Operation and Project Management Report
VerifiedAdded on 2020/12/09
|18
|5186
|269
Report
AI Summary
This report examines the implementation of operations management principles at Sainsbury, a leading UK retailer. It analyzes the company's continuous improvement plan, focusing on lean principles and Kaizen methodology. The report also includes a case study of Sainsbury's launch of a new milk chocolate product, exploring the stages of the product life cycle and its impact on the project's success.
Contribute Materials
Your contribution can guide someone’s learning journey. Share your
documents today.
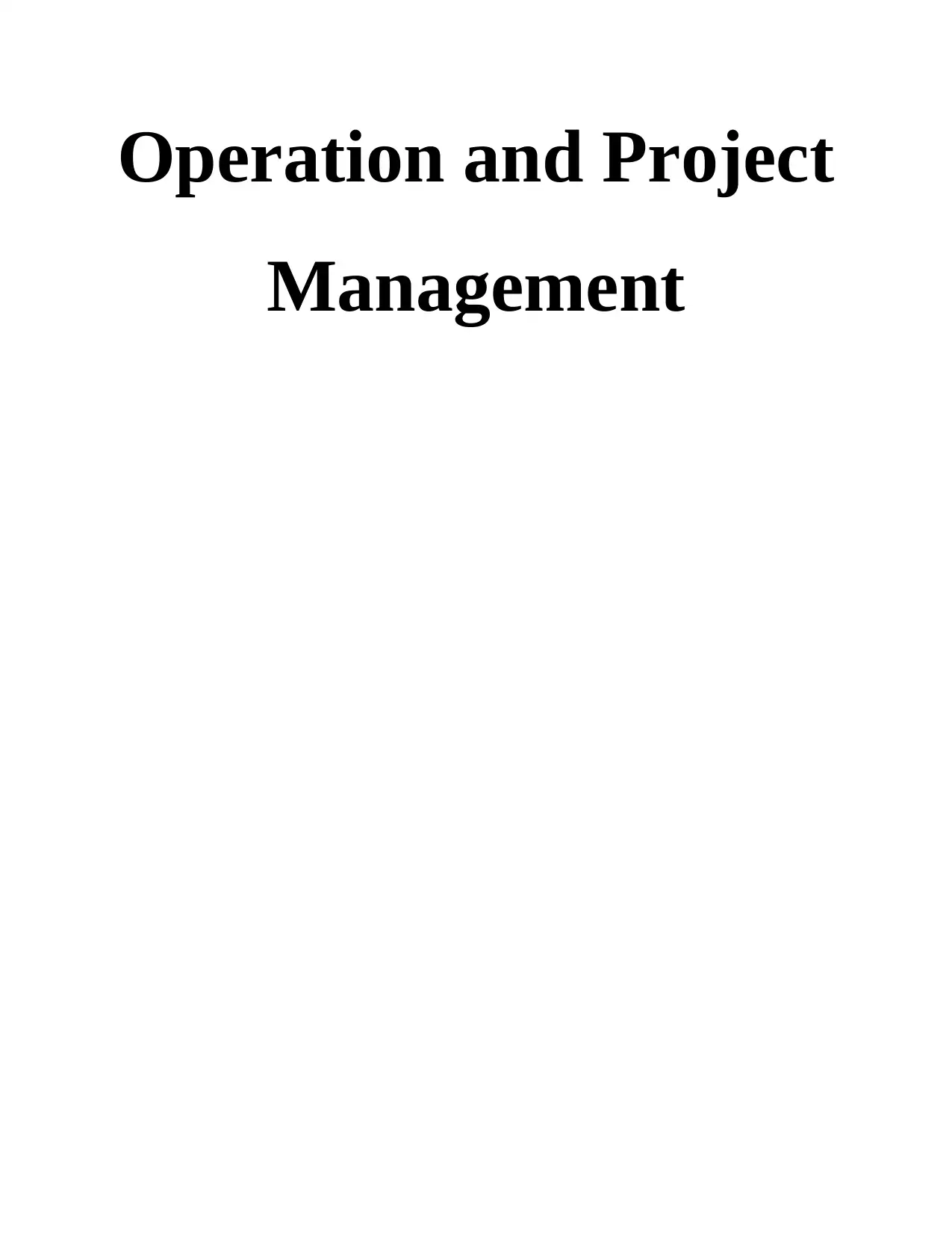
Operation and Project
Management
Management
Secure Best Marks with AI Grader
Need help grading? Try our AI Grader for instant feedback on your assignments.
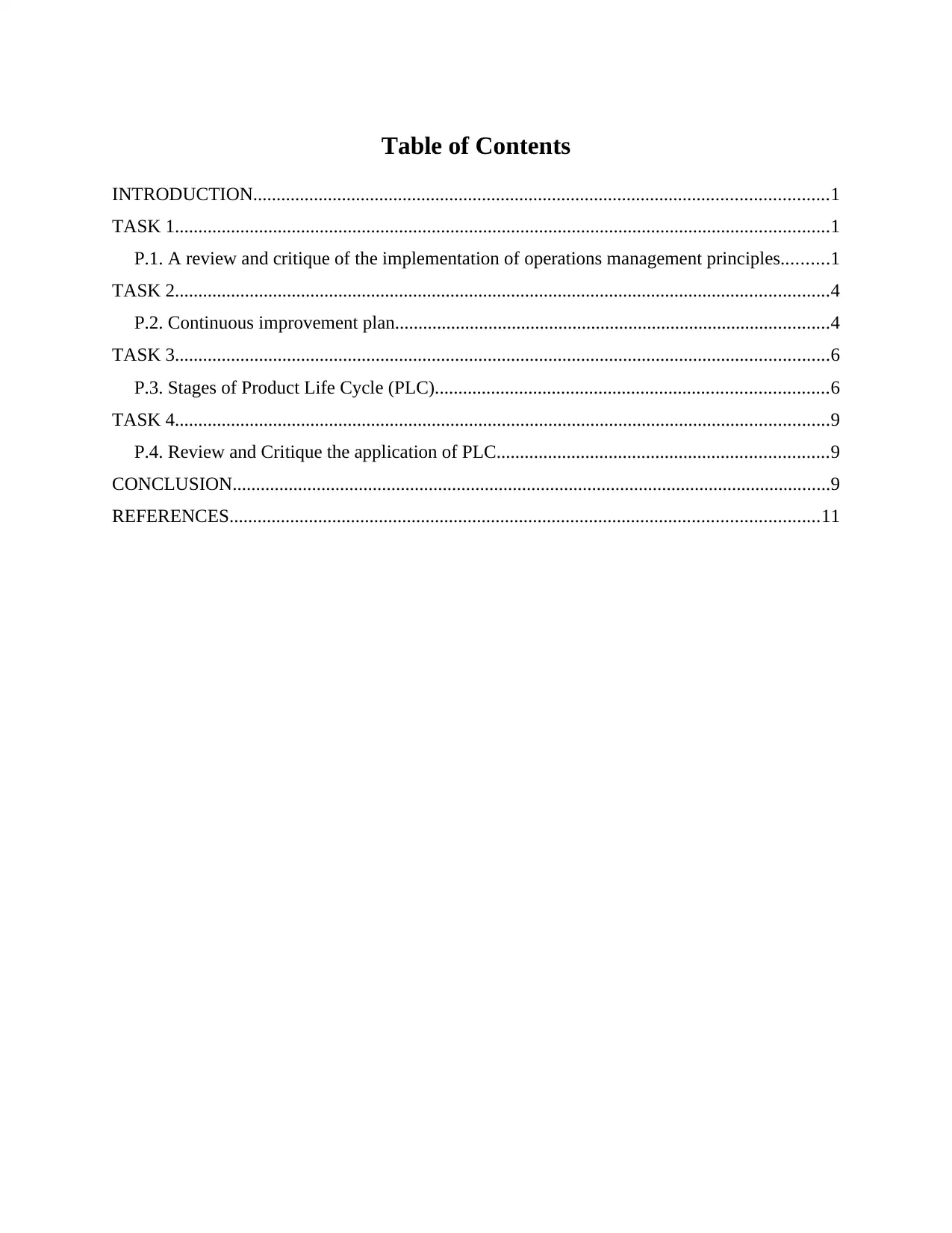
Table of Contents
INTRODUCTION...........................................................................................................................1
TASK 1............................................................................................................................................1
P.1. A review and critique of the implementation of operations management principles..........1
TASK 2............................................................................................................................................4
P.2. Continuous improvement plan.............................................................................................4
TASK 3............................................................................................................................................6
P.3. Stages of Product Life Cycle (PLC)....................................................................................6
TASK 4............................................................................................................................................9
P.4. Review and Critique the application of PLC.......................................................................9
CONCLUSION................................................................................................................................9
REFERENCES..............................................................................................................................11
INTRODUCTION...........................................................................................................................1
TASK 1............................................................................................................................................1
P.1. A review and critique of the implementation of operations management principles..........1
TASK 2............................................................................................................................................4
P.2. Continuous improvement plan.............................................................................................4
TASK 3............................................................................................................................................6
P.3. Stages of Product Life Cycle (PLC)....................................................................................6
TASK 4............................................................................................................................................9
P.4. Review and Critique the application of PLC.......................................................................9
CONCLUSION................................................................................................................................9
REFERENCES..............................................................................................................................11
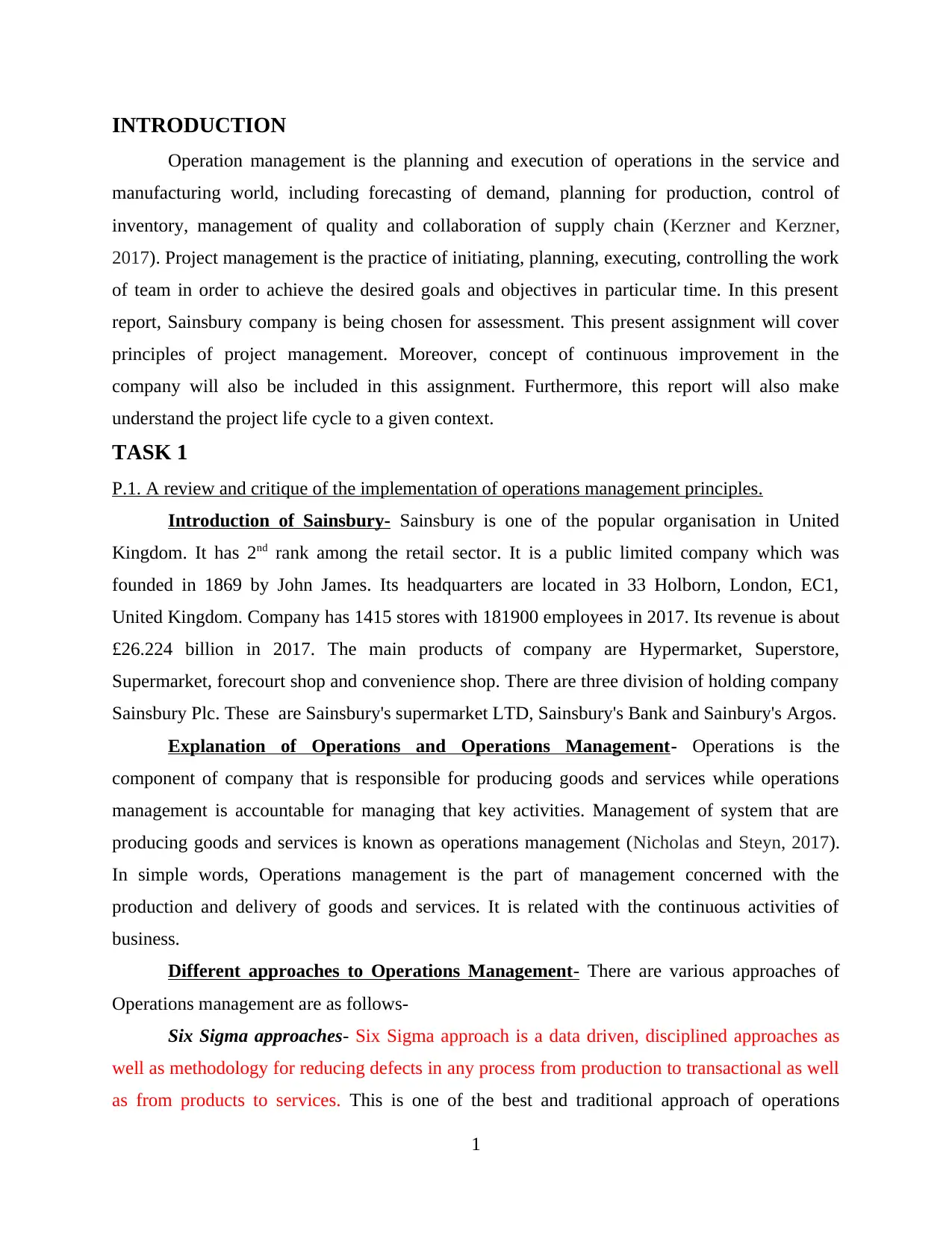
INTRODUCTION
Operation management is the planning and execution of operations in the service and
manufacturing world, including forecasting of demand, planning for production, control of
inventory, management of quality and collaboration of supply chain (Kerzner and Kerzner,
2017). Project management is the practice of initiating, planning, executing, controlling the work
of team in order to achieve the desired goals and objectives in particular time. In this present
report, Sainsbury company is being chosen for assessment. This present assignment will cover
principles of project management. Moreover, concept of continuous improvement in the
company will also be included in this assignment. Furthermore, this report will also make
understand the project life cycle to a given context.
TASK 1
P.1. A review and critique of the implementation of operations management principles.
Introduction of Sainsbury- Sainsbury is one of the popular organisation in United
Kingdom. It has 2nd rank among the retail sector. It is a public limited company which was
founded in 1869 by John James. Its headquarters are located in 33 Holborn, London, EC1,
United Kingdom. Company has 1415 stores with 181900 employees in 2017. Its revenue is about
£26.224 billion in 2017. The main products of company are Hypermarket, Superstore,
Supermarket, forecourt shop and convenience shop. There are three division of holding company
Sainsbury Plc. These are Sainsbury's supermarket LTD, Sainsbury's Bank and Sainbury's Argos.
Explanation of Operations and Operations Management- Operations is the
component of company that is responsible for producing goods and services while operations
management is accountable for managing that key activities. Management of system that are
producing goods and services is known as operations management (Nicholas and Steyn, 2017).
In simple words, Operations management is the part of management concerned with the
production and delivery of goods and services. It is related with the continuous activities of
business.
Different approaches to Operations Management- There are various approaches of
Operations management are as follows-
Six Sigma approaches- Six Sigma approach is a data driven, disciplined approaches as
well as methodology for reducing defects in any process from production to transactional as well
as from products to services. This is one of the best and traditional approach of operations
1
Operation management is the planning and execution of operations in the service and
manufacturing world, including forecasting of demand, planning for production, control of
inventory, management of quality and collaboration of supply chain (Kerzner and Kerzner,
2017). Project management is the practice of initiating, planning, executing, controlling the work
of team in order to achieve the desired goals and objectives in particular time. In this present
report, Sainsbury company is being chosen for assessment. This present assignment will cover
principles of project management. Moreover, concept of continuous improvement in the
company will also be included in this assignment. Furthermore, this report will also make
understand the project life cycle to a given context.
TASK 1
P.1. A review and critique of the implementation of operations management principles.
Introduction of Sainsbury- Sainsbury is one of the popular organisation in United
Kingdom. It has 2nd rank among the retail sector. It is a public limited company which was
founded in 1869 by John James. Its headquarters are located in 33 Holborn, London, EC1,
United Kingdom. Company has 1415 stores with 181900 employees in 2017. Its revenue is about
£26.224 billion in 2017. The main products of company are Hypermarket, Superstore,
Supermarket, forecourt shop and convenience shop. There are three division of holding company
Sainsbury Plc. These are Sainsbury's supermarket LTD, Sainsbury's Bank and Sainbury's Argos.
Explanation of Operations and Operations Management- Operations is the
component of company that is responsible for producing goods and services while operations
management is accountable for managing that key activities. Management of system that are
producing goods and services is known as operations management (Nicholas and Steyn, 2017).
In simple words, Operations management is the part of management concerned with the
production and delivery of goods and services. It is related with the continuous activities of
business.
Different approaches to Operations Management- There are various approaches of
Operations management are as follows-
Six Sigma approaches- Six Sigma approach is a data driven, disciplined approaches as
well as methodology for reducing defects in any process from production to transactional as well
as from products to services. This is one of the best and traditional approach of operations
1
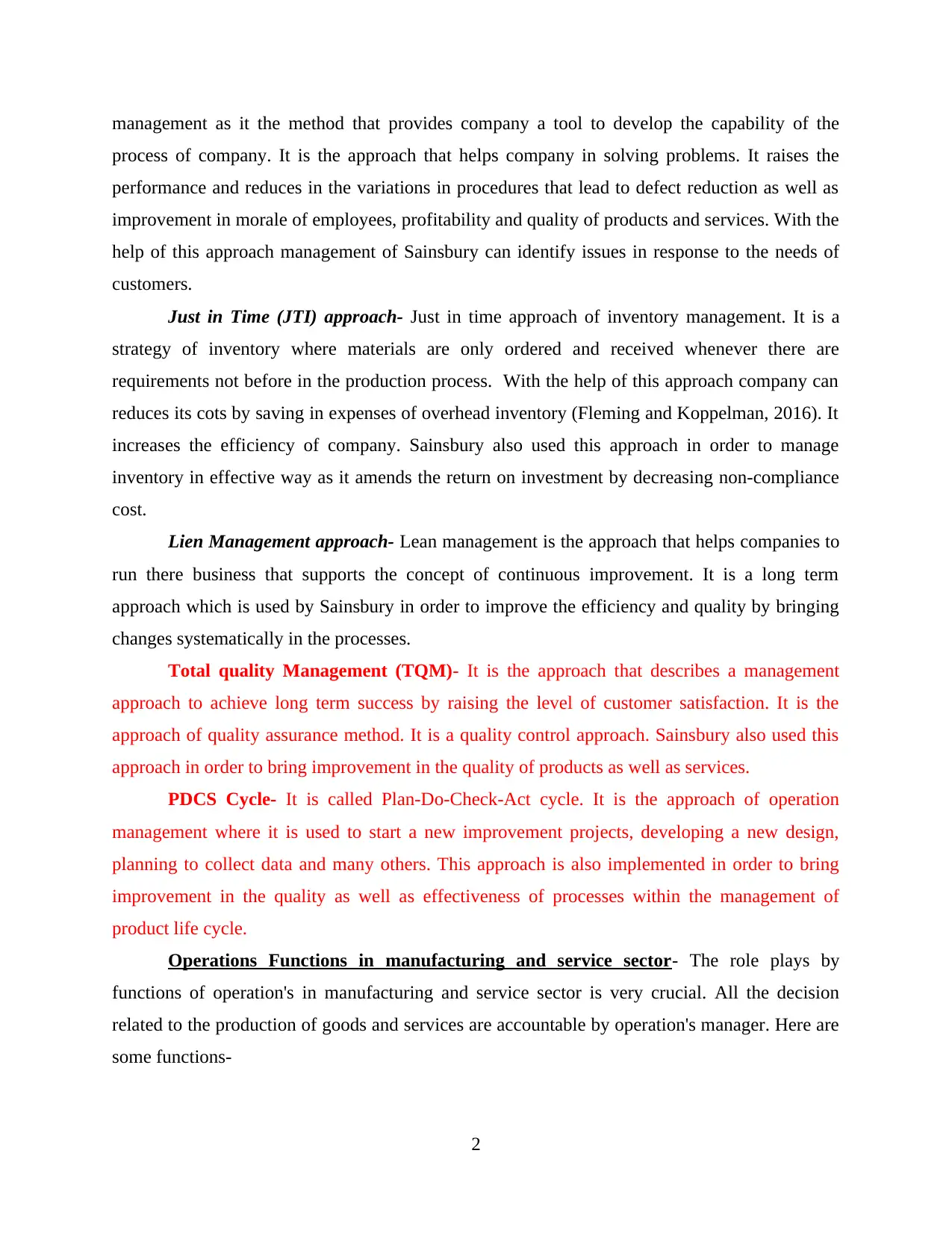
management as it the method that provides company a tool to develop the capability of the
process of company. It is the approach that helps company in solving problems. It raises the
performance and reduces in the variations in procedures that lead to defect reduction as well as
improvement in morale of employees, profitability and quality of products and services. With the
help of this approach management of Sainsbury can identify issues in response to the needs of
customers.
Just in Time (JTI) approach- Just in time approach of inventory management. It is a
strategy of inventory where materials are only ordered and received whenever there are
requirements not before in the production process. With the help of this approach company can
reduces its cots by saving in expenses of overhead inventory (Fleming and Koppelman, 2016). It
increases the efficiency of company. Sainsbury also used this approach in order to manage
inventory in effective way as it amends the return on investment by decreasing non-compliance
cost.
Lien Management approach- Lean management is the approach that helps companies to
run there business that supports the concept of continuous improvement. It is a long term
approach which is used by Sainsbury in order to improve the efficiency and quality by bringing
changes systematically in the processes.
Total quality Management (TQM)- It is the approach that describes a management
approach to achieve long term success by raising the level of customer satisfaction. It is the
approach of quality assurance method. It is a quality control approach. Sainsbury also used this
approach in order to bring improvement in the quality of products as well as services.
PDCS Cycle- It is called Plan-Do-Check-Act cycle. It is the approach of operation
management where it is used to start a new improvement projects, developing a new design,
planning to collect data and many others. This approach is also implemented in order to bring
improvement in the quality as well as effectiveness of processes within the management of
product life cycle.
Operations Functions in manufacturing and service sector- The role plays by
functions of operation's in manufacturing and service sector is very crucial. All the decision
related to the production of goods and services are accountable by operation's manager. Here are
some functions-
2
process of company. It is the approach that helps company in solving problems. It raises the
performance and reduces in the variations in procedures that lead to defect reduction as well as
improvement in morale of employees, profitability and quality of products and services. With the
help of this approach management of Sainsbury can identify issues in response to the needs of
customers.
Just in Time (JTI) approach- Just in time approach of inventory management. It is a
strategy of inventory where materials are only ordered and received whenever there are
requirements not before in the production process. With the help of this approach company can
reduces its cots by saving in expenses of overhead inventory (Fleming and Koppelman, 2016). It
increases the efficiency of company. Sainsbury also used this approach in order to manage
inventory in effective way as it amends the return on investment by decreasing non-compliance
cost.
Lien Management approach- Lean management is the approach that helps companies to
run there business that supports the concept of continuous improvement. It is a long term
approach which is used by Sainsbury in order to improve the efficiency and quality by bringing
changes systematically in the processes.
Total quality Management (TQM)- It is the approach that describes a management
approach to achieve long term success by raising the level of customer satisfaction. It is the
approach of quality assurance method. It is a quality control approach. Sainsbury also used this
approach in order to bring improvement in the quality of products as well as services.
PDCS Cycle- It is called Plan-Do-Check-Act cycle. It is the approach of operation
management where it is used to start a new improvement projects, developing a new design,
planning to collect data and many others. This approach is also implemented in order to bring
improvement in the quality as well as effectiveness of processes within the management of
product life cycle.
Operations Functions in manufacturing and service sector- The role plays by
functions of operation's in manufacturing and service sector is very crucial. All the decision
related to the production of goods and services are accountable by operation's manager. Here are
some functions-
2
Secure Best Marks with AI Grader
Need help grading? Try our AI Grader for instant feedback on your assignments.
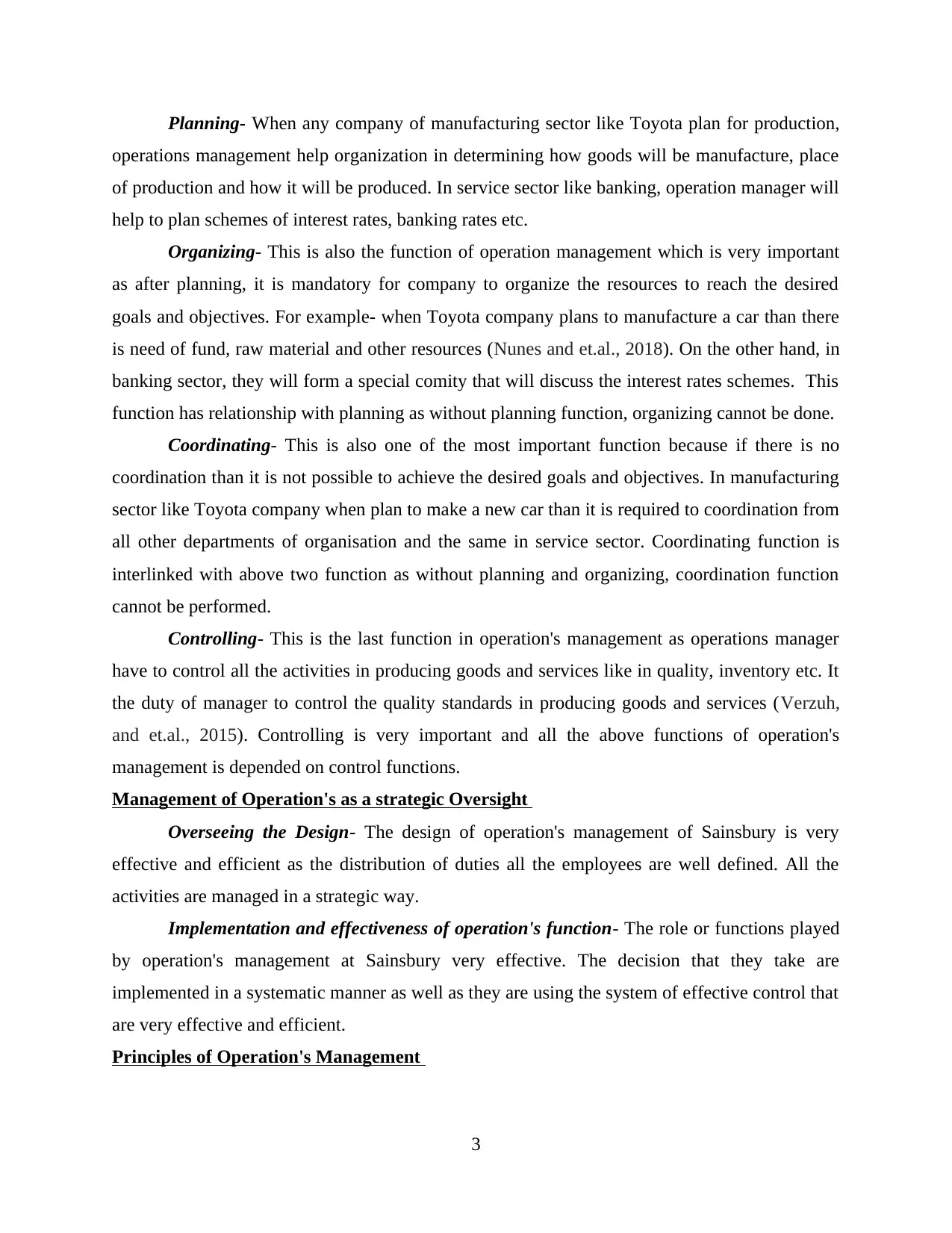
Planning- When any company of manufacturing sector like Toyota plan for production,
operations management help organization in determining how goods will be manufacture, place
of production and how it will be produced. In service sector like banking, operation manager will
help to plan schemes of interest rates, banking rates etc.
Organizing- This is also the function of operation management which is very important
as after planning, it is mandatory for company to organize the resources to reach the desired
goals and objectives. For example- when Toyota company plans to manufacture a car than there
is need of fund, raw material and other resources (Nunes and et.al., 2018). On the other hand, in
banking sector, they will form a special comity that will discuss the interest rates schemes. This
function has relationship with planning as without planning function, organizing cannot be done.
Coordinating- This is also one of the most important function because if there is no
coordination than it is not possible to achieve the desired goals and objectives. In manufacturing
sector like Toyota company when plan to make a new car than it is required to coordination from
all other departments of organisation and the same in service sector. Coordinating function is
interlinked with above two function as without planning and organizing, coordination function
cannot be performed.
Controlling- This is the last function in operation's management as operations manager
have to control all the activities in producing goods and services like in quality, inventory etc. It
the duty of manager to control the quality standards in producing goods and services (Verzuh,
and et.al., 2015). Controlling is very important and all the above functions of operation's
management is depended on control functions.
Management of Operation's as a strategic Oversight
Overseeing the Design- The design of operation's management of Sainsbury is very
effective and efficient as the distribution of duties all the employees are well defined. All the
activities are managed in a strategic way.
Implementation and effectiveness of operation's function- The role or functions played
by operation's management at Sainsbury very effective. The decision that they take are
implemented in a systematic manner as well as they are using the system of effective control that
are very effective and efficient.
Principles of Operation's Management
3
operations management help organization in determining how goods will be manufacture, place
of production and how it will be produced. In service sector like banking, operation manager will
help to plan schemes of interest rates, banking rates etc.
Organizing- This is also the function of operation management which is very important
as after planning, it is mandatory for company to organize the resources to reach the desired
goals and objectives. For example- when Toyota company plans to manufacture a car than there
is need of fund, raw material and other resources (Nunes and et.al., 2018). On the other hand, in
banking sector, they will form a special comity that will discuss the interest rates schemes. This
function has relationship with planning as without planning function, organizing cannot be done.
Coordinating- This is also one of the most important function because if there is no
coordination than it is not possible to achieve the desired goals and objectives. In manufacturing
sector like Toyota company when plan to make a new car than it is required to coordination from
all other departments of organisation and the same in service sector. Coordinating function is
interlinked with above two function as without planning and organizing, coordination function
cannot be performed.
Controlling- This is the last function in operation's management as operations manager
have to control all the activities in producing goods and services like in quality, inventory etc. It
the duty of manager to control the quality standards in producing goods and services (Verzuh,
and et.al., 2015). Controlling is very important and all the above functions of operation's
management is depended on control functions.
Management of Operation's as a strategic Oversight
Overseeing the Design- The design of operation's management of Sainsbury is very
effective and efficient as the distribution of duties all the employees are well defined. All the
activities are managed in a strategic way.
Implementation and effectiveness of operation's function- The role or functions played
by operation's management at Sainsbury very effective. The decision that they take are
implemented in a systematic manner as well as they are using the system of effective control that
are very effective and efficient.
Principles of Operation's Management
3
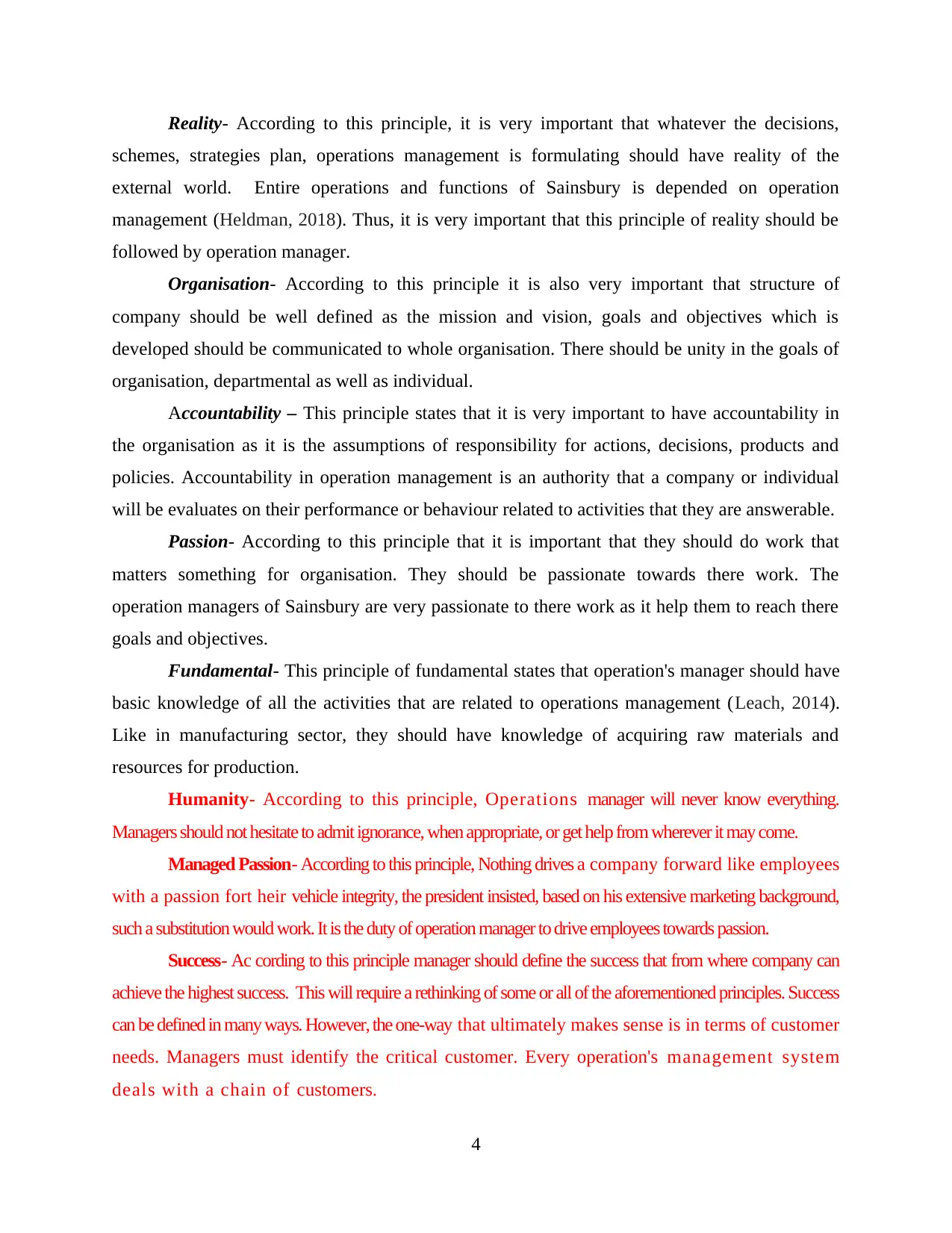
Reality- According to this principle, it is very important that whatever the decisions,
schemes, strategies plan, operations management is formulating should have reality of the
external world. Entire operations and functions of Sainsbury is depended on operation
management (Heldman, 2018). Thus, it is very important that this principle of reality should be
followed by operation manager.
Organisation- According to this principle it is also very important that structure of
company should be well defined as the mission and vision, goals and objectives which is
developed should be communicated to whole organisation. There should be unity in the goals of
organisation, departmental as well as individual.
Accountability – This principle states that it is very important to have accountability in
the organisation as it is the assumptions of responsibility for actions, decisions, products and
policies. Accountability in operation management is an authority that a company or individual
will be evaluates on their performance or behaviour related to activities that they are answerable.
Passion- According to this principle that it is important that they should do work that
matters something for organisation. They should be passionate towards there work. The
operation managers of Sainsbury are very passionate to there work as it help them to reach there
goals and objectives.
Fundamental- This principle of fundamental states that operation's manager should have
basic knowledge of all the activities that are related to operations management (Leach, 2014).
Like in manufacturing sector, they should have knowledge of acquiring raw materials and
resources for production.
Humanity- According to this principle, Operations manager will never know everything.
Managers should not hesitate to admit ignorance, when appropriate, or get help from wherever it may come.
Managed Passion- According to this principle, Nothing drives a company forward like employees
with a passion fort heir vehicle integrity, the president insisted, based on his extensive marketing background,
such a substitution would work. It is the duty of operation manager to drive employees towards passion.
Success- Ac cording to this principle manager should define the success that from where company can
achieve the highest success. This will require a rethinking of some or all of the aforementioned principles. Success
can be defined in many ways. However, the one-way that ultimately makes sense is in terms of customer
needs. Managers must identify the critical customer. Every operation's management system
deals with a chain of customers.
4
schemes, strategies plan, operations management is formulating should have reality of the
external world. Entire operations and functions of Sainsbury is depended on operation
management (Heldman, 2018). Thus, it is very important that this principle of reality should be
followed by operation manager.
Organisation- According to this principle it is also very important that structure of
company should be well defined as the mission and vision, goals and objectives which is
developed should be communicated to whole organisation. There should be unity in the goals of
organisation, departmental as well as individual.
Accountability – This principle states that it is very important to have accountability in
the organisation as it is the assumptions of responsibility for actions, decisions, products and
policies. Accountability in operation management is an authority that a company or individual
will be evaluates on their performance or behaviour related to activities that they are answerable.
Passion- According to this principle that it is important that they should do work that
matters something for organisation. They should be passionate towards there work. The
operation managers of Sainsbury are very passionate to there work as it help them to reach there
goals and objectives.
Fundamental- This principle of fundamental states that operation's manager should have
basic knowledge of all the activities that are related to operations management (Leach, 2014).
Like in manufacturing sector, they should have knowledge of acquiring raw materials and
resources for production.
Humanity- According to this principle, Operations manager will never know everything.
Managers should not hesitate to admit ignorance, when appropriate, or get help from wherever it may come.
Managed Passion- According to this principle, Nothing drives a company forward like employees
with a passion fort heir vehicle integrity, the president insisted, based on his extensive marketing background,
such a substitution would work. It is the duty of operation manager to drive employees towards passion.
Success- Ac cording to this principle manager should define the success that from where company can
achieve the highest success. This will require a rethinking of some or all of the aforementioned principles. Success
can be defined in many ways. However, the one-way that ultimately makes sense is in terms of customer
needs. Managers must identify the critical customer. Every operation's management system
deals with a chain of customers.
4
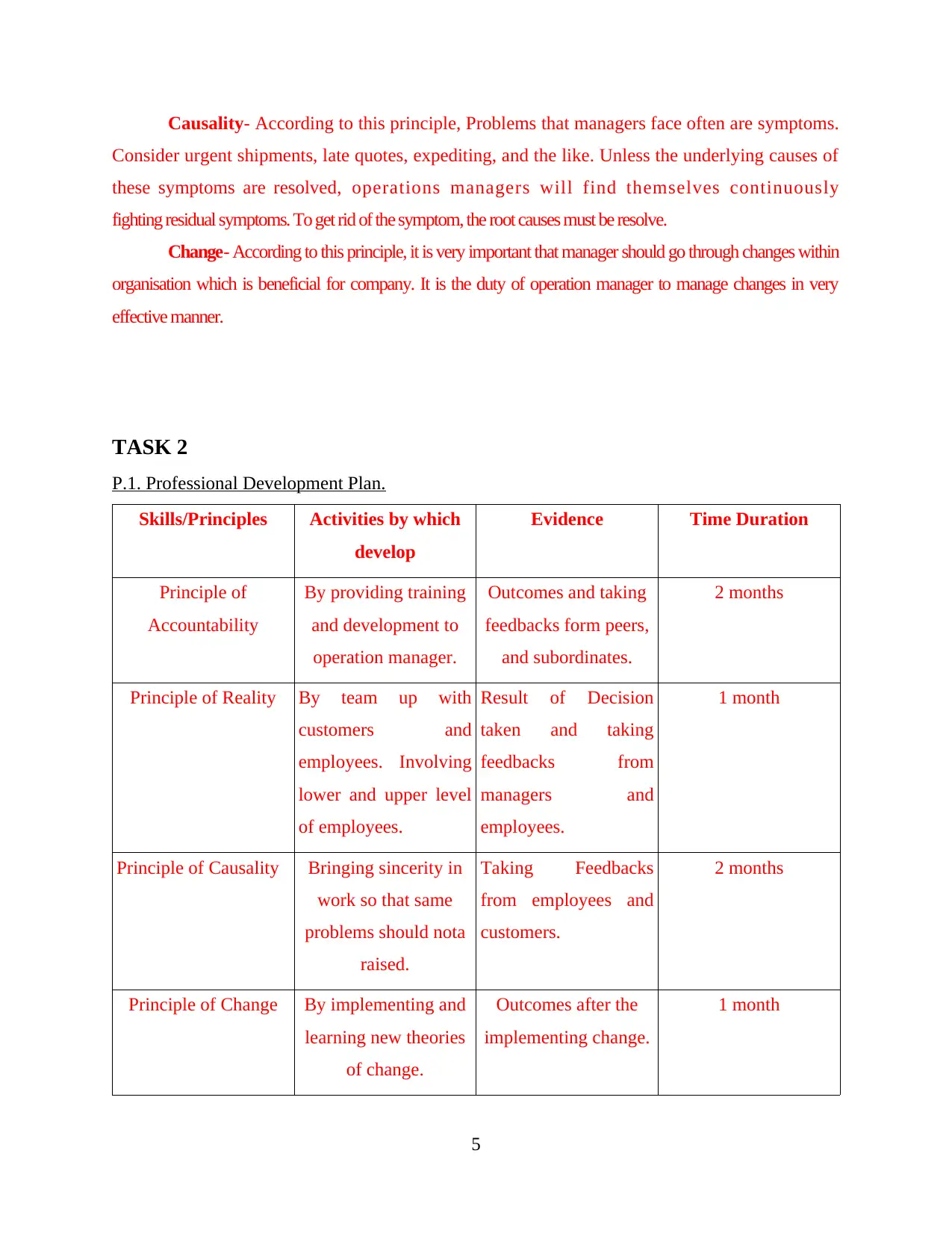
Causality- According to this principle, Problems that managers face often are symptoms.
Consider urgent shipments, late quotes, expediting, and the like. Unless the underlying causes of
these symptoms are resolved, operations managers will find themselves continuously
fighting residual symptoms. To get rid of the symptom, the root causes must be resolve.
Change- According to this principle, it is very important that manager should go through changes within
organisation which is beneficial for company. It is the duty of operation manager to manage changes in very
effective manner.
TASK 2
P.1. Professional Development Plan.
Skills/Principles Activities by which
develop
Evidence Time Duration
Principle of
Accountability
By providing training
and development to
operation manager.
Outcomes and taking
feedbacks form peers,
and subordinates.
2 months
Principle of Reality By team up with
customers and
employees. Involving
lower and upper level
of employees.
Result of Decision
taken and taking
feedbacks from
managers and
employees.
1 month
Principle of Causality Bringing sincerity in
work so that same
problems should nota
raised.
Taking Feedbacks
from employees and
customers.
2 months
Principle of Change By implementing and
learning new theories
of change.
Outcomes after the
implementing change.
1 month
5
Consider urgent shipments, late quotes, expediting, and the like. Unless the underlying causes of
these symptoms are resolved, operations managers will find themselves continuously
fighting residual symptoms. To get rid of the symptom, the root causes must be resolve.
Change- According to this principle, it is very important that manager should go through changes within
organisation which is beneficial for company. It is the duty of operation manager to manage changes in very
effective manner.
TASK 2
P.1. Professional Development Plan.
Skills/Principles Activities by which
develop
Evidence Time Duration
Principle of
Accountability
By providing training
and development to
operation manager.
Outcomes and taking
feedbacks form peers,
and subordinates.
2 months
Principle of Reality By team up with
customers and
employees. Involving
lower and upper level
of employees.
Result of Decision
taken and taking
feedbacks from
managers and
employees.
1 month
Principle of Causality Bringing sincerity in
work so that same
problems should nota
raised.
Taking Feedbacks
from employees and
customers.
2 months
Principle of Change By implementing and
learning new theories
of change.
Outcomes after the
implementing change.
1 month
5
Paraphrase This Document
Need a fresh take? Get an instant paraphrase of this document with our AI Paraphraser
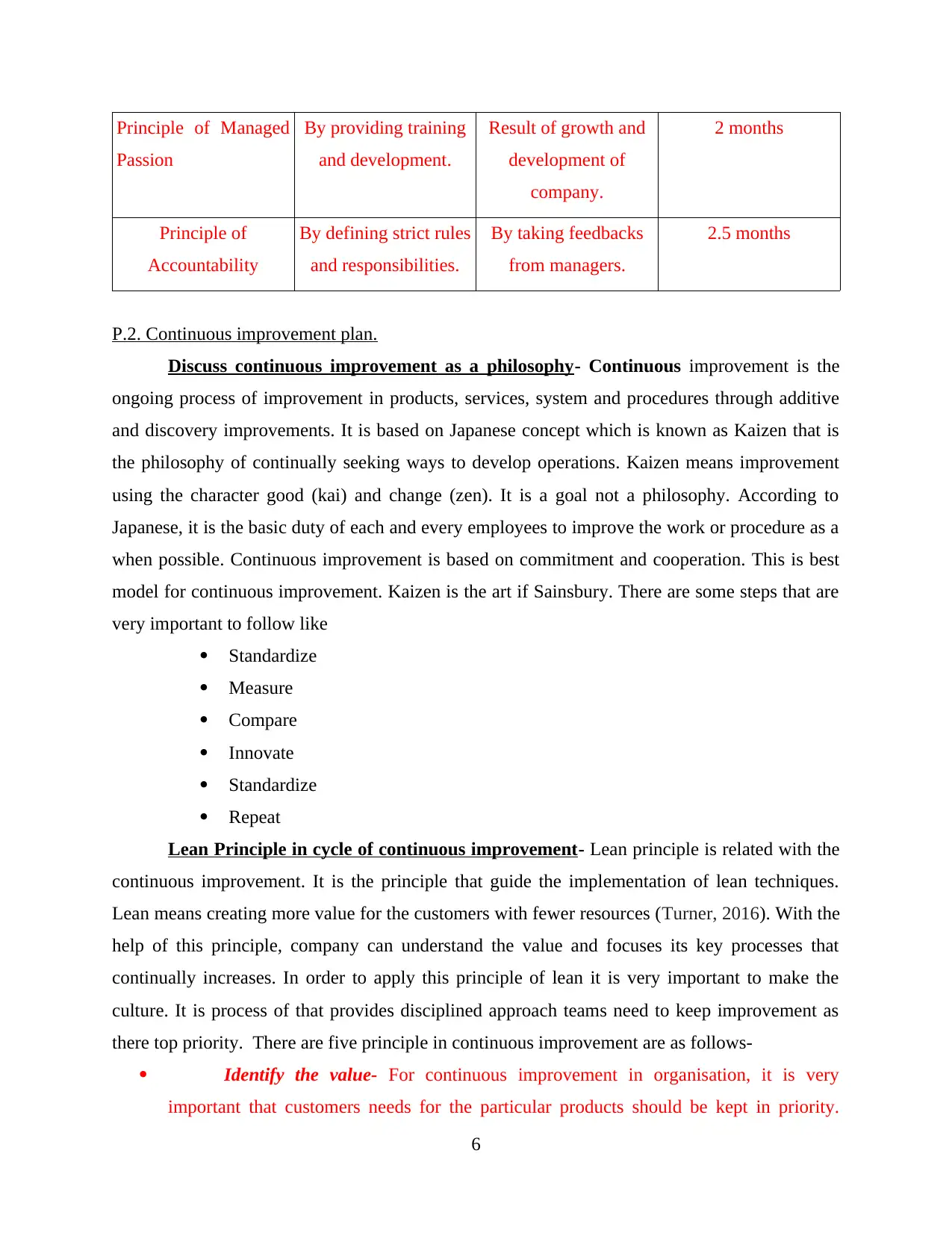
Principle of Managed
Passion
By providing training
and development.
Result of growth and
development of
company.
2 months
Principle of
Accountability
By defining strict rules
and responsibilities.
By taking feedbacks
from managers.
2.5 months
P.2. Continuous improvement plan.
Discuss continuous improvement as a philosophy- Continuous improvement is the
ongoing process of improvement in products, services, system and procedures through additive
and discovery improvements. It is based on Japanese concept which is known as Kaizen that is
the philosophy of continually seeking ways to develop operations. Kaizen means improvement
using the character good (kai) and change (zen). It is a goal not a philosophy. According to
Japanese, it is the basic duty of each and every employees to improve the work or procedure as a
when possible. Continuous improvement is based on commitment and cooperation. This is best
model for continuous improvement. Kaizen is the art if Sainsbury. There are some steps that are
very important to follow like
Standardize
Measure
Compare
Innovate
Standardize
Repeat
Lean Principle in cycle of continuous improvement- Lean principle is related with the
continuous improvement. It is the principle that guide the implementation of lean techniques.
Lean means creating more value for the customers with fewer resources (Turner, 2016). With the
help of this principle, company can understand the value and focuses its key processes that
continually increases. In order to apply this principle of lean it is very important to make the
culture. It is process of that provides disciplined approach teams need to keep improvement as
there top priority. There are five principle in continuous improvement are as follows-
Identify the value- For continuous improvement in organisation, it is very
important that customers needs for the particular products should be kept in priority.
6
Passion
By providing training
and development.
Result of growth and
development of
company.
2 months
Principle of
Accountability
By defining strict rules
and responsibilities.
By taking feedbacks
from managers.
2.5 months
P.2. Continuous improvement plan.
Discuss continuous improvement as a philosophy- Continuous improvement is the
ongoing process of improvement in products, services, system and procedures through additive
and discovery improvements. It is based on Japanese concept which is known as Kaizen that is
the philosophy of continually seeking ways to develop operations. Kaizen means improvement
using the character good (kai) and change (zen). It is a goal not a philosophy. According to
Japanese, it is the basic duty of each and every employees to improve the work or procedure as a
when possible. Continuous improvement is based on commitment and cooperation. This is best
model for continuous improvement. Kaizen is the art if Sainsbury. There are some steps that are
very important to follow like
Standardize
Measure
Compare
Innovate
Standardize
Repeat
Lean Principle in cycle of continuous improvement- Lean principle is related with the
continuous improvement. It is the principle that guide the implementation of lean techniques.
Lean means creating more value for the customers with fewer resources (Turner, 2016). With the
help of this principle, company can understand the value and focuses its key processes that
continually increases. In order to apply this principle of lean it is very important to make the
culture. It is process of that provides disciplined approach teams need to keep improvement as
there top priority. There are five principle in continuous improvement are as follows-
Identify the value- For continuous improvement in organisation, it is very
important that customers needs for the particular products should be kept in priority.
6
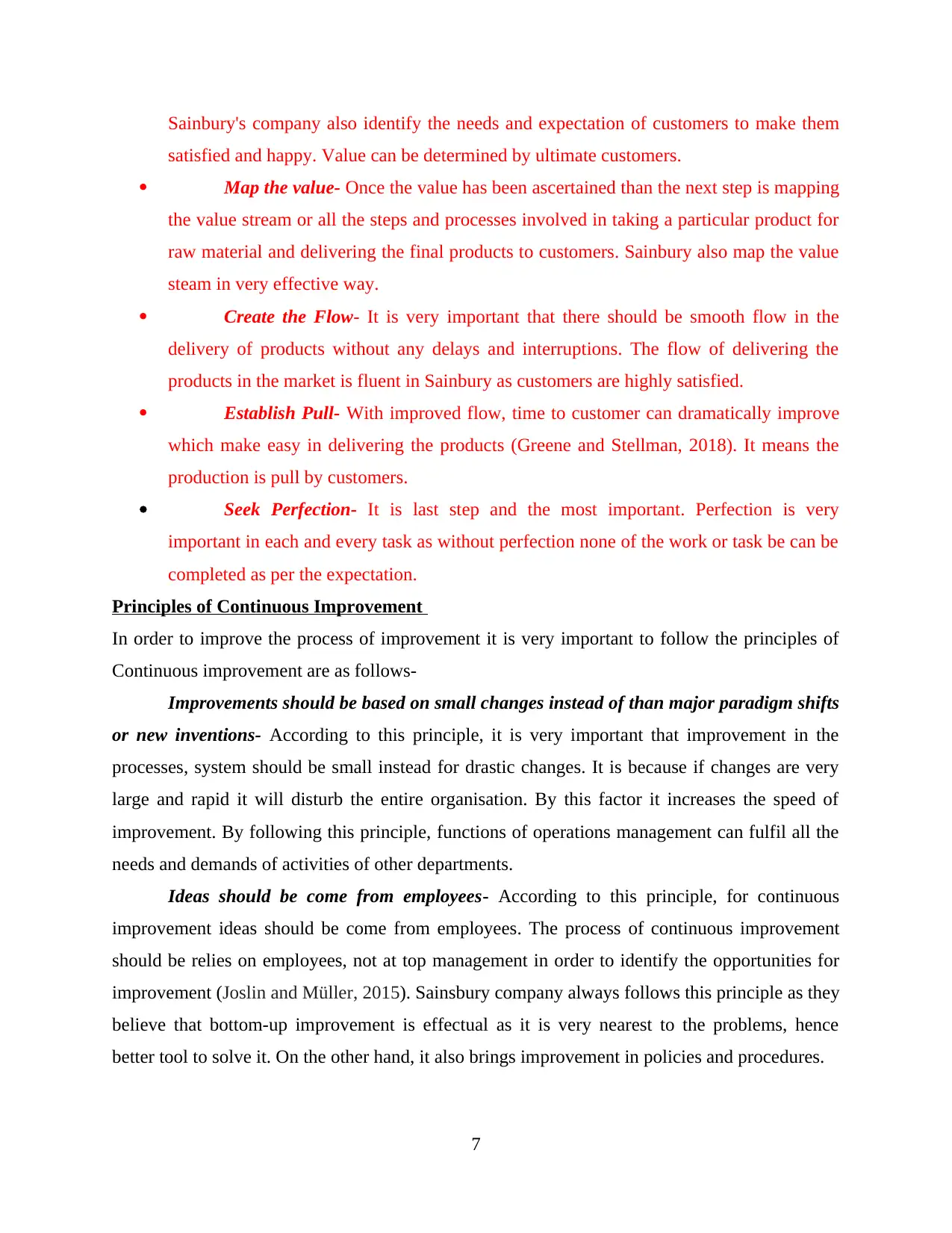
Sainbury's company also identify the needs and expectation of customers to make them
satisfied and happy. Value can be determined by ultimate customers.
Map the value- Once the value has been ascertained than the next step is mapping
the value stream or all the steps and processes involved in taking a particular product for
raw material and delivering the final products to customers. Sainbury also map the value
steam in very effective way.
Create the Flow- It is very important that there should be smooth flow in the
delivery of products without any delays and interruptions. The flow of delivering the
products in the market is fluent in Sainbury as customers are highly satisfied.
Establish Pull- With improved flow, time to customer can dramatically improve
which make easy in delivering the products (Greene and Stellman, 2018). It means the
production is pull by customers.
Seek Perfection- It is last step and the most important. Perfection is very
important in each and every task as without perfection none of the work or task be can be
completed as per the expectation.
Principles of Continuous Improvement
In order to improve the process of improvement it is very important to follow the principles of
Continuous improvement are as follows-
Improvements should be based on small changes instead of than major paradigm shifts
or new inventions- According to this principle, it is very important that improvement in the
processes, system should be small instead for drastic changes. It is because if changes are very
large and rapid it will disturb the entire organisation. By this factor it increases the speed of
improvement. By following this principle, functions of operations management can fulfil all the
needs and demands of activities of other departments.
Ideas should be come from employees- According to this principle, for continuous
improvement ideas should be come from employees. The process of continuous improvement
should be relies on employees, not at top management in order to identify the opportunities for
improvement (Joslin and Müller, 2015). Sainsbury company always follows this principle as they
believe that bottom-up improvement is effectual as it is very nearest to the problems, hence
better tool to solve it. On the other hand, it also brings improvement in policies and procedures.
7
satisfied and happy. Value can be determined by ultimate customers.
Map the value- Once the value has been ascertained than the next step is mapping
the value stream or all the steps and processes involved in taking a particular product for
raw material and delivering the final products to customers. Sainbury also map the value
steam in very effective way.
Create the Flow- It is very important that there should be smooth flow in the
delivery of products without any delays and interruptions. The flow of delivering the
products in the market is fluent in Sainbury as customers are highly satisfied.
Establish Pull- With improved flow, time to customer can dramatically improve
which make easy in delivering the products (Greene and Stellman, 2018). It means the
production is pull by customers.
Seek Perfection- It is last step and the most important. Perfection is very
important in each and every task as without perfection none of the work or task be can be
completed as per the expectation.
Principles of Continuous Improvement
In order to improve the process of improvement it is very important to follow the principles of
Continuous improvement are as follows-
Improvements should be based on small changes instead of than major paradigm shifts
or new inventions- According to this principle, it is very important that improvement in the
processes, system should be small instead for drastic changes. It is because if changes are very
large and rapid it will disturb the entire organisation. By this factor it increases the speed of
improvement. By following this principle, functions of operations management can fulfil all the
needs and demands of activities of other departments.
Ideas should be come from employees- According to this principle, for continuous
improvement ideas should be come from employees. The process of continuous improvement
should be relies on employees, not at top management in order to identify the opportunities for
improvement (Joslin and Müller, 2015). Sainsbury company always follows this principle as they
believe that bottom-up improvement is effectual as it is very nearest to the problems, hence
better tool to solve it. On the other hand, it also brings improvement in policies and procedures.
7
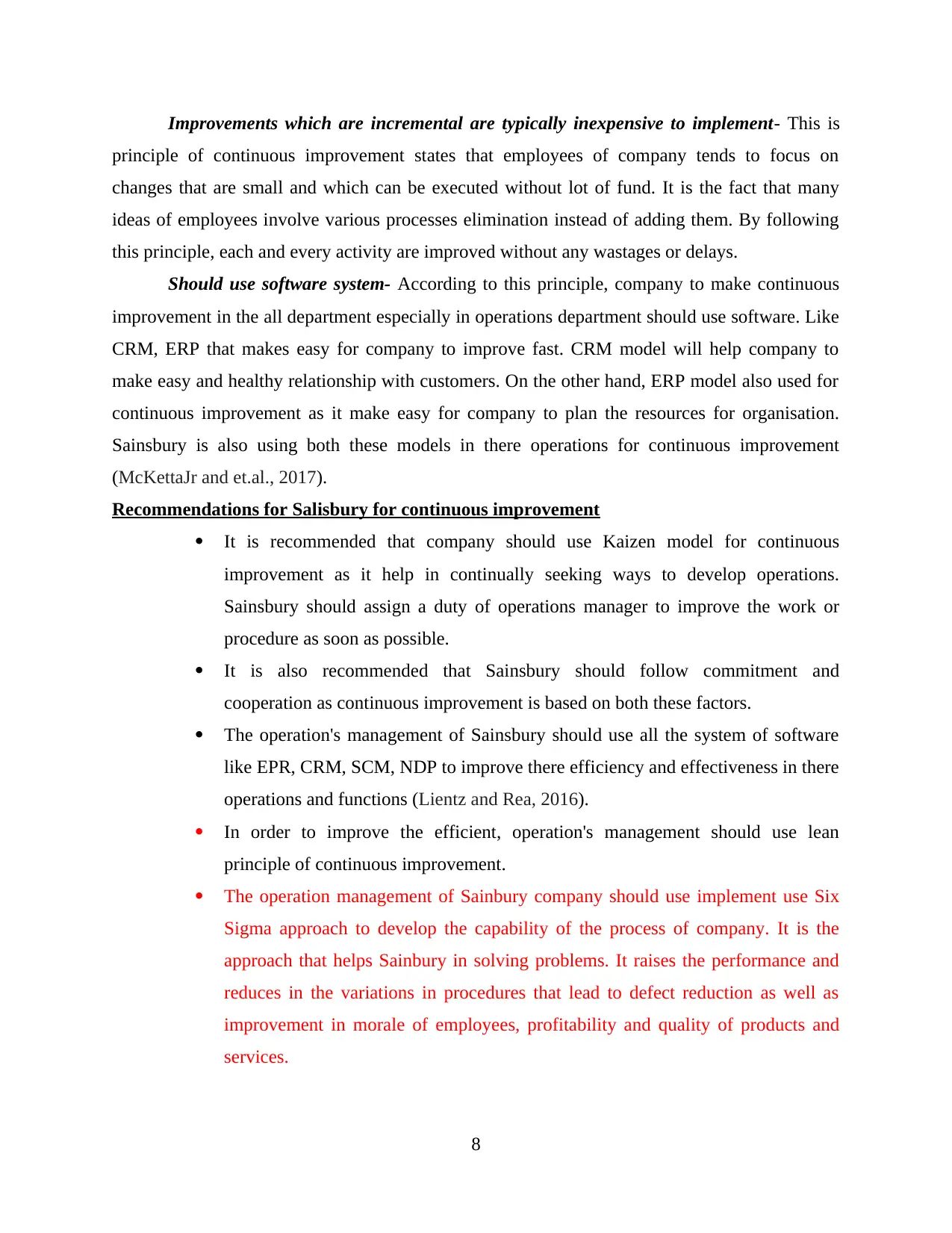
Improvements which are incremental are typically inexpensive to implement- This is
principle of continuous improvement states that employees of company tends to focus on
changes that are small and which can be executed without lot of fund. It is the fact that many
ideas of employees involve various processes elimination instead of adding them. By following
this principle, each and every activity are improved without any wastages or delays.
Should use software system- According to this principle, company to make continuous
improvement in the all department especially in operations department should use software. Like
CRM, ERP that makes easy for company to improve fast. CRM model will help company to
make easy and healthy relationship with customers. On the other hand, ERP model also used for
continuous improvement as it make easy for company to plan the resources for organisation.
Sainsbury is also using both these models in there operations for continuous improvement
(McKettaJr and et.al., 2017).
Recommendations for Salisbury for continuous improvement
It is recommended that company should use Kaizen model for continuous
improvement as it help in continually seeking ways to develop operations.
Sainsbury should assign a duty of operations manager to improve the work or
procedure as soon as possible.
It is also recommended that Sainsbury should follow commitment and
cooperation as continuous improvement is based on both these factors.
The operation's management of Sainsbury should use all the system of software
like EPR, CRM, SCM, NDP to improve there efficiency and effectiveness in there
operations and functions (Lientz and Rea, 2016).
In order to improve the efficient, operation's management should use lean
principle of continuous improvement.
The operation management of Sainbury company should use implement use Six
Sigma approach to develop the capability of the process of company. It is the
approach that helps Sainbury in solving problems. It raises the performance and
reduces in the variations in procedures that lead to defect reduction as well as
improvement in morale of employees, profitability and quality of products and
services.
8
principle of continuous improvement states that employees of company tends to focus on
changes that are small and which can be executed without lot of fund. It is the fact that many
ideas of employees involve various processes elimination instead of adding them. By following
this principle, each and every activity are improved without any wastages or delays.
Should use software system- According to this principle, company to make continuous
improvement in the all department especially in operations department should use software. Like
CRM, ERP that makes easy for company to improve fast. CRM model will help company to
make easy and healthy relationship with customers. On the other hand, ERP model also used for
continuous improvement as it make easy for company to plan the resources for organisation.
Sainsbury is also using both these models in there operations for continuous improvement
(McKettaJr and et.al., 2017).
Recommendations for Salisbury for continuous improvement
It is recommended that company should use Kaizen model for continuous
improvement as it help in continually seeking ways to develop operations.
Sainsbury should assign a duty of operations manager to improve the work or
procedure as soon as possible.
It is also recommended that Sainsbury should follow commitment and
cooperation as continuous improvement is based on both these factors.
The operation's management of Sainsbury should use all the system of software
like EPR, CRM, SCM, NDP to improve there efficiency and effectiveness in there
operations and functions (Lientz and Rea, 2016).
In order to improve the efficient, operation's management should use lean
principle of continuous improvement.
The operation management of Sainbury company should use implement use Six
Sigma approach to develop the capability of the process of company. It is the
approach that helps Sainbury in solving problems. It raises the performance and
reduces in the variations in procedures that lead to defect reduction as well as
improvement in morale of employees, profitability and quality of products and
services.
8
Secure Best Marks with AI Grader
Need help grading? Try our AI Grader for instant feedback on your assignments.
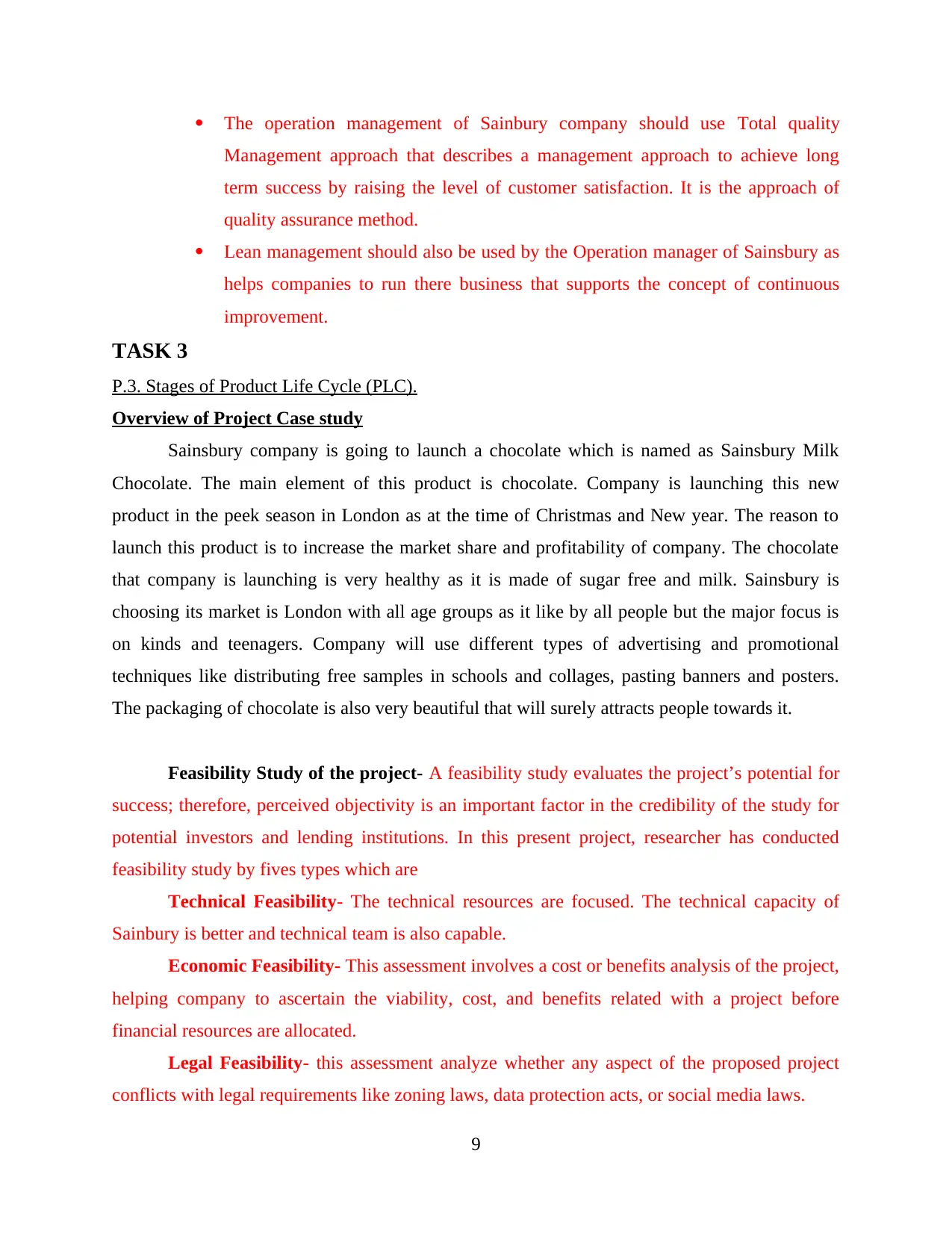
The operation management of Sainbury company should use Total quality
Management approach that describes a management approach to achieve long
term success by raising the level of customer satisfaction. It is the approach of
quality assurance method.
Lean management should also be used by the Operation manager of Sainsbury as
helps companies to run there business that supports the concept of continuous
improvement.
TASK 3
P.3. Stages of Product Life Cycle (PLC).
Overview of Project Case study
Sainsbury company is going to launch a chocolate which is named as Sainsbury Milk
Chocolate. The main element of this product is chocolate. Company is launching this new
product in the peek season in London as at the time of Christmas and New year. The reason to
launch this product is to increase the market share and profitability of company. The chocolate
that company is launching is very healthy as it is made of sugar free and milk. Sainsbury is
choosing its market is London with all age groups as it like by all people but the major focus is
on kinds and teenagers. Company will use different types of advertising and promotional
techniques like distributing free samples in schools and collages, pasting banners and posters.
The packaging of chocolate is also very beautiful that will surely attracts people towards it.
Feasibility Study of the project- A feasibility study evaluates the project’s potential for
success; therefore, perceived objectivity is an important factor in the credibility of the study for
potential investors and lending institutions. In this present project, researcher has conducted
feasibility study by fives types which are
Technical Feasibility- The technical resources are focused. The technical capacity of
Sainbury is better and technical team is also capable.
Economic Feasibility- This assessment involves a cost or benefits analysis of the project,
helping company to ascertain the viability, cost, and benefits related with a project before
financial resources are allocated.
Legal Feasibility- this assessment analyze whether any aspect of the proposed project
conflicts with legal requirements like zoning laws, data protection acts, or social media laws.
9
Management approach that describes a management approach to achieve long
term success by raising the level of customer satisfaction. It is the approach of
quality assurance method.
Lean management should also be used by the Operation manager of Sainsbury as
helps companies to run there business that supports the concept of continuous
improvement.
TASK 3
P.3. Stages of Product Life Cycle (PLC).
Overview of Project Case study
Sainsbury company is going to launch a chocolate which is named as Sainsbury Milk
Chocolate. The main element of this product is chocolate. Company is launching this new
product in the peek season in London as at the time of Christmas and New year. The reason to
launch this product is to increase the market share and profitability of company. The chocolate
that company is launching is very healthy as it is made of sugar free and milk. Sainsbury is
choosing its market is London with all age groups as it like by all people but the major focus is
on kinds and teenagers. Company will use different types of advertising and promotional
techniques like distributing free samples in schools and collages, pasting banners and posters.
The packaging of chocolate is also very beautiful that will surely attracts people towards it.
Feasibility Study of the project- A feasibility study evaluates the project’s potential for
success; therefore, perceived objectivity is an important factor in the credibility of the study for
potential investors and lending institutions. In this present project, researcher has conducted
feasibility study by fives types which are
Technical Feasibility- The technical resources are focused. The technical capacity of
Sainbury is better and technical team is also capable.
Economic Feasibility- This assessment involves a cost or benefits analysis of the project,
helping company to ascertain the viability, cost, and benefits related with a project before
financial resources are allocated.
Legal Feasibility- this assessment analyze whether any aspect of the proposed project
conflicts with legal requirements like zoning laws, data protection acts, or social media laws.
9
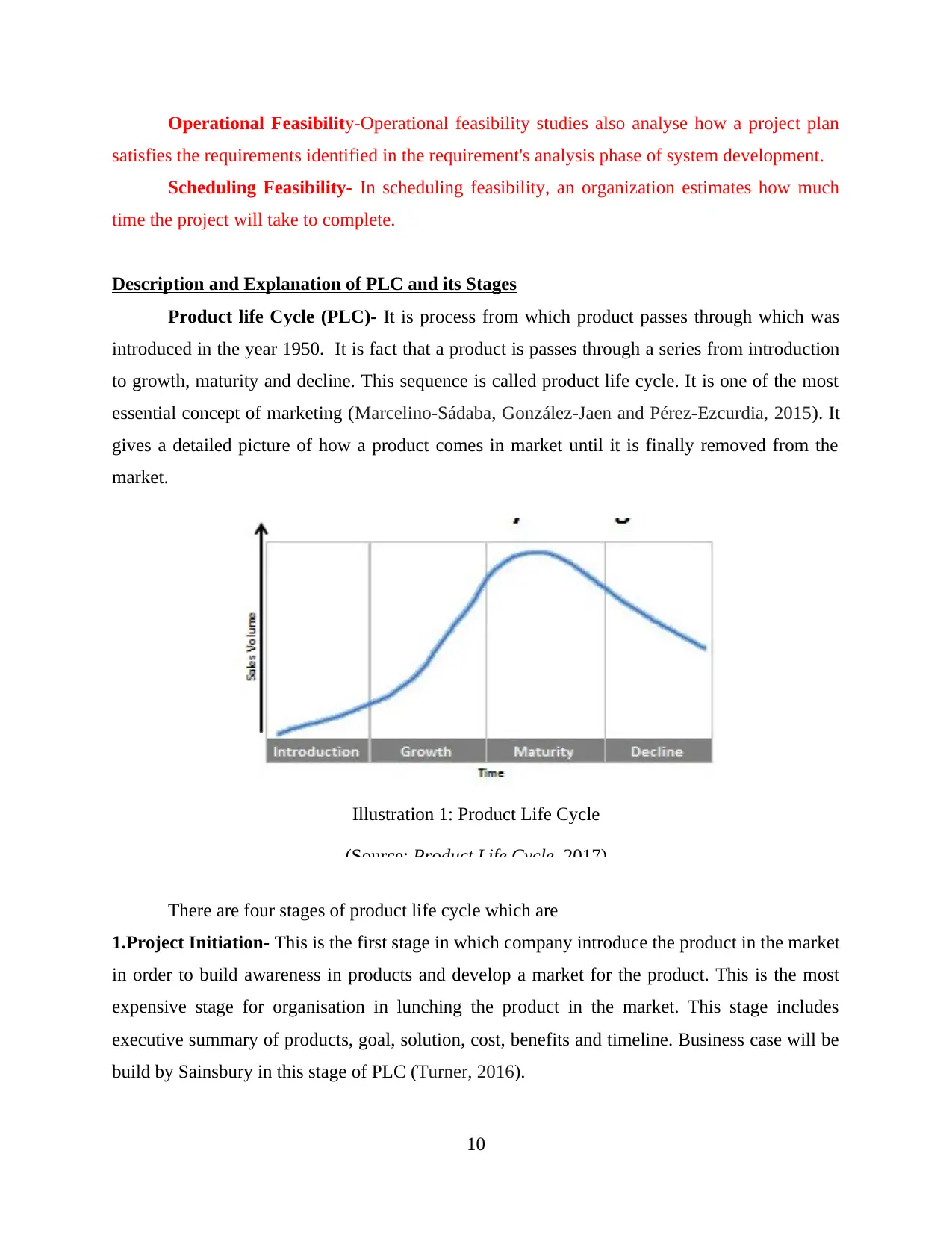
Operational Feasibility-Operational feasibility studies also analyse how a project plan
satisfies the requirements identified in the requirement's analysis phase of system development.
Scheduling Feasibility- In scheduling feasibility, an organization estimates how much
time the project will take to complete.
Description and Explanation of PLC and its Stages
Product life Cycle (PLC)- It is process from which product passes through which was
introduced in the year 1950. It is fact that a product is passes through a series from introduction
to growth, maturity and decline. This sequence is called product life cycle. It is one of the most
essential concept of marketing (Marcelino-Sádaba, González-Jaen and Pérez-Ezcurdia, 2015). It
gives a detailed picture of how a product comes in market until it is finally removed from the
market.
There are four stages of product life cycle which are
1.Project Initiation- This is the first stage in which company introduce the product in the market
in order to build awareness in products and develop a market for the product. This is the most
expensive stage for organisation in lunching the product in the market. This stage includes
executive summary of products, goal, solution, cost, benefits and timeline. Business case will be
build by Sainsbury in this stage of PLC (Turner, 2016).
10
Illustration 1: Product Life Cycle
(Source: Product Life Cycle, 2017)
satisfies the requirements identified in the requirement's analysis phase of system development.
Scheduling Feasibility- In scheduling feasibility, an organization estimates how much
time the project will take to complete.
Description and Explanation of PLC and its Stages
Product life Cycle (PLC)- It is process from which product passes through which was
introduced in the year 1950. It is fact that a product is passes through a series from introduction
to growth, maturity and decline. This sequence is called product life cycle. It is one of the most
essential concept of marketing (Marcelino-Sádaba, González-Jaen and Pérez-Ezcurdia, 2015). It
gives a detailed picture of how a product comes in market until it is finally removed from the
market.
There are four stages of product life cycle which are
1.Project Initiation- This is the first stage in which company introduce the product in the market
in order to build awareness in products and develop a market for the product. This is the most
expensive stage for organisation in lunching the product in the market. This stage includes
executive summary of products, goal, solution, cost, benefits and timeline. Business case will be
build by Sainsbury in this stage of PLC (Turner, 2016).
10
Illustration 1: Product Life Cycle
(Source: Product Life Cycle, 2017)
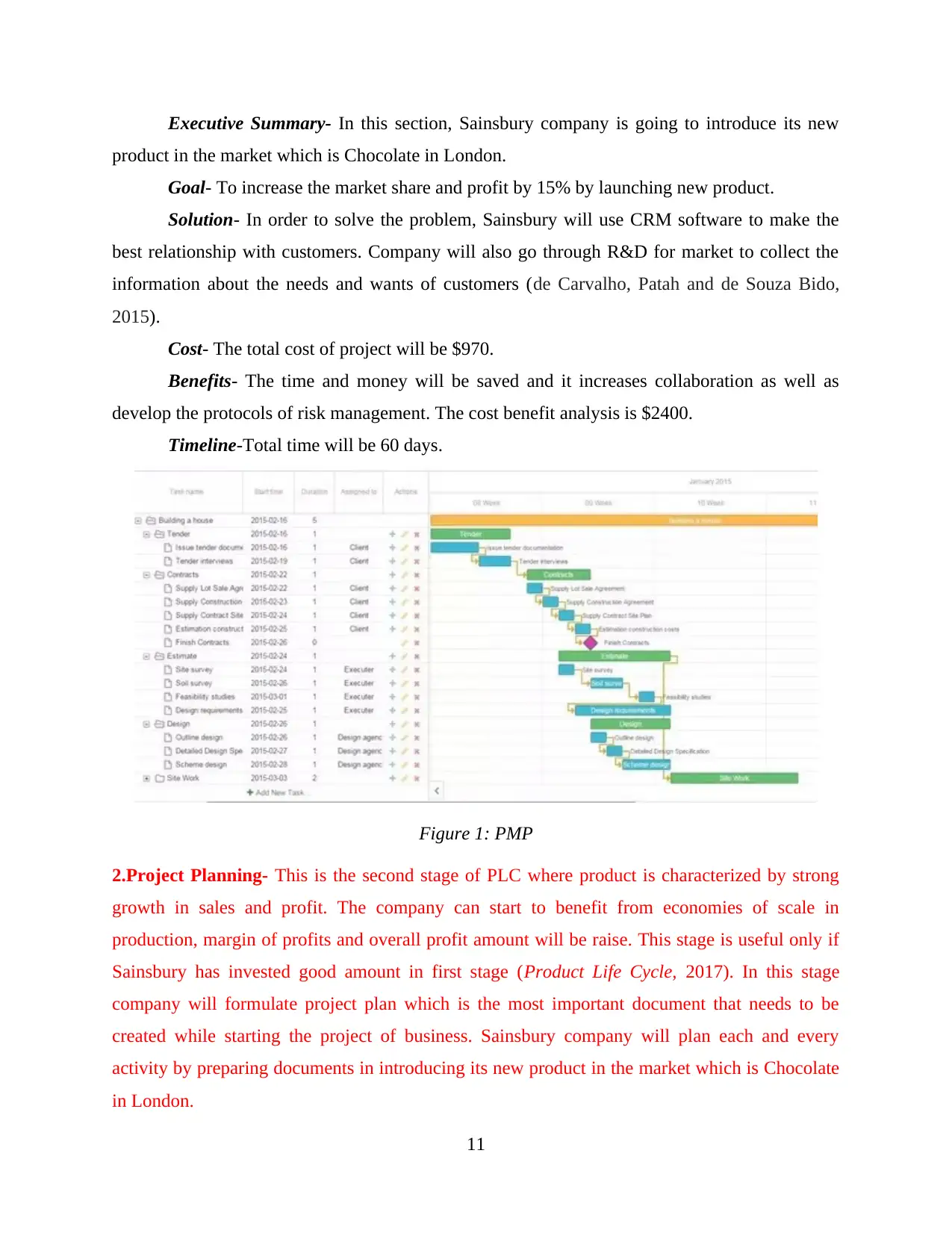
Executive Summary- In this section, Sainsbury company is going to introduce its new
product in the market which is Chocolate in London.
Goal- To increase the market share and profit by 15% by launching new product.
Solution- In order to solve the problem, Sainsbury will use CRM software to make the
best relationship with customers. Company will also go through R&D for market to collect the
information about the needs and wants of customers (de Carvalho, Patah and de Souza Bido,
2015).
Cost- The total cost of project will be $970.
Benefits- The time and money will be saved and it increases collaboration as well as
develop the protocols of risk management. The cost benefit analysis is $2400.
Timeline-Total time will be 60 days.
Figure 1: PMP
2.Project Planning- This is the second stage of PLC where product is characterized by strong
growth in sales and profit. The company can start to benefit from economies of scale in
production, margin of profits and overall profit amount will be raise. This stage is useful only if
Sainsbury has invested good amount in first stage (Product Life Cycle, 2017). In this stage
company will formulate project plan which is the most important document that needs to be
created while starting the project of business. Sainsbury company will plan each and every
activity by preparing documents in introducing its new product in the market which is Chocolate
in London.
11
product in the market which is Chocolate in London.
Goal- To increase the market share and profit by 15% by launching new product.
Solution- In order to solve the problem, Sainsbury will use CRM software to make the
best relationship with customers. Company will also go through R&D for market to collect the
information about the needs and wants of customers (de Carvalho, Patah and de Souza Bido,
2015).
Cost- The total cost of project will be $970.
Benefits- The time and money will be saved and it increases collaboration as well as
develop the protocols of risk management. The cost benefit analysis is $2400.
Timeline-Total time will be 60 days.
Figure 1: PMP
2.Project Planning- This is the second stage of PLC where product is characterized by strong
growth in sales and profit. The company can start to benefit from economies of scale in
production, margin of profits and overall profit amount will be raise. This stage is useful only if
Sainsbury has invested good amount in first stage (Product Life Cycle, 2017). In this stage
company will formulate project plan which is the most important document that needs to be
created while starting the project of business. Sainsbury company will plan each and every
activity by preparing documents in introducing its new product in the market which is Chocolate
in London.
11
Paraphrase This Document
Need a fresh take? Get an instant paraphrase of this document with our AI Paraphraser
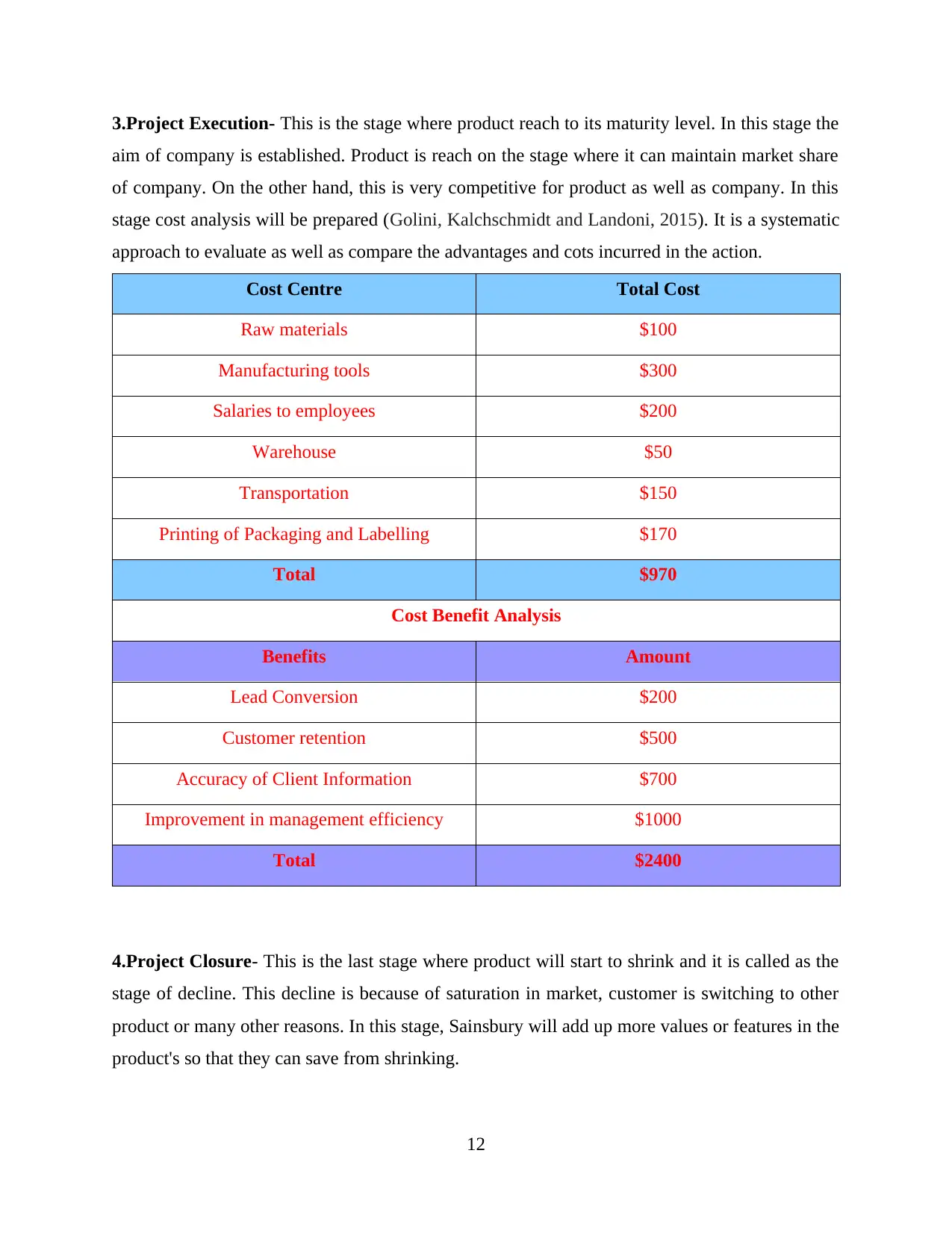
3.Project Execution- This is the stage where product reach to its maturity level. In this stage the
aim of company is established. Product is reach on the stage where it can maintain market share
of company. On the other hand, this is very competitive for product as well as company. In this
stage cost analysis will be prepared (Golini, Kalchschmidt and Landoni, 2015). It is a systematic
approach to evaluate as well as compare the advantages and cots incurred in the action.
Cost Centre Total Cost
Raw materials $100
Manufacturing tools $300
Salaries to employees $200
Warehouse $50
Transportation $150
Printing of Packaging and Labelling $170
Total $970
Cost Benefit Analysis
Benefits Amount
Lead Conversion $200
Customer retention $500
Accuracy of Client Information $700
Improvement in management efficiency $1000
Total $2400
4.Project Closure- This is the last stage where product will start to shrink and it is called as the
stage of decline. This decline is because of saturation in market, customer is switching to other
product or many other reasons. In this stage, Sainsbury will add up more values or features in the
product's so that they can save from shrinking.
12
aim of company is established. Product is reach on the stage where it can maintain market share
of company. On the other hand, this is very competitive for product as well as company. In this
stage cost analysis will be prepared (Golini, Kalchschmidt and Landoni, 2015). It is a systematic
approach to evaluate as well as compare the advantages and cots incurred in the action.
Cost Centre Total Cost
Raw materials $100
Manufacturing tools $300
Salaries to employees $200
Warehouse $50
Transportation $150
Printing of Packaging and Labelling $170
Total $970
Cost Benefit Analysis
Benefits Amount
Lead Conversion $200
Customer retention $500
Accuracy of Client Information $700
Improvement in management efficiency $1000
Total $2400
4.Project Closure- This is the last stage where product will start to shrink and it is called as the
stage of decline. This decline is because of saturation in market, customer is switching to other
product or many other reasons. In this stage, Sainsbury will add up more values or features in the
product's so that they can save from shrinking.
12
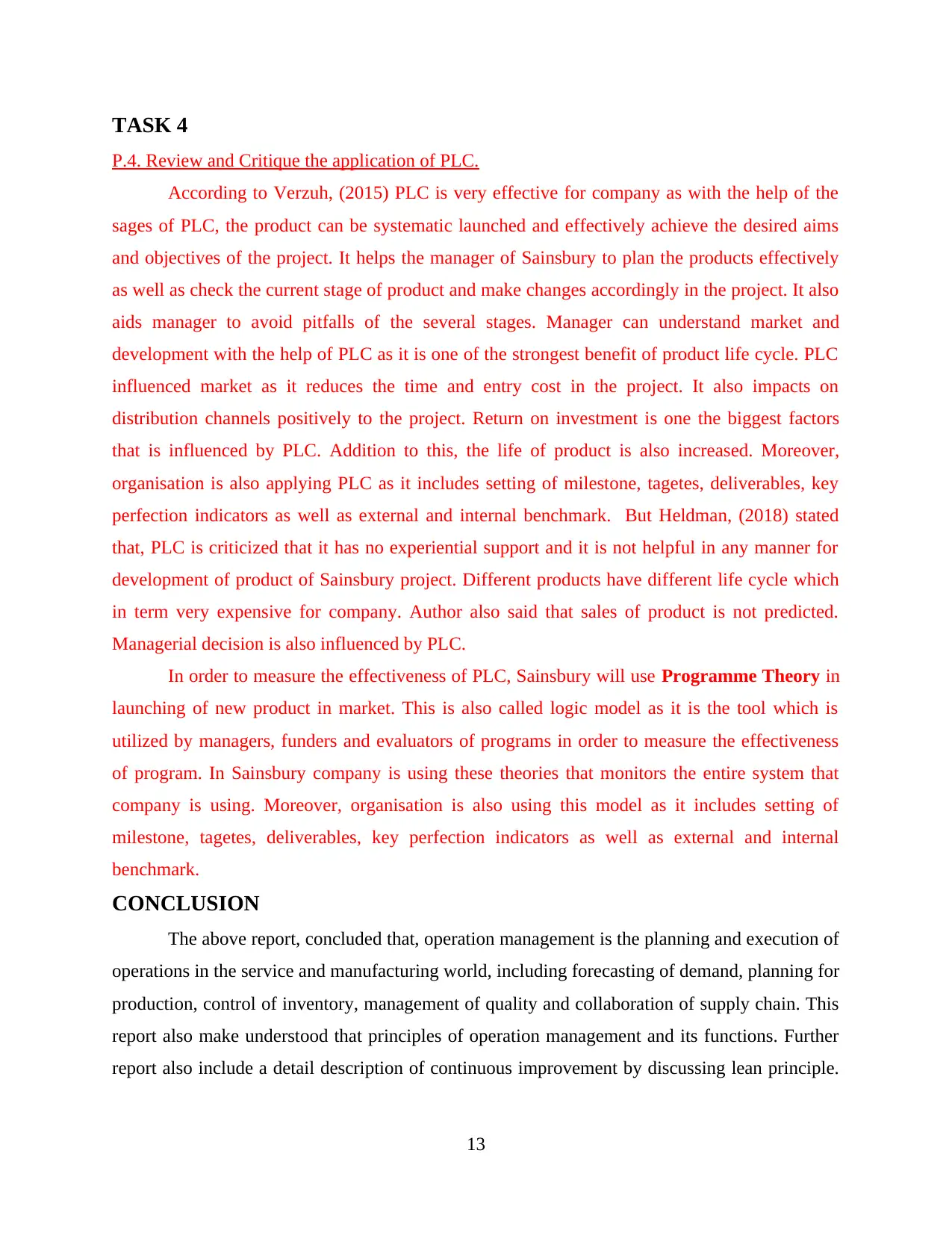
TASK 4
P.4. Review and Critique the application of PLC.
According to Verzuh, (2015) PLC is very effective for company as with the help of the
sages of PLC, the product can be systematic launched and effectively achieve the desired aims
and objectives of the project. It helps the manager of Sainsbury to plan the products effectively
as well as check the current stage of product and make changes accordingly in the project. It also
aids manager to avoid pitfalls of the several stages. Manager can understand market and
development with the help of PLC as it is one of the strongest benefit of product life cycle. PLC
influenced market as it reduces the time and entry cost in the project. It also impacts on
distribution channels positively to the project. Return on investment is one the biggest factors
that is influenced by PLC. Addition to this, the life of product is also increased. Moreover,
organisation is also applying PLC as it includes setting of milestone, tagetes, deliverables, key
perfection indicators as well as external and internal benchmark. But Heldman, (2018) stated
that, PLC is criticized that it has no experiential support and it is not helpful in any manner for
development of product of Sainsbury project. Different products have different life cycle which
in term very expensive for company. Author also said that sales of product is not predicted.
Managerial decision is also influenced by PLC.
In order to measure the effectiveness of PLC, Sainsbury will use Programme Theory in
launching of new product in market. This is also called logic model as it is the tool which is
utilized by managers, funders and evaluators of programs in order to measure the effectiveness
of program. In Sainsbury company is using these theories that monitors the entire system that
company is using. Moreover, organisation is also using this model as it includes setting of
milestone, tagetes, deliverables, key perfection indicators as well as external and internal
benchmark.
CONCLUSION
The above report, concluded that, operation management is the planning and execution of
operations in the service and manufacturing world, including forecasting of demand, planning for
production, control of inventory, management of quality and collaboration of supply chain. This
report also make understood that principles of operation management and its functions. Further
report also include a detail description of continuous improvement by discussing lean principle.
13
P.4. Review and Critique the application of PLC.
According to Verzuh, (2015) PLC is very effective for company as with the help of the
sages of PLC, the product can be systematic launched and effectively achieve the desired aims
and objectives of the project. It helps the manager of Sainsbury to plan the products effectively
as well as check the current stage of product and make changes accordingly in the project. It also
aids manager to avoid pitfalls of the several stages. Manager can understand market and
development with the help of PLC as it is one of the strongest benefit of product life cycle. PLC
influenced market as it reduces the time and entry cost in the project. It also impacts on
distribution channels positively to the project. Return on investment is one the biggest factors
that is influenced by PLC. Addition to this, the life of product is also increased. Moreover,
organisation is also applying PLC as it includes setting of milestone, tagetes, deliverables, key
perfection indicators as well as external and internal benchmark. But Heldman, (2018) stated
that, PLC is criticized that it has no experiential support and it is not helpful in any manner for
development of product of Sainsbury project. Different products have different life cycle which
in term very expensive for company. Author also said that sales of product is not predicted.
Managerial decision is also influenced by PLC.
In order to measure the effectiveness of PLC, Sainsbury will use Programme Theory in
launching of new product in market. This is also called logic model as it is the tool which is
utilized by managers, funders and evaluators of programs in order to measure the effectiveness
of program. In Sainsbury company is using these theories that monitors the entire system that
company is using. Moreover, organisation is also using this model as it includes setting of
milestone, tagetes, deliverables, key perfection indicators as well as external and internal
benchmark.
CONCLUSION
The above report, concluded that, operation management is the planning and execution of
operations in the service and manufacturing world, including forecasting of demand, planning for
production, control of inventory, management of quality and collaboration of supply chain. This
report also make understood that principles of operation management and its functions. Further
report also include a detail description of continuous improvement by discussing lean principle.
13
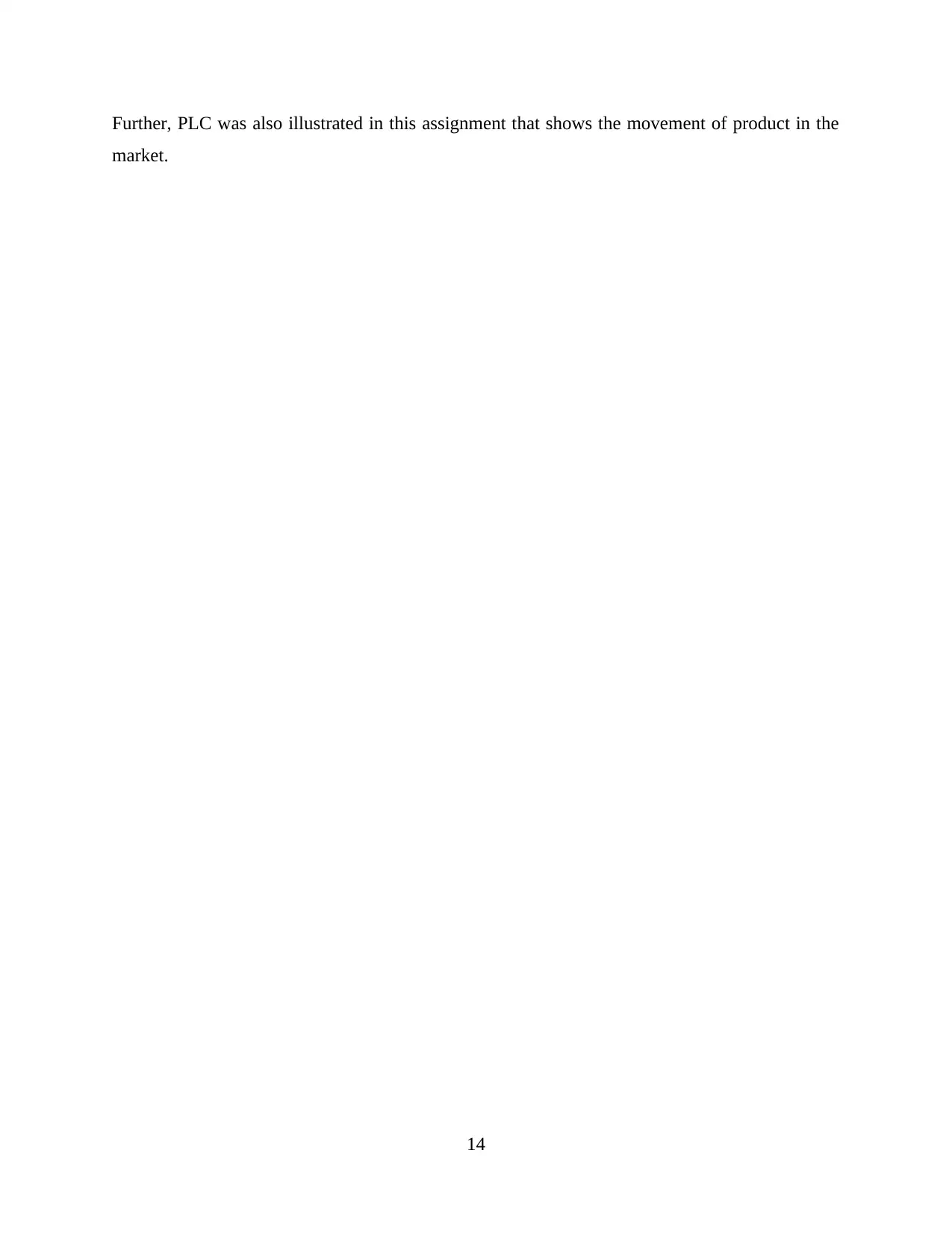
Further, PLC was also illustrated in this assignment that shows the movement of product in the
market.
14
market.
14
Secure Best Marks with AI Grader
Need help grading? Try our AI Grader for instant feedback on your assignments.
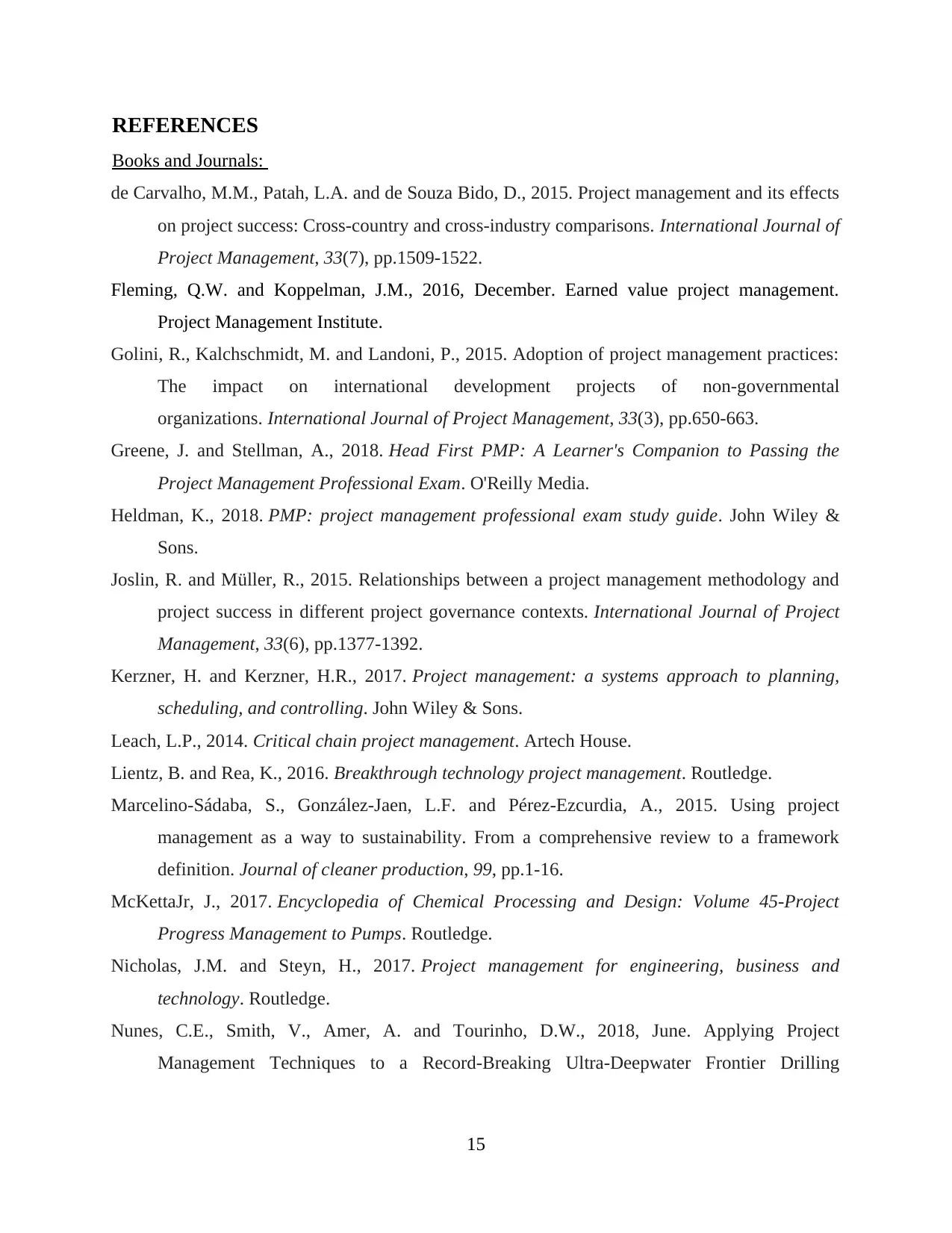
REFERENCES
Books and Journals:
de Carvalho, M.M., Patah, L.A. and de Souza Bido, D., 2015. Project management and its effects
on project success: Cross-country and cross-industry comparisons. International Journal of
Project Management, 33(7), pp.1509-1522.
Fleming, Q.W. and Koppelman, J.M., 2016, December. Earned value project management.
Project Management Institute.
Golini, R., Kalchschmidt, M. and Landoni, P., 2015. Adoption of project management practices:
The impact on international development projects of non-governmental
organizations. International Journal of Project Management, 33(3), pp.650-663.
Greene, J. and Stellman, A., 2018. Head First PMP: A Learner's Companion to Passing the
Project Management Professional Exam. O'Reilly Media.
Heldman, K., 2018. PMP: project management professional exam study guide. John Wiley &
Sons.
Joslin, R. and Müller, R., 2015. Relationships between a project management methodology and
project success in different project governance contexts. International Journal of Project
Management, 33(6), pp.1377-1392.
Kerzner, H. and Kerzner, H.R., 2017. Project management: a systems approach to planning,
scheduling, and controlling. John Wiley & Sons.
Leach, L.P., 2014. Critical chain project management. Artech House.
Lientz, B. and Rea, K., 2016. Breakthrough technology project management. Routledge.
Marcelino-Sádaba, S., González-Jaen, L.F. and Pérez-Ezcurdia, A., 2015. Using project
management as a way to sustainability. From a comprehensive review to a framework
definition. Journal of cleaner production, 99, pp.1-16.
McKettaJr, J., 2017. Encyclopedia of Chemical Processing and Design: Volume 45-Project
Progress Management to Pumps. Routledge.
Nicholas, J.M. and Steyn, H., 2017. Project management for engineering, business and
technology. Routledge.
Nunes, C.E., Smith, V., Amer, A. and Tourinho, D.W., 2018, June. Applying Project
Management Techniques to a Record-Breaking Ultra-Deepwater Frontier Drilling
15
Books and Journals:
de Carvalho, M.M., Patah, L.A. and de Souza Bido, D., 2015. Project management and its effects
on project success: Cross-country and cross-industry comparisons. International Journal of
Project Management, 33(7), pp.1509-1522.
Fleming, Q.W. and Koppelman, J.M., 2016, December. Earned value project management.
Project Management Institute.
Golini, R., Kalchschmidt, M. and Landoni, P., 2015. Adoption of project management practices:
The impact on international development projects of non-governmental
organizations. International Journal of Project Management, 33(3), pp.650-663.
Greene, J. and Stellman, A., 2018. Head First PMP: A Learner's Companion to Passing the
Project Management Professional Exam. O'Reilly Media.
Heldman, K., 2018. PMP: project management professional exam study guide. John Wiley &
Sons.
Joslin, R. and Müller, R., 2015. Relationships between a project management methodology and
project success in different project governance contexts. International Journal of Project
Management, 33(6), pp.1377-1392.
Kerzner, H. and Kerzner, H.R., 2017. Project management: a systems approach to planning,
scheduling, and controlling. John Wiley & Sons.
Leach, L.P., 2014. Critical chain project management. Artech House.
Lientz, B. and Rea, K., 2016. Breakthrough technology project management. Routledge.
Marcelino-Sádaba, S., González-Jaen, L.F. and Pérez-Ezcurdia, A., 2015. Using project
management as a way to sustainability. From a comprehensive review to a framework
definition. Journal of cleaner production, 99, pp.1-16.
McKettaJr, J., 2017. Encyclopedia of Chemical Processing and Design: Volume 45-Project
Progress Management to Pumps. Routledge.
Nicholas, J.M. and Steyn, H., 2017. Project management for engineering, business and
technology. Routledge.
Nunes, C.E., Smith, V., Amer, A. and Tourinho, D.W., 2018, June. Applying Project
Management Techniques to a Record-Breaking Ultra-Deepwater Frontier Drilling
15
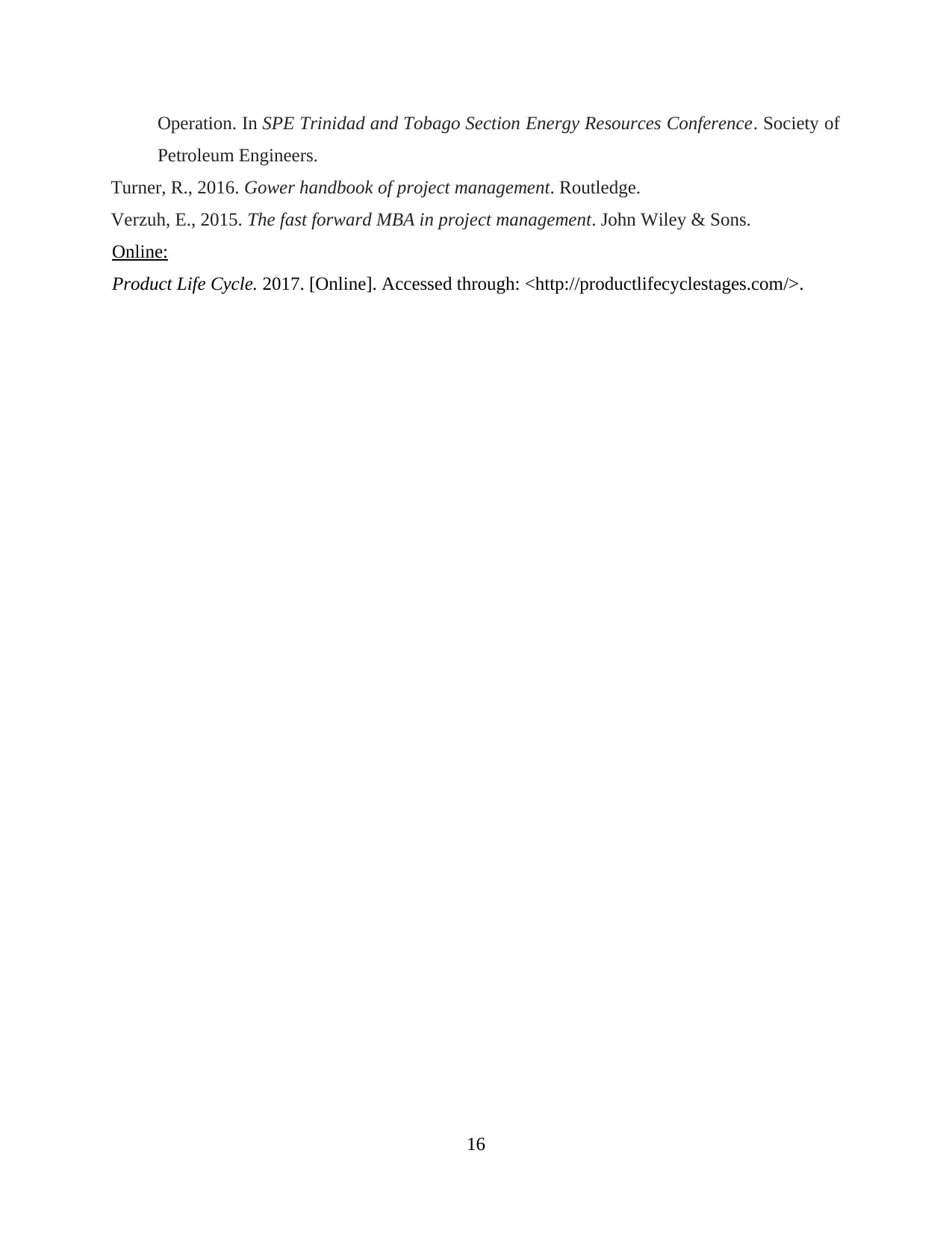
Operation. In SPE Trinidad and Tobago Section Energy Resources Conference. Society of
Petroleum Engineers.
Turner, R., 2016. Gower handbook of project management. Routledge.
Verzuh, E., 2015. The fast forward MBA in project management. John Wiley & Sons.
Online:
Product Life Cycle. 2017. [Online]. Accessed through: <http://productlifecyclestages.com/>.
16
Petroleum Engineers.
Turner, R., 2016. Gower handbook of project management. Routledge.
Verzuh, E., 2015. The fast forward MBA in project management. John Wiley & Sons.
Online:
Product Life Cycle. 2017. [Online]. Accessed through: <http://productlifecyclestages.com/>.
16
1 out of 18
Related Documents
![[object Object]](/_next/image/?url=%2F_next%2Fstatic%2Fmedia%2Flogo.6d15ce61.png&w=640&q=75)
Your All-in-One AI-Powered Toolkit for Academic Success.
+13062052269
info@desklib.com
Available 24*7 on WhatsApp / Email
Unlock your academic potential
© 2024 | Zucol Services PVT LTD | All rights reserved.