Operational Efficiency and Management
VerifiedAdded on 2020/10/22
|16
|4791
|498
AI Summary
This assignment explores the significance of operational management in businesses. It highlights the need for effective management to meet customer needs and build loyalty towards brands. Lean manufacturing is discussed as a method to minimize wastage and reduce costs. The importance of developing healthy relationships with employees, monitoring progress, and controlling operations are emphasized. Six sigma is also mentioned as an efficient approach to improve quality and produce satisfactory goods for buyers.
Contribute Materials
Your contribution can guide someone’s learning journey. Share your
documents today.
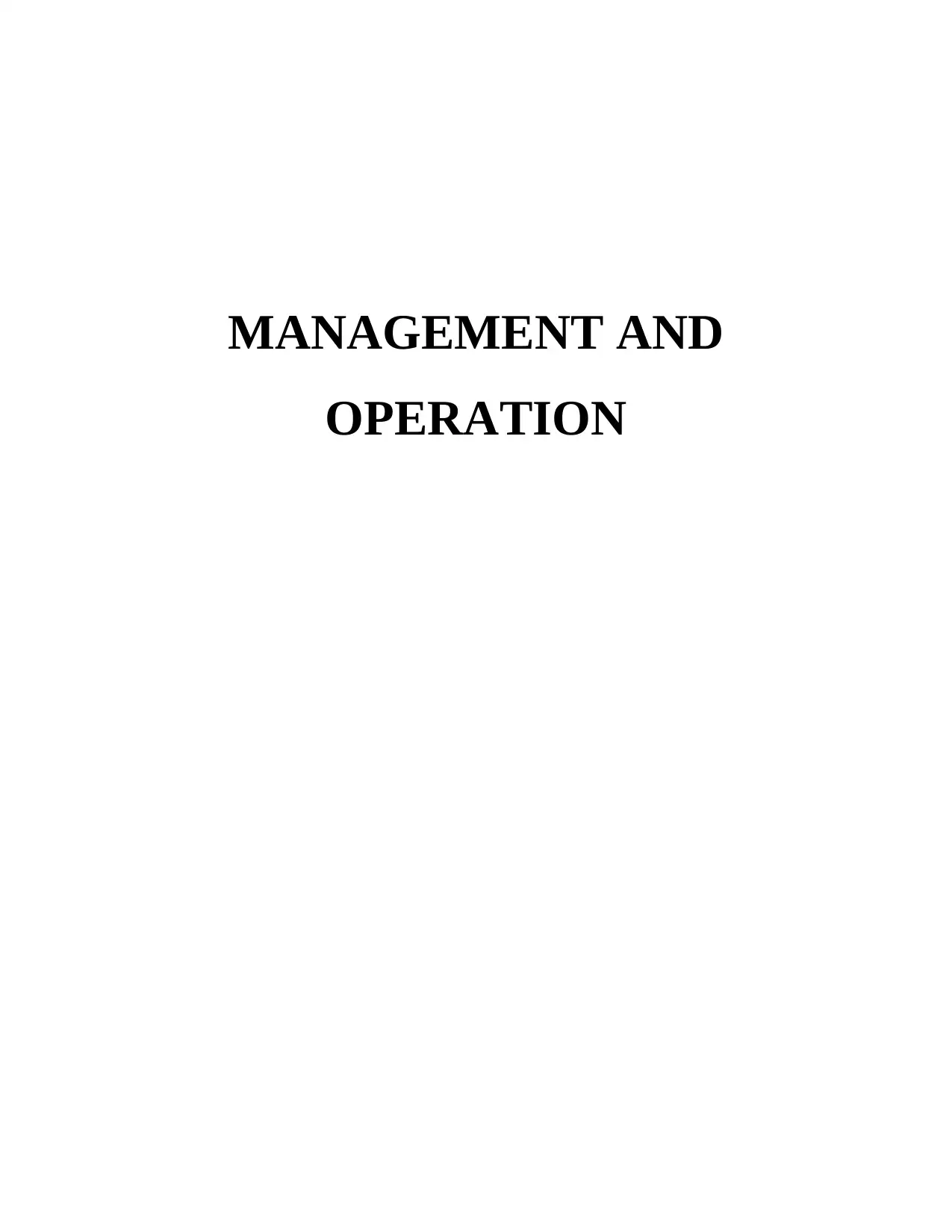
MANAGEMENT AND
OPERATION
OPERATION
Secure Best Marks with AI Grader
Need help grading? Try our AI Grader for instant feedback on your assignments.
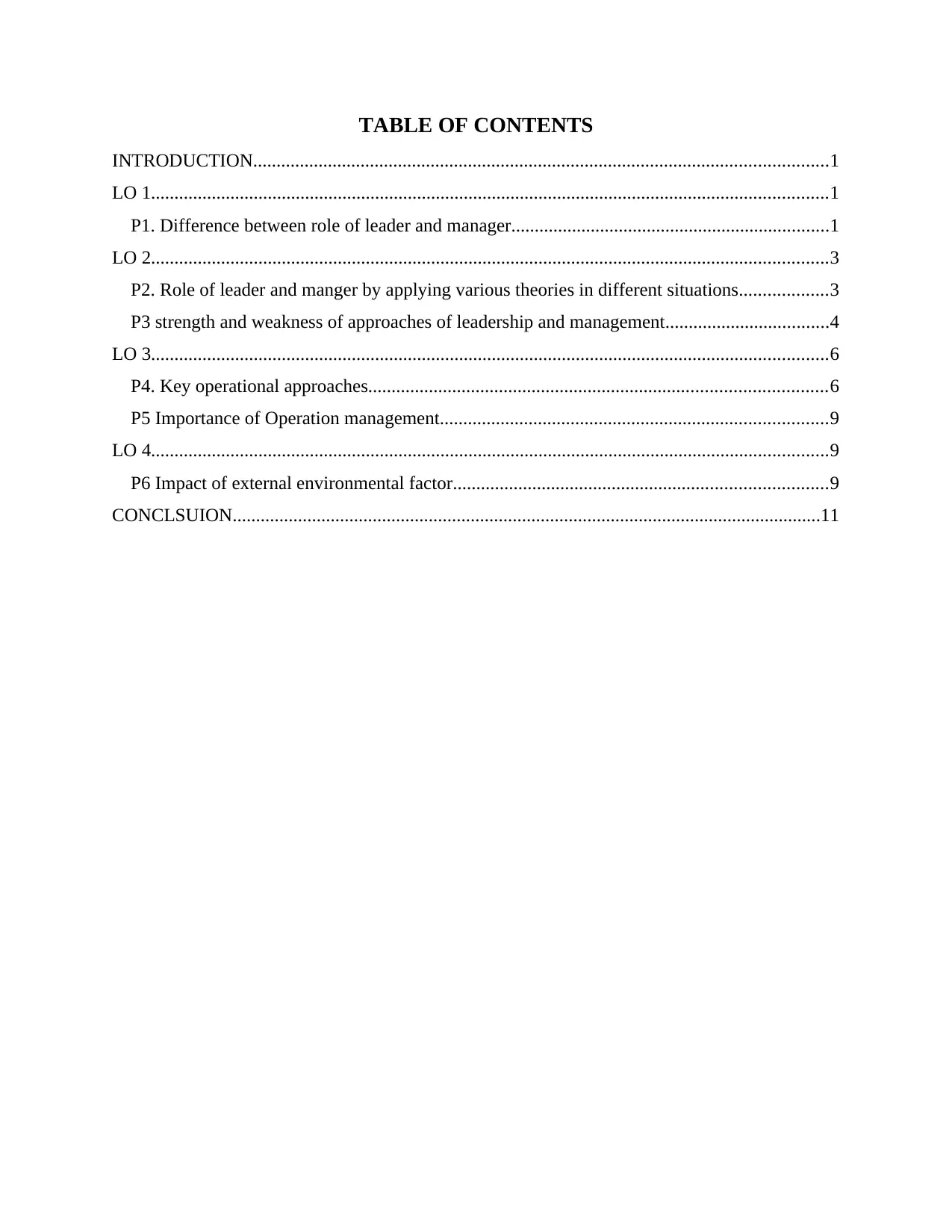
TABLE OF CONTENTS
INTRODUCTION...........................................................................................................................1
LO 1.................................................................................................................................................1
P1. Difference between role of leader and manager....................................................................1
LO 2.................................................................................................................................................3
P2. Role of leader and manger by applying various theories in different situations...................3
P3 strength and weakness of approaches of leadership and management...................................4
LO 3.................................................................................................................................................6
P4. Key operational approaches..................................................................................................6
P5 Importance of Operation management...................................................................................9
LO 4.................................................................................................................................................9
P6 Impact of external environmental factor................................................................................9
CONCLSUION..............................................................................................................................11
INTRODUCTION...........................................................................................................................1
LO 1.................................................................................................................................................1
P1. Difference between role of leader and manager....................................................................1
LO 2.................................................................................................................................................3
P2. Role of leader and manger by applying various theories in different situations...................3
P3 strength and weakness of approaches of leadership and management...................................4
LO 3.................................................................................................................................................6
P4. Key operational approaches..................................................................................................6
P5 Importance of Operation management...................................................................................9
LO 4.................................................................................................................................................9
P6 Impact of external environmental factor................................................................................9
CONCLSUION..............................................................................................................................11
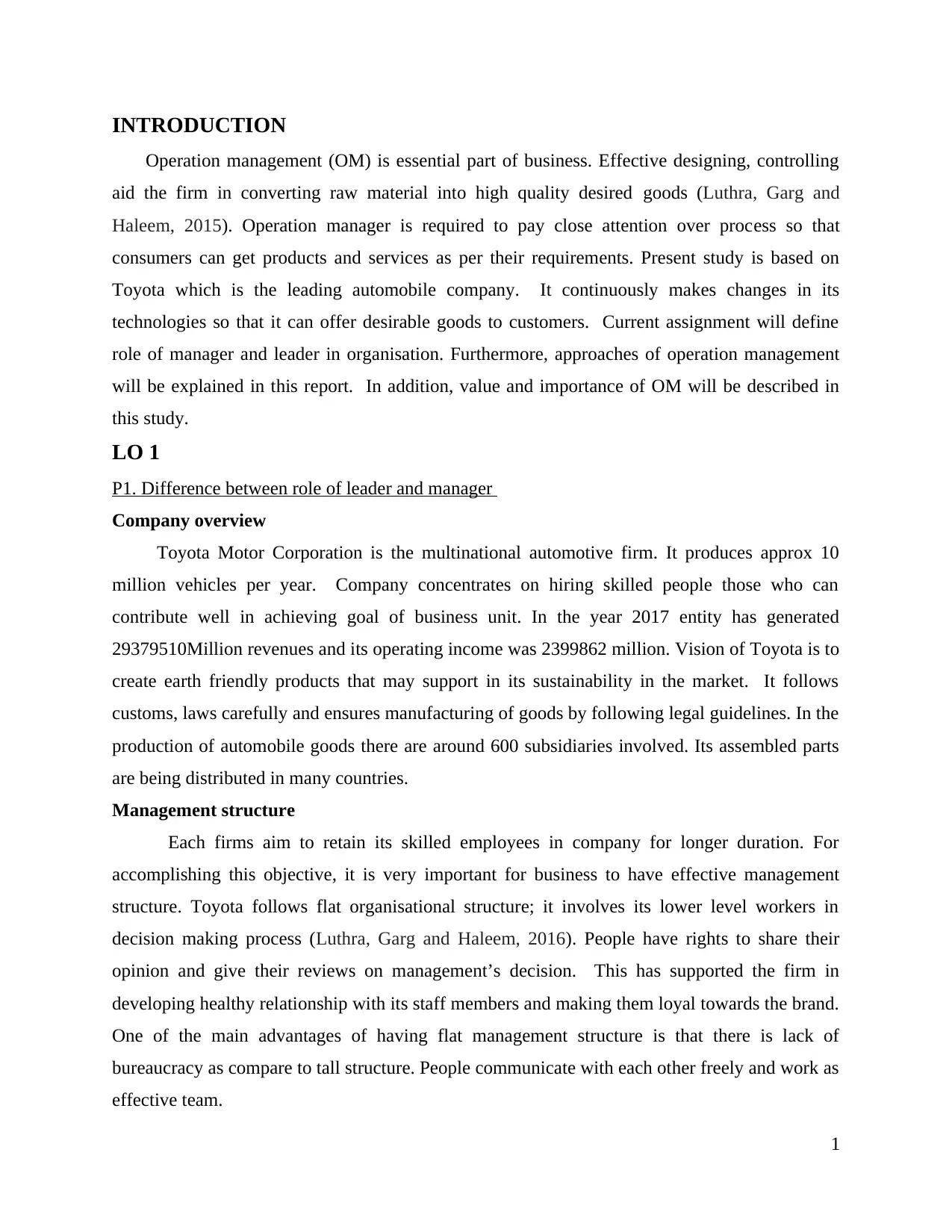
INTRODUCTION
Operation management (OM) is essential part of business. Effective designing, controlling
aid the firm in converting raw material into high quality desired goods (Luthra, Garg and
Haleem, 2015). Operation manager is required to pay close attention over process so that
consumers can get products and services as per their requirements. Present study is based on
Toyota which is the leading automobile company. It continuously makes changes in its
technologies so that it can offer desirable goods to customers. Current assignment will define
role of manager and leader in organisation. Furthermore, approaches of operation management
will be explained in this report. In addition, value and importance of OM will be described in
this study.
LO 1
P1. Difference between role of leader and manager
Company overview
Toyota Motor Corporation is the multinational automotive firm. It produces approx 10
million vehicles per year. Company concentrates on hiring skilled people those who can
contribute well in achieving goal of business unit. In the year 2017 entity has generated
29379510Million revenues and its operating income was 2399862 million. Vision of Toyota is to
create earth friendly products that may support in its sustainability in the market. It follows
customs, laws carefully and ensures manufacturing of goods by following legal guidelines. In the
production of automobile goods there are around 600 subsidiaries involved. Its assembled parts
are being distributed in many countries.
Management structure
Each firms aim to retain its skilled employees in company for longer duration. For
accomplishing this objective, it is very important for business to have effective management
structure. Toyota follows flat organisational structure; it involves its lower level workers in
decision making process (Luthra, Garg and Haleem, 2016). People have rights to share their
opinion and give their reviews on management’s decision. This has supported the firm in
developing healthy relationship with its staff members and making them loyal towards the brand.
One of the main advantages of having flat management structure is that there is lack of
bureaucracy as compare to tall structure. People communicate with each other freely and work as
effective team.
1
Operation management (OM) is essential part of business. Effective designing, controlling
aid the firm in converting raw material into high quality desired goods (Luthra, Garg and
Haleem, 2015). Operation manager is required to pay close attention over process so that
consumers can get products and services as per their requirements. Present study is based on
Toyota which is the leading automobile company. It continuously makes changes in its
technologies so that it can offer desirable goods to customers. Current assignment will define
role of manager and leader in organisation. Furthermore, approaches of operation management
will be explained in this report. In addition, value and importance of OM will be described in
this study.
LO 1
P1. Difference between role of leader and manager
Company overview
Toyota Motor Corporation is the multinational automotive firm. It produces approx 10
million vehicles per year. Company concentrates on hiring skilled people those who can
contribute well in achieving goal of business unit. In the year 2017 entity has generated
29379510Million revenues and its operating income was 2399862 million. Vision of Toyota is to
create earth friendly products that may support in its sustainability in the market. It follows
customs, laws carefully and ensures manufacturing of goods by following legal guidelines. In the
production of automobile goods there are around 600 subsidiaries involved. Its assembled parts
are being distributed in many countries.
Management structure
Each firms aim to retain its skilled employees in company for longer duration. For
accomplishing this objective, it is very important for business to have effective management
structure. Toyota follows flat organisational structure; it involves its lower level workers in
decision making process (Luthra, Garg and Haleem, 2016). People have rights to share their
opinion and give their reviews on management’s decision. This has supported the firm in
developing healthy relationship with its staff members and making them loyal towards the brand.
One of the main advantages of having flat management structure is that there is lack of
bureaucracy as compare to tall structure. People communicate with each other freely and work as
effective team.
1
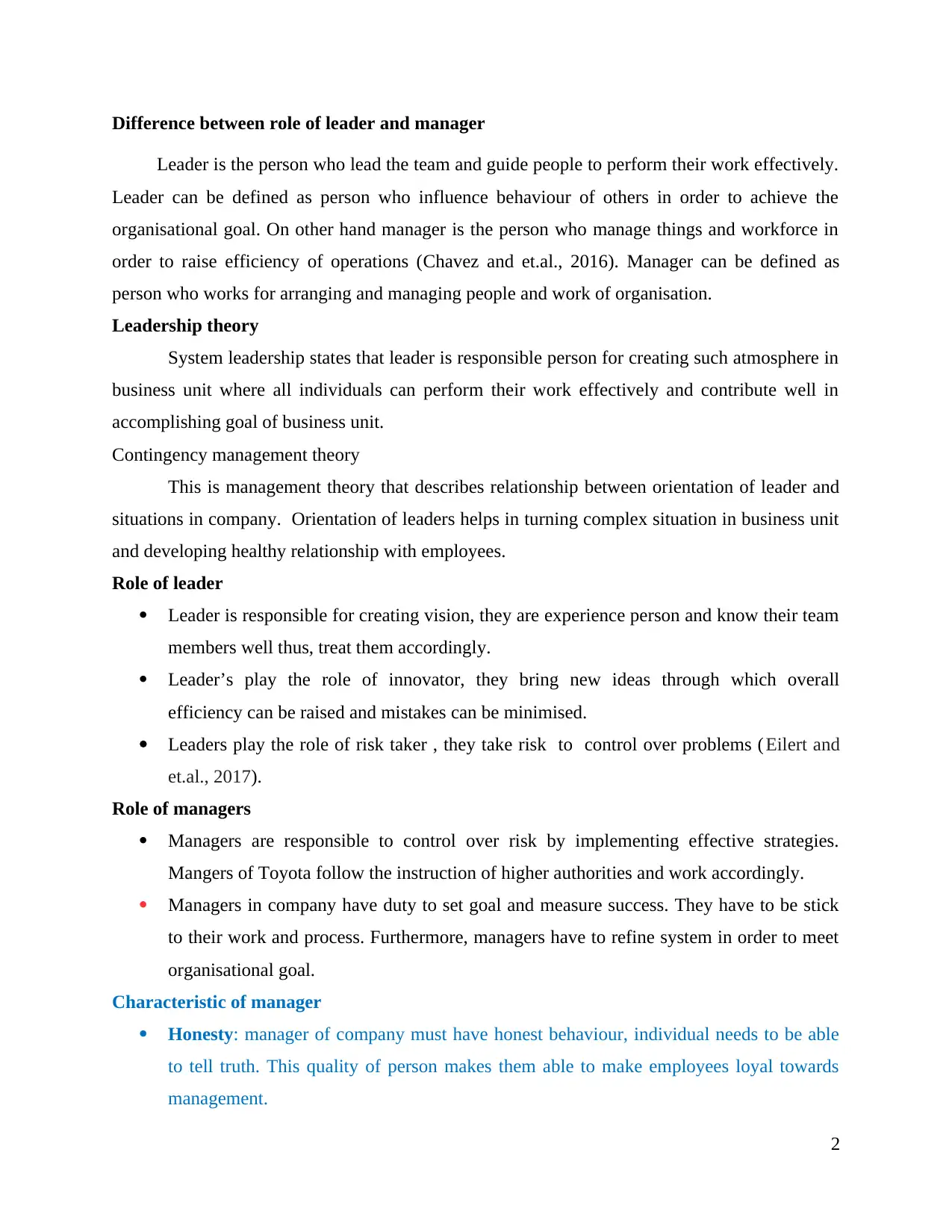
Difference between role of leader and manager
Leader is the person who lead the team and guide people to perform their work effectively.
Leader can be defined as person who influence behaviour of others in order to achieve the
organisational goal. On other hand manager is the person who manage things and workforce in
order to raise efficiency of operations (Chavez and et.al., 2016). Manager can be defined as
person who works for arranging and managing people and work of organisation.
Leadership theory
System leadership states that leader is responsible person for creating such atmosphere in
business unit where all individuals can perform their work effectively and contribute well in
accomplishing goal of business unit.
Contingency management theory
This is management theory that describes relationship between orientation of leader and
situations in company. Orientation of leaders helps in turning complex situation in business unit
and developing healthy relationship with employees.
Role of leader
Leader is responsible for creating vision, they are experience person and know their team
members well thus, treat them accordingly.
Leader’s play the role of innovator, they bring new ideas through which overall
efficiency can be raised and mistakes can be minimised.
Leaders play the role of risk taker , they take risk to control over problems ( Eilert and
et.al., 2017).
Role of managers
Managers are responsible to control over risk by implementing effective strategies.
Mangers of Toyota follow the instruction of higher authorities and work accordingly.
Managers in company have duty to set goal and measure success. They have to be stick
to their work and process. Furthermore, managers have to refine system in order to meet
organisational goal.
Characteristic of manager
Honesty: manager of company must have honest behaviour, individual needs to be able
to tell truth. This quality of person makes them able to make employees loyal towards
management.
2
Leader is the person who lead the team and guide people to perform their work effectively.
Leader can be defined as person who influence behaviour of others in order to achieve the
organisational goal. On other hand manager is the person who manage things and workforce in
order to raise efficiency of operations (Chavez and et.al., 2016). Manager can be defined as
person who works for arranging and managing people and work of organisation.
Leadership theory
System leadership states that leader is responsible person for creating such atmosphere in
business unit where all individuals can perform their work effectively and contribute well in
accomplishing goal of business unit.
Contingency management theory
This is management theory that describes relationship between orientation of leader and
situations in company. Orientation of leaders helps in turning complex situation in business unit
and developing healthy relationship with employees.
Role of leader
Leader is responsible for creating vision, they are experience person and know their team
members well thus, treat them accordingly.
Leader’s play the role of innovator, they bring new ideas through which overall
efficiency can be raised and mistakes can be minimised.
Leaders play the role of risk taker , they take risk to control over problems ( Eilert and
et.al., 2017).
Role of managers
Managers are responsible to control over risk by implementing effective strategies.
Mangers of Toyota follow the instruction of higher authorities and work accordingly.
Managers in company have duty to set goal and measure success. They have to be stick
to their work and process. Furthermore, managers have to refine system in order to meet
organisational goal.
Characteristic of manager
Honesty: manager of company must have honest behaviour, individual needs to be able
to tell truth. This quality of person makes them able to make employees loyal towards
management.
2
Secure Best Marks with AI Grader
Need help grading? Try our AI Grader for instant feedback on your assignments.
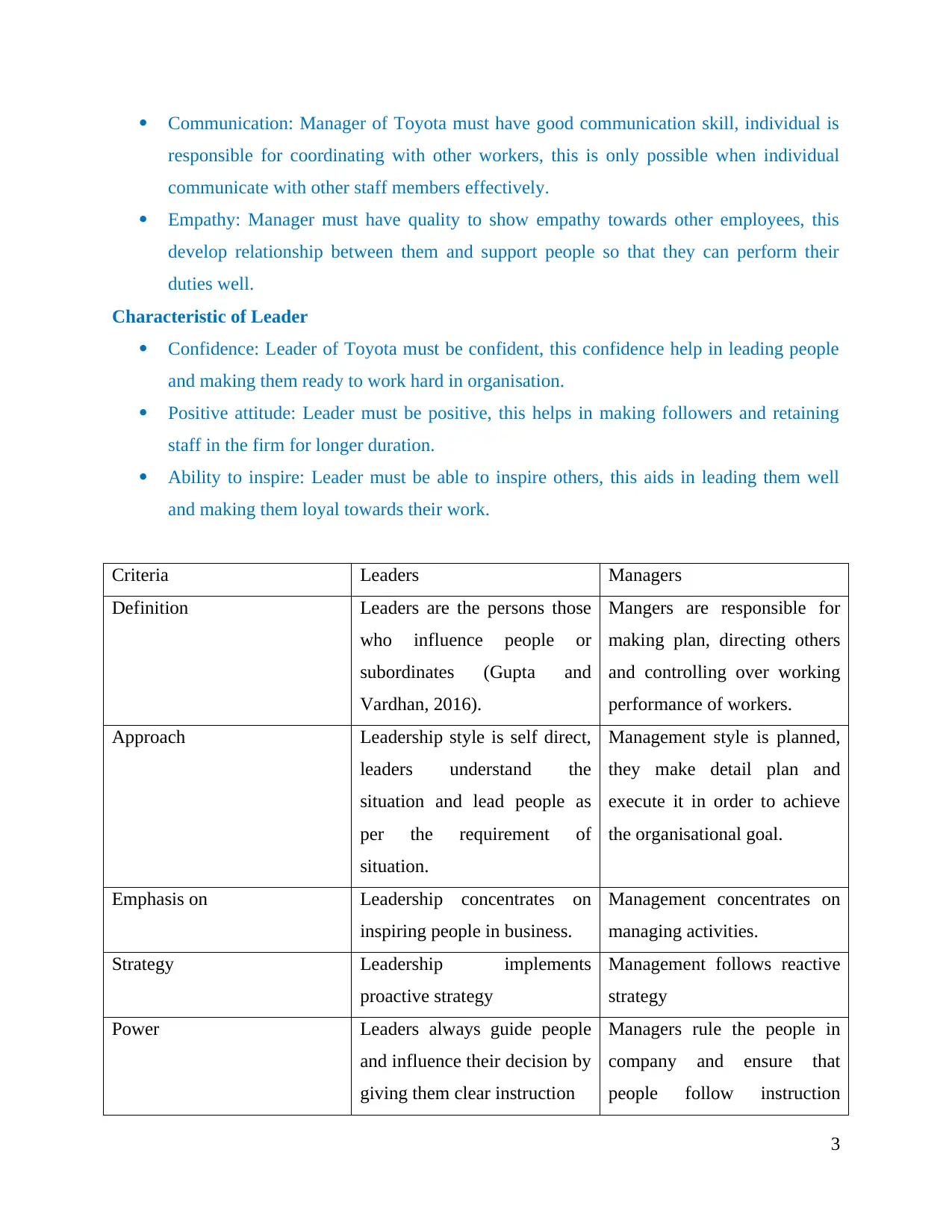
Communication: Manager of Toyota must have good communication skill, individual is
responsible for coordinating with other workers, this is only possible when individual
communicate with other staff members effectively.
Empathy: Manager must have quality to show empathy towards other employees, this
develop relationship between them and support people so that they can perform their
duties well.
Characteristic of Leader
Confidence: Leader of Toyota must be confident, this confidence help in leading people
and making them ready to work hard in organisation.
Positive attitude: Leader must be positive, this helps in making followers and retaining
staff in the firm for longer duration.
Ability to inspire: Leader must be able to inspire others, this aids in leading them well
and making them loyal towards their work.
Criteria Leaders Managers
Definition Leaders are the persons those
who influence people or
subordinates (Gupta and
Vardhan, 2016).
Mangers are responsible for
making plan, directing others
and controlling over working
performance of workers.
Approach Leadership style is self direct,
leaders understand the
situation and lead people as
per the requirement of
situation.
Management style is planned,
they make detail plan and
execute it in order to achieve
the organisational goal.
Emphasis on Leadership concentrates on
inspiring people in business.
Management concentrates on
managing activities.
Strategy Leadership implements
proactive strategy
Management follows reactive
strategy
Power Leaders always guide people
and influence their decision by
giving them clear instruction
Managers rule the people in
company and ensure that
people follow instruction
3
responsible for coordinating with other workers, this is only possible when individual
communicate with other staff members effectively.
Empathy: Manager must have quality to show empathy towards other employees, this
develop relationship between them and support people so that they can perform their
duties well.
Characteristic of Leader
Confidence: Leader of Toyota must be confident, this confidence help in leading people
and making them ready to work hard in organisation.
Positive attitude: Leader must be positive, this helps in making followers and retaining
staff in the firm for longer duration.
Ability to inspire: Leader must be able to inspire others, this aids in leading them well
and making them loyal towards their work.
Criteria Leaders Managers
Definition Leaders are the persons those
who influence people or
subordinates (Gupta and
Vardhan, 2016).
Mangers are responsible for
making plan, directing others
and controlling over working
performance of workers.
Approach Leadership style is self direct,
leaders understand the
situation and lead people as
per the requirement of
situation.
Management style is planned,
they make detail plan and
execute it in order to achieve
the organisational goal.
Emphasis on Leadership concentrates on
inspiring people in business.
Management concentrates on
managing activities.
Strategy Leadership implements
proactive strategy
Management follows reactive
strategy
Power Leaders always guide people
and influence their decision by
giving them clear instruction
Managers rule the people in
company and ensure that
people follow instruction
3
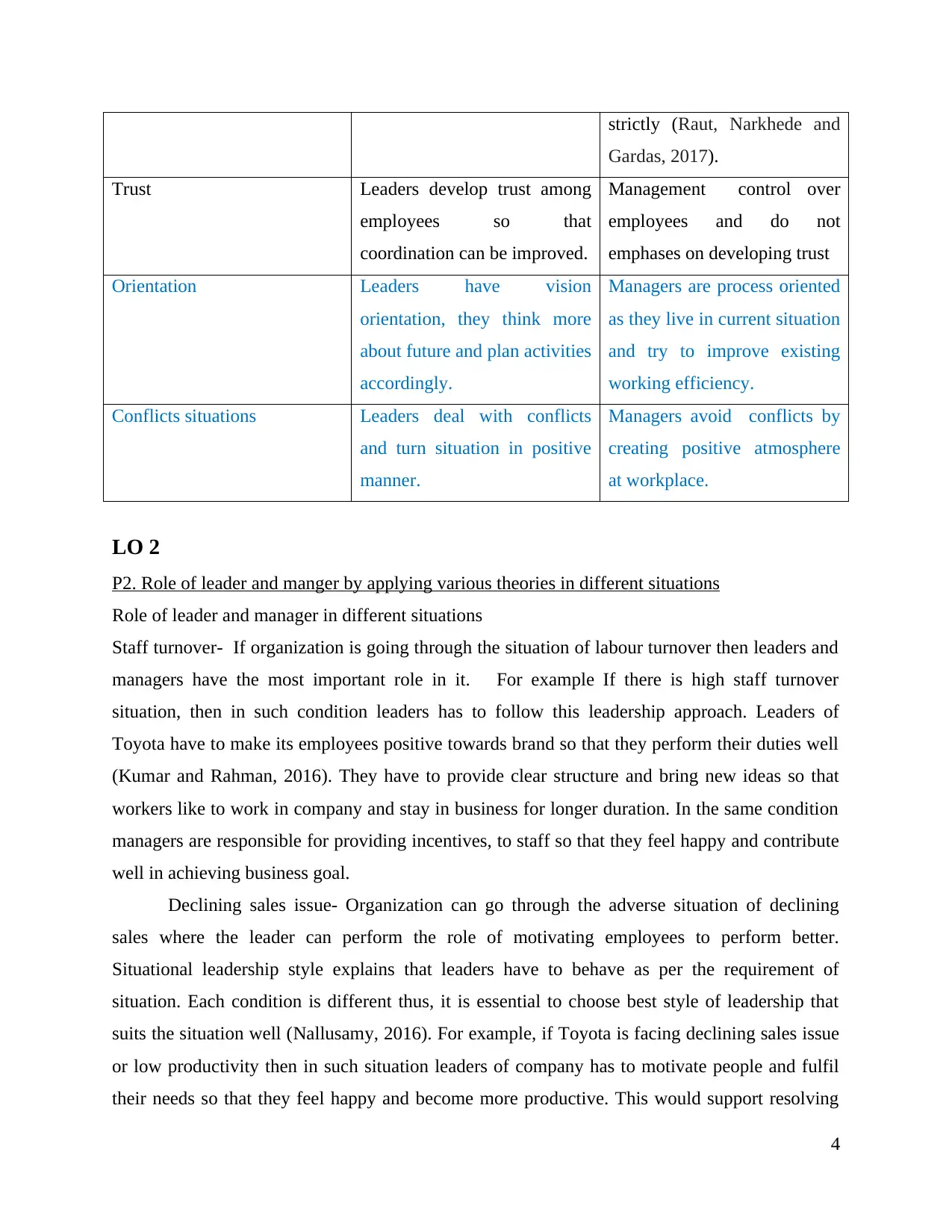
strictly (Raut, Narkhede and
Gardas, 2017).
Trust Leaders develop trust among
employees so that
coordination can be improved.
Management control over
employees and do not
emphases on developing trust
Orientation Leaders have vision
orientation, they think more
about future and plan activities
accordingly.
Managers are process oriented
as they live in current situation
and try to improve existing
working efficiency.
Conflicts situations Leaders deal with conflicts
and turn situation in positive
manner.
Managers avoid conflicts by
creating positive atmosphere
at workplace.
LO 2
P2. Role of leader and manger by applying various theories in different situations
Role of leader and manager in different situations
Staff turnover- If organization is going through the situation of labour turnover then leaders and
managers have the most important role in it. For example If there is high staff turnover
situation, then in such condition leaders has to follow this leadership approach. Leaders of
Toyota have to make its employees positive towards brand so that they perform their duties well
(Kumar and Rahman, 2016). They have to provide clear structure and bring new ideas so that
workers like to work in company and stay in business for longer duration. In the same condition
managers are responsible for providing incentives, to staff so that they feel happy and contribute
well in achieving business goal.
Declining sales issue- Organization can go through the adverse situation of declining
sales where the leader can perform the role of motivating employees to perform better.
Situational leadership style explains that leaders have to behave as per the requirement of
situation. Each condition is different thus, it is essential to choose best style of leadership that
suits the situation well (Nallusamy, 2016). For example, if Toyota is facing declining sales issue
or low productivity then in such situation leaders of company has to motivate people and fulfil
their needs so that they feel happy and become more productive. This would support resolving
4
Gardas, 2017).
Trust Leaders develop trust among
employees so that
coordination can be improved.
Management control over
employees and do not
emphases on developing trust
Orientation Leaders have vision
orientation, they think more
about future and plan activities
accordingly.
Managers are process oriented
as they live in current situation
and try to improve existing
working efficiency.
Conflicts situations Leaders deal with conflicts
and turn situation in positive
manner.
Managers avoid conflicts by
creating positive atmosphere
at workplace.
LO 2
P2. Role of leader and manger by applying various theories in different situations
Role of leader and manager in different situations
Staff turnover- If organization is going through the situation of labour turnover then leaders and
managers have the most important role in it. For example If there is high staff turnover
situation, then in such condition leaders has to follow this leadership approach. Leaders of
Toyota have to make its employees positive towards brand so that they perform their duties well
(Kumar and Rahman, 2016). They have to provide clear structure and bring new ideas so that
workers like to work in company and stay in business for longer duration. In the same condition
managers are responsible for providing incentives, to staff so that they feel happy and contribute
well in achieving business goal.
Declining sales issue- Organization can go through the adverse situation of declining
sales where the leader can perform the role of motivating employees to perform better.
Situational leadership style explains that leaders have to behave as per the requirement of
situation. Each condition is different thus, it is essential to choose best style of leadership that
suits the situation well (Nallusamy, 2016). For example, if Toyota is facing declining sales issue
or low productivity then in such situation leaders of company has to motivate people and fulfil
their needs so that they feel happy and become more productive. This would support resolving
4
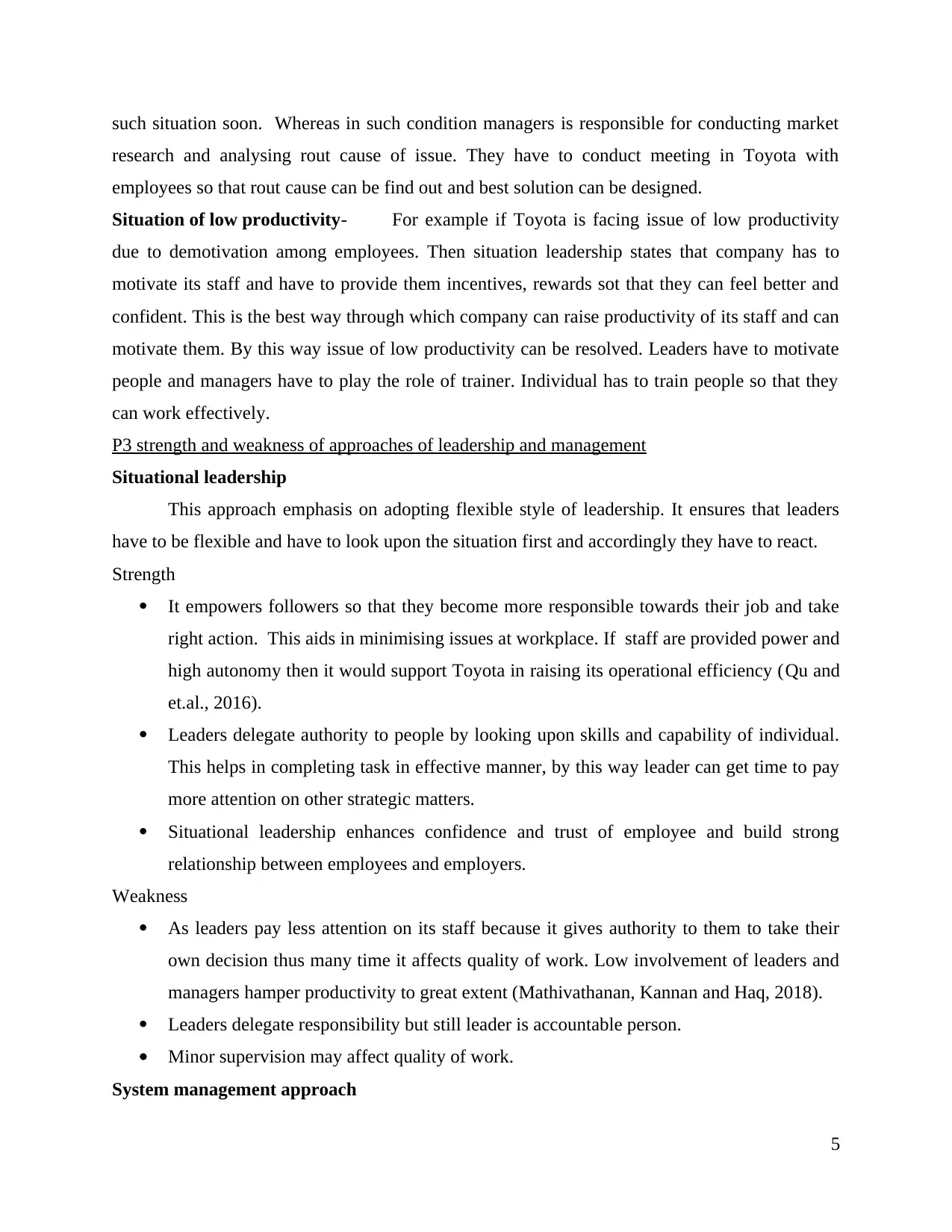
such situation soon. Whereas in such condition managers is responsible for conducting market
research and analysing rout cause of issue. They have to conduct meeting in Toyota with
employees so that rout cause can be find out and best solution can be designed.
Situation of low productivity- For example if Toyota is facing issue of low productivity
due to demotivation among employees. Then situation leadership states that company has to
motivate its staff and have to provide them incentives, rewards sot that they can feel better and
confident. This is the best way through which company can raise productivity of its staff and can
motivate them. By this way issue of low productivity can be resolved. Leaders have to motivate
people and managers have to play the role of trainer. Individual has to train people so that they
can work effectively.
P3 strength and weakness of approaches of leadership and management
Situational leadership
This approach emphasis on adopting flexible style of leadership. It ensures that leaders
have to be flexible and have to look upon the situation first and accordingly they have to react.
Strength
It empowers followers so that they become more responsible towards their job and take
right action. This aids in minimising issues at workplace. If staff are provided power and
high autonomy then it would support Toyota in raising its operational efficiency (Qu and
et.al., 2016).
Leaders delegate authority to people by looking upon skills and capability of individual.
This helps in completing task in effective manner, by this way leader can get time to pay
more attention on other strategic matters.
Situational leadership enhances confidence and trust of employee and build strong
relationship between employees and employers.
Weakness
As leaders pay less attention on its staff because it gives authority to them to take their
own decision thus many time it affects quality of work. Low involvement of leaders and
managers hamper productivity to great extent (Mathivathanan, Kannan and Haq, 2018).
Leaders delegate responsibility but still leader is accountable person.
Minor supervision may affect quality of work.
System management approach
5
research and analysing rout cause of issue. They have to conduct meeting in Toyota with
employees so that rout cause can be find out and best solution can be designed.
Situation of low productivity- For example if Toyota is facing issue of low productivity
due to demotivation among employees. Then situation leadership states that company has to
motivate its staff and have to provide them incentives, rewards sot that they can feel better and
confident. This is the best way through which company can raise productivity of its staff and can
motivate them. By this way issue of low productivity can be resolved. Leaders have to motivate
people and managers have to play the role of trainer. Individual has to train people so that they
can work effectively.
P3 strength and weakness of approaches of leadership and management
Situational leadership
This approach emphasis on adopting flexible style of leadership. It ensures that leaders
have to be flexible and have to look upon the situation first and accordingly they have to react.
Strength
It empowers followers so that they become more responsible towards their job and take
right action. This aids in minimising issues at workplace. If staff are provided power and
high autonomy then it would support Toyota in raising its operational efficiency (Qu and
et.al., 2016).
Leaders delegate authority to people by looking upon skills and capability of individual.
This helps in completing task in effective manner, by this way leader can get time to pay
more attention on other strategic matters.
Situational leadership enhances confidence and trust of employee and build strong
relationship between employees and employers.
Weakness
As leaders pay less attention on its staff because it gives authority to them to take their
own decision thus many time it affects quality of work. Low involvement of leaders and
managers hamper productivity to great extent (Mathivathanan, Kannan and Haq, 2018).
Leaders delegate responsibility but still leader is accountable person.
Minor supervision may affect quality of work.
System management approach
5
Paraphrase This Document
Need a fresh take? Get an instant paraphrase of this document with our AI Paraphraser
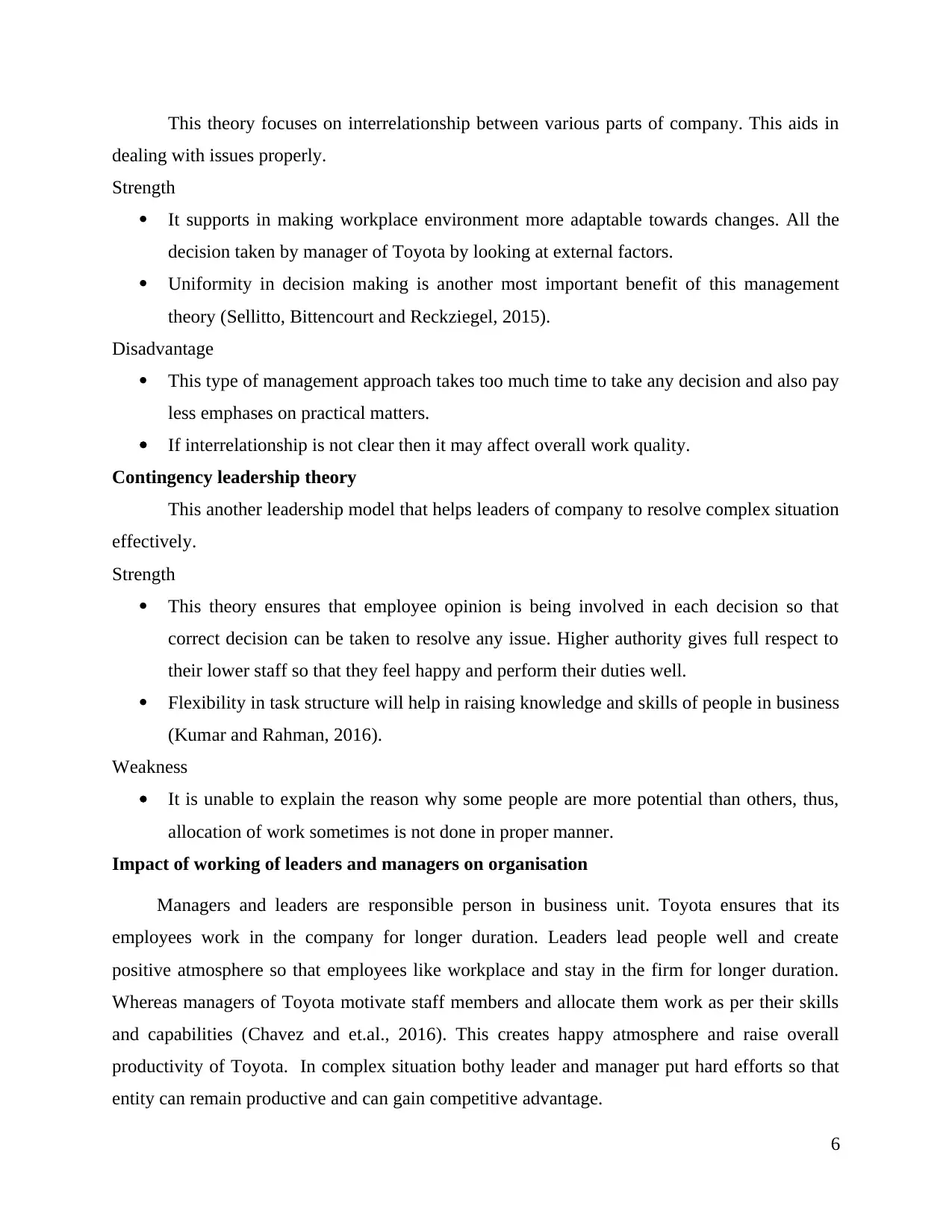
This theory focuses on interrelationship between various parts of company. This aids in
dealing with issues properly.
Strength
It supports in making workplace environment more adaptable towards changes. All the
decision taken by manager of Toyota by looking at external factors.
Uniformity in decision making is another most important benefit of this management
theory (Sellitto, Bittencourt and Reckziegel, 2015).
Disadvantage
This type of management approach takes too much time to take any decision and also pay
less emphases on practical matters.
If interrelationship is not clear then it may affect overall work quality.
Contingency leadership theory
This another leadership model that helps leaders of company to resolve complex situation
effectively.
Strength
This theory ensures that employee opinion is being involved in each decision so that
correct decision can be taken to resolve any issue. Higher authority gives full respect to
their lower staff so that they feel happy and perform their duties well.
Flexibility in task structure will help in raising knowledge and skills of people in business
(Kumar and Rahman, 2016).
Weakness
It is unable to explain the reason why some people are more potential than others, thus,
allocation of work sometimes is not done in proper manner.
Impact of working of leaders and managers on organisation
Managers and leaders are responsible person in business unit. Toyota ensures that its
employees work in the company for longer duration. Leaders lead people well and create
positive atmosphere so that employees like workplace and stay in the firm for longer duration.
Whereas managers of Toyota motivate staff members and allocate them work as per their skills
and capabilities (Chavez and et.al., 2016). This creates happy atmosphere and raise overall
productivity of Toyota. In complex situation bothy leader and manager put hard efforts so that
entity can remain productive and can gain competitive advantage.
6
dealing with issues properly.
Strength
It supports in making workplace environment more adaptable towards changes. All the
decision taken by manager of Toyota by looking at external factors.
Uniformity in decision making is another most important benefit of this management
theory (Sellitto, Bittencourt and Reckziegel, 2015).
Disadvantage
This type of management approach takes too much time to take any decision and also pay
less emphases on practical matters.
If interrelationship is not clear then it may affect overall work quality.
Contingency leadership theory
This another leadership model that helps leaders of company to resolve complex situation
effectively.
Strength
This theory ensures that employee opinion is being involved in each decision so that
correct decision can be taken to resolve any issue. Higher authority gives full respect to
their lower staff so that they feel happy and perform their duties well.
Flexibility in task structure will help in raising knowledge and skills of people in business
(Kumar and Rahman, 2016).
Weakness
It is unable to explain the reason why some people are more potential than others, thus,
allocation of work sometimes is not done in proper manner.
Impact of working of leaders and managers on organisation
Managers and leaders are responsible person in business unit. Toyota ensures that its
employees work in the company for longer duration. Leaders lead people well and create
positive atmosphere so that employees like workplace and stay in the firm for longer duration.
Whereas managers of Toyota motivate staff members and allocate them work as per their skills
and capabilities (Chavez and et.al., 2016). This creates happy atmosphere and raise overall
productivity of Toyota. In complex situation bothy leader and manager put hard efforts so that
entity can remain productive and can gain competitive advantage.
6
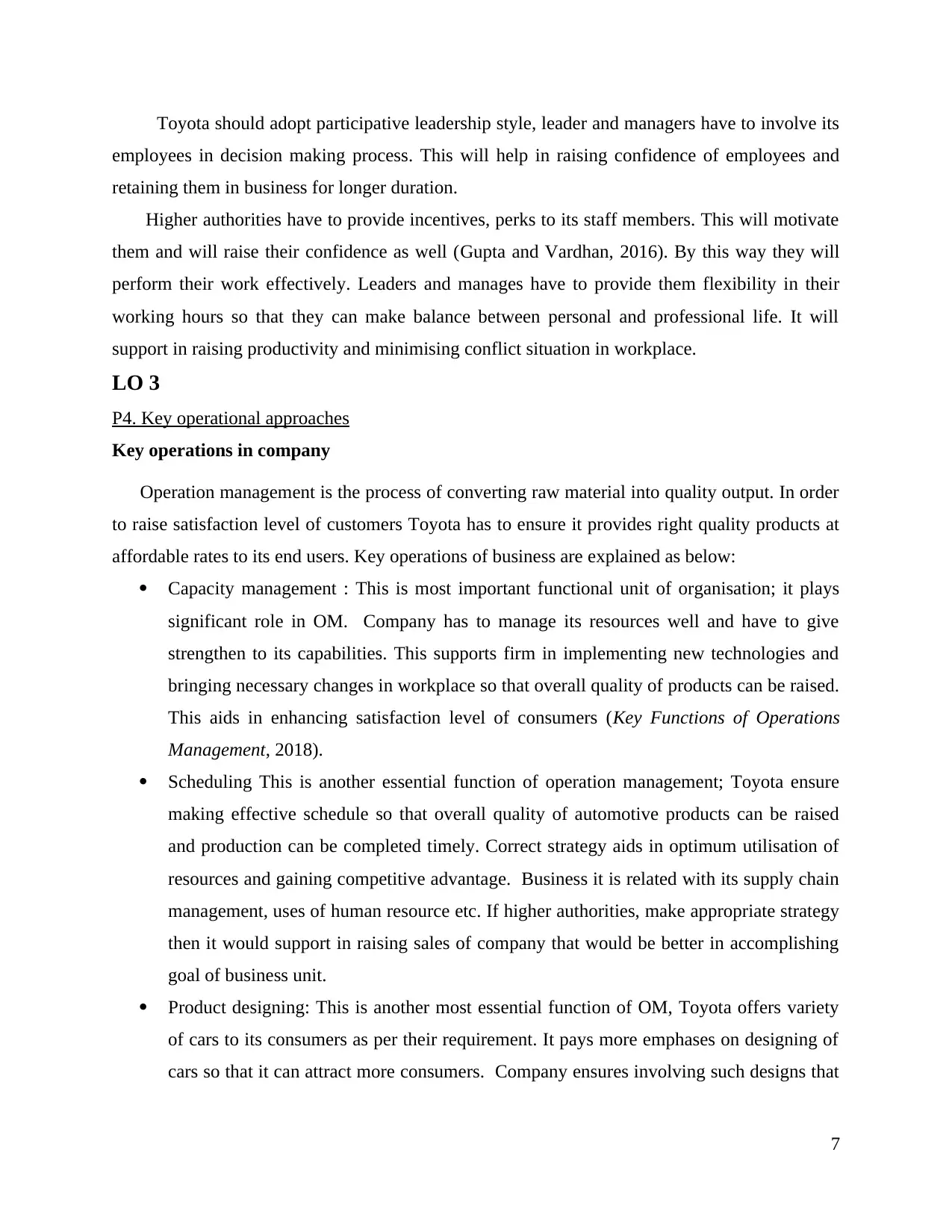
Toyota should adopt participative leadership style, leader and managers have to involve its
employees in decision making process. This will help in raising confidence of employees and
retaining them in business for longer duration.
Higher authorities have to provide incentives, perks to its staff members. This will motivate
them and will raise their confidence as well (Gupta and Vardhan, 2016). By this way they will
perform their work effectively. Leaders and manages have to provide them flexibility in their
working hours so that they can make balance between personal and professional life. It will
support in raising productivity and minimising conflict situation in workplace.
LO 3
P4. Key operational approaches
Key operations in company
Operation management is the process of converting raw material into quality output. In order
to raise satisfaction level of customers Toyota has to ensure it provides right quality products at
affordable rates to its end users. Key operations of business are explained as below:
Capacity management : This is most important functional unit of organisation; it plays
significant role in OM. Company has to manage its resources well and have to give
strengthen to its capabilities. This supports firm in implementing new technologies and
bringing necessary changes in workplace so that overall quality of products can be raised.
This aids in enhancing satisfaction level of consumers (Key Functions of Operations
Management, 2018).
Scheduling This is another essential function of operation management; Toyota ensure
making effective schedule so that overall quality of automotive products can be raised
and production can be completed timely. Correct strategy aids in optimum utilisation of
resources and gaining competitive advantage. Business it is related with its supply chain
management, uses of human resource etc. If higher authorities, make appropriate strategy
then it would support in raising sales of company that would be better in accomplishing
goal of business unit.
Product designing: This is another most essential function of OM, Toyota offers variety
of cars to its consumers as per their requirement. It pays more emphases on designing of
cars so that it can attract more consumers. Company ensures involving such designs that
7
employees in decision making process. This will help in raising confidence of employees and
retaining them in business for longer duration.
Higher authorities have to provide incentives, perks to its staff members. This will motivate
them and will raise their confidence as well (Gupta and Vardhan, 2016). By this way they will
perform their work effectively. Leaders and manages have to provide them flexibility in their
working hours so that they can make balance between personal and professional life. It will
support in raising productivity and minimising conflict situation in workplace.
LO 3
P4. Key operational approaches
Key operations in company
Operation management is the process of converting raw material into quality output. In order
to raise satisfaction level of customers Toyota has to ensure it provides right quality products at
affordable rates to its end users. Key operations of business are explained as below:
Capacity management : This is most important functional unit of organisation; it plays
significant role in OM. Company has to manage its resources well and have to give
strengthen to its capabilities. This supports firm in implementing new technologies and
bringing necessary changes in workplace so that overall quality of products can be raised.
This aids in enhancing satisfaction level of consumers (Key Functions of Operations
Management, 2018).
Scheduling This is another essential function of operation management; Toyota ensure
making effective schedule so that overall quality of automotive products can be raised
and production can be completed timely. Correct strategy aids in optimum utilisation of
resources and gaining competitive advantage. Business it is related with its supply chain
management, uses of human resource etc. If higher authorities, make appropriate strategy
then it would support in raising sales of company that would be better in accomplishing
goal of business unit.
Product designing: This is another most essential function of OM, Toyota offers variety
of cars to its consumers as per their requirement. It pays more emphases on designing of
cars so that it can attract more consumers. Company ensures involving such designs that
7
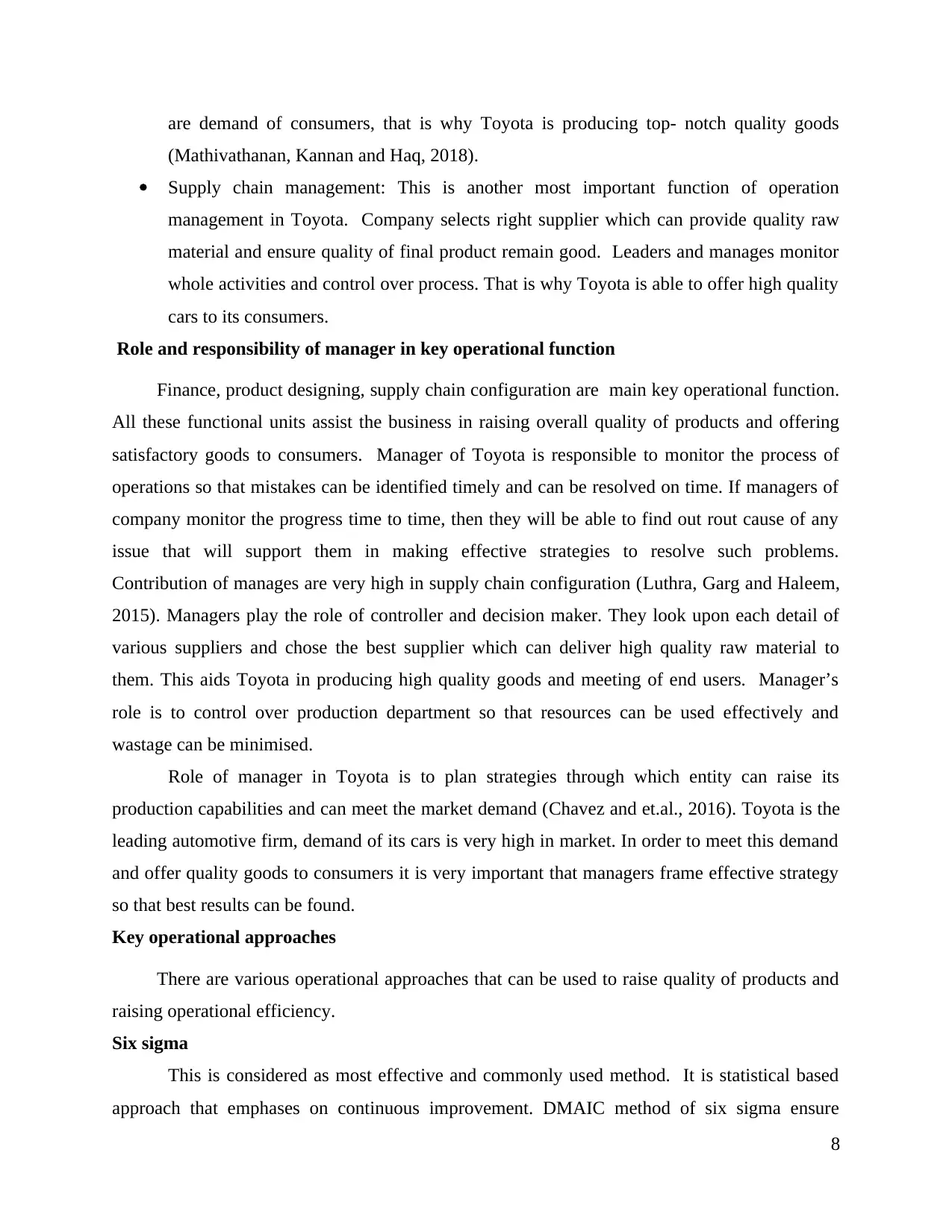
are demand of consumers, that is why Toyota is producing top- notch quality goods
(Mathivathanan, Kannan and Haq, 2018).
Supply chain management: This is another most important function of operation
management in Toyota. Company selects right supplier which can provide quality raw
material and ensure quality of final product remain good. Leaders and manages monitor
whole activities and control over process. That is why Toyota is able to offer high quality
cars to its consumers.
Role and responsibility of manager in key operational function
Finance, product designing, supply chain configuration are main key operational function.
All these functional units assist the business in raising overall quality of products and offering
satisfactory goods to consumers. Manager of Toyota is responsible to monitor the process of
operations so that mistakes can be identified timely and can be resolved on time. If managers of
company monitor the progress time to time, then they will be able to find out rout cause of any
issue that will support them in making effective strategies to resolve such problems.
Contribution of manages are very high in supply chain configuration (Luthra, Garg and Haleem,
2015). Managers play the role of controller and decision maker. They look upon each detail of
various suppliers and chose the best supplier which can deliver high quality raw material to
them. This aids Toyota in producing high quality goods and meeting of end users. Manager’s
role is to control over production department so that resources can be used effectively and
wastage can be minimised.
Role of manager in Toyota is to plan strategies through which entity can raise its
production capabilities and can meet the market demand (Chavez and et.al., 2016). Toyota is the
leading automotive firm, demand of its cars is very high in market. In order to meet this demand
and offer quality goods to consumers it is very important that managers frame effective strategy
so that best results can be found.
Key operational approaches
There are various operational approaches that can be used to raise quality of products and
raising operational efficiency.
Six sigma
This is considered as most effective and commonly used method. It is statistical based
approach that emphases on continuous improvement. DMAIC method of six sigma ensure
8
(Mathivathanan, Kannan and Haq, 2018).
Supply chain management: This is another most important function of operation
management in Toyota. Company selects right supplier which can provide quality raw
material and ensure quality of final product remain good. Leaders and manages monitor
whole activities and control over process. That is why Toyota is able to offer high quality
cars to its consumers.
Role and responsibility of manager in key operational function
Finance, product designing, supply chain configuration are main key operational function.
All these functional units assist the business in raising overall quality of products and offering
satisfactory goods to consumers. Manager of Toyota is responsible to monitor the process of
operations so that mistakes can be identified timely and can be resolved on time. If managers of
company monitor the progress time to time, then they will be able to find out rout cause of any
issue that will support them in making effective strategies to resolve such problems.
Contribution of manages are very high in supply chain configuration (Luthra, Garg and Haleem,
2015). Managers play the role of controller and decision maker. They look upon each detail of
various suppliers and chose the best supplier which can deliver high quality raw material to
them. This aids Toyota in producing high quality goods and meeting of end users. Manager’s
role is to control over production department so that resources can be used effectively and
wastage can be minimised.
Role of manager in Toyota is to plan strategies through which entity can raise its
production capabilities and can meet the market demand (Chavez and et.al., 2016). Toyota is the
leading automotive firm, demand of its cars is very high in market. In order to meet this demand
and offer quality goods to consumers it is very important that managers frame effective strategy
so that best results can be found.
Key operational approaches
There are various operational approaches that can be used to raise quality of products and
raising operational efficiency.
Six sigma
This is considered as most effective and commonly used method. It is statistical based
approach that emphases on continuous improvement. DMAIC method of six sigma ensure
8
Secure Best Marks with AI Grader
Need help grading? Try our AI Grader for instant feedback on your assignments.
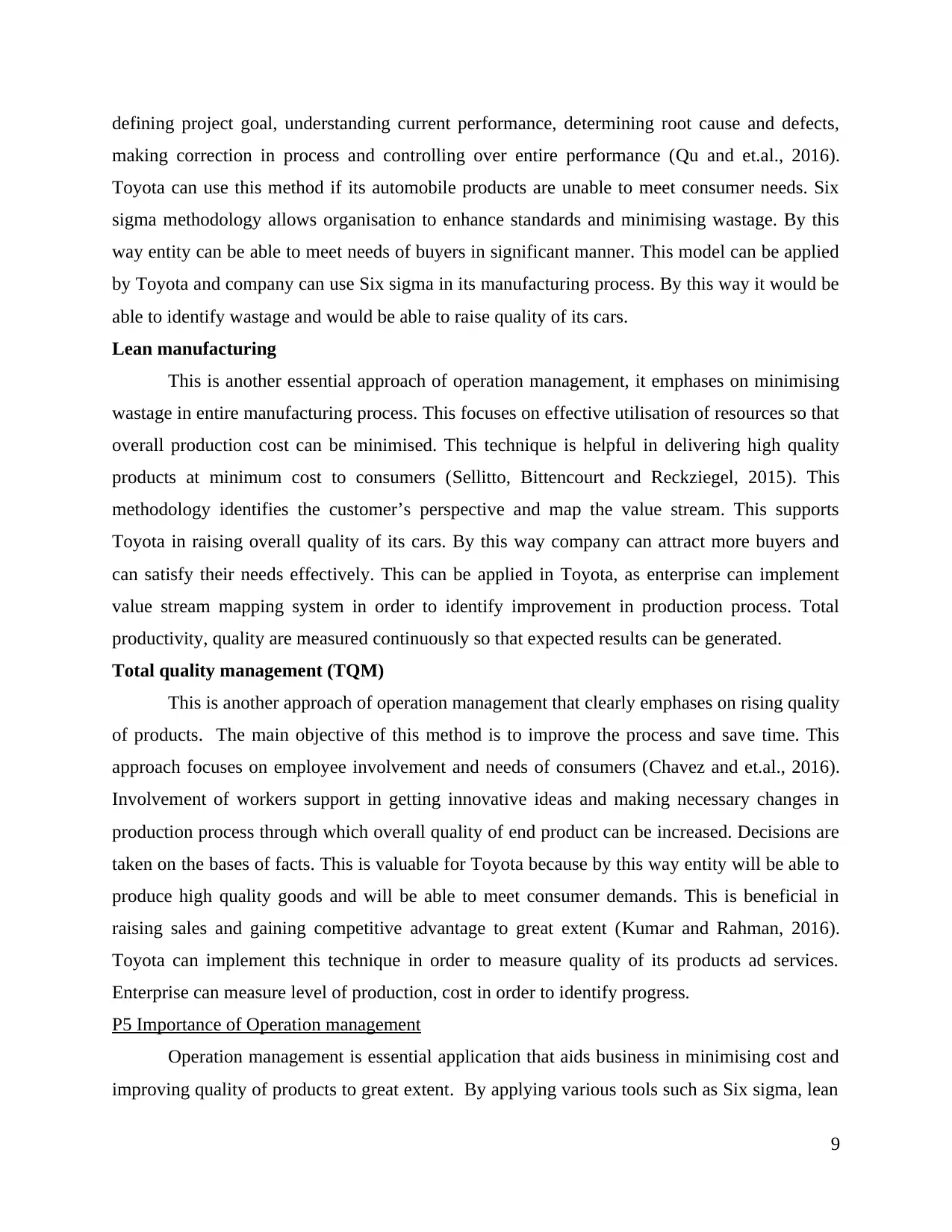
defining project goal, understanding current performance, determining root cause and defects,
making correction in process and controlling over entire performance (Qu and et.al., 2016).
Toyota can use this method if its automobile products are unable to meet consumer needs. Six
sigma methodology allows organisation to enhance standards and minimising wastage. By this
way entity can be able to meet needs of buyers in significant manner. This model can be applied
by Toyota and company can use Six sigma in its manufacturing process. By this way it would be
able to identify wastage and would be able to raise quality of its cars.
Lean manufacturing
This is another essential approach of operation management, it emphases on minimising
wastage in entire manufacturing process. This focuses on effective utilisation of resources so that
overall production cost can be minimised. This technique is helpful in delivering high quality
products at minimum cost to consumers (Sellitto, Bittencourt and Reckziegel, 2015). This
methodology identifies the customer’s perspective and map the value stream. This supports
Toyota in raising overall quality of its cars. By this way company can attract more buyers and
can satisfy their needs effectively. This can be applied in Toyota, as enterprise can implement
value stream mapping system in order to identify improvement in production process. Total
productivity, quality are measured continuously so that expected results can be generated.
Total quality management (TQM)
This is another approach of operation management that clearly emphases on rising quality
of products. The main objective of this method is to improve the process and save time. This
approach focuses on employee involvement and needs of consumers (Chavez and et.al., 2016).
Involvement of workers support in getting innovative ideas and making necessary changes in
production process through which overall quality of end product can be increased. Decisions are
taken on the bases of facts. This is valuable for Toyota because by this way entity will be able to
produce high quality goods and will be able to meet consumer demands. This is beneficial in
raising sales and gaining competitive advantage to great extent (Kumar and Rahman, 2016).
Toyota can implement this technique in order to measure quality of its products ad services.
Enterprise can measure level of production, cost in order to identify progress.
P5 Importance of Operation management
Operation management is essential application that aids business in minimising cost and
improving quality of products to great extent. By applying various tools such as Six sigma, lean
9
making correction in process and controlling over entire performance (Qu and et.al., 2016).
Toyota can use this method if its automobile products are unable to meet consumer needs. Six
sigma methodology allows organisation to enhance standards and minimising wastage. By this
way entity can be able to meet needs of buyers in significant manner. This model can be applied
by Toyota and company can use Six sigma in its manufacturing process. By this way it would be
able to identify wastage and would be able to raise quality of its cars.
Lean manufacturing
This is another essential approach of operation management, it emphases on minimising
wastage in entire manufacturing process. This focuses on effective utilisation of resources so that
overall production cost can be minimised. This technique is helpful in delivering high quality
products at minimum cost to consumers (Sellitto, Bittencourt and Reckziegel, 2015). This
methodology identifies the customer’s perspective and map the value stream. This supports
Toyota in raising overall quality of its cars. By this way company can attract more buyers and
can satisfy their needs effectively. This can be applied in Toyota, as enterprise can implement
value stream mapping system in order to identify improvement in production process. Total
productivity, quality are measured continuously so that expected results can be generated.
Total quality management (TQM)
This is another approach of operation management that clearly emphases on rising quality
of products. The main objective of this method is to improve the process and save time. This
approach focuses on employee involvement and needs of consumers (Chavez and et.al., 2016).
Involvement of workers support in getting innovative ideas and making necessary changes in
production process through which overall quality of end product can be increased. Decisions are
taken on the bases of facts. This is valuable for Toyota because by this way entity will be able to
produce high quality goods and will be able to meet consumer demands. This is beneficial in
raising sales and gaining competitive advantage to great extent (Kumar and Rahman, 2016).
Toyota can implement this technique in order to measure quality of its products ad services.
Enterprise can measure level of production, cost in order to identify progress.
P5 Importance of Operation management
Operation management is essential application that aids business in minimising cost and
improving quality of products to great extent. By applying various tools such as Six sigma, lean
9
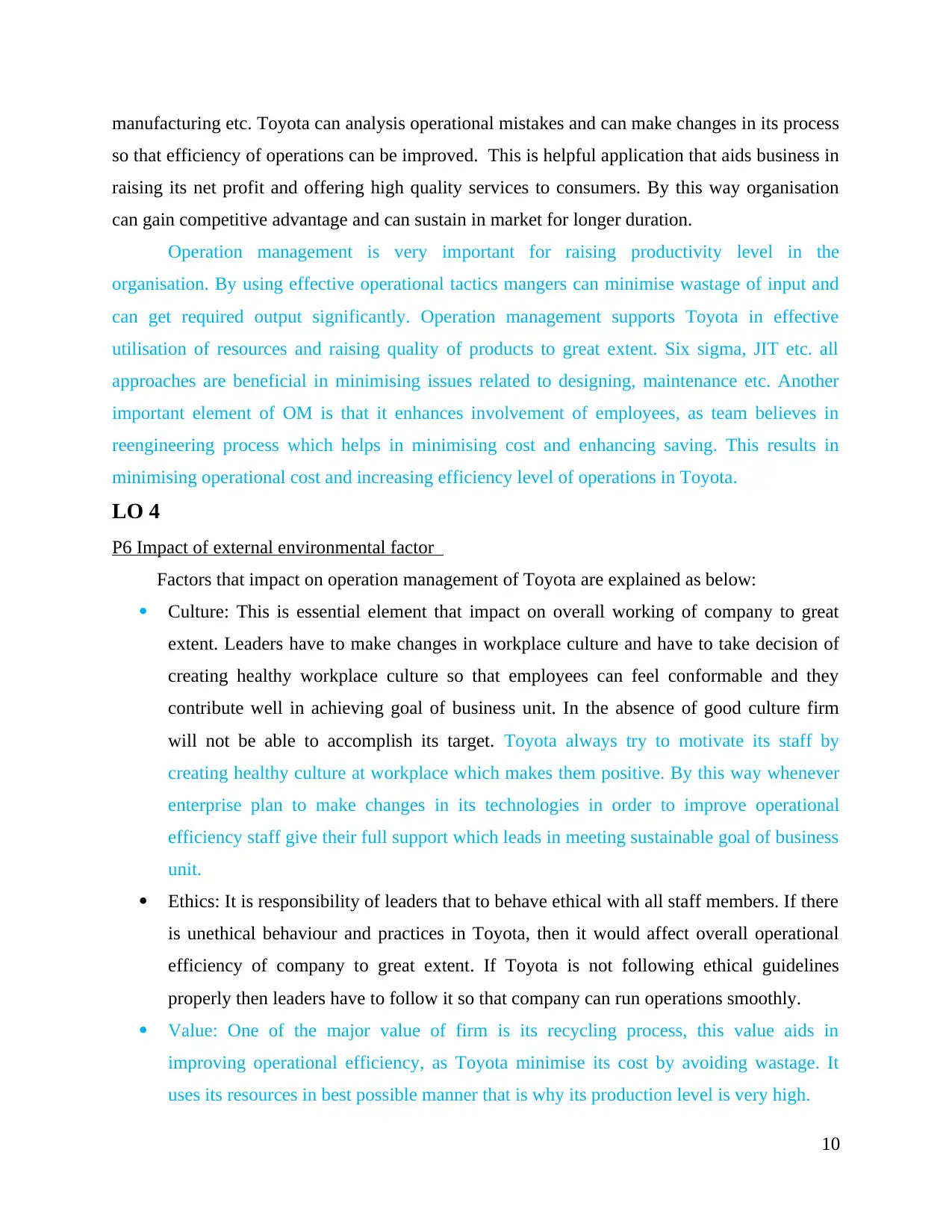
manufacturing etc. Toyota can analysis operational mistakes and can make changes in its process
so that efficiency of operations can be improved. This is helpful application that aids business in
raising its net profit and offering high quality services to consumers. By this way organisation
can gain competitive advantage and can sustain in market for longer duration.
Operation management is very important for raising productivity level in the
organisation. By using effective operational tactics mangers can minimise wastage of input and
can get required output significantly. Operation management supports Toyota in effective
utilisation of resources and raising quality of products to great extent. Six sigma, JIT etc. all
approaches are beneficial in minimising issues related to designing, maintenance etc. Another
important element of OM is that it enhances involvement of employees, as team believes in
reengineering process which helps in minimising cost and enhancing saving. This results in
minimising operational cost and increasing efficiency level of operations in Toyota.
LO 4
P6 Impact of external environmental factor
Factors that impact on operation management of Toyota are explained as below:
Culture: This is essential element that impact on overall working of company to great
extent. Leaders have to make changes in workplace culture and have to take decision of
creating healthy workplace culture so that employees can feel conformable and they
contribute well in achieving goal of business unit. In the absence of good culture firm
will not be able to accomplish its target. Toyota always try to motivate its staff by
creating healthy culture at workplace which makes them positive. By this way whenever
enterprise plan to make changes in its technologies in order to improve operational
efficiency staff give their full support which leads in meeting sustainable goal of business
unit.
Ethics: It is responsibility of leaders that to behave ethical with all staff members. If there
is unethical behaviour and practices in Toyota, then it would affect overall operational
efficiency of company to great extent. If Toyota is not following ethical guidelines
properly then leaders have to follow it so that company can run operations smoothly.
Value: One of the major value of firm is its recycling process, this value aids in
improving operational efficiency, as Toyota minimise its cost by avoiding wastage. It
uses its resources in best possible manner that is why its production level is very high.
10
so that efficiency of operations can be improved. This is helpful application that aids business in
raising its net profit and offering high quality services to consumers. By this way organisation
can gain competitive advantage and can sustain in market for longer duration.
Operation management is very important for raising productivity level in the
organisation. By using effective operational tactics mangers can minimise wastage of input and
can get required output significantly. Operation management supports Toyota in effective
utilisation of resources and raising quality of products to great extent. Six sigma, JIT etc. all
approaches are beneficial in minimising issues related to designing, maintenance etc. Another
important element of OM is that it enhances involvement of employees, as team believes in
reengineering process which helps in minimising cost and enhancing saving. This results in
minimising operational cost and increasing efficiency level of operations in Toyota.
LO 4
P6 Impact of external environmental factor
Factors that impact on operation management of Toyota are explained as below:
Culture: This is essential element that impact on overall working of company to great
extent. Leaders have to make changes in workplace culture and have to take decision of
creating healthy workplace culture so that employees can feel conformable and they
contribute well in achieving goal of business unit. In the absence of good culture firm
will not be able to accomplish its target. Toyota always try to motivate its staff by
creating healthy culture at workplace which makes them positive. By this way whenever
enterprise plan to make changes in its technologies in order to improve operational
efficiency staff give their full support which leads in meeting sustainable goal of business
unit.
Ethics: It is responsibility of leaders that to behave ethical with all staff members. If there
is unethical behaviour and practices in Toyota, then it would affect overall operational
efficiency of company to great extent. If Toyota is not following ethical guidelines
properly then leaders have to follow it so that company can run operations smoothly.
Value: One of the major value of firm is its recycling process, this value aids in
improving operational efficiency, as Toyota minimise its cost by avoiding wastage. It
uses its resources in best possible manner that is why its production level is very high.
10
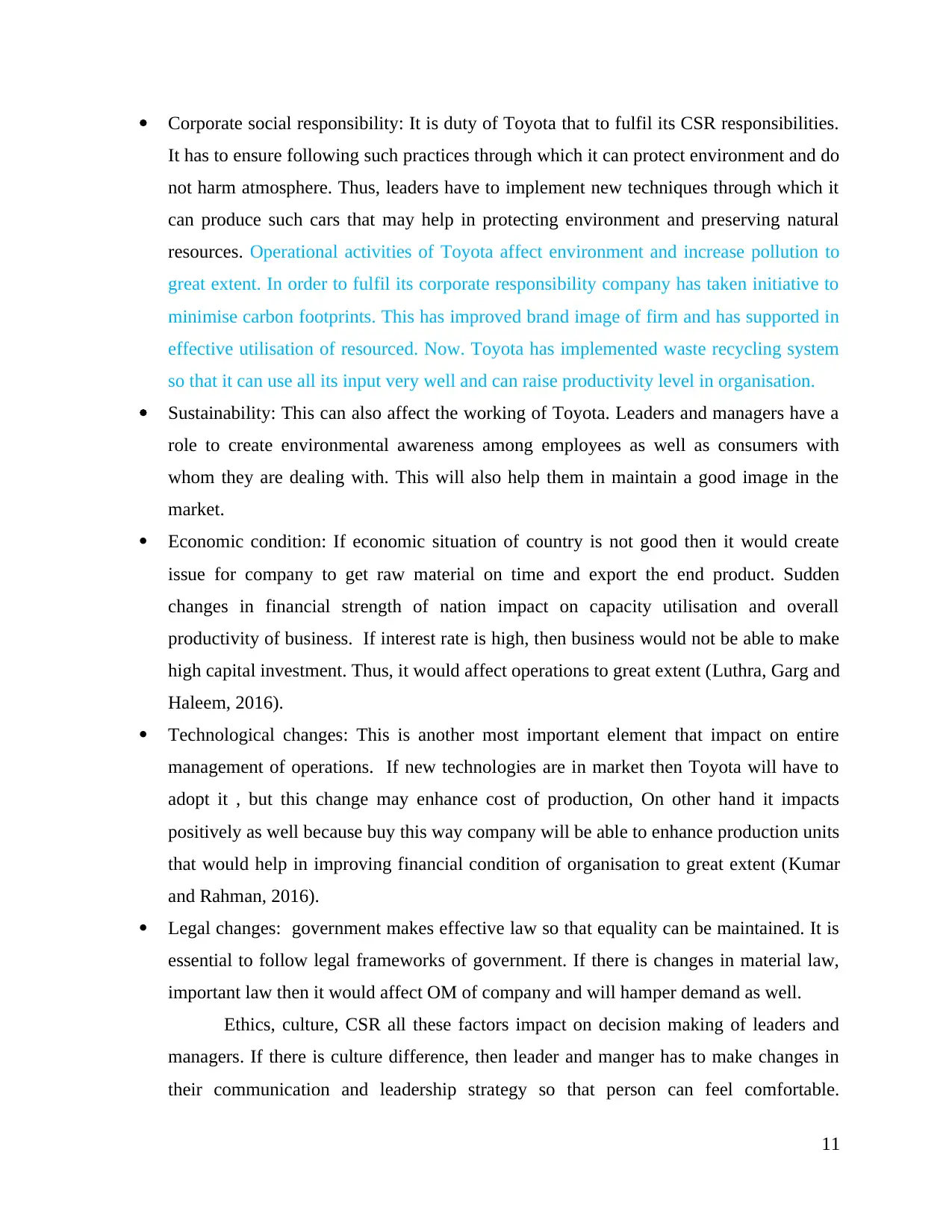
Corporate social responsibility: It is duty of Toyota that to fulfil its CSR responsibilities.
It has to ensure following such practices through which it can protect environment and do
not harm atmosphere. Thus, leaders have to implement new techniques through which it
can produce such cars that may help in protecting environment and preserving natural
resources. Operational activities of Toyota affect environment and increase pollution to
great extent. In order to fulfil its corporate responsibility company has taken initiative to
minimise carbon footprints. This has improved brand image of firm and has supported in
effective utilisation of resourced. Now. Toyota has implemented waste recycling system
so that it can use all its input very well and can raise productivity level in organisation.
Sustainability: This can also affect the working of Toyota. Leaders and managers have a
role to create environmental awareness among employees as well as consumers with
whom they are dealing with. This will also help them in maintain a good image in the
market.
Economic condition: If economic situation of country is not good then it would create
issue for company to get raw material on time and export the end product. Sudden
changes in financial strength of nation impact on capacity utilisation and overall
productivity of business. If interest rate is high, then business would not be able to make
high capital investment. Thus, it would affect operations to great extent (Luthra, Garg and
Haleem, 2016).
Technological changes: This is another most important element that impact on entire
management of operations. If new technologies are in market then Toyota will have to
adopt it , but this change may enhance cost of production, On other hand it impacts
positively as well because buy this way company will be able to enhance production units
that would help in improving financial condition of organisation to great extent (Kumar
and Rahman, 2016).
Legal changes: government makes effective law so that equality can be maintained. It is
essential to follow legal frameworks of government. If there is changes in material law,
important law then it would affect OM of company and will hamper demand as well.
Ethics, culture, CSR all these factors impact on decision making of leaders and
managers. If there is culture difference, then leader and manger has to make changes in
their communication and leadership strategy so that person can feel comfortable.
11
It has to ensure following such practices through which it can protect environment and do
not harm atmosphere. Thus, leaders have to implement new techniques through which it
can produce such cars that may help in protecting environment and preserving natural
resources. Operational activities of Toyota affect environment and increase pollution to
great extent. In order to fulfil its corporate responsibility company has taken initiative to
minimise carbon footprints. This has improved brand image of firm and has supported in
effective utilisation of resourced. Now. Toyota has implemented waste recycling system
so that it can use all its input very well and can raise productivity level in organisation.
Sustainability: This can also affect the working of Toyota. Leaders and managers have a
role to create environmental awareness among employees as well as consumers with
whom they are dealing with. This will also help them in maintain a good image in the
market.
Economic condition: If economic situation of country is not good then it would create
issue for company to get raw material on time and export the end product. Sudden
changes in financial strength of nation impact on capacity utilisation and overall
productivity of business. If interest rate is high, then business would not be able to make
high capital investment. Thus, it would affect operations to great extent (Luthra, Garg and
Haleem, 2016).
Technological changes: This is another most important element that impact on entire
management of operations. If new technologies are in market then Toyota will have to
adopt it , but this change may enhance cost of production, On other hand it impacts
positively as well because buy this way company will be able to enhance production units
that would help in improving financial condition of organisation to great extent (Kumar
and Rahman, 2016).
Legal changes: government makes effective law so that equality can be maintained. It is
essential to follow legal frameworks of government. If there is changes in material law,
important law then it would affect OM of company and will hamper demand as well.
Ethics, culture, CSR all these factors impact on decision making of leaders and
managers. If there is culture difference, then leader and manger has to make changes in
their communication and leadership strategy so that person can feel comfortable.
11
Paraphrase This Document
Need a fresh take? Get an instant paraphrase of this document with our AI Paraphraser
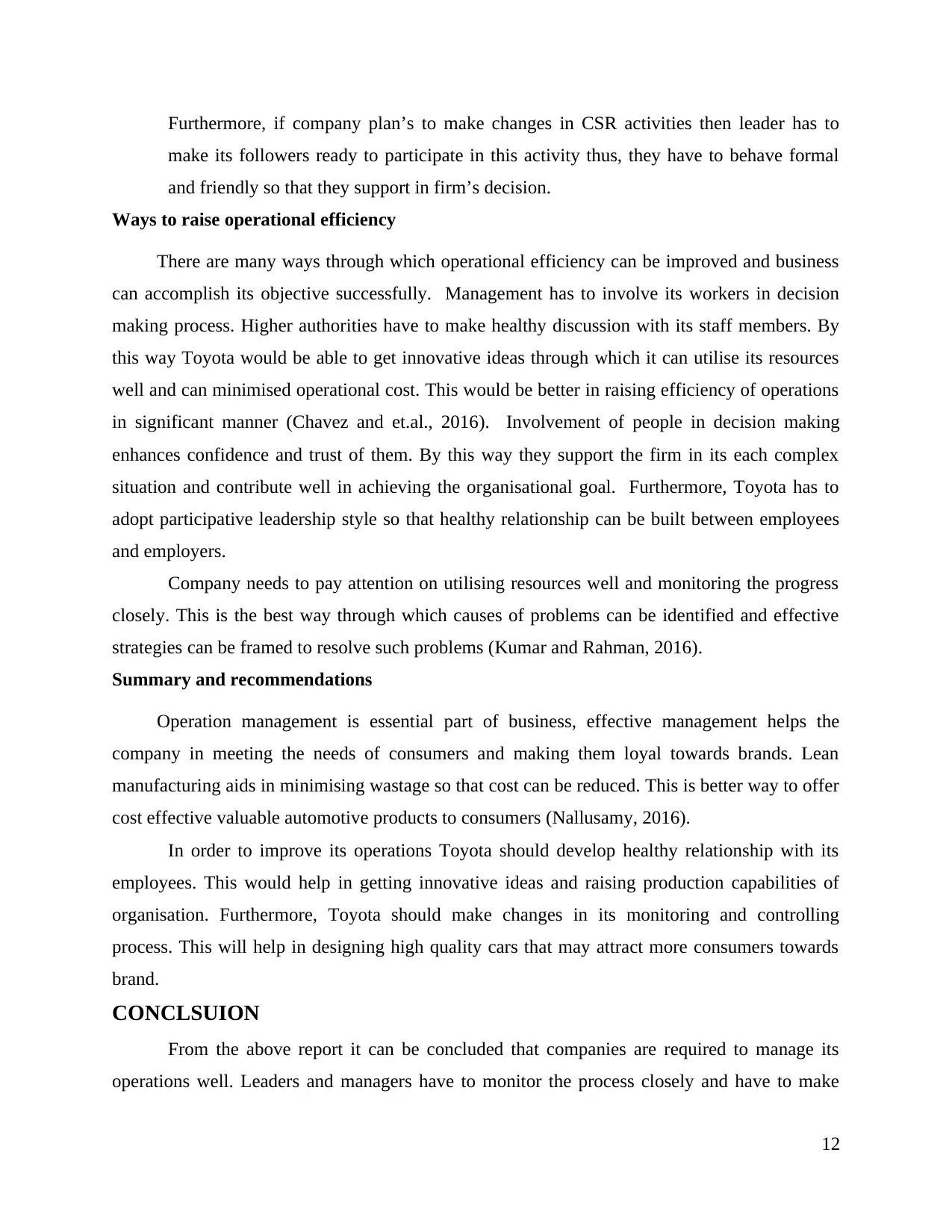
Furthermore, if company plan’s to make changes in CSR activities then leader has to
make its followers ready to participate in this activity thus, they have to behave formal
and friendly so that they support in firm’s decision.
Ways to raise operational efficiency
There are many ways through which operational efficiency can be improved and business
can accomplish its objective successfully. Management has to involve its workers in decision
making process. Higher authorities have to make healthy discussion with its staff members. By
this way Toyota would be able to get innovative ideas through which it can utilise its resources
well and can minimised operational cost. This would be better in raising efficiency of operations
in significant manner (Chavez and et.al., 2016). Involvement of people in decision making
enhances confidence and trust of them. By this way they support the firm in its each complex
situation and contribute well in achieving the organisational goal. Furthermore, Toyota has to
adopt participative leadership style so that healthy relationship can be built between employees
and employers.
Company needs to pay attention on utilising resources well and monitoring the progress
closely. This is the best way through which causes of problems can be identified and effective
strategies can be framed to resolve such problems (Kumar and Rahman, 2016).
Summary and recommendations
Operation management is essential part of business, effective management helps the
company in meeting the needs of consumers and making them loyal towards brands. Lean
manufacturing aids in minimising wastage so that cost can be reduced. This is better way to offer
cost effective valuable automotive products to consumers (Nallusamy, 2016).
In order to improve its operations Toyota should develop healthy relationship with its
employees. This would help in getting innovative ideas and raising production capabilities of
organisation. Furthermore, Toyota should make changes in its monitoring and controlling
process. This will help in designing high quality cars that may attract more consumers towards
brand.
CONCLSUION
From the above report it can be concluded that companies are required to manage its
operations well. Leaders and managers have to monitor the process closely and have to make
12
make its followers ready to participate in this activity thus, they have to behave formal
and friendly so that they support in firm’s decision.
Ways to raise operational efficiency
There are many ways through which operational efficiency can be improved and business
can accomplish its objective successfully. Management has to involve its workers in decision
making process. Higher authorities have to make healthy discussion with its staff members. By
this way Toyota would be able to get innovative ideas through which it can utilise its resources
well and can minimised operational cost. This would be better in raising efficiency of operations
in significant manner (Chavez and et.al., 2016). Involvement of people in decision making
enhances confidence and trust of them. By this way they support the firm in its each complex
situation and contribute well in achieving the organisational goal. Furthermore, Toyota has to
adopt participative leadership style so that healthy relationship can be built between employees
and employers.
Company needs to pay attention on utilising resources well and monitoring the progress
closely. This is the best way through which causes of problems can be identified and effective
strategies can be framed to resolve such problems (Kumar and Rahman, 2016).
Summary and recommendations
Operation management is essential part of business, effective management helps the
company in meeting the needs of consumers and making them loyal towards brands. Lean
manufacturing aids in minimising wastage so that cost can be reduced. This is better way to offer
cost effective valuable automotive products to consumers (Nallusamy, 2016).
In order to improve its operations Toyota should develop healthy relationship with its
employees. This would help in getting innovative ideas and raising production capabilities of
organisation. Furthermore, Toyota should make changes in its monitoring and controlling
process. This will help in designing high quality cars that may attract more consumers towards
brand.
CONCLSUION
From the above report it can be concluded that companies are required to manage its
operations well. Leaders and managers have to monitor the process closely and have to make
12
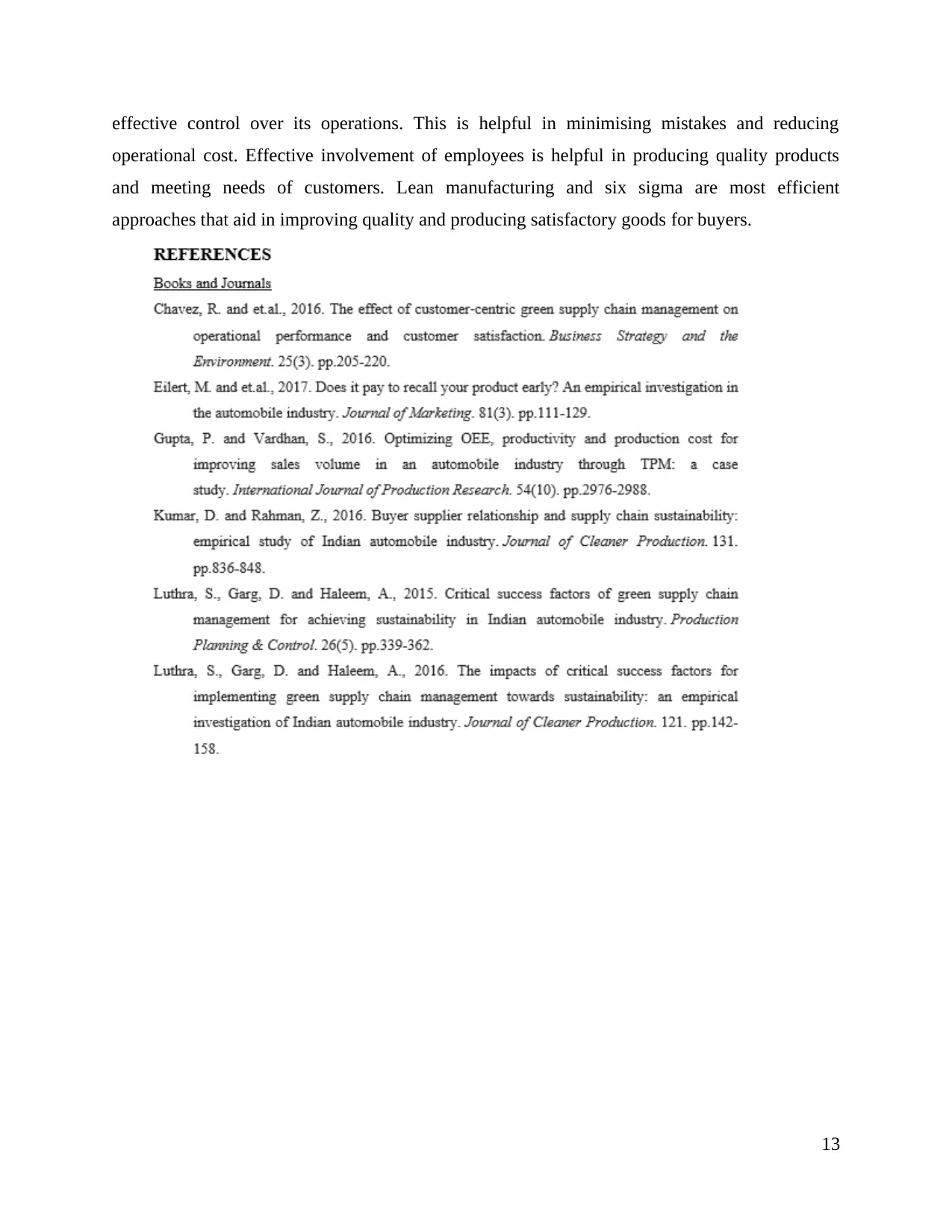
effective control over its operations. This is helpful in minimising mistakes and reducing
operational cost. Effective involvement of employees is helpful in producing quality products
and meeting needs of customers. Lean manufacturing and six sigma are most efficient
approaches that aid in improving quality and producing satisfactory goods for buyers.
13
operational cost. Effective involvement of employees is helpful in producing quality products
and meeting needs of customers. Lean manufacturing and six sigma are most efficient
approaches that aid in improving quality and producing satisfactory goods for buyers.
13
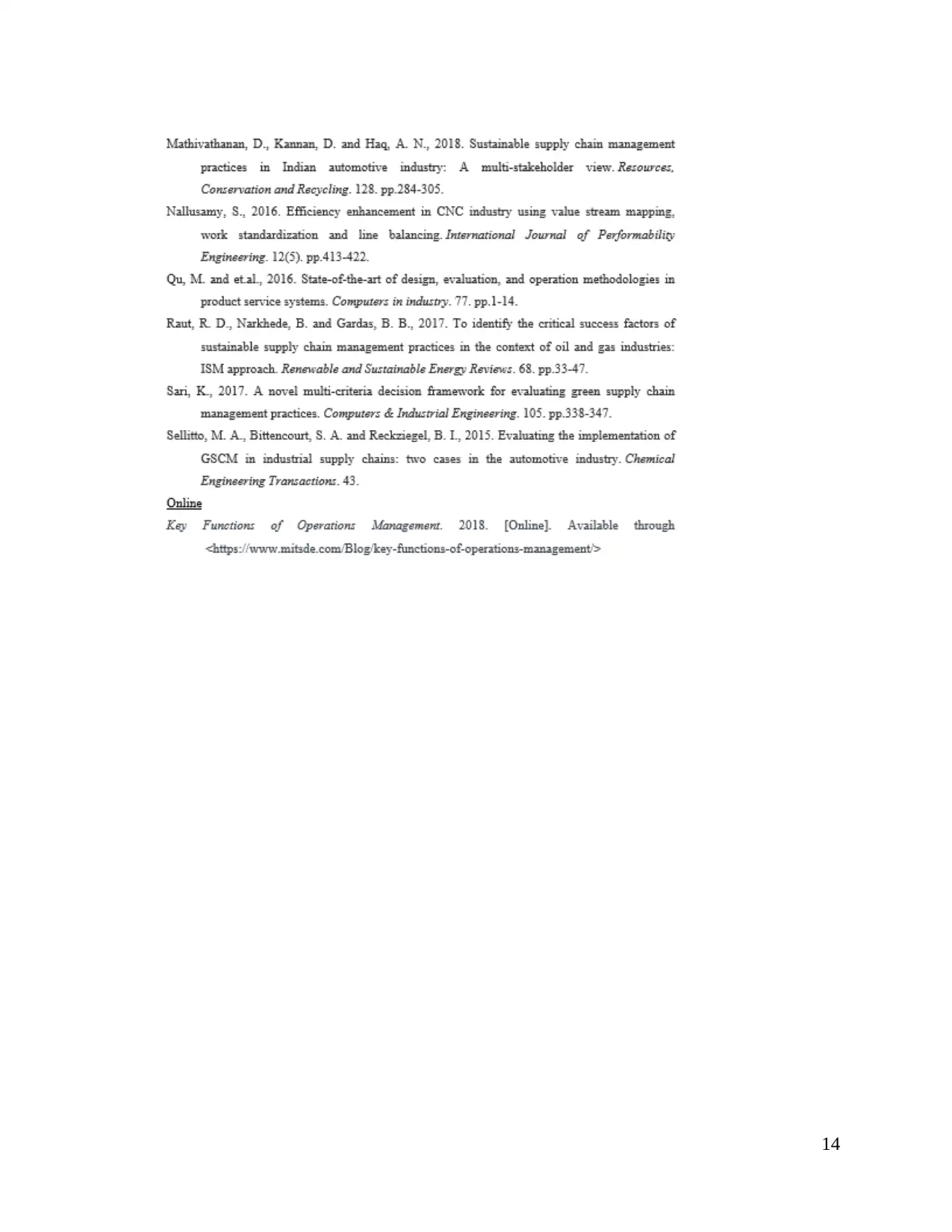
14
1 out of 16
Related Documents
![[object Object]](/_next/image/?url=%2F_next%2Fstatic%2Fmedia%2Flogo.6d15ce61.png&w=640&q=75)
Your All-in-One AI-Powered Toolkit for Academic Success.
+13062052269
info@desklib.com
Available 24*7 on WhatsApp / Email
Unlock your academic potential
© 2024 | Zucol Services PVT LTD | All rights reserved.