BSBMGT608 Implementation and Follow Up Plan
Added on 2023-06-12
12 Pages2124 Words185 Views
Running head: BSBMGT608
BSBMGT608
Name of the Student
Name of the University
Author Note
BSBMGT608
Name of the Student
Name of the University
Author Note
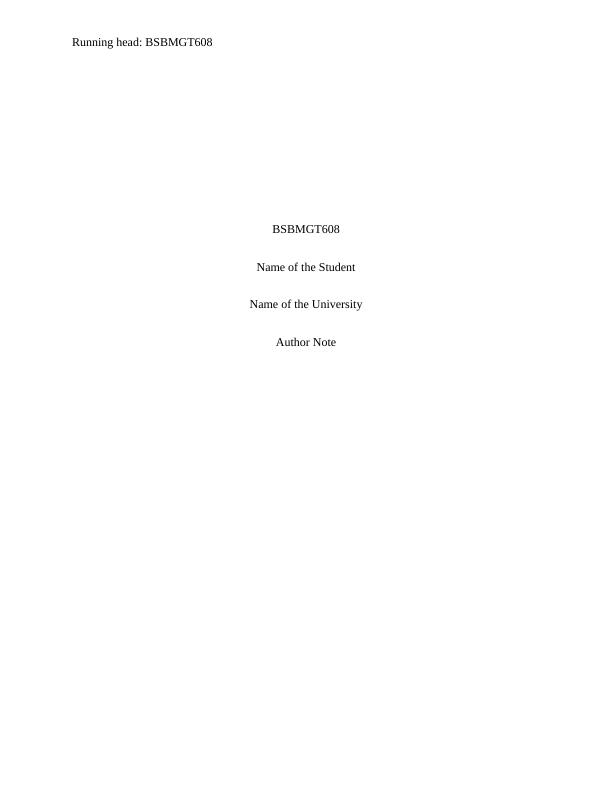
1
BSBMGT608
Table of Contents
Part 1: Implementation........................................................................................................2
1.1. Action Plan for Transition........................................................................................2
1.2. Action Plan for Communication...............................................................................5
1.3. Contingency Plan for implementation issue.............................................................5
Part 2: Follow Up.................................................................................................................6
2.1. Implementation Issues and Failures..........................................................................6
2.2. Amendment in Action Plan and Contingency Plan..................................................7
2.3. Schedule for evaluation and continuous improvement.............................................7
Bibliography......................................................................................................................10
BSBMGT608
Table of Contents
Part 1: Implementation........................................................................................................2
1.1. Action Plan for Transition........................................................................................2
1.2. Action Plan for Communication...............................................................................5
1.3. Contingency Plan for implementation issue.............................................................5
Part 2: Follow Up.................................................................................................................6
2.1. Implementation Issues and Failures..........................................................................6
2.2. Amendment in Action Plan and Contingency Plan..................................................7
2.3. Schedule for evaluation and continuous improvement.............................................7
Bibliography......................................................................................................................10
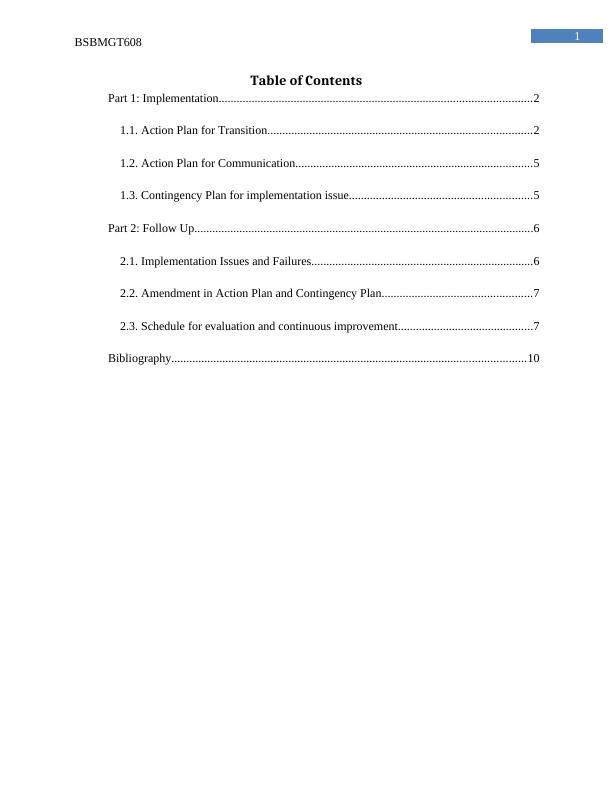
2
BSBMGT608
Part 1: Implementation
1.1. Action Plan for Transition
The main goal of the program is to increase the productivity and considerably reduce the
waste associated with the manufacturing process in order to improve the sustainability and error
reduction in the production lines. Furthermore, the program aims at reducing the staff’s which is
on an average is 32% per annum to 20% per annum. This aims at improving the skills levels and
the efficiency of the firm by reducing the cost of recruitment and training of the new staffs.
Reducing the employees’ turnover will only be possible by increasing the job satisfaction of the
employees.
Activities of Transition
In order to achieve the set goal, the authorities have decided to divide the workers into
five different teams. These teams will be responsible for manufacturing of five different product
lines. This will ensure that each team is working on their specialty line only. This roster will be
altered timely in order to enable every staffs to work on different lines.
In order to make the regular work more interesting John the production manager of the
firm has suggested the teams to work in a particular goal or objective that is set for a particular
product line. This goal will be based on reducing the error rate to only 4% from a rate of 22%.
Along with this, it is essential that the productivity of the firm to be increased by 40% within 24
months.
The main activity of the program further includes the closing of the production lines for
48 hours. This time is needed for re tooling. The activities of re tooling include staff retraining.
BSBMGT608
Part 1: Implementation
1.1. Action Plan for Transition
The main goal of the program is to increase the productivity and considerably reduce the
waste associated with the manufacturing process in order to improve the sustainability and error
reduction in the production lines. Furthermore, the program aims at reducing the staff’s which is
on an average is 32% per annum to 20% per annum. This aims at improving the skills levels and
the efficiency of the firm by reducing the cost of recruitment and training of the new staffs.
Reducing the employees’ turnover will only be possible by increasing the job satisfaction of the
employees.
Activities of Transition
In order to achieve the set goal, the authorities have decided to divide the workers into
five different teams. These teams will be responsible for manufacturing of five different product
lines. This will ensure that each team is working on their specialty line only. This roster will be
altered timely in order to enable every staffs to work on different lines.
In order to make the regular work more interesting John the production manager of the
firm has suggested the teams to work in a particular goal or objective that is set for a particular
product line. This goal will be based on reducing the error rate to only 4% from a rate of 22%.
Along with this, it is essential that the productivity of the firm to be increased by 40% within 24
months.
The main activity of the program further includes the closing of the production lines for
48 hours. This time is needed for re tooling. The activities of re tooling include staff retraining.
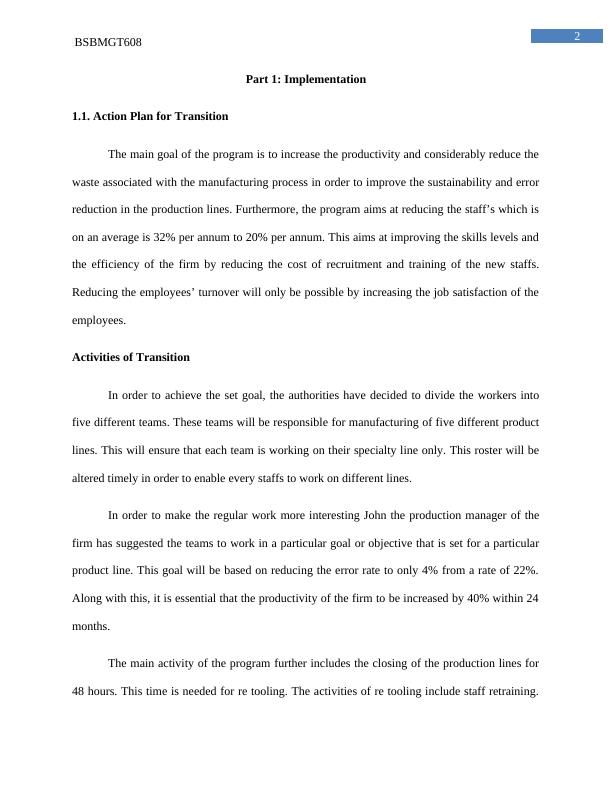
3
BSBMGT608
The retraining process will incorporate technical training, motivational training, training on
quality control along with clear definition of goal and objectives. This will help in reducing the
error in the production and manufacturing work and will keep the staffs and employees
motivated as well.
Objectives of the transition
The main objective of the transition is to redesign the production and the manufacturing
process. This will help in increasing the productivity of the firm. Waste reduction is further
essential for which it is essential to design an error free product. The objective of this program is
to reduce the error lines up to 20% in order to reduce the sustainability.
The firm has seen quite a huge number of employee losses in recent years. Therefore the
secondary objective of the program is to reduce the staff turnover from a rate of 32% per annum
to 20% per annum. This objective aims at reducing the costs of recruiting and training of new
staffs every year.
Another significant objective of this program is to close the production lines for 48 hours
for retooling. In this period, the staffs will be retrained in order to improve their skills and
knowledge.
KPIs of Transition
The key performance indicators of the program will be reduction in the error rate in order
to reduce the wastes associated with the manufacturing process. The current error rate is 22%
which must be reduced to 4% for improving the sustainability of the organization. The staff
workers are divided into five teams in order to ensure that each work supervised by them is done
BSBMGT608
The retraining process will incorporate technical training, motivational training, training on
quality control along with clear definition of goal and objectives. This will help in reducing the
error in the production and manufacturing work and will keep the staffs and employees
motivated as well.
Objectives of the transition
The main objective of the transition is to redesign the production and the manufacturing
process. This will help in increasing the productivity of the firm. Waste reduction is further
essential for which it is essential to design an error free product. The objective of this program is
to reduce the error lines up to 20% in order to reduce the sustainability.
The firm has seen quite a huge number of employee losses in recent years. Therefore the
secondary objective of the program is to reduce the staff turnover from a rate of 32% per annum
to 20% per annum. This objective aims at reducing the costs of recruiting and training of new
staffs every year.
Another significant objective of this program is to close the production lines for 48 hours
for retooling. In this period, the staffs will be retrained in order to improve their skills and
knowledge.
KPIs of Transition
The key performance indicators of the program will be reduction in the error rate in order
to reduce the wastes associated with the manufacturing process. The current error rate is 22%
which must be reduced to 4% for improving the sustainability of the organization. The staff
workers are divided into five teams in order to ensure that each work supervised by them is done
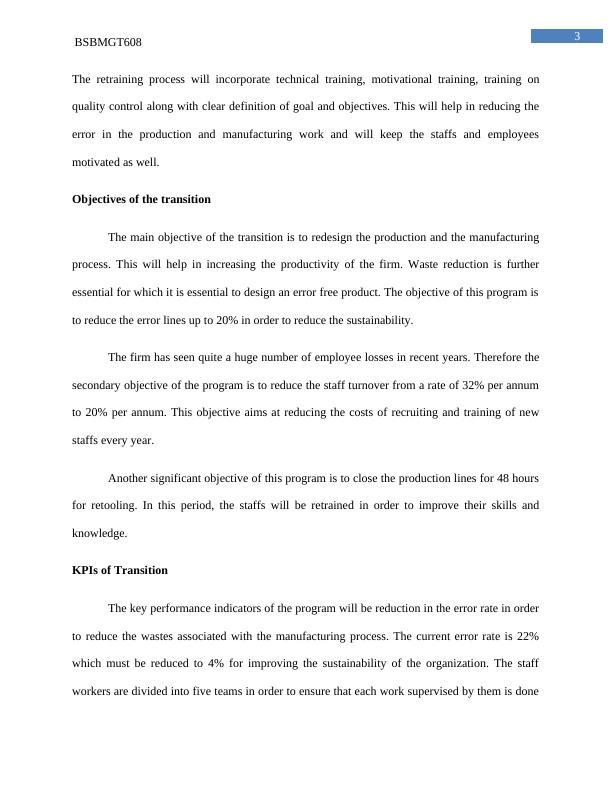
End of preview
Want to access all the pages? Upload your documents or become a member.
Related Documents
Implementation of Innovative Processes - Action Plan, Contingency Plans, and Amended Planslg...
|13
|648
|229
Implementation of new processes in the factory A.C. Gilbertlg...
|10
|1822
|72
Managing Innovation and Continuous Improvement - Part 3lg...
|6
|868
|203
Implementation of Innovative Processes.lg...
|13
|306
|48
Innovation Adoption: A Review of Theories and Constructslg...
|13
|305
|39
BSBMGT617 Order Processing Time - Reportlg...
|5
|1421
|291