Preparing and Using Lathes for Turning Operations (Doc)
VerifiedAdded on  2020/04/15
|8
|3666
|4180
AI Summary
This document covers all the possible 21 questions/queries based on th "Unit 011 - Preparing and using lathes for turningoperations". Check out another document on "Using Lathe in Turning Operations" if you want get more about lathe and turning operations.
Contribute Materials
Your contribution can guide someone’s learning journey. Share your
documents today.
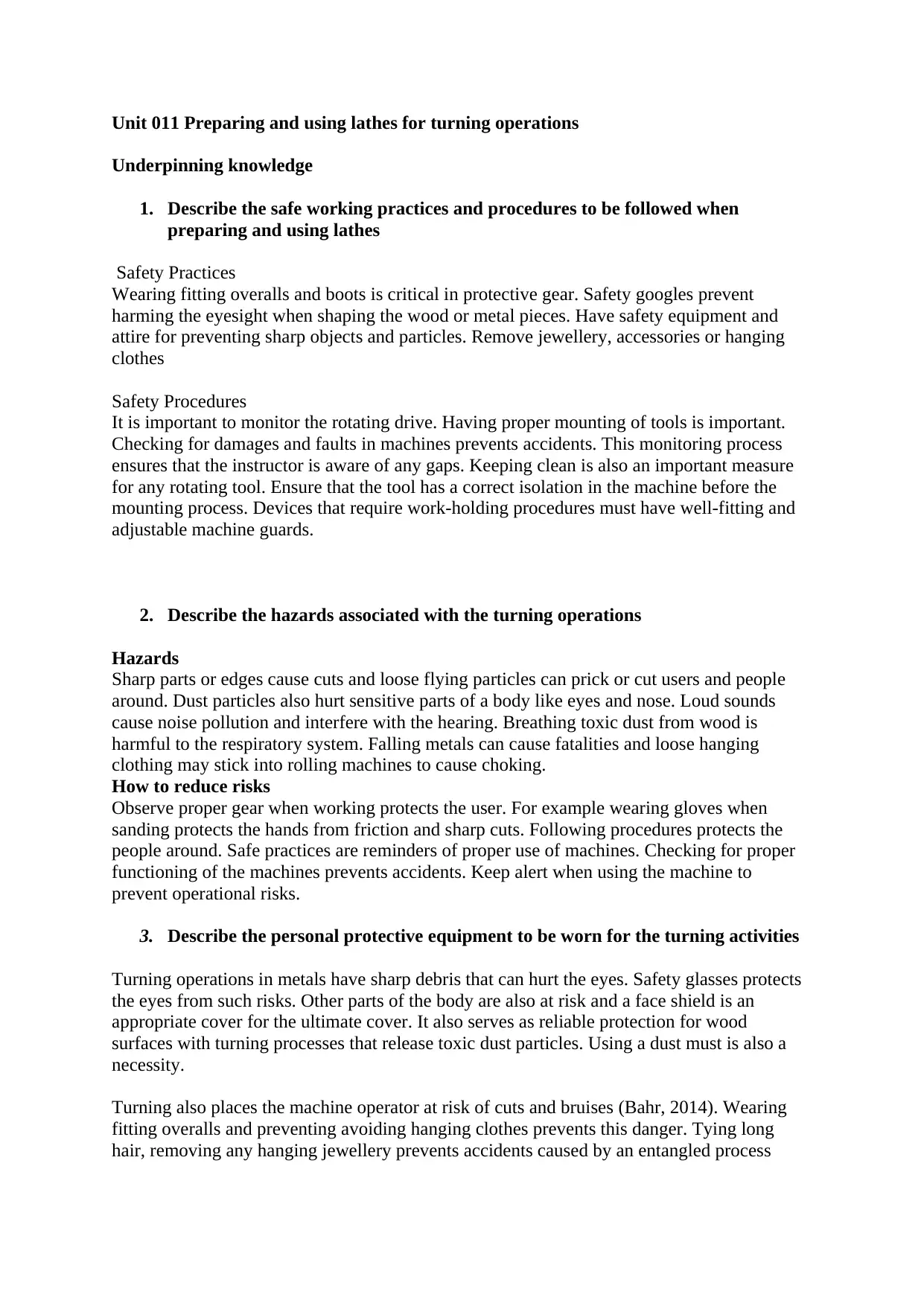
Unit 011 Preparing and using lathes for turning operations
Underpinning knowledge
1. Describe the safe working practices and procedures to be followed when
preparing and using lathes
Safety Practices
Wearing fitting overalls and boots is critical in protective gear. Safety googles prevent
harming the eyesight when shaping the wood or metal pieces. Have safety equipment and
attire for preventing sharp objects and particles. Remove jewellery, accessories or hanging
clothes
Safety Procedures
It is important to monitor the rotating drive. Having proper mounting of tools is important.
Checking for damages and faults in machines prevents accidents. This monitoring process
ensures that the instructor is aware of any gaps. Keeping clean is also an important measure
for any rotating tool. Ensure that the tool has a correct isolation in the machine before the
mounting process. Devices that require work-holding procedures must have well-fitting and
adjustable machine guards.
2. Describe the hazards associated with the turning operations
Hazards
Sharp parts or edges cause cuts and loose flying particles can prick or cut users and people
around. Dust particles also hurt sensitive parts of a body like eyes and nose. Loud sounds
cause noise pollution and interfere with the hearing. Breathing toxic dust from wood is
harmful to the respiratory system. Falling metals can cause fatalities and loose hanging
clothing may stick into rolling machines to cause choking.
How to reduce risks
Observe proper gear when working protects the user. For example wearing gloves when
sanding protects the hands from friction and sharp cuts. Following procedures protects the
people around. Safe practices are reminders of proper use of machines. Checking for proper
functioning of the machines prevents accidents. Keep alert when using the machine to
prevent operational risks.
3. Describe the personal protective equipment to be worn for the turning activities
Turning operations in metals have sharp debris that can hurt the eyes. Safety glasses protects
the eyes from such risks. Other parts of the body are also at risk and a face shield is an
appropriate cover for the ultimate cover. It also serves as reliable protection for wood
surfaces with turning processes that release toxic dust particles. Using a dust must is also a
necessity.
Turning also places the machine operator at risk of cuts and bruises (Bahr, 2014). Wearing
fitting overalls and preventing avoiding hanging clothes prevents this danger. Tying long
hair, removing any hanging jewellery prevents accidents caused by an entangled process
Underpinning knowledge
1. Describe the safe working practices and procedures to be followed when
preparing and using lathes
Safety Practices
Wearing fitting overalls and boots is critical in protective gear. Safety googles prevent
harming the eyesight when shaping the wood or metal pieces. Have safety equipment and
attire for preventing sharp objects and particles. Remove jewellery, accessories or hanging
clothes
Safety Procedures
It is important to monitor the rotating drive. Having proper mounting of tools is important.
Checking for damages and faults in machines prevents accidents. This monitoring process
ensures that the instructor is aware of any gaps. Keeping clean is also an important measure
for any rotating tool. Ensure that the tool has a correct isolation in the machine before the
mounting process. Devices that require work-holding procedures must have well-fitting and
adjustable machine guards.
2. Describe the hazards associated with the turning operations
Hazards
Sharp parts or edges cause cuts and loose flying particles can prick or cut users and people
around. Dust particles also hurt sensitive parts of a body like eyes and nose. Loud sounds
cause noise pollution and interfere with the hearing. Breathing toxic dust from wood is
harmful to the respiratory system. Falling metals can cause fatalities and loose hanging
clothing may stick into rolling machines to cause choking.
How to reduce risks
Observe proper gear when working protects the user. For example wearing gloves when
sanding protects the hands from friction and sharp cuts. Following procedures protects the
people around. Safe practices are reminders of proper use of machines. Checking for proper
functioning of the machines prevents accidents. Keep alert when using the machine to
prevent operational risks.
3. Describe the personal protective equipment to be worn for the turning activities
Turning operations in metals have sharp debris that can hurt the eyes. Safety glasses protects
the eyes from such risks. Other parts of the body are also at risk and a face shield is an
appropriate cover for the ultimate cover. It also serves as reliable protection for wood
surfaces with turning processes that release toxic dust particles. Using a dust must is also a
necessity.
Turning also places the machine operator at risk of cuts and bruises (Bahr, 2014). Wearing
fitting overalls and preventing avoiding hanging clothes prevents this danger. Tying long
hair, removing any hanging jewellery prevents accidents caused by an entangled process
Secure Best Marks with AI Grader
Need help grading? Try our AI Grader for instant feedback on your assignments.
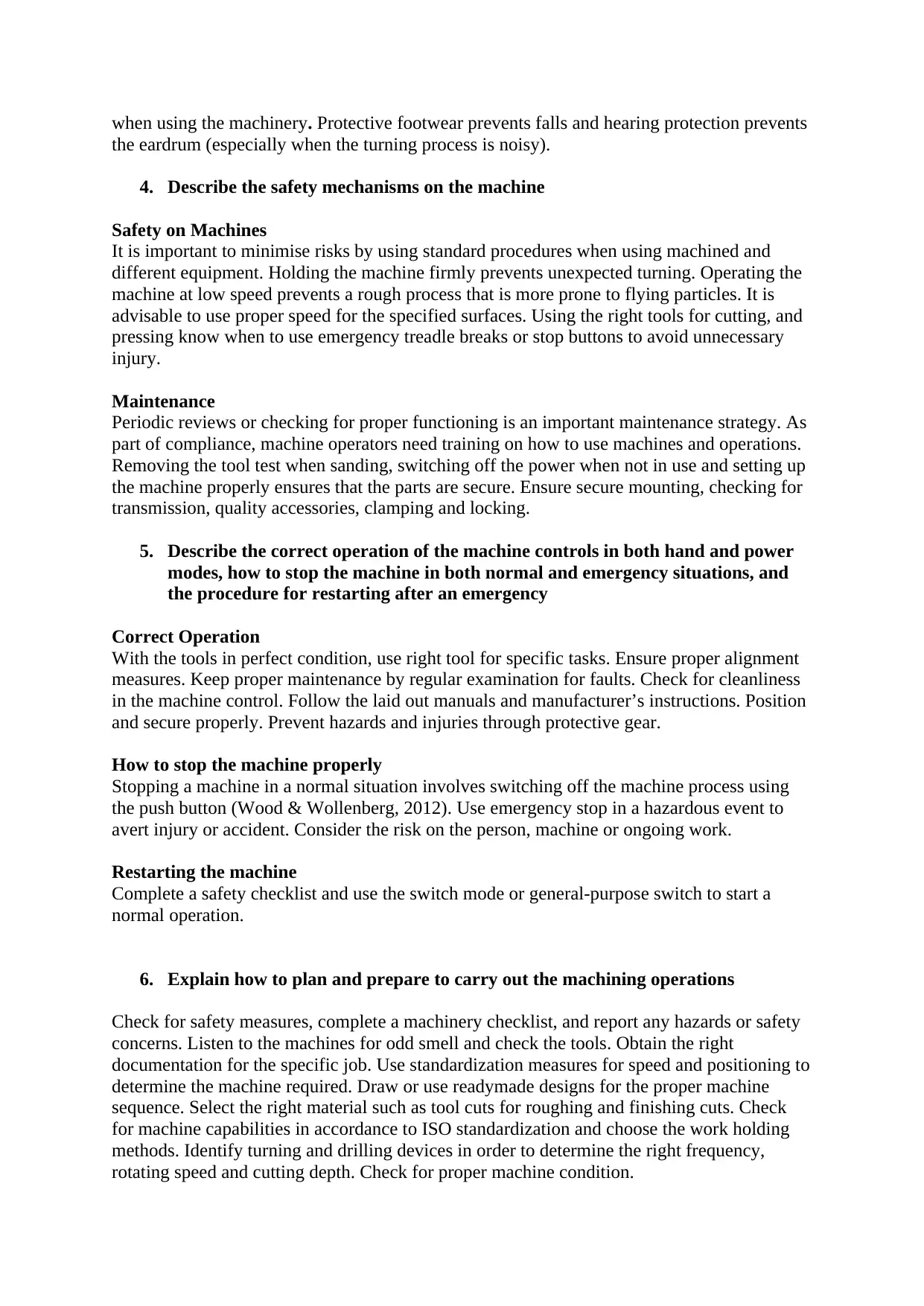
when using the machinery. Protective footwear prevents falls and hearing protection prevents
the eardrum (especially when the turning process is noisy).
4. Describe the safety mechanisms on the machine
Safety on Machines
It is important to minimise risks by using standard procedures when using machined and
different equipment. Holding the machine firmly prevents unexpected turning. Operating the
machine at low speed prevents a rough process that is more prone to flying particles. It is
advisable to use proper speed for the specified surfaces. Using the right tools for cutting, and
pressing know when to use emergency treadle breaks or stop buttons to avoid unnecessary
injury.
Maintenance
Periodic reviews or checking for proper functioning is an important maintenance strategy. As
part of compliance, machine operators need training on how to use machines and operations.
Removing the tool test when sanding, switching off the power when not in use and setting up
the machine properly ensures that the parts are secure. Ensure secure mounting, checking for
transmission, quality accessories, clamping and locking.
5. Describe the correct operation of the machine controls in both hand and power
modes, how to stop the machine in both normal and emergency situations, and
the procedure for restarting after an emergency
Correct Operation
With the tools in perfect condition, use right tool for specific tasks. Ensure proper alignment
measures. Keep proper maintenance by regular examination for faults. Check for cleanliness
in the machine control. Follow the laid out manuals and manufacturer’s instructions. Position
and secure properly. Prevent hazards and injuries through protective gear.
How to stop the machine properly
Stopping a machine in a normal situation involves switching off the machine process using
the push button (Wood & Wollenberg, 2012). Use emergency stop in a hazardous event to
avert injury or accident. Consider the risk on the person, machine or ongoing work.
Restarting the machine
Complete a safety checklist and use the switch mode or general-purpose switch to start a
normal operation.
6. Explain how to plan and prepare to carry out the machining operations
Check for safety measures, complete a machinery checklist, and report any hazards or safety
concerns. Listen to the machines for odd smell and check the tools. Obtain the right
documentation for the specific job. Use standardization measures for speed and positioning to
determine the machine required. Draw or use readymade designs for the proper machine
sequence. Select the right material such as tool cuts for roughing and finishing cuts. Check
for machine capabilities in accordance to ISO standardization and choose the work holding
methods. Identify turning and drilling devices in order to determine the right frequency,
rotating speed and cutting depth. Check for proper machine condition.
the eardrum (especially when the turning process is noisy).
4. Describe the safety mechanisms on the machine
Safety on Machines
It is important to minimise risks by using standard procedures when using machined and
different equipment. Holding the machine firmly prevents unexpected turning. Operating the
machine at low speed prevents a rough process that is more prone to flying particles. It is
advisable to use proper speed for the specified surfaces. Using the right tools for cutting, and
pressing know when to use emergency treadle breaks or stop buttons to avoid unnecessary
injury.
Maintenance
Periodic reviews or checking for proper functioning is an important maintenance strategy. As
part of compliance, machine operators need training on how to use machines and operations.
Removing the tool test when sanding, switching off the power when not in use and setting up
the machine properly ensures that the parts are secure. Ensure secure mounting, checking for
transmission, quality accessories, clamping and locking.
5. Describe the correct operation of the machine controls in both hand and power
modes, how to stop the machine in both normal and emergency situations, and
the procedure for restarting after an emergency
Correct Operation
With the tools in perfect condition, use right tool for specific tasks. Ensure proper alignment
measures. Keep proper maintenance by regular examination for faults. Check for cleanliness
in the machine control. Follow the laid out manuals and manufacturer’s instructions. Position
and secure properly. Prevent hazards and injuries through protective gear.
How to stop the machine properly
Stopping a machine in a normal situation involves switching off the machine process using
the push button (Wood & Wollenberg, 2012). Use emergency stop in a hazardous event to
avert injury or accident. Consider the risk on the person, machine or ongoing work.
Restarting the machine
Complete a safety checklist and use the switch mode or general-purpose switch to start a
normal operation.
6. Explain how to plan and prepare to carry out the machining operations
Check for safety measures, complete a machinery checklist, and report any hazards or safety
concerns. Listen to the machines for odd smell and check the tools. Obtain the right
documentation for the specific job. Use standardization measures for speed and positioning to
determine the machine required. Draw or use readymade designs for the proper machine
sequence. Select the right material such as tool cuts for roughing and finishing cuts. Check
for machine capabilities in accordance to ISO standardization and choose the work holding
methods. Identify turning and drilling devices in order to determine the right frequency,
rotating speed and cutting depth. Check for proper machine condition.
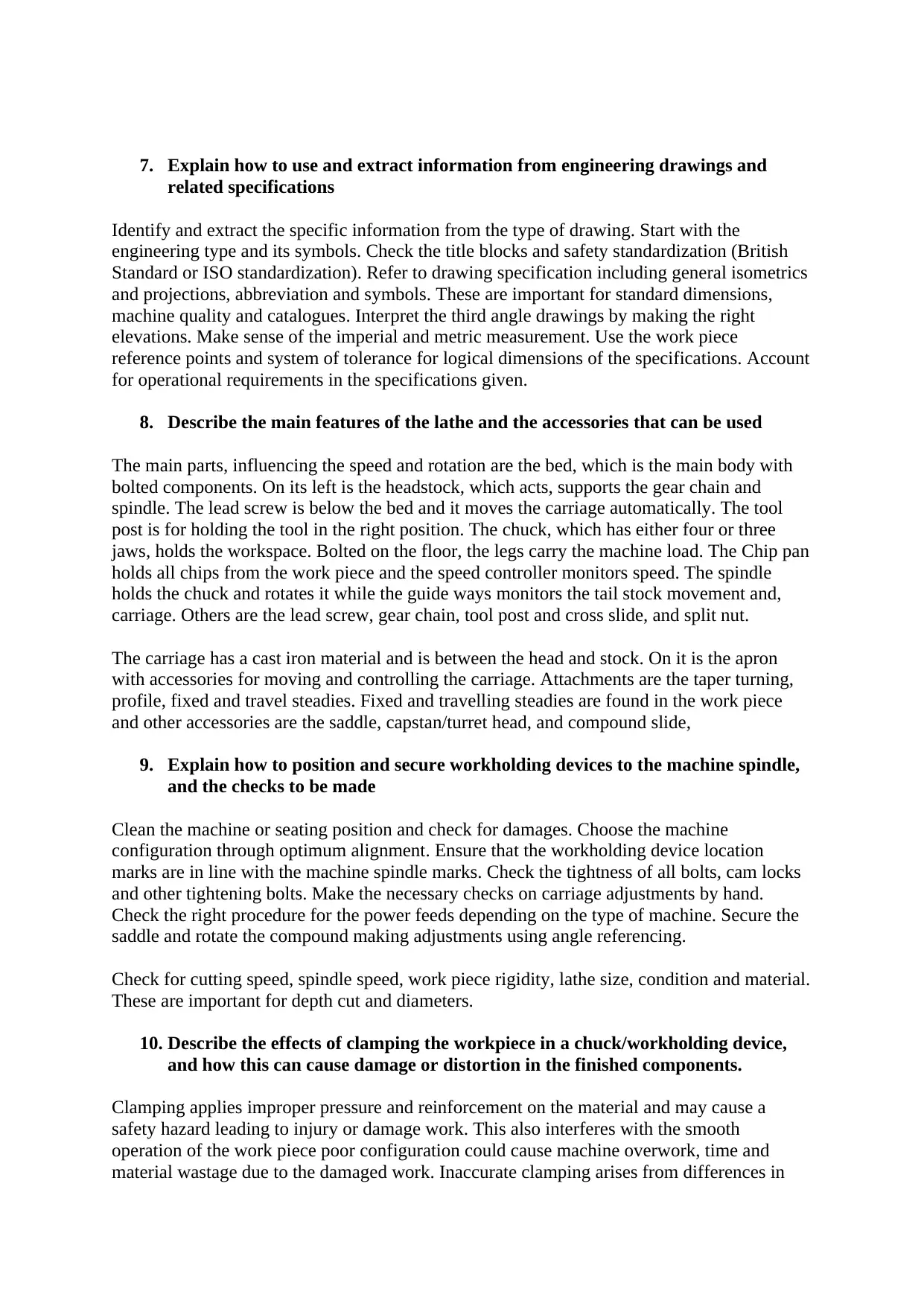
7. Explain how to use and extract information from engineering drawings and
related specifications
Identify and extract the specific information from the type of drawing. Start with the
engineering type and its symbols. Check the title blocks and safety standardization (British
Standard or ISO standardization). Refer to drawing specification including general isometrics
and projections, abbreviation and symbols. These are important for standard dimensions,
machine quality and catalogues. Interpret the third angle drawings by making the right
elevations. Make sense of the imperial and metric measurement. Use the work piece
reference points and system of tolerance for logical dimensions of the specifications. Account
for operational requirements in the specifications given.
8. Describe the main features of the lathe and the accessories that can be used
The main parts, influencing the speed and rotation are the bed, which is the main body with
bolted components. On its left is the headstock, which acts, supports the gear chain and
spindle. The lead screw is below the bed and it moves the carriage automatically. The tool
post is for holding the tool in the right position. The chuck, which has either four or three
jaws, holds the workspace. Bolted on the floor, the legs carry the machine load. The Chip pan
holds all chips from the work piece and the speed controller monitors speed. The spindle
holds the chuck and rotates it while the guide ways monitors the tail stock movement and,
carriage. Others are the lead screw, gear chain, tool post and cross slide, and split nut.
The carriage has a cast iron material and is between the head and stock. On it is the apron
with accessories for moving and controlling the carriage. Attachments are the taper turning,
profile, fixed and travel steadies. Fixed and travelling steadies are found in the work piece
and other accessories are the saddle, capstan/turret head, and compound slide,
9. Explain how to position and secure workholding devices to the machine spindle,
and the checks to be made
Clean the machine or seating position and check for damages. Choose the machine
configuration through optimum alignment. Ensure that the workholding device location
marks are in line with the machine spindle marks. Check the tightness of all bolts, cam locks
and other tightening bolts. Make the necessary checks on carriage adjustments by hand.
Check the right procedure for the power feeds depending on the type of machine. Secure the
saddle and rotate the compound making adjustments using angle referencing.
Check for cutting speed, spindle speed, work piece rigidity, lathe size, condition and material.
These are important for depth cut and diameters.
10. Describe the effects of clamping the workpiece in a chuck/workholding device,
and how this can cause damage or distortion in the finished components.
Clamping applies improper pressure and reinforcement on the material and may cause a
safety hazard leading to injury or damage work. This also interferes with the smooth
operation of the work piece poor configuration could cause machine overwork, time and
material wastage due to the damaged work. Inaccurate clamping arises from differences in
related specifications
Identify and extract the specific information from the type of drawing. Start with the
engineering type and its symbols. Check the title blocks and safety standardization (British
Standard or ISO standardization). Refer to drawing specification including general isometrics
and projections, abbreviation and symbols. These are important for standard dimensions,
machine quality and catalogues. Interpret the third angle drawings by making the right
elevations. Make sense of the imperial and metric measurement. Use the work piece
reference points and system of tolerance for logical dimensions of the specifications. Account
for operational requirements in the specifications given.
8. Describe the main features of the lathe and the accessories that can be used
The main parts, influencing the speed and rotation are the bed, which is the main body with
bolted components. On its left is the headstock, which acts, supports the gear chain and
spindle. The lead screw is below the bed and it moves the carriage automatically. The tool
post is for holding the tool in the right position. The chuck, which has either four or three
jaws, holds the workspace. Bolted on the floor, the legs carry the machine load. The Chip pan
holds all chips from the work piece and the speed controller monitors speed. The spindle
holds the chuck and rotates it while the guide ways monitors the tail stock movement and,
carriage. Others are the lead screw, gear chain, tool post and cross slide, and split nut.
The carriage has a cast iron material and is between the head and stock. On it is the apron
with accessories for moving and controlling the carriage. Attachments are the taper turning,
profile, fixed and travel steadies. Fixed and travelling steadies are found in the work piece
and other accessories are the saddle, capstan/turret head, and compound slide,
9. Explain how to position and secure workholding devices to the machine spindle,
and the checks to be made
Clean the machine or seating position and check for damages. Choose the machine
configuration through optimum alignment. Ensure that the workholding device location
marks are in line with the machine spindle marks. Check the tightness of all bolts, cam locks
and other tightening bolts. Make the necessary checks on carriage adjustments by hand.
Check the right procedure for the power feeds depending on the type of machine. Secure the
saddle and rotate the compound making adjustments using angle referencing.
Check for cutting speed, spindle speed, work piece rigidity, lathe size, condition and material.
These are important for depth cut and diameters.
10. Describe the effects of clamping the workpiece in a chuck/workholding device,
and how this can cause damage or distortion in the finished components.
Clamping applies improper pressure and reinforcement on the material and may cause a
safety hazard leading to injury or damage work. This also interferes with the smooth
operation of the work piece poor configuration could cause machine overwork, time and
material wastage due to the damaged work. Inaccurate clamping arises from differences in
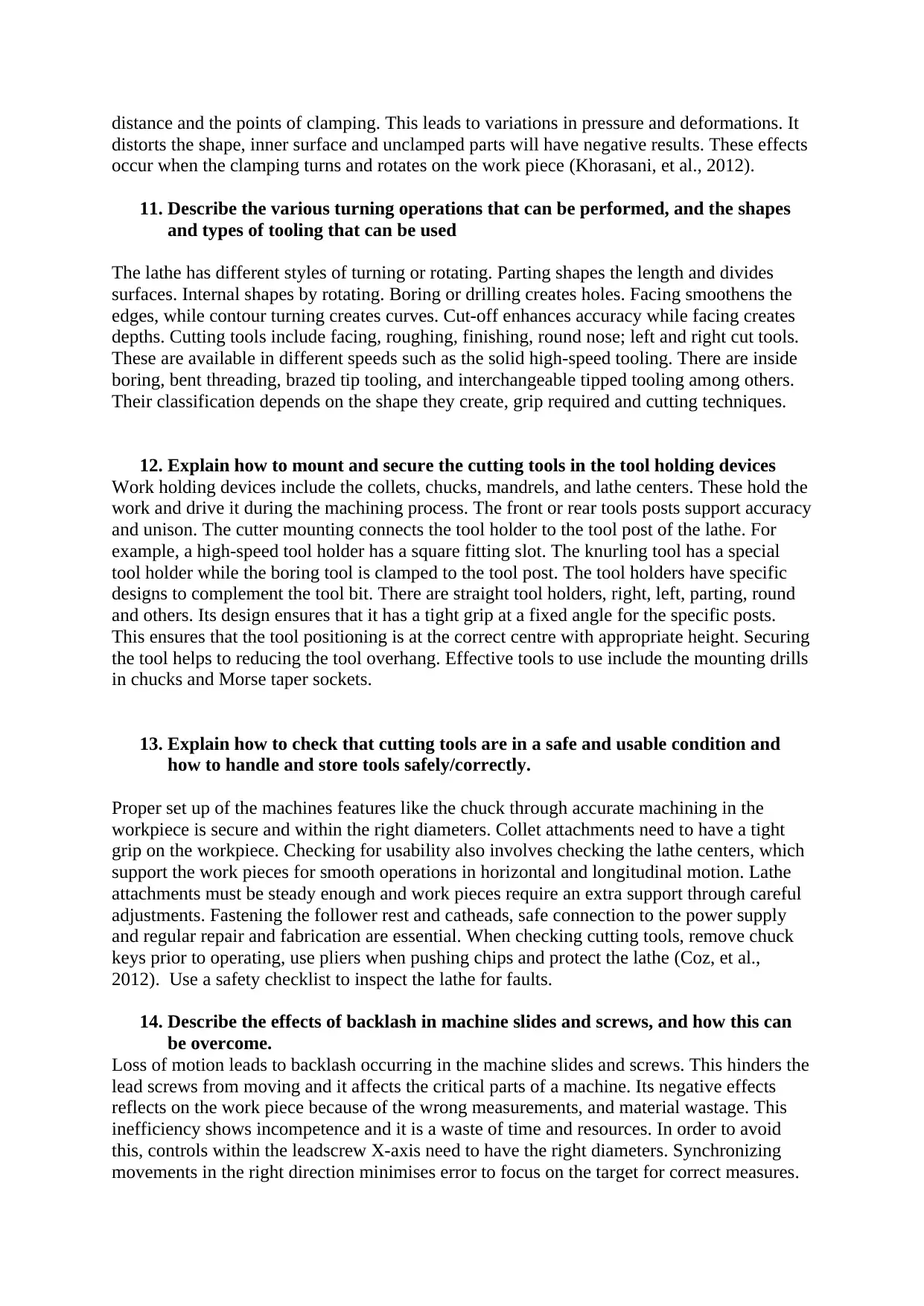
distance and the points of clamping. This leads to variations in pressure and deformations. It
distorts the shape, inner surface and unclamped parts will have negative results. These effects
occur when the clamping turns and rotates on the work piece (Khorasani, et al., 2012).
11. Describe the various turning operations that can be performed, and the shapes
and types of tooling that can be used
The lathe has different styles of turning or rotating. Parting shapes the length and divides
surfaces. Internal shapes by rotating. Boring or drilling creates holes. Facing smoothens the
edges, while contour turning creates curves. Cut-off enhances accuracy while facing creates
depths. Cutting tools include facing, roughing, finishing, round nose; left and right cut tools.
These are available in different speeds such as the solid high-speed tooling. There are inside
boring, bent threading, brazed tip tooling, and interchangeable tipped tooling among others.
Their classification depends on the shape they create, grip required and cutting techniques.
12. Explain how to mount and secure the cutting tools in the tool holding devices
Work holding devices include the collets, chucks, mandrels, and lathe centers. These hold the
work and drive it during the machining process. The front or rear tools posts support accuracy
and unison. The cutter mounting connects the tool holder to the tool post of the lathe. For
example, a high-speed tool holder has a square fitting slot. The knurling tool has a special
tool holder while the boring tool is clamped to the tool post. The tool holders have specific
designs to complement the tool bit. There are straight tool holders, right, left, parting, round
and others. Its design ensures that it has a tight grip at a fixed angle for the specific posts.
This ensures that the tool positioning is at the correct centre with appropriate height. Securing
the tool helps to reducing the tool overhang. Effective tools to use include the mounting drills
in chucks and Morse taper sockets.
13. Explain how to check that cutting tools are in a safe and usable condition and
how to handle and store tools safely/correctly.
Proper set up of the machines features like the chuck through accurate machining in the
workpiece is secure and within the right diameters. Collet attachments need to have a tight
grip on the workpiece. Checking for usability also involves checking the lathe centers, which
support the work pieces for smooth operations in horizontal and longitudinal motion. Lathe
attachments must be steady enough and work pieces require an extra support through careful
adjustments. Fastening the follower rest and catheads, safe connection to the power supply
and regular repair and fabrication are essential. When checking cutting tools, remove chuck
keys prior to operating, use pliers when pushing chips and protect the lathe (Coz, et al.,
2012). Use a safety checklist to inspect the lathe for faults.
14. Describe the effects of backlash in machine slides and screws, and how this can
be overcome.
Loss of motion leads to backlash occurring in the machine slides and screws. This hinders the
lead screws from moving and it affects the critical parts of a machine. Its negative effects
reflects on the work piece because of the wrong measurements, and material wastage. This
inefficiency shows incompetence and it is a waste of time and resources. In order to avoid
this, controls within the leadscrew X-axis need to have the right diameters. Synchronizing
movements in the right direction minimises error to focus on the target for correct measures.
distorts the shape, inner surface and unclamped parts will have negative results. These effects
occur when the clamping turns and rotates on the work piece (Khorasani, et al., 2012).
11. Describe the various turning operations that can be performed, and the shapes
and types of tooling that can be used
The lathe has different styles of turning or rotating. Parting shapes the length and divides
surfaces. Internal shapes by rotating. Boring or drilling creates holes. Facing smoothens the
edges, while contour turning creates curves. Cut-off enhances accuracy while facing creates
depths. Cutting tools include facing, roughing, finishing, round nose; left and right cut tools.
These are available in different speeds such as the solid high-speed tooling. There are inside
boring, bent threading, brazed tip tooling, and interchangeable tipped tooling among others.
Their classification depends on the shape they create, grip required and cutting techniques.
12. Explain how to mount and secure the cutting tools in the tool holding devices
Work holding devices include the collets, chucks, mandrels, and lathe centers. These hold the
work and drive it during the machining process. The front or rear tools posts support accuracy
and unison. The cutter mounting connects the tool holder to the tool post of the lathe. For
example, a high-speed tool holder has a square fitting slot. The knurling tool has a special
tool holder while the boring tool is clamped to the tool post. The tool holders have specific
designs to complement the tool bit. There are straight tool holders, right, left, parting, round
and others. Its design ensures that it has a tight grip at a fixed angle for the specific posts.
This ensures that the tool positioning is at the correct centre with appropriate height. Securing
the tool helps to reducing the tool overhang. Effective tools to use include the mounting drills
in chucks and Morse taper sockets.
13. Explain how to check that cutting tools are in a safe and usable condition and
how to handle and store tools safely/correctly.
Proper set up of the machines features like the chuck through accurate machining in the
workpiece is secure and within the right diameters. Collet attachments need to have a tight
grip on the workpiece. Checking for usability also involves checking the lathe centers, which
support the work pieces for smooth operations in horizontal and longitudinal motion. Lathe
attachments must be steady enough and work pieces require an extra support through careful
adjustments. Fastening the follower rest and catheads, safe connection to the power supply
and regular repair and fabrication are essential. When checking cutting tools, remove chuck
keys prior to operating, use pliers when pushing chips and protect the lathe (Coz, et al.,
2012). Use a safety checklist to inspect the lathe for faults.
14. Describe the effects of backlash in machine slides and screws, and how this can
be overcome.
Loss of motion leads to backlash occurring in the machine slides and screws. This hinders the
lead screws from moving and it affects the critical parts of a machine. Its negative effects
reflects on the work piece because of the wrong measurements, and material wastage. This
inefficiency shows incompetence and it is a waste of time and resources. In order to avoid
this, controls within the leadscrew X-axis need to have the right diameters. Synchronizing
movements in the right direction minimises error to focus on the target for correct measures.
Secure Best Marks with AI Grader
Need help grading? Try our AI Grader for instant feedback on your assignments.
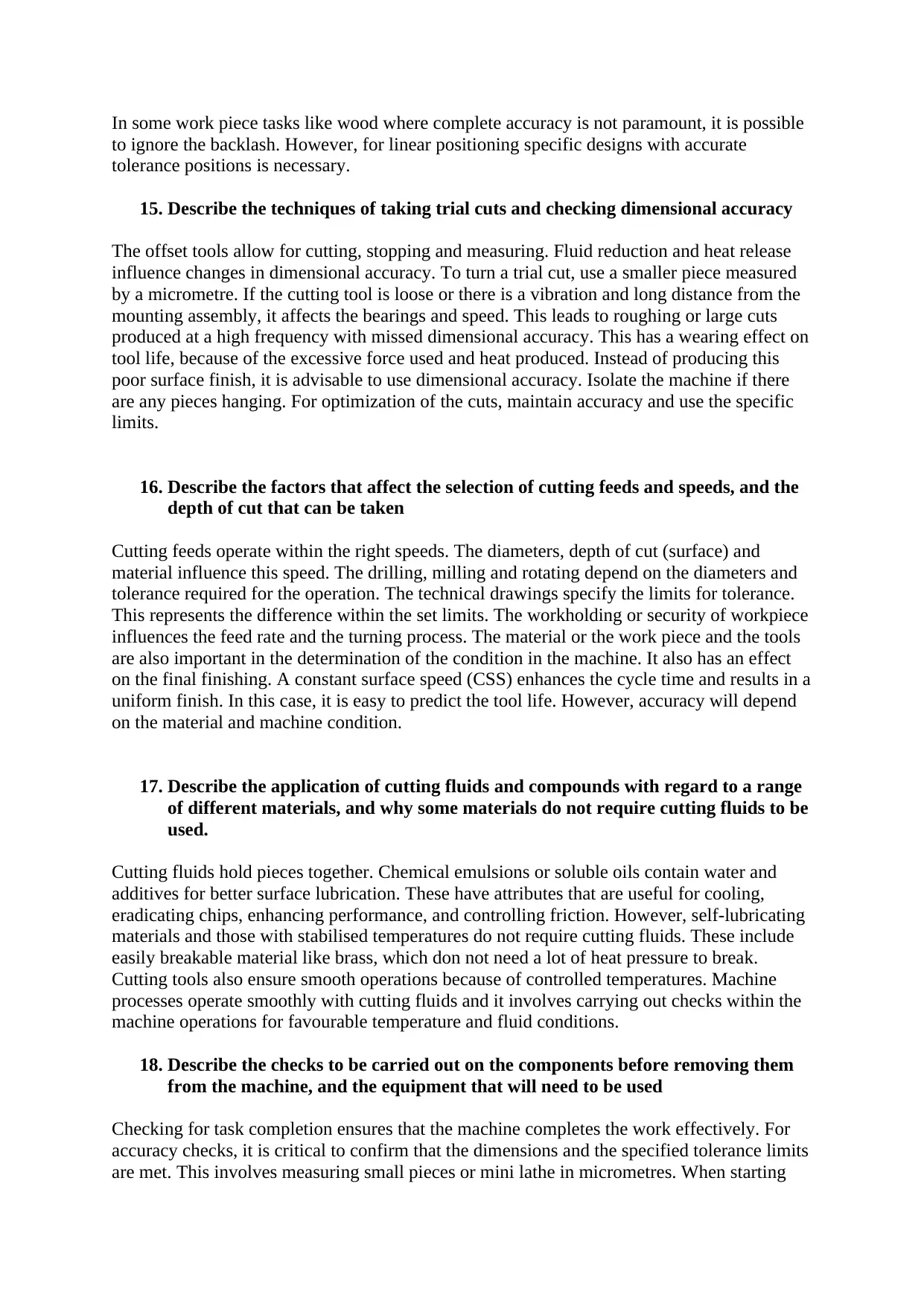
In some work piece tasks like wood where complete accuracy is not paramount, it is possible
to ignore the backlash. However, for linear positioning specific designs with accurate
tolerance positions is necessary.
15. Describe the techniques of taking trial cuts and checking dimensional accuracy
The offset tools allow for cutting, stopping and measuring. Fluid reduction and heat release
influence changes in dimensional accuracy. To turn a trial cut, use a smaller piece measured
by a micrometre. If the cutting tool is loose or there is a vibration and long distance from the
mounting assembly, it affects the bearings and speed. This leads to roughing or large cuts
produced at a high frequency with missed dimensional accuracy. This has a wearing effect on
tool life, because of the excessive force used and heat produced. Instead of producing this
poor surface finish, it is advisable to use dimensional accuracy. Isolate the machine if there
are any pieces hanging. For optimization of the cuts, maintain accuracy and use the specific
limits.
16. Describe the factors that affect the selection of cutting feeds and speeds, and the
depth of cut that can be taken
Cutting feeds operate within the right speeds. The diameters, depth of cut (surface) and
material influence this speed. The drilling, milling and rotating depend on the diameters and
tolerance required for the operation. The technical drawings specify the limits for tolerance.
This represents the difference within the set limits. The workholding or security of workpiece
influences the feed rate and the turning process. The material or the work piece and the tools
are also important in the determination of the condition in the machine. It also has an effect
on the final finishing. A constant surface speed (CSS) enhances the cycle time and results in a
uniform finish. In this case, it is easy to predict the tool life. However, accuracy will depend
on the material and machine condition.
17. Describe the application of cutting fluids and compounds with regard to a range
of different materials, and why some materials do not require cutting fluids to be
used.
Cutting fluids hold pieces together. Chemical emulsions or soluble oils contain water and
additives for better surface lubrication. These have attributes that are useful for cooling,
eradicating chips, enhancing performance, and controlling friction. However, self-lubricating
materials and those with stabilised temperatures do not require cutting fluids. These include
easily breakable material like brass, which don not need a lot of heat pressure to break.
Cutting tools also ensure smooth operations because of controlled temperatures. Machine
processes operate smoothly with cutting fluids and it involves carrying out checks within the
machine operations for favourable temperature and fluid conditions.
18. Describe the checks to be carried out on the components before removing them
from the machine, and the equipment that will need to be used
Checking for task completion ensures that the machine completes the work effectively. For
accuracy checks, it is critical to confirm that the dimensions and the specified tolerance limits
are met. This involves measuring small pieces or mini lathe in micrometres. When starting
to ignore the backlash. However, for linear positioning specific designs with accurate
tolerance positions is necessary.
15. Describe the techniques of taking trial cuts and checking dimensional accuracy
The offset tools allow for cutting, stopping and measuring. Fluid reduction and heat release
influence changes in dimensional accuracy. To turn a trial cut, use a smaller piece measured
by a micrometre. If the cutting tool is loose or there is a vibration and long distance from the
mounting assembly, it affects the bearings and speed. This leads to roughing or large cuts
produced at a high frequency with missed dimensional accuracy. This has a wearing effect on
tool life, because of the excessive force used and heat produced. Instead of producing this
poor surface finish, it is advisable to use dimensional accuracy. Isolate the machine if there
are any pieces hanging. For optimization of the cuts, maintain accuracy and use the specific
limits.
16. Describe the factors that affect the selection of cutting feeds and speeds, and the
depth of cut that can be taken
Cutting feeds operate within the right speeds. The diameters, depth of cut (surface) and
material influence this speed. The drilling, milling and rotating depend on the diameters and
tolerance required for the operation. The technical drawings specify the limits for tolerance.
This represents the difference within the set limits. The workholding or security of workpiece
influences the feed rate and the turning process. The material or the work piece and the tools
are also important in the determination of the condition in the machine. It also has an effect
on the final finishing. A constant surface speed (CSS) enhances the cycle time and results in a
uniform finish. In this case, it is easy to predict the tool life. However, accuracy will depend
on the material and machine condition.
17. Describe the application of cutting fluids and compounds with regard to a range
of different materials, and why some materials do not require cutting fluids to be
used.
Cutting fluids hold pieces together. Chemical emulsions or soluble oils contain water and
additives for better surface lubrication. These have attributes that are useful for cooling,
eradicating chips, enhancing performance, and controlling friction. However, self-lubricating
materials and those with stabilised temperatures do not require cutting fluids. These include
easily breakable material like brass, which don not need a lot of heat pressure to break.
Cutting tools also ensure smooth operations because of controlled temperatures. Machine
processes operate smoothly with cutting fluids and it involves carrying out checks within the
machine operations for favourable temperature and fluid conditions.
18. Describe the checks to be carried out on the components before removing them
from the machine, and the equipment that will need to be used
Checking for task completion ensures that the machine completes the work effectively. For
accuracy checks, it is critical to confirm that the dimensions and the specified tolerance limits
are met. This involves measuring small pieces or mini lathe in micrometres. When starting
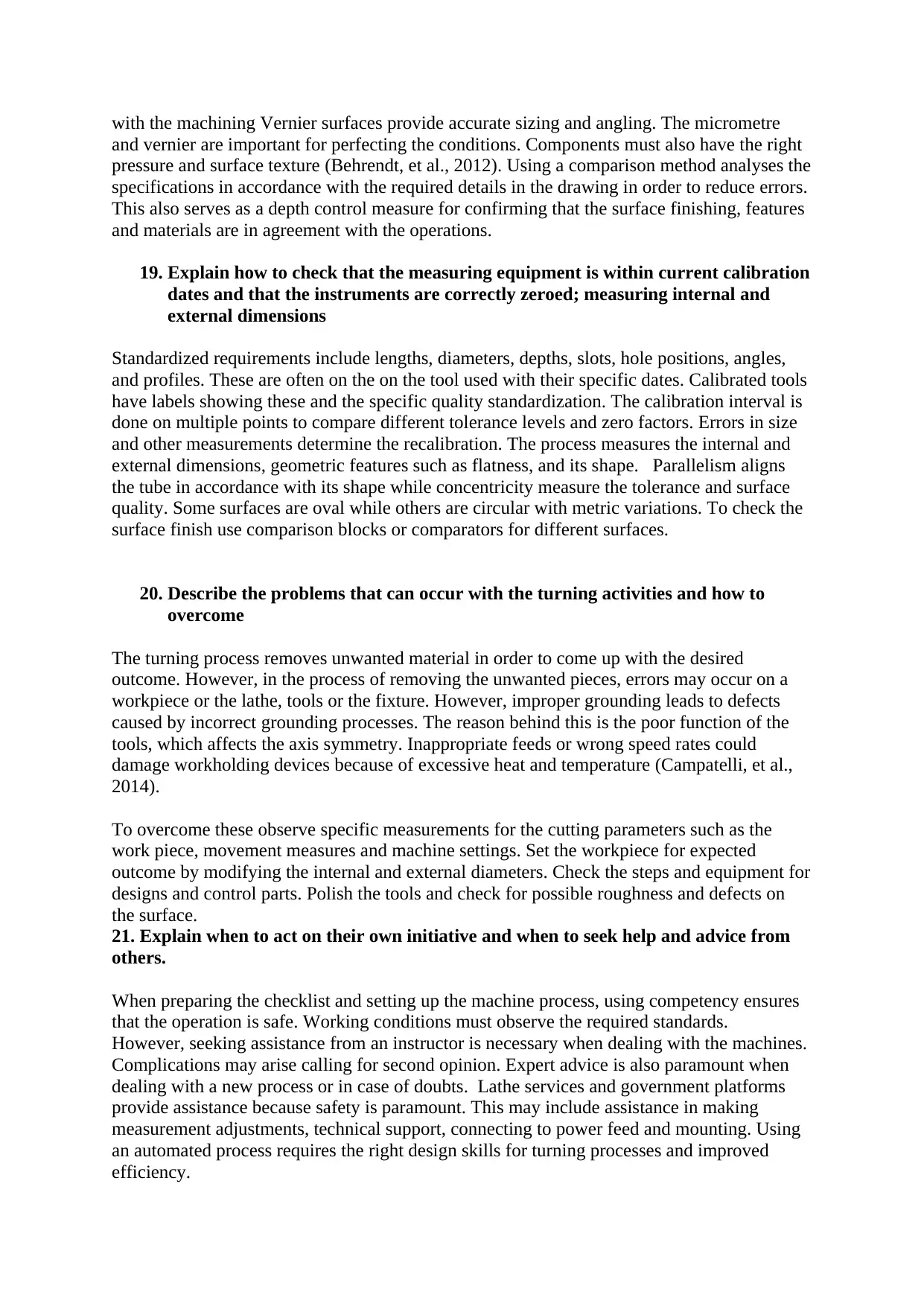
with the machining Vernier surfaces provide accurate sizing and angling. The micrometre
and vernier are important for perfecting the conditions. Components must also have the right
pressure and surface texture (Behrendt, et al., 2012). Using a comparison method analyses the
specifications in accordance with the required details in the drawing in order to reduce errors.
This also serves as a depth control measure for confirming that the surface finishing, features
and materials are in agreement with the operations.
19. Explain how to check that the measuring equipment is within current calibration
dates and that the instruments are correctly zeroed; measuring internal and
external dimensions
Standardized requirements include lengths, diameters, depths, slots, hole positions, angles,
and profiles. These are often on the on the tool used with their specific dates. Calibrated tools
have labels showing these and the specific quality standardization. The calibration interval is
done on multiple points to compare different tolerance levels and zero factors. Errors in size
and other measurements determine the recalibration. The process measures the internal and
external dimensions, geometric features such as flatness, and its shape. Parallelism aligns
the tube in accordance with its shape while concentricity measure the tolerance and surface
quality. Some surfaces are oval while others are circular with metric variations. To check the
surface finish use comparison blocks or comparators for different surfaces.
20. Describe the problems that can occur with the turning activities and how to
overcome
The turning process removes unwanted material in order to come up with the desired
outcome. However, in the process of removing the unwanted pieces, errors may occur on a
workpiece or the lathe, tools or the fixture. However, improper grounding leads to defects
caused by incorrect grounding processes. The reason behind this is the poor function of the
tools, which affects the axis symmetry. Inappropriate feeds or wrong speed rates could
damage workholding devices because of excessive heat and temperature (Campatelli, et al.,
2014).
To overcome these observe specific measurements for the cutting parameters such as the
work piece, movement measures and machine settings. Set the workpiece for expected
outcome by modifying the internal and external diameters. Check the steps and equipment for
designs and control parts. Polish the tools and check for possible roughness and defects on
the surface.
21. Explain when to act on their own initiative and when to seek help and advice from
others.
When preparing the checklist and setting up the machine process, using competency ensures
that the operation is safe. Working conditions must observe the required standards.
However, seeking assistance from an instructor is necessary when dealing with the machines.
Complications may arise calling for second opinion. Expert advice is also paramount when
dealing with a new process or in case of doubts. Lathe services and government platforms
provide assistance because safety is paramount. This may include assistance in making
measurement adjustments, technical support, connecting to power feed and mounting. Using
an automated process requires the right design skills for turning processes and improved
efficiency.
and vernier are important for perfecting the conditions. Components must also have the right
pressure and surface texture (Behrendt, et al., 2012). Using a comparison method analyses the
specifications in accordance with the required details in the drawing in order to reduce errors.
This also serves as a depth control measure for confirming that the surface finishing, features
and materials are in agreement with the operations.
19. Explain how to check that the measuring equipment is within current calibration
dates and that the instruments are correctly zeroed; measuring internal and
external dimensions
Standardized requirements include lengths, diameters, depths, slots, hole positions, angles,
and profiles. These are often on the on the tool used with their specific dates. Calibrated tools
have labels showing these and the specific quality standardization. The calibration interval is
done on multiple points to compare different tolerance levels and zero factors. Errors in size
and other measurements determine the recalibration. The process measures the internal and
external dimensions, geometric features such as flatness, and its shape. Parallelism aligns
the tube in accordance with its shape while concentricity measure the tolerance and surface
quality. Some surfaces are oval while others are circular with metric variations. To check the
surface finish use comparison blocks or comparators for different surfaces.
20. Describe the problems that can occur with the turning activities and how to
overcome
The turning process removes unwanted material in order to come up with the desired
outcome. However, in the process of removing the unwanted pieces, errors may occur on a
workpiece or the lathe, tools or the fixture. However, improper grounding leads to defects
caused by incorrect grounding processes. The reason behind this is the poor function of the
tools, which affects the axis symmetry. Inappropriate feeds or wrong speed rates could
damage workholding devices because of excessive heat and temperature (Campatelli, et al.,
2014).
To overcome these observe specific measurements for the cutting parameters such as the
work piece, movement measures and machine settings. Set the workpiece for expected
outcome by modifying the internal and external diameters. Check the steps and equipment for
designs and control parts. Polish the tools and check for possible roughness and defects on
the surface.
21. Explain when to act on their own initiative and when to seek help and advice from
others.
When preparing the checklist and setting up the machine process, using competency ensures
that the operation is safe. Working conditions must observe the required standards.
However, seeking assistance from an instructor is necessary when dealing with the machines.
Complications may arise calling for second opinion. Expert advice is also paramount when
dealing with a new process or in case of doubts. Lathe services and government platforms
provide assistance because safety is paramount. This may include assistance in making
measurement adjustments, technical support, connecting to power feed and mounting. Using
an automated process requires the right design skills for turning processes and improved
efficiency.
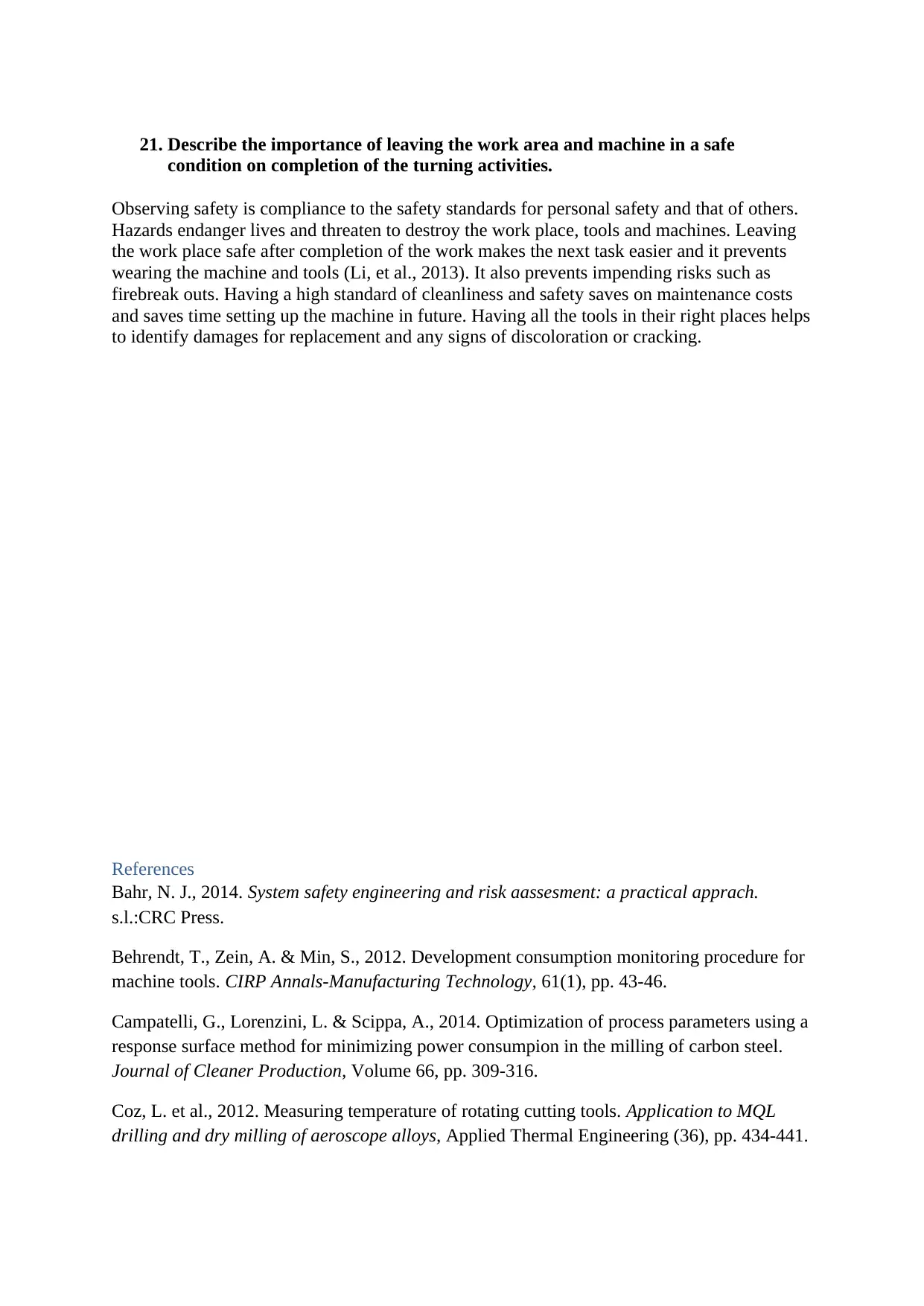
21. Describe the importance of leaving the work area and machine in a safe
condition on completion of the turning activities.
Observing safety is compliance to the safety standards for personal safety and that of others.
Hazards endanger lives and threaten to destroy the work place, tools and machines. Leaving
the work place safe after completion of the work makes the next task easier and it prevents
wearing the machine and tools (Li, et al., 2013). It also prevents impending risks such as
firebreak outs. Having a high standard of cleanliness and safety saves on maintenance costs
and saves time setting up the machine in future. Having all the tools in their right places helps
to identify damages for replacement and any signs of discoloration or cracking.
References
Bahr, N. J., 2014. System safety engineering and risk aassesment: a practical apprach.
s.l.:CRC Press.
Behrendt, T., Zein, A. & Min, S., 2012. Development consumption monitoring procedure for
machine tools. CIRP Annals-Manufacturing Technology, 61(1), pp. 43-46.
Campatelli, G., Lorenzini, L. & Scippa, A., 2014. Optimization of process parameters using a
response surface method for minimizing power consumpion in the milling of carbon steel.
Journal of Cleaner Production, Volume 66, pp. 309-316.
Coz, L. et al., 2012. Measuring temperature of rotating cutting tools. Application to MQL
drilling and dry milling of aeroscope alloys, Applied Thermal Engineering (36), pp. 434-441.
condition on completion of the turning activities.
Observing safety is compliance to the safety standards for personal safety and that of others.
Hazards endanger lives and threaten to destroy the work place, tools and machines. Leaving
the work place safe after completion of the work makes the next task easier and it prevents
wearing the machine and tools (Li, et al., 2013). It also prevents impending risks such as
firebreak outs. Having a high standard of cleanliness and safety saves on maintenance costs
and saves time setting up the machine in future. Having all the tools in their right places helps
to identify damages for replacement and any signs of discoloration or cracking.
References
Bahr, N. J., 2014. System safety engineering and risk aassesment: a practical apprach.
s.l.:CRC Press.
Behrendt, T., Zein, A. & Min, S., 2012. Development consumption monitoring procedure for
machine tools. CIRP Annals-Manufacturing Technology, 61(1), pp. 43-46.
Campatelli, G., Lorenzini, L. & Scippa, A., 2014. Optimization of process parameters using a
response surface method for minimizing power consumpion in the milling of carbon steel.
Journal of Cleaner Production, Volume 66, pp. 309-316.
Coz, L. et al., 2012. Measuring temperature of rotating cutting tools. Application to MQL
drilling and dry milling of aeroscope alloys, Applied Thermal Engineering (36), pp. 434-441.
Paraphrase This Document
Need a fresh take? Get an instant paraphrase of this document with our AI Paraphraser
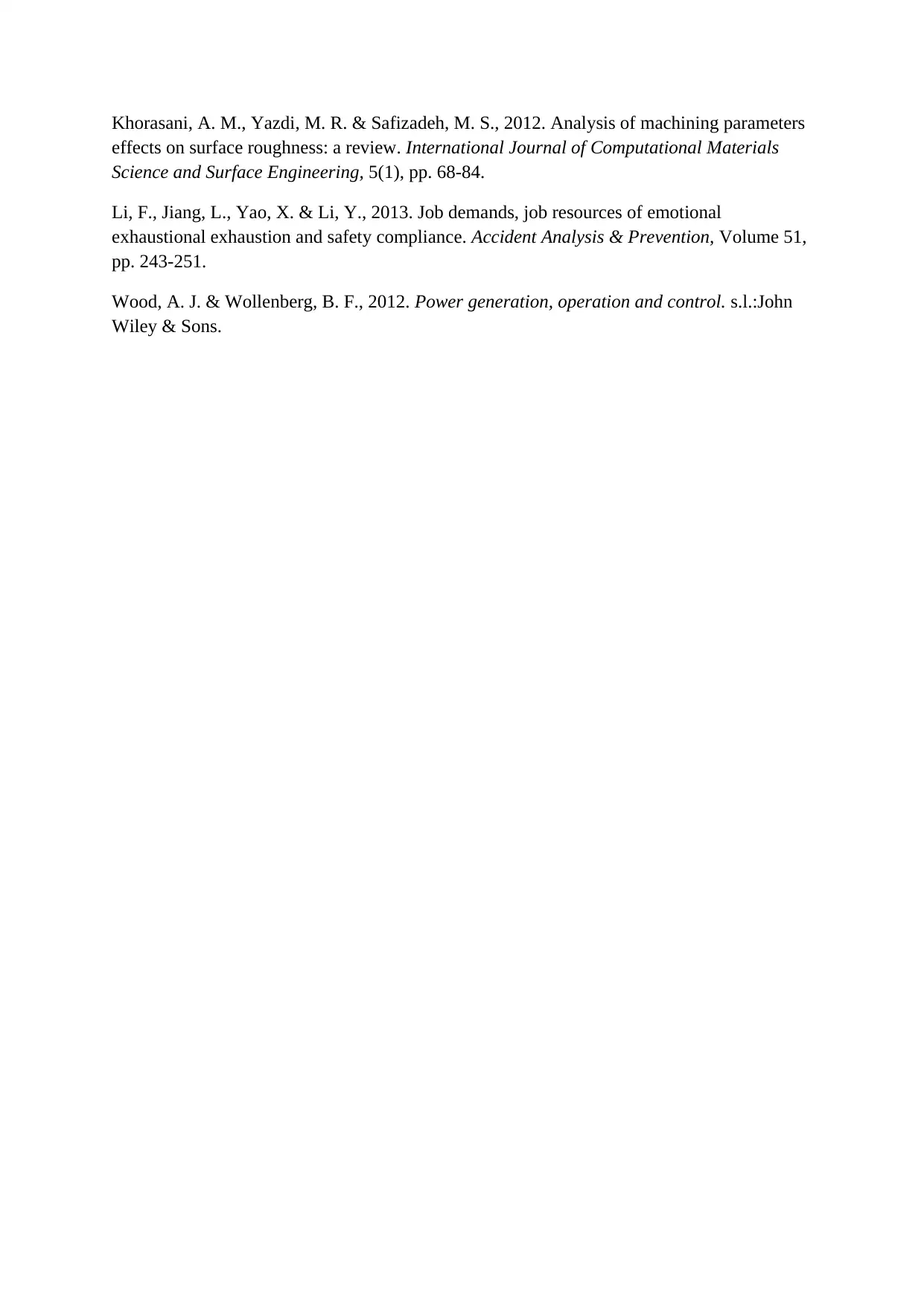
Khorasani, A. M., Yazdi, M. R. & Safizadeh, M. S., 2012. Analysis of machining parameters
effects on surface roughness: a review. International Journal of Computational Materials
Science and Surface Engineering, 5(1), pp. 68-84.
Li, F., Jiang, L., Yao, X. & Li, Y., 2013. Job demands, job resources of emotional
exhaustional exhaustion and safety compliance. Accident Analysis & Prevention, Volume 51,
pp. 243-251.
Wood, A. J. & Wollenberg, B. F., 2012. Power generation, operation and control. s.l.:John
Wiley & Sons.
effects on surface roughness: a review. International Journal of Computational Materials
Science and Surface Engineering, 5(1), pp. 68-84.
Li, F., Jiang, L., Yao, X. & Li, Y., 2013. Job demands, job resources of emotional
exhaustional exhaustion and safety compliance. Accident Analysis & Prevention, Volume 51,
pp. 243-251.
Wood, A. J. & Wollenberg, B. F., 2012. Power generation, operation and control. s.l.:John
Wiley & Sons.
1 out of 8
Related Documents
![[object Object]](/_next/image/?url=%2F_next%2Fstatic%2Fmedia%2Flogo.6d15ce61.png&w=640&q=75)
Your All-in-One AI-Powered Toolkit for Academic Success.
 +13062052269
info@desklib.com
Available 24*7 on WhatsApp / Email
Unlock your academic potential
© 2024  |  Zucol Services PVT LTD  |  All rights reserved.