Workplace Health and Safety Management - Measuring and Evaluating HSW Performance
VerifiedAdded on  2023/06/13
|12
|1589
|233
AI Summary
This report examines the performance of the organization structure and operations after a moderately successful implementation of WHSMS plan taking the example of Pitstop Australia simulated case study. It also suggests actions to ensure compliance to the WHSMS plan and overcome the risks and challenges.
Contribute Materials
Your contribution can guide someone’s learning journey. Share your
documents today.

Running head: WORKPLACE HEALTH AND SAFETY MANAGEMENT
Workplace health and safety management
Name of the Student:
Name of the University:
Author Note:
Workplace health and safety management
Name of the Student:
Name of the University:
Author Note:
Secure Best Marks with AI Grader
Need help grading? Try our AI Grader for instant feedback on your assignments.
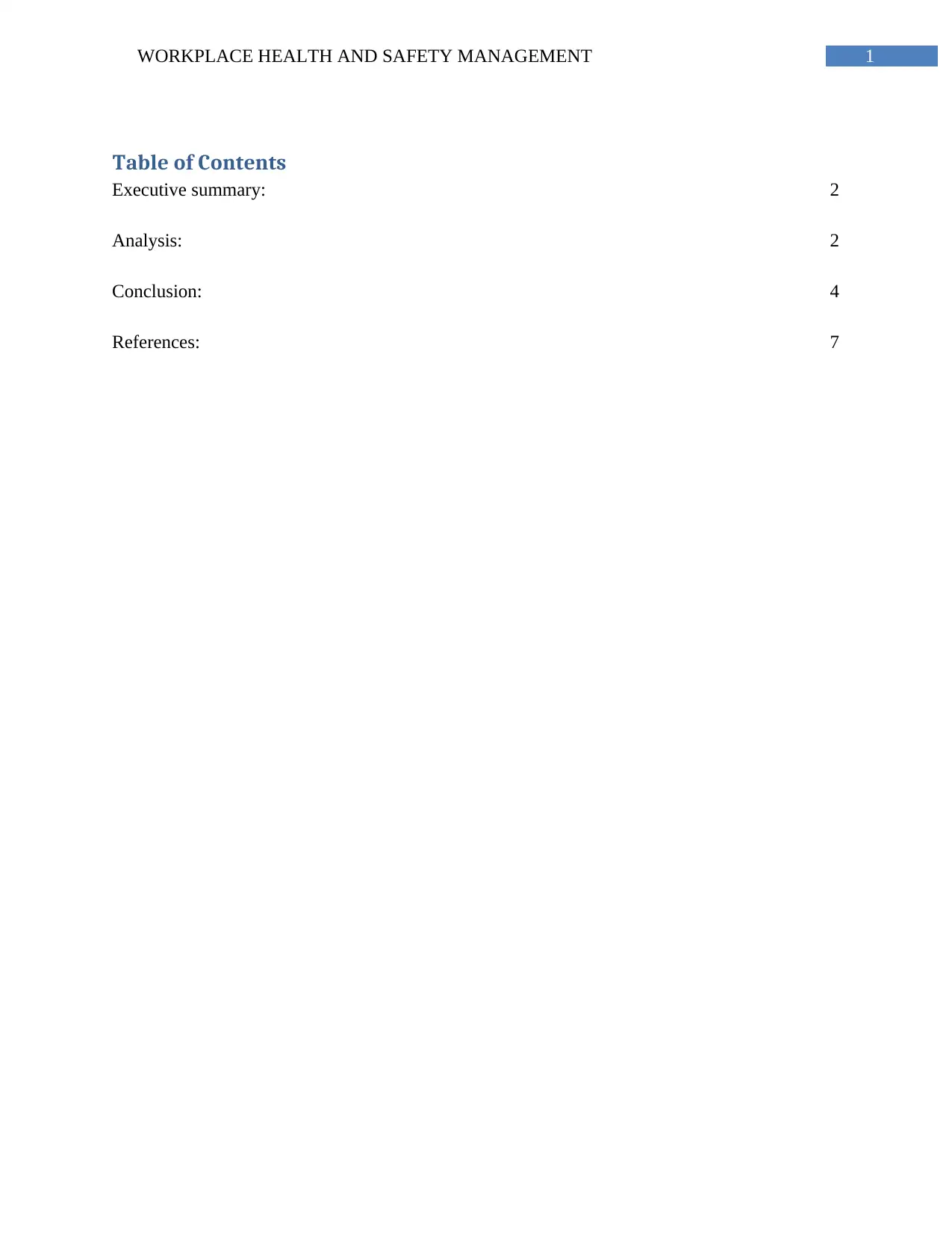
1WORKPLACE HEALTH AND SAFETY MANAGEMENT
Table of Contents
Executive summary: 2
Analysis: 2
Conclusion: 4
References: 7
Table of Contents
Executive summary: 2
Analysis: 2
Conclusion: 4
References: 7
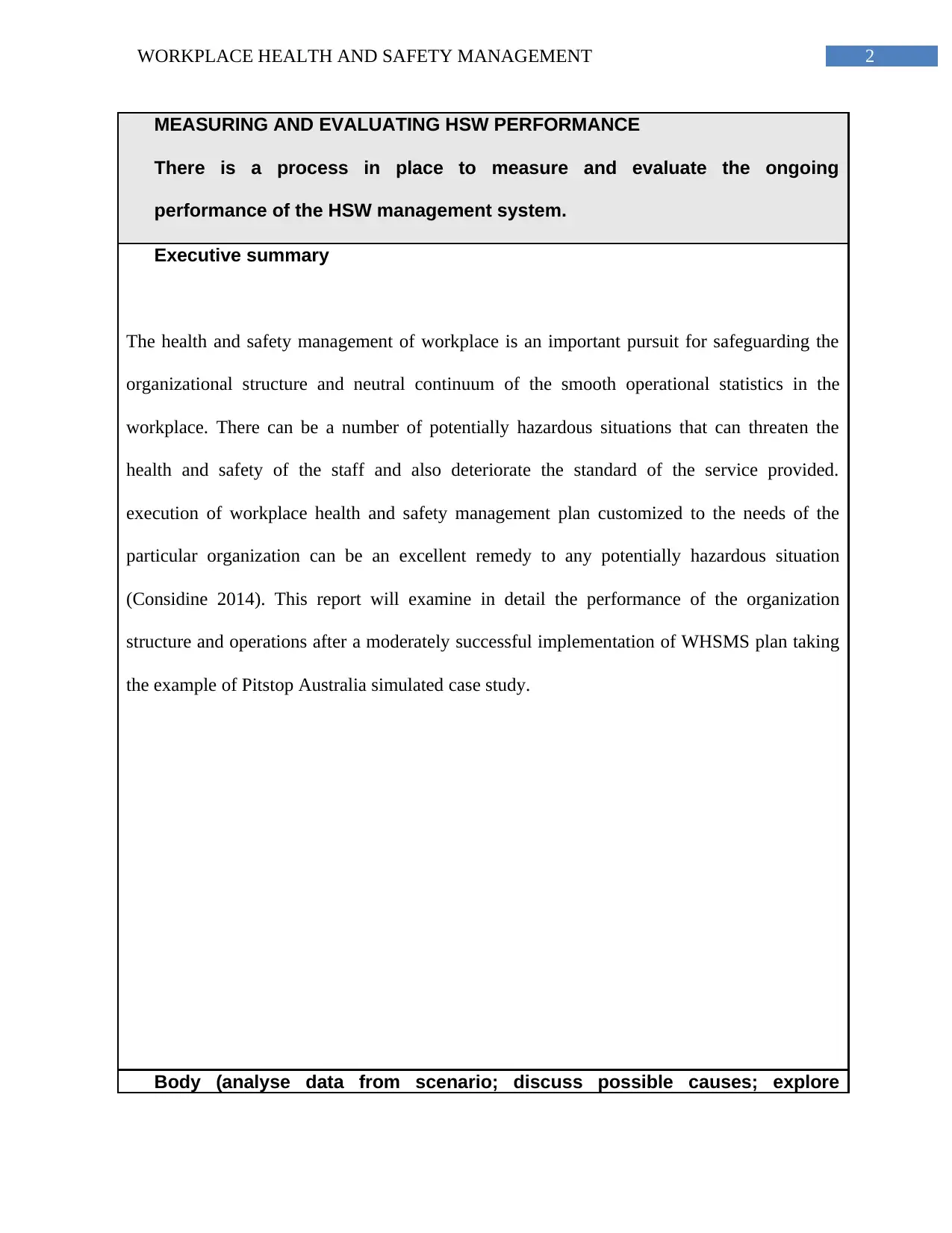
2WORKPLACE HEALTH AND SAFETY MANAGEMENT
MEASURING AND EVALUATING HSW PERFORMANCE
There is a process in place to measure and evaluate the ongoing
performance of the HSW management system.
Executive summary
The health and safety management of workplace is an important pursuit for safeguarding the
organizational structure and neutral continuum of the smooth operational statistics in the
workplace. There can be a number of potentially hazardous situations that can threaten the
health and safety of the staff and also deteriorate the standard of the service provided.
execution of workplace health and safety management plan customized to the needs of the
particular organization can be an excellent remedy to any potentially hazardous situation
(Considine 2014). This report will examine in detail the performance of the organization
structure and operations after a moderately successful implementation of WHSMS plan taking
the example of Pitstop Australia simulated case study.
Body (analyse data from scenario; discuss possible causes; explore
MEASURING AND EVALUATING HSW PERFORMANCE
There is a process in place to measure and evaluate the ongoing
performance of the HSW management system.
Executive summary
The health and safety management of workplace is an important pursuit for safeguarding the
organizational structure and neutral continuum of the smooth operational statistics in the
workplace. There can be a number of potentially hazardous situations that can threaten the
health and safety of the staff and also deteriorate the standard of the service provided.
execution of workplace health and safety management plan customized to the needs of the
particular organization can be an excellent remedy to any potentially hazardous situation
(Considine 2014). This report will examine in detail the performance of the organization
structure and operations after a moderately successful implementation of WHSMS plan taking
the example of Pitstop Australia simulated case study.
Body (analyse data from scenario; discuss possible causes; explore

3WORKPLACE HEALTH AND SAFETY MANAGEMENT
possible solutions;
explain your reasoning and support with evidence).
Pitstop is a fairly big pumping station store in the northern beaches of Sydney with complete
Australian ownership. With the motor vehicle oriented business of the store, there have been
hazards associated with the everyday business operations; the need for an injury management
has been the most important pursuit for this particular case scenario. The major objectives
behind the completion of workplace health and safety management plan in Pitstop Wollongong
had been to minimize the frequency of injuries, reduce the number of days of lost work,
establish risk management scenario, ensure compliance to WHS policy implementation, and
ensure culture of safety in the workplace. The persisting issued with hazard potential with the
business operational characteristics associated with Pitstop enterprise includes issues with the
heat oven, issues with the petrol or LPG pumps, cleaning the forecourt pumps, measurement of
fuel volumes, and restocking (Gerber 2015).
Now it has to be understood that the organization has been expanding with a steady growth
of 20 to 160 employees along the implementation of the workplace health and safety
management system plan. Analysing the advancement of the implementation process in the
Pitstop store it has to be mentioned that the store has grown considerably to opening up 30
stores within the six months of implementation program of the WHSMS, and the plan has
benefitted the organizational management significantly. The initial feedback from the
managerial staff had been positive however the growth of the implementation program of the
WHSMS plan has lost its momentum and the recent data collected indicates at the lost
momentum of the implementation program. For instance, 3 fire instances have been reported
possible solutions;
explain your reasoning and support with evidence).
Pitstop is a fairly big pumping station store in the northern beaches of Sydney with complete
Australian ownership. With the motor vehicle oriented business of the store, there have been
hazards associated with the everyday business operations; the need for an injury management
has been the most important pursuit for this particular case scenario. The major objectives
behind the completion of workplace health and safety management plan in Pitstop Wollongong
had been to minimize the frequency of injuries, reduce the number of days of lost work,
establish risk management scenario, ensure compliance to WHS policy implementation, and
ensure culture of safety in the workplace. The persisting issued with hazard potential with the
business operational characteristics associated with Pitstop enterprise includes issues with the
heat oven, issues with the petrol or LPG pumps, cleaning the forecourt pumps, measurement of
fuel volumes, and restocking (Gerber 2015).
Now it has to be understood that the organization has been expanding with a steady growth
of 20 to 160 employees along the implementation of the workplace health and safety
management system plan. Analysing the advancement of the implementation process in the
Pitstop store it has to be mentioned that the store has grown considerably to opening up 30
stores within the six months of implementation program of the WHSMS, and the plan has
benefitted the organizational management significantly. The initial feedback from the
managerial staff had been positive however the growth of the implementation program of the
WHSMS plan has lost its momentum and the recent data collected indicates at the lost
momentum of the implementation program. For instance, 3 fire instances have been reported
Secure Best Marks with AI Grader
Need help grading? Try our AI Grader for instant feedback on your assignments.

4WORKPLACE HEALTH AND SAFETY MANAGEMENT
for which 1 working day has been lost, floor slips and resultant employee injuries have
persisted as well. Major injuries include 10 incidences of head injuries due to falling stock, 12
lifting injuries, 60 incidences of burn, and 40 breathing troubles reported by the employees. All
these incidents have contributed to a large number of days of lost work, and have been a big
reason behind the lost momentum of the WHSMS implementation plan (Komendantova et al.
2013).
One of the biggest reasons behind the differential success of the implementation program in
different stores, is the varying approach taken by the different store managers to establish risk
management and workplace safety. Employee feedback indicates at the recent lenience in the
store managers to stick to the WHSMS system and introduction of strong solvents without
complying with WHSMS safety procedures (Parker and Handmer 2013). Along with that the
employee feedback has also hinted at the disorganized and careless nature of the training
session has impacted the progress of the plan as well. However some of the stores have regular
managerial sessions based on the WHS issues and concerns of the store and these stores have
had lesser WHS accidents along the course of 6 months. Lastly only 250 weekly safety audits
have been reported out of the 500 expected, hence, one of the biggest reasons behind the lost
impetus of the WHSMS plan is the incompetence and negligence of some of the store
managers to actively comply with the WHSMS guidelines and take adequate actions to ensure
successful implementation of the plan (Martinov-Bennie et al. 2014).
for which 1 working day has been lost, floor slips and resultant employee injuries have
persisted as well. Major injuries include 10 incidences of head injuries due to falling stock, 12
lifting injuries, 60 incidences of burn, and 40 breathing troubles reported by the employees. All
these incidents have contributed to a large number of days of lost work, and have been a big
reason behind the lost momentum of the WHSMS implementation plan (Komendantova et al.
2013).
One of the biggest reasons behind the differential success of the implementation program in
different stores, is the varying approach taken by the different store managers to establish risk
management and workplace safety. Employee feedback indicates at the recent lenience in the
store managers to stick to the WHSMS system and introduction of strong solvents without
complying with WHSMS safety procedures (Parker and Handmer 2013). Along with that the
employee feedback has also hinted at the disorganized and careless nature of the training
session has impacted the progress of the plan as well. However some of the stores have regular
managerial sessions based on the WHS issues and concerns of the store and these stores have
had lesser WHS accidents along the course of 6 months. Lastly only 250 weekly safety audits
have been reported out of the 500 expected, hence, one of the biggest reasons behind the lost
impetus of the WHSMS plan is the incompetence and negligence of some of the store
managers to actively comply with the WHSMS guidelines and take adequate actions to ensure
successful implementation of the plan (Martinov-Bennie et al. 2014).
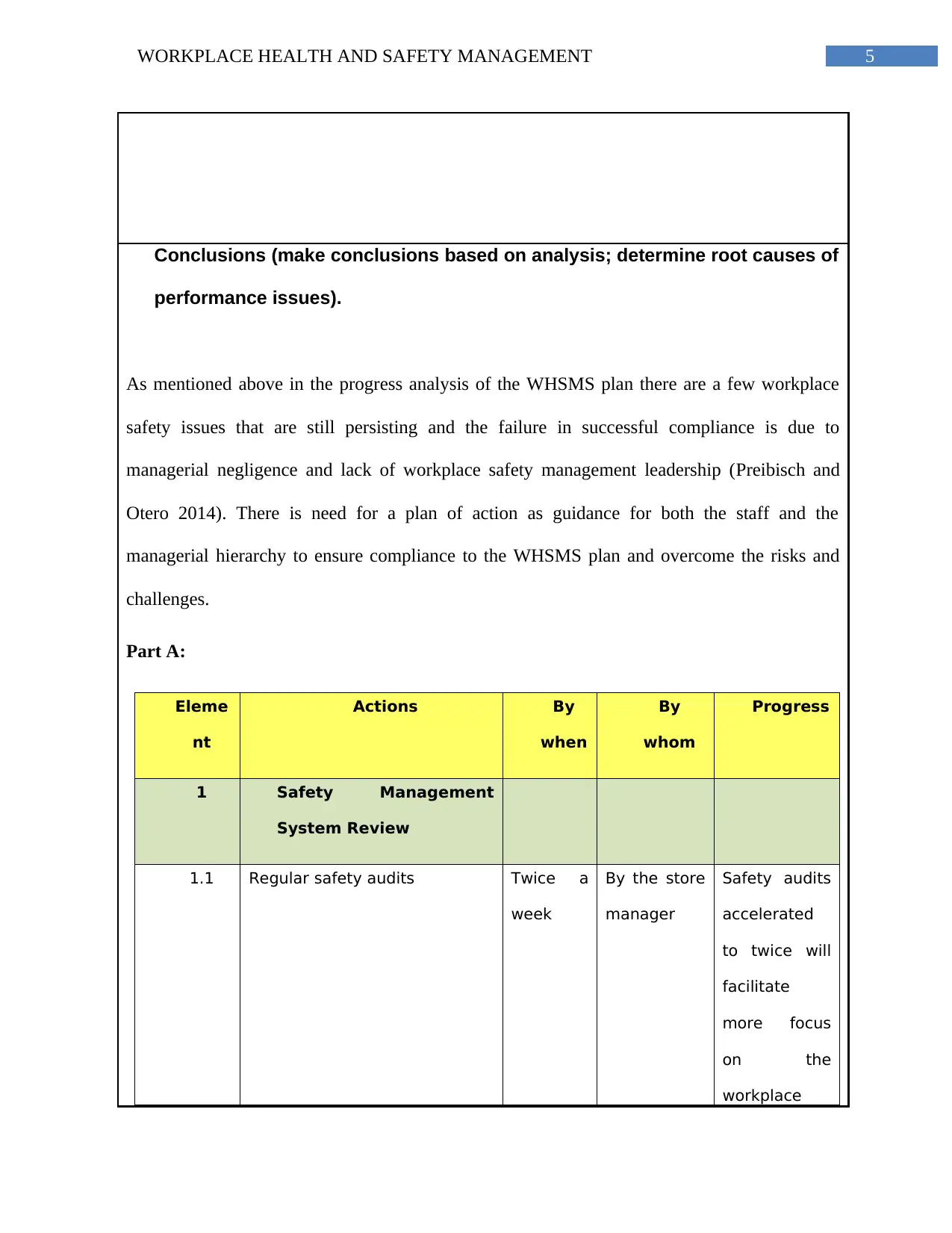
5WORKPLACE HEALTH AND SAFETY MANAGEMENT
Conclusions (make conclusions based on analysis; determine root causes of
performance issues).
As mentioned above in the progress analysis of the WHSMS plan there are a few workplace
safety issues that are still persisting and the failure in successful compliance is due to
managerial negligence and lack of workplace safety management leadership (Preibisch and
Otero 2014). There is need for a plan of action as guidance for both the staff and the
managerial hierarchy to ensure compliance to the WHSMS plan and overcome the risks and
challenges.
Part A:
Eleme
nt
Actions By
when
By
whom
Progress
1 Safety Management
System Review
1.1 Regular safety audits Twice a
week
By the store
manager
Safety audits
accelerated
to twice will
facilitate
more focus
on the
workplace
Conclusions (make conclusions based on analysis; determine root causes of
performance issues).
As mentioned above in the progress analysis of the WHSMS plan there are a few workplace
safety issues that are still persisting and the failure in successful compliance is due to
managerial negligence and lack of workplace safety management leadership (Preibisch and
Otero 2014). There is need for a plan of action as guidance for both the staff and the
managerial hierarchy to ensure compliance to the WHSMS plan and overcome the risks and
challenges.
Part A:
Eleme
nt
Actions By
when
By
whom
Progress
1 Safety Management
System Review
1.1 Regular safety audits Twice a
week
By the store
manager
Safety audits
accelerated
to twice will
facilitate
more focus
on the
workplace
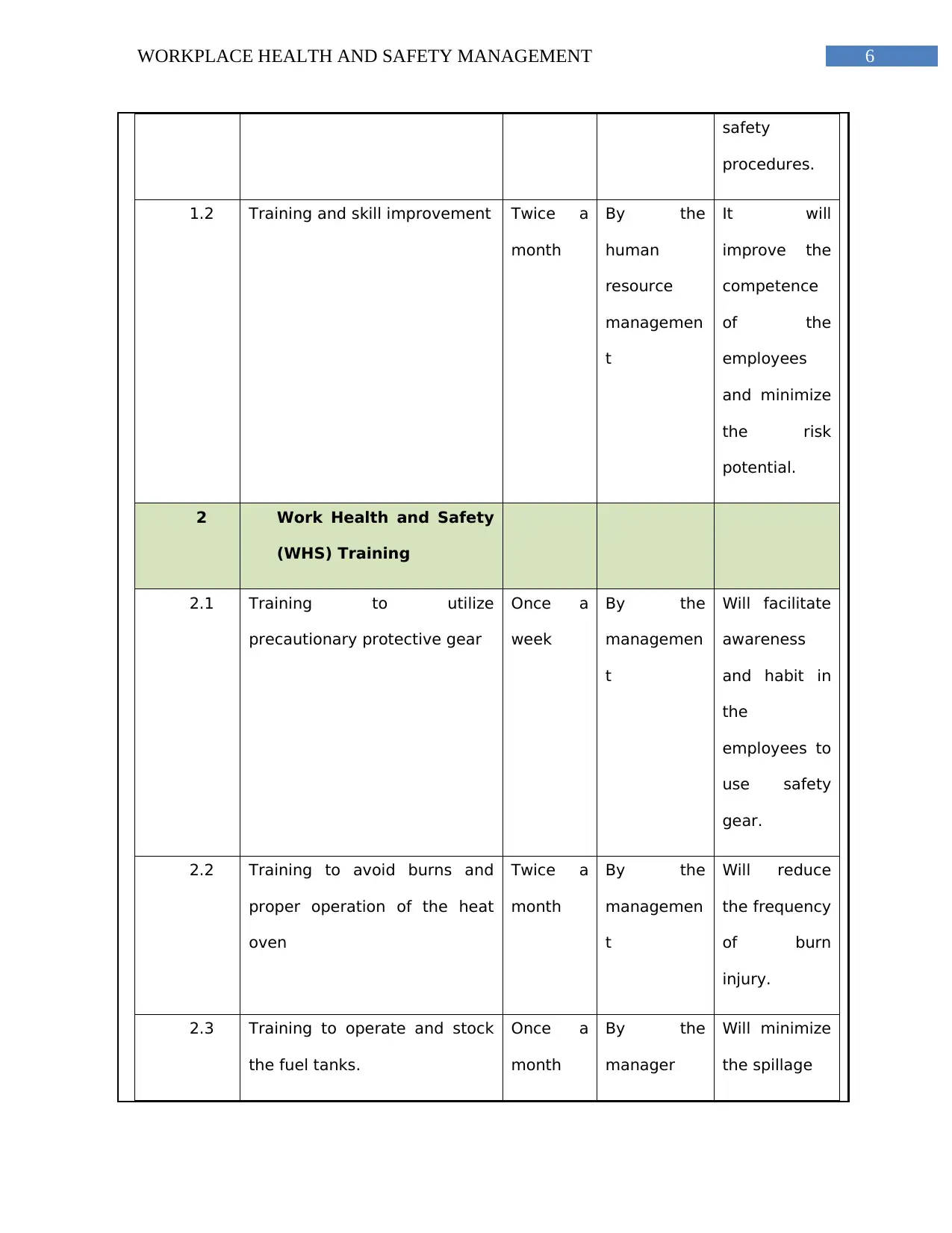
6WORKPLACE HEALTH AND SAFETY MANAGEMENT
safety
procedures.
1.2 Training and skill improvement Twice a
month
By the
human
resource
managemen
t
It will
improve the
competence
of the
employees
and minimize
the risk
potential.
2 Work Health and Safety
(WHS) Training
2.1 Training to utilize
precautionary protective gear
Once a
week
By the
managemen
t
Will facilitate
awareness
and habit in
the
employees to
use safety
gear.
2.2 Training to avoid burns and
proper operation of the heat
oven
Twice a
month
By the
managemen
t
Will reduce
the frequency
of burn
injury.
2.3 Training to operate and stock
the fuel tanks.
Once a
month
By the
manager
Will minimize
the spillage
safety
procedures.
1.2 Training and skill improvement Twice a
month
By the
human
resource
managemen
t
It will
improve the
competence
of the
employees
and minimize
the risk
potential.
2 Work Health and Safety
(WHS) Training
2.1 Training to utilize
precautionary protective gear
Once a
week
By the
managemen
t
Will facilitate
awareness
and habit in
the
employees to
use safety
gear.
2.2 Training to avoid burns and
proper operation of the heat
oven
Twice a
month
By the
managemen
t
Will reduce
the frequency
of burn
injury.
2.3 Training to operate and stock
the fuel tanks.
Once a
month
By the
manager
Will minimize
the spillage
Paraphrase This Document
Need a fresh take? Get an instant paraphrase of this document with our AI Paraphraser

7WORKPLACE HEALTH AND SAFETY MANAGEMENT
3 Incident Notification
3.1 Mandatory documentation
process training
Once a
month
By the
manager
Will train the
employees to
notify any
accident
efficiently
Eleme
nt
Actions By
when
By
whom
Progress
4 Injury Management
4.1 First aid training Once a
week
By the
WHSMS
officer
Will minimize
the possibility
of work loss
during minor
accidents.
4.2 Sharp object and tentative
dangerous element handling
training
Twice a
month
By the
WHSMS
officer
Will minimize
the possibility
of work loss
during minor
accidents.
5 Hazard Management
5.1 Evacuation training Once a
month
By the
WHSMS
officer
Will avoid any
chances of
potential
3 Incident Notification
3.1 Mandatory documentation
process training
Once a
month
By the
manager
Will train the
employees to
notify any
accident
efficiently
Eleme
nt
Actions By
when
By
whom
Progress
4 Injury Management
4.1 First aid training Once a
week
By the
WHSMS
officer
Will minimize
the possibility
of work loss
during minor
accidents.
4.2 Sharp object and tentative
dangerous element handling
training
Twice a
month
By the
WHSMS
officer
Will minimize
the possibility
of work loss
during minor
accidents.
5 Hazard Management
5.1 Evacuation training Once a
month
By the
WHSMS
officer
Will avoid any
chances of
potential

8WORKPLACE HEALTH AND SAFETY MANAGEMENT
hazards
Part B:
Element Actions By
when
By
whom
Progress
1 Implementation of WHSMS checklist
system
At the end
of
everyday
The store
manager
All the staff
will positively
comply with
the
requirements.
2 Rolling out compliance bonus At the end
of each
month
The store
manager
Will encourage
the employees
Part C:
hazards
Part B:
Element Actions By
when
By
whom
Progress
1 Implementation of WHSMS checklist
system
At the end
of
everyday
The store
manager
All the staff
will positively
comply with
the
requirements.
2 Rolling out compliance bonus At the end
of each
month
The store
manager
Will encourage
the employees
Part C:

9WORKPLACE HEALTH AND SAFETY MANAGEMENT
Eleme
nt
Actions By when By
whom
Progress
1 Educating the staff about the
New Work Health and Safety laws
The start of
re-
implementati
on process
The store
manager
The staff will
be
acquainted
with the law.
Eleme
nt
Actions By when By
whom
Progress
1 Educating the staff about the
New Work Health and Safety laws
The start of
re-
implementati
on process
The store
manager
The staff will
be
acquainted
with the law.
Secure Best Marks with AI Grader
Need help grading? Try our AI Grader for instant feedback on your assignments.

10WORKPLACE HEALTH AND SAFETY MANAGEMENT
Part D:
Eleme
nt
Actions By
when
By
whom
Progress
1. WHSMS performance auditing Every
week
The store
manager
will track the
progress of
the store
2 Mandatory penalization for
consistent noncompliance
Every
month
The store
manager
Will propel
the staff to
comply
Part E:
Eleme
nt
Actions By
when
By
whom
Progress
1 Ensuring lost days of work
minimized to 1 per month.
By the
end of
2018
The entire
staff
The lost days
of work will be
minimized
2 Ensuring no heat injuries in the
office
By the
end of
2018
The entire
staff
The injuries
top staff will
be minimum.
Part D:
Eleme
nt
Actions By
when
By
whom
Progress
1. WHSMS performance auditing Every
week
The store
manager
will track the
progress of
the store
2 Mandatory penalization for
consistent noncompliance
Every
month
The store
manager
Will propel
the staff to
comply
Part E:
Eleme
nt
Actions By
when
By
whom
Progress
1 Ensuring lost days of work
minimized to 1 per month.
By the
end of
2018
The entire
staff
The lost days
of work will be
minimized
2 Ensuring no heat injuries in the
office
By the
end of
2018
The entire
staff
The injuries
top staff will
be minimum.
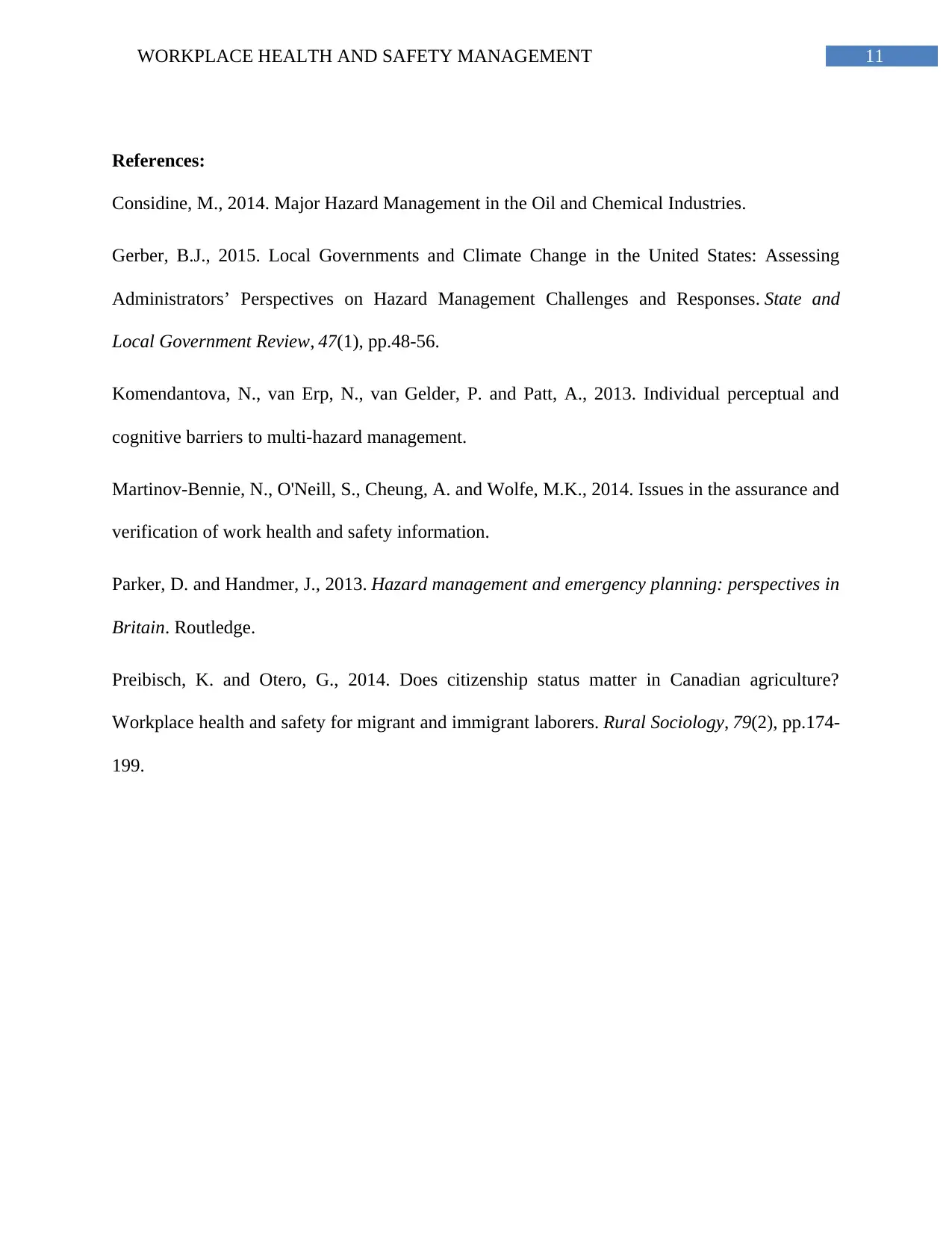
11WORKPLACE HEALTH AND SAFETY MANAGEMENT
References:
Considine, M., 2014. Major Hazard Management in the Oil and Chemical Industries.
Gerber, B.J., 2015. Local Governments and Climate Change in the United States: Assessing
Administrators’ Perspectives on Hazard Management Challenges and Responses. State and
Local Government Review, 47(1), pp.48-56.
Komendantova, N., van Erp, N., van Gelder, P. and Patt, A., 2013. Individual perceptual and
cognitive barriers to multi-hazard management.
Martinov-Bennie, N., O'Neill, S., Cheung, A. and Wolfe, M.K., 2014. Issues in the assurance and
verification of work health and safety information.
Parker, D. and Handmer, J., 2013. Hazard management and emergency planning: perspectives in
Britain. Routledge.
Preibisch, K. and Otero, G., 2014. Does citizenship status matter in Canadian agriculture?
Workplace health and safety for migrant and immigrant laborers. Rural Sociology, 79(2), pp.174-
199.
References:
Considine, M., 2014. Major Hazard Management in the Oil and Chemical Industries.
Gerber, B.J., 2015. Local Governments and Climate Change in the United States: Assessing
Administrators’ Perspectives on Hazard Management Challenges and Responses. State and
Local Government Review, 47(1), pp.48-56.
Komendantova, N., van Erp, N., van Gelder, P. and Patt, A., 2013. Individual perceptual and
cognitive barriers to multi-hazard management.
Martinov-Bennie, N., O'Neill, S., Cheung, A. and Wolfe, M.K., 2014. Issues in the assurance and
verification of work health and safety information.
Parker, D. and Handmer, J., 2013. Hazard management and emergency planning: perspectives in
Britain. Routledge.
Preibisch, K. and Otero, G., 2014. Does citizenship status matter in Canadian agriculture?
Workplace health and safety for migrant and immigrant laborers. Rural Sociology, 79(2), pp.174-
199.
1 out of 12
Related Documents
![[object Object]](/_next/image/?url=%2F_next%2Fstatic%2Fmedia%2Flogo.6d15ce61.png&w=640&q=75)
Your All-in-One AI-Powered Toolkit for Academic Success.
 +13062052269
info@desklib.com
Available 24*7 on WhatsApp / Email
Unlock your academic potential
© 2024  |  Zucol Services PVT LTD  |  All rights reserved.