Companywide Quality Improvement Strategy
VerifiedAdded on 2023/01/19
|14
|3275
|74
AI Summary
This document discusses the importance of implementing a companywide quality improvement strategy. It explores the meaning of quality and the key elements of total quality management. The document also provides steps for implementing total quality management and strategies for establishing a quality culture. Additionally, it explains how ISO 9000 can be used as an entry into total quality management.
Contribute Materials
Your contribution can guide someone’s learning journey. Share your
documents today.
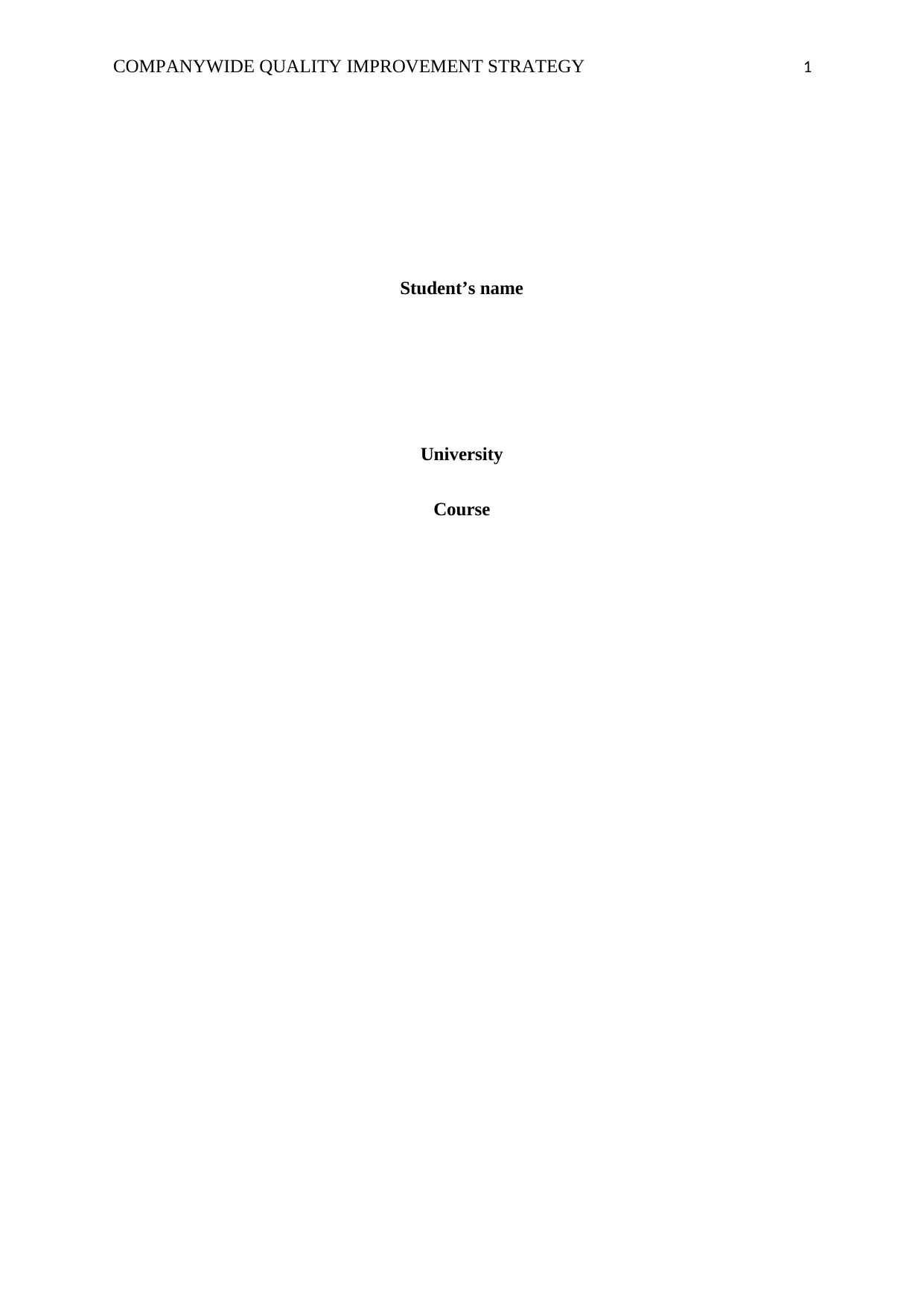
COMPANYWIDE QUALITY IMPROVEMENT STRATEGY 1
Student’s name
University
Course
Student’s name
University
Course
Secure Best Marks with AI Grader
Need help grading? Try our AI Grader for instant feedback on your assignments.
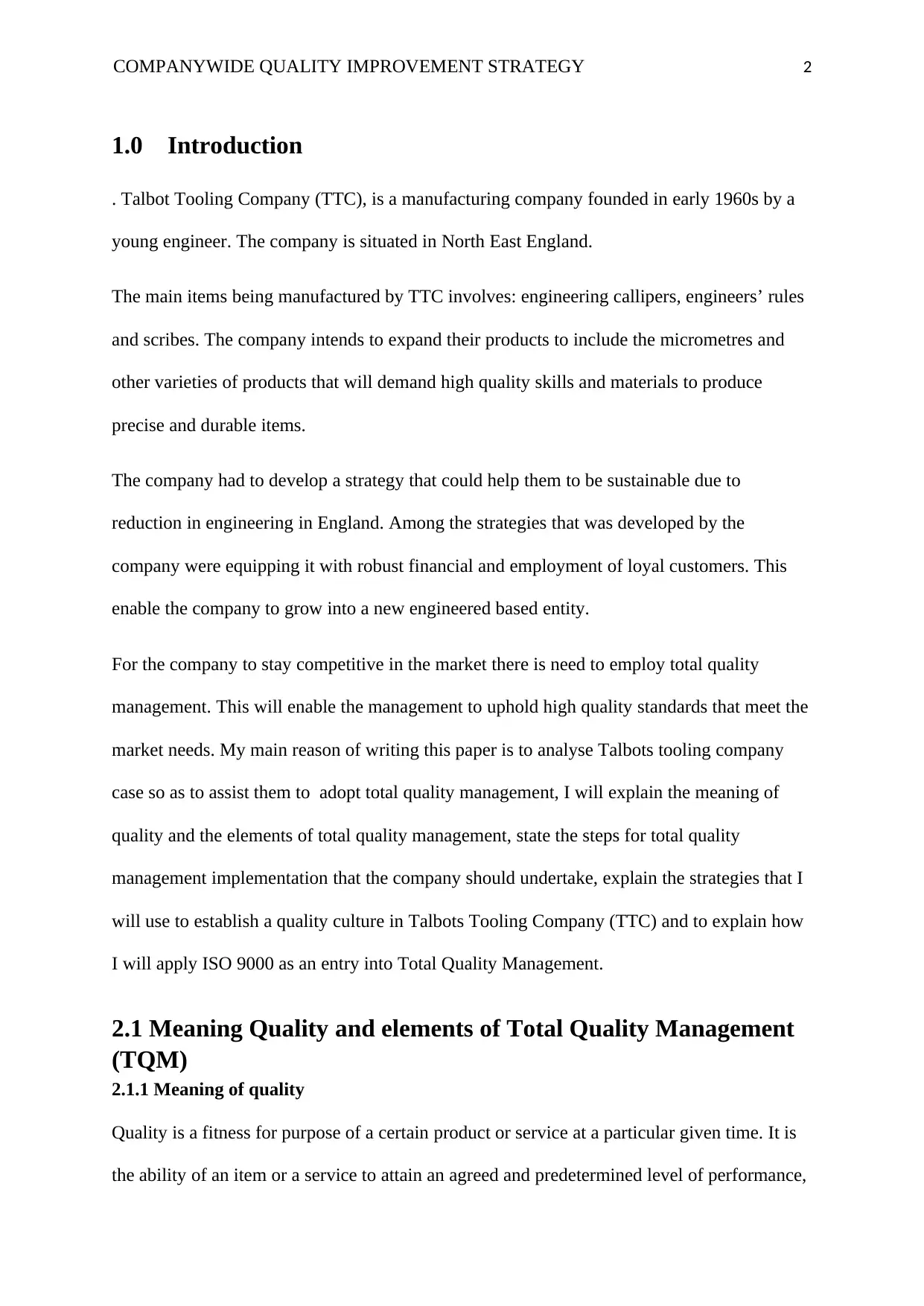
COMPANYWIDE QUALITY IMPROVEMENT STRATEGY 2
1.0 Introduction
. Talbot Tooling Company (TTC), is a manufacturing company founded in early 1960s by a
young engineer. The company is situated in North East England.
The main items being manufactured by TTC involves: engineering callipers, engineers’ rules
and scribes. The company intends to expand their products to include the micrometres and
other varieties of products that will demand high quality skills and materials to produce
precise and durable items.
The company had to develop a strategy that could help them to be sustainable due to
reduction in engineering in England. Among the strategies that was developed by the
company were equipping it with robust financial and employment of loyal customers. This
enable the company to grow into a new engineered based entity.
For the company to stay competitive in the market there is need to employ total quality
management. This will enable the management to uphold high quality standards that meet the
market needs. My main reason of writing this paper is to analyse Talbots tooling company
case so as to assist them to adopt total quality management, I will explain the meaning of
quality and the elements of total quality management, state the steps for total quality
management implementation that the company should undertake, explain the strategies that I
will use to establish a quality culture in Talbots Tooling Company (TTC) and to explain how
I will apply ISO 9000 as an entry into Total Quality Management.
2.1 Meaning Quality and elements of Total Quality Management
(TQM)
2.1.1 Meaning of quality
Quality is a fitness for purpose of a certain product or service at a particular given time. It is
the ability of an item or a service to attain an agreed and predetermined level of performance,
1.0 Introduction
. Talbot Tooling Company (TTC), is a manufacturing company founded in early 1960s by a
young engineer. The company is situated in North East England.
The main items being manufactured by TTC involves: engineering callipers, engineers’ rules
and scribes. The company intends to expand their products to include the micrometres and
other varieties of products that will demand high quality skills and materials to produce
precise and durable items.
The company had to develop a strategy that could help them to be sustainable due to
reduction in engineering in England. Among the strategies that was developed by the
company were equipping it with robust financial and employment of loyal customers. This
enable the company to grow into a new engineered based entity.
For the company to stay competitive in the market there is need to employ total quality
management. This will enable the management to uphold high quality standards that meet the
market needs. My main reason of writing this paper is to analyse Talbots tooling company
case so as to assist them to adopt total quality management, I will explain the meaning of
quality and the elements of total quality management, state the steps for total quality
management implementation that the company should undertake, explain the strategies that I
will use to establish a quality culture in Talbots Tooling Company (TTC) and to explain how
I will apply ISO 9000 as an entry into Total Quality Management.
2.1 Meaning Quality and elements of Total Quality Management
(TQM)
2.1.1 Meaning of quality
Quality is a fitness for purpose of a certain product or service at a particular given time. It is
the ability of an item or a service to attain an agreed and predetermined level of performance,
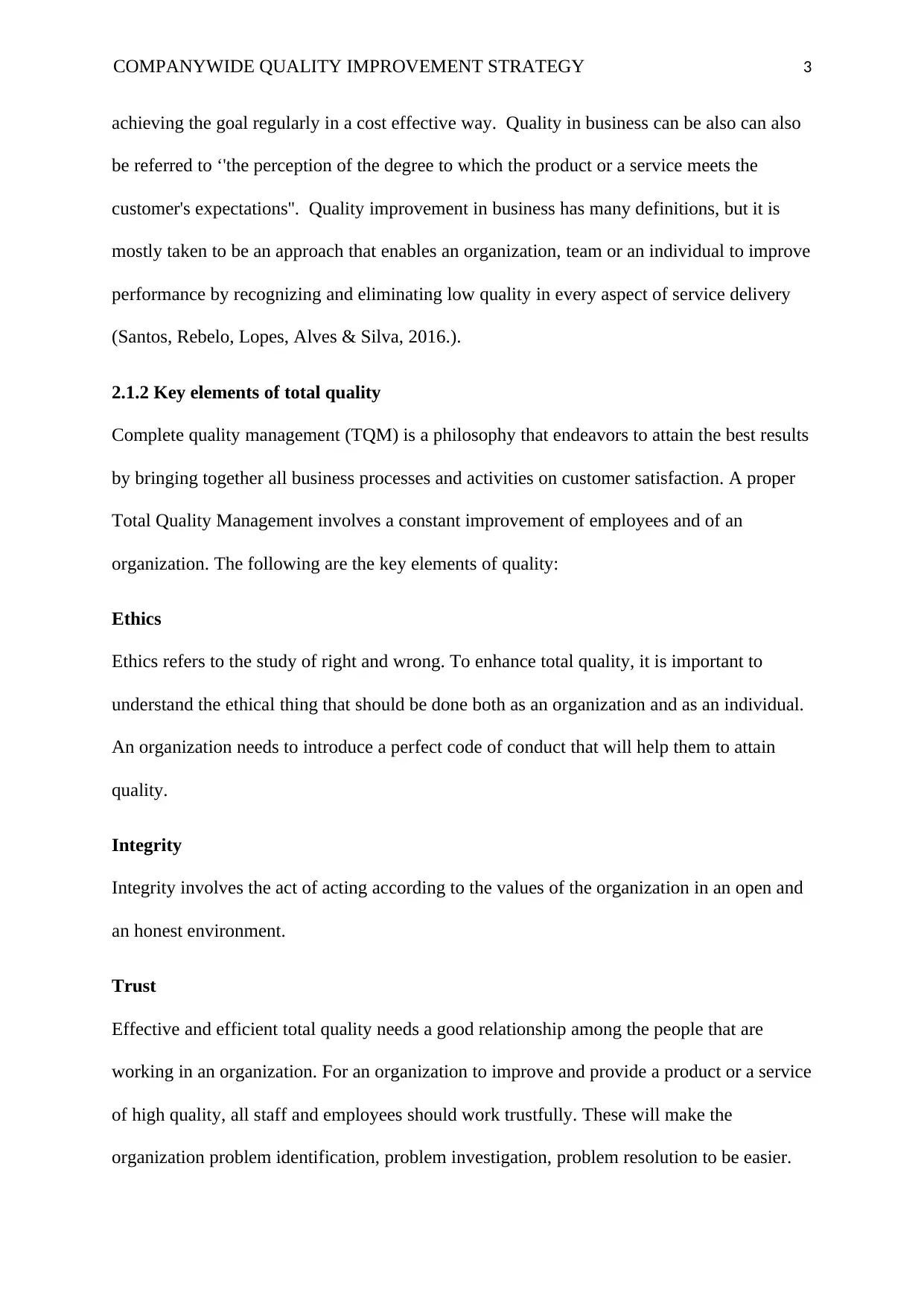
COMPANYWIDE QUALITY IMPROVEMENT STRATEGY 3
achieving the goal regularly in a cost effective way. Quality in business can be also can also
be referred to ‘'the perception of the degree to which the product or a service meets the
customer's expectations''. Quality improvement in business has many definitions, but it is
mostly taken to be an approach that enables an organization, team or an individual to improve
performance by recognizing and eliminating low quality in every aspect of service delivery
(Santos, Rebelo, Lopes, Alves & Silva, 2016.).
2.1.2 Key elements of total quality
Complete quality management (TQM) is a philosophy that endeavors to attain the best results
by bringing together all business processes and activities on customer satisfaction. A proper
Total Quality Management involves a constant improvement of employees and of an
organization. The following are the key elements of quality:
Ethics
Ethics refers to the study of right and wrong. To enhance total quality, it is important to
understand the ethical thing that should be done both as an organization and as an individual.
An organization needs to introduce a perfect code of conduct that will help them to attain
quality.
Integrity
Integrity involves the act of acting according to the values of the organization in an open and
an honest environment.
Trust
Effective and efficient total quality needs a good relationship among the people that are
working in an organization. For an organization to improve and provide a product or a service
of high quality, all staff and employees should work trustfully. These will make the
organization problem identification, problem investigation, problem resolution to be easier.
achieving the goal regularly in a cost effective way. Quality in business can be also can also
be referred to ‘'the perception of the degree to which the product or a service meets the
customer's expectations''. Quality improvement in business has many definitions, but it is
mostly taken to be an approach that enables an organization, team or an individual to improve
performance by recognizing and eliminating low quality in every aspect of service delivery
(Santos, Rebelo, Lopes, Alves & Silva, 2016.).
2.1.2 Key elements of total quality
Complete quality management (TQM) is a philosophy that endeavors to attain the best results
by bringing together all business processes and activities on customer satisfaction. A proper
Total Quality Management involves a constant improvement of employees and of an
organization. The following are the key elements of quality:
Ethics
Ethics refers to the study of right and wrong. To enhance total quality, it is important to
understand the ethical thing that should be done both as an organization and as an individual.
An organization needs to introduce a perfect code of conduct that will help them to attain
quality.
Integrity
Integrity involves the act of acting according to the values of the organization in an open and
an honest environment.
Trust
Effective and efficient total quality needs a good relationship among the people that are
working in an organization. For an organization to improve and provide a product or a service
of high quality, all staff and employees should work trustfully. These will make the
organization problem identification, problem investigation, problem resolution to be easier.
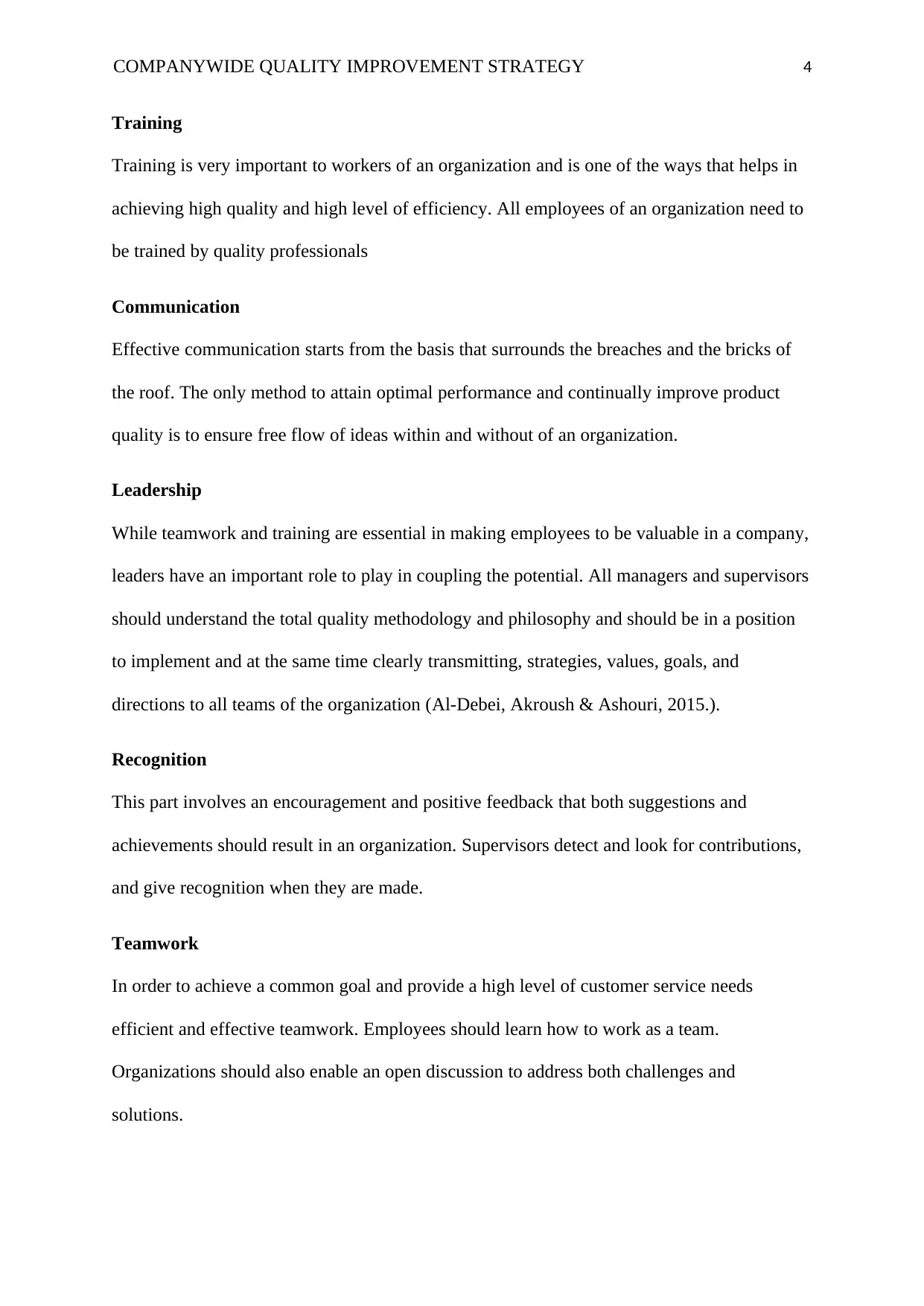
COMPANYWIDE QUALITY IMPROVEMENT STRATEGY 4
Training
Training is very important to workers of an organization and is one of the ways that helps in
achieving high quality and high level of efficiency. All employees of an organization need to
be trained by quality professionals
Communication
Effective communication starts from the basis that surrounds the breaches and the bricks of
the roof. The only method to attain optimal performance and continually improve product
quality is to ensure free flow of ideas within and without of an organization.
Leadership
While teamwork and training are essential in making employees to be valuable in a company,
leaders have an important role to play in coupling the potential. All managers and supervisors
should understand the total quality methodology and philosophy and should be in a position
to implement and at the same time clearly transmitting, strategies, values, goals, and
directions to all teams of the organization (Al-Debei, Akroush & Ashouri, 2015.).
Recognition
This part involves an encouragement and positive feedback that both suggestions and
achievements should result in an organization. Supervisors detect and look for contributions,
and give recognition when they are made.
Teamwork
In order to achieve a common goal and provide a high level of customer service needs
efficient and effective teamwork. Employees should learn how to work as a team.
Organizations should also enable an open discussion to address both challenges and
solutions.
Training
Training is very important to workers of an organization and is one of the ways that helps in
achieving high quality and high level of efficiency. All employees of an organization need to
be trained by quality professionals
Communication
Effective communication starts from the basis that surrounds the breaches and the bricks of
the roof. The only method to attain optimal performance and continually improve product
quality is to ensure free flow of ideas within and without of an organization.
Leadership
While teamwork and training are essential in making employees to be valuable in a company,
leaders have an important role to play in coupling the potential. All managers and supervisors
should understand the total quality methodology and philosophy and should be in a position
to implement and at the same time clearly transmitting, strategies, values, goals, and
directions to all teams of the organization (Al-Debei, Akroush & Ashouri, 2015.).
Recognition
This part involves an encouragement and positive feedback that both suggestions and
achievements should result in an organization. Supervisors detect and look for contributions,
and give recognition when they are made.
Teamwork
In order to achieve a common goal and provide a high level of customer service needs
efficient and effective teamwork. Employees should learn how to work as a team.
Organizations should also enable an open discussion to address both challenges and
solutions.
Secure Best Marks with AI Grader
Need help grading? Try our AI Grader for instant feedback on your assignments.
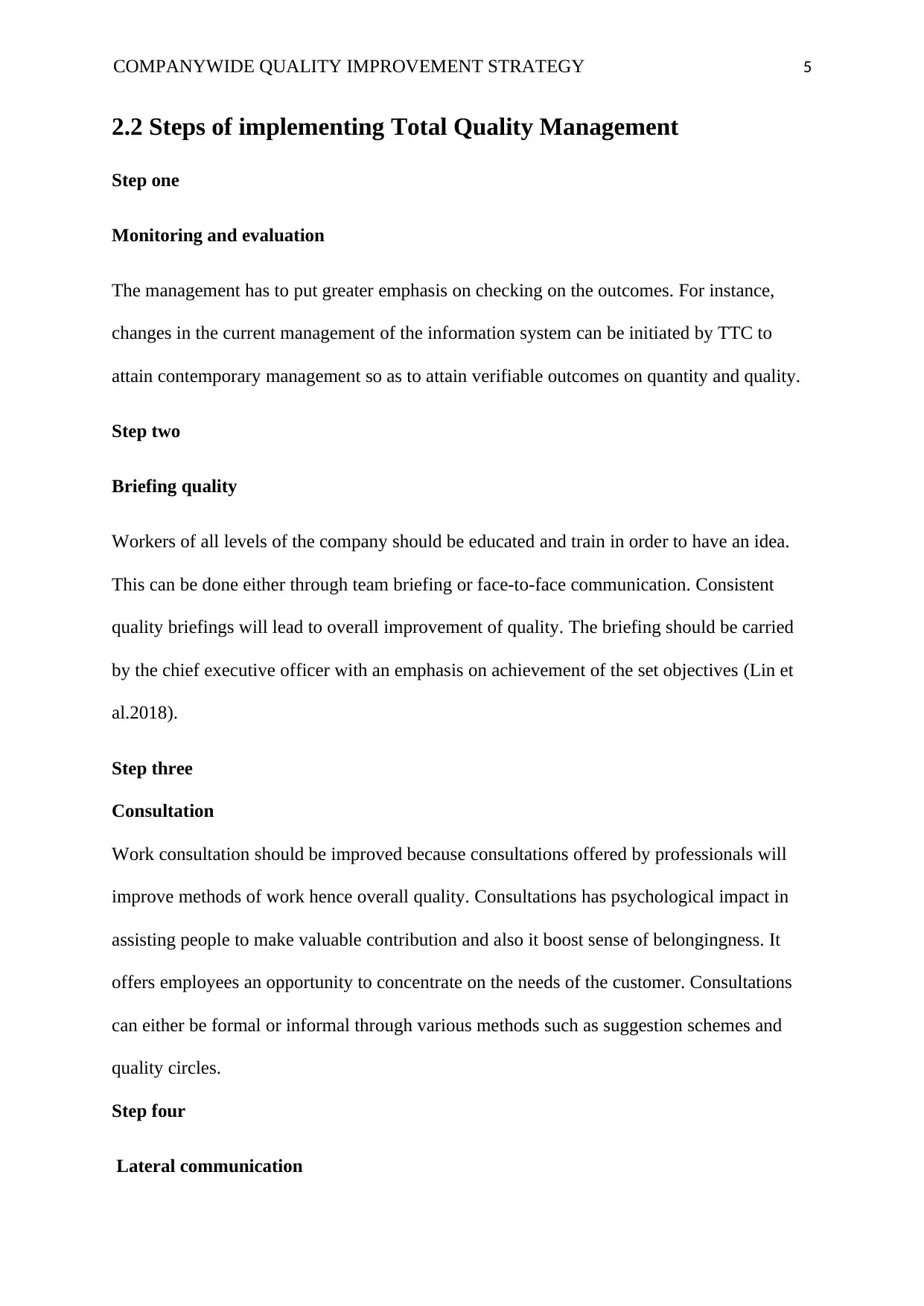
COMPANYWIDE QUALITY IMPROVEMENT STRATEGY 5
2.2 Steps of implementing Total Quality Management
Step one
Monitoring and evaluation
The management has to put greater emphasis on checking on the outcomes. For instance,
changes in the current management of the information system can be initiated by TTC to
attain contemporary management so as to attain verifiable outcomes on quantity and quality.
Step two
Briefing quality
Workers of all levels of the company should be educated and train in order to have an idea.
This can be done either through team briefing or face-to-face communication. Consistent
quality briefings will lead to overall improvement of quality. The briefing should be carried
by the chief executive officer with an emphasis on achievement of the set objectives (Lin et
al.2018).
Step three
Consultation
Work consultation should be improved because consultations offered by professionals will
improve methods of work hence overall quality. Consultations has psychological impact in
assisting people to make valuable contribution and also it boost sense of belongingness. It
offers employees an opportunity to concentrate on the needs of the customer. Consultations
can either be formal or informal through various methods such as suggestion schemes and
quality circles.
Step four
Lateral communication
2.2 Steps of implementing Total Quality Management
Step one
Monitoring and evaluation
The management has to put greater emphasis on checking on the outcomes. For instance,
changes in the current management of the information system can be initiated by TTC to
attain contemporary management so as to attain verifiable outcomes on quantity and quality.
Step two
Briefing quality
Workers of all levels of the company should be educated and train in order to have an idea.
This can be done either through team briefing or face-to-face communication. Consistent
quality briefings will lead to overall improvement of quality. The briefing should be carried
by the chief executive officer with an emphasis on achievement of the set objectives (Lin et
al.2018).
Step three
Consultation
Work consultation should be improved because consultations offered by professionals will
improve methods of work hence overall quality. Consultations has psychological impact in
assisting people to make valuable contribution and also it boost sense of belongingness. It
offers employees an opportunity to concentrate on the needs of the customer. Consultations
can either be formal or informal through various methods such as suggestion schemes and
quality circles.
Step four
Lateral communication
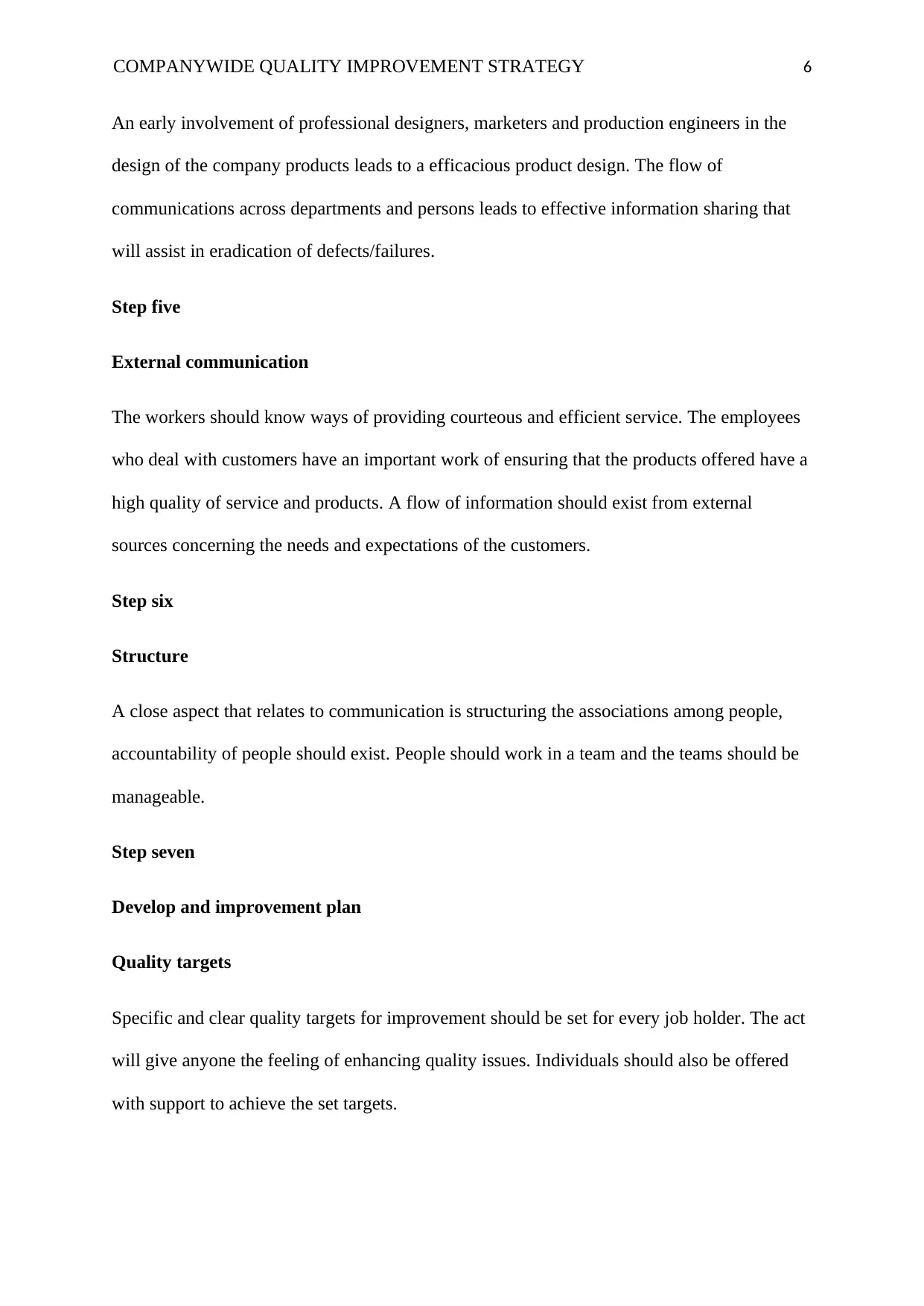
COMPANYWIDE QUALITY IMPROVEMENT STRATEGY 6
An early involvement of professional designers, marketers and production engineers in the
design of the company products leads to a efficacious product design. The flow of
communications across departments and persons leads to effective information sharing that
will assist in eradication of defects/failures.
Step five
External communication
The workers should know ways of providing courteous and efficient service. The employees
who deal with customers have an important work of ensuring that the products offered have a
high quality of service and products. A flow of information should exist from external
sources concerning the needs and expectations of the customers.
Step six
Structure
A close aspect that relates to communication is structuring the associations among people,
accountability of people should exist. People should work in a team and the teams should be
manageable.
Step seven
Develop and improvement plan
Quality targets
Specific and clear quality targets for improvement should be set for every job holder. The act
will give anyone the feeling of enhancing quality issues. Individuals should also be offered
with support to achieve the set targets.
An early involvement of professional designers, marketers and production engineers in the
design of the company products leads to a efficacious product design. The flow of
communications across departments and persons leads to effective information sharing that
will assist in eradication of defects/failures.
Step five
External communication
The workers should know ways of providing courteous and efficient service. The employees
who deal with customers have an important work of ensuring that the products offered have a
high quality of service and products. A flow of information should exist from external
sources concerning the needs and expectations of the customers.
Step six
Structure
A close aspect that relates to communication is structuring the associations among people,
accountability of people should exist. People should work in a team and the teams should be
manageable.
Step seven
Develop and improvement plan
Quality targets
Specific and clear quality targets for improvement should be set for every job holder. The act
will give anyone the feeling of enhancing quality issues. Individuals should also be offered
with support to achieve the set targets.

COMPANYWIDE QUALITY IMPROVEMENT STRATEGY 7
Step eight
Measure and accounting
There would be a need for TTC to track and monitor their progress once the company has
identified the critical success factors has been identified. The company can do this by giving
reports of the process that it uses to share information and gather the specified data with high-
ranking leaders.
For instance, if the objective of the organization is to increase the satisfaction of customers,
there should be a method that would be used to demonstrate if the goal is achieved.
2.3 Strategies that I would use to establish quality culture in
Talbots tooling company (TTC)
Talbots Tooling Company should develop a quality culture in order to remain competitive in
the market. Some of the strategies it could adopt include: developing a strategic and
functional management model of quality, innovate new products, establish good relationships
with suppliers and distributers, motivate their employees and development of a proper
communication. If these strategies are effectively employed, the company will then develop a
good quality culture.
Develop a strategic and functional management model of quality: It is observed that
organizations that dominate or have a big market share focuses on quality production. The
management of these organizations are so keen on quality just are they would be in financial
management. The company need to adopt the strategy in that when there is an issue with
quality they can question the quality department where the manager in charge is answerable.
This department is responsible for ensuring quality throughout the production process.
Step eight
Measure and accounting
There would be a need for TTC to track and monitor their progress once the company has
identified the critical success factors has been identified. The company can do this by giving
reports of the process that it uses to share information and gather the specified data with high-
ranking leaders.
For instance, if the objective of the organization is to increase the satisfaction of customers,
there should be a method that would be used to demonstrate if the goal is achieved.
2.3 Strategies that I would use to establish quality culture in
Talbots tooling company (TTC)
Talbots Tooling Company should develop a quality culture in order to remain competitive in
the market. Some of the strategies it could adopt include: developing a strategic and
functional management model of quality, innovate new products, establish good relationships
with suppliers and distributers, motivate their employees and development of a proper
communication. If these strategies are effectively employed, the company will then develop a
good quality culture.
Develop a strategic and functional management model of quality: It is observed that
organizations that dominate or have a big market share focuses on quality production. The
management of these organizations are so keen on quality just are they would be in financial
management. The company need to adopt the strategy in that when there is an issue with
quality they can question the quality department where the manager in charge is answerable.
This department is responsible for ensuring quality throughout the production process.
Paraphrase This Document
Need a fresh take? Get an instant paraphrase of this document with our AI Paraphraser
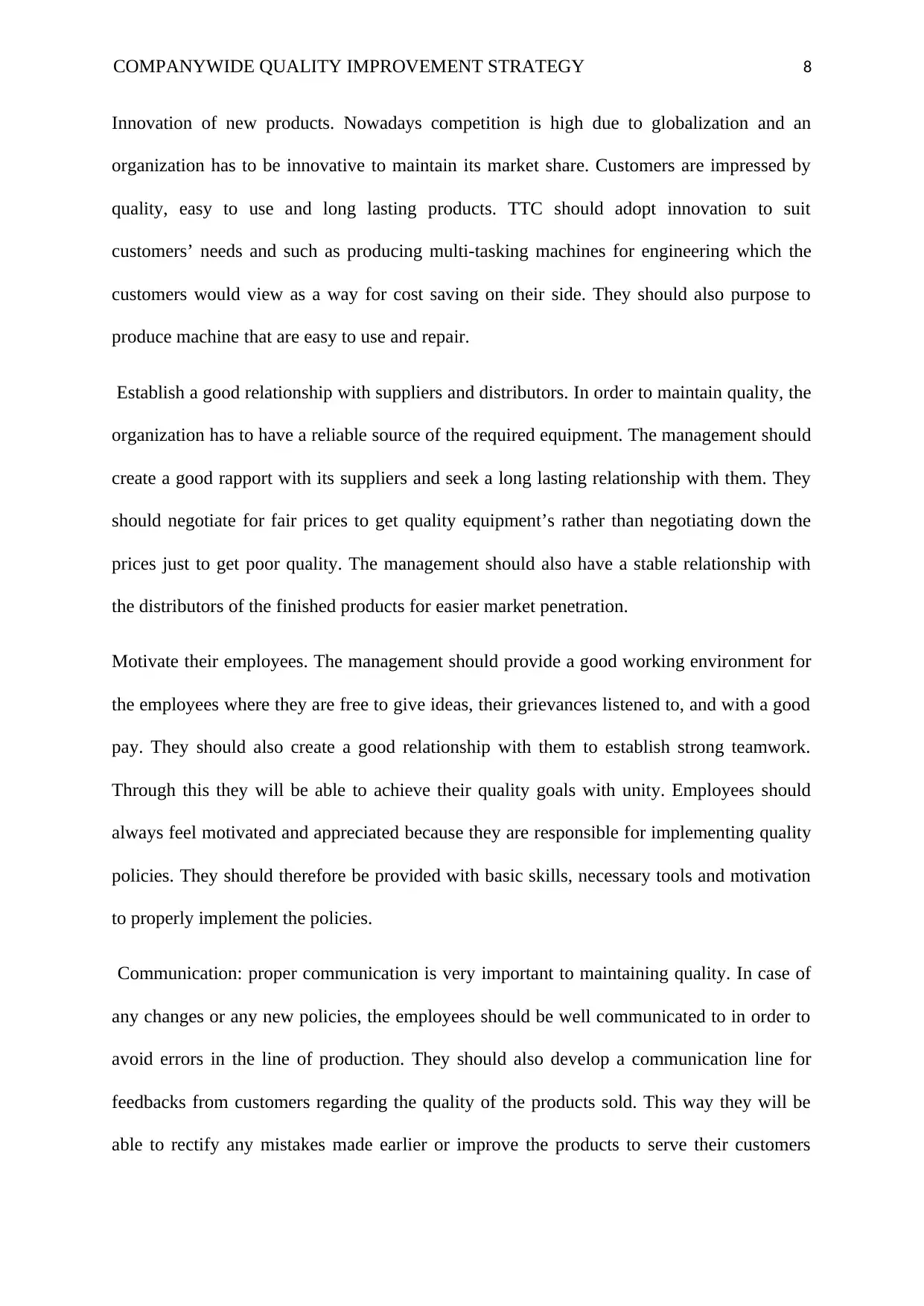
COMPANYWIDE QUALITY IMPROVEMENT STRATEGY 8
Innovation of new products. Nowadays competition is high due to globalization and an
organization has to be innovative to maintain its market share. Customers are impressed by
quality, easy to use and long lasting products. TTC should adopt innovation to suit
customers’ needs and such as producing multi-tasking machines for engineering which the
customers would view as a way for cost saving on their side. They should also purpose to
produce machine that are easy to use and repair.
Establish a good relationship with suppliers and distributors. In order to maintain quality, the
organization has to have a reliable source of the required equipment. The management should
create a good rapport with its suppliers and seek a long lasting relationship with them. They
should negotiate for fair prices to get quality equipment’s rather than negotiating down the
prices just to get poor quality. The management should also have a stable relationship with
the distributors of the finished products for easier market penetration.
Motivate their employees. The management should provide a good working environment for
the employees where they are free to give ideas, their grievances listened to, and with a good
pay. They should also create a good relationship with them to establish strong teamwork.
Through this they will be able to achieve their quality goals with unity. Employees should
always feel motivated and appreciated because they are responsible for implementing quality
policies. They should therefore be provided with basic skills, necessary tools and motivation
to properly implement the policies.
Communication: proper communication is very important to maintaining quality. In case of
any changes or any new policies, the employees should be well communicated to in order to
avoid errors in the line of production. They should also develop a communication line for
feedbacks from customers regarding the quality of the products sold. This way they will be
able to rectify any mistakes made earlier or improve the products to serve their customers
Innovation of new products. Nowadays competition is high due to globalization and an
organization has to be innovative to maintain its market share. Customers are impressed by
quality, easy to use and long lasting products. TTC should adopt innovation to suit
customers’ needs and such as producing multi-tasking machines for engineering which the
customers would view as a way for cost saving on their side. They should also purpose to
produce machine that are easy to use and repair.
Establish a good relationship with suppliers and distributors. In order to maintain quality, the
organization has to have a reliable source of the required equipment. The management should
create a good rapport with its suppliers and seek a long lasting relationship with them. They
should negotiate for fair prices to get quality equipment’s rather than negotiating down the
prices just to get poor quality. The management should also have a stable relationship with
the distributors of the finished products for easier market penetration.
Motivate their employees. The management should provide a good working environment for
the employees where they are free to give ideas, their grievances listened to, and with a good
pay. They should also create a good relationship with them to establish strong teamwork.
Through this they will be able to achieve their quality goals with unity. Employees should
always feel motivated and appreciated because they are responsible for implementing quality
policies. They should therefore be provided with basic skills, necessary tools and motivation
to properly implement the policies.
Communication: proper communication is very important to maintaining quality. In case of
any changes or any new policies, the employees should be well communicated to in order to
avoid errors in the line of production. They should also develop a communication line for
feedbacks from customers regarding the quality of the products sold. This way they will be
able to rectify any mistakes made earlier or improve the products to serve their customers
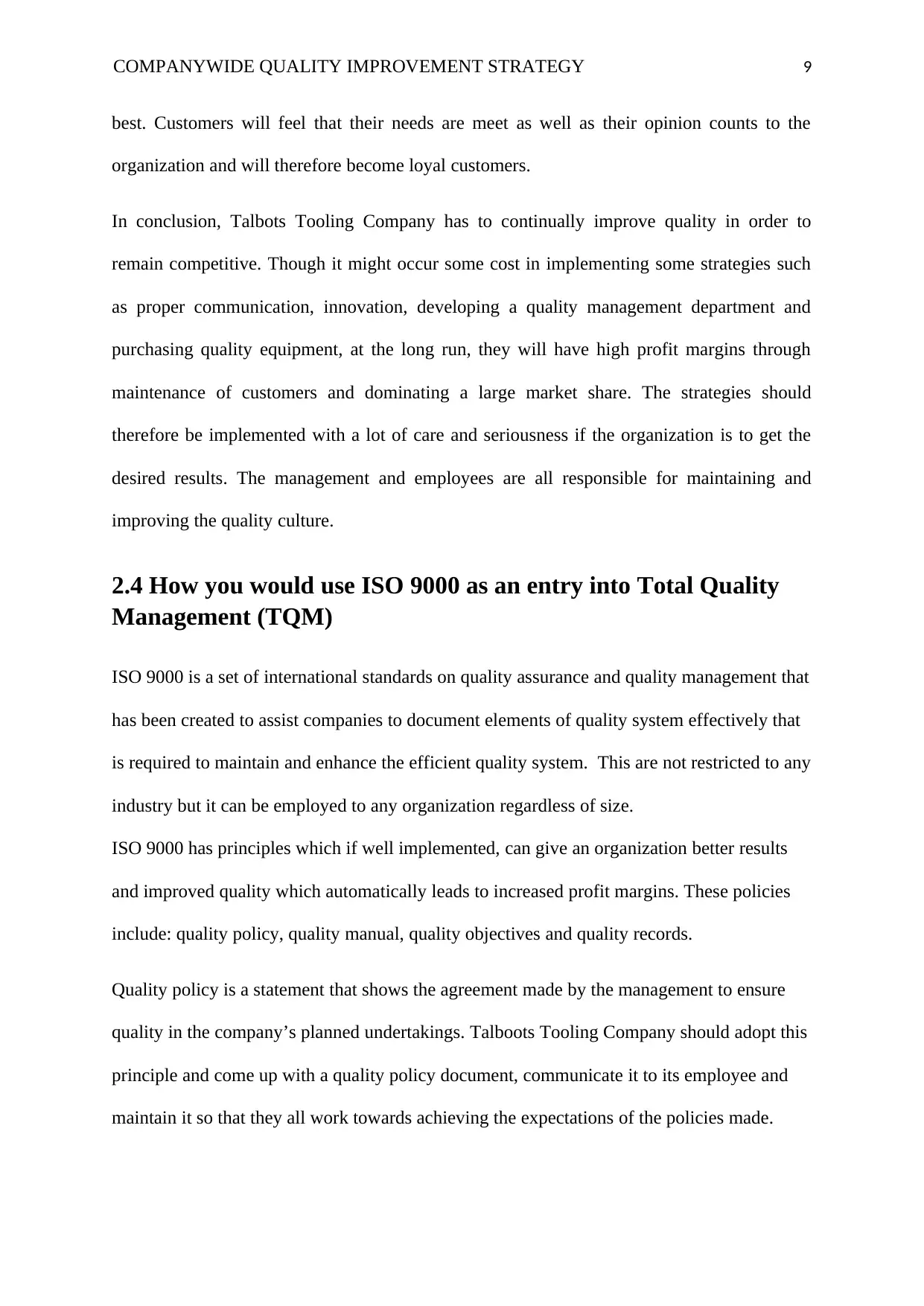
COMPANYWIDE QUALITY IMPROVEMENT STRATEGY 9
best. Customers will feel that their needs are meet as well as their opinion counts to the
organization and will therefore become loyal customers.
In conclusion, Talbots Tooling Company has to continually improve quality in order to
remain competitive. Though it might occur some cost in implementing some strategies such
as proper communication, innovation, developing a quality management department and
purchasing quality equipment, at the long run, they will have high profit margins through
maintenance of customers and dominating a large market share. The strategies should
therefore be implemented with a lot of care and seriousness if the organization is to get the
desired results. The management and employees are all responsible for maintaining and
improving the quality culture.
2.4 How you would use ISO 9000 as an entry into Total Quality
Management (TQM)
ISO 9000 is a set of international standards on quality assurance and quality management that
has been created to assist companies to document elements of quality system effectively that
is required to maintain and enhance the efficient quality system. This are not restricted to any
industry but it can be employed to any organization regardless of size.
ISO 9000 has principles which if well implemented, can give an organization better results
and improved quality which automatically leads to increased profit margins. These policies
include: quality policy, quality manual, quality objectives and quality records.
Quality policy is a statement that shows the agreement made by the management to ensure
quality in the company’s planned undertakings. Talboots Tooling Company should adopt this
principle and come up with a quality policy document, communicate it to its employee and
maintain it so that they all work towards achieving the expectations of the policies made.
best. Customers will feel that their needs are meet as well as their opinion counts to the
organization and will therefore become loyal customers.
In conclusion, Talbots Tooling Company has to continually improve quality in order to
remain competitive. Though it might occur some cost in implementing some strategies such
as proper communication, innovation, developing a quality management department and
purchasing quality equipment, at the long run, they will have high profit margins through
maintenance of customers and dominating a large market share. The strategies should
therefore be implemented with a lot of care and seriousness if the organization is to get the
desired results. The management and employees are all responsible for maintaining and
improving the quality culture.
2.4 How you would use ISO 9000 as an entry into Total Quality
Management (TQM)
ISO 9000 is a set of international standards on quality assurance and quality management that
has been created to assist companies to document elements of quality system effectively that
is required to maintain and enhance the efficient quality system. This are not restricted to any
industry but it can be employed to any organization regardless of size.
ISO 9000 has principles which if well implemented, can give an organization better results
and improved quality which automatically leads to increased profit margins. These policies
include: quality policy, quality manual, quality objectives and quality records.
Quality policy is a statement that shows the agreement made by the management to ensure
quality in the company’s planned undertakings. Talboots Tooling Company should adopt this
principle and come up with a quality policy document, communicate it to its employee and
maintain it so that they all work towards achieving the expectations of the policies made.
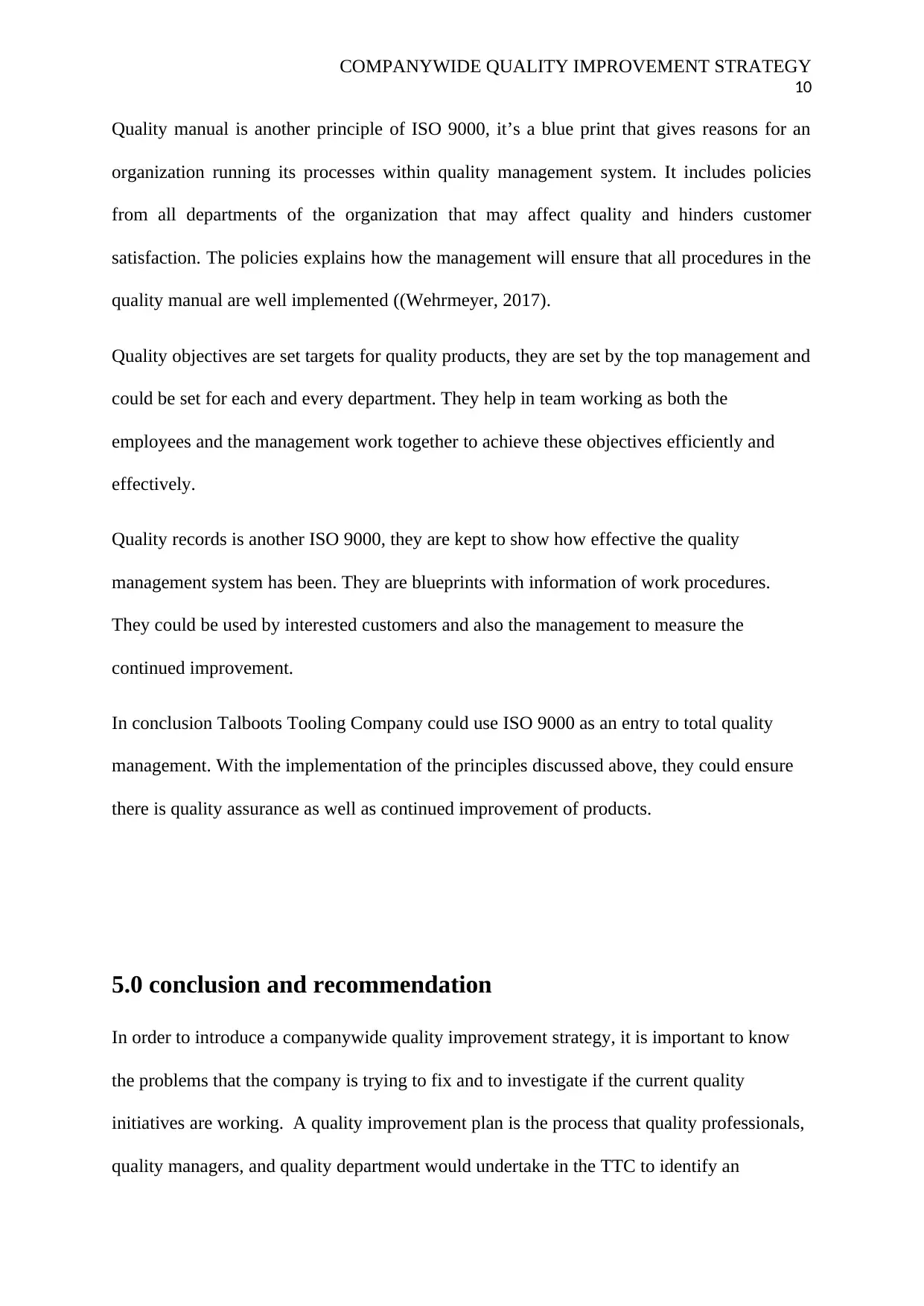
COMPANYWIDE QUALITY IMPROVEMENT STRATEGY
10
Quality manual is another principle of ISO 9000, it’s a blue print that gives reasons for an
organization running its processes within quality management system. It includes policies
from all departments of the organization that may affect quality and hinders customer
satisfaction. The policies explains how the management will ensure that all procedures in the
quality manual are well implemented ((Wehrmeyer, 2017).
Quality objectives are set targets for quality products, they are set by the top management and
could be set for each and every department. They help in team working as both the
employees and the management work together to achieve these objectives efficiently and
effectively.
Quality records is another ISO 9000, they are kept to show how effective the quality
management system has been. They are blueprints with information of work procedures.
They could be used by interested customers and also the management to measure the
continued improvement.
In conclusion Talboots Tooling Company could use ISO 9000 as an entry to total quality
management. With the implementation of the principles discussed above, they could ensure
there is quality assurance as well as continued improvement of products.
5.0 conclusion and recommendation
In order to introduce a companywide quality improvement strategy, it is important to know
the problems that the company is trying to fix and to investigate if the current quality
initiatives are working. A quality improvement plan is the process that quality professionals,
quality managers, and quality department would undertake in the TTC to identify an
10
Quality manual is another principle of ISO 9000, it’s a blue print that gives reasons for an
organization running its processes within quality management system. It includes policies
from all departments of the organization that may affect quality and hinders customer
satisfaction. The policies explains how the management will ensure that all procedures in the
quality manual are well implemented ((Wehrmeyer, 2017).
Quality objectives are set targets for quality products, they are set by the top management and
could be set for each and every department. They help in team working as both the
employees and the management work together to achieve these objectives efficiently and
effectively.
Quality records is another ISO 9000, they are kept to show how effective the quality
management system has been. They are blueprints with information of work procedures.
They could be used by interested customers and also the management to measure the
continued improvement.
In conclusion Talboots Tooling Company could use ISO 9000 as an entry to total quality
management. With the implementation of the principles discussed above, they could ensure
there is quality assurance as well as continued improvement of products.
5.0 conclusion and recommendation
In order to introduce a companywide quality improvement strategy, it is important to know
the problems that the company is trying to fix and to investigate if the current quality
initiatives are working. A quality improvement plan is the process that quality professionals,
quality managers, and quality department would undertake in the TTC to identify an
Secure Best Marks with AI Grader
Need help grading? Try our AI Grader for instant feedback on your assignments.
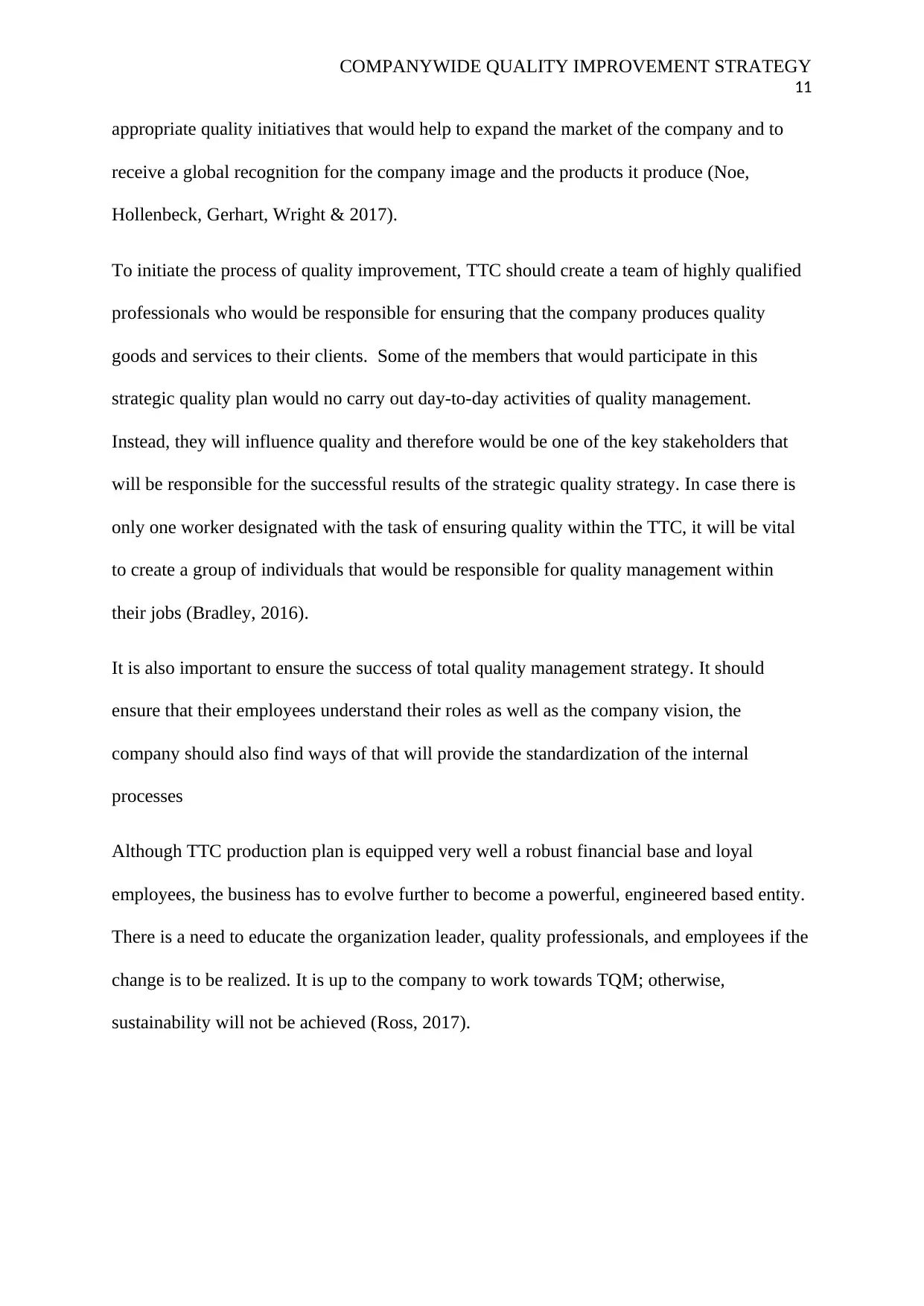
COMPANYWIDE QUALITY IMPROVEMENT STRATEGY
11
appropriate quality initiatives that would help to expand the market of the company and to
receive a global recognition for the company image and the products it produce (Noe,
Hollenbeck, Gerhart, Wright & 2017).
To initiate the process of quality improvement, TTC should create a team of highly qualified
professionals who would be responsible for ensuring that the company produces quality
goods and services to their clients. Some of the members that would participate in this
strategic quality plan would no carry out day-to-day activities of quality management.
Instead, they will influence quality and therefore would be one of the key stakeholders that
will be responsible for the successful results of the strategic quality strategy. In case there is
only one worker designated with the task of ensuring quality within the TTC, it will be vital
to create a group of individuals that would be responsible for quality management within
their jobs (Bradley, 2016).
It is also important to ensure the success of total quality management strategy. It should
ensure that their employees understand their roles as well as the company vision, the
company should also find ways of that will provide the standardization of the internal
processes
Although TTC production plan is equipped very well a robust financial base and loyal
employees, the business has to evolve further to become a powerful, engineered based entity.
There is a need to educate the organization leader, quality professionals, and employees if the
change is to be realized. It is up to the company to work towards TQM; otherwise,
sustainability will not be achieved (Ross, 2017).
11
appropriate quality initiatives that would help to expand the market of the company and to
receive a global recognition for the company image and the products it produce (Noe,
Hollenbeck, Gerhart, Wright & 2017).
To initiate the process of quality improvement, TTC should create a team of highly qualified
professionals who would be responsible for ensuring that the company produces quality
goods and services to their clients. Some of the members that would participate in this
strategic quality plan would no carry out day-to-day activities of quality management.
Instead, they will influence quality and therefore would be one of the key stakeholders that
will be responsible for the successful results of the strategic quality strategy. In case there is
only one worker designated with the task of ensuring quality within the TTC, it will be vital
to create a group of individuals that would be responsible for quality management within
their jobs (Bradley, 2016).
It is also important to ensure the success of total quality management strategy. It should
ensure that their employees understand their roles as well as the company vision, the
company should also find ways of that will provide the standardization of the internal
processes
Although TTC production plan is equipped very well a robust financial base and loyal
employees, the business has to evolve further to become a powerful, engineered based entity.
There is a need to educate the organization leader, quality professionals, and employees if the
change is to be realized. It is up to the company to work towards TQM; otherwise,
sustainability will not be achieved (Ross, 2017).
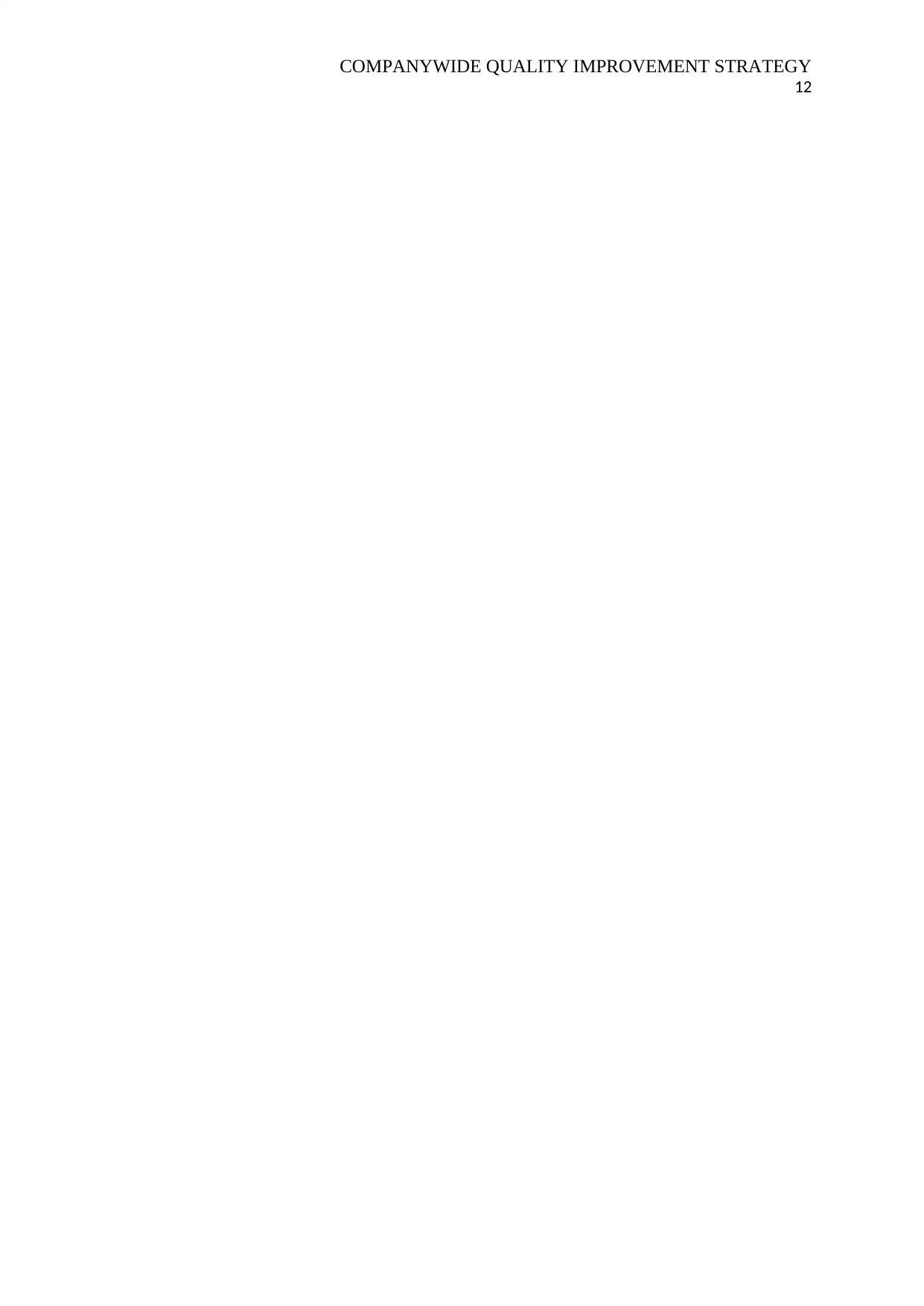
COMPANYWIDE QUALITY IMPROVEMENT STRATEGY
12
12
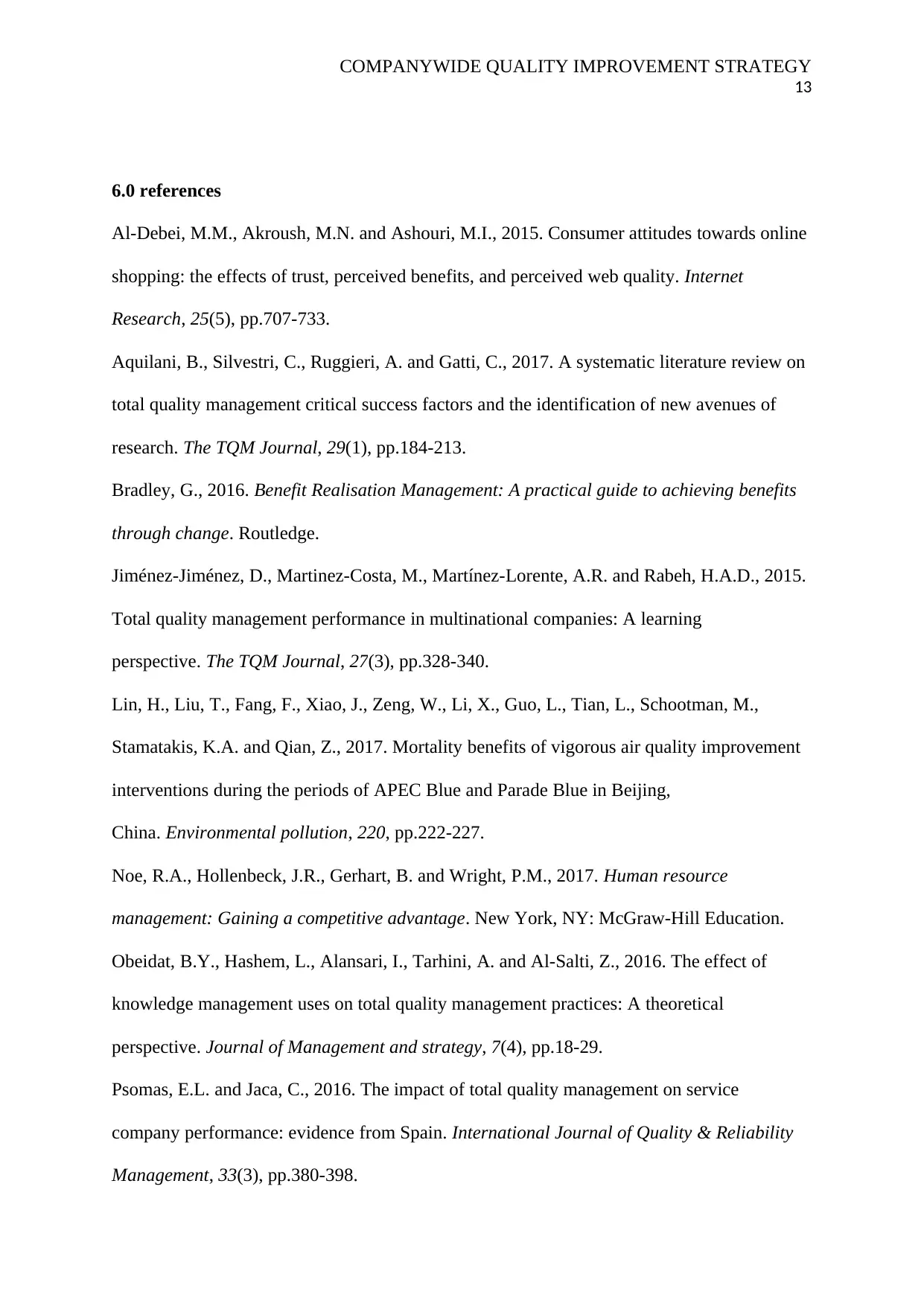
COMPANYWIDE QUALITY IMPROVEMENT STRATEGY
13
6.0 references
Al-Debei, M.M., Akroush, M.N. and Ashouri, M.I., 2015. Consumer attitudes towards online
shopping: the effects of trust, perceived benefits, and perceived web quality. Internet
Research, 25(5), pp.707-733.
Aquilani, B., Silvestri, C., Ruggieri, A. and Gatti, C., 2017. A systematic literature review on
total quality management critical success factors and the identification of new avenues of
research. The TQM Journal, 29(1), pp.184-213.
Bradley, G., 2016. Benefit Realisation Management: A practical guide to achieving benefits
through change. Routledge.
Jiménez-Jiménez, D., Martinez-Costa, M., Martínez-Lorente, A.R. and Rabeh, H.A.D., 2015.
Total quality management performance in multinational companies: A learning
perspective. The TQM Journal, 27(3), pp.328-340.
Lin, H., Liu, T., Fang, F., Xiao, J., Zeng, W., Li, X., Guo, L., Tian, L., Schootman, M.,
Stamatakis, K.A. and Qian, Z., 2017. Mortality benefits of vigorous air quality improvement
interventions during the periods of APEC Blue and Parade Blue in Beijing,
China. Environmental pollution, 220, pp.222-227.
Noe, R.A., Hollenbeck, J.R., Gerhart, B. and Wright, P.M., 2017. Human resource
management: Gaining a competitive advantage. New York, NY: McGraw-Hill Education.
Obeidat, B.Y., Hashem, L., Alansari, I., Tarhini, A. and Al-Salti, Z., 2016. The effect of
knowledge management uses on total quality management practices: A theoretical
perspective. Journal of Management and strategy, 7(4), pp.18-29.
Psomas, E.L. and Jaca, C., 2016. The impact of total quality management on service
company performance: evidence from Spain. International Journal of Quality & Reliability
Management, 33(3), pp.380-398.
13
6.0 references
Al-Debei, M.M., Akroush, M.N. and Ashouri, M.I., 2015. Consumer attitudes towards online
shopping: the effects of trust, perceived benefits, and perceived web quality. Internet
Research, 25(5), pp.707-733.
Aquilani, B., Silvestri, C., Ruggieri, A. and Gatti, C., 2017. A systematic literature review on
total quality management critical success factors and the identification of new avenues of
research. The TQM Journal, 29(1), pp.184-213.
Bradley, G., 2016. Benefit Realisation Management: A practical guide to achieving benefits
through change. Routledge.
Jiménez-Jiménez, D., Martinez-Costa, M., Martínez-Lorente, A.R. and Rabeh, H.A.D., 2015.
Total quality management performance in multinational companies: A learning
perspective. The TQM Journal, 27(3), pp.328-340.
Lin, H., Liu, T., Fang, F., Xiao, J., Zeng, W., Li, X., Guo, L., Tian, L., Schootman, M.,
Stamatakis, K.A. and Qian, Z., 2017. Mortality benefits of vigorous air quality improvement
interventions during the periods of APEC Blue and Parade Blue in Beijing,
China. Environmental pollution, 220, pp.222-227.
Noe, R.A., Hollenbeck, J.R., Gerhart, B. and Wright, P.M., 2017. Human resource
management: Gaining a competitive advantage. New York, NY: McGraw-Hill Education.
Obeidat, B.Y., Hashem, L., Alansari, I., Tarhini, A. and Al-Salti, Z., 2016. The effect of
knowledge management uses on total quality management practices: A theoretical
perspective. Journal of Management and strategy, 7(4), pp.18-29.
Psomas, E.L. and Jaca, C., 2016. The impact of total quality management on service
company performance: evidence from Spain. International Journal of Quality & Reliability
Management, 33(3), pp.380-398.
Paraphrase This Document
Need a fresh take? Get an instant paraphrase of this document with our AI Paraphraser
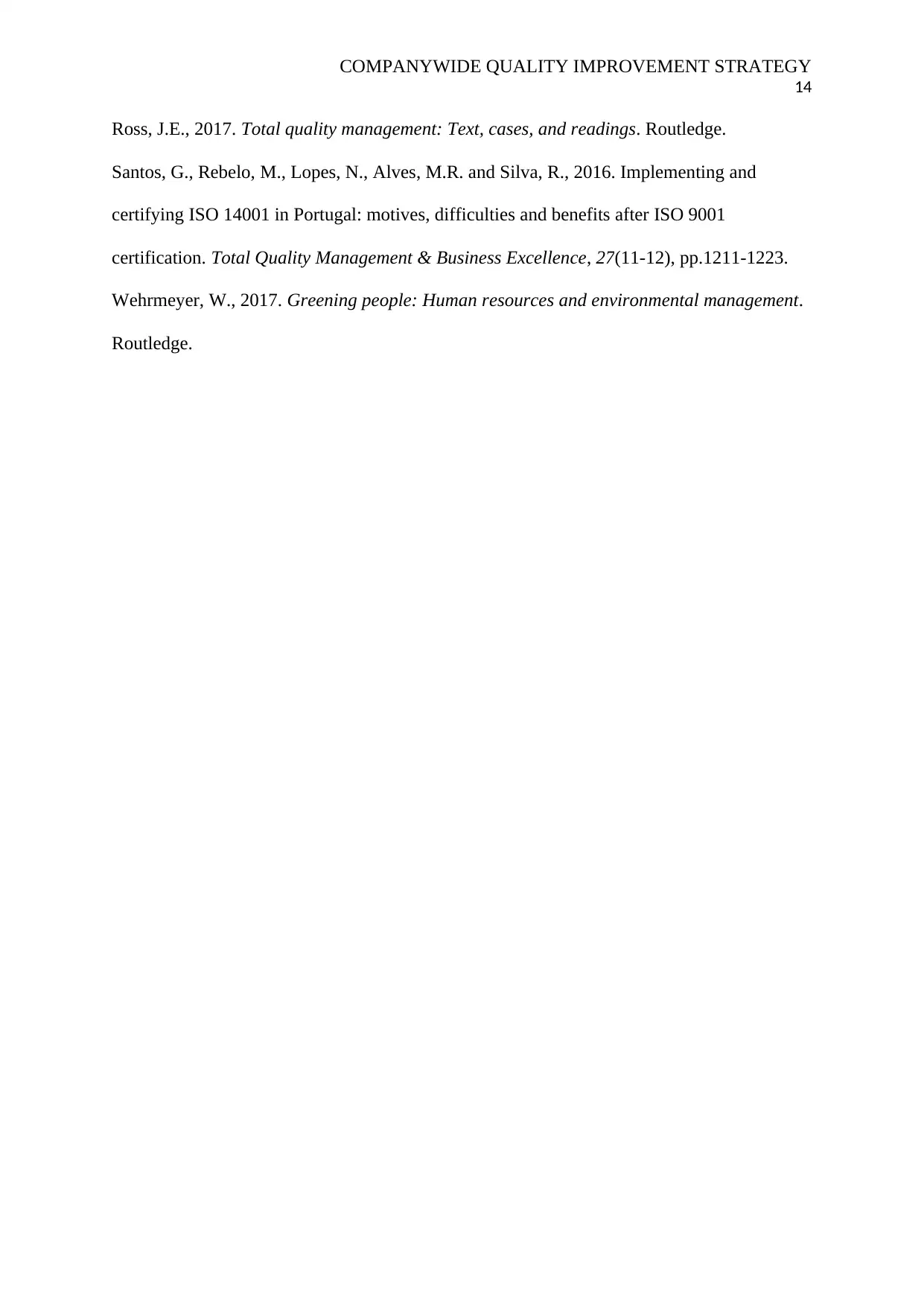
COMPANYWIDE QUALITY IMPROVEMENT STRATEGY
14
Ross, J.E., 2017. Total quality management: Text, cases, and readings. Routledge.
Santos, G., Rebelo, M., Lopes, N., Alves, M.R. and Silva, R., 2016. Implementing and
certifying ISO 14001 in Portugal: motives, difficulties and benefits after ISO 9001
certification. Total Quality Management & Business Excellence, 27(11-12), pp.1211-1223.
Wehrmeyer, W., 2017. Greening people: Human resources and environmental management.
Routledge.
14
Ross, J.E., 2017. Total quality management: Text, cases, and readings. Routledge.
Santos, G., Rebelo, M., Lopes, N., Alves, M.R. and Silva, R., 2016. Implementing and
certifying ISO 14001 in Portugal: motives, difficulties and benefits after ISO 9001
certification. Total Quality Management & Business Excellence, 27(11-12), pp.1211-1223.
Wehrmeyer, W., 2017. Greening people: Human resources and environmental management.
Routledge.
1 out of 14
Related Documents
![[object Object]](/_next/image/?url=%2F_next%2Fstatic%2Fmedia%2Flogo.6d15ce61.png&w=640&q=75)
Your All-in-One AI-Powered Toolkit for Academic Success.
+13062052269
info@desklib.com
Available 24*7 on WhatsApp / Email
Unlock your academic potential
© 2024 | Zucol Services PVT LTD | All rights reserved.