Quality Management And Sustainability Quality
VerifiedAdded on 2022/08/26
|13
|4241
|19
AI Summary
Contribute Materials
Your contribution can guide someone’s learning journey. Share your
documents today.
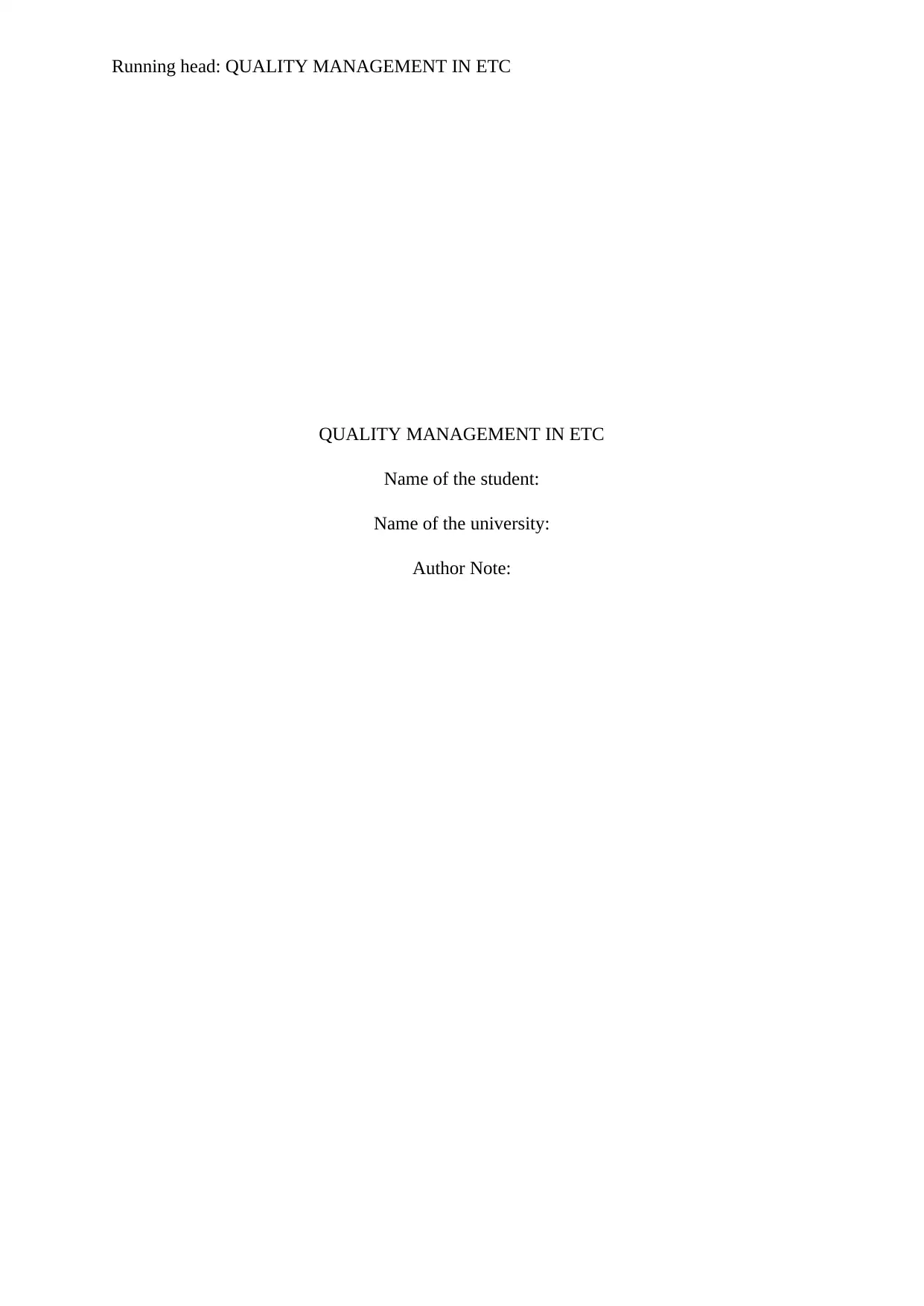
Running head: QUALITY MANAGEMENT IN ETC
QUALITY MANAGEMENT IN ETC
Name of the student:
Name of the university:
Author Note:
QUALITY MANAGEMENT IN ETC
Name of the student:
Name of the university:
Author Note:
Secure Best Marks with AI Grader
Need help grading? Try our AI Grader for instant feedback on your assignments.

1QUALITY MANAGEMENT IN ETC
Table of Contents
Introduction................................................................................................................................2
Discussion..................................................................................................................................2
Total Quality Management....................................................................................................2
Quality Assurance..................................................................................................................4
Quality Control.......................................................................................................................6
Sustainability of the Culture of Quality.................................................................................7
Conclusion and Recommendation..............................................................................................8
References................................................................................................................................10
Table of Contents
Introduction................................................................................................................................2
Discussion..................................................................................................................................2
Total Quality Management....................................................................................................2
Quality Assurance..................................................................................................................4
Quality Control.......................................................................................................................6
Sustainability of the Culture of Quality.................................................................................7
Conclusion and Recommendation..............................................................................................8
References................................................................................................................................10
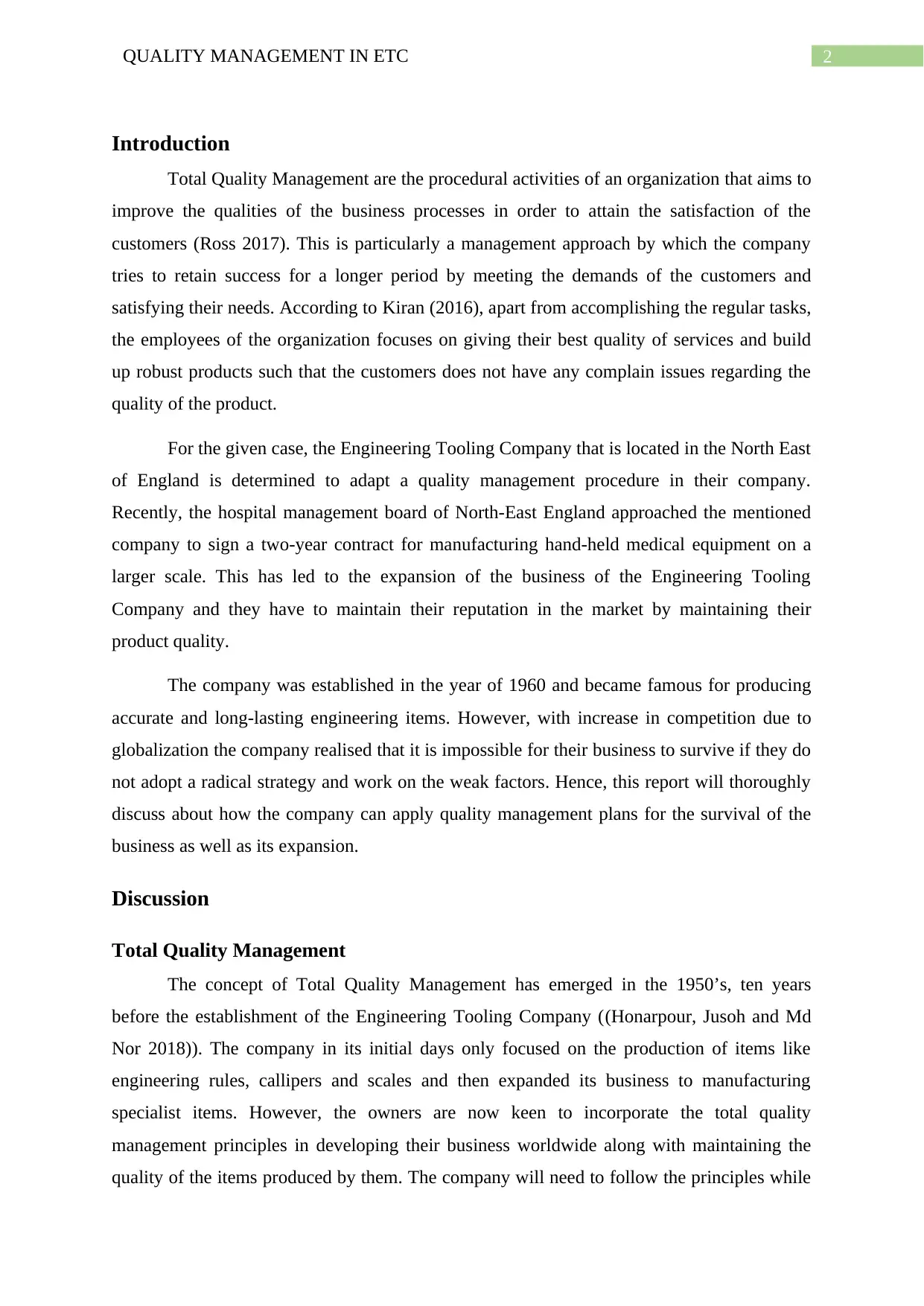
2QUALITY MANAGEMENT IN ETC
Introduction
Total Quality Management are the procedural activities of an organization that aims to
improve the qualities of the business processes in order to attain the satisfaction of the
customers (Ross 2017). This is particularly a management approach by which the company
tries to retain success for a longer period by meeting the demands of the customers and
satisfying their needs. According to Kiran (2016), apart from accomplishing the regular tasks,
the employees of the organization focuses on giving their best quality of services and build
up robust products such that the customers does not have any complain issues regarding the
quality of the product.
For the given case, the Engineering Tooling Company that is located in the North East
of England is determined to adapt a quality management procedure in their company.
Recently, the hospital management board of North-East England approached the mentioned
company to sign a two-year contract for manufacturing hand-held medical equipment on a
larger scale. This has led to the expansion of the business of the Engineering Tooling
Company and they have to maintain their reputation in the market by maintaining their
product quality.
The company was established in the year of 1960 and became famous for producing
accurate and long-lasting engineering items. However, with increase in competition due to
globalization the company realised that it is impossible for their business to survive if they do
not adopt a radical strategy and work on the weak factors. Hence, this report will thoroughly
discuss about how the company can apply quality management plans for the survival of the
business as well as its expansion.
Discussion
Total Quality Management
The concept of Total Quality Management has emerged in the 1950’s, ten years
before the establishment of the Engineering Tooling Company ((Honarpour, Jusoh and Md
Nor 2018)). The company in its initial days only focused on the production of items like
engineering rules, callipers and scales and then expanded its business to manufacturing
specialist items. However, the owners are now keen to incorporate the total quality
management principles in developing their business worldwide along with maintaining the
quality of the items produced by them. The company will need to follow the principles while
Introduction
Total Quality Management are the procedural activities of an organization that aims to
improve the qualities of the business processes in order to attain the satisfaction of the
customers (Ross 2017). This is particularly a management approach by which the company
tries to retain success for a longer period by meeting the demands of the customers and
satisfying their needs. According to Kiran (2016), apart from accomplishing the regular tasks,
the employees of the organization focuses on giving their best quality of services and build
up robust products such that the customers does not have any complain issues regarding the
quality of the product.
For the given case, the Engineering Tooling Company that is located in the North East
of England is determined to adapt a quality management procedure in their company.
Recently, the hospital management board of North-East England approached the mentioned
company to sign a two-year contract for manufacturing hand-held medical equipment on a
larger scale. This has led to the expansion of the business of the Engineering Tooling
Company and they have to maintain their reputation in the market by maintaining their
product quality.
The company was established in the year of 1960 and became famous for producing
accurate and long-lasting engineering items. However, with increase in competition due to
globalization the company realised that it is impossible for their business to survive if they do
not adopt a radical strategy and work on the weak factors. Hence, this report will thoroughly
discuss about how the company can apply quality management plans for the survival of the
business as well as its expansion.
Discussion
Total Quality Management
The concept of Total Quality Management has emerged in the 1950’s, ten years
before the establishment of the Engineering Tooling Company ((Honarpour, Jusoh and Md
Nor 2018)). The company in its initial days only focused on the production of items like
engineering rules, callipers and scales and then expanded its business to manufacturing
specialist items. However, the owners are now keen to incorporate the total quality
management principles in developing their business worldwide along with maintaining the
quality of the items produced by them. The company will need to follow the principles while
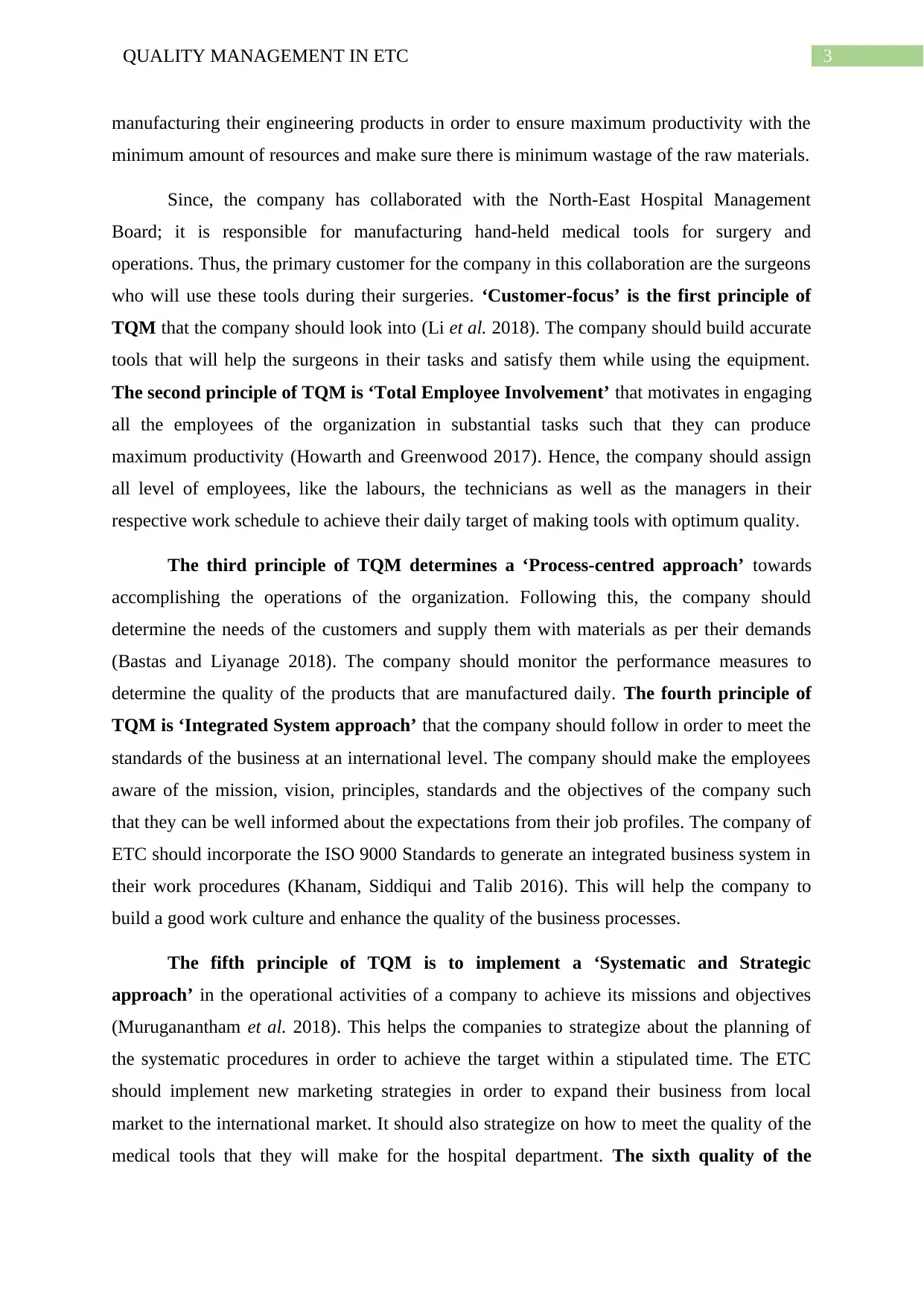
3QUALITY MANAGEMENT IN ETC
manufacturing their engineering products in order to ensure maximum productivity with the
minimum amount of resources and make sure there is minimum wastage of the raw materials.
Since, the company has collaborated with the North-East Hospital Management
Board; it is responsible for manufacturing hand-held medical tools for surgery and
operations. Thus, the primary customer for the company in this collaboration are the surgeons
who will use these tools during their surgeries. ‘Customer-focus’ is the first principle of
TQM that the company should look into (Li et al. 2018). The company should build accurate
tools that will help the surgeons in their tasks and satisfy them while using the equipment.
The second principle of TQM is ‘Total Employee Involvement’ that motivates in engaging
all the employees of the organization in substantial tasks such that they can produce
maximum productivity (Howarth and Greenwood 2017). Hence, the company should assign
all level of employees, like the labours, the technicians as well as the managers in their
respective work schedule to achieve their daily target of making tools with optimum quality.
The third principle of TQM determines a ‘Process-centred approach’ towards
accomplishing the operations of the organization. Following this, the company should
determine the needs of the customers and supply them with materials as per their demands
(Bastas and Liyanage 2018). The company should monitor the performance measures to
determine the quality of the products that are manufactured daily. The fourth principle of
TQM is ‘Integrated System approach’ that the company should follow in order to meet the
standards of the business at an international level. The company should make the employees
aware of the mission, vision, principles, standards and the objectives of the company such
that they can be well informed about the expectations from their job profiles. The company of
ETC should incorporate the ISO 9000 Standards to generate an integrated business system in
their work procedures (Khanam, Siddiqui and Talib 2016). This will help the company to
build a good work culture and enhance the quality of the business processes.
The fifth principle of TQM is to implement a ‘Systematic and Strategic
approach’ in the operational activities of a company to achieve its missions and objectives
(Muruganantham et al. 2018). This helps the companies to strategize about the planning of
the systematic procedures in order to achieve the target within a stipulated time. The ETC
should implement new marketing strategies in order to expand their business from local
market to the international market. It should also strategize on how to meet the quality of the
medical tools that they will make for the hospital department. The sixth quality of the
manufacturing their engineering products in order to ensure maximum productivity with the
minimum amount of resources and make sure there is minimum wastage of the raw materials.
Since, the company has collaborated with the North-East Hospital Management
Board; it is responsible for manufacturing hand-held medical tools for surgery and
operations. Thus, the primary customer for the company in this collaboration are the surgeons
who will use these tools during their surgeries. ‘Customer-focus’ is the first principle of
TQM that the company should look into (Li et al. 2018). The company should build accurate
tools that will help the surgeons in their tasks and satisfy them while using the equipment.
The second principle of TQM is ‘Total Employee Involvement’ that motivates in engaging
all the employees of the organization in substantial tasks such that they can produce
maximum productivity (Howarth and Greenwood 2017). Hence, the company should assign
all level of employees, like the labours, the technicians as well as the managers in their
respective work schedule to achieve their daily target of making tools with optimum quality.
The third principle of TQM determines a ‘Process-centred approach’ towards
accomplishing the operations of the organization. Following this, the company should
determine the needs of the customers and supply them with materials as per their demands
(Bastas and Liyanage 2018). The company should monitor the performance measures to
determine the quality of the products that are manufactured daily. The fourth principle of
TQM is ‘Integrated System approach’ that the company should follow in order to meet the
standards of the business at an international level. The company should make the employees
aware of the mission, vision, principles, standards and the objectives of the company such
that they can be well informed about the expectations from their job profiles. The company of
ETC should incorporate the ISO 9000 Standards to generate an integrated business system in
their work procedures (Khanam, Siddiqui and Talib 2016). This will help the company to
build a good work culture and enhance the quality of the business processes.
The fifth principle of TQM is to implement a ‘Systematic and Strategic
approach’ in the operational activities of a company to achieve its missions and objectives
(Muruganantham et al. 2018). This helps the companies to strategize about the planning of
the systematic procedures in order to achieve the target within a stipulated time. The ETC
should implement new marketing strategies in order to expand their business from local
market to the international market. It should also strategize on how to meet the quality of the
medical tools that they will make for the hospital department. The sixth quality of the
Secure Best Marks with AI Grader
Need help grading? Try our AI Grader for instant feedback on your assignments.
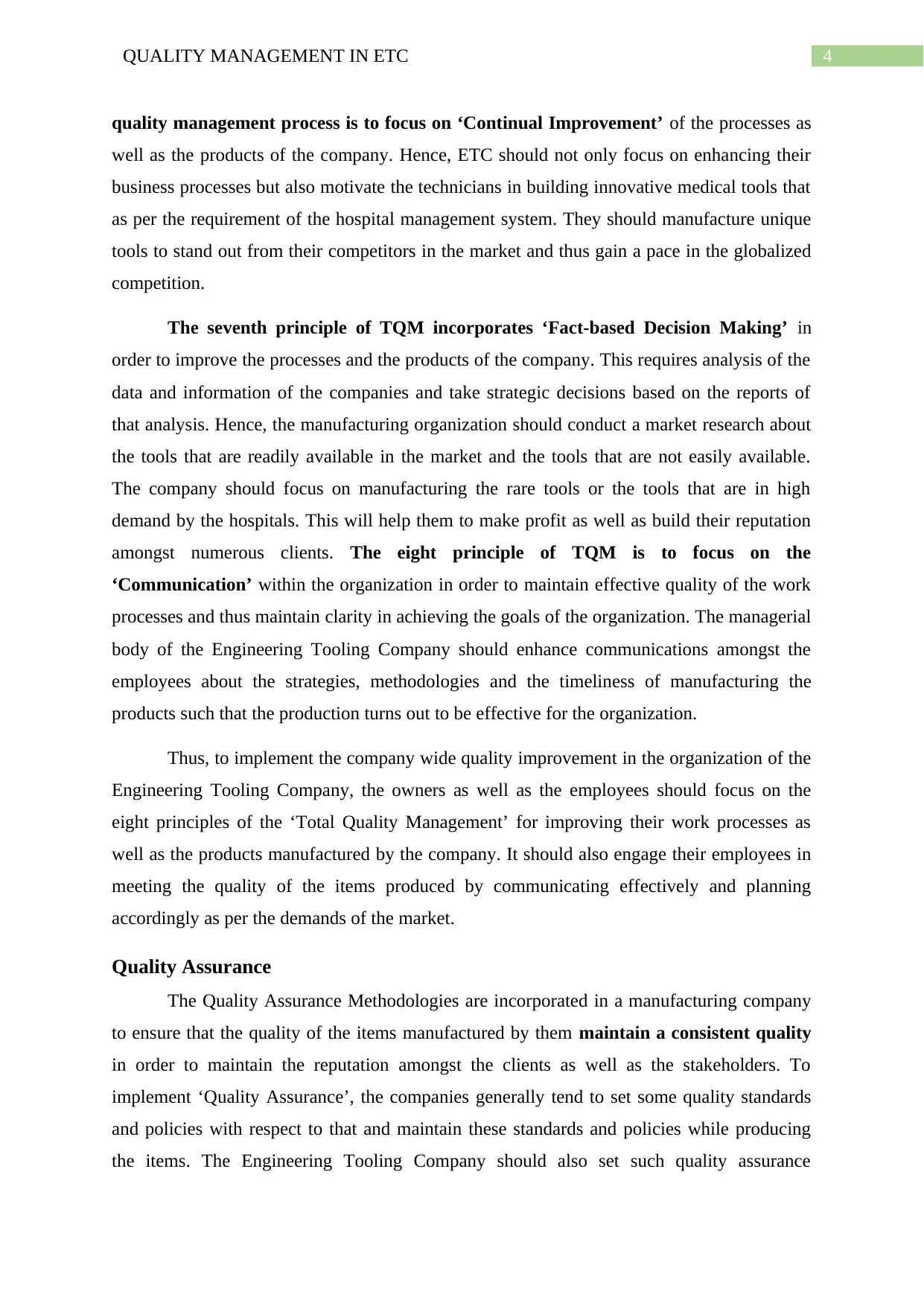
4QUALITY MANAGEMENT IN ETC
quality management process is to focus on ‘Continual Improvement’ of the processes as
well as the products of the company. Hence, ETC should not only focus on enhancing their
business processes but also motivate the technicians in building innovative medical tools that
as per the requirement of the hospital management system. They should manufacture unique
tools to stand out from their competitors in the market and thus gain a pace in the globalized
competition.
The seventh principle of TQM incorporates ‘Fact-based Decision Making’ in
order to improve the processes and the products of the company. This requires analysis of the
data and information of the companies and take strategic decisions based on the reports of
that analysis. Hence, the manufacturing organization should conduct a market research about
the tools that are readily available in the market and the tools that are not easily available.
The company should focus on manufacturing the rare tools or the tools that are in high
demand by the hospitals. This will help them to make profit as well as build their reputation
amongst numerous clients. The eight principle of TQM is to focus on the
‘Communication’ within the organization in order to maintain effective quality of the work
processes and thus maintain clarity in achieving the goals of the organization. The managerial
body of the Engineering Tooling Company should enhance communications amongst the
employees about the strategies, methodologies and the timeliness of manufacturing the
products such that the production turns out to be effective for the organization.
Thus, to implement the company wide quality improvement in the organization of the
Engineering Tooling Company, the owners as well as the employees should focus on the
eight principles of the ‘Total Quality Management’ for improving their work processes as
well as the products manufactured by the company. It should also engage their employees in
meeting the quality of the items produced by communicating effectively and planning
accordingly as per the demands of the market.
Quality Assurance
The Quality Assurance Methodologies are incorporated in a manufacturing company
to ensure that the quality of the items manufactured by them maintain a consistent quality
in order to maintain the reputation amongst the clients as well as the stakeholders. To
implement ‘Quality Assurance’, the companies generally tend to set some quality standards
and policies with respect to that and maintain these standards and policies while producing
the items. The Engineering Tooling Company should also set such quality assurance
quality management process is to focus on ‘Continual Improvement’ of the processes as
well as the products of the company. Hence, ETC should not only focus on enhancing their
business processes but also motivate the technicians in building innovative medical tools that
as per the requirement of the hospital management system. They should manufacture unique
tools to stand out from their competitors in the market and thus gain a pace in the globalized
competition.
The seventh principle of TQM incorporates ‘Fact-based Decision Making’ in
order to improve the processes and the products of the company. This requires analysis of the
data and information of the companies and take strategic decisions based on the reports of
that analysis. Hence, the manufacturing organization should conduct a market research about
the tools that are readily available in the market and the tools that are not easily available.
The company should focus on manufacturing the rare tools or the tools that are in high
demand by the hospitals. This will help them to make profit as well as build their reputation
amongst numerous clients. The eight principle of TQM is to focus on the
‘Communication’ within the organization in order to maintain effective quality of the work
processes and thus maintain clarity in achieving the goals of the organization. The managerial
body of the Engineering Tooling Company should enhance communications amongst the
employees about the strategies, methodologies and the timeliness of manufacturing the
products such that the production turns out to be effective for the organization.
Thus, to implement the company wide quality improvement in the organization of the
Engineering Tooling Company, the owners as well as the employees should focus on the
eight principles of the ‘Total Quality Management’ for improving their work processes as
well as the products manufactured by the company. It should also engage their employees in
meeting the quality of the items produced by communicating effectively and planning
accordingly as per the demands of the market.
Quality Assurance
The Quality Assurance Methodologies are incorporated in a manufacturing company
to ensure that the quality of the items manufactured by them maintain a consistent quality
in order to maintain the reputation amongst the clients as well as the stakeholders. To
implement ‘Quality Assurance’, the companies generally tend to set some quality standards
and policies with respect to that and maintain these standards and policies while producing
the items. The Engineering Tooling Company should also set such quality assurance
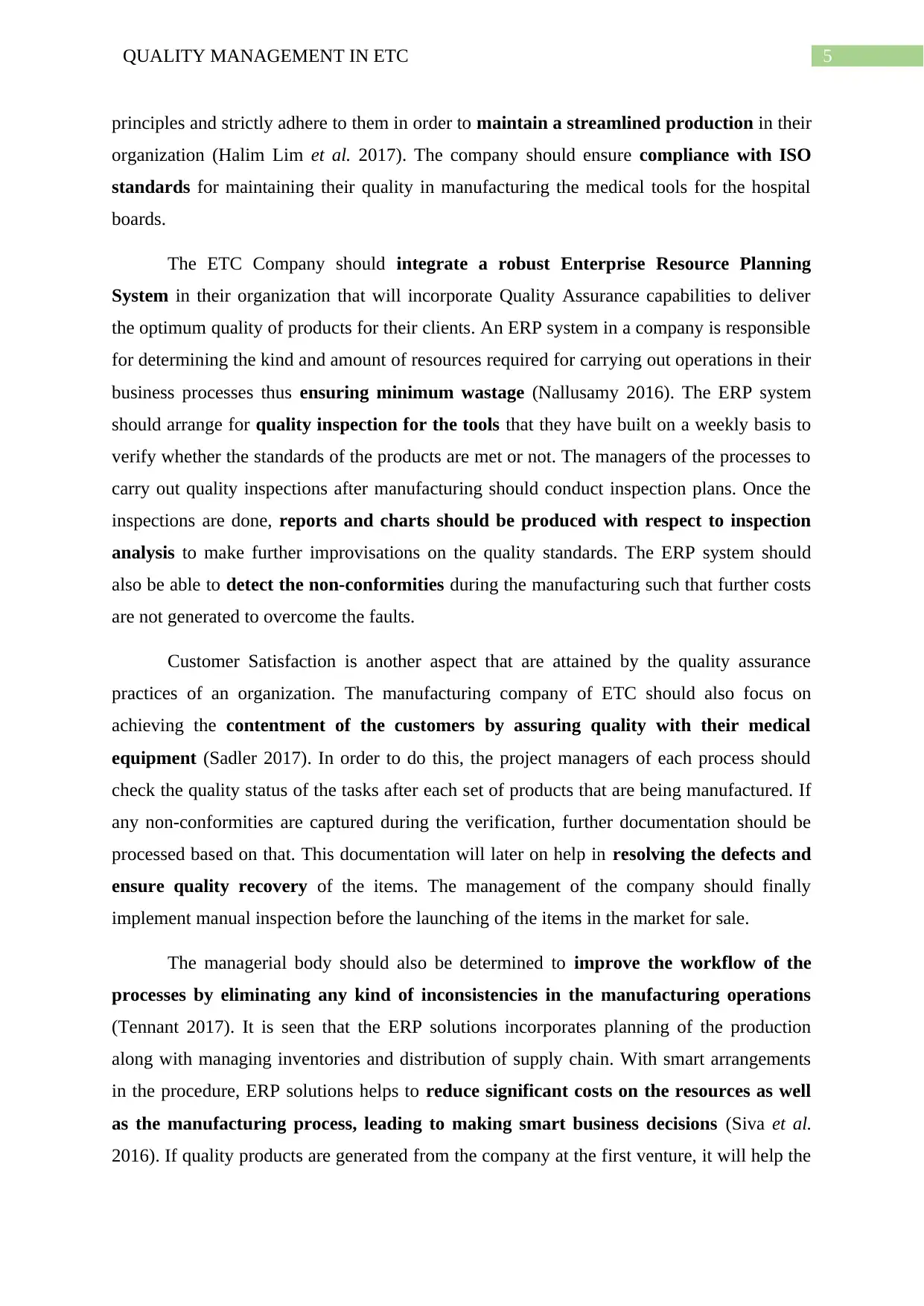
5QUALITY MANAGEMENT IN ETC
principles and strictly adhere to them in order to maintain a streamlined production in their
organization (Halim Lim et al. 2017). The company should ensure compliance with ISO
standards for maintaining their quality in manufacturing the medical tools for the hospital
boards.
The ETC Company should integrate a robust Enterprise Resource Planning
System in their organization that will incorporate Quality Assurance capabilities to deliver
the optimum quality of products for their clients. An ERP system in a company is responsible
for determining the kind and amount of resources required for carrying out operations in their
business processes thus ensuring minimum wastage (Nallusamy 2016). The ERP system
should arrange for quality inspection for the tools that they have built on a weekly basis to
verify whether the standards of the products are met or not. The managers of the processes to
carry out quality inspections after manufacturing should conduct inspection plans. Once the
inspections are done, reports and charts should be produced with respect to inspection
analysis to make further improvisations on the quality standards. The ERP system should
also be able to detect the non-conformities during the manufacturing such that further costs
are not generated to overcome the faults.
Customer Satisfaction is another aspect that are attained by the quality assurance
practices of an organization. The manufacturing company of ETC should also focus on
achieving the contentment of the customers by assuring quality with their medical
equipment (Sadler 2017). In order to do this, the project managers of each process should
check the quality status of the tasks after each set of products that are being manufactured. If
any non-conformities are captured during the verification, further documentation should be
processed based on that. This documentation will later on help in resolving the defects and
ensure quality recovery of the items. The management of the company should finally
implement manual inspection before the launching of the items in the market for sale.
The managerial body should also be determined to improve the workflow of the
processes by eliminating any kind of inconsistencies in the manufacturing operations
(Tennant 2017). It is seen that the ERP solutions incorporates planning of the production
along with managing inventories and distribution of supply chain. With smart arrangements
in the procedure, ERP solutions helps to reduce significant costs on the resources as well
as the manufacturing process, leading to making smart business decisions (Siva et al.
2016). If quality products are generated from the company at the first venture, it will help the
principles and strictly adhere to them in order to maintain a streamlined production in their
organization (Halim Lim et al. 2017). The company should ensure compliance with ISO
standards for maintaining their quality in manufacturing the medical tools for the hospital
boards.
The ETC Company should integrate a robust Enterprise Resource Planning
System in their organization that will incorporate Quality Assurance capabilities to deliver
the optimum quality of products for their clients. An ERP system in a company is responsible
for determining the kind and amount of resources required for carrying out operations in their
business processes thus ensuring minimum wastage (Nallusamy 2016). The ERP system
should arrange for quality inspection for the tools that they have built on a weekly basis to
verify whether the standards of the products are met or not. The managers of the processes to
carry out quality inspections after manufacturing should conduct inspection plans. Once the
inspections are done, reports and charts should be produced with respect to inspection
analysis to make further improvisations on the quality standards. The ERP system should
also be able to detect the non-conformities during the manufacturing such that further costs
are not generated to overcome the faults.
Customer Satisfaction is another aspect that are attained by the quality assurance
practices of an organization. The manufacturing company of ETC should also focus on
achieving the contentment of the customers by assuring quality with their medical
equipment (Sadler 2017). In order to do this, the project managers of each process should
check the quality status of the tasks after each set of products that are being manufactured. If
any non-conformities are captured during the verification, further documentation should be
processed based on that. This documentation will later on help in resolving the defects and
ensure quality recovery of the items. The management of the company should finally
implement manual inspection before the launching of the items in the market for sale.
The managerial body should also be determined to improve the workflow of the
processes by eliminating any kind of inconsistencies in the manufacturing operations
(Tennant 2017). It is seen that the ERP solutions incorporates planning of the production
along with managing inventories and distribution of supply chain. With smart arrangements
in the procedure, ERP solutions helps to reduce significant costs on the resources as well
as the manufacturing process, leading to making smart business decisions (Siva et al.
2016). If quality products are generated from the company at the first venture, it will help the

6QUALITY MANAGEMENT IN ETC
organization to gain customer loyalty and ensure free marketing amongst other clients.
Another way to gain customer loyalty is to update them continuously about the quality status
of the items and maintain transparency towards them.
Compliance is another quality assurance practise that the organization of ETC
should focus on predominantly such that the standards and guidelines are revised for the
manufacturing of the items. The ETC should implement health and safety guidelines in order
to maintain the safety of the employees in the work sphere of the company (Dale and Plunkett
2017). Potential workplace hazards should be readily resolved with the help of the
compliance with quality assurance of the ERP systems. The ERP system should also
generate safety reports on a monthly basis that will also help in improving safety measures
adapted by the company.
Quality Control
Quality Control within a manufacturing organization determines the defects that has
occurred while manufacturing and effectively eliminate those defects to ensure the
production of a robust item to the client (Tao et al. 2018). The defect may be found even
after the customers have achieved the items in their hand and in this case, too, the
organization is bound to eliminate the defect from the product to ensure that the customer is
satisfied with the product. The company of ETC has been producing medical equipment at
large to expand their business market across various hospitals. Hence, they need to ensure
that their manufacturing machineries are robust to produce equipment that will be
perfect in shape as well as quality.
The company can incorporate ‘Lean Manufacturing’ for controlling quality of the
manufactured items. Lean methodology focuses on using the resources with minimum
waste and ensure maximum efficiency in the product quality (Isaac et al. 2016). Hence, ETC
should incorporate lean manufacturing strategies in eliminating defects in products to ensure
cost reduction in manufacturing processes. Another quality control technique is the
‘Statistical Process Control’ that determines control of quality at every step of
manufacturing procedure. By this methodology, the managers track the performance
metrics to check the kinds of defects that exist in the product and eliminate them before
they move onto an advanced level (Sharma and Suri 2017). Hence, the managers will be able
to check the defects and ensure enhanced quality of the medical tools at every step of
manufacturing.
organization to gain customer loyalty and ensure free marketing amongst other clients.
Another way to gain customer loyalty is to update them continuously about the quality status
of the items and maintain transparency towards them.
Compliance is another quality assurance practise that the organization of ETC
should focus on predominantly such that the standards and guidelines are revised for the
manufacturing of the items. The ETC should implement health and safety guidelines in order
to maintain the safety of the employees in the work sphere of the company (Dale and Plunkett
2017). Potential workplace hazards should be readily resolved with the help of the
compliance with quality assurance of the ERP systems. The ERP system should also
generate safety reports on a monthly basis that will also help in improving safety measures
adapted by the company.
Quality Control
Quality Control within a manufacturing organization determines the defects that has
occurred while manufacturing and effectively eliminate those defects to ensure the
production of a robust item to the client (Tao et al. 2018). The defect may be found even
after the customers have achieved the items in their hand and in this case, too, the
organization is bound to eliminate the defect from the product to ensure that the customer is
satisfied with the product. The company of ETC has been producing medical equipment at
large to expand their business market across various hospitals. Hence, they need to ensure
that their manufacturing machineries are robust to produce equipment that will be
perfect in shape as well as quality.
The company can incorporate ‘Lean Manufacturing’ for controlling quality of the
manufactured items. Lean methodology focuses on using the resources with minimum
waste and ensure maximum efficiency in the product quality (Isaac et al. 2016). Hence, ETC
should incorporate lean manufacturing strategies in eliminating defects in products to ensure
cost reduction in manufacturing processes. Another quality control technique is the
‘Statistical Process Control’ that determines control of quality at every step of
manufacturing procedure. By this methodology, the managers track the performance
metrics to check the kinds of defects that exist in the product and eliminate them before
they move onto an advanced level (Sharma and Suri 2017). Hence, the managers will be able
to check the defects and ensure enhanced quality of the medical tools at every step of
manufacturing.
Paraphrase This Document
Need a fresh take? Get an instant paraphrase of this document with our AI Paraphraser
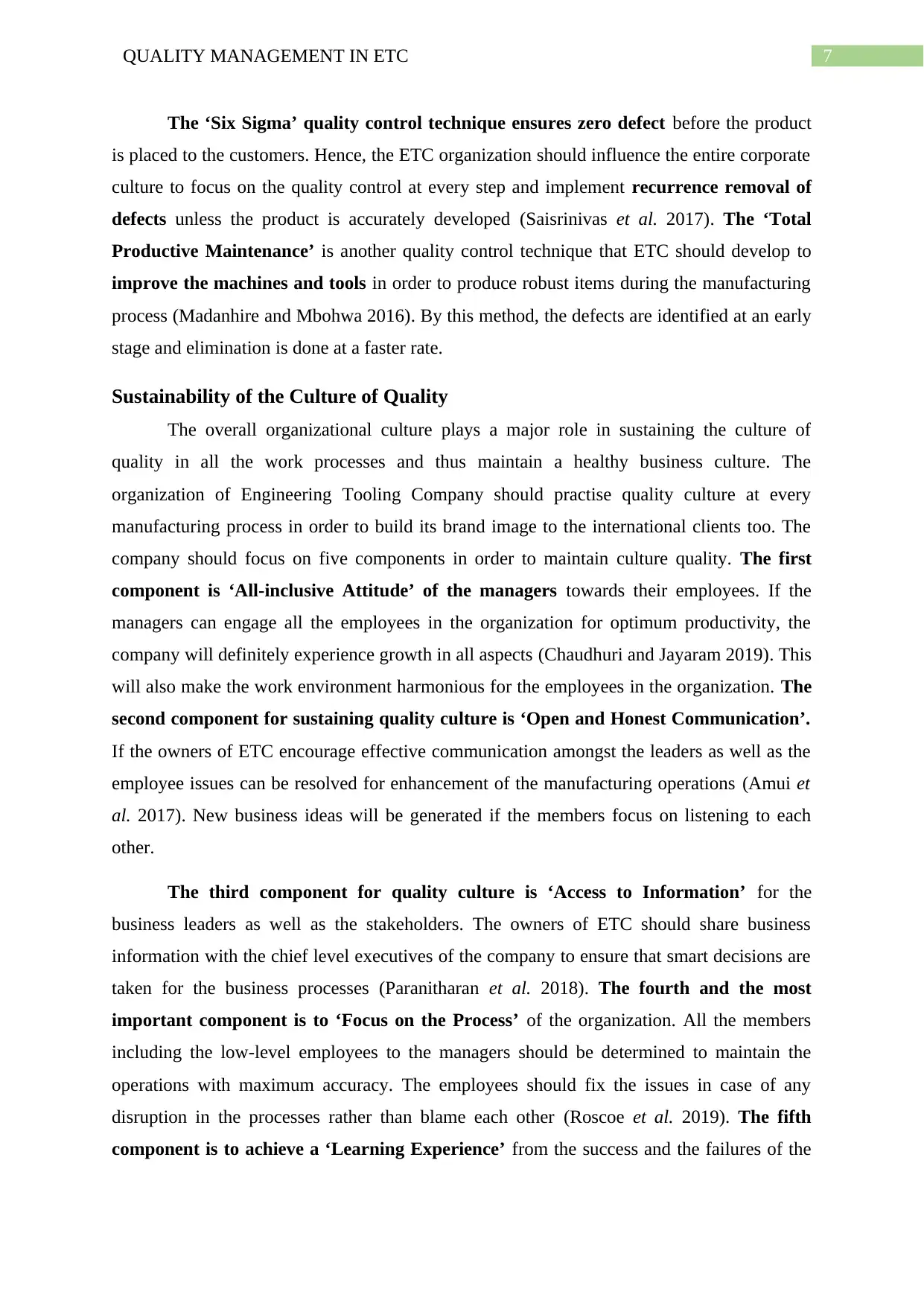
7QUALITY MANAGEMENT IN ETC
The ‘Six Sigma’ quality control technique ensures zero defect before the product
is placed to the customers. Hence, the ETC organization should influence the entire corporate
culture to focus on the quality control at every step and implement recurrence removal of
defects unless the product is accurately developed (Saisrinivas et al. 2017). The ‘Total
Productive Maintenance’ is another quality control technique that ETC should develop to
improve the machines and tools in order to produce robust items during the manufacturing
process (Madanhire and Mbohwa 2016). By this method, the defects are identified at an early
stage and elimination is done at a faster rate.
Sustainability of the Culture of Quality
The overall organizational culture plays a major role in sustaining the culture of
quality in all the work processes and thus maintain a healthy business culture. The
organization of Engineering Tooling Company should practise quality culture at every
manufacturing process in order to build its brand image to the international clients too. The
company should focus on five components in order to maintain culture quality. The first
component is ‘All-inclusive Attitude’ of the managers towards their employees. If the
managers can engage all the employees in the organization for optimum productivity, the
company will definitely experience growth in all aspects (Chaudhuri and Jayaram 2019). This
will also make the work environment harmonious for the employees in the organization. The
second component for sustaining quality culture is ‘Open and Honest Communication’.
If the owners of ETC encourage effective communication amongst the leaders as well as the
employee issues can be resolved for enhancement of the manufacturing operations (Amui et
al. 2017). New business ideas will be generated if the members focus on listening to each
other.
The third component for quality culture is ‘Access to Information’ for the
business leaders as well as the stakeholders. The owners of ETC should share business
information with the chief level executives of the company to ensure that smart decisions are
taken for the business processes (Paranitharan et al. 2018). The fourth and the most
important component is to ‘Focus on the Process’ of the organization. All the members
including the low-level employees to the managers should be determined to maintain the
operations with maximum accuracy. The employees should fix the issues in case of any
disruption in the processes rather than blame each other (Roscoe et al. 2019). The fifth
component is to achieve a ‘Learning Experience’ from the success and the failures of the
The ‘Six Sigma’ quality control technique ensures zero defect before the product
is placed to the customers. Hence, the ETC organization should influence the entire corporate
culture to focus on the quality control at every step and implement recurrence removal of
defects unless the product is accurately developed (Saisrinivas et al. 2017). The ‘Total
Productive Maintenance’ is another quality control technique that ETC should develop to
improve the machines and tools in order to produce robust items during the manufacturing
process (Madanhire and Mbohwa 2016). By this method, the defects are identified at an early
stage and elimination is done at a faster rate.
Sustainability of the Culture of Quality
The overall organizational culture plays a major role in sustaining the culture of
quality in all the work processes and thus maintain a healthy business culture. The
organization of Engineering Tooling Company should practise quality culture at every
manufacturing process in order to build its brand image to the international clients too. The
company should focus on five components in order to maintain culture quality. The first
component is ‘All-inclusive Attitude’ of the managers towards their employees. If the
managers can engage all the employees in the organization for optimum productivity, the
company will definitely experience growth in all aspects (Chaudhuri and Jayaram 2019). This
will also make the work environment harmonious for the employees in the organization. The
second component for sustaining quality culture is ‘Open and Honest Communication’.
If the owners of ETC encourage effective communication amongst the leaders as well as the
employee issues can be resolved for enhancement of the manufacturing operations (Amui et
al. 2017). New business ideas will be generated if the members focus on listening to each
other.
The third component for quality culture is ‘Access to Information’ for the
business leaders as well as the stakeholders. The owners of ETC should share business
information with the chief level executives of the company to ensure that smart decisions are
taken for the business processes (Paranitharan et al. 2018). The fourth and the most
important component is to ‘Focus on the Process’ of the organization. All the members
including the low-level employees to the managers should be determined to maintain the
operations with maximum accuracy. The employees should fix the issues in case of any
disruption in the processes rather than blame each other (Roscoe et al. 2019). The fifth
component is to achieve a ‘Learning Experience’ from the success and the failures of the
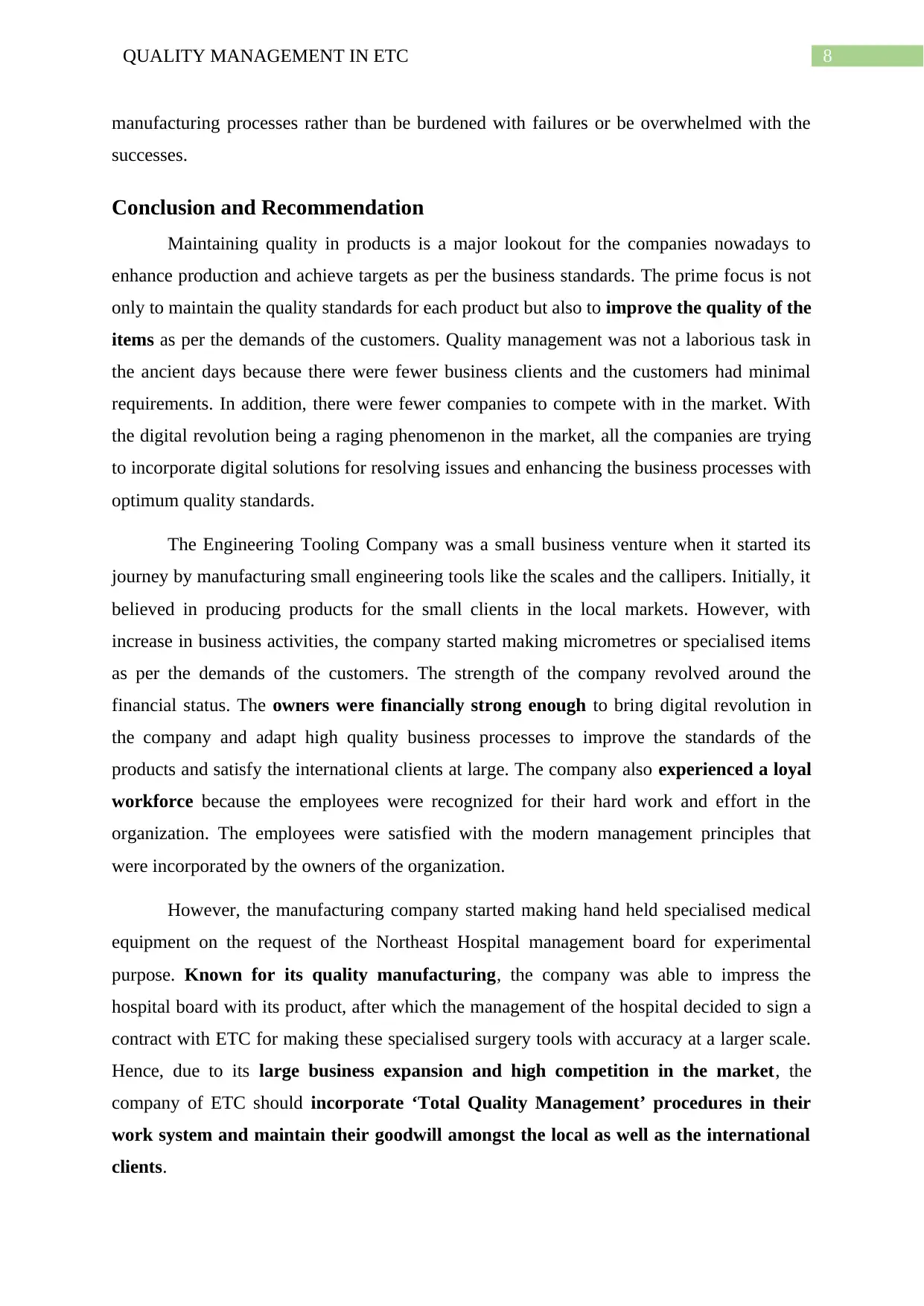
8QUALITY MANAGEMENT IN ETC
manufacturing processes rather than be burdened with failures or be overwhelmed with the
successes.
Conclusion and Recommendation
Maintaining quality in products is a major lookout for the companies nowadays to
enhance production and achieve targets as per the business standards. The prime focus is not
only to maintain the quality standards for each product but also to improve the quality of the
items as per the demands of the customers. Quality management was not a laborious task in
the ancient days because there were fewer business clients and the customers had minimal
requirements. In addition, there were fewer companies to compete with in the market. With
the digital revolution being a raging phenomenon in the market, all the companies are trying
to incorporate digital solutions for resolving issues and enhancing the business processes with
optimum quality standards.
The Engineering Tooling Company was a small business venture when it started its
journey by manufacturing small engineering tools like the scales and the callipers. Initially, it
believed in producing products for the small clients in the local markets. However, with
increase in business activities, the company started making micrometres or specialised items
as per the demands of the customers. The strength of the company revolved around the
financial status. The owners were financially strong enough to bring digital revolution in
the company and adapt high quality business processes to improve the standards of the
products and satisfy the international clients at large. The company also experienced a loyal
workforce because the employees were recognized for their hard work and effort in the
organization. The employees were satisfied with the modern management principles that
were incorporated by the owners of the organization.
However, the manufacturing company started making hand held specialised medical
equipment on the request of the Northeast Hospital management board for experimental
purpose. Known for its quality manufacturing, the company was able to impress the
hospital board with its product, after which the management of the hospital decided to sign a
contract with ETC for making these specialised surgery tools with accuracy at a larger scale.
Hence, due to its large business expansion and high competition in the market, the
company of ETC should incorporate ‘Total Quality Management’ procedures in their
work system and maintain their goodwill amongst the local as well as the international
clients.
manufacturing processes rather than be burdened with failures or be overwhelmed with the
successes.
Conclusion and Recommendation
Maintaining quality in products is a major lookout for the companies nowadays to
enhance production and achieve targets as per the business standards. The prime focus is not
only to maintain the quality standards for each product but also to improve the quality of the
items as per the demands of the customers. Quality management was not a laborious task in
the ancient days because there were fewer business clients and the customers had minimal
requirements. In addition, there were fewer companies to compete with in the market. With
the digital revolution being a raging phenomenon in the market, all the companies are trying
to incorporate digital solutions for resolving issues and enhancing the business processes with
optimum quality standards.
The Engineering Tooling Company was a small business venture when it started its
journey by manufacturing small engineering tools like the scales and the callipers. Initially, it
believed in producing products for the small clients in the local markets. However, with
increase in business activities, the company started making micrometres or specialised items
as per the demands of the customers. The strength of the company revolved around the
financial status. The owners were financially strong enough to bring digital revolution in
the company and adapt high quality business processes to improve the standards of the
products and satisfy the international clients at large. The company also experienced a loyal
workforce because the employees were recognized for their hard work and effort in the
organization. The employees were satisfied with the modern management principles that
were incorporated by the owners of the organization.
However, the manufacturing company started making hand held specialised medical
equipment on the request of the Northeast Hospital management board for experimental
purpose. Known for its quality manufacturing, the company was able to impress the
hospital board with its product, after which the management of the hospital decided to sign a
contract with ETC for making these specialised surgery tools with accuracy at a larger scale.
Hence, due to its large business expansion and high competition in the market, the
company of ETC should incorporate ‘Total Quality Management’ procedures in their
work system and maintain their goodwill amongst the local as well as the international
clients.
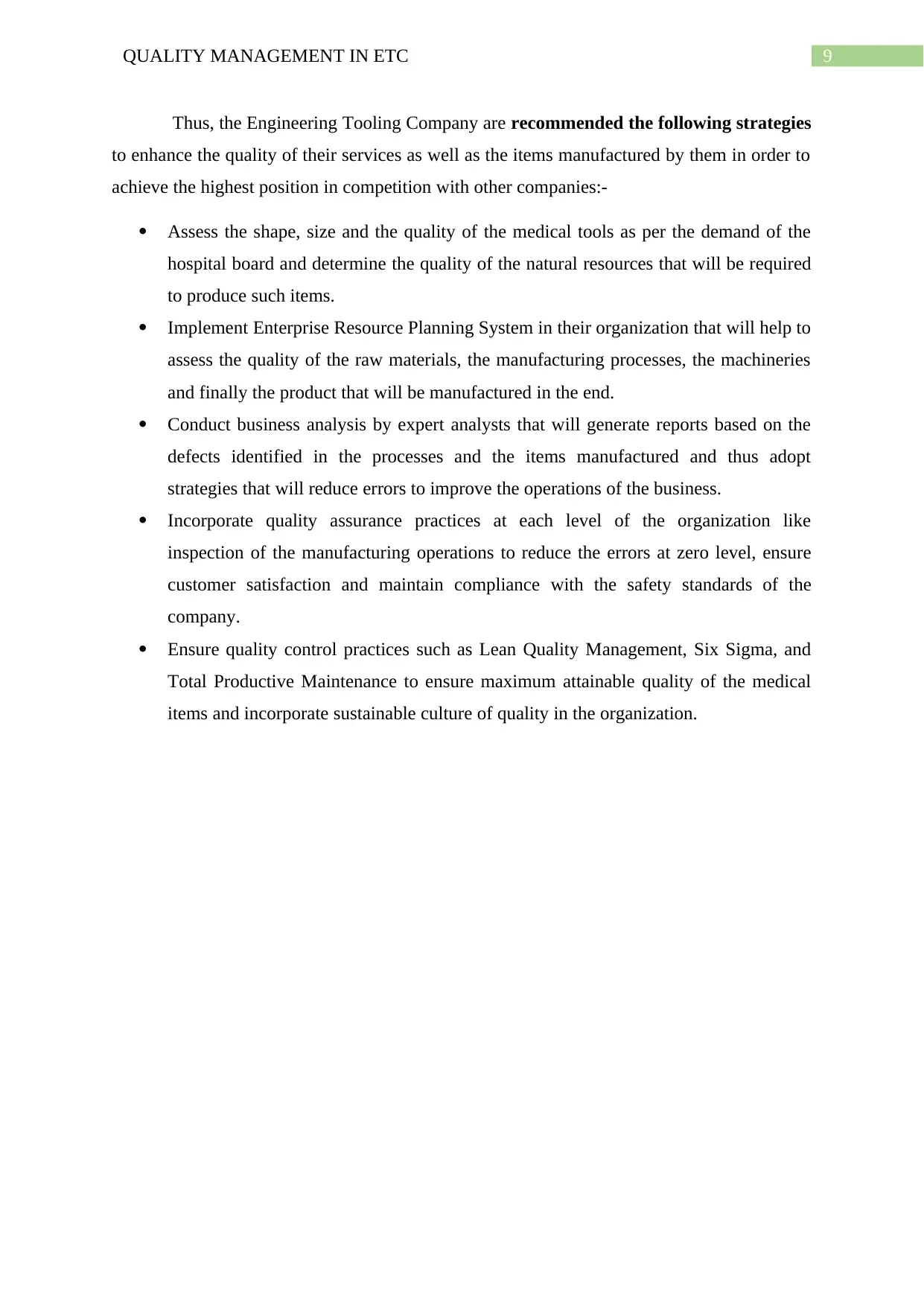
9QUALITY MANAGEMENT IN ETC
Thus, the Engineering Tooling Company are recommended the following strategies
to enhance the quality of their services as well as the items manufactured by them in order to
achieve the highest position in competition with other companies:-
Assess the shape, size and the quality of the medical tools as per the demand of the
hospital board and determine the quality of the natural resources that will be required
to produce such items.
Implement Enterprise Resource Planning System in their organization that will help to
assess the quality of the raw materials, the manufacturing processes, the machineries
and finally the product that will be manufactured in the end.
Conduct business analysis by expert analysts that will generate reports based on the
defects identified in the processes and the items manufactured and thus adopt
strategies that will reduce errors to improve the operations of the business.
Incorporate quality assurance practices at each level of the organization like
inspection of the manufacturing operations to reduce the errors at zero level, ensure
customer satisfaction and maintain compliance with the safety standards of the
company.
Ensure quality control practices such as Lean Quality Management, Six Sigma, and
Total Productive Maintenance to ensure maximum attainable quality of the medical
items and incorporate sustainable culture of quality in the organization.
Thus, the Engineering Tooling Company are recommended the following strategies
to enhance the quality of their services as well as the items manufactured by them in order to
achieve the highest position in competition with other companies:-
Assess the shape, size and the quality of the medical tools as per the demand of the
hospital board and determine the quality of the natural resources that will be required
to produce such items.
Implement Enterprise Resource Planning System in their organization that will help to
assess the quality of the raw materials, the manufacturing processes, the machineries
and finally the product that will be manufactured in the end.
Conduct business analysis by expert analysts that will generate reports based on the
defects identified in the processes and the items manufactured and thus adopt
strategies that will reduce errors to improve the operations of the business.
Incorporate quality assurance practices at each level of the organization like
inspection of the manufacturing operations to reduce the errors at zero level, ensure
customer satisfaction and maintain compliance with the safety standards of the
company.
Ensure quality control practices such as Lean Quality Management, Six Sigma, and
Total Productive Maintenance to ensure maximum attainable quality of the medical
items and incorporate sustainable culture of quality in the organization.
Secure Best Marks with AI Grader
Need help grading? Try our AI Grader for instant feedback on your assignments.
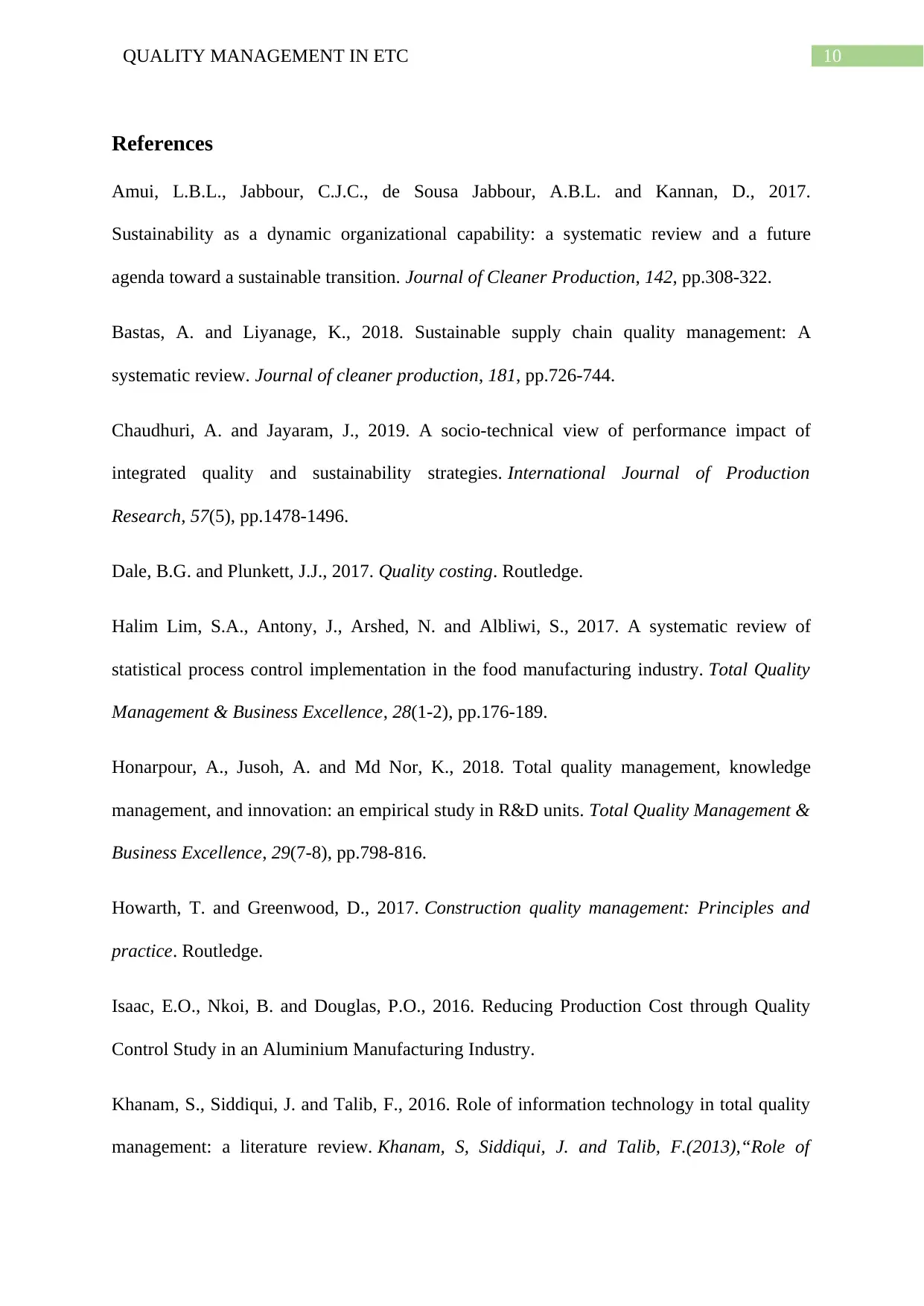
10QUALITY MANAGEMENT IN ETC
References
Amui, L.B.L., Jabbour, C.J.C., de Sousa Jabbour, A.B.L. and Kannan, D., 2017.
Sustainability as a dynamic organizational capability: a systematic review and a future
agenda toward a sustainable transition. Journal of Cleaner Production, 142, pp.308-322.
Bastas, A. and Liyanage, K., 2018. Sustainable supply chain quality management: A
systematic review. Journal of cleaner production, 181, pp.726-744.
Chaudhuri, A. and Jayaram, J., 2019. A socio-technical view of performance impact of
integrated quality and sustainability strategies. International Journal of Production
Research, 57(5), pp.1478-1496.
Dale, B.G. and Plunkett, J.J., 2017. Quality costing. Routledge.
Halim Lim, S.A., Antony, J., Arshed, N. and Albliwi, S., 2017. A systematic review of
statistical process control implementation in the food manufacturing industry. Total Quality
Management & Business Excellence, 28(1-2), pp.176-189.
Honarpour, A., Jusoh, A. and Md Nor, K., 2018. Total quality management, knowledge
management, and innovation: an empirical study in R&D units. Total Quality Management &
Business Excellence, 29(7-8), pp.798-816.
Howarth, T. and Greenwood, D., 2017. Construction quality management: Principles and
practice. Routledge.
Isaac, E.O., Nkoi, B. and Douglas, P.O., 2016. Reducing Production Cost through Quality
Control Study in an Aluminium Manufacturing Industry.
Khanam, S., Siddiqui, J. and Talib, F., 2016. Role of information technology in total quality
management: a literature review. Khanam, S, Siddiqui, J. and Talib, F.(2013),“Role of
References
Amui, L.B.L., Jabbour, C.J.C., de Sousa Jabbour, A.B.L. and Kannan, D., 2017.
Sustainability as a dynamic organizational capability: a systematic review and a future
agenda toward a sustainable transition. Journal of Cleaner Production, 142, pp.308-322.
Bastas, A. and Liyanage, K., 2018. Sustainable supply chain quality management: A
systematic review. Journal of cleaner production, 181, pp.726-744.
Chaudhuri, A. and Jayaram, J., 2019. A socio-technical view of performance impact of
integrated quality and sustainability strategies. International Journal of Production
Research, 57(5), pp.1478-1496.
Dale, B.G. and Plunkett, J.J., 2017. Quality costing. Routledge.
Halim Lim, S.A., Antony, J., Arshed, N. and Albliwi, S., 2017. A systematic review of
statistical process control implementation in the food manufacturing industry. Total Quality
Management & Business Excellence, 28(1-2), pp.176-189.
Honarpour, A., Jusoh, A. and Md Nor, K., 2018. Total quality management, knowledge
management, and innovation: an empirical study in R&D units. Total Quality Management &
Business Excellence, 29(7-8), pp.798-816.
Howarth, T. and Greenwood, D., 2017. Construction quality management: Principles and
practice. Routledge.
Isaac, E.O., Nkoi, B. and Douglas, P.O., 2016. Reducing Production Cost through Quality
Control Study in an Aluminium Manufacturing Industry.
Khanam, S., Siddiqui, J. and Talib, F., 2016. Role of information technology in total quality
management: a literature review. Khanam, S, Siddiqui, J. and Talib, F.(2013),“Role of
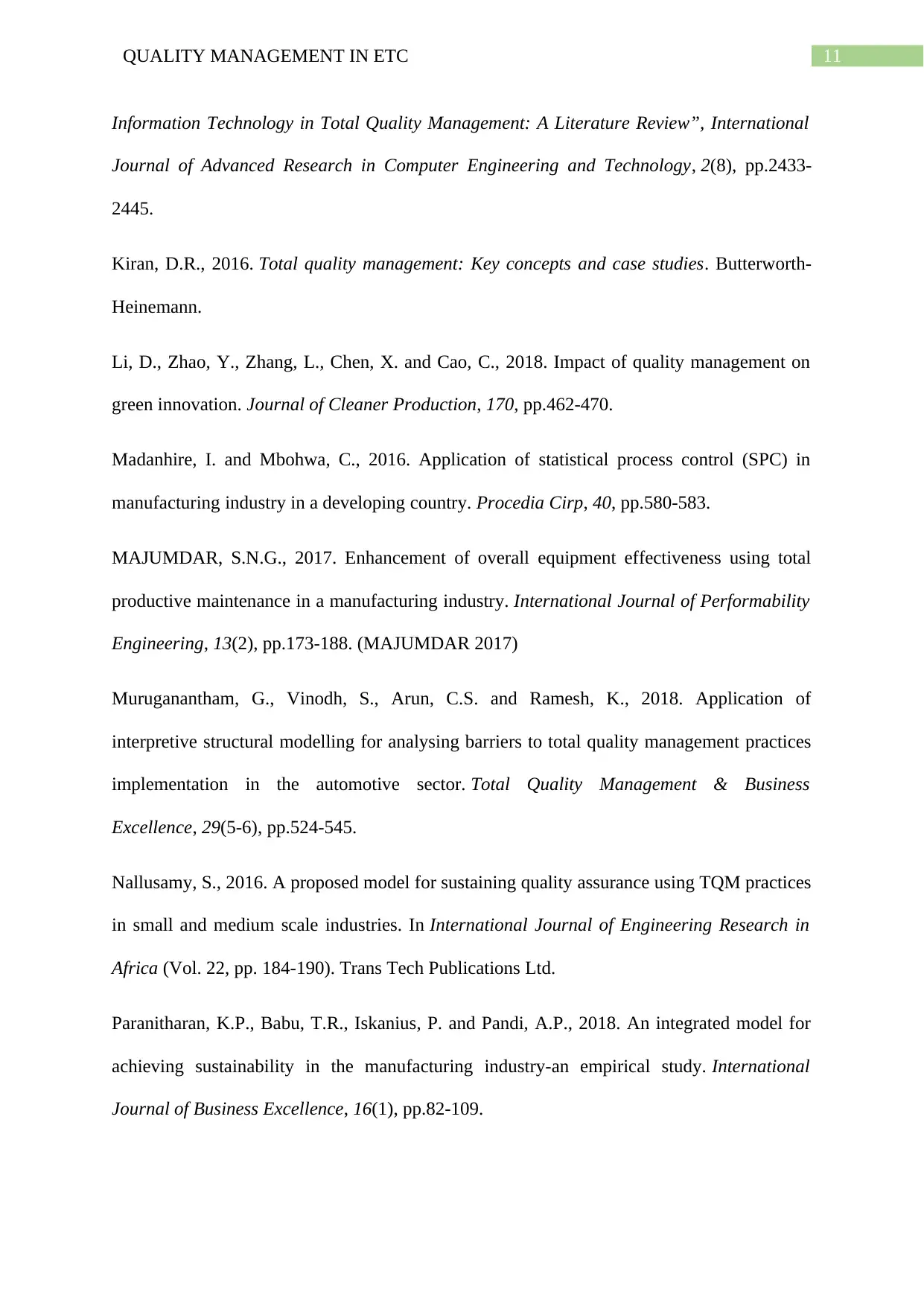
11QUALITY MANAGEMENT IN ETC
Information Technology in Total Quality Management: A Literature Review”, International
Journal of Advanced Research in Computer Engineering and Technology, 2(8), pp.2433-
2445.
Kiran, D.R., 2016. Total quality management: Key concepts and case studies. Butterworth-
Heinemann.
Li, D., Zhao, Y., Zhang, L., Chen, X. and Cao, C., 2018. Impact of quality management on
green innovation. Journal of Cleaner Production, 170, pp.462-470.
Madanhire, I. and Mbohwa, C., 2016. Application of statistical process control (SPC) in
manufacturing industry in a developing country. Procedia Cirp, 40, pp.580-583.
MAJUMDAR, S.N.G., 2017. Enhancement of overall equipment effectiveness using total
productive maintenance in a manufacturing industry. International Journal of Performability
Engineering, 13(2), pp.173-188. (MAJUMDAR 2017)
Muruganantham, G., Vinodh, S., Arun, C.S. and Ramesh, K., 2018. Application of
interpretive structural modelling for analysing barriers to total quality management practices
implementation in the automotive sector. Total Quality Management & Business
Excellence, 29(5-6), pp.524-545.
Nallusamy, S., 2016. A proposed model for sustaining quality assurance using TQM practices
in small and medium scale industries. In International Journal of Engineering Research in
Africa (Vol. 22, pp. 184-190). Trans Tech Publications Ltd.
Paranitharan, K.P., Babu, T.R., Iskanius, P. and Pandi, A.P., 2018. An integrated model for
achieving sustainability in the manufacturing industry-an empirical study. International
Journal of Business Excellence, 16(1), pp.82-109.
Information Technology in Total Quality Management: A Literature Review”, International
Journal of Advanced Research in Computer Engineering and Technology, 2(8), pp.2433-
2445.
Kiran, D.R., 2016. Total quality management: Key concepts and case studies. Butterworth-
Heinemann.
Li, D., Zhao, Y., Zhang, L., Chen, X. and Cao, C., 2018. Impact of quality management on
green innovation. Journal of Cleaner Production, 170, pp.462-470.
Madanhire, I. and Mbohwa, C., 2016. Application of statistical process control (SPC) in
manufacturing industry in a developing country. Procedia Cirp, 40, pp.580-583.
MAJUMDAR, S.N.G., 2017. Enhancement of overall equipment effectiveness using total
productive maintenance in a manufacturing industry. International Journal of Performability
Engineering, 13(2), pp.173-188. (MAJUMDAR 2017)
Muruganantham, G., Vinodh, S., Arun, C.S. and Ramesh, K., 2018. Application of
interpretive structural modelling for analysing barriers to total quality management practices
implementation in the automotive sector. Total Quality Management & Business
Excellence, 29(5-6), pp.524-545.
Nallusamy, S., 2016. A proposed model for sustaining quality assurance using TQM practices
in small and medium scale industries. In International Journal of Engineering Research in
Africa (Vol. 22, pp. 184-190). Trans Tech Publications Ltd.
Paranitharan, K.P., Babu, T.R., Iskanius, P. and Pandi, A.P., 2018. An integrated model for
achieving sustainability in the manufacturing industry-an empirical study. International
Journal of Business Excellence, 16(1), pp.82-109.
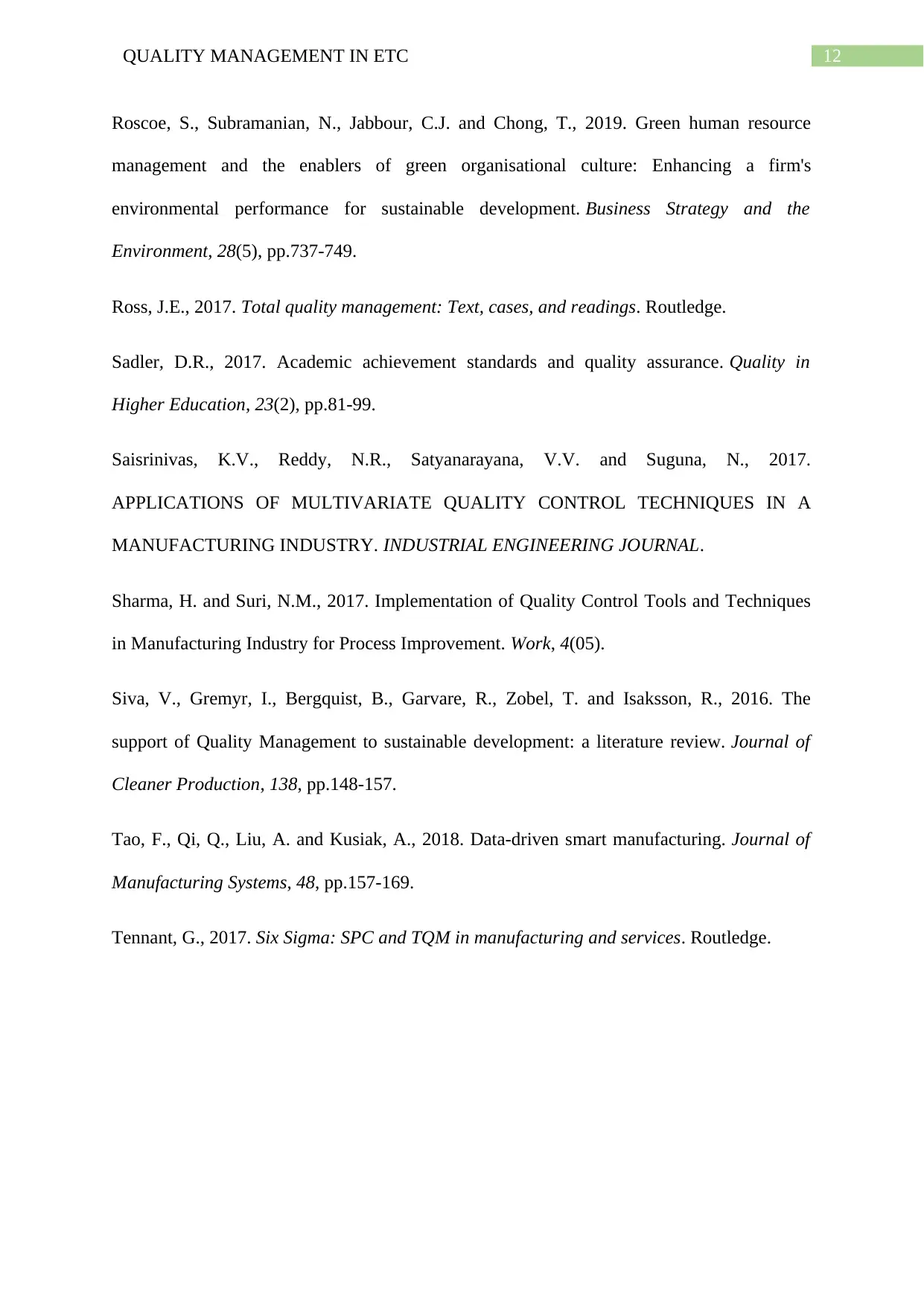
12QUALITY MANAGEMENT IN ETC
Roscoe, S., Subramanian, N., Jabbour, C.J. and Chong, T., 2019. Green human resource
management and the enablers of green organisational culture: Enhancing a firm's
environmental performance for sustainable development. Business Strategy and the
Environment, 28(5), pp.737-749.
Ross, J.E., 2017. Total quality management: Text, cases, and readings. Routledge.
Sadler, D.R., 2017. Academic achievement standards and quality assurance. Quality in
Higher Education, 23(2), pp.81-99.
Saisrinivas, K.V., Reddy, N.R., Satyanarayana, V.V. and Suguna, N., 2017.
APPLICATIONS OF MULTIVARIATE QUALITY CONTROL TECHNIQUES IN A
MANUFACTURING INDUSTRY. INDUSTRIAL ENGINEERING JOURNAL.
Sharma, H. and Suri, N.M., 2017. Implementation of Quality Control Tools and Techniques
in Manufacturing Industry for Process Improvement. Work, 4(05).
Siva, V., Gremyr, I., Bergquist, B., Garvare, R., Zobel, T. and Isaksson, R., 2016. The
support of Quality Management to sustainable development: a literature review. Journal of
Cleaner Production, 138, pp.148-157.
Tao, F., Qi, Q., Liu, A. and Kusiak, A., 2018. Data-driven smart manufacturing. Journal of
Manufacturing Systems, 48, pp.157-169.
Tennant, G., 2017. Six Sigma: SPC and TQM in manufacturing and services. Routledge.
Roscoe, S., Subramanian, N., Jabbour, C.J. and Chong, T., 2019. Green human resource
management and the enablers of green organisational culture: Enhancing a firm's
environmental performance for sustainable development. Business Strategy and the
Environment, 28(5), pp.737-749.
Ross, J.E., 2017. Total quality management: Text, cases, and readings. Routledge.
Sadler, D.R., 2017. Academic achievement standards and quality assurance. Quality in
Higher Education, 23(2), pp.81-99.
Saisrinivas, K.V., Reddy, N.R., Satyanarayana, V.V. and Suguna, N., 2017.
APPLICATIONS OF MULTIVARIATE QUALITY CONTROL TECHNIQUES IN A
MANUFACTURING INDUSTRY. INDUSTRIAL ENGINEERING JOURNAL.
Sharma, H. and Suri, N.M., 2017. Implementation of Quality Control Tools and Techniques
in Manufacturing Industry for Process Improvement. Work, 4(05).
Siva, V., Gremyr, I., Bergquist, B., Garvare, R., Zobel, T. and Isaksson, R., 2016. The
support of Quality Management to sustainable development: a literature review. Journal of
Cleaner Production, 138, pp.148-157.
Tao, F., Qi, Q., Liu, A. and Kusiak, A., 2018. Data-driven smart manufacturing. Journal of
Manufacturing Systems, 48, pp.157-169.
Tennant, G., 2017. Six Sigma: SPC and TQM in manufacturing and services. Routledge.
1 out of 13
Related Documents
![[object Object]](/_next/image/?url=%2F_next%2Fstatic%2Fmedia%2Flogo.6d15ce61.png&w=640&q=75)
Your All-in-One AI-Powered Toolkit for Academic Success.
+13062052269
info@desklib.com
Available 24*7 on WhatsApp / Email
Unlock your academic potential
© 2024 | Zucol Services PVT LTD | All rights reserved.