Understanding Operations and Logistics in McDonald's
VerifiedAdded on  2023/01/07
|10
|3191
|84
AI Summary
This essay explores the operations and logistics management in McDonald's, focusing on two areas: new product development and managing quality. It discusses the challenges faced by the company and provides recommendations for improvement. The essay also considers the triple bottom line framework and its impact on McDonald's operations. The conclusion highlights the importance of strategic leadership and diversification strategy for enhancing operations and logistics.
Contribute Materials
Your contribution can guide someone’s learning journey. Share your
documents today.
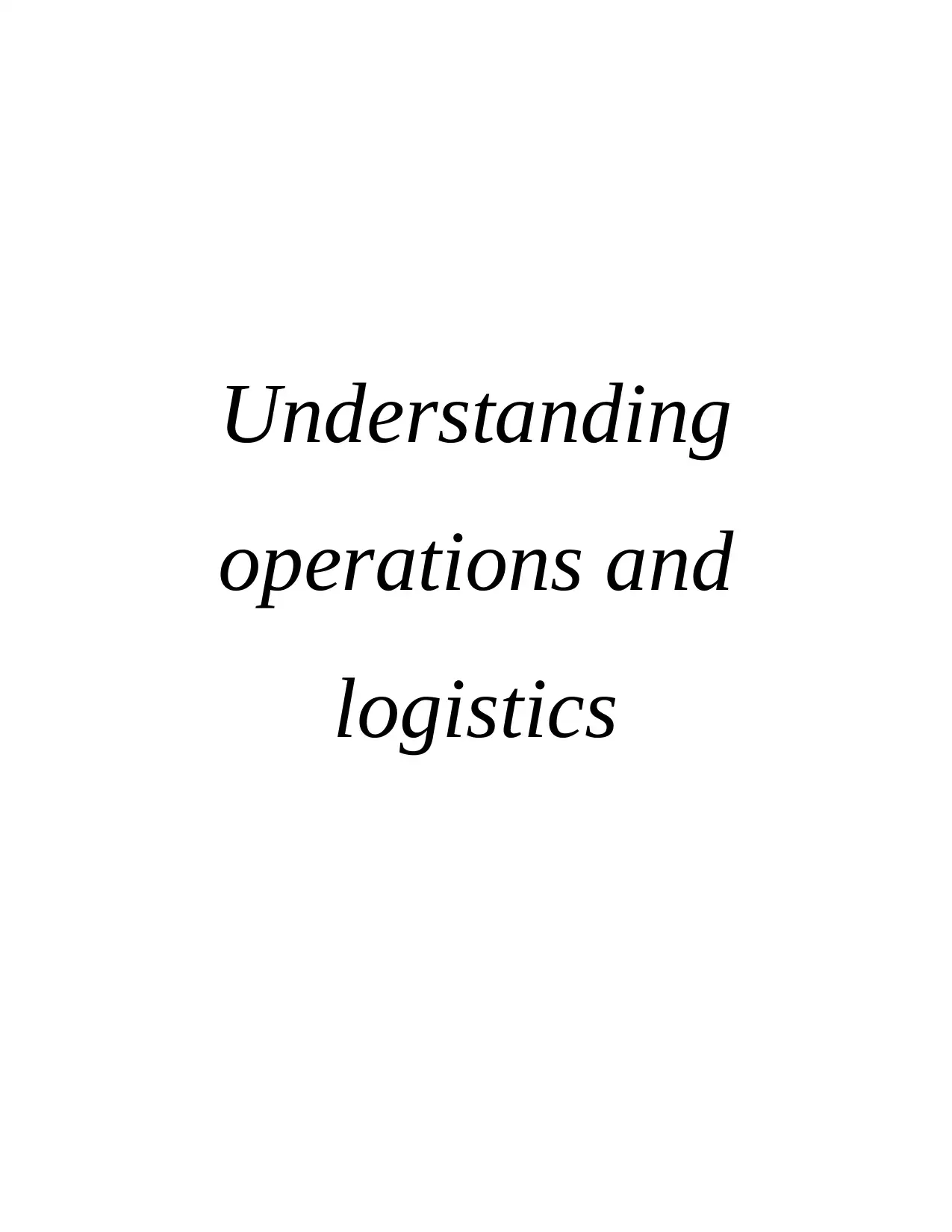
Understanding
operations and
logistics
operations and
logistics
Secure Best Marks with AI Grader
Need help grading? Try our AI Grader for instant feedback on your assignments.
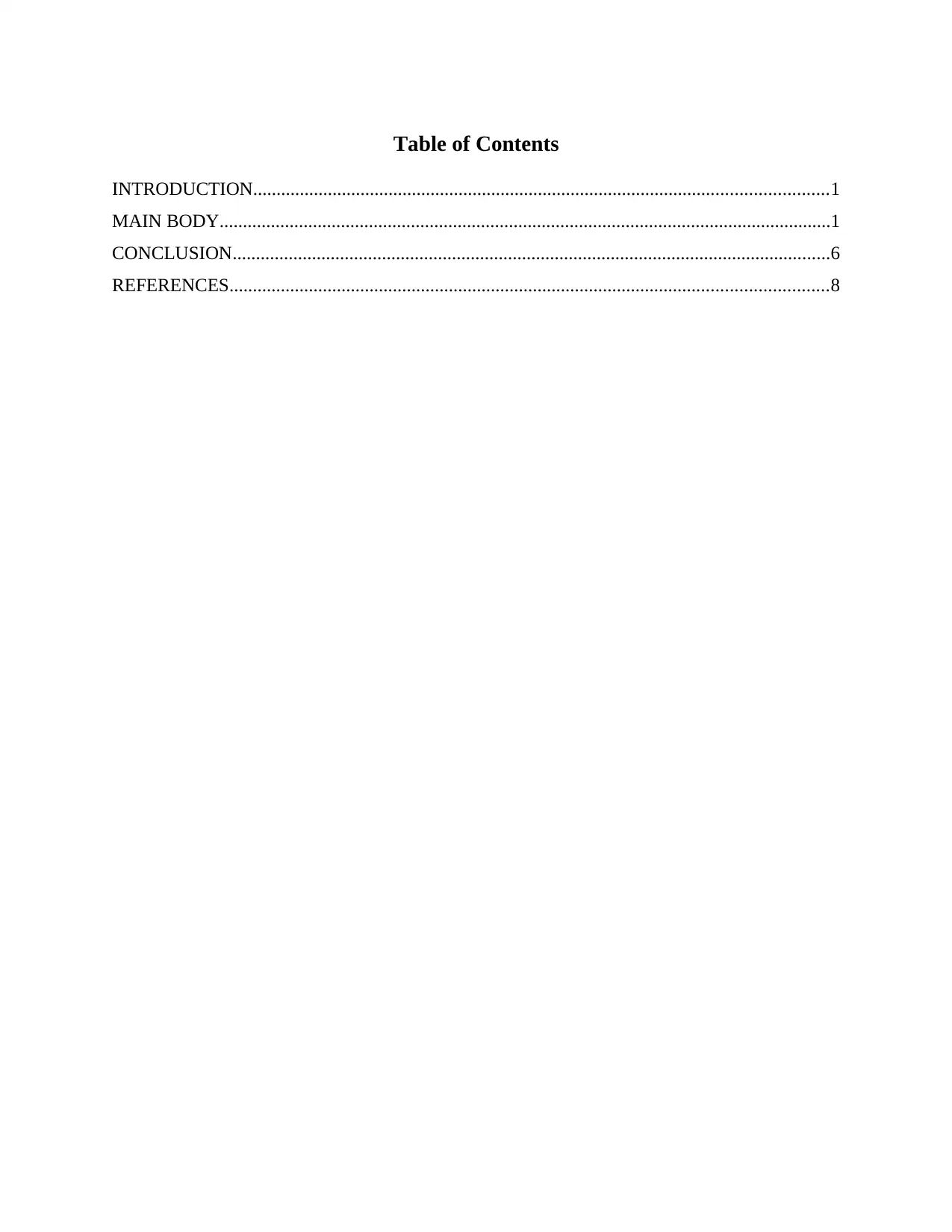
Table of Contents
INTRODUCTION...........................................................................................................................1
MAIN BODY...................................................................................................................................1
CONCLUSION................................................................................................................................6
REFERENCES................................................................................................................................8
INTRODUCTION...........................................................................................................................1
MAIN BODY...................................................................................................................................1
CONCLUSION................................................................................................................................6
REFERENCES................................................................................................................................8
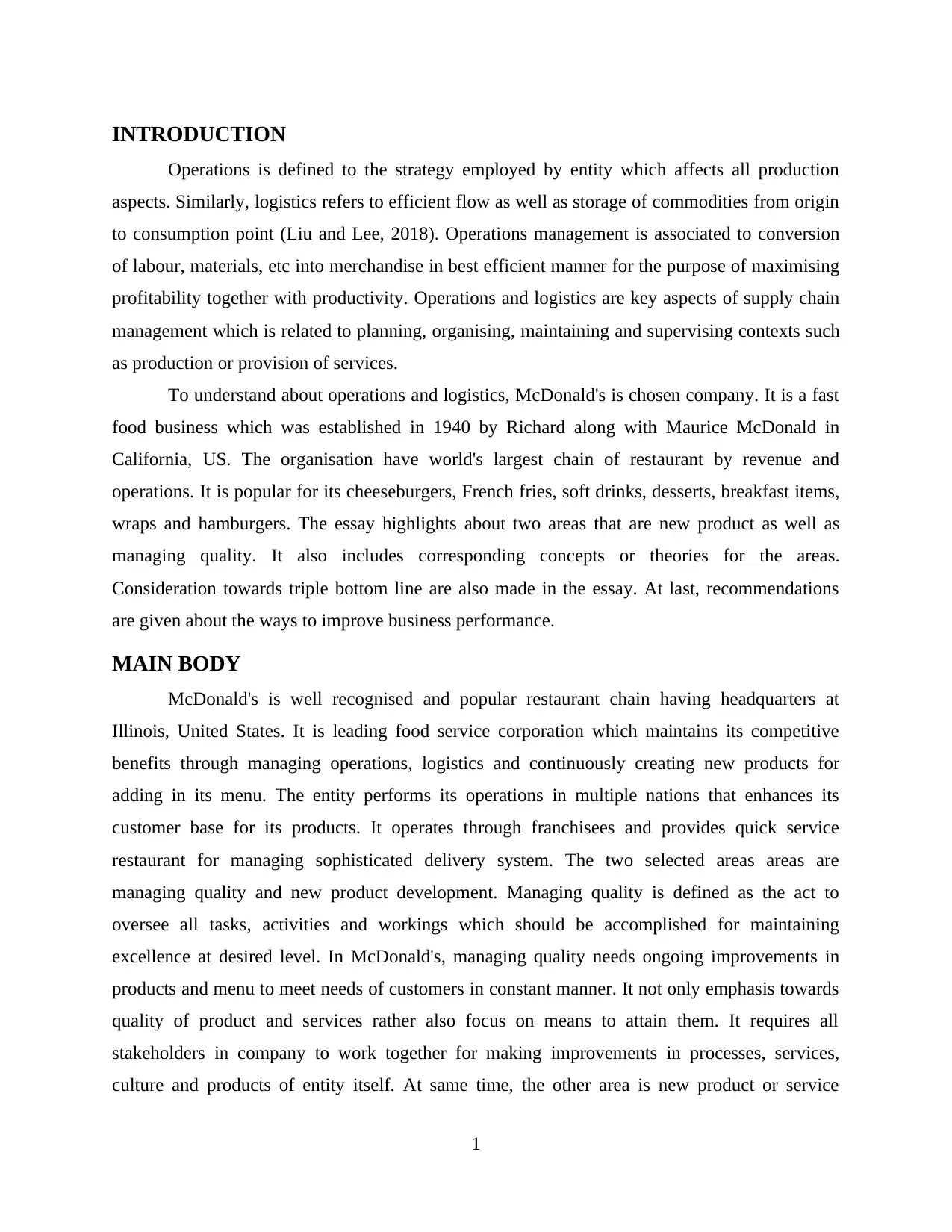
INTRODUCTION
Operations is defined to the strategy employed by entity which affects all production
aspects. Similarly, logistics refers to efficient flow as well as storage of commodities from origin
to consumption point (Liu and Lee, 2018). Operations management is associated to conversion
of labour, materials, etc into merchandise in best efficient manner for the purpose of maximising
profitability together with productivity. Operations and logistics are key aspects of supply chain
management which is related to planning, organising, maintaining and supervising contexts such
as production or provision of services.
To understand about operations and logistics, McDonald's is chosen company. It is a fast
food business which was established in 1940 by Richard along with Maurice McDonald in
California, US. The organisation have world's largest chain of restaurant by revenue and
operations. It is popular for its cheeseburgers, French fries, soft drinks, desserts, breakfast items,
wraps and hamburgers. The essay highlights about two areas that are new product as well as
managing quality. It also includes corresponding concepts or theories for the areas.
Consideration towards triple bottom line are also made in the essay. At last, recommendations
are given about the ways to improve business performance.
MAIN BODY
McDonald's is well recognised and popular restaurant chain having headquarters at
Illinois, United States. It is leading food service corporation which maintains its competitive
benefits through managing operations, logistics and continuously creating new products for
adding in its menu. The entity performs its operations in multiple nations that enhances its
customer base for its products. It operates through franchisees and provides quick service
restaurant for managing sophisticated delivery system. The two selected areas areas are
managing quality and new product development. Managing quality is defined as the act to
oversee all tasks, activities and workings which should be accomplished for maintaining
excellence at desired level. In McDonald's, managing quality needs ongoing improvements in
products and menu to meet needs of customers in constant manner. It not only emphasis towards
quality of product and services rather also focus on means to attain them. It requires all
stakeholders in company to work together for making improvements in processes, services,
culture and products of entity itself. At same time, the other area is new product or service
1
Operations is defined to the strategy employed by entity which affects all production
aspects. Similarly, logistics refers to efficient flow as well as storage of commodities from origin
to consumption point (Liu and Lee, 2018). Operations management is associated to conversion
of labour, materials, etc into merchandise in best efficient manner for the purpose of maximising
profitability together with productivity. Operations and logistics are key aspects of supply chain
management which is related to planning, organising, maintaining and supervising contexts such
as production or provision of services.
To understand about operations and logistics, McDonald's is chosen company. It is a fast
food business which was established in 1940 by Richard along with Maurice McDonald in
California, US. The organisation have world's largest chain of restaurant by revenue and
operations. It is popular for its cheeseburgers, French fries, soft drinks, desserts, breakfast items,
wraps and hamburgers. The essay highlights about two areas that are new product as well as
managing quality. It also includes corresponding concepts or theories for the areas.
Consideration towards triple bottom line are also made in the essay. At last, recommendations
are given about the ways to improve business performance.
MAIN BODY
McDonald's is well recognised and popular restaurant chain having headquarters at
Illinois, United States. It is leading food service corporation which maintains its competitive
benefits through managing operations, logistics and continuously creating new products for
adding in its menu. The entity performs its operations in multiple nations that enhances its
customer base for its products. It operates through franchisees and provides quick service
restaurant for managing sophisticated delivery system. The two selected areas areas are
managing quality and new product development. Managing quality is defined as the act to
oversee all tasks, activities and workings which should be accomplished for maintaining
excellence at desired level. In McDonald's, managing quality needs ongoing improvements in
products and menu to meet needs of customers in constant manner. It not only emphasis towards
quality of product and services rather also focus on means to attain them. It requires all
stakeholders in company to work together for making improvements in processes, services,
culture and products of entity itself. At same time, the other area is new product or service
1
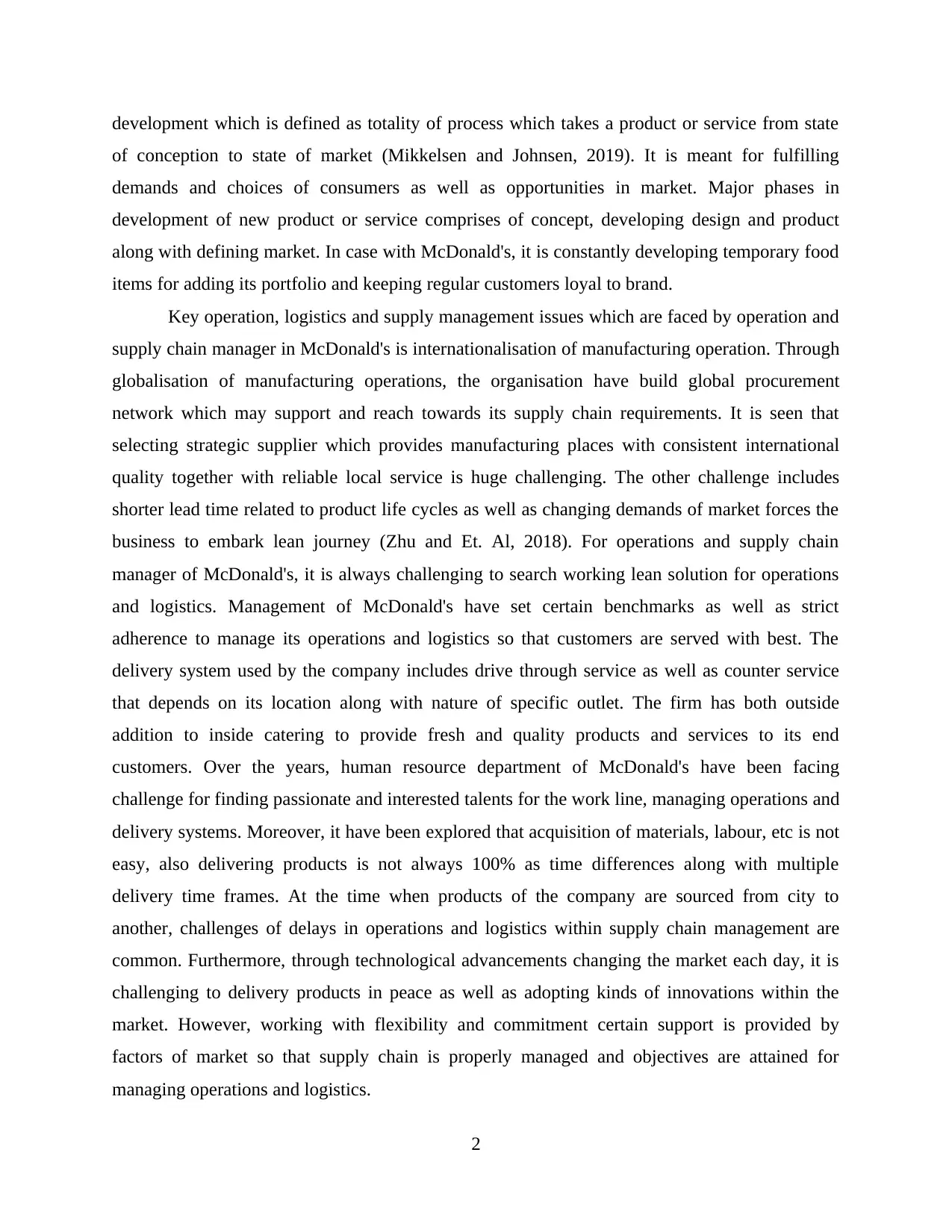
development which is defined as totality of process which takes a product or service from state
of conception to state of market (Mikkelsen and Johnsen, 2019). It is meant for fulfilling
demands and choices of consumers as well as opportunities in market. Major phases in
development of new product or service comprises of concept, developing design and product
along with defining market. In case with McDonald's, it is constantly developing temporary food
items for adding its portfolio and keeping regular customers loyal to brand.
Key operation, logistics and supply management issues which are faced by operation and
supply chain manager in McDonald's is internationalisation of manufacturing operation. Through
globalisation of manufacturing operations, the organisation have build global procurement
network which may support and reach towards its supply chain requirements. It is seen that
selecting strategic supplier which provides manufacturing places with consistent international
quality together with reliable local service is huge challenging. The other challenge includes
shorter lead time related to product life cycles as well as changing demands of market forces the
business to embark lean journey (Zhu and Et. Al, 2018). For operations and supply chain
manager of McDonald's, it is always challenging to search working lean solution for operations
and logistics. Management of McDonald's have set certain benchmarks as well as strict
adherence to manage its operations and logistics so that customers are served with best. The
delivery system used by the company includes drive through service as well as counter service
that depends on its location along with nature of specific outlet. The firm has both outside
addition to inside catering to provide fresh and quality products and services to its end
customers. Over the years, human resource department of McDonald's have been facing
challenge for finding passionate and interested talents for the work line, managing operations and
delivery systems. Moreover, it have been explored that acquisition of materials, labour, etc is not
easy, also delivering products is not always 100% as time differences along with multiple
delivery time frames. At the time when products of the company are sourced from city to
another, challenges of delays in operations and logistics within supply chain management are
common. Furthermore, through technological advancements changing the market each day, it is
challenging to delivery products in peace as well as adopting kinds of innovations within the
market. However, working with flexibility and commitment certain support is provided by
factors of market so that supply chain is properly managed and objectives are attained for
managing operations and logistics.
2
of conception to state of market (Mikkelsen and Johnsen, 2019). It is meant for fulfilling
demands and choices of consumers as well as opportunities in market. Major phases in
development of new product or service comprises of concept, developing design and product
along with defining market. In case with McDonald's, it is constantly developing temporary food
items for adding its portfolio and keeping regular customers loyal to brand.
Key operation, logistics and supply management issues which are faced by operation and
supply chain manager in McDonald's is internationalisation of manufacturing operation. Through
globalisation of manufacturing operations, the organisation have build global procurement
network which may support and reach towards its supply chain requirements. It is seen that
selecting strategic supplier which provides manufacturing places with consistent international
quality together with reliable local service is huge challenging. The other challenge includes
shorter lead time related to product life cycles as well as changing demands of market forces the
business to embark lean journey (Zhu and Et. Al, 2018). For operations and supply chain
manager of McDonald's, it is always challenging to search working lean solution for operations
and logistics. Management of McDonald's have set certain benchmarks as well as strict
adherence to manage its operations and logistics so that customers are served with best. The
delivery system used by the company includes drive through service as well as counter service
that depends on its location along with nature of specific outlet. The firm has both outside
addition to inside catering to provide fresh and quality products and services to its end
customers. Over the years, human resource department of McDonald's have been facing
challenge for finding passionate and interested talents for the work line, managing operations and
delivery systems. Moreover, it have been explored that acquisition of materials, labour, etc is not
easy, also delivering products is not always 100% as time differences along with multiple
delivery time frames. At the time when products of the company are sourced from city to
another, challenges of delays in operations and logistics within supply chain management are
common. Furthermore, through technological advancements changing the market each day, it is
challenging to delivery products in peace as well as adopting kinds of innovations within the
market. However, working with flexibility and commitment certain support is provided by
factors of market so that supply chain is properly managed and objectives are attained for
managing operations and logistics.
2
Secure Best Marks with AI Grader
Need help grading? Try our AI Grader for instant feedback on your assignments.
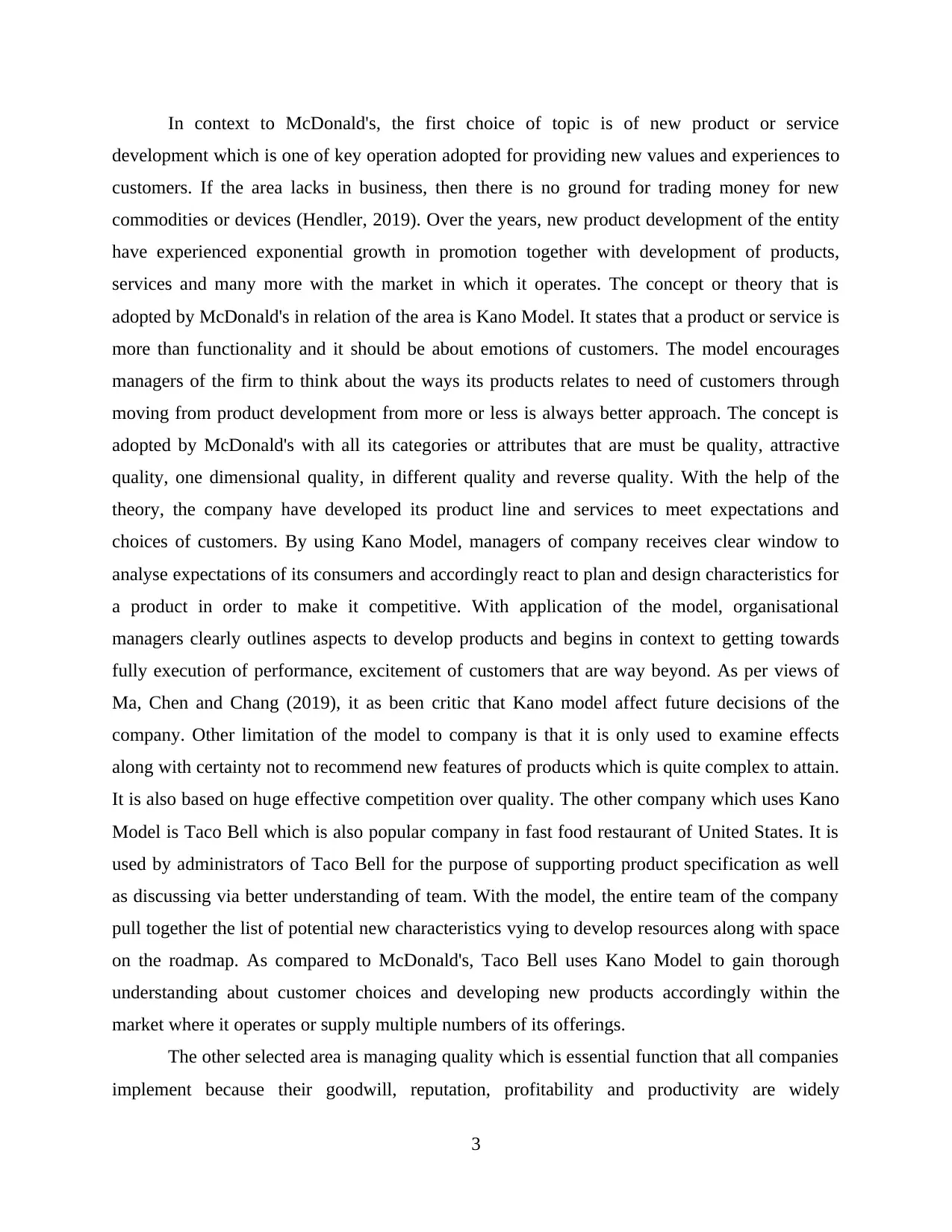
In context to McDonald's, the first choice of topic is of new product or service
development which is one of key operation adopted for providing new values and experiences to
customers. If the area lacks in business, then there is no ground for trading money for new
commodities or devices (Hendler, 2019). Over the years, new product development of the entity
have experienced exponential growth in promotion together with development of products,
services and many more with the market in which it operates. The concept or theory that is
adopted by McDonald's in relation of the area is Kano Model. It states that a product or service is
more than functionality and it should be about emotions of customers. The model encourages
managers of the firm to think about the ways its products relates to need of customers through
moving from product development from more or less is always better approach. The concept is
adopted by McDonald's with all its categories or attributes that are must be quality, attractive
quality, one dimensional quality, in different quality and reverse quality. With the help of the
theory, the company have developed its product line and services to meet expectations and
choices of customers. By using Kano Model, managers of company receives clear window to
analyse expectations of its consumers and accordingly react to plan and design characteristics for
a product in order to make it competitive. With application of the model, organisational
managers clearly outlines aspects to develop products and begins in context to getting towards
fully execution of performance, excitement of customers that are way beyond. As per views of
Ma, Chen and Chang (2019), it as been critic that Kano model affect future decisions of the
company. Other limitation of the model to company is that it is only used to examine effects
along with certainty not to recommend new features of products which is quite complex to attain.
It is also based on huge effective competition over quality. The other company which uses Kano
Model is Taco Bell which is also popular company in fast food restaurant of United States. It is
used by administrators of Taco Bell for the purpose of supporting product specification as well
as discussing via better understanding of team. With the model, the entire team of the company
pull together the list of potential new characteristics vying to develop resources along with space
on the roadmap. As compared to McDonald's, Taco Bell uses Kano Model to gain thorough
understanding about customer choices and developing new products accordingly within the
market where it operates or supply multiple numbers of its offerings.
The other selected area is managing quality which is essential function that all companies
implement because their goodwill, reputation, profitability and productivity are widely
3
development which is one of key operation adopted for providing new values and experiences to
customers. If the area lacks in business, then there is no ground for trading money for new
commodities or devices (Hendler, 2019). Over the years, new product development of the entity
have experienced exponential growth in promotion together with development of products,
services and many more with the market in which it operates. The concept or theory that is
adopted by McDonald's in relation of the area is Kano Model. It states that a product or service is
more than functionality and it should be about emotions of customers. The model encourages
managers of the firm to think about the ways its products relates to need of customers through
moving from product development from more or less is always better approach. The concept is
adopted by McDonald's with all its categories or attributes that are must be quality, attractive
quality, one dimensional quality, in different quality and reverse quality. With the help of the
theory, the company have developed its product line and services to meet expectations and
choices of customers. By using Kano Model, managers of company receives clear window to
analyse expectations of its consumers and accordingly react to plan and design characteristics for
a product in order to make it competitive. With application of the model, organisational
managers clearly outlines aspects to develop products and begins in context to getting towards
fully execution of performance, excitement of customers that are way beyond. As per views of
Ma, Chen and Chang (2019), it as been critic that Kano model affect future decisions of the
company. Other limitation of the model to company is that it is only used to examine effects
along with certainty not to recommend new features of products which is quite complex to attain.
It is also based on huge effective competition over quality. The other company which uses Kano
Model is Taco Bell which is also popular company in fast food restaurant of United States. It is
used by administrators of Taco Bell for the purpose of supporting product specification as well
as discussing via better understanding of team. With the model, the entire team of the company
pull together the list of potential new characteristics vying to develop resources along with space
on the roadmap. As compared to McDonald's, Taco Bell uses Kano Model to gain thorough
understanding about customer choices and developing new products accordingly within the
market where it operates or supply multiple numbers of its offerings.
The other selected area is managing quality which is essential function that all companies
implement because their goodwill, reputation, profitability and productivity are widely
3
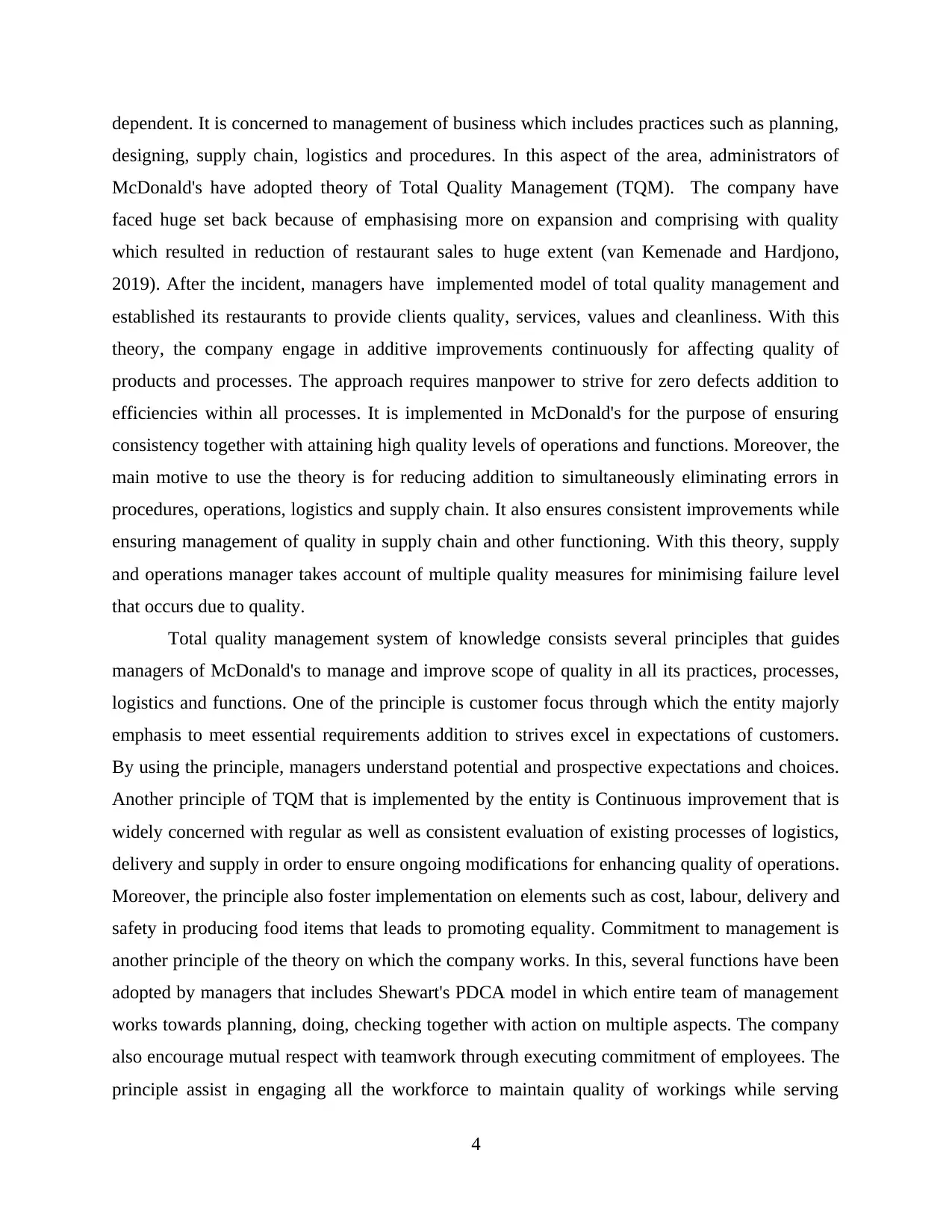
dependent. It is concerned to management of business which includes practices such as planning,
designing, supply chain, logistics and procedures. In this aspect of the area, administrators of
McDonald's have adopted theory of Total Quality Management (TQM). The company have
faced huge set back because of emphasising more on expansion and comprising with quality
which resulted in reduction of restaurant sales to huge extent (van Kemenade and Hardjono,
2019). After the incident, managers have implemented model of total quality management and
established its restaurants to provide clients quality, services, values and cleanliness. With this
theory, the company engage in additive improvements continuously for affecting quality of
products and processes. The approach requires manpower to strive for zero defects addition to
efficiencies within all processes. It is implemented in McDonald's for the purpose of ensuring
consistency together with attaining high quality levels of operations and functions. Moreover, the
main motive to use the theory is for reducing addition to simultaneously eliminating errors in
procedures, operations, logistics and supply chain. It also ensures consistent improvements while
ensuring management of quality in supply chain and other functioning. With this theory, supply
and operations manager takes account of multiple quality measures for minimising failure level
that occurs due to quality.
Total quality management system of knowledge consists several principles that guides
managers of McDonald's to manage and improve scope of quality in all its practices, processes,
logistics and functions. One of the principle is customer focus through which the entity majorly
emphasis to meet essential requirements addition to strives excel in expectations of customers.
By using the principle, managers understand potential and prospective expectations and choices.
Another principle of TQM that is implemented by the entity is Continuous improvement that is
widely concerned with regular as well as consistent evaluation of existing processes of logistics,
delivery and supply in order to ensure ongoing modifications for enhancing quality of operations.
Moreover, the principle also foster implementation on elements such as cost, labour, delivery and
safety in producing food items that leads to promoting equality. Commitment to management is
another principle of the theory on which the company works. In this, several functions have been
adopted by managers that includes Shewart's PDCA model in which entire team of management
works towards planning, doing, checking together with action on multiple aspects. The company
also encourage mutual respect with teamwork through executing commitment of employees. The
principle assist in engaging all the workforce to maintain quality of workings while serving
4
designing, supply chain, logistics and procedures. In this aspect of the area, administrators of
McDonald's have adopted theory of Total Quality Management (TQM). The company have
faced huge set back because of emphasising more on expansion and comprising with quality
which resulted in reduction of restaurant sales to huge extent (van Kemenade and Hardjono,
2019). After the incident, managers have implemented model of total quality management and
established its restaurants to provide clients quality, services, values and cleanliness. With this
theory, the company engage in additive improvements continuously for affecting quality of
products and processes. The approach requires manpower to strive for zero defects addition to
efficiencies within all processes. It is implemented in McDonald's for the purpose of ensuring
consistency together with attaining high quality levels of operations and functions. Moreover, the
main motive to use the theory is for reducing addition to simultaneously eliminating errors in
procedures, operations, logistics and supply chain. It also ensures consistent improvements while
ensuring management of quality in supply chain and other functioning. With this theory, supply
and operations manager takes account of multiple quality measures for minimising failure level
that occurs due to quality.
Total quality management system of knowledge consists several principles that guides
managers of McDonald's to manage and improve scope of quality in all its practices, processes,
logistics and functions. One of the principle is customer focus through which the entity majorly
emphasis to meet essential requirements addition to strives excel in expectations of customers.
By using the principle, managers understand potential and prospective expectations and choices.
Another principle of TQM that is implemented by the entity is Continuous improvement that is
widely concerned with regular as well as consistent evaluation of existing processes of logistics,
delivery and supply in order to ensure ongoing modifications for enhancing quality of operations.
Moreover, the principle also foster implementation on elements such as cost, labour, delivery and
safety in producing food items that leads to promoting equality. Commitment to management is
another principle of the theory on which the company works. In this, several functions have been
adopted by managers that includes Shewart's PDCA model in which entire team of management
works towards planning, doing, checking together with action on multiple aspects. The company
also encourage mutual respect with teamwork through executing commitment of employees. The
principle assist in engaging all the workforce to maintain quality of workings while serving
4
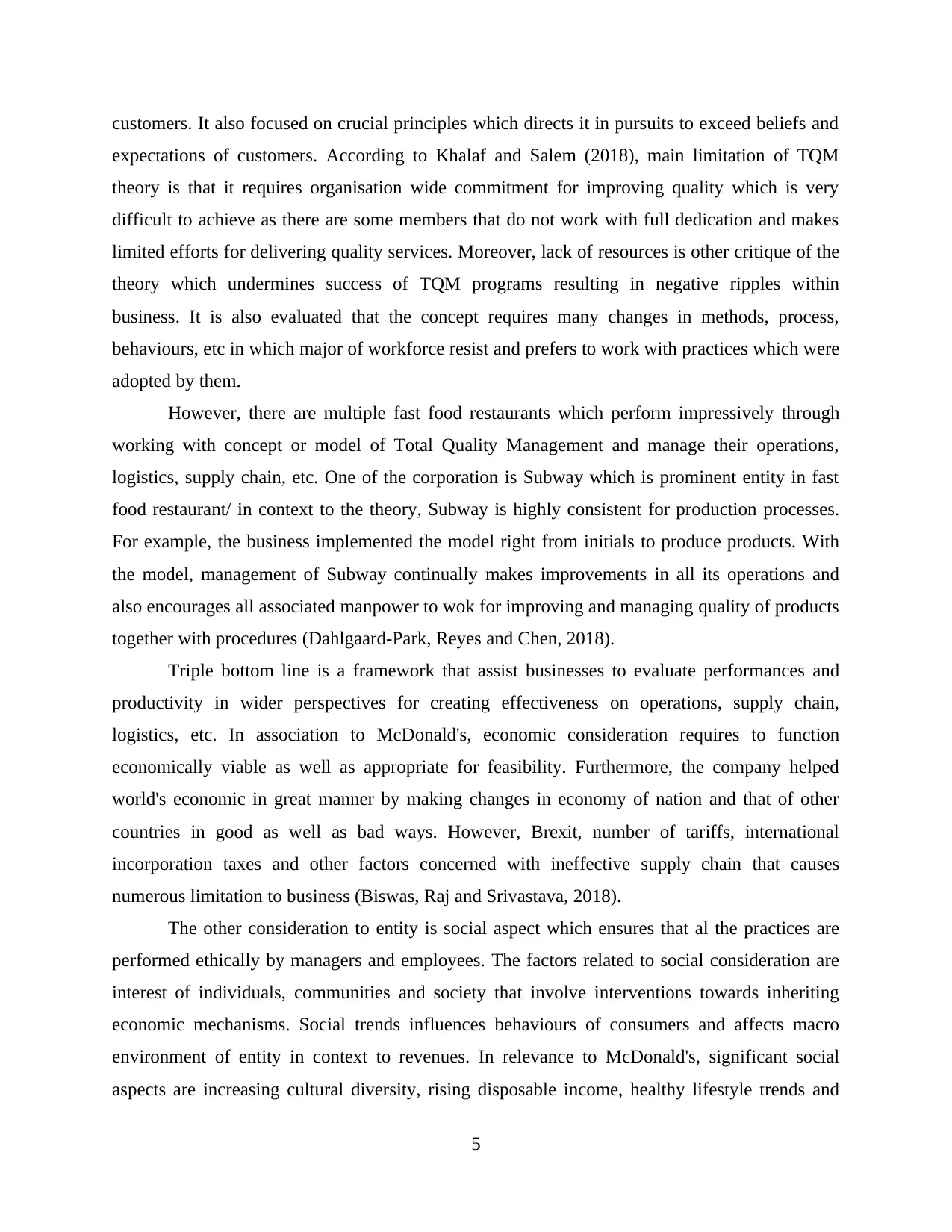
customers. It also focused on crucial principles which directs it in pursuits to exceed beliefs and
expectations of customers. According to Khalaf and Salem (2018), main limitation of TQM
theory is that it requires organisation wide commitment for improving quality which is very
difficult to achieve as there are some members that do not work with full dedication and makes
limited efforts for delivering quality services. Moreover, lack of resources is other critique of the
theory which undermines success of TQM programs resulting in negative ripples within
business. It is also evaluated that the concept requires many changes in methods, process,
behaviours, etc in which major of workforce resist and prefers to work with practices which were
adopted by them.
However, there are multiple fast food restaurants which perform impressively through
working with concept or model of Total Quality Management and manage their operations,
logistics, supply chain, etc. One of the corporation is Subway which is prominent entity in fast
food restaurant/ in context to the theory, Subway is highly consistent for production processes.
For example, the business implemented the model right from initials to produce products. With
the model, management of Subway continually makes improvements in all its operations and
also encourages all associated manpower to wok for improving and managing quality of products
together with procedures (Dahlgaard-Park, Reyes and Chen, 2018).
Triple bottom line is a framework that assist businesses to evaluate performances and
productivity in wider perspectives for creating effectiveness on operations, supply chain,
logistics, etc. In association to McDonald's, economic consideration requires to function
economically viable as well as appropriate for feasibility. Furthermore, the company helped
world's economic in great manner by making changes in economy of nation and that of other
countries in good as well as bad ways. However, Brexit, number of tariffs, international
incorporation taxes and other factors concerned with ineffective supply chain that causes
numerous limitation to business (Biswas, Raj and Srivastava, 2018).
The other consideration to entity is social aspect which ensures that al the practices are
performed ethically by managers and employees. The factors related to social consideration are
interest of individuals, communities and society that involve interventions towards inheriting
economic mechanisms. Social trends influences behaviours of consumers and affects macro
environment of entity in context to revenues. In relevance to McDonald's, significant social
aspects are increasing cultural diversity, rising disposable income, healthy lifestyle trends and
5
expectations of customers. According to Khalaf and Salem (2018), main limitation of TQM
theory is that it requires organisation wide commitment for improving quality which is very
difficult to achieve as there are some members that do not work with full dedication and makes
limited efforts for delivering quality services. Moreover, lack of resources is other critique of the
theory which undermines success of TQM programs resulting in negative ripples within
business. It is also evaluated that the concept requires many changes in methods, process,
behaviours, etc in which major of workforce resist and prefers to work with practices which were
adopted by them.
However, there are multiple fast food restaurants which perform impressively through
working with concept or model of Total Quality Management and manage their operations,
logistics, supply chain, etc. One of the corporation is Subway which is prominent entity in fast
food restaurant/ in context to the theory, Subway is highly consistent for production processes.
For example, the business implemented the model right from initials to produce products. With
the model, management of Subway continually makes improvements in all its operations and
also encourages all associated manpower to wok for improving and managing quality of products
together with procedures (Dahlgaard-Park, Reyes and Chen, 2018).
Triple bottom line is a framework that assist businesses to evaluate performances and
productivity in wider perspectives for creating effectiveness on operations, supply chain,
logistics, etc. In association to McDonald's, economic consideration requires to function
economically viable as well as appropriate for feasibility. Furthermore, the company helped
world's economic in great manner by making changes in economy of nation and that of other
countries in good as well as bad ways. However, Brexit, number of tariffs, international
incorporation taxes and other factors concerned with ineffective supply chain that causes
numerous limitation to business (Biswas, Raj and Srivastava, 2018).
The other consideration to entity is social aspect which ensures that al the practices are
performed ethically by managers and employees. The factors related to social consideration are
interest of individuals, communities and society that involve interventions towards inheriting
economic mechanisms. Social trends influences behaviours of consumers and affects macro
environment of entity in context to revenues. In relevance to McDonald's, significant social
aspects are increasing cultural diversity, rising disposable income, healthy lifestyle trends and
5
Paraphrase This Document
Need a fresh take? Get an instant paraphrase of this document with our AI Paraphraser
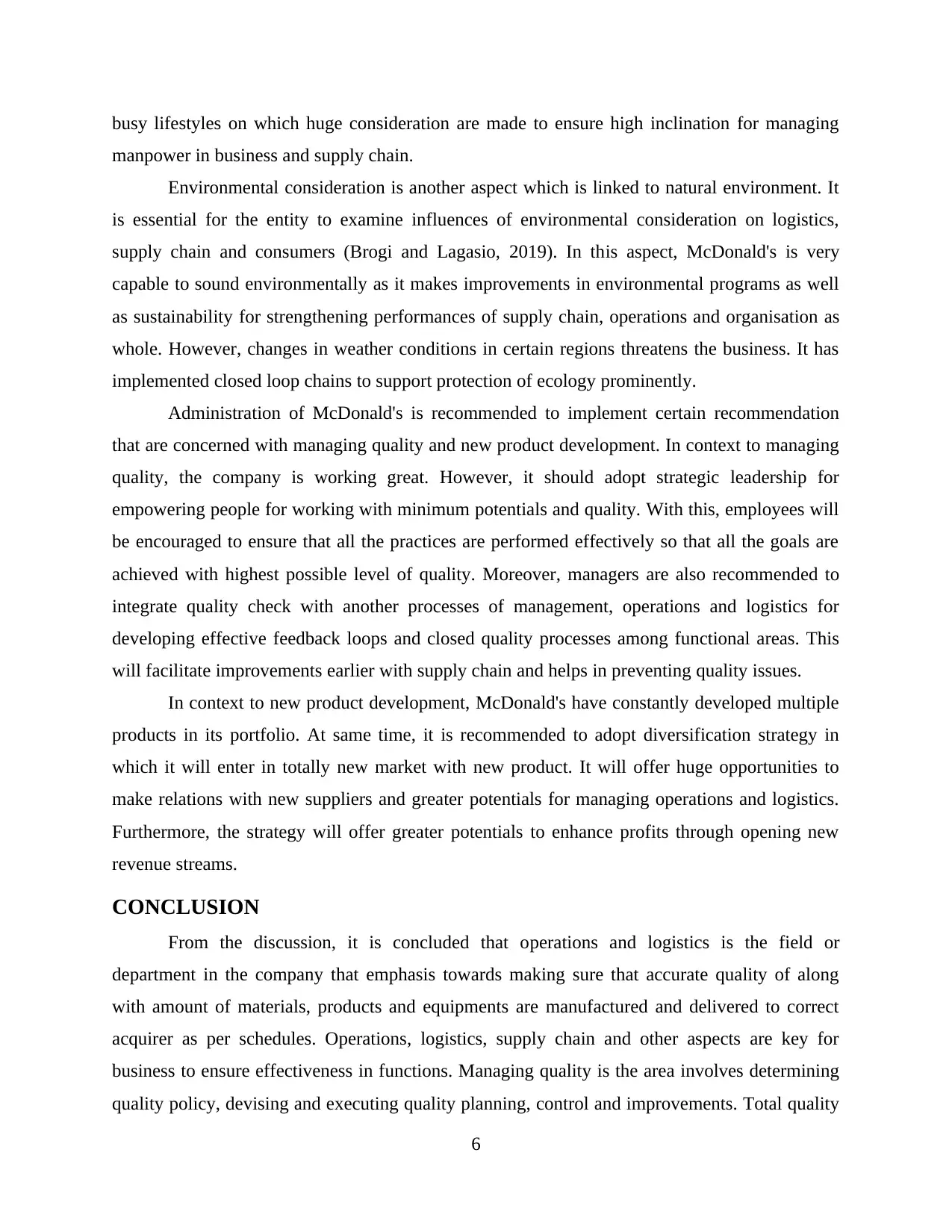
busy lifestyles on which huge consideration are made to ensure high inclination for managing
manpower in business and supply chain.
Environmental consideration is another aspect which is linked to natural environment. It
is essential for the entity to examine influences of environmental consideration on logistics,
supply chain and consumers (Brogi and Lagasio, 2019). In this aspect, McDonald's is very
capable to sound environmentally as it makes improvements in environmental programs as well
as sustainability for strengthening performances of supply chain, operations and organisation as
whole. However, changes in weather conditions in certain regions threatens the business. It has
implemented closed loop chains to support protection of ecology prominently.
Administration of McDonald's is recommended to implement certain recommendation
that are concerned with managing quality and new product development. In context to managing
quality, the company is working great. However, it should adopt strategic leadership for
empowering people for working with minimum potentials and quality. With this, employees will
be encouraged to ensure that all the practices are performed effectively so that all the goals are
achieved with highest possible level of quality. Moreover, managers are also recommended to
integrate quality check with another processes of management, operations and logistics for
developing effective feedback loops and closed quality processes among functional areas. This
will facilitate improvements earlier with supply chain and helps in preventing quality issues.
In context to new product development, McDonald's have constantly developed multiple
products in its portfolio. At same time, it is recommended to adopt diversification strategy in
which it will enter in totally new market with new product. It will offer huge opportunities to
make relations with new suppliers and greater potentials for managing operations and logistics.
Furthermore, the strategy will offer greater potentials to enhance profits through opening new
revenue streams.
CONCLUSION
From the discussion, it is concluded that operations and logistics is the field or
department in the company that emphasis towards making sure that accurate quality of along
with amount of materials, products and equipments are manufactured and delivered to correct
acquirer as per schedules. Operations, logistics, supply chain and other aspects are key for
business to ensure effectiveness in functions. Managing quality is the area involves determining
quality policy, devising and executing quality planning, control and improvements. Total quality
6
manpower in business and supply chain.
Environmental consideration is another aspect which is linked to natural environment. It
is essential for the entity to examine influences of environmental consideration on logistics,
supply chain and consumers (Brogi and Lagasio, 2019). In this aspect, McDonald's is very
capable to sound environmentally as it makes improvements in environmental programs as well
as sustainability for strengthening performances of supply chain, operations and organisation as
whole. However, changes in weather conditions in certain regions threatens the business. It has
implemented closed loop chains to support protection of ecology prominently.
Administration of McDonald's is recommended to implement certain recommendation
that are concerned with managing quality and new product development. In context to managing
quality, the company is working great. However, it should adopt strategic leadership for
empowering people for working with minimum potentials and quality. With this, employees will
be encouraged to ensure that all the practices are performed effectively so that all the goals are
achieved with highest possible level of quality. Moreover, managers are also recommended to
integrate quality check with another processes of management, operations and logistics for
developing effective feedback loops and closed quality processes among functional areas. This
will facilitate improvements earlier with supply chain and helps in preventing quality issues.
In context to new product development, McDonald's have constantly developed multiple
products in its portfolio. At same time, it is recommended to adopt diversification strategy in
which it will enter in totally new market with new product. It will offer huge opportunities to
make relations with new suppliers and greater potentials for managing operations and logistics.
Furthermore, the strategy will offer greater potentials to enhance profits through opening new
revenue streams.
CONCLUSION
From the discussion, it is concluded that operations and logistics is the field or
department in the company that emphasis towards making sure that accurate quality of along
with amount of materials, products and equipments are manufactured and delivered to correct
acquirer as per schedules. Operations, logistics, supply chain and other aspects are key for
business to ensure effectiveness in functions. Managing quality is the area involves determining
quality policy, devising and executing quality planning, control and improvements. Total quality
6
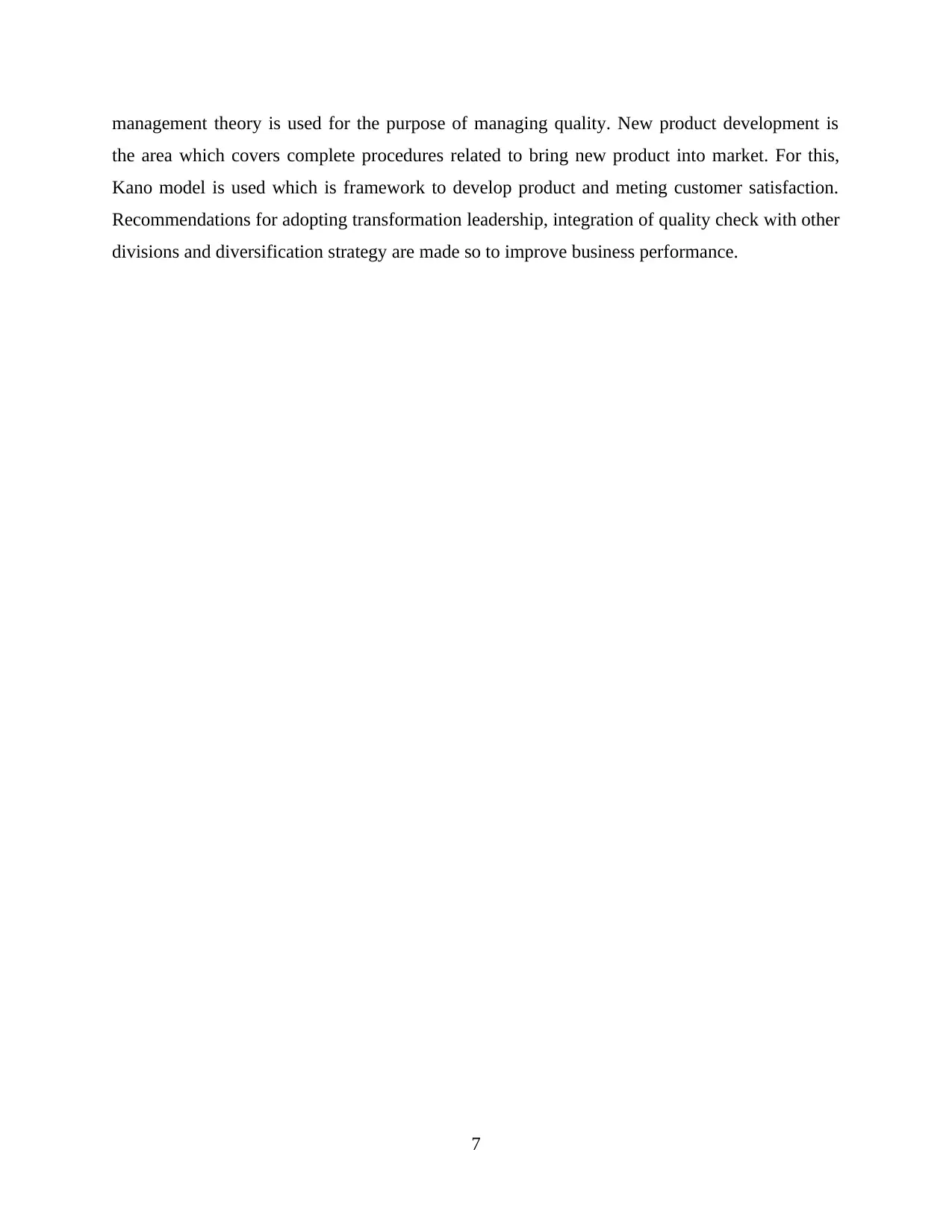
management theory is used for the purpose of managing quality. New product development is
the area which covers complete procedures related to bring new product into market. For this,
Kano model is used which is framework to develop product and meting customer satisfaction.
Recommendations for adopting transformation leadership, integration of quality check with other
divisions and diversification strategy are made so to improve business performance.
7
the area which covers complete procedures related to bring new product into market. For this,
Kano model is used which is framework to develop product and meting customer satisfaction.
Recommendations for adopting transformation leadership, integration of quality check with other
divisions and diversification strategy are made so to improve business performance.
7
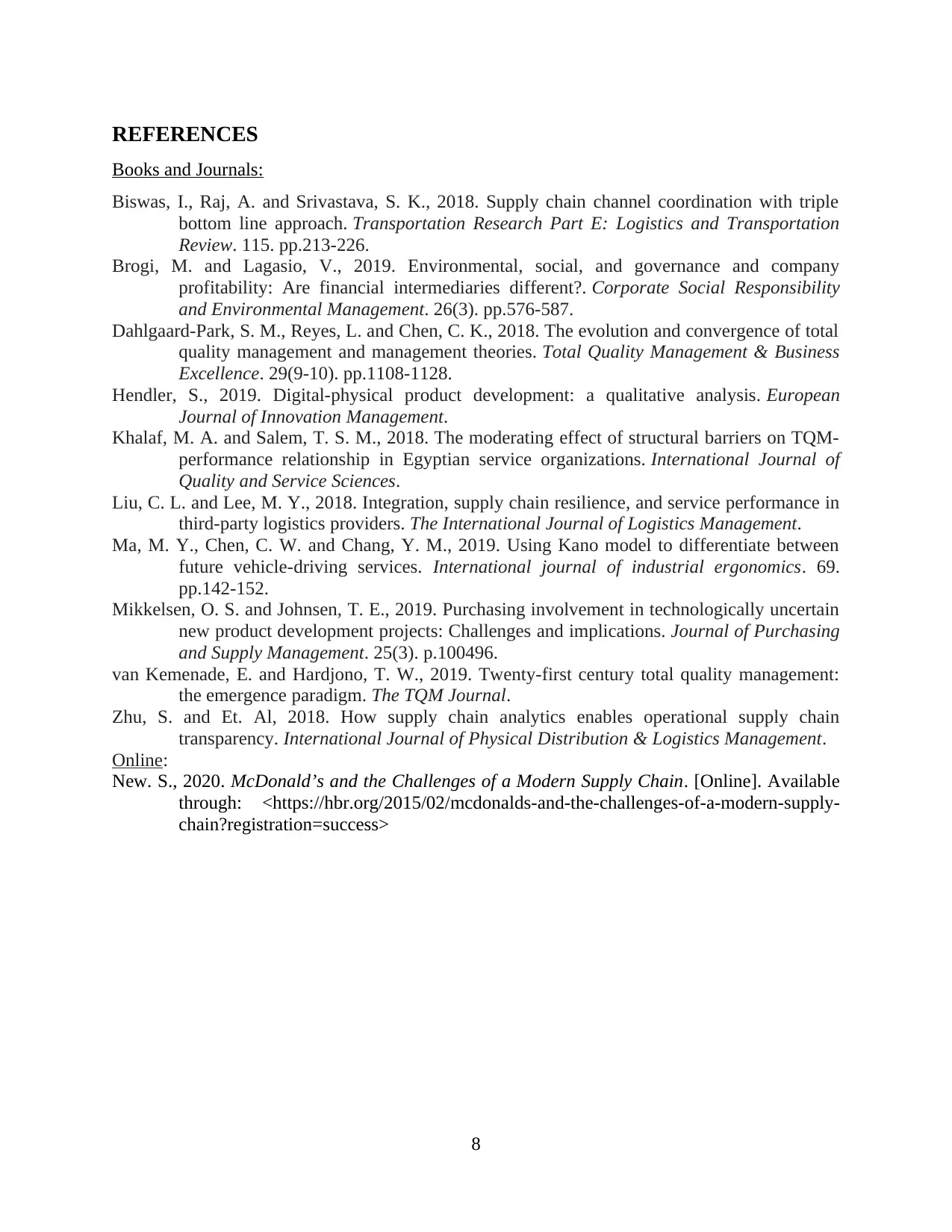
REFERENCES
Books and Journals:
Biswas, I., Raj, A. and Srivastava, S. K., 2018. Supply chain channel coordination with triple
bottom line approach. Transportation Research Part E: Logistics and Transportation
Review. 115. pp.213-226.
Brogi, M. and Lagasio, V., 2019. Environmental, social, and governance and company
profitability: Are financial intermediaries different?. Corporate Social Responsibility
and Environmental Management. 26(3). pp.576-587.
Dahlgaard-Park, S. M., Reyes, L. and Chen, C. K., 2018. The evolution and convergence of total
quality management and management theories. Total Quality Management & Business
Excellence. 29(9-10). pp.1108-1128.
Hendler, S., 2019. Digital-physical product development: a qualitative analysis. European
Journal of Innovation Management.
Khalaf, M. A. and Salem, T. S. M., 2018. The moderating effect of structural barriers on TQM-
performance relationship in Egyptian service organizations. International Journal of
Quality and Service Sciences.
Liu, C. L. and Lee, M. Y., 2018. Integration, supply chain resilience, and service performance in
third-party logistics providers. The International Journal of Logistics Management.
Ma, M. Y., Chen, C. W. and Chang, Y. M., 2019. Using Kano model to differentiate between
future vehicle-driving services. International journal of industrial ergonomics. 69.
pp.142-152.
Mikkelsen, O. S. and Johnsen, T. E., 2019. Purchasing involvement in technologically uncertain
new product development projects: Challenges and implications. Journal of Purchasing
and Supply Management. 25(3). p.100496.
van Kemenade, E. and Hardjono, T. W., 2019. Twenty-first century total quality management:
the emergence paradigm. The TQM Journal.
Zhu, S. and Et. Al, 2018. How supply chain analytics enables operational supply chain
transparency. International Journal of Physical Distribution & Logistics Management.
Online:
New. S., 2020. McDonald’s and the Challenges of a Modern Supply Chain. [Online]. Available
through: <https://hbr.org/2015/02/mcdonalds-and-the-challenges-of-a-modern-supply-
chain?registration=success>
8
Books and Journals:
Biswas, I., Raj, A. and Srivastava, S. K., 2018. Supply chain channel coordination with triple
bottom line approach. Transportation Research Part E: Logistics and Transportation
Review. 115. pp.213-226.
Brogi, M. and Lagasio, V., 2019. Environmental, social, and governance and company
profitability: Are financial intermediaries different?. Corporate Social Responsibility
and Environmental Management. 26(3). pp.576-587.
Dahlgaard-Park, S. M., Reyes, L. and Chen, C. K., 2018. The evolution and convergence of total
quality management and management theories. Total Quality Management & Business
Excellence. 29(9-10). pp.1108-1128.
Hendler, S., 2019. Digital-physical product development: a qualitative analysis. European
Journal of Innovation Management.
Khalaf, M. A. and Salem, T. S. M., 2018. The moderating effect of structural barriers on TQM-
performance relationship in Egyptian service organizations. International Journal of
Quality and Service Sciences.
Liu, C. L. and Lee, M. Y., 2018. Integration, supply chain resilience, and service performance in
third-party logistics providers. The International Journal of Logistics Management.
Ma, M. Y., Chen, C. W. and Chang, Y. M., 2019. Using Kano model to differentiate between
future vehicle-driving services. International journal of industrial ergonomics. 69.
pp.142-152.
Mikkelsen, O. S. and Johnsen, T. E., 2019. Purchasing involvement in technologically uncertain
new product development projects: Challenges and implications. Journal of Purchasing
and Supply Management. 25(3). p.100496.
van Kemenade, E. and Hardjono, T. W., 2019. Twenty-first century total quality management:
the emergence paradigm. The TQM Journal.
Zhu, S. and Et. Al, 2018. How supply chain analytics enables operational supply chain
transparency. International Journal of Physical Distribution & Logistics Management.
Online:
New. S., 2020. McDonald’s and the Challenges of a Modern Supply Chain. [Online]. Available
through: <https://hbr.org/2015/02/mcdonalds-and-the-challenges-of-a-modern-supply-
chain?registration=success>
8
1 out of 10
Related Documents
![[object Object]](/_next/image/?url=%2F_next%2Fstatic%2Fmedia%2Flogo.6d15ce61.png&w=640&q=75)
Your All-in-One AI-Powered Toolkit for Academic Success.
 +13062052269
info@desklib.com
Available 24*7 on WhatsApp / Email
Unlock your academic potential
© 2024  |  Zucol Services PVT LTD  |  All rights reserved.