Quality Management and Corporate Social Responsibility
VerifiedAdded on 2020/05/08
|13
|3416
|132
AI Summary
This assignment explores the relationship between quality management systems, ISO standards (ISO 9001 and ISO 14001), and corporate social responsibility. It utilizes Woolworths Group as a case study to analyze how these systems are implemented and their impact on various aspects of the business, including product development, customer satisfaction, environmental sustainability, and ethical practices. The assignment requires students to critically evaluate the effectiveness of these systems in promoting organizational excellence and responsible business conduct.
Contribute Materials
Your contribution can guide someone’s learning journey. Share your
documents today.
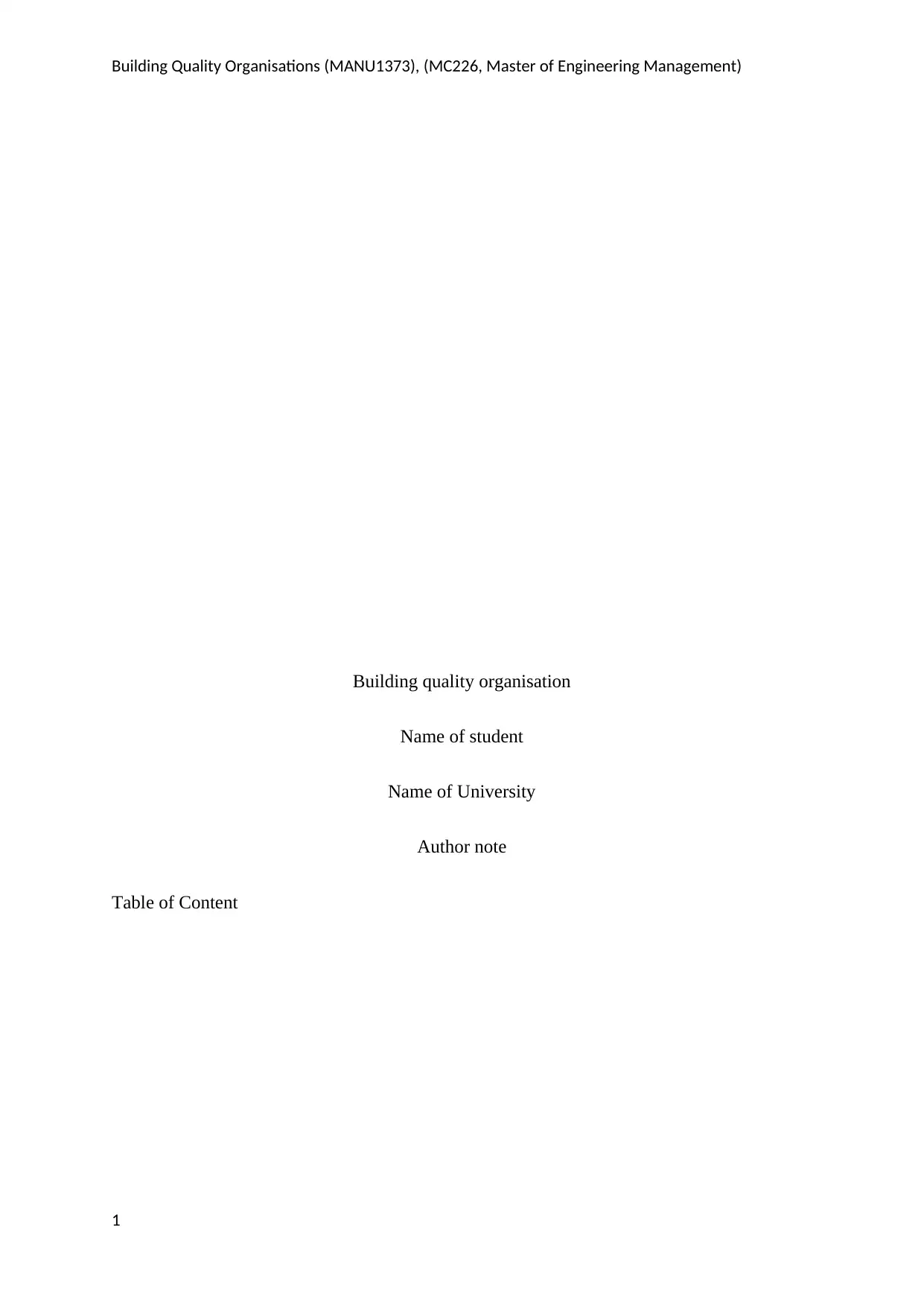
Building Quality Organisations (MANU1373), (MC226, Master of Engineering Management)
Building quality organisation
Name of student
Name of University
Author note
Table of Content
1
Building quality organisation
Name of student
Name of University
Author note
Table of Content
1
Secure Best Marks with AI Grader
Need help grading? Try our AI Grader for instant feedback on your assignments.
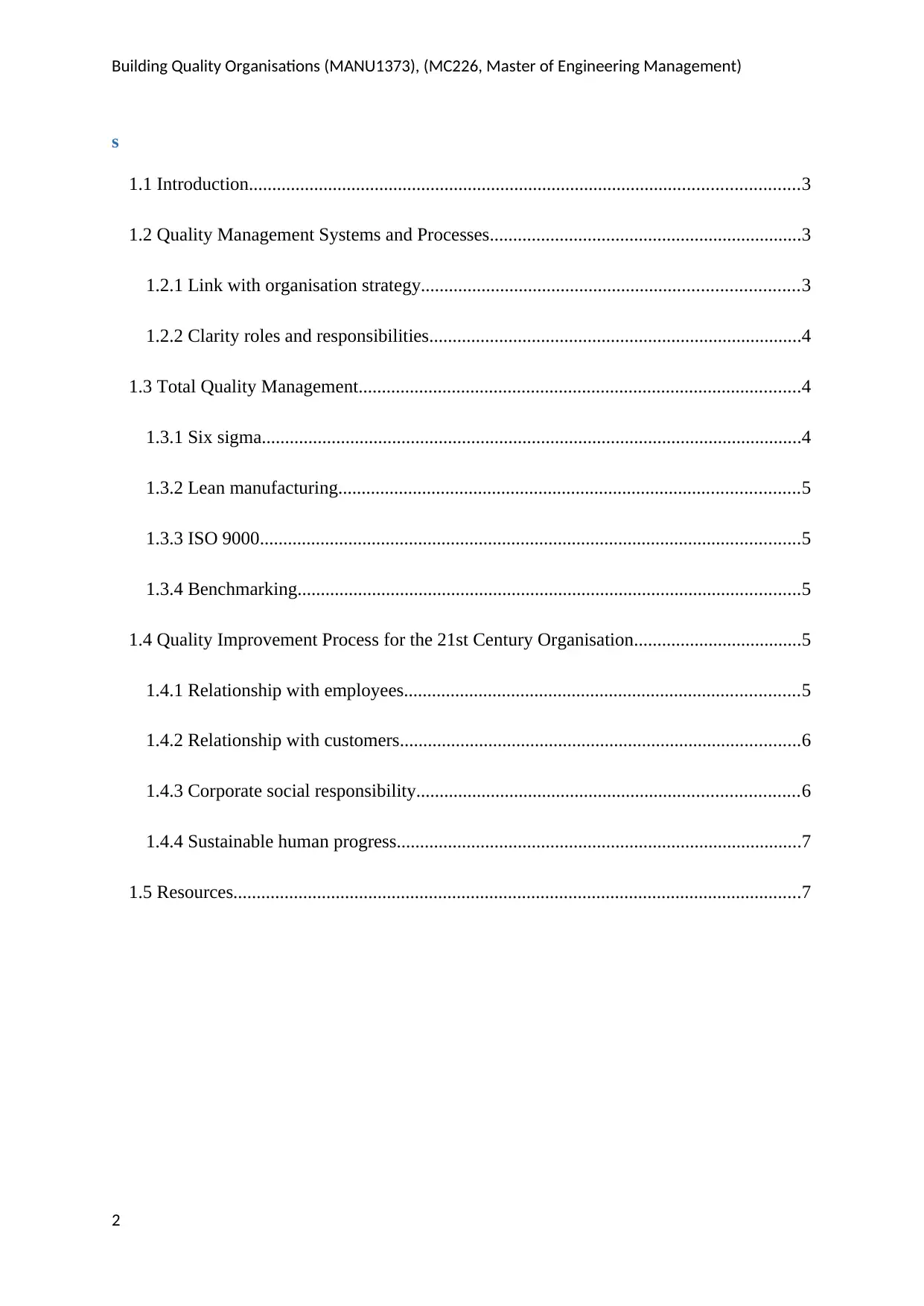
Building Quality Organisations (MANU1373), (MC226, Master of Engineering Management)
s
1.1 Introduction......................................................................................................................3
1.2 Quality Management Systems and Processes...................................................................3
1.2.1 Link with organisation strategy.................................................................................3
1.2.2 Clarity roles and responsibilities................................................................................4
1.3 Total Quality Management...............................................................................................4
1.3.1 Six sigma....................................................................................................................4
1.3.2 Lean manufacturing...................................................................................................5
1.3.3 ISO 9000....................................................................................................................5
1.3.4 Benchmarking............................................................................................................5
1.4 Quality Improvement Process for the 21st Century Organisation....................................5
1.4.1 Relationship with employees.....................................................................................5
1.4.2 Relationship with customers......................................................................................6
1.4.3 Corporate social responsibility..................................................................................6
1.4.4 Sustainable human progress.......................................................................................7
1.5 Resources..........................................................................................................................7
2
s
1.1 Introduction......................................................................................................................3
1.2 Quality Management Systems and Processes...................................................................3
1.2.1 Link with organisation strategy.................................................................................3
1.2.2 Clarity roles and responsibilities................................................................................4
1.3 Total Quality Management...............................................................................................4
1.3.1 Six sigma....................................................................................................................4
1.3.2 Lean manufacturing...................................................................................................5
1.3.3 ISO 9000....................................................................................................................5
1.3.4 Benchmarking............................................................................................................5
1.4 Quality Improvement Process for the 21st Century Organisation....................................5
1.4.1 Relationship with employees.....................................................................................5
1.4.2 Relationship with customers......................................................................................6
1.4.3 Corporate social responsibility..................................................................................6
1.4.4 Sustainable human progress.......................................................................................7
1.5 Resources..........................................................................................................................7
2
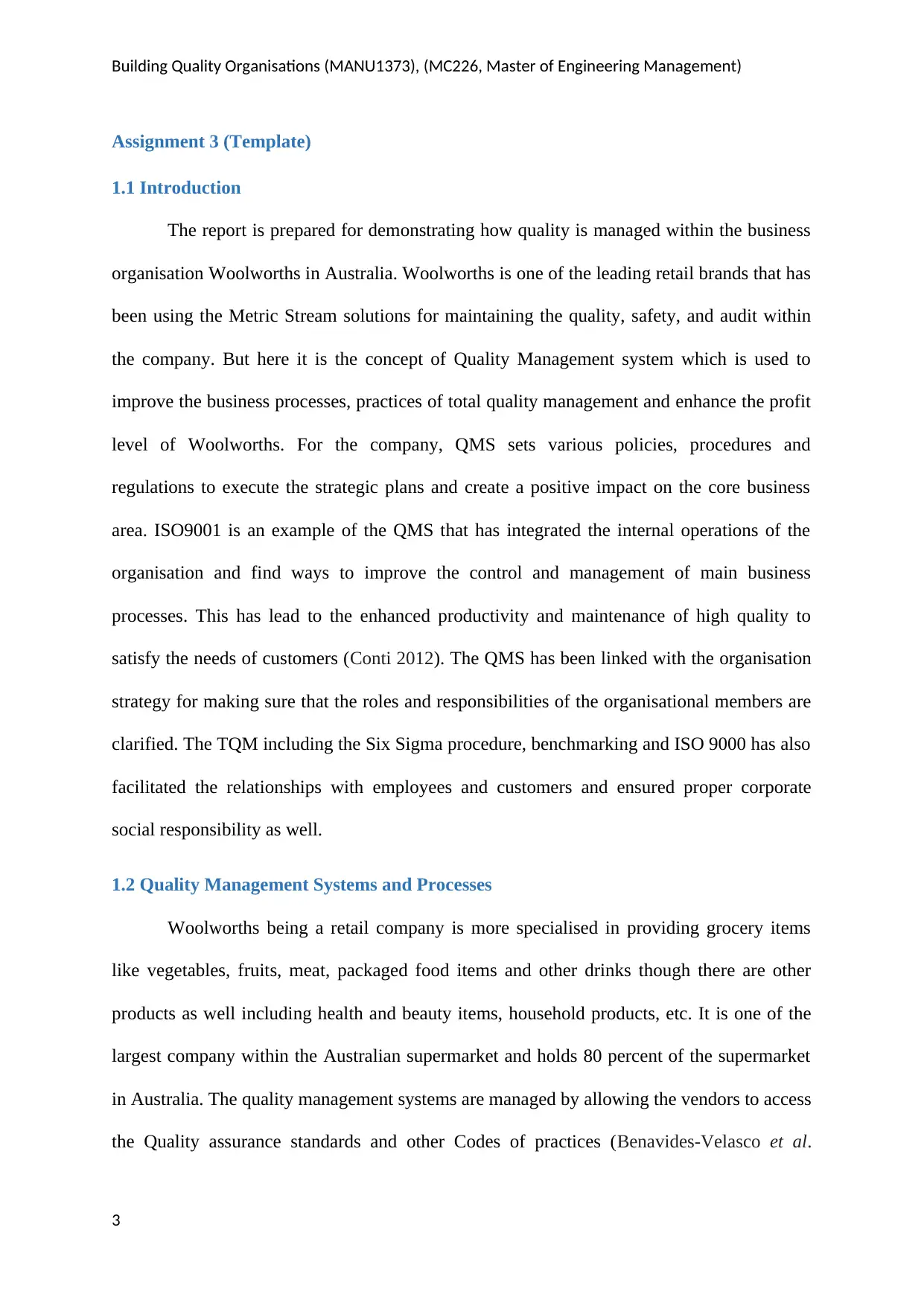
Building Quality Organisations (MANU1373), (MC226, Master of Engineering Management)
Assignment 3 (Template)
1.1 Introduction
The report is prepared for demonstrating how quality is managed within the business
organisation Woolworths in Australia. Woolworths is one of the leading retail brands that has
been using the Metric Stream solutions for maintaining the quality, safety, and audit within
the company. But here it is the concept of Quality Management system which is used to
improve the business processes, practices of total quality management and enhance the profit
level of Woolworths. For the company, QMS sets various policies, procedures and
regulations to execute the strategic plans and create a positive impact on the core business
area. ISO9001 is an example of the QMS that has integrated the internal operations of the
organisation and find ways to improve the control and management of main business
processes. This has lead to the enhanced productivity and maintenance of high quality to
satisfy the needs of customers (Conti 2012). The QMS has been linked with the organisation
strategy for making sure that the roles and responsibilities of the organisational members are
clarified. The TQM including the Six Sigma procedure, benchmarking and ISO 9000 has also
facilitated the relationships with employees and customers and ensured proper corporate
social responsibility as well.
1.2 Quality Management Systems and Processes
Woolworths being a retail company is more specialised in providing grocery items
like vegetables, fruits, meat, packaged food items and other drinks though there are other
products as well including health and beauty items, household products, etc. It is one of the
largest company within the Australian supermarket and holds 80 percent of the supermarket
in Australia. The quality management systems are managed by allowing the vendors to access
the Quality assurance standards and other Codes of practices (Benavides-Velasco et al.
3
Assignment 3 (Template)
1.1 Introduction
The report is prepared for demonstrating how quality is managed within the business
organisation Woolworths in Australia. Woolworths is one of the leading retail brands that has
been using the Metric Stream solutions for maintaining the quality, safety, and audit within
the company. But here it is the concept of Quality Management system which is used to
improve the business processes, practices of total quality management and enhance the profit
level of Woolworths. For the company, QMS sets various policies, procedures and
regulations to execute the strategic plans and create a positive impact on the core business
area. ISO9001 is an example of the QMS that has integrated the internal operations of the
organisation and find ways to improve the control and management of main business
processes. This has lead to the enhanced productivity and maintenance of high quality to
satisfy the needs of customers (Conti 2012). The QMS has been linked with the organisation
strategy for making sure that the roles and responsibilities of the organisational members are
clarified. The TQM including the Six Sigma procedure, benchmarking and ISO 9000 has also
facilitated the relationships with employees and customers and ensured proper corporate
social responsibility as well.
1.2 Quality Management Systems and Processes
Woolworths being a retail company is more specialised in providing grocery items
like vegetables, fruits, meat, packaged food items and other drinks though there are other
products as well including health and beauty items, household products, etc. It is one of the
largest company within the Australian supermarket and holds 80 percent of the supermarket
in Australia. The quality management systems are managed by allowing the vendors to access
the Quality assurance standards and other Codes of practices (Benavides-Velasco et al.
3
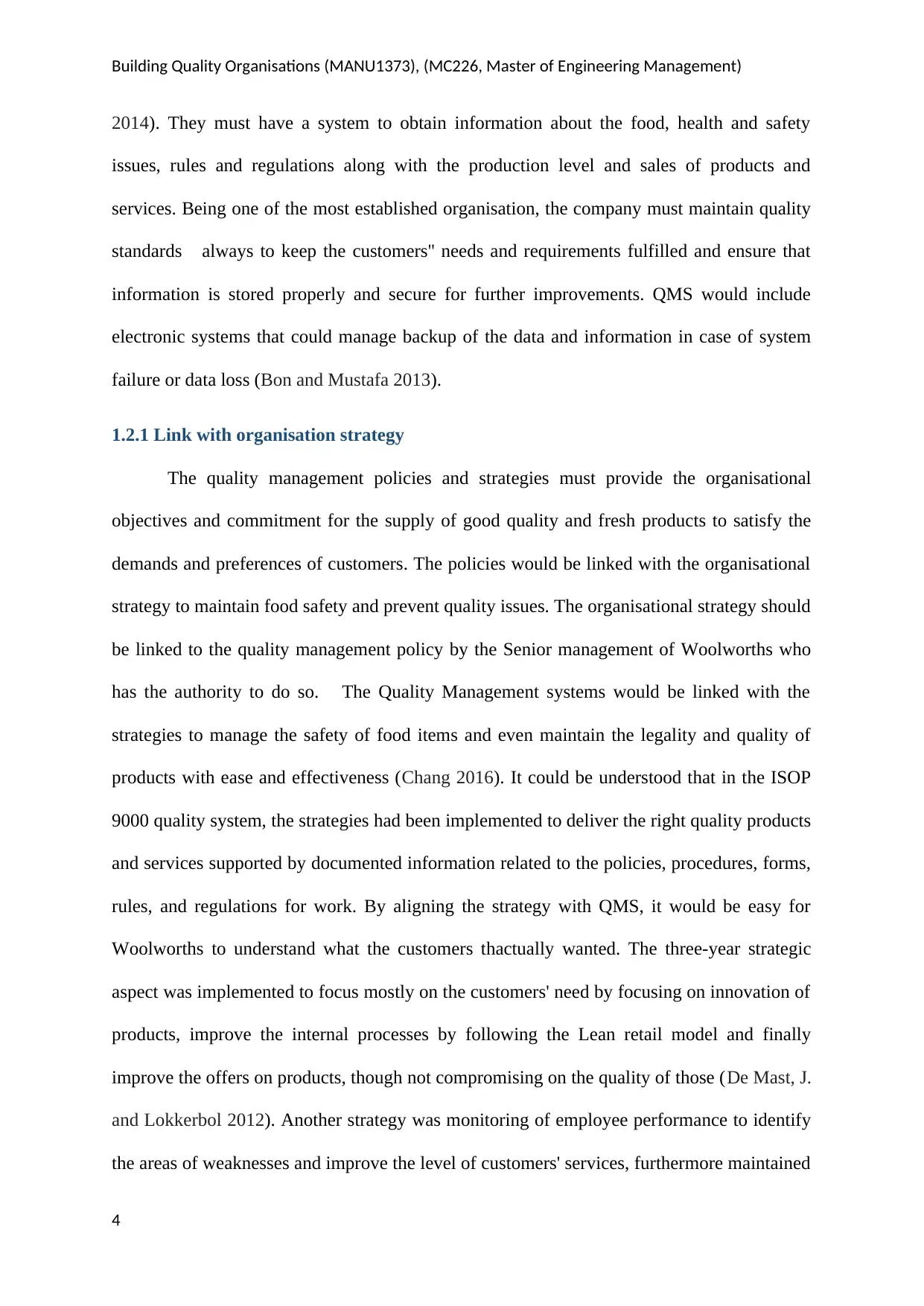
Building Quality Organisations (MANU1373), (MC226, Master of Engineering Management)
2014). They must have a system to obtain information about the food, health and safety
issues, rules and regulations along with the production level and sales of products and
services. Being one of the most established organisation, the company must maintain quality
standards always to keep the customers'' needs and requirements fulfilled and ensure that
information is stored properly and secure for further improvements. QMS would include
electronic systems that could manage backup of the data and information in case of system
failure or data loss (Bon and Mustafa 2013).
1.2.1 Link with organisation strategy
The quality management policies and strategies must provide the organisational
objectives and commitment for the supply of good quality and fresh products to satisfy the
demands and preferences of customers. The policies would be linked with the organisational
strategy to maintain food safety and prevent quality issues. The organisational strategy should
be linked to the quality management policy by the Senior management of Woolworths who
has the authority to do so. The Quality Management systems would be linked with the
strategies to manage the safety of food items and even maintain the legality and quality of
products with ease and effectiveness (Chang 2016). It could be understood that in the ISOP
9000 quality system, the strategies had been implemented to deliver the right quality products
and services supported by documented information related to the policies, procedures, forms,
rules, and regulations for work. By aligning the strategy with QMS, it would be easy for
Woolworths to understand what the customers thactually wanted. The three-year strategic
aspect was implemented to focus mostly on the customers' need by focusing on innovation of
products, improve the internal processes by following the Lean retail model and finally
improve the offers on products, though not compromising on the quality of those (De Mast, J.
and Lokkerbol 2012). Another strategy was monitoring of employee performance to identify
the areas of weaknesses and improve the level of customers' services, furthermore maintained
4
2014). They must have a system to obtain information about the food, health and safety
issues, rules and regulations along with the production level and sales of products and
services. Being one of the most established organisation, the company must maintain quality
standards always to keep the customers'' needs and requirements fulfilled and ensure that
information is stored properly and secure for further improvements. QMS would include
electronic systems that could manage backup of the data and information in case of system
failure or data loss (Bon and Mustafa 2013).
1.2.1 Link with organisation strategy
The quality management policies and strategies must provide the organisational
objectives and commitment for the supply of good quality and fresh products to satisfy the
demands and preferences of customers. The policies would be linked with the organisational
strategy to maintain food safety and prevent quality issues. The organisational strategy should
be linked to the quality management policy by the Senior management of Woolworths who
has the authority to do so. The Quality Management systems would be linked with the
strategies to manage the safety of food items and even maintain the legality and quality of
products with ease and effectiveness (Chang 2016). It could be understood that in the ISOP
9000 quality system, the strategies had been implemented to deliver the right quality products
and services supported by documented information related to the policies, procedures, forms,
rules, and regulations for work. By aligning the strategy with QMS, it would be easy for
Woolworths to understand what the customers thactually wanted. The three-year strategic
aspect was implemented to focus mostly on the customers' need by focusing on innovation of
products, improve the internal processes by following the Lean retail model and finally
improve the offers on products, though not compromising on the quality of those (De Mast, J.
and Lokkerbol 2012). Another strategy was monitoring of employee performance to identify
the areas of weaknesses and improve the level of customers' services, furthermore maintained
4
Secure Best Marks with AI Grader
Need help grading? Try our AI Grader for instant feedback on your assignments.
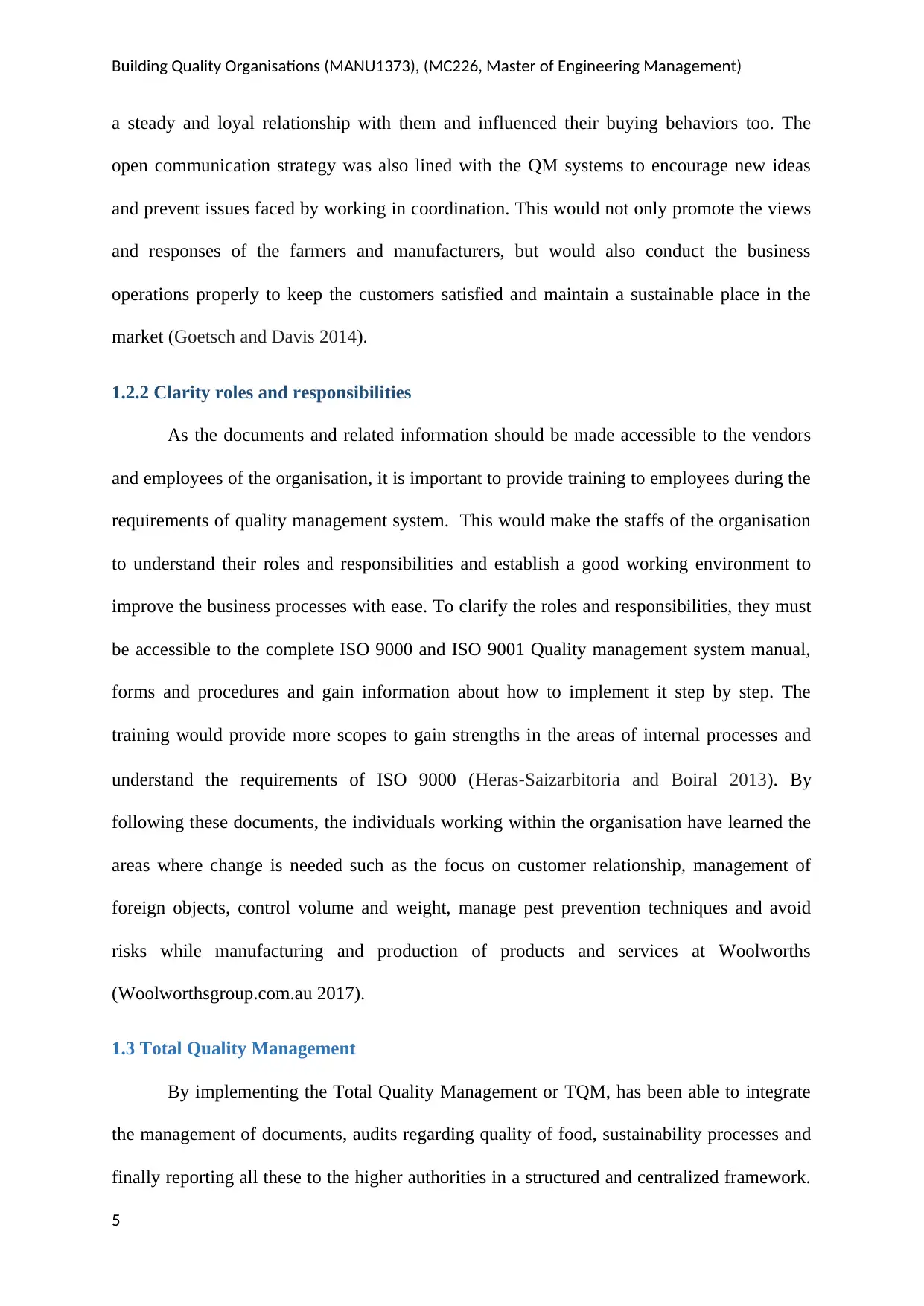
Building Quality Organisations (MANU1373), (MC226, Master of Engineering Management)
a steady and loyal relationship with them and influenced their buying behaviors too. The
open communication strategy was also lined with the QM systems to encourage new ideas
and prevent issues faced by working in coordination. This would not only promote the views
and responses of the farmers and manufacturers, but would also conduct the business
operations properly to keep the customers satisfied and maintain a sustainable place in the
market (Goetsch and Davis 2014).
1.2.2 Clarity roles and responsibilities
As the documents and related information should be made accessible to the vendors
and employees of the organisation, it is important to provide training to employees during the
requirements of quality management system. This would make the staffs of the organisation
to understand their roles and responsibilities and establish a good working environment to
improve the business processes with ease. To clarify the roles and responsibilities, they must
be accessible to the complete ISO 9000 and ISO 9001 Quality management system manual,
forms and procedures and gain information about how to implement it step by step. The
training would provide more scopes to gain strengths in the areas of internal processes and
understand the requirements of ISO 9000 (Heras‐Saizarbitoria and Boiral 2013). By
following these documents, the individuals working within the organisation have learned the
areas where change is needed such as the focus on customer relationship, management of
foreign objects, control volume and weight, manage pest prevention techniques and avoid
risks while manufacturing and production of products and services at Woolworths
(Woolworthsgroup.com.au 2017).
1.3 Total Quality Management
By implementing the Total Quality Management or TQM, has been able to integrate
the management of documents, audits regarding quality of food, sustainability processes and
finally reporting all these to the higher authorities in a structured and centralized framework.
5
a steady and loyal relationship with them and influenced their buying behaviors too. The
open communication strategy was also lined with the QM systems to encourage new ideas
and prevent issues faced by working in coordination. This would not only promote the views
and responses of the farmers and manufacturers, but would also conduct the business
operations properly to keep the customers satisfied and maintain a sustainable place in the
market (Goetsch and Davis 2014).
1.2.2 Clarity roles and responsibilities
As the documents and related information should be made accessible to the vendors
and employees of the organisation, it is important to provide training to employees during the
requirements of quality management system. This would make the staffs of the organisation
to understand their roles and responsibilities and establish a good working environment to
improve the business processes with ease. To clarify the roles and responsibilities, they must
be accessible to the complete ISO 9000 and ISO 9001 Quality management system manual,
forms and procedures and gain information about how to implement it step by step. The
training would provide more scopes to gain strengths in the areas of internal processes and
understand the requirements of ISO 9000 (Heras‐Saizarbitoria and Boiral 2013). By
following these documents, the individuals working within the organisation have learned the
areas where change is needed such as the focus on customer relationship, management of
foreign objects, control volume and weight, manage pest prevention techniques and avoid
risks while manufacturing and production of products and services at Woolworths
(Woolworthsgroup.com.au 2017).
1.3 Total Quality Management
By implementing the Total Quality Management or TQM, has been able to integrate
the management of documents, audits regarding quality of food, sustainability processes and
finally reporting all these to the higher authorities in a structured and centralized framework.
5
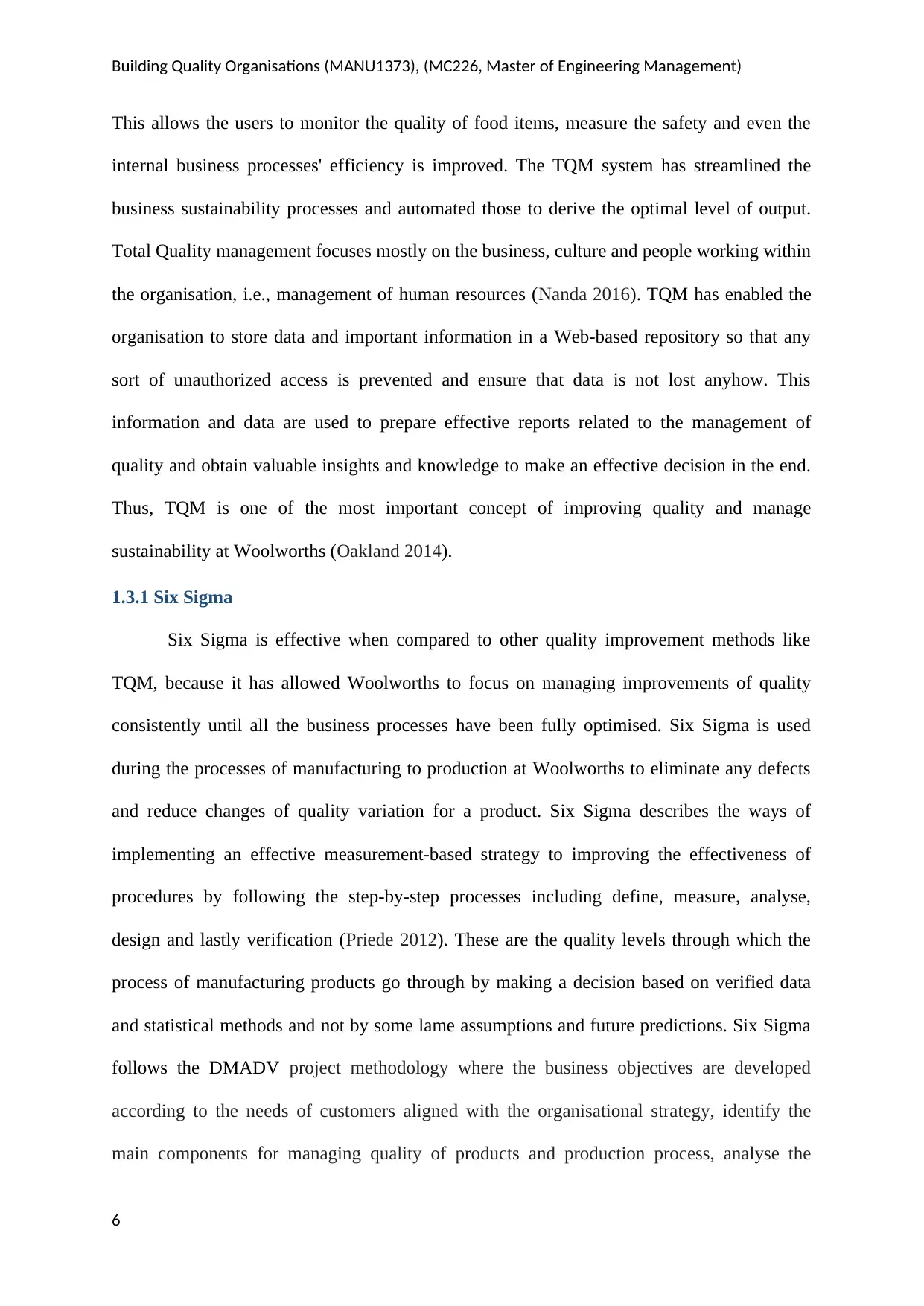
Building Quality Organisations (MANU1373), (MC226, Master of Engineering Management)
This allows the users to monitor the quality of food items, measure the safety and even the
internal business processes' efficiency is improved. The TQM system has streamlined the
business sustainability processes and automated those to derive the optimal level of output.
Total Quality management focuses mostly on the business, culture and people working within
the organisation, i.e., management of human resources (Nanda 2016). TQM has enabled the
organisation to store data and important information in a Web-based repository so that any
sort of unauthorized access is prevented and ensure that data is not lost anyhow. This
information and data are used to prepare effective reports related to the management of
quality and obtain valuable insights and knowledge to make an effective decision in the end.
Thus, TQM is one of the most important concept of improving quality and manage
sustainability at Woolworths (Oakland 2014).
1.3.1 Six Sigma
Six Sigma is effective when compared to other quality improvement methods like
TQM, because it has allowed Woolworths to focus on managing improvements of quality
consistently until all the business processes have been fully optimised. Six Sigma is used
during the processes of manufacturing to production at Woolworths to eliminate any defects
and reduce changes of quality variation for a product. Six Sigma describes the ways of
implementing an effective measurement-based strategy to improving the effectiveness of
procedures by following the step-by-step processes including define, measure, analyse,
design and lastly verification (Priede 2012). These are the quality levels through which the
process of manufacturing products go through by making a decision based on verified data
and statistical methods and not by some lame assumptions and future predictions. Six Sigma
follows the DMADV project methodology where the business objectives are developed
according to the needs of customers aligned with the organisational strategy, identify the
main components for managing quality of products and production process, analyse the
6
This allows the users to monitor the quality of food items, measure the safety and even the
internal business processes' efficiency is improved. The TQM system has streamlined the
business sustainability processes and automated those to derive the optimal level of output.
Total Quality management focuses mostly on the business, culture and people working within
the organisation, i.e., management of human resources (Nanda 2016). TQM has enabled the
organisation to store data and important information in a Web-based repository so that any
sort of unauthorized access is prevented and ensure that data is not lost anyhow. This
information and data are used to prepare effective reports related to the management of
quality and obtain valuable insights and knowledge to make an effective decision in the end.
Thus, TQM is one of the most important concept of improving quality and manage
sustainability at Woolworths (Oakland 2014).
1.3.1 Six Sigma
Six Sigma is effective when compared to other quality improvement methods like
TQM, because it has allowed Woolworths to focus on managing improvements of quality
consistently until all the business processes have been fully optimised. Six Sigma is used
during the processes of manufacturing to production at Woolworths to eliminate any defects
and reduce changes of quality variation for a product. Six Sigma describes the ways of
implementing an effective measurement-based strategy to improving the effectiveness of
procedures by following the step-by-step processes including define, measure, analyse,
design and lastly verification (Priede 2012). These are the quality levels through which the
process of manufacturing products go through by making a decision based on verified data
and statistical methods and not by some lame assumptions and future predictions. Six Sigma
follows the DMADV project methodology where the business objectives are developed
according to the needs of customers aligned with the organisational strategy, identify the
main components for managing quality of products and production process, analyse the
6
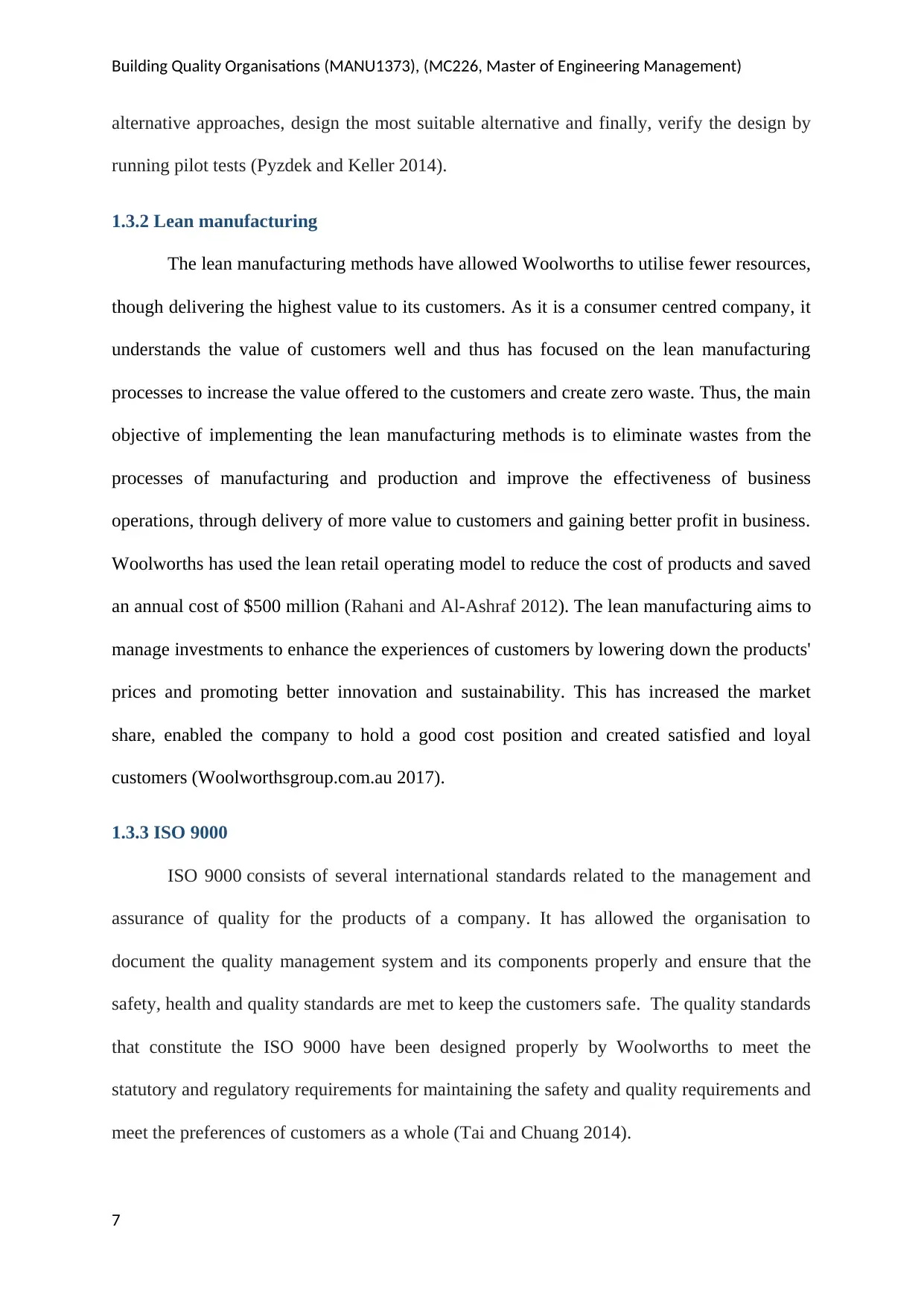
Building Quality Organisations (MANU1373), (MC226, Master of Engineering Management)
alternative approaches, design the most suitable alternative and finally, verify the design by
running pilot tests (Pyzdek and Keller 2014).
1.3.2 Lean manufacturing
The lean manufacturing methods have allowed Woolworths to utilise fewer resources,
though delivering the highest value to its customers. As it is a consumer centred company, it
understands the value of customers well and thus has focused on the lean manufacturing
processes to increase the value offered to the customers and create zero waste. Thus, the main
objective of implementing the lean manufacturing methods is to eliminate wastes from the
processes of manufacturing and production and improve the effectiveness of business
operations, through delivery of more value to customers and gaining better profit in business.
Woolworths has used the lean retail operating model to reduce the cost of products and saved
an annual cost of $500 million (Rahani and Al-Ashraf 2012). The lean manufacturing aims to
manage investments to enhance the experiences of customers by lowering down the products'
prices and promoting better innovation and sustainability. This has increased the market
share, enabled the company to hold a good cost position and created satisfied and loyal
customers (Woolworthsgroup.com.au 2017).
1.3.3 ISO 9000
ISO 9000 consists of several international standards related to the management and
assurance of quality for the products of a company. It has allowed the organisation to
document the quality management system and its components properly and ensure that the
safety, health and quality standards are met to keep the customers safe. The quality standards
that constitute the ISO 9000 have been designed properly by Woolworths to meet the
statutory and regulatory requirements for maintaining the safety and quality requirements and
meet the preferences of customers as a whole (Tai and Chuang 2014).
7
alternative approaches, design the most suitable alternative and finally, verify the design by
running pilot tests (Pyzdek and Keller 2014).
1.3.2 Lean manufacturing
The lean manufacturing methods have allowed Woolworths to utilise fewer resources,
though delivering the highest value to its customers. As it is a consumer centred company, it
understands the value of customers well and thus has focused on the lean manufacturing
processes to increase the value offered to the customers and create zero waste. Thus, the main
objective of implementing the lean manufacturing methods is to eliminate wastes from the
processes of manufacturing and production and improve the effectiveness of business
operations, through delivery of more value to customers and gaining better profit in business.
Woolworths has used the lean retail operating model to reduce the cost of products and saved
an annual cost of $500 million (Rahani and Al-Ashraf 2012). The lean manufacturing aims to
manage investments to enhance the experiences of customers by lowering down the products'
prices and promoting better innovation and sustainability. This has increased the market
share, enabled the company to hold a good cost position and created satisfied and loyal
customers (Woolworthsgroup.com.au 2017).
1.3.3 ISO 9000
ISO 9000 consists of several international standards related to the management and
assurance of quality for the products of a company. It has allowed the organisation to
document the quality management system and its components properly and ensure that the
safety, health and quality standards are met to keep the customers safe. The quality standards
that constitute the ISO 9000 have been designed properly by Woolworths to meet the
statutory and regulatory requirements for maintaining the safety and quality requirements and
meet the preferences of customers as a whole (Tai and Chuang 2014).
7
Paraphrase This Document
Need a fresh take? Get an instant paraphrase of this document with our AI Paraphraser
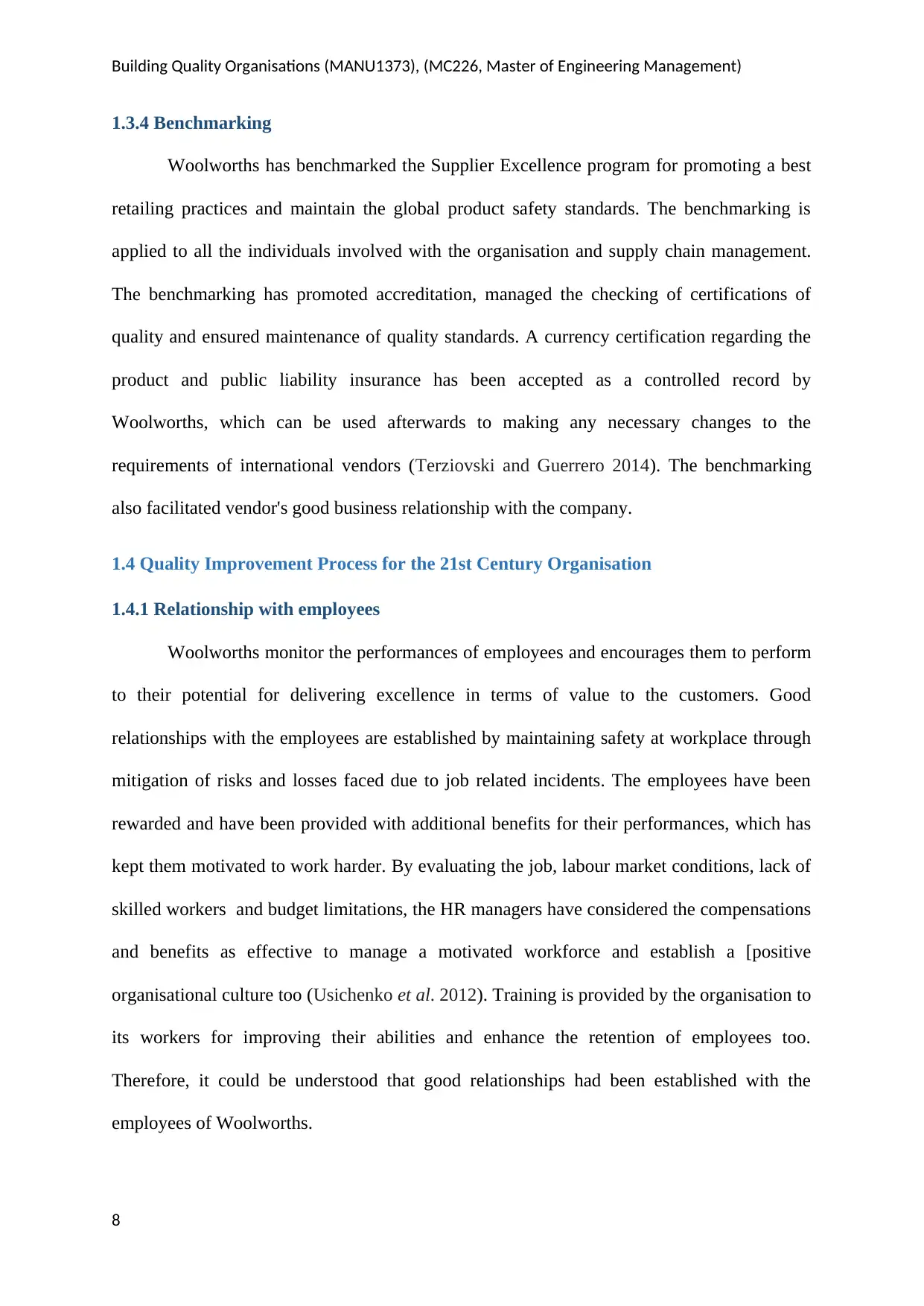
Building Quality Organisations (MANU1373), (MC226, Master of Engineering Management)
1.3.4 Benchmarking
Woolworths has benchmarked the Supplier Excellence program for promoting a best
retailing practices and maintain the global product safety standards. The benchmarking is
applied to all the individuals involved with the organisation and supply chain management.
The benchmarking has promoted accreditation, managed the checking of certifications of
quality and ensured maintenance of quality standards. A currency certification regarding the
product and public liability insurance has been accepted as a controlled record by
Woolworths, which can be used afterwards to making any necessary changes to the
requirements of international vendors (Terziovski and Guerrero 2014). The benchmarking
also facilitated vendor's good business relationship with the company.
1.4 Quality Improvement Process for the 21st Century Organisation
1.4.1 Relationship with employees
Woolworths monitor the performances of employees and encourages them to perform
to their potential for delivering excellence in terms of value to the customers. Good
relationships with the employees are established by maintaining safety at workplace through
mitigation of risks and losses faced due to job related incidents. The employees have been
rewarded and have been provided with additional benefits for their performances, which has
kept them motivated to work harder. By evaluating the job, labour market conditions, lack of
skilled workers and budget limitations, the HR managers have considered the compensations
and benefits as effective to manage a motivated workforce and establish a [positive
organisational culture too (Usichenko et al. 2012). Training is provided by the organisation to
its workers for improving their abilities and enhance the retention of employees too.
Therefore, it could be understood that good relationships had been established with the
employees of Woolworths.
8
1.3.4 Benchmarking
Woolworths has benchmarked the Supplier Excellence program for promoting a best
retailing practices and maintain the global product safety standards. The benchmarking is
applied to all the individuals involved with the organisation and supply chain management.
The benchmarking has promoted accreditation, managed the checking of certifications of
quality and ensured maintenance of quality standards. A currency certification regarding the
product and public liability insurance has been accepted as a controlled record by
Woolworths, which can be used afterwards to making any necessary changes to the
requirements of international vendors (Terziovski and Guerrero 2014). The benchmarking
also facilitated vendor's good business relationship with the company.
1.4 Quality Improvement Process for the 21st Century Organisation
1.4.1 Relationship with employees
Woolworths monitor the performances of employees and encourages them to perform
to their potential for delivering excellence in terms of value to the customers. Good
relationships with the employees are established by maintaining safety at workplace through
mitigation of risks and losses faced due to job related incidents. The employees have been
rewarded and have been provided with additional benefits for their performances, which has
kept them motivated to work harder. By evaluating the job, labour market conditions, lack of
skilled workers and budget limitations, the HR managers have considered the compensations
and benefits as effective to manage a motivated workforce and establish a [positive
organisational culture too (Usichenko et al. 2012). Training is provided by the organisation to
its workers for improving their abilities and enhance the retention of employees too.
Therefore, it could be understood that good relationships had been established with the
employees of Woolworths.
8
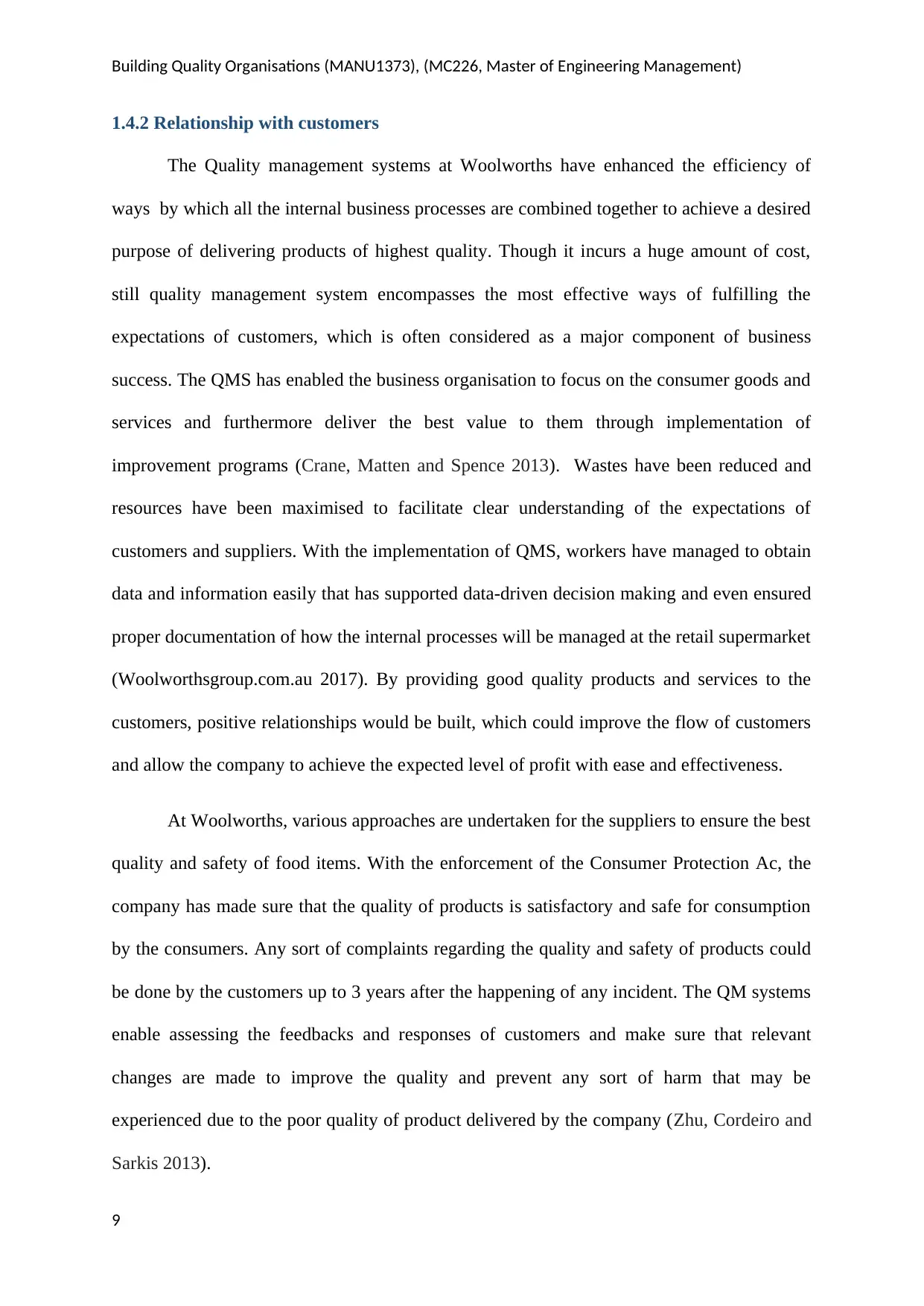
Building Quality Organisations (MANU1373), (MC226, Master of Engineering Management)
1.4.2 Relationship with customers
The Quality management systems at Woolworths have enhanced the efficiency of
ways by which all the internal business processes are combined together to achieve a desired
purpose of delivering products of highest quality. Though it incurs a huge amount of cost,
still quality management system encompasses the most effective ways of fulfilling the
expectations of customers, which is often considered as a major component of business
success. The QMS has enabled the business organisation to focus on the consumer goods and
services and furthermore deliver the best value to them through implementation of
improvement programs (Crane, Matten and Spence 2013). Wastes have been reduced and
resources have been maximised to facilitate clear understanding of the expectations of
customers and suppliers. With the implementation of QMS, workers have managed to obtain
data and information easily that has supported data-driven decision making and even ensured
proper documentation of how the internal processes will be managed at the retail supermarket
(Woolworthsgroup.com.au 2017). By providing good quality products and services to the
customers, positive relationships would be built, which could improve the flow of customers
and allow the company to achieve the expected level of profit with ease and effectiveness.
At Woolworths, various approaches are undertaken for the suppliers to ensure the best
quality and safety of food items. With the enforcement of the Consumer Protection Ac, the
company has made sure that the quality of products is satisfactory and safe for consumption
by the consumers. Any sort of complaints regarding the quality and safety of products could
be done by the customers up to 3 years after the happening of any incident. The QM systems
enable assessing the feedbacks and responses of customers and make sure that relevant
changes are made to improve the quality and prevent any sort of harm that may be
experienced due to the poor quality of product delivered by the company (Zhu, Cordeiro and
Sarkis 2013).
9
1.4.2 Relationship with customers
The Quality management systems at Woolworths have enhanced the efficiency of
ways by which all the internal business processes are combined together to achieve a desired
purpose of delivering products of highest quality. Though it incurs a huge amount of cost,
still quality management system encompasses the most effective ways of fulfilling the
expectations of customers, which is often considered as a major component of business
success. The QMS has enabled the business organisation to focus on the consumer goods and
services and furthermore deliver the best value to them through implementation of
improvement programs (Crane, Matten and Spence 2013). Wastes have been reduced and
resources have been maximised to facilitate clear understanding of the expectations of
customers and suppliers. With the implementation of QMS, workers have managed to obtain
data and information easily that has supported data-driven decision making and even ensured
proper documentation of how the internal processes will be managed at the retail supermarket
(Woolworthsgroup.com.au 2017). By providing good quality products and services to the
customers, positive relationships would be built, which could improve the flow of customers
and allow the company to achieve the expected level of profit with ease and effectiveness.
At Woolworths, various approaches are undertaken for the suppliers to ensure the best
quality and safety of food items. With the enforcement of the Consumer Protection Ac, the
company has made sure that the quality of products is satisfactory and safe for consumption
by the consumers. Any sort of complaints regarding the quality and safety of products could
be done by the customers up to 3 years after the happening of any incident. The QM systems
enable assessing the feedbacks and responses of customers and make sure that relevant
changes are made to improve the quality and prevent any sort of harm that may be
experienced due to the poor quality of product delivered by the company (Zhu, Cordeiro and
Sarkis 2013).
9
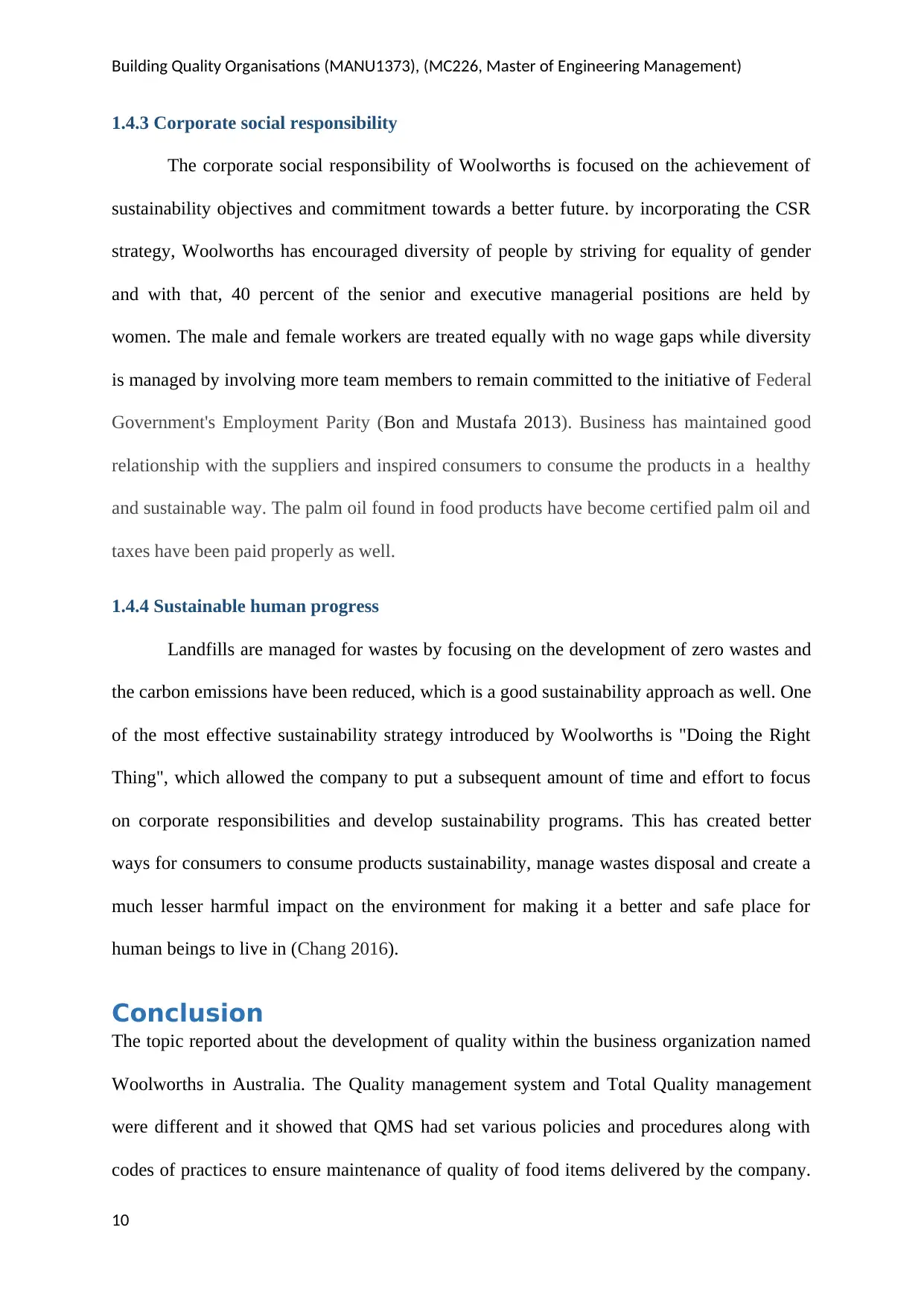
Building Quality Organisations (MANU1373), (MC226, Master of Engineering Management)
1.4.3 Corporate social responsibility
The corporate social responsibility of Woolworths is focused on the achievement of
sustainability objectives and commitment towards a better future. by incorporating the CSR
strategy, Woolworths has encouraged diversity of people by striving for equality of gender
and with that, 40 percent of the senior and executive managerial positions are held by
women. The male and female workers are treated equally with no wage gaps while diversity
is managed by involving more team members to remain committed to the initiative of Federal
Government's Employment Parity (Bon and Mustafa 2013). Business has maintained good
relationship with the suppliers and inspired consumers to consume the products in a healthy
and sustainable way. The palm oil found in food products have become certified palm oil and
taxes have been paid properly as well.
1.4.4 Sustainable human progress
Landfills are managed for wastes by focusing on the development of zero wastes and
the carbon emissions have been reduced, which is a good sustainability approach as well. One
of the most effective sustainability strategy introduced by Woolworths is "Doing the Right
Thing", which allowed the company to put a subsequent amount of time and effort to focus
on corporate responsibilities and develop sustainability programs. This has created better
ways for consumers to consume products sustainability, manage wastes disposal and create a
much lesser harmful impact on the environment for making it a better and safe place for
human beings to live in (Chang 2016).
Conclusion
The topic reported about the development of quality within the business organization named
Woolworths in Australia. The Quality management system and Total Quality management
were different and it showed that QMS had set various policies and procedures along with
codes of practices to ensure maintenance of quality of food items delivered by the company.
10
1.4.3 Corporate social responsibility
The corporate social responsibility of Woolworths is focused on the achievement of
sustainability objectives and commitment towards a better future. by incorporating the CSR
strategy, Woolworths has encouraged diversity of people by striving for equality of gender
and with that, 40 percent of the senior and executive managerial positions are held by
women. The male and female workers are treated equally with no wage gaps while diversity
is managed by involving more team members to remain committed to the initiative of Federal
Government's Employment Parity (Bon and Mustafa 2013). Business has maintained good
relationship with the suppliers and inspired consumers to consume the products in a healthy
and sustainable way. The palm oil found in food products have become certified palm oil and
taxes have been paid properly as well.
1.4.4 Sustainable human progress
Landfills are managed for wastes by focusing on the development of zero wastes and
the carbon emissions have been reduced, which is a good sustainability approach as well. One
of the most effective sustainability strategy introduced by Woolworths is "Doing the Right
Thing", which allowed the company to put a subsequent amount of time and effort to focus
on corporate responsibilities and develop sustainability programs. This has created better
ways for consumers to consume products sustainability, manage wastes disposal and create a
much lesser harmful impact on the environment for making it a better and safe place for
human beings to live in (Chang 2016).
Conclusion
The topic reported about the development of quality within the business organization named
Woolworths in Australia. The Quality management system and Total Quality management
were different and it showed that QMS had set various policies and procedures along with
codes of practices to ensure maintenance of quality of food items delivered by the company.
10
Secure Best Marks with AI Grader
Need help grading? Try our AI Grader for instant feedback on your assignments.
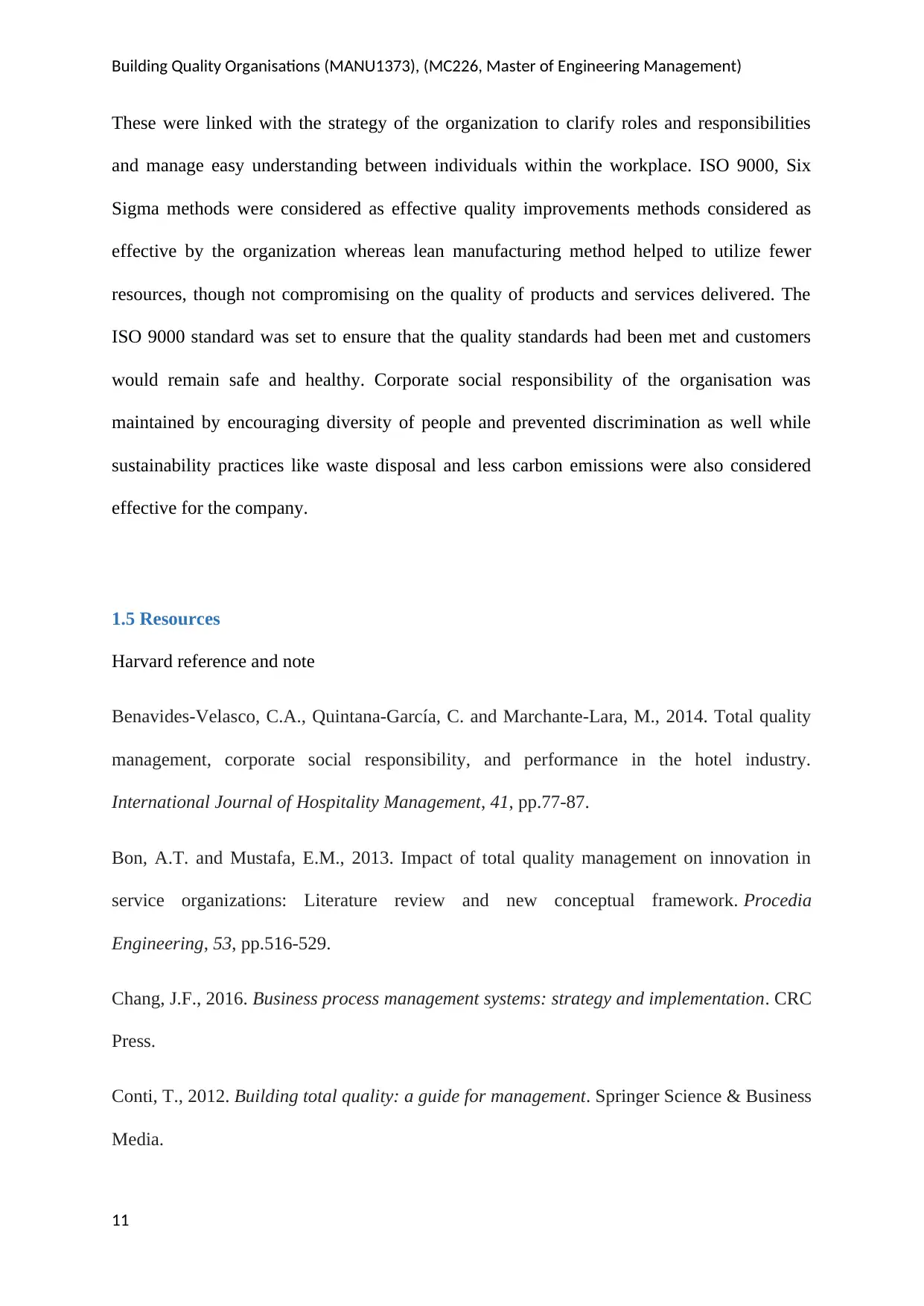
Building Quality Organisations (MANU1373), (MC226, Master of Engineering Management)
These were linked with the strategy of the organization to clarify roles and responsibilities
and manage easy understanding between individuals within the workplace. ISO 9000, Six
Sigma methods were considered as effective quality improvements methods considered as
effective by the organization whereas lean manufacturing method helped to utilize fewer
resources, though not compromising on the quality of products and services delivered. The
ISO 9000 standard was set to ensure that the quality standards had been met and customers
would remain safe and healthy. Corporate social responsibility of the organisation was
maintained by encouraging diversity of people and prevented discrimination as well while
sustainability practices like waste disposal and less carbon emissions were also considered
effective for the company.
1.5 Resources
Harvard reference and note
Benavides-Velasco, C.A., Quintana-García, C. and Marchante-Lara, M., 2014. Total quality
management, corporate social responsibility, and performance in the hotel industry.
International Journal of Hospitality Management, 41, pp.77-87.
Bon, A.T. and Mustafa, E.M., 2013. Impact of total quality management on innovation in
service organizations: Literature review and new conceptual framework. Procedia
Engineering, 53, pp.516-529.
Chang, J.F., 2016. Business process management systems: strategy and implementation. CRC
Press.
Conti, T., 2012. Building total quality: a guide for management. Springer Science & Business
Media.
11
These were linked with the strategy of the organization to clarify roles and responsibilities
and manage easy understanding between individuals within the workplace. ISO 9000, Six
Sigma methods were considered as effective quality improvements methods considered as
effective by the organization whereas lean manufacturing method helped to utilize fewer
resources, though not compromising on the quality of products and services delivered. The
ISO 9000 standard was set to ensure that the quality standards had been met and customers
would remain safe and healthy. Corporate social responsibility of the organisation was
maintained by encouraging diversity of people and prevented discrimination as well while
sustainability practices like waste disposal and less carbon emissions were also considered
effective for the company.
1.5 Resources
Harvard reference and note
Benavides-Velasco, C.A., Quintana-García, C. and Marchante-Lara, M., 2014. Total quality
management, corporate social responsibility, and performance in the hotel industry.
International Journal of Hospitality Management, 41, pp.77-87.
Bon, A.T. and Mustafa, E.M., 2013. Impact of total quality management on innovation in
service organizations: Literature review and new conceptual framework. Procedia
Engineering, 53, pp.516-529.
Chang, J.F., 2016. Business process management systems: strategy and implementation. CRC
Press.
Conti, T., 2012. Building total quality: a guide for management. Springer Science & Business
Media.
11
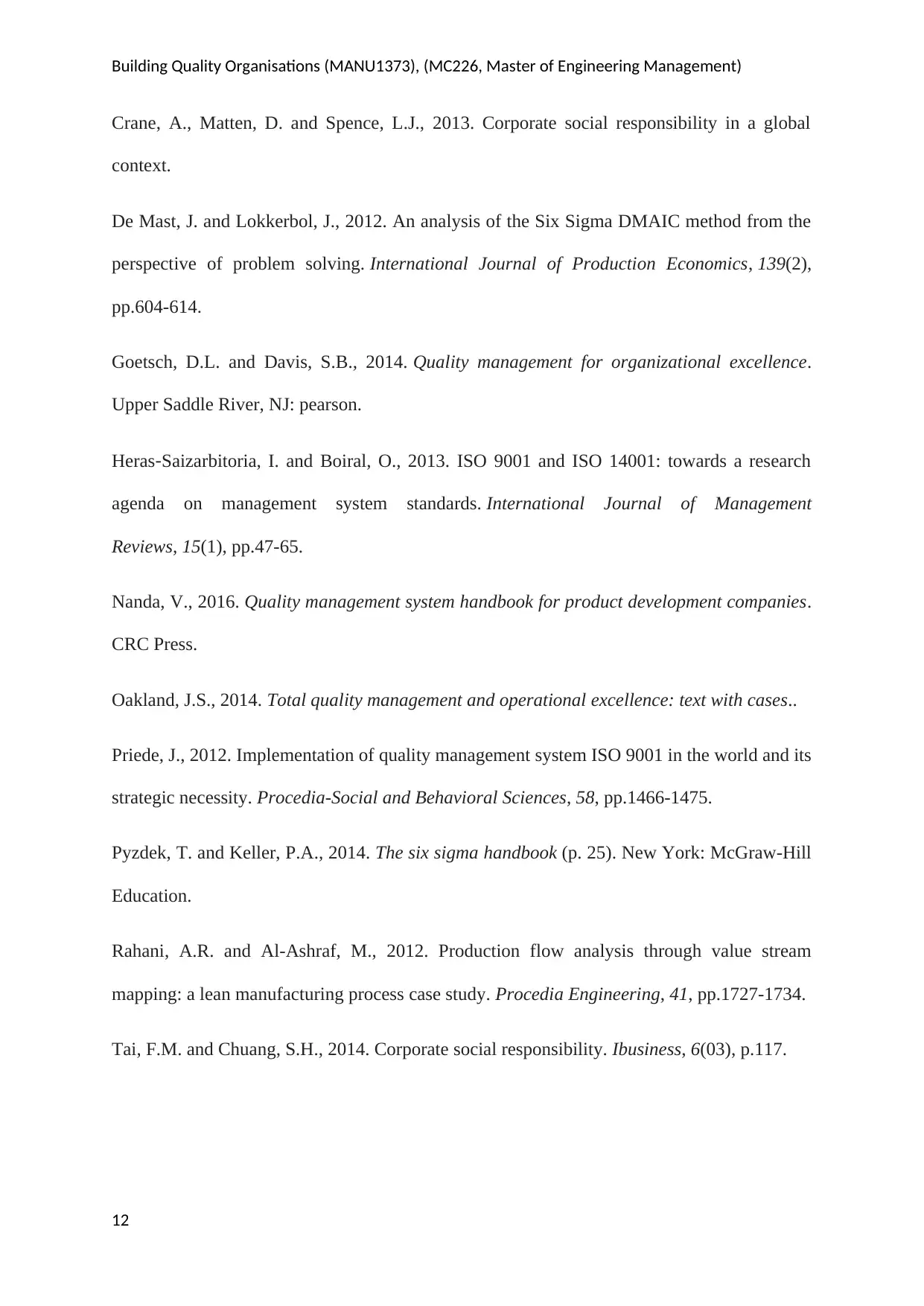
Building Quality Organisations (MANU1373), (MC226, Master of Engineering Management)
Crane, A., Matten, D. and Spence, L.J., 2013. Corporate social responsibility in a global
context.
De Mast, J. and Lokkerbol, J., 2012. An analysis of the Six Sigma DMAIC method from the
perspective of problem solving. International Journal of Production Economics, 139(2),
pp.604-614.
Goetsch, D.L. and Davis, S.B., 2014. Quality management for organizational excellence.
Upper Saddle River, NJ: pearson.
Heras‐Saizarbitoria, I. and Boiral, O., 2013. ISO 9001 and ISO 14001: towards a research
agenda on management system standards. International Journal of Management
Reviews, 15(1), pp.47-65.
Nanda, V., 2016. Quality management system handbook for product development companies.
CRC Press.
Oakland, J.S., 2014. Total quality management and operational excellence: text with cases..
Priede, J., 2012. Implementation of quality management system ISO 9001 in the world and its
strategic necessity. Procedia-Social and Behavioral Sciences, 58, pp.1466-1475.
Pyzdek, T. and Keller, P.A., 2014. The six sigma handbook (p. 25). New York: McGraw-Hill
Education.
Rahani, A.R. and Al-Ashraf, M., 2012. Production flow analysis through value stream
mapping: a lean manufacturing process case study. Procedia Engineering, 41, pp.1727-1734.
Tai, F.M. and Chuang, S.H., 2014. Corporate social responsibility. Ibusiness, 6(03), p.117.
12
Crane, A., Matten, D. and Spence, L.J., 2013. Corporate social responsibility in a global
context.
De Mast, J. and Lokkerbol, J., 2012. An analysis of the Six Sigma DMAIC method from the
perspective of problem solving. International Journal of Production Economics, 139(2),
pp.604-614.
Goetsch, D.L. and Davis, S.B., 2014. Quality management for organizational excellence.
Upper Saddle River, NJ: pearson.
Heras‐Saizarbitoria, I. and Boiral, O., 2013. ISO 9001 and ISO 14001: towards a research
agenda on management system standards. International Journal of Management
Reviews, 15(1), pp.47-65.
Nanda, V., 2016. Quality management system handbook for product development companies.
CRC Press.
Oakland, J.S., 2014. Total quality management and operational excellence: text with cases..
Priede, J., 2012. Implementation of quality management system ISO 9001 in the world and its
strategic necessity. Procedia-Social and Behavioral Sciences, 58, pp.1466-1475.
Pyzdek, T. and Keller, P.A., 2014. The six sigma handbook (p. 25). New York: McGraw-Hill
Education.
Rahani, A.R. and Al-Ashraf, M., 2012. Production flow analysis through value stream
mapping: a lean manufacturing process case study. Procedia Engineering, 41, pp.1727-1734.
Tai, F.M. and Chuang, S.H., 2014. Corporate social responsibility. Ibusiness, 6(03), p.117.
12
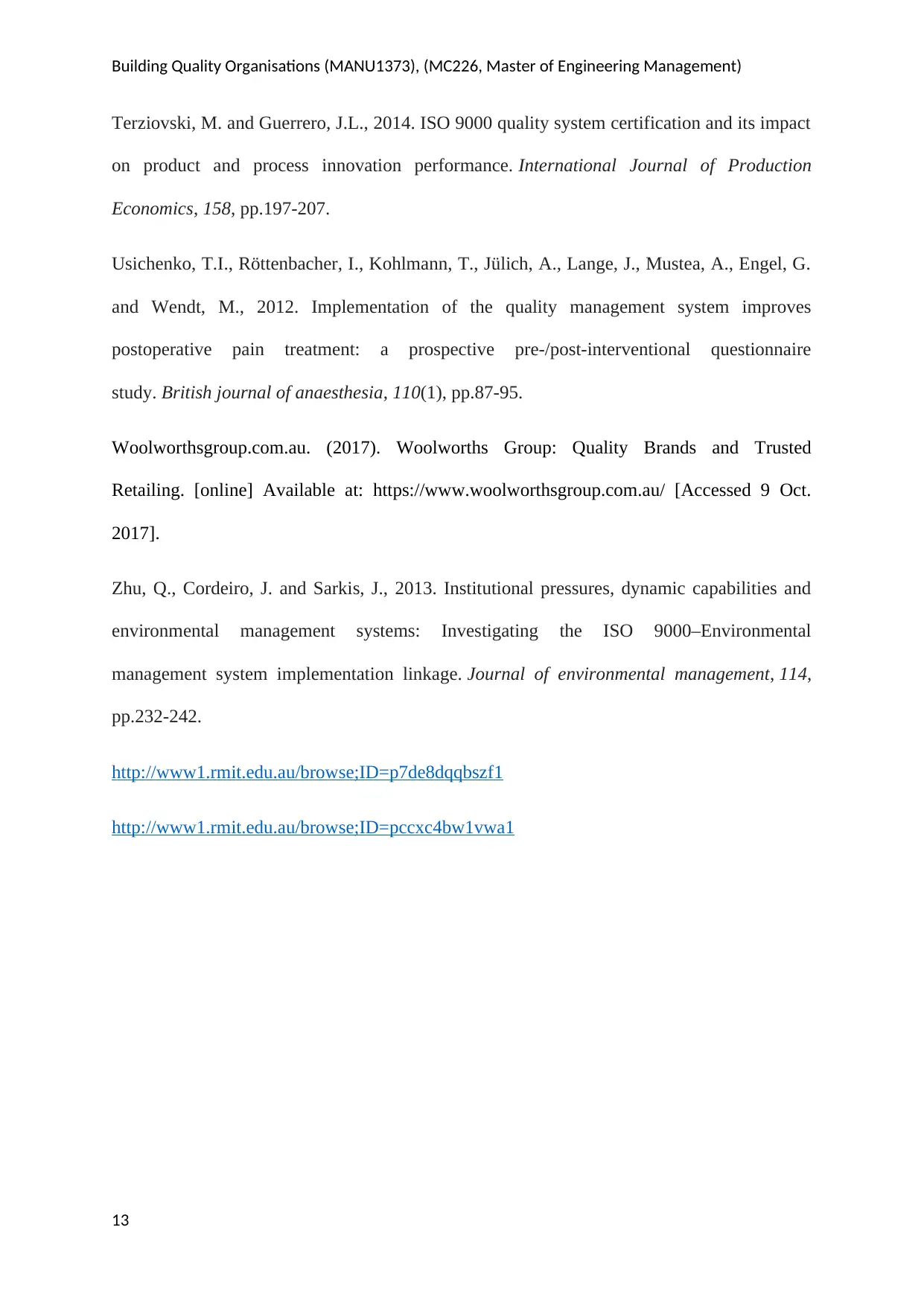
Building Quality Organisations (MANU1373), (MC226, Master of Engineering Management)
Terziovski, M. and Guerrero, J.L., 2014. ISO 9000 quality system certification and its impact
on product and process innovation performance. International Journal of Production
Economics, 158, pp.197-207.
Usichenko, T.I., Röttenbacher, I., Kohlmann, T., Jülich, A., Lange, J., Mustea, A., Engel, G.
and Wendt, M., 2012. Implementation of the quality management system improves
postoperative pain treatment: a prospective pre-/post-interventional questionnaire
study. British journal of anaesthesia, 110(1), pp.87-95.
Woolworthsgroup.com.au. (2017). Woolworths Group: Quality Brands and Trusted
Retailing. [online] Available at: https://www.woolworthsgroup.com.au/ [Accessed 9 Oct.
2017].
Zhu, Q., Cordeiro, J. and Sarkis, J., 2013. Institutional pressures, dynamic capabilities and
environmental management systems: Investigating the ISO 9000–Environmental
management system implementation linkage. Journal of environmental management, 114,
pp.232-242.
http://www1.rmit.edu.au/browse;ID=p7de8dqqbszf1
http://www1.rmit.edu.au/browse;ID=pccxc4bw1vwa1
13
Terziovski, M. and Guerrero, J.L., 2014. ISO 9000 quality system certification and its impact
on product and process innovation performance. International Journal of Production
Economics, 158, pp.197-207.
Usichenko, T.I., Röttenbacher, I., Kohlmann, T., Jülich, A., Lange, J., Mustea, A., Engel, G.
and Wendt, M., 2012. Implementation of the quality management system improves
postoperative pain treatment: a prospective pre-/post-interventional questionnaire
study. British journal of anaesthesia, 110(1), pp.87-95.
Woolworthsgroup.com.au. (2017). Woolworths Group: Quality Brands and Trusted
Retailing. [online] Available at: https://www.woolworthsgroup.com.au/ [Accessed 9 Oct.
2017].
Zhu, Q., Cordeiro, J. and Sarkis, J., 2013. Institutional pressures, dynamic capabilities and
environmental management systems: Investigating the ISO 9000–Environmental
management system implementation linkage. Journal of environmental management, 114,
pp.232-242.
http://www1.rmit.edu.au/browse;ID=p7de8dqqbszf1
http://www1.rmit.edu.au/browse;ID=pccxc4bw1vwa1
13
1 out of 13
Related Documents
![[object Object]](/_next/image/?url=%2F_next%2Fstatic%2Fmedia%2Flogo.6d15ce61.png&w=640&q=75)
Your All-in-One AI-Powered Toolkit for Academic Success.
+13062052269
info@desklib.com
Available 24*7 on WhatsApp / Email
Unlock your academic potential
© 2024 | Zucol Services PVT LTD | All rights reserved.