International Auditing Standards and Quality
VerifiedAdded on 2020/03/23
|24
|7141
|39
AI Summary
This assignment delves into the realm of international auditing standards. It examines key concepts, principles, and frameworks that govern audits across diverse sectors. The focus lies on understanding how these standards contribute to enhancing audit quality, reliability of financial information, and promoting transparency within organizations. The provided readings explore various aspects of auditing, continuous improvement, quality management in healthcare, and the application of tools like nominal group technique for consensus building in defining pain outcomes.
Contribute Materials
Your contribution can guide someone’s learning journey. Share your
documents today.
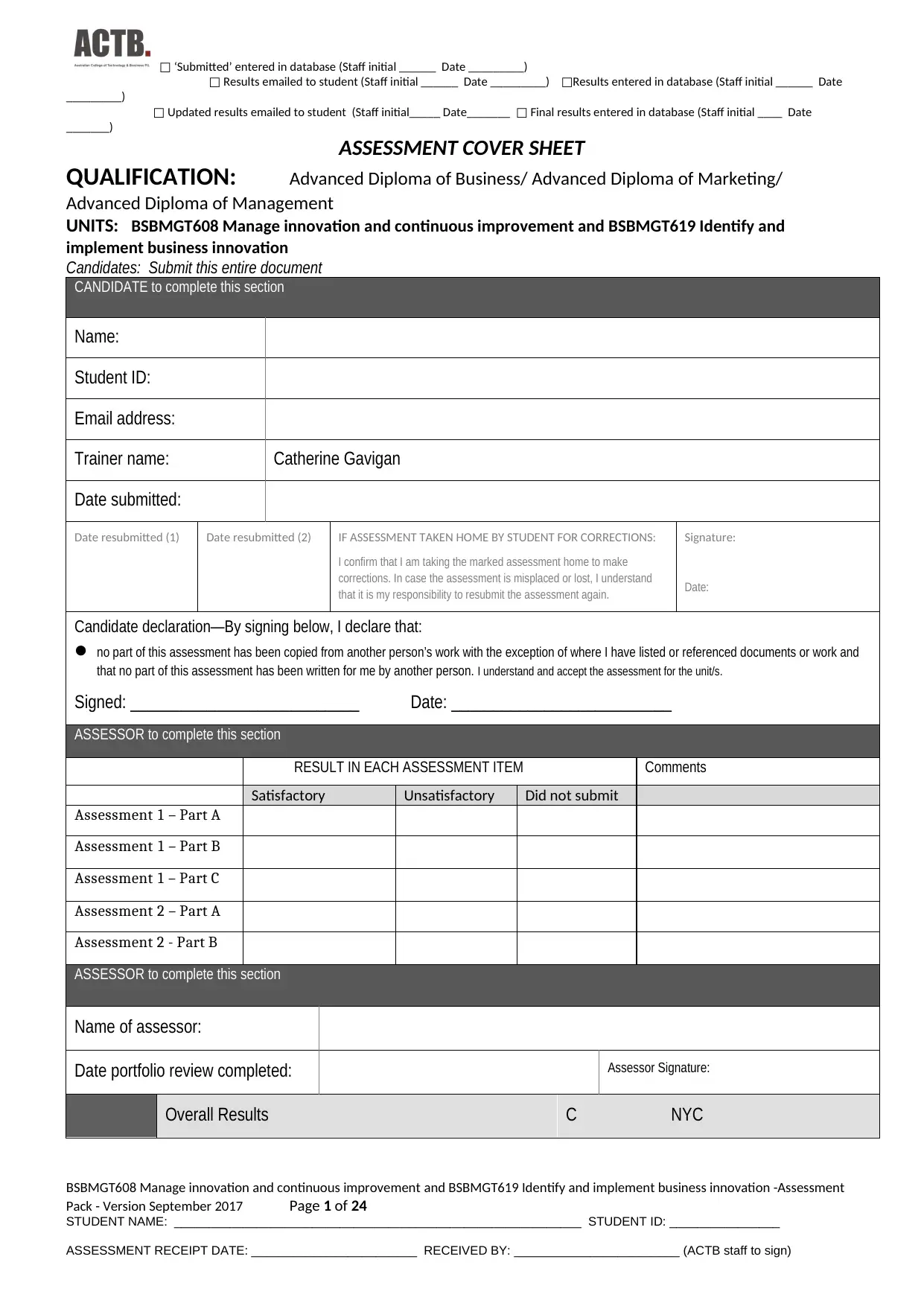
□ ‘Submitted’ entered in database (Staff initial ______ Date _________)
□ Results emailed to student (Staff initial ______ Date _________) □Results entered in database (Staff initial ______ Date
_________)
□ Updated results emailed to student (Staff initial_____ Date_______ □ Final results entered in database (Staff initial ____ Date
_______)
ASSESSMENT COVER SHEET
QUALIFICATION: Advanced Diploma of Business/ Advanced Diploma of Marketing/
Advanced Diploma of Management
UNITS: BSBMGT608 Manage innovation and continuous improvement and BSBMGT619 Identify and
implement business innovation
Candidates: Submit this entire document
CANDIDATE to complete this section
Name:
Student ID:
Email address:
Trainer name: Catherine Gavigan
Date submitted:
Date resubmitted (1) Date resubmitted (2) IF ASSESSMENT TAKEN HOME BY STUDENT FOR CORRECTIONS:
I confirm that I am taking the marked assessment home to make
corrections. In case the assessment is misplaced or lost, I understand
that it is my responsibility to resubmit the assessment again.
Signature:
Date:
Candidate declaration—By signing below, I declare that:
no part of this assessment has been copied from another person’s work with the exception of where I have listed or referenced documents or work and
that no part of this assessment has been written for me by another person. I understand and accept the assessment for the unit/s.
Signed: ___________________________ Date: __________________________
ASSESSOR to complete this section
RESULT IN EACH ASSESSMENT ITEM Comments
Satisfactory Unsatisfactory Did not submit
Assessment 1 – Part A
Assessment 1 – Part B
Assessment 1 – Part C
Assessment 2 – Part A
Assessment 2 - Part B
ASSESSOR to complete this section
Name of assessor:
Date portfolio review completed: Assessor Signature:
Overall Results C NYC
BSBMGT608 Manage innovation and continuous improvement and BSBMGT619 Identify and implement business innovation -Assessment
Pack - Version September 2017 Page 1 of 24
STUDENT NAME: ___________________________________________________________ STUDENT ID: ________________
ASSESSMENT RECEIPT DATE: ________________________ RECEIVED BY: ________________________ (ACTB staff to sign)
□ Results emailed to student (Staff initial ______ Date _________) □Results entered in database (Staff initial ______ Date
_________)
□ Updated results emailed to student (Staff initial_____ Date_______ □ Final results entered in database (Staff initial ____ Date
_______)
ASSESSMENT COVER SHEET
QUALIFICATION: Advanced Diploma of Business/ Advanced Diploma of Marketing/
Advanced Diploma of Management
UNITS: BSBMGT608 Manage innovation and continuous improvement and BSBMGT619 Identify and
implement business innovation
Candidates: Submit this entire document
CANDIDATE to complete this section
Name:
Student ID:
Email address:
Trainer name: Catherine Gavigan
Date submitted:
Date resubmitted (1) Date resubmitted (2) IF ASSESSMENT TAKEN HOME BY STUDENT FOR CORRECTIONS:
I confirm that I am taking the marked assessment home to make
corrections. In case the assessment is misplaced or lost, I understand
that it is my responsibility to resubmit the assessment again.
Signature:
Date:
Candidate declaration—By signing below, I declare that:
no part of this assessment has been copied from another person’s work with the exception of where I have listed or referenced documents or work and
that no part of this assessment has been written for me by another person. I understand and accept the assessment for the unit/s.
Signed: ___________________________ Date: __________________________
ASSESSOR to complete this section
RESULT IN EACH ASSESSMENT ITEM Comments
Satisfactory Unsatisfactory Did not submit
Assessment 1 – Part A
Assessment 1 – Part B
Assessment 1 – Part C
Assessment 2 – Part A
Assessment 2 - Part B
ASSESSOR to complete this section
Name of assessor:
Date portfolio review completed: Assessor Signature:
Overall Results C NYC
BSBMGT608 Manage innovation and continuous improvement and BSBMGT619 Identify and implement business innovation -Assessment
Pack - Version September 2017 Page 1 of 24
STUDENT NAME: ___________________________________________________________ STUDENT ID: ________________
ASSESSMENT RECEIPT DATE: ________________________ RECEIVED BY: ________________________ (ACTB staff to sign)
Secure Best Marks with AI Grader
Need help grading? Try our AI Grader for instant feedback on your assignments.
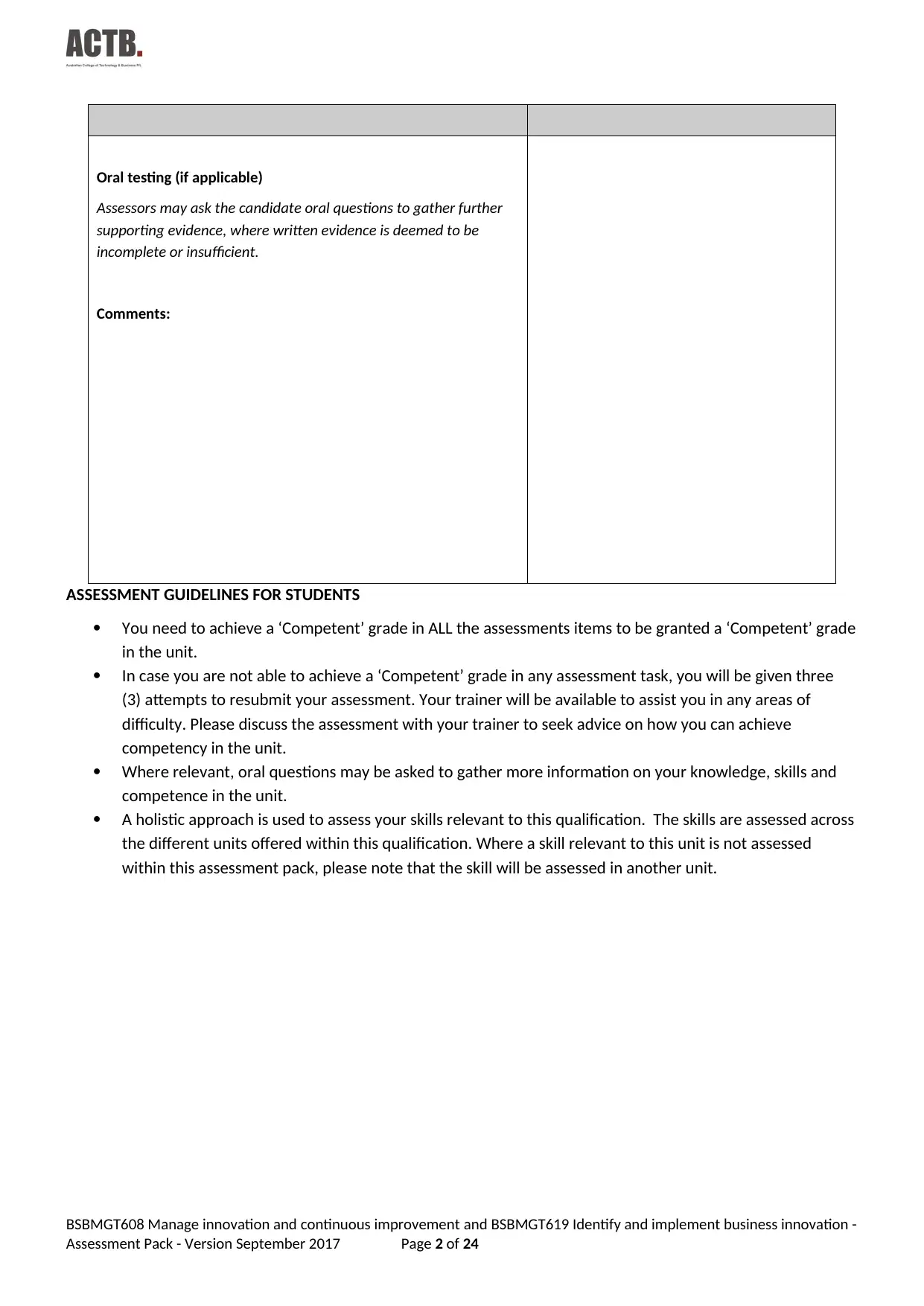
Oral testing (if applicable)
Assessors may ask the candidate oral questions to gather further
supporting evidence, where written evidence is deemed to be
incomplete or insufficient.
Comments:
ASSESSMENT GUIDELINES FOR STUDENTS
You need to achieve a ‘Competent’ grade in ALL the assessments items to be granted a ‘Competent’ grade
in the unit.
In case you are not able to achieve a ‘Competent’ grade in any assessment task, you will be given three
(3) attempts to resubmit your assessment. Your trainer will be available to assist you in any areas of
difficulty. Please discuss the assessment with your trainer to seek advice on how you can achieve
competency in the unit.
Where relevant, oral questions may be asked to gather more information on your knowledge, skills and
competence in the unit.
A holistic approach is used to assess your skills relevant to this qualification. The skills are assessed across
the different units offered within this qualification. Where a skill relevant to this unit is not assessed
within this assessment pack, please note that the skill will be assessed in another unit.
BSBMGT608 Manage innovation and continuous improvement and BSBMGT619 Identify and implement business innovation -
Assessment Pack - Version September 2017 Page 2 of 24
Assessors may ask the candidate oral questions to gather further
supporting evidence, where written evidence is deemed to be
incomplete or insufficient.
Comments:
ASSESSMENT GUIDELINES FOR STUDENTS
You need to achieve a ‘Competent’ grade in ALL the assessments items to be granted a ‘Competent’ grade
in the unit.
In case you are not able to achieve a ‘Competent’ grade in any assessment task, you will be given three
(3) attempts to resubmit your assessment. Your trainer will be available to assist you in any areas of
difficulty. Please discuss the assessment with your trainer to seek advice on how you can achieve
competency in the unit.
Where relevant, oral questions may be asked to gather more information on your knowledge, skills and
competence in the unit.
A holistic approach is used to assess your skills relevant to this qualification. The skills are assessed across
the different units offered within this qualification. Where a skill relevant to this unit is not assessed
within this assessment pack, please note that the skill will be assessed in another unit.
BSBMGT608 Manage innovation and continuous improvement and BSBMGT619 Identify and implement business innovation -
Assessment Pack - Version September 2017 Page 2 of 24
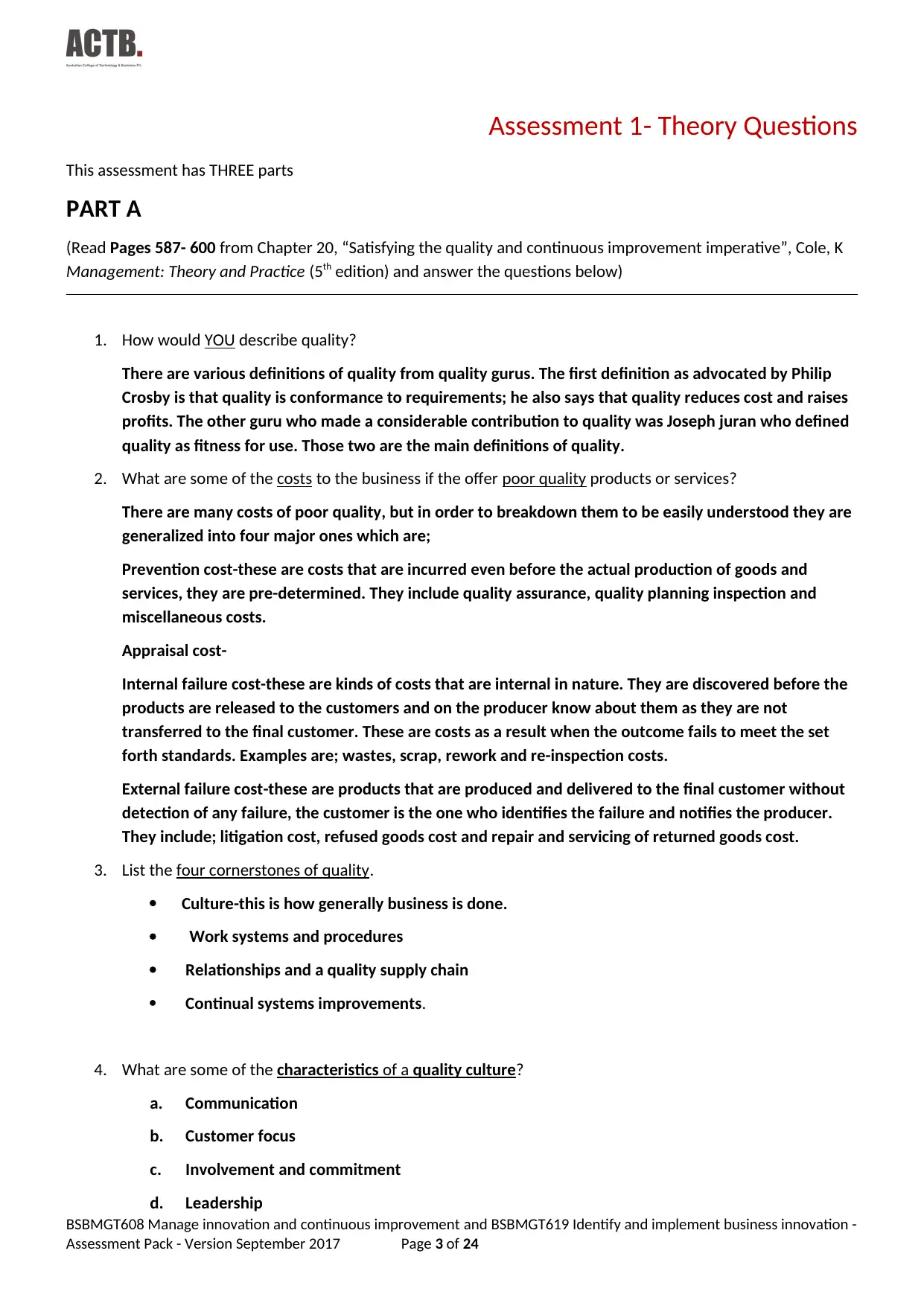
Assessment 1- Theory Questions
This assessment has THREE parts
PART A
(Read Pages 587- 600 from Chapter 20, “Satisfying the quality and continuous improvement imperative”, Cole, K
Management: Theory and Practice (5th edition) and answer the questions below)
1. How would YOU describe quality?
There are various definitions of quality from quality gurus. The first definition as advocated by Philip
Crosby is that quality is conformance to requirements; he also says that quality reduces cost and raises
profits. The other guru who made a considerable contribution to quality was Joseph juran who defined
quality as fitness for use. Those two are the main definitions of quality.
2. What are some of the costs to the business if the offer poor quality products or services?
There are many costs of poor quality, but in order to breakdown them to be easily understood they are
generalized into four major ones which are;
Prevention cost-these are costs that are incurred even before the actual production of goods and
services, they are pre-determined. They include quality assurance, quality planning inspection and
miscellaneous costs.
Appraisal cost-
Internal failure cost-these are kinds of costs that are internal in nature. They are discovered before the
products are released to the customers and on the producer know about them as they are not
transferred to the final customer. These are costs as a result when the outcome fails to meet the set
forth standards. Examples are; wastes, scrap, rework and re-inspection costs.
External failure cost-these are products that are produced and delivered to the final customer without
detection of any failure, the customer is the one who identifies the failure and notifies the producer.
They include; litigation cost, refused goods cost and repair and servicing of returned goods cost.
3. List the four cornerstones of quality.
Culture-this is how generally business is done.
Work systems and procedures
Relationships and a quality supply chain
Continual systems improvements.
4. What are some of the characteristics of a quality culture?
a. Communication
b. Customer focus
c. Involvement and commitment
d. Leadership
BSBMGT608 Manage innovation and continuous improvement and BSBMGT619 Identify and implement business innovation -
Assessment Pack - Version September 2017 Page 3 of 24
This assessment has THREE parts
PART A
(Read Pages 587- 600 from Chapter 20, “Satisfying the quality and continuous improvement imperative”, Cole, K
Management: Theory and Practice (5th edition) and answer the questions below)
1. How would YOU describe quality?
There are various definitions of quality from quality gurus. The first definition as advocated by Philip
Crosby is that quality is conformance to requirements; he also says that quality reduces cost and raises
profits. The other guru who made a considerable contribution to quality was Joseph juran who defined
quality as fitness for use. Those two are the main definitions of quality.
2. What are some of the costs to the business if the offer poor quality products or services?
There are many costs of poor quality, but in order to breakdown them to be easily understood they are
generalized into four major ones which are;
Prevention cost-these are costs that are incurred even before the actual production of goods and
services, they are pre-determined. They include quality assurance, quality planning inspection and
miscellaneous costs.
Appraisal cost-
Internal failure cost-these are kinds of costs that are internal in nature. They are discovered before the
products are released to the customers and on the producer know about them as they are not
transferred to the final customer. These are costs as a result when the outcome fails to meet the set
forth standards. Examples are; wastes, scrap, rework and re-inspection costs.
External failure cost-these are products that are produced and delivered to the final customer without
detection of any failure, the customer is the one who identifies the failure and notifies the producer.
They include; litigation cost, refused goods cost and repair and servicing of returned goods cost.
3. List the four cornerstones of quality.
Culture-this is how generally business is done.
Work systems and procedures
Relationships and a quality supply chain
Continual systems improvements.
4. What are some of the characteristics of a quality culture?
a. Communication
b. Customer focus
c. Involvement and commitment
d. Leadership
BSBMGT608 Manage innovation and continuous improvement and BSBMGT619 Identify and implement business innovation -
Assessment Pack - Version September 2017 Page 3 of 24
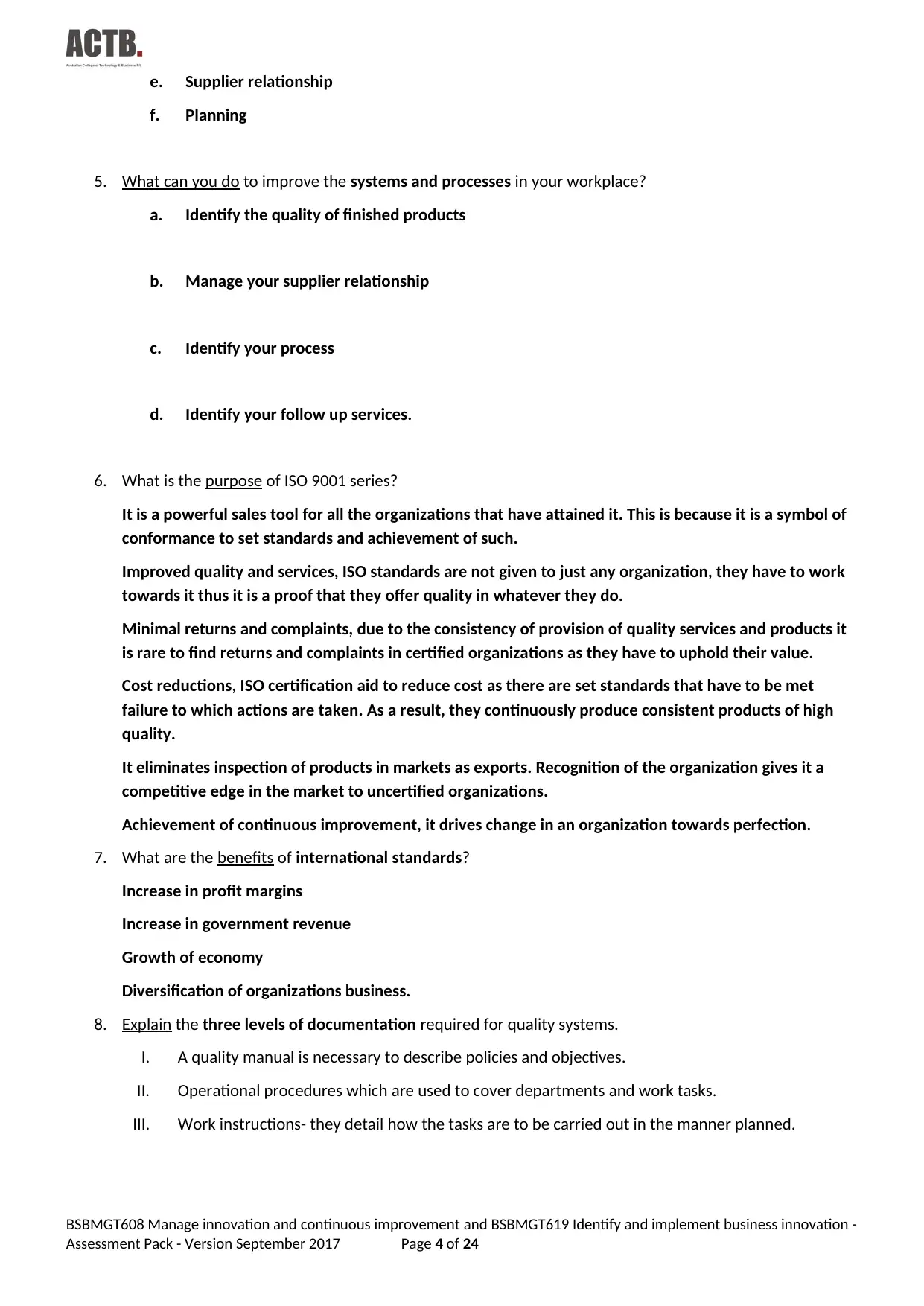
e. Supplier relationship
f. Planning
5. What can you do to improve the systems and processes in your workplace?
a. Identify the quality of finished products
b. Manage your supplier relationship
c. Identify your process
d. Identify your follow up services.
6. What is the purpose of ISO 9001 series?
It is a powerful sales tool for all the organizations that have attained it. This is because it is a symbol of
conformance to set standards and achievement of such.
Improved quality and services, ISO standards are not given to just any organization, they have to work
towards it thus it is a proof that they offer quality in whatever they do.
Minimal returns and complaints, due to the consistency of provision of quality services and products it
is rare to find returns and complaints in certified organizations as they have to uphold their value.
Cost reductions, ISO certification aid to reduce cost as there are set standards that have to be met
failure to which actions are taken. As a result, they continuously produce consistent products of high
quality.
It eliminates inspection of products in markets as exports. Recognition of the organization gives it a
competitive edge in the market to uncertified organizations.
Achievement of continuous improvement, it drives change in an organization towards perfection.
7. What are the benefits of international standards?
Increase in profit margins
Increase in government revenue
Growth of economy
Diversification of organizations business.
8. Explain the three levels of documentation required for quality systems.
I. A quality manual is necessary to describe policies and objectives.
II. Operational procedures which are used to cover departments and work tasks.
III. Work instructions- they detail how the tasks are to be carried out in the manner planned.
BSBMGT608 Manage innovation and continuous improvement and BSBMGT619 Identify and implement business innovation -
Assessment Pack - Version September 2017 Page 4 of 24
f. Planning
5. What can you do to improve the systems and processes in your workplace?
a. Identify the quality of finished products
b. Manage your supplier relationship
c. Identify your process
d. Identify your follow up services.
6. What is the purpose of ISO 9001 series?
It is a powerful sales tool for all the organizations that have attained it. This is because it is a symbol of
conformance to set standards and achievement of such.
Improved quality and services, ISO standards are not given to just any organization, they have to work
towards it thus it is a proof that they offer quality in whatever they do.
Minimal returns and complaints, due to the consistency of provision of quality services and products it
is rare to find returns and complaints in certified organizations as they have to uphold their value.
Cost reductions, ISO certification aid to reduce cost as there are set standards that have to be met
failure to which actions are taken. As a result, they continuously produce consistent products of high
quality.
It eliminates inspection of products in markets as exports. Recognition of the organization gives it a
competitive edge in the market to uncertified organizations.
Achievement of continuous improvement, it drives change in an organization towards perfection.
7. What are the benefits of international standards?
Increase in profit margins
Increase in government revenue
Growth of economy
Diversification of organizations business.
8. Explain the three levels of documentation required for quality systems.
I. A quality manual is necessary to describe policies and objectives.
II. Operational procedures which are used to cover departments and work tasks.
III. Work instructions- they detail how the tasks are to be carried out in the manner planned.
BSBMGT608 Manage innovation and continuous improvement and BSBMGT619 Identify and implement business innovation -
Assessment Pack - Version September 2017 Page 4 of 24
Secure Best Marks with AI Grader
Need help grading? Try our AI Grader for instant feedback on your assignments.
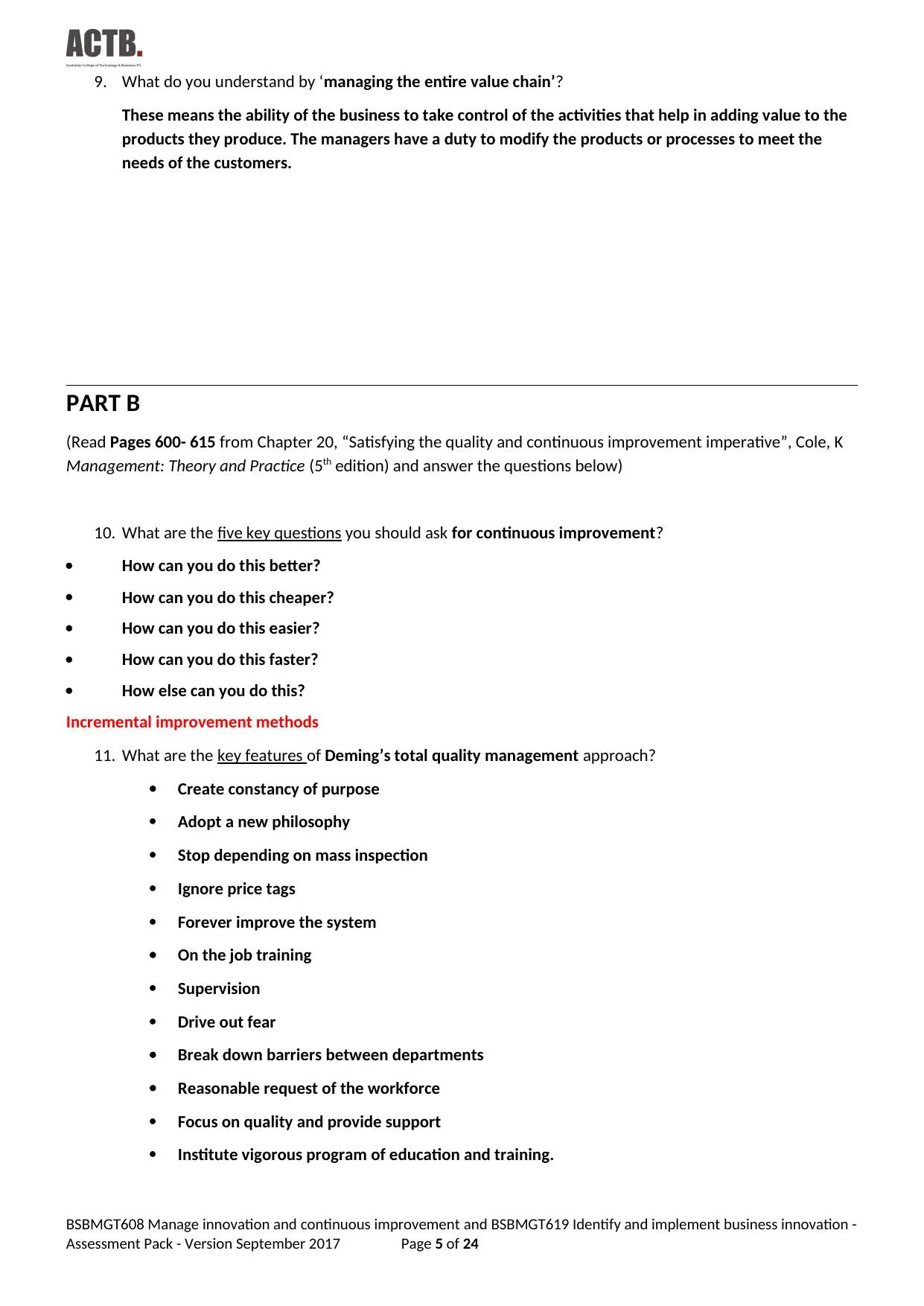
9. What do you understand by ‘managing the entire value chain’?
These means the ability of the business to take control of the activities that help in adding value to the
products they produce. The managers have a duty to modify the products or processes to meet the
needs of the customers.
PART B
(Read Pages 600- 615 from Chapter 20, “Satisfying the quality and continuous improvement imperative”, Cole, K
Management: Theory and Practice (5th edition) and answer the questions below)
10. What are the five key questions you should ask for continuous improvement?
How can you do this better?
How can you do this cheaper?
How can you do this easier?
How can you do this faster?
How else can you do this?
Incremental improvement methods
11. What are the key features of Deming’s total quality management approach?
Create constancy of purpose
Adopt a new philosophy
Stop depending on mass inspection
Ignore price tags
Forever improve the system
On the job training
Supervision
Drive out fear
Break down barriers between departments
Reasonable request of the workforce
Focus on quality and provide support
Institute vigorous program of education and training.
BSBMGT608 Manage innovation and continuous improvement and BSBMGT619 Identify and implement business innovation -
Assessment Pack - Version September 2017 Page 5 of 24
These means the ability of the business to take control of the activities that help in adding value to the
products they produce. The managers have a duty to modify the products or processes to meet the
needs of the customers.
PART B
(Read Pages 600- 615 from Chapter 20, “Satisfying the quality and continuous improvement imperative”, Cole, K
Management: Theory and Practice (5th edition) and answer the questions below)
10. What are the five key questions you should ask for continuous improvement?
How can you do this better?
How can you do this cheaper?
How can you do this easier?
How can you do this faster?
How else can you do this?
Incremental improvement methods
11. What are the key features of Deming’s total quality management approach?
Create constancy of purpose
Adopt a new philosophy
Stop depending on mass inspection
Ignore price tags
Forever improve the system
On the job training
Supervision
Drive out fear
Break down barriers between departments
Reasonable request of the workforce
Focus on quality and provide support
Institute vigorous program of education and training.
BSBMGT608 Manage innovation and continuous improvement and BSBMGT619 Identify and implement business innovation -
Assessment Pack - Version September 2017 Page 5 of 24
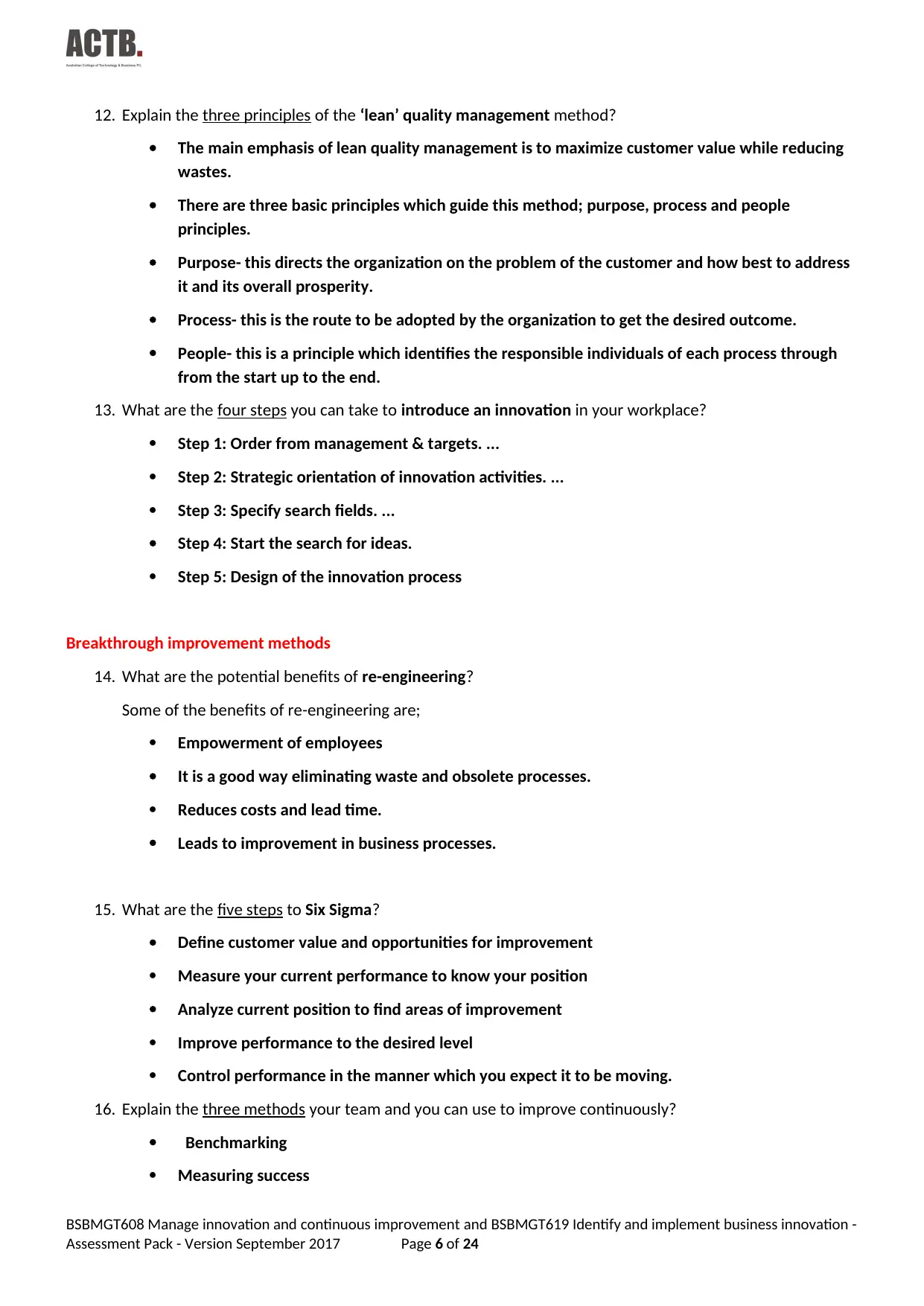
12. Explain the three principles of the ‘lean’ quality management method?
The main emphasis of lean quality management is to maximize customer value while reducing
wastes.
There are three basic principles which guide this method; purpose, process and people
principles.
Purpose- this directs the organization on the problem of the customer and how best to address
it and its overall prosperity.
Process- this is the route to be adopted by the organization to get the desired outcome.
People- this is a principle which identifies the responsible individuals of each process through
from the start up to the end.
13. What are the four steps you can take to introduce an innovation in your workplace?
Step 1: Order from management & targets. ...
Step 2: Strategic orientation of innovation activities. ...
Step 3: Specify search fields. ...
Step 4: Start the search for ideas.
Step 5: Design of the innovation process
Breakthrough improvement methods
14. What are the potential benefits of re-engineering?
Some of the benefits of re-engineering are;
Empowerment of employees
It is a good way eliminating waste and obsolete processes.
Reduces costs and lead time.
Leads to improvement in business processes.
15. What are the five steps to Six Sigma?
Define customer value and opportunities for improvement
Measure your current performance to know your position
Analyze current position to find areas of improvement
Improve performance to the desired level
Control performance in the manner which you expect it to be moving.
16. Explain the three methods your team and you can use to improve continuously?
Benchmarking
Measuring success
BSBMGT608 Manage innovation and continuous improvement and BSBMGT619 Identify and implement business innovation -
Assessment Pack - Version September 2017 Page 6 of 24
The main emphasis of lean quality management is to maximize customer value while reducing
wastes.
There are three basic principles which guide this method; purpose, process and people
principles.
Purpose- this directs the organization on the problem of the customer and how best to address
it and its overall prosperity.
Process- this is the route to be adopted by the organization to get the desired outcome.
People- this is a principle which identifies the responsible individuals of each process through
from the start up to the end.
13. What are the four steps you can take to introduce an innovation in your workplace?
Step 1: Order from management & targets. ...
Step 2: Strategic orientation of innovation activities. ...
Step 3: Specify search fields. ...
Step 4: Start the search for ideas.
Step 5: Design of the innovation process
Breakthrough improvement methods
14. What are the potential benefits of re-engineering?
Some of the benefits of re-engineering are;
Empowerment of employees
It is a good way eliminating waste and obsolete processes.
Reduces costs and lead time.
Leads to improvement in business processes.
15. What are the five steps to Six Sigma?
Define customer value and opportunities for improvement
Measure your current performance to know your position
Analyze current position to find areas of improvement
Improve performance to the desired level
Control performance in the manner which you expect it to be moving.
16. Explain the three methods your team and you can use to improve continuously?
Benchmarking
Measuring success
BSBMGT608 Manage innovation and continuous improvement and BSBMGT619 Identify and implement business innovation -
Assessment Pack - Version September 2017 Page 6 of 24
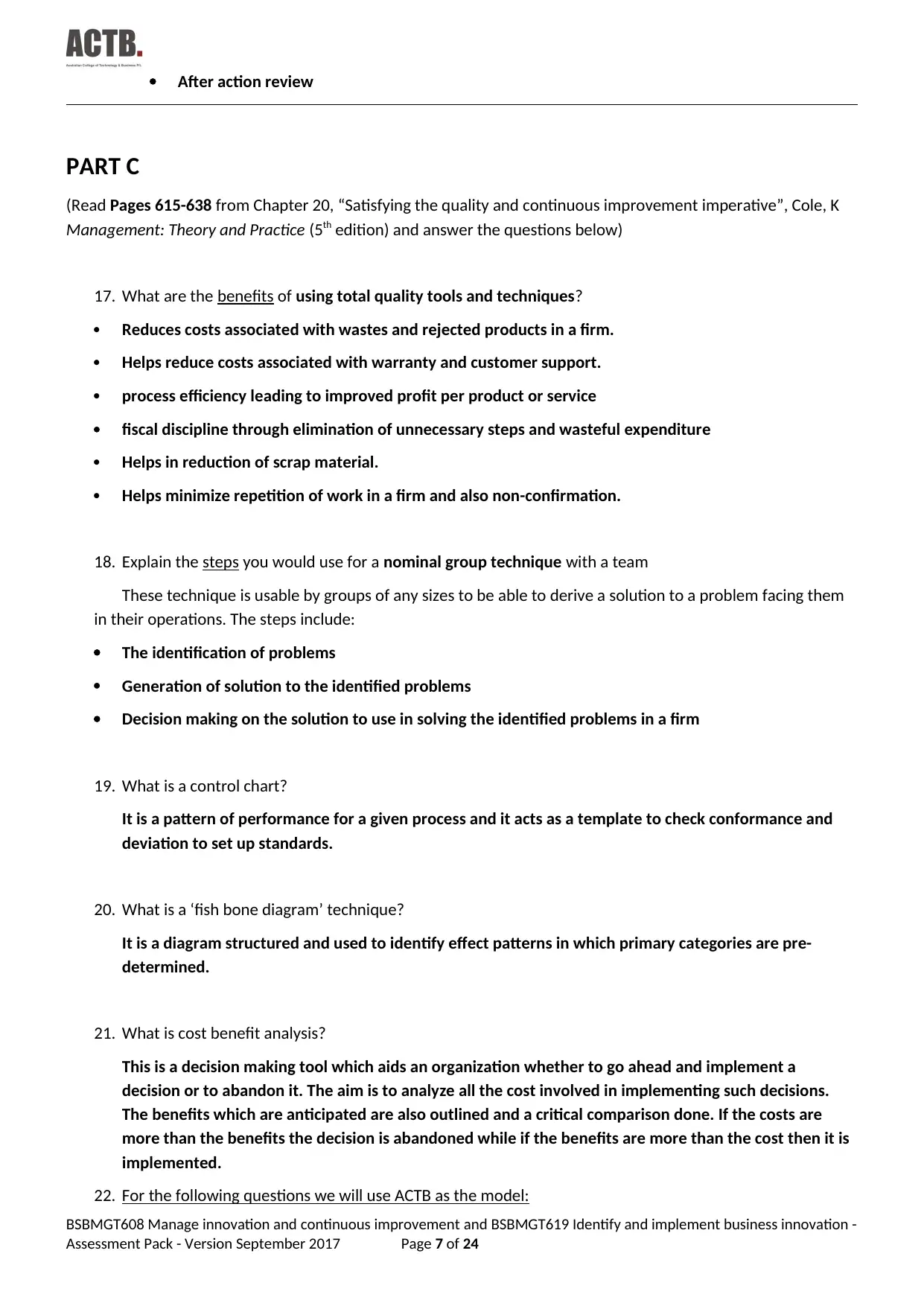
After action review
PART C
(Read Pages 615-638 from Chapter 20, “Satisfying the quality and continuous improvement imperative”, Cole, K
Management: Theory and Practice (5th edition) and answer the questions below)
17. What are the benefits of using total quality tools and techniques?
Reduces costs associated with wastes and rejected products in a firm.
Helps reduce costs associated with warranty and customer support.
process efficiency leading to improved profit per product or service
fiscal discipline through elimination of unnecessary steps and wasteful expenditure
Helps in reduction of scrap material.
Helps minimize repetition of work in a firm and also non-confirmation.
18. Explain the steps you would use for a nominal group technique with a team
These technique is usable by groups of any sizes to be able to derive a solution to a problem facing them
in their operations. The steps include:
The identification of problems
Generation of solution to the identified problems
Decision making on the solution to use in solving the identified problems in a firm
19. What is a control chart?
It is a pattern of performance for a given process and it acts as a template to check conformance and
deviation to set up standards.
20. What is a ‘fish bone diagram’ technique?
It is a diagram structured and used to identify effect patterns in which primary categories are pre-
determined.
21. What is cost benefit analysis?
This is a decision making tool which aids an organization whether to go ahead and implement a
decision or to abandon it. The aim is to analyze all the cost involved in implementing such decisions.
The benefits which are anticipated are also outlined and a critical comparison done. If the costs are
more than the benefits the decision is abandoned while if the benefits are more than the cost then it is
implemented.
22. For the following questions we will use ACTB as the model:
BSBMGT608 Manage innovation and continuous improvement and BSBMGT619 Identify and implement business innovation -
Assessment Pack - Version September 2017 Page 7 of 24
PART C
(Read Pages 615-638 from Chapter 20, “Satisfying the quality and continuous improvement imperative”, Cole, K
Management: Theory and Practice (5th edition) and answer the questions below)
17. What are the benefits of using total quality tools and techniques?
Reduces costs associated with wastes and rejected products in a firm.
Helps reduce costs associated with warranty and customer support.
process efficiency leading to improved profit per product or service
fiscal discipline through elimination of unnecessary steps and wasteful expenditure
Helps in reduction of scrap material.
Helps minimize repetition of work in a firm and also non-confirmation.
18. Explain the steps you would use for a nominal group technique with a team
These technique is usable by groups of any sizes to be able to derive a solution to a problem facing them
in their operations. The steps include:
The identification of problems
Generation of solution to the identified problems
Decision making on the solution to use in solving the identified problems in a firm
19. What is a control chart?
It is a pattern of performance for a given process and it acts as a template to check conformance and
deviation to set up standards.
20. What is a ‘fish bone diagram’ technique?
It is a diagram structured and used to identify effect patterns in which primary categories are pre-
determined.
21. What is cost benefit analysis?
This is a decision making tool which aids an organization whether to go ahead and implement a
decision or to abandon it. The aim is to analyze all the cost involved in implementing such decisions.
The benefits which are anticipated are also outlined and a critical comparison done. If the costs are
more than the benefits the decision is abandoned while if the benefits are more than the cost then it is
implemented.
22. For the following questions we will use ACTB as the model:
BSBMGT608 Manage innovation and continuous improvement and BSBMGT619 Identify and implement business innovation -
Assessment Pack - Version September 2017 Page 7 of 24
Paraphrase This Document
Need a fresh take? Get an instant paraphrase of this document with our AI Paraphraser
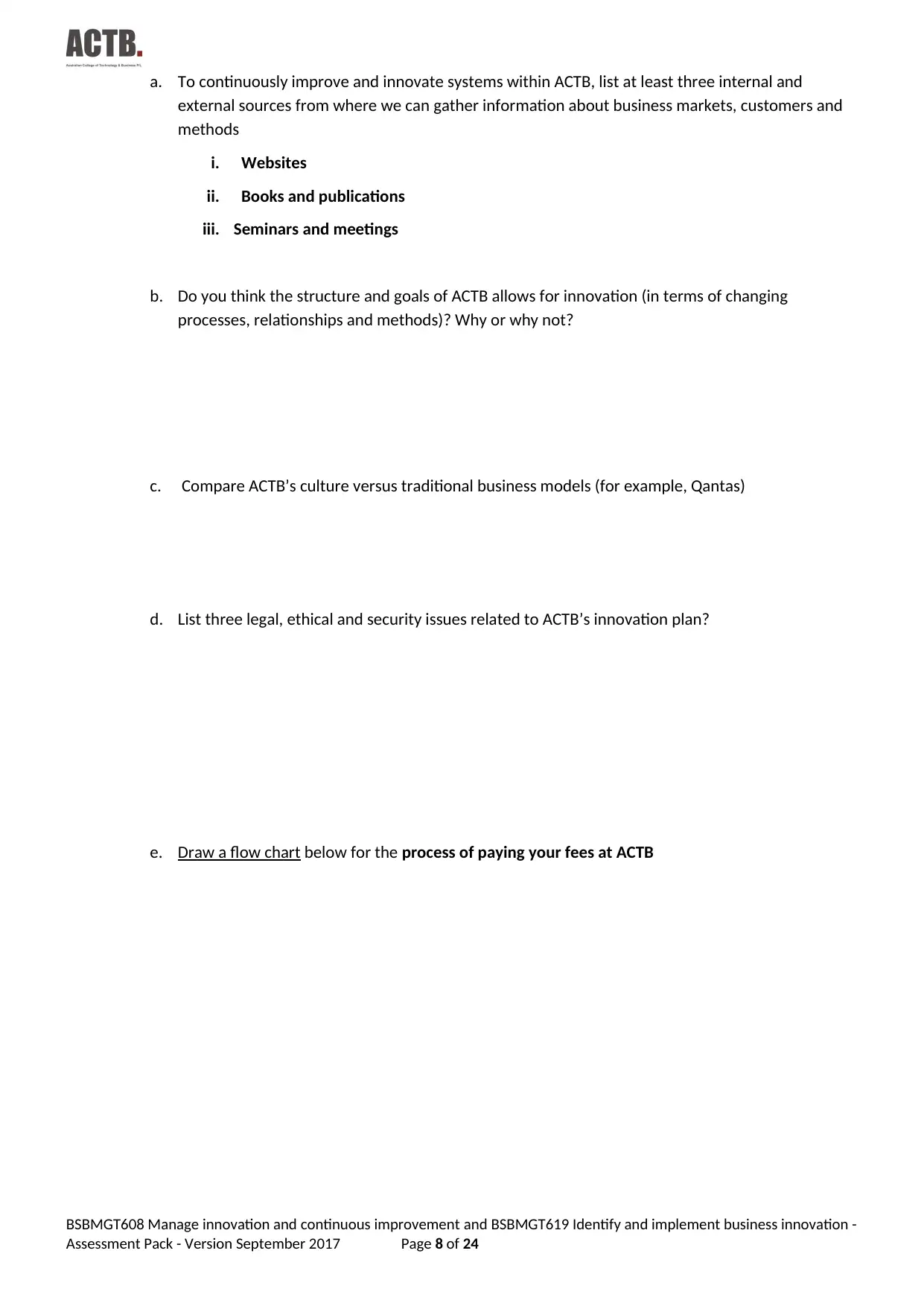
a. To continuously improve and innovate systems within ACTB, list at least three internal and
external sources from where we can gather information about business markets, customers and
methods
i. Websites
ii. Books and publications
iii. Seminars and meetings
b. Do you think the structure and goals of ACTB allows for innovation (in terms of changing
processes, relationships and methods)? Why or why not?
c. Compare ACTB’s culture versus traditional business models (for example, Qantas)
d. List three legal, ethical and security issues related to ACTB’s innovation plan?
e. Draw a flow chart below for the process of paying your fees at ACTB
BSBMGT608 Manage innovation and continuous improvement and BSBMGT619 Identify and implement business innovation -
Assessment Pack - Version September 2017 Page 8 of 24
external sources from where we can gather information about business markets, customers and
methods
i. Websites
ii. Books and publications
iii. Seminars and meetings
b. Do you think the structure and goals of ACTB allows for innovation (in terms of changing
processes, relationships and methods)? Why or why not?
c. Compare ACTB’s culture versus traditional business models (for example, Qantas)
d. List three legal, ethical and security issues related to ACTB’s innovation plan?
e. Draw a flow chart below for the process of paying your fees at ACTB
BSBMGT608 Manage innovation and continuous improvement and BSBMGT619 Identify and implement business innovation -
Assessment Pack - Version September 2017 Page 8 of 24
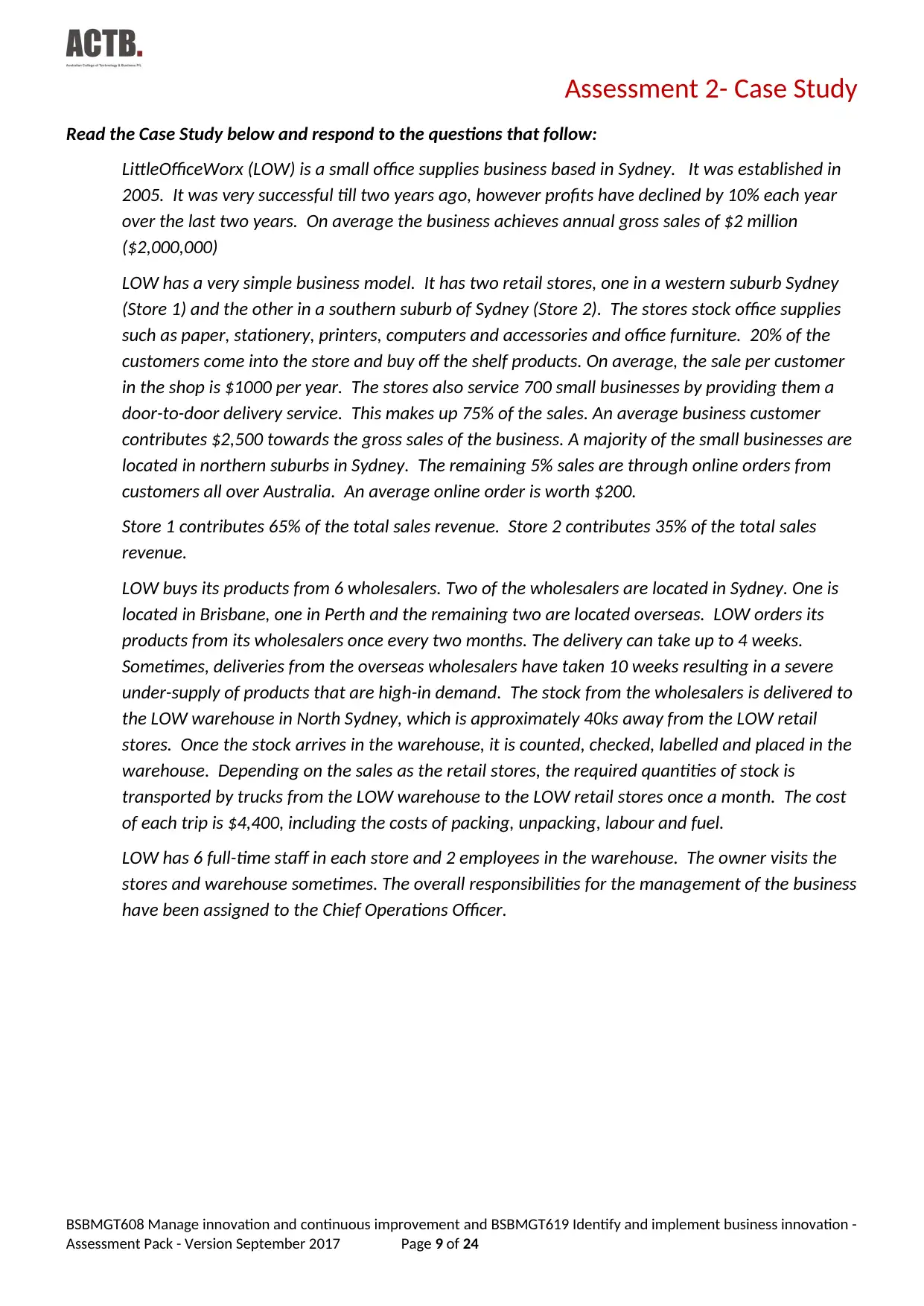
Assessment 2- Case Study
Read the Case Study below and respond to the questions that follow:
LittleOfficeWorx (LOW) is a small office supplies business based in Sydney. It was established in
2005. It was very successful till two years ago, however profits have declined by 10% each year
over the last two years. On average the business achieves annual gross sales of $2 million
($2,000,000)
LOW has a very simple business model. It has two retail stores, one in a western suburb Sydney
(Store 1) and the other in a southern suburb of Sydney (Store 2). The stores stock office supplies
such as paper, stationery, printers, computers and accessories and office furniture. 20% of the
customers come into the store and buy off the shelf products. On average, the sale per customer
in the shop is $1000 per year. The stores also service 700 small businesses by providing them a
door-to-door delivery service. This makes up 75% of the sales. An average business customer
contributes $2,500 towards the gross sales of the business. A majority of the small businesses are
located in northern suburbs in Sydney. The remaining 5% sales are through online orders from
customers all over Australia. An average online order is worth $200.
Store 1 contributes 65% of the total sales revenue. Store 2 contributes 35% of the total sales
revenue.
LOW buys its products from 6 wholesalers. Two of the wholesalers are located in Sydney. One is
located in Brisbane, one in Perth and the remaining two are located overseas. LOW orders its
products from its wholesalers once every two months. The delivery can take up to 4 weeks.
Sometimes, deliveries from the overseas wholesalers have taken 10 weeks resulting in a severe
under-supply of products that are high-in demand. The stock from the wholesalers is delivered to
the LOW warehouse in North Sydney, which is approximately 40ks away from the LOW retail
stores. Once the stock arrives in the warehouse, it is counted, checked, labelled and placed in the
warehouse. Depending on the sales as the retail stores, the required quantities of stock is
transported by trucks from the LOW warehouse to the LOW retail stores once a month. The cost
of each trip is $4,400, including the costs of packing, unpacking, labour and fuel.
LOW has 6 full-time staff in each store and 2 employees in the warehouse. The owner visits the
stores and warehouse sometimes. The overall responsibilities for the management of the business
have been assigned to the Chief Operations Officer.
BSBMGT608 Manage innovation and continuous improvement and BSBMGT619 Identify and implement business innovation -
Assessment Pack - Version September 2017 Page 9 of 24
Read the Case Study below and respond to the questions that follow:
LittleOfficeWorx (LOW) is a small office supplies business based in Sydney. It was established in
2005. It was very successful till two years ago, however profits have declined by 10% each year
over the last two years. On average the business achieves annual gross sales of $2 million
($2,000,000)
LOW has a very simple business model. It has two retail stores, one in a western suburb Sydney
(Store 1) and the other in a southern suburb of Sydney (Store 2). The stores stock office supplies
such as paper, stationery, printers, computers and accessories and office furniture. 20% of the
customers come into the store and buy off the shelf products. On average, the sale per customer
in the shop is $1000 per year. The stores also service 700 small businesses by providing them a
door-to-door delivery service. This makes up 75% of the sales. An average business customer
contributes $2,500 towards the gross sales of the business. A majority of the small businesses are
located in northern suburbs in Sydney. The remaining 5% sales are through online orders from
customers all over Australia. An average online order is worth $200.
Store 1 contributes 65% of the total sales revenue. Store 2 contributes 35% of the total sales
revenue.
LOW buys its products from 6 wholesalers. Two of the wholesalers are located in Sydney. One is
located in Brisbane, one in Perth and the remaining two are located overseas. LOW orders its
products from its wholesalers once every two months. The delivery can take up to 4 weeks.
Sometimes, deliveries from the overseas wholesalers have taken 10 weeks resulting in a severe
under-supply of products that are high-in demand. The stock from the wholesalers is delivered to
the LOW warehouse in North Sydney, which is approximately 40ks away from the LOW retail
stores. Once the stock arrives in the warehouse, it is counted, checked, labelled and placed in the
warehouse. Depending on the sales as the retail stores, the required quantities of stock is
transported by trucks from the LOW warehouse to the LOW retail stores once a month. The cost
of each trip is $4,400, including the costs of packing, unpacking, labour and fuel.
LOW has 6 full-time staff in each store and 2 employees in the warehouse. The owner visits the
stores and warehouse sometimes. The overall responsibilities for the management of the business
have been assigned to the Chief Operations Officer.
BSBMGT608 Manage innovation and continuous improvement and BSBMGT619 Identify and implement business innovation -
Assessment Pack - Version September 2017 Page 9 of 24
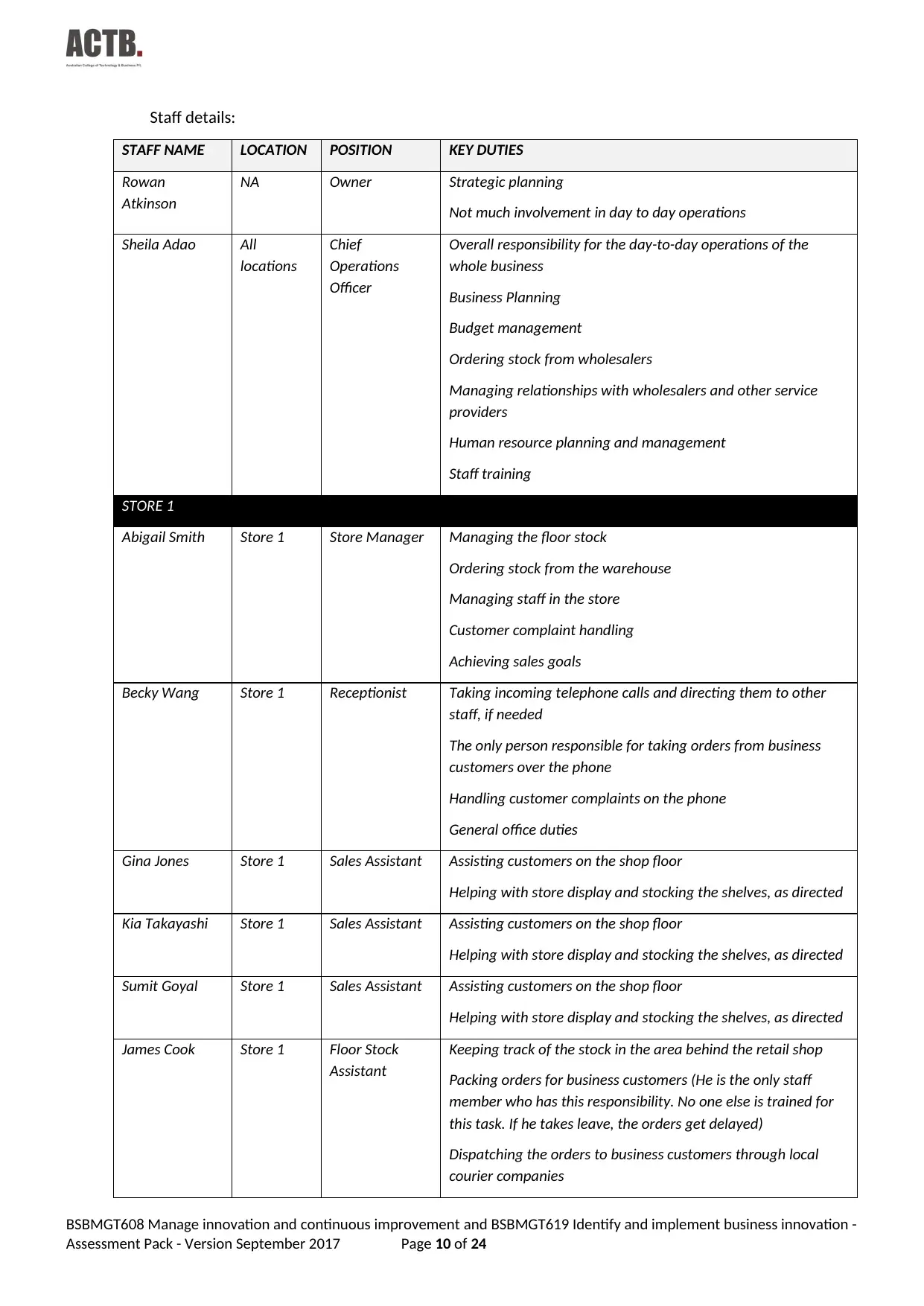
Staff details:
STAFF NAME LOCATION POSITION KEY DUTIES
Rowan
Atkinson
NA Owner Strategic planning
Not much involvement in day to day operations
Sheila Adao All
locations
Chief
Operations
Officer
Overall responsibility for the day-to-day operations of the
whole business
Business Planning
Budget management
Ordering stock from wholesalers
Managing relationships with wholesalers and other service
providers
Human resource planning and management
Staff training
STORE 1
Abigail Smith Store 1 Store Manager Managing the floor stock
Ordering stock from the warehouse
Managing staff in the store
Customer complaint handling
Achieving sales goals
Becky Wang Store 1 Receptionist Taking incoming telephone calls and directing them to other
staff, if needed
The only person responsible for taking orders from business
customers over the phone
Handling customer complaints on the phone
General office duties
Gina Jones Store 1 Sales Assistant Assisting customers on the shop floor
Helping with store display and stocking the shelves, as directed
Kia Takayashi Store 1 Sales Assistant Assisting customers on the shop floor
Helping with store display and stocking the shelves, as directed
Sumit Goyal Store 1 Sales Assistant Assisting customers on the shop floor
Helping with store display and stocking the shelves, as directed
James Cook Store 1 Floor Stock
Assistant
Keeping track of the stock in the area behind the retail shop
Packing orders for business customers (He is the only staff
member who has this responsibility. No one else is trained for
this task. If he takes leave, the orders get delayed)
Dispatching the orders to business customers through local
courier companies
BSBMGT608 Manage innovation and continuous improvement and BSBMGT619 Identify and implement business innovation -
Assessment Pack - Version September 2017 Page 10 of 24
STAFF NAME LOCATION POSITION KEY DUTIES
Rowan
Atkinson
NA Owner Strategic planning
Not much involvement in day to day operations
Sheila Adao All
locations
Chief
Operations
Officer
Overall responsibility for the day-to-day operations of the
whole business
Business Planning
Budget management
Ordering stock from wholesalers
Managing relationships with wholesalers and other service
providers
Human resource planning and management
Staff training
STORE 1
Abigail Smith Store 1 Store Manager Managing the floor stock
Ordering stock from the warehouse
Managing staff in the store
Customer complaint handling
Achieving sales goals
Becky Wang Store 1 Receptionist Taking incoming telephone calls and directing them to other
staff, if needed
The only person responsible for taking orders from business
customers over the phone
Handling customer complaints on the phone
General office duties
Gina Jones Store 1 Sales Assistant Assisting customers on the shop floor
Helping with store display and stocking the shelves, as directed
Kia Takayashi Store 1 Sales Assistant Assisting customers on the shop floor
Helping with store display and stocking the shelves, as directed
Sumit Goyal Store 1 Sales Assistant Assisting customers on the shop floor
Helping with store display and stocking the shelves, as directed
James Cook Store 1 Floor Stock
Assistant
Keeping track of the stock in the area behind the retail shop
Packing orders for business customers (He is the only staff
member who has this responsibility. No one else is trained for
this task. If he takes leave, the orders get delayed)
Dispatching the orders to business customers through local
courier companies
BSBMGT608 Manage innovation and continuous improvement and BSBMGT619 Identify and implement business innovation -
Assessment Pack - Version September 2017 Page 10 of 24
Secure Best Marks with AI Grader
Need help grading? Try our AI Grader for instant feedback on your assignments.
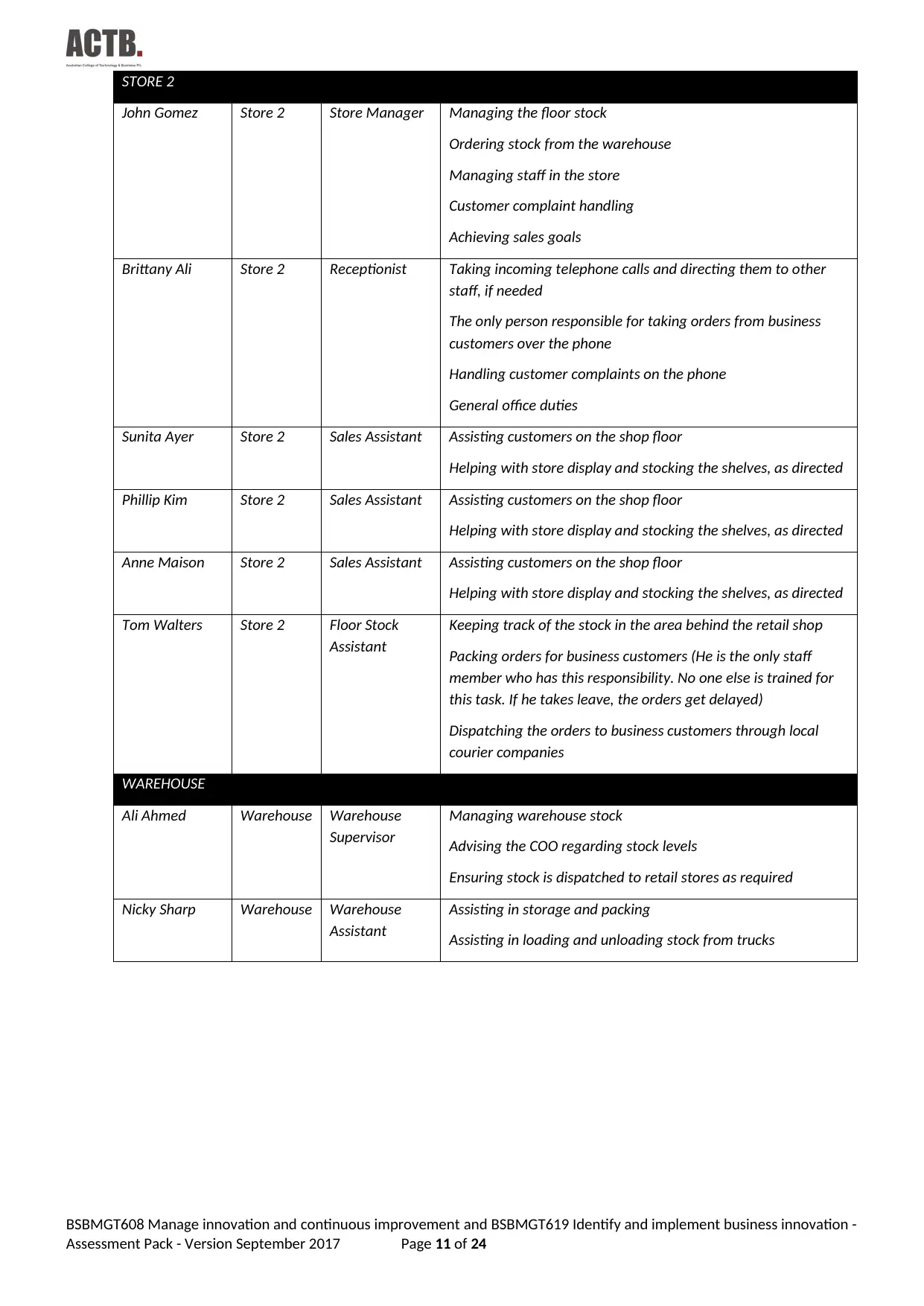
STORE 2
John Gomez Store 2 Store Manager Managing the floor stock
Ordering stock from the warehouse
Managing staff in the store
Customer complaint handling
Achieving sales goals
Brittany Ali Store 2 Receptionist Taking incoming telephone calls and directing them to other
staff, if needed
The only person responsible for taking orders from business
customers over the phone
Handling customer complaints on the phone
General office duties
Sunita Ayer Store 2 Sales Assistant Assisting customers on the shop floor
Helping with store display and stocking the shelves, as directed
Phillip Kim Store 2 Sales Assistant Assisting customers on the shop floor
Helping with store display and stocking the shelves, as directed
Anne Maison Store 2 Sales Assistant Assisting customers on the shop floor
Helping with store display and stocking the shelves, as directed
Tom Walters Store 2 Floor Stock
Assistant
Keeping track of the stock in the area behind the retail shop
Packing orders for business customers (He is the only staff
member who has this responsibility. No one else is trained for
this task. If he takes leave, the orders get delayed)
Dispatching the orders to business customers through local
courier companies
WAREHOUSE
Ali Ahmed Warehouse Warehouse
Supervisor
Managing warehouse stock
Advising the COO regarding stock levels
Ensuring stock is dispatched to retail stores as required
Nicky Sharp Warehouse Warehouse
Assistant
Assisting in storage and packing
Assisting in loading and unloading stock from trucks
BSBMGT608 Manage innovation and continuous improvement and BSBMGT619 Identify and implement business innovation -
Assessment Pack - Version September 2017 Page 11 of 24
John Gomez Store 2 Store Manager Managing the floor stock
Ordering stock from the warehouse
Managing staff in the store
Customer complaint handling
Achieving sales goals
Brittany Ali Store 2 Receptionist Taking incoming telephone calls and directing them to other
staff, if needed
The only person responsible for taking orders from business
customers over the phone
Handling customer complaints on the phone
General office duties
Sunita Ayer Store 2 Sales Assistant Assisting customers on the shop floor
Helping with store display and stocking the shelves, as directed
Phillip Kim Store 2 Sales Assistant Assisting customers on the shop floor
Helping with store display and stocking the shelves, as directed
Anne Maison Store 2 Sales Assistant Assisting customers on the shop floor
Helping with store display and stocking the shelves, as directed
Tom Walters Store 2 Floor Stock
Assistant
Keeping track of the stock in the area behind the retail shop
Packing orders for business customers (He is the only staff
member who has this responsibility. No one else is trained for
this task. If he takes leave, the orders get delayed)
Dispatching the orders to business customers through local
courier companies
WAREHOUSE
Ali Ahmed Warehouse Warehouse
Supervisor
Managing warehouse stock
Advising the COO regarding stock levels
Ensuring stock is dispatched to retail stores as required
Nicky Sharp Warehouse Warehouse
Assistant
Assisting in storage and packing
Assisting in loading and unloading stock from trucks
BSBMGT608 Manage innovation and continuous improvement and BSBMGT619 Identify and implement business innovation -
Assessment Pack - Version September 2017 Page 11 of 24
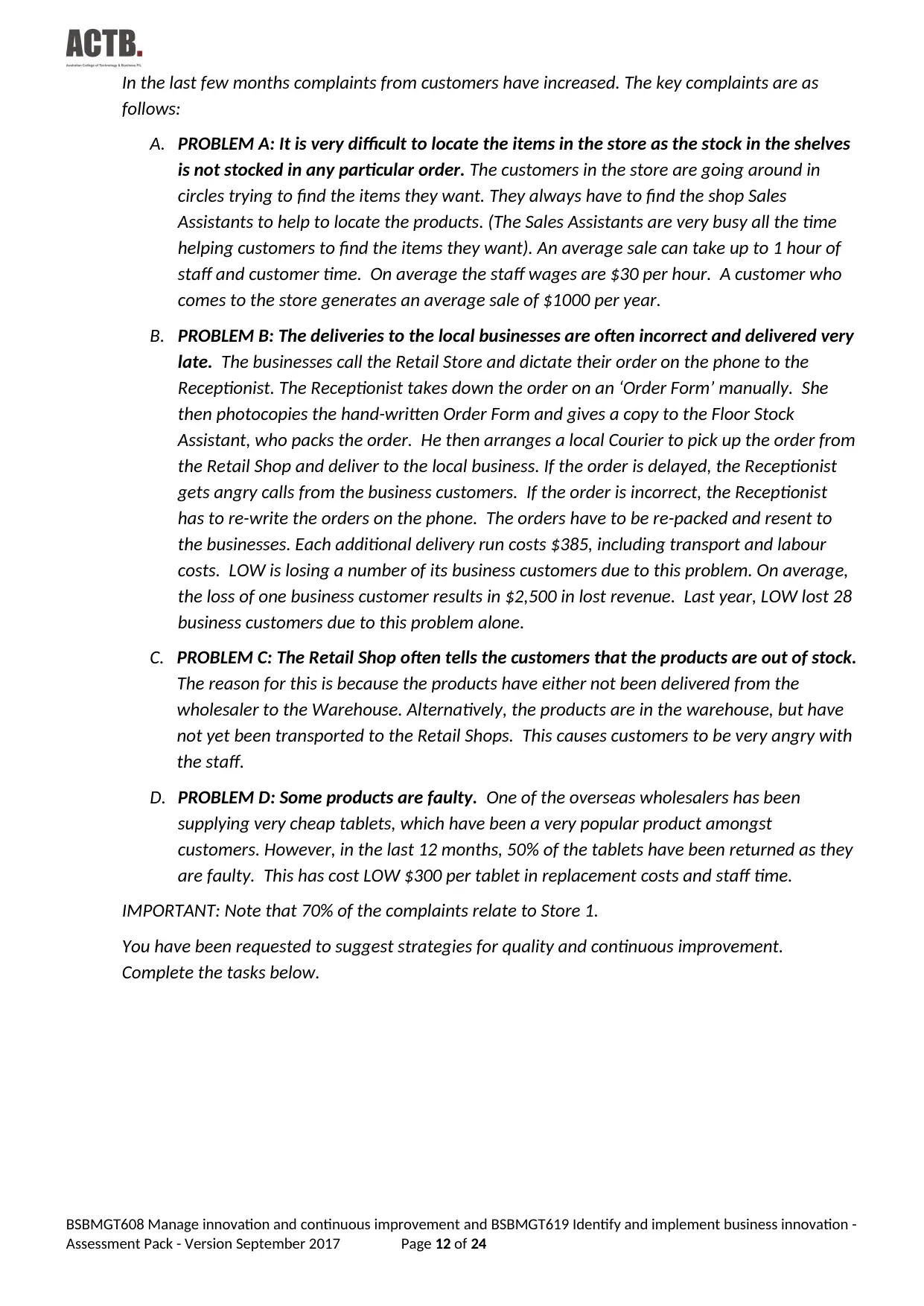
In the last few months complaints from customers have increased. The key complaints are as
follows:
A. PROBLEM A: It is very difficult to locate the items in the store as the stock in the shelves
is not stocked in any particular order. The customers in the store are going around in
circles trying to find the items they want. They always have to find the shop Sales
Assistants to help to locate the products. (The Sales Assistants are very busy all the time
helping customers to find the items they want). An average sale can take up to 1 hour of
staff and customer time. On average the staff wages are $30 per hour. A customer who
comes to the store generates an average sale of $1000 per year.
B. PROBLEM B: The deliveries to the local businesses are often incorrect and delivered very
late. The businesses call the Retail Store and dictate their order on the phone to the
Receptionist. The Receptionist takes down the order on an ‘Order Form’ manually. She
then photocopies the hand-written Order Form and gives a copy to the Floor Stock
Assistant, who packs the order. He then arranges a local Courier to pick up the order from
the Retail Shop and deliver to the local business. If the order is delayed, the Receptionist
gets angry calls from the business customers. If the order is incorrect, the Receptionist
has to re-write the orders on the phone. The orders have to be re-packed and resent to
the businesses. Each additional delivery run costs $385, including transport and labour
costs. LOW is losing a number of its business customers due to this problem. On average,
the loss of one business customer results in $2,500 in lost revenue. Last year, LOW lost 28
business customers due to this problem alone.
C. PROBLEM C: The Retail Shop often tells the customers that the products are out of stock.
The reason for this is because the products have either not been delivered from the
wholesaler to the Warehouse. Alternatively, the products are in the warehouse, but have
not yet been transported to the Retail Shops. This causes customers to be very angry with
the staff.
D. PROBLEM D: Some products are faulty. One of the overseas wholesalers has been
supplying very cheap tablets, which have been a very popular product amongst
customers. However, in the last 12 months, 50% of the tablets have been returned as they
are faulty. This has cost LOW $300 per tablet in replacement costs and staff time.
IMPORTANT: Note that 70% of the complaints relate to Store 1.
You have been requested to suggest strategies for quality and continuous improvement.
Complete the tasks below.
BSBMGT608 Manage innovation and continuous improvement and BSBMGT619 Identify and implement business innovation -
Assessment Pack - Version September 2017 Page 12 of 24
follows:
A. PROBLEM A: It is very difficult to locate the items in the store as the stock in the shelves
is not stocked in any particular order. The customers in the store are going around in
circles trying to find the items they want. They always have to find the shop Sales
Assistants to help to locate the products. (The Sales Assistants are very busy all the time
helping customers to find the items they want). An average sale can take up to 1 hour of
staff and customer time. On average the staff wages are $30 per hour. A customer who
comes to the store generates an average sale of $1000 per year.
B. PROBLEM B: The deliveries to the local businesses are often incorrect and delivered very
late. The businesses call the Retail Store and dictate their order on the phone to the
Receptionist. The Receptionist takes down the order on an ‘Order Form’ manually. She
then photocopies the hand-written Order Form and gives a copy to the Floor Stock
Assistant, who packs the order. He then arranges a local Courier to pick up the order from
the Retail Shop and deliver to the local business. If the order is delayed, the Receptionist
gets angry calls from the business customers. If the order is incorrect, the Receptionist
has to re-write the orders on the phone. The orders have to be re-packed and resent to
the businesses. Each additional delivery run costs $385, including transport and labour
costs. LOW is losing a number of its business customers due to this problem. On average,
the loss of one business customer results in $2,500 in lost revenue. Last year, LOW lost 28
business customers due to this problem alone.
C. PROBLEM C: The Retail Shop often tells the customers that the products are out of stock.
The reason for this is because the products have either not been delivered from the
wholesaler to the Warehouse. Alternatively, the products are in the warehouse, but have
not yet been transported to the Retail Shops. This causes customers to be very angry with
the staff.
D. PROBLEM D: Some products are faulty. One of the overseas wholesalers has been
supplying very cheap tablets, which have been a very popular product amongst
customers. However, in the last 12 months, 50% of the tablets have been returned as they
are faulty. This has cost LOW $300 per tablet in replacement costs and staff time.
IMPORTANT: Note that 70% of the complaints relate to Store 1.
You have been requested to suggest strategies for quality and continuous improvement.
Complete the tasks below.
BSBMGT608 Manage innovation and continuous improvement and BSBMGT619 Identify and implement business innovation -
Assessment Pack - Version September 2017 Page 12 of 24
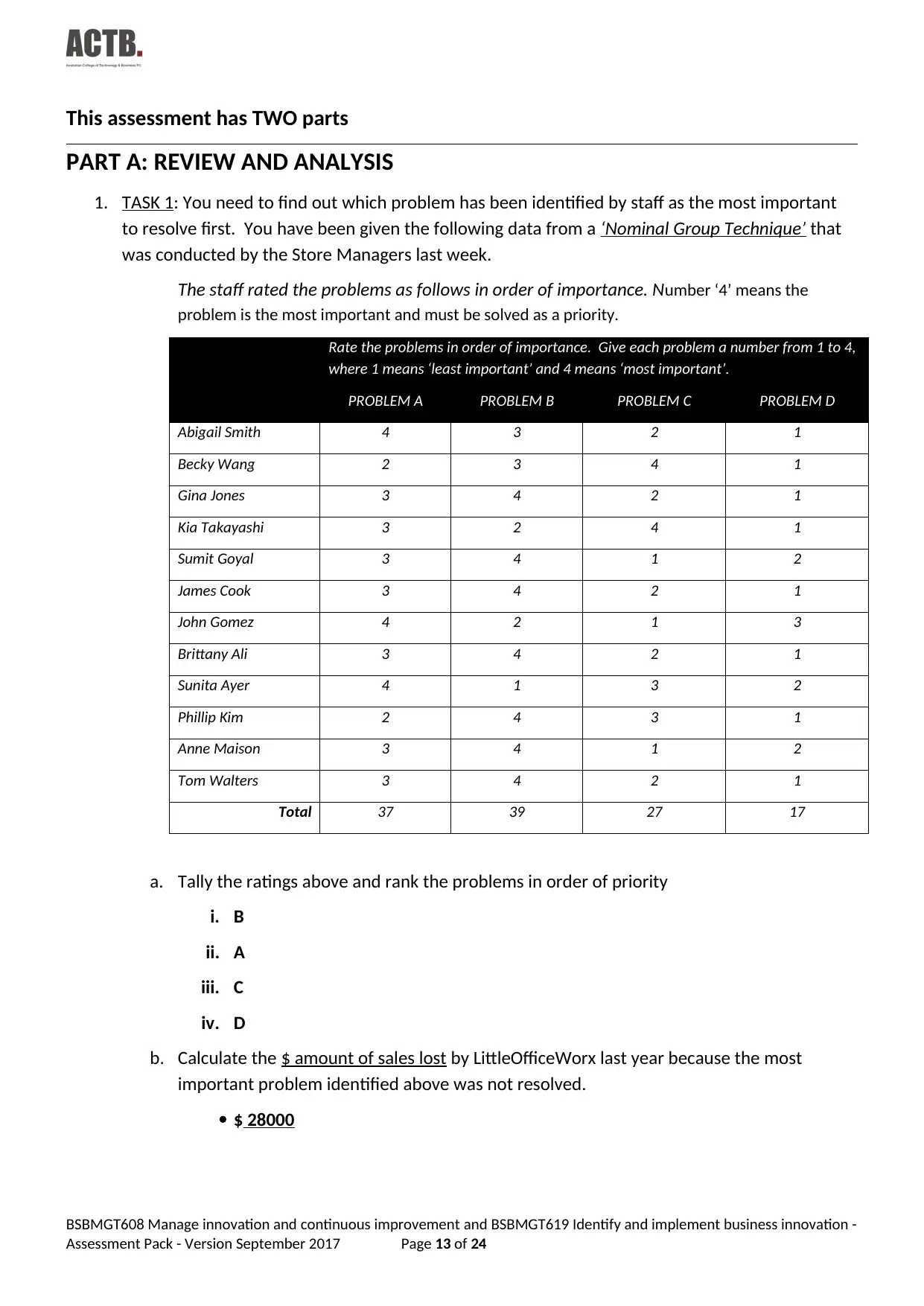
This assessment has TWO parts
PART A: REVIEW AND ANALYSIS
1. TASK 1: You need to find out which problem has been identified by staff as the most important
to resolve first. You have been given the following data from a ‘Nominal Group Technique’ that
was conducted by the Store Managers last week.
The staff rated the problems as follows in order of importance. Number ‘4’ means the
problem is the most important and must be solved as a priority.
Rate the problems in order of importance. Give each problem a number from 1 to 4,
where 1 means ‘least important’ and 4 means ‘most important’.
PROBLEM A PROBLEM B PROBLEM C PROBLEM D
Abigail Smith 4 3 2 1
Becky Wang 2 3 4 1
Gina Jones 3 4 2 1
Kia Takayashi 3 2 4 1
Sumit Goyal 3 4 1 2
James Cook 3 4 2 1
John Gomez 4 2 1 3
Brittany Ali 3 4 2 1
Sunita Ayer 4 1 3 2
Phillip Kim 2 4 3 1
Anne Maison 3 4 1 2
Tom Walters 3 4 2 1
Total 37 39 27 17
a. Tally the ratings above and rank the problems in order of priority
i. B
ii. A
iii. C
iv. D
b. Calculate the $ amount of sales lost by LittleOfficeWorx last year because the most
important problem identified above was not resolved.
$ 28000
BSBMGT608 Manage innovation and continuous improvement and BSBMGT619 Identify and implement business innovation -
Assessment Pack - Version September 2017 Page 13 of 24
PART A: REVIEW AND ANALYSIS
1. TASK 1: You need to find out which problem has been identified by staff as the most important
to resolve first. You have been given the following data from a ‘Nominal Group Technique’ that
was conducted by the Store Managers last week.
The staff rated the problems as follows in order of importance. Number ‘4’ means the
problem is the most important and must be solved as a priority.
Rate the problems in order of importance. Give each problem a number from 1 to 4,
where 1 means ‘least important’ and 4 means ‘most important’.
PROBLEM A PROBLEM B PROBLEM C PROBLEM D
Abigail Smith 4 3 2 1
Becky Wang 2 3 4 1
Gina Jones 3 4 2 1
Kia Takayashi 3 2 4 1
Sumit Goyal 3 4 1 2
James Cook 3 4 2 1
John Gomez 4 2 1 3
Brittany Ali 3 4 2 1
Sunita Ayer 4 1 3 2
Phillip Kim 2 4 3 1
Anne Maison 3 4 1 2
Tom Walters 3 4 2 1
Total 37 39 27 17
a. Tally the ratings above and rank the problems in order of priority
i. B
ii. A
iii. C
iv. D
b. Calculate the $ amount of sales lost by LittleOfficeWorx last year because the most
important problem identified above was not resolved.
$ 28000
BSBMGT608 Manage innovation and continuous improvement and BSBMGT619 Identify and implement business innovation -
Assessment Pack - Version September 2017 Page 13 of 24
Paraphrase This Document
Need a fresh take? Get an instant paraphrase of this document with our AI Paraphraser
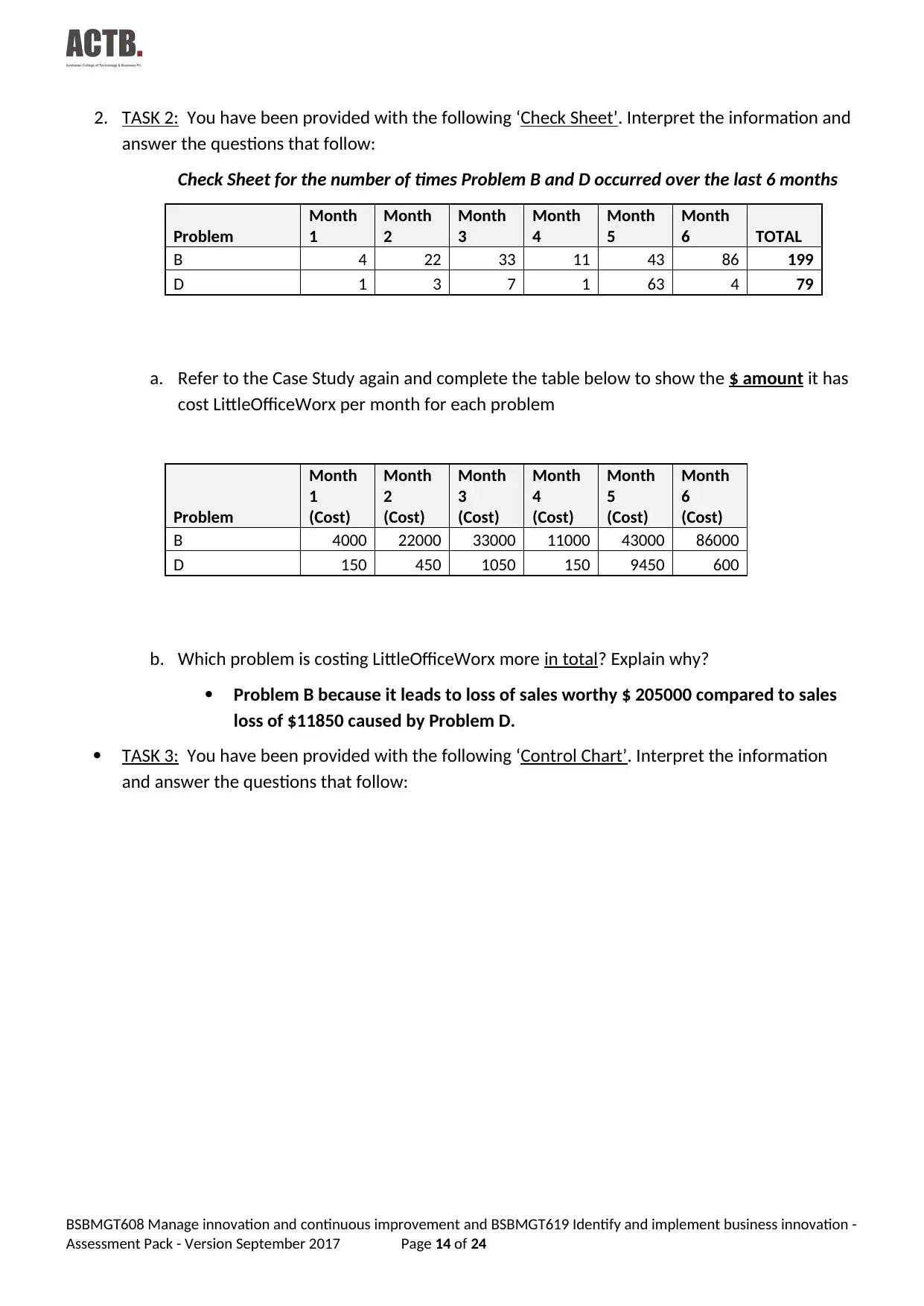
2. TASK 2: You have been provided with the following ‘Check Sheet’. Interpret the information and
answer the questions that follow:
Check Sheet for the number of times Problem B and D occurred over the last 6 months
Problem
Month
1
Month
2
Month
3
Month
4
Month
5
Month
6 TOTAL
B 4 22 33 11 43 86 199
D 1 3 7 1 63 4 79
a. Refer to the Case Study again and complete the table below to show the $ amount it has
cost LittleOfficeWorx per month for each problem
Problem
Month
1
(Cost)
Month
2
(Cost)
Month
3
(Cost)
Month
4
(Cost)
Month
5
(Cost)
Month
6
(Cost)
B 4000 22000 33000 11000 43000 86000
D 150 450 1050 150 9450 600
b. Which problem is costing LittleOfficeWorx more in total? Explain why?
Problem B because it leads to loss of sales worthy $ 205000 compared to sales
loss of $11850 caused by Problem D.
TASK 3: You have been provided with the following ‘Control Chart’. Interpret the information
and answer the questions that follow:
BSBMGT608 Manage innovation and continuous improvement and BSBMGT619 Identify and implement business innovation -
Assessment Pack - Version September 2017 Page 14 of 24
answer the questions that follow:
Check Sheet for the number of times Problem B and D occurred over the last 6 months
Problem
Month
1
Month
2
Month
3
Month
4
Month
5
Month
6 TOTAL
B 4 22 33 11 43 86 199
D 1 3 7 1 63 4 79
a. Refer to the Case Study again and complete the table below to show the $ amount it has
cost LittleOfficeWorx per month for each problem
Problem
Month
1
(Cost)
Month
2
(Cost)
Month
3
(Cost)
Month
4
(Cost)
Month
5
(Cost)
Month
6
(Cost)
B 4000 22000 33000 11000 43000 86000
D 150 450 1050 150 9450 600
b. Which problem is costing LittleOfficeWorx more in total? Explain why?
Problem B because it leads to loss of sales worthy $ 205000 compared to sales
loss of $11850 caused by Problem D.
TASK 3: You have been provided with the following ‘Control Chart’. Interpret the information
and answer the questions that follow:
BSBMGT608 Manage innovation and continuous improvement and BSBMGT619 Identify and implement business innovation -
Assessment Pack - Version September 2017 Page 14 of 24
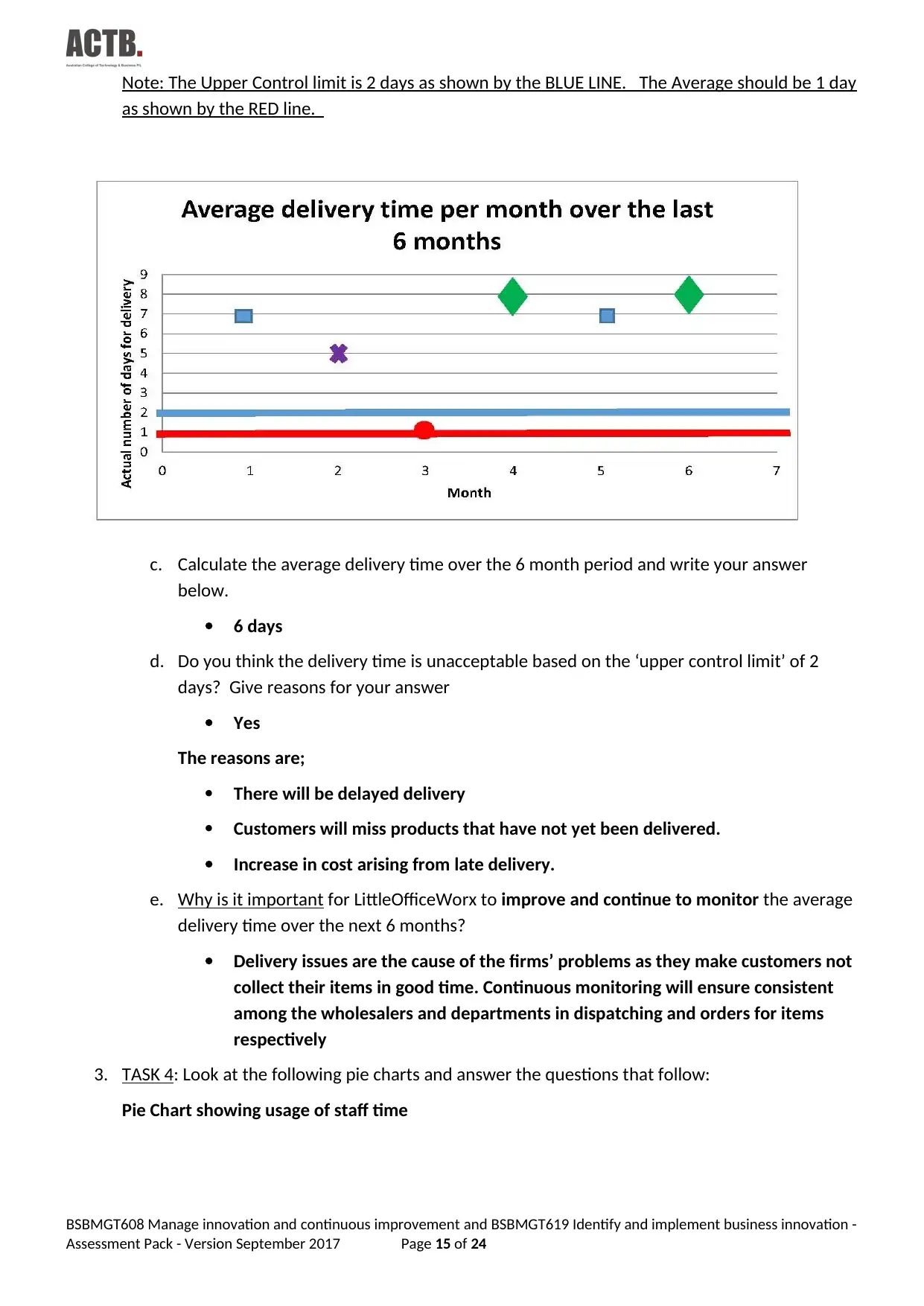
Note: The Upper Control limit is 2 days as shown by the BLUE LINE. The Average should be 1 day
as shown by the RED line.
c. Calculate the average delivery time over the 6 month period and write your answer
below.
6 days
d. Do you think the delivery time is unacceptable based on the ‘upper control limit’ of 2
days? Give reasons for your answer
Yes
The reasons are;
There will be delayed delivery
Customers will miss products that have not yet been delivered.
Increase in cost arising from late delivery.
e. Why is it important for LittleOfficeWorx to improve and continue to monitor the average
delivery time over the next 6 months?
Delivery issues are the cause of the firms’ problems as they make customers not
collect their items in good time. Continuous monitoring will ensure consistent
among the wholesalers and departments in dispatching and orders for items
respectively
3. TASK 4: Look at the following pie charts and answer the questions that follow:
Pie Chart showing usage of staff time
BSBMGT608 Manage innovation and continuous improvement and BSBMGT619 Identify and implement business innovation -
Assessment Pack - Version September 2017 Page 15 of 24
as shown by the RED line.
c. Calculate the average delivery time over the 6 month period and write your answer
below.
6 days
d. Do you think the delivery time is unacceptable based on the ‘upper control limit’ of 2
days? Give reasons for your answer
Yes
The reasons are;
There will be delayed delivery
Customers will miss products that have not yet been delivered.
Increase in cost arising from late delivery.
e. Why is it important for LittleOfficeWorx to improve and continue to monitor the average
delivery time over the next 6 months?
Delivery issues are the cause of the firms’ problems as they make customers not
collect their items in good time. Continuous monitoring will ensure consistent
among the wholesalers and departments in dispatching and orders for items
respectively
3. TASK 4: Look at the following pie charts and answer the questions that follow:
Pie Chart showing usage of staff time
BSBMGT608 Manage innovation and continuous improvement and BSBMGT619 Identify and implement business innovation -
Assessment Pack - Version September 2017 Page 15 of 24
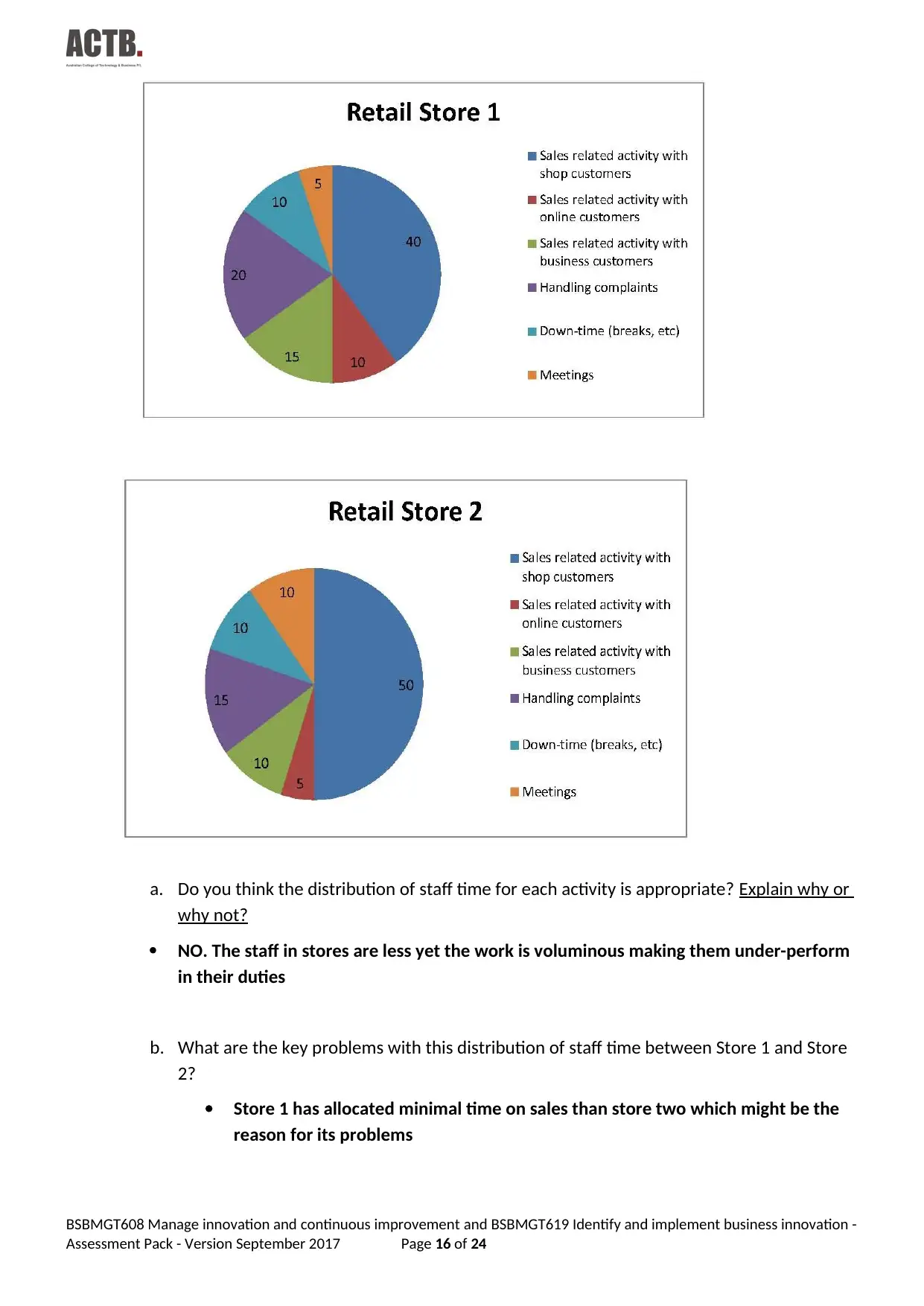
a. Do you think the distribution of staff time for each activity is appropriate? Explain why or
why not?
NO. The staff in stores are less yet the work is voluminous making them under-perform
in their duties
b. What are the key problems with this distribution of staff time between Store 1 and Store
2?
Store 1 has allocated minimal time on sales than store two which might be the
reason for its problems
BSBMGT608 Manage innovation and continuous improvement and BSBMGT619 Identify and implement business innovation -
Assessment Pack - Version September 2017 Page 16 of 24
why not?
NO. The staff in stores are less yet the work is voluminous making them under-perform
in their duties
b. What are the key problems with this distribution of staff time between Store 1 and Store
2?
Store 1 has allocated minimal time on sales than store two which might be the
reason for its problems
BSBMGT608 Manage innovation and continuous improvement and BSBMGT619 Identify and implement business innovation -
Assessment Pack - Version September 2017 Page 16 of 24
Secure Best Marks with AI Grader
Need help grading? Try our AI Grader for instant feedback on your assignments.
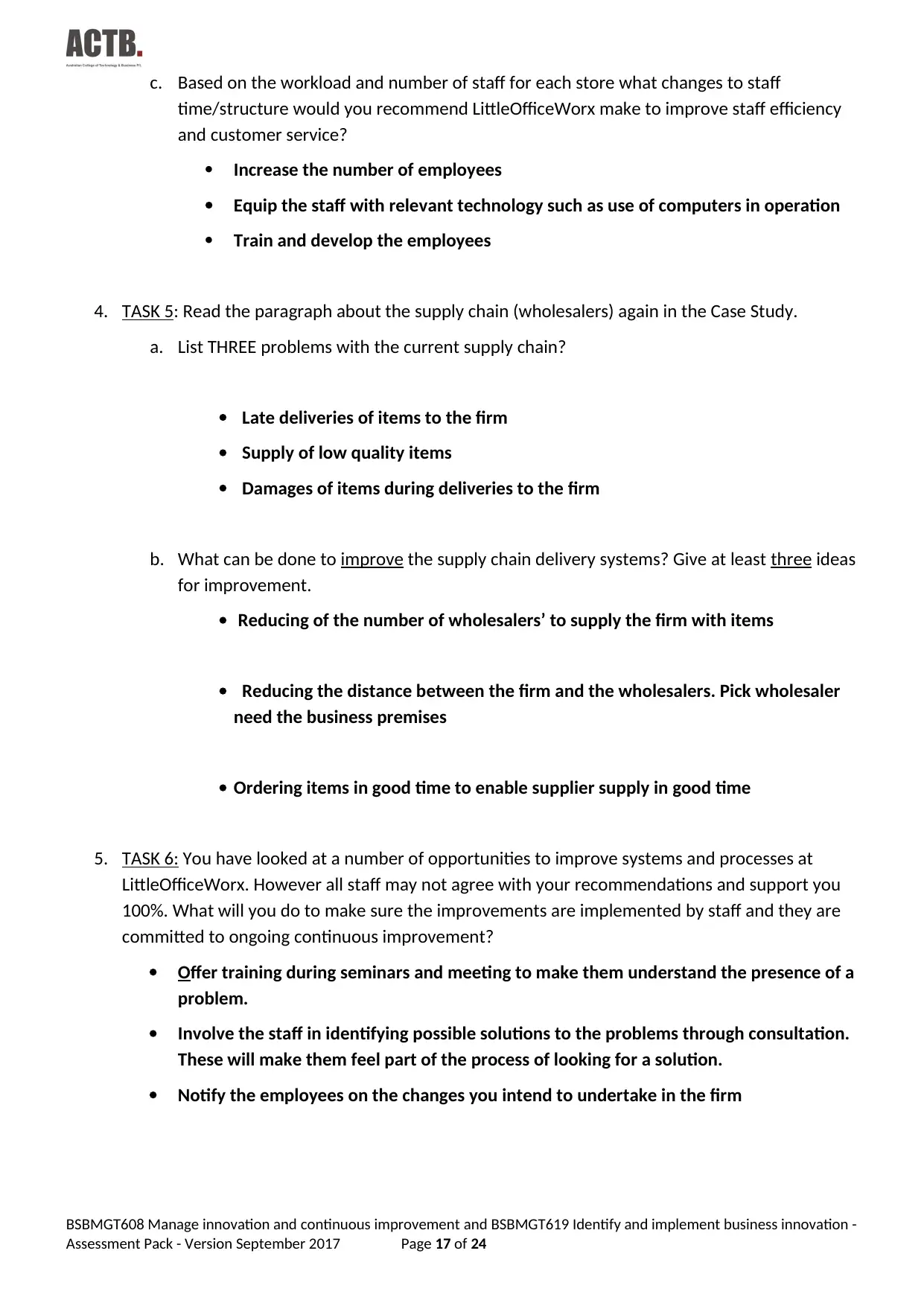
c. Based on the workload and number of staff for each store what changes to staff
time/structure would you recommend LittleOfficeWorx make to improve staff efficiency
and customer service?
Increase the number of employees
Equip the staff with relevant technology such as use of computers in operation
Train and develop the employees
4. TASK 5: Read the paragraph about the supply chain (wholesalers) again in the Case Study.
a. List THREE problems with the current supply chain?
Late deliveries of items to the firm
Supply of low quality items
Damages of items during deliveries to the firm
b. What can be done to improve the supply chain delivery systems? Give at least three ideas
for improvement.
Reducing of the number of wholesalers’ to supply the firm with items
Reducing the distance between the firm and the wholesalers. Pick wholesaler
need the business premises
Ordering items in good time to enable supplier supply in good time
5. TASK 6: You have looked at a number of opportunities to improve systems and processes at
LittleOfficeWorx. However all staff may not agree with your recommendations and support you
100%. What will you do to make sure the improvements are implemented by staff and they are
committed to ongoing continuous improvement?
Offer training during seminars and meeting to make them understand the presence of a
problem.
Involve the staff in identifying possible solutions to the problems through consultation.
These will make them feel part of the process of looking for a solution.
Notify the employees on the changes you intend to undertake in the firm
BSBMGT608 Manage innovation and continuous improvement and BSBMGT619 Identify and implement business innovation -
Assessment Pack - Version September 2017 Page 17 of 24
time/structure would you recommend LittleOfficeWorx make to improve staff efficiency
and customer service?
Increase the number of employees
Equip the staff with relevant technology such as use of computers in operation
Train and develop the employees
4. TASK 5: Read the paragraph about the supply chain (wholesalers) again in the Case Study.
a. List THREE problems with the current supply chain?
Late deliveries of items to the firm
Supply of low quality items
Damages of items during deliveries to the firm
b. What can be done to improve the supply chain delivery systems? Give at least three ideas
for improvement.
Reducing of the number of wholesalers’ to supply the firm with items
Reducing the distance between the firm and the wholesalers. Pick wholesaler
need the business premises
Ordering items in good time to enable supplier supply in good time
5. TASK 6: You have looked at a number of opportunities to improve systems and processes at
LittleOfficeWorx. However all staff may not agree with your recommendations and support you
100%. What will you do to make sure the improvements are implemented by staff and they are
committed to ongoing continuous improvement?
Offer training during seminars and meeting to make them understand the presence of a
problem.
Involve the staff in identifying possible solutions to the problems through consultation.
These will make them feel part of the process of looking for a solution.
Notify the employees on the changes you intend to undertake in the firm
BSBMGT608 Manage innovation and continuous improvement and BSBMGT619 Identify and implement business innovation -
Assessment Pack - Version September 2017 Page 17 of 24
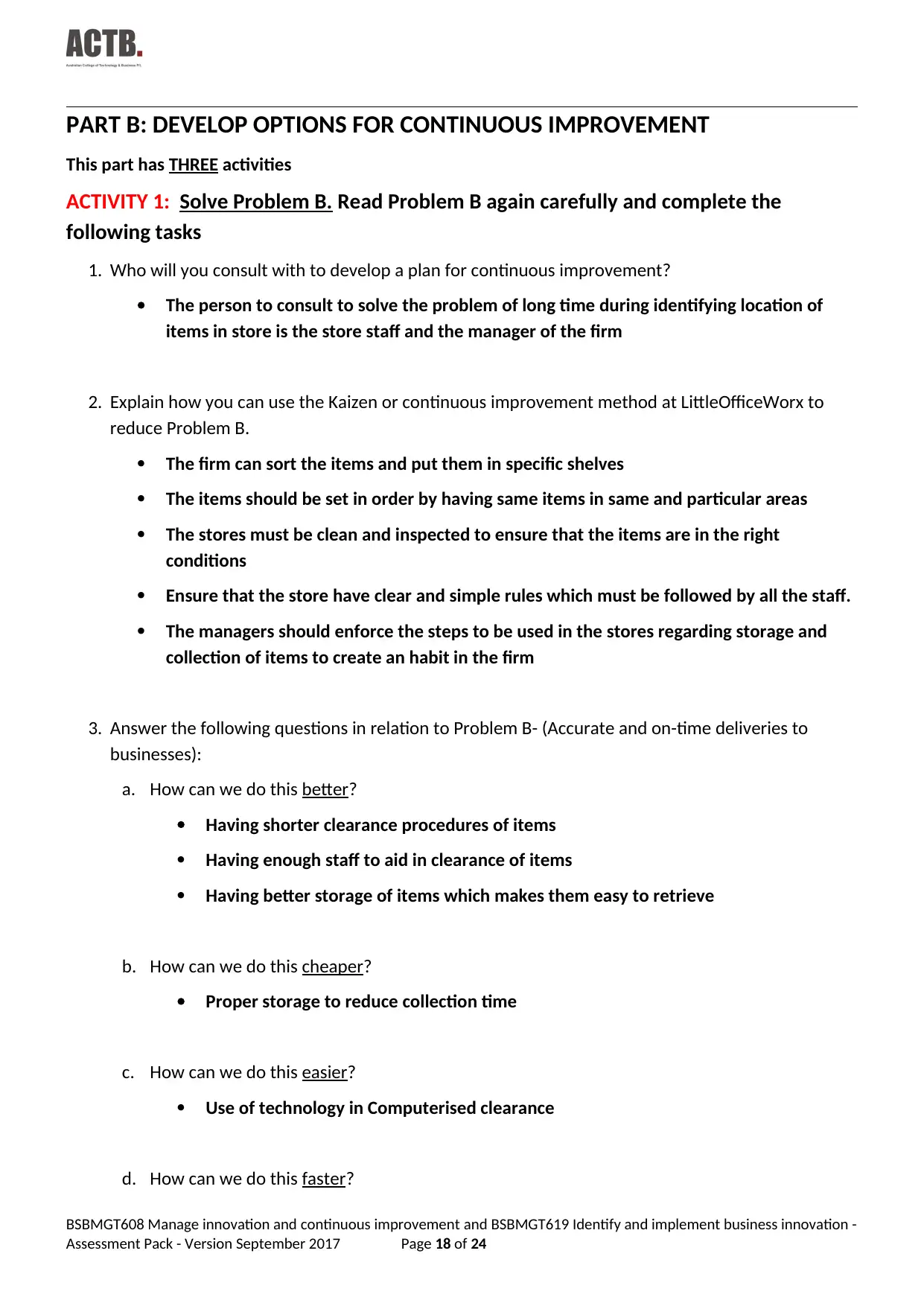
PART B: DEVELOP OPTIONS FOR CONTINUOUS IMPROVEMENT
This part has THREE activities
ACTIVITY 1: Solve Problem B. Read Problem B again carefully and complete the
following tasks
1. Who will you consult with to develop a plan for continuous improvement?
The person to consult to solve the problem of long time during identifying location of
items in store is the store staff and the manager of the firm
2. Explain how you can use the Kaizen or continuous improvement method at LittleOfficeWorx to
reduce Problem B.
The firm can sort the items and put them in specific shelves
The items should be set in order by having same items in same and particular areas
The stores must be clean and inspected to ensure that the items are in the right
conditions
Ensure that the store have clear and simple rules which must be followed by all the staff.
The managers should enforce the steps to be used in the stores regarding storage and
collection of items to create an habit in the firm
3. Answer the following questions in relation to Problem B- (Accurate and on-time deliveries to
businesses):
a. How can we do this better?
Having shorter clearance procedures of items
Having enough staff to aid in clearance of items
Having better storage of items which makes them easy to retrieve
b. How can we do this cheaper?
Proper storage to reduce collection time
c. How can we do this easier?
Use of technology in Computerised clearance
d. How can we do this faster?
BSBMGT608 Manage innovation and continuous improvement and BSBMGT619 Identify and implement business innovation -
Assessment Pack - Version September 2017 Page 18 of 24
This part has THREE activities
ACTIVITY 1: Solve Problem B. Read Problem B again carefully and complete the
following tasks
1. Who will you consult with to develop a plan for continuous improvement?
The person to consult to solve the problem of long time during identifying location of
items in store is the store staff and the manager of the firm
2. Explain how you can use the Kaizen or continuous improvement method at LittleOfficeWorx to
reduce Problem B.
The firm can sort the items and put them in specific shelves
The items should be set in order by having same items in same and particular areas
The stores must be clean and inspected to ensure that the items are in the right
conditions
Ensure that the store have clear and simple rules which must be followed by all the staff.
The managers should enforce the steps to be used in the stores regarding storage and
collection of items to create an habit in the firm
3. Answer the following questions in relation to Problem B- (Accurate and on-time deliveries to
businesses):
a. How can we do this better?
Having shorter clearance procedures of items
Having enough staff to aid in clearance of items
Having better storage of items which makes them easy to retrieve
b. How can we do this cheaper?
Proper storage to reduce collection time
c. How can we do this easier?
Use of technology in Computerised clearance
d. How can we do this faster?
BSBMGT608 Manage innovation and continuous improvement and BSBMGT619 Identify and implement business innovation -
Assessment Pack - Version September 2017 Page 18 of 24
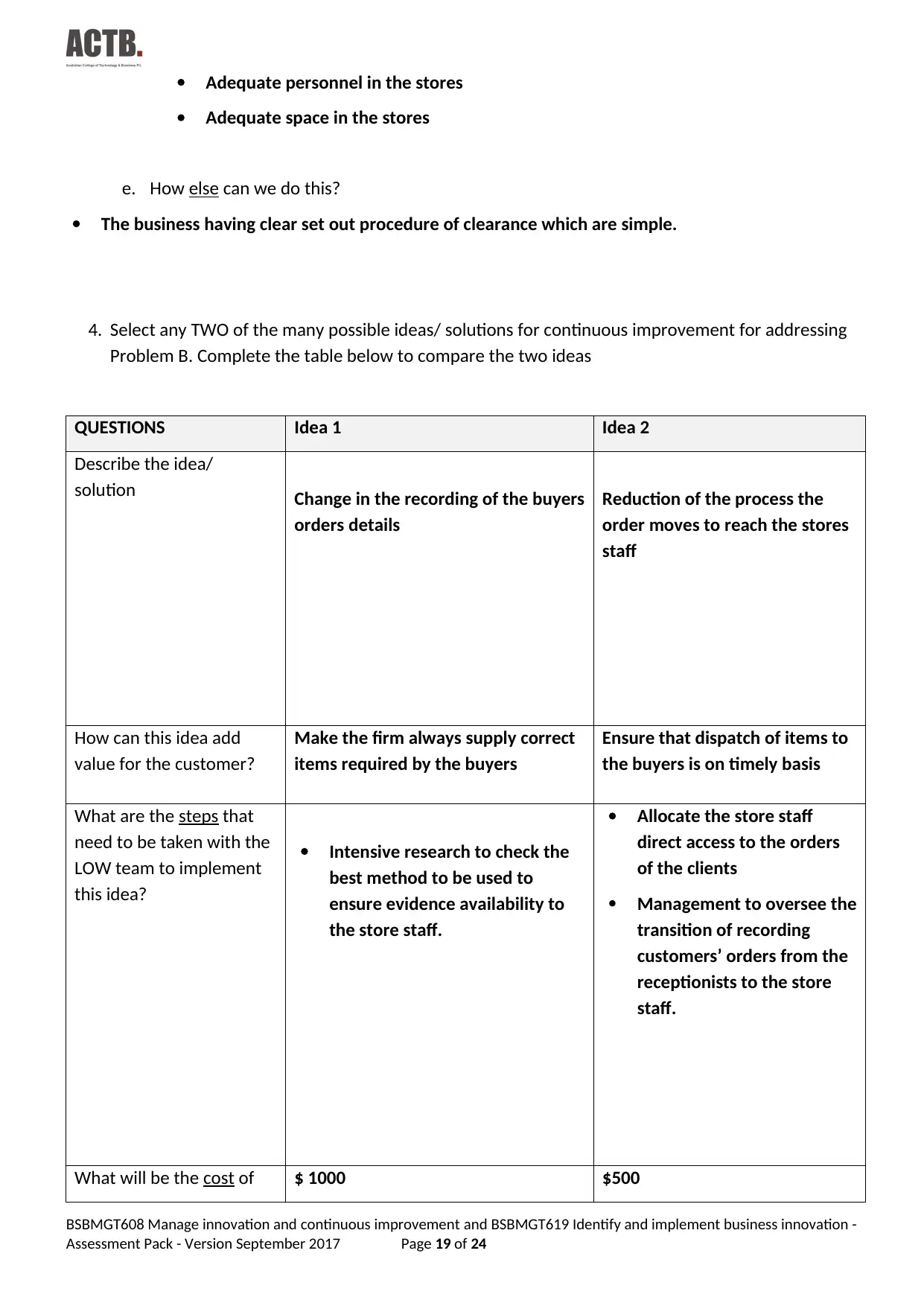
Adequate personnel in the stores
Adequate space in the stores
e. How else can we do this?
The business having clear set out procedure of clearance which are simple.
4. Select any TWO of the many possible ideas/ solutions for continuous improvement for addressing
Problem B. Complete the table below to compare the two ideas
QUESTIONS Idea 1 Idea 2
Describe the idea/
solution Change in the recording of the buyers
orders details
Reduction of the process the
order moves to reach the stores
staff
How can this idea add
value for the customer?
Make the firm always supply correct
items required by the buyers
Ensure that dispatch of items to
the buyers is on timely basis
What are the steps that
need to be taken with the
LOW team to implement
this idea?
Intensive research to check the
best method to be used to
ensure evidence availability to
the store staff.
Allocate the store staff
direct access to the orders
of the clients
Management to oversee the
transition of recording
customers’ orders from the
receptionists to the store
staff.
What will be the cost of $ 1000 $500
BSBMGT608 Manage innovation and continuous improvement and BSBMGT619 Identify and implement business innovation -
Assessment Pack - Version September 2017 Page 19 of 24
Adequate space in the stores
e. How else can we do this?
The business having clear set out procedure of clearance which are simple.
4. Select any TWO of the many possible ideas/ solutions for continuous improvement for addressing
Problem B. Complete the table below to compare the two ideas
QUESTIONS Idea 1 Idea 2
Describe the idea/
solution Change in the recording of the buyers
orders details
Reduction of the process the
order moves to reach the stores
staff
How can this idea add
value for the customer?
Make the firm always supply correct
items required by the buyers
Ensure that dispatch of items to
the buyers is on timely basis
What are the steps that
need to be taken with the
LOW team to implement
this idea?
Intensive research to check the
best method to be used to
ensure evidence availability to
the store staff.
Allocate the store staff
direct access to the orders
of the clients
Management to oversee the
transition of recording
customers’ orders from the
receptionists to the store
staff.
What will be the cost of $ 1000 $500
BSBMGT608 Manage innovation and continuous improvement and BSBMGT619 Identify and implement business innovation -
Assessment Pack - Version September 2017 Page 19 of 24
Paraphrase This Document
Need a fresh take? Get an instant paraphrase of this document with our AI Paraphraser
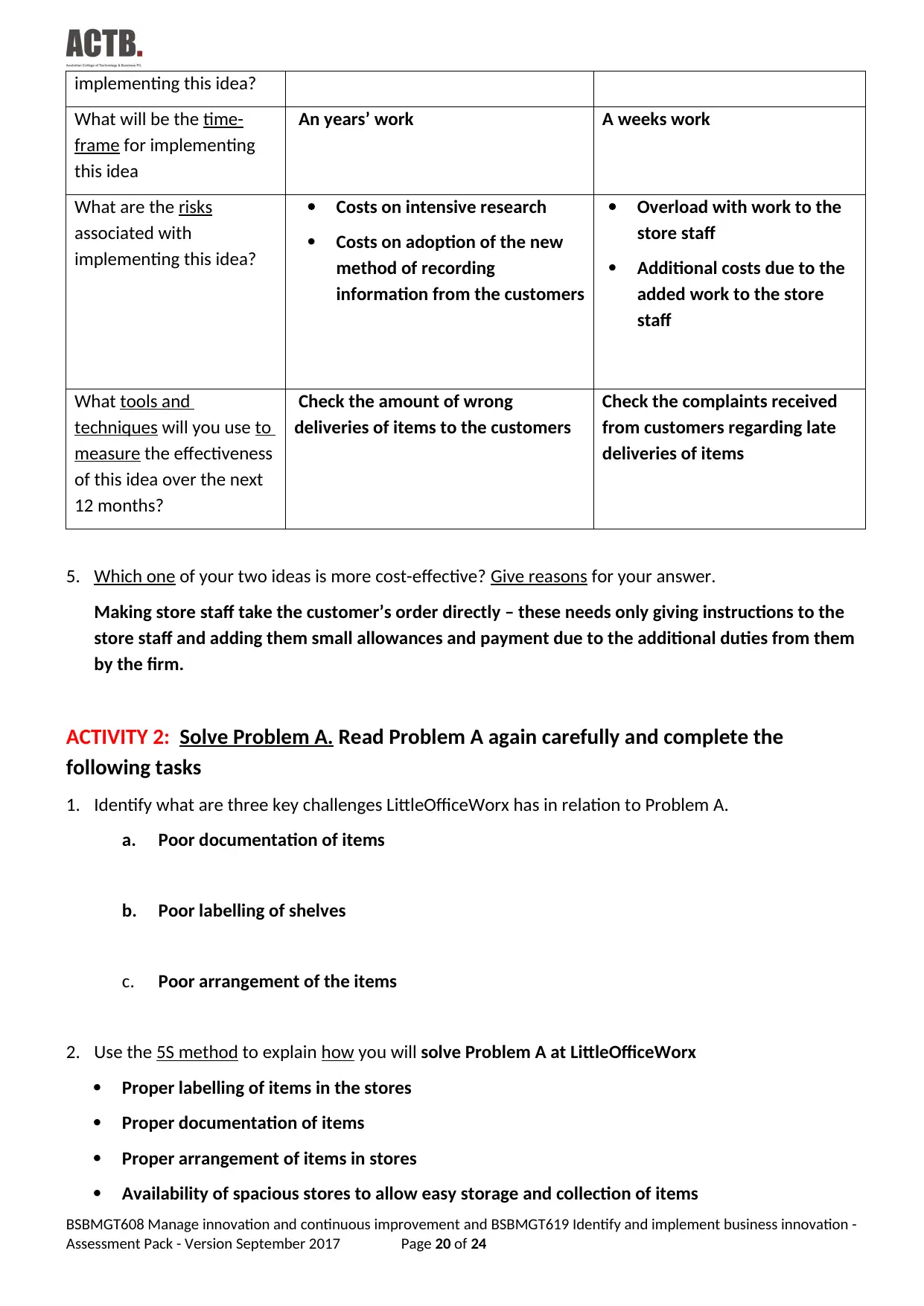
implementing this idea?
What will be the time-
frame for implementing
this idea
An years’ work A weeks work
What are the risks
associated with
implementing this idea?
Costs on intensive research
Costs on adoption of the new
method of recording
information from the customers
Overload with work to the
store staff
Additional costs due to the
added work to the store
staff
What tools and
techniques will you use to
measure the effectiveness
of this idea over the next
12 months?
Check the amount of wrong
deliveries of items to the customers
Check the complaints received
from customers regarding late
deliveries of items
5. Which one of your two ideas is more cost-effective? Give reasons for your answer.
Making store staff take the customer’s order directly – these needs only giving instructions to the
store staff and adding them small allowances and payment due to the additional duties from them
by the firm.
ACTIVITY 2: Solve Problem A. Read Problem A again carefully and complete the
following tasks
1. Identify what are three key challenges LittleOfficeWorx has in relation to Problem A.
a. Poor documentation of items
b. Poor labelling of shelves
c. Poor arrangement of the items
2. Use the 5S method to explain how you will solve Problem A at LittleOfficeWorx
Proper labelling of items in the stores
Proper documentation of items
Proper arrangement of items in stores
Availability of spacious stores to allow easy storage and collection of items
BSBMGT608 Manage innovation and continuous improvement and BSBMGT619 Identify and implement business innovation -
Assessment Pack - Version September 2017 Page 20 of 24
What will be the time-
frame for implementing
this idea
An years’ work A weeks work
What are the risks
associated with
implementing this idea?
Costs on intensive research
Costs on adoption of the new
method of recording
information from the customers
Overload with work to the
store staff
Additional costs due to the
added work to the store
staff
What tools and
techniques will you use to
measure the effectiveness
of this idea over the next
12 months?
Check the amount of wrong
deliveries of items to the customers
Check the complaints received
from customers regarding late
deliveries of items
5. Which one of your two ideas is more cost-effective? Give reasons for your answer.
Making store staff take the customer’s order directly – these needs only giving instructions to the
store staff and adding them small allowances and payment due to the additional duties from them
by the firm.
ACTIVITY 2: Solve Problem A. Read Problem A again carefully and complete the
following tasks
1. Identify what are three key challenges LittleOfficeWorx has in relation to Problem A.
a. Poor documentation of items
b. Poor labelling of shelves
c. Poor arrangement of the items
2. Use the 5S method to explain how you will solve Problem A at LittleOfficeWorx
Proper labelling of items in the stores
Proper documentation of items
Proper arrangement of items in stores
Availability of spacious stores to allow easy storage and collection of items
BSBMGT608 Manage innovation and continuous improvement and BSBMGT619 Identify and implement business innovation -
Assessment Pack - Version September 2017 Page 20 of 24
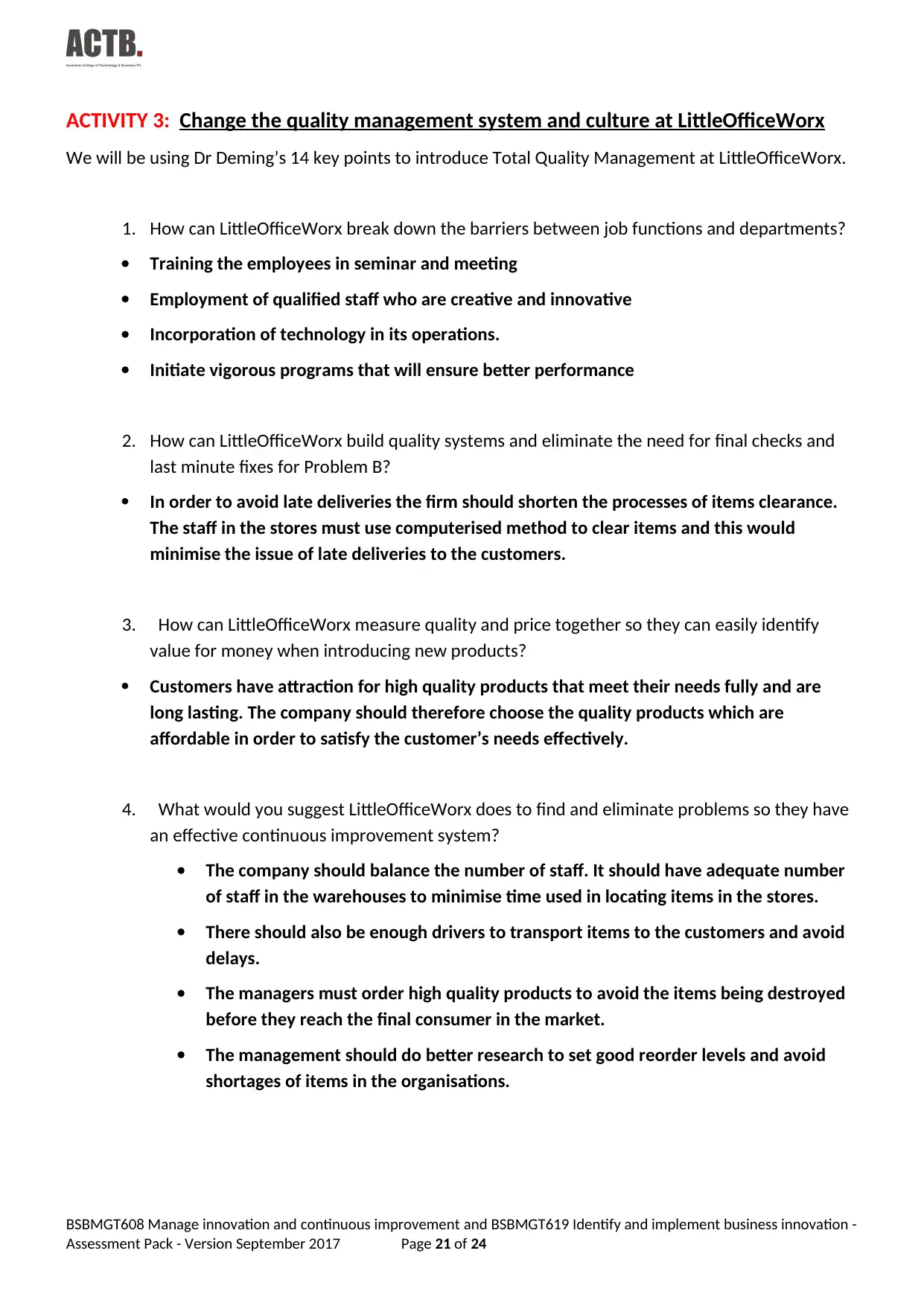
ACTIVITY 3: Change the quality management system and culture at LittleOfficeWorx
We will be using Dr Deming’s 14 key points to introduce Total Quality Management at LittleOfficeWorx.
1. How can LittleOfficeWorx break down the barriers between job functions and departments?
Training the employees in seminar and meeting
Employment of qualified staff who are creative and innovative
Incorporation of technology in its operations.
Initiate vigorous programs that will ensure better performance
2. How can LittleOfficeWorx build quality systems and eliminate the need for final checks and
last minute fixes for Problem B?
In order to avoid late deliveries the firm should shorten the processes of items clearance.
The staff in the stores must use computerised method to clear items and this would
minimise the issue of late deliveries to the customers.
3. How can LittleOfficeWorx measure quality and price together so they can easily identify
value for money when introducing new products?
Customers have attraction for high quality products that meet their needs fully and are
long lasting. The company should therefore choose the quality products which are
affordable in order to satisfy the customer’s needs effectively.
4. What would you suggest LittleOfficeWorx does to find and eliminate problems so they have
an effective continuous improvement system?
The company should balance the number of staff. It should have adequate number
of staff in the warehouses to minimise time used in locating items in the stores.
There should also be enough drivers to transport items to the customers and avoid
delays.
The managers must order high quality products to avoid the items being destroyed
before they reach the final consumer in the market.
The management should do better research to set good reorder levels and avoid
shortages of items in the organisations.
BSBMGT608 Manage innovation and continuous improvement and BSBMGT619 Identify and implement business innovation -
Assessment Pack - Version September 2017 Page 21 of 24
We will be using Dr Deming’s 14 key points to introduce Total Quality Management at LittleOfficeWorx.
1. How can LittleOfficeWorx break down the barriers between job functions and departments?
Training the employees in seminar and meeting
Employment of qualified staff who are creative and innovative
Incorporation of technology in its operations.
Initiate vigorous programs that will ensure better performance
2. How can LittleOfficeWorx build quality systems and eliminate the need for final checks and
last minute fixes for Problem B?
In order to avoid late deliveries the firm should shorten the processes of items clearance.
The staff in the stores must use computerised method to clear items and this would
minimise the issue of late deliveries to the customers.
3. How can LittleOfficeWorx measure quality and price together so they can easily identify
value for money when introducing new products?
Customers have attraction for high quality products that meet their needs fully and are
long lasting. The company should therefore choose the quality products which are
affordable in order to satisfy the customer’s needs effectively.
4. What would you suggest LittleOfficeWorx does to find and eliminate problems so they have
an effective continuous improvement system?
The company should balance the number of staff. It should have adequate number
of staff in the warehouses to minimise time used in locating items in the stores.
There should also be enough drivers to transport items to the customers and avoid
delays.
The managers must order high quality products to avoid the items being destroyed
before they reach the final consumer in the market.
The management should do better research to set good reorder levels and avoid
shortages of items in the organisations.
BSBMGT608 Manage innovation and continuous improvement and BSBMGT619 Identify and implement business innovation -
Assessment Pack - Version September 2017 Page 21 of 24
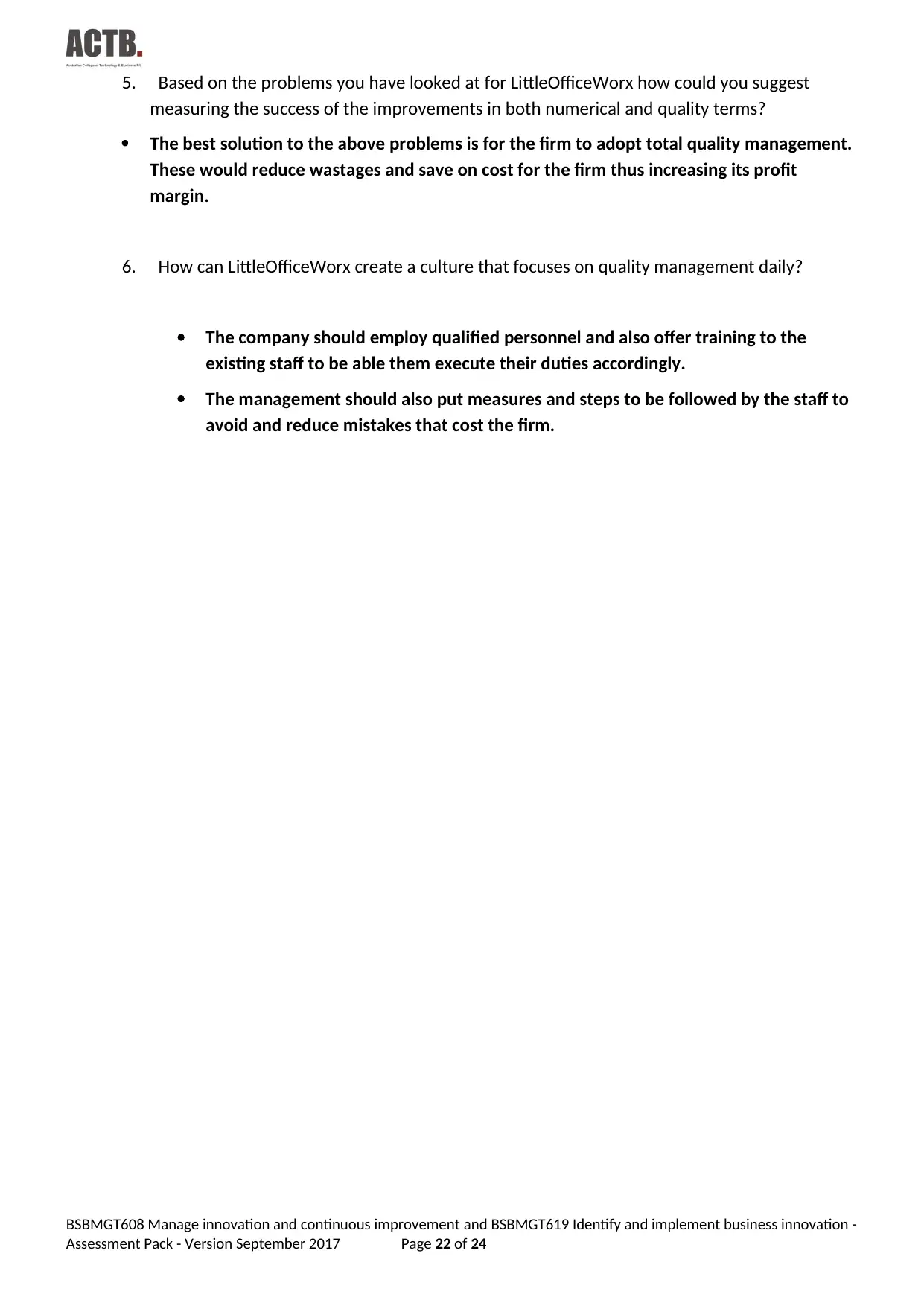
5. Based on the problems you have looked at for LittleOfficeWorx how could you suggest
measuring the success of the improvements in both numerical and quality terms?
The best solution to the above problems is for the firm to adopt total quality management.
These would reduce wastages and save on cost for the firm thus increasing its profit
margin.
6. How can LittleOfficeWorx create a culture that focuses on quality management daily?
The company should employ qualified personnel and also offer training to the
existing staff to be able them execute their duties accordingly.
The management should also put measures and steps to be followed by the staff to
avoid and reduce mistakes that cost the firm.
BSBMGT608 Manage innovation and continuous improvement and BSBMGT619 Identify and implement business innovation -
Assessment Pack - Version September 2017 Page 22 of 24
measuring the success of the improvements in both numerical and quality terms?
The best solution to the above problems is for the firm to adopt total quality management.
These would reduce wastages and save on cost for the firm thus increasing its profit
margin.
6. How can LittleOfficeWorx create a culture that focuses on quality management daily?
The company should employ qualified personnel and also offer training to the
existing staff to be able them execute their duties accordingly.
The management should also put measures and steps to be followed by the staff to
avoid and reduce mistakes that cost the firm.
BSBMGT608 Manage innovation and continuous improvement and BSBMGT619 Identify and implement business innovation -
Assessment Pack - Version September 2017 Page 22 of 24
Secure Best Marks with AI Grader
Need help grading? Try our AI Grader for instant feedback on your assignments.
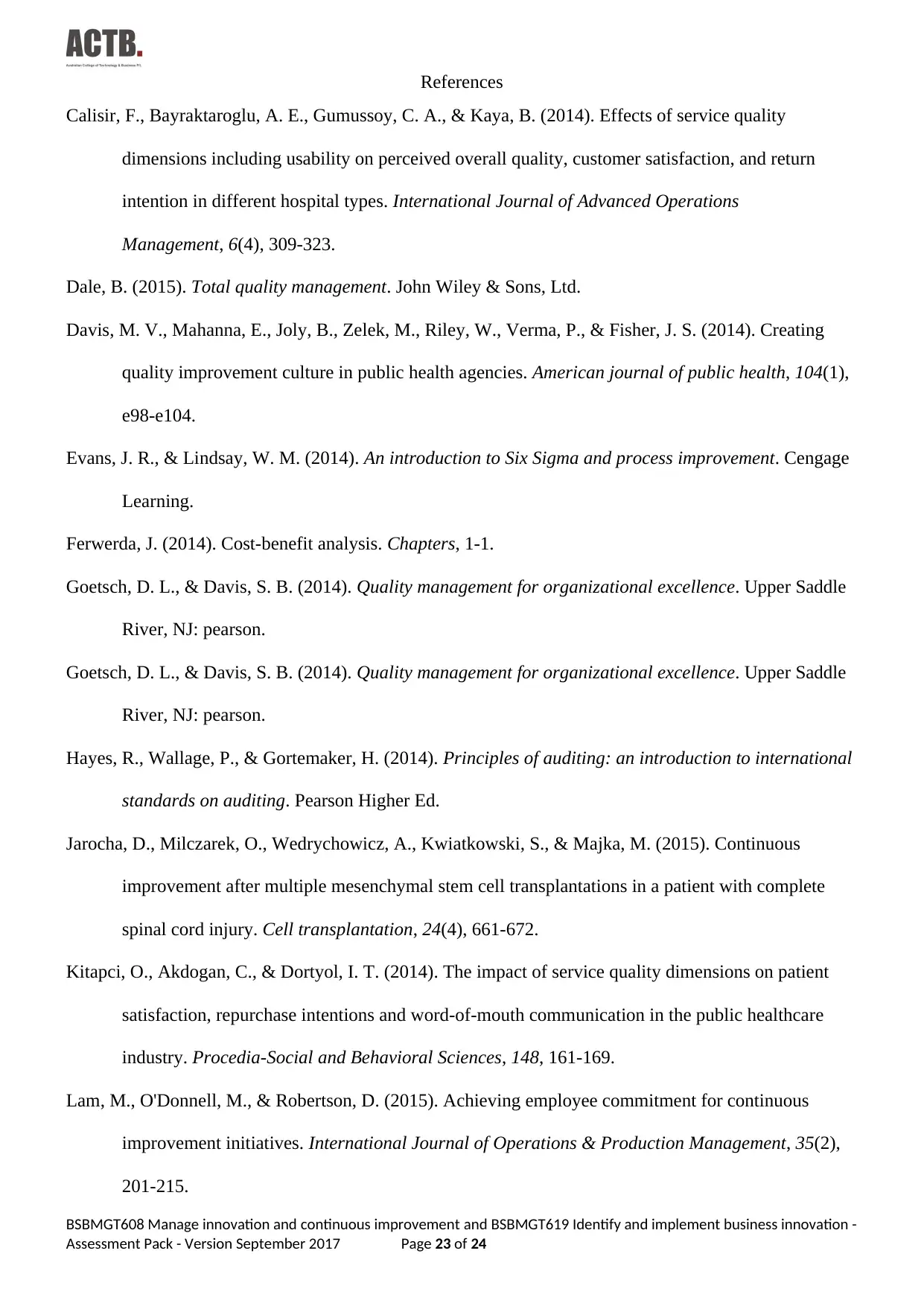
References
Calisir, F., Bayraktaroglu, A. E., Gumussoy, C. A., & Kaya, B. (2014). Effects of service quality
dimensions including usability on perceived overall quality, customer satisfaction, and return
intention in different hospital types. International Journal of Advanced Operations
Management, 6(4), 309-323.
Dale, B. (2015). Total quality management. John Wiley & Sons, Ltd.
Davis, M. V., Mahanna, E., Joly, B., Zelek, M., Riley, W., Verma, P., & Fisher, J. S. (2014). Creating
quality improvement culture in public health agencies. American journal of public health, 104(1),
e98-e104.
Evans, J. R., & Lindsay, W. M. (2014). An introduction to Six Sigma and process improvement. Cengage
Learning.
Ferwerda, J. (2014). Cost-benefit analysis. Chapters, 1-1.
Goetsch, D. L., & Davis, S. B. (2014). Quality management for organizational excellence. Upper Saddle
River, NJ: pearson.
Goetsch, D. L., & Davis, S. B. (2014). Quality management for organizational excellence. Upper Saddle
River, NJ: pearson.
Hayes, R., Wallage, P., & Gortemaker, H. (2014). Principles of auditing: an introduction to international
standards on auditing. Pearson Higher Ed.
Jarocha, D., Milczarek, O., Wedrychowicz, A., Kwiatkowski, S., & Majka, M. (2015). Continuous
improvement after multiple mesenchymal stem cell transplantations in a patient with complete
spinal cord injury. Cell transplantation, 24(4), 661-672.
Kitapci, O., Akdogan, C., & Dortyol, I. T. (2014). The impact of service quality dimensions on patient
satisfaction, repurchase intentions and word-of-mouth communication in the public healthcare
industry. Procedia-Social and Behavioral Sciences, 148, 161-169.
Lam, M., O'Donnell, M., & Robertson, D. (2015). Achieving employee commitment for continuous
improvement initiatives. International Journal of Operations & Production Management, 35(2),
201-215.
BSBMGT608 Manage innovation and continuous improvement and BSBMGT619 Identify and implement business innovation -
Assessment Pack - Version September 2017 Page 23 of 24
Calisir, F., Bayraktaroglu, A. E., Gumussoy, C. A., & Kaya, B. (2014). Effects of service quality
dimensions including usability on perceived overall quality, customer satisfaction, and return
intention in different hospital types. International Journal of Advanced Operations
Management, 6(4), 309-323.
Dale, B. (2015). Total quality management. John Wiley & Sons, Ltd.
Davis, M. V., Mahanna, E., Joly, B., Zelek, M., Riley, W., Verma, P., & Fisher, J. S. (2014). Creating
quality improvement culture in public health agencies. American journal of public health, 104(1),
e98-e104.
Evans, J. R., & Lindsay, W. M. (2014). An introduction to Six Sigma and process improvement. Cengage
Learning.
Ferwerda, J. (2014). Cost-benefit analysis. Chapters, 1-1.
Goetsch, D. L., & Davis, S. B. (2014). Quality management for organizational excellence. Upper Saddle
River, NJ: pearson.
Goetsch, D. L., & Davis, S. B. (2014). Quality management for organizational excellence. Upper Saddle
River, NJ: pearson.
Hayes, R., Wallage, P., & Gortemaker, H. (2014). Principles of auditing: an introduction to international
standards on auditing. Pearson Higher Ed.
Jarocha, D., Milczarek, O., Wedrychowicz, A., Kwiatkowski, S., & Majka, M. (2015). Continuous
improvement after multiple mesenchymal stem cell transplantations in a patient with complete
spinal cord injury. Cell transplantation, 24(4), 661-672.
Kitapci, O., Akdogan, C., & Dortyol, I. T. (2014). The impact of service quality dimensions on patient
satisfaction, repurchase intentions and word-of-mouth communication in the public healthcare
industry. Procedia-Social and Behavioral Sciences, 148, 161-169.
Lam, M., O'Donnell, M., & Robertson, D. (2015). Achieving employee commitment for continuous
improvement initiatives. International Journal of Operations & Production Management, 35(2),
201-215.
BSBMGT608 Manage innovation and continuous improvement and BSBMGT619 Identify and implement business innovation -
Assessment Pack - Version September 2017 Page 23 of 24
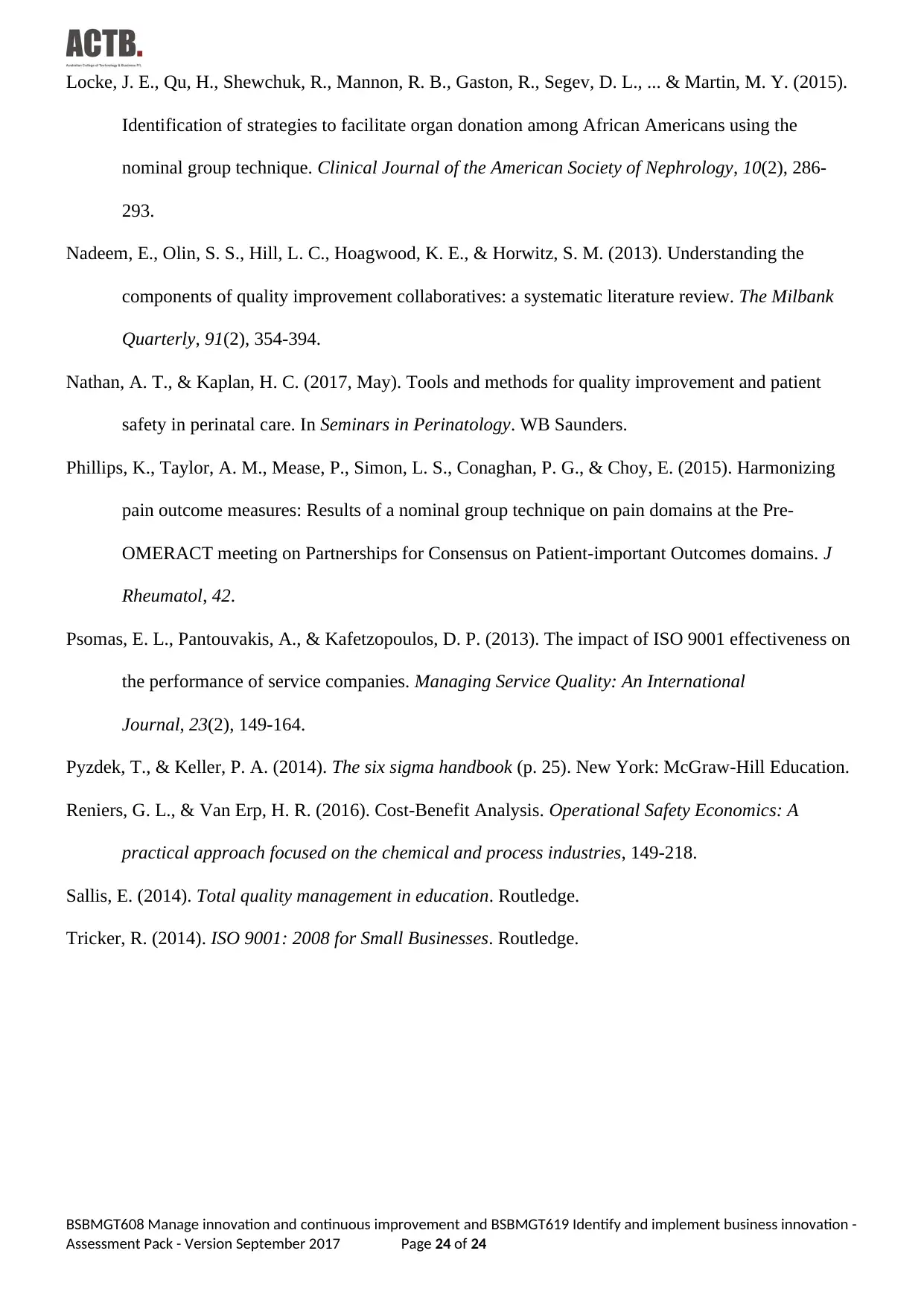
Locke, J. E., Qu, H., Shewchuk, R., Mannon, R. B., Gaston, R., Segev, D. L., ... & Martin, M. Y. (2015).
Identification of strategies to facilitate organ donation among African Americans using the
nominal group technique. Clinical Journal of the American Society of Nephrology, 10(2), 286-
293.
Nadeem, E., Olin, S. S., Hill, L. C., Hoagwood, K. E., & Horwitz, S. M. (2013). Understanding the
components of quality improvement collaboratives: a systematic literature review. The Milbank
Quarterly, 91(2), 354-394.
Nathan, A. T., & Kaplan, H. C. (2017, May). Tools and methods for quality improvement and patient
safety in perinatal care. In Seminars in Perinatology. WB Saunders.
Phillips, K., Taylor, A. M., Mease, P., Simon, L. S., Conaghan, P. G., & Choy, E. (2015). Harmonizing
pain outcome measures: Results of a nominal group technique on pain domains at the Pre-
OMERACT meeting on Partnerships for Consensus on Patient-important Outcomes domains. J
Rheumatol, 42.
Psomas, E. L., Pantouvakis, A., & Kafetzopoulos, D. P. (2013). The impact of ISO 9001 effectiveness on
the performance of service companies. Managing Service Quality: An International
Journal, 23(2), 149-164.
Pyzdek, T., & Keller, P. A. (2014). The six sigma handbook (p. 25). New York: McGraw-Hill Education.
Reniers, G. L., & Van Erp, H. R. (2016). Cost‐Benefit Analysis. Operational Safety Economics: A
practical approach focused on the chemical and process industries, 149-218.
Sallis, E. (2014). Total quality management in education. Routledge.
Tricker, R. (2014). ISO 9001: 2008 for Small Businesses. Routledge.
BSBMGT608 Manage innovation and continuous improvement and BSBMGT619 Identify and implement business innovation -
Assessment Pack - Version September 2017 Page 24 of 24
Identification of strategies to facilitate organ donation among African Americans using the
nominal group technique. Clinical Journal of the American Society of Nephrology, 10(2), 286-
293.
Nadeem, E., Olin, S. S., Hill, L. C., Hoagwood, K. E., & Horwitz, S. M. (2013). Understanding the
components of quality improvement collaboratives: a systematic literature review. The Milbank
Quarterly, 91(2), 354-394.
Nathan, A. T., & Kaplan, H. C. (2017, May). Tools and methods for quality improvement and patient
safety in perinatal care. In Seminars in Perinatology. WB Saunders.
Phillips, K., Taylor, A. M., Mease, P., Simon, L. S., Conaghan, P. G., & Choy, E. (2015). Harmonizing
pain outcome measures: Results of a nominal group technique on pain domains at the Pre-
OMERACT meeting on Partnerships for Consensus on Patient-important Outcomes domains. J
Rheumatol, 42.
Psomas, E. L., Pantouvakis, A., & Kafetzopoulos, D. P. (2013). The impact of ISO 9001 effectiveness on
the performance of service companies. Managing Service Quality: An International
Journal, 23(2), 149-164.
Pyzdek, T., & Keller, P. A. (2014). The six sigma handbook (p. 25). New York: McGraw-Hill Education.
Reniers, G. L., & Van Erp, H. R. (2016). Cost‐Benefit Analysis. Operational Safety Economics: A
practical approach focused on the chemical and process industries, 149-218.
Sallis, E. (2014). Total quality management in education. Routledge.
Tricker, R. (2014). ISO 9001: 2008 for Small Businesses. Routledge.
BSBMGT608 Manage innovation and continuous improvement and BSBMGT619 Identify and implement business innovation -
Assessment Pack - Version September 2017 Page 24 of 24
1 out of 24
Related Documents
![[object Object]](/_next/image/?url=%2F_next%2Fstatic%2Fmedia%2Flogo.6d15ce61.png&w=640&q=75)
Your All-in-One AI-Powered Toolkit for Academic Success.
+13062052269
info@desklib.com
Available 24*7 on WhatsApp / Email
Unlock your academic potential
© 2024 | Zucol Services PVT LTD | All rights reserved.