Companywide Quality Improvement Strategy
Added on 2023-01-19
14 Pages3275 Words74 Views
COMPANYWIDE QUALITY IMPROVEMENT STRATEGY 1
Student’s name
University
Course
Student’s name
University
Course
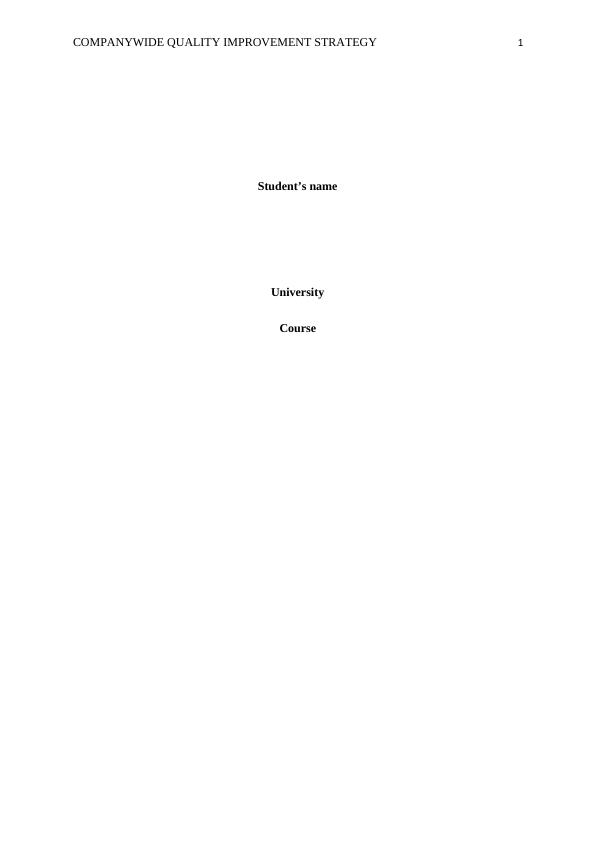
COMPANYWIDE QUALITY IMPROVEMENT STRATEGY 2
1.0 Introduction
. Talbot Tooling Company (TTC), is a manufacturing company founded in early 1960s by a
young engineer. The company is situated in North East England.
The main items being manufactured by TTC involves: engineering callipers, engineers’ rules
and scribes. The company intends to expand their products to include the micrometres and
other varieties of products that will demand high quality skills and materials to produce
precise and durable items.
The company had to develop a strategy that could help them to be sustainable due to
reduction in engineering in England. Among the strategies that was developed by the
company were equipping it with robust financial and employment of loyal customers. This
enable the company to grow into a new engineered based entity.
For the company to stay competitive in the market there is need to employ total quality
management. This will enable the management to uphold high quality standards that meet the
market needs. My main reason of writing this paper is to analyse Talbots tooling company
case so as to assist them to adopt total quality management, I will explain the meaning of
quality and the elements of total quality management, state the steps for total quality
management implementation that the company should undertake, explain the strategies that I
will use to establish a quality culture in Talbots Tooling Company (TTC) and to explain how
I will apply ISO 9000 as an entry into Total Quality Management.
2.1 Meaning Quality and elements of Total Quality Management
(TQM)
2.1.1 Meaning of quality
Quality is a fitness for purpose of a certain product or service at a particular given time. It is
the ability of an item or a service to attain an agreed and predetermined level of performance,
1.0 Introduction
. Talbot Tooling Company (TTC), is a manufacturing company founded in early 1960s by a
young engineer. The company is situated in North East England.
The main items being manufactured by TTC involves: engineering callipers, engineers’ rules
and scribes. The company intends to expand their products to include the micrometres and
other varieties of products that will demand high quality skills and materials to produce
precise and durable items.
The company had to develop a strategy that could help them to be sustainable due to
reduction in engineering in England. Among the strategies that was developed by the
company were equipping it with robust financial and employment of loyal customers. This
enable the company to grow into a new engineered based entity.
For the company to stay competitive in the market there is need to employ total quality
management. This will enable the management to uphold high quality standards that meet the
market needs. My main reason of writing this paper is to analyse Talbots tooling company
case so as to assist them to adopt total quality management, I will explain the meaning of
quality and the elements of total quality management, state the steps for total quality
management implementation that the company should undertake, explain the strategies that I
will use to establish a quality culture in Talbots Tooling Company (TTC) and to explain how
I will apply ISO 9000 as an entry into Total Quality Management.
2.1 Meaning Quality and elements of Total Quality Management
(TQM)
2.1.1 Meaning of quality
Quality is a fitness for purpose of a certain product or service at a particular given time. It is
the ability of an item or a service to attain an agreed and predetermined level of performance,
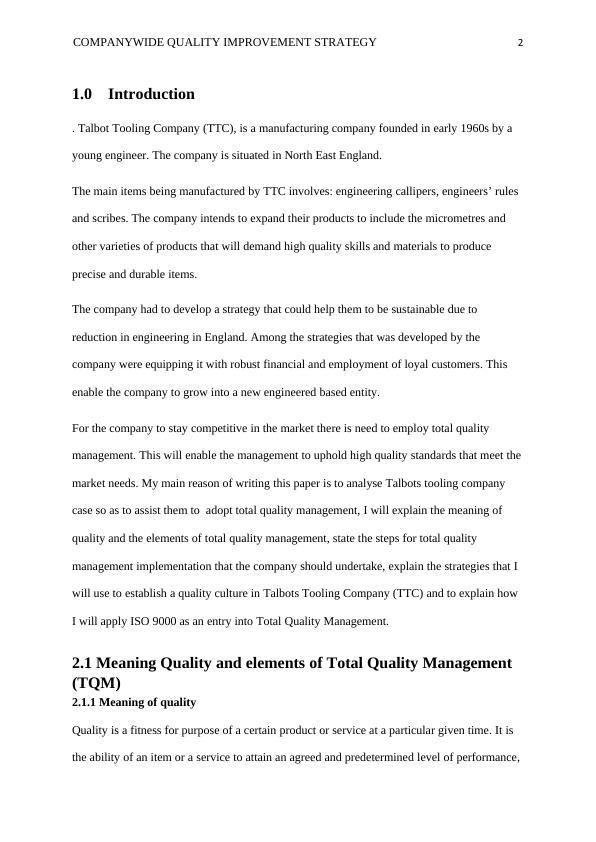
COMPANYWIDE QUALITY IMPROVEMENT STRATEGY 3
achieving the goal regularly in a cost effective way. Quality in business can be also can also
be referred to ‘'the perception of the degree to which the product or a service meets the
customer's expectations''. Quality improvement in business has many definitions, but it is
mostly taken to be an approach that enables an organization, team or an individual to improve
performance by recognizing and eliminating low quality in every aspect of service delivery
(Santos, Rebelo, Lopes, Alves & Silva, 2016.).
2.1.2 Key elements of total quality
Complete quality management (TQM) is a philosophy that endeavors to attain the best results
by bringing together all business processes and activities on customer satisfaction. A proper
Total Quality Management involves a constant improvement of employees and of an
organization. The following are the key elements of quality:
Ethics
Ethics refers to the study of right and wrong. To enhance total quality, it is important to
understand the ethical thing that should be done both as an organization and as an individual.
An organization needs to introduce a perfect code of conduct that will help them to attain
quality.
Integrity
Integrity involves the act of acting according to the values of the organization in an open and
an honest environment.
Trust
Effective and efficient total quality needs a good relationship among the people that are
working in an organization. For an organization to improve and provide a product or a service
of high quality, all staff and employees should work trustfully. These will make the
organization problem identification, problem investigation, problem resolution to be easier.
achieving the goal regularly in a cost effective way. Quality in business can be also can also
be referred to ‘'the perception of the degree to which the product or a service meets the
customer's expectations''. Quality improvement in business has many definitions, but it is
mostly taken to be an approach that enables an organization, team or an individual to improve
performance by recognizing and eliminating low quality in every aspect of service delivery
(Santos, Rebelo, Lopes, Alves & Silva, 2016.).
2.1.2 Key elements of total quality
Complete quality management (TQM) is a philosophy that endeavors to attain the best results
by bringing together all business processes and activities on customer satisfaction. A proper
Total Quality Management involves a constant improvement of employees and of an
organization. The following are the key elements of quality:
Ethics
Ethics refers to the study of right and wrong. To enhance total quality, it is important to
understand the ethical thing that should be done both as an organization and as an individual.
An organization needs to introduce a perfect code of conduct that will help them to attain
quality.
Integrity
Integrity involves the act of acting according to the values of the organization in an open and
an honest environment.
Trust
Effective and efficient total quality needs a good relationship among the people that are
working in an organization. For an organization to improve and provide a product or a service
of high quality, all staff and employees should work trustfully. These will make the
organization problem identification, problem investigation, problem resolution to be easier.
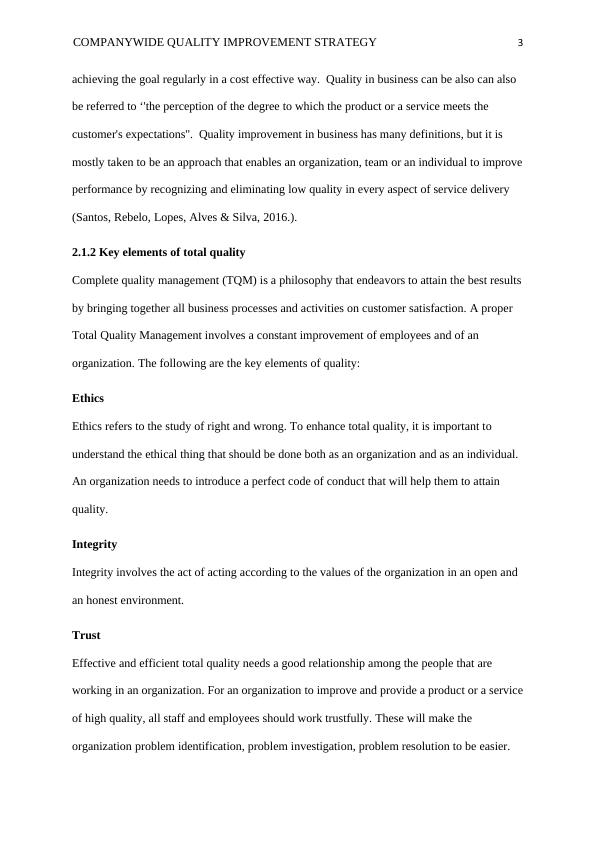
COMPANYWIDE QUALITY IMPROVEMENT STRATEGY 4
Training
Training is very important to workers of an organization and is one of the ways that helps in
achieving high quality and high level of efficiency. All employees of an organization need to
be trained by quality professionals
Communication
Effective communication starts from the basis that surrounds the breaches and the bricks of
the roof. The only method to attain optimal performance and continually improve product
quality is to ensure free flow of ideas within and without of an organization.
Leadership
While teamwork and training are essential in making employees to be valuable in a company,
leaders have an important role to play in coupling the potential. All managers and supervisors
should understand the total quality methodology and philosophy and should be in a position
to implement and at the same time clearly transmitting, strategies, values, goals, and
directions to all teams of the organization (Al-Debei, Akroush & Ashouri, 2015.).
Recognition
This part involves an encouragement and positive feedback that both suggestions and
achievements should result in an organization. Supervisors detect and look for contributions,
and give recognition when they are made.
Teamwork
In order to achieve a common goal and provide a high level of customer service needs
efficient and effective teamwork. Employees should learn how to work as a team.
Organizations should also enable an open discussion to address both challenges and
solutions.
Training
Training is very important to workers of an organization and is one of the ways that helps in
achieving high quality and high level of efficiency. All employees of an organization need to
be trained by quality professionals
Communication
Effective communication starts from the basis that surrounds the breaches and the bricks of
the roof. The only method to attain optimal performance and continually improve product
quality is to ensure free flow of ideas within and without of an organization.
Leadership
While teamwork and training are essential in making employees to be valuable in a company,
leaders have an important role to play in coupling the potential. All managers and supervisors
should understand the total quality methodology and philosophy and should be in a position
to implement and at the same time clearly transmitting, strategies, values, goals, and
directions to all teams of the organization (Al-Debei, Akroush & Ashouri, 2015.).
Recognition
This part involves an encouragement and positive feedback that both suggestions and
achievements should result in an organization. Supervisors detect and look for contributions,
and give recognition when they are made.
Teamwork
In order to achieve a common goal and provide a high level of customer service needs
efficient and effective teamwork. Employees should learn how to work as a team.
Organizations should also enable an open discussion to address both challenges and
solutions.
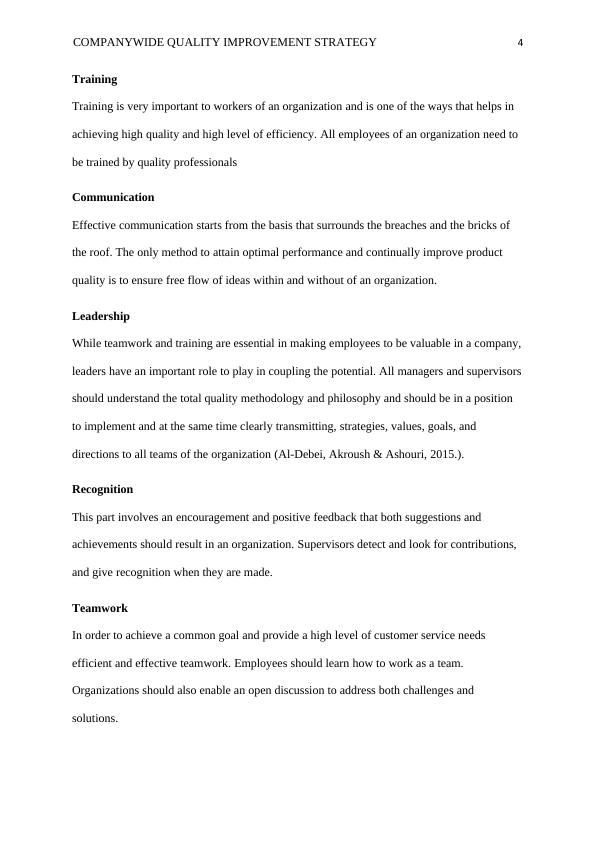
End of preview
Want to access all the pages? Upload your documents or become a member.
Related Documents
Quality Management for Organizational Excellencelg...
|16
|5294
|81
Business Ethics Responsibility and Sustainabilitylg...
|11
|3624
|38
Quality Management for Organisational Excellencelg...
|12
|3626
|419
Quality Management for Organisational Excellence - UGB 262 Canvas 202021lg...
|11
|3486
|80
Companywide Quality Improvement Strategy for Quality Tooling Companylg...
|11
|3703
|325
Project Management & Total Quality Managementlg...
|9
|3015
|42