Total Quality Management Report
VerifiedAdded on 2020/12/29
|13
|3932
|189
Report
AI Summary
This report examines the concept of Total Quality Management (TQM) and its application in enhancing firm effectiveness. It explores the principles of TQM, its benefits in terms of cost savings, customer satisfaction, organizational development, and competitive advantage, and provides a comprehensive overview of TQM implementation and its impact on business success.
Contribute Materials
Your contribution can guide someone’s learning journey. Share your
documents today.
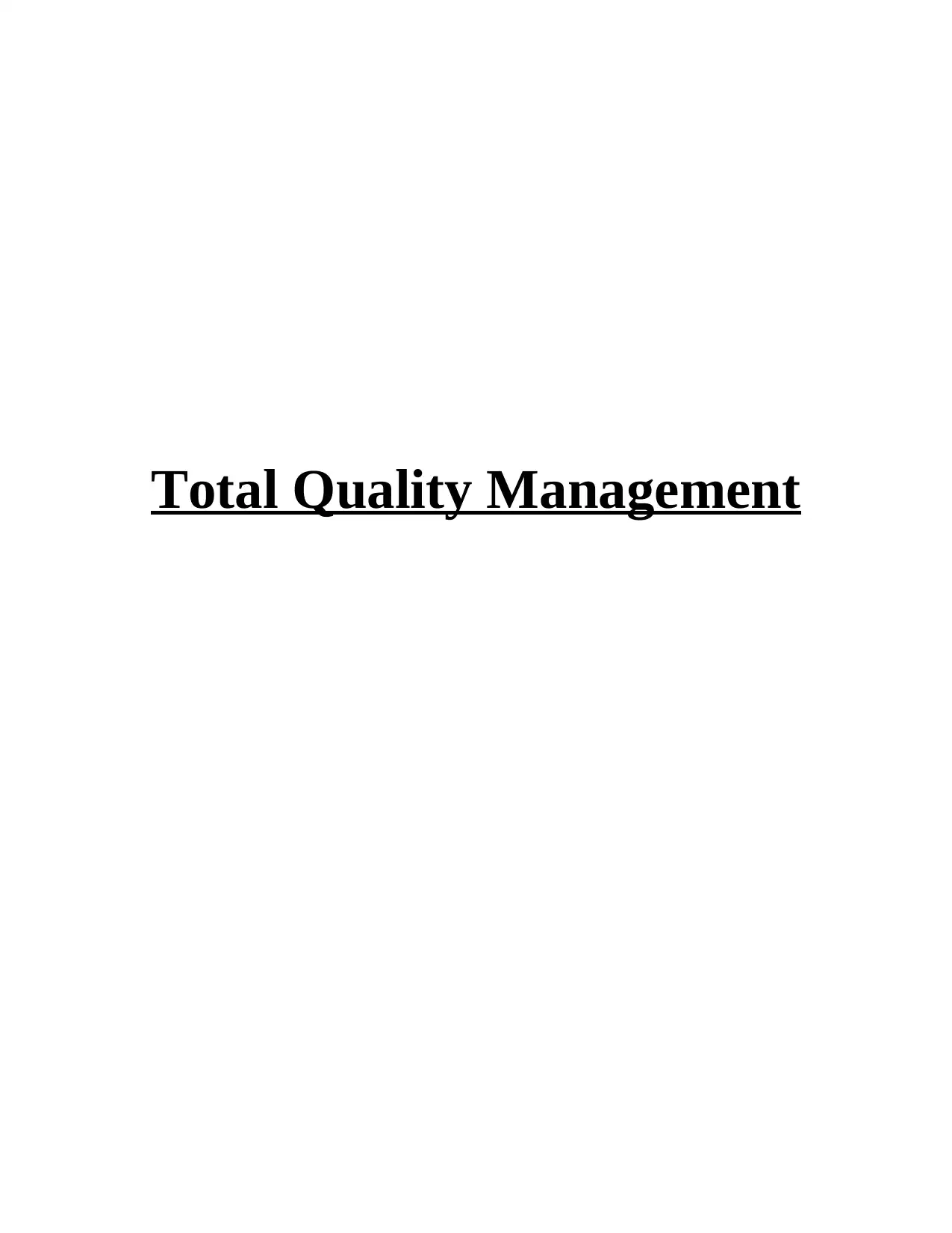
Total Quality Management
Secure Best Marks with AI Grader
Need help grading? Try our AI Grader for instant feedback on your assignments.
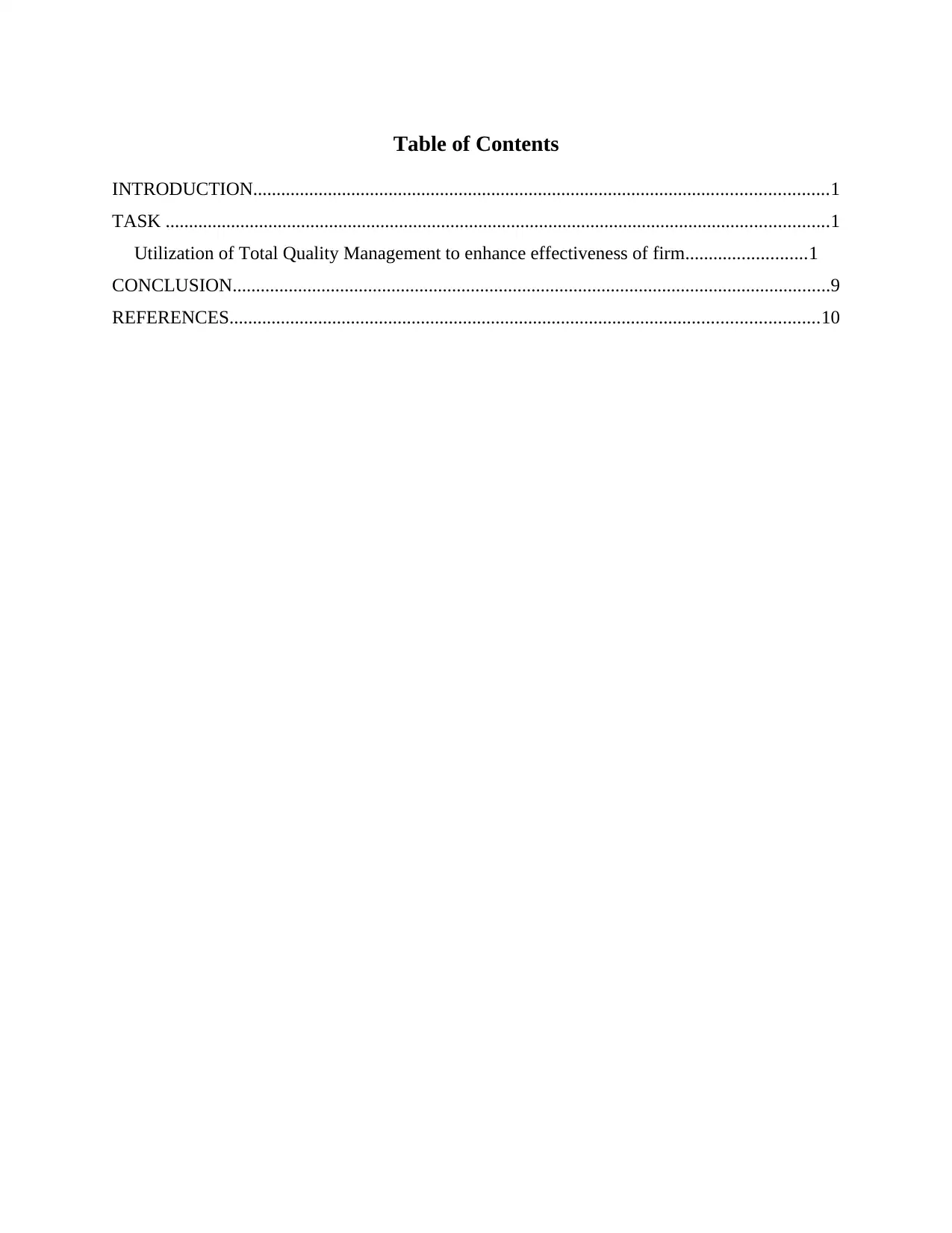
Table of Contents
INTRODUCTION...........................................................................................................................1
TASK ..............................................................................................................................................1
Utilization of Total Quality Management to enhance effectiveness of firm..........................1
CONCLUSION................................................................................................................................9
REFERENCES..............................................................................................................................10
INTRODUCTION...........................................................................................................................1
TASK ..............................................................................................................................................1
Utilization of Total Quality Management to enhance effectiveness of firm..........................1
CONCLUSION................................................................................................................................9
REFERENCES..............................................................................................................................10
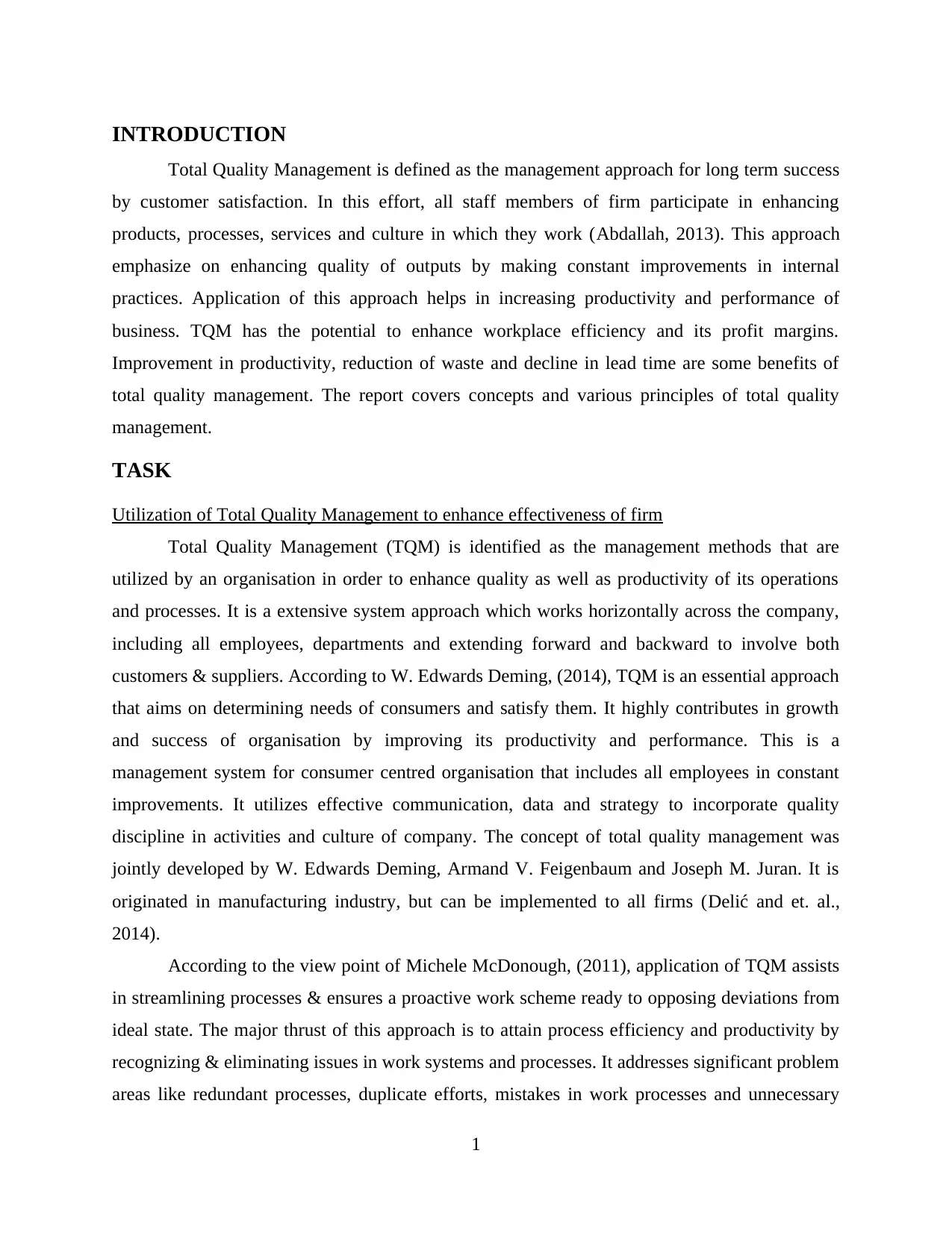
INTRODUCTION
Total Quality Management is defined as the management approach for long term success
by customer satisfaction. In this effort, all staff members of firm participate in enhancing
products, processes, services and culture in which they work (Abdallah, 2013). This approach
emphasize on enhancing quality of outputs by making constant improvements in internal
practices. Application of this approach helps in increasing productivity and performance of
business. TQM has the potential to enhance workplace efficiency and its profit margins.
Improvement in productivity, reduction of waste and decline in lead time are some benefits of
total quality management. The report covers concepts and various principles of total quality
management.
TASK
Utilization of Total Quality Management to enhance effectiveness of firm
Total Quality Management (TQM) is identified as the management methods that are
utilized by an organisation in order to enhance quality as well as productivity of its operations
and processes. It is a extensive system approach which works horizontally across the company,
including all employees, departments and extending forward and backward to involve both
customers & suppliers. According to W. Edwards Deming, (2014), TQM is an essential approach
that aims on determining needs of consumers and satisfy them. It highly contributes in growth
and success of organisation by improving its productivity and performance. This is a
management system for consumer centred organisation that includes all employees in constant
improvements. It utilizes effective communication, data and strategy to incorporate quality
discipline in activities and culture of company. The concept of total quality management was
jointly developed by W. Edwards Deming, Armand V. Feigenbaum and Joseph M. Juran. It is
originated in manufacturing industry, but can be implemented to all firms (Delić and et. al.,
2014).
According to the view point of Michele McDonough, (2011), application of TQM assists
in streamlining processes & ensures a proactive work scheme ready to opposing deviations from
ideal state. The major thrust of this approach is to attain process efficiency and productivity by
recognizing & eliminating issues in work systems and processes. It addresses significant problem
areas like redundant processes, duplicate efforts, mistakes in work processes and unnecessary
1
Total Quality Management is defined as the management approach for long term success
by customer satisfaction. In this effort, all staff members of firm participate in enhancing
products, processes, services and culture in which they work (Abdallah, 2013). This approach
emphasize on enhancing quality of outputs by making constant improvements in internal
practices. Application of this approach helps in increasing productivity and performance of
business. TQM has the potential to enhance workplace efficiency and its profit margins.
Improvement in productivity, reduction of waste and decline in lead time are some benefits of
total quality management. The report covers concepts and various principles of total quality
management.
TASK
Utilization of Total Quality Management to enhance effectiveness of firm
Total Quality Management (TQM) is identified as the management methods that are
utilized by an organisation in order to enhance quality as well as productivity of its operations
and processes. It is a extensive system approach which works horizontally across the company,
including all employees, departments and extending forward and backward to involve both
customers & suppliers. According to W. Edwards Deming, (2014), TQM is an essential approach
that aims on determining needs of consumers and satisfy them. It highly contributes in growth
and success of organisation by improving its productivity and performance. This is a
management system for consumer centred organisation that includes all employees in constant
improvements. It utilizes effective communication, data and strategy to incorporate quality
discipline in activities and culture of company. The concept of total quality management was
jointly developed by W. Edwards Deming, Armand V. Feigenbaum and Joseph M. Juran. It is
originated in manufacturing industry, but can be implemented to all firms (Delić and et. al.,
2014).
According to the view point of Michele McDonough, (2011), application of TQM assists
in streamlining processes & ensures a proactive work scheme ready to opposing deviations from
ideal state. The major thrust of this approach is to attain process efficiency and productivity by
recognizing & eliminating issues in work systems and processes. It addresses significant problem
areas like redundant processes, duplicate efforts, mistakes in work processes and unnecessary
1
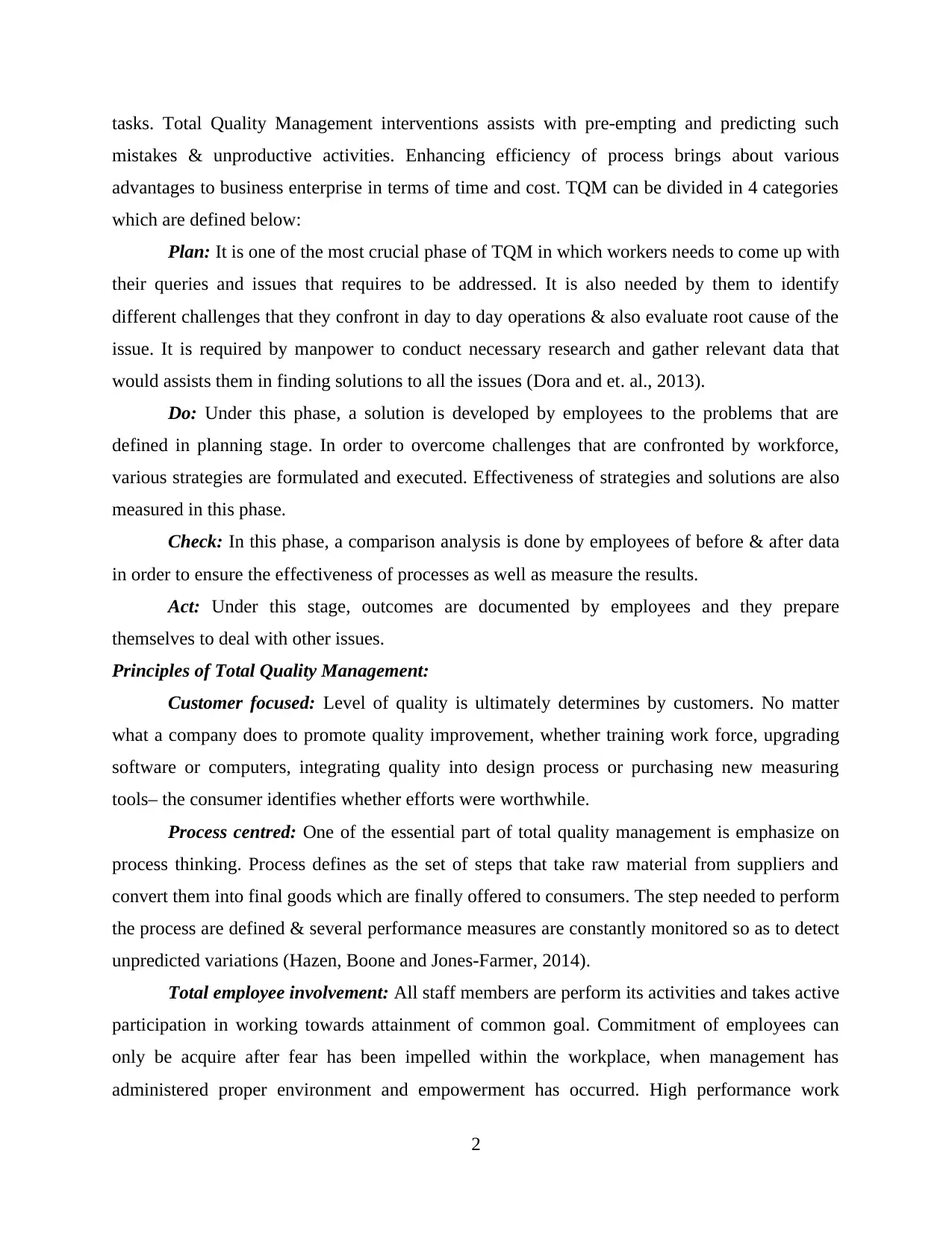
tasks. Total Quality Management interventions assists with pre-empting and predicting such
mistakes & unproductive activities. Enhancing efficiency of process brings about various
advantages to business enterprise in terms of time and cost. TQM can be divided in 4 categories
which are defined below:
Plan: It is one of the most crucial phase of TQM in which workers needs to come up with
their queries and issues that requires to be addressed. It is also needed by them to identify
different challenges that they confront in day to day operations & also evaluate root cause of the
issue. It is required by manpower to conduct necessary research and gather relevant data that
would assists them in finding solutions to all the issues (Dora and et. al., 2013).
Do: Under this phase, a solution is developed by employees to the problems that are
defined in planning stage. In order to overcome challenges that are confronted by workforce,
various strategies are formulated and executed. Effectiveness of strategies and solutions are also
measured in this phase.
Check: In this phase, a comparison analysis is done by employees of before & after data
in order to ensure the effectiveness of processes as well as measure the results.
Act: Under this stage, outcomes are documented by employees and they prepare
themselves to deal with other issues.
Principles of Total Quality Management:
Customer focused: Level of quality is ultimately determines by customers. No matter
what a company does to promote quality improvement, whether training work force, upgrading
software or computers, integrating quality into design process or purchasing new measuring
tools– the consumer identifies whether efforts were worthwhile.
Process centred: One of the essential part of total quality management is emphasize on
process thinking. Process defines as the set of steps that take raw material from suppliers and
convert them into final goods which are finally offered to consumers. The step needed to perform
the process are defined & several performance measures are constantly monitored so as to detect
unpredicted variations (Hazen, Boone and Jones-Farmer, 2014).
Total employee involvement: All staff members are perform its activities and takes active
participation in working towards attainment of common goal. Commitment of employees can
only be acquire after fear has been impelled within the workplace, when management has
administered proper environment and empowerment has occurred. High performance work
2
mistakes & unproductive activities. Enhancing efficiency of process brings about various
advantages to business enterprise in terms of time and cost. TQM can be divided in 4 categories
which are defined below:
Plan: It is one of the most crucial phase of TQM in which workers needs to come up with
their queries and issues that requires to be addressed. It is also needed by them to identify
different challenges that they confront in day to day operations & also evaluate root cause of the
issue. It is required by manpower to conduct necessary research and gather relevant data that
would assists them in finding solutions to all the issues (Dora and et. al., 2013).
Do: Under this phase, a solution is developed by employees to the problems that are
defined in planning stage. In order to overcome challenges that are confronted by workforce,
various strategies are formulated and executed. Effectiveness of strategies and solutions are also
measured in this phase.
Check: In this phase, a comparison analysis is done by employees of before & after data
in order to ensure the effectiveness of processes as well as measure the results.
Act: Under this stage, outcomes are documented by employees and they prepare
themselves to deal with other issues.
Principles of Total Quality Management:
Customer focused: Level of quality is ultimately determines by customers. No matter
what a company does to promote quality improvement, whether training work force, upgrading
software or computers, integrating quality into design process or purchasing new measuring
tools– the consumer identifies whether efforts were worthwhile.
Process centred: One of the essential part of total quality management is emphasize on
process thinking. Process defines as the set of steps that take raw material from suppliers and
convert them into final goods which are finally offered to consumers. The step needed to perform
the process are defined & several performance measures are constantly monitored so as to detect
unpredicted variations (Hazen, Boone and Jones-Farmer, 2014).
Total employee involvement: All staff members are perform its activities and takes active
participation in working towards attainment of common goal. Commitment of employees can
only be acquire after fear has been impelled within the workplace, when management has
administered proper environment and empowerment has occurred. High performance work
2
Secure Best Marks with AI Grader
Need help grading? Try our AI Grader for instant feedback on your assignments.
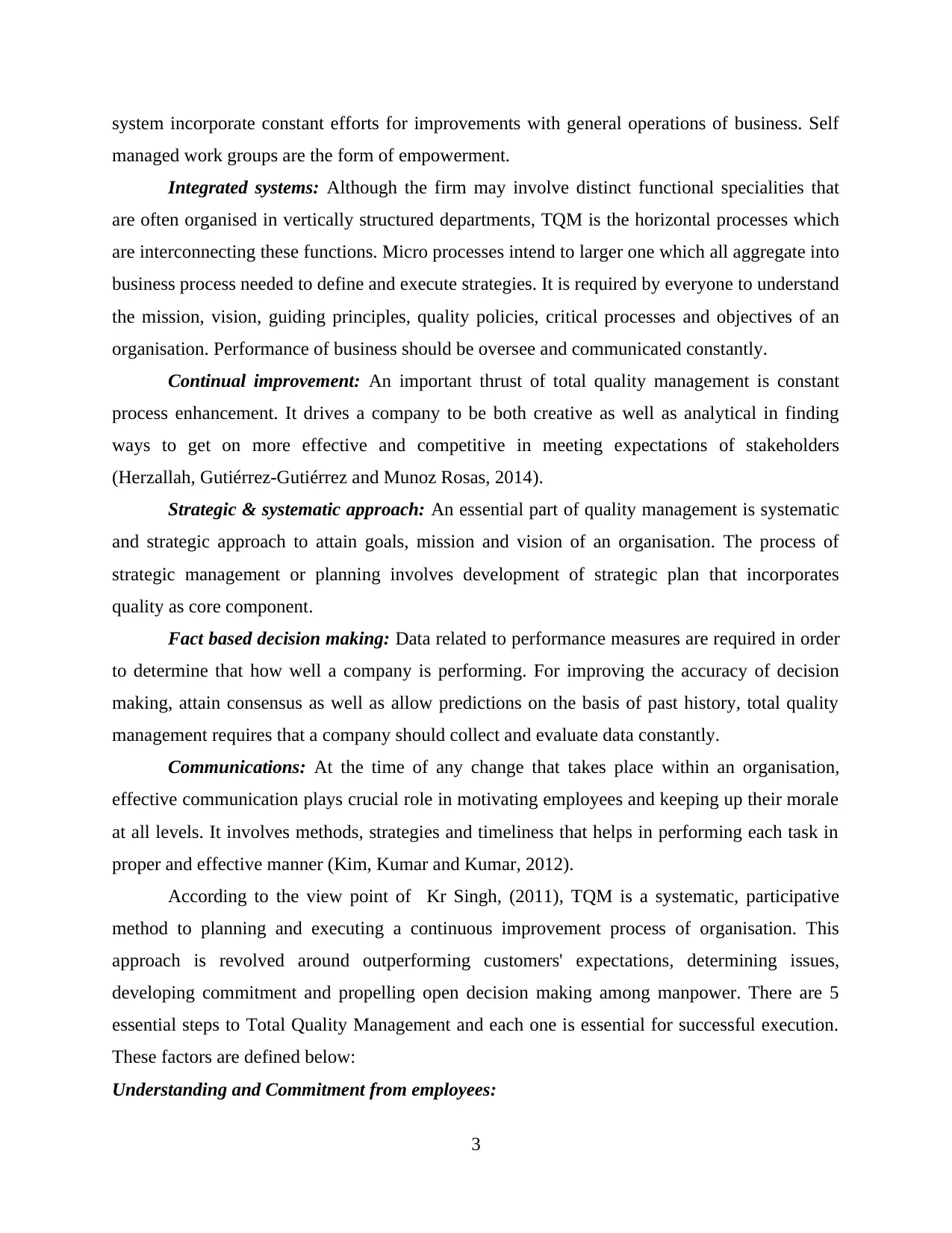
system incorporate constant efforts for improvements with general operations of business. Self
managed work groups are the form of empowerment.
Integrated systems: Although the firm may involve distinct functional specialities that
are often organised in vertically structured departments, TQM is the horizontal processes which
are interconnecting these functions. Micro processes intend to larger one which all aggregate into
business process needed to define and execute strategies. It is required by everyone to understand
the mission, vision, guiding principles, quality policies, critical processes and objectives of an
organisation. Performance of business should be oversee and communicated constantly.
Continual improvement: An important thrust of total quality management is constant
process enhancement. It drives a company to be both creative as well as analytical in finding
ways to get on more effective and competitive in meeting expectations of stakeholders
(Herzallah, Gutiérrez-Gutiérrez and Munoz Rosas, 2014).
Strategic & systematic approach: An essential part of quality management is systematic
and strategic approach to attain goals, mission and vision of an organisation. The process of
strategic management or planning involves development of strategic plan that incorporates
quality as core component.
Fact based decision making: Data related to performance measures are required in order
to determine that how well a company is performing. For improving the accuracy of decision
making, attain consensus as well as allow predictions on the basis of past history, total quality
management requires that a company should collect and evaluate data constantly.
Communications: At the time of any change that takes place within an organisation,
effective communication plays crucial role in motivating employees and keeping up their morale
at all levels. It involves methods, strategies and timeliness that helps in performing each task in
proper and effective manner (Kim, Kumar and Kumar, 2012).
According to the view point of Kr Singh, (2011), TQM is a systematic, participative
method to planning and executing a continuous improvement process of organisation. This
approach is revolved around outperforming customers' expectations, determining issues,
developing commitment and propelling open decision making among manpower. There are 5
essential steps to Total Quality Management and each one is essential for successful execution.
These factors are defined below:
Understanding and Commitment from employees:
3
managed work groups are the form of empowerment.
Integrated systems: Although the firm may involve distinct functional specialities that
are often organised in vertically structured departments, TQM is the horizontal processes which
are interconnecting these functions. Micro processes intend to larger one which all aggregate into
business process needed to define and execute strategies. It is required by everyone to understand
the mission, vision, guiding principles, quality policies, critical processes and objectives of an
organisation. Performance of business should be oversee and communicated constantly.
Continual improvement: An important thrust of total quality management is constant
process enhancement. It drives a company to be both creative as well as analytical in finding
ways to get on more effective and competitive in meeting expectations of stakeholders
(Herzallah, Gutiérrez-Gutiérrez and Munoz Rosas, 2014).
Strategic & systematic approach: An essential part of quality management is systematic
and strategic approach to attain goals, mission and vision of an organisation. The process of
strategic management or planning involves development of strategic plan that incorporates
quality as core component.
Fact based decision making: Data related to performance measures are required in order
to determine that how well a company is performing. For improving the accuracy of decision
making, attain consensus as well as allow predictions on the basis of past history, total quality
management requires that a company should collect and evaluate data constantly.
Communications: At the time of any change that takes place within an organisation,
effective communication plays crucial role in motivating employees and keeping up their morale
at all levels. It involves methods, strategies and timeliness that helps in performing each task in
proper and effective manner (Kim, Kumar and Kumar, 2012).
According to the view point of Kr Singh, (2011), TQM is a systematic, participative
method to planning and executing a continuous improvement process of organisation. This
approach is revolved around outperforming customers' expectations, determining issues,
developing commitment and propelling open decision making among manpower. There are 5
essential steps to Total Quality Management and each one is essential for successful execution.
These factors are defined below:
Understanding and Commitment from employees:
3
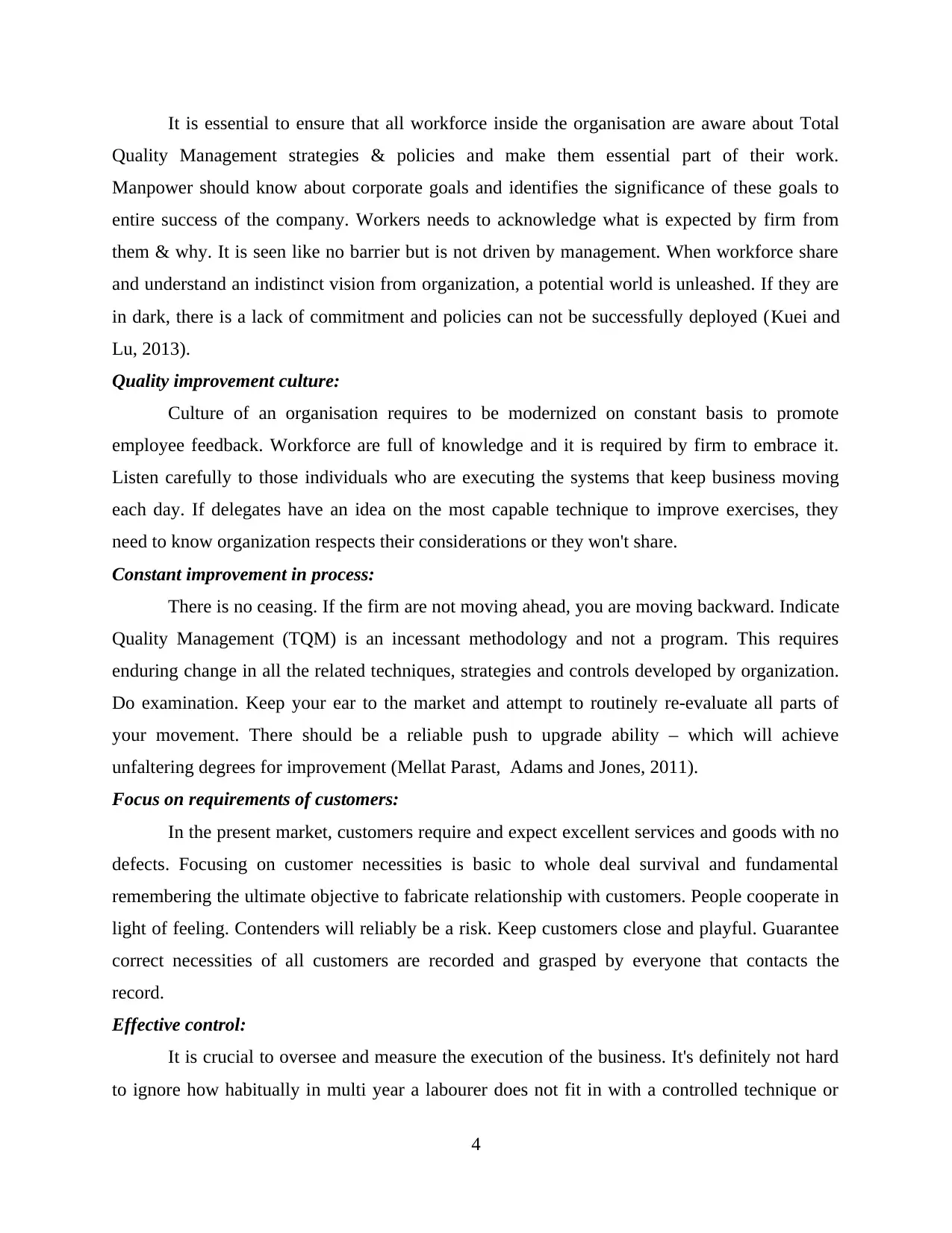
It is essential to ensure that all workforce inside the organisation are aware about Total
Quality Management strategies & policies and make them essential part of their work.
Manpower should know about corporate goals and identifies the significance of these goals to
entire success of the company. Workers needs to acknowledge what is expected by firm from
them & why. It is seen like no barrier but is not driven by management. When workforce share
and understand an indistinct vision from organization, a potential world is unleashed. If they are
in dark, there is a lack of commitment and policies can not be successfully deployed (Kuei and
Lu, 2013).
Quality improvement culture:
Culture of an organisation requires to be modernized on constant basis to promote
employee feedback. Workforce are full of knowledge and it is required by firm to embrace it.
Listen carefully to those individuals who are executing the systems that keep business moving
each day. If delegates have an idea on the most capable technique to improve exercises, they
need to know organization respects their considerations or they won't share.
Constant improvement in process:
There is no ceasing. If the firm are not moving ahead, you are moving backward. Indicate
Quality Management (TQM) is an incessant methodology and not a program. This requires
enduring change in all the related techniques, strategies and controls developed by organization.
Do examination. Keep your ear to the market and attempt to routinely re-evaluate all parts of
your movement. There should be a reliable push to upgrade ability – which will achieve
unfaltering degrees for improvement (Mellat Parast, Adams and Jones, 2011).
Focus on requirements of customers:
In the present market, customers require and expect excellent services and goods with no
defects. Focusing on customer necessities is basic to whole deal survival and fundamental
remembering the ultimate objective to fabricate relationship with customers. People cooperate in
light of feeling. Contenders will reliably be a risk. Keep customers close and playful. Guarantee
correct necessities of all customers are recorded and grasped by everyone that contacts the
record.
Effective control:
It is crucial to oversee and measure the execution of the business. It's definitely not hard
to ignore how habitually in multi year a labourer does not fit in with a controlled technique or
4
Quality Management strategies & policies and make them essential part of their work.
Manpower should know about corporate goals and identifies the significance of these goals to
entire success of the company. Workers needs to acknowledge what is expected by firm from
them & why. It is seen like no barrier but is not driven by management. When workforce share
and understand an indistinct vision from organization, a potential world is unleashed. If they are
in dark, there is a lack of commitment and policies can not be successfully deployed (Kuei and
Lu, 2013).
Quality improvement culture:
Culture of an organisation requires to be modernized on constant basis to promote
employee feedback. Workforce are full of knowledge and it is required by firm to embrace it.
Listen carefully to those individuals who are executing the systems that keep business moving
each day. If delegates have an idea on the most capable technique to improve exercises, they
need to know organization respects their considerations or they won't share.
Constant improvement in process:
There is no ceasing. If the firm are not moving ahead, you are moving backward. Indicate
Quality Management (TQM) is an incessant methodology and not a program. This requires
enduring change in all the related techniques, strategies and controls developed by organization.
Do examination. Keep your ear to the market and attempt to routinely re-evaluate all parts of
your movement. There should be a reliable push to upgrade ability – which will achieve
unfaltering degrees for improvement (Mellat Parast, Adams and Jones, 2011).
Focus on requirements of customers:
In the present market, customers require and expect excellent services and goods with no
defects. Focusing on customer necessities is basic to whole deal survival and fundamental
remembering the ultimate objective to fabricate relationship with customers. People cooperate in
light of feeling. Contenders will reliably be a risk. Keep customers close and playful. Guarantee
correct necessities of all customers are recorded and grasped by everyone that contacts the
record.
Effective control:
It is crucial to oversee and measure the execution of the business. It's definitely not hard
to ignore how habitually in multi year a labourer does not fit in with a controlled technique or
4
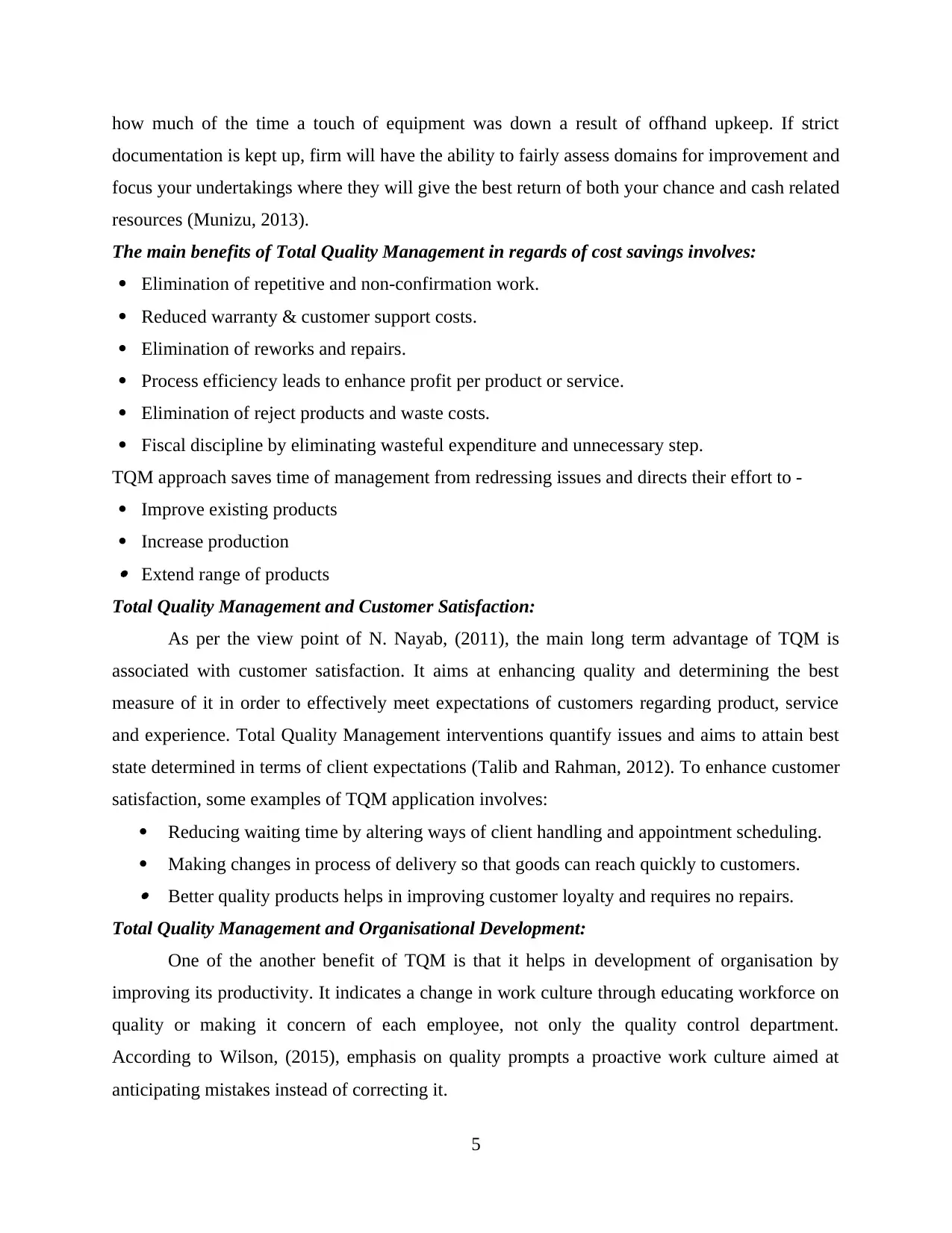
how much of the time a touch of equipment was down a result of offhand upkeep. If strict
documentation is kept up, firm will have the ability to fairly assess domains for improvement and
focus your undertakings where they will give the best return of both your chance and cash related
resources (Munizu, 2013).
The main benefits of Total Quality Management in regards of cost savings involves:
Elimination of repetitive and non-confirmation work.
Reduced warranty & customer support costs.
Elimination of reworks and repairs.
Process efficiency leads to enhance profit per product or service.
Elimination of reject products and waste costs.
Fiscal discipline by eliminating wasteful expenditure and unnecessary step.
TQM approach saves time of management from redressing issues and directs their effort to -
Improve existing products
Increase production Extend range of products
Total Quality Management and Customer Satisfaction:
As per the view point of N. Nayab, (2011), the main long term advantage of TQM is
associated with customer satisfaction. It aims at enhancing quality and determining the best
measure of it in order to effectively meet expectations of customers regarding product, service
and experience. Total Quality Management interventions quantify issues and aims to attain best
state determined in terms of client expectations (Talib and Rahman, 2012). To enhance customer
satisfaction, some examples of TQM application involves:
Reducing waiting time by altering ways of client handling and appointment scheduling.
Making changes in process of delivery so that goods can reach quickly to customers. Better quality products helps in improving customer loyalty and requires no repairs.
Total Quality Management and Organisational Development:
One of the another benefit of TQM is that it helps in development of organisation by
improving its productivity. It indicates a change in work culture through educating workforce on
quality or making it concern of each employee, not only the quality control department.
According to Wilson, (2015), emphasis on quality prompts a proactive work culture aimed at
anticipating mistakes instead of correcting it.
5
documentation is kept up, firm will have the ability to fairly assess domains for improvement and
focus your undertakings where they will give the best return of both your chance and cash related
resources (Munizu, 2013).
The main benefits of Total Quality Management in regards of cost savings involves:
Elimination of repetitive and non-confirmation work.
Reduced warranty & customer support costs.
Elimination of reworks and repairs.
Process efficiency leads to enhance profit per product or service.
Elimination of reject products and waste costs.
Fiscal discipline by eliminating wasteful expenditure and unnecessary step.
TQM approach saves time of management from redressing issues and directs their effort to -
Improve existing products
Increase production Extend range of products
Total Quality Management and Customer Satisfaction:
As per the view point of N. Nayab, (2011), the main long term advantage of TQM is
associated with customer satisfaction. It aims at enhancing quality and determining the best
measure of it in order to effectively meet expectations of customers regarding product, service
and experience. Total Quality Management interventions quantify issues and aims to attain best
state determined in terms of client expectations (Talib and Rahman, 2012). To enhance customer
satisfaction, some examples of TQM application involves:
Reducing waiting time by altering ways of client handling and appointment scheduling.
Making changes in process of delivery so that goods can reach quickly to customers. Better quality products helps in improving customer loyalty and requires no repairs.
Total Quality Management and Organisational Development:
One of the another benefit of TQM is that it helps in development of organisation by
improving its productivity. It indicates a change in work culture through educating workforce on
quality or making it concern of each employee, not only the quality control department.
According to Wilson, (2015), emphasis on quality prompts a proactive work culture aimed at
anticipating mistakes instead of correcting it.
5
Paraphrase This Document
Need a fresh take? Get an instant paraphrase of this document with our AI Paraphraser
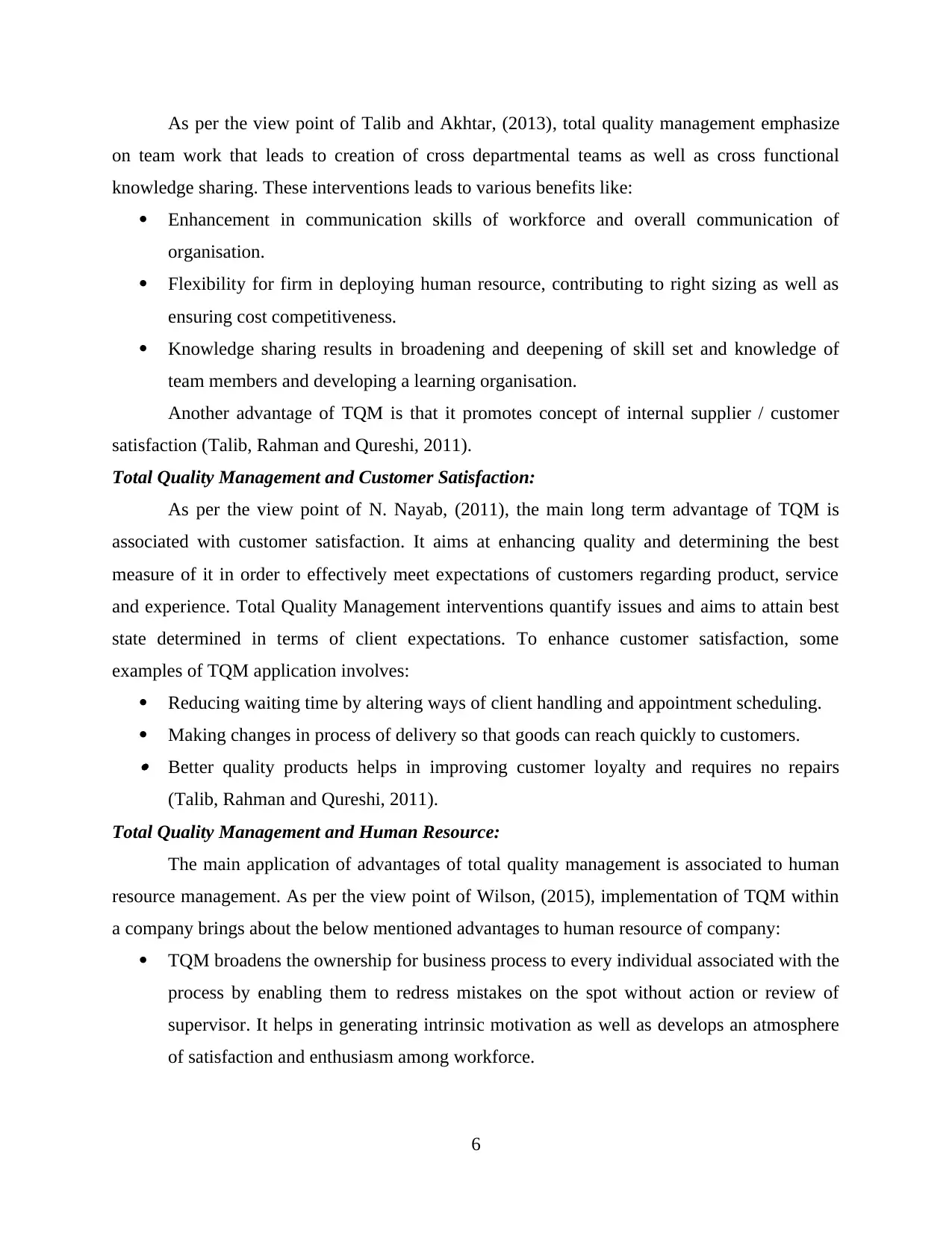
As per the view point of Talib and Akhtar, (2013), total quality management emphasize
on team work that leads to creation of cross departmental teams as well as cross functional
knowledge sharing. These interventions leads to various benefits like:
Enhancement in communication skills of workforce and overall communication of
organisation.
Flexibility for firm in deploying human resource, contributing to right sizing as well as
ensuring cost competitiveness.
Knowledge sharing results in broadening and deepening of skill set and knowledge of
team members and developing a learning organisation.
Another advantage of TQM is that it promotes concept of internal supplier / customer
satisfaction (Talib, Rahman and Qureshi, 2011).
Total Quality Management and Customer Satisfaction:
As per the view point of N. Nayab, (2011), the main long term advantage of TQM is
associated with customer satisfaction. It aims at enhancing quality and determining the best
measure of it in order to effectively meet expectations of customers regarding product, service
and experience. Total Quality Management interventions quantify issues and aims to attain best
state determined in terms of client expectations. To enhance customer satisfaction, some
examples of TQM application involves:
Reducing waiting time by altering ways of client handling and appointment scheduling.
Making changes in process of delivery so that goods can reach quickly to customers. Better quality products helps in improving customer loyalty and requires no repairs
(Talib, Rahman and Qureshi, 2011).
Total Quality Management and Human Resource:
The main application of advantages of total quality management is associated to human
resource management. As per the view point of Wilson, (2015), implementation of TQM within
a company brings about the below mentioned advantages to human resource of company:
TQM broadens the ownership for business process to every individual associated with the
process by enabling them to redress mistakes on the spot without action or review of
supervisor. It helps in generating intrinsic motivation as well as develops an atmosphere
of satisfaction and enthusiasm among workforce.
6
on team work that leads to creation of cross departmental teams as well as cross functional
knowledge sharing. These interventions leads to various benefits like:
Enhancement in communication skills of workforce and overall communication of
organisation.
Flexibility for firm in deploying human resource, contributing to right sizing as well as
ensuring cost competitiveness.
Knowledge sharing results in broadening and deepening of skill set and knowledge of
team members and developing a learning organisation.
Another advantage of TQM is that it promotes concept of internal supplier / customer
satisfaction (Talib, Rahman and Qureshi, 2011).
Total Quality Management and Customer Satisfaction:
As per the view point of N. Nayab, (2011), the main long term advantage of TQM is
associated with customer satisfaction. It aims at enhancing quality and determining the best
measure of it in order to effectively meet expectations of customers regarding product, service
and experience. Total Quality Management interventions quantify issues and aims to attain best
state determined in terms of client expectations. To enhance customer satisfaction, some
examples of TQM application involves:
Reducing waiting time by altering ways of client handling and appointment scheduling.
Making changes in process of delivery so that goods can reach quickly to customers. Better quality products helps in improving customer loyalty and requires no repairs
(Talib, Rahman and Qureshi, 2011).
Total Quality Management and Human Resource:
The main application of advantages of total quality management is associated to human
resource management. As per the view point of Wilson, (2015), implementation of TQM within
a company brings about the below mentioned advantages to human resource of company:
TQM broadens the ownership for business process to every individual associated with the
process by enabling them to redress mistakes on the spot without action or review of
supervisor. It helps in generating intrinsic motivation as well as develops an atmosphere
of satisfaction and enthusiasm among workforce.
6
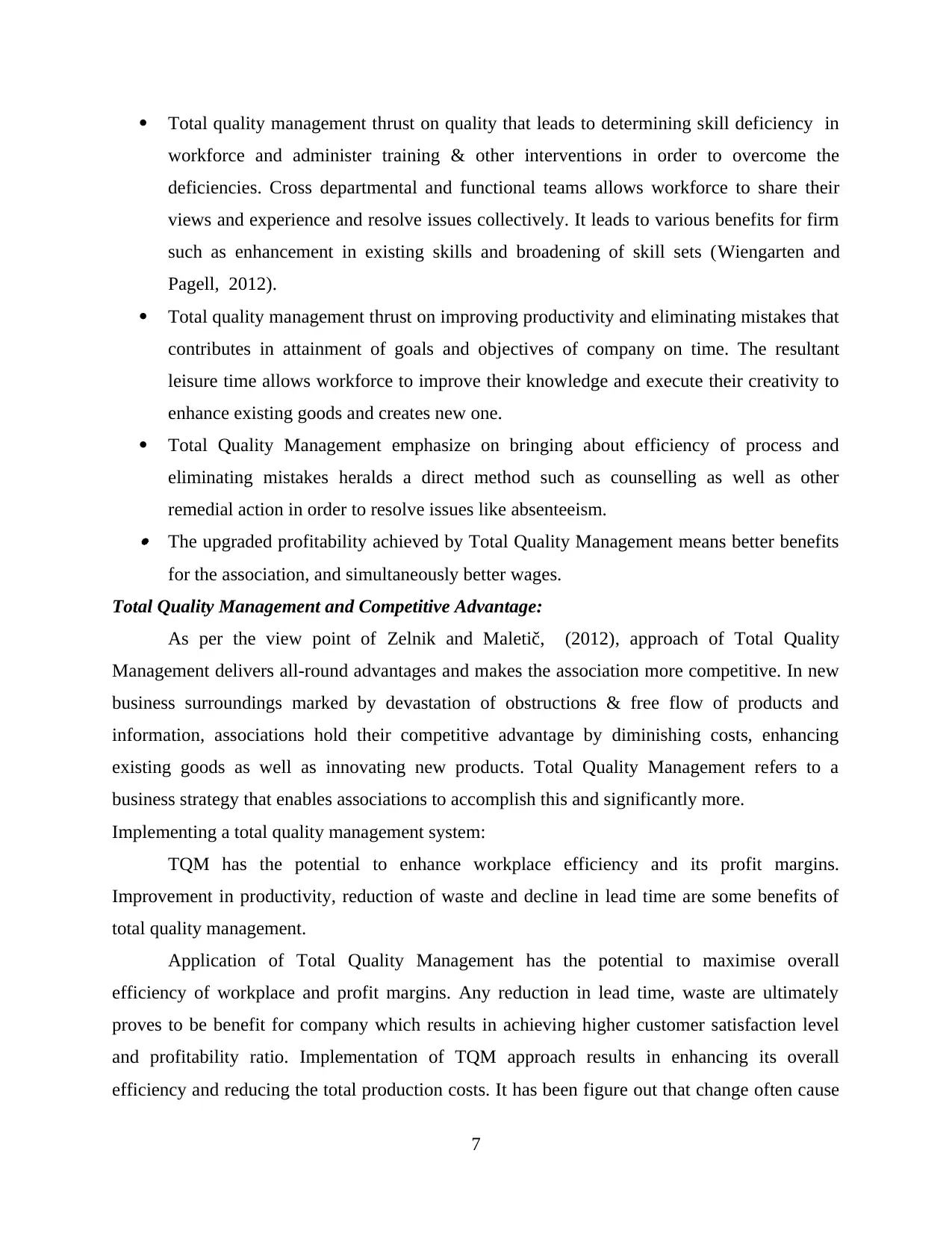
Total quality management thrust on quality that leads to determining skill deficiency in
workforce and administer training & other interventions in order to overcome the
deficiencies. Cross departmental and functional teams allows workforce to share their
views and experience and resolve issues collectively. It leads to various benefits for firm
such as enhancement in existing skills and broadening of skill sets (Wiengarten and
Pagell, 2012).
Total quality management thrust on improving productivity and eliminating mistakes that
contributes in attainment of goals and objectives of company on time. The resultant
leisure time allows workforce to improve their knowledge and execute their creativity to
enhance existing goods and creates new one.
Total Quality Management emphasize on bringing about efficiency of process and
eliminating mistakes heralds a direct method such as counselling as well as other
remedial action in order to resolve issues like absenteeism. The upgraded profitability achieved by Total Quality Management means better benefits
for the association, and simultaneously better wages.
Total Quality Management and Competitive Advantage:
As per the view point of Zelnik and Maletič, (2012), approach of Total Quality
Management delivers all-round advantages and makes the association more competitive. In new
business surroundings marked by devastation of obstructions & free flow of products and
information, associations hold their competitive advantage by diminishing costs, enhancing
existing goods as well as innovating new products. Total Quality Management refers to a
business strategy that enables associations to accomplish this and significantly more.
Implementing a total quality management system:
TQM has the potential to enhance workplace efficiency and its profit margins.
Improvement in productivity, reduction of waste and decline in lead time are some benefits of
total quality management.
Application of Total Quality Management has the potential to maximise overall
efficiency of workplace and profit margins. Any reduction in lead time, waste are ultimately
proves to be benefit for company which results in achieving higher customer satisfaction level
and profitability ratio. Implementation of TQM approach results in enhancing its overall
efficiency and reducing the total production costs. It has been figure out that change often cause
7
workforce and administer training & other interventions in order to overcome the
deficiencies. Cross departmental and functional teams allows workforce to share their
views and experience and resolve issues collectively. It leads to various benefits for firm
such as enhancement in existing skills and broadening of skill sets (Wiengarten and
Pagell, 2012).
Total quality management thrust on improving productivity and eliminating mistakes that
contributes in attainment of goals and objectives of company on time. The resultant
leisure time allows workforce to improve their knowledge and execute their creativity to
enhance existing goods and creates new one.
Total Quality Management emphasize on bringing about efficiency of process and
eliminating mistakes heralds a direct method such as counselling as well as other
remedial action in order to resolve issues like absenteeism. The upgraded profitability achieved by Total Quality Management means better benefits
for the association, and simultaneously better wages.
Total Quality Management and Competitive Advantage:
As per the view point of Zelnik and Maletič, (2012), approach of Total Quality
Management delivers all-round advantages and makes the association more competitive. In new
business surroundings marked by devastation of obstructions & free flow of products and
information, associations hold their competitive advantage by diminishing costs, enhancing
existing goods as well as innovating new products. Total Quality Management refers to a
business strategy that enables associations to accomplish this and significantly more.
Implementing a total quality management system:
TQM has the potential to enhance workplace efficiency and its profit margins.
Improvement in productivity, reduction of waste and decline in lead time are some benefits of
total quality management.
Application of Total Quality Management has the potential to maximise overall
efficiency of workplace and profit margins. Any reduction in lead time, waste are ultimately
proves to be benefit for company which results in achieving higher customer satisfaction level
and profitability ratio. Implementation of TQM approach results in enhancing its overall
efficiency and reducing the total production costs. It has been figure out that change often cause
7
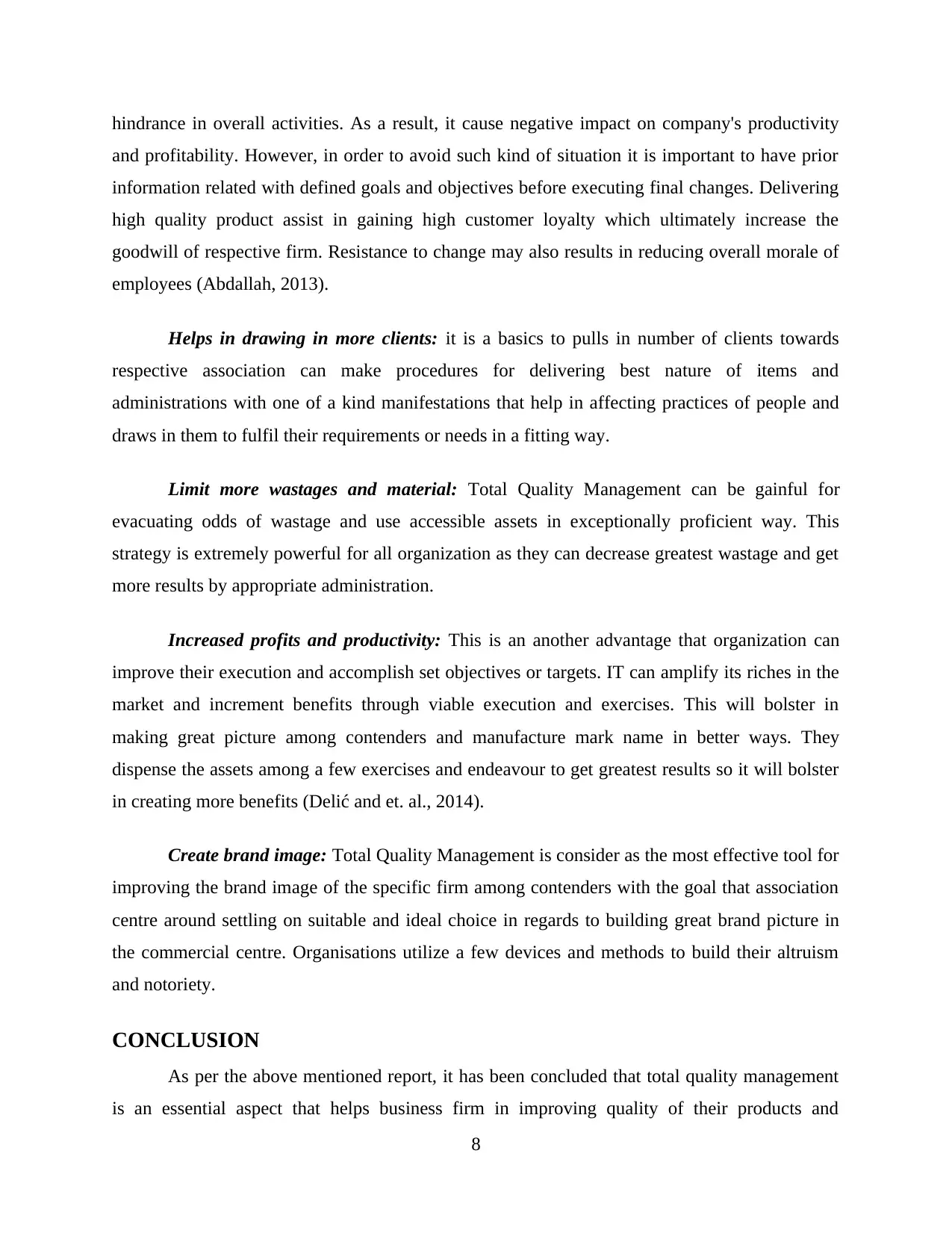
hindrance in overall activities. As a result, it cause negative impact on company's productivity
and profitability. However, in order to avoid such kind of situation it is important to have prior
information related with defined goals and objectives before executing final changes. Delivering
high quality product assist in gaining high customer loyalty which ultimately increase the
goodwill of respective firm. Resistance to change may also results in reducing overall morale of
employees (Abdallah, 2013).
Helps in drawing in more clients: it is a basics to pulls in number of clients towards
respective association can make procedures for delivering best nature of items and
administrations with one of a kind manifestations that help in affecting practices of people and
draws in them to fulfil their requirements or needs in a fitting way.
Limit more wastages and material: Total Quality Management can be gainful for
evacuating odds of wastage and use accessible assets in exceptionally proficient way. This
strategy is extremely powerful for all organization as they can decrease greatest wastage and get
more results by appropriate administration.
Increased profits and productivity: This is an another advantage that organization can
improve their execution and accomplish set objectives or targets. IT can amplify its riches in the
market and increment benefits through viable execution and exercises. This will bolster in
making great picture among contenders and manufacture mark name in better ways. They
dispense the assets among a few exercises and endeavour to get greatest results so it will bolster
in creating more benefits (Delić and et. al., 2014).
Create brand image: Total Quality Management is consider as the most effective tool for
improving the brand image of the specific firm among contenders with the goal that association
centre around settling on suitable and ideal choice in regards to building great brand picture in
the commercial centre. Organisations utilize a few devices and methods to build their altruism
and notoriety.
CONCLUSION
As per the above mentioned report, it has been concluded that total quality management
is an essential aspect that helps business firm in improving quality of their products and
8
and profitability. However, in order to avoid such kind of situation it is important to have prior
information related with defined goals and objectives before executing final changes. Delivering
high quality product assist in gaining high customer loyalty which ultimately increase the
goodwill of respective firm. Resistance to change may also results in reducing overall morale of
employees (Abdallah, 2013).
Helps in drawing in more clients: it is a basics to pulls in number of clients towards
respective association can make procedures for delivering best nature of items and
administrations with one of a kind manifestations that help in affecting practices of people and
draws in them to fulfil their requirements or needs in a fitting way.
Limit more wastages and material: Total Quality Management can be gainful for
evacuating odds of wastage and use accessible assets in exceptionally proficient way. This
strategy is extremely powerful for all organization as they can decrease greatest wastage and get
more results by appropriate administration.
Increased profits and productivity: This is an another advantage that organization can
improve their execution and accomplish set objectives or targets. IT can amplify its riches in the
market and increment benefits through viable execution and exercises. This will bolster in
making great picture among contenders and manufacture mark name in better ways. They
dispense the assets among a few exercises and endeavour to get greatest results so it will bolster
in creating more benefits (Delić and et. al., 2014).
Create brand image: Total Quality Management is consider as the most effective tool for
improving the brand image of the specific firm among contenders with the goal that association
centre around settling on suitable and ideal choice in regards to building great brand picture in
the commercial centre. Organisations utilize a few devices and methods to build their altruism
and notoriety.
CONCLUSION
As per the above mentioned report, it has been concluded that total quality management
is an essential aspect that helps business firm in improving quality of their products and
8
Secure Best Marks with AI Grader
Need help grading? Try our AI Grader for instant feedback on your assignments.
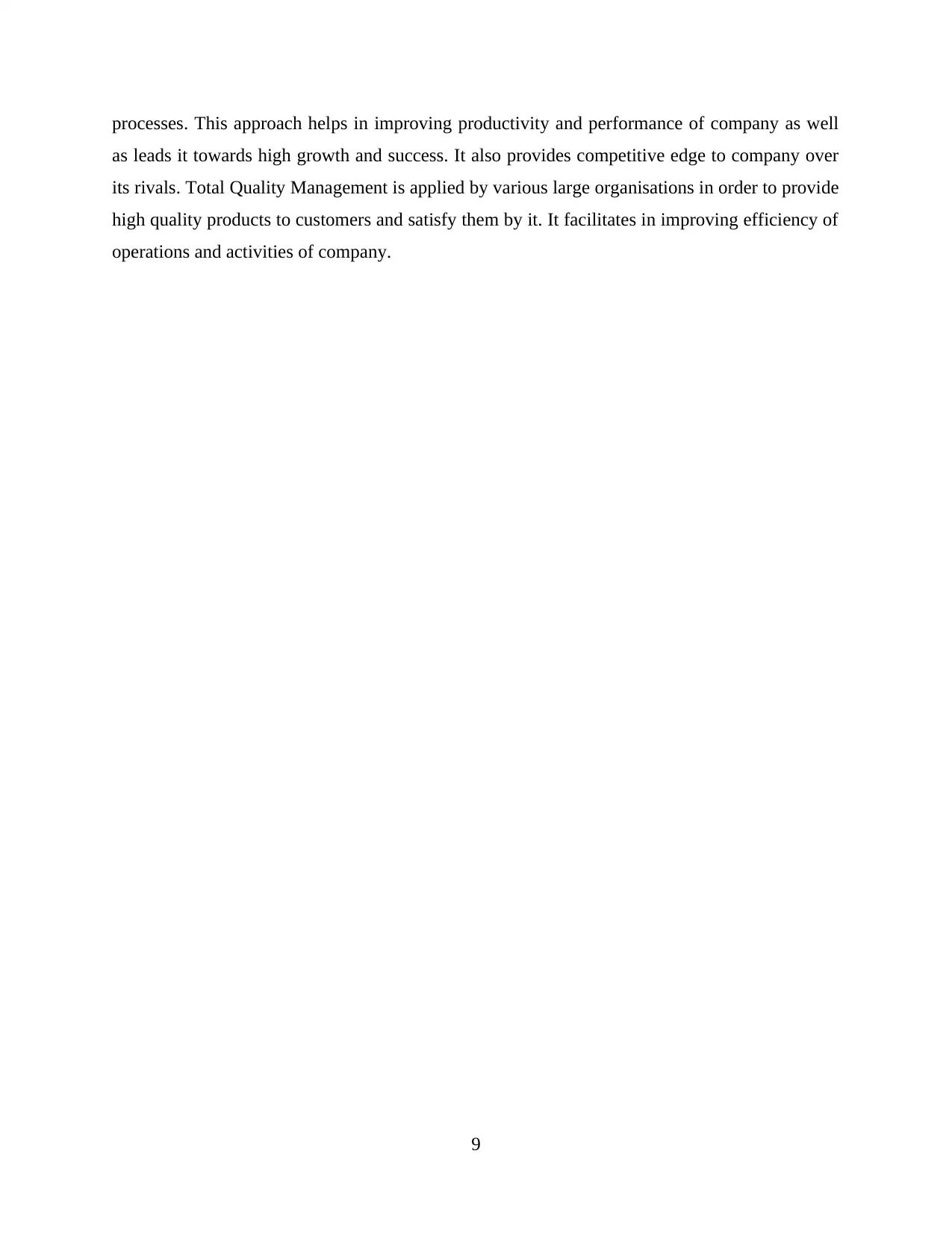
processes. This approach helps in improving productivity and performance of company as well
as leads it towards high growth and success. It also provides competitive edge to company over
its rivals. Total Quality Management is applied by various large organisations in order to provide
high quality products to customers and satisfy them by it. It facilitates in improving efficiency of
operations and activities of company.
9
as leads it towards high growth and success. It also provides competitive edge to company over
its rivals. Total Quality Management is applied by various large organisations in order to provide
high quality products to customers and satisfy them by it. It facilitates in improving efficiency of
operations and activities of company.
9
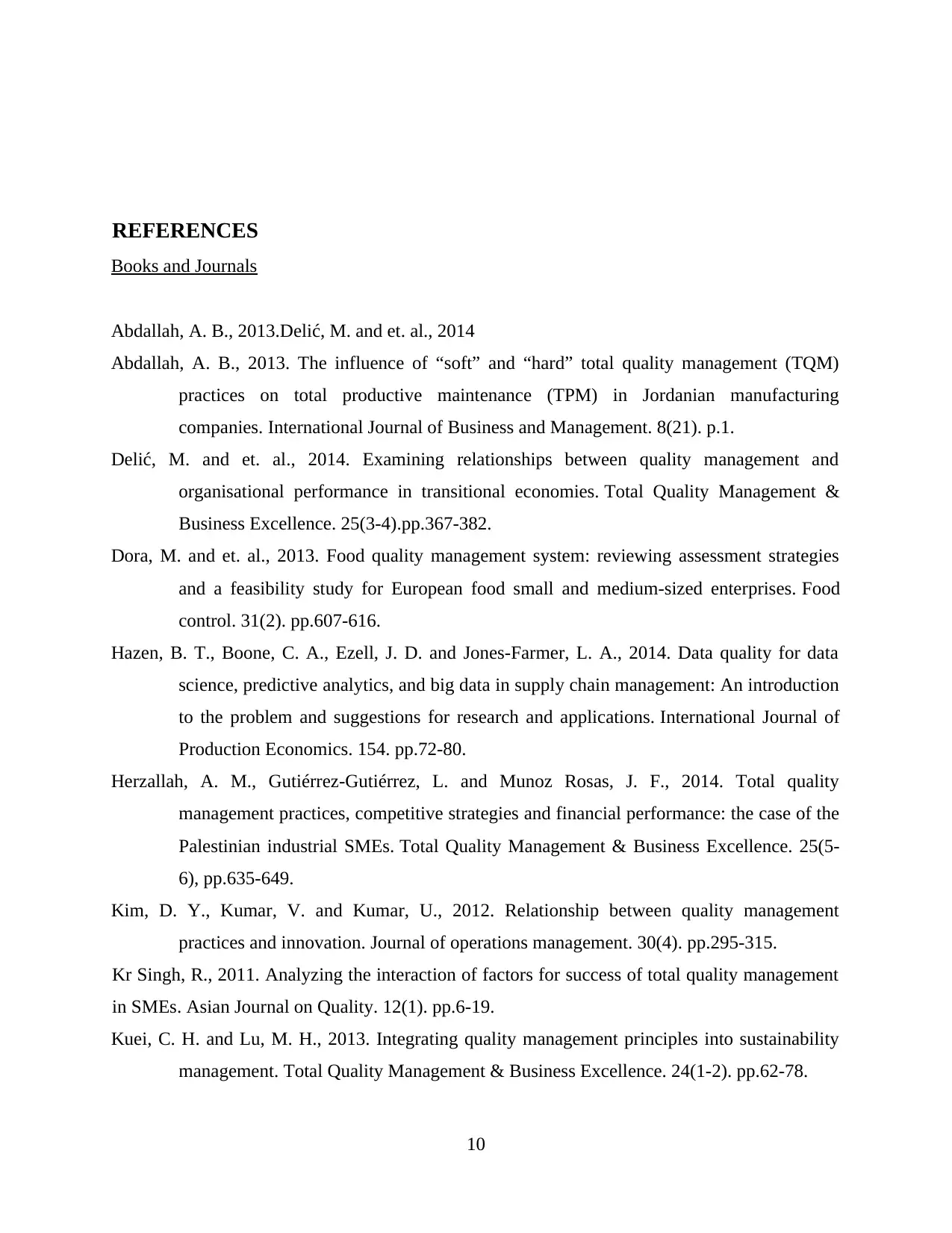
REFERENCES
Books and Journals
Abdallah, A. B., 2013.Delić, M. and et. al., 2014
Abdallah, A. B., 2013. The influence of “soft” and “hard” total quality management (TQM)
practices on total productive maintenance (TPM) in Jordanian manufacturing
companies. International Journal of Business and Management. 8(21). p.1.
Delić, M. and et. al., 2014. Examining relationships between quality management and
organisational performance in transitional economies. Total Quality Management &
Business Excellence. 25(3-4).pp.367-382.
Dora, M. and et. al., 2013. Food quality management system: reviewing assessment strategies
and a feasibility study for European food small and medium-sized enterprises. Food
control. 31(2). pp.607-616.
Hazen, B. T., Boone, C. A., Ezell, J. D. and Jones-Farmer, L. A., 2014. Data quality for data
science, predictive analytics, and big data in supply chain management: An introduction
to the problem and suggestions for research and applications. International Journal of
Production Economics. 154. pp.72-80.
Herzallah, A. M., Gutiérrez-Gutiérrez, L. and Munoz Rosas, J. F., 2014. Total quality
management practices, competitive strategies and financial performance: the case of the
Palestinian industrial SMEs. Total Quality Management & Business Excellence. 25(5-
6), pp.635-649.
Kim, D. Y., Kumar, V. and Kumar, U., 2012. Relationship between quality management
practices and innovation. Journal of operations management. 30(4). pp.295-315.
Kr Singh, R., 2011. Analyzing the interaction of factors for success of total quality management
in SMEs. Asian Journal on Quality. 12(1). pp.6-19.
Kuei, C. H. and Lu, M. H., 2013. Integrating quality management principles into sustainability
management. Total Quality Management & Business Excellence. 24(1-2). pp.62-78.
10
Books and Journals
Abdallah, A. B., 2013.Delić, M. and et. al., 2014
Abdallah, A. B., 2013. The influence of “soft” and “hard” total quality management (TQM)
practices on total productive maintenance (TPM) in Jordanian manufacturing
companies. International Journal of Business and Management. 8(21). p.1.
Delić, M. and et. al., 2014. Examining relationships between quality management and
organisational performance in transitional economies. Total Quality Management &
Business Excellence. 25(3-4).pp.367-382.
Dora, M. and et. al., 2013. Food quality management system: reviewing assessment strategies
and a feasibility study for European food small and medium-sized enterprises. Food
control. 31(2). pp.607-616.
Hazen, B. T., Boone, C. A., Ezell, J. D. and Jones-Farmer, L. A., 2014. Data quality for data
science, predictive analytics, and big data in supply chain management: An introduction
to the problem and suggestions for research and applications. International Journal of
Production Economics. 154. pp.72-80.
Herzallah, A. M., Gutiérrez-Gutiérrez, L. and Munoz Rosas, J. F., 2014. Total quality
management practices, competitive strategies and financial performance: the case of the
Palestinian industrial SMEs. Total Quality Management & Business Excellence. 25(5-
6), pp.635-649.
Kim, D. Y., Kumar, V. and Kumar, U., 2012. Relationship between quality management
practices and innovation. Journal of operations management. 30(4). pp.295-315.
Kr Singh, R., 2011. Analyzing the interaction of factors for success of total quality management
in SMEs. Asian Journal on Quality. 12(1). pp.6-19.
Kuei, C. H. and Lu, M. H., 2013. Integrating quality management principles into sustainability
management. Total Quality Management & Business Excellence. 24(1-2). pp.62-78.
10
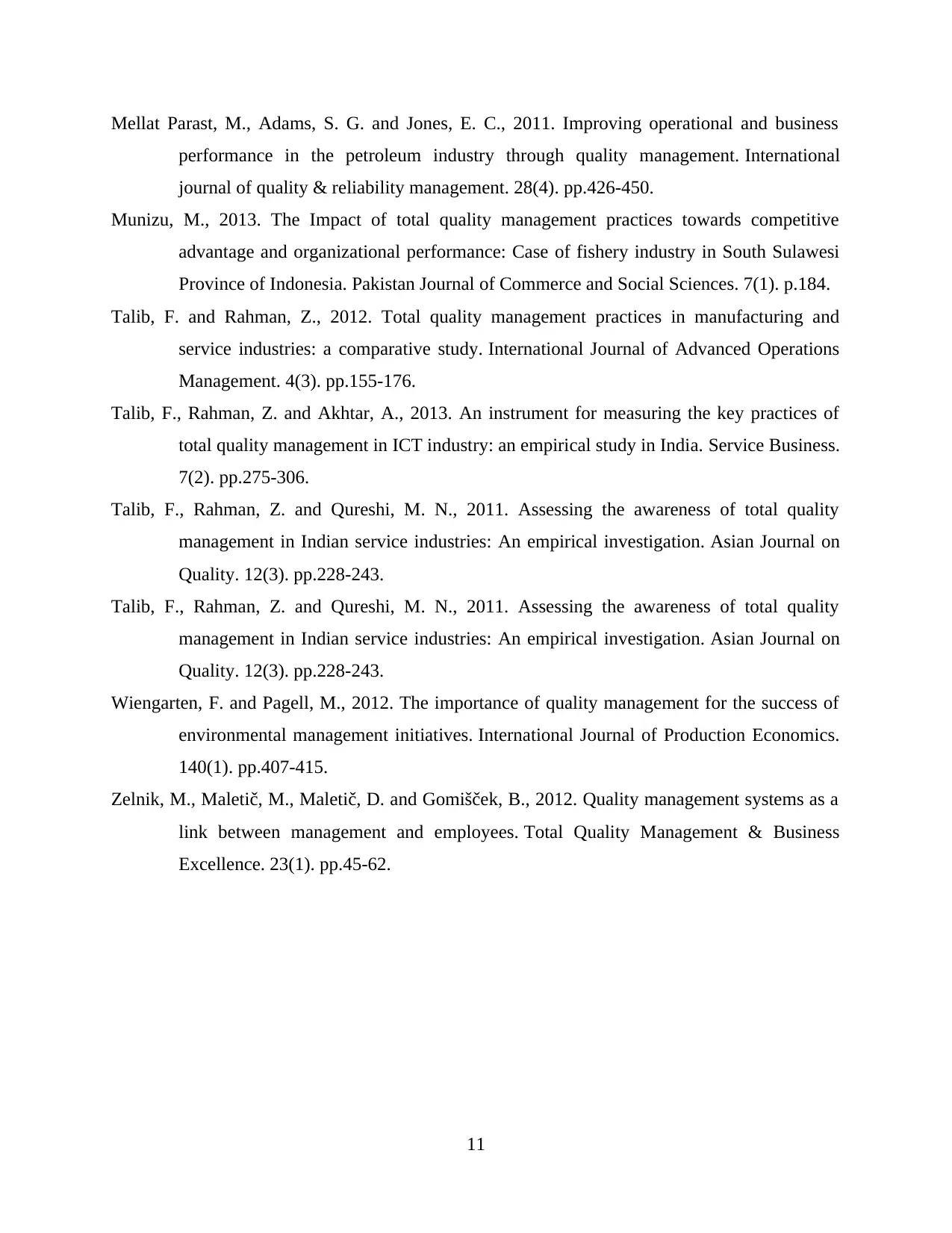
Mellat Parast, M., Adams, S. G. and Jones, E. C., 2011. Improving operational and business
performance in the petroleum industry through quality management. International
journal of quality & reliability management. 28(4). pp.426-450.
Munizu, M., 2013. The Impact of total quality management practices towards competitive
advantage and organizational performance: Case of fishery industry in South Sulawesi
Province of Indonesia. Pakistan Journal of Commerce and Social Sciences. 7(1). p.184.
Talib, F. and Rahman, Z., 2012. Total quality management practices in manufacturing and
service industries: a comparative study. International Journal of Advanced Operations
Management. 4(3). pp.155-176.
Talib, F., Rahman, Z. and Akhtar, A., 2013. An instrument for measuring the key practices of
total quality management in ICT industry: an empirical study in India. Service Business.
7(2). pp.275-306.
Talib, F., Rahman, Z. and Qureshi, M. N., 2011. Assessing the awareness of total quality
management in Indian service industries: An empirical investigation. Asian Journal on
Quality. 12(3). pp.228-243.
Talib, F., Rahman, Z. and Qureshi, M. N., 2011. Assessing the awareness of total quality
management in Indian service industries: An empirical investigation. Asian Journal on
Quality. 12(3). pp.228-243.
Wiengarten, F. and Pagell, M., 2012. The importance of quality management for the success of
environmental management initiatives. International Journal of Production Economics.
140(1). pp.407-415.
Zelnik, M., Maletič, M., Maletič, D. and Gomišček, B., 2012. Quality management systems as a
link between management and employees. Total Quality Management & Business
Excellence. 23(1). pp.45-62.
11
performance in the petroleum industry through quality management. International
journal of quality & reliability management. 28(4). pp.426-450.
Munizu, M., 2013. The Impact of total quality management practices towards competitive
advantage and organizational performance: Case of fishery industry in South Sulawesi
Province of Indonesia. Pakistan Journal of Commerce and Social Sciences. 7(1). p.184.
Talib, F. and Rahman, Z., 2012. Total quality management practices in manufacturing and
service industries: a comparative study. International Journal of Advanced Operations
Management. 4(3). pp.155-176.
Talib, F., Rahman, Z. and Akhtar, A., 2013. An instrument for measuring the key practices of
total quality management in ICT industry: an empirical study in India. Service Business.
7(2). pp.275-306.
Talib, F., Rahman, Z. and Qureshi, M. N., 2011. Assessing the awareness of total quality
management in Indian service industries: An empirical investigation. Asian Journal on
Quality. 12(3). pp.228-243.
Talib, F., Rahman, Z. and Qureshi, M. N., 2011. Assessing the awareness of total quality
management in Indian service industries: An empirical investigation. Asian Journal on
Quality. 12(3). pp.228-243.
Wiengarten, F. and Pagell, M., 2012. The importance of quality management for the success of
environmental management initiatives. International Journal of Production Economics.
140(1). pp.407-415.
Zelnik, M., Maletič, M., Maletič, D. and Gomišček, B., 2012. Quality management systems as a
link between management and employees. Total Quality Management & Business
Excellence. 23(1). pp.45-62.
11
1 out of 13
Related Documents
![[object Object]](/_next/image/?url=%2F_next%2Fstatic%2Fmedia%2Flogo.6d15ce61.png&w=640&q=75)
Your All-in-One AI-Powered Toolkit for Academic Success.
+13062052269
info@desklib.com
Available 24*7 on WhatsApp / Email
Unlock your academic potential
© 2024 | Zucol Services PVT LTD | All rights reserved.