Theoretical Production Process Layout Design
VerifiedAdded on 2020/02/24
|15
|3810
|86
AI Summary
This assignment requires students to design a theoretical production process layout for an organization. The goal is to address existing problems such as high material handling costs and inefficient material flow. The new layout should prioritize cost reduction and improved operational efficiency t...
Read More
Contribute Materials
Your contribution can guide someone’s learning journey. Share your
documents today.
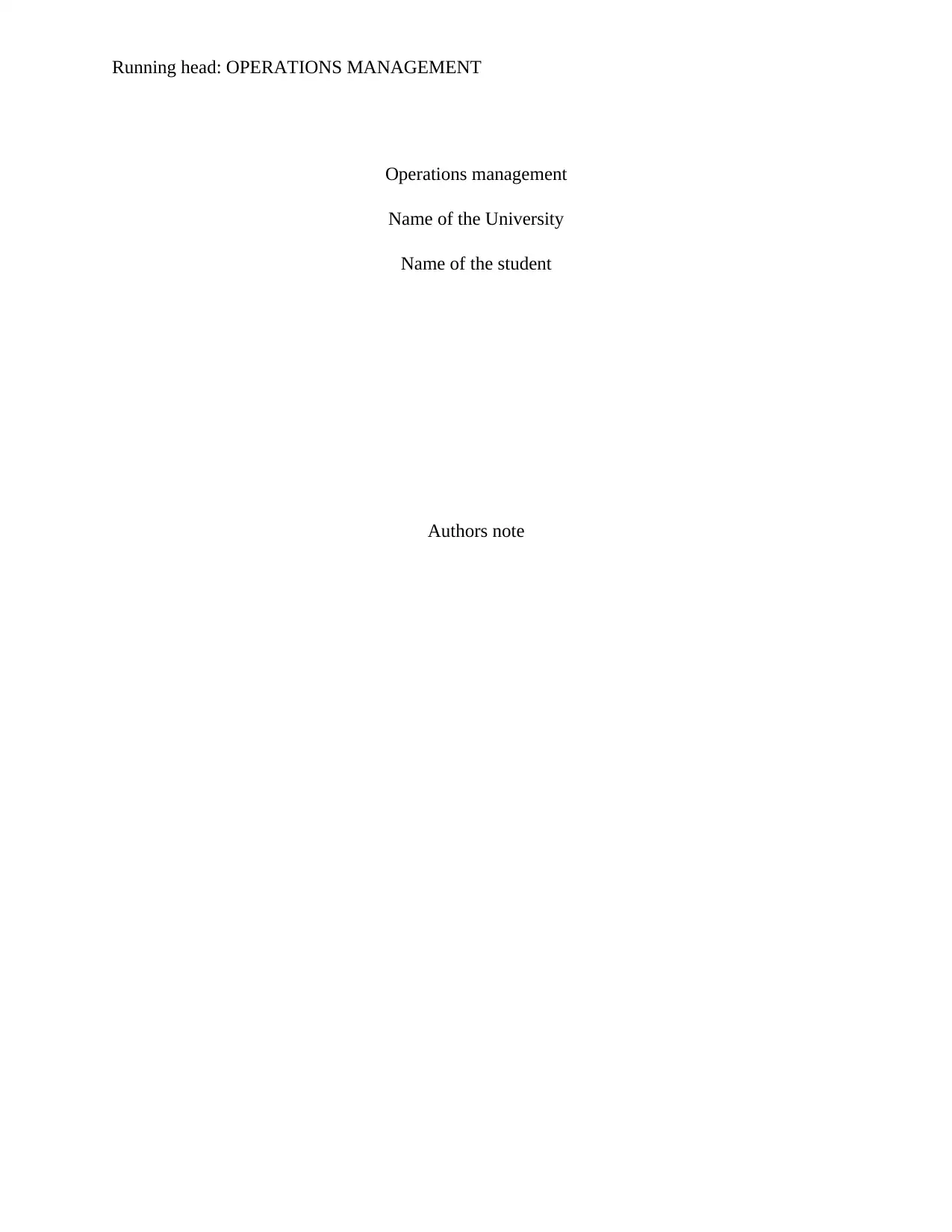
Running head: OPERATIONS MANAGEMENT
Operations management
Name of the University
Name of the student
Authors note
Operations management
Name of the University
Name of the student
Authors note
Secure Best Marks with AI Grader
Need help grading? Try our AI Grader for instant feedback on your assignments.
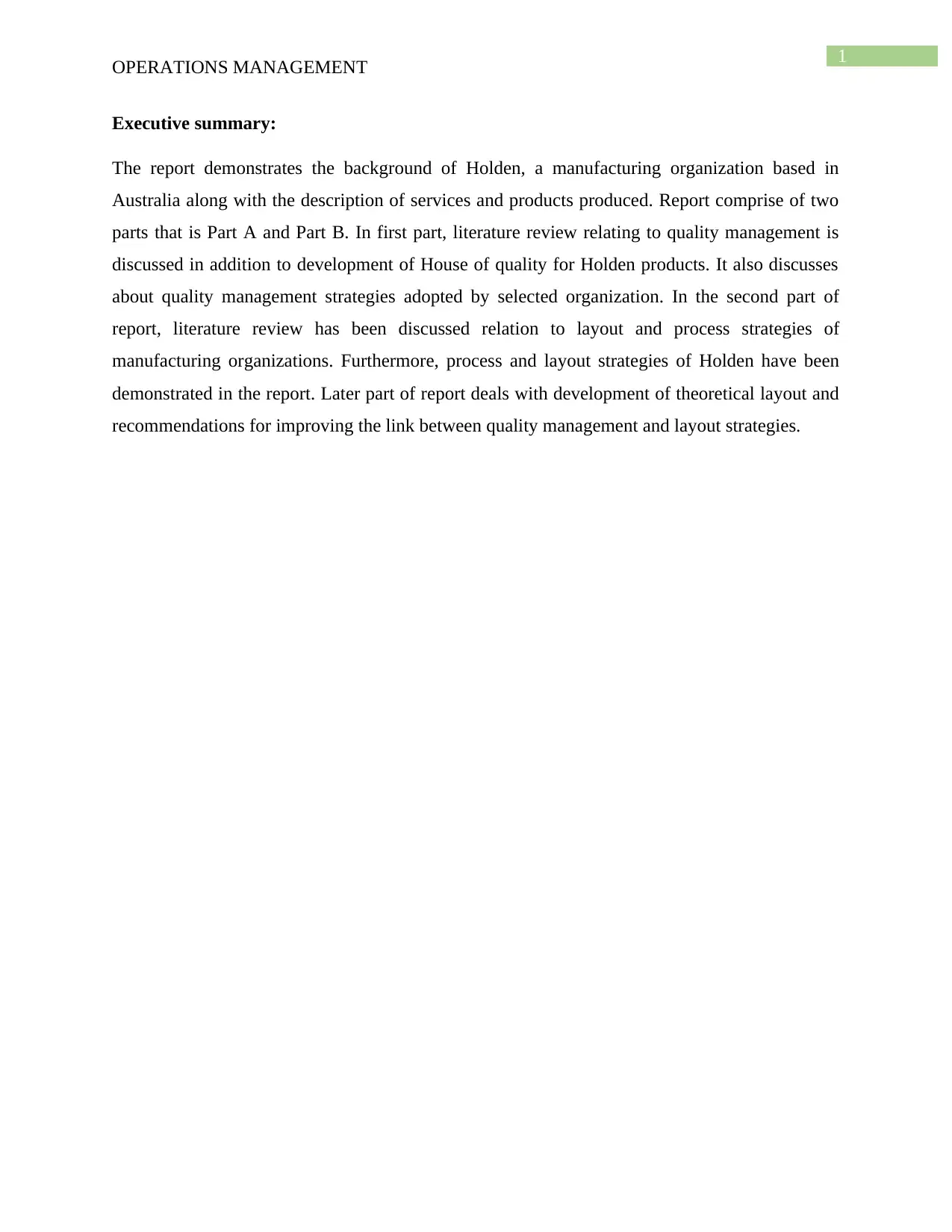
1
OPERATIONS MANAGEMENT
Executive summary:
The report demonstrates the background of Holden, a manufacturing organization based in
Australia along with the description of services and products produced. Report comprise of two
parts that is Part A and Part B. In first part, literature review relating to quality management is
discussed in addition to development of House of quality for Holden products. It also discusses
about quality management strategies adopted by selected organization. In the second part of
report, literature review has been discussed relation to layout and process strategies of
manufacturing organizations. Furthermore, process and layout strategies of Holden have been
demonstrated in the report. Later part of report deals with development of theoretical layout and
recommendations for improving the link between quality management and layout strategies.
OPERATIONS MANAGEMENT
Executive summary:
The report demonstrates the background of Holden, a manufacturing organization based in
Australia along with the description of services and products produced. Report comprise of two
parts that is Part A and Part B. In first part, literature review relating to quality management is
discussed in addition to development of House of quality for Holden products. It also discusses
about quality management strategies adopted by selected organization. In the second part of
report, literature review has been discussed relation to layout and process strategies of
manufacturing organizations. Furthermore, process and layout strategies of Holden have been
demonstrated in the report. Later part of report deals with development of theoretical layout and
recommendations for improving the link between quality management and layout strategies.
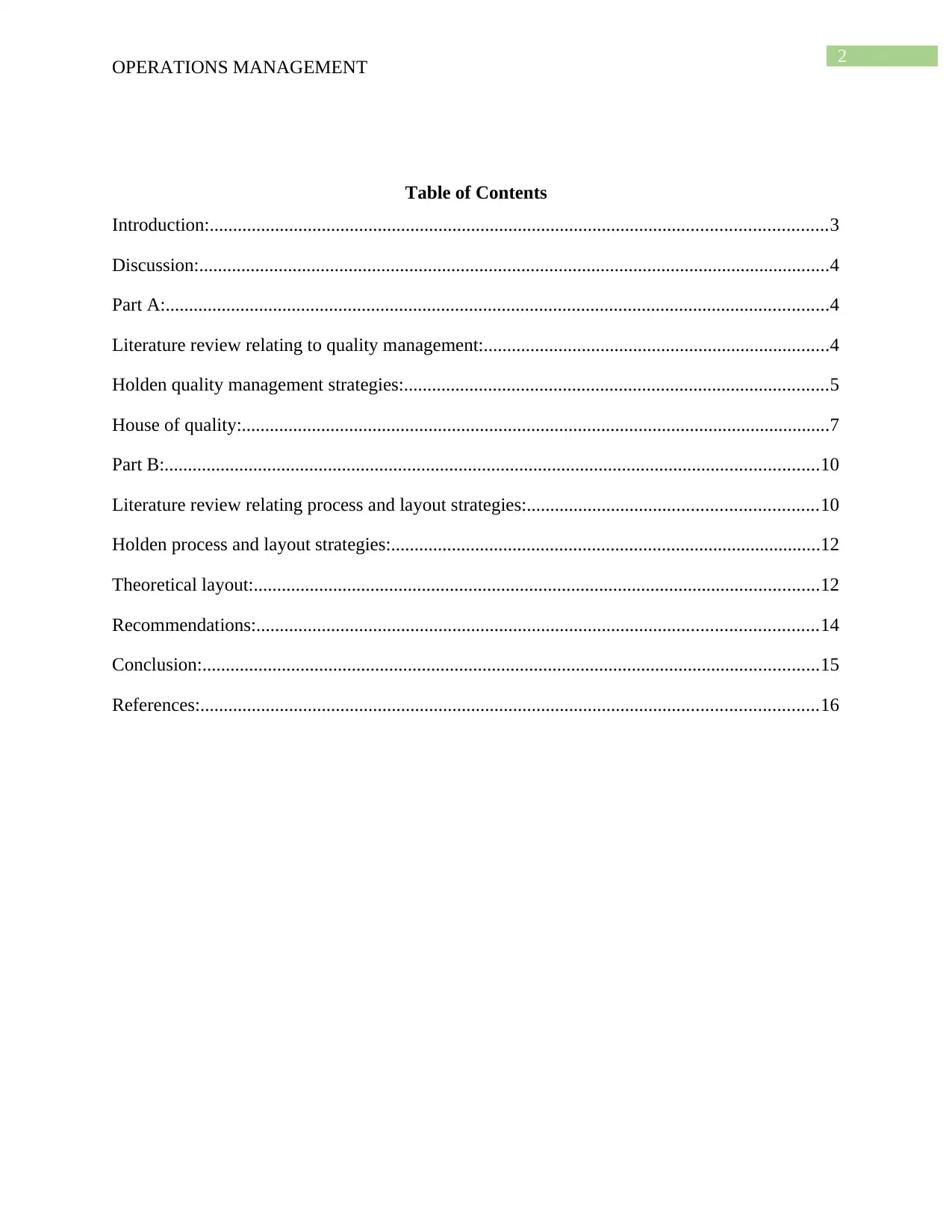
2
OPERATIONS MANAGEMENT
Table of Contents
Introduction:....................................................................................................................................3
Discussion:.......................................................................................................................................4
Part A:..............................................................................................................................................4
Literature review relating to quality management:..........................................................................4
Holden quality management strategies:...........................................................................................5
House of quality:..............................................................................................................................7
Part B:............................................................................................................................................10
Literature review relating process and layout strategies:..............................................................10
Holden process and layout strategies:............................................................................................12
Theoretical layout:.........................................................................................................................12
Recommendations:........................................................................................................................14
Conclusion:....................................................................................................................................15
References:....................................................................................................................................16
OPERATIONS MANAGEMENT
Table of Contents
Introduction:....................................................................................................................................3
Discussion:.......................................................................................................................................4
Part A:..............................................................................................................................................4
Literature review relating to quality management:..........................................................................4
Holden quality management strategies:...........................................................................................5
House of quality:..............................................................................................................................7
Part B:............................................................................................................................................10
Literature review relating process and layout strategies:..............................................................10
Holden process and layout strategies:............................................................................................12
Theoretical layout:.........................................................................................................................12
Recommendations:........................................................................................................................14
Conclusion:....................................................................................................................................15
References:....................................................................................................................................16
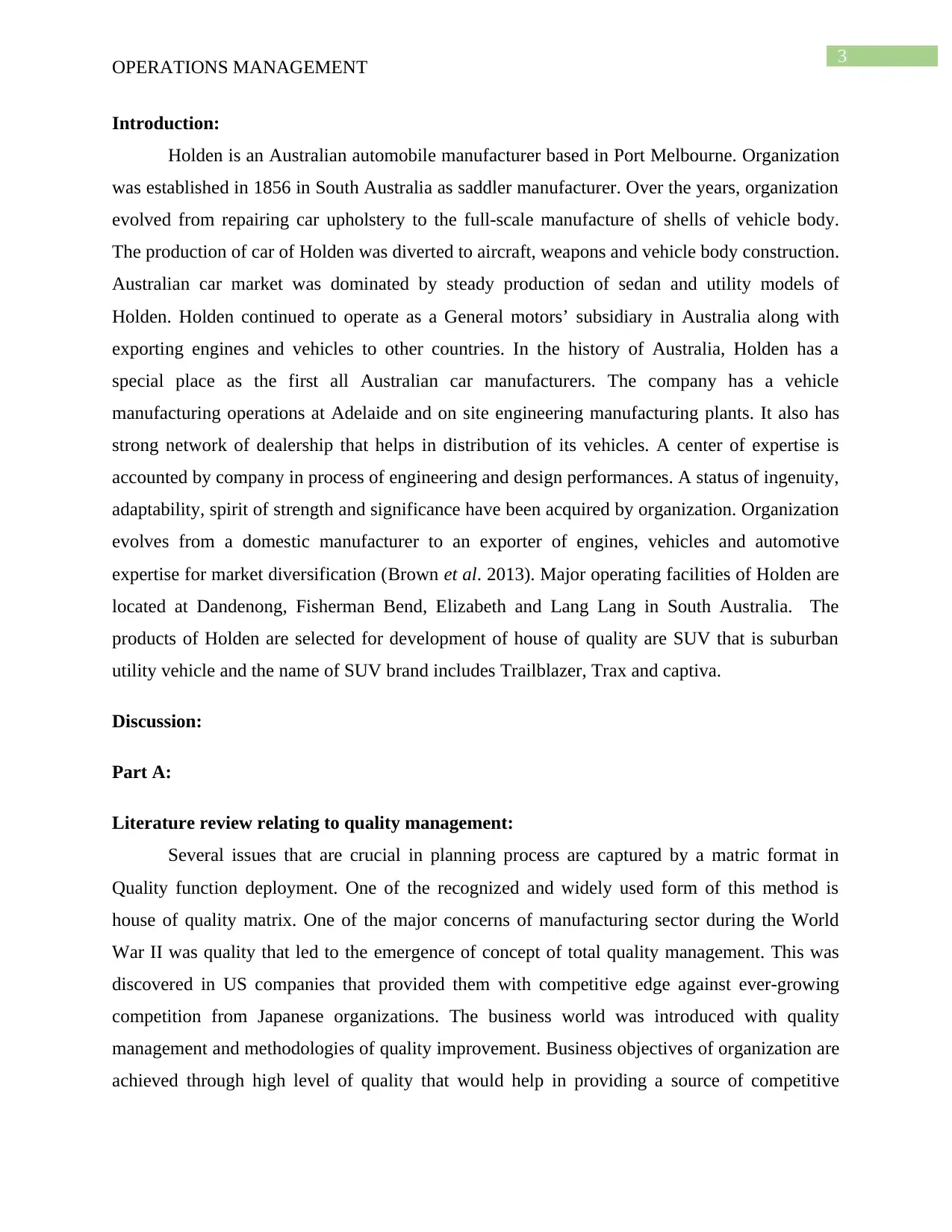
3
OPERATIONS MANAGEMENT
Introduction:
Holden is an Australian automobile manufacturer based in Port Melbourne. Organization
was established in 1856 in South Australia as saddler manufacturer. Over the years, organization
evolved from repairing car upholstery to the full-scale manufacture of shells of vehicle body.
The production of car of Holden was diverted to aircraft, weapons and vehicle body construction.
Australian car market was dominated by steady production of sedan and utility models of
Holden. Holden continued to operate as a General motors’ subsidiary in Australia along with
exporting engines and vehicles to other countries. In the history of Australia, Holden has a
special place as the first all Australian car manufacturers. The company has a vehicle
manufacturing operations at Adelaide and on site engineering manufacturing plants. It also has
strong network of dealership that helps in distribution of its vehicles. A center of expertise is
accounted by company in process of engineering and design performances. A status of ingenuity,
adaptability, spirit of strength and significance have been acquired by organization. Organization
evolves from a domestic manufacturer to an exporter of engines, vehicles and automotive
expertise for market diversification (Brown et al. 2013). Major operating facilities of Holden are
located at Dandenong, Fisherman Bend, Elizabeth and Lang Lang in South Australia. The
products of Holden are selected for development of house of quality are SUV that is suburban
utility vehicle and the name of SUV brand includes Trailblazer, Trax and captiva.
Discussion:
Part A:
Literature review relating to quality management:
Several issues that are crucial in planning process are captured by a matric format in
Quality function deployment. One of the recognized and widely used form of this method is
house of quality matrix. One of the major concerns of manufacturing sector during the World
War II was quality that led to the emergence of concept of total quality management. This was
discovered in US companies that provided them with competitive edge against ever-growing
competition from Japanese organizations. The business world was introduced with quality
management and methodologies of quality improvement. Business objectives of organization are
achieved through high level of quality that would help in providing a source of competitive
OPERATIONS MANAGEMENT
Introduction:
Holden is an Australian automobile manufacturer based in Port Melbourne. Organization
was established in 1856 in South Australia as saddler manufacturer. Over the years, organization
evolved from repairing car upholstery to the full-scale manufacture of shells of vehicle body.
The production of car of Holden was diverted to aircraft, weapons and vehicle body construction.
Australian car market was dominated by steady production of sedan and utility models of
Holden. Holden continued to operate as a General motors’ subsidiary in Australia along with
exporting engines and vehicles to other countries. In the history of Australia, Holden has a
special place as the first all Australian car manufacturers. The company has a vehicle
manufacturing operations at Adelaide and on site engineering manufacturing plants. It also has
strong network of dealership that helps in distribution of its vehicles. A center of expertise is
accounted by company in process of engineering and design performances. A status of ingenuity,
adaptability, spirit of strength and significance have been acquired by organization. Organization
evolves from a domestic manufacturer to an exporter of engines, vehicles and automotive
expertise for market diversification (Brown et al. 2013). Major operating facilities of Holden are
located at Dandenong, Fisherman Bend, Elizabeth and Lang Lang in South Australia. The
products of Holden are selected for development of house of quality are SUV that is suburban
utility vehicle and the name of SUV brand includes Trailblazer, Trax and captiva.
Discussion:
Part A:
Literature review relating to quality management:
Several issues that are crucial in planning process are captured by a matric format in
Quality function deployment. One of the recognized and widely used form of this method is
house of quality matrix. One of the major concerns of manufacturing sector during the World
War II was quality that led to the emergence of concept of total quality management. This was
discovered in US companies that provided them with competitive edge against ever-growing
competition from Japanese organizations. The business world was introduced with quality
management and methodologies of quality improvement. Business objectives of organization are
achieved through high level of quality that would help in providing a source of competitive
Secure Best Marks with AI Grader
Need help grading? Try our AI Grader for instant feedback on your assignments.
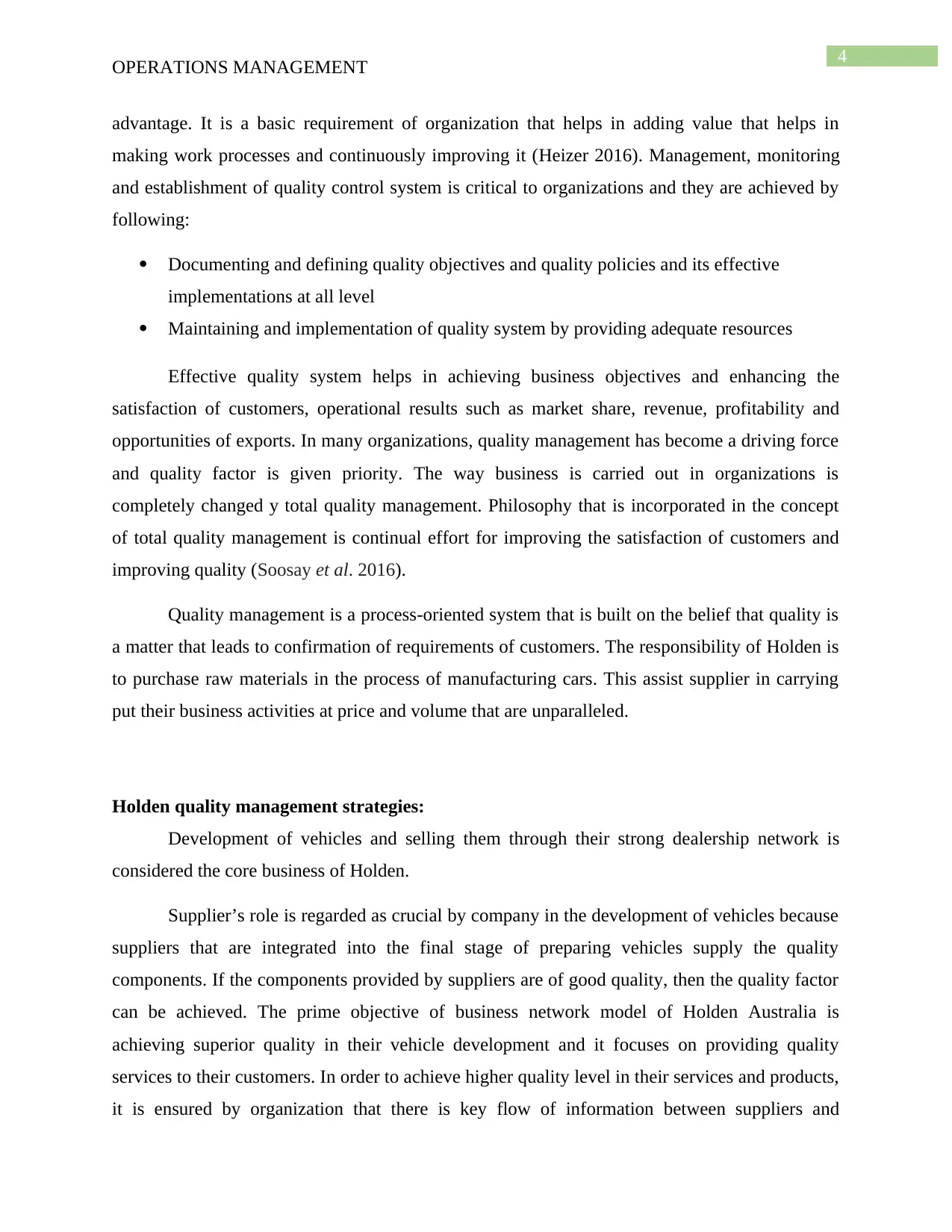
4
OPERATIONS MANAGEMENT
advantage. It is a basic requirement of organization that helps in adding value that helps in
making work processes and continuously improving it (Heizer 2016). Management, monitoring
and establishment of quality control system is critical to organizations and they are achieved by
following:
Documenting and defining quality objectives and quality policies and its effective
implementations at all level
Maintaining and implementation of quality system by providing adequate resources
Effective quality system helps in achieving business objectives and enhancing the
satisfaction of customers, operational results such as market share, revenue, profitability and
opportunities of exports. In many organizations, quality management has become a driving force
and quality factor is given priority. The way business is carried out in organizations is
completely changed y total quality management. Philosophy that is incorporated in the concept
of total quality management is continual effort for improving the satisfaction of customers and
improving quality (Soosay et al. 2016).
Quality management is a process-oriented system that is built on the belief that quality is
a matter that leads to confirmation of requirements of customers. The responsibility of Holden is
to purchase raw materials in the process of manufacturing cars. This assist supplier in carrying
put their business activities at price and volume that are unparalleled.
Holden quality management strategies:
Development of vehicles and selling them through their strong dealership network is
considered the core business of Holden.
Supplier’s role is regarded as crucial by company in the development of vehicles because
suppliers that are integrated into the final stage of preparing vehicles supply the quality
components. If the components provided by suppliers are of good quality, then the quality factor
can be achieved. The prime objective of business network model of Holden Australia is
achieving superior quality in their vehicle development and it focuses on providing quality
services to their customers. In order to achieve higher quality level in their services and products,
it is ensured by organization that there is key flow of information between suppliers and
OPERATIONS MANAGEMENT
advantage. It is a basic requirement of organization that helps in adding value that helps in
making work processes and continuously improving it (Heizer 2016). Management, monitoring
and establishment of quality control system is critical to organizations and they are achieved by
following:
Documenting and defining quality objectives and quality policies and its effective
implementations at all level
Maintaining and implementation of quality system by providing adequate resources
Effective quality system helps in achieving business objectives and enhancing the
satisfaction of customers, operational results such as market share, revenue, profitability and
opportunities of exports. In many organizations, quality management has become a driving force
and quality factor is given priority. The way business is carried out in organizations is
completely changed y total quality management. Philosophy that is incorporated in the concept
of total quality management is continual effort for improving the satisfaction of customers and
improving quality (Soosay et al. 2016).
Quality management is a process-oriented system that is built on the belief that quality is
a matter that leads to confirmation of requirements of customers. The responsibility of Holden is
to purchase raw materials in the process of manufacturing cars. This assist supplier in carrying
put their business activities at price and volume that are unparalleled.
Holden quality management strategies:
Development of vehicles and selling them through their strong dealership network is
considered the core business of Holden.
Supplier’s role is regarded as crucial by company in the development of vehicles because
suppliers that are integrated into the final stage of preparing vehicles supply the quality
components. If the components provided by suppliers are of good quality, then the quality factor
can be achieved. The prime objective of business network model of Holden Australia is
achieving superior quality in their vehicle development and it focuses on providing quality
services to their customers. In order to achieve higher quality level in their services and products,
it is ensured by organization that there is key flow of information between suppliers and
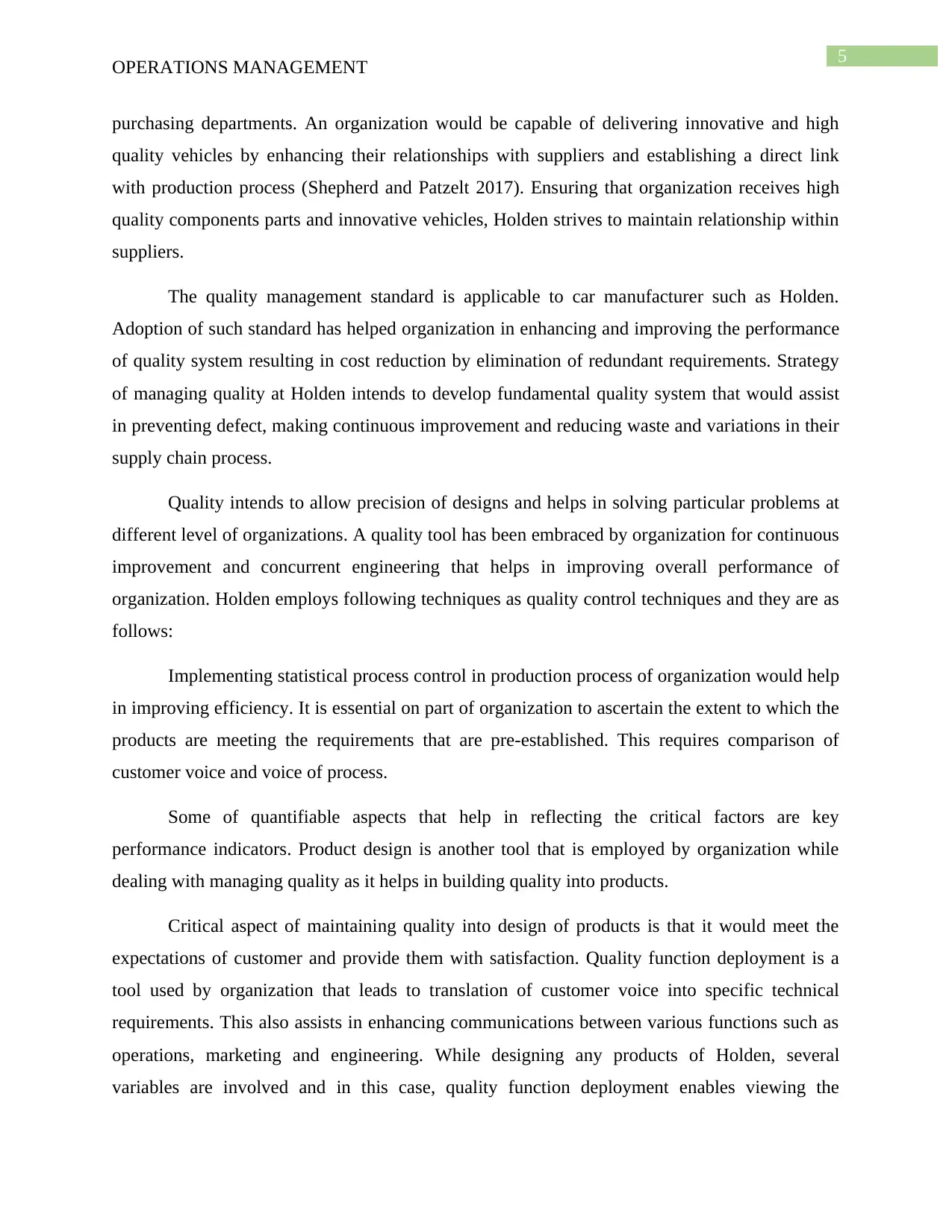
5
OPERATIONS MANAGEMENT
purchasing departments. An organization would be capable of delivering innovative and high
quality vehicles by enhancing their relationships with suppliers and establishing a direct link
with production process (Shepherd and Patzelt 2017). Ensuring that organization receives high
quality components parts and innovative vehicles, Holden strives to maintain relationship within
suppliers.
The quality management standard is applicable to car manufacturer such as Holden.
Adoption of such standard has helped organization in enhancing and improving the performance
of quality system resulting in cost reduction by elimination of redundant requirements. Strategy
of managing quality at Holden intends to develop fundamental quality system that would assist
in preventing defect, making continuous improvement and reducing waste and variations in their
supply chain process.
Quality intends to allow precision of designs and helps in solving particular problems at
different level of organizations. A quality tool has been embraced by organization for continuous
improvement and concurrent engineering that helps in improving overall performance of
organization. Holden employs following techniques as quality control techniques and they are as
follows:
Implementing statistical process control in production process of organization would help
in improving efficiency. It is essential on part of organization to ascertain the extent to which the
products are meeting the requirements that are pre-established. This requires comparison of
customer voice and voice of process.
Some of quantifiable aspects that help in reflecting the critical factors are key
performance indicators. Product design is another tool that is employed by organization while
dealing with managing quality as it helps in building quality into products.
Critical aspect of maintaining quality into design of products is that it would meet the
expectations of customer and provide them with satisfaction. Quality function deployment is a
tool used by organization that leads to translation of customer voice into specific technical
requirements. This also assists in enhancing communications between various functions such as
operations, marketing and engineering. While designing any products of Holden, several
variables are involved and in this case, quality function deployment enables viewing the
OPERATIONS MANAGEMENT
purchasing departments. An organization would be capable of delivering innovative and high
quality vehicles by enhancing their relationships with suppliers and establishing a direct link
with production process (Shepherd and Patzelt 2017). Ensuring that organization receives high
quality components parts and innovative vehicles, Holden strives to maintain relationship within
suppliers.
The quality management standard is applicable to car manufacturer such as Holden.
Adoption of such standard has helped organization in enhancing and improving the performance
of quality system resulting in cost reduction by elimination of redundant requirements. Strategy
of managing quality at Holden intends to develop fundamental quality system that would assist
in preventing defect, making continuous improvement and reducing waste and variations in their
supply chain process.
Quality intends to allow precision of designs and helps in solving particular problems at
different level of organizations. A quality tool has been embraced by organization for continuous
improvement and concurrent engineering that helps in improving overall performance of
organization. Holden employs following techniques as quality control techniques and they are as
follows:
Implementing statistical process control in production process of organization would help
in improving efficiency. It is essential on part of organization to ascertain the extent to which the
products are meeting the requirements that are pre-established. This requires comparison of
customer voice and voice of process.
Some of quantifiable aspects that help in reflecting the critical factors are key
performance indicators. Product design is another tool that is employed by organization while
dealing with managing quality as it helps in building quality into products.
Critical aspect of maintaining quality into design of products is that it would meet the
expectations of customer and provide them with satisfaction. Quality function deployment is a
tool used by organization that leads to translation of customer voice into specific technical
requirements. This also assists in enhancing communications between various functions such as
operations, marketing and engineering. While designing any products of Holden, several
variables are involved and in this case, quality function deployment enables viewing the

6
OPERATIONS MANAGEMENT
relationship among them. For instance, it can be considered how customer safety requirements
are affected by changes in materials used in manufacturing of cars. The concept of quality is
further extended to suppliers of company with the implementation of total quality management
as a tool for managing quality. Total quality management principle intends to satisfy external
customer needs with good quality products and services by encouraging participation amongst
managers and shop flow workers (Krajewski et al. 2013).
Developing House of quality:
Six major components are involved in House of quality and this comprise of planning
matrix, technical requirements, a technical correlation matrix and interrelationship matrix. The
initial steps in developing house of quality involve clarifying, determining and specifying the
needs of customers.
Clarifying customer needs
It is essential on part of organization to translate customer wishes into tangible values that
would lead to engineering specifications. Some of the features includes parts, processes,
functions, tasks, quality character and reliability.
Customer needs specification
Determining specifications of customers, organizations are required to translate them into
particulate specifications.
Technical requirements:
In this step of quality, functional development is the identification of customer wants and
the steps taken to achieve wants. Necessary requirements are fulfilled by designing products.
This can be related to steering system sought by customers. Requirement of steering system of
SUV customers are transformed into major technical measures of steering system. It can be seen
that material quality is considered to be of the highest priority to the customers and for most of
the customers, requirements are associated with texture, color, attractive designs, scratch proof
and tear resistance. Dimension and structure of rigid of SUV cars are considered to be another
priority.
OPERATIONS MANAGEMENT
relationship among them. For instance, it can be considered how customer safety requirements
are affected by changes in materials used in manufacturing of cars. The concept of quality is
further extended to suppliers of company with the implementation of total quality management
as a tool for managing quality. Total quality management principle intends to satisfy external
customer needs with good quality products and services by encouraging participation amongst
managers and shop flow workers (Krajewski et al. 2013).
Developing House of quality:
Six major components are involved in House of quality and this comprise of planning
matrix, technical requirements, a technical correlation matrix and interrelationship matrix. The
initial steps in developing house of quality involve clarifying, determining and specifying the
needs of customers.
Clarifying customer needs
It is essential on part of organization to translate customer wishes into tangible values that
would lead to engineering specifications. Some of the features includes parts, processes,
functions, tasks, quality character and reliability.
Customer needs specification
Determining specifications of customers, organizations are required to translate them into
particulate specifications.
Technical requirements:
In this step of quality, functional development is the identification of customer wants and
the steps taken to achieve wants. Necessary requirements are fulfilled by designing products.
This can be related to steering system sought by customers. Requirement of steering system of
SUV customers are transformed into major technical measures of steering system. It can be seen
that material quality is considered to be of the highest priority to the customers and for most of
the customers, requirements are associated with texture, color, attractive designs, scratch proof
and tear resistance. Dimension and structure of rigid of SUV cars are considered to be another
priority.
Paraphrase This Document
Need a fresh take? Get an instant paraphrase of this document with our AI Paraphraser
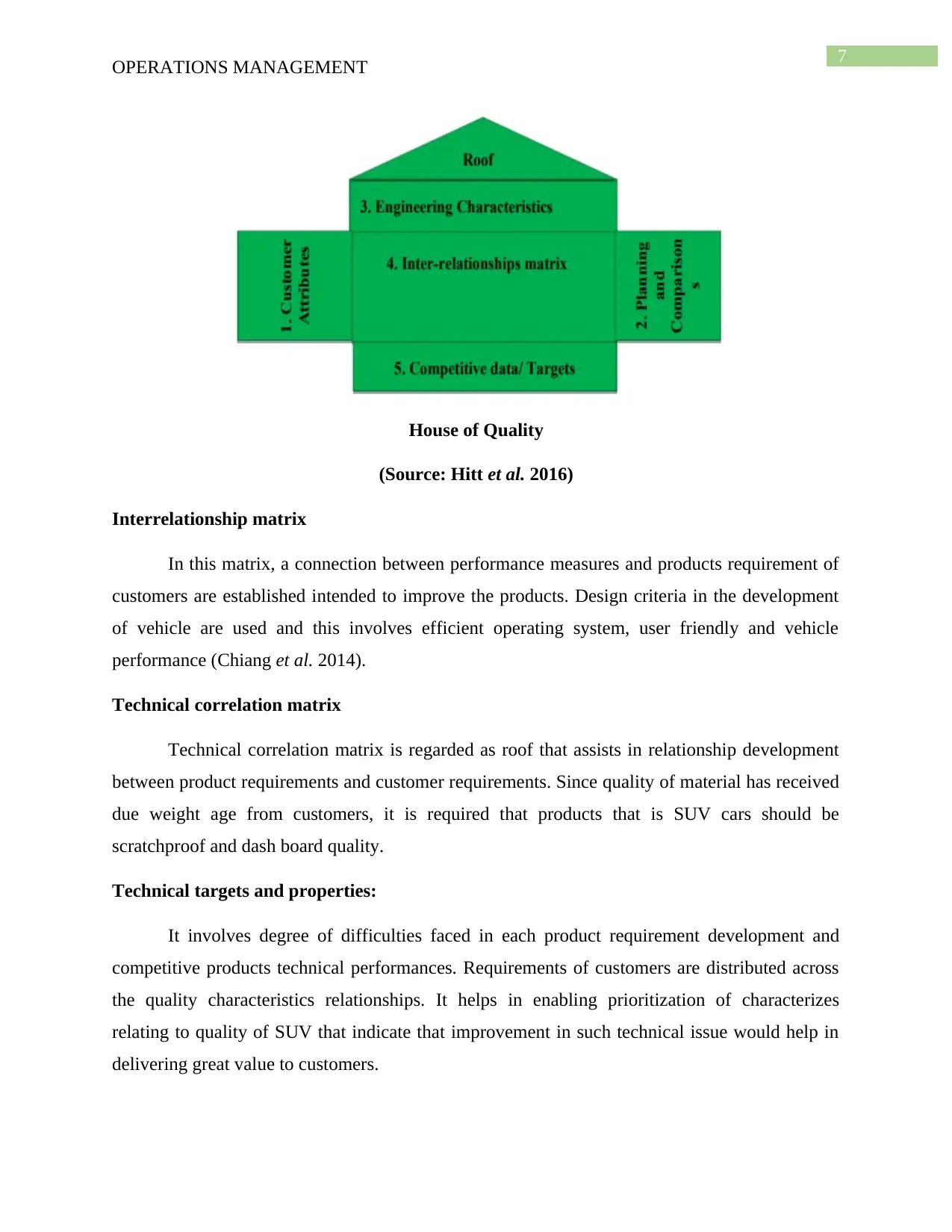
7
OPERATIONS MANAGEMENT
House of Quality
(Source: Hitt et al. 2016)
Interrelationship matrix
In this matrix, a connection between performance measures and products requirement of
customers are established intended to improve the products. Design criteria in the development
of vehicle are used and this involves efficient operating system, user friendly and vehicle
performance (Chiang et al. 2014).
Technical correlation matrix
Technical correlation matrix is regarded as roof that assists in relationship development
between product requirements and customer requirements. Since quality of material has received
due weight age from customers, it is required that products that is SUV cars should be
scratchproof and dash board quality.
Technical targets and properties:
It involves degree of difficulties faced in each product requirement development and
competitive products technical performances. Requirements of customers are distributed across
the quality characteristics relationships. It helps in enabling prioritization of characterizes
relating to quality of SUV that indicate that improvement in such technical issue would help in
delivering great value to customers.
OPERATIONS MANAGEMENT
House of Quality
(Source: Hitt et al. 2016)
Interrelationship matrix
In this matrix, a connection between performance measures and products requirement of
customers are established intended to improve the products. Design criteria in the development
of vehicle are used and this involves efficient operating system, user friendly and vehicle
performance (Chiang et al. 2014).
Technical correlation matrix
Technical correlation matrix is regarded as roof that assists in relationship development
between product requirements and customer requirements. Since quality of material has received
due weight age from customers, it is required that products that is SUV cars should be
scratchproof and dash board quality.
Technical targets and properties:
It involves degree of difficulties faced in each product requirement development and
competitive products technical performances. Requirements of customers are distributed across
the quality characteristics relationships. It helps in enabling prioritization of characterizes
relating to quality of SUV that indicate that improvement in such technical issue would help in
delivering great value to customers.
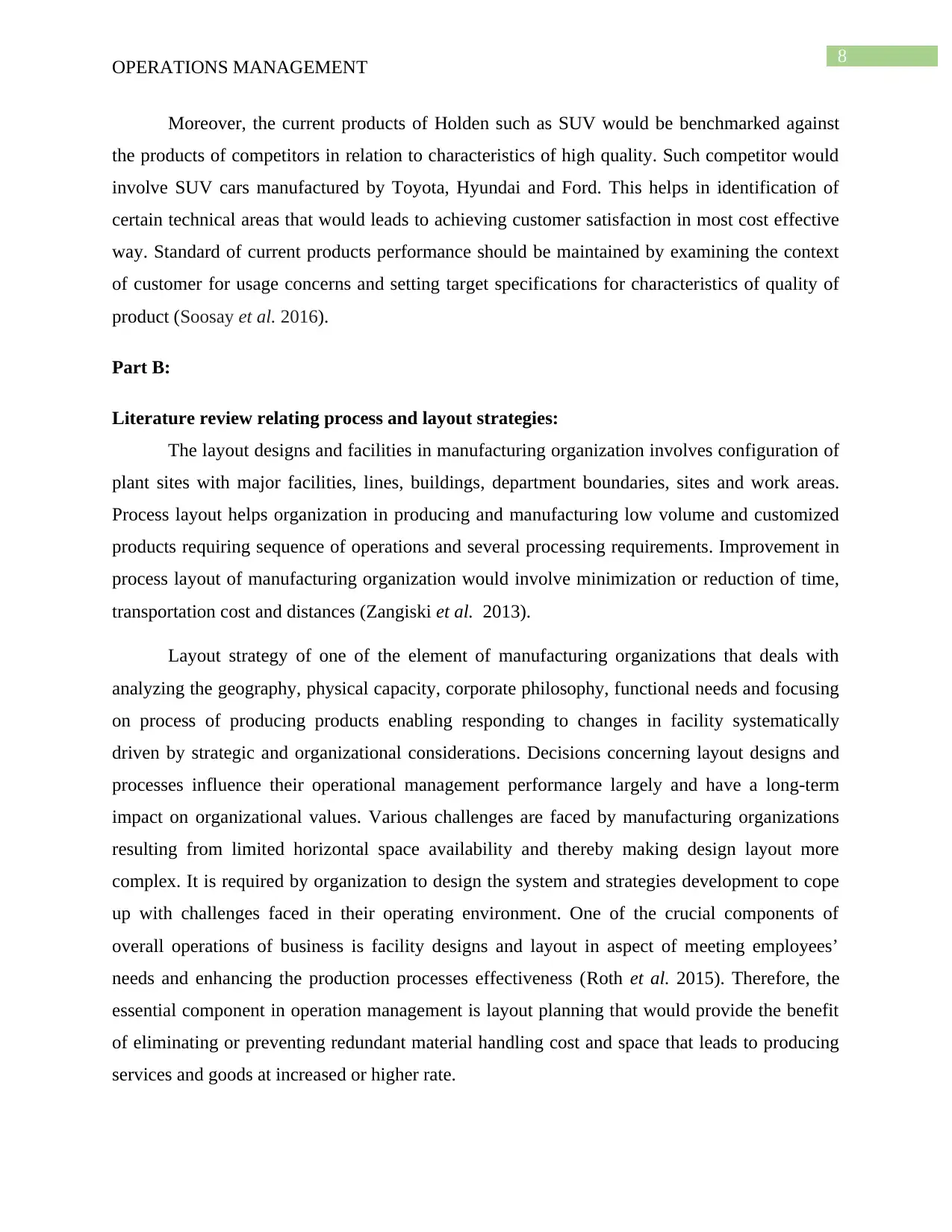
8
OPERATIONS MANAGEMENT
Moreover, the current products of Holden such as SUV would be benchmarked against
the products of competitors in relation to characteristics of high quality. Such competitor would
involve SUV cars manufactured by Toyota, Hyundai and Ford. This helps in identification of
certain technical areas that would leads to achieving customer satisfaction in most cost effective
way. Standard of current products performance should be maintained by examining the context
of customer for usage concerns and setting target specifications for characteristics of quality of
product (Soosay et al. 2016).
Part B:
Literature review relating process and layout strategies:
The layout designs and facilities in manufacturing organization involves configuration of
plant sites with major facilities, lines, buildings, department boundaries, sites and work areas.
Process layout helps organization in producing and manufacturing low volume and customized
products requiring sequence of operations and several processing requirements. Improvement in
process layout of manufacturing organization would involve minimization or reduction of time,
transportation cost and distances (Zangiski et al. 2013).
Layout strategy of one of the element of manufacturing organizations that deals with
analyzing the geography, physical capacity, corporate philosophy, functional needs and focusing
on process of producing products enabling responding to changes in facility systematically
driven by strategic and organizational considerations. Decisions concerning layout designs and
processes influence their operational management performance largely and have a long-term
impact on organizational values. Various challenges are faced by manufacturing organizations
resulting from limited horizontal space availability and thereby making design layout more
complex. It is required by organization to design the system and strategies development to cope
up with challenges faced in their operating environment. One of the crucial components of
overall operations of business is facility designs and layout in aspect of meeting employees’
needs and enhancing the production processes effectiveness (Roth et al. 2015). Therefore, the
essential component in operation management is layout planning that would provide the benefit
of eliminating or preventing redundant material handling cost and space that leads to producing
services and goods at increased or higher rate.
OPERATIONS MANAGEMENT
Moreover, the current products of Holden such as SUV would be benchmarked against
the products of competitors in relation to characteristics of high quality. Such competitor would
involve SUV cars manufactured by Toyota, Hyundai and Ford. This helps in identification of
certain technical areas that would leads to achieving customer satisfaction in most cost effective
way. Standard of current products performance should be maintained by examining the context
of customer for usage concerns and setting target specifications for characteristics of quality of
product (Soosay et al. 2016).
Part B:
Literature review relating process and layout strategies:
The layout designs and facilities in manufacturing organization involves configuration of
plant sites with major facilities, lines, buildings, department boundaries, sites and work areas.
Process layout helps organization in producing and manufacturing low volume and customized
products requiring sequence of operations and several processing requirements. Improvement in
process layout of manufacturing organization would involve minimization or reduction of time,
transportation cost and distances (Zangiski et al. 2013).
Layout strategy of one of the element of manufacturing organizations that deals with
analyzing the geography, physical capacity, corporate philosophy, functional needs and focusing
on process of producing products enabling responding to changes in facility systematically
driven by strategic and organizational considerations. Decisions concerning layout designs and
processes influence their operational management performance largely and have a long-term
impact on organizational values. Various challenges are faced by manufacturing organizations
resulting from limited horizontal space availability and thereby making design layout more
complex. It is required by organization to design the system and strategies development to cope
up with challenges faced in their operating environment. One of the crucial components of
overall operations of business is facility designs and layout in aspect of meeting employees’
needs and enhancing the production processes effectiveness (Roth et al. 2015). Therefore, the
essential component in operation management is layout planning that would provide the benefit
of eliminating or preventing redundant material handling cost and space that leads to producing
services and goods at increased or higher rate.
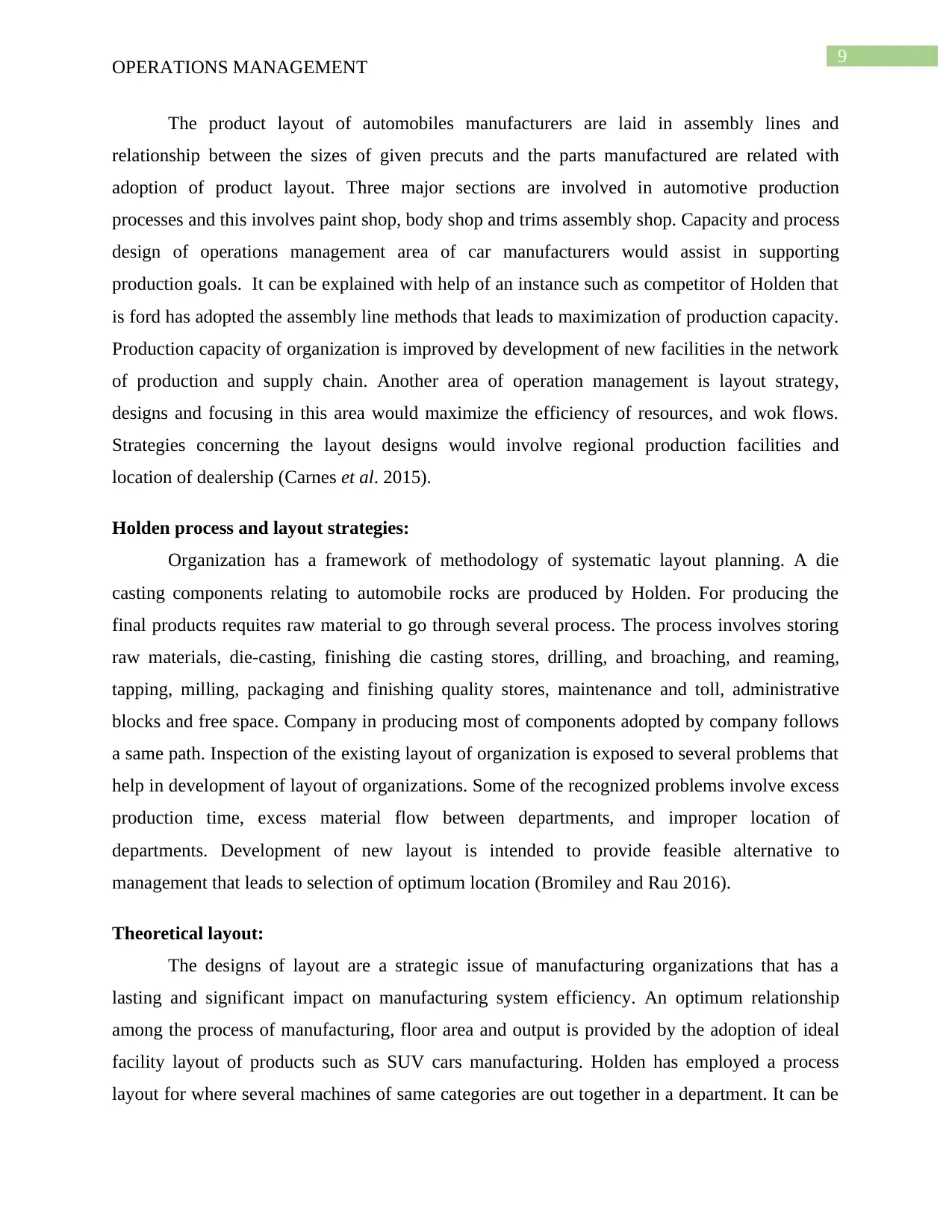
9
OPERATIONS MANAGEMENT
The product layout of automobiles manufacturers are laid in assembly lines and
relationship between the sizes of given precuts and the parts manufactured are related with
adoption of product layout. Three major sections are involved in automotive production
processes and this involves paint shop, body shop and trims assembly shop. Capacity and process
design of operations management area of car manufacturers would assist in supporting
production goals. It can be explained with help of an instance such as competitor of Holden that
is ford has adopted the assembly line methods that leads to maximization of production capacity.
Production capacity of organization is improved by development of new facilities in the network
of production and supply chain. Another area of operation management is layout strategy,
designs and focusing in this area would maximize the efficiency of resources, and wok flows.
Strategies concerning the layout designs would involve regional production facilities and
location of dealership (Carnes et al. 2015).
Holden process and layout strategies:
Organization has a framework of methodology of systematic layout planning. A die
casting components relating to automobile rocks are produced by Holden. For producing the
final products requites raw material to go through several process. The process involves storing
raw materials, die-casting, finishing die casting stores, drilling, and broaching, and reaming,
tapping, milling, packaging and finishing quality stores, maintenance and toll, administrative
blocks and free space. Company in producing most of components adopted by company follows
a same path. Inspection of the existing layout of organization is exposed to several problems that
help in development of layout of organizations. Some of the recognized problems involve excess
production time, excess material flow between departments, and improper location of
departments. Development of new layout is intended to provide feasible alternative to
management that leads to selection of optimum location (Bromiley and Rau 2016).
Theoretical layout:
The designs of layout are a strategic issue of manufacturing organizations that has a
lasting and significant impact on manufacturing system efficiency. An optimum relationship
among the process of manufacturing, floor area and output is provided by the adoption of ideal
facility layout of products such as SUV cars manufacturing. Holden has employed a process
layout for where several machines of same categories are out together in a department. It can be
OPERATIONS MANAGEMENT
The product layout of automobiles manufacturers are laid in assembly lines and
relationship between the sizes of given precuts and the parts manufactured are related with
adoption of product layout. Three major sections are involved in automotive production
processes and this involves paint shop, body shop and trims assembly shop. Capacity and process
design of operations management area of car manufacturers would assist in supporting
production goals. It can be explained with help of an instance such as competitor of Holden that
is ford has adopted the assembly line methods that leads to maximization of production capacity.
Production capacity of organization is improved by development of new facilities in the network
of production and supply chain. Another area of operation management is layout strategy,
designs and focusing in this area would maximize the efficiency of resources, and wok flows.
Strategies concerning the layout designs would involve regional production facilities and
location of dealership (Carnes et al. 2015).
Holden process and layout strategies:
Organization has a framework of methodology of systematic layout planning. A die
casting components relating to automobile rocks are produced by Holden. For producing the
final products requites raw material to go through several process. The process involves storing
raw materials, die-casting, finishing die casting stores, drilling, and broaching, and reaming,
tapping, milling, packaging and finishing quality stores, maintenance and toll, administrative
blocks and free space. Company in producing most of components adopted by company follows
a same path. Inspection of the existing layout of organization is exposed to several problems that
help in development of layout of organizations. Some of the recognized problems involve excess
production time, excess material flow between departments, and improper location of
departments. Development of new layout is intended to provide feasible alternative to
management that leads to selection of optimum location (Bromiley and Rau 2016).
Theoretical layout:
The designs of layout are a strategic issue of manufacturing organizations that has a
lasting and significant impact on manufacturing system efficiency. An optimum relationship
among the process of manufacturing, floor area and output is provided by the adoption of ideal
facility layout of products such as SUV cars manufacturing. Holden has employed a process
layout for where several machines of same categories are out together in a department. It can be
Secure Best Marks with AI Grader
Need help grading? Try our AI Grader for instant feedback on your assignments.
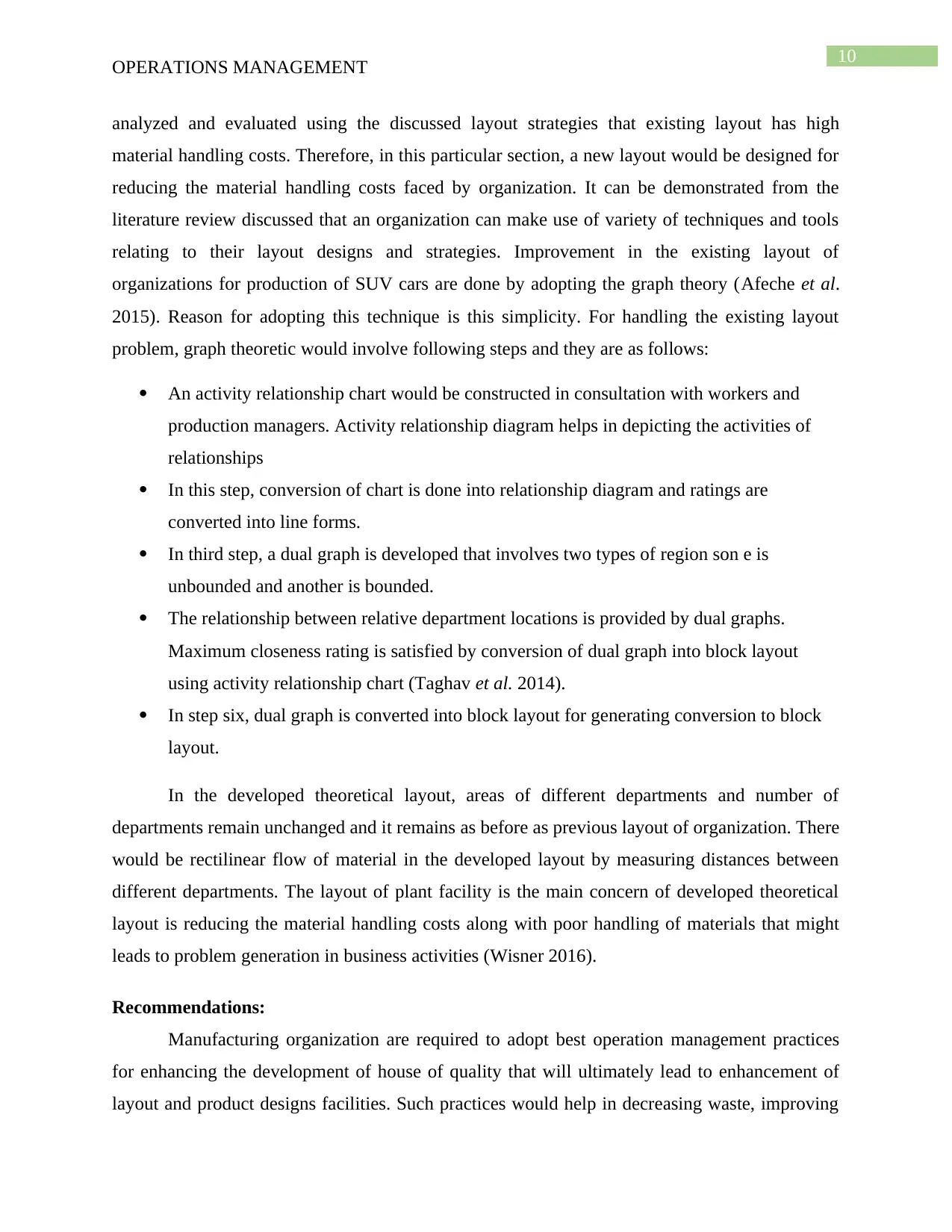
10
OPERATIONS MANAGEMENT
analyzed and evaluated using the discussed layout strategies that existing layout has high
material handling costs. Therefore, in this particular section, a new layout would be designed for
reducing the material handling costs faced by organization. It can be demonstrated from the
literature review discussed that an organization can make use of variety of techniques and tools
relating to their layout designs and strategies. Improvement in the existing layout of
organizations for production of SUV cars are done by adopting the graph theory (Afeche et al.
2015). Reason for adopting this technique is this simplicity. For handling the existing layout
problem, graph theoretic would involve following steps and they are as follows:
An activity relationship chart would be constructed in consultation with workers and
production managers. Activity relationship diagram helps in depicting the activities of
relationships
In this step, conversion of chart is done into relationship diagram and ratings are
converted into line forms.
In third step, a dual graph is developed that involves two types of region son e is
unbounded and another is bounded.
The relationship between relative department locations is provided by dual graphs.
Maximum closeness rating is satisfied by conversion of dual graph into block layout
using activity relationship chart (Taghav et al. 2014).
In step six, dual graph is converted into block layout for generating conversion to block
layout.
In the developed theoretical layout, areas of different departments and number of
departments remain unchanged and it remains as before as previous layout of organization. There
would be rectilinear flow of material in the developed layout by measuring distances between
different departments. The layout of plant facility is the main concern of developed theoretical
layout is reducing the material handling costs along with poor handling of materials that might
leads to problem generation in business activities (Wisner 2016).
Recommendations:
Manufacturing organization are required to adopt best operation management practices
for enhancing the development of house of quality that will ultimately lead to enhancement of
layout and product designs facilities. Such practices would help in decreasing waste, improving
OPERATIONS MANAGEMENT
analyzed and evaluated using the discussed layout strategies that existing layout has high
material handling costs. Therefore, in this particular section, a new layout would be designed for
reducing the material handling costs faced by organization. It can be demonstrated from the
literature review discussed that an organization can make use of variety of techniques and tools
relating to their layout designs and strategies. Improvement in the existing layout of
organizations for production of SUV cars are done by adopting the graph theory (Afeche et al.
2015). Reason for adopting this technique is this simplicity. For handling the existing layout
problem, graph theoretic would involve following steps and they are as follows:
An activity relationship chart would be constructed in consultation with workers and
production managers. Activity relationship diagram helps in depicting the activities of
relationships
In this step, conversion of chart is done into relationship diagram and ratings are
converted into line forms.
In third step, a dual graph is developed that involves two types of region son e is
unbounded and another is bounded.
The relationship between relative department locations is provided by dual graphs.
Maximum closeness rating is satisfied by conversion of dual graph into block layout
using activity relationship chart (Taghav et al. 2014).
In step six, dual graph is converted into block layout for generating conversion to block
layout.
In the developed theoretical layout, areas of different departments and number of
departments remain unchanged and it remains as before as previous layout of organization. There
would be rectilinear flow of material in the developed layout by measuring distances between
different departments. The layout of plant facility is the main concern of developed theoretical
layout is reducing the material handling costs along with poor handling of materials that might
leads to problem generation in business activities (Wisner 2016).
Recommendations:
Manufacturing organization are required to adopt best operation management practices
for enhancing the development of house of quality that will ultimately lead to enhancement of
layout and product designs facilities. Such practices would help in decreasing waste, improving
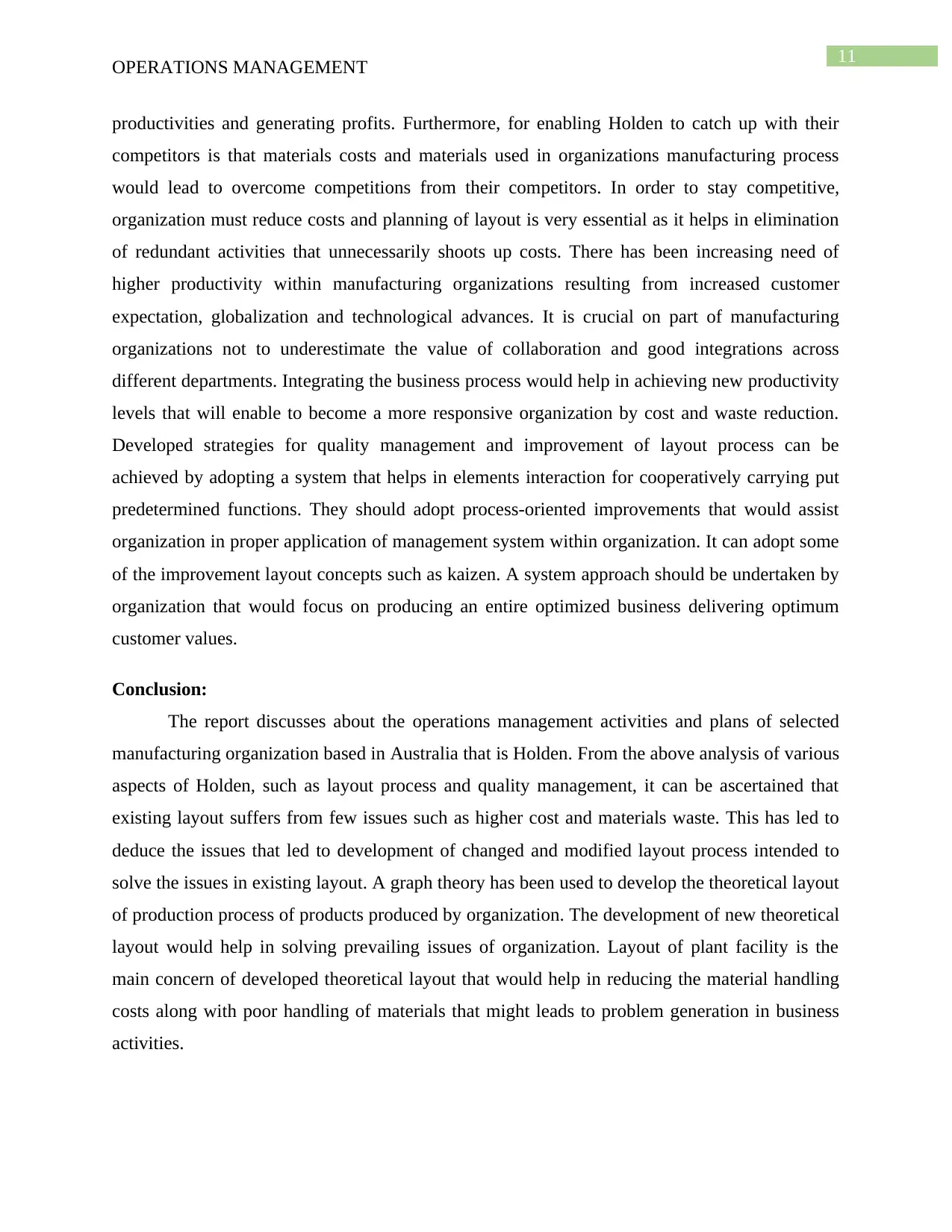
11
OPERATIONS MANAGEMENT
productivities and generating profits. Furthermore, for enabling Holden to catch up with their
competitors is that materials costs and materials used in organizations manufacturing process
would lead to overcome competitions from their competitors. In order to stay competitive,
organization must reduce costs and planning of layout is very essential as it helps in elimination
of redundant activities that unnecessarily shoots up costs. There has been increasing need of
higher productivity within manufacturing organizations resulting from increased customer
expectation, globalization and technological advances. It is crucial on part of manufacturing
organizations not to underestimate the value of collaboration and good integrations across
different departments. Integrating the business process would help in achieving new productivity
levels that will enable to become a more responsive organization by cost and waste reduction.
Developed strategies for quality management and improvement of layout process can be
achieved by adopting a system that helps in elements interaction for cooperatively carrying put
predetermined functions. They should adopt process-oriented improvements that would assist
organization in proper application of management system within organization. It can adopt some
of the improvement layout concepts such as kaizen. A system approach should be undertaken by
organization that would focus on producing an entire optimized business delivering optimum
customer values.
Conclusion:
The report discusses about the operations management activities and plans of selected
manufacturing organization based in Australia that is Holden. From the above analysis of various
aspects of Holden, such as layout process and quality management, it can be ascertained that
existing layout suffers from few issues such as higher cost and materials waste. This has led to
deduce the issues that led to development of changed and modified layout process intended to
solve the issues in existing layout. A graph theory has been used to develop the theoretical layout
of production process of products produced by organization. The development of new theoretical
layout would help in solving prevailing issues of organization. Layout of plant facility is the
main concern of developed theoretical layout that would help in reducing the material handling
costs along with poor handling of materials that might leads to problem generation in business
activities.
OPERATIONS MANAGEMENT
productivities and generating profits. Furthermore, for enabling Holden to catch up with their
competitors is that materials costs and materials used in organizations manufacturing process
would lead to overcome competitions from their competitors. In order to stay competitive,
organization must reduce costs and planning of layout is very essential as it helps in elimination
of redundant activities that unnecessarily shoots up costs. There has been increasing need of
higher productivity within manufacturing organizations resulting from increased customer
expectation, globalization and technological advances. It is crucial on part of manufacturing
organizations not to underestimate the value of collaboration and good integrations across
different departments. Integrating the business process would help in achieving new productivity
levels that will enable to become a more responsive organization by cost and waste reduction.
Developed strategies for quality management and improvement of layout process can be
achieved by adopting a system that helps in elements interaction for cooperatively carrying put
predetermined functions. They should adopt process-oriented improvements that would assist
organization in proper application of management system within organization. It can adopt some
of the improvement layout concepts such as kaizen. A system approach should be undertaken by
organization that would focus on producing an entire optimized business delivering optimum
customer values.
Conclusion:
The report discusses about the operations management activities and plans of selected
manufacturing organization based in Australia that is Holden. From the above analysis of various
aspects of Holden, such as layout process and quality management, it can be ascertained that
existing layout suffers from few issues such as higher cost and materials waste. This has led to
deduce the issues that led to development of changed and modified layout process intended to
solve the issues in existing layout. A graph theory has been used to develop the theoretical layout
of production process of products produced by organization. The development of new theoretical
layout would help in solving prevailing issues of organization. Layout of plant facility is the
main concern of developed theoretical layout that would help in reducing the material handling
costs along with poor handling of materials that might leads to problem generation in business
activities.

12
OPERATIONS MANAGEMENT
OPERATIONS MANAGEMENT
Paraphrase This Document
Need a fresh take? Get an instant paraphrase of this document with our AI Paraphraser
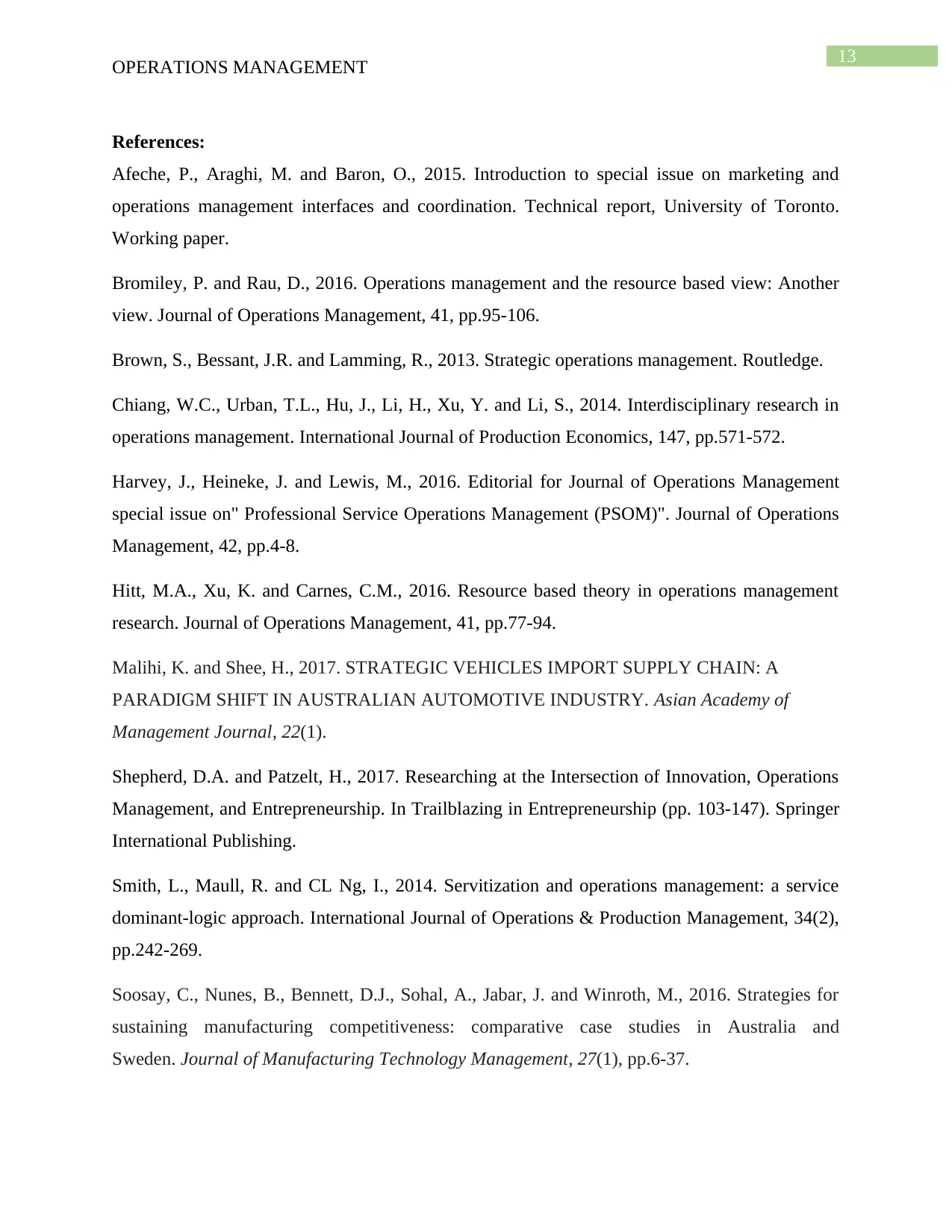
13
OPERATIONS MANAGEMENT
References:
Afeche, P., Araghi, M. and Baron, O., 2015. Introduction to special issue on marketing and
operations management interfaces and coordination. Technical report, University of Toronto.
Working paper.
Bromiley, P. and Rau, D., 2016. Operations management and the resource based view: Another
view. Journal of Operations Management, 41, pp.95-106.
Brown, S., Bessant, J.R. and Lamming, R., 2013. Strategic operations management. Routledge.
Chiang, W.C., Urban, T.L., Hu, J., Li, H., Xu, Y. and Li, S., 2014. Interdisciplinary research in
operations management. International Journal of Production Economics, 147, pp.571-572.
Harvey, J., Heineke, J. and Lewis, M., 2016. Editorial for Journal of Operations Management
special issue on" Professional Service Operations Management (PSOM)". Journal of Operations
Management, 42, pp.4-8.
Hitt, M.A., Xu, K. and Carnes, C.M., 2016. Resource based theory in operations management
research. Journal of Operations Management, 41, pp.77-94.
Malihi, K. and Shee, H., 2017. STRATEGIC VEHICLES IMPORT SUPPLY CHAIN: A
PARADIGM SHIFT IN AUSTRALIAN AUTOMOTIVE INDUSTRY. Asian Academy of
Management Journal, 22(1).
Shepherd, D.A. and Patzelt, H., 2017. Researching at the Intersection of Innovation, Operations
Management, and Entrepreneurship. In Trailblazing in Entrepreneurship (pp. 103-147). Springer
International Publishing.
Smith, L., Maull, R. and CL Ng, I., 2014. Servitization and operations management: a service
dominant-logic approach. International Journal of Operations & Production Management, 34(2),
pp.242-269.
Soosay, C., Nunes, B., Bennett, D.J., Sohal, A., Jabar, J. and Winroth, M., 2016. Strategies for
sustaining manufacturing competitiveness: comparative case studies in Australia and
Sweden. Journal of Manufacturing Technology Management, 27(1), pp.6-37.
OPERATIONS MANAGEMENT
References:
Afeche, P., Araghi, M. and Baron, O., 2015. Introduction to special issue on marketing and
operations management interfaces and coordination. Technical report, University of Toronto.
Working paper.
Bromiley, P. and Rau, D., 2016. Operations management and the resource based view: Another
view. Journal of Operations Management, 41, pp.95-106.
Brown, S., Bessant, J.R. and Lamming, R., 2013. Strategic operations management. Routledge.
Chiang, W.C., Urban, T.L., Hu, J., Li, H., Xu, Y. and Li, S., 2014. Interdisciplinary research in
operations management. International Journal of Production Economics, 147, pp.571-572.
Harvey, J., Heineke, J. and Lewis, M., 2016. Editorial for Journal of Operations Management
special issue on" Professional Service Operations Management (PSOM)". Journal of Operations
Management, 42, pp.4-8.
Hitt, M.A., Xu, K. and Carnes, C.M., 2016. Resource based theory in operations management
research. Journal of Operations Management, 41, pp.77-94.
Malihi, K. and Shee, H., 2017. STRATEGIC VEHICLES IMPORT SUPPLY CHAIN: A
PARADIGM SHIFT IN AUSTRALIAN AUTOMOTIVE INDUSTRY. Asian Academy of
Management Journal, 22(1).
Shepherd, D.A. and Patzelt, H., 2017. Researching at the Intersection of Innovation, Operations
Management, and Entrepreneurship. In Trailblazing in Entrepreneurship (pp. 103-147). Springer
International Publishing.
Smith, L., Maull, R. and CL Ng, I., 2014. Servitization and operations management: a service
dominant-logic approach. International Journal of Operations & Production Management, 34(2),
pp.242-269.
Soosay, C., Nunes, B., Bennett, D.J., Sohal, A., Jabar, J. and Winroth, M., 2016. Strategies for
sustaining manufacturing competitiveness: comparative case studies in Australia and
Sweden. Journal of Manufacturing Technology Management, 27(1), pp.6-37.
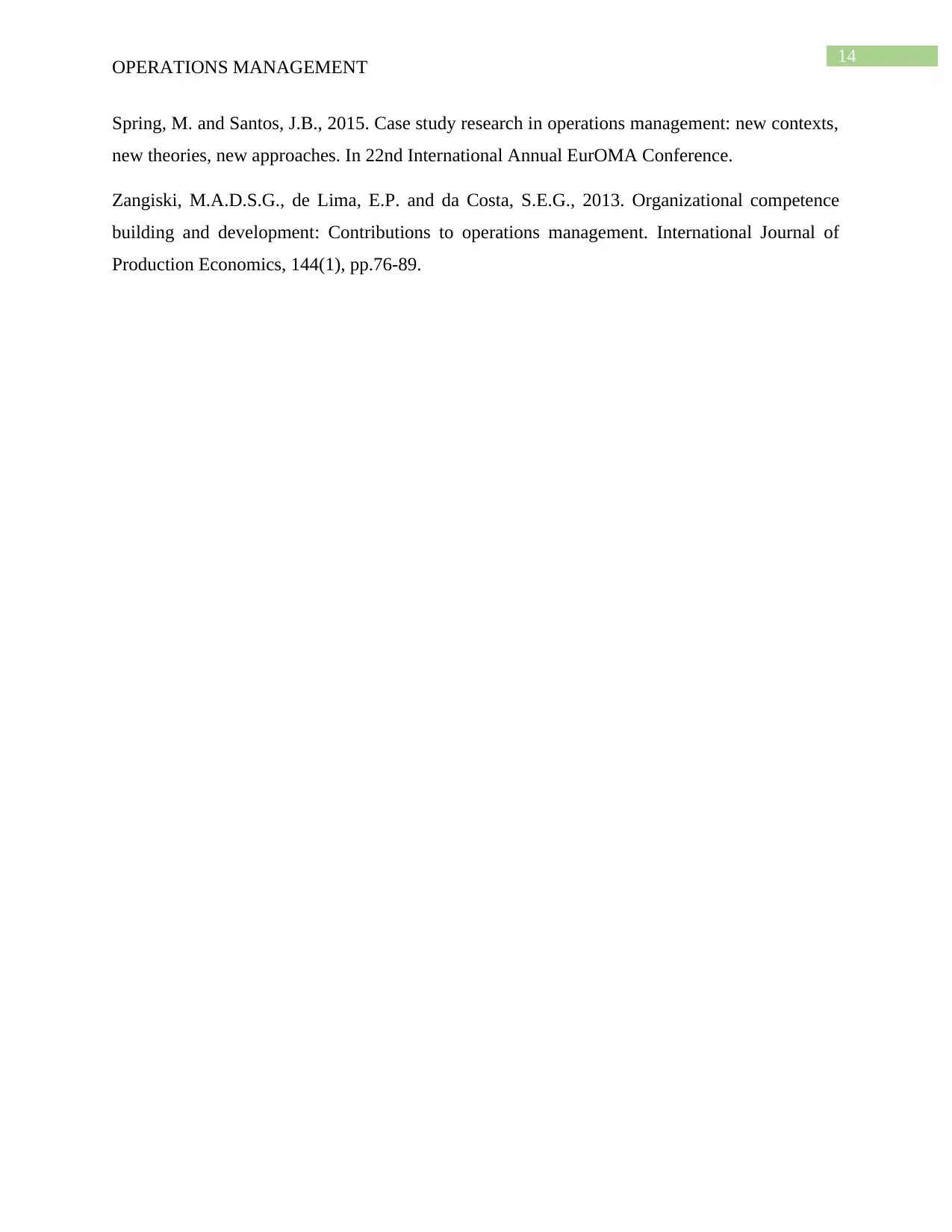
14
OPERATIONS MANAGEMENT
Spring, M. and Santos, J.B., 2015. Case study research in operations management: new contexts,
new theories, new approaches. In 22nd International Annual EurOMA Conference.
Zangiski, M.A.D.S.G., de Lima, E.P. and da Costa, S.E.G., 2013. Organizational competence
building and development: Contributions to operations management. International Journal of
Production Economics, 144(1), pp.76-89.
OPERATIONS MANAGEMENT
Spring, M. and Santos, J.B., 2015. Case study research in operations management: new contexts,
new theories, new approaches. In 22nd International Annual EurOMA Conference.
Zangiski, M.A.D.S.G., de Lima, E.P. and da Costa, S.E.G., 2013. Organizational competence
building and development: Contributions to operations management. International Journal of
Production Economics, 144(1), pp.76-89.
1 out of 15
Related Documents
![[object Object]](/_next/image/?url=%2F_next%2Fstatic%2Fmedia%2Flogo.6d15ce61.png&w=640&q=75)
Your All-in-One AI-Powered Toolkit for Academic Success.
+13062052269
info@desklib.com
Available 24*7 on WhatsApp / Email
Unlock your academic potential
© 2024 | Zucol Services PVT LTD | All rights reserved.