other employee founds defects in such aids than
they are restricted for further usage.
Containers: These are characterised as large buckets or wheel barrow
to store multiple equipments. They are specifically used for stocking
tools and equipments. These are made up of strong materials which
shows they have high durability and sustainability for long term. They
gets defected through different sizes of tools put into them and hinges
break. Their limitation are that it is difficulty to move large containers
from one place to other at workplace.
Fixing, holding and securing systems: These are used for holding
Version 1
June 2020
pg. 17
relevant to the work should
be used in accordance with
the given instructions.
tools or equipment are used as per the instructions by training workers
to use all types of equipments, having proper tool box talks,
maintaining own PPE and allocating responsibilities to workers for
reporting changed situations or accidents while afooting, handling and
managing resources. Moreover, all employees are delegated
responsibilities to maintain their PPR, LEV, CPM as per the provided
instructions.
3.6 State how emergencies
should be responded to in
accordance with
organisational authorisation
and personal skills when
involved with fires,
spillages, injuries, and other
task-related hazards.
Following are the ways in which emergencies should be responded to
authorisation and skills or workers of Mace Group Ltd when involved
in:
Fires: Through raising alarm first and then using fire extinguishers
can help in responding towards emergencies of related to fire.
Spillages: When spillage found then its is responded by ensuring
awareness about what the substance is and then cleaning it
appropriately with accurate cleaning material.
Injuries: When injuries occurs at Mace Group Ltd, it is responded
through informing first aider and providing proper treatment to injured
person. It is necessary top report all incidents in accident book.
Other task related risks: In emergencies of other work related
hazards, these should be responded by informing senior authority and
ringing ambulance as well as getting colleagues to perform so.
4.2 Describe the characteristics,
quality, uses, sustainability,
limitations, and defects
associated with the
occupational resources in
relation to:
– lifting and handling
aids
– container(s)
– fixing, holding, and
securing systems.
The characteristics, uses, limitations, sustainability, quality and defects
related to occupational resources of Mace Group Ltd in context to:
Lifting along with handling aids: These are characterised as
equipments to lift or handle resources. Tools such as wheel borrows,
fork lifts and other are lifting and handling aids used at Mace Group
Ltd. These are used to handle or move heavier and bulk resources.
They are of high quality as they carry heavy resources. For example,
when managers or other employee founds defects in such aids than
they are restricted for further usage.
Containers: These are characterised as large buckets or wheel barrow
to store multiple equipments. They are specifically used for stocking
tools and equipments. These are made up of strong materials which
shows they have high durability and sustainability for long term. They
gets defected through different sizes of tools put into them and hinges
break. Their limitation are that it is difficulty to move large containers
from one place to other at workplace.
Fixing, holding and securing systems: These are used for holding
Version 1
June 2020
pg. 17
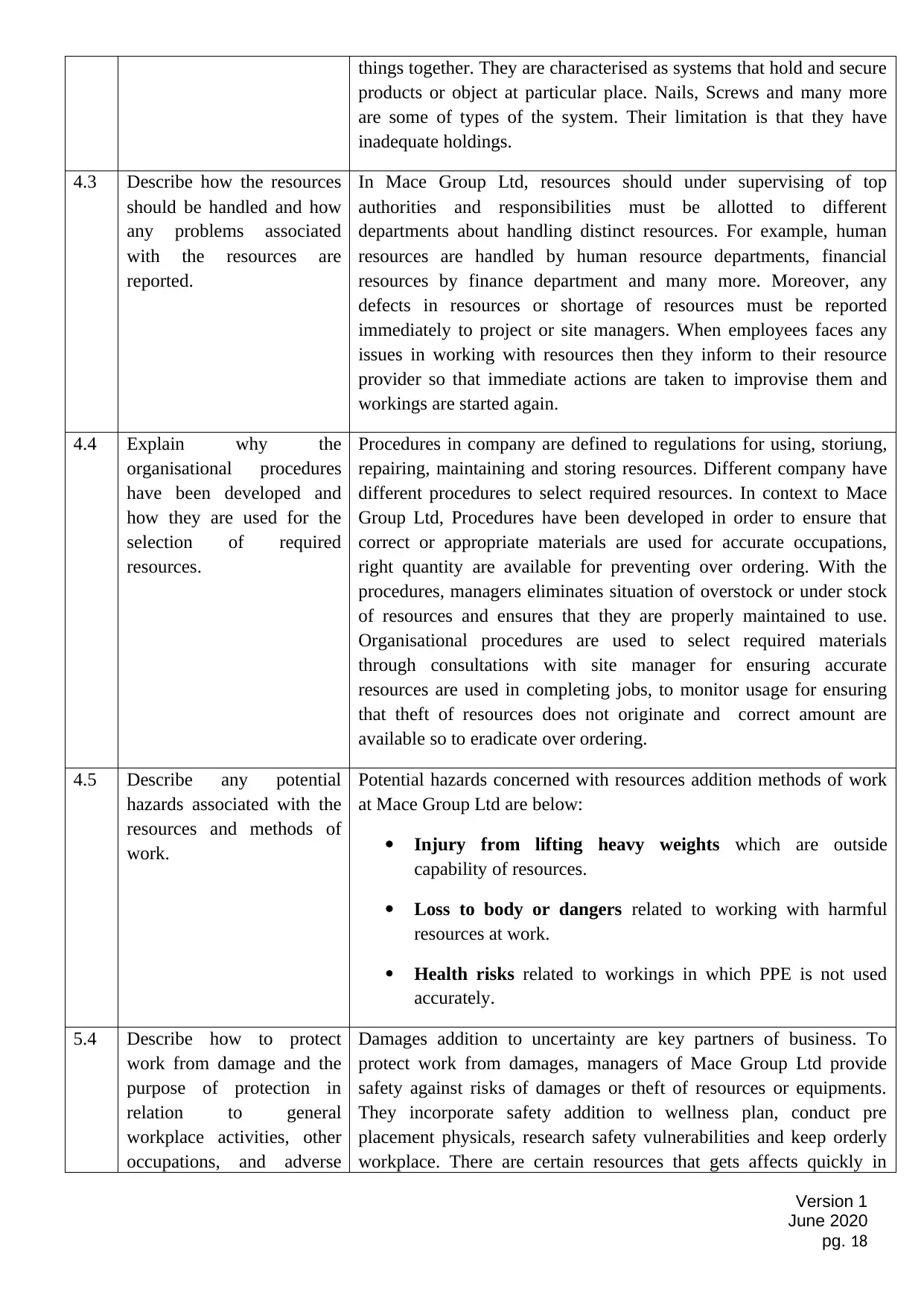
things together. They are characterised as systems that hold and secure
products or object at particular place. Nails, Screws and many more
are some of types of the system. Their limitation is that they have
inadequate holdings.
4.3 Describe how the resources
should be handled and how
any problems associated
with the resources are
reported.
In Mace Group Ltd, resources should under supervising of top
authorities and responsibilities must be allotted to different
departments about handling distinct resources. For example, human
resources are handled by human resource departments, financial
resources by finance department and many more. Moreover, any
defects in resources or shortage of resources must be reported
immediately to project or site managers. When employees faces any
issues in working with resources then they inform to their resource
provider so that immediate actions are taken to improvise them and
workings are started again.
4.4 Explain why the
organisational procedures
have been developed and
how they are used for the
selection of required
resources.
Procedures in company are defined to regulations for using, storiung,
repairing, maintaining and storing resources. Different company have
different procedures to select required resources. In context to Mace
Group Ltd, Procedures have been developed in order to ensure that
correct or appropriate materials are used for accurate occupations,
right quantity are available for preventing over ordering. With the
procedures, managers eliminates situation of overstock or under stock
of resources and ensures that they are properly maintained to use.
Organisational procedures are used to select required materials
through consultations with site manager for ensuring accurate
resources are used in completing jobs, to monitor usage for ensuring
that theft of resources does not originate and correct amount are
available so to eradicate over ordering.
4.5 Describe any potential
hazards associated with the
resources and methods of
work.
Potential hazards concerned with resources addition methods of work
at Mace Group Ltd are below:
Injury from lifting heavy weights which are outside
capability of resources.
Loss to body or dangers related to working with harmful
resources at work.
Health risks related to workings in which PPE is not used
accurately.
5.4 Describe how to protect
work from damage and the
purpose of protection in
relation to general
workplace activities, other
occupations, and adverse
Damages addition to uncertainty are key partners of business. To
protect work from damages, managers of Mace Group Ltd provide
safety against risks of damages or theft of resources or equipments.
They incorporate safety addition to wellness plan, conduct pre
placement physicals, research safety vulnerabilities and keep orderly
workplace. There are certain resources that gets affects quickly in
Version 1
June 2020
pg. 18
products or object at particular place. Nails, Screws and many more
are some of types of the system. Their limitation is that they have
inadequate holdings.
4.3 Describe how the resources
should be handled and how
any problems associated
with the resources are
reported.
In Mace Group Ltd, resources should under supervising of top
authorities and responsibilities must be allotted to different
departments about handling distinct resources. For example, human
resources are handled by human resource departments, financial
resources by finance department and many more. Moreover, any
defects in resources or shortage of resources must be reported
immediately to project or site managers. When employees faces any
issues in working with resources then they inform to their resource
provider so that immediate actions are taken to improvise them and
workings are started again.
4.4 Explain why the
organisational procedures
have been developed and
how they are used for the
selection of required
resources.
Procedures in company are defined to regulations for using, storiung,
repairing, maintaining and storing resources. Different company have
different procedures to select required resources. In context to Mace
Group Ltd, Procedures have been developed in order to ensure that
correct or appropriate materials are used for accurate occupations,
right quantity are available for preventing over ordering. With the
procedures, managers eliminates situation of overstock or under stock
of resources and ensures that they are properly maintained to use.
Organisational procedures are used to select required materials
through consultations with site manager for ensuring accurate
resources are used in completing jobs, to monitor usage for ensuring
that theft of resources does not originate and correct amount are
available so to eradicate over ordering.
4.5 Describe any potential
hazards associated with the
resources and methods of
work.
Potential hazards concerned with resources addition methods of work
at Mace Group Ltd are below:
Injury from lifting heavy weights which are outside
capability of resources.
Loss to body or dangers related to working with harmful
resources at work.
Health risks related to workings in which PPE is not used
accurately.
5.4 Describe how to protect
work from damage and the
purpose of protection in
relation to general
workplace activities, other
occupations, and adverse
Damages addition to uncertainty are key partners of business. To
protect work from damages, managers of Mace Group Ltd provide
safety against risks of damages or theft of resources or equipments.
They incorporate safety addition to wellness plan, conduct pre
placement physicals, research safety vulnerabilities and keep orderly
workplace. There are certain resources that gets affects quickly in
Version 1
June 2020
pg. 18
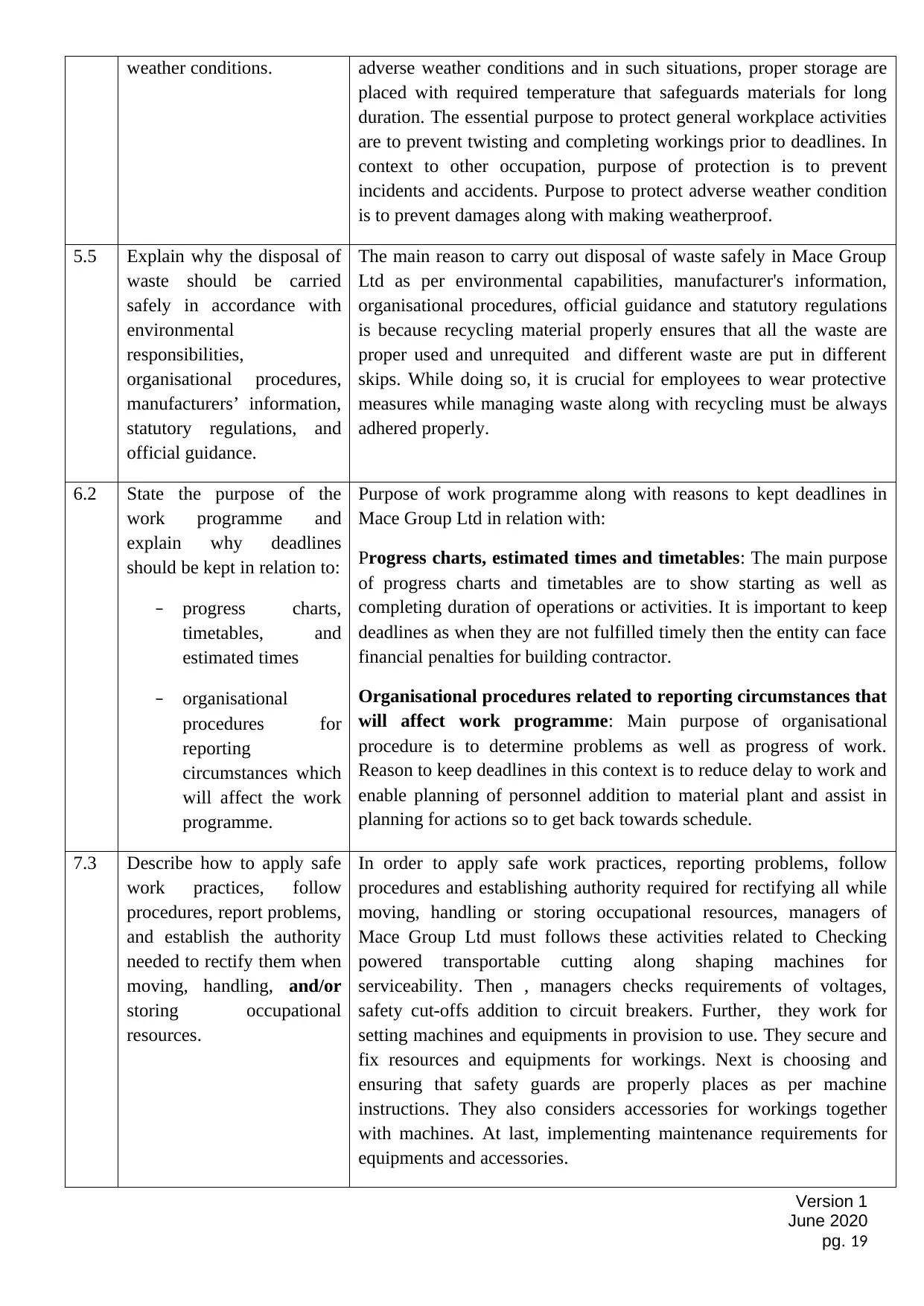
weather conditions. adverse weather conditions and in such situations, proper storage are
placed with required temperature that safeguards materials for long
duration. The essential purpose to protect general workplace activities
are to prevent twisting and completing workings prior to deadlines. In
context to other occupation, purpose of protection is to prevent
incidents and accidents. Purpose to protect adverse weather condition
is to prevent damages along with making weatherproof.
5.5 Explain why the disposal of
waste should be carried
safely in accordance with
environmental
responsibilities,
organisational procedures,
manufacturers’ information,
statutory regulations, and
official guidance.
The main reason to carry out disposal of waste safely in Mace Group
Ltd as per environmental capabilities, manufacturer's information,
organisational procedures, official guidance and statutory regulations
is because recycling material properly ensures that all the waste are
proper used and unrequited and different waste are put in different
skips. While doing so, it is crucial for employees to wear protective
measures while managing waste along with recycling must be always
adhered properly.
6.2 State the purpose of the
work programme and
explain why deadlines
should be kept in relation to:
– progress charts,
timetables, and
estimated times
– organisational
procedures for
reporting
circumstances which
will affect the work
programme.
Purpose of work programme along with reasons to kept deadlines in
Mace Group Ltd in relation with:
Progress charts, estimated times and timetables: The main purpose
of progress charts and timetables are to show starting as well as
completing duration of operations or activities. It is important to keep
deadlines as when they are not fulfilled timely then the entity can face
financial penalties for building contractor.
Organisational procedures related to reporting circumstances that
will affect work programme: Main purpose of organisational
procedure is to determine problems as well as progress of work.
Reason to keep deadlines in this context is to reduce delay to work and
enable planning of personnel addition to material plant and assist in
planning for actions so to get back towards schedule.
7.3 Describe how to apply safe
work practices, follow
procedures, report problems,
and establish the authority
needed to rectify them when
moving, handling, and/or
storing occupational
resources.
In order to apply safe work practices, reporting problems, follow
procedures and establishing authority required for rectifying all while
moving, handling or storing occupational resources, managers of
Mace Group Ltd must follows these activities related to Checking
powered transportable cutting along shaping machines for
serviceability. Then , managers checks requirements of voltages,
safety cut-offs addition to circuit breakers. Further, they work for
setting machines and equipments in provision to use. They secure and
fix resources and equipments for workings. Next is choosing and
ensuring that safety guards are properly places as per machine
instructions. They also considers accessories for workings together
with machines. At last, implementing maintenance requirements for
equipments and accessories.
Version 1
June 2020
pg. 19
placed with required temperature that safeguards materials for long
duration. The essential purpose to protect general workplace activities
are to prevent twisting and completing workings prior to deadlines. In
context to other occupation, purpose of protection is to prevent
incidents and accidents. Purpose to protect adverse weather condition
is to prevent damages along with making weatherproof.
5.5 Explain why the disposal of
waste should be carried
safely in accordance with
environmental
responsibilities,
organisational procedures,
manufacturers’ information,
statutory regulations, and
official guidance.
The main reason to carry out disposal of waste safely in Mace Group
Ltd as per environmental capabilities, manufacturer's information,
organisational procedures, official guidance and statutory regulations
is because recycling material properly ensures that all the waste are
proper used and unrequited and different waste are put in different
skips. While doing so, it is crucial for employees to wear protective
measures while managing waste along with recycling must be always
adhered properly.
6.2 State the purpose of the
work programme and
explain why deadlines
should be kept in relation to:
– progress charts,
timetables, and
estimated times
– organisational
procedures for
reporting
circumstances which
will affect the work
programme.
Purpose of work programme along with reasons to kept deadlines in
Mace Group Ltd in relation with:
Progress charts, estimated times and timetables: The main purpose
of progress charts and timetables are to show starting as well as
completing duration of operations or activities. It is important to keep
deadlines as when they are not fulfilled timely then the entity can face
financial penalties for building contractor.
Organisational procedures related to reporting circumstances that
will affect work programme: Main purpose of organisational
procedure is to determine problems as well as progress of work.
Reason to keep deadlines in this context is to reduce delay to work and
enable planning of personnel addition to material plant and assist in
planning for actions so to get back towards schedule.
7.3 Describe how to apply safe
work practices, follow
procedures, report problems,
and establish the authority
needed to rectify them when
moving, handling, and/or
storing occupational
resources.
In order to apply safe work practices, reporting problems, follow
procedures and establishing authority required for rectifying all while
moving, handling or storing occupational resources, managers of
Mace Group Ltd must follows these activities related to Checking
powered transportable cutting along shaping machines for
serviceability. Then , managers checks requirements of voltages,
safety cut-offs addition to circuit breakers. Further, they work for
setting machines and equipments in provision to use. They secure and
fix resources and equipments for workings. Next is choosing and
ensuring that safety guards are properly places as per machine
instructions. They also considers accessories for workings together
with machines. At last, implementing maintenance requirements for
equipments and accessories.
Version 1
June 2020
pg. 19
Paraphrase This Document
Need a fresh take? Get an instant paraphrase of this document with our AI Paraphraser

7.4 Describe the needs of other
occupations when moving,
handling, and/or storing
resources.
When moving, handling or storing resources in Mace Group Ltd, other
occupations needs prior information so that their workings of others
are not interrupted. While moving and storing resources, the main
responsibility required is to provide safety to workers that are involved
in performing such type of working. Moreover, other occupations also
needs proper information to move and store resources so that they can
make necessary changes in their activities in order to wok as they were
doing before.
K/503/3402 Installing First Fixing Components in the
Workplace
Ref
No.
Assessment Criteria Candidate Response
(to discuss, describe, explain etc.)
1.4 Describe different types of
information, their source
and how they are interpreted
in relation to:
– drawings,
specifications,
schedules, method
statements, risk
assessments,
manufacturers'
information and
regulations
governing buildings
Different kinds of information, sources as well as the ways they are
interpreted in Mace Group Ltd in relevance to:
Drawing: Drawing shows information types related to what is to be
designed or built in which some will be detailed and some are to be
scale. These are designed before starting of the working and includes
accurate specifications such as space, height, size and others. There
sources are drawings are site offices as they are prepared there itself.
They are implemented by workers and supervisors to build rooms as
per instructions in drawing.
Specifications: It is a type of information about material quality
addition to details of fixing wooden construction work. These are
found at organisational office or at site office. They are implemented
with drawings and proper material quantity for construction workings
in building.
Schedules: Types of information of schedules are capacity schedule,
service schedule and resource schedule. Their sources are site offices.
Schedule related information are implemented by making gates, door
making along with their manholes, ironmongery, finishing to rooms
and many more in defined durations.
Risk assessments: Information types in risk assessment are about
potential risks which many be part of any activity. Site offices are
main source of information of risk assessment. These are implemented
with risk register and giving information to each employee.
Manufacturer's information: The information type are available in
product itself. Their sources are manufacturers and site buildings.
Manufacturer information are implemented through recognising MES
operates in diverse functional areas and explaining the ways in which
wooden products must be handled or used.
Version 1
June 2020
pg. 20
occupations when moving,
handling, and/or storing
resources.
When moving, handling or storing resources in Mace Group Ltd, other
occupations needs prior information so that their workings of others
are not interrupted. While moving and storing resources, the main
responsibility required is to provide safety to workers that are involved
in performing such type of working. Moreover, other occupations also
needs proper information to move and store resources so that they can
make necessary changes in their activities in order to wok as they were
doing before.
K/503/3402 Installing First Fixing Components in the
Workplace
Ref
No.
Assessment Criteria Candidate Response
(to discuss, describe, explain etc.)
1.4 Describe different types of
information, their source
and how they are interpreted
in relation to:
– drawings,
specifications,
schedules, method
statements, risk
assessments,
manufacturers'
information and
regulations
governing buildings
Different kinds of information, sources as well as the ways they are
interpreted in Mace Group Ltd in relevance to:
Drawing: Drawing shows information types related to what is to be
designed or built in which some will be detailed and some are to be
scale. These are designed before starting of the working and includes
accurate specifications such as space, height, size and others. There
sources are drawings are site offices as they are prepared there itself.
They are implemented by workers and supervisors to build rooms as
per instructions in drawing.
Specifications: It is a type of information about material quality
addition to details of fixing wooden construction work. These are
found at organisational office or at site office. They are implemented
with drawings and proper material quantity for construction workings
in building.
Schedules: Types of information of schedules are capacity schedule,
service schedule and resource schedule. Their sources are site offices.
Schedule related information are implemented by making gates, door
making along with their manholes, ironmongery, finishing to rooms
and many more in defined durations.
Risk assessments: Information types in risk assessment are about
potential risks which many be part of any activity. Site offices are
main source of information of risk assessment. These are implemented
with risk register and giving information to each employee.
Manufacturer's information: The information type are available in
product itself. Their sources are manufacturers and site buildings.
Manufacturer information are implemented through recognising MES
operates in diverse functional areas and explaining the ways in which
wooden products must be handled or used.
Version 1
June 2020
pg. 20
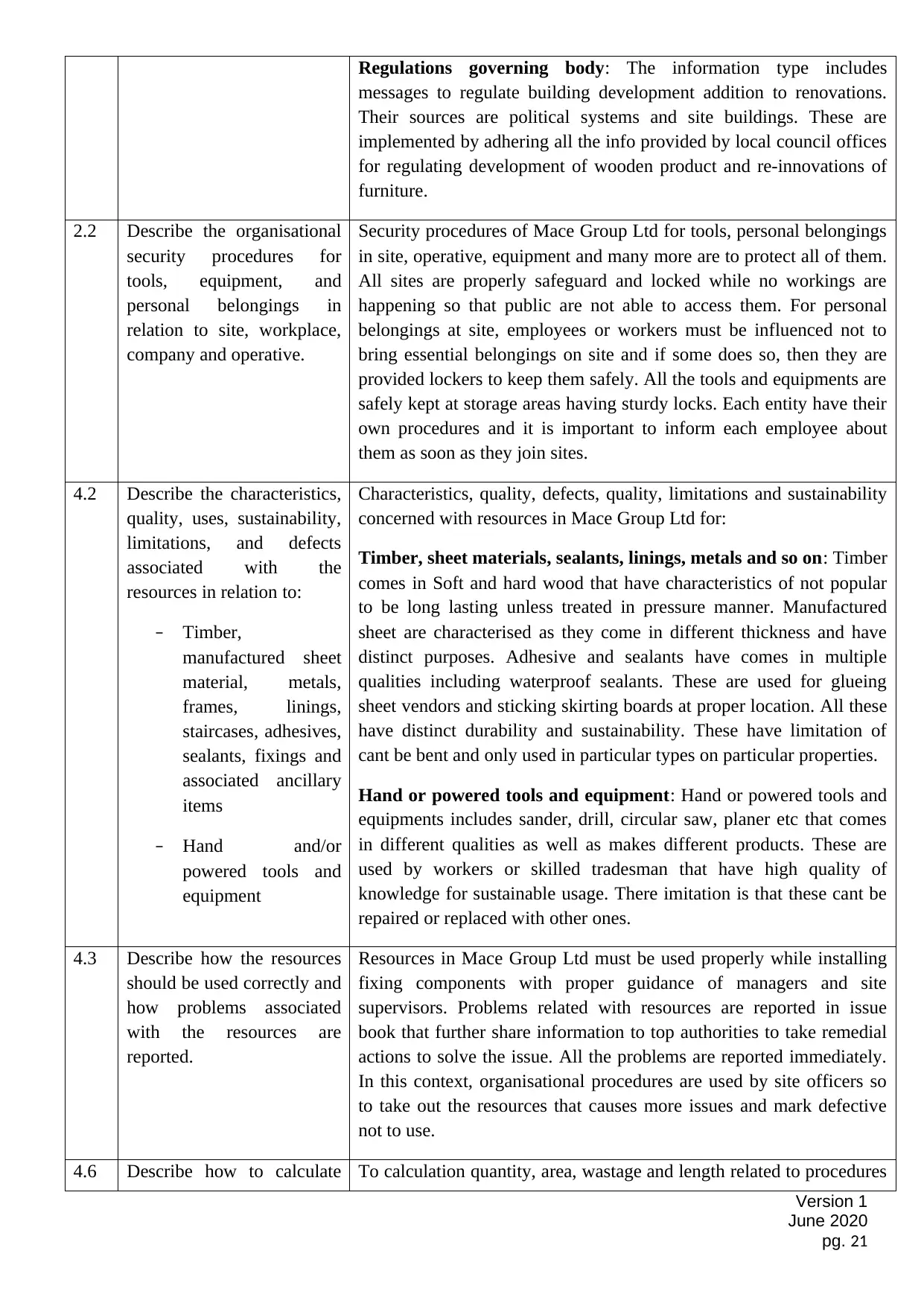
Regulations governing body: The information type includes
messages to regulate building development addition to renovations.
Their sources are political systems and site buildings. These are
implemented by adhering all the info provided by local council offices
for regulating development of wooden product and re-innovations of
furniture.
2.2 Describe the organisational
security procedures for
tools, equipment, and
personal belongings in
relation to site, workplace,
company and operative.
Security procedures of Mace Group Ltd for tools, personal belongings
in site, operative, equipment and many more are to protect all of them.
All sites are properly safeguard and locked while no workings are
happening so that public are not able to access them. For personal
belongings at site, employees or workers must be influenced not to
bring essential belongings on site and if some does so, then they are
provided lockers to keep them safely. All the tools and equipments are
safely kept at storage areas having sturdy locks. Each entity have their
own procedures and it is important to inform each employee about
them as soon as they join sites.
4.2 Describe the characteristics,
quality, uses, sustainability,
limitations, and defects
associated with the
resources in relation to:
– Timber,
manufactured sheet
material, metals,
frames, linings,
staircases, adhesives,
sealants, fixings and
associated ancillary
items
– Hand and/or
powered tools and
equipment
Characteristics, quality, defects, quality, limitations and sustainability
concerned with resources in Mace Group Ltd for:
Timber, sheet materials, sealants, linings, metals and so on: Timber
comes in Soft and hard wood that have characteristics of not popular
to be long lasting unless treated in pressure manner. Manufactured
sheet are characterised as they come in different thickness and have
distinct purposes. Adhesive and sealants have comes in multiple
qualities including waterproof sealants. These are used for glueing
sheet vendors and sticking skirting boards at proper location. All these
have distinct durability and sustainability. These have limitation of
cant be bent and only used in particular types on particular properties.
Hand or powered tools and equipment: Hand or powered tools and
equipments includes sander, drill, circular saw, planer etc that comes
in different qualities as well as makes different products. These are
used by workers or skilled tradesman that have high quality of
knowledge for sustainable usage. There imitation is that these cant be
repaired or replaced with other ones.
4.3 Describe how the resources
should be used correctly and
how problems associated
with the resources are
reported.
Resources in Mace Group Ltd must be used properly while installing
fixing components with proper guidance of managers and site
supervisors. Problems related with resources are reported in issue
book that further share information to top authorities to take remedial
actions to solve the issue. All the problems are reported immediately.
In this context, organisational procedures are used by site officers so
to take out the resources that causes more issues and mark defective
not to use.
4.6 Describe how to calculate To calculation quantity, area, wastage and length related to procedures
Version 1
June 2020
pg. 21
messages to regulate building development addition to renovations.
Their sources are political systems and site buildings. These are
implemented by adhering all the info provided by local council offices
for regulating development of wooden product and re-innovations of
furniture.
2.2 Describe the organisational
security procedures for
tools, equipment, and
personal belongings in
relation to site, workplace,
company and operative.
Security procedures of Mace Group Ltd for tools, personal belongings
in site, operative, equipment and many more are to protect all of them.
All sites are properly safeguard and locked while no workings are
happening so that public are not able to access them. For personal
belongings at site, employees or workers must be influenced not to
bring essential belongings on site and if some does so, then they are
provided lockers to keep them safely. All the tools and equipments are
safely kept at storage areas having sturdy locks. Each entity have their
own procedures and it is important to inform each employee about
them as soon as they join sites.
4.2 Describe the characteristics,
quality, uses, sustainability,
limitations, and defects
associated with the
resources in relation to:
– Timber,
manufactured sheet
material, metals,
frames, linings,
staircases, adhesives,
sealants, fixings and
associated ancillary
items
– Hand and/or
powered tools and
equipment
Characteristics, quality, defects, quality, limitations and sustainability
concerned with resources in Mace Group Ltd for:
Timber, sheet materials, sealants, linings, metals and so on: Timber
comes in Soft and hard wood that have characteristics of not popular
to be long lasting unless treated in pressure manner. Manufactured
sheet are characterised as they come in different thickness and have
distinct purposes. Adhesive and sealants have comes in multiple
qualities including waterproof sealants. These are used for glueing
sheet vendors and sticking skirting boards at proper location. All these
have distinct durability and sustainability. These have limitation of
cant be bent and only used in particular types on particular properties.
Hand or powered tools and equipment: Hand or powered tools and
equipments includes sander, drill, circular saw, planer etc that comes
in different qualities as well as makes different products. These are
used by workers or skilled tradesman that have high quality of
knowledge for sustainable usage. There imitation is that these cant be
repaired or replaced with other ones.
4.3 Describe how the resources
should be used correctly and
how problems associated
with the resources are
reported.
Resources in Mace Group Ltd must be used properly while installing
fixing components with proper guidance of managers and site
supervisors. Problems related with resources are reported in issue
book that further share information to top authorities to take remedial
actions to solve the issue. All the problems are reported immediately.
In this context, organisational procedures are used by site officers so
to take out the resources that causes more issues and mark defective
not to use.
4.6 Describe how to calculate To calculation quantity, area, wastage and length related to procedures
Version 1
June 2020
pg. 21
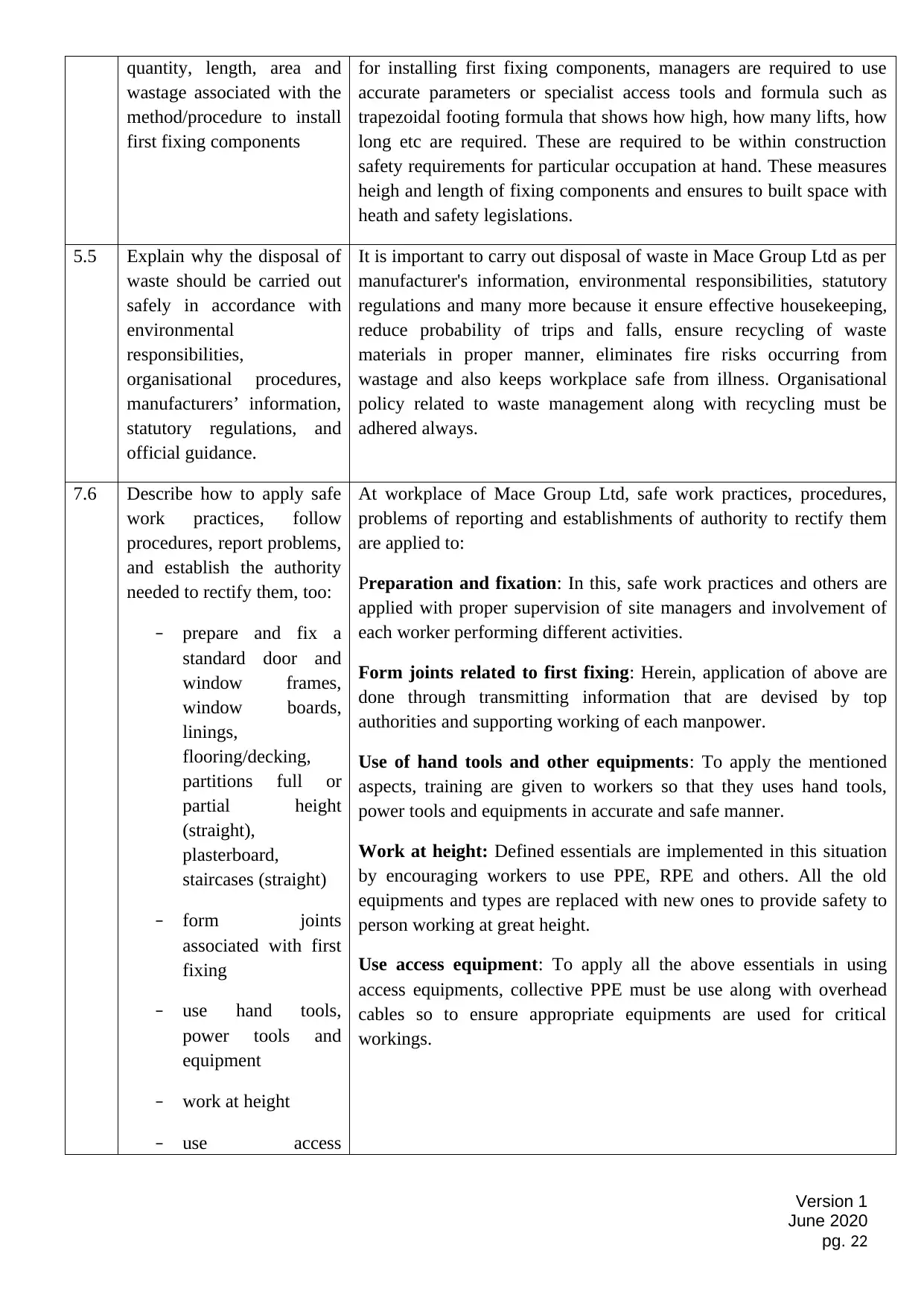
quantity, length, area and
wastage associated with the
method/procedure to install
first fixing components
for installing first fixing components, managers are required to use
accurate parameters or specialist access tools and formula such as
trapezoidal footing formula that shows how high, how many lifts, how
long etc are required. These are required to be within construction
safety requirements for particular occupation at hand. These measures
heigh and length of fixing components and ensures to built space with
heath and safety legislations.
5.5 Explain why the disposal of
waste should be carried out
safely in accordance with
environmental
responsibilities,
organisational procedures,
manufacturers’ information,
statutory regulations, and
official guidance.
It is important to carry out disposal of waste in Mace Group Ltd as per
manufacturer's information, environmental responsibilities, statutory
regulations and many more because it ensure effective housekeeping,
reduce probability of trips and falls, ensure recycling of waste
materials in proper manner, eliminates fire risks occurring from
wastage and also keeps workplace safe from illness. Organisational
policy related to waste management along with recycling must be
adhered always.
7.6 Describe how to apply safe
work practices, follow
procedures, report problems,
and establish the authority
needed to rectify them, too:
– prepare and fix a
standard door and
window frames,
window boards,
linings,
flooring/decking,
partitions full or
partial height
(straight),
plasterboard,
staircases (straight)
– form joints
associated with first
fixing
– use hand tools,
power tools and
equipment
– work at height
– use access
At workplace of Mace Group Ltd, safe work practices, procedures,
problems of reporting and establishments of authority to rectify them
are applied to:
Preparation and fixation: In this, safe work practices and others are
applied with proper supervision of site managers and involvement of
each worker performing different activities.
Form joints related to first fixing: Herein, application of above are
done through transmitting information that are devised by top
authorities and supporting working of each manpower.
Use of hand tools and other equipments: To apply the mentioned
aspects, training are given to workers so that they uses hand tools,
power tools and equipments in accurate and safe manner.
Work at height: Defined essentials are implemented in this situation
by encouraging workers to use PPE, RPE and others. All the old
equipments and types are replaced with new ones to provide safety to
person working at great height.
Use access equipment: To apply all the above essentials in using
access equipments, collective PPE must be use along with overhead
cables so to ensure appropriate equipments are used for critical
workings.
Version 1
June 2020
pg. 22
wastage associated with the
method/procedure to install
first fixing components
for installing first fixing components, managers are required to use
accurate parameters or specialist access tools and formula such as
trapezoidal footing formula that shows how high, how many lifts, how
long etc are required. These are required to be within construction
safety requirements for particular occupation at hand. These measures
heigh and length of fixing components and ensures to built space with
heath and safety legislations.
5.5 Explain why the disposal of
waste should be carried out
safely in accordance with
environmental
responsibilities,
organisational procedures,
manufacturers’ information,
statutory regulations, and
official guidance.
It is important to carry out disposal of waste in Mace Group Ltd as per
manufacturer's information, environmental responsibilities, statutory
regulations and many more because it ensure effective housekeeping,
reduce probability of trips and falls, ensure recycling of waste
materials in proper manner, eliminates fire risks occurring from
wastage and also keeps workplace safe from illness. Organisational
policy related to waste management along with recycling must be
adhered always.
7.6 Describe how to apply safe
work practices, follow
procedures, report problems,
and establish the authority
needed to rectify them, too:
– prepare and fix a
standard door and
window frames,
window boards,
linings,
flooring/decking,
partitions full or
partial height
(straight),
plasterboard,
staircases (straight)
– form joints
associated with first
fixing
– use hand tools,
power tools and
equipment
– work at height
– use access
At workplace of Mace Group Ltd, safe work practices, procedures,
problems of reporting and establishments of authority to rectify them
are applied to:
Preparation and fixation: In this, safe work practices and others are
applied with proper supervision of site managers and involvement of
each worker performing different activities.
Form joints related to first fixing: Herein, application of above are
done through transmitting information that are devised by top
authorities and supporting working of each manpower.
Use of hand tools and other equipments: To apply the mentioned
aspects, training are given to workers so that they uses hand tools,
power tools and equipments in accurate and safe manner.
Work at height: Defined essentials are implemented in this situation
by encouraging workers to use PPE, RPE and others. All the old
equipments and types are replaced with new ones to provide safety to
person working at great height.
Use access equipment: To apply all the above essentials in using
access equipments, collective PPE must be use along with overhead
cables so to ensure appropriate equipments are used for critical
workings.
Version 1
June 2020
pg. 22
Secure Best Marks with AI Grader
Need help grading? Try our AI Grader for instant feedback on your assignments.
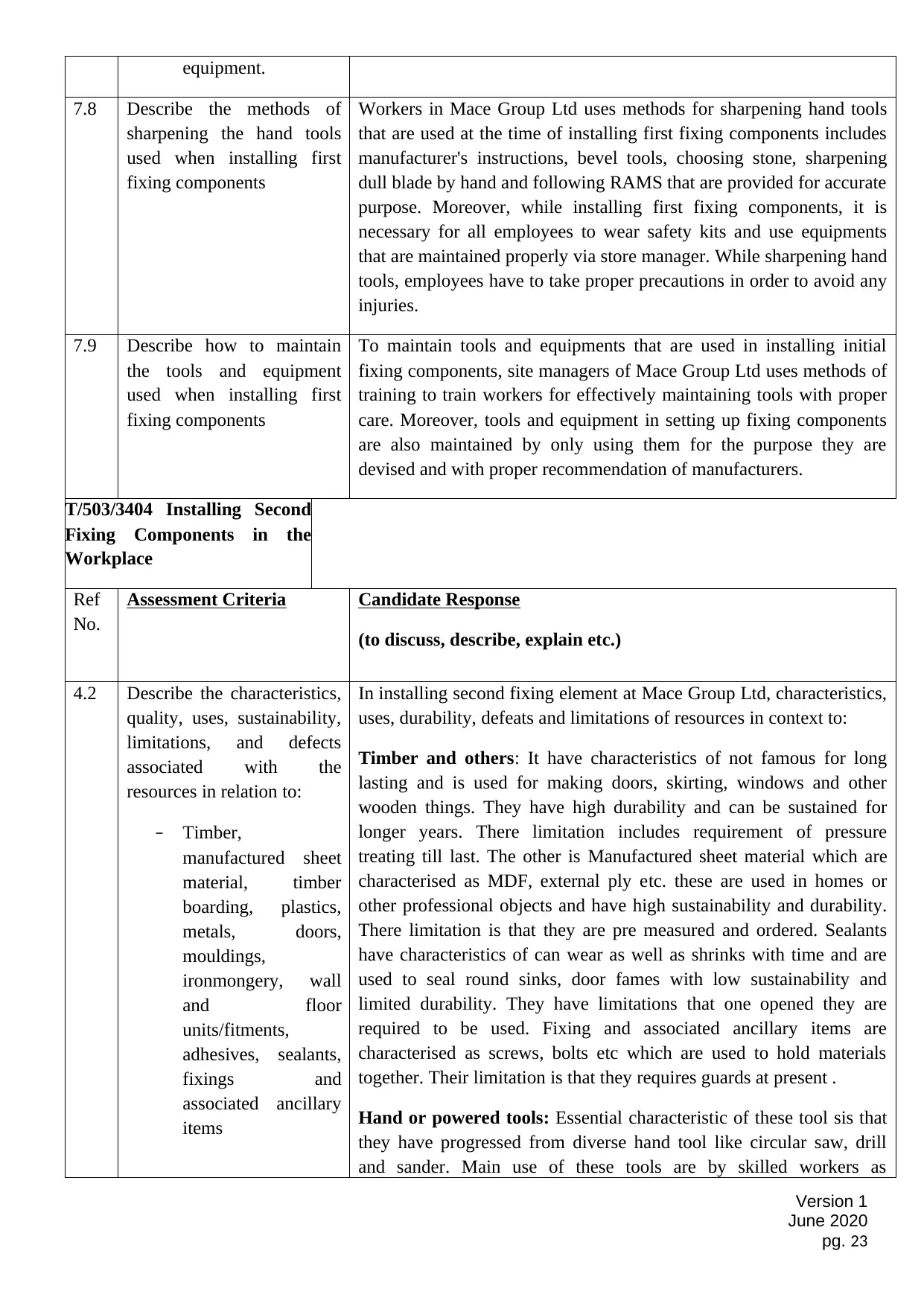
equipment.
7.8 Describe the methods of
sharpening the hand tools
used when installing first
fixing components
Workers in Mace Group Ltd uses methods for sharpening hand tools
that are used at the time of installing first fixing components includes
manufacturer's instructions, bevel tools, choosing stone, sharpening
dull blade by hand and following RAMS that are provided for accurate
purpose. Moreover, while installing first fixing components, it is
necessary for all employees to wear safety kits and use equipments
that are maintained properly via store manager. While sharpening hand
tools, employees have to take proper precautions in order to avoid any
injuries.
7.9 Describe how to maintain
the tools and equipment
used when installing first
fixing components
To maintain tools and equipments that are used in installing initial
fixing components, site managers of Mace Group Ltd uses methods of
training to train workers for effectively maintaining tools with proper
care. Moreover, tools and equipment in setting up fixing components
are also maintained by only using them for the purpose they are
devised and with proper recommendation of manufacturers.
T/503/3404 Installing Second
Fixing Components in the
Workplace
Ref
No.
Assessment Criteria Candidate Response
(to discuss, describe, explain etc.)
4.2 Describe the characteristics,
quality, uses, sustainability,
limitations, and defects
associated with the
resources in relation to:
– Timber,
manufactured sheet
material, timber
boarding, plastics,
metals, doors,
mouldings,
ironmongery, wall
and floor
units/fitments,
adhesives, sealants,
fixings and
associated ancillary
items
In installing second fixing element at Mace Group Ltd, characteristics,
uses, durability, defeats and limitations of resources in context to:
Timber and others: It have characteristics of not famous for long
lasting and is used for making doors, skirting, windows and other
wooden things. They have high durability and can be sustained for
longer years. There limitation includes requirement of pressure
treating till last. The other is Manufactured sheet material which are
characterised as MDF, external ply etc. these are used in homes or
other professional objects and have high sustainability and durability.
There limitation is that they are pre measured and ordered. Sealants
have characteristics of can wear as well as shrinks with time and are
used to seal round sinks, door fames with low sustainability and
limited durability. They have limitations that one opened they are
required to be used. Fixing and associated ancillary items are
characterised as screws, bolts etc which are used to hold materials
together. Their limitation is that they requires guards at present .
Hand or powered tools: Essential characteristic of these tool sis that
they have progressed from diverse hand tool like circular saw, drill
and sander. Main use of these tools are by skilled workers as
Version 1
June 2020
pg. 23
7.8 Describe the methods of
sharpening the hand tools
used when installing first
fixing components
Workers in Mace Group Ltd uses methods for sharpening hand tools
that are used at the time of installing first fixing components includes
manufacturer's instructions, bevel tools, choosing stone, sharpening
dull blade by hand and following RAMS that are provided for accurate
purpose. Moreover, while installing first fixing components, it is
necessary for all employees to wear safety kits and use equipments
that are maintained properly via store manager. While sharpening hand
tools, employees have to take proper precautions in order to avoid any
injuries.
7.9 Describe how to maintain
the tools and equipment
used when installing first
fixing components
To maintain tools and equipments that are used in installing initial
fixing components, site managers of Mace Group Ltd uses methods of
training to train workers for effectively maintaining tools with proper
care. Moreover, tools and equipment in setting up fixing components
are also maintained by only using them for the purpose they are
devised and with proper recommendation of manufacturers.
T/503/3404 Installing Second
Fixing Components in the
Workplace
Ref
No.
Assessment Criteria Candidate Response
(to discuss, describe, explain etc.)
4.2 Describe the characteristics,
quality, uses, sustainability,
limitations, and defects
associated with the
resources in relation to:
– Timber,
manufactured sheet
material, timber
boarding, plastics,
metals, doors,
mouldings,
ironmongery, wall
and floor
units/fitments,
adhesives, sealants,
fixings and
associated ancillary
items
In installing second fixing element at Mace Group Ltd, characteristics,
uses, durability, defeats and limitations of resources in context to:
Timber and others: It have characteristics of not famous for long
lasting and is used for making doors, skirting, windows and other
wooden things. They have high durability and can be sustained for
longer years. There limitation includes requirement of pressure
treating till last. The other is Manufactured sheet material which are
characterised as MDF, external ply etc. these are used in homes or
other professional objects and have high sustainability and durability.
There limitation is that they are pre measured and ordered. Sealants
have characteristics of can wear as well as shrinks with time and are
used to seal round sinks, door fames with low sustainability and
limited durability. They have limitations that one opened they are
required to be used. Fixing and associated ancillary items are
characterised as screws, bolts etc which are used to hold materials
together. Their limitation is that they requires guards at present .
Hand or powered tools: Essential characteristic of these tool sis that
they have progressed from diverse hand tool like circular saw, drill
and sander. Main use of these tools are by skilled workers as
Version 1
June 2020
pg. 23
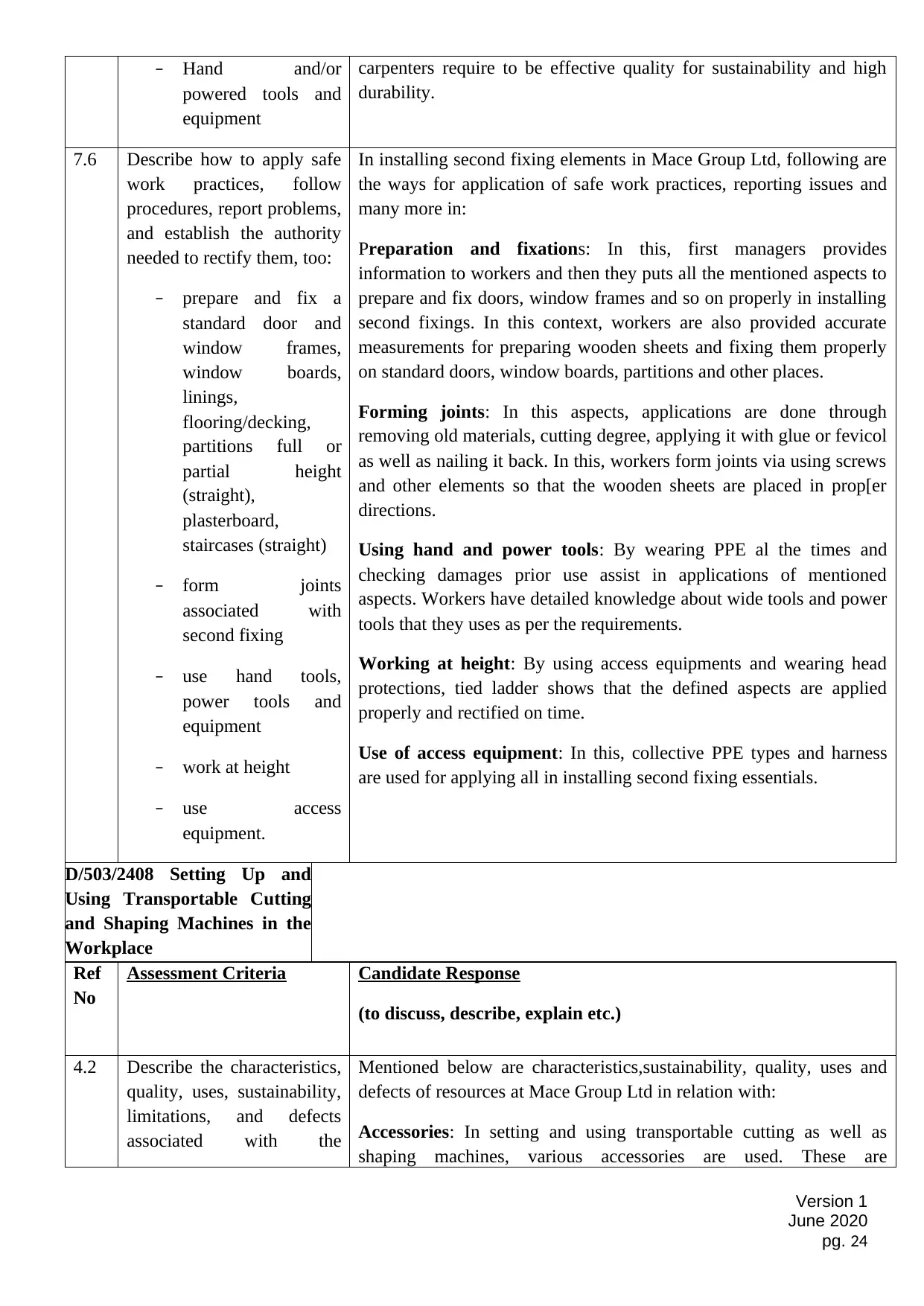
– Hand and/or
powered tools and
equipment
carpenters require to be effective quality for sustainability and high
durability.
7.6 Describe how to apply safe
work practices, follow
procedures, report problems,
and establish the authority
needed to rectify them, too:
– prepare and fix a
standard door and
window frames,
window boards,
linings,
flooring/decking,
partitions full or
partial height
(straight),
plasterboard,
staircases (straight)
– form joints
associated with
second fixing
– use hand tools,
power tools and
equipment
– work at height
– use access
equipment.
In installing second fixing elements in Mace Group Ltd, following are
the ways for application of safe work practices, reporting issues and
many more in:
Preparation and fixations: In this, first managers provides
information to workers and then they puts all the mentioned aspects to
prepare and fix doors, window frames and so on properly in installing
second fixings. In this context, workers are also provided accurate
measurements for preparing wooden sheets and fixing them properly
on standard doors, window boards, partitions and other places.
Forming joints: In this aspects, applications are done through
removing old materials, cutting degree, applying it with glue or fevicol
as well as nailing it back. In this, workers form joints via using screws
and other elements so that the wooden sheets are placed in prop[er
directions.
Using hand and power tools: By wearing PPE al the times and
checking damages prior use assist in applications of mentioned
aspects. Workers have detailed knowledge about wide tools and power
tools that they uses as per the requirements.
Working at height: By using access equipments and wearing head
protections, tied ladder shows that the defined aspects are applied
properly and rectified on time.
Use of access equipment: In this, collective PPE types and harness
are used for applying all in installing second fixing essentials.
D/503/2408 Setting Up and
Using Transportable Cutting
and Shaping Machines in the
Workplace
Ref
No
Assessment Criteria Candidate Response
(to discuss, describe, explain etc.)
4.2 Describe the characteristics,
quality, uses, sustainability,
limitations, and defects
associated with the
Mentioned below are characteristics,sustainability, quality, uses and
defects of resources at Mace Group Ltd in relation with:
Accessories: In setting and using transportable cutting as well as
shaping machines, various accessories are used. These are
Version 1
June 2020
pg. 24
powered tools and
equipment
carpenters require to be effective quality for sustainability and high
durability.
7.6 Describe how to apply safe
work practices, follow
procedures, report problems,
and establish the authority
needed to rectify them, too:
– prepare and fix a
standard door and
window frames,
window boards,
linings,
flooring/decking,
partitions full or
partial height
(straight),
plasterboard,
staircases (straight)
– form joints
associated with
second fixing
– use hand tools,
power tools and
equipment
– work at height
– use access
equipment.
In installing second fixing elements in Mace Group Ltd, following are
the ways for application of safe work practices, reporting issues and
many more in:
Preparation and fixations: In this, first managers provides
information to workers and then they puts all the mentioned aspects to
prepare and fix doors, window frames and so on properly in installing
second fixings. In this context, workers are also provided accurate
measurements for preparing wooden sheets and fixing them properly
on standard doors, window boards, partitions and other places.
Forming joints: In this aspects, applications are done through
removing old materials, cutting degree, applying it with glue or fevicol
as well as nailing it back. In this, workers form joints via using screws
and other elements so that the wooden sheets are placed in prop[er
directions.
Using hand and power tools: By wearing PPE al the times and
checking damages prior use assist in applications of mentioned
aspects. Workers have detailed knowledge about wide tools and power
tools that they uses as per the requirements.
Working at height: By using access equipments and wearing head
protections, tied ladder shows that the defined aspects are applied
properly and rectified on time.
Use of access equipment: In this, collective PPE types and harness
are used for applying all in installing second fixing essentials.
D/503/2408 Setting Up and
Using Transportable Cutting
and Shaping Machines in the
Workplace
Ref
No
Assessment Criteria Candidate Response
(to discuss, describe, explain etc.)
4.2 Describe the characteristics,
quality, uses, sustainability,
limitations, and defects
associated with the
Mentioned below are characteristics,sustainability, quality, uses and
defects of resources at Mace Group Ltd in relation with:
Accessories: In setting and using transportable cutting as well as
shaping machines, various accessories are used. These are
Version 1
June 2020
pg. 24
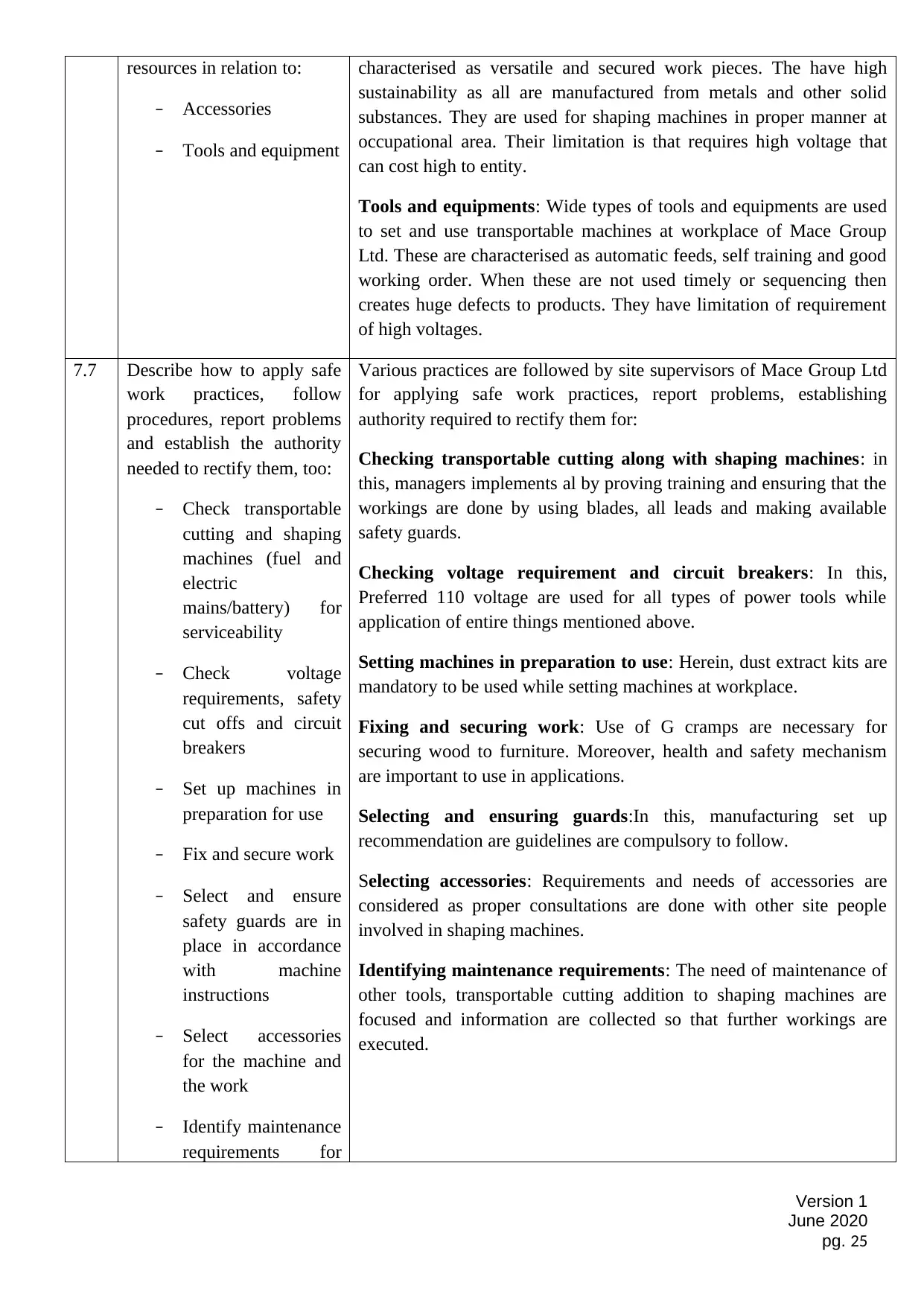
resources in relation to:
– Accessories
– Tools and equipment
characterised as versatile and secured work pieces. The have high
sustainability as all are manufactured from metals and other solid
substances. They are used for shaping machines in proper manner at
occupational area. Their limitation is that requires high voltage that
can cost high to entity.
Tools and equipments: Wide types of tools and equipments are used
to set and use transportable machines at workplace of Mace Group
Ltd. These are characterised as automatic feeds, self training and good
working order. When these are not used timely or sequencing then
creates huge defects to products. They have limitation of requirement
of high voltages.
7.7 Describe how to apply safe
work practices, follow
procedures, report problems
and establish the authority
needed to rectify them, too:
– Check transportable
cutting and shaping
machines (fuel and
electric
mains/battery) for
serviceability
– Check voltage
requirements, safety
cut offs and circuit
breakers
– Set up machines in
preparation for use
– Fix and secure work
– Select and ensure
safety guards are in
place in accordance
with machine
instructions
– Select accessories
for the machine and
the work
– Identify maintenance
requirements for
Various practices are followed by site supervisors of Mace Group Ltd
for applying safe work practices, report problems, establishing
authority required to rectify them for:
Checking transportable cutting along with shaping machines: in
this, managers implements al by proving training and ensuring that the
workings are done by using blades, all leads and making available
safety guards.
Checking voltage requirement and circuit breakers: In this,
Preferred 110 voltage are used for all types of power tools while
application of entire things mentioned above.
Setting machines in preparation to use: Herein, dust extract kits are
mandatory to be used while setting machines at workplace.
Fixing and securing work: Use of G cramps are necessary for
securing wood to furniture. Moreover, health and safety mechanism
are important to use in applications.
Selecting and ensuring guards:In this, manufacturing set up
recommendation are guidelines are compulsory to follow.
Selecting accessories: Requirements and needs of accessories are
considered as proper consultations are done with other site people
involved in shaping machines.
Identifying maintenance requirements: The need of maintenance of
other tools, transportable cutting addition to shaping machines are
focused and information are collected so that further workings are
executed.
Version 1
June 2020
pg. 25
– Accessories
– Tools and equipment
characterised as versatile and secured work pieces. The have high
sustainability as all are manufactured from metals and other solid
substances. They are used for shaping machines in proper manner at
occupational area. Their limitation is that requires high voltage that
can cost high to entity.
Tools and equipments: Wide types of tools and equipments are used
to set and use transportable machines at workplace of Mace Group
Ltd. These are characterised as automatic feeds, self training and good
working order. When these are not used timely or sequencing then
creates huge defects to products. They have limitation of requirement
of high voltages.
7.7 Describe how to apply safe
work practices, follow
procedures, report problems
and establish the authority
needed to rectify them, too:
– Check transportable
cutting and shaping
machines (fuel and
electric
mains/battery) for
serviceability
– Check voltage
requirements, safety
cut offs and circuit
breakers
– Set up machines in
preparation for use
– Fix and secure work
– Select and ensure
safety guards are in
place in accordance
with machine
instructions
– Select accessories
for the machine and
the work
– Identify maintenance
requirements for
Various practices are followed by site supervisors of Mace Group Ltd
for applying safe work practices, report problems, establishing
authority required to rectify them for:
Checking transportable cutting along with shaping machines: in
this, managers implements al by proving training and ensuring that the
workings are done by using blades, all leads and making available
safety guards.
Checking voltage requirement and circuit breakers: In this,
Preferred 110 voltage are used for all types of power tools while
application of entire things mentioned above.
Setting machines in preparation to use: Herein, dust extract kits are
mandatory to be used while setting machines at workplace.
Fixing and securing work: Use of G cramps are necessary for
securing wood to furniture. Moreover, health and safety mechanism
are important to use in applications.
Selecting and ensuring guards:In this, manufacturing set up
recommendation are guidelines are compulsory to follow.
Selecting accessories: Requirements and needs of accessories are
considered as proper consultations are done with other site people
involved in shaping machines.
Identifying maintenance requirements: The need of maintenance of
other tools, transportable cutting addition to shaping machines are
focused and information are collected so that further workings are
executed.
Version 1
June 2020
pg. 25
Paraphrase This Document
Need a fresh take? Get an instant paraphrase of this document with our AI Paraphraser
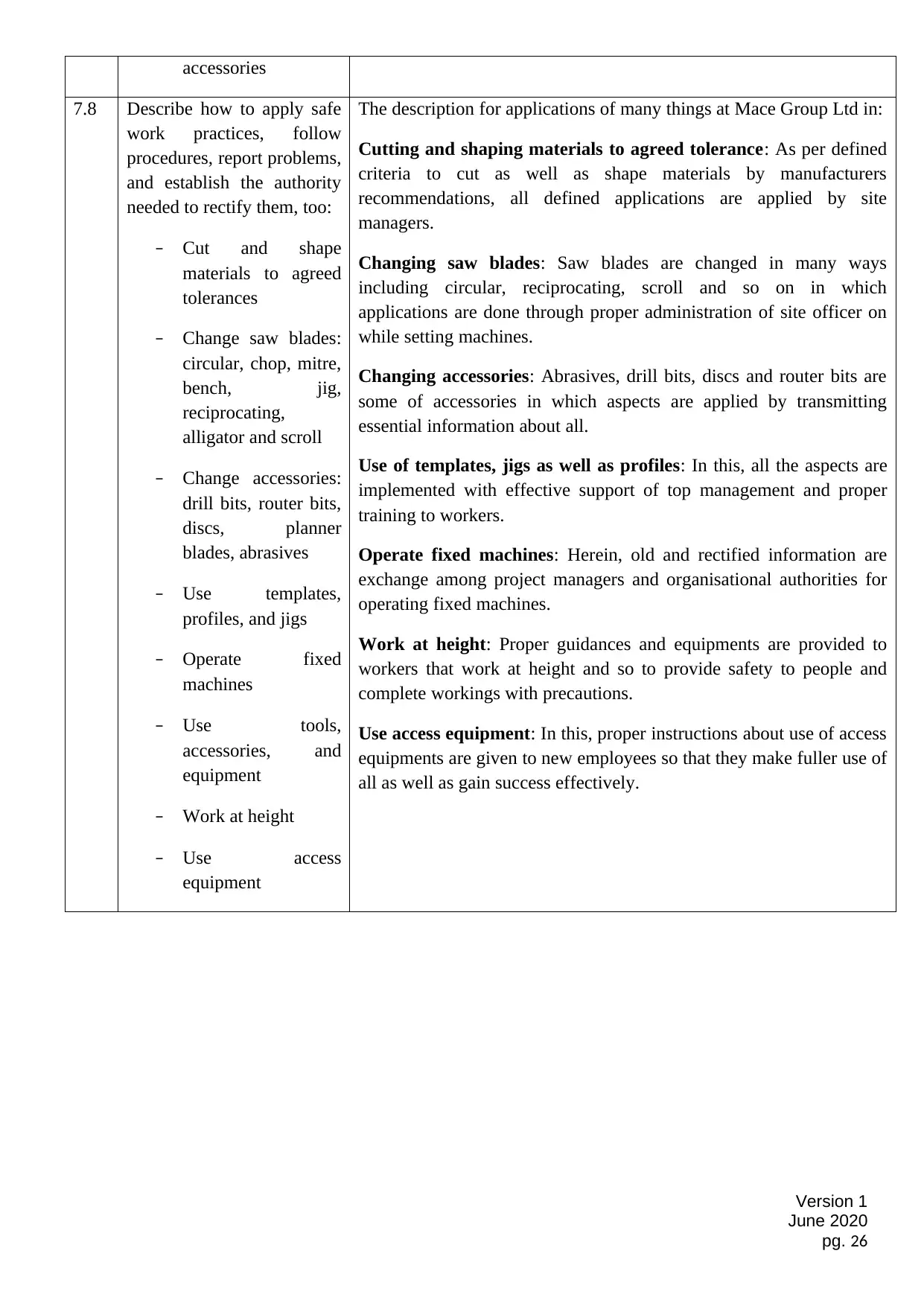
accessories
7.8 Describe how to apply safe
work practices, follow
procedures, report problems,
and establish the authority
needed to rectify them, too:
– Cut and shape
materials to agreed
tolerances
– Change saw blades:
circular, chop, mitre,
bench, jig,
reciprocating,
alligator and scroll
– Change accessories:
drill bits, router bits,
discs, planner
blades, abrasives
– Use templates,
profiles, and jigs
– Operate fixed
machines
– Use tools,
accessories, and
equipment
– Work at height
– Use access
equipment
The description for applications of many things at Mace Group Ltd in:
Cutting and shaping materials to agreed tolerance: As per defined
criteria to cut as well as shape materials by manufacturers
recommendations, all defined applications are applied by site
managers.
Changing saw blades: Saw blades are changed in many ways
including circular, reciprocating, scroll and so on in which
applications are done through proper administration of site officer on
while setting machines.
Changing accessories: Abrasives, drill bits, discs and router bits are
some of accessories in which aspects are applied by transmitting
essential information about all.
Use of templates, jigs as well as profiles: In this, all the aspects are
implemented with effective support of top management and proper
training to workers.
Operate fixed machines: Herein, old and rectified information are
exchange among project managers and organisational authorities for
operating fixed machines.
Work at height: Proper guidances and equipments are provided to
workers that work at height and so to provide safety to people and
complete workings with precautions.
Use access equipment: In this, proper instructions about use of access
equipments are given to new employees so that they make fuller use of
all as well as gain success effectively.
Version 1
June 2020
pg. 26
7.8 Describe how to apply safe
work practices, follow
procedures, report problems,
and establish the authority
needed to rectify them, too:
– Cut and shape
materials to agreed
tolerances
– Change saw blades:
circular, chop, mitre,
bench, jig,
reciprocating,
alligator and scroll
– Change accessories:
drill bits, router bits,
discs, planner
blades, abrasives
– Use templates,
profiles, and jigs
– Operate fixed
machines
– Use tools,
accessories, and
equipment
– Work at height
– Use access
equipment
The description for applications of many things at Mace Group Ltd in:
Cutting and shaping materials to agreed tolerance: As per defined
criteria to cut as well as shape materials by manufacturers
recommendations, all defined applications are applied by site
managers.
Changing saw blades: Saw blades are changed in many ways
including circular, reciprocating, scroll and so on in which
applications are done through proper administration of site officer on
while setting machines.
Changing accessories: Abrasives, drill bits, discs and router bits are
some of accessories in which aspects are applied by transmitting
essential information about all.
Use of templates, jigs as well as profiles: In this, all the aspects are
implemented with effective support of top management and proper
training to workers.
Operate fixed machines: Herein, old and rectified information are
exchange among project managers and organisational authorities for
operating fixed machines.
Work at height: Proper guidances and equipments are provided to
workers that work at height and so to provide safety to people and
complete workings with precautions.
Use access equipment: In this, proper instructions about use of access
equipments are given to new employees so that they make fuller use of
all as well as gain success effectively.
Version 1
June 2020
pg. 26
1 out of 26
Related Documents
![[object Object]](/_next/image/?url=%2F_next%2Fstatic%2Fmedia%2Flogo.6d15ce61.png&w=640&q=75)
Your All-in-One AI-Powered Toolkit for Academic Success.
+13062052269
info@desklib.com
Available 24*7 on WhatsApp / Email
Unlock your academic potential
© 2024 | Zucol Services PVT LTD | All rights reserved.