Integrated Management System Implementation
VerifiedAdded on 2020/01/21
|11
|3496
|469
AI Summary
The assignment focuses on implementing integrated management systems, particularly within the context of Small and Medium-Sized Enterprises (SMEs). It delves into Total Quality Management (TQM) principles and methodologies, highlighting their relevance and practical applications in improving organizational efficiency, customer satisfaction, and overall business excellence. The assignment references a variety of scholarly sources to provide a comprehensive understanding of the topic.
Contribute Materials
Your contribution can guide someone’s learning journey. Share your
documents today.
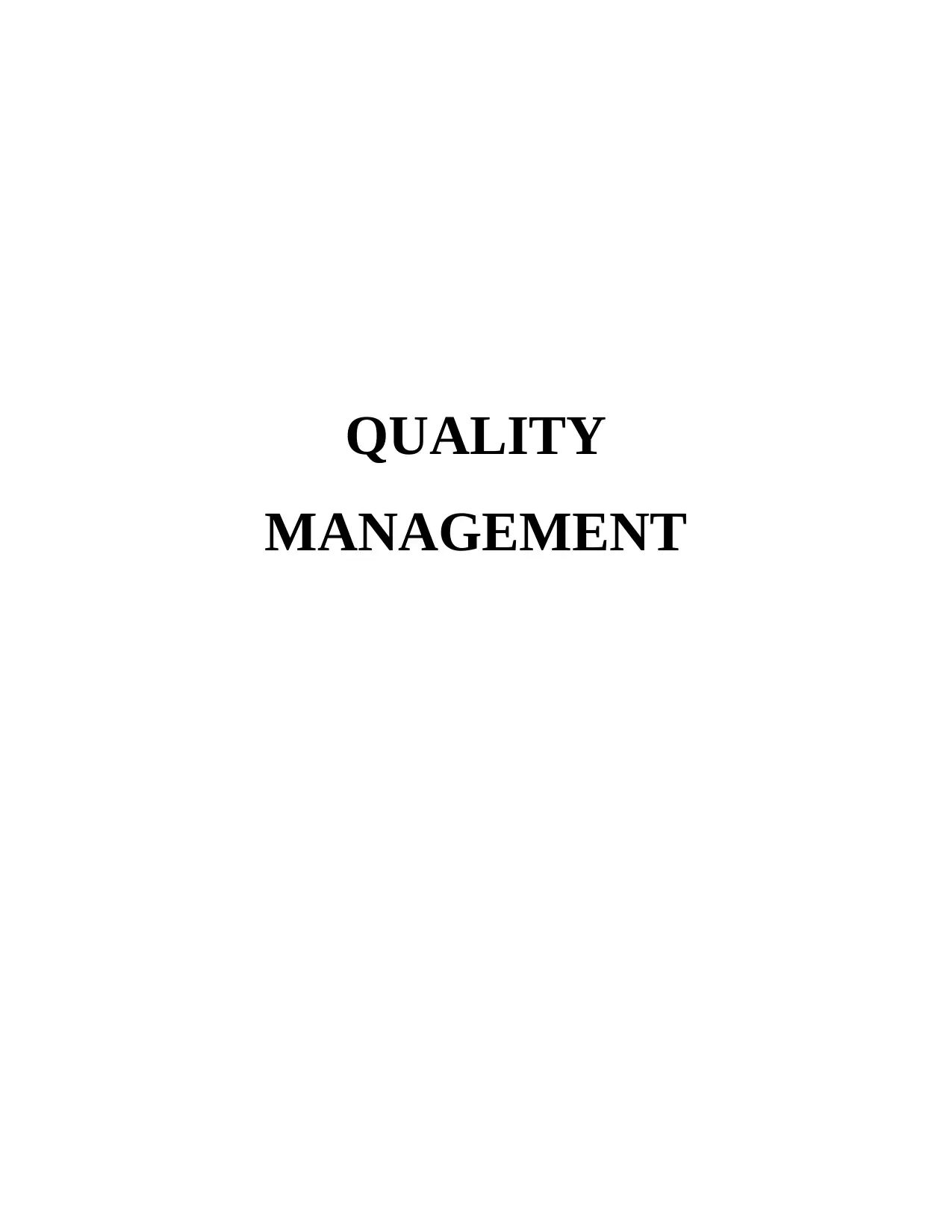
QUALITY
MANAGEMENT
MANAGEMENT
Secure Best Marks with AI Grader
Need help grading? Try our AI Grader for instant feedback on your assignments.
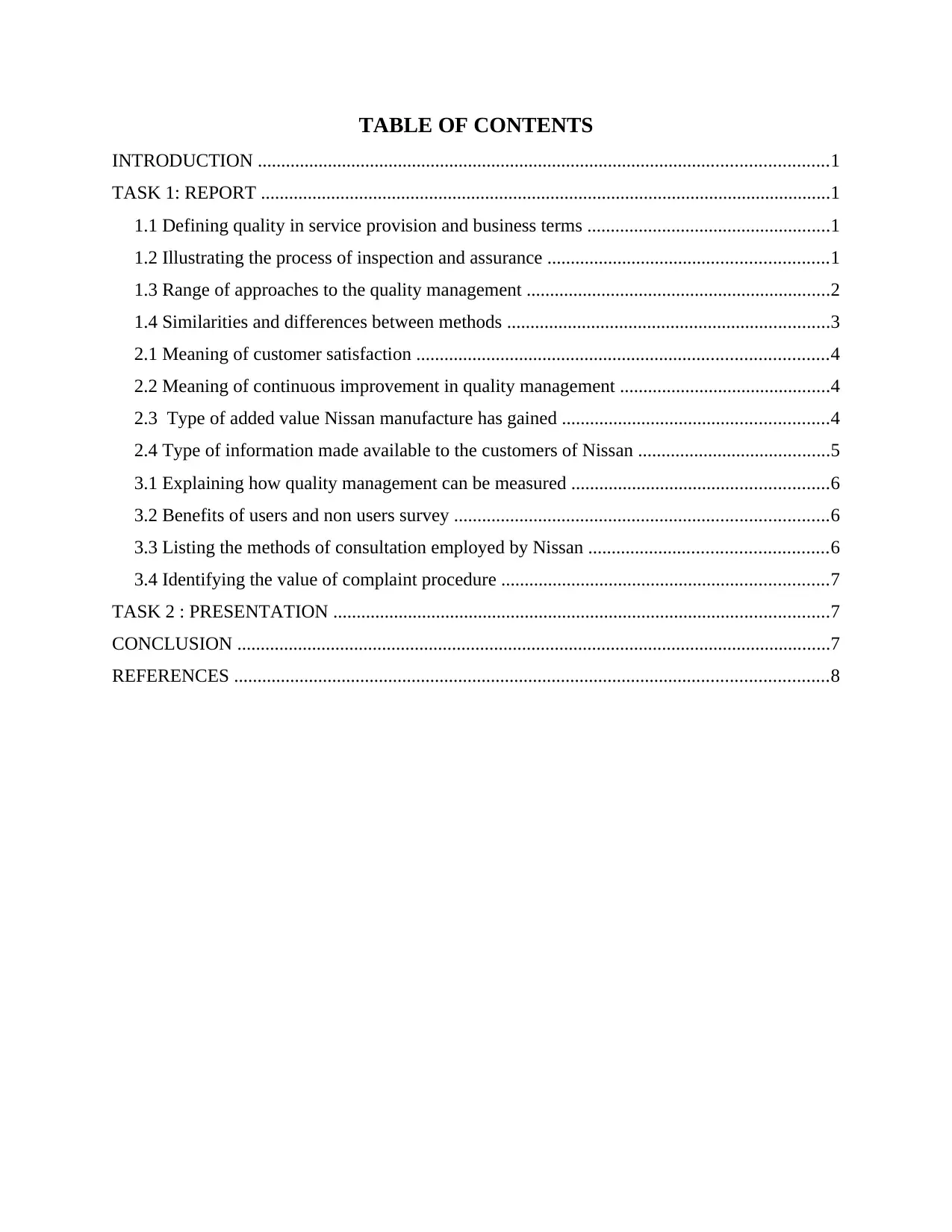
TABLE OF CONTENTS
INTRODUCTION ..........................................................................................................................1
TASK 1: REPORT ..........................................................................................................................1
1.1 Defining quality in service provision and business terms ....................................................1
1.2 Illustrating the process of inspection and assurance ............................................................1
1.3 Range of approaches to the quality management .................................................................2
1.4 Similarities and differences between methods .....................................................................3
2.1 Meaning of customer satisfaction ........................................................................................4
2.2 Meaning of continuous improvement in quality management .............................................4
2.3 Type of added value Nissan manufacture has gained .........................................................4
2.4 Type of information made available to the customers of Nissan .........................................5
3.1 Explaining how quality management can be measured .......................................................6
3.2 Benefits of users and non users survey ................................................................................6
3.3 Listing the methods of consultation employed by Nissan ...................................................6
3.4 Identifying the value of complaint procedure ......................................................................7
TASK 2 : PRESENTATION ..........................................................................................................7
CONCLUSION ...............................................................................................................................7
REFERENCES ...............................................................................................................................8
INTRODUCTION ..........................................................................................................................1
TASK 1: REPORT ..........................................................................................................................1
1.1 Defining quality in service provision and business terms ....................................................1
1.2 Illustrating the process of inspection and assurance ............................................................1
1.3 Range of approaches to the quality management .................................................................2
1.4 Similarities and differences between methods .....................................................................3
2.1 Meaning of customer satisfaction ........................................................................................4
2.2 Meaning of continuous improvement in quality management .............................................4
2.3 Type of added value Nissan manufacture has gained .........................................................4
2.4 Type of information made available to the customers of Nissan .........................................5
3.1 Explaining how quality management can be measured .......................................................6
3.2 Benefits of users and non users survey ................................................................................6
3.3 Listing the methods of consultation employed by Nissan ...................................................6
3.4 Identifying the value of complaint procedure ......................................................................7
TASK 2 : PRESENTATION ..........................................................................................................7
CONCLUSION ...............................................................................................................................7
REFERENCES ...............................................................................................................................8
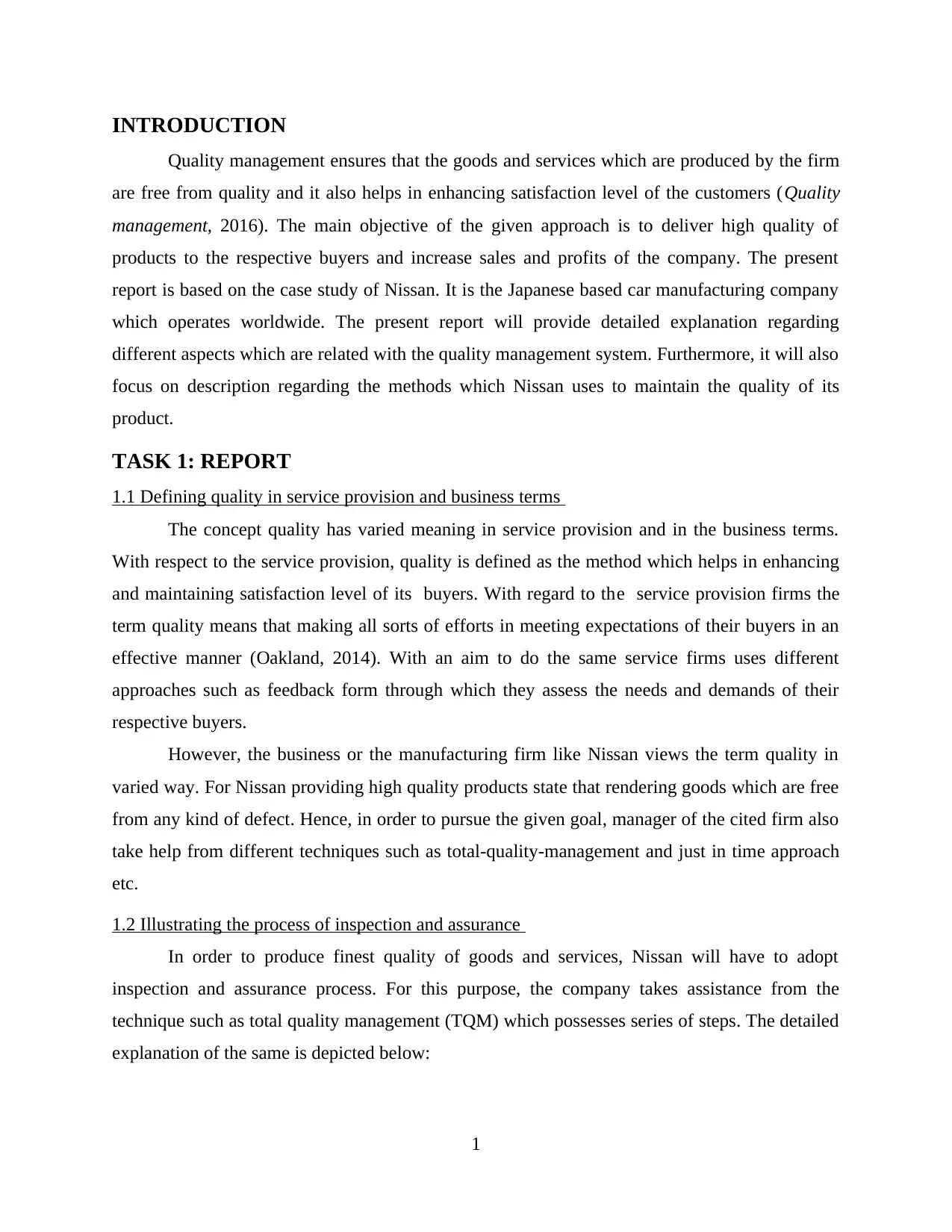
INTRODUCTION
Quality management ensures that the goods and services which are produced by the firm
are free from quality and it also helps in enhancing satisfaction level of the customers (Quality
management, 2016). The main objective of the given approach is to deliver high quality of
products to the respective buyers and increase sales and profits of the company. The present
report is based on the case study of Nissan. It is the Japanese based car manufacturing company
which operates worldwide. The present report will provide detailed explanation regarding
different aspects which are related with the quality management system. Furthermore, it will also
focus on description regarding the methods which Nissan uses to maintain the quality of its
product.
TASK 1: REPORT
1.1 Defining quality in service provision and business terms
The concept quality has varied meaning in service provision and in the business terms.
With respect to the service provision, quality is defined as the method which helps in enhancing
and maintaining satisfaction level of its buyers. With regard to the service provision firms the
term quality means that making all sorts of efforts in meeting expectations of their buyers in an
effective manner (Oakland, 2014). With an aim to do the same service firms uses different
approaches such as feedback form through which they assess the needs and demands of their
respective buyers.
However, the business or the manufacturing firm like Nissan views the term quality in
varied way. For Nissan providing high quality products state that rendering goods which are free
from any kind of defect. Hence, in order to pursue the given goal, manager of the cited firm also
take help from different techniques such as total-quality-management and just in time approach
etc.
1.2 Illustrating the process of inspection and assurance
In order to produce finest quality of goods and services, Nissan will have to adopt
inspection and assurance process. For this purpose, the company takes assistance from the
technique such as total quality management (TQM) which possesses series of steps. The detailed
explanation of the same is depicted below:
1
Quality management ensures that the goods and services which are produced by the firm
are free from quality and it also helps in enhancing satisfaction level of the customers (Quality
management, 2016). The main objective of the given approach is to deliver high quality of
products to the respective buyers and increase sales and profits of the company. The present
report is based on the case study of Nissan. It is the Japanese based car manufacturing company
which operates worldwide. The present report will provide detailed explanation regarding
different aspects which are related with the quality management system. Furthermore, it will also
focus on description regarding the methods which Nissan uses to maintain the quality of its
product.
TASK 1: REPORT
1.1 Defining quality in service provision and business terms
The concept quality has varied meaning in service provision and in the business terms.
With respect to the service provision, quality is defined as the method which helps in enhancing
and maintaining satisfaction level of its buyers. With regard to the service provision firms the
term quality means that making all sorts of efforts in meeting expectations of their buyers in an
effective manner (Oakland, 2014). With an aim to do the same service firms uses different
approaches such as feedback form through which they assess the needs and demands of their
respective buyers.
However, the business or the manufacturing firm like Nissan views the term quality in
varied way. For Nissan providing high quality products state that rendering goods which are free
from any kind of defect. Hence, in order to pursue the given goal, manager of the cited firm also
take help from different techniques such as total-quality-management and just in time approach
etc.
1.2 Illustrating the process of inspection and assurance
In order to produce finest quality of goods and services, Nissan will have to adopt
inspection and assurance process. For this purpose, the company takes assistance from the
technique such as total quality management (TQM) which possesses series of steps. The detailed
explanation of the same is depicted below:
1
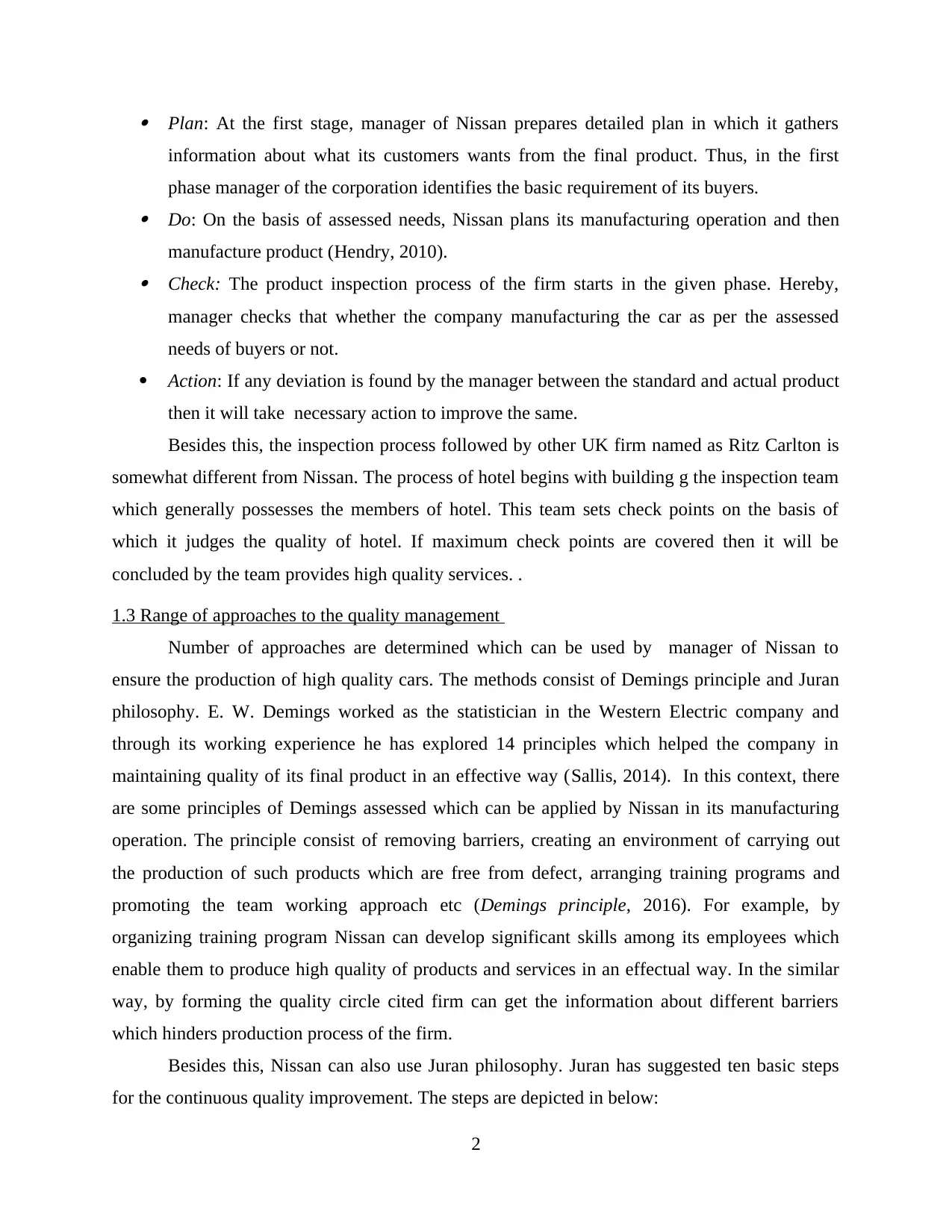
Plan: At the first stage, manager of Nissan prepares detailed plan in which it gathers
information about what its customers wants from the final product. Thus, in the first
phase manager of the corporation identifies the basic requirement of its buyers. Do: On the basis of assessed needs, Nissan plans its manufacturing operation and then
manufacture product (Hendry, 2010). Check: The product inspection process of the firm starts in the given phase. Hereby,
manager checks that whether the company manufacturing the car as per the assessed
needs of buyers or not.
Action: If any deviation is found by the manager between the standard and actual product
then it will take necessary action to improve the same.
Besides this, the inspection process followed by other UK firm named as Ritz Carlton is
somewhat different from Nissan. The process of hotel begins with building g the inspection team
which generally possesses the members of hotel. This team sets check points on the basis of
which it judges the quality of hotel. If maximum check points are covered then it will be
concluded by the team provides high quality services. .
1.3 Range of approaches to the quality management
Number of approaches are determined which can be used by manager of Nissan to
ensure the production of high quality cars. The methods consist of Demings principle and Juran
philosophy. E. W. Demings worked as the statistician in the Western Electric company and
through its working experience he has explored 14 principles which helped the company in
maintaining quality of its final product in an effective way (Sallis, 2014). In this context, there
are some principles of Demings assessed which can be applied by Nissan in its manufacturing
operation. The principle consist of removing barriers, creating an environment of carrying out
the production of such products which are free from defect, arranging training programs and
promoting the team working approach etc (Demings principle, 2016). For example, by
organizing training program Nissan can develop significant skills among its employees which
enable them to produce high quality of products and services in an effectual way. In the similar
way, by forming the quality circle cited firm can get the information about different barriers
which hinders production process of the firm.
Besides this, Nissan can also use Juran philosophy. Juran has suggested ten basic steps
for the continuous quality improvement. The steps are depicted in below:
2
information about what its customers wants from the final product. Thus, in the first
phase manager of the corporation identifies the basic requirement of its buyers. Do: On the basis of assessed needs, Nissan plans its manufacturing operation and then
manufacture product (Hendry, 2010). Check: The product inspection process of the firm starts in the given phase. Hereby,
manager checks that whether the company manufacturing the car as per the assessed
needs of buyers or not.
Action: If any deviation is found by the manager between the standard and actual product
then it will take necessary action to improve the same.
Besides this, the inspection process followed by other UK firm named as Ritz Carlton is
somewhat different from Nissan. The process of hotel begins with building g the inspection team
which generally possesses the members of hotel. This team sets check points on the basis of
which it judges the quality of hotel. If maximum check points are covered then it will be
concluded by the team provides high quality services. .
1.3 Range of approaches to the quality management
Number of approaches are determined which can be used by manager of Nissan to
ensure the production of high quality cars. The methods consist of Demings principle and Juran
philosophy. E. W. Demings worked as the statistician in the Western Electric company and
through its working experience he has explored 14 principles which helped the company in
maintaining quality of its final product in an effective way (Sallis, 2014). In this context, there
are some principles of Demings assessed which can be applied by Nissan in its manufacturing
operation. The principle consist of removing barriers, creating an environment of carrying out
the production of such products which are free from defect, arranging training programs and
promoting the team working approach etc (Demings principle, 2016). For example, by
organizing training program Nissan can develop significant skills among its employees which
enable them to produce high quality of products and services in an effectual way. In the similar
way, by forming the quality circle cited firm can get the information about different barriers
which hinders production process of the firm.
Besides this, Nissan can also use Juran philosophy. Juran has suggested ten basic steps
for the continuous quality improvement. The steps are depicted in below:
2
Secure Best Marks with AI Grader
Need help grading? Try our AI Grader for instant feedback on your assignments.
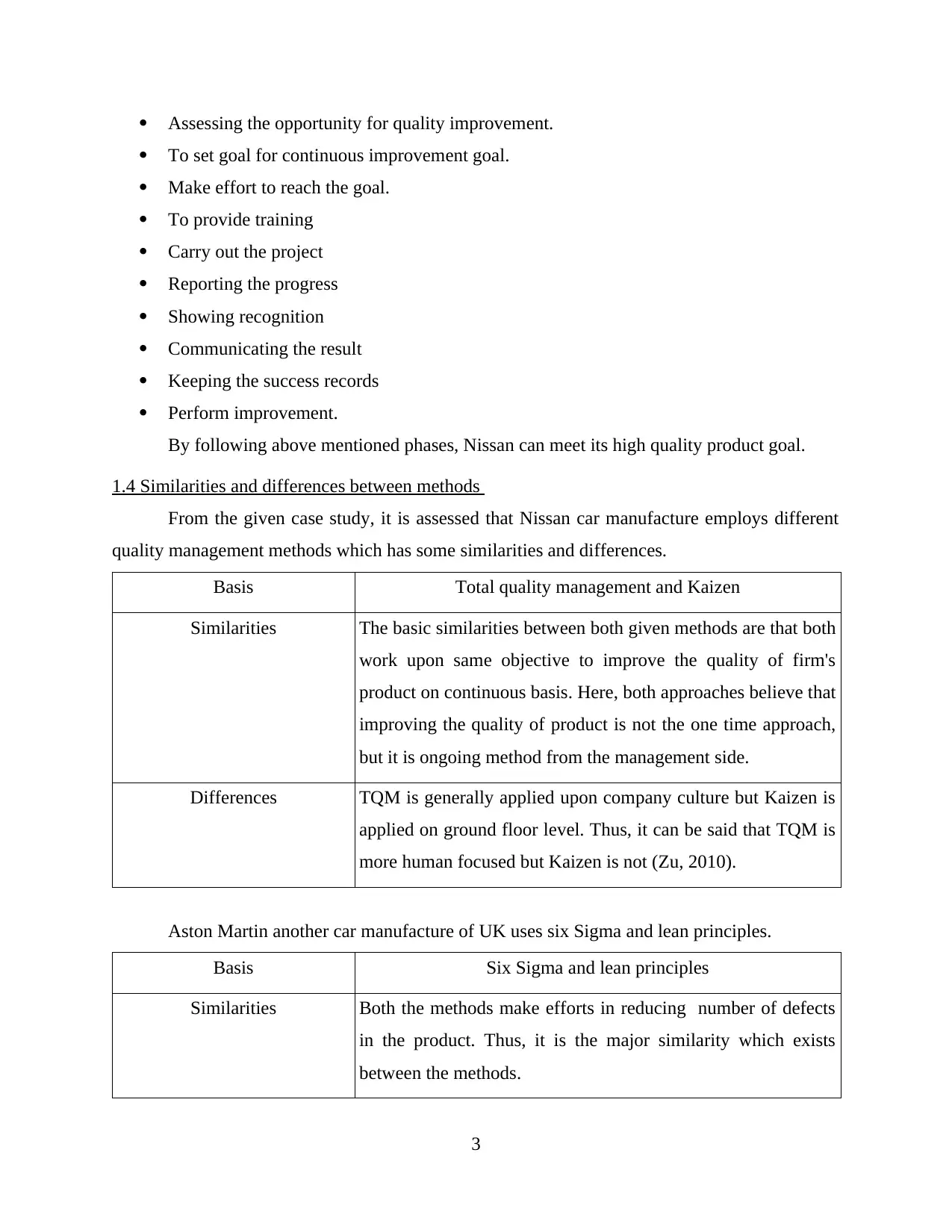
Assessing the opportunity for quality improvement.
To set goal for continuous improvement goal.
Make effort to reach the goal.
To provide training
Carry out the project
Reporting the progress
Showing recognition
Communicating the result
Keeping the success records
Perform improvement.
By following above mentioned phases, Nissan can meet its high quality product goal.
1.4 Similarities and differences between methods
From the given case study, it is assessed that Nissan car manufacture employs different
quality management methods which has some similarities and differences.
Basis Total quality management and Kaizen
Similarities The basic similarities between both given methods are that both
work upon same objective to improve the quality of firm's
product on continuous basis. Here, both approaches believe that
improving the quality of product is not the one time approach,
but it is ongoing method from the management side.
Differences TQM is generally applied upon company culture but Kaizen is
applied on ground floor level. Thus, it can be said that TQM is
more human focused but Kaizen is not (Zu, 2010).
Aston Martin another car manufacture of UK uses six Sigma and lean principles.
Basis Six Sigma and lean principles
Similarities Both the methods make efforts in reducing number of defects
in the product. Thus, it is the major similarity which exists
between the methods.
3
To set goal for continuous improvement goal.
Make effort to reach the goal.
To provide training
Carry out the project
Reporting the progress
Showing recognition
Communicating the result
Keeping the success records
Perform improvement.
By following above mentioned phases, Nissan can meet its high quality product goal.
1.4 Similarities and differences between methods
From the given case study, it is assessed that Nissan car manufacture employs different
quality management methods which has some similarities and differences.
Basis Total quality management and Kaizen
Similarities The basic similarities between both given methods are that both
work upon same objective to improve the quality of firm's
product on continuous basis. Here, both approaches believe that
improving the quality of product is not the one time approach,
but it is ongoing method from the management side.
Differences TQM is generally applied upon company culture but Kaizen is
applied on ground floor level. Thus, it can be said that TQM is
more human focused but Kaizen is not (Zu, 2010).
Aston Martin another car manufacture of UK uses six Sigma and lean principles.
Basis Six Sigma and lean principles
Similarities Both the methods make efforts in reducing number of defects
in the product. Thus, it is the major similarity which exists
between the methods.
3
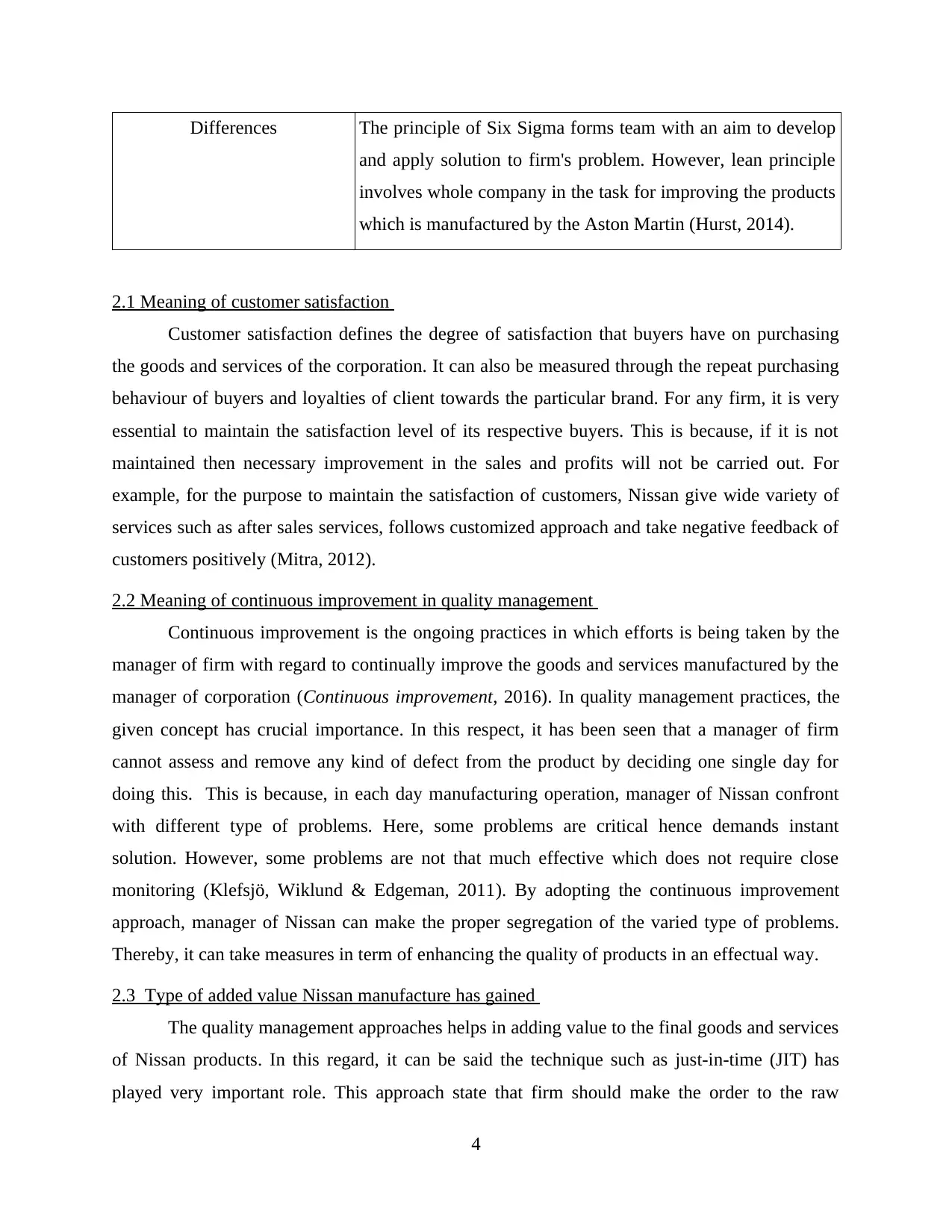
Differences The principle of Six Sigma forms team with an aim to develop
and apply solution to firm's problem. However, lean principle
involves whole company in the task for improving the products
which is manufactured by the Aston Martin (Hurst, 2014).
2.1 Meaning of customer satisfaction
Customer satisfaction defines the degree of satisfaction that buyers have on purchasing
the goods and services of the corporation. It can also be measured through the repeat purchasing
behaviour of buyers and loyalties of client towards the particular brand. For any firm, it is very
essential to maintain the satisfaction level of its respective buyers. This is because, if it is not
maintained then necessary improvement in the sales and profits will not be carried out. For
example, for the purpose to maintain the satisfaction of customers, Nissan give wide variety of
services such as after sales services, follows customized approach and take negative feedback of
customers positively (Mitra, 2012).
2.2 Meaning of continuous improvement in quality management
Continuous improvement is the ongoing practices in which efforts is being taken by the
manager of firm with regard to continually improve the goods and services manufactured by the
manager of corporation (Continuous improvement, 2016). In quality management practices, the
given concept has crucial importance. In this respect, it has been seen that a manager of firm
cannot assess and remove any kind of defect from the product by deciding one single day for
doing this. This is because, in each day manufacturing operation, manager of Nissan confront
with different type of problems. Here, some problems are critical hence demands instant
solution. However, some problems are not that much effective which does not require close
monitoring (Klefsjö, Wiklund & Edgeman, 2011). By adopting the continuous improvement
approach, manager of Nissan can make the proper segregation of the varied type of problems.
Thereby, it can take measures in term of enhancing the quality of products in an effectual way.
2.3 Type of added value Nissan manufacture has gained
The quality management approaches helps in adding value to the final goods and services
of Nissan products. In this regard, it can be said the technique such as just-in-time (JIT) has
played very important role. This approach state that firm should make the order to the raw
4
and apply solution to firm's problem. However, lean principle
involves whole company in the task for improving the products
which is manufactured by the Aston Martin (Hurst, 2014).
2.1 Meaning of customer satisfaction
Customer satisfaction defines the degree of satisfaction that buyers have on purchasing
the goods and services of the corporation. It can also be measured through the repeat purchasing
behaviour of buyers and loyalties of client towards the particular brand. For any firm, it is very
essential to maintain the satisfaction level of its respective buyers. This is because, if it is not
maintained then necessary improvement in the sales and profits will not be carried out. For
example, for the purpose to maintain the satisfaction of customers, Nissan give wide variety of
services such as after sales services, follows customized approach and take negative feedback of
customers positively (Mitra, 2012).
2.2 Meaning of continuous improvement in quality management
Continuous improvement is the ongoing practices in which efforts is being taken by the
manager of firm with regard to continually improve the goods and services manufactured by the
manager of corporation (Continuous improvement, 2016). In quality management practices, the
given concept has crucial importance. In this respect, it has been seen that a manager of firm
cannot assess and remove any kind of defect from the product by deciding one single day for
doing this. This is because, in each day manufacturing operation, manager of Nissan confront
with different type of problems. Here, some problems are critical hence demands instant
solution. However, some problems are not that much effective which does not require close
monitoring (Klefsjö, Wiklund & Edgeman, 2011). By adopting the continuous improvement
approach, manager of Nissan can make the proper segregation of the varied type of problems.
Thereby, it can take measures in term of enhancing the quality of products in an effectual way.
2.3 Type of added value Nissan manufacture has gained
The quality management approaches helps in adding value to the final goods and services
of Nissan products. In this regard, it can be said the technique such as just-in-time (JIT) has
played very important role. This approach state that firm should make the order to the raw
4
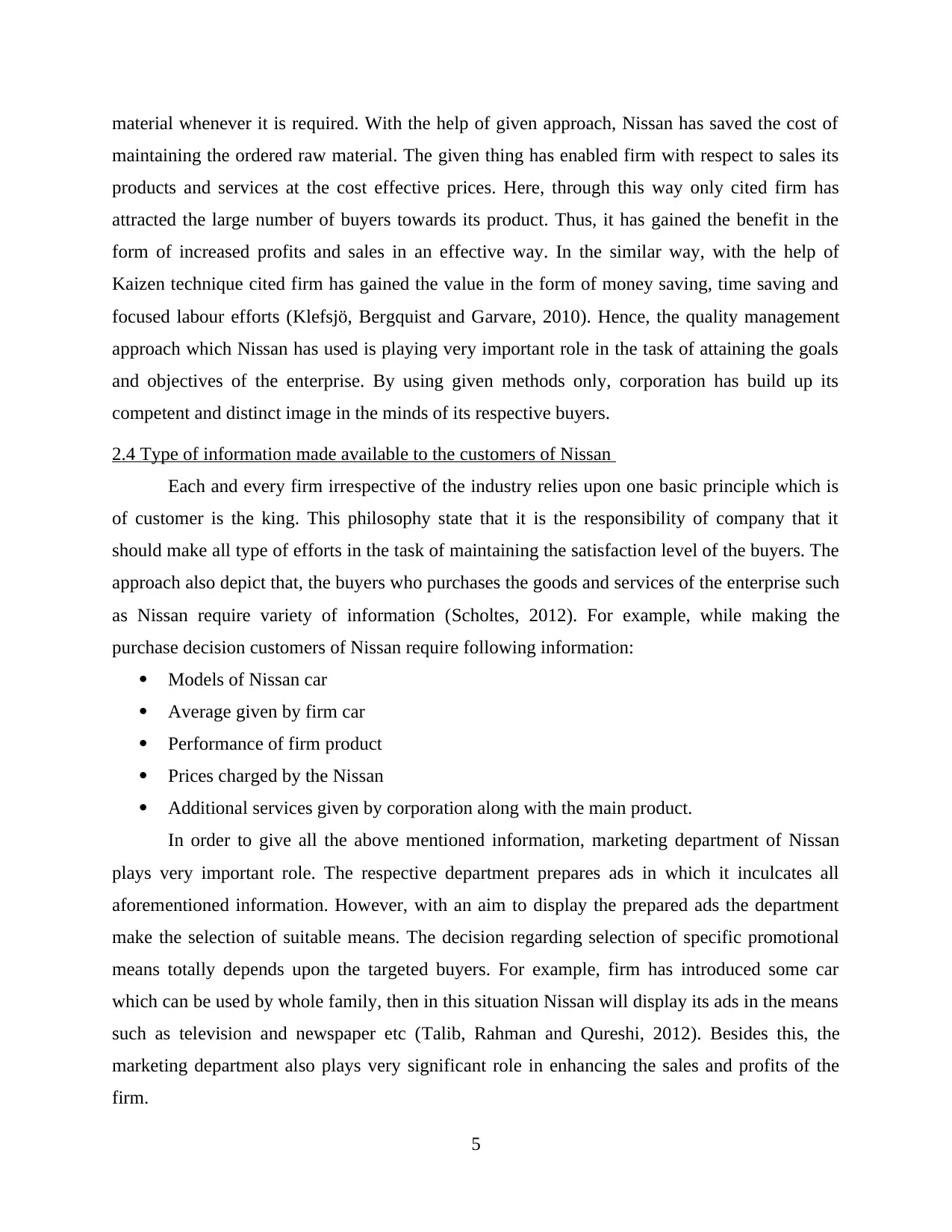
material whenever it is required. With the help of given approach, Nissan has saved the cost of
maintaining the ordered raw material. The given thing has enabled firm with respect to sales its
products and services at the cost effective prices. Here, through this way only cited firm has
attracted the large number of buyers towards its product. Thus, it has gained the benefit in the
form of increased profits and sales in an effective way. In the similar way, with the help of
Kaizen technique cited firm has gained the value in the form of money saving, time saving and
focused labour efforts (Klefsjö, Bergquist and Garvare, 2010). Hence, the quality management
approach which Nissan has used is playing very important role in the task of attaining the goals
and objectives of the enterprise. By using given methods only, corporation has build up its
competent and distinct image in the minds of its respective buyers.
2.4 Type of information made available to the customers of Nissan
Each and every firm irrespective of the industry relies upon one basic principle which is
of customer is the king. This philosophy state that it is the responsibility of company that it
should make all type of efforts in the task of maintaining the satisfaction level of the buyers. The
approach also depict that, the buyers who purchases the goods and services of the enterprise such
as Nissan require variety of information (Scholtes, 2012). For example, while making the
purchase decision customers of Nissan require following information:
Models of Nissan car
Average given by firm car
Performance of firm product
Prices charged by the Nissan
Additional services given by corporation along with the main product.
In order to give all the above mentioned information, marketing department of Nissan
plays very important role. The respective department prepares ads in which it inculcates all
aforementioned information. However, with an aim to display the prepared ads the department
make the selection of suitable means. The decision regarding selection of specific promotional
means totally depends upon the targeted buyers. For example, firm has introduced some car
which can be used by whole family, then in this situation Nissan will display its ads in the means
such as television and newspaper etc (Talib, Rahman and Qureshi, 2012). Besides this, the
marketing department also plays very significant role in enhancing the sales and profits of the
firm.
5
maintaining the ordered raw material. The given thing has enabled firm with respect to sales its
products and services at the cost effective prices. Here, through this way only cited firm has
attracted the large number of buyers towards its product. Thus, it has gained the benefit in the
form of increased profits and sales in an effective way. In the similar way, with the help of
Kaizen technique cited firm has gained the value in the form of money saving, time saving and
focused labour efforts (Klefsjö, Bergquist and Garvare, 2010). Hence, the quality management
approach which Nissan has used is playing very important role in the task of attaining the goals
and objectives of the enterprise. By using given methods only, corporation has build up its
competent and distinct image in the minds of its respective buyers.
2.4 Type of information made available to the customers of Nissan
Each and every firm irrespective of the industry relies upon one basic principle which is
of customer is the king. This philosophy state that it is the responsibility of company that it
should make all type of efforts in the task of maintaining the satisfaction level of the buyers. The
approach also depict that, the buyers who purchases the goods and services of the enterprise such
as Nissan require variety of information (Scholtes, 2012). For example, while making the
purchase decision customers of Nissan require following information:
Models of Nissan car
Average given by firm car
Performance of firm product
Prices charged by the Nissan
Additional services given by corporation along with the main product.
In order to give all the above mentioned information, marketing department of Nissan
plays very important role. The respective department prepares ads in which it inculcates all
aforementioned information. However, with an aim to display the prepared ads the department
make the selection of suitable means. The decision regarding selection of specific promotional
means totally depends upon the targeted buyers. For example, firm has introduced some car
which can be used by whole family, then in this situation Nissan will display its ads in the means
such as television and newspaper etc (Talib, Rahman and Qureshi, 2012). Besides this, the
marketing department also plays very significant role in enhancing the sales and profits of the
firm.
5
Paraphrase This Document
Need a fresh take? Get an instant paraphrase of this document with our AI Paraphraser
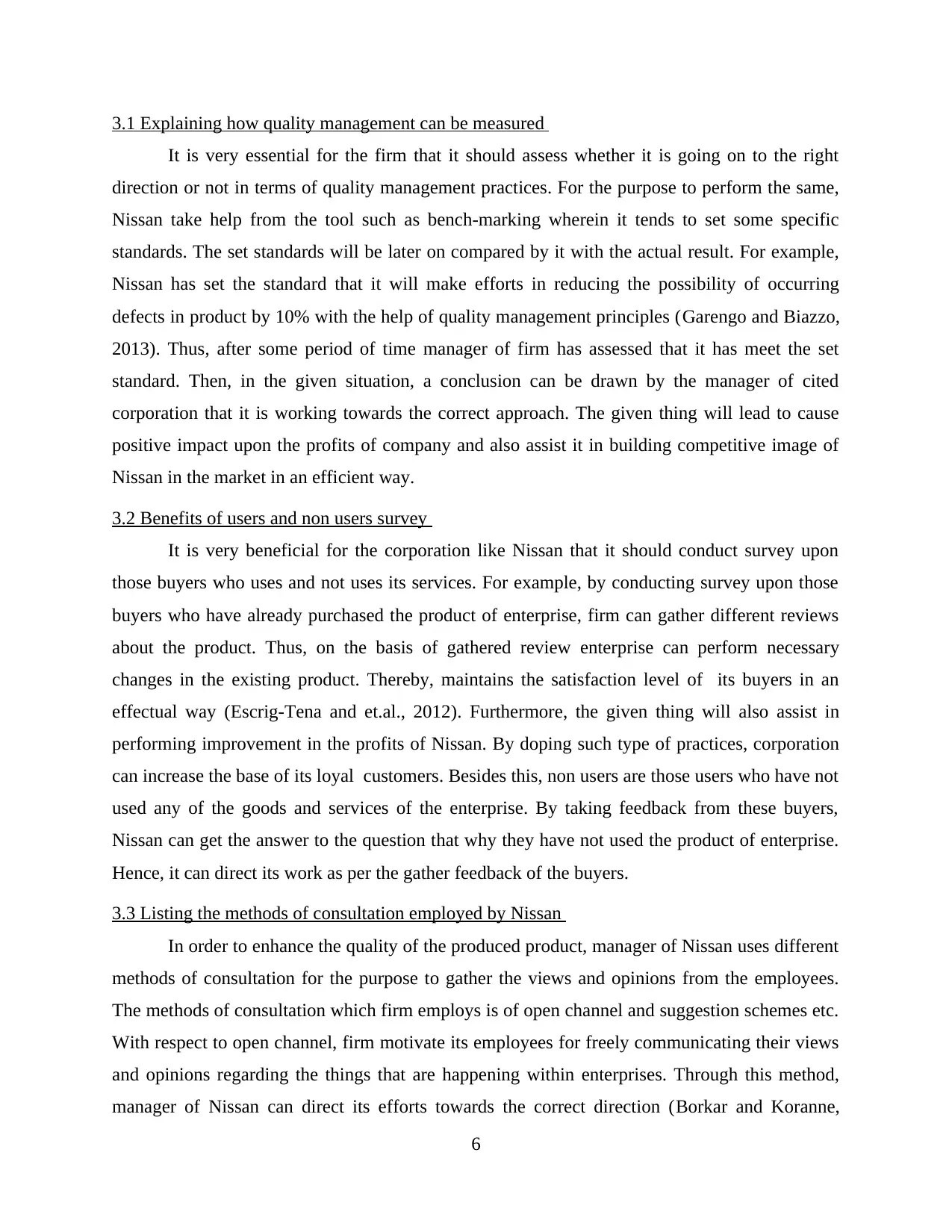
3.1 Explaining how quality management can be measured
It is very essential for the firm that it should assess whether it is going on to the right
direction or not in terms of quality management practices. For the purpose to perform the same,
Nissan take help from the tool such as bench-marking wherein it tends to set some specific
standards. The set standards will be later on compared by it with the actual result. For example,
Nissan has set the standard that it will make efforts in reducing the possibility of occurring
defects in product by 10% with the help of quality management principles (Garengo and Biazzo,
2013). Thus, after some period of time manager of firm has assessed that it has meet the set
standard. Then, in the given situation, a conclusion can be drawn by the manager of cited
corporation that it is working towards the correct approach. The given thing will lead to cause
positive impact upon the profits of company and also assist it in building competitive image of
Nissan in the market in an efficient way.
3.2 Benefits of users and non users survey
It is very beneficial for the corporation like Nissan that it should conduct survey upon
those buyers who uses and not uses its services. For example, by conducting survey upon those
buyers who have already purchased the product of enterprise, firm can gather different reviews
about the product. Thus, on the basis of gathered review enterprise can perform necessary
changes in the existing product. Thereby, maintains the satisfaction level of its buyers in an
effectual way (Escrig-Tena and et.al., 2012). Furthermore, the given thing will also assist in
performing improvement in the profits of Nissan. By doping such type of practices, corporation
can increase the base of its loyal customers. Besides this, non users are those users who have not
used any of the goods and services of the enterprise. By taking feedback from these buyers,
Nissan can get the answer to the question that why they have not used the product of enterprise.
Hence, it can direct its work as per the gather feedback of the buyers.
3.3 Listing the methods of consultation employed by Nissan
In order to enhance the quality of the produced product, manager of Nissan uses different
methods of consultation for the purpose to gather the views and opinions from the employees.
The methods of consultation which firm employs is of open channel and suggestion schemes etc.
With respect to open channel, firm motivate its employees for freely communicating their views
and opinions regarding the things that are happening within enterprises. Through this method,
manager of Nissan can direct its efforts towards the correct direction (Borkar and Koranne,
6
It is very essential for the firm that it should assess whether it is going on to the right
direction or not in terms of quality management practices. For the purpose to perform the same,
Nissan take help from the tool such as bench-marking wherein it tends to set some specific
standards. The set standards will be later on compared by it with the actual result. For example,
Nissan has set the standard that it will make efforts in reducing the possibility of occurring
defects in product by 10% with the help of quality management principles (Garengo and Biazzo,
2013). Thus, after some period of time manager of firm has assessed that it has meet the set
standard. Then, in the given situation, a conclusion can be drawn by the manager of cited
corporation that it is working towards the correct approach. The given thing will lead to cause
positive impact upon the profits of company and also assist it in building competitive image of
Nissan in the market in an efficient way.
3.2 Benefits of users and non users survey
It is very beneficial for the corporation like Nissan that it should conduct survey upon
those buyers who uses and not uses its services. For example, by conducting survey upon those
buyers who have already purchased the product of enterprise, firm can gather different reviews
about the product. Thus, on the basis of gathered review enterprise can perform necessary
changes in the existing product. Thereby, maintains the satisfaction level of its buyers in an
effectual way (Escrig-Tena and et.al., 2012). Furthermore, the given thing will also assist in
performing improvement in the profits of Nissan. By doping such type of practices, corporation
can increase the base of its loyal customers. Besides this, non users are those users who have not
used any of the goods and services of the enterprise. By taking feedback from these buyers,
Nissan can get the answer to the question that why they have not used the product of enterprise.
Hence, it can direct its work as per the gather feedback of the buyers.
3.3 Listing the methods of consultation employed by Nissan
In order to enhance the quality of the produced product, manager of Nissan uses different
methods of consultation for the purpose to gather the views and opinions from the employees.
The methods of consultation which firm employs is of open channel and suggestion schemes etc.
With respect to open channel, firm motivate its employees for freely communicating their views
and opinions regarding the things that are happening within enterprises. Through this method,
manager of Nissan can direct its efforts towards the correct direction (Borkar and Koranne,
6
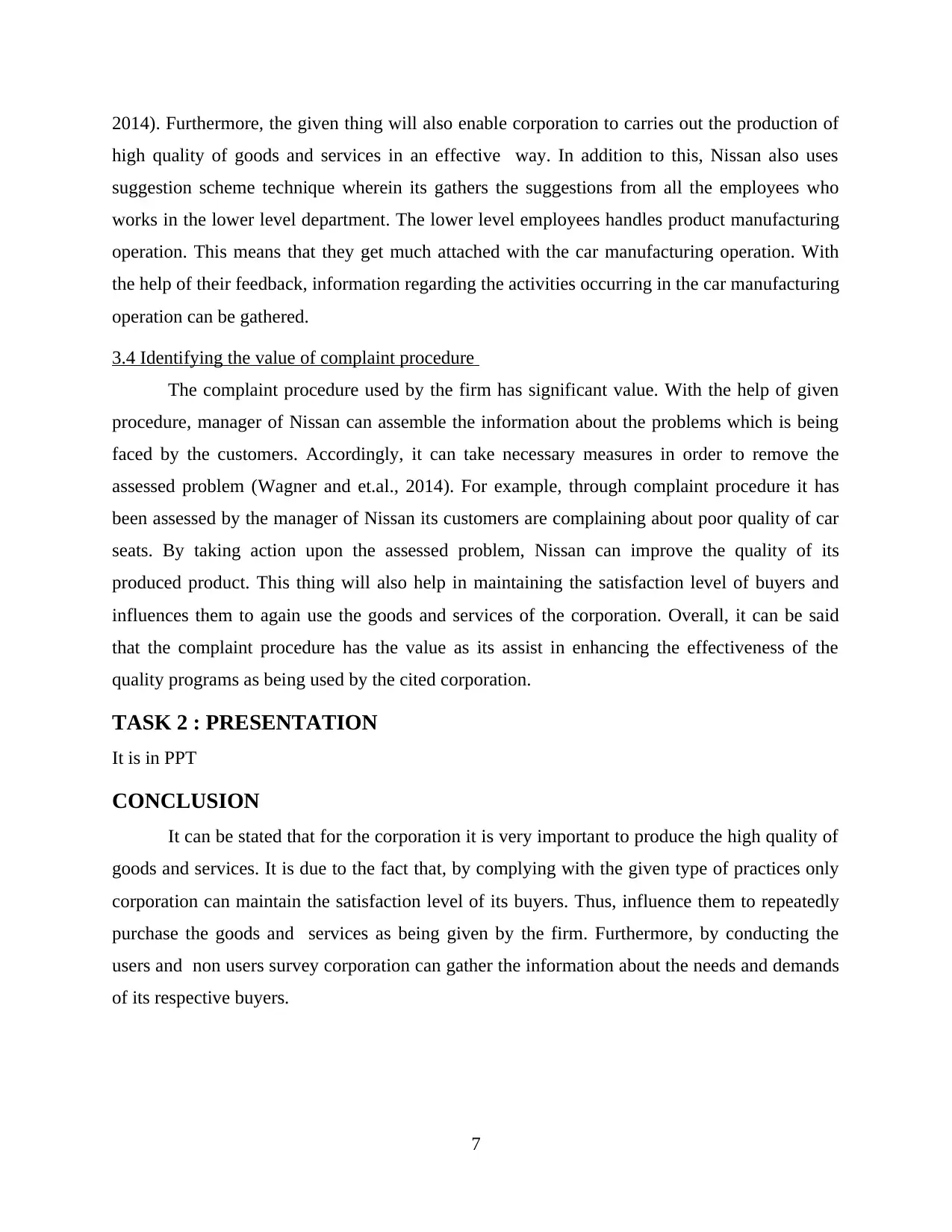
2014). Furthermore, the given thing will also enable corporation to carries out the production of
high quality of goods and services in an effective way. In addition to this, Nissan also uses
suggestion scheme technique wherein its gathers the suggestions from all the employees who
works in the lower level department. The lower level employees handles product manufacturing
operation. This means that they get much attached with the car manufacturing operation. With
the help of their feedback, information regarding the activities occurring in the car manufacturing
operation can be gathered.
3.4 Identifying the value of complaint procedure
The complaint procedure used by the firm has significant value. With the help of given
procedure, manager of Nissan can assemble the information about the problems which is being
faced by the customers. Accordingly, it can take necessary measures in order to remove the
assessed problem (Wagner and et.al., 2014). For example, through complaint procedure it has
been assessed by the manager of Nissan its customers are complaining about poor quality of car
seats. By taking action upon the assessed problem, Nissan can improve the quality of its
produced product. This thing will also help in maintaining the satisfaction level of buyers and
influences them to again use the goods and services of the corporation. Overall, it can be said
that the complaint procedure has the value as its assist in enhancing the effectiveness of the
quality programs as being used by the cited corporation.
TASK 2 : PRESENTATION
It is in PPT
CONCLUSION
It can be stated that for the corporation it is very important to produce the high quality of
goods and services. It is due to the fact that, by complying with the given type of practices only
corporation can maintain the satisfaction level of its buyers. Thus, influence them to repeatedly
purchase the goods and services as being given by the firm. Furthermore, by conducting the
users and non users survey corporation can gather the information about the needs and demands
of its respective buyers.
7
high quality of goods and services in an effective way. In addition to this, Nissan also uses
suggestion scheme technique wherein its gathers the suggestions from all the employees who
works in the lower level department. The lower level employees handles product manufacturing
operation. This means that they get much attached with the car manufacturing operation. With
the help of their feedback, information regarding the activities occurring in the car manufacturing
operation can be gathered.
3.4 Identifying the value of complaint procedure
The complaint procedure used by the firm has significant value. With the help of given
procedure, manager of Nissan can assemble the information about the problems which is being
faced by the customers. Accordingly, it can take necessary measures in order to remove the
assessed problem (Wagner and et.al., 2014). For example, through complaint procedure it has
been assessed by the manager of Nissan its customers are complaining about poor quality of car
seats. By taking action upon the assessed problem, Nissan can improve the quality of its
produced product. This thing will also help in maintaining the satisfaction level of buyers and
influences them to again use the goods and services of the corporation. Overall, it can be said
that the complaint procedure has the value as its assist in enhancing the effectiveness of the
quality programs as being used by the cited corporation.
TASK 2 : PRESENTATION
It is in PPT
CONCLUSION
It can be stated that for the corporation it is very important to produce the high quality of
goods and services. It is due to the fact that, by complying with the given type of practices only
corporation can maintain the satisfaction level of its buyers. Thus, influence them to repeatedly
purchase the goods and services as being given by the firm. Furthermore, by conducting the
users and non users survey corporation can gather the information about the needs and demands
of its respective buyers.
7
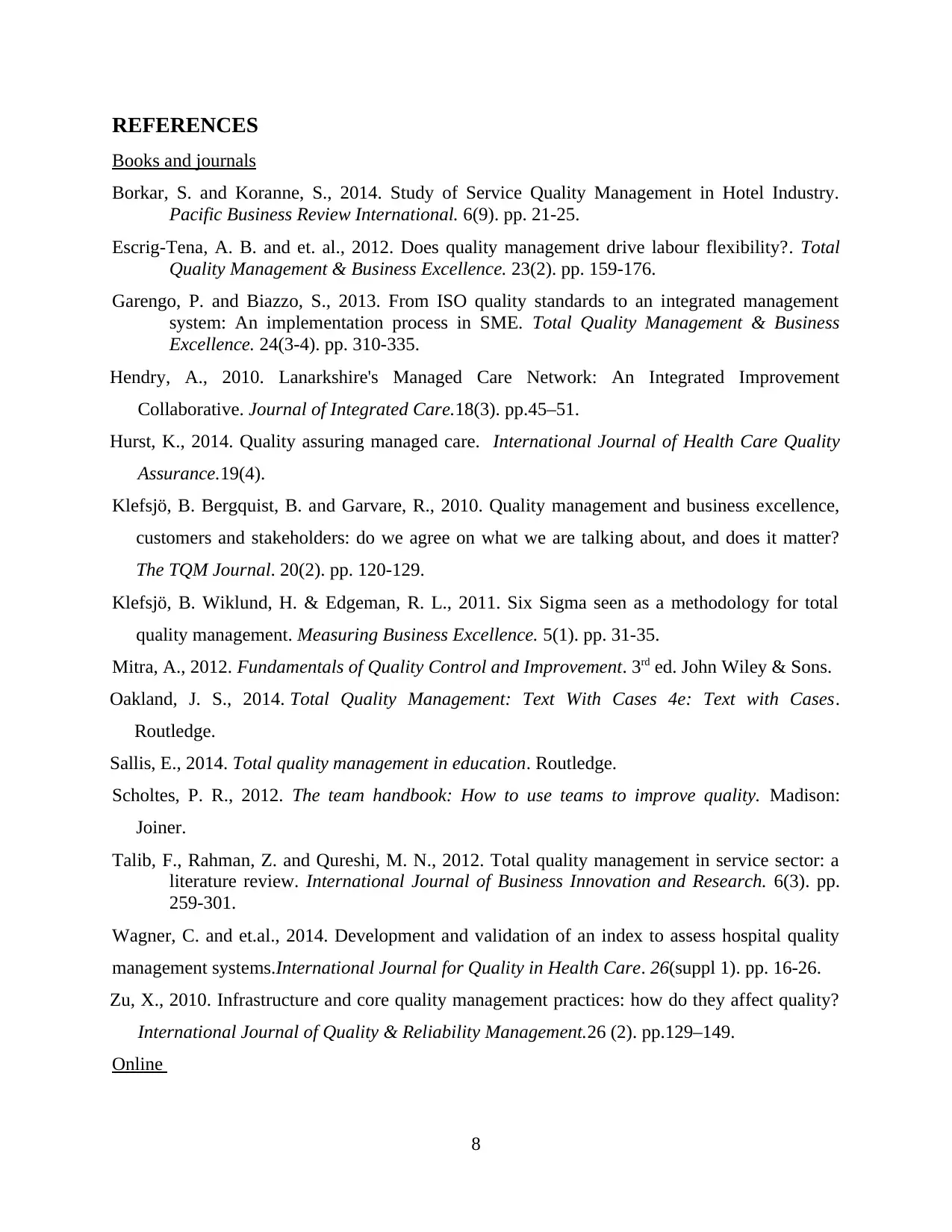
REFERENCES
Books and journals
Borkar, S. and Koranne, S., 2014. Study of Service Quality Management in Hotel Industry.
Pacific Business Review International. 6(9). pp. 21-25.
Escrig-Tena, A. B. and et. al., 2012. Does quality management drive labour flexibility?. Total
Quality Management & Business Excellence. 23(2). pp. 159-176.
Garengo, P. and Biazzo, S., 2013. From ISO quality standards to an integrated management
system: An implementation process in SME. Total Quality Management & Business
Excellence. 24(3-4). pp. 310-335.
Hendry, A., 2010. Lanarkshire's Managed Care Network: An Integrated Improvement
Collaborative. Journal of Integrated Care.18(3). pp.45–51.
Hurst, K., 2014. Quality assuring managed care. International Journal of Health Care Quality
Assurance.19(4).
Klefsjö, B. Bergquist, B. and Garvare, R., 2010. Quality management and business excellence,
customers and stakeholders: do we agree on what we are talking about, and does it matter?
The TQM Journal. 20(2). pp. 120-129.
Klefsjö, B. Wiklund, H. & Edgeman, R. L., 2011. Six Sigma seen as a methodology for total
quality management. Measuring Business Excellence. 5(1). pp. 31-35.
Mitra, A., 2012. Fundamentals of Quality Control and Improvement. 3rd ed. John Wiley & Sons.
Oakland, J. S., 2014. Total Quality Management: Text With Cases 4e: Text with Cases.
Routledge.
Sallis, E., 2014. Total quality management in education. Routledge.
Scholtes, P. R., 2012. The team handbook: How to use teams to improve quality. Madison:
Joiner.
Talib, F., Rahman, Z. and Qureshi, M. N., 2012. Total quality management in service sector: a
literature review. International Journal of Business Innovation and Research. 6(3). pp.
259-301.
Wagner, C. and et.al., 2014. Development and validation of an index to assess hospital quality
management systems.International Journal for Quality in Health Care. 26(suppl 1). pp. 16-26.
Zu, X., 2010. Infrastructure and core quality management practices: how do they affect quality?
International Journal of Quality & Reliability Management.26 (2). pp.129–149.
Online
8
Books and journals
Borkar, S. and Koranne, S., 2014. Study of Service Quality Management in Hotel Industry.
Pacific Business Review International. 6(9). pp. 21-25.
Escrig-Tena, A. B. and et. al., 2012. Does quality management drive labour flexibility?. Total
Quality Management & Business Excellence. 23(2). pp. 159-176.
Garengo, P. and Biazzo, S., 2013. From ISO quality standards to an integrated management
system: An implementation process in SME. Total Quality Management & Business
Excellence. 24(3-4). pp. 310-335.
Hendry, A., 2010. Lanarkshire's Managed Care Network: An Integrated Improvement
Collaborative. Journal of Integrated Care.18(3). pp.45–51.
Hurst, K., 2014. Quality assuring managed care. International Journal of Health Care Quality
Assurance.19(4).
Klefsjö, B. Bergquist, B. and Garvare, R., 2010. Quality management and business excellence,
customers and stakeholders: do we agree on what we are talking about, and does it matter?
The TQM Journal. 20(2). pp. 120-129.
Klefsjö, B. Wiklund, H. & Edgeman, R. L., 2011. Six Sigma seen as a methodology for total
quality management. Measuring Business Excellence. 5(1). pp. 31-35.
Mitra, A., 2012. Fundamentals of Quality Control and Improvement. 3rd ed. John Wiley & Sons.
Oakland, J. S., 2014. Total Quality Management: Text With Cases 4e: Text with Cases.
Routledge.
Sallis, E., 2014. Total quality management in education. Routledge.
Scholtes, P. R., 2012. The team handbook: How to use teams to improve quality. Madison:
Joiner.
Talib, F., Rahman, Z. and Qureshi, M. N., 2012. Total quality management in service sector: a
literature review. International Journal of Business Innovation and Research. 6(3). pp.
259-301.
Wagner, C. and et.al., 2014. Development and validation of an index to assess hospital quality
management systems.International Journal for Quality in Health Care. 26(suppl 1). pp. 16-26.
Zu, X., 2010. Infrastructure and core quality management practices: how do they affect quality?
International Journal of Quality & Reliability Management.26 (2). pp.129–149.
Online
8
Secure Best Marks with AI Grader
Need help grading? Try our AI Grader for instant feedback on your assignments.
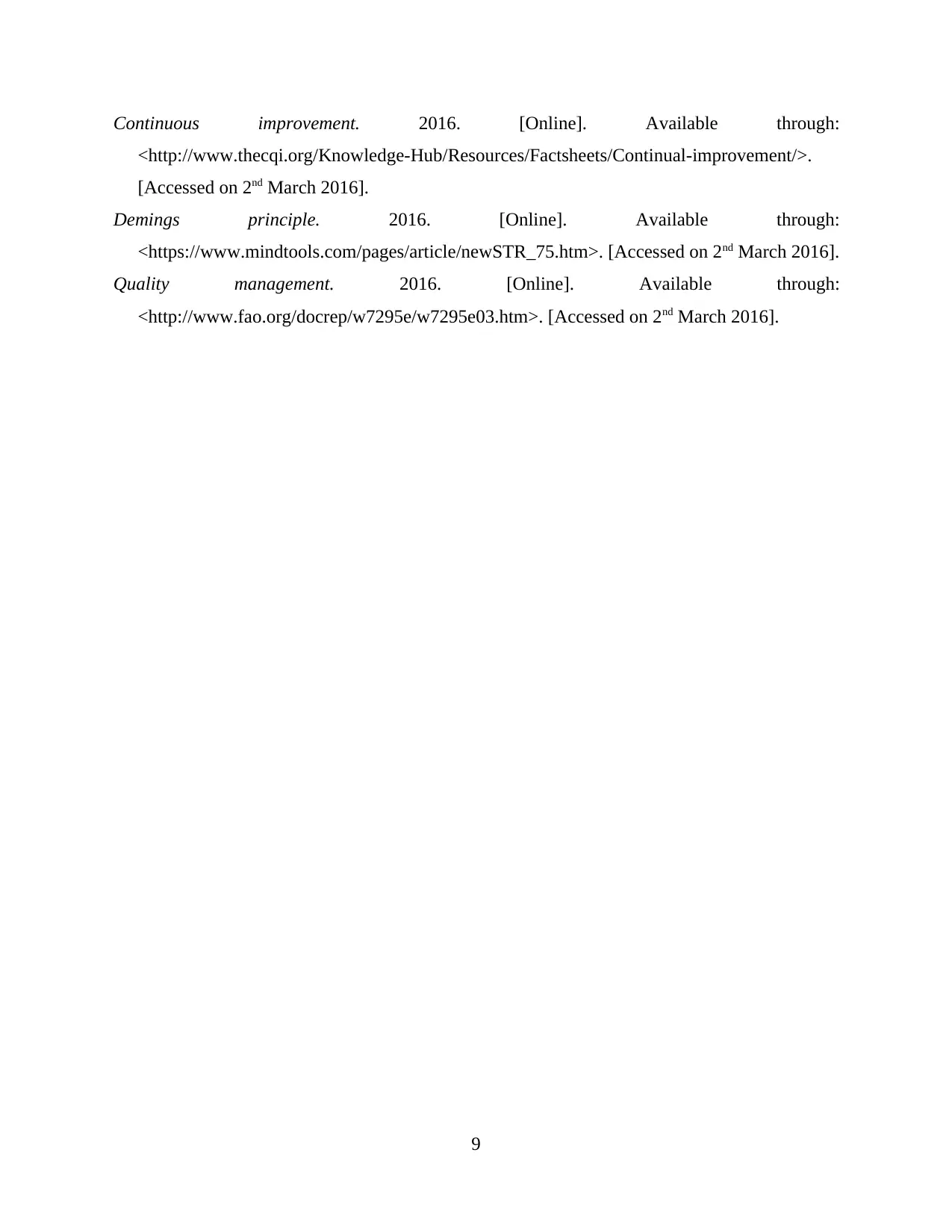
Continuous improvement. 2016. [Online]. Available through:
<http://www.thecqi.org/Knowledge-Hub/Resources/Factsheets/Continual-improvement/>.
[Accessed on 2nd March 2016].
Demings principle. 2016. [Online]. Available through:
<https://www.mindtools.com/pages/article/newSTR_75.htm>. [Accessed on 2nd March 2016].
Quality management. 2016. [Online]. Available through:
<http://www.fao.org/docrep/w7295e/w7295e03.htm>. [Accessed on 2nd March 2016].
9
<http://www.thecqi.org/Knowledge-Hub/Resources/Factsheets/Continual-improvement/>.
[Accessed on 2nd March 2016].
Demings principle. 2016. [Online]. Available through:
<https://www.mindtools.com/pages/article/newSTR_75.htm>. [Accessed on 2nd March 2016].
Quality management. 2016. [Online]. Available through:
<http://www.fao.org/docrep/w7295e/w7295e03.htm>. [Accessed on 2nd March 2016].
9
1 out of 11
Related Documents
![[object Object]](/_next/image/?url=%2F_next%2Fstatic%2Fmedia%2Flogo.6d15ce61.png&w=640&q=75)
Your All-in-One AI-Powered Toolkit for Academic Success.
+13062052269
info@desklib.com
Available 24*7 on WhatsApp / Email
Unlock your academic potential
© 2024 | Zucol Services PVT LTD | All rights reserved.