Operational and Service Management Practices in Aston Martin
VerifiedAdded on 2023/06/12
|11
|3141
|163
AI Summary
This report evaluates the operational and service management practices in Aston Martin, including total quality management, interconnection with supporting functions, and the use of technology. It also discusses the benefits and challenges of these practices.
Contribute Materials
Your contribution can guide someone’s learning journey. Share your
documents today.

BM563 Operations and
Service Management
Service Management
Secure Best Marks with AI Grader
Need help grading? Try our AI Grader for instant feedback on your assignments.

Contents
INTRODUCTION ..........................................................................................................................1
MAIN BODY...................................................................................................................................1
Identification of operational management practice in Aston Martin ..........................................1
Critical evaluation of total quality management practice that influence organisation regarding
efficiency .....................................................................................................................................3
Assessing how technology could be interlinked with operational management practices ........3
Interconnection of supporting functions with total quality management practice and their
assistance on those functions .....................................................................................................5
CONCLUSION ...............................................................................................................................6
REFERENCES................................................................................................................................8
INTRODUCTION ..........................................................................................................................1
MAIN BODY...................................................................................................................................1
Identification of operational management practice in Aston Martin ..........................................1
Critical evaluation of total quality management practice that influence organisation regarding
efficiency .....................................................................................................................................3
Assessing how technology could be interlinked with operational management practices ........3
Interconnection of supporting functions with total quality management practice and their
assistance on those functions .....................................................................................................5
CONCLUSION ...............................................................................................................................6
REFERENCES................................................................................................................................8
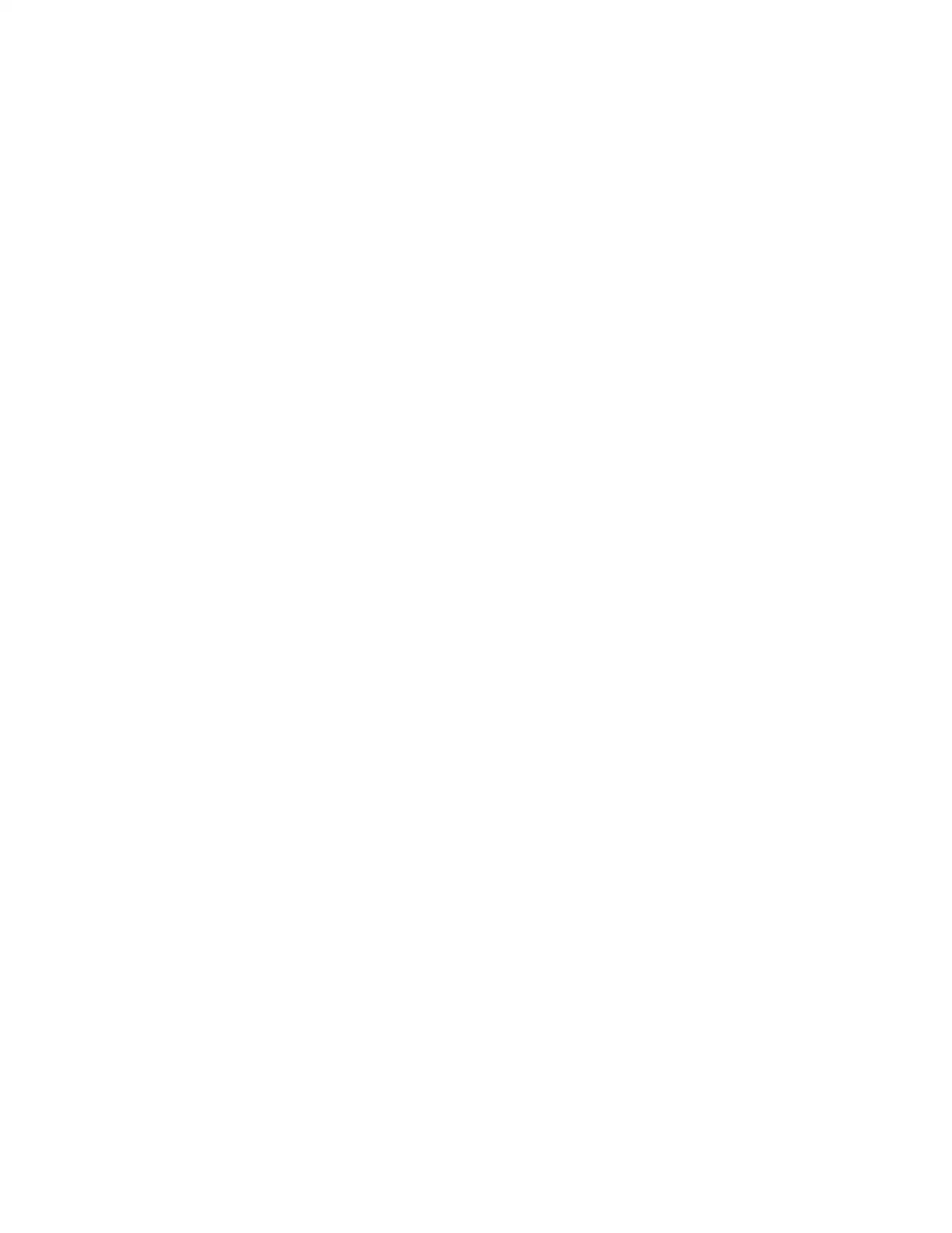
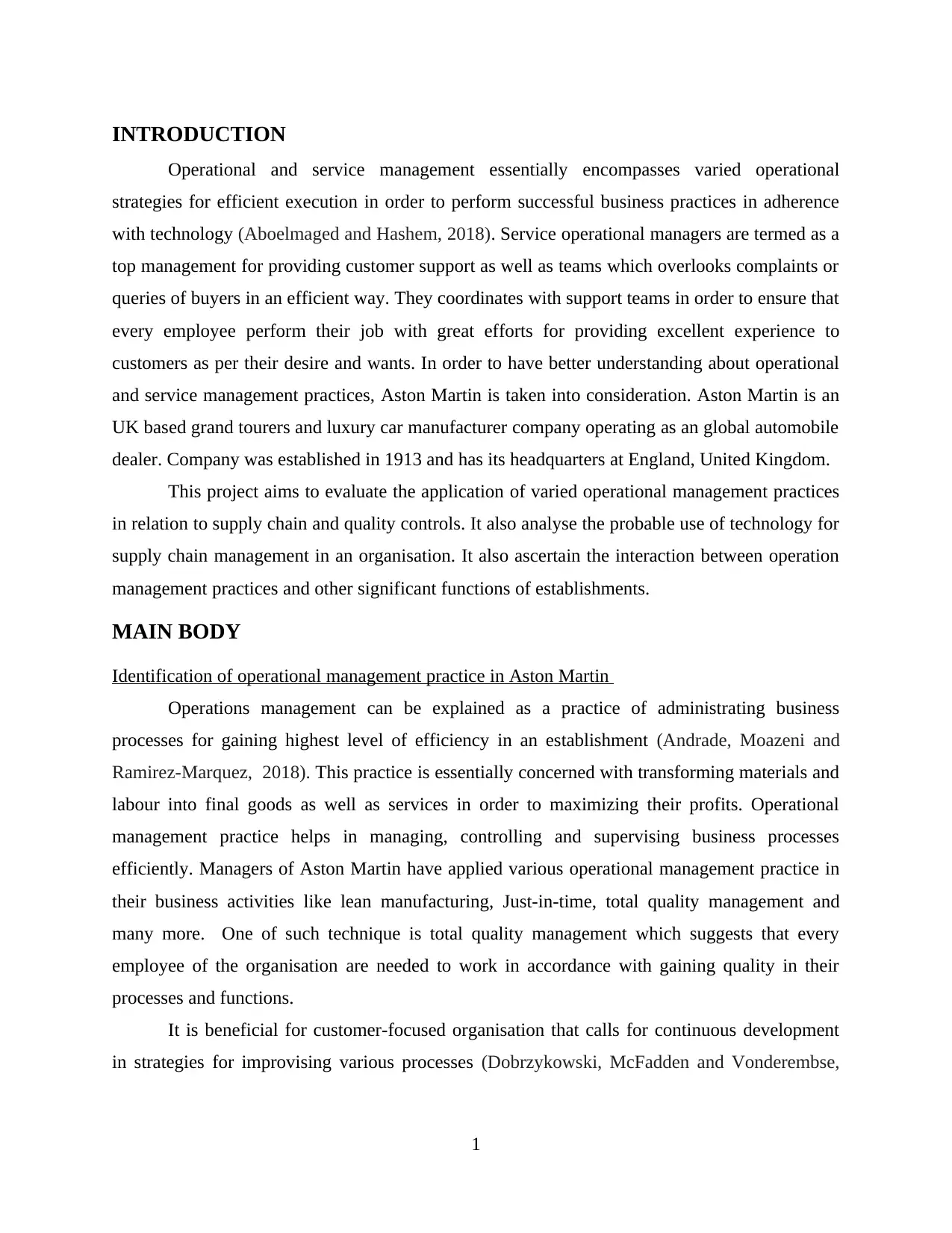
INTRODUCTION
Operational and service management essentially encompasses varied operational
strategies for efficient execution in order to perform successful business practices in adherence
with technology (Aboelmaged and Hashem, 2018). Service operational managers are termed as a
top management for providing customer support as well as teams which overlooks complaints or
queries of buyers in an efficient way. They coordinates with support teams in order to ensure that
every employee perform their job with great efforts for providing excellent experience to
customers as per their desire and wants. In order to have better understanding about operational
and service management practices, Aston Martin is taken into consideration. Aston Martin is an
UK based grand tourers and luxury car manufacturer company operating as an global automobile
dealer. Company was established in 1913 and has its headquarters at England, United Kingdom.
This project aims to evaluate the application of varied operational management practices
in relation to supply chain and quality controls. It also analyse the probable use of technology for
supply chain management in an organisation. It also ascertain the interaction between operation
management practices and other significant functions of establishments.
MAIN BODY
Identification of operational management practice in Aston Martin
Operations management can be explained as a practice of administrating business
processes for gaining highest level of efficiency in an establishment (Andrade, Moazeni and
Ramirez-Marquez, 2018). This practice is essentially concerned with transforming materials and
labour into final goods as well as services in order to maximizing their profits. Operational
management practice helps in managing, controlling and supervising business processes
efficiently. Managers of Aston Martin have applied various operational management practice in
their business activities like lean manufacturing, Just-in-time, total quality management and
many more. One of such technique is total quality management which suggests that every
employee of the organisation are needed to work in accordance with gaining quality in their
processes and functions.
It is beneficial for customer-focused organisation that calls for continuous development
in strategies for improvising various processes (Dobrzykowski, McFadden and Vonderembse,
1
Operational and service management essentially encompasses varied operational
strategies for efficient execution in order to perform successful business practices in adherence
with technology (Aboelmaged and Hashem, 2018). Service operational managers are termed as a
top management for providing customer support as well as teams which overlooks complaints or
queries of buyers in an efficient way. They coordinates with support teams in order to ensure that
every employee perform their job with great efforts for providing excellent experience to
customers as per their desire and wants. In order to have better understanding about operational
and service management practices, Aston Martin is taken into consideration. Aston Martin is an
UK based grand tourers and luxury car manufacturer company operating as an global automobile
dealer. Company was established in 1913 and has its headquarters at England, United Kingdom.
This project aims to evaluate the application of varied operational management practices
in relation to supply chain and quality controls. It also analyse the probable use of technology for
supply chain management in an organisation. It also ascertain the interaction between operation
management practices and other significant functions of establishments.
MAIN BODY
Identification of operational management practice in Aston Martin
Operations management can be explained as a practice of administrating business
processes for gaining highest level of efficiency in an establishment (Andrade, Moazeni and
Ramirez-Marquez, 2018). This practice is essentially concerned with transforming materials and
labour into final goods as well as services in order to maximizing their profits. Operational
management practice helps in managing, controlling and supervising business processes
efficiently. Managers of Aston Martin have applied various operational management practice in
their business activities like lean manufacturing, Just-in-time, total quality management and
many more. One of such technique is total quality management which suggests that every
employee of the organisation are needed to work in accordance with gaining quality in their
processes and functions.
It is beneficial for customer-focused organisation that calls for continuous development
in strategies for improvising various processes (Dobrzykowski, McFadden and Vonderembse,
1
Secure Best Marks with AI Grader
Need help grading? Try our AI Grader for instant feedback on your assignments.

2016). Elements of total quality management practices in accordance with Aston Martin are
discussed below:
Customer-focused practice- Total quality management works on customer-centric
approach where quality is managed and controlled by organisations which is assessed on the
basis of revenue generation reports. Managers of Aston Martin have controlled their operations
for providing quality luxury cars to their customers.
Employee improvement- In order to provide excellent quality to customers, it is
significant for organisations to involve their employees as well as provide them proper training
sessions along with working environment. In context to Aston Martin, managers provide flexible
and safe working environment to their employees as well as workers for maintaining efficiency
of their workforce.
Process-Centred- Total quality management is principally based on building and
maintaining systematic procedures which are ought to be tracked on a continuous basis for
providing quality products to their customers. Managers of Aston Martin track their supply chain
and operations procedures in a systematic manner.
Continuous improvement- A significant aspect of total quality management is the need
of continuous improvement in organisational operations (Kumar and Singh, 2019). In relation to
Aston Martin, managers tries to improve their processes on a continuous basis which help them
to be creative and critical in their approach. They try to make constant improvements in their
process through adoption of artificial intelligence in their processes.
Fact-based decision-making- It is significant for organisations to asses their performance
reports on a continuous basis in order to take critical decisions in an accurate manner. Managers
of Aston Martin ascertain fact-based and critical decision-making process by analysing
performance of their functions and their processes.
Strategic approach- For maintaining quality management, it is imperative for
organisation to achieve mission, vision, objectives and goals in an effective way while
maintaining quality standards in an organisation (Helo and Hao, 2019). In context to Aston
Martin, top management perform strategic planning for maintaining their quality standards in an
effective way. Managers of Aston Martin take their decisions by planning in a strategic manner
which helps them to achieve consensus.
2
discussed below:
Customer-focused practice- Total quality management works on customer-centric
approach where quality is managed and controlled by organisations which is assessed on the
basis of revenue generation reports. Managers of Aston Martin have controlled their operations
for providing quality luxury cars to their customers.
Employee improvement- In order to provide excellent quality to customers, it is
significant for organisations to involve their employees as well as provide them proper training
sessions along with working environment. In context to Aston Martin, managers provide flexible
and safe working environment to their employees as well as workers for maintaining efficiency
of their workforce.
Process-Centred- Total quality management is principally based on building and
maintaining systematic procedures which are ought to be tracked on a continuous basis for
providing quality products to their customers. Managers of Aston Martin track their supply chain
and operations procedures in a systematic manner.
Continuous improvement- A significant aspect of total quality management is the need
of continuous improvement in organisational operations (Kumar and Singh, 2019). In relation to
Aston Martin, managers tries to improve their processes on a continuous basis which help them
to be creative and critical in their approach. They try to make constant improvements in their
process through adoption of artificial intelligence in their processes.
Fact-based decision-making- It is significant for organisations to asses their performance
reports on a continuous basis in order to take critical decisions in an accurate manner. Managers
of Aston Martin ascertain fact-based and critical decision-making process by analysing
performance of their functions and their processes.
Strategic approach- For maintaining quality management, it is imperative for
organisation to achieve mission, vision, objectives and goals in an effective way while
maintaining quality standards in an organisation (Helo and Hao, 2019). In context to Aston
Martin, top management perform strategic planning for maintaining their quality standards in an
effective way. Managers of Aston Martin take their decisions by planning in a strategic manner
which helps them to achieve consensus.
2
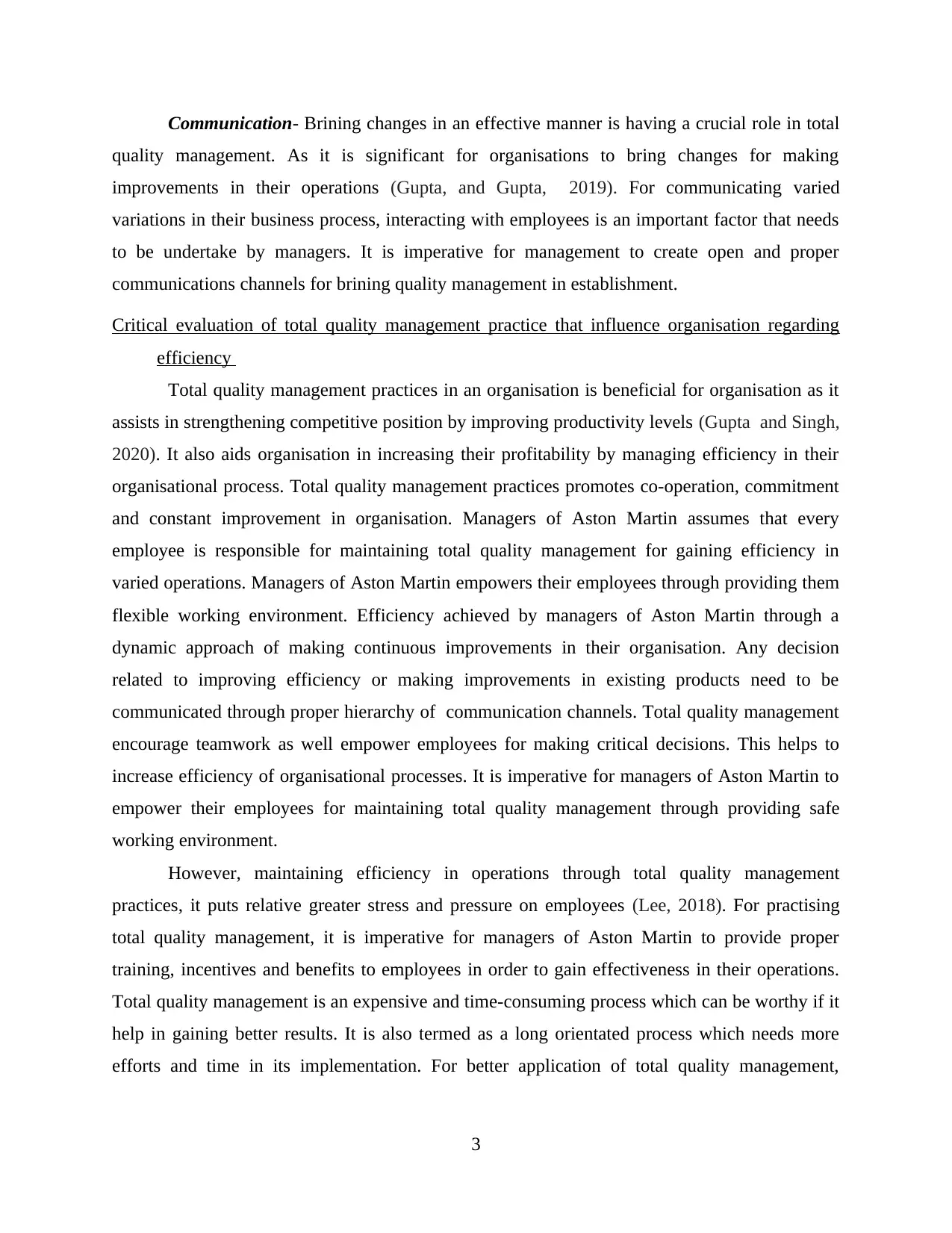
Communication- Brining changes in an effective manner is having a crucial role in total
quality management. As it is significant for organisations to bring changes for making
improvements in their operations (Gupta, and Gupta, 2019). For communicating varied
variations in their business process, interacting with employees is an important factor that needs
to be undertake by managers. It is imperative for management to create open and proper
communications channels for brining quality management in establishment.
Critical evaluation of total quality management practice that influence organisation regarding
efficiency
Total quality management practices in an organisation is beneficial for organisation as it
assists in strengthening competitive position by improving productivity levels (Gupta and Singh,
2020). It also aids organisation in increasing their profitability by managing efficiency in their
organisational process. Total quality management practices promotes co-operation, commitment
and constant improvement in organisation. Managers of Aston Martin assumes that every
employee is responsible for maintaining total quality management for gaining efficiency in
varied operations. Managers of Aston Martin empowers their employees through providing them
flexible working environment. Efficiency achieved by managers of Aston Martin through a
dynamic approach of making continuous improvements in their organisation. Any decision
related to improving efficiency or making improvements in existing products need to be
communicated through proper hierarchy of communication channels. Total quality management
encourage teamwork as well empower employees for making critical decisions. This helps to
increase efficiency of organisational processes. It is imperative for managers of Aston Martin to
empower their employees for maintaining total quality management through providing safe
working environment.
However, maintaining efficiency in operations through total quality management
practices, it puts relative greater stress and pressure on employees (Lee, 2018). For practising
total quality management, it is imperative for managers of Aston Martin to provide proper
training, incentives and benefits to employees in order to gain effectiveness in their operations.
Total quality management is an expensive and time-consuming process which can be worthy if it
help in gaining better results. It is also termed as a long orientated process which needs more
efforts and time in its implementation. For better application of total quality management,
3
quality management. As it is significant for organisations to bring changes for making
improvements in their operations (Gupta, and Gupta, 2019). For communicating varied
variations in their business process, interacting with employees is an important factor that needs
to be undertake by managers. It is imperative for management to create open and proper
communications channels for brining quality management in establishment.
Critical evaluation of total quality management practice that influence organisation regarding
efficiency
Total quality management practices in an organisation is beneficial for organisation as it
assists in strengthening competitive position by improving productivity levels (Gupta and Singh,
2020). It also aids organisation in increasing their profitability by managing efficiency in their
organisational process. Total quality management practices promotes co-operation, commitment
and constant improvement in organisation. Managers of Aston Martin assumes that every
employee is responsible for maintaining total quality management for gaining efficiency in
varied operations. Managers of Aston Martin empowers their employees through providing them
flexible working environment. Efficiency achieved by managers of Aston Martin through a
dynamic approach of making continuous improvements in their organisation. Any decision
related to improving efficiency or making improvements in existing products need to be
communicated through proper hierarchy of communication channels. Total quality management
encourage teamwork as well empower employees for making critical decisions. This helps to
increase efficiency of organisational processes. It is imperative for managers of Aston Martin to
empower their employees for maintaining total quality management through providing safe
working environment.
However, maintaining efficiency in operations through total quality management
practices, it puts relative greater stress and pressure on employees (Lee, 2018). For practising
total quality management, it is imperative for managers of Aston Martin to provide proper
training, incentives and benefits to employees in order to gain effectiveness in their operations.
Total quality management is an expensive and time-consuming process which can be worthy if it
help in gaining better results. It is also termed as a long orientated process which needs more
efforts and time in its implementation. For better application of total quality management,
3

managers of Aston Martin makes continuous improvement in their processes and track their
performance on a constant basis.
Assessing how technology could be interlinked with operational management practices
Automobile industry use varied automated software and techniques for leveraging their
quality standards which is used in tracking, identifying and resolving issues related to products
or services (Lee and Tang 2018). It helps them in enhancing their productivity level. Ii also
assist them in making compliance with standards set with industry. Automated systems and
machine learning assists establishments in making their customers satisfied and retain for a long
period of time. Total quality management is an approach whereby organisational managers
provide proper trainings and empower employees for maintaining and controlling quality
standards. This can be interlinked with artificial intelligence and automated robotics technology
in their operations. Quality can be managed better in an organisation by connecting it to the
information technology. Managers of Aston Martin can use automated robotics system in their
approach which help them to gain efficiency in their assembly line. It also helps in lowering the
burden of workers. This are the expensive techniques which needs significant time and efforts.
To make this strategies adaptive and effective, top management of Aston Martin have to
collaborate with company who can design automated system for them. It is needful for managers
to hire software professional for managing those system which helps them to perform
accordingly with given standards.
Managers of Aston Martin uses immersive technological practices for evolving their
business to a greater which assists them in providing excellent customer service. Top
management of Aston Martin started using virtual reality augments to enhance their customer
experiences and provide quality products. They believe that covid pandemic has hit them in a
significant manner and stops their customers to visit their stores for purchasing their luxury cars
(Netessine, 2021). For providing them quality experience, they have started this virtual reality
augmentation practices for their customers. Managers of Aston Martin use virtual reality and
machine learning to their other business processes like designing, engineering, assembling lines
and many more. They also this technology in their dealer training sessions for smooth running of
familiarization sessions in order to gain standards of total quality management. Adoption of
artificial intelligence in their operations, assists their designers to make better designs rather
than application of more costly methods for this purpose. For managing their operations in more
4
performance on a constant basis.
Assessing how technology could be interlinked with operational management practices
Automobile industry use varied automated software and techniques for leveraging their
quality standards which is used in tracking, identifying and resolving issues related to products
or services (Lee and Tang 2018). It helps them in enhancing their productivity level. Ii also
assist them in making compliance with standards set with industry. Automated systems and
machine learning assists establishments in making their customers satisfied and retain for a long
period of time. Total quality management is an approach whereby organisational managers
provide proper trainings and empower employees for maintaining and controlling quality
standards. This can be interlinked with artificial intelligence and automated robotics technology
in their operations. Quality can be managed better in an organisation by connecting it to the
information technology. Managers of Aston Martin can use automated robotics system in their
approach which help them to gain efficiency in their assembly line. It also helps in lowering the
burden of workers. This are the expensive techniques which needs significant time and efforts.
To make this strategies adaptive and effective, top management of Aston Martin have to
collaborate with company who can design automated system for them. It is needful for managers
to hire software professional for managing those system which helps them to perform
accordingly with given standards.
Managers of Aston Martin uses immersive technological practices for evolving their
business to a greater which assists them in providing excellent customer service. Top
management of Aston Martin started using virtual reality augments to enhance their customer
experiences and provide quality products. They believe that covid pandemic has hit them in a
significant manner and stops their customers to visit their stores for purchasing their luxury cars
(Netessine, 2021). For providing them quality experience, they have started this virtual reality
augmentation practices for their customers. Managers of Aston Martin use virtual reality and
machine learning to their other business processes like designing, engineering, assembling lines
and many more. They also this technology in their dealer training sessions for smooth running of
familiarization sessions in order to gain standards of total quality management. Adoption of
artificial intelligence in their operations, assists their designers to make better designs rather
than application of more costly methods for this purpose. For managing their operations in more
4
Paraphrase This Document
Need a fresh take? Get an instant paraphrase of this document with our AI Paraphraser

effective manner for gaining total quality management, managers of Aston Martin have adopted
extended version of virtual reality which assists them in enhancing image and graphics viability.
It also helps them in gaining competitive advantage helps them in staying ahead of their
competitors.
In order to maintain standards for total quality management and gaining those in their
operations, managers of Aston Martin use a software named Siemens NX Software that helps
them in integrating varied organisational processes together such as computer-aided designs,
engineering and their assembling line (Qi and Shen, 2019). It also uses same software for
managing quality in their products and processes. Top management of Aston Martin believed
that it would assists them in driving their productivity improvements as well as enhancing global
collaborations for the development of product designs.
Adoption of total quality management measures with advanced technology helps Aston
Martin in lowering their market as well as improving quality of products (Reddicharla, Bangari
and Konkati, 2016). It also helps in reducing extra operating cost which is incurred by Aston
Martin in manufacturing and re manufacturing the products. It helps in reducing repetitive
production methods sue to wastage and also saves efforts as well as time. With the help of
advanced technological aspects, total quality management practices help them in identifying any
issue or loophole so that it can be addressed on a immediate basis. Automation processes help
managers of Aston Martin in taking corrective measures on a timely basis which takes less time
as compared to manual workings. It also helps them to keep their records safe in their systems.
Effective automation techniques helps in making compliance with industry standards while
maintaining quality adherence with stated benchmarks. Issues with products or services can
deteriorate their brand image in front of public.
Through adoption of automated technological practices and artificial intelligence, it helps
in increasing overall productivity and setting standards for maintaining quality (Russell and
Taylor, 2019). Through artificial intelligence and information technology, managers of Aston
Martin can communicate in an effective way to their employees for making them understand
varied changes and variations in the processes for maintaining quality. Through this, they can
save records of their employees as well as customers in their system which will help them to
make interactions with them effectively.
5
extended version of virtual reality which assists them in enhancing image and graphics viability.
It also helps them in gaining competitive advantage helps them in staying ahead of their
competitors.
In order to maintain standards for total quality management and gaining those in their
operations, managers of Aston Martin use a software named Siemens NX Software that helps
them in integrating varied organisational processes together such as computer-aided designs,
engineering and their assembling line (Qi and Shen, 2019). It also uses same software for
managing quality in their products and processes. Top management of Aston Martin believed
that it would assists them in driving their productivity improvements as well as enhancing global
collaborations for the development of product designs.
Adoption of total quality management measures with advanced technology helps Aston
Martin in lowering their market as well as improving quality of products (Reddicharla, Bangari
and Konkati, 2016). It also helps in reducing extra operating cost which is incurred by Aston
Martin in manufacturing and re manufacturing the products. It helps in reducing repetitive
production methods sue to wastage and also saves efforts as well as time. With the help of
advanced technological aspects, total quality management practices help them in identifying any
issue or loophole so that it can be addressed on a immediate basis. Automation processes help
managers of Aston Martin in taking corrective measures on a timely basis which takes less time
as compared to manual workings. It also helps them to keep their records safe in their systems.
Effective automation techniques helps in making compliance with industry standards while
maintaining quality adherence with stated benchmarks. Issues with products or services can
deteriorate their brand image in front of public.
Through adoption of automated technological practices and artificial intelligence, it helps
in increasing overall productivity and setting standards for maintaining quality (Russell and
Taylor, 2019). Through artificial intelligence and information technology, managers of Aston
Martin can communicate in an effective way to their employees for making them understand
varied changes and variations in the processes for maintaining quality. Through this, they can
save records of their employees as well as customers in their system which will help them to
make interactions with them effectively.
5
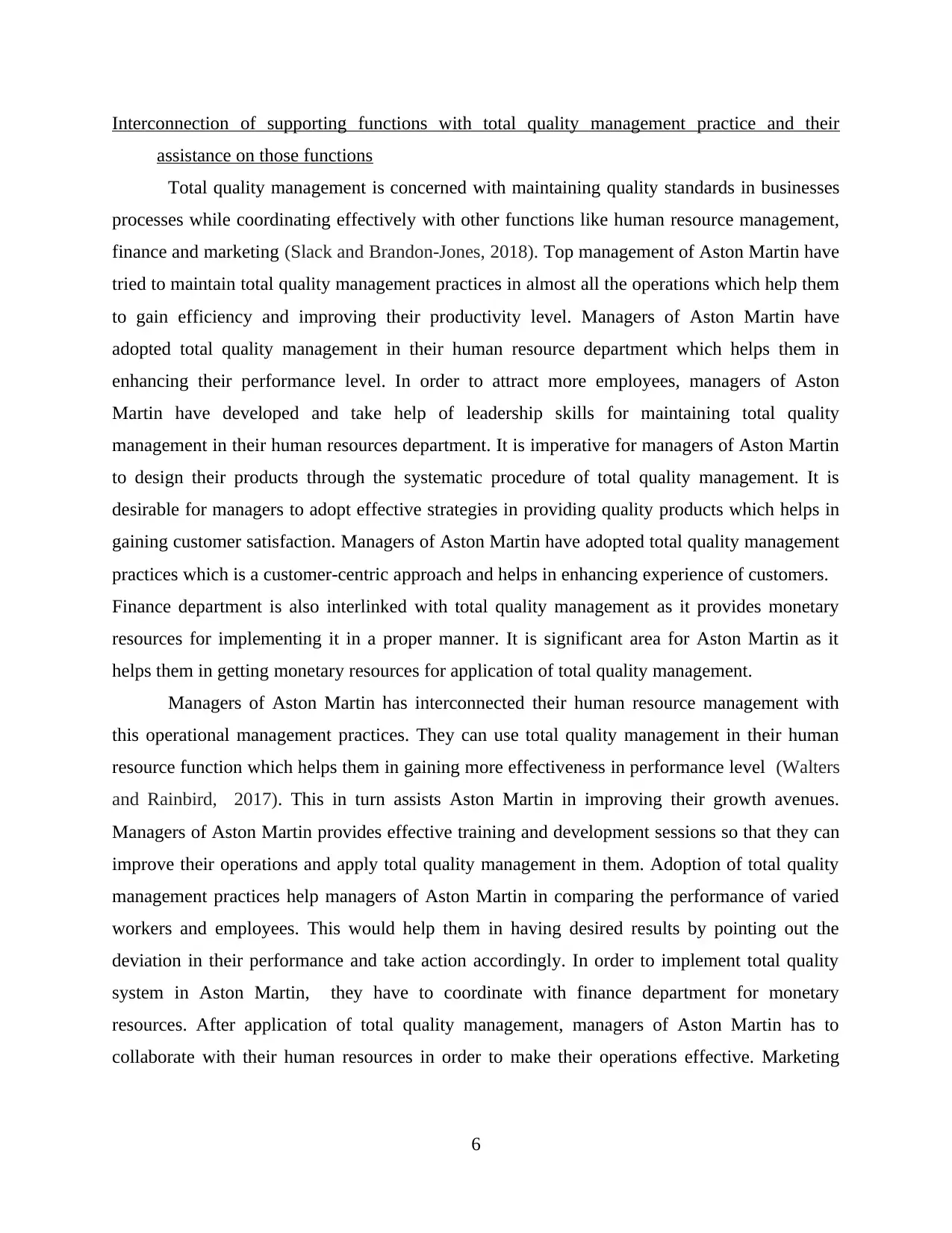
Interconnection of supporting functions with total quality management practice and their
assistance on those functions
Total quality management is concerned with maintaining quality standards in businesses
processes while coordinating effectively with other functions like human resource management,
finance and marketing (Slack and Brandon-Jones, 2018). Top management of Aston Martin have
tried to maintain total quality management practices in almost all the operations which help them
to gain efficiency and improving their productivity level. Managers of Aston Martin have
adopted total quality management in their human resource department which helps them in
enhancing their performance level. In order to attract more employees, managers of Aston
Martin have developed and take help of leadership skills for maintaining total quality
management in their human resources department. It is imperative for managers of Aston Martin
to design their products through the systematic procedure of total quality management. It is
desirable for managers to adopt effective strategies in providing quality products which helps in
gaining customer satisfaction. Managers of Aston Martin have adopted total quality management
practices which is a customer-centric approach and helps in enhancing experience of customers.
Finance department is also interlinked with total quality management as it provides monetary
resources for implementing it in a proper manner. It is significant area for Aston Martin as it
helps them in getting monetary resources for application of total quality management.
Managers of Aston Martin has interconnected their human resource management with
this operational management practices. They can use total quality management in their human
resource function which helps them in gaining more effectiveness in performance level (Walters
and Rainbird, 2017). This in turn assists Aston Martin in improving their growth avenues.
Managers of Aston Martin provides effective training and development sessions so that they can
improve their operations and apply total quality management in them. Adoption of total quality
management practices help managers of Aston Martin in comparing the performance of varied
workers and employees. This would help them in having desired results by pointing out the
deviation in their performance and take action accordingly. In order to implement total quality
system in Aston Martin, they have to coordinate with finance department for monetary
resources. After application of total quality management, managers of Aston Martin has to
collaborate with their human resources in order to make their operations effective. Marketing
6
assistance on those functions
Total quality management is concerned with maintaining quality standards in businesses
processes while coordinating effectively with other functions like human resource management,
finance and marketing (Slack and Brandon-Jones, 2018). Top management of Aston Martin have
tried to maintain total quality management practices in almost all the operations which help them
to gain efficiency and improving their productivity level. Managers of Aston Martin have
adopted total quality management in their human resource department which helps them in
enhancing their performance level. In order to attract more employees, managers of Aston
Martin have developed and take help of leadership skills for maintaining total quality
management in their human resources department. It is imperative for managers of Aston Martin
to design their products through the systematic procedure of total quality management. It is
desirable for managers to adopt effective strategies in providing quality products which helps in
gaining customer satisfaction. Managers of Aston Martin have adopted total quality management
practices which is a customer-centric approach and helps in enhancing experience of customers.
Finance department is also interlinked with total quality management as it provides monetary
resources for implementing it in a proper manner. It is significant area for Aston Martin as it
helps them in getting monetary resources for application of total quality management.
Managers of Aston Martin has interconnected their human resource management with
this operational management practices. They can use total quality management in their human
resource function which helps them in gaining more effectiveness in performance level (Walters
and Rainbird, 2017). This in turn assists Aston Martin in improving their growth avenues.
Managers of Aston Martin provides effective training and development sessions so that they can
improve their operations and apply total quality management in them. Adoption of total quality
management practices help managers of Aston Martin in comparing the performance of varied
workers and employees. This would help them in having desired results by pointing out the
deviation in their performance and take action accordingly. In order to implement total quality
system in Aston Martin, they have to coordinate with finance department for monetary
resources. After application of total quality management, managers of Aston Martin has to
collaborate with their human resources in order to make their operations effective. Marketing
6
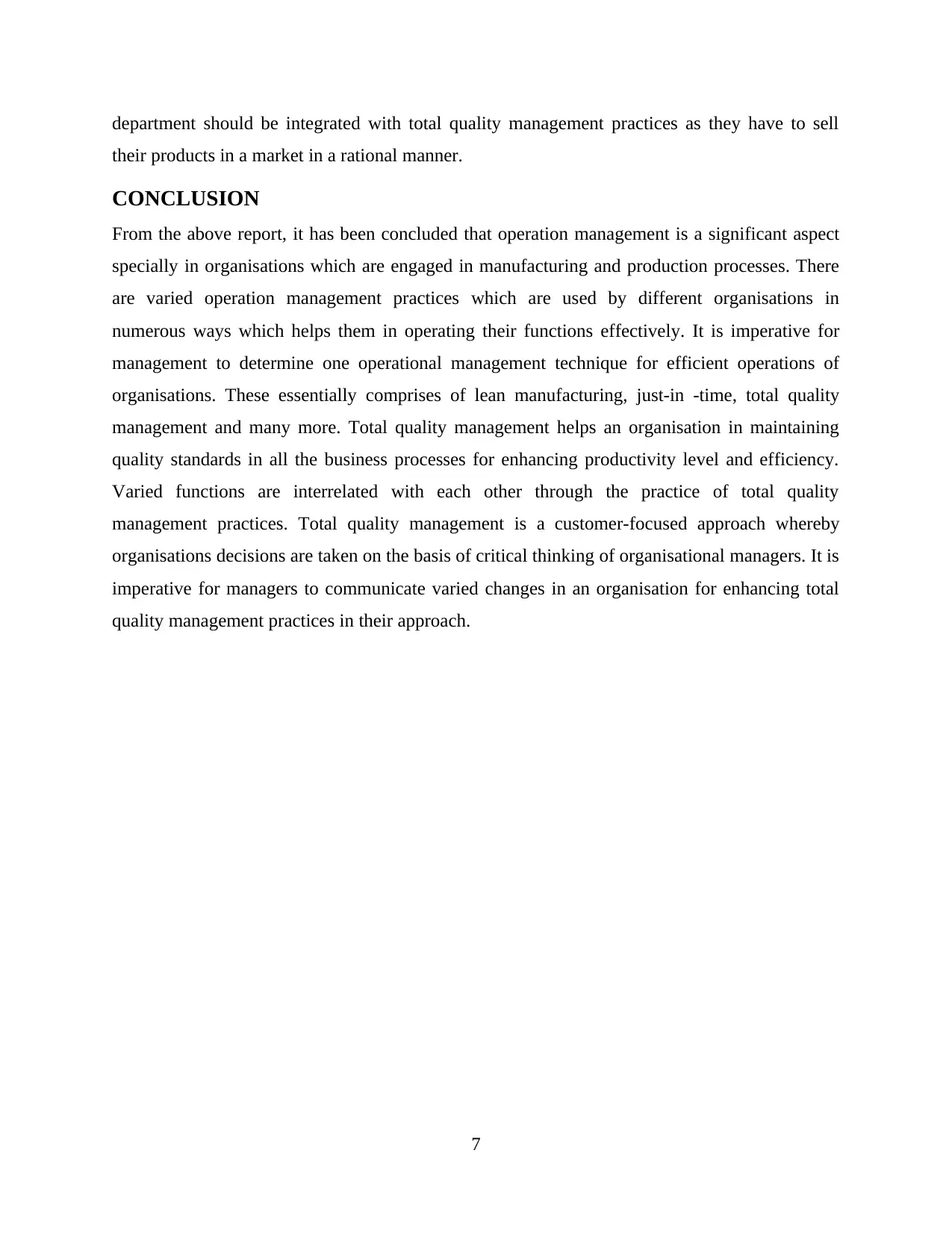
department should be integrated with total quality management practices as they have to sell
their products in a market in a rational manner.
CONCLUSION
From the above report, it has been concluded that operation management is a significant aspect
specially in organisations which are engaged in manufacturing and production processes. There
are varied operation management practices which are used by different organisations in
numerous ways which helps them in operating their functions effectively. It is imperative for
management to determine one operational management technique for efficient operations of
organisations. These essentially comprises of lean manufacturing, just-in -time, total quality
management and many more. Total quality management helps an organisation in maintaining
quality standards in all the business processes for enhancing productivity level and efficiency.
Varied functions are interrelated with each other through the practice of total quality
management practices. Total quality management is a customer-focused approach whereby
organisations decisions are taken on the basis of critical thinking of organisational managers. It is
imperative for managers to communicate varied changes in an organisation for enhancing total
quality management practices in their approach.
7
their products in a market in a rational manner.
CONCLUSION
From the above report, it has been concluded that operation management is a significant aspect
specially in organisations which are engaged in manufacturing and production processes. There
are varied operation management practices which are used by different organisations in
numerous ways which helps them in operating their functions effectively. It is imperative for
management to determine one operational management technique for efficient operations of
organisations. These essentially comprises of lean manufacturing, just-in -time, total quality
management and many more. Total quality management helps an organisation in maintaining
quality standards in all the business processes for enhancing productivity level and efficiency.
Varied functions are interrelated with each other through the practice of total quality
management practices. Total quality management is a customer-focused approach whereby
organisations decisions are taken on the basis of critical thinking of organisational managers. It is
imperative for managers to communicate varied changes in an organisation for enhancing total
quality management practices in their approach.
7
Secure Best Marks with AI Grader
Need help grading? Try our AI Grader for instant feedback on your assignments.

REFERENCES
Books and Journals:
Aboelmaged, M. and Hashem, G., 2018. RFID application in patient and medical asset
operations management: A technology, organizational and environmental (TOE)
perspective into key enablers and impediments. International journal of medical
informatics. 118. pp.58-64.
Andrade, R., Moazeni, S. and Ramirez-Marquez, J., 2018. Contact Center Operations
Management Systems Architecture and Reliability. Available at SSRN 3320821.
Dobrzykowski, D. D., McFadden, K. L. and Vonderembse, M. A., 2016. Examining pathways to
safety and financial performance in hospitals: A study of lean in professional service
operations. Journal of operations management. 42(1). pp.39-51.
Gupta, A. and Singh, R.K., 2020. Managing operations by a logistics company for sustainable
service quality: Indian perspective. Management of Environmental Quality: An
International Journal.
Gupta, M. and Gupta, S., 2019. Influence of national cultures on operations management and
supply chain management practices—a research agenda. Production and Operations
Management, 28(11), pp.2681-2698.
Helo, P. and Hao, Y., 2019. Blockchains in operations and supply chains: A model and reference
implementation. Computers & Industrial Engineering. 136. pp.242-251.
Kumar, P. and Singh, A.P., 2019. Flexibility in service operations: review, synthesis and
research agenda. Benchmarking: An International Journal.
Lee, C. K. H., 2018. A review of applications of genetic algorithms in operations
management. Engineering Applications of Artificial Intelligence. 76. pp.1-12.
Lee, H. L. and Tang, C.S., 2018. Socially and environmentally responsible value chain
innovations: New operations management research opportunities. Management
Science, 64(3), pp.983-996.
McCrie, R. and Lee, S., 2021. Security operations management. Butterworth-Heinemann.
Netessine, S., 2021. A vision of responsible research in operations management. Manufacturing
& Service Operations Management.
Qi, W. and Shen, Z. J. M., 2019. A smart‐city scope of operations management. Production and
Operations Management, 28(2), pp.393-406.
Reddicharla, N., Bangari, P. and Konkati, S., 2016, September. Increase Efficiency of Smart
Field Integrated Operations Through Service Level Management. In SPE Annual
Technical Conference and Exhibition. OnePetro.
Russell, R. S. and Taylor, B. W., 2019. Operations and supply chain management. John Wiley
& Sons.
Slack, N. and Brandon-Jones, A., 2018. Operations and process management: principles and
practice for strategic impact. Pearson UK.
Walters, D. and Rainbird, M., 2017. Strategic operations management: a value chain approach.
Bloomsbury Publishing.
8
Books and Journals:
Aboelmaged, M. and Hashem, G., 2018. RFID application in patient and medical asset
operations management: A technology, organizational and environmental (TOE)
perspective into key enablers and impediments. International journal of medical
informatics. 118. pp.58-64.
Andrade, R., Moazeni, S. and Ramirez-Marquez, J., 2018. Contact Center Operations
Management Systems Architecture and Reliability. Available at SSRN 3320821.
Dobrzykowski, D. D., McFadden, K. L. and Vonderembse, M. A., 2016. Examining pathways to
safety and financial performance in hospitals: A study of lean in professional service
operations. Journal of operations management. 42(1). pp.39-51.
Gupta, A. and Singh, R.K., 2020. Managing operations by a logistics company for sustainable
service quality: Indian perspective. Management of Environmental Quality: An
International Journal.
Gupta, M. and Gupta, S., 2019. Influence of national cultures on operations management and
supply chain management practices—a research agenda. Production and Operations
Management, 28(11), pp.2681-2698.
Helo, P. and Hao, Y., 2019. Blockchains in operations and supply chains: A model and reference
implementation. Computers & Industrial Engineering. 136. pp.242-251.
Kumar, P. and Singh, A.P., 2019. Flexibility in service operations: review, synthesis and
research agenda. Benchmarking: An International Journal.
Lee, C. K. H., 2018. A review of applications of genetic algorithms in operations
management. Engineering Applications of Artificial Intelligence. 76. pp.1-12.
Lee, H. L. and Tang, C.S., 2018. Socially and environmentally responsible value chain
innovations: New operations management research opportunities. Management
Science, 64(3), pp.983-996.
McCrie, R. and Lee, S., 2021. Security operations management. Butterworth-Heinemann.
Netessine, S., 2021. A vision of responsible research in operations management. Manufacturing
& Service Operations Management.
Qi, W. and Shen, Z. J. M., 2019. A smart‐city scope of operations management. Production and
Operations Management, 28(2), pp.393-406.
Reddicharla, N., Bangari, P. and Konkati, S., 2016, September. Increase Efficiency of Smart
Field Integrated Operations Through Service Level Management. In SPE Annual
Technical Conference and Exhibition. OnePetro.
Russell, R. S. and Taylor, B. W., 2019. Operations and supply chain management. John Wiley
& Sons.
Slack, N. and Brandon-Jones, A., 2018. Operations and process management: principles and
practice for strategic impact. Pearson UK.
Walters, D. and Rainbird, M., 2017. Strategic operations management: a value chain approach.
Bloomsbury Publishing.
8
1 out of 11
Related Documents
![[object Object]](/_next/image/?url=%2F_next%2Fstatic%2Fmedia%2Flogo.6d15ce61.png&w=640&q=75)
Your All-in-One AI-Powered Toolkit for Academic Success.
+13062052269
info@desklib.com
Available 24*7 on WhatsApp / Email
Unlock your academic potential
© 2024 | Zucol Services PVT LTD | All rights reserved.