Quality mamagement for organisational exellence
VerifiedAdded on 2023/01/11
|12
|4039
|39
AI Summary
I will upload the document requirements
Contribute Materials
Your contribution can guide someone’s learning journey. Share your
documents today.
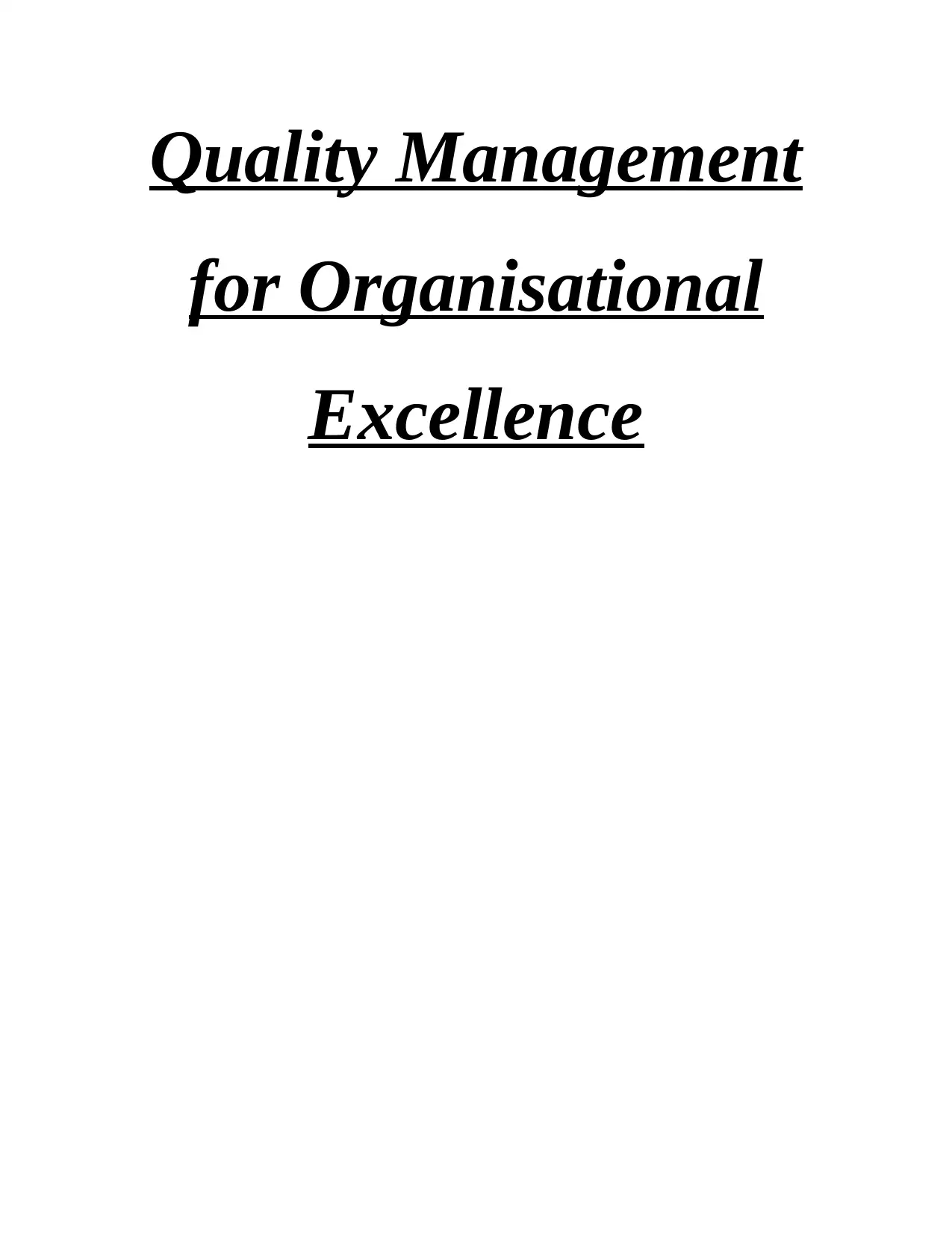
Quality Management
for Organisational
Excellence
for Organisational
Excellence
Secure Best Marks with AI Grader
Need help grading? Try our AI Grader for instant feedback on your assignments.
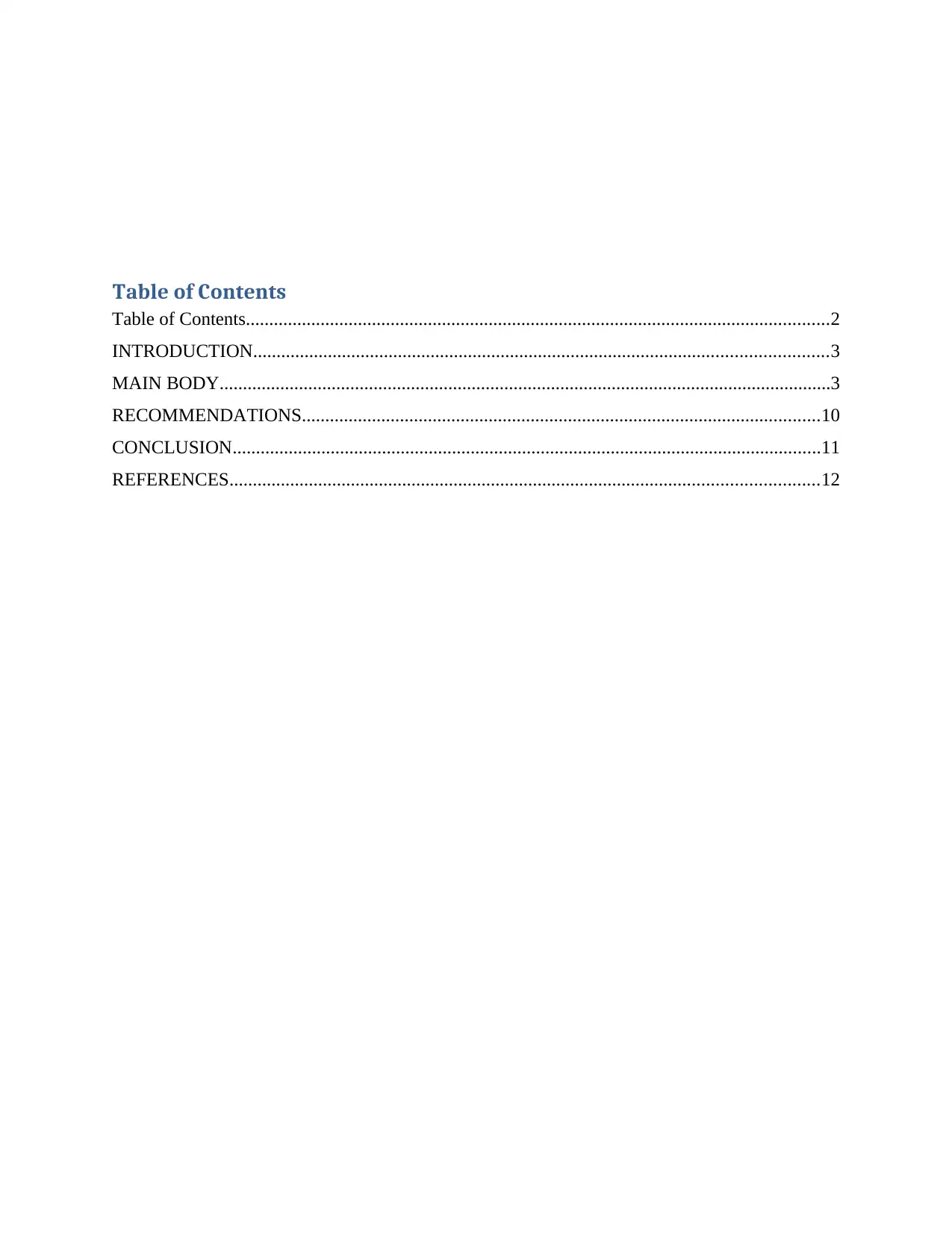
Table of Contents
Table of Contents.............................................................................................................................2
INTRODUCTION...........................................................................................................................3
MAIN BODY...................................................................................................................................3
RECOMMENDATIONS...............................................................................................................10
CONCLUSION..............................................................................................................................11
REFERENCES..............................................................................................................................12
Table of Contents.............................................................................................................................2
INTRODUCTION...........................................................................................................................3
MAIN BODY...................................................................................................................................3
RECOMMENDATIONS...............................................................................................................10
CONCLUSION..............................................................................................................................11
REFERENCES..............................................................................................................................12
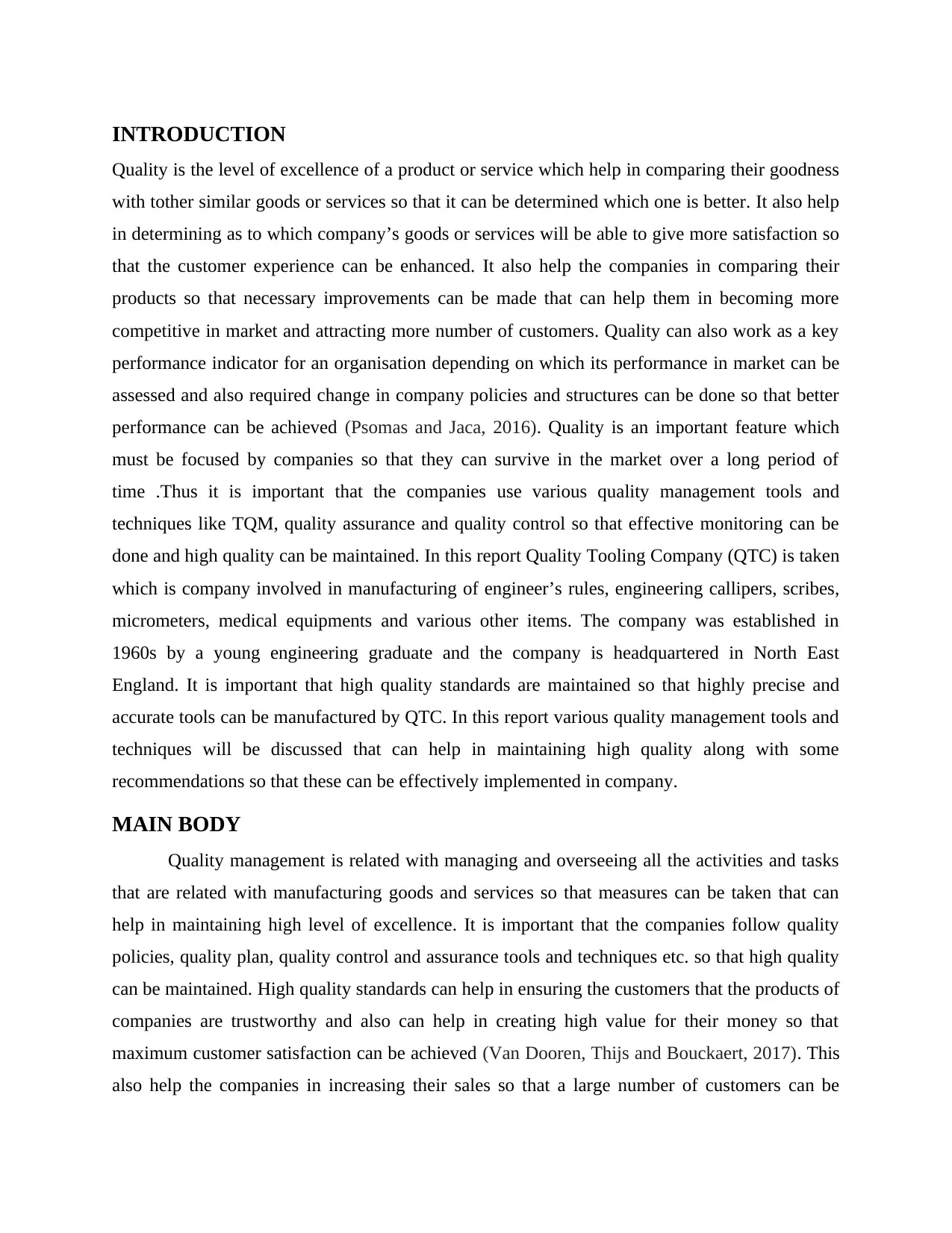
INTRODUCTION
Quality is the level of excellence of a product or service which help in comparing their goodness
with tother similar goods or services so that it can be determined which one is better. It also help
in determining as to which company’s goods or services will be able to give more satisfaction so
that the customer experience can be enhanced. It also help the companies in comparing their
products so that necessary improvements can be made that can help them in becoming more
competitive in market and attracting more number of customers. Quality can also work as a key
performance indicator for an organisation depending on which its performance in market can be
assessed and also required change in company policies and structures can be done so that better
performance can be achieved (Psomas and Jaca, 2016). Quality is an important feature which
must be focused by companies so that they can survive in the market over a long period of
time .Thus it is important that the companies use various quality management tools and
techniques like TQM, quality assurance and quality control so that effective monitoring can be
done and high quality can be maintained. In this report Quality Tooling Company (QTC) is taken
which is company involved in manufacturing of engineer’s rules, engineering callipers, scribes,
micrometers, medical equipments and various other items. The company was established in
1960s by a young engineering graduate and the company is headquartered in North East
England. It is important that high quality standards are maintained so that highly precise and
accurate tools can be manufactured by QTC. In this report various quality management tools and
techniques will be discussed that can help in maintaining high quality along with some
recommendations so that these can be effectively implemented in company.
MAIN BODY
Quality management is related with managing and overseeing all the activities and tasks
that are related with manufacturing goods and services so that measures can be taken that can
help in maintaining high level of excellence. It is important that the companies follow quality
policies, quality plan, quality control and assurance tools and techniques etc. so that high quality
can be maintained. High quality standards can help in ensuring the customers that the products of
companies are trustworthy and also can help in creating high value for their money so that
maximum customer satisfaction can be achieved (Van Dooren, Thijs and Bouckaert, 2017). This
also help the companies in increasing their sales so that a large number of customers can be
Quality is the level of excellence of a product or service which help in comparing their goodness
with tother similar goods or services so that it can be determined which one is better. It also help
in determining as to which company’s goods or services will be able to give more satisfaction so
that the customer experience can be enhanced. It also help the companies in comparing their
products so that necessary improvements can be made that can help them in becoming more
competitive in market and attracting more number of customers. Quality can also work as a key
performance indicator for an organisation depending on which its performance in market can be
assessed and also required change in company policies and structures can be done so that better
performance can be achieved (Psomas and Jaca, 2016). Quality is an important feature which
must be focused by companies so that they can survive in the market over a long period of
time .Thus it is important that the companies use various quality management tools and
techniques like TQM, quality assurance and quality control so that effective monitoring can be
done and high quality can be maintained. In this report Quality Tooling Company (QTC) is taken
which is company involved in manufacturing of engineer’s rules, engineering callipers, scribes,
micrometers, medical equipments and various other items. The company was established in
1960s by a young engineering graduate and the company is headquartered in North East
England. It is important that high quality standards are maintained so that highly precise and
accurate tools can be manufactured by QTC. In this report various quality management tools and
techniques will be discussed that can help in maintaining high quality along with some
recommendations so that these can be effectively implemented in company.
MAIN BODY
Quality management is related with managing and overseeing all the activities and tasks
that are related with manufacturing goods and services so that measures can be taken that can
help in maintaining high level of excellence. It is important that the companies follow quality
policies, quality plan, quality control and assurance tools and techniques etc. so that high quality
can be maintained. High quality standards can help in ensuring the customers that the products of
companies are trustworthy and also can help in creating high value for their money so that
maximum customer satisfaction can be achieved (Van Dooren, Thijs and Bouckaert, 2017). This
also help the companies in increasing their sales so that a large number of customers can be
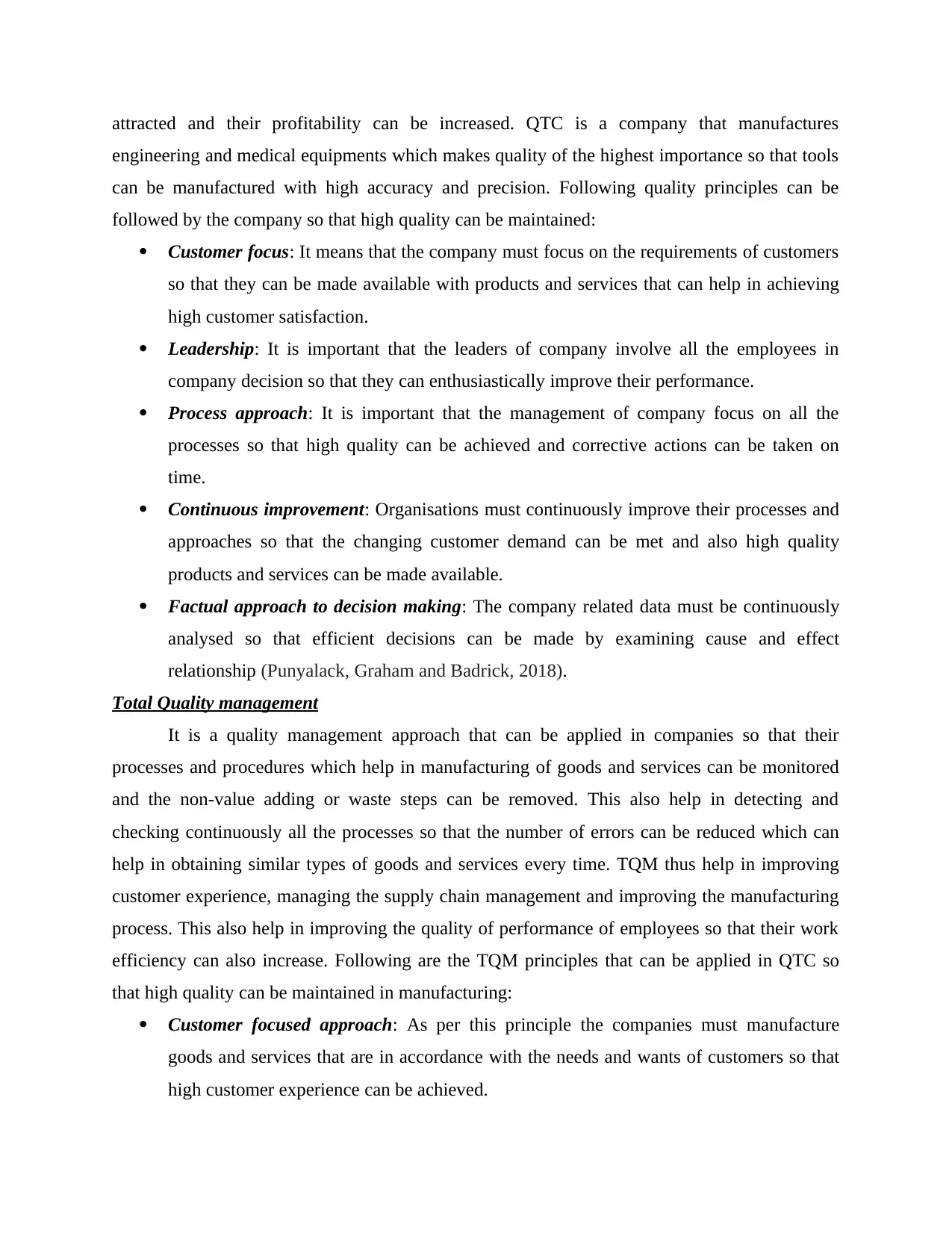
attracted and their profitability can be increased. QTC is a company that manufactures
engineering and medical equipments which makes quality of the highest importance so that tools
can be manufactured with high accuracy and precision. Following quality principles can be
followed by the company so that high quality can be maintained:
Customer focus: It means that the company must focus on the requirements of customers
so that they can be made available with products and services that can help in achieving
high customer satisfaction.
Leadership: It is important that the leaders of company involve all the employees in
company decision so that they can enthusiastically improve their performance.
Process approach: It is important that the management of company focus on all the
processes so that high quality can be achieved and corrective actions can be taken on
time.
Continuous improvement: Organisations must continuously improve their processes and
approaches so that the changing customer demand can be met and also high quality
products and services can be made available.
Factual approach to decision making: The company related data must be continuously
analysed so that efficient decisions can be made by examining cause and effect
relationship (Punyalack, Graham and Badrick, 2018).
Total Quality management
It is a quality management approach that can be applied in companies so that their
processes and procedures which help in manufacturing of goods and services can be monitored
and the non-value adding or waste steps can be removed. This also help in detecting and
checking continuously all the processes so that the number of errors can be reduced which can
help in obtaining similar types of goods and services every time. TQM thus help in improving
customer experience, managing the supply chain management and improving the manufacturing
process. This also help in improving the quality of performance of employees so that their work
efficiency can also increase. Following are the TQM principles that can be applied in QTC so
that high quality can be maintained in manufacturing:
Customer focused approach: As per this principle the companies must manufacture
goods and services that are in accordance with the needs and wants of customers so that
high customer experience can be achieved.
engineering and medical equipments which makes quality of the highest importance so that tools
can be manufactured with high accuracy and precision. Following quality principles can be
followed by the company so that high quality can be maintained:
Customer focus: It means that the company must focus on the requirements of customers
so that they can be made available with products and services that can help in achieving
high customer satisfaction.
Leadership: It is important that the leaders of company involve all the employees in
company decision so that they can enthusiastically improve their performance.
Process approach: It is important that the management of company focus on all the
processes so that high quality can be achieved and corrective actions can be taken on
time.
Continuous improvement: Organisations must continuously improve their processes and
approaches so that the changing customer demand can be met and also high quality
products and services can be made available.
Factual approach to decision making: The company related data must be continuously
analysed so that efficient decisions can be made by examining cause and effect
relationship (Punyalack, Graham and Badrick, 2018).
Total Quality management
It is a quality management approach that can be applied in companies so that their
processes and procedures which help in manufacturing of goods and services can be monitored
and the non-value adding or waste steps can be removed. This also help in detecting and
checking continuously all the processes so that the number of errors can be reduced which can
help in obtaining similar types of goods and services every time. TQM thus help in improving
customer experience, managing the supply chain management and improving the manufacturing
process. This also help in improving the quality of performance of employees so that their work
efficiency can also increase. Following are the TQM principles that can be applied in QTC so
that high quality can be maintained in manufacturing:
Customer focused approach: As per this principle the companies must manufacture
goods and services that are in accordance with the needs and wants of customers so that
high customer experience can be achieved.
Secure Best Marks with AI Grader
Need help grading? Try our AI Grader for instant feedback on your assignments.
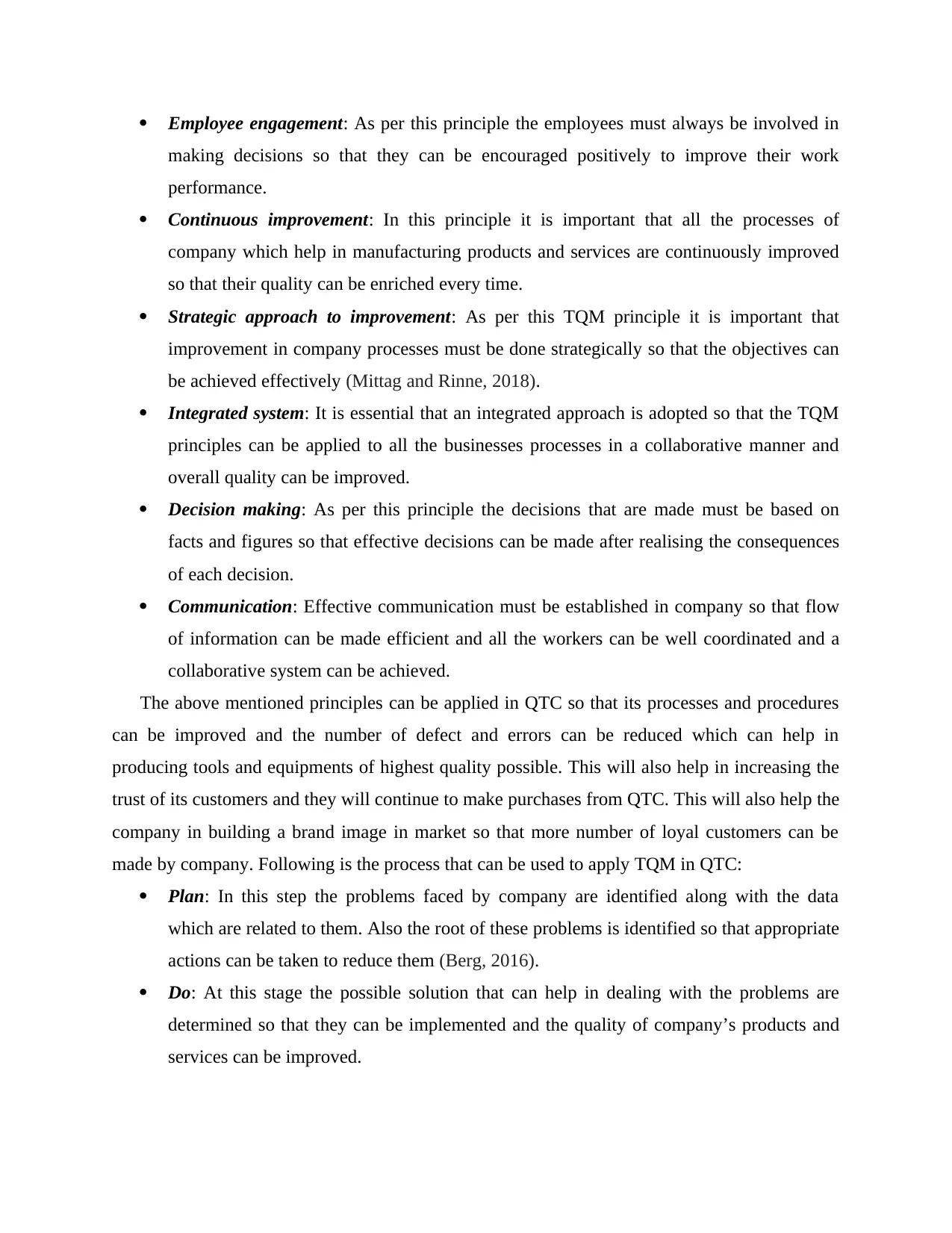
Employee engagement: As per this principle the employees must always be involved in
making decisions so that they can be encouraged positively to improve their work
performance.
Continuous improvement: In this principle it is important that all the processes of
company which help in manufacturing products and services are continuously improved
so that their quality can be enriched every time.
Strategic approach to improvement: As per this TQM principle it is important that
improvement in company processes must be done strategically so that the objectives can
be achieved effectively (Mittag and Rinne, 2018).
Integrated system: It is essential that an integrated approach is adopted so that the TQM
principles can be applied to all the businesses processes in a collaborative manner and
overall quality can be improved.
Decision making: As per this principle the decisions that are made must be based on
facts and figures so that effective decisions can be made after realising the consequences
of each decision.
Communication: Effective communication must be established in company so that flow
of information can be made efficient and all the workers can be well coordinated and a
collaborative system can be achieved.
The above mentioned principles can be applied in QTC so that its processes and procedures
can be improved and the number of defect and errors can be reduced which can help in
producing tools and equipments of highest quality possible. This will also help in increasing the
trust of its customers and they will continue to make purchases from QTC. This will also help the
company in building a brand image in market so that more number of loyal customers can be
made by company. Following is the process that can be used to apply TQM in QTC:
Plan: In this step the problems faced by company are identified along with the data
which are related to them. Also the root of these problems is identified so that appropriate
actions can be taken to reduce them (Berg, 2016).
Do: At this stage the possible solution that can help in dealing with the problems are
determined so that they can be implemented and the quality of company’s products and
services can be improved.
making decisions so that they can be encouraged positively to improve their work
performance.
Continuous improvement: In this principle it is important that all the processes of
company which help in manufacturing products and services are continuously improved
so that their quality can be enriched every time.
Strategic approach to improvement: As per this TQM principle it is important that
improvement in company processes must be done strategically so that the objectives can
be achieved effectively (Mittag and Rinne, 2018).
Integrated system: It is essential that an integrated approach is adopted so that the TQM
principles can be applied to all the businesses processes in a collaborative manner and
overall quality can be improved.
Decision making: As per this principle the decisions that are made must be based on
facts and figures so that effective decisions can be made after realising the consequences
of each decision.
Communication: Effective communication must be established in company so that flow
of information can be made efficient and all the workers can be well coordinated and a
collaborative system can be achieved.
The above mentioned principles can be applied in QTC so that its processes and procedures
can be improved and the number of defect and errors can be reduced which can help in
producing tools and equipments of highest quality possible. This will also help in increasing the
trust of its customers and they will continue to make purchases from QTC. This will also help the
company in building a brand image in market so that more number of loyal customers can be
made by company. Following is the process that can be used to apply TQM in QTC:
Plan: In this step the problems faced by company are identified along with the data
which are related to them. Also the root of these problems is identified so that appropriate
actions can be taken to reduce them (Berg, 2016).
Do: At this stage the possible solution that can help in dealing with the problems are
determined so that they can be implemented and the quality of company’s products and
services can be improved.
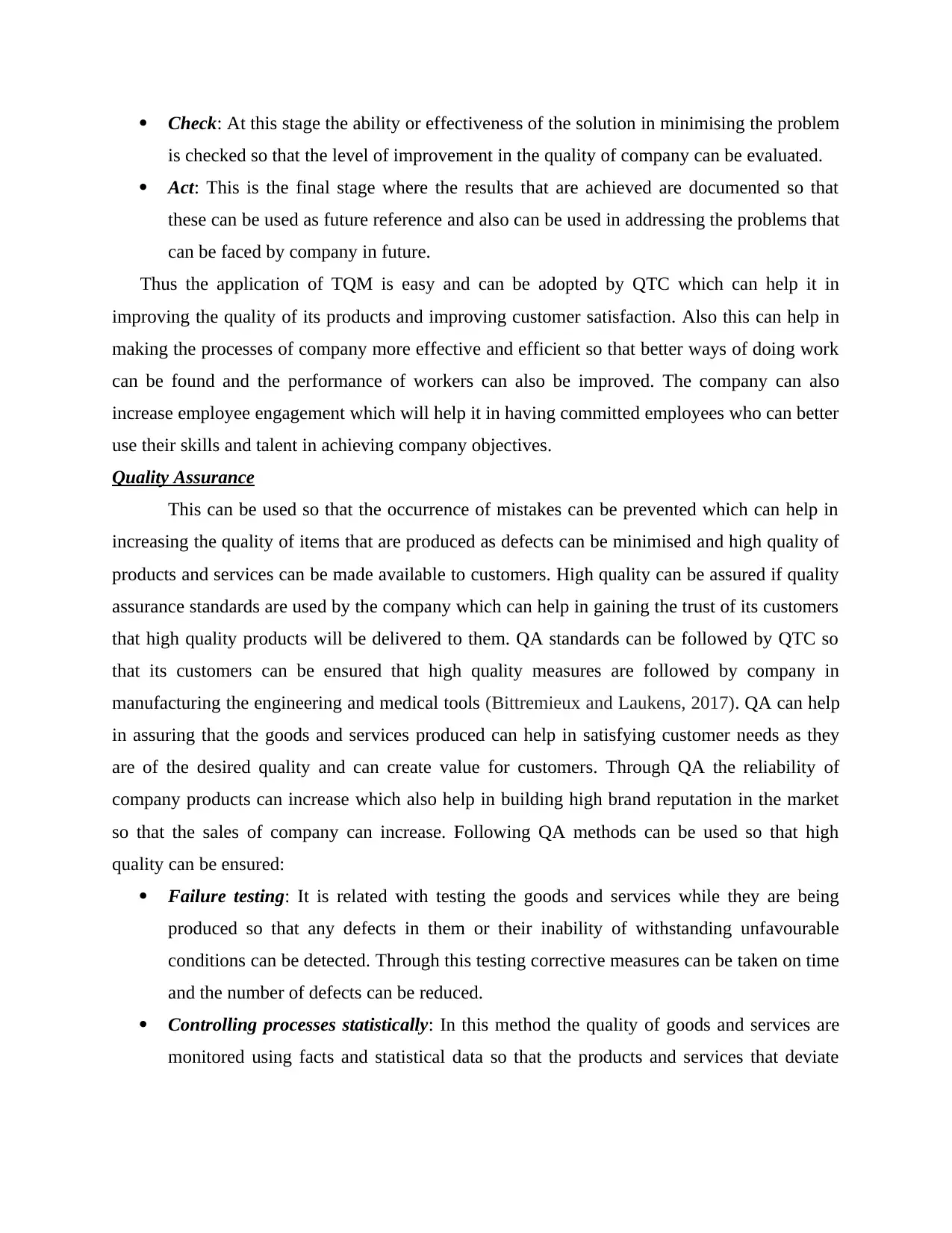
Check: At this stage the ability or effectiveness of the solution in minimising the problem
is checked so that the level of improvement in the quality of company can be evaluated.
Act: This is the final stage where the results that are achieved are documented so that
these can be used as future reference and also can be used in addressing the problems that
can be faced by company in future.
Thus the application of TQM is easy and can be adopted by QTC which can help it in
improving the quality of its products and improving customer satisfaction. Also this can help in
making the processes of company more effective and efficient so that better ways of doing work
can be found and the performance of workers can also be improved. The company can also
increase employee engagement which will help it in having committed employees who can better
use their skills and talent in achieving company objectives.
Quality Assurance
This can be used so that the occurrence of mistakes can be prevented which can help in
increasing the quality of items that are produced as defects can be minimised and high quality of
products and services can be made available to customers. High quality can be assured if quality
assurance standards are used by the company which can help in gaining the trust of its customers
that high quality products will be delivered to them. QA standards can be followed by QTC so
that its customers can be ensured that high quality measures are followed by company in
manufacturing the engineering and medical tools (Bittremieux and Laukens, 2017). QA can help
in assuring that the goods and services produced can help in satisfying customer needs as they
are of the desired quality and can create value for customers. Through QA the reliability of
company products can increase which also help in building high brand reputation in the market
so that the sales of company can increase. Following QA methods can be used so that high
quality can be ensured:
Failure testing: It is related with testing the goods and services while they are being
produced so that any defects in them or their inability of withstanding unfavourable
conditions can be detected. Through this testing corrective measures can be taken on time
and the number of defects can be reduced.
Controlling processes statistically: In this method the quality of goods and services are
monitored using facts and statistical data so that the products and services that deviate
is checked so that the level of improvement in the quality of company can be evaluated.
Act: This is the final stage where the results that are achieved are documented so that
these can be used as future reference and also can be used in addressing the problems that
can be faced by company in future.
Thus the application of TQM is easy and can be adopted by QTC which can help it in
improving the quality of its products and improving customer satisfaction. Also this can help in
making the processes of company more effective and efficient so that better ways of doing work
can be found and the performance of workers can also be improved. The company can also
increase employee engagement which will help it in having committed employees who can better
use their skills and talent in achieving company objectives.
Quality Assurance
This can be used so that the occurrence of mistakes can be prevented which can help in
increasing the quality of items that are produced as defects can be minimised and high quality of
products and services can be made available to customers. High quality can be assured if quality
assurance standards are used by the company which can help in gaining the trust of its customers
that high quality products will be delivered to them. QA standards can be followed by QTC so
that its customers can be ensured that high quality measures are followed by company in
manufacturing the engineering and medical tools (Bittremieux and Laukens, 2017). QA can help
in assuring that the goods and services produced can help in satisfying customer needs as they
are of the desired quality and can create value for customers. Through QA the reliability of
company products can increase which also help in building high brand reputation in the market
so that the sales of company can increase. Following QA methods can be used so that high
quality can be ensured:
Failure testing: It is related with testing the goods and services while they are being
produced so that any defects in them or their inability of withstanding unfavourable
conditions can be detected. Through this testing corrective measures can be taken on time
and the number of defects can be reduced.
Controlling processes statistically: In this method the quality of goods and services are
monitored using facts and statistical data so that the products and services that deviate
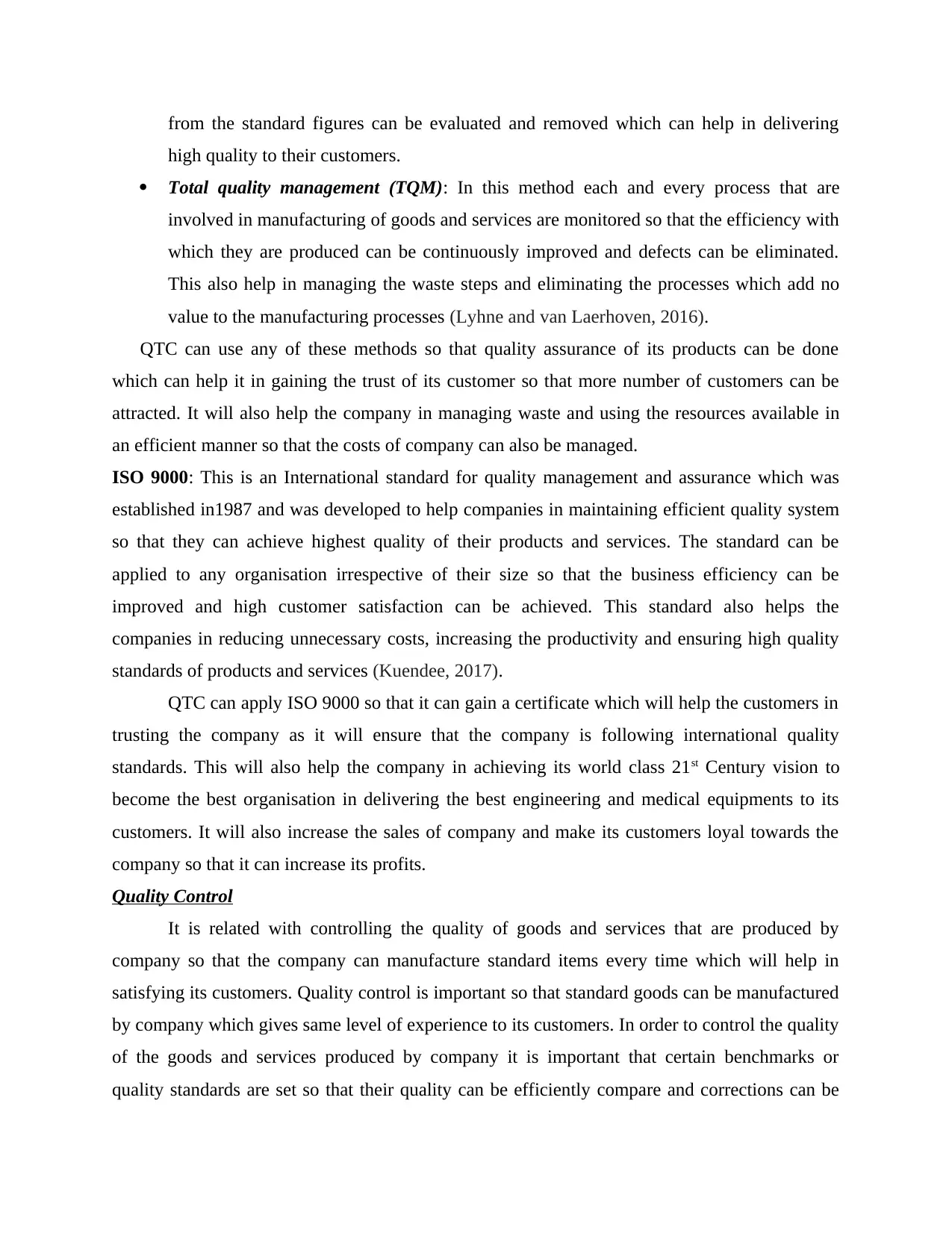
from the standard figures can be evaluated and removed which can help in delivering
high quality to their customers.
Total quality management (TQM): In this method each and every process that are
involved in manufacturing of goods and services are monitored so that the efficiency with
which they are produced can be continuously improved and defects can be eliminated.
This also help in managing the waste steps and eliminating the processes which add no
value to the manufacturing processes (Lyhne and van Laerhoven, 2016).
QTC can use any of these methods so that quality assurance of its products can be done
which can help it in gaining the trust of its customer so that more number of customers can be
attracted. It will also help the company in managing waste and using the resources available in
an efficient manner so that the costs of company can also be managed.
ISO 9000: This is an International standard for quality management and assurance which was
established in1987 and was developed to help companies in maintaining efficient quality system
so that they can achieve highest quality of their products and services. The standard can be
applied to any organisation irrespective of their size so that the business efficiency can be
improved and high customer satisfaction can be achieved. This standard also helps the
companies in reducing unnecessary costs, increasing the productivity and ensuring high quality
standards of products and services (Kuendee, 2017).
QTC can apply ISO 9000 so that it can gain a certificate which will help the customers in
trusting the company as it will ensure that the company is following international quality
standards. This will also help the company in achieving its world class 21st Century vision to
become the best organisation in delivering the best engineering and medical equipments to its
customers. It will also increase the sales of company and make its customers loyal towards the
company so that it can increase its profits.
Quality Control
It is related with controlling the quality of goods and services that are produced by
company so that the company can manufacture standard items every time which will help in
satisfying its customers. Quality control is important so that standard goods can be manufactured
by company which gives same level of experience to its customers. In order to control the quality
of the goods and services produced by company it is important that certain benchmarks or
quality standards are set so that their quality can be efficiently compare and corrections can be
high quality to their customers.
Total quality management (TQM): In this method each and every process that are
involved in manufacturing of goods and services are monitored so that the efficiency with
which they are produced can be continuously improved and defects can be eliminated.
This also help in managing the waste steps and eliminating the processes which add no
value to the manufacturing processes (Lyhne and van Laerhoven, 2016).
QTC can use any of these methods so that quality assurance of its products can be done
which can help it in gaining the trust of its customer so that more number of customers can be
attracted. It will also help the company in managing waste and using the resources available in
an efficient manner so that the costs of company can also be managed.
ISO 9000: This is an International standard for quality management and assurance which was
established in1987 and was developed to help companies in maintaining efficient quality system
so that they can achieve highest quality of their products and services. The standard can be
applied to any organisation irrespective of their size so that the business efficiency can be
improved and high customer satisfaction can be achieved. This standard also helps the
companies in reducing unnecessary costs, increasing the productivity and ensuring high quality
standards of products and services (Kuendee, 2017).
QTC can apply ISO 9000 so that it can gain a certificate which will help the customers in
trusting the company as it will ensure that the company is following international quality
standards. This will also help the company in achieving its world class 21st Century vision to
become the best organisation in delivering the best engineering and medical equipments to its
customers. It will also increase the sales of company and make its customers loyal towards the
company so that it can increase its profits.
Quality Control
It is related with controlling the quality of goods and services that are produced by
company so that the company can manufacture standard items every time which will help in
satisfying its customers. Quality control is important so that standard goods can be manufactured
by company which gives same level of experience to its customers. In order to control the quality
of the goods and services produced by company it is important that certain benchmarks or
quality standards are set so that their quality can be efficiently compare and corrections can be
Paraphrase This Document
Need a fresh take? Get an instant paraphrase of this document with our AI Paraphraser
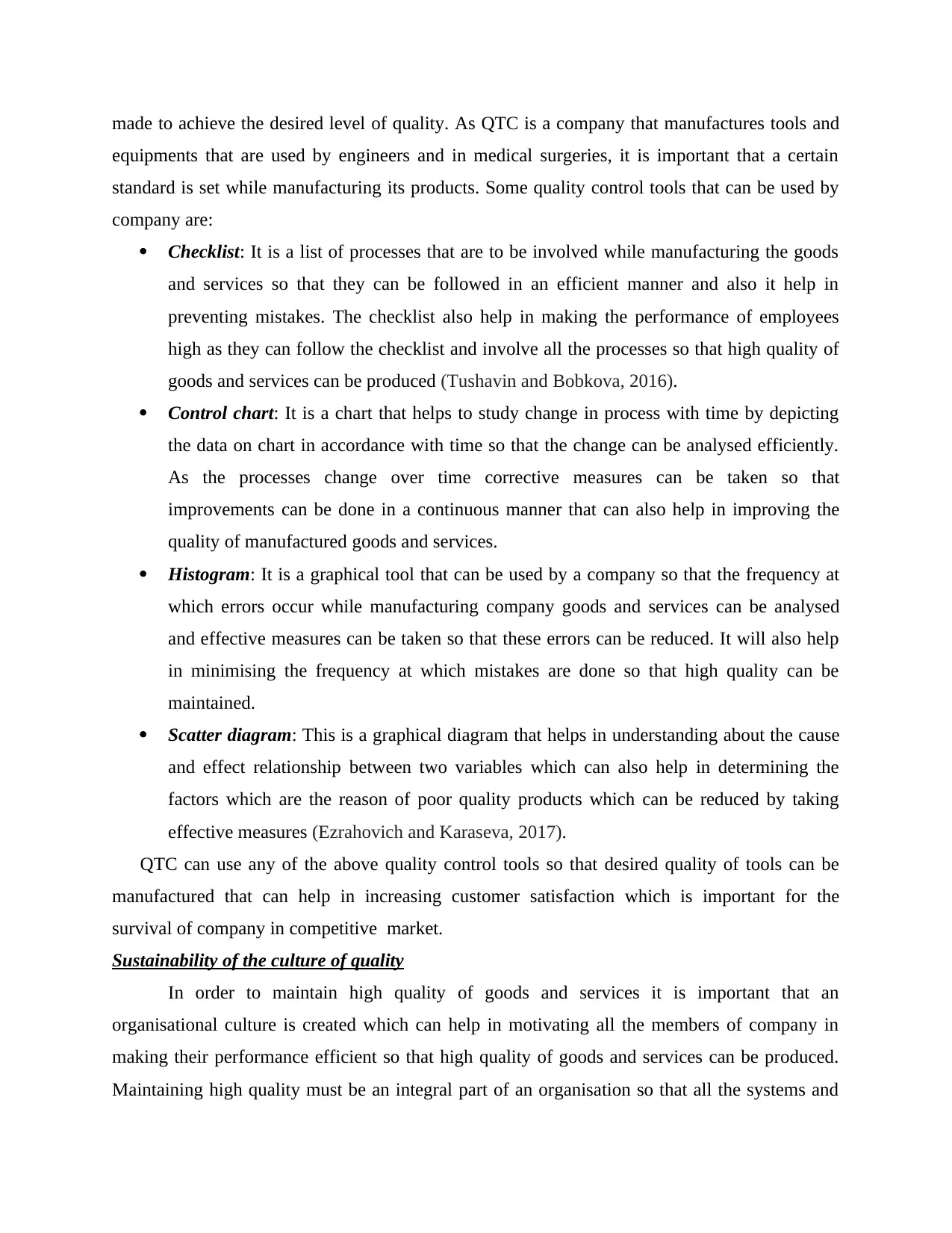
made to achieve the desired level of quality. As QTC is a company that manufactures tools and
equipments that are used by engineers and in medical surgeries, it is important that a certain
standard is set while manufacturing its products. Some quality control tools that can be used by
company are:
Checklist: It is a list of processes that are to be involved while manufacturing the goods
and services so that they can be followed in an efficient manner and also it help in
preventing mistakes. The checklist also help in making the performance of employees
high as they can follow the checklist and involve all the processes so that high quality of
goods and services can be produced (Tushavin and Bobkova, 2016).
Control chart: It is a chart that helps to study change in process with time by depicting
the data on chart in accordance with time so that the change can be analysed efficiently.
As the processes change over time corrective measures can be taken so that
improvements can be done in a continuous manner that can also help in improving the
quality of manufactured goods and services.
Histogram: It is a graphical tool that can be used by a company so that the frequency at
which errors occur while manufacturing company goods and services can be analysed
and effective measures can be taken so that these errors can be reduced. It will also help
in minimising the frequency at which mistakes are done so that high quality can be
maintained.
Scatter diagram: This is a graphical diagram that helps in understanding about the cause
and effect relationship between two variables which can also help in determining the
factors which are the reason of poor quality products which can be reduced by taking
effective measures (Ezrahovich and Karaseva, 2017).
QTC can use any of the above quality control tools so that desired quality of tools can be
manufactured that can help in increasing customer satisfaction which is important for the
survival of company in competitive market.
Sustainability of the culture of quality
In order to maintain high quality of goods and services it is important that an
organisational culture is created which can help in motivating all the members of company in
making their performance efficient so that high quality of goods and services can be produced.
Maintaining high quality must be an integral part of an organisation so that all the systems and
equipments that are used by engineers and in medical surgeries, it is important that a certain
standard is set while manufacturing its products. Some quality control tools that can be used by
company are:
Checklist: It is a list of processes that are to be involved while manufacturing the goods
and services so that they can be followed in an efficient manner and also it help in
preventing mistakes. The checklist also help in making the performance of employees
high as they can follow the checklist and involve all the processes so that high quality of
goods and services can be produced (Tushavin and Bobkova, 2016).
Control chart: It is a chart that helps to study change in process with time by depicting
the data on chart in accordance with time so that the change can be analysed efficiently.
As the processes change over time corrective measures can be taken so that
improvements can be done in a continuous manner that can also help in improving the
quality of manufactured goods and services.
Histogram: It is a graphical tool that can be used by a company so that the frequency at
which errors occur while manufacturing company goods and services can be analysed
and effective measures can be taken so that these errors can be reduced. It will also help
in minimising the frequency at which mistakes are done so that high quality can be
maintained.
Scatter diagram: This is a graphical diagram that helps in understanding about the cause
and effect relationship between two variables which can also help in determining the
factors which are the reason of poor quality products which can be reduced by taking
effective measures (Ezrahovich and Karaseva, 2017).
QTC can use any of the above quality control tools so that desired quality of tools can be
manufactured that can help in increasing customer satisfaction which is important for the
survival of company in competitive market.
Sustainability of the culture of quality
In order to maintain high quality of goods and services it is important that an
organisational culture is created which can help in motivating all the members of company in
making their performance efficient so that high quality of goods and services can be produced.
Maintaining high quality must be an integral part of an organisation so that all the systems and
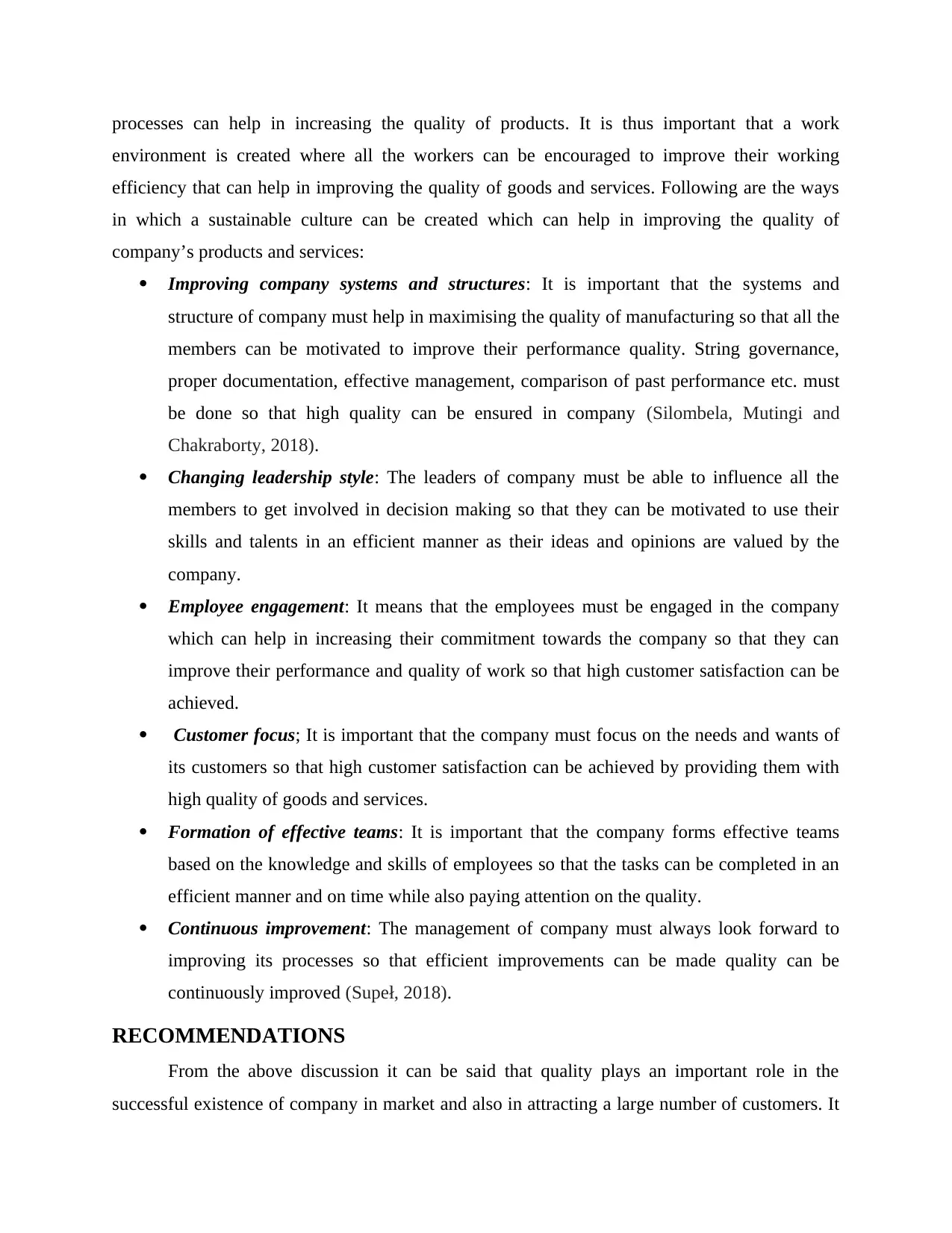
processes can help in increasing the quality of products. It is thus important that a work
environment is created where all the workers can be encouraged to improve their working
efficiency that can help in improving the quality of goods and services. Following are the ways
in which a sustainable culture can be created which can help in improving the quality of
company’s products and services:
Improving company systems and structures: It is important that the systems and
structure of company must help in maximising the quality of manufacturing so that all the
members can be motivated to improve their performance quality. String governance,
proper documentation, effective management, comparison of past performance etc. must
be done so that high quality can be ensured in company (Silombela, Mutingi and
Chakraborty, 2018).
Changing leadership style: The leaders of company must be able to influence all the
members to get involved in decision making so that they can be motivated to use their
skills and talents in an efficient manner as their ideas and opinions are valued by the
company.
Employee engagement: It means that the employees must be engaged in the company
which can help in increasing their commitment towards the company so that they can
improve their performance and quality of work so that high customer satisfaction can be
achieved.
Customer focus; It is important that the company must focus on the needs and wants of
its customers so that high customer satisfaction can be achieved by providing them with
high quality of goods and services.
Formation of effective teams: It is important that the company forms effective teams
based on the knowledge and skills of employees so that the tasks can be completed in an
efficient manner and on time while also paying attention on the quality.
Continuous improvement: The management of company must always look forward to
improving its processes so that efficient improvements can be made quality can be
continuously improved (Supeł, 2018).
RECOMMENDATIONS
From the above discussion it can be said that quality plays an important role in the
successful existence of company in market and also in attracting a large number of customers. It
environment is created where all the workers can be encouraged to improve their working
efficiency that can help in improving the quality of goods and services. Following are the ways
in which a sustainable culture can be created which can help in improving the quality of
company’s products and services:
Improving company systems and structures: It is important that the systems and
structure of company must help in maximising the quality of manufacturing so that all the
members can be motivated to improve their performance quality. String governance,
proper documentation, effective management, comparison of past performance etc. must
be done so that high quality can be ensured in company (Silombela, Mutingi and
Chakraborty, 2018).
Changing leadership style: The leaders of company must be able to influence all the
members to get involved in decision making so that they can be motivated to use their
skills and talents in an efficient manner as their ideas and opinions are valued by the
company.
Employee engagement: It means that the employees must be engaged in the company
which can help in increasing their commitment towards the company so that they can
improve their performance and quality of work so that high customer satisfaction can be
achieved.
Customer focus; It is important that the company must focus on the needs and wants of
its customers so that high customer satisfaction can be achieved by providing them with
high quality of goods and services.
Formation of effective teams: It is important that the company forms effective teams
based on the knowledge and skills of employees so that the tasks can be completed in an
efficient manner and on time while also paying attention on the quality.
Continuous improvement: The management of company must always look forward to
improving its processes so that efficient improvements can be made quality can be
continuously improved (Supeł, 2018).
RECOMMENDATIONS
From the above discussion it can be said that quality plays an important role in the
successful existence of company in market and also in attracting a large number of customers. It
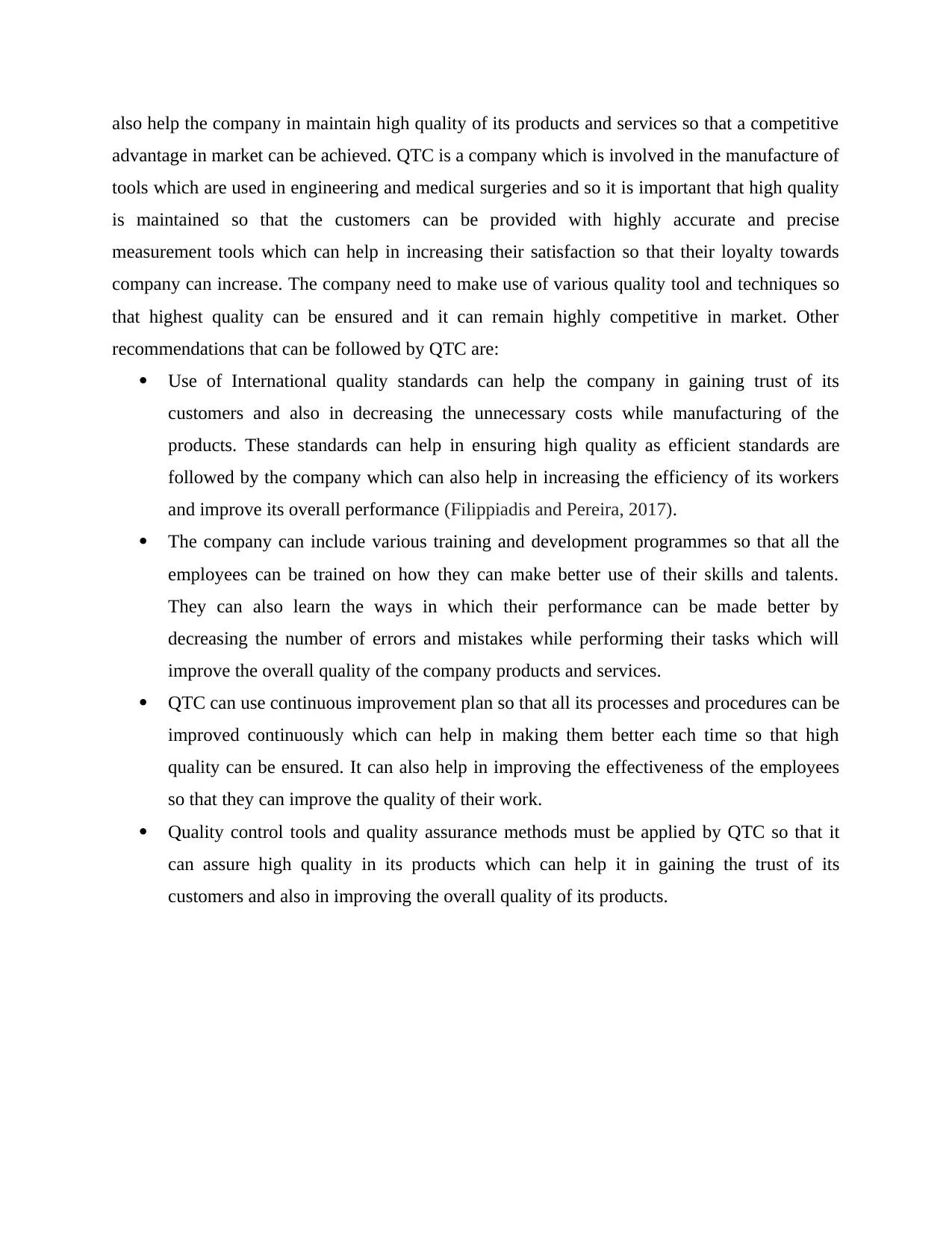
also help the company in maintain high quality of its products and services so that a competitive
advantage in market can be achieved. QTC is a company which is involved in the manufacture of
tools which are used in engineering and medical surgeries and so it is important that high quality
is maintained so that the customers can be provided with highly accurate and precise
measurement tools which can help in increasing their satisfaction so that their loyalty towards
company can increase. The company need to make use of various quality tool and techniques so
that highest quality can be ensured and it can remain highly competitive in market. Other
recommendations that can be followed by QTC are:
Use of International quality standards can help the company in gaining trust of its
customers and also in decreasing the unnecessary costs while manufacturing of the
products. These standards can help in ensuring high quality as efficient standards are
followed by the company which can also help in increasing the efficiency of its workers
and improve its overall performance (Filippiadis and Pereira, 2017).
The company can include various training and development programmes so that all the
employees can be trained on how they can make better use of their skills and talents.
They can also learn the ways in which their performance can be made better by
decreasing the number of errors and mistakes while performing their tasks which will
improve the overall quality of the company products and services.
QTC can use continuous improvement plan so that all its processes and procedures can be
improved continuously which can help in making them better each time so that high
quality can be ensured. It can also help in improving the effectiveness of the employees
so that they can improve the quality of their work.
Quality control tools and quality assurance methods must be applied by QTC so that it
can assure high quality in its products which can help it in gaining the trust of its
customers and also in improving the overall quality of its products.
advantage in market can be achieved. QTC is a company which is involved in the manufacture of
tools which are used in engineering and medical surgeries and so it is important that high quality
is maintained so that the customers can be provided with highly accurate and precise
measurement tools which can help in increasing their satisfaction so that their loyalty towards
company can increase. The company need to make use of various quality tool and techniques so
that highest quality can be ensured and it can remain highly competitive in market. Other
recommendations that can be followed by QTC are:
Use of International quality standards can help the company in gaining trust of its
customers and also in decreasing the unnecessary costs while manufacturing of the
products. These standards can help in ensuring high quality as efficient standards are
followed by the company which can also help in increasing the efficiency of its workers
and improve its overall performance (Filippiadis and Pereira, 2017).
The company can include various training and development programmes so that all the
employees can be trained on how they can make better use of their skills and talents.
They can also learn the ways in which their performance can be made better by
decreasing the number of errors and mistakes while performing their tasks which will
improve the overall quality of the company products and services.
QTC can use continuous improvement plan so that all its processes and procedures can be
improved continuously which can help in making them better each time so that high
quality can be ensured. It can also help in improving the effectiveness of the employees
so that they can improve the quality of their work.
Quality control tools and quality assurance methods must be applied by QTC so that it
can assure high quality in its products which can help it in gaining the trust of its
customers and also in improving the overall quality of its products.
Secure Best Marks with AI Grader
Need help grading? Try our AI Grader for instant feedback on your assignments.
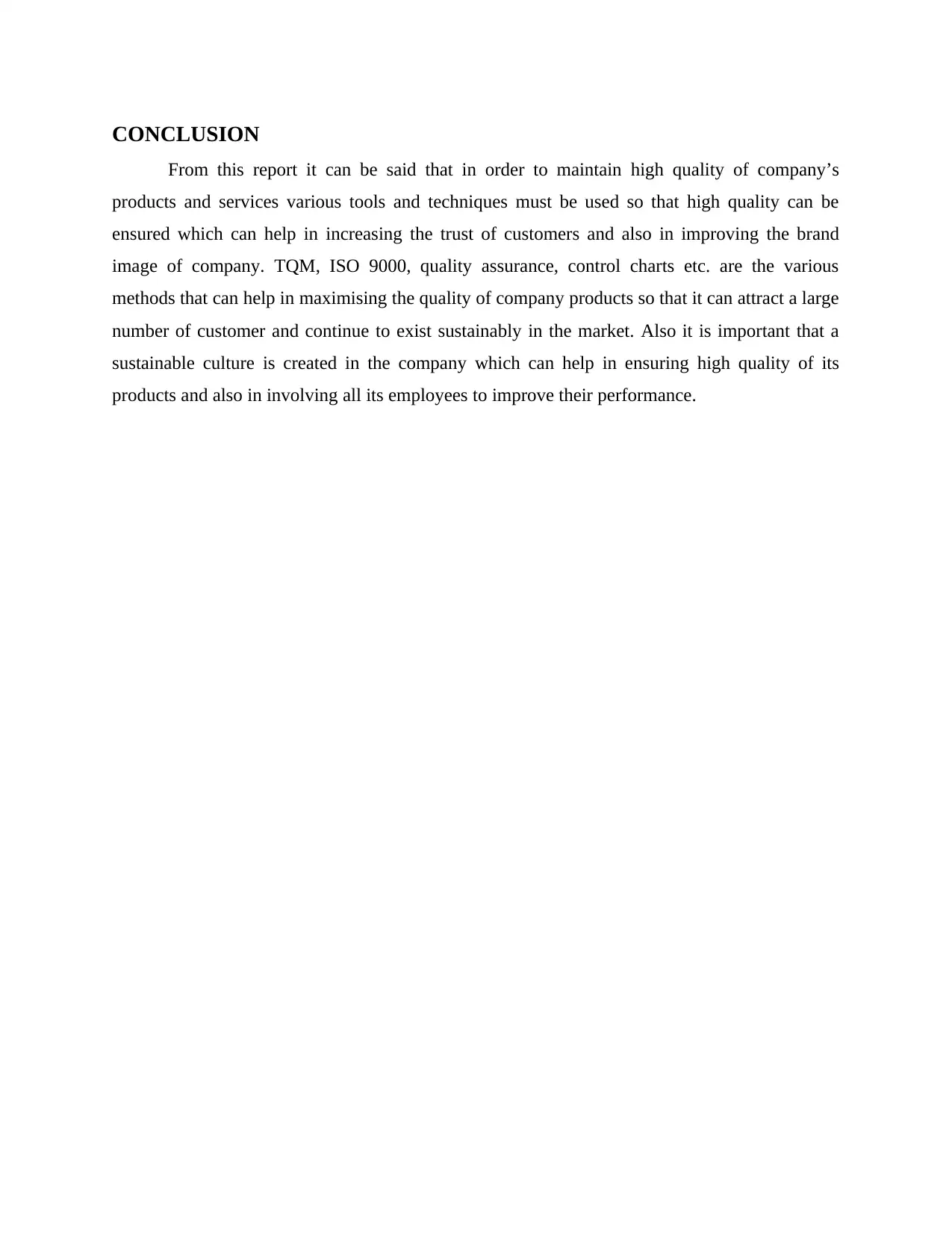
CONCLUSION
From this report it can be said that in order to maintain high quality of company’s
products and services various tools and techniques must be used so that high quality can be
ensured which can help in increasing the trust of customers and also in improving the brand
image of company. TQM, ISO 9000, quality assurance, control charts etc. are the various
methods that can help in maximising the quality of company products so that it can attract a large
number of customer and continue to exist sustainably in the market. Also it is important that a
sustainable culture is created in the company which can help in ensuring high quality of its
products and also in involving all its employees to improve their performance.
From this report it can be said that in order to maintain high quality of company’s
products and services various tools and techniques must be used so that high quality can be
ensured which can help in increasing the trust of customers and also in improving the brand
image of company. TQM, ISO 9000, quality assurance, control charts etc. are the various
methods that can help in maximising the quality of company products so that it can attract a large
number of customer and continue to exist sustainably in the market. Also it is important that a
sustainable culture is created in the company which can help in ensuring high quality of its
products and also in involving all its employees to improve their performance.
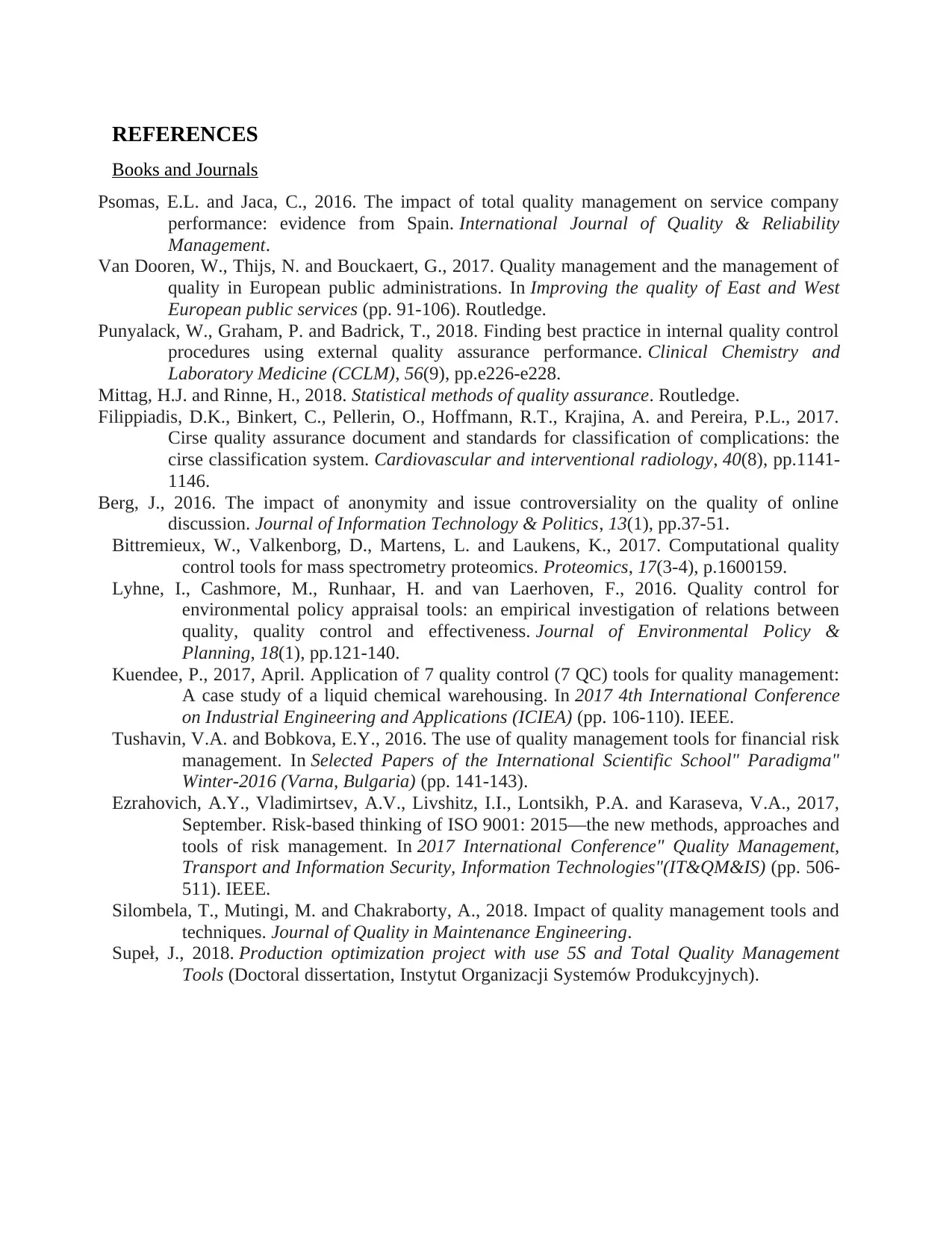
REFERENCES
Books and Journals
Psomas, E.L. and Jaca, C., 2016. The impact of total quality management on service company
performance: evidence from Spain. International Journal of Quality & Reliability
Management.
Van Dooren, W., Thijs, N. and Bouckaert, G., 2017. Quality management and the management of
quality in European public administrations. In Improving the quality of East and West
European public services (pp. 91-106). Routledge.
Punyalack, W., Graham, P. and Badrick, T., 2018. Finding best practice in internal quality control
procedures using external quality assurance performance. Clinical Chemistry and
Laboratory Medicine (CCLM), 56(9), pp.e226-e228.
Mittag, H.J. and Rinne, H., 2018. Statistical methods of quality assurance. Routledge.
Filippiadis, D.K., Binkert, C., Pellerin, O., Hoffmann, R.T., Krajina, A. and Pereira, P.L., 2017.
Cirse quality assurance document and standards for classification of complications: the
cirse classification system. Cardiovascular and interventional radiology, 40(8), pp.1141-
1146.
Berg, J., 2016. The impact of anonymity and issue controversiality on the quality of online
discussion. Journal of Information Technology & Politics, 13(1), pp.37-51.
Bittremieux, W., Valkenborg, D., Martens, L. and Laukens, K., 2017. Computational quality
control tools for mass spectrometry proteomics. Proteomics, 17(3-4), p.1600159.
Lyhne, I., Cashmore, M., Runhaar, H. and van Laerhoven, F., 2016. Quality control for
environmental policy appraisal tools: an empirical investigation of relations between
quality, quality control and effectiveness. Journal of Environmental Policy &
Planning, 18(1), pp.121-140.
Kuendee, P., 2017, April. Application of 7 quality control (7 QC) tools for quality management:
A case study of a liquid chemical warehousing. In 2017 4th International Conference
on Industrial Engineering and Applications (ICIEA) (pp. 106-110). IEEE.
Tushavin, V.A. and Bobkova, E.Y., 2016. The use of quality management tools for financial risk
management. In Selected Papers of the International Scientific School" Paradigma"
Winter-2016 (Varna, Bulgaria) (pp. 141-143).
Ezrahovich, A.Y., Vladimirtsev, A.V., Livshitz, I.I., Lontsikh, P.A. and Karaseva, V.A., 2017,
September. Risk-based thinking of ISO 9001: 2015—the new methods, approaches and
tools of risk management. In 2017 International Conference" Quality Management,
Transport and Information Security, Information Technologies"(IT&QM&IS) (pp. 506-
511). IEEE.
Silombela, T., Mutingi, M. and Chakraborty, A., 2018. Impact of quality management tools and
techniques. Journal of Quality in Maintenance Engineering.
Supeł, J., 2018. Production optimization project with use 5S and Total Quality Management
Tools (Doctoral dissertation, Instytut Organizacji Systemów Produkcyjnych).
Books and Journals
Psomas, E.L. and Jaca, C., 2016. The impact of total quality management on service company
performance: evidence from Spain. International Journal of Quality & Reliability
Management.
Van Dooren, W., Thijs, N. and Bouckaert, G., 2017. Quality management and the management of
quality in European public administrations. In Improving the quality of East and West
European public services (pp. 91-106). Routledge.
Punyalack, W., Graham, P. and Badrick, T., 2018. Finding best practice in internal quality control
procedures using external quality assurance performance. Clinical Chemistry and
Laboratory Medicine (CCLM), 56(9), pp.e226-e228.
Mittag, H.J. and Rinne, H., 2018. Statistical methods of quality assurance. Routledge.
Filippiadis, D.K., Binkert, C., Pellerin, O., Hoffmann, R.T., Krajina, A. and Pereira, P.L., 2017.
Cirse quality assurance document and standards for classification of complications: the
cirse classification system. Cardiovascular and interventional radiology, 40(8), pp.1141-
1146.
Berg, J., 2016. The impact of anonymity and issue controversiality on the quality of online
discussion. Journal of Information Technology & Politics, 13(1), pp.37-51.
Bittremieux, W., Valkenborg, D., Martens, L. and Laukens, K., 2017. Computational quality
control tools for mass spectrometry proteomics. Proteomics, 17(3-4), p.1600159.
Lyhne, I., Cashmore, M., Runhaar, H. and van Laerhoven, F., 2016. Quality control for
environmental policy appraisal tools: an empirical investigation of relations between
quality, quality control and effectiveness. Journal of Environmental Policy &
Planning, 18(1), pp.121-140.
Kuendee, P., 2017, April. Application of 7 quality control (7 QC) tools for quality management:
A case study of a liquid chemical warehousing. In 2017 4th International Conference
on Industrial Engineering and Applications (ICIEA) (pp. 106-110). IEEE.
Tushavin, V.A. and Bobkova, E.Y., 2016. The use of quality management tools for financial risk
management. In Selected Papers of the International Scientific School" Paradigma"
Winter-2016 (Varna, Bulgaria) (pp. 141-143).
Ezrahovich, A.Y., Vladimirtsev, A.V., Livshitz, I.I., Lontsikh, P.A. and Karaseva, V.A., 2017,
September. Risk-based thinking of ISO 9001: 2015—the new methods, approaches and
tools of risk management. In 2017 International Conference" Quality Management,
Transport and Information Security, Information Technologies"(IT&QM&IS) (pp. 506-
511). IEEE.
Silombela, T., Mutingi, M. and Chakraborty, A., 2018. Impact of quality management tools and
techniques. Journal of Quality in Maintenance Engineering.
Supeł, J., 2018. Production optimization project with use 5S and Total Quality Management
Tools (Doctoral dissertation, Instytut Organizacji Systemów Produkcyjnych).
1 out of 12
Related Documents
![[object Object]](/_next/image/?url=%2F_next%2Fstatic%2Fmedia%2Flogo.6d15ce61.png&w=640&q=75)
Your All-in-One AI-Powered Toolkit for Academic Success.
+13062052269
info@desklib.com
Available 24*7 on WhatsApp / Email
Unlock your academic potential
© 2024 | Zucol Services PVT LTD | All rights reserved.